氯化钠注射液工艺规程
二乙酰氨乙酸乙二胺氯化钠注射液生产工艺规程

技术标准本品为二乙酰氨乙酸乙二胺和氯化钠制成的灭菌水溶液。
1 品名: 二乙酰氨乙酸乙二胺氯化钠注射液2 剂型: 大容量注射剂3 规格: 100ml:二乙酰氨乙酸乙二胺0.3g与氯化钠0.9g4 代码:Y3145处方:5·1基准处方二乙酰氨乙酸乙二胺 3.0g氯化钠9.0g注射用水加至1000ml5·2 标准生产量:1200000 ml/批所用的原辅料及数量。
名称代码数量二乙酰氨乙酸乙二胺Y121 3.6Kg氯化钠Y102 10.8Kg针用活性炭F101 240g注射用水F108 至1200000 ml6 生产工艺及操作要求:6·1 配制(万级、温度18~26℃、湿度45~65%):本工序包括称量、浓配、稀配等。
6·1·1 称量:在备料间根据指令核对原辅料品名、规格、批号、生产厂家、数量,本厂检验报告单或合格证(绿色合格证)、递交单。
称量前校准天平、电子称并检查是否在效期内。
按处方要求进行原辅料的称量,填写物料标示卡附于容器内外各一张,注明品名、规格、批号、重量、日期和操作者。
经复核后填写称量记录。
剩余原辅料扎紧袋口,标明原辅料名称、批号、剩余量、使用人,放置于暂存架。
换品种清场时,将剩余料密封,贴上卡片,标明名称、规格、批号、数量、日期,退回脱包间,返至仓库。
6·1·2 浓配:取规定量氯化钠在浓配间投入到放有适量注射用水(70~85℃)的SH-Ⅰ浓配罐中,搅拌溶解,使成20%~22%的浓溶液,加入0.01%(g/ml,以稀配体积计)的针用活性炭,搅拌混匀,煮沸(100℃)15分钟,稍冷,用钛棒过滤器加压过滤,内循环10分钟,泵入稀配罐。
6·1·3 稀配:在稀配间向SH-Ⅰ稀配罐中加注射用水至全量的约80%,加规定量二乙酰氨乙酸乙二胺,加0.01%(g/ml,以稀配体积计)的针用活性炭,补加注射用水至全量,搅拌、回流15分钟,测pH值(规定:5.5~6.0,若不符合规定用稀盐酸或1M氢氧化钠调整)、含量(二乙酰氨乙酸乙二胺为99.0%~101.5%、氯化钠为98.5%~101.0%)(g/ml)符合规定后,降温至40~50℃,用钛棒过滤器和0.22μm 的膜滤芯加压过滤,终端用0.22μm的膜滤芯过滤至灌装。
氯化钠注射液500ml生产工艺规程
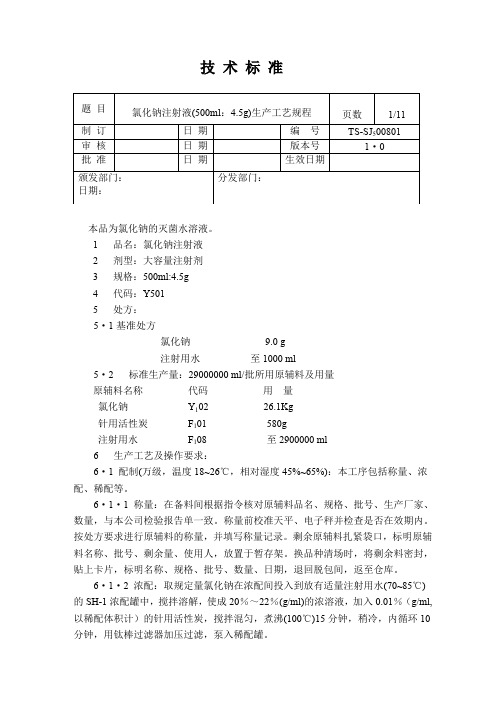
技术标准本品为氯化钠的灭菌水溶液。
1 品名:氯化钠注射液2 剂型:大容量注射剂3 规格:500ml:4.5g4 代码:Y5015 处方:5·1基准处方氯化钠9.0 g注射用水至1000 ml5·2 标准生产量:29000000 ml/批所用原辅料及用量原辅料名称代码用量氯化钠Y102 26.1Kg针用活性炭F101 580g注射用水F108 至2900000 ml6 生产工艺及操作要求:6·1 配制(万级,温度18~26℃,相对湿度45%~65%):本工序包括称量、浓配、稀配等。
6·1·1 称量:在备料间根据指令核对原辅料品名、规格、批号、生产厂家、数量,与本公司检验报告单一致。
称量前校准天平、电子秤并检查是否在效期内。
按处方要求进行原辅料的称量,并填写称量记录。
剩余原辅料扎紧袋口,标明原辅料名称、批号、剩余量、使用人,放置于暂存架。
换品种清场时,将剩余料密封,贴上卡片,标明名称、规格、批号、数量、日期,退回脱包间,返至仓库。
6·1·2 浓配:取规定量氯化钠在浓配间投入到放有适量注射用水(70~85℃)的SH-1浓配罐中,搅拌溶解,使成20%~22%(g/ml)的浓溶液,加入0.01%(g/ml,以稀配体积计)的针用活性炭,搅拌混匀,煮沸(100℃)15分钟,稍冷,内循环10分钟,用钛棒过滤器加压过滤,泵入稀配罐。
6·1·3 稀配:在稀配间向SH-Ⅰ稀配罐中加注射用水至全量的约80%,加0.01%(g/ml,以稀配体积计)的针用活性炭,补加注射用水至全量,搅拌、回流15分钟,测pH值(规定:5.0~6.0)、含量(0.880%~0.920%)(g/ml)符合规定后,降温至40~50℃,用钛棒过滤器和0.22μm的膜滤芯加压过滤,终端用0.22μm的膜滤芯过滤至灌装。
生产结束后,操作者做好清场卫生工作(按清场操作规程),并做好记录。
多层共挤膜输液袋氟康唑氯化钠注射液工艺规程

多层共挤输液用袋包装氟康唑氯化钠注射液工艺规程多层共挤输液用袋包装氟康唑氯化钠注射液工艺规程目录第一章主题内容与适应范围 1第二章工艺流程及区域划分 2第三章处方与依据 3第四章操作过程、工艺条件及质量控制要点 4第五章原辅料质量标准10第六章中间产品检查方法及控制15第七章成品质量标准16第八章工艺卫生、技术安全及劳动保护17第九章设备一览表及主要设备生产能力21第十章包装要求、标签、说明书及贮存方法22第十一章物料平衡指标及计算方法36第十二章劳动组织及定岗定员37第十三章附录38第十四章变更登记表40第十五章附页41标题:多层共挤输液用袋包装氟康唑氯化钠注射液工艺规程编号:JS02-21 第1页共42页第一章主题内容与适用范围本标准规定了氟康唑氯化钠注射液的主题内容与适用范围、生产工艺规程及区域划分、处方与依据、操作过程、工艺条件与质量控制点、原辅料质量标准、中间产品检查方法与控制、成品质量标准、工艺卫生、技术安全劳动保护、设备一览表及主要设备生产能力、包装要求、标签、说明书与贮存方法、物料平衡指标及计算方法、劳动组织与定岗定员等内容。
