悬臂支架铸造工艺设计说明书
铸造工艺设计说明书

铸造⼯艺设计说明书铸造⼯艺设计说明书课程设计:机械⼯艺课程设计设计题⽬:底座铸造⼯艺设计班级:机⾃1103设计⼈:学号:指导教师:张锁梅、贾志新前⾔学⽣通过设计能获得综合运⽤过去所学过的全部课程进⾏机械制造⼯艺及结构设计的基本能⼒,为以后做好毕业设计、⾛上⼯作岗位进⾏⼀次综合训练和准备。
它要求学⽣全⾯地综合运⽤本课程及有关选修课程的理论和实践知识,进⾏零件加⼯⼯艺规程的设计和机床夹具的设计。
其⽬的是:(1)培养学⽣综合运⽤机械制造⼯程原理课程及专业课程的理论知识,结合⾦⼯实习、⽣产实习中学到的实践知识,独⽴地分析和解决机械加⼯⼯艺问题,初步具备设计中等复杂程度零件⼯艺规程的能⼒。
(2)培养学⽣能根据被加⼯零件的技术要求,运⽤夹具设计的基本原理和⽅法,学会拟订夹具设计⽅案,完成夹具结构设计,进⼀步提⾼结构设计能⼒。
(3)培养学⽣熟悉并运⽤有关⼿册、图表、规范等有关技术资料的能⼒。
(4)进⼀步培养学⽣识图、制图、运算和编写技术⽂件的基本技能。
(5)培养学⽣独⽴思考和独⽴⼯作的能⼒,为毕业后⾛向社会从事相关技术⼯作打下良好的基础。
⽬录⼀、⼯艺审核 (1)1.数量与材料 (1)2.图样 (1)3.零件的结构性 (1)⼆、成形⼯艺设计 (1)1.确定⼯艺⽅案 (1)(1)浇注位置的选择 (2)(2)分型⾯的选择 (2)2.确定铸造⼯艺参数 (4)(1)机械加⼯余量和铸出孔 (4)(2)浇注位置的选择 (5)(3)拔模斜度 (5)(4)铸造收缩率 (6)3.砂芯设计 (6)4.浇注系统的设计 (6)5. 冷铁的设置 (6)三、⼼得体会 (7)⼀、⼯艺审核1、数量与材料由零件图可知,该零件结构⽐较简单,但是形状不是很规则,⼯作条件⼀般以承受压⼒为主,故要求该零件有良好的刚性和强度。
另外,根据零件图的要求,该底座零件为单件⼩批量⽣产,另外材料选⽤灰铸铁HT200,流动性较好,适于铸造。
2、图样该零件图给出了主视图、左视图、俯视图3个视图。
支架零件铸造工艺设计说明书

支架零件铸造工艺设计一、零件的生产条件、结构及技术要求1、生产性质:大批量生产2、材料:HT2003、零件加工方法:零件上有多个孔,除中间的大孔需要铸造以外,其他孔在考虑加工余量后不宜铸造成型,采用机械方法加工,均不铸出。
造型方法:机器造型;造芯方法:机器制芯4、主要技术要求:满足HT200的机械性能要求,去毛刺及锐边,铸件表面不允取有缺陷。
二、零件图及立体图结构分析1、零件图如下:零件主视图零件俯视图2、立体图如下:三、工艺设计过程1、铸造工艺设计方法及分析(1)铸件壁厚为了避免浇不到、冷隔等缺陷,铸件不应太薄。
铸件的最小允许壁厚与铸造的流动性密切相关。
在普通砂型铸造的条件下,铸件最小允许壁厚见表1。
表1. 铸件最小允许壁厚查得灰铁铸件在100~200mm的轮廓尺寸下,最小允许壁厚为5~6mm。
由零件图可知,零件中不存在壁厚小于设计要求的结构,在设计过程中,也没有出现壁厚小于最小壁厚要求的情况。
(2)造型、制芯方法造型方法:该零件需批量生产,为中小型铸件,因此,采用湿型粘土砂机器造型,模样采用金属模,采用技术先进的机器造型。
制芯方法:在造芯用料及方法选择中,如用粘土砂制作砂芯原料成本较低,但是烘干后容易产生裂纹,容易变形。
在大批量生产的条件下,由于需要提高造芯效率,且常要求砂芯具有高的尺寸精度,此工艺所需的砂芯采用热芯盒法生产砂芯,以增加其强度及保证铸件质量。
选择使用射芯工艺生产砂芯。
采用热芯盒制芯工艺热芯盒法制芯,是用液态固性树脂粘结剂和催化剂制成的一种芯砂,填入加热到一定的芯盒内,贴近芯盒表面的砂芯受热,其粘结剂在很短的时间内硬化。
而且只要砂芯表层有数毫米的硬壳即可自芯取出,中心部分的砂芯利用余热可自行硬化。
(3)砂箱中铸件数目的确定及排布初步确定一箱中放几个铸件,作为进行浇冒口设计的依据。
一箱中的铸件数目,应该是在保证铸件质量的前提下越多越好。
本铸件在一砂箱中高约130mm,长约200mm,宽约110mm,体积约99.7cm^3,密度7.2g/cm^3,重约0.8Kg。
机械制造工艺课程设计--支架设计说明书

机械制造工艺学课程设计说明书题目:设计“支架”零件的机械加工工艺规程(大批生产)院、系别机电工程学院班级2012级机械设计制造及其自动化(2)班姓名xxx学号xxxxxxxxxxxx指导老师邓志勇三明学院2015 年 3 月 8日目录机械制造工艺学课程设计任务书 (1)1、序言………………………………………..…………………….……..………...22、课程设计的目的 (2)3、支架工艺设计分析 (2)3.1确定毛坯的成形方法 (2)3.2确定铸造工艺方案 (2)4、支架机械加工工艺路线的制定 (2)4.1定位基准的选择 (3)4.2拟定工艺路线 (5)4.3加工余量和工序尺寸的拟定 (12)5、总结 (40)参考文献 (4)1机械制造工艺学课程设计任务书设计题目:设计“支架”零件的机械加工工艺规程(大批生产)设计要求: 1.表面处理:发蓝2.锐边倒角设计容: 1.熟悉零件图2.绘制零件图(1)3.绘制毛坯图(1)4.编写工艺过程综合卡片(1)5.工序卡片(7)6.课程设计说明书(1份)2015年 3月13日1、序言机械制造工艺学课程设计是我们机械累专业的主干课程。
容覆盖了金属切削原理、刀具、机械加工工艺及设备、测量技术等,是一门实践性和综合性的课程。
本着力求与生产实际相结合的指导思想,本次课程设计达到了综合运用基本理论知识,解决实际生产问题的目的。
2、课程设计的目的机械基础课程设计旨在在理论基础上让学生进行一次机械加工工艺规程和典型夹具设计的锻炼,对所学知识的加深和巩固。
通过设计提高学生的学习能力,熟悉机械设计工艺手册、图表和技术资料,特别是熟悉机械加工工艺规程和夹具设计的知识,理论结合实际。
3、支架工艺设计分析3.1 支架的结构及其工艺分析支架零件图零件毛坯图由支架的零件图可知,结构性相对对称布置。
该支架的主要技术要求:1、表面处理:发蓝;2、锐边倒角;3、未标注表面粗糙度6.3um。
3.2 确定铸造工艺方案3.2.1铸造方法的选择查表得知此为大批生产,在毛培的制造方法和加工余量、机床设备、夹具及尺寸保证、刀具、生产率、成本等各方面因素,根据零件的尺寸较大,形状比较复杂,而且选用灰铸铁为材料,选用熔模铸造,毛培形状可以与零件形状尽量接近。
支座铸造课程设计说明书

