最新孔的加工及其达到的精度
各种加工方法的经济精度和表面粗糙度

各种加工方法能够达到的尺寸的经济精度表1 孔加工的经济精度表2 圆锥形孔加工的经济精度表3 圆柱形深孔加工的经济精度表4 花键孔加工的经济精度表5 外圆柱表面加工的经济精度表6 端面加工的经济精度(mm)表7 用成形铣刀加工的经济精度(mm)注:指加工表面至基准的尺寸精度。
表8 同时加工平行表面的经刘精度(mm)注:指两平行表面距离的尺寸精度。
表9 平面加工的经济精度注:1 表内资料适用于尺寸<1m,结构刚性好的零件加工,用光洁的加工表面作为定位和测量基准。
2 端铣刀铣削的加工精度在相同的条件下大体上比圆柱铣刀铣削高一级。
3 细铣仅用于端铣刀铣削。
表10 公制螺纹加工的经济精度表11 花键加工的经济精度表12 齿形加工的经济精度各种加工方法能够达到的形状的经济精度表13 平面度和直线度的经济精度表14 圆柱形表面形状精度的经济精度注:形状精度等级的公差值见附表2、3。
表15 曲面加工的经济精度表16 在各种机床上加工时形状的平均经济精度各种加工方法所能够达到的相互位置的经济精度表17 平行度的经济精度表18 端面跳动和垂直度的经济精度表19 同轴度的经济精度表20 轴心线相互平行的孔的位置经济精度注:对于钻、卧镗及组合机床的镗孔偏差同样适用于铰孔。
表21 轴心线相互垂直的孔的位置经济精度注:在镗空间的垂直孔时,中心距误差可按上式相应的找正方法选用。
各种加工方法能够达到的零件表面粗糙度表22 各种加工方法能够达到的零件表面粗糙度各类型面的加工方案及经济精度表23 外圆表面加工方案表24 孔加工方案表25 平面加工方案——机械篇标准公差及形位公差附表1 标准公差值注:基本尺寸小于1mm时,无IT14至IT18。
13 22-4-25 10:32附表2 平面度、直线度公差值附表3 圆度、圆柱度公差值附表4 平行度、垂直度、倾斜度公差值附表5 同轴度、对称度、圆跳动、全跳动公差值参考文献1 《金属机械加工工艺人员手册》修订本上海科学技术出版社1981年2 《机械制造工艺学》顾崇衔等编著陕西科学技术出版社1982年3 《航空机械设计手册》第三机械工业部612所编1979年4 《机械制造工艺学课程设计简明手册》华中工学院机械制造工艺教研室编1981年5 《机械工程手册》第46篇机械工业出版社1981年6 《圆柱齿轮加工》上海科学技术出版社1979年切削用量切削用量的选择原则正确地选择切削用量,对提高切削效率,保证必要的刀具耐用度和经济性,保证加工质量,具有重要的作用。
浅淡模具制造中孔的加工方法
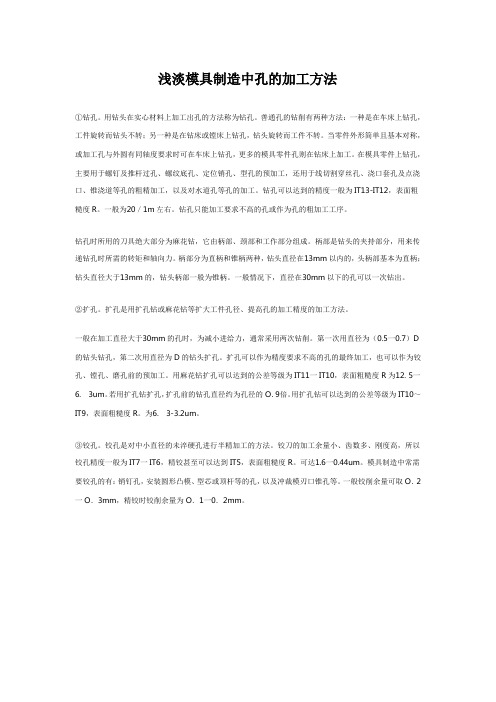
浅淡模具制造中孔的加工方法①钻孔。
用钻头在实心材料上加工出孔的方法称为钻孔。
善通孔的钻削有两种方法:一种是在车床上钻孔,工件旋转而钻头不转;另一种是在钻床或镗床上钻孔,钻头旋转而工件不转。
当零件外形简单且基本对称,或加工孔与外圆有同轴度要求时可在车床上钻孔,更多的模具零件孔则在钻床上加工。
在模具零件上钻孔,主要用于螺钉及推杆过孔、螺纹底孔、定位销孔、型孔的预加工,还用于线切割穿丝孔、浇口套孔及点浇口、锥浇道等孔的粗精加工,以及对水道孔等孔的加工。
钻孔可以达到的精度一般为IT13-IT12,表面粗糙度R。
一般为20/1m左右。
钻孔只能加工要求不高的孔或作为孔的粗加工工序。
钻孔时所用的刀具绝大部分为麻花钻,它由柄部、颈部和工作部分组成。
柄部是钻头的夹持部分,用来传递钻孔时所需的转矩和轴向力。
柄部分为直柄和锥柄两种,钻头直径在13mm以内的,头柄部基本为直柄;钻头直径大于13mm的,钻头柄部一般为锥柄。
一般情况下,直径在30mm以下的孔可以一次钻出。
②扩孔。
扩孔是用扩孔钻或麻花钻等扩大工件孔径、提高孔的加工精度的加工方法。
一般在加工直径大于30mm的孔时,为减小进给力,通常采用两次钻削。
第一次用直径为(0.5一0.7)D的钻头钻孔,第二次用直径为D的钻头扩孔。
扩孔可以作为精度要求不高的孔的最终加工,也可以作为铰孔、镗孔、磨孔前的预加工。
用麻花钻扩孔可以达到的公差等级为IT11一IT10,表面粗糙度R为12. 5一6. 3um。
