施耐德电气公司精益生产体系流程评估标准
精益生产体系CCPS评估手册

精益生产体系CCPS评估手册1. 简介精益生产体系(Continuous Process Improvement System,CCPS)是一种旨在提高生产效率和质量的管理方法。
本手册旨在为组织提供评估其精益生产体系的指导和框架。
2. CCPS评估的目的CCPS评估的主要目的是确定组织内精益生产体系的成熟度水平,以及识别潜在的改进机会。
评估包括对组织的流程、方法和工具进行审查,以确定其符合精益生产体系的要求。
评估结果可以为组织制定改善计划和目标提供依据。
3. CCPS评估的步骤CCPS评估通常包括以下步骤:3.1 筹备阶段在筹备阶段,应明确评估的目的和范围,制定评估的计划和时间表,并确定评估的参与人员。
3.2 数据收集数据收集阶段是评估的核心。
评估团队应通过文件审查、访谈和观察等方法,收集与精益生产体系相关的数据和信息。
这些数据和信息包括组织的流程图、标准操作程序、业绩指标等。
3.3 数据分析在数据收集完成后,评估团队应对收集到的数据进行分析。
通过对数据的分析,评估团队可以确定组织的强项和改进的机会,并建议相应的改进措施。
3.4 结果汇报评估结果应以报告的形式呈现给组织管理层。
报告应清晰地描述评估的目标、方法、结果和建议,在报告中可以包括评估的总结、发现的问题、改进建议和实施计划。
4. CCPS评估指标为了评估组织的精益生产体系,可以使用以下指标:4.1 流程稳定性流程稳定性指标可以评估组织的流程是否具有稳定性和可预测性。
常用的指标包括平均流程时间、流程的标准偏差和流程的控制限等。
4.2 资源利用率资源利用率可以评估组织在生产过程中是否合理利用资源。
常用的指标包括设备利用率、人力资源利用率和原材料利用率等。
4.3 质量指标质量指标可以评估组织的产品或服务的质量水平。
常用的指标包括不良品率、误报率和客户投诉率等。
4.4 交付能力交付能力可以评估组织按时交付产品或服务的能力。
常用的指标包括交货准时率、订单满足率和交付延误时间等。
施耐德供应商管理流程
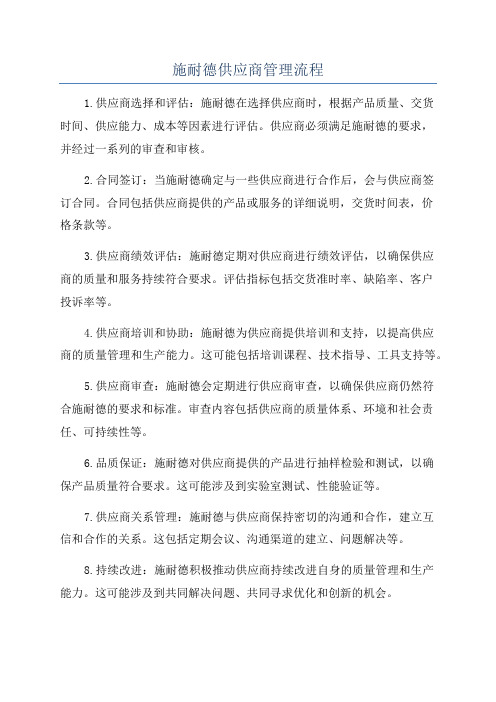
施耐德供应商管理流程1.供应商选择和评估:施耐德在选择供应商时,根据产品质量、交货时间、供应能力、成本等因素进行评估。
供应商必须满足施耐德的要求,并经过一系列的审查和审核。
2.合同签订:当施耐德确定与一些供应商进行合作后,会与供应商签订合同。
合同包括供应商提供的产品或服务的详细说明,交货时间表,价格条款等。
3.供应商绩效评估:施耐德定期对供应商进行绩效评估,以确保供应商的质量和服务持续符合要求。
评估指标包括交货准时率、缺陷率、客户投诉率等。
4.供应商培训和协助:施耐德为供应商提供培训和支持,以提高供应商的质量管理和生产能力。
这可能包括培训课程、技术指导、工具支持等。
5.供应商审查:施耐德会定期进行供应商审查,以确保供应商仍然符合施耐德的要求和标准。
审查内容包括供应商的质量体系、环境和社会责任、可持续性等。
6.品质保证:施耐德对供应商提供的产品进行抽样检验和测试,以确保产品质量符合要求。
这可能涉及到实验室测试、性能验证等。
7.供应商关系管理:施耐德与供应商保持密切的沟通和合作,建立互信和合作的关系。
这包括定期会议、沟通渠道的建立、问题解决等。
8.持续改进:施耐德积极推动供应商持续改进自身的质量管理和生产能力。