摘要支座铸造工艺设计其实是对金属零件的铸造工艺分析、铸造工艺方案拟定、铸造工艺文件制定等的综合考察。
同时也在其中让我们学习绘制铸造工艺图、铸型图、铸件图等。
这既考察我们对CAD的运用,也让我们了解图形的绘制步骤及要求。
铸造生产通常是指用熔融的合金材料制作产品的方法,将液态合金注人预先制备好的铸型中使之冷却、凝固,而获得毛坯或零件,这种制造过程称为铸造生产,简称铸造,所铸出的产品称为铸件。
大多数铸件作为毛坯,需要经过机械加工后才能成为各种机器零件;有的铸件当达到使用的尺寸精度和表面粗糙度要求时,可作为成品或零件直接应用。
铸造是将金属炼成符合一定要求的液体并里,经冷却凝固,清除处理后得到预定形状、尺寸和性能的铸件工艺过程,铸件毛坯因近乎成形而达到免机械加工或少量加工的目的,降低了成本并在一定程度上减少了时间。
铸造是现代机械制造工业的基础之一。
铸造种类很多,按造型方法习惯上分为:普通砂型铸造和特种铸造。
铸造工艺通常包括铸型准备,铸造金属的溶化与浇注,铸件处理和检验。
关键词:铸造,铸型,浇注目录第1章选材 (3)1.1材料的选择 (3)第2章零件铸造工艺方案的确定 (3)2.1 支座生产要求、结构及技术要求 (3)2.2铸造工艺方法的确定 (4)2.3支座结构的铸造工艺性 (4)2.4造型,造芯方法的选择 (5)2.5分型方案的确定 (5)第3章铸造工艺方案参数的确定 (7)3.1 工艺设计参数确定 (7)3.2铸造收缩率 (7)3.3切削加工余量 (7)3.4铸件尺寸公差 (7)3.5 起模斜度及圆角 (8)第4章浇注系统设置 (8)4.1 浇注系统的作用 (8)4.2浇注位置的确定 (8)4.3浇冒口设置方案 (9)4.4浇冒口尺寸 (9)第5章铸造工艺图绘制 (10)第6章铸造工艺卡绘制 (11)总结 (12)致谢 (13)参考文献 (14)第1章选材1.1材料的选择铸造毛坯适用于不宜用型材作坯料的场合,例如当零件形状很复杂或呈流线型外形时,若在用型材制坯,不仅成形困难而需增加设备及模具费用,还需增加许多切削加工余量,从而增加材料耗费和加工费。
QT700-2机体支架铸造作业指导书

QT450-10树脂砂手工造型作业指导书编号:持有人:BH3,GC03-20082 QT450-10树脂砂手工造型作业指导书1 范围本规程适用于采用树脂砂手工造型生产的QT450-10材质类铸件。
2 型(芯)砂制备2.1原材料准备1、普通湿型用砂:SiO2≥90%,泥份≦2%,粒度75/150、100/200。
2、粘土技术条件:不得结块,受潮。
3、煤粉技术条件:光泽碳析出能力≥7%,挥发份≥30%,无大颗粒,结块现象。
2.2 型砂混制1、配砂前首先检查设备(混砂机)是否正常,润滑是否足够,电器是否安全,出砂门是否开关灵活关闭严密。
2、混砂机碾轮与底盘的间隙10-30毫米,内外刮刀与底盘的间隙<10毫米。
3、检查配所用材料是否全部备齐,是否符合技术要求,并估算所需配砂的用量。
4、加料顺序如下:普通湿型:新砂→旧砂→粘土(煤粉) →水;干混2—3分钟,湿混3—5分钟。
5、先开混砂机后加料,所加混合料不得超过混砂机的额定混砂量。
6、混砂过程中不准用手在机内直接取样。
2.3 型(芯)砂的质量控制:紧实率控制在50%左右,可凭手感检测,用手捏一把型(芯)砂,感到有潮的感觉但不粘手,柔軟易变形,捏成砂团放开手后可看到清晰的手纹,掰断时断面不粉碎,有足够的强度。
面砂的有效煤粉含量一般控制在3—8%,小件取下限,大件取上限,以铸件不粘砂,不出现铸件表面发蓝为好。
型砂中的活性粘土的含量一般控制在5—9%,不可过高或过低。
3 手工造型3.1 造型前的准备3.1.1 操作者应了解所生产铸件的工艺要求。
3.1.2 检查模样是否完好,有下列情况者应修复后再用:a) 缺角,变形及尺寸不符合图纸规定。
b) 活块残缺不全。
BH3,GC03--2003c) 模样的定位销,孔配合松紧不合适。
3.1.3 需用底板时,检查底板是否平直,大小是否符合要求。
3.1.4 选择的砂箱吃砂量是否符合要求,吃砂量可参照表3.1.4 。
表3.1.4 砂箱吃砂量表(mm)3.1.5 砂箱有下列情况不能使用:a)箱把脱落或有严重变形。
推荐-铸造工艺课程设计说明书29页 精品
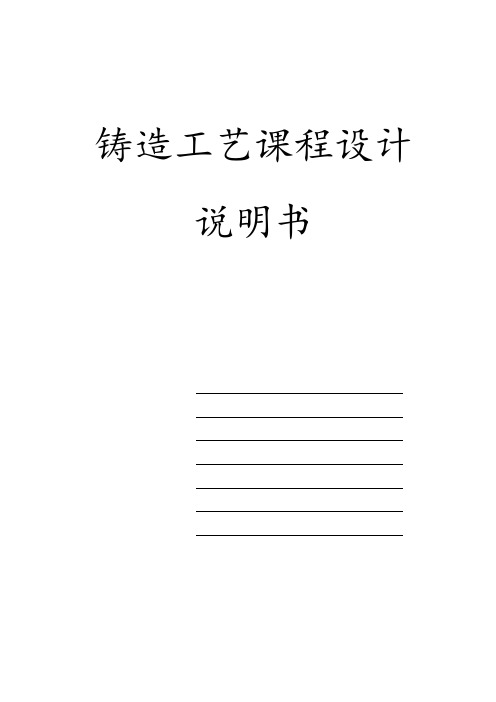
铸造工艺课程设计说明书目录1 前言 (3)1.1本设计的意义 (3)1.1.1 本设计的目的 (3)1.1.2 本设计的意义 (3)1.2本设计的技术要求 (4)1.3本课题的发展现状 (4)1.4本领域存在的问题 (4)1.5本设计的指导思想 (5)1.6本设计拟解决的关键问题 (5)2 设计方案 (5)2.1零件的材质分析 (6)2.2支座工艺设计的内容和要求 (7)2.3造型造芯方法的选择 (9)2.4浇注位置的选择与分型面的选择 (9)2.4.1 浇注位置的选择 (9)2.4.2 分型面的确定 (11)2.4.3 砂箱中铸件数目的确定 (13)3 设计说明 (14)3.1工艺设计参数确定 (14)3.1.1 最小铸出的孔和槽 (14)3.1.2 铸件的尺寸公差 (15)3.1.3 机械加工余量 (16)3.2铸造收缩率 (16)3.2.1 起模斜度 (17)3.2.2 浇注温度和冷却时间 (18)3.3砂芯设计 (18)3.3.1芯头的设计 (19)3.3.2 砂芯的定位结构 (19)3.3.3 芯骨设计 (20)3.3.4 砂芯的排气 (20)3.4浇注系统及冒口,冷铁,出气孔的设计 (20)3.4.1 浇注系统的类型和应用范围 (20)3.4.2 确定内浇道在铸件上的位置、数目、金属引入方向 (20)3.5决定直浇道的位置和高度 (21)3.5.1计算内浇道截面积 (21)3.5.2计算横浇道截面积 (22)3.5.3计算直浇道截面积 (23)3.5.4 冒口的设计 (23)4 铸造工艺装备设计 (24)4.1模样的设计 (24)4.1.1 模样材料的选用 (24)4.1.2 金属模样尺寸的确定 (25)4.1.3 壁厚与加强筋的设计 (25)4.1.4 金属模样的技术要求 (25)4.1.5 金属模样的生产方法 (25)4.2模板的设计 (25)4.2.1 模底板材料的选用 (26)4.2.2 模底板尺寸确定 (26)4.2.3 模底板与砂箱的定位 (26)4.3芯盒的设计 (26)4.3.1 芯盒的类型和材质 (26)4.3.2 芯盒的结构设计 (26)4.4砂箱的设计 (26)4.4.1 砂箱的材质及尺寸 (26)5 结论........................................................................................................ 错误!未定义书签。
一种汽车悬置支架挤压铸造工艺技术