本标准适用于多层共挤输液用袋包装氟康唑氯化钠注射液生产操作与检查。
标题:多层共挤输液用袋包装氟康唑氯化钠注射液工艺规程编号:JS02-021 第2页共41页第二章 工艺流程及区域划分图例100000级区 10000级区 *局部100级标题:多层共挤输液用袋包装氟康唑氯化钠注射液工艺规程 编号:JS02-021 第3页 共41页第三章处方与依据3.1名称:氟康唑氯化钠注射液3.2生产处方:原料名称用量(250ml:0.5g)氟康唑:20g氯化钠:90g活性炭适量适量注射液用水加至10000ml 10000ml3.3规格:100 ml:0.2g3.4产品的批准文件:(附后)3.5批准文号:规格批准文号100ml :0.2g 国药准字3.6依据:《中国药典》2000年版二部3.7有效期:2年标题:多层共挤输液用袋包装氟康唑氯化钠注射液工艺规程编号:JS02-021 第4页共41页第四章操作过程、工艺条件及质量控制要点本部分主要规定了多层共挤输液用袋包装氟康唑氯化钠注射液生产过程中配制、制袋、灌装、封口、灭菌、检漏、灯检、包装操作等几部分的工艺流程及其工艺条件和质量监控要点。
0.9%氯化钠注射液的工艺流程

0.9%氯化钠注射液的工艺流程下载温馨提示:该文档是我店铺精心编制而成,希望大家下载以后,能够帮助大家解决实际的问题。
文档下载后可定制随意修改,请根据实际需要进行相应的调整和使用,谢谢!并且,本店铺为大家提供各种各样类型的实用资料,如教育随笔、日记赏析、句子摘抄、古诗大全、经典美文、话题作文、工作总结、词语解析、文案摘录、其他资料等等,如想了解不同资料格式和写法,敬请关注!Download tips: This document is carefully compiled by theeditor. I hope that after you download them,they can help yousolve practical problems. The document can be customized andmodified after downloading,please adjust and use it according toactual needs, thank you!In addition, our shop provides you with various types ofpractical materials,such as educational essays, diaryappreciation,sentence excerpts,ancient poems,classic articles,topic composition,work summary,word parsing,copy excerpts,other materials and so on,want to know different data formats andwriting methods,please pay attention!0.9%氯化钠注射液,也被称为生理盐水,是一种常用的生理盐水溶液,用于补充体液和电解质,维持人体正常的生理功能。
012.氯化钠注射液浓配标准操作规程

江西捷众生物化学有限公司氯化钠注射液浓配标准操作规程1.目的:规范氯化钠注射液的浓配液操作,确保配制的药液质量符合规定。
2.适用范围:适用于浓配岗位操作。
3.职责:3.1浓配岗位操作人员按本规程操作。
3.2车间主任、QA负责监督检查。
4.操作内容与要求4.1生产前准备4.1.1检查配液系统卫生状态及性能状态标志,配液系统应在配液罐的“清洁合格证”是否在有效期内和“设备状态标志卡”是否完好,否则不得使用。
4.1.2检查输液泵电机、搅拌系统电机供电线路是否正常。
4.1.3检查系统管道、泵体、滤罐、连接处有无松动,渗漏现象,如有应及时紧固或更换密封件。
4.1.4检查注射用水、蒸汽、电源、冷却水是否处于可供状态。
4.1.5开启温度仪、水位仪电源、检查温度仪、水位仪是否正常。
4.1.6按批生产指令填写“生产状态标志卡”并挂于操作间门口。
4.2配液系统清洗4.2.1开启洗涤阀,检查其它阀门均应处于关闭状态,用注射用水冲洗配液罐5分钟,关闭洗涤阀。
4.2.2开启出液阀、回流阀,开启输液泵电源,回流冲洗管道及滤罐5分钟,关闭输液泵电源。
4.2.3开启排污阀,排净配液罐中存水,关闭排污阀。
4.3活性炭打底4.3.1开启进水阀,在配液罐中放入约300L注射用水,关闭进水阀。
4.3.2按每根滤棒10g活性炭的量从投料口加入称量调配好的活性炭。
4.3.3开启搅拌5分钟,关闭。
4.3.4开启输液泵电源,回流5分钟后通知稀配操作工冲洗管道,开启送稀配阀,关闭回流阀。
4.3.5待配液系统注射用水抽干后,关闭输液泵电源,关闭送稀配阀、出液阀,检查排污阀应处于关闭状态,准备投料配液4.4称料4.4.1标准投料处方:按3500L/批进行投料品名:氯化钠注射液规格: 500ml: 4.5g ;250ml: 2.25g;100ml: 0.9g注射用氯化钠:31.5kg767型活性炭:126g注射用水加至:150L4.4.2称料4.4.2.1根据《投料处方》称取所需物料。
GMP 葡萄糖氯化钠注射液工艺规程.

