硫化工艺简介
硫化工艺技术

硫化工艺技术硫化工艺技术是一种常用的制造工艺,用于改善材料的性能和增加其使用寿命。
硫化是指在一定条件下,通过硫黄与材料反应,形成硫化物,并在材料中形成交联结构的过程。
硫化工艺技术广泛应用于橡胶、塑料和纤维等材料的生产中,下面我们来介绍一下硫化工艺技术的基本原理。
首先,硫化工艺技术的目的是通过交联结构的形成,增加材料的强度、耐磨性和耐老化性能。
硫化是通过硫黄与材料中的双键反应形成硫化物,从而将材料的分子间锁定在一起,形成交联结构。
硫黄在硫化过程中充当交联剂的角色,它能够与材料中的双键发生反应,将分子间的链断裂,并形成新的交联结构。
其次,硫化工艺技术的关键是控制硫化反应的温度和时间。
硫化反应需要一定的温度和时间才能完成。
温度过高或时间过长会导致硫化反应过度,使材料变硬、脆化甚至破裂。
温度过低或时间过短则无法完成硫化反应,材料性能改善效果不明显。
因此,在硫化工艺技术中,需要根据不同材料的特性和要求,合理选择硫化温度和时间,以达到最佳硫化效果。
此外,硫化工艺技术还需要使用一定的硫化助剂和适当的硫化条件。
硫化助剂有助于加快硫化反应速度,提高硫化效果。
常用的硫化助剂有活性剂、抗老化剂和加成剂等。
硫化条件主要包括硫化温度、硫化时间和硫化环境等,不同材料对硫化条件的要求也有所不同。
最后,硫化工艺技术在实际应用中还需要注意一些问题。
首先是硫化过程中产生的气体和有害物质的处理问题。
硫化反应会产生一些有害气体和污染物,需要通过适当的处理措施将其排出和处理,以保护环境和人体健康。
其次是硫化后材料的贮存和使用问题。
硫化后的材料需要避免日光直射和潮湿环境,以防止硫化物的分解和材料的老化。
总之,硫化工艺技术是一种重要的制造工艺,通过硫化反应能够改善材料的性能和增加其使用寿命。
在应用硫化工艺技术时,需要合理选择硫化条件、使用适当的硫化助剂,并注意硫化过程中产生的气体和有害物质的处理问题。
通过科学的硫化工艺技术,可以使材料的性能得到有效提升,推动工业的发展。
硫化工艺过程控制

硫化工艺过程控制1. 硫化工艺概述硫化是一种常见的化学工艺,用于制造硫化橡胶、硫化塑料等材料。
硫化过程控制是确保硫化反应达到所需质量和性能的关键因素。
本文将介绍硫化工艺的基本原理和常见的过程控制方法。
2. 硫化反应的原理硫化反应是将天然橡胶或合成橡胶中的不饱和键与硫化剂发生反应,形成交联结构的过程。
硫化剂在反应中起着催化剂的作用,加速反应速度。
硫化反应过程中主要涉及以下几个方面的控制:•反应温度:反应温度不同会导致反应速度和交联结构的形成不同。
•反应时间:反应时间决定了反应程度和硫化物的生成。
•硫化剂浓度:硫化剂浓度的调控可以控制反应速度和交联密度。
3. 硫化工艺的过程控制方法3.1 温度控制硫化反应温度是影响硫化速率和硫化物结构的重要因素。
温度过低会导致反应速度慢,交联结构不完全;温度过高会导致反应过度,交联结构过强。
要控制硫化反应温度,可以采用以下方法:•传统控制方法:传统控制方法是通过控制加热器的功率或控制炉内的加热介质温度来实现温度控制。
•PID控制方法:PID控制方法是通过传感器测量温度,根据反馈信号进行控制,使温度稳定在设定值附近。
3.2 时间控制硫化反应时间是控制硫化程度的重要因素。
过长的反应时间会导致硫化过度,而过短的反应时间会导致交联结构不完全。
要控制硫化反应时间,可以采用以下方法:•手动控制方法:通过观察反应过程中硫化物的形成情况来控制硫化反应时间。
•自动控制方法:使用计时器或自动控制系统来控制硫化反应时间。
3.3 硫化剂浓度控制硫化剂浓度是影响硫化反应速度和交联结构的重要因素。
浓度过高会导致反应速度过快,交联结构过强;浓度过低会导致反应速度慢,交联结构不完全。
要控制硫化剂浓度,可以采用以下方法:•手动控制方法:通过调整硫化剂的投入量来控制硫化剂浓度。
•自动控制方法:使用流量控制器和比例控制器来控制硫化剂的投入量,从而实现硫化剂浓度的控制。
4. 硫化工艺的优化为了提高硫化工艺的效率和产品质量,可以采取以下优化措施:•优化硫化剂选择:选择适合特定反应条件的硫化剂,可以提高反应速率和交联结构的形成。
硫化工艺
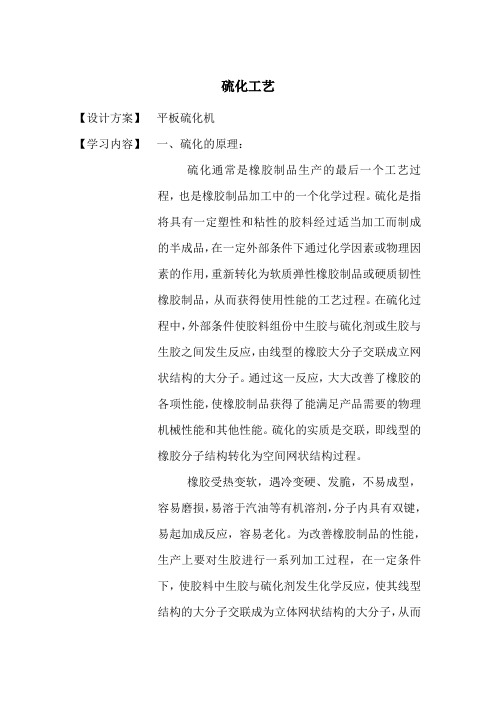
硫化工艺【设计方案】平板硫化机【学习内容】一、硫化的原理:硫化通常是橡胶制品生产的最后一个工艺过程,也是橡胶制品加工中的一个化学过程。
硫化是指将具有一定塑性和粘性的胶料经过适当加工而制成的半成品,在一定外部条件下通过化学因素或物理因素的作用,重新转化为软质弹性橡胶制品或硬质韧性橡胶制品,从而获得使用性能的工艺过程。
在硫化过程中,外部条件使胶料组份中生胶与硫化剂或生胶与生胶之间发生反应,由线型的橡胶大分子交联成立网状结构的大分子。
通过这一反应,大大改善了橡胶的各项性能,使橡胶制品获得了能满足产品需要的物理机械性能和其他性能。
硫化的实质是交联,即线型的橡胶分子结构转化为空间网状结构过程。
橡胶受热变软,遇冷变硬、发脆,不易成型,容易磨损,易溶于汽油等有机溶剂,分子内具有双键,易起加成反应,容易老化。
为改善橡胶制品的性能,生产上要对生胶进行一系列加工过程,在一定条件下,使胶料中生胶与硫化剂发生化学反应,使其线型结构的大分子交联成为立体网状结构的大分子,从而使胶料具备高强度、高弹性、抗腐蚀等优良性能。
二、硫化的方法1、温室硫化法温室硫化法用于需求在室温及不加压的条件下进行硫化的场合。
室温硫化通常将硫化剂与溶剂、惰性配合剂等配成一个组份,橡胶、树脂等与其他配合剂配成另一组分,使用是进行混合。
2、冷硫化法把制成品浸入2%-5%的一氯化硫的溶液中,时间从几秒到几分钟不等。
3、热硫化法⑴、间歇式硫化①、热水槽硫化法此法为直接常压硫化法,把需要硫化的产品浸于热水或盐水,适于乳胶薄膜制品的硫化。
