第二章 质量分析与控制方法
软件开发过程的质量控制和管理

软件开发过程的质量控制和管理第一章:引言在不断发展的数字时代,软件已成为人们生活和工作中必不可少的工具。
软件开发不再是一个独立的技能,而是需要多个专业人士的合作完成。
软件开发过程的质量控制和管理已经成为开发高质量软件的必要措施。
在这篇文章中,我们将了解软件开发过程中的质量控制和管理。
第二章:软件开发过程中的质量控制质量控制是确保软件产品满足特定要求和标准的过程。
在软件开发过程中,质量控制需要在整个生命周期中进行。
软件开发过程中的质量控制主要包括以下几个方面:1.需求定义和分析需求定义和分析是软件开发过程中最重要的环节之一。
在这个阶段,开发团队需要与客户密切合作,确认需求和相关标准。
这是确保软件能够满足客户需求的关键步骤。
必须对需求进行仔细的分析和评估,确保需求的准确性、完整性和一致性。
2.设计软件设计是开发过程中的另一个重要环节,它是根据已经确认的需求创建软件体系结构的过程。
在这个阶段需要考虑性能、可靠性和可维护性等因素。
还可以通过软件建模和模拟来评估设计和架构的有效性。
3.编码/代码审查编码是将设计转化为实际软件代码的过程。
编码需要遵循标准和最佳实践,确保代码质量和可扩展性。
代码审查还可以在编码过程中进行,以确保代码符合标准。
4.测试测试是确保软件符合质量标准的重要工具。
测试可以通过不同的方法进行,如单元测试、集成测试、系统测试和验收测试等。
测试可以检测软件产品中的错误和潜在的问题,并在开发过程中进行修复。
第三章:软件开发过程中的质量管理软件开发过程的质量管理是一种管理方法,旨在确保软件产品能够满足客户和相关标准的要求。
质量管理包括以下几个方面:1.项目管理在软件开发过程中,项目管理是确保产品质量和按时完成的重要组成部分。
项目管理涉及计划、协调和跟踪项目进展,以确保项目按时交付、满足客户需求。
2.质量计划质量计划是确定质量标准、程序和流程的过程。
质量计划必须在项目开始前制定,以确保项目的顺利进行。
gmp指南第二版质量控制实验室目录
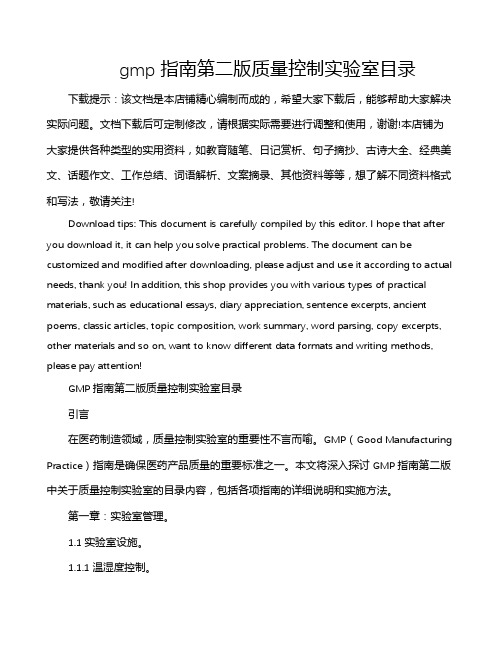
gmp指南第二版质量控制实验室目录下载提示:该文档是本店铺精心编制而成的,希望大家下载后,能够帮助大家解决实际问题。
文档下载后可定制修改,请根据实际需要进行调整和使用,谢谢!本店铺为大家提供各种类型的实用资料,如教育随笔、日记赏析、句子摘抄、古诗大全、经典美文、话题作文、工作总结、词语解析、文案摘录、其他资料等等,想了解不同资料格式和写法,敬请关注!Download tips: This document is carefully compiled by this editor. I hope that after you download it, it can help you solve practical problems. The document can be customized and modified after downloading, please adjust and use it according to actual needs, thank you! In addition, this shop provides you with various types of practical materials, such as educational essays, diary appreciation, sentence excerpts, ancient poems, classic articles, topic composition, work summary, word parsing, copy excerpts, other materials and so on, want to know different data formats and writing methods, please pay attention!GMP指南第二版质量控制实验室目录引言在医药制造领域,质量控制实验室的重要性不言而喻。
数控机床轴类课程设计
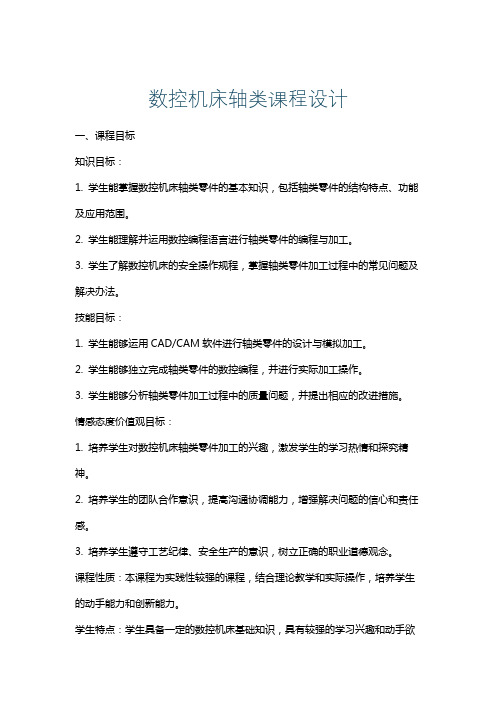
数控机床轴类课程设计一、课程目标知识目标:1. 学生能掌握数控机床轴类零件的基本知识,包括轴类零件的结构特点、功能及应用范围。
2. 学生能理解并运用数控编程语言进行轴类零件的编程与加工。
3. 学生了解数控机床的安全操作规程,掌握轴类零件加工过程中的常见问题及解决办法。
技能目标:1. 学生能够运用CAD/CAM软件进行轴类零件的设计与模拟加工。
2. 学生能够独立完成轴类零件的数控编程,并进行实际加工操作。
3. 学生能够分析轴类零件加工过程中的质量问题,并提出相应的改进措施。
情感态度价值观目标:1. 培养学生对数控机床轴类零件加工的兴趣,激发学生的学习热情和探究精神。
2. 培养学生的团队合作意识,提高沟通协调能力,增强解决问题的信心和责任感。
3. 培养学生遵守工艺纪律、安全生产的意识,树立正确的职业道德观念。
课程性质:本课程为实践性较强的课程,结合理论教学和实际操作,培养学生的动手能力和创新能力。
学生特点:学生具备一定的数控机床基础知识,具有较强的学习兴趣和动手欲望,但对实际操作经验尚不足。
教学要求:教师需结合学生特点,注重理论与实践相结合,充分调动学生的主观能动性,提高学生的实际操作技能。
同时,关注学生的情感态度价值观培养,使学生在学习过程中形成良好的职业素养。
通过分解课程目标为具体的学习成果,为后续的教学设计和评估提供依据。
二、教学内容1. 轴类零件概述:介绍轴类零件的概念、分类及应用,使学生了解轴类零件在数控加工中的重要性。
教材章节:第一章 轴类零件概述2. 轴类零件结构设计:讲解轴类零件的结构特点、设计原则及设计方法,培养学生具备初步的轴类零件设计能力。
教材章节:第二章 轴类零件结构设计3. 数控编程基础:教授数控编程的基本概念、编程方法和编程技巧,为学生编写轴类零件数控程序奠定基础。
教材章节:第三章 数控编程基础4. 数控加工工艺:分析轴类零件的加工工艺,包括刀具选择、加工参数设置等,提高学生对加工过程的控制能力。
公司质量控制管理制度(三篇)
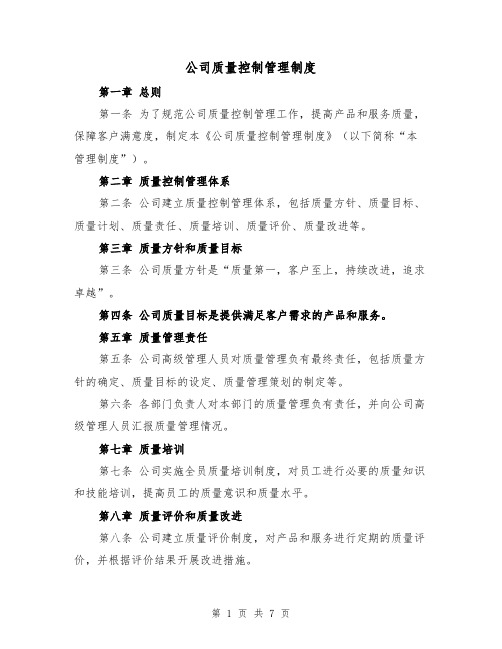
公司质量控制管理制度第一章总则第一条为了规范公司质量控制管理工作,提高产品和服务质量,保障客户满意度,制定本《公司质量控制管理制度》(以下简称“本管理制度”)。