宁波市 xx 制药有限公司输液车间管理文件1. 目的:编制规范化、标准化的工艺规程,作为全面指导生产和控制质量的基准性技术文件。
2. 范围:葡萄糖氯化钠注射液生产和质量控制的全过程。
3. 责任3.1 输液车间负责生产全过程。
3.2 质量管理部门负责质量控制全过程。
3.3 工程部负责提供工艺用水、电、汽及洁净空气等。
4. 管理内容11-14.1 生产工艺流程其中:粗洗、浓配采用 10万级稀配、轧盖采用 1万级灌装、压塞采用局部 100级4.2 操作过程及工艺条件4.2.1 理瓶根据生产量准备相应数量的瓶子 , 脱去外包装后正立于理瓶台上,挑选出破损瓶子,待理瓶台集满瓶子后可开动理瓶机传送带,送瓶。
4.2.2 外洗4.2.2.1 开启饮用水水源,启动外洗机主机开关进行外洗操作。
4.2.2.2 检查经过外洗的输液瓶,将破损瓶及时挑出,放在指定地点。
4.2.3 粗洗4.2.3.1 开启电源;将水箱和储水箱注满水至溢水管顶部,水温控制到 50~ 60℃,开启水泵,打开喷淋水控制阀(以能将空瓶注满水为准 ,启动超声波、输液轨道和主机,进行粗洗操作。
4.2.3.2 操作过程中,碰到紧急情况,应按下紧急停车按钮,立即停车,检查调整后再开机。
4.2.4 精洗4.2.4.1 检查过滤后注射用水可见异物,合格后方可进行精洗操作。
4.2.4.2 打开电源开关,将储水罐注满水,水温控制到 50~60℃,调节新鲜水压力0.2~0.4MPa ,调节压缩空气控制阀至压力 0.2~0.4MPa ,打开水泵,调节循环水压至0.2~0.4MPa ,开启主机,进行精洗操作。
4.2.4.3 检查精洗后玻璃瓶可见异物合格,注射用水残存应不超过 2滴,输液瓶方可进行灌装。
4.2.4.4 精洗好的瓶子存放时间不超过 30分钟,否则重新清洗。
4.2.5 配料4.2.5.1 浓配4.2.5.1.1 核对原辅料品名、规格、批号、数量、检验报告单,确认无误后按生产指令书上的处方量进行称量,称量过程要有人复核。
甲硝唑氯化钠注射液工艺-玻瓶

甲硝唑氯化钠注射液工艺1 处方和依据、生产批量1.1 处方甲硝唑 5.0g氯化钠 8.0g注射用水加至 1000ml1.2 工艺依据: 再注册工艺标准依据:《中国药典》2015年版二部规格:100ml 玻璃输液瓶批准文号:国药准字H13022486有效期:24个月2 配料:2.1 活性炭架桥:每日配液前需向上述浓配罐内注入注射用水约600L,通过粉体输送系统向浓配罐投入300g(每个钛棒罐的需用量)活性炭,投料完毕,然后经5.0μm钛棒过滤器以及1μm聚醚砜折叠式滤芯过滤,回滤15分钟。
2.2 浓配:在溶解罐内预加入注射用水,投入计算量的甲硝唑(100%投料)溶解后,通过粉体输送系统投入计算量的氯化钠,搅拌使氯化钠溶解后,通过粉体输送系统输送计算量的活性炭(0.01% w/v稀配体积),自身循环均匀后,经5.0μm钛棒及1.0μm聚醚砜滤芯过滤。
2.3稀配:浓配液滤入补加注射用水至稀配定容量,依次经0.45μm和0.2μm的聚醚砜折叠式滤芯过滤至灌封岗位循环均匀,检测药液含量和pH值,必要时用1mol/LHCl溶液调节pH值,检查可见异物和不溶性微粒,合格后灌装。
灌装药液温度控制40~50℃。
稀配开始至灌装结束时间不得超过16小时。
注意事项:生产结束后需将钛棒罐拆开,彻底清除积炭。
3 中间产品质量标准及检查方法3.1 含量:本品含甲硝唑及氯化钠(NaCl)应为标示量的99.0-102.0%甲硝唑 精密量取本品适量,加盐酸溶液(9→1000)稀释成每1ml 中约含甲硝唑12.5μg 溶液(5ml 药液定容到100ml ,取稀释液5ml 定容到100ml ),照分光光度法,在277±1nm 的波长处测定吸收度,按C 6H 9N 3O 3的吸收系数E 1%1cm 为377计算,即得。
A×400计算公式 标示量%= ────── ×100% = 2.122A×100% 377×0.5 氯化钠测定方法:银量法精密量取本品10ml 置250ml 锥形瓶中,加水40ml ,加铬酸钾指示剂 3—4滴,用硝酸银试液(0.1mol/L)滴定至产生砖红色沉淀为终点。
乳酸环丙沙星氯化钠注射液生产工艺规程

技术标准本品为乳酸环丙沙星与氯化钠制成的灭菌水溶液1 品名: 乳酸环丙沙星氯化钠注射液2 剂型: 大容量注射剂3 规格: 100ml:0.2g(以C17H18FN3O3计)4 代码:Y6065 处方:5·1基准处方乳酸环丙沙星 2.54g氯化钠9.0g注射用水至1000ml5·2 标准生产量:1100000 ml/批所用的原辅料及数量名称代码数量乳酸环丙沙星Y120 2.794Kg(理论投料量)氯化钠Y102 9.9Kg针用活性炭F101 220g依地酸钙钠F109 55g10%乳酸F104 1.8L注射用水F108 至1100000 ml乳酸环丙沙星原料折算公式:实际投料量=理论投料量含量×(1-干燥失重)6 生产工艺及操作要求:6·1 配制(万级、温度18~26℃、湿度45~65%):本工序包括称量、浓配、稀配等。
6·1·1 称量:在备料间根据指令核对原辅料品名、规格、批号、生产厂家、数量,与本公司检验报告单一致。
称量前校准天平、电子秤并检查是否在效期内。
按处方要求进行原辅料的称量,并填写称量记录。
剩余原辅料扎紧袋口,标明原辅料名称、批号、剩余量、使用人,放置于暂存架。
换品种清场时,将剩余料密封,贴上卡片,标明名称、规格、批号、数量、日期,退回脱包间,返至仓库。
6·1·2 浓配:取规定量氯化钠在浓配间投入到放有适量注射用水(70~85℃)的SH-Ⅰ浓配罐中,搅拌溶解,使成20%~22%的浓溶液,加入0.01%(g/ml,以稀配体积计)的针用活性炭,搅拌混匀,煮沸(100℃)15分钟,稍冷,用钛棒过滤器加压过滤,内循环10分钟,泵入稀配罐。