若用扩孔钻扩孔,扩孔前的钻孔直径约为孔径的O.9倍。
用扩孔钻可以达到的公差等级为IT10~IT9,表面粗糙度R。
为6. 3-3.2um。
③铰孔。
铰孔是对中小直径的未淬硬孔进行半精加工的方法。
铰刀的加工余量小、齿数多、刚度高,所以铰孔精度一般为IT7一IT6,精铰甚至可以达到IT5,表面粗糙度R。
可达1.6一0.44um。
模具制造中常需要铰孔的有:销钉孔,安装圆形凸模、型芯或顶杆等的孔,以及冲裁模刃口锥孔等。
等厚形三面轴孔的加工方法及其配合精度
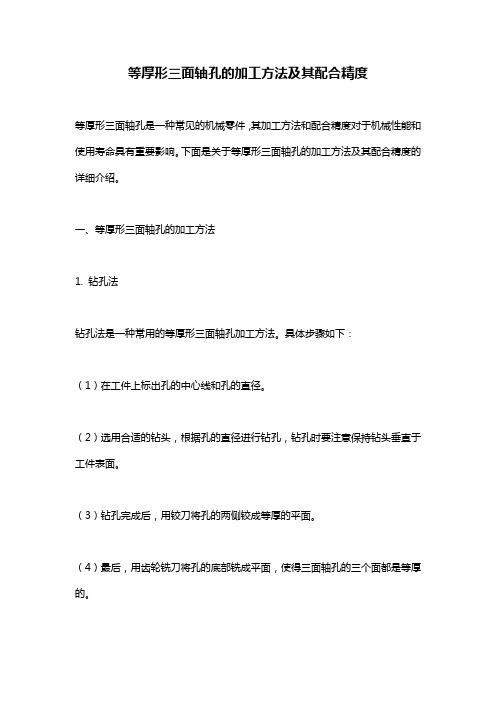
等厚形三面轴孔的加工方法及其配合精度等厚形三面轴孔是一种常见的机械零件,其加工方法和配合精度对于机械性能和使用寿命具有重要影响。
下面是关于等厚形三面轴孔的加工方法及其配合精度的详细介绍。
一、等厚形三面轴孔的加工方法1. 钻孔法钻孔法是一种常用的等厚形三面轴孔加工方法。
具体步骤如下:(1)在工件上标出孔的中心线和孔的直径。
(2)选用合适的钻头,根据孔的直径进行钻孔,钻孔时要注意保持钻头垂直于工件表面。
(3)钻孔完成后,用铰刀将孔的两侧铰成等厚的平面。
(4)最后,用齿轮铣刀将孔的底部铣成平面,使得三面轴孔的三个面都是等厚的。
2. 铰孔法铰孔法也是一种常用的等厚形三面轴孔加工方法。
具体步骤如下:(1)在工件上标出孔的中心线和孔的直径。
(2)选用合适的铰刀,根据孔的直径进行铰孔,铰孔时要注意保持铰刀垂直于工件表面。
(3)铰孔完成后,用齿轮铣刀将孔的底部铣成平面,使得三面轴孔的三个面都是等厚的。
3. 铣孔法铣孔法是一种适用于大孔径等厚形三面轴孔的加工方法。
具体步骤如下:(1)在工件上标出孔的中心线和孔的直径。
(2)选用合适的铣刀,根据孔的直径进行铣孔,铣孔时要注意保持铣刀垂直于工件表面。
(3)铣孔完成后,用铰刀将孔的两侧铰成等厚的平面。
(4)最后,用齿轮铣刀将孔的底部铣成平面,使得三面轴孔的三个面都是等厚的。
二、等厚形三面轴孔的配合精度等厚形三面轴孔的配合精度是指轴孔的尺寸精度、形位精度和表面粗糙度等指标。
其配合精度对于机械性能和使用寿命具有重要影响。
1. 尺寸精度等厚形三面轴孔的尺寸精度应符合设计要求,一般要求孔径和孔深的公差不大于0.01mm。
尺寸精度的控制需要采用精密加工设备和精密测量工具,如数控机床、三坐标测量仪等。
2. 形位精度等厚形三面轴孔的形位精度包括圆度、同心度、垂直度和平行度等指标。
这些指标的控制需要采用精密加工设备和精密测量工具,如圆度测量仪、同心度测量仪等。
3. 表面粗糙度等厚形三面轴孔的表面粗糙度对于轴和孔的配合有重要影响。
内孔的加工讲解
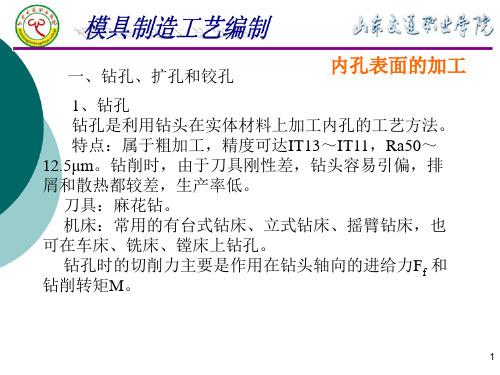
15
11
四、磨孔与孔的精密加工 1 磨孔工艺特点:属于孔的精加方法。精度可达IT7, Ra1.6~0.4 μm。 磨孔不仅能获得较高的尺寸精度和表面质量,而且 还可以提高孔的位置精度和孔的轴线的直线度。与外圆 磨削相比,工作条件较差:砂轮直径小,刚性差,排屑 和散热困难,生产率低。对于淬硬零件中的孔加工,磨 孔是主要的加工方法。 内孔为断续圆周表面(如有键槽或花键的孔)、阶 梯孔及盲孔时,常采用磨孔作为精加工。
研磨孔是一种光整加工方法。精度可达IT7~IT6, Ra0.4~0.025μm,形状精度也有相应的提高,但不能提 高位置精度。
16
珩磨头对孔施加一定压力,结构如图;切除极小的 加工余量。
17
②研磨孔是一种光整加工方法。精度可达IT7~IT6, Ra0.4~0.025μm,形状精度也有相应的提高,但不能提 高位置精度。需要在精镗、精铰或精磨之后进行。
18
固定式研磨棒多用于单件生产。带槽研磨棒便于存 贮研磨剂,用于粗研,光滑研磨棒,一般用于精研。如 图所示 。所有研具采用比工件软的材料制成,这些材料 为铸铁、铜、青铜、巴氏合金及硬木等。有时也可用钢 做研具。研磨时,部分磨粒悬浮于工件与研具之间,部 分磨粒则嵌入研具的表面层,工件与研具作相对运动, 磨料就在工件表面上切除很薄的一层金属 ( 主要是上工 序在工件表面上留下的凸峰 ) 。