一种汽车悬置支架挤压铸造工艺技术汽车悬置支架挤压铸造工艺技术是一种常见于汽车制造业的生产工艺,它通过将熔化的金属材料注入模具中,然后施加压力使其充分填充模具腔体,最终得到所需形状的零件。
本文将详细介绍汽车悬置支架挤压铸造工艺技术的原理、过程和优势。
一、工艺原理汽车悬置支架挤压铸造工艺技术是一种将熔化的金属材料通过机械力作用,使其在模具腔体中充分填充并形成所需形状的工艺。
其主要原理是利用压力将金属材料推动至模具腔体内,同时通过模具的几何形状使金属材料在充填过程中发生塑性变形,最终形成所需的汽车悬置支架。
二、工艺过程汽车悬置支架挤压铸造工艺技术的过程主要可以分为以下几个步骤:1. 材料准备:选择适合的金属材料,并按照一定的比例将其熔化。
通常使用的金属材料有铝合金、镁合金等。
2. 模具设计与制造:根据悬置支架的设计要求,设计合适的模具,并制造出模具。
3. 模具预热:将制造好的模具进行预热处理,以保证在注入熔化金属材料时能够保持合适的温度,避免出现冷热断裂等问题。
4. 注入金属材料:将熔化的金属材料注入至预热好的模具中,并施加一定的压力,使其充分填充模具腔体。
5. 冷却与固化:待金属材料充填完成后,模具中的金属材料开始冷却,并逐渐固化成为所需的形状。
6. 反压与脱模:在金属材料冷却固化之后,通过一定的反压作用,将悬置支架从模具中取出。
7. 修整与加工:取出的悬置支架经过修整与加工,去除多余的材料,并进行必要的加工处理,以达到最终的要求。
三、工艺优势汽车悬置支架挤压铸造工艺技术相比于其他传统的铸造工艺具有以下优势:1. 成型精度高:挤压铸造工艺能够通过模具的设计与加工,实现对悬置支架的高精度成型,保证其尺寸和形状的准确性。
2. 生产效率高:挤压铸造工艺具有高度自动化和连续化的特点,能够实现大规模生产,并且生产效率高,有利于降低制造成本。
3. 材料利用率高:挤压铸造工艺可以有效控制金属材料的用量,并且通过模具的设计,减少废料的产生,提高材料利用率。
铸态QT800—5悬挂支架铸件的研制

i n o c u l a t i o n a n d c o n c o mi t a n t wi t h t h e l f o w i n o c u l a t i o n . ( 4) T h e c h e mi c a l c o mp o s i t i o n o f n o d u l a r i r o n l i q u i d wa s c o n t r o l l e d a s
( C) 3 . 6 %~ 3 . 8 %, w ( S i ) 2 . 5 %~ 2 . 8 %, ( Mn )0 . 2 5 % 0 . 4 5 %, ( S ) < 0 . 0 2 %, 鲫( P ) < O . 0 3 %, W ( C u )0 . 2 %~ 0 . 4 %, W ( Mo ) 0 . 1 %一
Z HANG J u n, W ANG J i n — f e i , Z HE NG Ya n — b i a o , L I Z h i — h u a , S UN J i n - mi n g , T AO Ha n — d e
( Hu b e i Me c h a n i c a l a n d E l e c t i r c a l R e s e a r c h a n d D e s i g n I n s t i t u t e C o . , L t d . , Wu h a n 4 3 0 0 7 0 , C h i n a )
( Mn ) 0 . 2 5 %~ 0 . 4 5 %, 协 ( s ) < 0 . 0 2 %, ( P ) < 0 . 0 3 %, w ( C u ) 0 . 2 % 0 . 4 %, w ( Mo ) 0 . 1 %~ 0 . 3 %, w( S b ) 0 . 0 1 %~ 0 . 0 2 %。试验结果表
支架铸造课程设计说明书