6·1·3 稀配:在稀配间向SH-Ⅰ稀配罐中加注射用水至全量的约80%,加入规定量乳酸环丙沙星,加0.005%(g/ml,以稀配体积计)的依地酸钙钠,用10%乳酸0.9L/Kg(以环丙沙星计)调节pH值,加0.01%(g/ml,以稀配体积计)的针用活性炭,补加注射用水至全量,搅拌、回流15分钟,测pH值(3.8~4.2)、含量(以环丙沙星计为98.0%~101.0%)符合规定后,降温至40~50℃,用钛棒过滤器和0.22μm的膜滤芯加压过滤,终端用0.22μm的膜滤芯过滤至灌装。
氯化钠注射液工艺规程
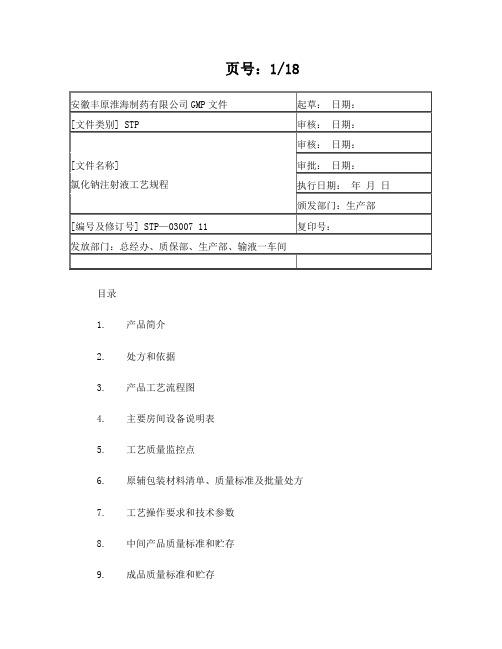
页号:1/18目录1. 产品简介2. 处方和依据3. 产品工艺流程图4. 主要房间设备说明表5. 工艺质量监控点6. 原辅包装材料清单、质量标准及批量处方7. 工艺操作要求和技术参数8. 中间产品质量标准和贮存9. 成品质量标准和贮存10. 劳动组织与岗位定员11. 文件变更表12. 附件1. 产品简介1.1 品名氯化钠注射液1.2 代码 00-0091.3 剂型大容量注射剂1.4 规格 250ml:2.25g1.5 包装聚丙烯输液瓶装,40瓶/箱1.6 贮藏密闭保存1.7 有效期 36个月1.8 批次量 16000瓶/批1.9 生产线 J线2. 处方和依据2.1 处方氯化钠 9g ;注射用水加至1000ml2.2 依据国家食品药品监督管理局批件批准文号:国药准字H20093237页号:2/18文件名称:氯化钠注射液工艺规程编号及修订号:STP—03007 11 复印号:3. 产品工艺流程图D级区C级区C级背景下的A级区一般区页号:3/184. 主要房间设备说明表页号:4/18页号:5/18页号:6/18页号:7/185. 工艺质量监控点页号:8/18页号:9/186.原辅包装材料清单、质量标准及批量处方7. 工艺操作要求和技术参数7.1 浓配7.1.1 生产前检查:每日生产前检查生产设备、过滤器已清洁、灭菌,状态标志明显;所用称量器具、各类仪表、仪器在校验周期内,标志明显;上批清场应合格,并将上批清场合格证副本附于记录之前;每批生产前检查设备情况应正常;已撤去上批生产状态标志、无上批生产记录和与本批生产无关的遗留物,生产现场卫生整洁;换好本批生产状态标志,操作文件、批生产记录应齐全;本批所需原、辅料已备齐,并与称量记录一致。
7.1.2 原辅料的领用:车间领料人员按生产部下发的批生产指令的限料量由仓库领料至车间物流通道外清间。
所领到的原辅料脱除外包装后用纯化水擦拭清洁,然后用75%的乙醇擦拭消毒后进入缓冲间。
氯化钠注射液

.1012
氯化钾片 【 检 查 】 p H 值 应 为 4 . 5~7.0(附录YI H ) 。 重 金 属 取 本 品 1 0 . Oml ,加醋酸盐缓冲液( P H3. 5)2ml 与水适量使成25ml,依法检查(附录《 不得过百万分之一。 细菌内毒素取本品,依法检査(附录M 钠中含内毒素的量应小于 25EU。 其 他 应 符 合 注 射 剂 项 下 有 关 的 各 项 规 定 ( 附 录 I B )。 【含量测定】精密量取本品 10ml ,置 100ml 量瓶中,加 水至刻度,摇匀;精密量取10ml,置锥形瓶中,加水40ml、2% 糊精溶液5ml、2. 5 % 硼 砂 溶 液 2 m l 与 荧 光 黄 指 示 液 5 - ~ 8 滴 , 用硝酸银滴定液( 0. l m o l / L ) 滴 定 。 每 l m l 硝 酸 银 滴 定 液 (0. lmol/L) 相当于 5. 844mg的NaCl。 【类别】同氯化钠。 【规格】(l)10ml : lg (2)100ml = 10g 【贮藏】密闭保存。 E) ,每 lg 氯化 H 第一法),含重金属 8-羟基喹啉三氯甲烷溶液提取三次(20、20、10ml),合并提取 液,置 50ml 量瓶中,加三氯甲烷至刻度,摇匀,照荧光分析法 (附录IV E) 测定,在激发波长 392nm 、发射波长 518nm 处测 定,供试品溶液的荧光强度应不大于对照溶液的荧光强度(百 万分之 一)。 碘化物、钡盐、钙盐、镁盐与铁盐照氯化钠项下的方法 检查,均应符合规定。 溴 化 物 取 本 品 0 . 2g,置100ml量瓶中,加水溶解并稀释 至刻度,摇匀,精密量取 5ml ,置 10ml 比色管中,照氯化钠项 下的方法检查,应符合规定 (0. 1 % ) 。 干燥失重取本品,在105°C干燥至恒重,减失重量不得 过 1.0% (附录 W L )。
复方氯化钠注射液500ml生产工艺规程
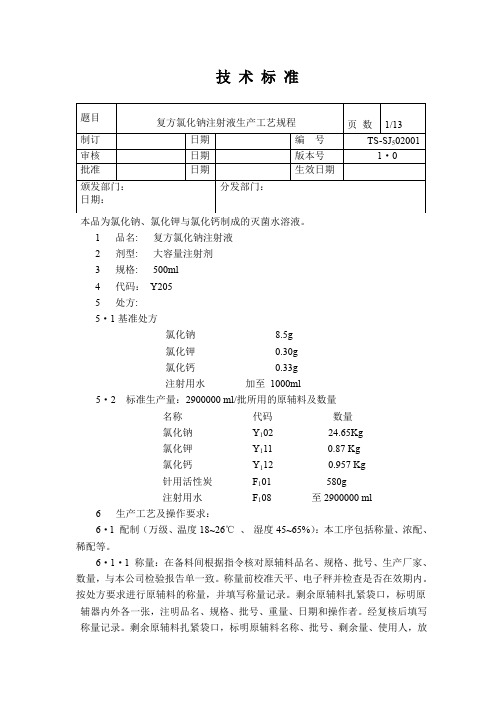
技术标准本品为氯化钠、氯化钾与氯化钙制成的灭菌水溶液。
1 品名: 复方氯化钠注射液2 剂型: 大容量注射剂3 规格: 500ml4 代码:Y2055 处方:5·1基准处方氯化钠8.5g氯化钾0.30g氯化钙0.33g注射用水加至1000ml5·2 标准生产量:2900000 ml/批所用的原辅料及数量名称代码数量氯化钠Y102 24.65Kg氯化钾Y111 0.87 Kg氯化钙Y112 0.957 Kg针用活性炭F101 580g注射用水F108 至2900000 ml6 生产工艺及操作要求:6·1 配制(万级、温度18~26℃、湿度45~65%):本工序包括称量、浓配、稀配等。
6·1·1 称量:在备料间根据指令核对原辅料品名、规格、批号、生产厂家、数量,与本公司检验报告单一致。
称量前校准天平、电子秤并检查是否在效期内。
按处方要求进行原辅料的称量,并填写称量记录。
剩余原辅料扎紧袋口,标明原辅器内外各一张,注明品名、规格、批号、重量、日期和操作者。
经复核后填写称量记录。
剩余原辅料扎紧袋口,标明原辅料名称、批号、剩余量、使用人,放置于暂存架。
换品种清场时,将剩余料密封,贴上卡片,标明名称、规格、批号、数量、日期,退回脱包间,返至仓库。
6·1·2 浓配:取规定量氯化钠在浓配间投入到放有适量注射用水(70~85℃)的SH-Ⅰ浓配罐中,搅拌溶解,使成20%~22%的浓溶液,加入0.01%(g/ml,以稀配体积计)的针用活性炭,搅拌混匀,煮沸(100℃)15分钟,稍冷,用钛棒过滤器加压过滤,内循环10分钟,泵入稀配罐。