12
磨孔时砂轮的尺寸受被加工孔径尺寸的限制,一般 砂轮直径为工件孔径的 0.5—0.9 倍,磨头轴的直径和 长度也取决于被加工孔的直径和深度。故磨削速度低, 磨头的刚度差,磨削质量和生产率均受到影响。
孔的加工方法

孔的加工方法孔的加工是机械加工中的一项重要工艺,它在许多领域都有着广泛的应用。
孔的加工方法多种多样,根据不同的工件材料、形状和精度要求,选择合适的孔加工方法对于提高加工效率和产品质量至关重要。
下面将介绍几种常见的孔的加工方法。
首先,钻孔是最常见的孔加工方法之一。
钻孔是利用钻头在工件上旋转切削,形成孔洞的加工方法。
钻孔适用于一般的孔加工,如在金属、塑料、木材等材料上加工圆孔。
钻孔的工艺简单、成本较低,适用于中小批量生产。
其次,铰削是一种用铰刀在工件上旋转切削,形成内螺纹孔或外螺纹孔的加工方法。
铰削适用于加工螺纹孔,如在机械零件中常见的螺纹孔加工。
铰削工艺精度高,表面质量好,适用于要求较高的螺纹孔加工。
另外,镗削是利用镗刀在工件上旋转切削,形成孔洞的加工方法。
镗削适用于加工大孔径、大深度、高精度的孔洞,如在汽车发动机缸体上的气缸孔加工。
镗削工艺适用范围广,加工效率高,适用于大型工件的孔加工。
最后,激光打孔是利用激光束对工件进行瞬间加热,使其熔化或汽化,形成孔洞的加工方法。
激光打孔适用于金属、塑料、陶瓷等材料的孔加工,尤其适用于复杂形状、高精度要求的孔加工。
激光打孔工艺无接触、无切削力,适用于对工件表面要求严格的孔加工。
综上所述,不同的孔加工方法各有特点,根据具体的加工要求选择合适的孔加工方法至关重要。
在实际生产中,应根据工件材料、形状、精度要求等因素综合考虑,选择最合适的孔加工方法,以提高加工效率和产品质量。
同时,随着科技的不断进步,孔的加工方法也在不断创新和发展,相信在未来会有更多更先进的孔加工方法出现,为各行各业的生产提供更加高效、精准的孔加工解决方案。
提高孔加工的精度的方法
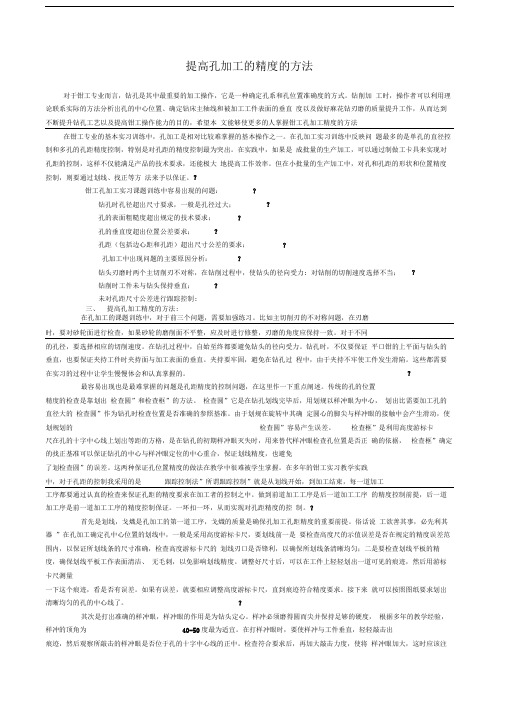
提高孔加工的精度的方法对于钳工专业而言,钻孔是其中最重要的加工操作,它是一种确定孔系和孔位置准确度的方式。
钻削加工时,操作者可以利用理论联系实际的方法分析岀孔的中心位置、确定钻床主轴线和被加工工件表面的垂直度以及做好麻花钻刃磨的质量提升工作,从而达到不断提升钻孔工艺以及提高钳工操作能力的目的,希望本文能够使更多的人掌握钳工孔加工精度的方法在钳工专业的基本实习训练中,孔加工是相对比较难掌握的基本操作之一。
在孔加工实习训练中反映问题最多的是单孔的直径控制和多孔的孔距精度控制,特别是对孔距的精度控制最为突出。
在实践中,如果是成批量的生产加工,可以通过制做工卡具来实现对孔距的控制,这样不仅能满足产品的技术要求,还能极大地提高工作效率。
但在小批量的生产加工中,对孔和孔距的形状和位置精度控制,则要通过划线、找正等方法来予以保证。
?钳工孔加工实习课题训练中容易岀现的问题:?钻孔时孔径超岀尺寸要求,一般是孔径过大;?孔的表面粗糙度超岀规定的技术要求;?孔的垂直度超出位置公差要求;?孔距(包括边心距和孔距)超出尺寸公差的要求;?孔加工中岀现问题的主要原因分析:?钻头刃磨时两个主切削刃不对称,在钻削过程中,使钻头的径向受力; 对钻削的切削速度选择不当;?钻削时工件未与钻头保持垂直;?未对孔距尺寸公差进行跟踪控制;三、提高孔加工精度的方法:在孔加工的课题训练中,对于前三个问题,需要加强练习。
比如主切削刃的不对称问题,在刃磨时,要对砂轮面进行检查,如果砂轮的磨削面不平整,应及时进行修整,刃磨的角度应保持一致。
对于不同的孔径,要选择相应的切削速度。
在钻孔过程中,自始至终都要避免钻头的径向受力。
钻孔时,不仅要保证平口钳的上平面与钻头的垂直,也要保证夹持工件时夹持面与加工表面的垂直。
夹持要牢固,避免在钻孔过程中,由于夹持不牢使工件发生滑陷。
这些都需要在实习的过程中让学生慢慢体会和认真掌握的。
?最容易出现也是最难掌握的问题是孔距精度的控制问题,在这里作一下重点阐述。
高精度孔的加工方法