第二章质量控制管理体系第二条公司建立质量控制管理体系,包括质量方针、质量目标、质量计划、质量责任、质量培训、质量评价、质量改进等。
第三章质量方针和质量目标第三条公司质量方针是“质量第一,客户至上,持续改进,追求卓越”。
第四条公司质量目标是提供满足客户需求的产品和服务。
第五章质量管理责任第五条公司高级管理人员对质量管理负有最终责任,包括质量方针的确定、质量目标的设定、质量管理策划的制定等。
第六条各部门负责人对本部门的质量管理负有责任,并向公司高级管理人员汇报质量管理情况。
第七章质量培训第七条公司实施全员质量培训制度,对员工进行必要的质量知识和技能培训,提高员工的质量意识和质量水平。
第八章质量评价和质量改进第八条公司建立质量评价制度,对产品和服务进行定期的质量评价,并根据评价结果开展改进措施。
第九章质量控制管理的流程第九条公司质量控制管理按照以下流程进行:1.质量计划制定:制定年度质量计划,明确各部门的质量目标和质量计划。
2.质量目标分解:分解公司质量目标为各部门的质量目标。
3.质量控制措施制定:制定相应的质量控制措施,包括质量检查、质量测试、质量培训等。
4.质量控制执行:执行质量控制措施,确保产品和服务质量符合要求。
5.质量评价与改进:对产品和服务进行定期评价,根据评价结果制定改进措施。
第十章质量责任追究第十一条对于严重影响产品质量或服务质量的责任事故,公司将追究相关责任人的责任,并采取相应的处理措施。
第十二条对于质量问题的处理,公司将追究相关部门负责人的责任,并采取适当的纠正措施。
第十三章附则第十四条本管理制度自颁布日起执行,公司内部质量控制管理细则与本管理制度不一致的部分,以本制度为准。
第十五条本管理制度的解释权归公司高级管理人员所有。
工程质量、进度、安全文明施工管控办法

第一部分工程质量管控办法第一章总则第一条为了加强公司建设工程质量管理,切实落实“以质量求效益,以品牌求发展”的管理工作方针,建立质量管理网络,明确职责,使公司建设工程质量管理活动做到标准化、规范化、科学化,确保公司建设工程质量,特制定本管理制度。
第二条本制度适用于公司承建的土木工程、建筑工程、园林工程、市政工程、线路管道、设备安装和装修工程等的质量管理工作。
第二章质量管理组织体系第三条实行总经理领导下的项目部管理、施工现场管理、施工作业班组管理的三级质量管理组织体系,以保证质量管理工作协调有效地进行。
第四条工程部经理向总经理负责,对公司的工程质量、技术负直接的主管领导责任。
第五条项目技术负责人协助工程部经理管理工程质量、技术,协调工程各专业之间技术矛盾,处理和解决重大技术问题和关键问题。
第六条工程部各施工管理人员在工程部经理领导下开展工程质量管理工作,对质量进行控制,组织质量评价,研究和推广先进的质量管理控制方法,对工程质量负监督管理责任。
第三章质量管理方针、方法、标准和工作流程第七条工程质量管理实行“质量第一,预防为主”的方针。
第八条工程质量管理实行“计划、执行、检查、处理”(PDCA)循环工作方法,不断改进过程控制。
第九条工程质量管理标准1、符合公司制定的工程项目质量目标和《工程项目质量管理计划书》的要求。
2、符合与勘察、设计、施工、监理、材料设备供应商签定的合同及补充协议的约定和要求。
3、符合经批准的设计施工图和技术文件的要求。
4、符合工程建设各项规范和技术标准及政府部门有关质量管理的规章制度。
5、保证按项目任务书、设计图、合同规定的数量、质量完成工程,顺利通过验收,交付使用,实现使用功能。
第十条工程质量管理按下列工作流程实施:(一)确定工程项目质量目标。
1、每个项目在签订施工合同后,由工程部经理负责组织各工程技术人员参与,根据公司的具体情况,针对工程技术标准、材料设备的规格档次、使用年限、工程规模、达到的使用功能等质量标准,协调工期、成本、质量三者矛盾,制定出符合实际情况的项目质量目标。
矿石质量分析与质量控制
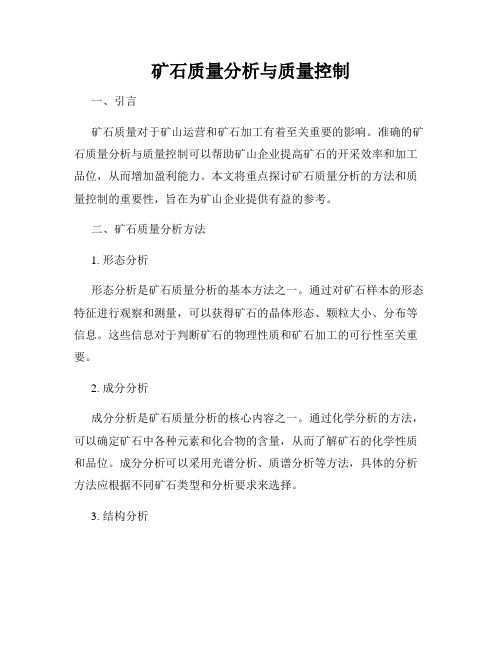
矿石质量分析与质量控制一、引言矿石质量对于矿山运营和矿石加工有着至关重要的影响。
准确的矿石质量分析与质量控制可以帮助矿山企业提高矿石的开采效率和加工品位,从而增加盈利能力。
本文将重点探讨矿石质量分析的方法和质量控制的重要性,旨在为矿山企业提供有益的参考。
二、矿石质量分析方法1. 形态分析形态分析是矿石质量分析的基本方法之一。
通过对矿石样本的形态特征进行观察和测量,可以获得矿石的晶体形态、颗粒大小、分布等信息。
这些信息对于判断矿石的物理性质和矿石加工的可行性至关重要。
2. 成分分析成分分析是矿石质量分析的核心内容之一。
通过化学分析的方法,可以确定矿石中各种元素和化合物的含量,从而了解矿石的化学性质和品位。
成分分析可以采用光谱分析、质谱分析等方法,具体的分析方法应根据不同矿石类型和分析要求来选择。
3. 结构分析结构分析可以揭示矿石中晶体结构、微观结构、晶体缺陷等方面的信息。
通过X射线衍射分析、电子显微镜等技术,可以对矿石的结构进行精确测定,以帮助矿山企业了解矿石的稳定性、可加工性等特性。
4. 热力学分析热力学分析可用于研究矿石的热力学性质和矿石加工过程中的热力学变化。
通过热分析仪器,可以测定矿石的热容、热导率、热膨胀系数等物理量,为矿石加工提供基本数据。
三、质量控制的重要性1. 提高矿石加工效率准确的矿石质量分析结果可以帮助矿山企业调整矿石加工流程,优化工艺参数,提高加工效率。
例如,根据矿石中有价值元素的含量,可以合理选择提矿方式和选矿条件,从而实现更高的选矿回收率。
2. 降低矿石加工成本矿石质量控制可以有效降低矿石加工成本。
通过对矿石质量进行精确控制,可以避免矿石的过度破碎和浪费,减少能源和矿石消耗,降低生产成本。
3. 提高矿石产品质量准确的矿石质量分析和有效的质量控制可以提高矿石产品的质量。
通过合理选矿和优化加工工艺,可以降低矿石中的杂质含量,提高产品品位和纯度,增加产品附加值。
4. 保证合规符合标准在矿石开采和加工过程中,合规符合标准是一项重要的要求。
计算机软件的代码审查与质量控制方法

计算机软件的代码审查与质量控制方法第一章:引言计算机软件的开发过程中,代码审查和质量控制是确保软件质量的重要环节。
代码审查是指对程序代码的评估和检查,以发现潜在的错误和缺陷。
而质量控制是指为了确保软件产品能够满足需求和质量标准而采取的一系列措施和方法。
本文将介绍代码审查和质量控制方法的概念和重要性,并详细讨论各种方法的具体内容。