这可能涉及到共同解决问题、共同寻求优化和创新的机会。
9.风险管理:施耐德识别和管理与供应商相关的各种风险,包括供应风险、质量风险、环境和社会责任风险等。
这可能涉及到风险评估、风险控制和应急准备措施。
10.供应商退出管理:如果供应商无法满足施耐德的要求或出现重大问题,施耐德会采取相应的措施,包括暂停或终止与供应商的合作关系。
总结起来,施耐德的供应商管理流程包括供应商选择和评估、合同签订、供应商绩效评估、供应商培训和协助、供应商审查、品质保证、供应商关系管理、持续改进、风险管理和供应商退出管理等步骤。
这些步骤有助于确保施耐德与供应商之间的合作稳定,并保证产品和服务的质量和可靠性。
精益生产企业的评估标准及评估方法(精益企业评估)
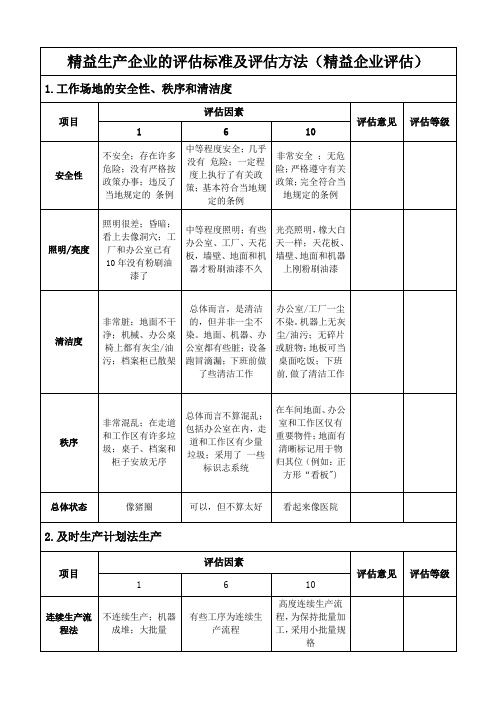
有些机器具有自动停机功能
当检测到次品时,所以有机器都能自动停机
操作工有权因质量不合格而停止生产
无
操作工权,但并非有的操作工
操作工有权有责任停止生产线;完全是个人质量负责制
有防错设计可防止次品
无
部分应用于重要工序
应用于所有重要工序
FIFO库存控制
无
部分
严重遵守;便于使用(例如,流动支架)
封闭环路质量问题的解决
所以关键工序都采用六西格玛质量管理法控制
标准化工序
无工作标准指令;完全是在职培训
对标准化工作和直观工作指令大约贯彻了50%
工作方法全面贯彻标准化并通过直观法可清楚地加以识别(即采用三维图纸)
进入厂内的产品和材料的质量
无自检合作供应商
有些供应商是自检合格的,并始终可以达到可靠的质量
所有主要供应商都自检合格的,并可一直提供获得同意的质量产品
无
有过程,但每项申请都必须“排队”;偶然也会对申请作出反应(仅当我们有时间时)
所有公司的组织机构都有能力对改革和申请支持迅速作出反应;在48小时内作出反应
改变贯彻执行
仅由工程部设计和管理人员批准之后
大致贯彻执行直观库存管理
操作工和办公室人员都有权、有责任贯彻执行改革
操作工和办公室人员的会议
偶尔进行(一个月一次或两次)
总体状态
像猪圈
可以,但不算太好
看起来像医院
2.及时生产计划法生产
项目
评估因素
评估意见
评估等级
1
6
10
连续生产流程法
不连续生产;机器成堆;大批量
有些工序为连续生产流程
高度连续生产流程,为保持批量加工,采用小批量规格
如何评估你公司的精益生产水平

如何评估你公司的精益生产水平精益生产是一种基于减少浪费和提高价值流动的管理方法,旨在提高生产效率和质量。
评估公司的精益生产水平可以帮助企业了解其生产过程中存在的问题,并找到改进的机会。
本文将介绍如何评估你公司的精益生产水平。
一、确定评估指标评估公司的精益生产水平需要明确评估指标,以便有针对性地进行评估。
常用的评估指标包括:1. 价值流图:通过绘制整个生产过程的价值流图,分析各个环节的价值流动情况,找出浪费的地方。
2. 周转时间:包括生产周期、加工时间、等待时间等,评估产品在生产过程中的流动速度,了解生产过程中的瓶颈和延误。
3. 库存水平:评估公司库存水平是否过高,过高的库存会导致资金占用和物料过期浪费。
4. 第一次通过率:评估产品的质量水平,第一次通过率越高,说明产品质量越好,减少了返工和废品产生的浪费。
5. 人力资源利用率:评估人力资源的使用情况,包括员工的工作效率、利用率和人力资源的流动性等。
二、数据收集评估精益生产水平需要收集相关的数据。