高精度孔的加工方法
高精度孔的加工方法是指对于精度要求较高的孔进行加工的方法,例如在精密机械、航空航天、高速列车等领域中需要使用的孔。
高精度孔的加工需要保证孔的直径、圆度、表面质量等指标都达到一定的要求。
目前常见的高精度孔加工方法有以下几种:
1. 珩磨加工:珩磨是一种高速旋转的研磨工艺,通过磨头在被加工物表面的摩擦作用中去除材料,从而达到加工目的。
珩磨加工可以在孔内进行,可以加工出高精度圆度的孔。
2. 钻孔加工:钻孔是最常见的孔加工方法之一,可以使用林格曼钻头等工具进行。
钻孔加工可以达到较高的精度要求,但是对于深孔加工会出现偏差的问题。
3. 放电加工:放电加工是一种特殊的非机械加工方法,通过电火花放电来将被加工物表面的材料溶解或脱落,从而达到加工的目的。
放电加工可以加工出高精度的孔,但是加工速度较慢。
4. 激光加工:激光加工是一种高精度的非机械加工方法,通过激光束直接照射被加工物表面,将材料蒸发或熔化,从而达到加工目的。
激光加工可以加工出极高精度的孔,但是设备价格高昂,适用范围有限。
- 1 -。
高精度深长孔的精密加工方法
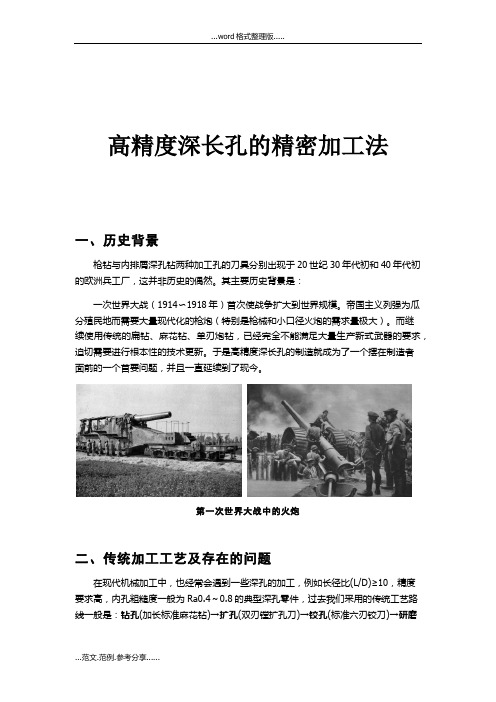
高精度深长孔的精密加工法一、历史背景枪钻与内排屑深孔钻两种加工孔的刀具分别出现于20世纪30年代初和40年代初的欧洲兵工厂,这并非历史的偶然。
其主要历史背景是:一次世界大战(1914〜1918年)首次使战争扩大到世界规模。
帝国主义列强为瓜分殖民地而需要大量现代化的枪炮(特别是枪械和小口径火炮的需求量极大)。
而继续使用传统的扁钻、麻花钻、单刃炮钻,已经完全不能满足大量生产新式武器的要求,迫切需要进行根本性的技术更新。
于是高精度深长孔的制造就成为了一个摆在制造者面前的一个首要问题,并且一直延续到了现今。
第一次世界大战中的火炮二、传统加工工艺及存在的问题在现代机械加工中,也经常会遇到一些深孔的加工,例如长径比(L/D)≥10,精度要求高,内孔粗糙度一般为Ra0.4~0.8的典型深孔零件,过去我们采用的传统工艺路线一般是:钻孔(加长标准麻花钻)→扩孔(双刃镗扩孔刀)→铰孔(标准六刃铰刀)→研磨此工艺虽可达到精度要求,但也存在诸多缺点,特别是在最初工序采用加长麻花钻钻孔时,切削刃越靠近中心,前脚就越大。
若钻头刚性差,则震动更大,表面形状误差难以控制,加工后孔的直线度误差,钻头易产生不均匀的磨损等现象,生产效率和产品合格率低,而且研磨抛光时,工作环境比较脏,由于钻孔工序的缺点,而带来的影响难以在后面的工序中克服,形状误差不能得以修正,因此加工质量差。
传统深孔的加工流程三、工艺路线与刀具的改进本着提高生产效率提高产品合格率的原则,结合深孔加工的一些特性,对加工工艺及刀具进行了改进,改进后的工艺路线是:钻孔(BTA钻)→扩孔(BTA扩)→铰孔(单刃铰刀)→研磨1、钻孔与扩孔刀具及工艺的改进单管内排屑深孔钻的由来单管内排屑深孔钻产生于枪钻之后。
其历史背景是:枪钻的发明,使小深孔加工中自动冷却润滑排屑和自导向问题获得了满意的解决,但由于存在钻头与钻杆难于快速拆装更换和钻杆刚性不足、进给量受到严格限制等先天缺陷,而不适用于较大直径深孔的加工。
在车床上加工内孔的精度和适用范围
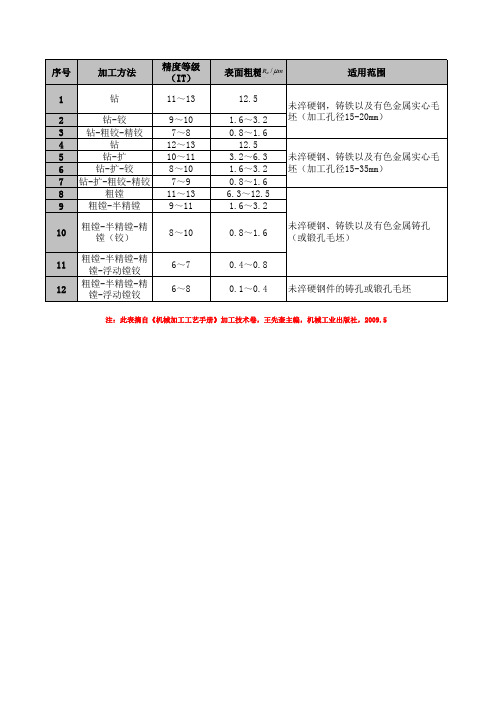
序号 1 2 3 4 5 6 7 8 9 10 11 12
加工方法 钻
R 精度等级(IT) 精度等级(IT) 表面粗糙度 a / µm
11~13 9~10 7~8 12~13 10~11 8~10 7~9 11~13 9~11 8~10 6~7 6~8
12.5 1.6~3.2 0.8~1.6 12.5 3.2~6.3 1.6~3.2 0.8~1.6 6.3~12.5 1.6~3.2 0.8~1.6 0.4~0.8 0.1~0.4
未淬硬钢、铸铁以及有色金属实心Байду номын сангаас 坯(加工孔径15-35mm)
未淬硬钢、铸铁以及有色金属铸孔 (或锻孔毛坯)
未淬硬钢件的铸孔或锻孔毛坯
王先奎主编,机械工业出版社,2009.5 王先奎主编,机械工业出版社,2009.