南昌航空大学铸造工艺专业课程设计题目:支架铸造工艺设计院系:航空制造工程学院专业:材料成型及控制工程学号: 09033104姓名:石婷指导老师:戴斌煜日期: 2012年11月30日目录1设计任务的分析 (1)铸件的结构特点 (1)铸件的材料及性能 (1)2铸造工艺方案的确定 (1)铸件在金属型中的位置 (1)铸件的凝固顺序 (2)浇注位置与分型面的选择 (2)2.3.1浇注位置的选择 (2)2.3.2分型面的选择 (2)铸造工艺参数的确定 (3)浇注系统类型的形式 (3)熔化与浇注 (5)3浇注系统的计算 (6)浇注时间的确定 (6)浇注系统截面积计算 (6)冒口设计计算 (7)4金属型的设计 (7)金属型设计 (7)4.1.1 金属型类型 (7)4.1.2主要结构形式 (7)4.1.3金属型壁厚 (7)4.1.4型腔尺寸计算 (8)4.1.5刚度强度 (8)4.1.6耐用性 (8)4.1.7 标准 (9)4.1.8其他尺寸要求 (9)4.1.10型腔的排气 (9)锁紧机构 (9)金属模材质选择 (9)5.铸造工艺 (10)金属型的准备 (10)5.1.1金属型的清理 (10)5.1.2金属型的涂料 (10)5.1.3金属型的预热 (10)浇注温度和速度 (10)参考文献 (11)设计总结 (13)1设计任务的分析铸件的结构特点铸件为支架,最大尺寸280mm,属小型铸件,支架基本壁厚为5mm,最大壁厚为18mm,有三个直径为11mm的孔,可采用机加工方法得到,不铸出。
有四个内凹空腔。
铸件的材料及性能材料为ZL201-T4,铸造铝铜合金,属Al-Mn-Cu-Ti合金,抗拉强度295MPa,硬度HB70,密度2.78g/cm³,熔化温度548-650℃。
(GB/T1173-1995)铸件的技术要求机加工余量:铸件最大尺寸为280mm,所以铸件机加工等级为D-F,D-1.3mm,E-1.4mm (GB/T 6414-1999)工艺余量:铸件支架壁厚5mm,设置冒口及高于铸件的浇口,作为充填铸型所必需的重力和补缩之用,作为工艺余量。
悬架毕业设计说明书

摘要本论文应用所学专业理论课程和生产实际知识进行了冲压模具设计工作的实际训练,从而培养和提高自己独立工作能力,巩固与扩充了冲压模具设计等课程所学的内容。
本设计为悬架冲压工艺分析与模具设计,在落料、拉深的基础上采用冲孔单工序模,对悬架进行冲孔。
冲裁效果好,能极大地提高生产效率。
本设计主要工序为:冲孔。
本设计分别论述了产品工艺分析,冲压方案的确定,工艺计算,模板及主要零件设计,模具装配等问题。
本设计的内容主要是确定单工序内型模和结构形式以及工艺性,绘制模具总图和主要工作零件图并画出Pro/E三维实体图。
关键词:悬架冲压工艺冲孔模具设计Pro/E三维实体图ABSTRACTThis paper apply their professional theory course and actual production knowledge stamping mould design work of the actual training, thus cultivating and improving students' ability to work independently, consolidated and expanded stamping mould design the contents of such lessons. This design USES the blanking punching composite modulus, mould design and manufacture is simple. Blanking effect is good, can greatly improve the production efficiency. This design for suspension stamping process analysis and mold design. In blanking, drawings on the basis of punching die single working procedure, the suspension for punching. Cutting effect is good, can greatly improve the production efficiency. The main process of this design is punching. This paper discusses the design product process analysis and determination of the stamping scheme, process calculation, template and main parts design, mold assembly, etc.This design is to determine the content of the single process mould structure form and in technology and drawing mould assembly drawing the main parts figure and the Pro/e three dimensional figure.Keywords:suspension stamping process punching mould design Pro/e three dimensional figure目录摘要 (I)ABSTRACT (II)第1章概述 (1)1.1冲压的概念特点及应用 (2)1.2冲压的基本工序及模具 (2)1.3国内冲压模具业发展现状 (3)1.4国内冲压模具制造技术发展趋势 (4)1.5课题来源、目的及意义 (6)第2章模具工艺分析及工艺方案 (7)2.1产品零件图 (7)2.2工件工艺分析 (8)2.3工艺方案及模具结构类型 (8)第3章模具设计 (9)3.1工艺方案及模具结构类型 (9)3.2计算冲孔力 (9)3.3计算压力中心 (9)第4章模具零、部件结构设计 (11)4.1模具总体设计 (11)4.1.1冲模的结构分类 (11)4.1.2模具的结构形式 (12)4.1.3 模具构成 (13)4.2凸、凹模结构设计 (18)4.2.1凸模 (18)4.2.2凹模 (20)4.2.3凸、凹模工作尺寸计算 (23)4.3定位形式与结构设计 (24)4.3.1设计原则 (24)4.3.2挡料销 (24)4.4安装和有关零、部件 (25)4.4.1结构件与安装 (25)4.4.2紧固件选用 (27)4.4.3 模具自制零件的材料及热处理要求 (28)第5章压力机的选用与校核 (29)5.1压力机的选用原则 (29)5.2压力机的选取 (30)第6章模具装配 (32)第7章三维图设计 (35)7.1凸模垫板的设计 (35)7.2三维图的装配 (36)第8章结论 (41)参考文献 (42)附录 (43)致谢 (45)第1章概述模具是大批量生产同形产品的工具,是工业生产的主要工艺设备。
(完整word版)铸造工艺课程设计说明书