②、烘房、烘箱热空气硫化法此法也为直接常压硫化法,该方法有两种方式,一是把半成品放在加热室中加热硫化;另一种是烘箱硫化,适用于某些特种橡胶制品的二次硫化。
③、硫化罐硫化硫化罐硫化工艺借助飞的硫化设备为硫化罐。
根据硫化介质的不同,硫化罐硫化工艺又有如下几种主要硫化方法:A、直接饱和蒸汽硫化法a、开放式硫化法b、包层硫化法c、埋粉硫化法d、模型硫化法B、热空气硫化法C、热空气-蒸汽混合硫化法⑵、外加压式硫化工艺①、平板硫化机模压硫化法采用这种方法可同时进行胶料在模具型腔内加压流动成型和胶料在硫化温度及硫化压力下发生硫化反应这两个过程。
硫化工艺过程范文

硫化工艺过程范文硫化是一种化学工艺过程,用于将硫与其他物质反应,从而形成硫化物。
这种工艺具有广泛的应用领域,例如橡胶、化学、能源等行业。
硫化橡胶是其中一种最常见的应用。
硫化作为橡胶制品的重要步骤,通过交联橡胶分子链,提高其耐热性、耐磨性和强度,从而使橡胶具有更好的物理性能。
硫化过程可以在橡胶原料中添加硫化剂,然后进行加热处理。
在加热过程中,硫化剂会与橡胶中的双键反应,形成硫化键,使橡胶分子链交联成网状结构。
硫化过程的关键参数包括温度、时间和硫化剂的种类和用量。
温度是影响硫化速率和硫化程度的重要因素。
在温度较低时,硫化反应速率较慢,所需时间较长。
而在温度较高时,硫化反应速率加快,但过高的温度可能导致橡胶材料的烧损。
因此,要根据具体材料和设备的要求选择适当的硫化温度。
硫化时间是指硫化过程持续的时间。
根据硫化剂的类型和含量,硫化时间可以从几分钟到几小时不等。
过短的硫化时间可能导致硫化不完全,从而影响橡胶制品的性能。
而过长的硫化时间则可能导致橡胶过硬或老化。
因此,要根据具体材料和硫化剂的要求确定适当的硫化时间。
硫化剂的种类和用量也对硫化过程的效果有重要影响。
硫化剂可以分为加热硫化剂和光照硫化剂两类。
加热硫化剂在加热过程中释放出硫,在硫化反应中起到催化作用。
常见的加热硫化剂有硫醇、硫代硫酸酯等。
光照硫化剂则通过光能诱导硫化反应。
常见的光照硫化剂有过氧化物、硝酸等。
硫化剂的用量也需要根据具体需要进行调整,以达到理想的硫化效果。
除了硫化橡胶,硫化还可以用于化学反应中。
例如,有机合成中的硫化反应常用于构建C-S键。
此类反应在有机合成中具有重要的应用,能够构建多种有机分子结构,如硫醚、硫醇等。
相应的硫化剂和反应条件也各有差异,需要根据具体反应目标进行选择。
在能源行业中,硫化过程也有重要的应用。
例如,燃料电池中的阳极催化剂通常采用硫化过程进行改性。
在这个过程中,阳极催化剂通常与硫反应,形成具有更好催化性能的硫化物。
平板硫化工艺

平板硫化工艺平板硫化工艺是一种常用于橡胶制品生产中的硫化工艺。
通过该工艺,可以使橡胶材料在一定温度和压力下,与硫进行反应,形成交联结构,从而增强橡胶材料的物理性能和化学稳定性。
本文将从工艺原理、工艺流程、设备要求和应用范围等方面,详细介绍平板硫化工艺。
一、工艺原理平板硫化工艺是利用硫化剂与橡胶材料进行反应,形成交联结构的过程。
硫化剂一般采用硫磺,其分子中的硫原子与橡胶材料中的双键发生反应,形成硫化交联结构。
这种交联结构可以增强橡胶材料的强度、弹性和耐磨性,提高其耐热性和耐化学腐蚀性。
二、工艺流程平板硫化工艺主要包括原料准备、混炼、成型、硫化和后处理等环节。
1. 原料准备:包括橡胶材料和硫磺的准备。
橡胶材料一般采用天然橡胶、合成橡胶或二者的混合物。
硫磺是硫化剂的一种,需要按照一定比例添加到橡胶材料中。
2. 混炼:将橡胶材料和硫磺进行混合,以确保硫磺能够均匀分散在橡胶材料中。
混炼过程中需要加热和搅拌,以提高硫化剂的分散性和混炼效果。
3. 成型:将混炼好的橡胶材料放入模具中,进行成型。
成型可以采用压力成型或挤出成型等方法,根据不同的产品需求选择不同的成型方式。
4. 硫化:将成型好的橡胶制品放入硫化炉中进行硫化。
硫化炉中需要控制一定的温度和时间,以确保硫磺能够与橡胶材料发生充分的反应,形成交联结构。
5. 后处理:硫化完成后,需要对橡胶制品进行一些后处理。
主要包括去除模具、修整制品表面、检查质量和包装等环节。
三、设备要求平板硫化工艺需要一些特殊的设备来完成,包括混炼机、硫化炉、模具和后处理设备等。
1. 混炼机:用于将橡胶材料和硫磺进行混合。
混炼机需要具备加热和搅拌功能,以确保混炼效果。
2. 硫化炉:用于将成型好的橡胶制品进行硫化。
硫化炉需要具备控制温度和时间的功能,以确保硫化效果。
3. 模具:用于成型橡胶制品。
模具需要具备一定的强度和耐磨性,以确保成型的准确性和稳定性。
4. 后处理设备:用于对硫化完成的橡胶制品进行后处理。
模压硫化方法和工艺过程简介

模压硫化方法和工艺过程简介1、硫化方法简介使橡胶分子交联起来,成为网络结构,因而改进了橡胶的使用性能,这种变化叫做“硫化” 。
天然胶起初是用硫磺硫化的,“硫化”这个名词就是由此而来。
按硫化方法的不同分为热硫化、冷硫化、高频硫化、高能射线辐射硫化等。
(1)热硫化热硫化是橡胶用电或蒸汽加热硫化。
用于硫化各种模型制品,各种胶带、胶板、轮胎、胶布等。
(2)冷硫化冷硫化是橡胶在常温下硫化,多用于自然硫化胶浆粘合的制品。
胶浆内配有活性强的超促进剂,使用这种胶浆粘合的制品,于室温停放一段时间即达到硫化的目的。
特别是大型的胶布制品,如橡胶水管、胶囊等多采用这种方法。
也可以制造快速自然硫化胶浆,使其在短时间内,得到相当高的粘合强度。
还有一种冷硫化方法是用2%-5% 的一氯化硫稀溶液浸渍不含硫磺的制品进行硫化。
因只能用于薄膜制品,同时一氯化硫毒性较大,所以航空工业中很少采用。
(3)高频硫化在均匀的高频交变电场作用下,橡胶分子随电场的变化而运动,由于分子间的运动、互相摩擦及位移,使胶料本身产生热量,从而达到硫化的目的。
