孔的加工及其达到的精度
各种加工方法的经济精度和表面粗糙度

各种加工方法能够达到的尺寸的经济精度表1 孔加工的经济精度表2 圆锥形孔加工的经济精度表3 圆柱形深孔加工的经济精度表4 花键孔加工的经济精度表5 外圆柱表面加工的经济精度表6 端面加工的经济精度(mm)表7 用成形铣刀加工的经济精度(mm)注:指加工表面至基准的尺寸精度。
表8 同时加工平行表面的经刘精度(mm)注:指两平行表面距离的尺寸精度。
表9 平面加工的经济精度注:1 表内资料适用于尺寸<1m,结构刚性好的零件加工,用光洁的加工表面作为定位和测量基准。
2 端铣刀铣削的加工精度在相同的条件下大体上比圆柱铣刀铣削高一级。
3 细铣仅用于端铣刀铣削。
表10 公制螺纹加工的经济精度表11 花键加工的经济精度表12 齿形加工的经济精度各种加工方法能够达到的形状的经济精度表13 平面度和直线度的经济精度表14 圆柱形表面形状精度的经济精度注:形状精度等级的公差值见附表2、3。
表15 曲面加工的经济精度表16 在各种机床上加工时形状的平均经济精度各种加工方法所能够达到的相互位置的经济精度表17 平行度的经济精度表18 端面跳动和垂直度的经济精度表19 同轴度的经济精度表20 轴心线相互平行的孔的位置经济精度注:对于钻、卧镗及组合机床的镗孔偏差同样适用于铰孔。
表21 轴心线相互垂直的孔的位置经济精度注:在镗空间的垂直孔时,中心距误差可按上式相应的找正方法选用。
各种加工方法能够达到的零件表面粗糙度表22 各种加工方法能够达到的零件表面粗糙度各类型面的加工方案及经济精度表23 外圆表面加工方案表24 孔加工方案表25 平面加工方案——机械篇标准公差及形位公差附表1 标准公差值注:基本尺寸小于1mm时,无IT14至IT18。
13 22-4-25 10:32附表2 平面度、直线度公差值附表3 圆度、圆柱度公差值附表4 平行度、垂直度、倾斜度公差值附表5 同轴度、对称度、圆跳动、全跳动公差值参考文献1 《金属机械加工工艺人员手册》修订本上海科学技术出版社1981年2 《机械制造工艺学》顾崇衔等编著陕西科学技术出版社1982年3 《航空机械设计手册》第三机械工业部612所编1979年4 《机械制造工艺学课程设计简明手册》华中工学院机械制造工艺教研室编1981年5 《机械工程手册》第46篇机械工业出版社1981年6 《圆柱齿轮加工》上海科学技术出版社1979年切削用量切削用量的选择原则正确地选择切削用量,对提高切削效率,保证必要的刀具耐用度和经济性,保证加工质量,具有重要的作用。
提高孔加工的精度的方法

提高孔加工的精度的方法对于钳工专业而言,钻孔是其中最重要的加工操作,它是一种确定孔系和孔位置准确度的方式。
钻削加工时,操作者可以利用理论联系实际的方法分析出孔的中心位置、确定钻床主轴线和被加工工件表面的垂直度以及做好麻花钻刃磨的质量提升工作,从而达到不断提升钻孔工艺以及提高钳工操作能力的目的,希望本文能够使更多的人掌握钳工孔加工精度的方法在钳工专业的基本实习训练中,孔加工是相对比较难掌握的基本操作之一。
在孔加工实习训练中反映问题最多的是单孔的直径控制和多孔的孔距精度控制,特别是对孔距的精度控制最为突出。
在实践中,如果是成批量的生产加工,可以通过制做工卡具来实现对孔距的控制,这样不仅能满足产品的技术要求,还能极大地提高工作效率。
但在小批量的生产加工中,对孔和孔距的形状和位置精度控制,则要通过划线、找正等方法来予以保证。
一、钳工孔加工实习课题训练中容易出现的问题:1、钻孔时孔径超出尺寸要求,一般是孔径过大;2、孔的表面粗糙度超出规定的技术要求;3、孔的垂直度超出位置公差要求;4、孔距(包括边心距和孔距)超出尺寸公差的要求;二、孔加工中出现问题的主要原因分析:1、钻头刃磨时两个主切削刃不对称,在钻削过程中,使钻头的径向受力;2、对钻削的切削速度选择不当;3、钻削时工件未与钻头保持垂直;4、未对孔距尺寸公差进行跟踪控制;三、提高孔加工精度的方法:在孔加工的课题训练中,对于前三个问题,需要加强练习。
比如主切削刃的不对称问题,在刃磨时,要对砂轮面进行检查,如果砂轮的磨削面不平整,应及时进行修整,刃磨的角度应保持一致。
对于不同的孔径,要选择相应的切削速度。
在钻孔过程中,自始至终都要避免钻头的径向受力。
钻孔时,不仅要保证平口钳的上平面与钻头的垂直,也要保证夹持工件时夹持面与加工表面的垂直。
夹持要牢固,避免在钻孔过程中,由于夹持不牢使工件发生滑陷。
这些都需要在实习的过程中让学生慢慢体会和认真掌握的。