铸造工艺课程设计说明书目录1 前言 (4)1。
1本设计的意义 (4)1.1.1 本设计的目的 (4)1.1。
2 本设计的意义 (5)1.2本设计的技术要求 (5)1。
3本课题的发展现状 (5)1.4本领域存在的问题 (6)1.5本设计的指导思想 (6)1。
6本设计拟解决的关键问题 (7)2 设计方案 (7)2。
1零件的材质分析 (8)2.2支座工艺设计的内容和要求 (9)2.3造型造芯方法的选择 (11)2。
4浇注位置的选择与分型面的选择 (12)2。
4.1 浇注位置的选择 (12)2.4.2 分型面的确定 (14)2.4.3 砂箱中铸件数目的确定 (15)3 设计说明 (17)3。
1工艺设计参数确定 (17)3。
1.1 最小铸出的孔和槽 (17)3.1.2 铸件的尺寸公差 (18)3。
1.3 机械加工余量 (19)3。
2铸造收缩率 (19)3。
2。
1 起模斜度 (20)3.2。
2 浇注温度和冷却时间 (21)3。
3砂芯设计 (22)3.3。
1 芯头的设计 (22)3。
3。
2 砂芯的定位结构 (23)3。
3.3 芯骨设计 (23)3.3.4 砂芯的排气 (23)3。
4浇注系统及冒口,冷铁,出气孔的设计 (24)3。
4.1 浇注系统的类型和应用范围 (24)3。
4。
2 确定内浇道在铸件上的位置、数目、金属引入方向 (24)3.5决定直浇道的位置和高度 (25)3.5.1 计算内浇道截面积 (25)3.5.2 计算横浇道截面积 (26)3。
5。
3 计算直浇道截面积 (27)3。
5.4 冒口的设计 (27)4 铸造工艺装备设计 (28)4。
1模样的设计 (28)4。
1.1 模样材料的选用 (28)4.1。
2 金属模样尺寸的确定 (29)4。
1。
3 壁厚与加强筋的设计 (29)4。
1。
4 金属模样的技术要求 (29)4.1。
5 金属模样的生产方法 (29)4.2模板的设计 (30)4。
2。
1 模底板材料的选用 (30)4.2。
模具支架铸造工艺设计说明书
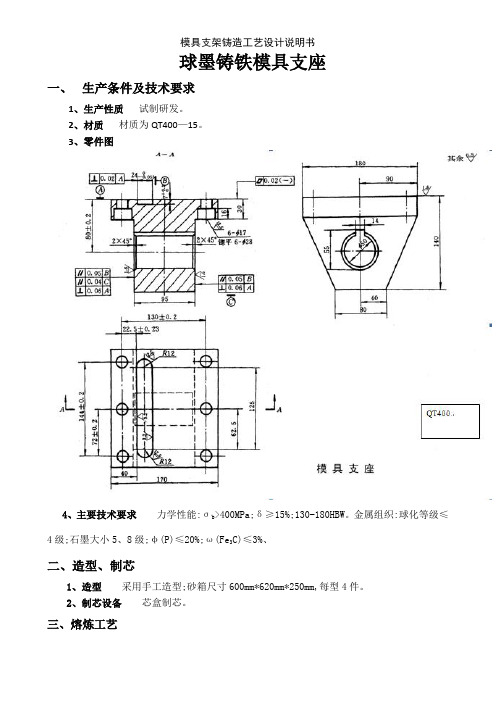
球墨铸铁模具支座一、生产条件及技术要求1、生产性质试制研发。
2、材质材质为QT400—15。
3、零件图4、主要技术要求力学性能:σb>400MPa;δ≥15%;130-180HBW。
金属组织:球化等级≤4级;石墨大小5、8级;φ(P)≤20%;ω(Fe3C)≤3%、二、造型、制芯1、造型采用手工造型;砂箱尺寸600mm*620mm*250mm,每型4件。
2、制芯设备芯盒制芯。
三、熔炼工艺1、铁液的化学成分ω(C)=3、6%-3、9%;ω(Si) ≤3、0%;ω(Mn)<0、5%;=0、03%-0、05%;ω(P) ≤0、07%;ω(S)<0、03%;ω(Mg)残=0、01%-0、03%。
ω(Re)残2、球化剂稀土镁硅铁合金,加入量为铁液质量分数的1、5%-1、7%。
3、出炉温度 1420-1440℃。
4、浇注温度 1320-1380℃。
5、孕育剂 75Si-Fe合金孕育,加入量为包内铁液质量分数的0、3%-0、7%。
6、熔炼设备0、5t无芯工频感应电炉熔炼原铁液;在100Kg铁液包中进行球化处理;转50Kg浇包进行浇注。
四、主要工艺参数1、加工余量 2-3mm,模具支座面机械加工余量取3mm;模具支座底面及侧面机械加工余量取2mm。
2、收缩率 1%。
3、拔模斜度 1°。
4、砂型硬度砂型硬度大于40(C型硬度计)。
5、吃砂量吃砂量为30-60mm。
6、型砂性能湿压强度为0、12-0、14MPa,透气性≥100cm2/(Pa*s),紧实率为40%-48%(夏季),41%-47%(冬季)。
7、铸造圆角铸造圆角为R2。
五、铸造工艺方案1、浇注位置及分型面的选择由于本铸件采用试制研发的方案进行设计,其可能的分型面的选取有如下图所示的6种:但就是,根据分析及铸件实际分型面的选取原则,我们不难发现方案3、4、5就是根本无法起模的,故应舍弃;再由于方案2不能很好的保证铸件孔的同轴度,且容易发生错型、不易合箱,故也应舍弃;方案1使得大部分铸件都处在下型,且能很好的保证铸件孔的同轴度及圆度;方案6下芯方便,上下模样相同;故最终,确定方案1与方案6为本铸件的可行分型面选择方案。
支架 工艺设计说明书 2

BE50注射支架的机械加工工艺及工装设计设计说明书姓名:白广贺学号:201000163002指导教师:李凯岭山东大学机械工程学院2013年10月——2013年12月目录一、设计任务 (3)二、零件分析 (3)(一)零件的生产纲领及生产类型 (3)(二)零件的类型及功用 (3)(三)零件的结构分析 (3)(四)零件主要技术条件及技术关键问题 (3)二、工艺规程设计 (4)(一)确定毛坯制造的形式................................................................. 错误!未定义书签。
(二)定位基准的选择......................................................................... 错误!未定义书签。
1、粗基准的选择................................................................................... 错误!未定义书签。
2、精基准的选择................................................................................... 错误!未定义书签。
(三)零件各个加工表面加工方法的选择......................................... 错误!未定义书签。
(四)制定工艺路线............................................................................. 错误!未定义书签。
三、确定机械加工余量及毛坯尺寸 (7)(一)机械加工余量 (7)(二)确定毛坯尺寸及公差 (8)(三)确定锻造圆角半径 (9)(四)确定拔模角 (9)(五)确定分模线位置 (9)四、工序设计 (9)(一)选择加工设备与工艺装备 (9)1、机床 (9)2、夹具 (10)3、刀具 (10)4、量具 (10)(二)确定工序尺寸 (10)1、确定圆柱面的工序尺寸 (11)2、确定两侧面加工的工序尺寸 (12)3、确定铣前面加工的工序尺寸 (13)五、确定工时 (13)(一)工序25: (13)1、切削用量的确定 (13)2、基本时间的确定 (15)(二)工序35: (15)1、切削用量的确定 (15)2、基本时间的确定 (16)(三)工序60工步1 (16)1、切削用量的确定 (16)2基本时间的确定 (16)(四)工序60工步2、3 (17)1、切削用量的确定 (17)2、基本时间的确定 (17)(五)工序65: (17)1、切削用量的确定 (17)2、基本时间 (18)(六)工序75: (18)1、切削用量 (18)2、基本时间 (19)(七)工序80: (19)1、切削用量 (19)2、基本时间 (20)(八)工序85: (20)1、切削用量 (20)2、基本时间 (21)(九)工序90工步1 (21)1、切削用量的确定 (21)2、基本时间的确定 (22)(十)工序90工步2 (22)1、切削用量的确定 (22)2、基本时间的确定 (22)六、工艺部分个人总结 (22)七、参考文献 (23)一、设计任务设计对象为全电式注塑机BE50射胶部分中的一个注射支架零件,据此拟定一套该零件的机械加工工艺及工装设计方案。
《铸造工艺》课程设计说明书