6·1·3 稀配:在稀配间向SH-Ⅰ稀配罐中加注射用水至全量的约80%,再加入规定量氯化钾、氯化钙,加入0.01%(g/ml,以稀配体积计)的针用活性炭,补加注射用水至全量,搅拌、回流15分钟,测pH值(规定:5.0~7.0,若不符合规定用稀盐酸或1M氢氧化钠调整)、含量〔总含氯量(cl):0.54%~0.57%(g/ml)、氯化钙(Cacl2·2H2O ):0.032%~0.034%(g/ml)、氯化钾为0.029%~0.031%〕符合规定后,降温至40~50℃,用钛棒过滤器和0.22μm的膜滤芯加压过滤,终端用0.22μm的膜滤芯过滤至灌装。
替硝唑氯化钠注射液工艺-玻瓶

替硝唑氯化钠注射液工艺1 处方和依据、生产批量1.1 处方替硝唑 4.0g氯化钠 9.0g注射用水加至 1000ml1.2 工艺依据: 再注册工艺标准依据:《中国药典》2015年版二部规格:100ml 玻璃输液瓶批准文号:国药准字H10980128有效期:24个月2 配料:2.1 活性炭架桥:每日配液前需向上述浓配罐内注入注射用水约600L,通过粉体输送系统向浓配罐投入300g(每个钛棒罐的需用量)活性炭,投料完毕,然后经5.0μm钛棒过滤器以及1μm聚醚砜折叠式滤芯过滤,回滤15分钟。
2.2 浓配:在溶解罐内预加入注射用水,投入计算量的替硝唑(101%投料)溶解后,通过粉体输送系统投入计算量的氯化钠,搅拌使氯化钠溶解后,通过粉体输送系统输送计算量的活性炭(0.01% w/v稀配体积),静置吸附15分钟后,经5.0μm钛棒及1.0μm聚醚砜滤芯过滤。
2.3稀配:浓配液滤入补加注射用水至稀配定容量,依次经0.45μm和0.1μm的聚醚砜折叠式滤芯过滤至灌封岗位循环均匀,检测药液含量和pH 值,必要时用1mol/LHCl溶液调节pH值,检查可见异物、不溶性微粒,合格后灌装。
灌装药液温度控制40~50℃。
稀配开始至灌装结束时间不得超过16小时。
3 中间产品质量标准及检查方法3.1 含量:本品含替硝唑及氯化钠(NaCl)应为标示量的98.0-101.0%替硝唑:取药液适量,冷却至室温,精密量取本品10ml,置100ml容量瓶中,加水稀释至刻度,摇匀;再精密量取稀释液10ml,置250ml容量瓶中,加水稀释至刻度,摇匀,照紫外光分光光度法,在317±1nm的波长处测定吸收度;另取干燥至恒重的替硝唑对照品适量,加水溶解,定量稀释成每1ml中约含16μg的溶液,同法测定,计算,即得。
计算公式: C对×A样标示量%= ──────×100%A对×16氯化钠测定方法:银量法精密量取本品10ml置250ml锥形瓶中,加水40ml,加铬酸钾指示剂3—4滴,用硝酸银试液(0.1mol/L)滴定至产生砖红色沉淀为终点。
复方氯化钠注射液工艺-玻瓶

复方氯化钠注射液工艺1 处方和依据、生产批量1.1 处方氯化钠 8.5g氯化钾 0.30g氯化钙 0.33g注射用水加至 1000ml1.2 工艺依据: 再注册工艺标准依据:《中国药典》2015年版二部规格:500ml 玻璃输液瓶批准文号:国药准字H13023036有效期:24个月2 配料:2.1 活性炭架桥:每日配液前需向上述浓配罐内注入注射用水约600L,通过粉体输送系统向浓配罐投入300g(每个钛棒罐的需用量)活性炭,投料完毕,然后经5.0μm钛棒过滤器以及1μm聚醚砜折叠式滤芯过滤,回滤15分钟。
2.2 浓配:在浓配罐内预加入注射用水,投入计算量的氯化钠、氯化钾、氯化钙,搅拌使溶解后,通过粉体输送系统输送计算量的活性炭(0.01% w/v 稀配体积),自身循环均匀后,经5.0μm钛棒及1.0μm聚醚砜滤芯过滤。
2.3稀配:浓配液滤入补加注射用水至稀配定容量,依次经0.45μm和0.2μm的聚醚砜折叠式滤芯过滤至灌封岗位循环均匀,检测药液含量和pH值,必要时用1mol/LHCl溶液调节pH值,检查可见异物和不溶性微粒,合格后灌装。
灌装药液温度控制40~50℃。
稀配开始至灌装结束时间不得超过16小时。
3 中间产品质量标准及检查方法3.1 含量:本品含总氯量(Cl)应为标示量的98%~102%,含氯化钙(CaCl2·2H2O)应为标示量的97%~103%。
总氯量:银量法:精密量取本品10ml置250ml锥形瓶中,加水40ml,加铬酸钾指示剂3—4滴,用硝酸银试液(0.1mol/L)滴定至产生砖红色沉淀为终点。
每1mlAgNO3液(0.1mol/L)相当于3.545mg的Cl。
计算公式: VAgNO3×3.545×F×100含量=────────────── ×100%10×1000×0.55式中VAgNO3: 消耗硝酸银的毫升数。
001 氯化钠注射液工艺规程

范围:氯化钠注射液职责:生产车间、生产部、质量部对本规程的4实施负责正文:2.1生产处方氯化钠9g注射用水加至1000ml2.2内包装材料非PVC复合膜塑料接口塑料密封盖2.4.1浓配——在浓配罐中放入注射用水适量,按处方量投入氯化钠,搅拌溶解完全,使其成50%-60%浓溶液,加入事先润湿的0.2%(g/g)活性炭。
通过钛棒将药液回流10分钟,从取样口取样检测药液澄清后,经1.0μm滤芯过滤至稀配罐内。
——执行SOP-MM-001《浓配标准操作规程》2.4.2稀配——于稀配罐内补加注射用水至规定量,开启搅拌和回流泵回流15分钟,取样中检测含量、PH值,检测合格后,将药液通过0.45μm、0.22μm过滤器至灌封。
——执行SOP-MM-006《稀配标准操作规程》2.4.3配料管道的清洗及消毒——执行SOP-HM-001《浓配系统在线清洗消毒标准操作规程》及SOP-HM-002《稀配系统在线清洗消毒标准操作规程》2.5制袋灌封——配制合格的药液在6小时内灌封完毕;——通过灌封机将药液分装到软袋中,熔封。
——执行SOP-MM-004《制袋灌封岗位标准操作规程》2.6灭菌——灌封合格的药液在4小时内进行灭菌。
——将灌封合格的药品进行装车,推进水浴式灭菌柜进行灭菌,(115℃,30分钟)。
——执行SOP-MM-010《灭菌(软袋)标准操作规程》2.7灯检——光源:照度为2000LX-3000LX.——每次取1袋产品,按SOP-MM-012《灯检(软袋)标准操作规程》进行灯检。