第二章:代码审查方法代码审查是一种对程序代码进行交流和反馈的过程,旨在保证代码的正确性、可读性和可维护性。
常见的代码审查方法包括如下几种:2.1 静态代码审查静态代码审查是指通过对代码的静态分析来发现潜在的错误和问题。
这种方法通过检查代码中的语法错误、不一致性、潜在的性能问题等来评估代码的质量。
常用的静态代码审查工具有Lint、PMD、CheckStyle等。
2.2 动态代码审查动态代码审查是指通过运行代码并观察其行为来评估代码的质量。
这种方法通过检查代码的执行过程、内存使用情况、异常处理等来发现潜在的问题。
常用的动态代码审查工具有Valgrind、Coverity等。
2.3 人工代码审查人工代码审查是指由开发人员手动检查代码,发现潜在的错误和问题。
这种方法通过对代码中的逻辑错误、安全漏洞、性能问题的评估来提高代码质量。
人工代码审查需要有经验丰富的开发人员参与,并配合一些代码审查工具。
第三章:质量控制方法质量控制是指为了确保软件产品能够满足需求和质量标准而采取的一系列措施和方法。
常见的质量控制方法包括如下几种:3.1 单元测试单元测试是指对软件中的最小代码单元进行测试,以验证其功能是否正确。
这种方法通过编写测试用例并运行代码来发现和修复潜在的错误。
常用的单元测试框架有JUnit、Pytest等。
3.2 集成测试集成测试是指对软件中的多个模块进行测试,以验证各个模块之间的协同工作是否正确。
这种方法通过模拟实际运行环境,并运行整个软件来发现和修复潜在的错误。
常用的集成测试框架有Selenium、Jenkins等。
质量控制方案(2篇)
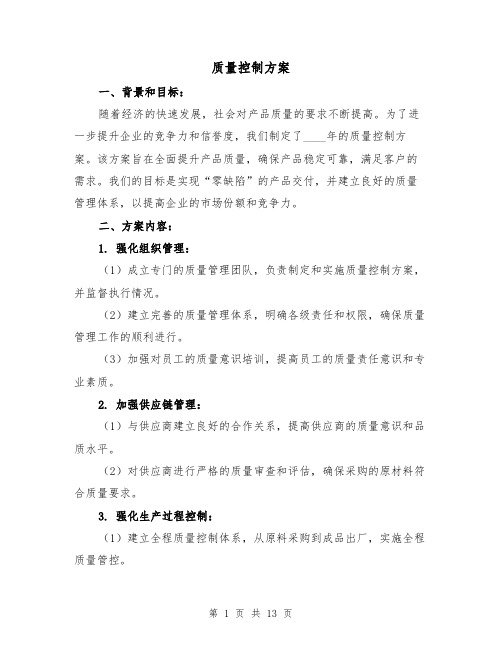
质量控制方案一、背景和目标:随着经济的快速发展,社会对产品质量的要求不断提高。
为了进一步提升企业的竞争力和信誉度,我们制定了____年的质量控制方案。
该方案旨在全面提升产品质量,确保产品稳定可靠,满足客户的需求。
我们的目标是实现“零缺陷”的产品交付,并建立良好的质量管理体系,以提高企业的市场份额和竞争力。
二、方案内容:1. 强化组织管理:(1)成立专门的质量管理团队,负责制定和实施质量控制方案,并监督执行情况。
(2)建立完善的质量管理体系,明确各级责任和权限,确保质量管理工作的顺利进行。
(3)加强对员工的质量意识培训,提高员工的质量责任意识和专业素质。
2. 加强供应链管理:(1)与供应商建立良好的合作关系,提高供应商的质量意识和品质水平。
(2)对供应商进行严格的质量审查和评估,确保采购的原材料符合质量要求。
3. 强化生产过程控制:(1)建立全程质量控制体系,从原料采购到成品出厂,实施全程质量管控。
(2)加强对生产设备的维护和保养,确保设备的正常运转和性能稳定。
(3)引进先进的生产技术和工艺,提高产品的生产效率和质量水平。
4. 加强检验检测:(1)建立完善的检验检测体系,对产品进行全面的检验检测。
(2)采用先进的检测设备和技术,提高检验检测的准确性和可靠性。
(3)加强对检验检测人员的培训,提高其专业水平和技能能力。
5. 加强客户反馈和投诉处理:(1)建立健全的客户反馈和投诉处理机制,及时解决客户提出的问题和意见。
(2)对客户的反馈和投诉进行分析和总结,及时改进产品和服务。
6. 引入质量管理工具和方法:(1)引入先进的质量管理工具和方法,如六西格玛、PDCA等,提高质量管理水平。
(2)加强对质量管理工具和方法的培训,提高员工的应用能力和效果。
7. 定期评估和改进:(1)定期对质量控制方案进行评估和改进,提高方案的可行性和有效性。
(2)建立定期的质量管理绩效评估机制,激励员工积极参与质量管理工作。
三、资源投入:为实施以上质量控制方案,我们将投入适当的资源,包括人力、物力和财力。
医学临床检验的质量分析及其控制方法
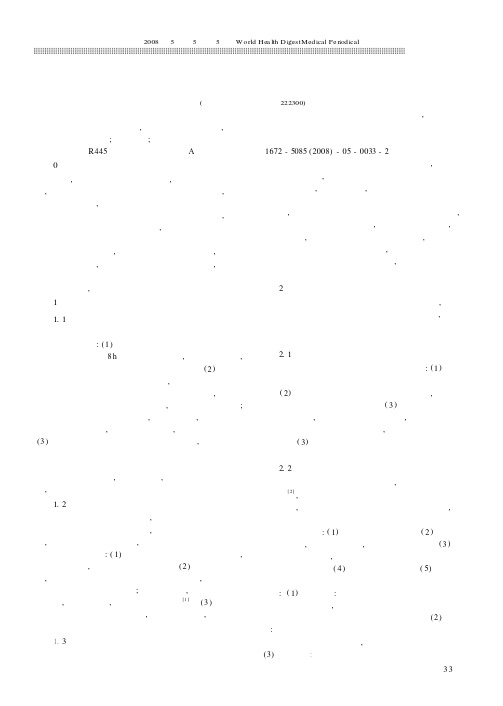
岗前培训 。上岗前要 系 统学习 检验 理论 知识 ,并熟 练掌 握各项检验技能 ,熟悉常用检验仪器 、设备试剂的 工作原 理及使用方 法 ,包 括精 确 度 ,明 确 质量 控 制和 抗 干 扰性 等。同时还应掌握检验仪器、设备的日常维护及故障维 修技术 ,保证检验工作的质量和 效率 。对于检验 标准 ,每 个检验工作人员都要心中有数 ,做到 判定标准统 一 ,尽可 能减小误差 ,使化验结果成为“真值 ”。另外 ,如果要想得 到一个有价值的“真值 ”检验数 据 ,还 要进行 医学 检验结 果分析前和分析后 的质 量控制 保证 ,以便 去除 以上 可能 影响临床检验结果的若干因素。
2 在临床检验中采用循证技术
1 影响检验质量的因素分析
1. 1 标本质量分析
影响标本质量的因素分为内在因素和外在因素。主 要包括以下因素 : (1 )一般 要求 在晨起 空腹 时采集 标本 。 空腹标本是指进食 8 h 后 所采 集的标 本 ,空 腹时间 过长 , 其标本同样不能准确反 映机体 的真实 情况 。 (2 )静 脉血 标本采集时扎止血 带时间 不宜 过长 , 以避 免血 管内 压增 高引起血管内血液 中的小 分子 物质 流人 组织 液 ,而 且局 部的缺氧也能引起血液成份的改变 ,影 响临床检验 结果 ; 患者静脉点滴时最好不要采血 ,如确为 必须 ,应在静 脉点 滴的对侧肢体采血 ,以免 血样 被稀 释 ,造 成很 大的 误差 。 (3 )尿样标本尿液是肾功能活动的最终产物 ,人体 绝大多 数的生物化学变化都能在尿中直接或间接得到反映。试 验性尿标本应按照试验目的和要求不同按时、按量留取。 由于尿中成份波动大 ,所含物质多 ,检测 时易相互发 生干 扰 ,所以应结合血生化检查结果综合分析 。
中外健康文摘 ·临床医师 2008年 5月 第 5卷第 5期 W orld H ea lth D igestMedical Pe riodical
第二章实验动物的遗传学分类及其质量控制
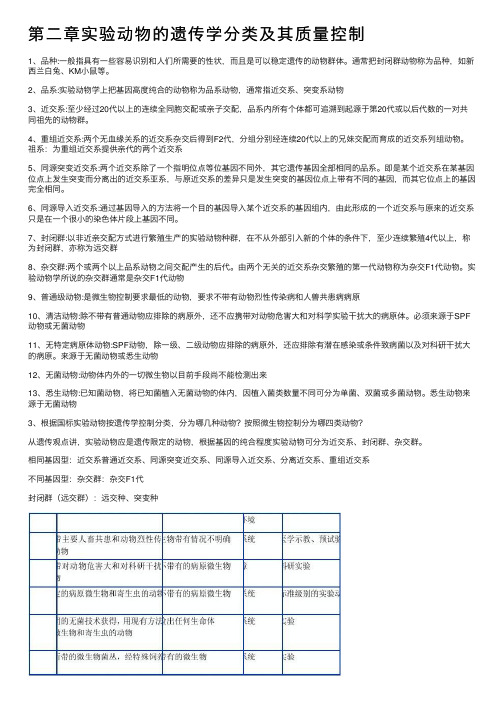
第⼆章实验动物的遗传学分类及其质量控制1、品种:⼀般指具有⼀些容易识别和⼈们所需要的性状,⽽且是可以稳定遗传的动物群体。
通常把封闭群动物称为品种,如新西兰⽩兔、KM⼩⿏等。
2、品系:实验动物学上把基因⾼度纯合的动物称为品系动物,通常指近交系、突变系动物3、近交系:⾄少经过20代以上的连续全同胞交配或亲⼦交配,品系内所有个体都可追溯到起源于第20代或以后代数的⼀对共同祖先的动物群。
4、重组近交系:两个⽆⾎缘关系的近交系杂交后得到F2代,分组分别经连续20代以上的兄妹交配⽽育成的近交系列组动物。