目录1绪言················································2铸造工艺设计···············2.1铸件结构的铸造工艺性·········2. 2铸造工艺方案的确定·················2.3参数的选择工艺2. 4砂芯设计2. 5浇注系统设计·············3铸造的工艺装备设计······3. 1模样设计·······3. 2模底板的设计·······················3. 3模样在模底板上的装配············4结束语·······参考文献1绪言我本次课程设计的任务是对灰铸铁支承座进行铸造工艺及工装设计。
支架零件课程设计说明书

序言本次机械加工工艺规程设计,是我们学完了机械制图、机械制造工艺学、工程材料、机械设计、CAD/CAM等专业基础课和主要专业课,又经过了上学期得机械设计课程设计之后,进行的又一次实践性环节,特别强调对机械制造工艺学和工程材料这两门课程的运用,同时也有对刀具和切屑的部分知识的综合,因此这是我们对以前所学各门课程的一次较为深入的综合总复习,同时还要对相关课外知识进行查阅和学习,也是一次对我们实际运用知识解决问题能力的练习。
我的设计题目是支架工艺规程设计,本次设计同时需要结合生产实习中学到的实践知识,并通过查找图册、手册等资料来解决工艺问题。
由于能力和经验所限,以及对知识掌握、熟悉程度以及综合运用还存在不足,因此在设计中难免会有考虑不周全或错误的地方,希望老师能够给予批评和指正。
目录任务介绍 (4)零件分析 (4)支架工艺规程设计 (5)1、确定支架毛坯的制造形式 (5)2、基准选择 (5)3、制定工艺路线 (6)4、机械加工余量、工序尺寸及毛坯尺寸的确定 (9)5、确定切削用量及基本工时 (11)小结 (22)参考文献 (23)任务1、对零件进行工艺分析;2、选择毛坯种类及制造方法,绘制毛坯图;3、制订零件的机械加工工艺过程,选择工序加工设备及工艺装备,确定各工序切削用量及工序尺寸工;4、填写工艺文件;5、撰写设计说明书。
零件分析1、零件的作用:设计做的零件支架位于车床的调节部位,起支撑、协调的作用。
本设计任务给定的零件支架即传递运动并保持其他零件正确工作方式,和保持互相之间的正确位置。
其对加工平面,加工孔,垂直度,等有一定的要求。
2、零件的工艺性分析和零件图的审查零件图(见附图)的主视图以工作位置放置,表达相互垂直的安装面、支撑肋、支撑孔以及夹紧用的螺孔等结构。
左视图主要表达其支架各个部分前后的相对位置及安装板的形状和工作部分的通孔等。
根据零件图可知,零件的整体精度要求除了重要端面和孔,其他端面和孔的要求并不很高。
支架的加工工艺及夹具设计说明书范文

支架的加工工艺及夹具设计说明书范文1.零件的工艺分析及生产类型确定1.1零件的作用题目所给的零件是“支架”,它的主要作用是起固定支撑作用。
图1支架零件图1.2零件的工艺分析从零件图上看来,知原图样的视图正确完整,尺寸和公差还有技术要求齐全。
从加工表面上看来,毛坯采用铸件,部分加工表面是主要的工作表面。
加工表面有:1).零件的左、右端面(由图纸所示),粗糙度达到6.32).Φ80H7的孔,要满足圆度公差为0.005,和前端面以及底面的平行度要求,自身的直线度要求.3).前端面,精度要求较高,粗糙度达到1.6,用于连接固定其它部件. 4).底面,和前端面的精度要求一样,粗糙度达到1.62.选择毛坯,确定毛坯尺寸和设计毛坯图2.1选择毛坯根据零件图可知,零件材料为HT15-33,也就是HT50,HBS为150,零件形状为异形件,且属中批及大批生产,因此选用铸造毛坯,这样,毛坯形状与成品相似,加工方便,省工省2.2确定毛坯尺寸和设计毛坯图为保证铸件加工表面的表面特征与尺寸精度要求,在设计铸造工艺时预先增加在机加工时要切去的金属层厚度,根据国家标准GB/T6414-1999,毛坯尺寸=零件尺寸+RMA+铸件公差等级对应的数值CT[1],对圆柱体铸件部分及双侧加工的表面RMA应加倍,对孔以及内腔加工的表面,毛坯尺寸=零件尺寸-RMA-铸件公差等级对应的数值CT.机器造型时,根据零件的最大尺寸,查表得出RMA=4mm,CT=1.4mm。
故毛坯尺寸是加工表面上的零件尺寸加上5.4mm。
毛坯图尺寸见图纸。
3选择加工方法,制定工艺路线3.1定位基准的选择基准选择是工艺规程设计中的重要工作之一。
基准选择的正确与合理,可以使加工质量得到保证、生产率得到提高。
否则,不但加工工艺规程中的问题百出,更有甚者,还会造成零件的大批报废,使生产不能正常进行。
(1)粗基准的选择。
由粗基准的选择原则:保证相互位置要求的原则。
应以不加工面为粗基准;保证加工面加工余量合理分配的原则。
铸造工艺设计说明书

铸造工艺设计说明书一、铸造工艺设计的目的和意义铸造是将液态金属浇注到与零件形状、尺寸相适应的铸型型腔中,待其冷却凝固,以获得毛坯或零件的生产方法。
铸造工艺设计则是根据零件的结构特点、技术要求、生产批量等因素,确定铸造方法、铸型分型面、浇注系统、冒口和冷铁等工艺参数,以保证获得高质量的铸件,并提高生产效率、降低成本。
良好的铸造工艺设计具有重要意义。
首先,它能够保证铸件的质量,减少铸造缺陷的产生,如气孔、缩孔、夹渣等。
其次,合理的工艺设计可以提高生产效率,降低生产成本,缩短生产周期。
此外,还能为后续的机械加工提供良好的基础,减少加工余量,提高材料利用率。
二、零件分析1、零件结构对需要铸造的零件进行结构分析,包括形状、尺寸、壁厚均匀性等。
例如,形状复杂的零件可能需要采用复杂的分型面和浇注系统;壁厚不均匀的零件容易产生缩孔、缩松等缺陷,需要合理设置冒口和冷铁。
2、技术要求明确零件的技术要求,如材质、力学性能、表面质量等。
不同的材质和性能要求会影响铸造工艺的选择和参数的确定。
3、生产批量生产批量的大小直接影响铸造方法的选择。
大批量生产时,通常采用金属型铸造、压力铸造等高效率的铸造方法;小批量生产则多采用砂型铸造。
三、铸造方法的选择1、砂型铸造砂型铸造是应用最广泛的铸造方法,其优点是成本低、适应性强,可生产各种形状和尺寸的铸件。
但砂型铸造的生产效率较低,铸件的表面质量相对较差。
2、金属型铸造金属型铸造的生产效率高,铸件的精度和表面质量好,但模具成本高,适用于大批量生产形状简单、尺寸较小的铸件。
3、压力铸造压力铸造能生产出形状复杂、薄壁的高精度铸件,但设备投资大,主要用于生产大批量的有色金属铸件。
4、熔模铸造熔模铸造适用于生产形状复杂、精度要求高、难以机械加工的小型零件。
根据零件的结构、技术要求和生产批量,综合考虑选择合适的铸造方法。
四、铸型分型面的选择分型面的选择直接影响铸型的制造、造型操作的难易程度以及铸件的质量。
左前悬置托架铸造工艺设计(DOC)