(4)高能射线辐射硫化用Co60放射丫射线作为能源,在常温下,辐射能将橡胶分子的氢原子脱离,在橡胶链上生成游离基,产生交联作用,使橡胶的直链分子生成网状结构,完成硫化过程。
高能射线辐射可使不含硫化剂、促进剂的橡胶进行硫化,获得优良的物理性能。
由于成本高昂,只用于特殊制品。
但是它可以简化工艺、加速生产,有发展前途。
2、模压硫化工艺过程简介(1)热炼胶料在硫化前应进行热炼,以便破坏其在停放时产生的凝胶,提高胶料的塑性和均匀程度。
方法是将胶料切成小块,用抹布浸航空汽油或苯洗去胶料上的脏物、灰尘和有关标记。
在室温下晾干10-15 分钟。
然后在炼胶机上热炼3-5 分钟,薄通数次,使胶料表面柔软、光滑。
再按规定尺寸切片。
经热炼的胶料应在12 小时内使用为宜。
过时的胶料可按30%的量掺入同牌号、同批次的胶料中,重新热炼后使用。
硫化工艺简介
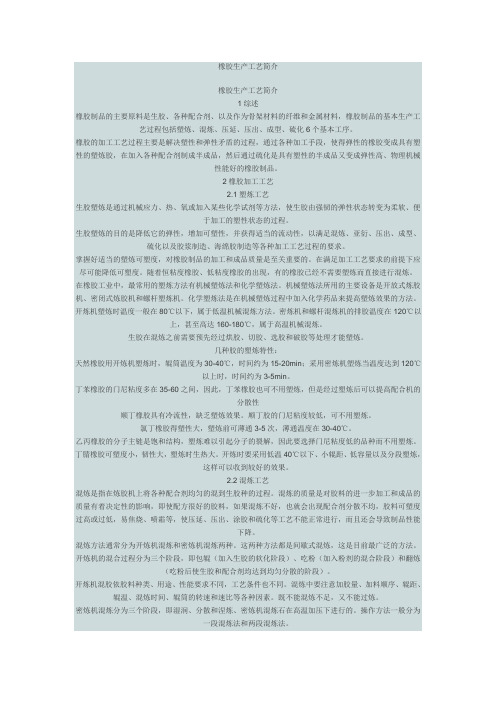
橡胶生产工艺简介橡胶生产工艺简介1综述橡胶制品的主要原料是生胶、各种配合剂、以及作为骨架材料的纤维和金属材料,橡胶制品的基本生产工艺过程包括塑炼、混炼、压延、压出、成型、硫化6个基本工序。
橡胶的加工工艺过程主要是解决塑性和弹性矛盾的过程,通过各种加工手段,使得弹性的橡胶变成具有塑性的塑炼胶,在加入各种配合剂制成半成品,然后通过硫化是具有塑性的半成品又变成弹性高、物理机械性能好的橡胶制品。
2橡胶加工工艺2.1塑炼工艺生胶塑炼是通过机械应力、热、氧或加入某些化学试剂等方法,使生胶由强韧的弹性状态转变为柔软、便于加工的塑性状态的过程。
生胶塑炼的目的是降低它的弹性,增加可塑性,并获得适当的流动性,以满足混炼、亚衍、压出、成型、硫化以及胶浆制造、海绵胶制造等各种加工工艺过程的要求。
掌握好适当的塑炼可塑度,对橡胶制品的加工和成品质量是至关重要的。
在满足加工工艺要求的前提下应尽可能降低可塑度。
随着恒粘度橡胶、低粘度橡胶的出现,有的橡胶已经不需要塑炼而直接进行混炼。
在橡胶工业中,最常用的塑炼方法有机械塑炼法和化学塑炼法。
机械塑炼法所用的主要设备是开放式炼胶机、密闭式炼胶机和螺杆塑炼机。
化学塑炼法是在机械塑炼过程中加入化学药品来提高塑炼效果的方法。
开炼机塑炼时温度一般在80℃以下,属于低温机械混炼方法。
密炼机和螺杆混炼机的排胶温度在120℃以上,甚至高达160-180℃,属于高温机械混炼。
生胶在混炼之前需要预先经过烘胶、切胶、选胶和破胶等处理才能塑炼。
几种胶的塑炼特性:天然橡胶用开炼机塑炼时,辊筒温度为30-40℃,时间约为15-20min;采用密炼机塑炼当温度达到120℃以上时,时间约为3-5min。
丁苯橡胶的门尼粘度多在35-60之间,因此,丁苯橡胶也可不用塑炼,但是经过塑炼后可以提高配合机的分散性顺丁橡胶具有冷流性,缺乏塑炼效果。
顺丁胶的门尼粘度较低,可不用塑炼。
氯丁橡胶得塑性大,塑炼前可薄通3-5次,薄通温度在30-40℃。
硫化工艺

硫化工艺硫化(Vulcanization) (引申定义)硫化过程中发生了硫的交联,这个过程是指把一个或更多的硫原子接在聚合物链上形成桥状结构。
反应的结果是生成了弹性体,它的性能在很多方面都有了改变,硫化剂可以是硫或者其它相关物质。
“硫化”一词有其历史性,因最初的天然橡胶制品用硫磺作交联剂进行交联而得名,随着橡胶工业的发展,现在可以用多种非硫磺交联剂进行交联。
因此硫化的更科学的意义应是“交联”或“架桥”,即线性高分子通过交联作用而形成的网状高分子的工艺过程。
硫化过程中发生了硫的交联,这个过程是指把一个或更多的硫原子接在聚合物链上形成桥状结构。
反应的结果是生成了弹性体,它的性能在很多方面都有了改变,硫化剂可以是硫或者其它相关物质。
从物性上即是塑性橡胶转化为弹性橡胶或硬质橡胶的过程。
“硫化”的含义不仅包含实际交联的过程,还包括产生交联的方法。
硫化过程可分为四个阶段,各阶段的特点:通过胶料定伸强度的测量(或硫化仪)可以看到,整个硫化过程可分为硫化诱导,预硫,正硫化和过硫(对天然胶来说是硫化返原)四个阶段。
硫化诱导期(焦烧时间)内,交联尚未开始,胶料有很好的流动性。
这一阶段决定了胶料的焦烧性及加工安全性。
这一阶段的终点,胶料开始交联并丧失流动性。
硫化诱导期的长短除与生胶本身性质有关,主要取决于所用助剂,如用迟延性促进剂可以得到较长的焦烧时间,且有较高的加工安全性。
硫化诱导期以后便是以一定速度进行交联的预硫化阶段。
预硫化期的交联程度低,即使到后期硫化胶的扯断强度,弹性也不能到达预想水平,但撕裂和动态裂口的性能却比相应的正硫化好。
到达正硫化阶段后,硫化胶的各项物理性能分别达到或接近最佳点,或达到性能的综全平衡。
正硫化阶段(硫化平坦区)之后,即为过硫阶段,有两种情况:天然胶出现“返原”现象(定伸强度下降),大部分合成胶(除丁基胶外)定伸强度继续增加。
对任何橡胶来说,硫化时不只是产生交联,还由于热及其它因素的作用产生产联链和分子链的断裂。
硫化工艺

三、硫化压力
1)橡胶制品硫化时都需要施加压力,其目的是: a.防止胶料产生气泡,提高胶料的致密性; b.使胶料流动,充满模具,以制得花纹清晰的制品 c.提高制品中各层(胶层与布层或金属层、布层与布层) 之间的粘着力,改善硫化胶的物理性能(如耐屈挠性能)。 2)一般来说,硫化压力的选取应根据产品类型、配方、可 塑性等因素决定。 3)原则上应遵循以下规律:可塑性大,压力宜小些;产品 厚、层数多、结构复杂压力宜大些;薄制品压宜小些,甚 至可用常压。
3. 硫化平坦阶段(正硫期-正硫化阶段) 硫化平坦阶段(正硫期-正硫化阶段)
硫化平坦阶段,交联反应已趋于完成,反应速度已 较为缓和。硫化胶的综合物理机械性能已达到或接 近最佳值。 正硫化:在平坦硫化阶段,橡胶制品的综合物理机 械性能达到最佳值,这种硫化状态称为正硫化,也 称最宜硫化。正硫化前期成为欠硫;正硫化后期则 成为过硫,欠硫或过硫,橡胶的物理机械性能均较 差。 正硫化时间:正硫化时间是指达到正硫化状态所需 的最短时间,也称为“正硫化点”。