祖系:为重组近交系提供亲代的两个近交系5、同源突变近交系:两个近交系除了⼀个指明位点等位基因不同外,其它遗传基因全部相同的品系。
即是某个近交系在某基因位点上发⽣突变⽽分离出的近交系亚系,与原近交系的差异只是发⽣突变的基因位点上带有不同的基因,⽽其它位点上的基因完全相同。
6、同源导⼊近交系:通过基因导⼊的⽅法将⼀个⽬的基因导⼊某个近交系的基因组内,由此形成的⼀个近交系与原来的近交系只是在⼀个很⼩的染⾊体⽚段上基因不同。
7、封闭群:以⾮近亲交配⽅式进⾏繁殖⽣产的实验动物种群,在不从外部引⼊新的个体的条件下,⾄少连续繁殖4代以上,称为封闭群,亦称为远交群8、杂交群:两个或两个以上品系动物之间交配产⽣的后代。
由两个⽆关的近交系杂交繁殖的第⼀代动物称为杂交F1代动物。
实验动物学所说的杂交群通常是杂交F1代动物9、普通级动物:是微⽣物控制要求最低的动物,要求不带有动物烈性传染病和⼈兽共患病病原10、清洁动物:除不带有普通动物应排除的病原外,还不应携带对动物危害⼤和对科学实验⼲扰⼤的病原体。
必须来源于SPF 动物或⽆菌动物11、⽆特定病原体动物:SPF动物,除⼀级、⼆级动物应排除的病原外,还应排除有潜在感染或条件致病菌以及对科研⼲扰⼤的病原。
来源于⽆菌动物或悉⽣动物12、⽆菌动物:动物体内外的⼀切微⽣物以⽬前⼿段尚不能检测出来13、悉⽣动物:已知菌动物,将已知菌植⼊⽆菌动物的体内,因植⼊菌类数量不同可分为单菌、双菌或多菌动物。
电力系统的电能质量分析与控制
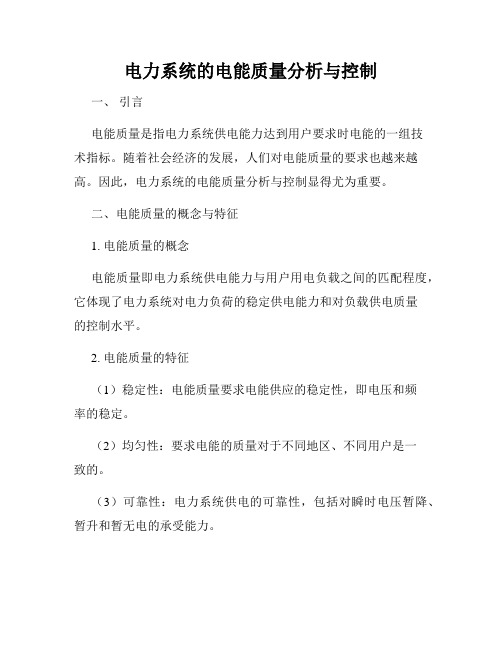
电力系统的电能质量分析与控制一、引言电能质量是指电力系统供电能力达到用户要求时电能的一组技术指标。
随着社会经济的发展,人们对电能质量的要求也越来越高。
因此,电力系统的电能质量分析与控制显得尤为重要。
二、电能质量的概念与特征1. 电能质量的概念电能质量即电力系统供电能力与用户用电负载之间的匹配程度,它体现了电力系统对电力负荷的稳定供电能力和对负载供电质量的控制水平。
2. 电能质量的特征(1)稳定性:电能质量要求电能供应的稳定性,即电压和频率的稳定。
(2)均匀性:要求电能的质量对于不同地区、不同用户是一致的。
(3)可靠性:电力系统供电的可靠性,包括对瞬时电压暂降、暂升和暂无电的承受能力。
(4)协调性:电源与负载之间的和谐性,即电源和负载在频率、电压、波形等特性上的协调。
三、电能质量的分类与分析1. 电压质量问题(1)瞬时电压变动瞬时电压变动是指电压在短时间内发生的波动,主要包括电压暂降、电压暂升和电压闪变等。
(2)谐波谐波是指电源电压或电流中频率是电源频率整数倍的非纯正弦组分。
(3)电压波形畸变电压波形畸变是指电源电压的波形在最佳的正弦形状上产生偏离。
2. 频率质量问题频率质量问题主要包括频率偏差和频率稳定度,分别表示电源电压频率与标称频率之间的差距和频率的变动程度。
3. 波形质量问题波形质量问题主要包括电源电压的波形畸变和波形失真程度。
波形畸变是指电压波形在最佳的正弦形状上发生偏离,而波形失真则是指电压波形受到非线性元件引起的扭曲。
4. 电能质量的分析方法(1)数据采集与监测通过采集电能质量监测点的电压和电流数据,可以了解电能质量的状况。
(2)参数计算与评估根据采集到的数据,计算出电能质量指标的数值,用于评估电能质量状况。
(3)故障诊断与分析通过监测数据的对比分析,可以找出电能质量的故障原因,进行故障诊断与分析。
四、电能质量的控制方法1. 电能质量优化技术(1)隔离技术采用隔离技术,将电源与用户隔离,减少电源中的电能质量问题对用户的影响。
高中教学质量控制管理细则(4篇)

高中教学质量控制管理细则第一章总则第一条为了提高高中教学质量,加强教育教学管理,确保学生全面素质的培养,特制订本管理细则。
第二章教师教学管理第二条高中教师应具备相应教育背景和专业知识,并具备一定的教学能力和教学经验。
第三条高中教师教学工作应遵循教育教学目标,以学生为中心,注重培养学生的创新能力和实践能力。
第四条高中教师教学应经常进行教学准备和培训,不断提高教学水平,更新教学理念和方法。
第五条高中教师应依据学生的不同特点和需求,科学安排教学内容和教学进程。
第六条高中教师应及时纠正学生成绩差、学习态度不端正等教育问题,引导学生正确学习和生活。
第七条高中教师应积极配合学校开展课程评价和教师评估工作,接受监督和指导。
第三章学生学习管理第八条学生应自觉遵守学校的各项规章制度,尊重教师和同学,培养良好的学习习惯和学习态度。
第九条学生应自觉参与各种学习活动,积极主动地学习新知识和新技能。
第十条学生应充分发挥自己的特长,实现自我价值的最大化。
第十一条学生应互相尊重,互相帮助,共同进步。
第十二条学生应认真对待成绩评估,接受成绩的公正评价。
第四章教学环境管理第十三条学校应提供良好的教学环境,包括教室设施、实验室设备等。
第十四条学校应加强对学生学习和生活的管理,确保学生在安全、健康的环境中学习和成长。
第十五条学校应定期检查和维护教学设施和设备,确保其正常运转。
第十六条学校应建立健全信息化教学管理系统,方便教师和学生进行教学和学习的互动。
第十七条学校应合理安排课程和作息时间,保证学生有充足的时间进行学习和休息。
第五章教学质量监控第十八条学校应建立定期的教学质量评估机制,对教师的教学进行评估和反馈。
第十九条学校应建立学生学习档案,全面记录学生的学习情况和成绩,为教育决策提供参考。
第二十条学校应定期进行学生综合素质评价,对学生的综合发展情况进行评估。
第二十一条学校应加强与家长的沟通和联系,及时反馈学生的学习情况和表现。
第六章教学质量改进第二十二条学校应建立教学改进机制,鼓励教师参加教育培训和学术交流,不断改进教学方法和教学内容。
施工质量分析与质量控制方法

施工质量分析与质量控制方法一、引言在现代社会,建筑施工质量是保证工程质量和安全的重要因素。
本文将从施工质量的定义和重要性出发,探讨施工质量的主要问题,并介绍一些常用的质量控制方法,以期提高建筑工程的施工质量。
二、施工质量的定义与重要性施工质量是指建筑工程在整个施工过程中是否符合设计、施工图纸、施工标准、规范要求以及是否满足建筑使用功能的标准。
施工质量的重要性不言而喻,一方面,高质量的建筑施工能够保证工程寿命长、使用安全,为人们的生活提供便利;另一方面,施工质量不合格可能导致工程事故、质量缺陷,给人们的生命和财产安全带来潜在威胁。
三、施工质量的主要问题在实际的建筑施工中,常常会面临一些施工质量的问题。