左前悬置托架铸造工艺设计专业:***班级:*级*班姓名:***目录1零件简介 (3)1.1零件介绍 (3)1.2生产批量的选择 (5)1.3技术要求 (5)1.4铸造工艺设计方法及分析 (5)1.4.1铸件壁厚 (5)1.4.2造型、制芯方法 (6)1.4.3砂箱中铸件数目的确定及排布 (7)2 铸造工艺设计 (8)2.1 工艺方案的选择 (8)2.1.1分型面的确定 (8)2.1.2浇注位置的确定 (10)2.2 铸造工艺参数的确定 (12)2.2.1 最小铸出孔 (12)2.2.2 加工余量和铸造圆角 (12)2.2.4 起模斜度 (14)2.2.5工艺补正量 (15)2.2.6铸件尺寸公差 (16)2.2.7铸件重量公差 (16)2.2.8非加工壁厚负余量 (16)2.2.9反变形量 (17)2.2.10分型负数 (17)2.3砂芯设计 (17)2.3.1砂芯的选择原则 (17)2.3.2芯头设计 (18)2.3.3芯骨设计 (19)2.3.4砂芯的排气 (19)2.3.5芯型负数 (20)3 浇注系统设计 (21)3.1 浇注系统的选择原则 (21)3.3 浇注系统的尺寸选择 (22)3.4 浇口杯设计 (23)3.5 浇口窝的设计 (24)4 冒口设计 (25)4.1 冒口位置的设置原则 (25)4.2 冒口的有效补缩距离 (26)4.3 冒口尺寸计算 (26)4.4 工艺出品率的校核 (27)5冷铁设计 (28)6 绘制工艺图 (29)7 铸造工艺装备设计 (30)7.1 模样的设计 (30)7.1.1 模样材料的选用 (30)7.1.2 金属模样的结构 (30)7.2 模板的设计 (32)7.2.1模底板材料的选用 (33)7.2.2模底板尺寸确定 (33)7.2.3模底板与砂箱的定位 (33)7.2.4模底板与造型机工作台的连接装配 (34)7.2.5模样在底面上的装配 (35)7.2.6模底板的壁厚和加强肋 (36)7.2.7模板图 (37)7.3砂箱的设计 (38)7.3.1砂箱的材质及尺寸 (38)7.3.2砂箱各部分的结构和尺寸 (38)7.3.3合箱图 (42)7.4芯盒的设计 (42)7.4.1芯盒的类型和材质 (42)7.4.2芯盒结构设计 (42)8 砂型铸造设备选用 (44)8.1造型工部设备选用 (44)8.2制芯工部设备选用 (44)8.3砂处理工部设备选用 (45)8.4熔化工部设备选用 (45)8.5清理工部设备选用 (45)结论 (47)致谢 .................................................................................................................................. 错误!未定义书签。
- 1、下载文档前请自行甄别文档内容的完整性,平台不提供额外的编辑、内容补充、找答案等附加服务。
- 2、"仅部分预览"的文档,不可在线预览部分如存在完整性等问题,可反馈申请退款(可完整预览的文档不适用该条件!)。
- 3、如文档侵犯您的权益,请联系客服反馈,我们会尽快为您处理(人工客服工作时间:9:00-18:30)。
xxxxxxxxxxxxxxxxxx课程设计报告课程设计名称:悬臂支架铸造工艺设计学生姓名:xxxxxxxxxxxxxxx学院:xxxxxxxxxxxxx专业及班级:xxxxxxxxxxxxxx学号:xxxxxxxx指导教师:xxxxxxxxxxxxxxxxxxxx摘要铸造生产通常是指用熔融的合金材料制作产品的方法,将液态合金注人预先制备好的铸型中使之冷却、凝固,而获得毛坯或零件,这种制造过程称为铸造生产,简称铸造,所铸出的产品称为铸件。
大多数铸件作为毛坯,需要经过机械加工后才能成为各种机器零件;有的铸件当达到使用的尺寸精度和表面粗糙度要求时,可作为成品或零件直接应用。
本课程设计是为了获得ZG270-500悬臂支架的合理铸造工艺设计方案,初步设计悬臂支架的铸造工艺方案,包括选择铸件的浇注位置及分型面,确定型芯的数量、定位方式、下芯顺序、芯头形状及尺寸,确定工艺参数(如机械加工余量、起模斜度、铸造圆角级收缩率等)以及浇注系统、冒口、冷铁的形状和尺寸及在砂型中的布置等,通过Pro/e进行仿真,根据模拟结果进行分析,铸造工艺方案的合理性,然后将所确定的工艺方案用文字和铸造工艺符号在CAD零件图上表示出来,绘制铸造工艺图。
关键词:铸造工艺设计,悬臂支架,Creo,CAD。
Usually refers to using the molten alloy casting production material products, the method of the liquid alloy preparation beforehand good mold in injection cooling and solidification, and blank or parts, the manufacturing process is referred to as casting production, referred to as "casting, casting out products are referred to as casting.As most of the casting blank, need after mechanical processing can be all kinds of machine parts;Some castings when to use the dimensional accuracy and surface roughness requi rem ent s, can be di rect l y appli ed as fini shed products or parts.This course is designed to obtain reasonable ZG270-500 cantilever casting process design, preliminary design of cantilever casting process, including selection of casting pouring position and parting surface, determine the number of cores, positioning way, the core order, core head shape and size, determine the process parameters (such as machining allowance, mould level Angle, casting the rounded shrinkage rate, etc.) and the pouring system, riser and chill the shape and size and arrangement in the sand mold, etc, through the Creo simulation, according to the result of simulation is analyzed, the rationality of the casting process, then determine the processing plan in words and casting process representation in the CAD drawing, mapping the casting process.Keywords: casting process design; cantilever; Creo; CAD.