最容易出现也是最难掌握的问题是孔距精度的控制问题,在这里作一下重点阐述。
浅淡模具制造中孔的加工方法
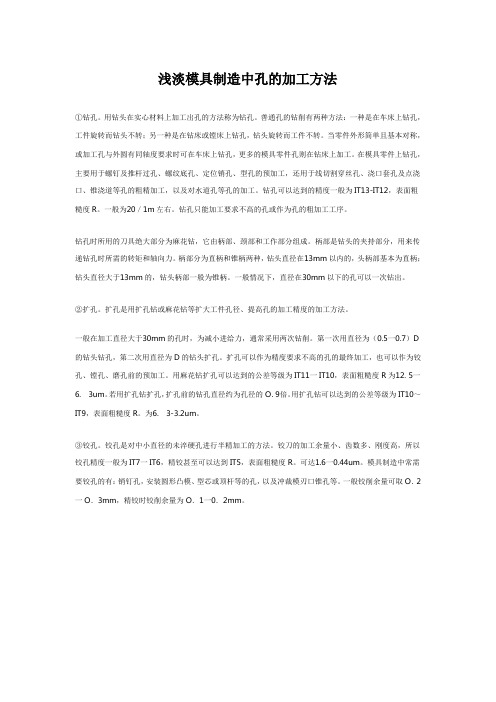
浅淡模具制造中孔的加工方法①钻孔。
用钻头在实心材料上加工出孔的方法称为钻孔。
善通孔的钻削有两种方法:一种是在车床上钻孔,工件旋转而钻头不转;另一种是在钻床或镗床上钻孔,钻头旋转而工件不转。
当零件外形简单且基本对称,或加工孔与外圆有同轴度要求时可在车床上钻孔,更多的模具零件孔则在钻床上加工。
在模具零件上钻孔,主要用于螺钉及推杆过孔、螺纹底孔、定位销孔、型孔的预加工,还用于线切割穿丝孔、浇口套孔及点浇口、锥浇道等孔的粗精加工,以及对水道孔等孔的加工。
钻孔可以达到的精度一般为IT13-IT12,表面粗糙度R。
一般为20/1m左右。
钻孔只能加工要求不高的孔或作为孔的粗加工工序。
钻孔时所用的刀具绝大部分为麻花钻,它由柄部、颈部和工作部分组成。
柄部是钻头的夹持部分,用来传递钻孔时所需的转矩和轴向力。
柄部分为直柄和锥柄两种,钻头直径在13mm以内的,头柄部基本为直柄;钻头直径大于13mm的,钻头柄部一般为锥柄。
一般情况下,直径在30mm以下的孔可以一次钻出。
②扩孔。
扩孔是用扩孔钻或麻花钻等扩大工件孔径、提高孔的加工精度的加工方法。
一般在加工直径大于30mm的孔时,为减小进给力,通常采用两次钻削。
第一次用直径为(0.5一0.7)D的钻头钻孔,第二次用直径为D的钻头扩孔。
扩孔可以作为精度要求不高的孔的最终加工,也可以作为铰孔、镗孔、磨孔前的预加工。
用麻花钻扩孔可以达到的公差等级为IT11一IT10,表面粗糙度R为12. 5一6. 3um。
若用扩孔钻扩孔,扩孔前的钻孔直径约为孔径的O.9倍。
用扩孔钻可以达到的公差等级为IT10~IT9,表面粗糙度R。
为6. 3-3.2um。
③铰孔。
铰孔是对中小直径的未淬硬孔进行半精加工的方法。
铰刀的加工余量小、齿数多、刚度高,所以铰孔精度一般为IT7一IT6,精铰甚至可以达到IT5,表面粗糙度R。
可达1.6一0.44um。
模具制造中常需要铰孔的有:销钉孔,安装圆形凸模、型芯或顶杆等的孔,以及冲裁模刃口锥孔等。
孔加工技术

四、铣镗加工中心
铣镗加工中心是一种计算机控制的、具有刀库的、 能自动 换刀的铣镗床。
主要部件: 刀库 主轴箱 机械手 工作台 数控装置
第六 节 镗刀和镗床加工工艺特点
一、镗刀 镗床常用的镗刀有单刃镗刀和双刃镗刀两 种。
1、单刃镗刀安装在镗刀杆上,加工的孔径大小由调整刀头 的伸出长度来保证,多用于单件小批量生产中。
➢横刃斜角Ψ 主切削刃与横刃在钻头端面上投影的夹角。 ➢螺旋角β 最外缘螺旋线切线与轴线的夹角
3.钻头受力分析:
在各切削刃上:
轴向力Ff 径向力Fp 切向力Fc 总的扭矩:
M=M0+M01+M横 轴向力:
F=F0+F01+F横 轴向力主要由横刃产生,
扭矩主要由主刃产生。
4.麻花钻的缺点shortcoming of twist drills
由于内排屑深
孔钻可以避免
切屑划伤孔壁
故加工质量较
高,精度达
IT9-7,Ra值
达3.2μm。
扁钻轴向尺寸小、刚性好,结构简单、制造容易,便 于采用先进刀具材料,换刀方便,适用于数控机床,尤 其在加工大直径孔(D>38mm)时,更是比麻花钻经济。
套料钻:中孔结构,切削刃分布在四周,加工孔时它只 切出一个环形的孔,而中间留下的料芯可二次使用。 适于加工直径大于60mm的深孔及贵重材料。
(3)铰孔的应用:铰孔用于软材料零件孔的精加工,不 能加工硬材料; 铰孔孔径φ1~φ80
铰孔的精度和表面粗糙度主要取决于铰刀的精度、安装方式、切
削用量、切削液等条件。为避免产生积屑瘤,铰孔时应采用较低
的切削速度、较大的进给量并施加适当的切削液。
铰刀分为机用铰刀和手用铰刀。手用铰刀的铰削直径为: ø1~ø50mm机用铰刀为: ø10~ø80mm
浅谈钳工实习教学中孔加工的精度
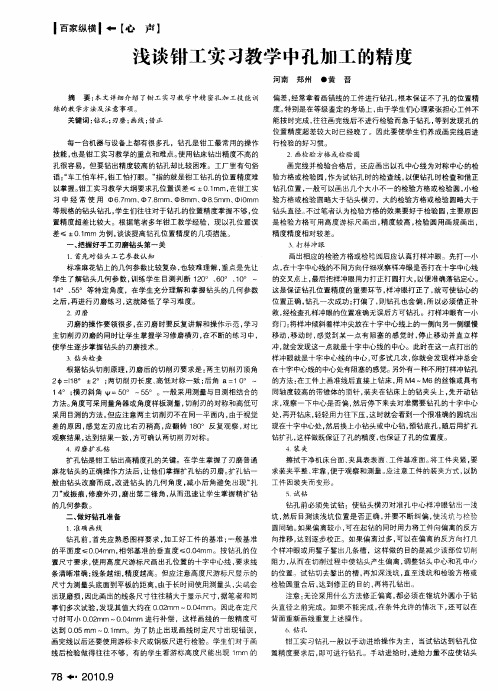
置精 度超 差比较大 。根据笔者 多年钳 工教学经 验 。现 以 位 置误 是检验 方格可 用 高度游 标尺 画 出 , 度较 高 , 验 圆用画 规画 出 , L 精 检 差≤ ±01 . mm 为例 , 谈谈提高 钻孔位 置精度 的几项措施 精 度精度 相对较 差。
一
、
把握好手 工刃磨钻 头第一 关
2 磨 刃
位 置正确 , 钻孔一 次成功 ; 偏 了, 打 则钻孔也 会偏 , 以必须 借正补 所 救 , 查孔样;眼的位置 准确无误后 方可钻孔 。打 样冲眼有一小 经检 中 窍 门 : 冲倾斜着样冲尖放 在十字 中心 线上的一侧 向另一侧缓慢 将样