可以通过以下方式进行数据收集:1. 生产数据记录:收集和记录生产过程中的各项数据,如完成时间、加工时间、数量、质量等。
2. 实地观察:亲自到生产现场观察生产过程,了解生产环节中的情况,收集相关数据。
3. 员工访谈:与生产过程相关的员工进行面对面的访谈,了解他们对生产过程的看法和存在的问题。
三、数据分析在收集到数据后,需要对数据进行深入的分析,找出问题和改进的机会。
可以采用以下方法进行数据分析:1. 流程图绘制:根据数据绘制生产过程的流程图,标记出每个环节的关键指标,使问题一目了然。
2. 对比分析:将不同时间段、不同产品线或不同工厂的数据进行对比分析,找出差异性和问题所在。
3. 帕累托图:用于优化问题的解决方案排序,通过分析每个问题的贡献度,确定改进的重点。
4. 五力分析:分析公司在供应链中的位置和竞争力,找出改进的机会。
四、改进措施在分析数据后,需要根据问题的具体情况制定相应的改进措施。
(2020)精益生产改善方案制造评估标准

4 = 75%的子单元和子单元里的工作站在工序间实现一件/一双/一刀流(所有工序间只存在标准的在制品数量)。单元间的标准安全库存在2小时以内。全流程的所有操作都在单元的内侧进行,线外加工的部件只有一种,并使用看板系统进行收发。
3 =单元内有50%以上的作业员能够以平均水平(满足节拍时间)操作一个以上的工作站。不同的工作级别对应不同的薪酬(技能与服务期限),采用集体计件。
4 =在每个子单元里,50%以上的作业员能够掌握与其相邻的上下道工序的操作,并满足节拍时间和质量标准的要求。每周有规律地更换工作岗位并能维持薪酬不变(仅有服务期待遇变化)。张贴多技能培训图表。采用集体计件。
5 =所有子单元里的作业员都能掌握与其相邻的上下道工序的操作,并满足节拍时间和质量标准的要求。每周有规律地更换工作岗位并能维持薪酬不变(仅有服务期待遇变化)。张贴多技能培训图表。采用集体计件。
9.增值率
消除多余的、非增值的作业:消除不必要的动作(必要的非增值操作未列入非增值作业)
1 =每个子单元最少有一个非增值作业
5 =全流程单元里所有的设备都是根据需要制作的,归该单元专用;所有机器的尺寸和速度都是正确的;没有无用的特性,所有的机器都容易移动。
12.按工序排列的机器
有助于一件/一双流的实现;可以让因果关系更容易确定。
(登记的可能数据有:循环时间与节拍时间,机器的不合格,等待时间,RFT等)
1 =使用红牌作战来移走不用的机器设备。红牌区域就位于全流程单元和精益车间内。有指定的红牌管理者。
精益评价标准
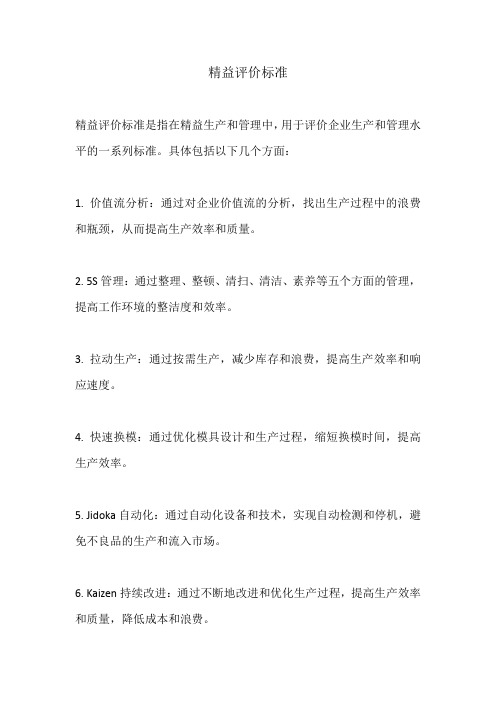
精益评价标准
精益评价标准是指在精益生产和管理中,用于评价企业生产和管理水平的一系列标准。
具体包括以下几个方面:
1. 价值流分析:通过对企业价值流的分析,找出生产过程中的浪费和瓶颈,从而提高生产效率和质量。
2. 5S管理:通过整理、整顿、清扫、清洁、素养等五个方面的管理,提高工作环境的整洁度和效率。
3. 拉动生产:通过按需生产,减少库存和浪费,提高生产效率和响应速度。
4. 快速换模:通过优化模具设计和生产过程,缩短换模时间,提高生产效率。
5. Jidoka自动化:通过自动化设备和技术,实现自动检测和停机,避免不良品的生产和流入市场。
6. Kaizen持续改进:通过不断地改进和优化生产过程,提高生产效率和质量,降低成本和浪费。
以上是精益评价标准的主要内容,企业可以根据自身情况选择适合的标准进行评价和改进。