二、硫化历程 在硫化过程中,各种性能均会随硫化的进程而发生 变化,这种变化曲线能够反映胶料的全过程,称为 硫化历程。 硫化历程大致分为四个阶段:A.焦烧阶段;B. 热硫化阶段;C.平坦硫化阶段;D.过硫化阶段。
1. 焦烧阶段(焦烧期-硫化起步阶段, 焦烧阶段(焦烧期-硫化起步阶段, 化诱导期) 硫 化诱导期) 焦烧阶段交联尚未开始,胶料在模腔内具 有良好的流动性,也称为硫化诱导阶段。胶料 焦烧时间的长短决定胶料的焦烧性能和操作安 全性。胶料焦烧时间受胶料中硫化促进剂和胶 料本身的热历史的影响较大。焦烧时间既包括 橡胶在加工过程中由于热积累消耗掉的焦烧时 间A1,称为操作焦烧时间;也包括胶料在模腔 中保持流动性的时间A2,称为剩余焦烧时间 。
硫化 生产工艺
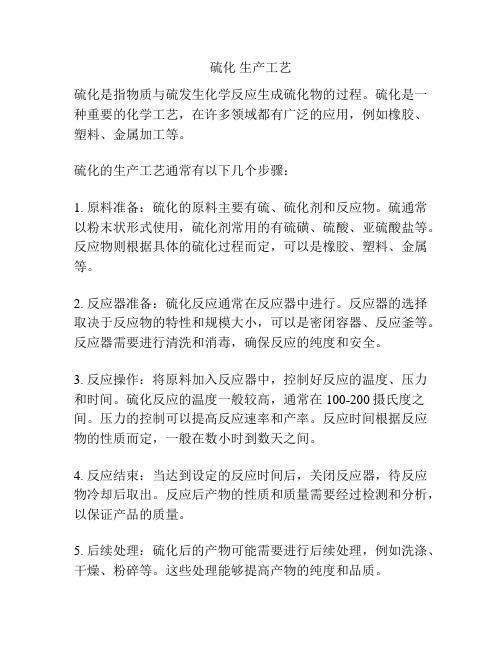
硫化生产工艺硫化是指物质与硫发生化学反应生成硫化物的过程。
硫化是一种重要的化学工艺,在许多领域都有广泛的应用,例如橡胶、塑料、金属加工等。
硫化的生产工艺通常有以下几个步骤:1. 原料准备:硫化的原料主要有硫、硫化剂和反应物。
硫通常以粉末状形式使用,硫化剂常用的有硫磺、硫酸、亚硫酸盐等。
反应物则根据具体的硫化过程而定,可以是橡胶、塑料、金属等。
2. 反应器准备:硫化反应通常在反应器中进行。
反应器的选择取决于反应物的特性和规模大小,可以是密闭容器、反应釜等。
反应器需要进行清洗和消毒,确保反应的纯度和安全。
3. 反应操作:将原料加入反应器中,控制好反应的温度、压力和时间。
硫化反应的温度一般较高,通常在100-200摄氏度之间。
压力的控制可以提高反应速率和产率。
反应时间根据反应物的性质而定,一般在数小时到数天之间。
4. 反应结束:当达到设定的反应时间后,关闭反应器,待反应物冷却后取出。
反应后产物的性质和质量需要经过检测和分析,以保证产品的质量。
5. 后续处理:硫化后的产物可能需要进行后续处理,例如洗涤、干燥、粉碎等。
这些处理能够提高产物的纯度和品质。
硫化工艺的选择和优化取决于具体应用的要求。
在橡胶工业中,硫化是一种常用的工艺,可以增强橡胶的强度、弹性和耐磨性。
硫化的机理是通过硫与橡胶中的双键反应,形成交联结构,从而增加橡胶的强度和耐热性。
总的来说,硫化是一种重要的化学工艺,通过控制好反应条件和使用合适的原料,可以获得高质量的硫化产物。
随着科技的发展,硫化工艺也在不断创新和改进,以满足不同领域的需求。
橡胶制品的硫化工艺
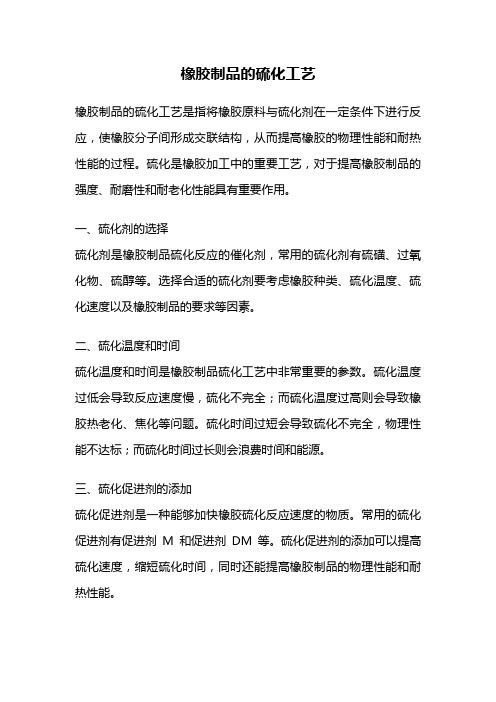
橡胶制品的硫化工艺橡胶制品的硫化工艺是指将橡胶原料与硫化剂在一定条件下进行反应,使橡胶分子间形成交联结构,从而提高橡胶的物理性能和耐热性能的过程。
硫化是橡胶加工中的重要工艺,对于提高橡胶制品的强度、耐磨性和耐老化性能具有重要作用。
一、硫化剂的选择硫化剂是橡胶制品硫化反应的催化剂,常用的硫化剂有硫磺、过氧化物、硫醇等。
选择合适的硫化剂要考虑橡胶种类、硫化温度、硫化速度以及橡胶制品的要求等因素。
二、硫化温度和时间硫化温度和时间是橡胶制品硫化工艺中非常重要的参数。
硫化温度过低会导致反应速度慢,硫化不完全;而硫化温度过高则会导致橡胶热老化、焦化等问题。
硫化时间过短会导致硫化不完全,物理性能不达标;而硫化时间过长则会浪费时间和能源。
三、硫化促进剂的添加硫化促进剂是一种能够加快橡胶硫化反应速度的物质。
常用的硫化促进剂有促进剂M和促进剂DM等。
硫化促进剂的添加可以提高硫化速度,缩短硫化时间,同时还能提高橡胶制品的物理性能和耐热性能。
四、硫化工艺条件控制硫化工艺条件的控制对于橡胶制品的质量起着至关重要的作用。
首先是硫化温度的控制,要根据橡胶种类和硫化剂的要求确定合适的硫化温度。
其次是硫化时间的控制,要根据硫化剂的种类和硫化速度确定合适的硫化时间。
此外,还需要对硫化压力、硫化介质等进行合理控制,以确保橡胶制品硫化过程的顺利进行。
五、硫化反应机理橡胶硫化反应是一个复杂的化学反应过程,其机理主要包括链断裂、硫醇与橡胶分子的反应、交联等。
硫化反应的机理研究对于优化硫化工艺、提高橡胶制品性能具有重要意义。
六、硫化后的橡胶制品处理硫化后的橡胶制品需要进行后处理,包括清洗、修整、检验等。
清洗可以去除硫化剩余物和杂质,使橡胶制品表面干净整洁;修整可以修剪橡胶制品的边缘,使其外观更加美观;检验则是对橡胶制品进行物理性能和外观质量的检测,以确保橡胶制品符合规定的标准和要求。
橡胶制品的硫化工艺是一个非常重要的工艺环节,对于提高橡胶制品的性能和质量至关重要。
硫化工艺
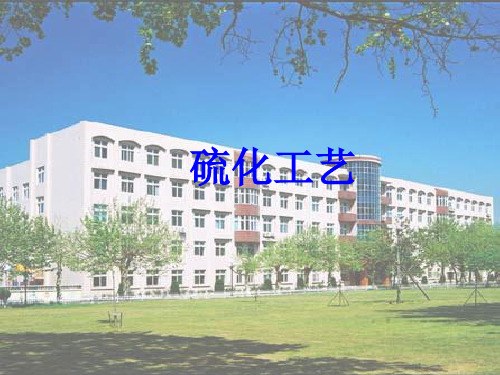
(四)、理想硫化曲线
硫化诱导期足够大,充分保证生产加工的安 全性; 硫化速度要快,提高生产效率,降低成本; 硫化平坦期要长。
达到上述要求,必须正确选择硫化条件和硫化 体系。
15
高分子材料加工基础
三、正硫化及其测定方法
1、正硫化及正硫化时间
正硫化,又称最宜硫化,通常是指橡胶制品 性能达最佳值时的硫化状态。
热空气硫化法
制品直接与硫化介质 接触而进行硫化,优 点是效率高、传热效 果好,温度分布均匀, 但由于与硫化直接接 触,易使制品表面不 光滑。
38
高分子材料加工基础
间接硫化法
用间接蒸气硫化,常用于胶鞋、胶靴等制 品,这类制品表面要求美观,颜色鲜艳,故 要求在干燥条件进行硫化。
使用的设备一般为卧式硫化罐,硫化罐为夹 套式或装有蛇盘管,内通蒸气加热,罐内的 加热介质为热空气。
7
高分子材料加工基础
(二)、硫化历程图