移 动 , 动时 , 移 感觉 到某一 点 有阳塞 的感 觉 时 , 止移 动并直 立样 停
练 的教 学方 法及 注意事 项。
关键 词 : 孔 ; 钻 刃磨 ; 线 ; 正 画 借
能按 时完成 , 往往 画完线后不 进行检验 而急 于钻孔 . 到发现 孔 的 等 位置 精度超 差较大 时已经晚 了。 因此 要使学 生们养成 画完线 后进
行检 验的好 习惯。
2 画检 验 方 格 或 检 验 圆
扩孔钻是 钳工钻 出高精度孔 的关键 。在学 生掌握 了 刃磨 普通
麻 花钻头 的正确操作 方法后 , 让他们掌 握扩孔 钻的刃 磨。 孔钻一 扩 般 由钻 头改磨而 成 。 改进 钻头 的几何 角 度 , 小后 角避 免 出现 “ 减 扎
刃磨 的操作要领 很 多, 刃磨 时要反复讲 解和 操作示 范 , 在 学习
主切 削刃刃磨 的同时让 学生掌握学 习修磨 横刃 , 不断 的练 习中 , 在
使学生逐 步掌握 钻头的 刃磨技术 。
3 钻 头 检 查
内孔的加工讲解
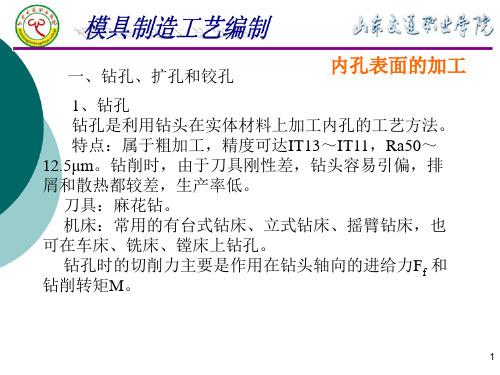
15
11
四、磨孔与孔的精密加工 1 磨孔工艺特点:属于孔的精加方法。精度可达IT7, Ra1.6~0.4 μm。 磨孔不仅能获得较高的尺寸精度和表面质量,而且 还可以提高孔的位置精度和孔的轴线的直线度。与外圆 磨削相比,工作条件较差:砂轮直径小,刚性差,排屑 和散热困难,生产率低。对于淬硬零件中的孔加工,磨 孔是主要的加工方法。 内孔为断续圆周表面(如有键槽或花键的孔)、阶 梯孔及盲孔时,常采用磨孔作为精加工。
研磨孔是一种光整加工方法。精度可达IT7~IT6, Ra0.4~0.025μm,形状精度也有相应的提高,但不能提 高位置精度。
16
珩磨头对孔施加一定压力,结构如图;切除极小的 加工余量。
17
②研磨孔是一种光整加工方法。精度可达IT7~IT6, Ra0.4~0.025μm,形状精度也有相应的提高,但不能提 高位置精度。需要在精镗、精铰或精磨之后进行。
18
固定式研磨棒多用于单件生产。带槽研磨棒便于存 贮研磨剂,用于粗研,光滑研磨棒,一般用于精研。如 图所示 。所有研具采用比工件软的材料制成,这些材料 为铸铁、铜、青铜、巴氏合金及硬木等。有时也可用钢 做研具。研磨时,部分磨粒悬浮于工件与研具之间,部 分磨粒则嵌入研具的表面层,工件与研具作相对运动, 磨料就在工件表面上切除很薄的一层金属 ( 主要是上工 序在工件表面上留下的凸峰 ) 。
12
磨孔时砂轮的尺寸受被加工孔径尺寸的限制,一般 砂轮直径为工件孔径的 0.5—0.9 倍,磨头轴的直径和 长度也取决于被加工孔的直径和深度。故磨削速度低, 磨头的刚度差,磨削质量和生产率均受到影响。
机加工第四章孔加工

六、拉削(P73)
拉削是一种高生产率的加工方法。加工精度可达IT7, Ra值可达0.8~0.4mm。 拉刀是一种多齿刀具。拉削时,由于后一个刀齿直径 大于前一个刀齿直径,从而能够一层层从工件上切出 金属。拉削过程如P74图4-19所示。 拉削视频 外拉削视频
圆孔拉刀的组成部分及作用(P73)
头部L1:用来将拉刀夹持在机床上并传递动力; 颈部L2:直径最小,拉力过大时在此部位发生断裂; 过渡锥L3:使拉刀容易进入工件的孔中; 前导部分L4:起引导作用,使工件轴线和拉孔轴线重 合; 切削部分L5:承担主要的切削任务; 校准部分L6:没有齿升量,起刮光孔壁和校正孔径作 用; 后导部分L7:保证拉刀最后一齿与工件间的正确位置。 拉孔刀视频
确定孔的加工方案的原则:首选满足技术要求,同时 考虑经济性和生产率等方面的因素。 拟定孔的加工方案比外圆表面复杂,这是因为: 1)孔的类型很多,功用不同,孔径和孔径比及技术要 求相关甚远; 2)孔的加工方法很多,且每一种加工都有一定的局限 性; 3)带孔零件的结构和尺寸多种多样。
一、机床的选用(P77)
铰削加工视频
2、铰削的特点(P70)
1)较高的精度和较低的Ra值:主要是刀具、加余量及切 削条件所致。 2)铰孔纠正位置误差的能力很差; 3)适应小孔和深孔的加工,Φ80mm以上的孔径不宜铰削 加工; 4)铰削的适应性较差:不能加工阶梯孔、短孔,且是定 径刀具。 5)可加工钢、铸铁和有色金属件,但不宜加工淬火件和 硬度较高的材料 。
二、孔的分类(P65)