例如,施工过程中的材料选择不当、施工质量监督不到位、技术工人的技能不够等。
这些问题都可能对施工质量带来不利影响。
因此,需要采取一些有效的方法来解决这些问题。
四、质量控制方法之一:合理施工方案的制定合理的施工方案是保证施工质量的重要保证。
施工方案应包括详细的工序、进度安排、质量要求等,同时要考虑到实际施工中遇到的各种情况,做到周密、合理、可行。
五、质量控制方法之二:材料的选择与控制材料的选择与控制直接影响着施工质量。
合适的材料能够保证工程的稳定性和耐久性。
在选择材料时,应考虑到其性能、特性以及符合相关标准,以确保材料的可靠性。
同时,在材料供应链的控制方面,应加强对材料供应商的审核与管理,确保供应商符合相关标准和要求。
六、质量控制方法之三:施工流程的管理与监督施工流程的管理与监督是保证施工质量的重要环节。
在施工过程中,应建立完善的流程管理制度,并通过现场监督、抽查等方式对施工质量进行监控。
同时,还可以借助现代化的施工技术手段,如无人机、大数据分析等,提高施工质量的监督效果。
七、质量控制方法之四:技术工人的培训与提升技术工人是施工质量的关键因素之一。
因此,培训和提升技术工人的技能至关重要。
可以通过定期的技能培训、技能竞赛等方式,激发技术工人的学习兴趣,提高其专业水平和技术能力。
冶金质量分析第二章炼钢过程中气体和夹杂物的冶金控制
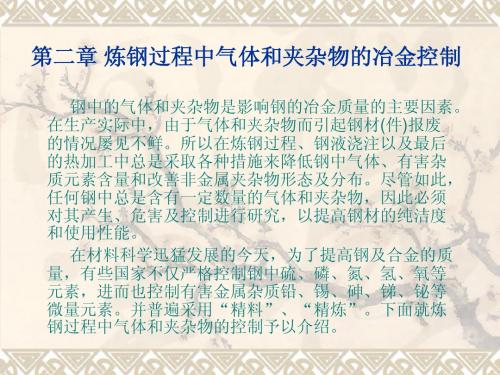
上式表明,给定的温度下,钢液中溶解的氢、 氮的浓度与钢液上氢、氮的分压的平方根成正 比。氢、氮在钢液中的溶解反应为吸热过程, 随着温度升高,溶解度也增大,由此可见,出 钢温度过高会增加氢、氮在钢中的溶解量,从 而降低钢的质量和性能。 钢液中其他溶质元素对气体的溶解度也有影 响,凡与气体有较强亲和力的元素(如V、Mn, Ti, Nb等),将增加气体在钢液中的溶解度,而 与铁的亲和力大于气体与铁的亲和力的元素(如 C , Si等),会降低气体在钢液中的溶解度。
(二)氢对钢质量的影响 氢的原子半径小(0.053nm),进入钢中后, 相当容易移动。由于氢在铁中移动的激活能 只为碳在铁中移动激活能的1/10,以致钢中的 氢容易在应力(主要指外加应力、残余应力、原 子之间相互作用力等)作用下,向钢中一些危险 区域扩散,以不同形式危害钢的性能。 钢中氢的危害主要表现在以下几个方面:
一般来讲,钢的氢脆随钢的强度增高而加剧, 高强度钢和超高强度钢含氢时脆性将明显 增加。研究认为,高强度钢平均含氢量不到 10-4%就可能产生氢脆。 图4--2中表明,在低于屈服强度的恒定静载 荷持续作用下,经过一定时间的孕育期后,、 在试样表面缺陷处或缺口根部产生裂纹源,随 着时间的延长,裂纹不断扩展长大,到一定程 度后导致试样突然断裂。由于图4-2中的断裂 曲线与疲劳曲线相似,因此这种氢脆也称为静 疲劳。图4-2中有一个下临界应力值(门槛值), 试样在低于此值的应力作用下,加载时间再长 也不会产生脆性断裂。下临界应力的大小与试 样表面缺口形状有关,缺口愈尖锐,下临界应 力也愈低。
Triano在1955年提出的应变时效型氢脆的 解释,目前已为较多的人所接受,其概念如 下:含氢试样受载后,在其缺口尖端处产生应力 集中。氢原子在应力作用下向这里扩散聚集, 使缺口尖端处的位错周围形成柯氏气团,对位 错产生钉扎作用,导致位错难以运动,表现为 缺口尖端处被局部硬化。在外加应力作用下, 如果试样缺口尖端处的基体不能通过位错运动 产生局部塑性变形而使应力集中松弛的话,此 处就会萌生裂纹并由此扩展长大。
全面质量管理的基本方法

第二章全面质量管理的基本方法第一节PDCA 循环法一、计划-执行-检查-总结➢制定计划(方针、目标)➢执行 (组织力量去实施)➢检查(对计划执行的情况进行检查)➢总结(总结成功的经验,形成标准,或者找出失败原因重新制定计划)PDCA 循环法的特点:1 。
四个顺序不能颠倒,相互衔接2 。
大环套小环,小环保大环,互相促进3 。
不停地转动,不断地提高4. 关键在于做好总结这一阶段二、解决和改进质量问题的八个步骤1 。
找出存在的问题2 。
分析产生问题的原因3 。
找出影响大的原因4 。
制定措施计划5 。
执行措施计划6 。
检查计划执行情况7 。
总结经验进行处理8. 提出尚未解决的问题第二节质量管理的数理统计方法一、质量管理数理统计方法的特点和应用条件1. 特点(1)抽样检查(2)伴有生产过程进行(3)可靠直观2. 质量管理数理统计方法的优点(1)防止废次品产生(防患于未然)(2)积累资料,为挖掘提高产品质量的潜力创造了可能(3)为制定合理的技术标准和工艺规程提供可靠数据(4)减少了检验工作量,提高了检验的准确性与效率,节省了开支3. 质量管理数理统计方法的应用条件(1)必须具备相对稳定的生产过程(完备的工艺文件、操作规程,严格的工艺纪律、岗位责任制,完好状态的设备等)(2)培训人员,掌握方法,明确意义(3)领导重视,创造条件赋予支持(4)各职能部门互相配合,齐心协力二、质量管理数理统计方法的基本原理➢随机现象和随机事件➢频数、频率和概率➢概率的几个性质产品质量变异和产生变异的原因:1. 偶然性原因(随机误差)对质量波动影响小,特点是大小、方向都不一定,不能事先确定它的数值。
2 。
系统性原因(条件误差)对质量波动影响大,特点是有规律、容易识别,可以避免。
随机误差与条件误差是相对的,在一定条件下,前者可变为后者。
正常波动偶然因素异常波动系统因素产生原因观察和研究质量变异,掌握质量变异的规律是质量控制的重要内容。
制药行业生物制剂研发方案

制药行业生物制剂研发方案第一章引言 (3)1.1 生物制剂概述 (3)1.2 研发背景与意义 (3)第二章市场调研与分析 (4)2.1 生物制剂市场现状 (4)2.1.1 市场规模 (4)2.1.2 市场结构 (4)2.1.3 市场分布 (4)2.2 竞争对手分析 (4)2.2.1 主要竞争对手 (4)2.2.2 竞争策略 (5)2.3 市场需求分析 (5)2.3.1 疾病谱变化 (5)2.3.2 政策支持 (5)2.3.3 市场潜力 (5)2.3.4 市场竞争格局 (5)第三章技术研究与发展趋势 (5)3.1 生物技术概述 (5)3.2 生物制剂研发趋势 (6)3.2.1 个性化治疗 (6)3.2.2 精准医疗 (6)3.2.3 生物类似物 (6)3.2.4 跨学科融合 (6)3.3 技术创新与应用 (6)3.3.1 基因工程技术 (6)3.3.2 细胞工程技术 (6)3.3.3 生物信息学技术 (6)3.3.4 人工智能技术 (7)3.3.5 纳米技术 (7)第四章目标产品筛选与评估 (7)4.1 产品筛选标准 (7)4.2 产品候选物评估 (7)4.3 产品研发策略 (8)第五章研发流程与方法 (8)5.1 研发流程设计 (8)5.2 研发方法选择 (9)5.3 关键技术攻关 (10)第六章生产工艺优化 (10)6.1 生产工艺流程 (10)6.1.1 原料准备 (10)6.1.2 细胞培养 (10)6.1.5 质量检验 (11)6.2 工艺参数优化 (11)6.2.1 培养工艺参数优化 (11)6.2.2 提取纯化工艺参数优化 (11)6.2.3 制剂工艺参数优化 (11)6.3 生产成本控制 (11)6.3.1 原材料成本控制 (11)6.3.2 设备投入与维护成本控制 (11)6.3.3 人力资源成本控制 (11)6.3.4 能源与环保成本控制 (11)第七章质量控制与安全评价 (12)7.1 质量标准制定 (12)7.1.1 引言 (12)7.1.2 质量标准内容 (12)7.1.3 质量标准修订 (12)7.2 质量控制方法 (12)7.2.1 引言 (12)7.2.2 原料质量控制 (12)7.2.3 生产过程质量控制 (12)7.2.4 成品质量控制 (13)7.2.5 包装材料质量控制 (13)7.3 安全性评价 (13)7.3.1 引言 (13)7.3.2 非临床安全性评价 (13)7.3.3 临床安全性评价 (13)7.3.4 安全性评价方法 (13)第八章临床试验与注册 (13)8.1 临床试验设计 (13)8.1.1 研究目的 (14)8.1.2 研究类型 (14)8.1.3 研究人群 (14)8.1.4 研究方法 (14)8.1.5 样本量计算 (14)8.1.6 监测和评估 (14)8.2 临床试验实施 (14)8.2.1 伦理审查 (14)8.2.2 研究者培训 (14)8.2.3 研究药物管理 (14)8.2.4 数据收集与记录 (14)8.2.5 安全性监测 (14)8.2.6 质量控制 (15)8.3 注册申请与审批 (15)8.3.1 注册申请资料 (15)8.3.3 审批程序 (15)8.3.4 审批结果 (15)8.3.5 注册证书 (15)第九章市场推广与销售 (15)9.1 市场推广策略 (15)9.2 销售渠道建设 (16)9.3 客户服务与维护 (16)第十章总结与展望 (17)10.1 研发成果总结 (17)10.2 项目不足与改进 (17)10.3 未来发展展望 (17)第一章引言生物制剂作为一种新兴的药物形式,在现代医药领域占据了日益重要的地位。
质量成本的分析与控制

如何理解、分析企业质量成本?质量成本的概念是由美国质量专家A.V.菲根堡姆在20世纪50年代提出来的。
他将企业中质量预防和鉴定成本费用与产品质量不符合企业自身和顾客要求所造成的损失一并考虑,形成质量报告,为企业高层管理者了解质量问题对企业经济效益的影响,进行质量管理决策提供重要依据。
此后人们充分认识了降低质量成本对提高企业经济效益的巨大潜力,从而进一步提高了质量成本管理在企业经营战略中的重要性质量成本又称质量费用。
根据ISO9000系列国际标准质量成本的定义是:将产品质量保持在规定的质量水平上所需的有关费用。
根据国际标准(ISO)的规定,质量成本是由两部分构成,即运行质量成本(或工作质量成本,或内部质量成本)和外部质量保证成本。
鉴定成本是指评定产品是否满足规定的质量水平所需要的费用1.运行质量成本运行质量成本是指企业为保证和提高产品质量而支付的一切费用以及因质量故障所造成的损失费用之和。
它又分为四类,即企业内部损失成本、鉴定成本、预防成本和外部损失成本等。
①企业内部损失成本,又称内部故障成本企业内部损失成本是指产品出厂前因不满足规定的质量要求而支付的费用。
主要包括:废品损失费用、返修损失费用和复试复验费用、停工损失费用、处理质量缺陷费用、减产损失及产品降级损失费用等。
②鉴定成本鉴定成本是指评定产品是否满足规定的质量水平所需要的费用。
主要包括:进货检验费用、工序检验费用、成品检验费用、质量审核费用、保持检验和试验设备精确性的费用、试验和检验损耗费用、存货复试复验费用、质量分级费用、检验仪器折旧费以及计量工具购置费等。
③预防成本预防成本是指用于预防产生不合格品与故障等所需的各种费用。
主要包括:质量计划工作费用、质量教育培训费用、新产品评审费用、工序控制费用、质量改进措施费用、质量审核费用、质量管理活动费用、质量奖励费、专职质量管理人员的工资及其附加费等。
④外部损失成本外部损失成本是指成品出厂后因不满足规定的质量要求,导致索赔、修理、更换或信誉损失等而支付的费用。
机械加工过程中的质量控制

机械加工过程中的质量控制机械加工过程中的质量控制第一章前言第二章质量控制流程1.计划阶段1.1 制定加工工艺流程,明确加工工艺参数和要求。
1.2 编制产品加工检验计划,确定检验方法和标准。
2.原材料检验2.1 对原材料进行外观检查,如表面有无明显缺陷。
2.2 测量原材料尺寸和重量,与要求进行比较。
2.3 进行化学成分分析,确保原材料符合要求。
3.工艺控制3.1 选择适当的机械加工设备和工具,确保其正常运行。
3.2 确定加工工艺参数,如切削速度、进给量等。
3.3 进行工艺试验,验证所选工艺参数是否合理。
3.4 进行加工前的设备检查,确保设备处于良好状态。
4.加工过程控制4.1 加工过程中进行实时监控,记录加工参数和数据。
4.2 定期对加工设备进行维护和保养,确保其正常运行。
4.3 加工过程中进行抽样检验,验证加工产品的质量。
5.产品检验5.1 对加工产品进行外观检查,如表面质量、尺寸偏差等。
5.2 进行物理性能测试,如硬度、拉伸强度等。
5.3 进行化学性能测试,确认产品的化学成分。
5.4 进行功能性能测试,验证产品的使用性能。
6.质量控制记录6.1 所有的质量控制活动都要记录下来,包括检验报告、检验记录等。
6.2 对不合格品进行处理,如返工、报废等,记录处理结果。
7.改进措施7.1 对加工过程中出现的问题进行分析,找出原因。
7.2 制定改进措施,防止问题再次发生。
7.3 对改进措施进行评估和监控,确保其有效性。
附件:________法律名词及注释:________1.《产品质量法》:________中华人民共和国国家法律,规定了产品质量的基本要求和相关责任。
2.《标准化法》:________中华人民共和国国家法律,规定了标准化的基本要求和相关责任。
《质量管理学》第二章:全面质量管理

分析现状