目录第一章零件简介 (1)1.1零件介绍 (1)1.2最大尺寸 (1)1.3铸件材料及性能 (1)第二章确定铸造工艺方案 (2)2.1造型方法与铸型种类的选择 (2)2.1.1造型的选择 (2)2.1.2型砂的选择 (2)2.2浇注位置及分型面的确定 (2)2.2.1分型面的选择 (2)2.2.2浇注位置的选择 (3)第三章铸造工艺参数设计 (5)3.1加工余量的选择 (5)3.2铸件孔是否铸出的确定 (6)3.3起模斜度的确定 (6)3.4铸造圆角的确定 (7)3.5铸造收缩率的确定 (8)3.6活块的确定 (8)第四章造型方法设计 (9)4.1型芯的设计 (9)4.1.1空心支座型芯 (10)4.1.2空心轴套型芯 (11)4.2活块设计 (13)第五章木模的设计 (14)第六章浇注系统和冒口设计 (16)6.1浇注系统选择 (16)6.2冒口的计算与选择 (16)第七章铸型装配图设计 (18)设计体会 (21)参考文献 (22)第一章零件简介1.1零件介绍悬臂支架的作用支架是起支撑作用的构架,承受较大的力,也具有定位作用,使零件之间保持正确的位置。
图1.1 零件3D1.2最大尺寸零件最大尺寸350mm,属于小型铸件,基本壁厚20mm,有四个直径20mm的孔,可采用机加工方法得到,不铸造出。
有一个内凹空腔。
1.3铸件材料及性能材料为ZG270.500,中碳铸钢,抗拉强度500Mpa。
第二章确定铸造工艺方案铸件生产的主要步骤就是根据零件的结构特征、材质、技术要求、生产批量和生产条件等因素确定铸造工艺方案。
其具体内容包括:选择铸件的浇注位置及分型面,确定型芯的数量、定位方式、下芯顺序、芯头形状及尺寸,确定工艺参数(如机械加工余量、起模斜度、铸造圆角级收缩率等)以及浇注系统、冒口、冷铁的形状和尺寸及在砂型中的布置等,然后将所确定的工艺方案用文字和铸造工艺符号在零件图上表示出来,绘制铸造工艺图。
2.1造型方法与铸型种类的选择2.1.1造型的选择因设计任务书要求选择手工造型2.1.2型砂的选择铸钢用的型砂和泥心砂,其主要的组成部分是石英砂和耐火粘土。
作为造型材料的沙子性质,由砂粒形状和大小,氧化硅的含量,以及沙子中存在的各种混合物来确定。
该铸件型砂选用瘦沙(粘土含量2~10%)来代替石英砂。
在湿模造型时,小型和中小型钢铸件泥心砂可以采用小颗粒的半肥沙(粘土含量10~20%)作为附加物加入石英砂中。
加入的耐火粘土,其工艺试样的抗压强度应为0.5~0.6kg/mm2。
耐火粘土应该是白色或者淡灰色的,不应有可被肉眼看出的混杂物,如砂子、矿石、石灰等。
碎粘土所含水分不应超过2%。
造芯的方法可采用芯盒造芯和刮板造芯,前者用于造各种形状、尺寸和批量的砂芯,后者用于造单件小批量生产,形状简单或回转体砂芯。
2.2浇注位置及分型面的确定2.2.1分型面的选择定义:分型面是指铸型之间的结合面。
铸型分型面选择的正确与否是铸造工艺合理性的关键之一。
若选择不当,不仅影响铸件质量,而且还将使制模、造型、造芯、合型或清理,甚至机械加工等工序复杂化。
分型面的选择主要以经济性为出发点,即在保证质量的前提下,尽量简化工艺过程、降低生产成本。
一般原则:1.尽量把分型面开在铸件的最大平面上,便于起模;2.减少分型面和活块的数量;3.重要加工面应位于同一型腔中;4.尽量采用平直的分型面,不要是曲面、折面;5.减少型芯数量,同时注意下芯、合型及检验的方便;6.便于浇冒口设置,型芯的安放和固定;7.避免在机加工平面设置分型面。
综合以上原则,有以下方案。
方案(1)铸件呈竖直状态,其零件的冶金质量及尺寸精度要求较好,但不易造型,需采用图示的三箱造型工艺;方案(2)铸件呈水平状态,且上下沙箱高度一致,造型方便适合于大批量流水生产作业,但需要改进型砂配比,加强撇渣等工艺措施来保证铸件质量。
根据生产方式,和生产的批量,选择方案二。
2.2.2浇注位置的选择铸件的浇注位置是指浇注时铸件在型腔中的位置。
浇注位置的选择取决于合金种类、铸件结构和轮廓尺寸、铸件表面质量要求以及现有的生产条件。
选择铸件浇注位置时,主要以保证铸件质量为前提,同时做到简化造型和浇注工艺,确定铸件浇注位置时,应注意以下几点:1.重要加工面应超下或呈直立状态;2.铸件的大平面应朝下;3.应有利于铸件的补缩;4.应保证铸件有良好的液态金属导入位置,保证铸件能充满;5.应尽量少用或不用砂芯。
综上所述,悬臂支架铸件采用中注式浇注系统,浇注位置的选择如下图所示:1.浇口杯2.冒口3.直浇道4.内浇道5.横浇道6.铸件图2.1 浇注示意图第三章铸造工艺参数设计确定铸造工艺参数必须以零件尺寸为依据,零件的详细尺寸如图所示。
图3.1零件尺寸3.1加工余量的选择该槽轮为成批、大量生产,可采用机器造型及造芯,但本次课程设计则全采用手工造型和造芯。
根据参考文献[2] P189表9.4可知查得尺寸公差等级CT应为11~14级,选11级,加工余量等级为G~K级,RMA选H。
由课程设计题目知最大尺寸为350mm,根据参考文献[2] P189表9.3查得尺寸公差配套使用的铸件机械加工余量(RMA),并由确定加工余量中铸件顶面(相对于浇注位置)的加工余量应比底、侧面加工余量大。
孔的加工余量与顶面的等级相同。
一般情况下,顶面加工余量应按照CT11级、RMA-H级;底面、侧面的加工余量为CT9级、RMA-G级。
则顶面的加工余量取5mm,底面和侧面的加工余量取3.5mm。
结论:顶面的加工余量取5mm,侧面的加工余量取3.5mm,底面的加工余量取3.5mm。
加工余量如图3.2。
图 3.2 加工余量图3.2铸件孔是否铸出的确定因为该铸件材料是ZG270.500,成批生产,孔径30mm,根据参考文献[2] P196表9.10查得普通碳钢铸件的最小铸出孔直径是60mm,则该孔不应该铸出。
结论:该孔径为20mm的孔不应铸出。
3.3起模斜度的确定根据标准《铸件模样起模斜度》中的规定,该铸件选用增加铸件厚度的起模斜度形式如图3.3:图3.3 起模斜度用手工方法加工模具时用宽度标注,该铸件模具是木模,高度100mm,由根据参考文献[2] P194表9.8砂型铸造时模样外表面及内表面的起模斜度查得木模外表面起模斜度1.4mm,木模内表面起模斜度2.6mm。