根据孔的结构和用途,可分为以下几种类型:(如 P65图4-1和图4-2所示) 1、紧固孔和辅助孔:IT12~IT11;Ra值12.5~6.3um。 2、回转体零件的轴心孔:一般是与轴类零件相配合的表 面或是其它表面的基准面。对精度要求很高。 3、箱体支架类零件的轴承孔:孔本身尺寸精度及Ra值均 要求很高;孔与孔、孔与基准面之间也有很高的位置 精度要求。
高精度孔的加工方法

高精度孔的加工方法
高精度孔的加工方法是指对于精度要求较高的孔进行加工的方法,例如在精密机械、航空航天、高速列车等领域中需要使用的孔。
高精度孔的加工需要保证孔的直径、圆度、表面质量等指标都达到一定的要求。
目前常见的高精度孔加工方法有以下几种:
1. 珩磨加工:珩磨是一种高速旋转的研磨工艺,通过磨头在被加工物表面的摩擦作用中去除材料,从而达到加工目的。
珩磨加工可以在孔内进行,可以加工出高精度圆度的孔。
2. 钻孔加工:钻孔是最常见的孔加工方法之一,可以使用林格曼钻头等工具进行。
钻孔加工可以达到较高的精度要求,但是对于深孔加工会出现偏差的问题。
3. 放电加工:放电加工是一种特殊的非机械加工方法,通过电火花放电来将被加工物表面的材料溶解或脱落,从而达到加工的目的。
放电加工可以加工出高精度的孔,但是加工速度较慢。
4. 激光加工:激光加工是一种高精度的非机械加工方法,通过激光束直接照射被加工物表面,将材料蒸发或熔化,从而达到加工目的。
激光加工可以加工出极高精度的孔,但是设备价格高昂,适用范围有限。
- 1 -。
钻孔工艺精度标准
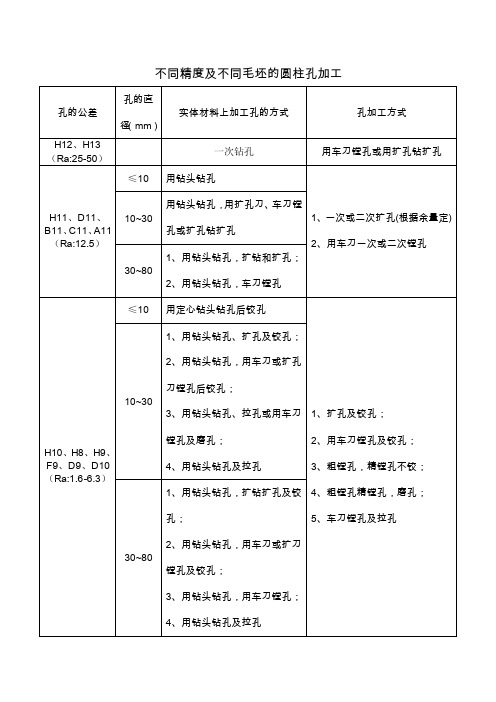
不同精度及不同毛坯的圆柱孔加工例:孔Φ25(0,+0.033),孔公差H8,麻花钻至孔Φ24.8,铰孔至Φ25(0,+0.033)孔Φ35(0,+0.062),孔公差H7,麻花钻Φ34.8,铰孔至Φ35(0,+0.062)Φ8(0,+0.018),孔公差约H7-H8,中心钻定位,麻花钻至Φ6,粗镗至Φ7.5,精镗至Φ8(0,+0.018)1、钻削直径较大的孔(大于30mm)时,不宜用大钻头一次钻出,最好分多次钻削,即先用直径较小的钻头钻孔,再用较大直径钻头扩到所要求的尺寸。
基孔制选作基准的孔称为基准孔,基准孔代号H(下偏差值0,上偏差值正值)基轴制选作基准的轴称为基准轴,基准轴代号h(上偏差值0,下偏差值负数)外圆面加工1.粗车:主要作为外圆的预加工,除淬硬钢以外,各种零件的加工都适用。
当零件的外圆要求精度低、表面粗糙度较大时,只粗车即可。
2.粗车-半精车:用于各类零件上不重要的表面或非配合表面。
3.粗车-半精车-精车:精度更高4.粗车-半精车-磨削:用于加工精度稍高、粗糙度值较小、且淬硬的钢件外圆面,也可广泛地用于加工未淬硬的钢件或铸铁件。
平面加工方法未注公差等级GB/T1804-2000公差等级约IT10-IT14之间下面是赠送的励志的100句经典话,需要的朋友可以学习下,不需要的朋友可以下载后编辑删除!!谢谢!!【励志的话】平凡却无私的人啊千万不要抱怨命运的不公。
也许,命运只是用另一种方式偏爱着你那是因为善良的她想让你尽快长大感知人间悲喜,聆听世间哀乐。
虽然有时跌倒,有时失败但请记住跌倒不是失败,失败不是否定。
平凡却无私的人啊千万不要抱怨命运的不公也许,命运只是用透明的方式倾向与你那是因为,慈爱的她想让你尽早成熟看尽人间繁华,尝便世间甘苦。
虽然有时哭泣,有时逃避但请记住哭泣不是永久逃避不是永恒平凡却无私的人啊千万不要抱怨命运的不公也许,命运只是施舍于被它偏爱的人那是因为严厉的她不想让你溺爱长大,感受人们欢呼,享受世界鼓舞虽然有时悲愤,有时无助。
在车床上加工内孔的精度和适用范围
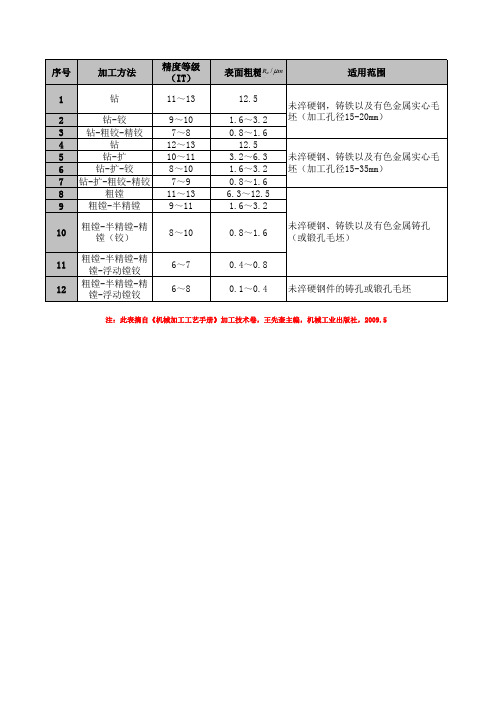
序号 1 2 3 4 5 6 7 8 9 10 11 12
加工方法 钻
R 精度等级(IT) 精度等级(IT) 表面粗糙度 a / µm
11~13 9~10 7~8 12~13 10~11 8~10 7~9 11~13 9~11 8~10 6~7 6~8
12.5 1.6~3.2 0.8~1.6 12.5 3.2~6.3 1.6~3.2 0.8~1.6 6.3~12.5 1.6~3.2 0.8~1.6 0.4~0.8 0.1~0.4
未淬硬钢、铸铁以及有色金属实心Байду номын сангаас 坯(加工孔径15-35mm)
未淬硬钢、铸铁以及有色金属铸孔 (或锻孔毛坯)
未淬硬钢件的铸孔或锻孔毛坯
王先奎主编,机械工业出版社,2009.5 王先奎主编,机械工业出版社,2009.