2.8包装——将灯检合格的产品进行包装。
——执行SOP-MM-014《包装(软袋)标准操作规程》2.9灯检废品的处理——废品作报废处理。
2.10物料平衡2.10.1浓配物料平衡计算:上批结存数+领用数-使用数=本批结存数实际灌封量+管道残留量2.10.2灌封物料平衡=×100%(允许范围为96%—100%)理论量2.10.3内包材物料平衡计算:领用量=使用量+剩余量+报废量2.10.4灭菌工序物料平衡: 灭菌装车数=灭菌检漏合格数+破损数+取样数2.10.5灯检工序物料平衡:灯检量=灯检合格品量+灯检不合格品量2.10.6包装工序物料平衡:产品实际包装量=成品入库量=灯检合格品量-取样量-包装报废量2.10.7包装材料使用量=领用量-剩余量-报废量2.11生产工艺流程图(见图一)①——滤芯起泡点控制②——含量、PH等中检指标控制③——装量、澄明度控制④——印字、袋成型、胫热合等外观控制⑤——灭菌时间、温度及F0值⑥——灯检视差率≤3%⑦——外包装印刷内容、生产批号、生产日期、有效期⑧——装箱量、封箱3.生产过程控制3.1半成品检验执行SOP-QM-201《氯化钠注射液半成品检验操作规程》3.2含量——98.0~102.0%3.3 PH值——5.0~7.03.4装量——测定容器为经校正的量筒,平均装量不少于标示量。
氯化钠注射液工艺规程

页号:1/18 安徽丰原淮海制药有限公司GMP文件起草:日期:[文件类别] STP 审核:日期:[文件名称]氯化钠注射液工艺规程审核:日期:审批:日期:执行日期:年月日颁发部门:生产部[编号及修订号] STP—03007 11 复印号:发放部门:总经办、质保部、生产部、输液一车间目录1.产品简介2.处方和依据3.产品工艺流程图4.主要房间设备说明表5.工艺质量监控点6.原辅包装材料清单、质量标准及批量处方7.工艺操作要求和技术参数8.中间产品质量标准和贮存9.成品质量标准和贮存10.劳动组织与岗位定员11.文件变更表12.附件1. 产品简介1.1 品名氯化钠注射液1.2 代码 00-0091.3 剂型大容量注射剂1.4 规格 250ml:2.25g1.5 包装聚丙烯输液瓶装,40瓶/箱1.6 贮藏密闭保存1.7 有效期 36个月1.8 批次量 16000瓶/批1.9 生产线 J线2. 处方和依据2.1 处方氯化钠 9g ;注射用水加至1000ml 2.2 依据国家食品药品监督管理局批件批准文号:国药准字H20093237页号:2/18 文件名称:氯化钠注射液工艺规程编号及修订号:STP—03007 11 复印号:3.产品工艺流程图D级区C级区C级背景下的A级区一般区称量浓配洗灌封灭菌稀配脱碳过滤0.22μm0.45μm脱碳过滤包装灯检入库原辅料聚丙烯塑料粒子注塑焊环、吹瓶1.活性炭0.02%(W/V)。
2.煮沸药液并维持沸腾10分钟。
3.冷却药液温度至70-75℃。
1.洗瓶压力0.8-1.0MPa、冷却水压力0.3-0.6 MPa。
2.经0.22μm滤器过滤。
3.稀配结束至灌封结束操作时间不超过4小时。
1.灭菌温度117℃、恒温时间35分钟、F0≥12、冷却温度(40-60℃)。
2.洗灌封结束至灭菌开始操作时间不超过2小时。
1.印字正确、端正、清晰、整洁、无漏印(贴)。
2.每箱装2份说明书,1份合格证。
葡萄糖氯化钠注射液工艺规程

宁波市xx制药有限公司输液车间管理文件1.目的:编制规范化、标准化的工艺规程,作为全面指导生产和控制质量的基准性技术文件。
2.范围:葡萄糖氯化钠注射液生产和质量控制的全过程。
3.责任3.1 输液车间负责生产全过程。
3.2 质量管理部门负责质量控制全过程。
3.3 工程部负责提供工艺用水、电、汽及洁净空气等。
4.管理内容11-14.1 生产工艺流程其中:粗洗、浓配采用10万级稀配、轧盖采用1万级灌装、压塞采用局部100级4.2 操作过程及工艺条件4.2.1 理瓶根据生产量准备相应数量的瓶子,脱去外包装后正立于理瓶台上,挑选出破损瓶子,待理瓶台集满瓶子后可开动理瓶机传送带,送瓶。
4.2.2 外洗4.2.2.1 开启饮用水水源,启动外洗机主机开关进行外洗操作。
4.2.2.2 检查经过外洗的输液瓶,将破损瓶及时挑出,放在指定地点。
4.2.3 粗洗4.2.3.1 开启电源;将水箱和储水箱注满水至溢水管顶部,水温控制到50~60℃,开启水泵,打开喷淋水控制阀(以能将空瓶注满水为准),启动超声波、输液轨道和主机,进行粗洗操作。
4.2.3.2 操作过程中,碰到紧急情况,应按下紧急停车按钮,立即停车,检查调整后再开机。
4.2.4 精洗4.2.4.1 检查过滤后注射用水可见异物,合格后方可进行精洗操作。
4.2.4.2 打开电源开关,将储水罐注满水,水温控制到50~60℃,调节新鲜水压力0.2~0.4MPa,调节压缩空气控制阀至压力0.2~0.4MPa,打开水泵,调节循环水压至0.2~0.4MPa,开启主机,进行精洗操作。
4.2.4.3 检查精洗后玻璃瓶可见异物合格,注射用水残存应不超过2滴,输液瓶方可进行灌装。
4.2.4.4 精洗好的瓶子存放时间不超过30分钟,否则重新清洗。
4.2.5 配料4.2.5.1 浓配4.2.5.1.1 核对原辅料品名、规格、批号、数量、检验报告单,确认无误后按生产指令书上的处方量进行称量,称量过程要有人复核。
甘油氯化钠注射液生产工艺规程

技术标准本品为甘油和氯化钠制成的灭菌水溶液。
1 品名: 甘油氯化钠注射液2 剂型: 大容量注射剂3 规格: 250ml:甘油25g与氯化钠2.25g4 代码:Y4115处方:5·1基准处方甘油 100.0g氯化钠 9.0g注射用水至 1000ml5·2 标准生产量:1800000 ml/批所用的原辅料及数量名称代码数量甘油Y119 180Kg(理论投料量)氯化钠Y102 16.2Kg针用活性炭F101 900g注射用水F108 至1800000 ml甘油原料折算公式:实际投料量=理论投料量含量6 生产工艺及操作要求:6·1 配制(万级、温度18~26℃、湿度45~65%):本工序包括称量、浓配、稀配等。