在硫化过程中橡胶的各种性能都随 着时间增加而发生变化,若将橡胶 的某一项性能的变化与对应的硫化 时间作图,则可得到一个曲线图形, 从这种曲线图形中可显示出胶料的 硫化历程,称为硫化历程图,也称 硫化曲线。
反映的是胶料在一定硫化温度下, 转矩(模量)随硫化时间的变化。
32
高分子材料加工基础
硫化效应(E)等于硫化强度(I)与硫化 时间(t)的乘积, 即E=It。
硫化强度指胶料在一定温度下单位时间所 取得的硫化程度,与硫化温度和硫化温度 系数K有关,即I=K(T-100)/10
E=K(T-100)/10 ·t
由上式可以求得在不同硫化条件下,达到 相同的硫化效应所需要的时间。
硫化时间的硫化胶样品的性能,然后绘制曲线, 找出最佳值作为正硫化时间; 后一种方法是用仪器在选定温度下测定出硫化 曲线,直接从曲线上取值,找出正硫化时间; 常用的是后两类方法。
硫化焙烧工艺

硫化焙烧工艺一、硫化焙烧概述硫化焙烧是一种高温处理金属或化合物的方法,通过与硫或其他硫化剂作用,使其转化为具有高反应活性和易处理的形式。
该工艺在矿业、化工、材料科学等领域应用广泛,主要用于金属提取、化合物合成以及材料制备等过程。
二、硫化焙烧原理硫化焙烧的原理主要是通过高温下金属与硫之间的化学反应,将金属从其氧化物或原生矿物中还原出来。
这个过程通常会生成一系列的硫化物,如MeO + SO2(其中,Me代表金属元素)。
这些硫化物可以以气态或液态的形式离开反应体系,从而使得金属得到分离和富集。
三、硫化焙烧工艺流程1.准备原料:选择合适的矿物或氧化物作为原料,并进行必要的破碎和磨细处理。
2.混合与造球:将原料与适量的粘结剂混合,然后制成一定形状的球团或颗粒。
3.硫化焙烧:将球团或颗粒放入炉中进行高温处理,通常需要在1000℃以上进行反应。
4.烟气处理:对排放的烟气进行处理,以防止污染环境。
5.产品处理:对焙烧后的产物进行必要的处理,如破碎、磨细、洗涤等,以得到最终的产品。
四、硫化焙烧设备与工具硫化焙烧工艺需要的主要设备包括焙烧炉、输送设备、烟气处理设备等。
同时,还需要各种工具如夹具、冷却装置、气体分析仪等。
五、硫化焙烧原料与辅料硫化焙烧的原料主要是金属氧化物或矿物,而辅料则包括粘结剂、还原剂、催化剂等。
这些辅料的作用是帮助原料更好地进行反应,提高产物的质量和产量。
六、硫化焙烧操作规程在进行硫化焙烧时,需要遵循一定的操作规程。
首先,要确保所有设备和工具处于良好状态,并进行必要的检查和校准。
其次,要按照规定的步骤进行操作,包括原料准备、混合造球、装炉焙烧、烟气处理等。
最后,要对焙烧后的产物进行必要的处理,以满足后续工艺的需求。
七、硫化焙烧质量标准与检测方法为了确保硫化焙烧产品的质量和满足客户需求,需要制定相应的质量标准和检测方法。
这些标准和方法应该包括产品的化学成分、物理性能、杂质含量等方面。
同时,还需要对生产过程中的关键参数进行监控和记录,以确保生产过程的稳定性和可重复性。
橡胶硫化工艺

橡胶硫化工艺橡胶硫化工艺是将天然橡胶或合成橡胶通过硫化反应,使其具备强度、耐磨性、耐老化性等特性的一种工艺。
本文将从橡胶硫化的原理、硫化剂的选择、硫化工艺流程以及硫化后橡胶的性能等方面展开阐述。
一、橡胶硫化的原理橡胶硫化是指通过将橡胶与硫化剂在一定温度下反应,使橡胶中的双键与硫原子发生加成反应,形成交联结构的过程。
在硫化过程中,硫化剂中的硫原子会与橡胶中的双键发生反应,形成硫化橡胶。
硫化反应可以使橡胶具备耐高温、耐溶剂、耐老化等优异性能。
二、硫化剂的选择硫化剂是橡胶硫化过程中的重要组成部分,常用的硫化剂有硫、过氧化氮、过氧化物等。
硫是一种常用的硫化剂,其硫化反应速度较慢,但可以获得较好的硫化效果。
过氧化氮是一种加速剂,可以提高硫化反应速度和效果。
过氧化物则是一种高温硫化剂,适用于高温硫化橡胶。
三、硫化工艺流程橡胶硫化一般包括预硫化和硫化两个阶段。
预硫化是指在较低温度下对橡胶进行预处理,使其具备一定的硫化程度,提高硫化效果。
硫化是指在较高温度下对橡胶进行硫化反应,形成交联结构。
硫化温度一般在120℃-180℃之间,硫化时间根据橡胶种类和硫化剂的不同而定。
四、硫化后橡胶的性能橡胶经过硫化后,其性能得到显著改善。
硫化可以提高橡胶的强度、硬度、耐磨性、耐油性、耐老化性等。
硫化后的橡胶具有较好的弹性和可塑性,广泛应用于橡胶制品、轮胎、密封材料等领域。
总结:橡胶硫化工艺是将橡胶经过硫化反应,使其具备优异性能的一种工艺。
硫化剂的选择和硫化工艺流程对于硫化效果具有重要影响。
硫化后的橡胶具有较好的强度、耐磨性、耐老化性等性能,广泛应用于各个领域。
橡胶硫化工艺的研究和应用对于提高橡胶制品的品质和性能具有重要意义。
橡胶的硫化工艺
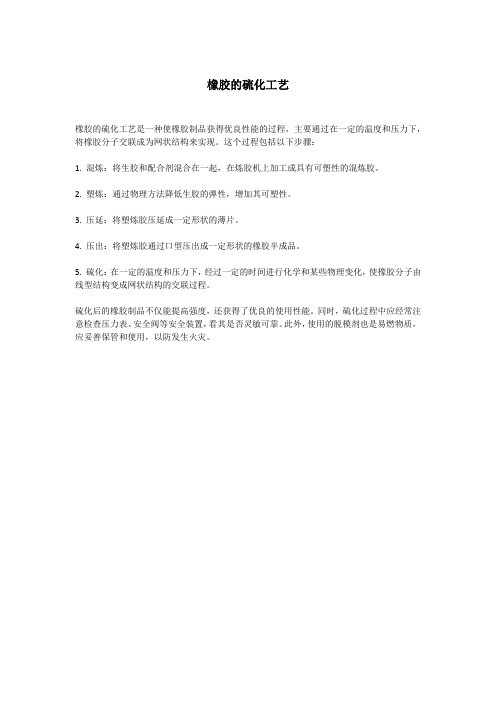
橡胶的硫化工艺
橡胶的硫化工艺是一种使橡胶制品获得优良性能的过程,主要通过在一定的温度和压力下,将橡胶分子交联成为网状结构来实现。
这个过程包括以下步骤:
1. 混炼:将生胶和配合剂混合在一起,在炼胶机上加工成具有可塑性的混炼胶。
2. 塑炼:通过物理方法降低生胶的弹性,增加其可塑性。
3. 压延:将塑炼胶压延成一定形状的薄片。
4. 压出:将塑炼胶通过口型压出成一定形状的橡胶半成品。
5. 硫化:在一定的温度和压力下,经过一定的时间进行化学和某些物理变化,使橡胶分子由线型结构变成网状结构的交联过程。
硫化后的橡胶制品不仅能提高强度,还获得了优良的使用性能。
同时,硫化过程中应经常注意检查压力表、安全阀等安全装置,看其是否灵敏可靠。
此外,使用的脱模剂也是易燃物质,应妥善保管和使用,以防发生火灾。
橡胶硫化工艺介绍

橡胶硫化工艺介绍
硫化橡胶工艺是指将橡胶加工成制品的工艺。
硫化工艺又称为硫化反应,是橡胶加工中的一个重要环节。
硫化过程是一个化学过程,由各种因素如温度、时间和压力等控制,以获得所要求的制品性能。