钻-铰 钻-粗铰-精铰 钻 钻-扩 钻-扩-铰 钻-扩-粗铰-精铰 粗镗 粗镗-半精镗 粗镗-半精镗-精 镗(铰) 粗镗-半精镗-精 镗-浮动镗铰 粗镗-半精镗-精 镗-浮动镗铰
注:此表摘自《机械加工工艺手册》加工技术卷,王先奎主编 此表摘自《机械加工工艺手册》加工技术卷,
适用范围 未淬硬钢,铸铁以及有色金属实心毛 坯(加工孔径15-20mm)
箱体零件的孔系加工方法与精度分析——《机械制造工程学》课程教学中的典型零件加工专题

机械加工精度作为机械制造工程学课程的重要内容之一,在教学中一般按照工艺系统的几何误差、受力变形等分立的内容进行教学。
为提高学生综合运用所需知识分析解决具体问题的能力,我们开展了“专题驱动式”教学方法研究。
下面以箱体零件的孔系加工为专题,对其工艺方案与加工精度进行分析。
箱体类零件是机械传动装置中重要的基础件,箱体上若干有相互位置精度要求的孔构成箱体孔系,包括平行孔系、同轴孔系等。
孔系的加工方法与孔系的加工精度对保证传动装置的性能和质量具有重要影响。
一、平行孔系加工平行孔系的精度要求主要是各孔轴线之间及轴线与基准面之间的尺寸精度和轴线间的平行度等几何精度。
可以通过以下几种方法保证平行孔系精度要求。
1.找正法。
采用辅助装置来确定各个被加工孔的正确位置,如划线找正、心轴块规找正等。
2.镗模法。
镗模是引导镗刀杆在工件上镗孔用的机床夹具,利用镗模板上的孔系保证箱体孔系位置精度,镗杆与镗床主轴多采用浮动连接,以减小机床主轴的回转精度对加工精度的影响。
3.坐标法。
首先将被加工孔之间的孔距尺寸换算为两个相互垂直的坐标尺寸,然后精确地调整机床主轴与工件在水平和垂直方向的相对位置,以间接保证孔距精度。
为保证工作台和主轴的位移精度,必须在镗床上加上坐标测量装置。
二、同轴孔系加工在成批生产中,常采用镗模加工箱体同轴孔系以保证其轴线的同轴度。
在单件小批生产时,一般不采用镗模,常采用如下两种方法保证其轴线孔的同轴度。
1.利用已加工孔作支承导向。
在加工好的箱体前壁孔内装一个导向套,对镗杆起支承支撑和引导作用。
它适用于加工壁间距较小的箱体同轴孔。
2.利用镗床后立柱作支承导向。
镗床后立柱上的导向套作支承导向,可解决因镗杆悬臂过长而挠度大进而影响同轴度的问题。
这种方法需用较长的镗杆,而且调整后立柱导套比较麻烦、费时,通常适用于大型箱体的孔系加工。
三、孔系加工的精度分析(一)受力变形的影响1.镗杆受力变形的影响。
镗削过程中,随着镗杆的回转,径向力Fy 与切向力Fz 的合力Fyz 方向不断改变。
h9孔加工方法
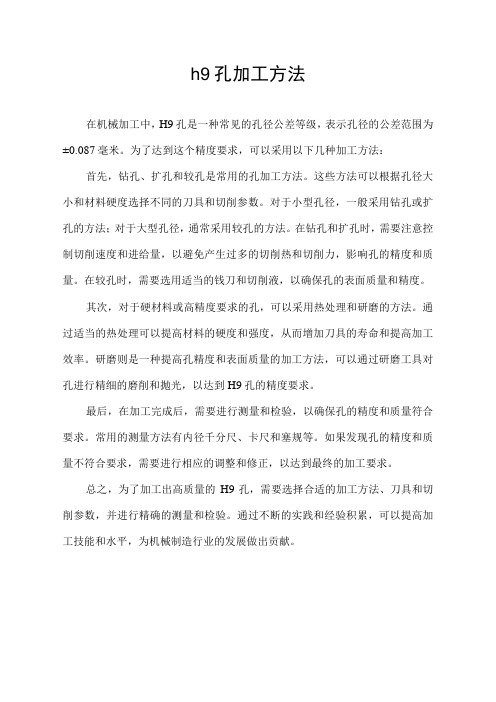
h9孔加工方法
在机械加工中,H9孔是一种常见的孔径公差等级,表示孔径的公差范围为±0.087毫米。
为了达到这个精度要求,可以采用以下几种加工方法:首先,钻孔、扩孔和较孔是常用的孔加工方法。
这些方法可以根据孔径大小和材料硬度选择不同的刀具和切削参数。
对于小型孔径,一般采用钻孔或扩孔的方法;对于大型孔径,通常采用较孔的方法。
在钻孔和扩孔时,需要注意控制切削速度和进给量,以避免产生过多的切削热和切削力,影响孔的精度和质量。
在较孔时,需要选用适当的钱刀和切削液,以确保孔的表面质量和精度。
其次,对于硬材料或高精度要求的孔,可以采用热处理和研磨的方法。
通过适当的热处理可以提高材料的硬度和强度,从而增加刀具的寿命和提高加工效率。
研磨则是一种提高孔精度和表面质量的加工方法,可以通过研磨工具对孔进行精细的磨削和抛光,以达到H9孔的精度要求。
最后,在加工完成后,需要进行测量和检验,以确保孔的精度和质量符合要求。
常用的测量方法有内径千分尺、卡尺和塞规等。
如果发现孔的精度和质量不符合要求,需要进行相应的调整和修正,以达到最终的加工要求。
总之,为了加工出高质量的H9孔,需要选择合适的加工方法、刀具和切削参数,并进行精确的测量和检验。
通过不断的实践和经验积累,可以提高加工技能和水平,为机械制造行业的发展做出贡献。
各种加工方法所能达到的精度等级

牌号字母
钢铁种类
牌号字母
钢铁种类
S ×× C
半精
0.4 ~ 1.6
精
0.025 ~ 0.4
珩磨 平面
0.025 ~ 1.6
圆柱
0.012 ~ 0.4
研磨 粗
0.2 ~ 1.6
半精
0.05 ~ 0.4
精
0.012 ~ 0.1
抛光 一般
0.1 ~ 1.6
精
0.012 ~ 0.1
滚压抛光
0.05 ~ 3.2
超精加工 平面
0.012 ~ 0.4
圆柱
0.012 ~ 0.4
滚压