精益生产优化全程-施耐德电气

灵活、可扩展的通讯架构 维护、优化和生产改进的 常规工具 污水、排放物、废弃物监控
高效选矿运行
控制污水排放(温度、 体积、浓度) 废弃物监控
施耐德电气的矿业解决方案可以帮助用户
● 实现基于时间使用模型的停机分析,将原矿产能提 升25%
● 对矿石粒度/化学成分进行实时分析,确保产品质量
● 对矿石和其他原材料在厂矿范围内的加工转运进行监 控,提升生产连续性
安全的配电系统保护操 作人员与设备
生产资料转运与加工 过程中的库存管理
能耗监控 高效变频器与 电机控制
关键电力 门禁控制
碾磨效率和颗粒尺寸控制 能耗监控 高效变频器与电机控制
在线生产管理报告
- 与实验室信息管理系 统相结合
- 与在线分析仪表 相结合
在线成本监控 厂级能耗监控 消耗品(如化学试剂)消 耗量监控 维护工具 - 停机时间分析 - 生产计划 - 资产管理
等等.
可靠供电
停机管理
事故预防
信息整合(纵向:现场到集控中心,横向:各层级子系统间)
机房系统管理
机房管理系统
机房综合布线方案 服务器机架系统 不间断电源UPS 关键制冷控制系统 监控系统
楼宇管理 楼宇管理系统
数据完整性
跨系统数据互联
1
矿业解决方案展示平台介绍
网络拓扑结构
矿业解决方案展示台由现场设备层,过程 控制层和工厂管理层三个层级组成,对一 个典型的洗煤厂L3整体解决方案进行了 展示。
2
现场设备层
现场设备层涵盖了典型洗选煤厂的四个工艺段,上仓原煤系统、洗选煤系统、成品煤仓库 系统和火车装车系统。在每个系统中,相关工艺设备可通过总线/网络与工艺段的控制器通 讯,也可以将电气信号直接接入到现场的IO板(Quantum远程IO或者Advantys STB 分布式 IO)卡。同时,现场的水泵,风机以及皮带等系统可以通过直接启动(TeSys T / TeSys U) 或者软启动(ATS48/ATV71/1100)的方式进行启停和调速控制。安装在现场关键位置的安 防视频摄像头(Pelco)可以远程采集现场的视频信息并在操作员站进行呈现,实现视频监 视。为了全面了解现场设备的能耗情况,相应的电能仪表(PowerLogic Meters)也可以采 集现场设备的关键电气参数,如电压、电流和功率因素并传输给控制器。
施耐德电气供应商质量管理(内部培训)

共同承诺Mutual Commitment
运行文件
Quality Terms and Conditions 质量术语及条款 Logistic Terms and Conditions 物流术语及条款
General Info Index
18
什么是SGB(施耐德电气供应商指南)
日常参考文件
* The purpose of this table is to track any change on the agreement with the supplier, i.e. Issue 01, 02…
General Info Index
22
SGB:运行文件
Logistics Terms and Conditions 物流术语及条件
供应链KPI (关键绩效指标)
NLD ESSR 100 % LTD
ESSR, External Supplier Service Rate, in %
NLD 当月按时或提前收到的完整订单行数 LTD 当月应收到的采购订单行数
17
SGB 施耐德电气供应商指南
什么是SGB
General Info