钻-铰 钻-粗铰-精铰 钻 钻-扩 钻-扩-铰 钻-扩-粗铰-精铰 粗镗 粗镗-半精镗 粗镗-半精镗-精 镗(铰) 粗镗-半精镗-精 镗-浮动镗铰 粗镗-半精镗-精 镗-浮动镗铰
注:此表摘自《机械加工工艺手册》加工技术卷,王先奎主编 此表摘自《机械加工工艺手册》加工技术卷,
适用范围 未淬硬钢,铸铁以及有色金属实心毛 坯(加工孔径15-20mm)
各种加工方法所能达到的精度等级

牌号字母
钢铁种类
牌号字母
钢铁种类
S ×× C
半精
0.4 ~ 1.6
精
0.025 ~ 0.4
珩磨 平面
0.025 ~ 1.6
圆柱
0.012 ~ 0.4
研磨 粗
0.2 ~ 1.6
半精
0.05 ~ 0.4
精
0.012 ~ 0.1
抛光 一般
0.1 ~ 1.6
精
0.012 ~ 0.1
滚压抛光
0.05 ~ 3.2
超精加工 平面
0.012 ~ 0.4
圆柱
0.012 ~ 0.4
滚压
0.4 ~ 3.2
磨
0.2 ~ 1.6
研磨
0.05 ~ 1.6
齿轮及花键加工 刨
0.8 ~ 6.3
滚
0.8 ~ 6.3
插
0.8 ~ 6.3
磨
0.1 ~ 0.8
剃
0.2 ~ 1.6
粗糙度:0.012、0.025、0.050、0.100、0.20、0.40、0.80、1.6、3.2、6.3、12.5、25、50、100
半精
0.4 ~ 6.3
精
.3 ~ 25
半精
1.6 ~ 12.5
精
0.2 ~ 1.6
金刚车
0.025 ~ 0.2
车端面 粗
6.3 ~ 25
半精
内孔高精度加工方法

内孔高精度加工方法嘿,咱今儿就来讲讲内孔高精度加工方法。
你说这内孔加工啊,就好比是给一件宝贝雕琢出最完美的内心。
要想做到高精度,那可不能马虎。
就像咱做饭一样,得讲究火候和调料搭配,一个环节不对,这道菜可能就不美味啦。
首先呢,得选对工具,就跟战士上战场得挑趁手的兵器一个道理。
合适的刀具、钻头,那是关键的第一步。
然后说说加工的过程,那得小心翼翼,轻拿轻放。
不能像个糙汉子似的不管不顾。
你想啊,这内孔就那么点地方,稍微一个不小心,可不就前功尽弃啦?这时候就得有耐心,像绣花一样,一针一线都得精细。
还有啊,加工的参数也得设置得恰到好处。
转速啦、进给量啦,这些都得根据实际情况来调整。
这就好比开车,速度太快容易出事,速度太慢又耽误时间,得找到那个最合适的平衡点。
咱再想想,要是加工的时候不注意冷却,那会咋样?那不就跟人跑了半天不喝水一样,得热晕乎啦!所以冷却也很重要,得让它时刻保持清醒的状态。
而且啊,在加工之前,一定要把准备工作做好。
就跟出门旅行前得收拾好行李一样,别到时候缺这少那的。
检查一下设备,看看有没有啥毛病,可别在关键时刻掉链子。
你说这内孔高精度加工是不是挺不容易的?但只要咱用心去做,就没有办不到的事儿。
就像爬山一样,虽然过程辛苦,但当你爬到山顶,看到那美丽的风景时,一切都值啦!你想想看,那些精密的仪器、设备,里面的内孔加工得多精细啊。
如果没有高精度的加工,这些东西能好用吗?能发挥出它们应有的作用吗?所以说啊,这内孔高精度加工可真是个技术活,也是个精细活。
咱可不能小瞧了它,它可是在很多领域都起着至关重要的作用呢!汽车制造、航空航天、医疗器械等等,哪一个离得开内孔高精度加工?这不就像是大楼的基石一样嘛,虽然不起眼,但没了它可不行。
总之呢,内孔高精度加工是个很有挑战性但又非常有意义的事儿。
咱得认真对待,用心钻研,让咱们加工出来的内孔都能达到高精度的标准。
这样咱们的制造业才能更上一层楼,咱们的国家才能更加强大呀!你说是不是这个理儿?。
提高钻孔位置精度的方法
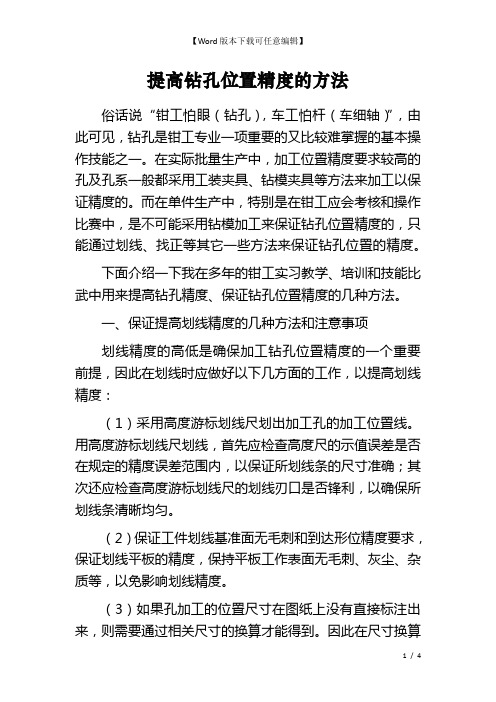
提高钻孔位置精度的方法俗话说“钳工怕眼(钻孔),车工怕杆(车细轴)”,由此可见,钻孔是钳工专业一项重要的又比较难掌握的基本操作技能之一。
在实际批量生产中,加工位置精度要求较高的孔及孔系一般都采用工装夹具、钻模夹具等方法来加工以保证精度的。
而在单件生产中,特别是在钳工应会考核和操作比赛中,是不可能采用钻模加工来保证钻孔位置精度的,只能通过划线、找正等其它一些方法来保证钻孔位置的精度。
下面介绍一下我在多年的钳工实习教学、培训和技能比武中用来提高钻孔精度、保证钻孔位置精度的几种方法。
一、保证提高划线精度的几种方法和注意事项划线精度的高低是确保加工钻孔位置精度的一个重要前提,因此在划线时应做好以下几方面的工作,以提高划线精度:(1)采用高度游标划线尺划出加工孔的加工位置线。
用高度游标划线尺划线,首先应检查高度尺的示值误差是否在规定的精度误差范围内,以保证所划线条的尺寸准确;其次还应检查高度游标划线尺的划线刃口是否锋利,以确保所划线条清晰均匀。
(2)保证工件划线基准面无毛刺和到达形位精度要求,保证划线平板的精度,保持平板工作表面无毛刺、灰尘、杂质等,以免影响划线精度。
(3)如果孔加工的位置尺寸在图纸上没有直接标注出来,则需要通过相关尺寸的换算才能得到。
因此在尺寸换算时,必须保存小数点后三位数,保证尺寸换算的准确性,提高划线精度。
(4)正确使用样冲。