在橡胶制品中,通常将含有其他助剂的聚合物制成的橡胶制品,经过一定时间后,可将其内部化学结构中的自由氨基转化为不饱和氨基,同时释放出一种称为“硫化剂”的化学物质。
经硫化后,该聚合物内的自由氨基被限制在分子内,形成分子内交联网络,从而使橡胶具有良好的弹性、耐磨性、耐屈挠性和抗老化性能等。
硫化胶生产中所使用的硫化剂主要有两种:一是含硫化合物(如硫磺、硫黄等);二是不含硫化合物(如白炭黑)。
不含硫化合物一般为其在硫化过程中提供硫源,而含硫化合物则在硫化过程中提供了交联网络所需的能量。
由于硫化剂可以通过加热使其分子中的自由氨基发生交联反应,因此在硫化过程中产生大量热和自由基,这不仅可提高硫化速度,而且能使橡胶制品具有良好的性能。
—— 1 —1 —。
电缆的硫化工艺
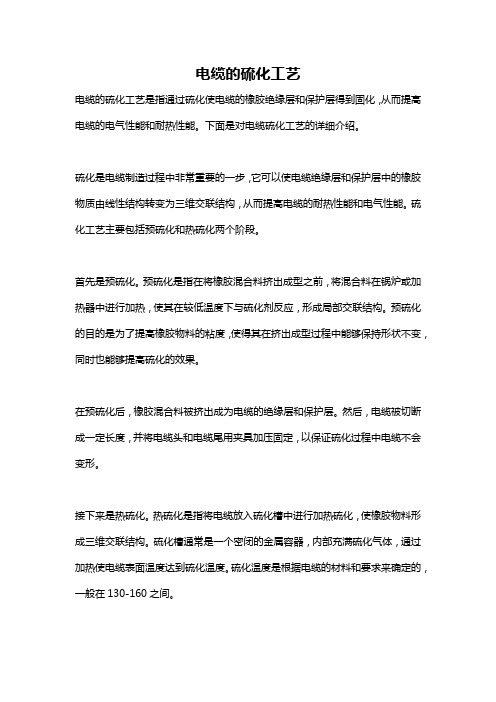
电缆的硫化工艺电缆的硫化工艺是指通过硫化使电缆的橡胶绝缘层和保护层得到固化,从而提高电缆的电气性能和耐热性能。
下面是对电缆硫化工艺的详细介绍。
硫化是电缆制造过程中非常重要的一步,它可以使电缆绝缘层和保护层中的橡胶物质由线性结构转变为三维交联结构,从而提高电缆的耐热性能和电气性能。
硫化工艺主要包括预硫化和热硫化两个阶段。
首先是预硫化。
预硫化是指在将橡胶混合料挤出成型之前,将混合料在锅炉或加热器中进行加热,使其在较低温度下与硫化剂反应,形成局部交联结构。
预硫化的目的是为了提高橡胶物料的粘度,使得其在挤出成型过程中能够保持形状不变,同时也能够提高硫化的效果。
在预硫化后,橡胶混合料被挤出成为电缆的绝缘层和保护层。
然后,电缆被切断成一定长度,并将电缆头和电缆尾用夹具加压固定,以保证硫化过程中电缆不会变形。
接下来是热硫化。
热硫化是指将电缆放入硫化槽中进行加热硫化,使橡胶物料形成三维交联结构。
硫化槽通常是一个密闭的金属容器,内部充满硫化气体,通过加热使电缆表面温度达到硫化温度。
硫化温度是根据电缆的材料和要求来确定的,一般在130-160之间。
在硫化槽中加热硫化过程中,硫化气体与橡胶表面的硫化剂发生反应,使橡胶物料形成交联结构。
硫化时间是根据电缆的尺寸和要求来确定的。
硫化时间一般为几小时到几十小时,甚至更长。
硫化后,电缆被取出硫化槽,在冷却室中冷却,使电缆表面温度降低。
冷却过程中,电缆的表面温度和内部温度逐渐均匀,从而形成一致的硫化结构。
最后,硫化后的电缆经过剥皮、成品检验等工序,完成整个制造过程。
硫化工艺的质量主要通过电缆的电气性能、耐热性能、机械性能等指标来评价。
总而言之,电缆的硫化工艺是通过预硫化和热硫化使电缆的橡胶物料形成三维交联结构,提高电缆的电气性能和耐热性能。
硫化工艺的实施需要控制好硫化温度、硫化时间等参数,以确保硫化质量。
硫化工艺的合理性和稳定性对电缆的质量和性能有着重要影响。
同时,硫化工艺也需要考虑环保和能源消耗等方面的要求,以实现电缆制造的可持续发展。
密封圈硫化工艺

密封圈硫化工艺密封圈硫化工艺密封圈是一种常见的密封元件,广泛应用于机械设备和工业装置中。
为了确保密封圈具有良好的密封性能和耐用性,密封圈硫化工艺被广泛采用。
本文将深入探讨密封圈硫化工艺的原理、步骤以及注意事项,并分享个人对该工艺的理解和观点。
1. 硫化工艺的原理密封圈硫化工艺是通过加热和氧化硫化特定材料以改变其物理和化学性质,使其具有较好的弹性和密封性能。
在硫化过程中,硫化剂与密封圈材料中的硫原子发生反应,从而形成交联结构,增强其弹性和耐化学性能。
2. 硫化工艺的步骤2.1 材料准备:选择合适的密封圈材料,根据具体需求确定硫化剂和其他辅助材料。
2.2 混炼:将密封圈材料与硫化剂以及其他辅助材料混合均匀,形成硫化混炼胶料。
2.3 成型:将硫化混炼胶料在模具中进行成型,通常采用挤出、压制或注塑等工艺。
2.4 压制:根据具体要求,对成型后的密封圈进行压制,以使其更好地与设备接触并确保较好的密封性。
2.5 硫化:将压制后的密封圈置于硫化炉中进行加热硫化处理。
硫化的温度和时间会根据材料的不同而有所变化,一般在硫化剂的指导下进行。
2.6 检验:对硫化后的密封圈进行外观检查、物理性能测试和尺寸测量等,确保其质量符合要求。
3. 注意事项3.1 材料选择:在硫化工艺中,密封圈材料的选择十分重要,需根据具体工作环境及介质进行合理的选材,以确保其密封性和耐用性。
3.2 硫化条件:硫化的温度和时间需要根据密封圈材料的特性进行合理的设定,过高或过低的硫化温度都可能对密封圈的性能产生负面影响。
3.3 工艺控制:在整个硫化工艺中,需要控制好各个步骤的工艺参数,以确保每个环节的质量可控和稳定,减少不良品的产生。
4. 个人观点和理解密封圈硫化工艺是一种重要的密封元件制造工艺,通过在材料内部形成交联结构,可以显著提高其密封性和耐用性。
在实际应用中,合理的材料选择和硫化条件的设定是确保密封圈质量的关键因素。
对工艺的严格控制和质量检验也是不可或缺的环节。
硫化工艺硫化氢产生量

硫化工艺硫化氢产生量
硫化工艺是橡胶加工中的重要环节,而硫化氢的产生量则是评估硫化工艺环保性能的重要指标。
本文将对硫化工艺中硫化氢的产生量进行专业分析,以期为相关领域提供参考。
一、硫化工艺简介
硫化工艺是橡胶加工中的重要环节,通过该工艺可以使橡胶分子链由线性结构转变为网状结构,从而提高橡胶的力学性能和使用寿命。
在硫化过程中,通常需要加入硫磺或含硫化合物,这些物质在高温下与橡胶分子发生反应,产生硫化氢等有害气体。
二、硫化氢的产生量
在硫化工艺中,硫化氢的产生量与多种因素有关,如原料橡胶的种类、配方、加工条件等。
一般来说,硫化氢的产生量取决于硫磺或含硫化合物的用量以及加工温度。
在常规的硫化工艺条件下,硫化氢的产生量通常在数毫克/克至数十毫克/克之间。
具体产生量还需根据实际生产条件而定。
三、硫化氢的危害与控制