对企业现有质量管理体系进行全面分析,找出存在的问题和薄弱环 节。
制定计划
针对问题和目标,制定具体的全面质量管理计划,包括时间节点、责 任人、资源保障等。
实施全面质量管理培训
01
02
03
培训对象
对企业全体员工进行全面 质量管理培训,提高员工 的质量意识和技能水平。
基于事实的决策方法
数据收集和分析
建立有效的数据收集和分析系统,确保决策基于准确、可 靠的数据和信息。
决策过程透明化
公开决策过程和依据,增强员工对决策的信任感和参与感。
纠正和预防措施
针对出现的问题采取及时的纠正措施,并预防类似问题的 再次发生。
03 全面质量管理的实施步骤
制定全面质量管理计划
确定质量目标和方针
经济效益指标
如质量成本、销售收入等,反映企业 实施全面质量管理后的经济效益变化。
全面质量管理持续改进机制
问题反馈机制
建立有效的问题反馈渠道,鼓励员工积极反映质量问题 ,以便及时发现和解决。
改进措施实施机制
制定具体的改进计划,明确责任人、时间节点和预期效 果,确保改进措施得到有效实施。
ABCD
原因分析机制
全员参与
全面质量管理鼓励全体员工参与质量改进活 动,发挥每个人的智慧和创造力。
事实决策
全面质量管理强调基于数据和事实进行决策, 避免主观臆断和盲目行动。
02 全面质量管理的原则与要 求
以顾客为中心
确定并理解顾客需求和期望
01
组织应明确其产品或服务的目标顾客群体,并深入了解他们的
需求和期望。
确保顾客满意度
公司质量控制与质量改进管理制度
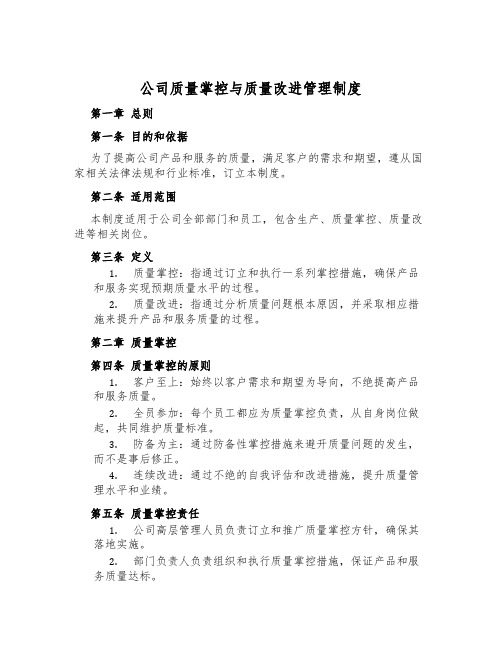
公司质量掌控与质量改进管理制度第一章总则第一条目的和依据为了提高公司产品和服务的质量,满足客户的需求和期望,遵从国家相关法律法规和行业标准,订立本制度。
第二条适用范围本制度适用于公司全部部门和员工,包含生产、质量掌控、质量改进等相关岗位。
第三条定义1.质量掌控:指通过订立和执行一系列掌控措施,确保产品和服务实现预期质量水平的过程。
2.质量改进:指通过分析质量问题根本原因,并采取相应措施来提升产品和服务质量的过程。
第二章质量掌控第四条质量掌控的原则1.客户至上:始终以客户需求和期望为导向,不绝提高产品和服务质量。
2.全员参加:每个员工都应为质量掌控负责,从自身岗位做起,共同维护质量标准。
3.防备为主:通过防备性掌控措施来避开质量问题的发生,而不是事后修正。
4.连续改进:通过不绝的自我评估和改进措施,提升质量管理水平和业绩。
第五条质量掌控责任1.公司高层管理人员负责订立和推广质量掌控方针,确保其落地实施。
2.部门负责人负责组织和执行质量掌控措施,保证产品和服务质量达标。
3.员工需严格依照质量掌控要求,执行工作任务,亲自检查和监控质量问题的解决情况。
第六条质量掌控措施1.设立质量掌控部门或委托专业机构进行质量检验和质量监控,确保产品和服务符合相关标准和规定。
2.建立并执行严格的质量管理体系,包含质量管理手册、程序文件和作业引导书等。
3.进行质量目标设定和质量绩效评估,确保产品和服务实现预期质量水平。
4.开展质量培训和教育活动,提高员工的质量意识和本领。
5.实施全面的过程掌控,包含原材料子采购、生产加工、产品测试等环节。
6.强化供应商质量管理,加强对供应商的质量管理要求和监督检查。
第七条质量问题处理1.快速响应:发现质量问题时,要及时报告并采取紧急措施,避开问题扩大。
2.问题分析:对质量问题进行深入分析,找出根本原因,并记录问题处理过程。
3.问题解决:订立并执行相应的矫正和防备措施,确保仿佛问题不再发生。
- 1、下载文档前请自行甄别文档内容的完整性,平台不提供额外的编辑、内容补充、找答案等附加服务。
- 2、"仅部分预览"的文档,不可在线预览部分如存在完整性等问题,可反馈申请退款(可完整预览的文档不适用该条件!)。
- 3、如文档侵犯您的权益,请联系客服反馈,我们会尽快为您处理(人工客服工作时间:9:00-18:30)。
(N=180) 6月1日至7月31日
100
150 82.22 100 88 48.89 50 32 66.67 50 100 58.62 94.44 89.44
一、因果图
因果图主要用于分析质量特性与影响质量特性的可能 原因之间的因果关系,通过把握现状、分析原因、寻找对 策来促进问题的解决。
因果图的绘制方法
绘制方法 特点 1、收集原因时采用行为逻辑推理法 2、整理原因时由大骨—中骨—小骨 1、收集原因较多采用“头脑风暴法” 2、整理原因时由小骨—中骨—大骨
94.44 89.44
Байду номын сангаас50
32
28
13
9
10
尺 寸 不合格
砂眼
擦伤
断裂
弯曲
其它
不合格项排列图
二、排列图
2、分析:使用因果图将影响主要项的所有原因列出来:
疲劳
操作者
集中 疾病 培训 成分 项目 零件
机器
精神
注意力 形状
稳定
健康
经验
素质
检验
方法
失恒
变形
磨损
教育
操作 夹具 工具
尺寸不合格
位置
拧紧程度
材料的质量
二、排列图
排列图和因果图结合使用案例
1、选题:使用排列图确定主要项:
频数 (N=180) 6月1日至7月31日
累 计 百分比 100
右图为某零件使用 不合格现象调查表统计 所得的排列图。 通过排列图确认尺 寸不合格为主要不合格 项。需要进行原因分析。
150 82.22 100 88 48.89 50 66.67
其中A类因素可确定为“关键的少数”。
二、排列图
排列图使用的注意事项
1、排列图可以分析影响质量问题的主要原因,即抓住“关键的少数”。但它 只在影响问题的数量上体现主要原因,在考察影响因素的重要性和安全性等方 面表现不足。 2、排列图可用来确定采取措施的顺序。 3、对采取措施前后的排列进行对照,可以验证措施的有效性。
(2)动作研究
动作研究是以“动作的经济原则冶进行流程中具体步骤(动作)的研究, 达到 以最低的劳动强度和劳动量, 多快好省地完成工作任务的目的。在动作分析过程 中, 必须遵循动作的经济原则, 不断改进操作, 以提高工作质量和工作效率。
1) 动作的经济原则 2) 为便于记忆将动作的经济原则简化
2. 工作研究的效果
工作研究是工业工程(IE)中的一项重要内容。当接受 某—工作任务时, 不应急于去实施, 而应采用科学方法研究 和分析, 才能达到事半功倍的效果, 这就是工作研究的目的 和任务。
(三)工作研究的适用范围 1. 工作研究的内容
(1)程序研究
某公司对加工工序流程
材料库
机床A 55500 件/h
中间库
机床B 5000 件 /h