2
SAM
Supplier Approval Module 供应商认证模块
这个模块旨在让供应商了解施耐德电气是如何选择供应商的。它提供了 一种通用的评估工具,要求不同部门共同确定供应商的优势和不足。 该评估适用于新供应商的选择,或发生下列情况的现有供应商:
ʘ 提供不同于现有产品的产品 ʘ 产品出自未经审核的工厂 ʘ 表现差(技术和/或服务质量)
SSQM Overview 施耐德电气供应商质量管理
精益评价标准
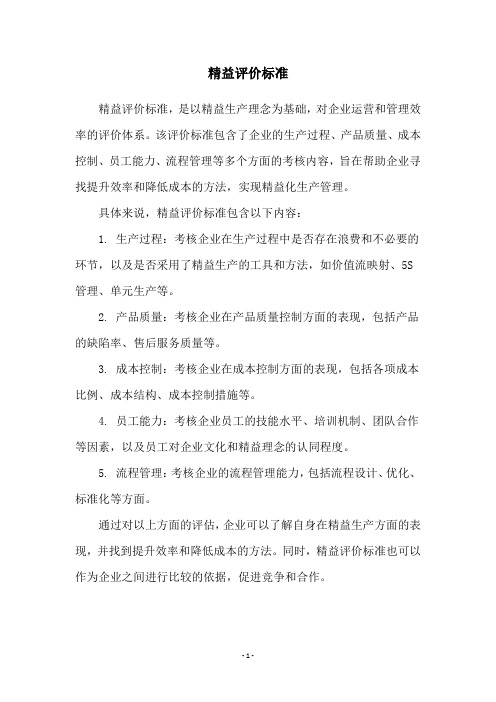
精益评价标准
精益评价标准,是以精益生产理念为基础,对企业运营和管理效率的评价体系。
该评价标准包含了企业的生产过程、产品质量、成本控制、员工能力、流程管理等多个方面的考核内容,旨在帮助企业寻找提升效率和降低成本的方法,实现精益化生产管理。
具体来说,精益评价标准包含以下内容:
1. 生产过程:考核企业在生产过程中是否存在浪费和不必要的环节,以及是否采用了精益生产的工具和方法,如价值流映射、5S 管理、单元生产等。
2. 产品质量:考核企业在产品质量控制方面的表现,包括产品的缺陷率、售后服务质量等。
3. 成本控制:考核企业在成本控制方面的表现,包括各项成本比例、成本结构、成本控制措施等。
4. 员工能力:考核企业员工的技能水平、培训机制、团队合作等因素,以及员工对企业文化和精益理念的认同程度。
5. 流程管理:考核企业的流程管理能力,包括流程设计、优化、标准化等方面。
通过对以上方面的评估,企业可以了解自身在精益生产方面的表现,并找到提升效率和降低成本的方法。
同时,精益评价标准也可以作为企业之间进行比较的依据,促进竞争和合作。
- 1 -。
精益生产企业的评估标准及评估方法(精益企业评估)
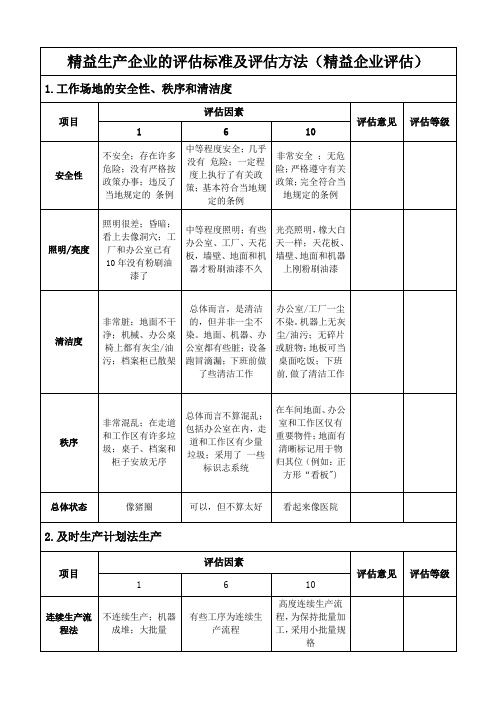
6
10
采购方式
将供应商视做敌人
介于两者之间
全面介入公司的指标和战略,与之结合
采购方针和措施
全面使用MPLeabharlann I书面传动;无直观指示标志有50%的供应商贯彻看板;书面控制和跟踪
看板传动;用最少量的书面控制作直观指标标志
采购的操作措施
独立组织结构,与制造和其他职能部门不断发生矛盾
介于两者之间
部分的业务组织,结合在其职能范围内
无
有过程,但每项申请都必须“排队”;偶然也会对申请作出反应(仅当我们有时间时)
所有公司的组织机构都有能力对改革和申请支持迅速作出反应;在48小时内作出反应
改变贯彻执行
仅由工程部设计和管理人员批准之后
大致贯彻执行直观库存管理
操作工和办公室人员都有权、有责任贯彻执行改革
操作工和办公室人员的会议
偶尔进行(一个月一次或两次)
从顾户订单至供应商,全面使用看板;MRPI仅用于计划和交货期较长的产品。仅根据顾客需求制定
生产线产品转换;机器设置
长达数小时
有些生产线产品转换时间短(数分钟);有些则时间长
在一个节拍时间里,对装配线进行产品转换;批量转换时间短于10分钟
总的生产维护
无“出毛病时,才解决”
有些贯彻TPM(全面生产维护)
无
有些机器具有自动停机功能
当检测到次品时,所以有机器都能自动停机
操作工有权因质量不合格而停止生产
无
操作工权,但并非有的操作工
操作工有权有责任停止生产线;完全是个人质量负责制
有防错设计可防止次品
无
部分应用于重要工序
应用于所有重要工序
FIFO库存控制
无
部分
施耐德电气能效管理案例分析