硫化氢是一种有毒有害气体,长期接触会对人体健康造成危害,如头痛、恶心、呕吐等症状。
因此,控制硫化氢的产生量对于保障工人健康和环境安全具有重要意义。
在实际生产中,可通过优化原料配方、改进加工工艺、加强通风排风等措施来降低硫化氢的产生量。
同时,对于高浓度的硫化氢气体,应采取有效的吸收或回收措施,以减
少对环境的污染。
四、结论
本文对硫化工艺中硫化氢的产生量进行了专业分析。
在硫化工艺中,硫化氢的产生量取决于原料橡胶的种类、配方、加工条件等因素。
通过优化配方和改进工艺等措施可以有效降低硫化氢的产生量,保障工人健康和环境安全。
未来还需进一步研究新型环保型橡胶材料的开发与应用,以降低硫化工艺对环境的影响。
- 1、下载文档前请自行甄别文档内容的完整性,平台不提供额外的编辑、内容补充、找答案等附加服务。
- 2、"仅部分预览"的文档,不可在线预览部分如存在完整性等问题,可反馈申请退款(可完整预览的文档不适用该条件!)。
- 3、如文档侵犯您的权益,请联系客服反馈,我们会尽快为您处理(人工客服工作时间:9:00-18:30)。
橡胶生产工艺简介橡胶生产工艺简介1综述橡胶制品的主要原料是生胶、各种配合剂、以及作为骨架材料的纤维和金属材料,橡胶制品的基本生产工艺过程包括塑炼、混炼、压延、压出、成型、硫化6个基本工序。
橡胶的加工工艺过程主要是解决塑性和弹性矛盾的过程,通过各种加工手段,使得弹性的橡胶变成具有塑性的塑炼胶,在加入各种配合剂制成半成品,然后通过硫化是具有塑性的半成品又变成弹性高、物理机械性能好的橡胶制品。
2橡胶加工工艺2.1塑炼工艺生胶塑炼是通过机械应力、热、氧或加入某些化学试剂等方法,使生胶由强韧的弹性状态转变为柔软、便于加工的塑性状态的过程。
生胶塑炼的目的是降低它的弹性,增加可塑性,并获得适当的流动性,以满足混炼、亚衍、压出、成型、硫化以及胶浆制造、海绵胶制造等各种加工工艺过程的要求。
掌握好适当的塑炼可塑度,对橡胶制品的加工和成品质量是至关重要的。
在满足加工工艺要求的前提下应尽可能降低可塑度。
随着恒粘度橡胶、低粘度橡胶的出现,有的橡胶已经不需要塑炼而直接进行混炼。
在橡胶工业中,最常用的塑炼方法有机械塑炼法和化学塑炼法。
机械塑炼法所用的主要设备是开放式炼胶机、密闭式炼胶机和螺杆塑炼机。
化学塑炼法是在机械塑炼过程中加入化学药品来提高塑炼效果的方法。
开炼机塑炼时温度一般在80℃以下,属于低温机械混炼方法。
密炼机和螺杆混炼机的排胶温度在120℃以上,甚至高达160-180℃,属于高温机械混炼。
生胶在混炼之前需要预先经过烘胶、切胶、选胶和破胶等处理才能塑炼。
几种胶的塑炼特性:天然橡胶用开炼机塑炼时,辊筒温度为30-40℃,时间约为15-20min;采用密炼机塑炼当温度达到120℃以上时,时间约为3-5min。
丁苯橡胶的门尼粘度多在35-60之间,因此,丁苯橡胶也可不用塑炼,但是经过塑炼后可以提高配合机的分散性顺丁橡胶具有冷流性,缺乏塑炼效果。
顺丁胶的门尼粘度较低,可不用塑炼。
氯丁橡胶得塑性大,塑炼前可薄通3-5次,薄通温度在30-40℃。
乙丙橡胶的分子主链是饱和结构,塑炼难以引起分子的裂解,因此要选择门尼粘度低的品种而不用塑炼。
丁腈橡胶可塑度小,韧性大,塑炼时生热大。
开炼时要采用低温40℃以下、小辊距、低容量以及分段塑炼,这样可以收到较好的效果。
2.2混炼工艺混炼是指在炼胶机上将各种配合剂均匀的混到生胶种的过程。
混炼的质量是对胶料的进一步加工和成品的质量有着决定性的影响,即使配方很好的胶料,如果混炼不好,也就会出现配合剂分散不均,胶料可塑度过高或过低,易焦烧、喷霜等,使压延、压出、涂胶和硫化等工艺不能正常进行,而且还会导致制品性能下降。
混炼方法通常分为开炼机混炼和密炼机混炼两种。
这两种方法都是间歇式混炼,这是目前最广泛的方法。
开炼机的混合过程分为三个阶段,即包辊(加入生胶的软化阶段)、吃粉(加入粉剂的混合阶段)和翻炼(吃粉后使生胶和配合剂均达到均匀分散的阶段)。
开炼机混胶依胶料种类、用途、性能要求不同,工艺条件也不同。
混炼中要注意加胶量、加料顺序、辊距、辊温、混炼时间、辊筒的转速和速比等各种因素。
既不能混炼不足,又不能过炼。
密炼机混炼分为三个阶段,即湿润、分散和涅炼、密炼机混炼石在高温加压下进行的。
操作方法一般分为一段混炼法和两段混炼法。
一段混炼法是指经密炼机一次完成混炼,然后压片得混炼胶的方法。
他适用于全天然橡胶或掺有合成橡胶不超过50%的胶料,在一段混炼操作中,常采用分批逐步加料法,为使胶料不至于剧烈升高,一般采用慢速密炼机,也可以采用双速密炼机,加入硫磺时的温度必须低于100℃。
其加料顺序为生胶—小料—补强剂—填充剂—油类软化剂—排料—冷却—加硫磺及超促进剂。
两段混炼法是指两次通过密炼机混炼压片制成混炼胶的方法。
这种方法适用于合成橡胶含量超过50%得胶料,可以避免一段混炼法过程中混炼时间长、胶料温度高的缺点。
第一阶段混炼与一段混炼法一样,只是不加硫化和活性大的促进剂,一段混炼完后下片冷却,停放一定的时间,然后再进行第二段混炼。
混炼均匀后排料到压片机上再加硫化剂,翻炼后下片。
分段混炼法每次炼胶时间较短,混炼温度较低,配合剂分散更均匀,胶料质量高。
2.3压延工艺压延是将混炼胶在压延机上制成胶片或与骨架材料制成胶布半成品的工艺过程,它包括压片、贴合、压型和纺织物挂胶等作业。
压延工艺的主要设备是压延机,压延机一般由工作辊筒、机架、机座、传动装置、调速和调距装置、辊筒加热和冷却装置、润滑系统和紧急停车装置。
压延机的种类很多,工作辊筒有两个、三个、四个不等,排列形式两辊有立式和卧式;三辊有直立式、Γ型和三角形;四辊有Γ型、L型、Z型和S型等多种。
按工艺用途来分主要有压片压延机(用于压延胶片或纺织物贴胶,大多数三辊或四辊,各辊塑度不同)、擦胶压延机(用于纺织物的擦胶,三辊,各辊有一定得速比,中辊速度大。