0.4 ~ 3.2
磨
0.2 ~ 1.6
研磨
0.05 ~ 1.6
齿轮及花键加工 刨
0.8 ~ 6.3
滚
0.8 ~ 6.3
插
0.8 ~ 6.3
磨
0.1 ~ 0.8
剃
0.2 ~ 1.6
粗糙度:0.012、0.025、0.050、0.100、0.20、0.40、0.80、1.6、3.2、6.3、12.5、25、50、100
半精
0.4 ~ 6.3
精
.3 ~ 25
半精
1.6 ~ 12.5
精
0.2 ~ 1.6
金刚车
0.025 ~ 0.2
车端面 粗
6.3 ~ 25
半精
关于 钻孔工艺精度标准

不同精度及不同毛坯的圆柱孔加工
孔Φ35(0,+0.062),孔公差H7,麻花钻Φ34.8,铰孔至Φ35(0,+0.062)Φ8(0,+0.018),孔公差约H7-H8,中心钻定位,麻花钻至Φ6,粗镗至Φ7.5,
精镗至Φ8(0,+0.018)
1、钻削直径较大的孔(大于30mm )时,不宜用大钻头一次钻出,最好分多次钻
削,即先用直径较小的钻头钻孔,再用较大直径钻头扩到所要求的尺寸。
基孔制选作基准的孔称为基准孔,基准孔代号H (下偏差值0,上偏差值正值) 基轴制选作基准的轴称为基准轴,基准轴代号h (上偏差值0,下偏差值负数)
1. 粗车:主要作为外圆的预加工,除淬硬钢以外,各种零件的加工都适用。
当
零件的外圆要求精度低、表面粗糙度较大时,只粗车即可。
2. 粗车-半精车:用于各类零件上不重要的表面或非配合表面。
3. 粗车-半精车
-精车:精度更高
4. 粗车-半精车-磨削:用于加工精度稍高、粗糙度值较小、且淬硬的钢件外圆
面,也可广泛地用于加工未淬硬的钢件或铸铁件。
未注公差等级GB/T1804-2000公差等级约IT10-IT14之间。
孔加工的四种方法

孔加工的四种方法
孔加工是切削加工中常用的一种技术,具有自身的法律规定,一般用来加工承受压力或连接零件的配件,是一种非常重要的加工形式。
孔加工有多种技术,主要有四种方法:切削孔加工,钻孔加工,粗减孔加工和冲孔加工。
首先是切削孔加工,它采用刀具切削来加工高精度的孔,具有良好的精度和光滑程度,且能迅速加工完成,但刀具损耗较大,刃容易磨损,且加工成本较高。
接下来是钻孔加工,它采用工具钻锉出孔洞,具有精密钉比较少、加工速度较快、成本较低等优点,但孔的精度和光滑程度不足,加工的工件材料也有限。
粗减孔加工是比较容易上手的加工方式,采用研磨、抛光等多种方法将加工材料抹减,从而达到加工的目的,可以解决精度等要求,但加工工艺不一定能满足要求,加工速度也较慢。
最后是冲孔加工,这是最常见的孔加工方法,可以根据不同的特性加工得到不同精度的孔洞,能快速获得所需精度,不但价格低廉,而且加工速度快,但受到材料的限制,加工的材料也有限。
综上所述,孔加工有四种常见方法,每种方法都有自身的优势和限制,因此,在采用孔加工时,必须根据具体情况综合评估,合理选择最适合的孔加工方法,以确保质量。
同时,严格把握相关工业环境法律法规,以确保安全,并合理使用和消耗,以降低孔加工成本。
孔加工方法及实例

孔的精加工方法
孔的精加工
٭铰孔 ٭镗孔
加工精度高(形位精度好) 加工效率高(切削速度高, 不同材质对应不同刀片) 柔性好(直径可调)
加工范围宽:Φ1-880mm
成本低(刀片可换)
孔加工案例一
用户: 柳工箱体厂
工件: 箱体
材质: 球墨铸铁
硬度: HB190
孔径:
Φ25
+0.021 0
粗糙度: Ra1.6
套镗
段差加工
用户:襄阳亿普机械制造 有限公司 工件:主轴承盖 材质:45#钢 孔径:R47.62±0.08 单边余量:4.5mm 粗镗头:RW68-100CK6 刀片座:RW86106E 刀片:CCMM120408EFM – AC2000 前刃:R46,后刃:R47.62
段差加工
反镗加工
用户:北京机床所 工件:机床立柱 材质:HT200 孔径:Φ80mm 镗刀组合:BT50-CK6300 镗头:EWN68150CKB6 刀片: TCGT110204FN(H1)
工序二 粗镗至¢24.9
刀柄: BT50-CK1-135 座:TW2026A
粗镗头:TWN20-31CKB1 刀片
刀片: SCMP060204EFM(AC300G)
切削速度: V= 80m/min S=1020rpm 进给量:F=0.2mm/rev
深孔加工案例
用户:浙江凯达机床
工件:数控车床传动箱
用户: 长春天合转向器
工件: 转向器壳体
材质: QT400
孔径:Φ36
+0.025 0
(H7)
余量:Φ3.5mm