施耐德电气能效管理案例分析在现今追求可持续发展的时代,能源效率成为企业经营中一个重要的方面。
施耐德电气作为一家在全球范围内具有影响力的能源管理公司,以其在能效管理方面的成功案例引领了行业的发展。
本文将对施耐德电气的一项能效管理案例进行分析,以便更好地了解其在能效管理方面的经验和做法。
该案例是施耐德电气与一家制造企业合作的项目,目的是提高该企业的能源效率和降低能源消耗。
施耐德电气通过评估企业的能源使用情况,针对性地制定了一系列的能效改进建议,并实施了相应的措施。
下面将详细介绍该项目的实施过程和取得的成果。
首先,施耐德电气与该制造企业进行了一次全面的能源测评,对企业的用电、用水、用气等能源使用情况进行了详细的调查和分析。
通过数据收集和能源消耗的监测,施耐德电气获得了对企业能源消耗情况的真实了解,为后续的能效改善提供了科学依据。
在评估的基础上,施耐德电气提出了一系列的能效改进建议。
这些建议包括设备升级、能源监测系统的搭建、生产流程的优化等。
其中,设备升级是核心措施之一。
通过更换能效更高的设备,企业可以在相同的产能下降低能源的消耗,并提高生产效率。
同时,施耐德电气提出了建立能源监测系统的方案,该系统可以实时监测能源的使用情况,及时发现和解决能源浪费的问题。
此外,通过对生产流程的优化,可以减少能源浪费和无效生产环节,提高整体的能源利用效率。
在能效改善措施的实施过程中,施耐德电气与该企业进行了紧密的合作。
他们共同策划并落实了一系列的改善方案,并确保改善措施的有效性和可持续性。
在设备升级方面,施耐德电气提供的设备不仅具有较高的能效,并且还能够与现有设备无缝衔接,减少了企业的换装成本和生产停机时间。
此外,施耐德电气还在能源监测系统的搭建和生产流程优化方面提供了全方位的技术指导和支持。
通过施耐德电气与该企业的合作,该企业在能源效率和能源消耗方面都取得了显著的改善。
根据实测数据,该企业的能源消耗降低了20%,生产效率提高了15%。
精益生产实施与评价

精益生产实施与评价精益生产是一种持续改进的生产方式,旨在通过减少浪费、提高效率和质量,为企业创造更大的价值。
实施和评价精益生产是企业成功转型的关键,下面将介绍精益生产的实施步骤和评价方式。
实施精益生产的步骤包括以下几个方面:1. 制定战略:明确精益生产的目标和愿景,确保所有员工都对精益思维的重要性有清晰的认识。
2. 培训员工:为员工提供关于精益思维和工具的培训,使他们能够全面理解并参与到改进过程中。
3. 建立价值流图:通过分析整个生产过程,找出其中的浪费环节,并制定改进计划。
价值流图可以帮助企业更直观地了解生产过程中的问题和瓶颈。
4. 实施改进计划:根据价值流图和制定的改进计划,有针对性地进行改进工作。
可以采用PDCA(Plan-Do-Check-Act)循环模式,逐步改进工作流程。
5. 增加灵活性:引入柔性生产和小批量生产的概念,以便更好地适应市场需求的变化。
6. 持续改进:精益生产是一个持续改进的过程,企业应该不断地监测和评估改进效果,并根据需要进行调整和优化。
评价精益生产的方式可以包括以下几个方面:1. 测量关键绩效指标:例如产能利用率、生产周期时间、质量缺陷率等,通过对这些指标的测量和比较,可以评估精益生产的效果。
2. 进行价值流分析:通过分析价值流图和生产过程中的数据,找出改进的潜力和问题所在。
3. 定期进行员工培训和参与度调查:员工是精益生产的关键推动者,对他们的培训和参与度进行评价可以了解员工对精益生产的理解和支持程度。