6·1·1 称量:在备料间根据指令核对原辅料品名、规格、批号、生产厂家、数量,与本公司检验报告单一致。
称量前校准天平、电子秤并检查是否在效期内。
按处方要求进行原辅料的称量,并填写称量记录。
剩余原辅料扎紧袋口,标明原辅料名称、批号、剩余量、使用人,放置于暂存架。
换品种清场时,将剩余料密封,贴上卡片,标明名称、规格、批号、数量、日期,退回脱包间,返至仓库。
6·1·2 浓配:取规定量甘油在浓配间投入到放有适量注射用水(70~85℃)的SH-Ⅰ浓配罐中,使成35%~40%的浓溶液,再加入规定量氯化钠,搅拌溶解,加入0.03%(g/ml,以稀配体积计)的针用活性炭,搅拌混匀,煮沸(100℃)30分钟,稍冷,用钛棒过滤器加压过滤,内循环10分钟,泵入稀配罐。
6·1·3 稀配:在稀配间向SH-Ⅰ稀配罐中加注射用水至全量的约80%,加0.02%(g/ml,以稀配体积计)的针用活性炭,补加注射用水至全量,搅拌、回流15分钟,测pH值(规定:5.0~6.0,若不符合规定用稀盐酸或1M氢氧化钠调整)、含量(甘油为98.0%~101.0%、氯化钠为98.5%~101.0%)符合规定后,降温至70~80℃,用钛棒过滤器和0.45μm的膜滤芯加压过滤,终端用0.45μm的膜滤芯过滤至灌装。
- 1、下载文档前请自行甄别文档内容的完整性,平台不提供额外的编辑、内容补充、找答案等附加服务。
- 2、"仅部分预览"的文档,不可在线预览部分如存在完整性等问题,可反馈申请退款(可完整预览的文档不适用该条件!)。
- 3、如文档侵犯您的权益,请联系客服反馈,我们会尽快为您处理(人工客服工作时间:9:00-18:30)。
目录1.产品简介2.处方和依据3.产品工艺流程图4.主要房间设备说明表5.工艺质量监控点6.原辅包装材料清单、质量标准及批量处方7.工艺操作要求和技术参数8.中间产品质量标准和贮存9.成品质量标准和贮存10.劳动组织与岗位定员11.文件变更表12.附件1. 产品简介1.1 品名氯化钠注射液1.2 代码 00-0091.3 剂型大容量注射剂1.4 规格 250ml:2.25g1.5 包装聚丙烯输液瓶装,40瓶/箱1.6 贮藏密闭保存1.7 有效期 36个月1.8 批次量 16000瓶/批1.9 生产线 J线2. 处方和依据2.1 处方氯化钠 9g ;注射用水加至1000ml 2.2 依据国家食品药品监督管理局批件批准文号:国药准字H200932373.产品工艺流程图D级区C级区C级背景下的A级区一般区7. 工艺操作要求和技术参数7.1 浓配7.1.1 生产前检查:每日生产前检查生产设备、过滤器已清洁、灭菌,状态标志明显;所用称量器具、各类仪表、仪器在校验周期内,标志明显;上批清场应合格,并将上批清场合格证副本附于记录之前;每批生产前检查设备情况应正常;已撤去上批生产状态标志、无上批生产记录和与本批生产无关的遗留物,生产现场卫生整洁;换好本批生产状态标志,操作文件、批生产记录应齐全;本批所需原、辅料已备齐,并与称量记录一致。
7.1.2 原辅料的领用:车间领料人员按生产部下发的批生产指令的限料量由仓库领料至车间物流通道外清间。
所领到的原辅料脱除外包装后用纯化水擦拭清洁,然后用75%的乙醇擦拭消毒后进入缓冲间。
领料人员将物料放在缓冲间分隔货架上,但本人不得越过隔离线,由浓配人员接收按“物料交接单”核对无误后,放入原辅料中转间,活性炭放入调炭间,登记岗位物料领用表,质量监督员监督。
7.1.3 计算:按批量和处方计算实际投料量,并复核。
原料实际投料量(Kg)=每升投料量(Kg)×配制量(L)浓配活性炭实际投料量(Kg)=配制量(L)×0.02%(Kg/L)稀配活性炭实际投料量(Kg)=配制量(L)×0.01%(Kg/L)7.1.4 称量、调炭:岗位称量人员、复核人员不得兼任,称量前按物料交接单对物料逐一核对。
操作员开启原辅料称量柜风机,按照由批量处方称量氯化钠用量后,由复核员再次复核称量并记录复核重量,质量监督员确认;在活性炭调碳操作台上,按照由批量处方计算得出的实际投料量分别称取浓、稀配活性炭用量后,由复核员再次复核称量并记录复核重量,质量监督员确认。
称量好的活性炭分别放入洁净调炭桶内,于活性炭调碳操作台上加注射用水搅拌调至糊状。
称量结束,填写称量记录,操作员、复核员、质量监督员对所填记录分别核对、签名。
7.1.5清洗:每日第一批生产前打开喷淋阀,用注射用水淋洗浓配罐,每次1分钟,淋洗3次,每次淋洗水下排完全。
7.1.6 浓配:打开注射用水阀向浓配罐注入注射用水(约300L),开启搅拌,将复核好的原料氯化钠投入浓配罐,以便使氯化钠充分溶解,加入活性炭0.02%(W/V),用注射用水清洗调炭桶和料勺无炭渍,清洗水加入浓配罐,煮沸药液并维持沸腾10分钟后,关闭蒸汽阀,冷却药液温度至70-75℃。
7.1.7清场7.1.7.1批清场:每批生产结束后,清理现场遗留物,撤去本批生产状态标志、记录等,将本批清场合格证正本附于记录之后;7.1.7.2日清场及更换品种清场:本日剩余原辅料日清场时登记数量转下批,更换品种清场时登记数量并做转下批、转线或退库处理;清理生产现场遗留物,撤去本批生产状态标志、相关生产记录等;按SOP-03219 07《配制系统在线清洗(钝化)、消毒、灭菌操作程序》对浓配系统进行在线清洗、消毒;钛棒按SOP-03221 07《钛棒处理操作程序》清洗、灭菌;清洁容器具及厂房;由工序负责人和质量监督员检查确认合格后,质量监督员签发清场合格证。
7.2稀配7.2.1 生产前检查:每日生产前检查生产设备、过滤器已清洁、灭菌,状态标志明显;对终端过滤器进行起泡点试验应合格,附检测记录;所用称量器具、各类仪表、仪器在校验周期内,标志明显;上批清场应合格,并将上批清场合格证副本附于记录之前;每批生产前检查设备情况应正常;已撤去上批生产状态标志、无上批生产记录和与本批生产无关的遗留物,生产现场卫生整洁;换好本批生产状态标志,操作文件、批生产记录应齐全。