精镗: 刀柄BT50-CK6300
减径器:CK63-80
孔的加工方法有哪些

孔的加工方法有哪些孔的加工方法有很多种,根据不同的需求和加工对象,选择合适的加工方法可以提高加工效率和产品质量。
以下是常见的孔的加工方法:1. 钻孔:钻孔是最基本的孔加工方法之一,通过钻头在工件上旋转并施加压力,将钻头逐渐深入工件中,形成所需直径和深度的孔。
钻孔通常适用于加工小直径和长孔,可以使用手动钻床、立式钻床、卧式钻床等设备进行。
2. 镗孔:镗孔是利用回转刀具,以旋转剥削的形式加工孔的一种方法。
镗孔可分为手动镗孔和机械镗孔两种方式。
手动镗孔常用于小型孔的加工,机械镗孔则通过镗床等设备实现,适用于各种尺寸和形状的孔的加工。
3. 铰孔:铰孔是在孔的表面加工切削螺旋槽的方法,通过旋转铰刀,并施加轴向流动来实现。
铰孔通常用于加工与螺纹配合的孔,如螺纹孔、锥孔等。
4. 攻丝:攻丝是在孔内加工内螺纹的方法,通常采用手动或机械操作攻丝刀具,将切削螺纹槽形成所需的螺纹孔。
攻丝广泛应用于机械制造和装配领域。
5. 火焰喷孔:火焰喷孔是利用火焰喷枪产生的高温热源,对工件表面局部加热,使其产生膨胀,再施加机械力,通过物理变形,在工件上形成所需的孔。
6. 激光加工:激光加工是一种高精度的孔加工方法,通过激光束对工件进行瞬时加热和蒸发,从而形成孔洞。
激光加工具有加工速度快、加工精度高的优点,适用于加工小孔和复杂形状的孔。
7. 电火花加工:电火花加工利用高频电脉冲的电火花熔化电极材料和工件,通过电极材料和工件之间的放电,形成孔洞。
电火花加工可以加工任何导电材料,适用于加工硬质合金和高硬度工件。
8. 高速切削:高速切削是通过高速旋转的工具,以快速高效的方式加工孔洞。
高速切削具有加工速度快、表面质量好的优点,适用于加工大批量的孔。
以上是一些常见的孔的加工方法,每种方法都有其适用的场景和优势。
在实际加工过程中,需要根据具体的要求和条件选择合适的加工方法,以提高加工效率和产品质量。
各种加工方法的经济精度和表面粗糙度
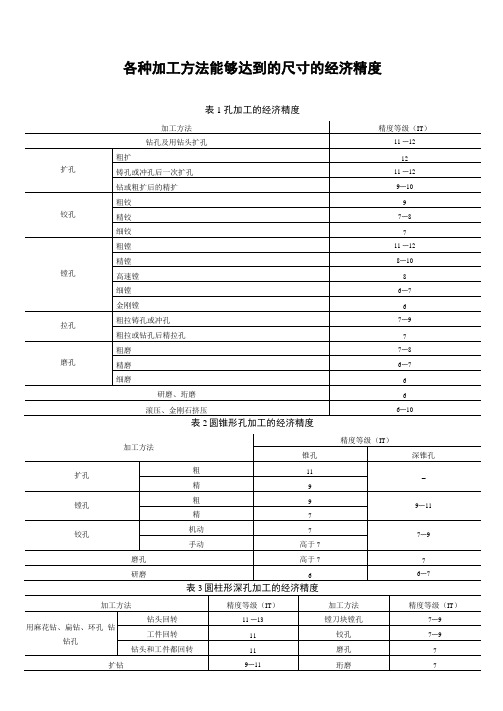
各种加工方法能够达到的尺寸的经济精度表1 孔加工的经济精度表2圆锥形孔加工的经济精度表3圆柱形深孔加工的经济精度6mm7mm91<1m2端铣刀铣削的加工精度在相同的条件下大体上比圆柱铣刀铣削高一级。
3细铣仅用于端铣刀铣削。
11各种加工方法能够达到的形状的经济精度2315各种加工方法所能够达到的相互位置的经济精度表19同轴度的经济精度表20 轴心线相互平行的孔的位置经济精度注:对于钻、卧镗及组合机床的镗孔偏差同样适用于铰孔。
表21轴心线相互垂直的孔的位置经济精度各种加工方法能够达到的零件表面粗糙度表22 各种加工方法能够达到的零件表面粗糙度各类型面的加工方案及经济精度表23外圆表面加工方案标准公差及形位公差附表1标准公差值1mm IT14IT1813 22-2-21 16:331 《金属机械加工工艺人员手册》修订本上海科学技术出版社1981年2 《机械制造工艺学》顾崇衔等编著陕西科学技术出版社1982年3 《航空机械设计手册》第三机械工业部612所编1979年4 《机械制造工艺学课程设计简明手册》华中工学院机械制造工艺教研室编1981年5 《机械工程手册》第46篇机械工业出版社1981年6 《圆柱齿轮加工》上海科学技术出版社1979年切削用量切削用量的选择原则正确地选择切削用量,对提高切削效率,保证必要的刀具耐用度和经济性,保证加工质量,具有重要的作用。
1粗加工切削用量的选择原则:粗加工时加工精度与表面求不高,毛坯余量较大。
因此,选择粗加工的切削用量时,要尽可能保证较高的单位时间金属切除量(金属切除率)和必要的刀具耐用度,以提高生产效率和降低加工成本。
金属切除率可以用下式计算:Z k vfa X1000式中Zw——单位时间内的金属切除量(mm3/s);v --- 切削速度(m/s);f --- 进给量(mm/r);a p -------- 切削深度(mm)。
提高切削速度、增大进给量和切削深度,都能提高金属切除率。
- 1、下载文档前请自行甄别文档内容的完整性,平台不提供额外的编辑、内容补充、找答案等附加服务。
- 2、"仅部分预览"的文档,不可在线预览部分如存在完整性等问题,可反馈申请退款(可完整预览的文档不适用该条件!)。
- 3、如文档侵犯您的权益,请联系客服反馈,我们会尽快为您处理(人工客服工作时间:9:00-18:30)。
孔的加工及其达到的精度
孔的加工及其达到的精度
一、钻孔
1. 工艺特点