4. 现场观察和记录:通过对生产现场的观察和记录,了解改进措施的实施情况和效果。
5. 持续改进评估:定期进行评估活动,总结经验和教训,并制定下一步的改进计划。
总之,实施和评价精益生产是企业转型过程中的重要环节。
通过精益生产的实施,企业可以实现持续改进和提高效率和质量的目标,并为企业的发展创造更大的价值。
实施和评价的过程需要不断地监测和调整,以确保持续改进的效果。
精益生产是一种以消除浪费为核心的生产方式,旨在通过提高效率、降低成本、提升质量和满足客户需求,为企业创造更大的价值。
精益生产的衡量指标
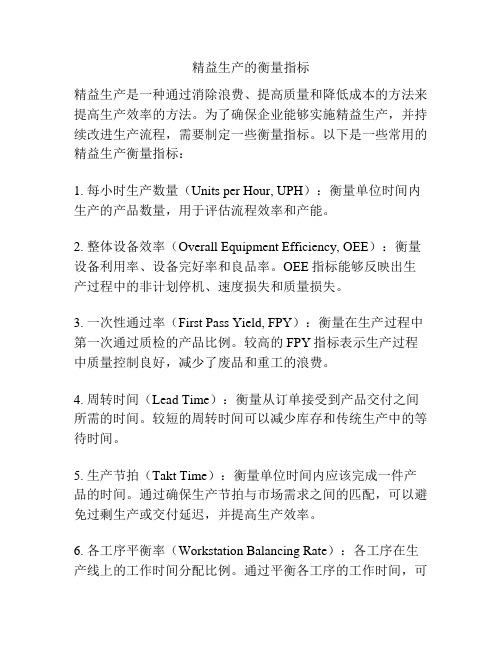
精益生产的衡量指标精益生产是一种通过消除浪费、提高质量和降低成本的方法来提高生产效率的方法。
为了确保企业能够实施精益生产,并持续改进生产流程,需要制定一些衡量指标。
以下是一些常用的精益生产衡量指标:1. 每小时生产数量(Units per Hour, UPH):衡量单位时间内生产的产品数量,用于评估流程效率和产能。
2. 整体设备效率(Overall Equipment Efficiency, OEE):衡量设备利用率、设备完好率和良品率。
OEE指标能够反映出生产过程中的非计划停机、速度损失和质量损失。
3. 一次性通过率(First Pass Yield, FPY):衡量在生产过程中第一次通过质检的产品比例。
较高的FPY指标表示生产过程中质量控制良好,减少了废品和重工的浪费。
4. 周转时间(Lead Time):衡量从订单接受到产品交付之间所需的时间。
较短的周转时间可以减少库存和传统生产中的等待时间。
5. 生产节拍(Takt Time):衡量单位时间内应该完成一件产品的时间。
通过确保生产节拍与市场需求之间的匹配,可以避免过剩生产或交付延迟,并提高生产效率。
6. 各工序平衡率(Workstation Balancing Rate):各工序在生产线上的工作时间分配比例。
通过平衡各工序的工作时间,可以避免生产线上的拥堵和等待时间,提高生产效率。
7. 变动性(Variability):衡量生产过程中的波动性和不确定性。
减少变动性可以降低生产过程中的风险和浪费。
8. 动作决策(Motion Decision):衡量生产过程中不必要的动作、移动和步骤。
通过减少不必要的动作决策,可以提高操作效率。
这些衡量指标可以帮助企业监控生产流程,并发现潜在的问题和改进机会。
根据这些指标,企业可以及时调整生产策略,降低成本,提高质量和交付效率,实现持续改进。
精益生产是一种通过消除浪费、提高质量和降低成本的方法来提高生产效率的方法。
精益生产评价标准
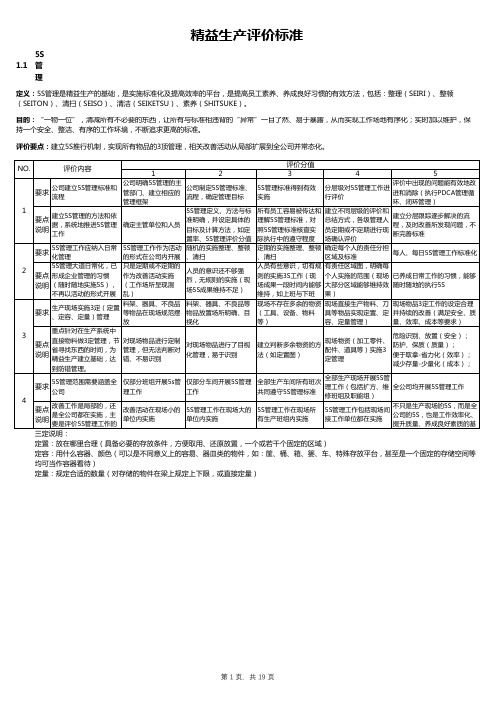
1.15S 管理精益生产评价标准定义:5S管理是精益生产的基础,是实施标准化及提高效率的平台,是提高员工素养、养成良好习惯的有效方法,包括:整理(SEIRI)、整顿(SEITON)、清扫(SEISO)、清洁(SEIKETSU)、素养(SHITSUKE)。
目的:“一物一位”,清减所有不必要的东西,让所有与标准相违背的“异常”一目了然、易于暴露,从而实现工作场地有序化;实时加以维护,保持一个安全、整洁、有序的工作环境,不断追求更高的标准。
评价要点:建立5S推行机制,实现所有物品的3顶管理,相关改善活动从局部扩展到全公司并常态化。