样冲眼的作用是为钻孔或划圆弧起定心作用的,因此,对刃磨样冲的要求是非常高的,要求样冲头必须磨得圆而尖和有足够的硬度。
在敲击样冲眼时,首先是轻轻敲打,然后从多个方向观察所敲击的样冲眼是否偏离孔的十字中心线的交点,判断无误后,再将样冲眼加大,以保证钻孔时标准麻花钻准确地定心。
(5)划出检查孔位置精度的“检查圆”和“检查框”。
在孔加工时,可以根据工作实际需要选择这两种找正基准。
钻孔划线完毕后,一般都要划出比需要加工孔的直径大的“检查圆”,作为钻孔时的找正基准。
但是用划规划“检查圆”时容易产生误差,因此,可采用高度尺将孔的“检查圆”划成“检查框”,“检查框”的方格与孔的十字中心线的四个交点即为孔的找正基准点,这样可以保证钻孔的中心与样冲眼定位的中心重合,保证划线精度,也防止了划“检查园”的误差。
高精度锥孔的精加工与检测
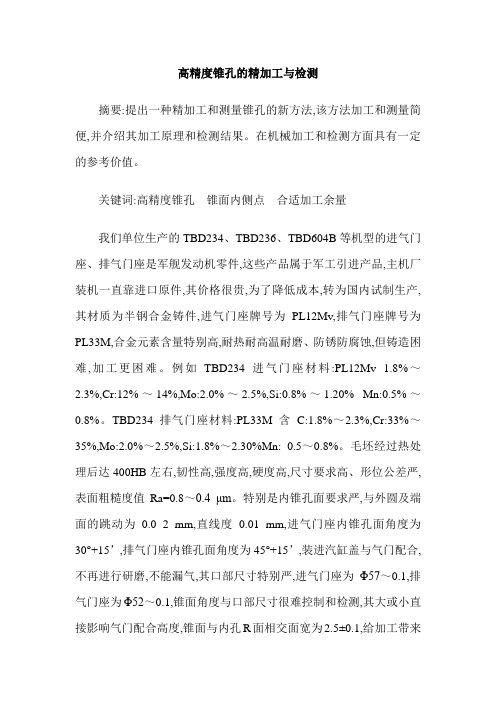
高精度锥孔的精加工与检测摘要:提出一种精加工和测量锥孔的新方法,该方法加工和测量简便,并介绍其加工原理和检测结果。
在机械加工和检测方面具有一定的参考价值。
关键词:高精度锥孔锥面内侧点合适加工余量我们单位生产的TBD234、TBD236、TBD604B等机型的进气门座、排气门座是军舰发动机零件,这些产品属于军工引进产品,主机厂装机一直靠进口原件,其价格很贵,为了降低成本,转为国内试制生产,其材质为半钢合金铸件,进气门座牌号为PL12Mv,排气门座牌号为PL33M,合金元素含量特别高,耐热耐高温耐磨、防锈防腐蚀,但铸造困难,加工更困难。
例如TBD234进气门座材料:PL12Mv 1.8%~2.3%,Cr:12%~14%,Mo:2.0%~2.5%,Si:0.8%~1.20% Mn:0.5%~0.8%。
TBD234排气门座材料:PL33M含C:1.8%~2.3%,Cr:33%~35%,Mo:2.0%~2.5%,Si:1.8%~2.30%Mn: 0.5~0.8%。
毛坯经过热处理后达400HB左右,韧性高,强度高,硬度高,尺寸要求高、形位公差严,表面粗糙度值Ra=0.8~0.4 μm。
特别是内锥孔面要求严,与外圆及端面的跳动为0.0 2 mm,直线度0.01 mm,进气门座内锥孔面角度为30°+15’,排气门座内锥孔面角度为45°+15’,装进汽缸盖与气门配合,不再进行研磨,不能漏气,其口部尺寸特别严,进气门座为Φ57~0.1,排气门座为Φ52~0.1,锥面角度与口部尺寸很难控制和检测,其大或小直接影响气门配合高度,锥面与内孔R面相交面宽为2.5±0.1,给加工带来了一定困难。
这样高精度内锥面通常应该采用专用精密内锥孔磨床进行加工,但是国内暂时还没有生产厂家,进口这种专用设备需要100多万元,曾经用普通磨床进行改装进行加工,而且砂轮前端磨损快,尺寸很难保证,表面粗糙度差,形位公差达不到要求。
高精度细长孔的数控加工研究

高精度细长孔的数控加工研究高精度细长孔加工技术是数控加工领域中的一个重要领域,也是目前工业制造领域中一个快速发展的技术。
随着现代高科技的不断发展,对细小孔洞的要求越来越高,因此,高精度细长孔加工技术的发展有着广泛而深远的意义。
一、高精度细长孔加工的背景现代工业生产中,高精度细长孔扮演着至关重要的角色。
例如在航空航天、汽车、电子、医疗设备等行业制造中,都需要进行细小孔洞的加工。
以航空制造为例,飞机发动机的缸体内需要加工出数百个细小孔洞,以保证发动机正常工作。
而在医疗设备领域,医学导管、内镜、骨钉等医疗器械的制造也需要进行高精度细小孔洞的加工。
因此,高精度细长孔加工技术的研究和发展对于现代工业制造具有重要的战略意义。
二、高精度细长孔加工技术的研究内容高精度细长孔加工技术的研究包含着多个方面,其中最主要的是细小孔径和长孔的加工。
1. 细小孔径的加工目前,传统的钻床加工细小孔洞已经无法满足工业制造对高精度细长孔加工的要求。
因此,需要对传统加工方法进行改进和优化,以适应工业现代化对细小孔径加工的需要。
现代高精度细长孔加工技术最常用的方法是电火花加工和激光加工。
电火花加工是高精度细小孔洞加工技术中的一种常用方法。
该技术主要采用电极和工件之间的电火花放电的方式对工件进行加工,可以高效地加工出高精度的细小孔洞。
这种加工方法可以加工各种不锈钢、塑料、玻璃等材料的细小孔洞。
但是,由于电极磨损等问题的存在,加工稳定性有待提高。
激光加工技术也是一种高效、高精度的细小孔洞加工方法。
它采用激光束对工件材料进行熔化并蒸发的方式进行加工。
相比于传统的机械加工方法,激光加工方法可以通过激光照射来实现对细小孔洞的加工。
同时,激光加工可以加工各种材料的孔洞,并且由于激光加工具有高能量密度和能量集中等特点,可以达到高精度、高速度、高质量的加工效果。
2. 长孔的加工高精度细小孔洞加工不仅涉及到孔径的大小,也与孔洞长度有关,因为现代制造工业生产中,很多机械零部件都需要有一定长度的孔洞,以实现该部件特定的功能。
各种加工方法的经济精度和表面粗糙度
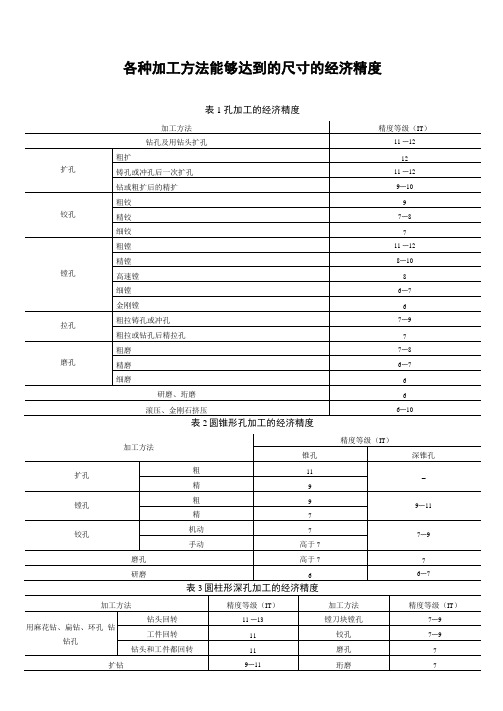
各种加工方法能够达到的尺寸的经济精度表1 孔加工的经济精度表2圆锥形孔加工的经济精度表3圆柱形深孔加工的经济精度6mm7mm91<1m2端铣刀铣削的加工精度在相同的条件下大体上比圆柱铣刀铣削高一级。