借助速比擦入纺织物中)、通用压延机(又称万能压延机,兼有压片和擦胶功能、三辊或四辊,可调速比)、压型压延机、贴合压延机和钢丝压延机。
压延过程一般包括以下工序:混炼胶的预热和供胶;纺织物的导开和干燥(有时还有浸胶)胶料在四辊或三辊压延机上的压片或在纺织物上挂胶依机压延半成品的冷却、卷取、截断、放置等。
在进行压延前,需要对胶料和纺织物进行预加工,胶料进入压延机之前,需要先将其在热炼机上翻炼,这一工艺为热炼或称预热,其目的是提高胶料的混炼均匀性,进一步增加可塑性,提高温度,增大可塑性。
为了提高胶料和纺织物的粘合性能,保证压延质量,需要对织物进行烘干,含水率控制在1-2%,含水量低,织物变硬,压延中易损坏,含水量高,粘附力差。
几种常见的橡胶的压延性能天然橡胶热塑形大,收缩率小,压延容易,易粘附热辊,应控制各辊温差,以便胶片顺利转移;丁苯橡胶热塑性小,收缩率大,因此用于压延的胶料要充分塑炼。
由于丁苯橡胶对压延的热敏性很显著,压延温度应低于天然橡胶,各辊温差有高到低;氯丁橡胶在75-95℃易粘辊,难于压延,应使用低温法或高温法,压延要迅速冷却,掺有石蜡、硬酯酸可以减少粘辊现象;乙丙橡胶压延性能良好,可以在广泛的温度范围内连续操作,温度过低时胶料收缩性大,易产生气泡;丁腈橡胶热塑性小,收缩性大,在胶料种加入填充剂或软化剂可减少收缩率,当填充剂重量占生胶重量的50%以上时,才能得到表面光滑的胶片,丁腈橡胶粘性小易粘冷辊。
2.4压出工艺压出工艺是通过压出机机筒筒壁和螺杆件的作用,使胶料达到挤压和初步造型的目的,压出工艺也成为挤出工艺。
压出工艺的主要设备是压出机。
几种橡胶的压出特性:天然橡胶压出速度快,半成品收缩率小。
机身温度50-60℃,机头70-80℃,口型80-90℃;丁苯橡胶压出速度慢,压缩变形大,表面粗糙,机身温度50-70℃,机头温度70-80℃,口型温度100-105℃;氯丁橡胶压出前不用充分热炼,机身温度50℃,机头℃,口型70℃;乙丙橡胶压出速度快、收缩率小,机身温度60-70℃,机头温度80-130℃,口型90-140℃。
丁腈橡胶压出性能差,压出时应充分热炼。
机身温度50-60℃,机头温度70-80℃。
2.5注射工艺橡胶注射成型工艺是一种把胶料直接从机筒注入模性硫化的生产方法。
包括喂料、塑化、注射、保压、硫化、出模等几个过程。
注射硫化的最大特点是内层和外层得胶料温度比较均匀一致,硫化速度快,可加工大多数模压制品。
橡胶注射成型的设备是橡胶注射成型硫化机。
2.6压铸工艺压铸法又称为传递模法或移模法。
这种方法是将胶料装在压铸机的塞筒内,在加压下降胶料铸入模腔硫化。
与注射成型法相似。
如骨架油封等用此法生产溢边少,产品质量好。
2.7硫化工艺早先,天然橡胶的主要用途只是做擦字橡皮;后来才用于制造小橡胶管。
直到1823年,英国化学家麦金托什才发明将橡胶溶解在煤焦油中然后涂在布上做成防水布,可以用来制造雨衣和雨靴。
但是,这种雨衣和雨靴一到夏天就熔化,一到冬天便变得又硬又脆。
为了克服这一缺点,当时许多人都在想办法。
美国发明家查理•古德伊尔也在进行橡胶改性的试验,他把天然橡胶和硫黄放在一起加热,希望能获得一种一年四季在所有温度下都保持干燥且富有弹性的物质。
直到1839年2月他才获得成功。
一天他把橡胶、硫黄和松节油混溶在一起倒入锅中(硫黄仅是用来染色的),不小心锅中的混合物溅到了灼热的火炉上。
令他吃惊的是,混合物落入火中后并未熔化,而是保持原样被烧焦了,炉中残留的未完全烧焦的混合物则富有弹性。
他把溅上去的东西从炉子上剥了下来,这才发现他已经制备了他想要的有弹性的橡胶。
经过不断改进,他终于在1844年发明了橡胶硫化技术。
在橡胶制品生产过程中,硫化是最后一道加工工序。
硫化是胶料在一定条件下,橡胶大分子由线型结构转变为网状结构的交联过程。
硫化方法有冷硫化、室温硫化和热硫化三种。
大多数橡胶制品采用热硫化。
热硫化的设备有硫化罐、平板硫化机等。
2.8其他生产工艺橡胶制品的生产工艺还有浸渍法、涂刮法、喷涂法、蕉塑法等。
3橡胶配方设计3.1橡胶的硫化(交联)交联是橡胶高弹性的基础,其特点是在一个橡胶分子链上仅形成少数几处交联点,因此不会影响橡胶分子链段的运动。
橡胶的硫化体系较多,常见的有:硫黄硫化体系、过氧化物硫化体系、树脂硫化体系、氧化物硫化体系等3.1.1硫黄硫化体系主要适应于二烯类橡胶,其硫化活性点是在双键旁边的α氢原子。
组成:硫黄⌝活性剂:氧化锌,硬脂酸⌝⌝促进剂:噻唑类(DM,M),次磺酰胺类(CZ,NOBS),秋兰姆类(TETD,TMTM,TMTD),胍(D)图 1 硫黄硫化体系的结构特点表1硫黄硫化体系分类硫化体系硫黄/促进剂(S/A)比交联键组成性能特点普通硫黄硫化体系>1 以多硫键为主动态疲劳性能好;老化性能差半有效硫黄硫化体系(Semi-EV)≈1 以单硫键和双硫键为主老化性能好;压缩永久变形小;无硫化返原有效硫黄硫化体系(EV)<<13.1.2过氧化物硫化体系-自由基机理1 常见的过氧化物有:DCP(二枯基过氧化物)、BPO、DCBP、双2,52 助交联剂:抑制聚合难自由基无用的副反应。
如TAIC,TAC,HVA-23 过氧化物硫化橡胶性能特点:老化性能好,压缩永久变形小,制品透明性好。
表 2 过氧化物的交联效率橡胶品种交联效率原因NR 1 自由基的活性主要与甲基的超共轭作用有关,同时位阻较大,无法出笼格BR,SBR 10-50 脱氢的速度为NR的1/3,但活性高,位阻小,能较快地与双键加成,形成交联键和新自由基NBR >1 腈基影响交联作用PE,EPDM 1EPR 0.4IIR 03.1.3氧化物硫化体系这是含卤素橡胶的主要硫化剂。
通常有氧化锌/氧化镁(5/4)、氧化铅或四氧化三铅(10-20,耐水制品)3.2橡胶的填料未加填料的橡胶,力学性能和工艺性能均较差,无法使用。