7.2.2 清洗:每日第一批生产前打开喷淋阀,用注射用水淋洗稀配罐,每次1分钟,淋洗3次,每次淋洗水下排完全。
于稀配罐加入300Kg注射用水,将注射用水送到灌装机,从灌装下排完全。
7.2.3 稀配:向稀配罐加入约2/3配制量的注射用水,开启搅拌,将浓配的药液经钛棒脱炭过滤后送至稀配罐,淋洗浓配罐3次,淋洗液打入稀配罐,送完后加活性炭0.01%(W/V),用注射用水清洗调炭桶和料勺无炭渍,清洗水加入稀配罐,停止搅拌,向稀配罐内加入注射用水至配制量,开启搅拌,药液经钛棒过滤器脱炭、0.45μm过滤器回滤20分钟,同时将药液冷却到40-60℃,然后取样,检测氯化钠的含量、pH值及药液异物检查(若pH不在规定范围内要进行适当调整,pH调整剂为1mol/LNaOH或1mol/LHCL),合格后待灌装。
每批药液浓配开始至稀配结束操作时间不超过2.5小时,超过规定时间按偏差处理。
7.2.4 注意:配制操作过程中操作人员要及时填写记录,复核后经质量监督员对所填记录分别核对、签名。
浓配液打入稀配时注意阀门开启情况并复核,避免差错;所使用的容器具应洁净并在期限内使用;岗位物料妥善保管和存放;取样时取样口应适当排放药液冲洗取样杯,以保证样品的代表性。
7.2.5 物料衡算:每批生产应对氯化钠进行物料平衡计算,超过衡算范围须分析原因。
实际配制量(L)×含量(g/ml)衡算公式(%)= ×100%原料投料量(Kg)物料衡算范围:97.0%~103.0%7.2.6清场7.2.6.1批清场:每批生产结束后,清理现场遗留物,撤去本批生产状态标志、记录等,将本批清场合格证正本附于记录之后;7.2.6.2日清场及更换品种清场:清理生产现场遗留物,撤去本批生产状态标志、相关生产记录等;按SOP-03219 07《配制系统在线清洗(钝化)、消毒、灭菌操作程序》对稀配系统进行在线清洗、消毒;钛棒按SOP-03221 07《钛棒处理操作程序》清洗、灭菌;滤器按SOP-03220 08《过滤器清洗灭菌操作程序》进行清洗、灭菌;清洁容器具及厂房;由工序负责人和质量监督员检查确认合格后,质量监督员签发清场合格证。
7.3 洗灌封7.3.1 生产前检查:每日生产前检查生产设备已清洁、消毒,状态标志明显;所用各类仪表、仪器在校验周期内,标志明显;上批清场应合格,并将上批清场合格证副本附于记录之前;终端过滤器状态标志明显;每批生产前检查设备情况应正常;已撤去上批生产状态标志、无上批生产记录和与本批生产无关的遗留物,生产现场卫生整洁;换好本批生产状态标志,操作文件、批生产记录应齐全。
7.3.2 领料:车间领料人员按生产部下发的批生产指令的限料量领料。
在外清间脱除聚丙烯组合盖的外包装,用纯化水擦拭清洁外表面,然后用75%的乙醇擦拭消毒后通过缓冲间进入洁净区储盖间。
洗灌封岗位操作人员收料后按“物料交接单”核对无误后将聚丙烯组合盖整齐的码放到储盖间,并登记岗位物料领用表。
7.3.3 操作:7.3.3.1打开洗灌封联动线电源和层流罩,打开负离子风道,压缩空气洗瓶压力:(0.8—1.0MPa)、冷却水压力(0.3—0.6MPa);开启封口机加热板电源,预热3分钟使加热温度均匀,于振荡器内加入聚丙烯组合盖。
调试洗瓶压缩空气压力符合要求后上瓶、洗瓶。
药液经0.22μm滤器过滤后灌装,设定灌装速度在150-200瓶/分钟,启动灌装机,检查药液可见异物和装量,合格后开始生产。
每批药液稀配结束至灌封结束操作时间不超过4小时,超过规定时间按偏差处理。
7.3.3.2灌装可见异物检查:每批生产前,岗位操作人员对应36个灌装头取灌装后的塑瓶36瓶按“可见异物检查法”,不得有可见异物,质量监督员在生产过程监督抽查“可见异物”项。
7.3.3.3灌装装量检查:岗位操作人员每批生产前期用容量法、生产过程中用称重法,分别对36个灌装头取样,检查装量。
容量法装量检查范围(250ml-270ml);称重法装量检查范围(250g-270g),若超出范围要进行适当调整。
7.3.3.4焊盖外观检查:岗位操作人员每30分钟检查焊盖外观,无漏液、碳化。
质量监督员每批抽查。
7.3.3.5注意:操作过程中操作人员要及时填写记录,复核后经质量监督员对所填记录分别核对、签名。
进入洁净区物料需脱外包、清洁、消毒后进入;生产过程根据各项检查情况调整设定参数使洗灌封产品质量符合要求;及时添加聚丙烯组合盖,保持生产连续性;因塑瓶中间品易产生静电吸附,操作过程应注意个人卫生和岗位卫生,A级层流罩下的操作人员不得裸手操作。
7.3.4 物料衡算:每批生产应对灌封后的产品进行物料平衡计算,超过衡算范围须分析原因。
「灌封交灭菌量(瓶)+ 灌封报废瓶数(瓶)」×平均装量(ml) 衡算公式(%)= ×100%配制交灌封量(L)×1000物料衡算范围:98.0%~102.0%。
7.3.5清场:每日生产结束清除振荡器和轨道内聚丙烯组合盖密封保存在储盖间,清洁、消毒振荡器和轨道;按SOP-03307 01《洗灌封联动线清洁、消毒、灭菌操作程序》清洁、消毒/灭菌洗灌封系统;拆除终端过滤器送至稀配班组按SOP-03222 07《滤器起泡点试验操作程序》进行起泡点试验,按SOP-03220 08《过滤器清洗灭菌操作程序》进行清洗、灭菌;清洁容器具及厂房、地面;检查水、电、气(汽);每批生产结束岗位操作人员清理本批产品,撤去本批生产状态标志及相关生产记录等;废物料放入指定存放间或移交;由工序负责人和质量监督员检查确认合格后,质量监督员签发清场合格证。
7.4 灭菌7.4.1 生产前检查:每日生产前检查生产设备已清洁,状态标志明显;所用各类仪表、仪器在校验周期内,标志明显;上批清场应合格,并将上批清场合格证副本附于记录之前;每批生产前检查设备情况应正常;已撤去上批生产状态标志、无上批生产记录和与本批生产无关的遗留物,生产现场卫生整洁;换好本批生产状态标志,操作规程、批生产记录应齐全;检查压缩空气、冷却水、蒸汽压力是否正常;核对待灭菌产品的品名、规格、批号、数量,准备好打印记录纸。
7.4.2 码瓶:操作人员将每批灌封后的产品手工直立码放在灭菌车;不得上下重叠码放,已码放产品待灭菌车要挂上标示牌标明顺序号。