3细铣仅用于端铣刀铣削。
11各种加工方法能够达到的形状的经济精度2315各种加工方法所能够达到的相互位置的经济精度表19同轴度的经济精度表20 轴心线相互平行的孔的位置经济精度注:对于钻、卧镗及组合机床的镗孔偏差同样适用于铰孔。
表21轴心线相互垂直的孔的位置经济精度各种加工方法能够达到的零件表面粗糙度表22 各种加工方法能够达到的零件表面粗糙度各类型面的加工方案及经济精度表23外圆表面加工方案标准公差及形位公差附表1标准公差值1mm IT14IT1813 22-2-21 16:331 《金属机械加工工艺人员手册》修订本上海科学技术出版社1981年2 《机械制造工艺学》顾崇衔等编著陕西科学技术出版社1982年3 《航空机械设计手册》第三机械工业部612所编1979年4 《机械制造工艺学课程设计简明手册》华中工学院机械制造工艺教研室编1981年5 《机械工程手册》第46篇机械工业出版社1981年6 《圆柱齿轮加工》上海科学技术出版社1979年切削用量切削用量的选择原则正确地选择切削用量,对提高切削效率,保证必要的刀具耐用度和经济性,保证加工质量,具有重要的作用。
1粗加工切削用量的选择原则:粗加工时加工精度与表面求不高,毛坯余量较大。
因此,选择粗加工的切削用量时,要尽可能保证较高的单位时间金属切除量(金属切除率)和必要的刀具耐用度,以提高生产效率和降低加工成本。
金属切除率可以用下式计算:Z k vfa X1000式中Zw——单位时间内的金属切除量(mm3/s);v --- 切削速度(m/s);f --- 进给量(mm/r);a p -------- 切削深度(mm)。
提高切削速度、增大进给量和切削深度,都能提高金属切除率。
H7与H8级精度孔加工方式及余量
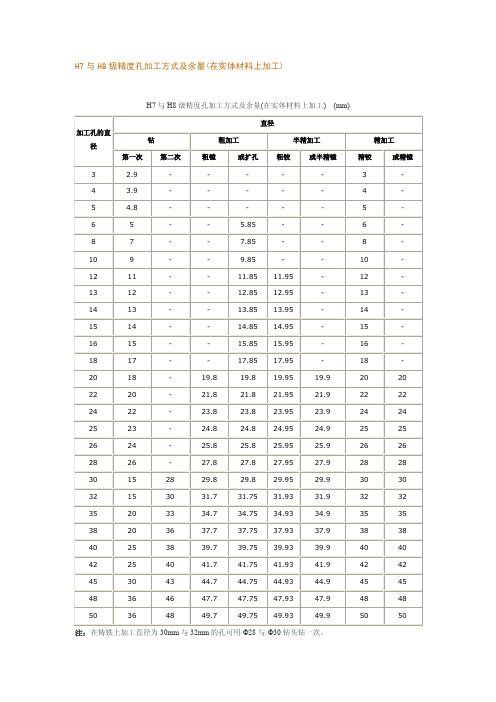
-
20
18
-
19.8
19.8 19.95
19.9
20
20
22
20
-
21.8
21.8 21.95
21.9
22
22
24
22
-
23.8
23.8 23.95
23.9
24
24
25
23
-
24.8
24.8 24.95
24.9
25
25
26
24
-
25.8
25.8 25.95
25.9
26
26
28
26
-
27.8
27.8 27.95
H7 与 H8 级精度孔加工方式及余量(在实体材料上加工)
H7 与 H8 级精度孔加工方式及余量(在实体材料上加工) (mm)
加工孔的直 径
钻
第一次
第二次
直径
粗加工
半精加工
粗镗
或扩孔
粗铰
或半精镗
精加工
精铰
或精镗
3
2.9
-
-
-
-
-
3
-
4
3.9
-
-
-
-
-
4
-
5
4.8
-
-
-
-
-
5
-
6
5
-
-
5.85
-
6
-
8
7
-
-
7.85
-
-
8
-
10
9
-
-
9.85
-
-
- 1、下载文档前请自行甄别文档内容的完整性,平台不提供额外的编辑、内容补充、找答案等附加服务。
- 2、"仅部分预览"的文档,不可在线预览部分如存在完整性等问题,可反馈申请退款(可完整预览的文档不适用该条件!)。
- 3、如文档侵犯您的权益,请联系客服反馈,我们会尽快为您处理(人工客服工作时间:9:00-18:30)。
孔的加工及其达到的精度
孔的加工及其达到的精度
一、钻孔
1. 工艺特点
1)钻孔是孔的粗加工方法;
2)可加工直径0.05~125mm的孔;
3)孔的尺寸精度在IT10以下;
4)孔的表面粗糙度一般只能控制在Ra12.5μm。
对于精度要求不高的孔,如螺栓的贯穿孔、油孔以及螺纹底孔,可直接采用钻孔。
二、扩孔
工艺特点
1)扩孔是孔的半精加工方法;
2)一般加工精度为IT10~IT9;
3)孔的表面粗糙度可控制在Ra6.3 ~3.2μm。
当钻削dw>30mm直径的孔时,为了减小钻削力及扭矩,提高孔的质量,一般先用(0.5~0.7)dw大小的钻头钻出底孔,再用扩孔钻进行扩孔,则可较好地保证孔的精度和控制表面粗糙度,且生产率比直接用大钻头一次钻出时还要高。
三、铰孔
铰削过程的实质
铰削过程不完全是一个切削过程,而是包括切削、刮削、挤压、熨平和摩擦等效应的一个综合作用过程。
铰削用量
1)铰削余量粗铰余量为0.10mm~0.35 mm;精铰余量为0.04mm~0.06mm。
2)切削速度和进给量铰削速度为1.5m/min ~5m/min;铰削钢件时,进给量为0.3mm/r ~2mm/r;铰削铸铁件时,进给量为0.5mm/r ~3mm/r。
工艺特点
1)铰孔是孔的精加工方法;
2)可加工精度为IT7、IT8、IT9的孔;
3)孔的表面粗糙度可控制在Ra3.2 ~0.2μm;
4)铰刀是定尺寸刀具;
5)切削液在铰削过程中起着重要的作用。
四、镗孔
工艺特点
1)镗孔可不同孔径的孔进行粗、半精和精加工;
2)加工精度可达为IT7~IT6;
3)孔的表面粗糙度可控制在Ra6.3 ~0.8μm。
4)能修正前工序造成的孔轴线的弯曲、偏斜等形状位置误差;
五、拉孔
工艺特点
1) 拉削生产率高。