1)钻孔是孔的粗加工方法;
2)可加工直径0.05〜125mm勺孔;
3)孔的尺寸精度在IT10 以下;
4)孔的表面粗糙度一般只能控制在Ra12.5卩m。
对于精度要求不高勺孔,如螺栓勺贯穿孔、油孔以及螺纹底孔,可直接采用钻孔。
二、扩孔
工艺特点
1)扩孔是孔的半精加工方法;
2)一般加工精度为IT10 〜IT9 ;
3)孔的表面粗糙度可控制在Ra6.3〜3.2卩m。
当钻削dw> 30mn直径的孔时,为了减小钻削力及扭矩,提高孔的质量,一般先用(0.5〜0.7 )dw大小的钻头钻出底孔,再用扩孔钻进行扩孔,则可较好地保证孔的精度和控制表面粗糙度,且生产率比直接用大钻头一次钻出时还要高。
三、铰孔
铰削过程的实质
铰削过程不完全是一个切削过程,而是包括切削、刮削、挤压、熨平和摩擦等效应的一个综合作用过程。
铰削用量
1)铰削余量粗铰余量为0.10mm- 0.35 mm; 精铰余量为
0.04mm- 0.06mm。
2)切削速度和进给量铰削速度为1.5m/min - 5m/min ;铰削钢件时,进给量为0.3mm/r - 2mm/r ;铰削铸铁件时,
进给量为0.5mm/r - 3mm/r 。
工艺特点
1 )铰孔是孔的精加工方法;
2)可加工精度为IT7 、IT8 、IT9 的孔;
3)孔的表面粗糙度可控制在Ra3.2〜0.2卩m
4)铰刀是定尺寸刀具;
5)切削液在铰削过程中起着重要的作用。
四、镗孔
工艺特点
1)镗孔可不同孔径的孔进行粗、半精和精加工;
2)加工精度可达为IT7 - IT6 ;
3)孔的表面粗糙度可控制在Ra6.3〜0.8卩
4)能修正前工序造成的孔轴线的弯曲、偏斜等形状位置误
差;五、拉孔工艺特点
1) 拉削生产率高。
2) 拉削精度高,质量稳定。
拉削精度一般可达IT9-IT7 级,表面粗糙度一般可控制到Ra1.6mn v Ra0.8mm拉削表面的形
状、尺寸精度和表面质量主要依靠拉刀设计、制造及正确使用保证。
3) 拉削成本低,经济效益高。
4) 拉刀是定尺寸、高精度、高生产率专用刀具,制造成本很高,所以,拉削加工只适用于批量生产,最好是大批大量生产,一般不宜用于单件、小批生产。
六、内圆磨削
工艺特点
1) 磨削是零件精加工的主要方法之一;
2) 对长径比小的,内孔磨削的经济精度可达IT5〜IT6,表
面粗糙度可控制到Ra0.8mn〜Ra0.2mm
3) 可加工较硬的金属材料和非金属材料,如淬火钢、硬质合金和陶瓷等。
内圆磨削与外圆磨削相比,存在如下一些主要问题:
1) 内圆磨削的表面较外圆磨削的粗糙。
2) 生产率较低。
3) 磨削接触区面积较大,砂轮易堵塞,散热和切削液冲刷困难。
因此内孔磨削一般仅适用于淬硬工件的精加工,在单件、小批生产中和在大批大量生产中都有应用。
七、总结
(一)小批量加工
1. 钻IT13 〜IT11 Ra 25
2. 钻—铰IT9 Ra 6.3 〜
3.2
3. 钻—粗铰—精铰IT8 〜IT7 Ra 3.2 〜1.6
4. 钻—扩IT11 Ra 25 〜12.5
5. 钻—扩—铰IT9 〜IT7 Ra
6.3 〜3.2
6. 钻—扩—粗铰—精铰IT7 Ra 3.2 〜1.6
7. 钻—扩—机铰—手铰IT7 〜IT6 Ra 0.8 〜0.2
8. 钻—扩—拉IT9 〜IT7 Ra 3.2 〜0.2
(二)大批大量生产
9. 粗镗(或扩孔)IT13 〜IT11Ra 25 〜12.5
10. 粗镗(粗扩)—半精镗(精扩)IT9 〜IT8 Ra 6.3 〜
3.2
11. 粗镗(粗扩)—半精镗(精扩)—精镗(铰)IT8〜IT7Ra
3.2 〜1.6
12. 粗镗—半精镗—精镗—浮动镗刀精镗IT7 〜IT6 Ra
1.6 〜0.8
13. 粗镗—半精镗—精镗—浮动镗刀精镗—挤压IT7 〜IT6 Ra 1.6 〜0.4
14. 粗镗—半精镗—磨孔IT8〜IT7 Ra 1.6 〜0.4
15. 粗镗—半精镗—粗磨—精磨IT7〜IT6 Ra 0.4
16. 粗镗—半精镗—精镗—金刚镗IT7 〜IT6 Ra 0.8
17. 钻—扩—粗铰—精铰—珩磨IT7 〜IT6 Ra 0.4
18. 钻—扩—拉—珩磨IT7 〜IT6 Ra 0.4 〜0.05
19. 粗镗—半精镗—精镗—珩磨
20. 钻—扩—粗铰—精铰—研磨
21. 钻—扩—拉—研磨IT6 以上Ra 0.2 〜0.012
22. 粗镗—半精镗—精镗—研磨0.2
〜0.1 0.05
欢迎您的下载,
资料仅供参考!
致力为企业和个人提供合同协议,策划案计划书,学习资料等等
打造全网一站式需求。