因果图——是一种用于分析质量特性(结果)与可能影响 质量特性的因素(原因)的一种工具。
因果图的作用:
1、分析(特性及其影响因素之间的)因果关系 2、表达(上述)因果关系 3、通过识别症状、分析原因、寻找措施,促进问题解决
一、因果图
大骨 小骨 中骨 主骨 特性
特性(结果)
因素(原因)
因果图的结构
1953年日本质量管理专家石川馨首先提出了因果图,现已成为应用最 为广泛的管理工具。因果图又称石川图和鱼刺图。
材料库
机床A
料盒
机床B
成品库
机床A工作中,半成品自动送入料盒,当料盒内满100件时,机床A自 动停止工作,当料盒内只剩10件半成品时,机床A开始工作,周而复 始,而机床B则连续工作。 改进效果为: ①两台机床联动,减少小间库和送料及管理人员; ②两台机床之间的料盒很小,节省大量生产面积; ③节约半成品输送时间和费用; ④发生质量问题可以及时反馈质量信息; ⑤生产周期缩短,满足市场需求。
存在自动反馈调整所得的数 据图形。
一、直方图
直方图的类型及其特征
5、平顶型 几种均值不同的分
6、双峰型 两种不同的均 值相差大的分布混 在一起,由于数据 分层不当或人、机、 料、法、环等因素 的差异引起。
7、孤岛型 工序异常、测量
布混在一起,或过程出
现缓慢劣化,如刀具磨 损、操作者疲劳或数据 分层不当等。
工作研究可以有效地提高劳动生产率, 具体表现如下。 一是企业获得三高: 高的工作质量, 高的工作效率, 高的经济效益。 二是有效地促进职工的劳动热情: 工作轻松不疲劳, 满负荷工作出效率, 优质高 产得效益。
(四)流程图的符号
1. 端点符 3. 判断符
表示一个流程的开始和结束。
表示检验、检查、评审、审核、 评价等判断性活动。 4. 停顿符
二、排列图
排列图的概念和作用
田口玄一的质量思想 —— 质量问题是以质量损失的形 式表现出来的,大多数损失往往是有几种不合格引起的,而 这几种不合格又是由少数原因引起的。
朱兰“2080原则” —— 朱兰博士最早运用巴雷特(或 洛伦兹)的经济理论将质量问题分为“关键的少数”和“次要 的多数”,即多数的质量问题是由少数的关键原因引起的。
•调查的目的 •调查的类型 •调查的方式 •调查表的应用程序
二、水平对比法 • 定义 水平对比法是把产品或服务的过程及性能与公认的 领先水平进行比较,以识别质量改进机会的一种方法。 • 应用范围 水平对比法的应用有助于认清目标和确定计划编制 优先顺序,以便使应用者在市场竞争中处于有利的地位 •应用程序 水平对比法的应用程序就是质量管理所提倡的科学工 作程序——PDCA循环。
贮存 尺寸
排列
直径
定位
顺序
安装材料
程序 角度
动作
零件与材料
操作方法
速度速度
因果图列出了所有影响零件尺寸波动的因素,通过现场调查和其它 方法对各种原因进行验证,找到主要原因,制定对策并实施。
二、排列图
3、验证改进效果:重新搜集数据制作排列图,将前后排列图进行对照以 验证改进的效果。
累 计 百分比
频数
逻辑推理法
发散整理法
在绘制因果图时,两种方法往往结合使用。
一、因果图 因果图绘制的注意事项
1.确定原因要充分发扬民主,集思广益,做到“重要的因素不要遗漏”。 2.确定原因要尽可能全面具体。 3.质量特性与因果图一一对应,有多少个质量特性就要绘制多少张因果 图。
4.确定的原因要经过验证。一方面原因要细分,直到能采取措施为止。
成品库
某产品加工工序如上图,其中机床A的生产能力5500 件/h,机床B的生产能力5000件/h,市场需求为5000 件/h。
经程序研究: 问:机床A与机床B之间为什么要设中间库? 答:由于两部机床功效不同,造成机床边堆放大量半成品,所以设中间库周转。 调查:机床A的工效为5500件/h,超过市场需求,机床B的工效为5000件/h, 能够满足市场需求。从科学管理角度看问题,认为机床A的全效工作只能造成库 房积压,是一种浪费,应让机床A的工效有10%的停机,使其与机床B同步,则 两台机床可以联动。
3、对造成问题的方面或项目进行划分或归类;如按不合格类型、不
合格位置、工序、机器设备、操作者、作业方法分等;不常出现的项目归入 “其他项”。(使用分层法进行分类,数据不分类就无法使用)
4、确定收集数据的方法、时间。
二、排列图
第二步,收集数据并填入数据统计表中 第三步,将数据统计表转化成排列图用数据表,表中依
二、排列图
排列图是对发生的频次从最高到最低的项目进行排列而 采取的简单图示技术。 排列图的作用是找出影响问题中“关键的少数”原因。 通过区分最重要和较次要的影响因素,用较小的努力获得最 佳的改进效果。
二、排列图 排列图的绘制方法
第一步,确定所要调查的问题以及如何收集数据。(关键) 需要考虑如下方面: 1、调查的是何种问题?不合格项目、损失金额、事故等。 2、确定问题调查的期限。
四、分层法
一、直方图
定义:直方图是描述定量数据分布情况的一种图形技术, 由一系列矩形组成。
作用:通过对数据的加工整理,观测并研究数据的
取值范围、集中和分散等分布的情况。 直方图可用于明确问题和把握现状。 直方图的横坐标是质量特性数据 直方图的纵坐标是数据的频率(频数)
一、直方图
直方图的类型及其特征
三、流程图法
流程图是一种提供质量改进机会及改进措施的现代 科学方法,而不是制图方法。 (一)定义 ISO 9004.4:1994标准给出的定义:流程图是用图 的方式将一个过程的步骤表示出来。通过对过程的 实际情况的详细了解来调查改进的机会;通过对各 步骤之间关系的研究通常能发现故障的潜在原因。
(二)工作研究简介
左右 纵纵 坐坐 标标
不 合 格 数
160 140 120 100 80 60 40 20
累 计 百 分 数
不累 合计 格百 数分 数
铸件不合格项目排列图
二、排列图
排列图的种类
用来发现造成质量、成本、交货 1、分析现象用排列图 期、安全等方面不良结果的主要问题。 用来发现因操作者、机器设备、 2、分析原因用排列图 原材料、作业方法等过程因素造成的主 要问题。
错误或混有另一分布
的少量数据。常因为 原材料变化或由不熟 练工人替班引起。
一、直方图
直方图与公差之间的关系、并能做出基本判断 (1)直方图符合公差要求的情况
TL
TU
TL
TU
充分满足公差要求。状况良 好,不需要调整。
满足公差要求,但不充分。或称(过 程能力已不充分)。 措施是:减少波动(提高加工精度)。
一、直方图
直方图不符合公差要求的情况
TL
TU
TL
TU
TL
TU
不满足公差要求 (过程能力已不足) 措施是:使均值接近规格 的中间值(减少偏移)。