2) 拉削精度高,质量稳定。
拉削精度一般可达IT9-IT7级,表面粗糙度一般可控制到Ra1.6mm~Ra0.8mm,拉削表面的形状、尺寸精度和表面质量主要依靠拉刀设计、制造及正确使用保证。
3) 拉削成本低,经济效益高。
4) 拉刀是定尺寸、高精度、高生产率专用刀具,制造成本很高,所以,拉削加工只适用于批量生产,最好是大批大量生产,一般不宜用于单件、小批生产。
六、内圆磨削
工艺特点
1)磨削是零件精加工的主要方法之一;
2)对长径比小的,内孔磨削的经济精度可达IT5~IT6,表面粗糙度可控制到Ra0.8mm~Ra0.2mm;
3)可加工较硬的金属材料和非金属材料,如淬火钢、硬质合金和陶瓷等。
内圆磨削与外圆磨削相比,存在如下一些主要问题:
1) 内圆磨削的表面较外圆磨削的粗糙。
2) 生产率较低。
3) 磨削接触区面积较大,砂轮易堵塞,散热和切削液冲刷困难。
因此内孔磨削一般仅适用于淬硬工件的精加工,在单件、小批生产中和在大批大量生产中都有应用。
七、总结
(一)小批量加工
1.钻IT13~IT11 Ra 25
2.钻→铰IT9 Ra 6.3~
3.2
3.钻→粗铰→精铰IT8~IT7 Ra 3.2~1.6
4.钻→扩IT11 Ra 25~12.5
5.钻→扩→铰IT9~IT7 Ra
6.3~3.2
6.钻→扩→粗铰→精铰IT7 Ra 3.2~1.6
7.钻→扩→机铰→手铰IT7~IT6 Ra 0.8~0.2
8.钻→扩→拉IT9~IT7 Ra 3.2~0.2
(二)大批大量生产
9.粗镗(或扩孔)IT13~IT11Ra 25~12.5
10.粗镗(粗扩)→半精镗(精扩)IT9~IT8 Ra 6.3~3.2
11.粗镗(粗扩)→半精镗(精扩)→精镗(铰)IT8~IT7Ra 3.2~1.6
12.粗镗→半精镗→精镗→浮动镗刀精镗IT7~IT6 Ra
1.6~0.8
13.粗镗→半精镗→精镗→浮动镗刀精镗→挤压IT7~IT6 Ra 1.6~0.4
14.粗镗→半精镗→磨孔IT8~IT7 Ra 1.6~0.4
15.粗镗→半精镗→粗磨→精磨IT7~IT6 Ra 0.4~0.2
16.粗镗→半精镗→精镗→金刚镗IT7~IT6 Ra 0.8~0.1
17.钻→扩→粗铰→精铰→珩磨IT7~IT6 Ra 0.4~0.05
18.钻→扩→拉→珩磨IT7~IT6 Ra 0.4~0.05
19.粗镗→半精镗→精镗→珩磨
20.钻→扩→粗铰→精铰→研磨
21.钻→扩→拉→研磨IT6以上Ra 0.2~0.012
22.粗镗→半精镗→精镗→研磨
第1章绪论
第1.1节焚烧技术的发展历史
垃圾焚烧技术作为一种以燃烧为手段的垃圾处理方法,其应用可以追溯至人类文明的早期,如刀耕火种时期的烧荒即可视为焚烧应用的一例。
但焚烧作为一种处理生活垃圾的专用技术,其发展历史与其他垃圾处理方法相比要短很多,大致经历了三个阶段。
1.1.1萌芽阶段
萌芽阶段是从19世纪80年代开始到20世纪初期。
1874年和1885年,英国诺丁汉和美国纽约先后建造了处理生活垃圾的焚烧炉,代表了生活垃圾焚烧技术的兴起。
1896年和1898年,德国汉堡和法国巴黎先后建立了世界上最早的生活垃圾焚烧厂,开始了生活垃圾焚烧技术的工程应用。
但是由于这一阶段的技术原始和垃圾中可燃物的比例较低,在垃圾焚烧过程中产生的浓烟和臭味,对环境的二次污染相当严重,因此这种方法曾一度为人们所抛弃。
1.1.2 发展阶段
从20世纪初到60年代末的约半个世纪,是垃圾焚烧技术的发展阶段。
一次世界大战后,发达国家的经济得到了较大发展,城市居民生活水平的提高和生活垃圾成分的变化,给垃圾焚烧创造了条件,因此垃圾焚烧技术又逐渐发展起来。
这期间,欧洲、北美及日本都陆续建起了一些生活垃圾焚烧厂,其工艺与设
施水平也在随着燃煤技术的发展而从固定炉排到机械炉排,从自然通风到机械供风而逐步得到发展。
二次世界大战以后,发达国家的经济得到更大发展,城市居民的生活水平进一步提高,垃圾中的可燃物和易燃物也随之迅速上升,促进了垃圾焚烧技术的应用。
特别是在20世纪60 年代的电子工业变革后,各种先进技术在垃圾焚烧炉上得到了应用,使垃圾焚烧炉得到了进一步完善。
但总体来说,由于当时城市生活垃圾中的可燃物仍然少于非可燃物,产生量与消耗空间的矛盾尚不突出,对垃圾焚烧伴随的环境问题的认识仍肤浅等因素,直到20世纪70年代以前,生活垃圾焚烧技术的发展并不十分理想。
1.1.3 成熟阶段
从20世纪70年代初到90年代中期的20多年间,是生活垃圾焚烧技术的成熟阶段,也是生活垃圾焚烧技术发展最快的时期。
这时期几乎所有的发达国家、中等发达国家都建设了不同规模、不同数量的垃圾焚烧发电厂,发展中国家建设的垃圾焚烧发电厂的也不在少数,垃圾焚烧技术的发展方兴未艾。
表1-1所示的数据可以对生活垃圾焚烧技术的当代发展史作一代表性的注解。
综合分析发达国家生活垃圾焚烧技术在近二十年间迅速发展的原因,除了经济、技术、观念等因素外,还有一些其他方面的影响,比如:随着城市建设的发展和城市规模的扩大,城市人口数量骤增,生活垃圾产量也快速递增,使原有的垃圾填埋场日益饱和或已经饱和,而新的垃圾填埋场地又难于寻找,采取垃圾焚烧方法,可使生活垃圾减容85%。