定置:放在哪里合理(具备必要的存放条件,方便取用、还原放置,一个或若干个固定的区域)定容:用什么容器、颜色(可以是不同意义上的容易、器皿类的物件,如:筐、桶、箱、篓、车、特殊存放平台,甚至是一个固定的存储空间等均可当作容器看待)定量:规定合适的数量(对存储的物件在梁上规定上下限,或直接定量)精益生产评价标准1.2目视化管理定义:一种能很快看得到工作场所的标准和实际情况的方法,主要分为标准、制度目视化和信息目视化目的:使所有员工很快看到现状(正常/异常),把我情况并采取行动恢复正常(标准)的状评价要点:从目视管理标准的建立、实施及维护角度进行精益生产评价标准精益生产评价标准1.3班组管理定义:班组管理是指以班组自身所进行的计划、组织、协调、控制、监督和激励等管理活动,其职能在于对班组的人、机、物进行合理组织、有效利用。
班组含生产班组和辅助班组(如:工装、维修、物料、检查、保洁等)。
目的:让所有员工参与管理并持续改进、生产合格产品、改善工作环境,以激发员工的热情、自豪感、工作满足感,促进个人成长。
评价要点:从班组组织机构设置、制度标准的建立、班组管理目标的明确性和适用性、班组主要活动的组织及评价机制建立进行评价。
精益生产评价标准1.4生产过程规划评价要点:主要从公司整体布局、生产线布局、一直到线内工位布局等角度考虑,强调布局的弹性化与质量的稳定性,以适应市场需求变化, 满足客定义:指根据以往的历史经验和未来的产品需求,为提高设备、工具、物资、人力资源和能源的使用效率,对公司内所有设施进行布置的一系 列系统的活动。
精益评估流程介绍

精益评估流程介绍精益评估流程是一种系统地评估组织内部业务流程和流程改进的方法。
它结合了精益生产和敏捷开发的原则,旨在提高效率、降低成本,同时确保产品和服务的质量和客户满意度。
首先,精益评估流程需要明确评估的目标。
评估的目标可以有很多种,比如降低生产成本、提高交付速度、改善产品质量等。
目标的明确性可以帮助评估团队更加有针对性地进行评估工作。
其次,评估团队需要收集相关数据。
收集数据的方式有很多种,可以通过面谈员工、观察业务流程以及分析已有数据等方式进行。
数据的收集需要尽可能地全面和客观,以便评估团队能够对业务流程进行准确的分析和判断。
然后,评估团队需要对收集到的数据进行分析。
数据分析可以帮助评估团队识别出业务流程中存在的问题和瓶颈,并找出问题的根本原因。
评估团队可以使用一些工具和方法,比如价值流图、故事板、鱼骨图等,来对数据进行分析和可视化展示。
接着,评估团队需要与相关利益相关者一起进行讨论和交流。
这个过程叫做“聚焦工厂”。
在聚焦工厂中,评估团队会邀请业务流程相关的各方参与,包括管理层、员工、客户等。
通过与利益相关者的交流和讨论,评估团队可以更加准确地了解业务流程的现状和问题,并与之一起确定改进方向和目标。
最后,评估团队需要制定和实施改进计划。
改进计划包括确定改进目标、制定实施步骤、明确责任人和时间表等。
评估团队可以使用PDCA(Plan-Do-Check-Act)循环来进行改进工作。
在实施改进计划的过程中,评估团队需要与相关利益相关者保持密切的沟通和协作,确保改进工作能够顺利地进行并取得预期的效果。
精益评估流程作为一种系统的评估方法,可以帮助组织发现业务流程中存在的问题和瓶颈,并找出解决问题的有效方法。
通过精益评估流程,组织可以不断优化业务流程,提高工作效率和质量,最终实现持续改进和持续增长的目标。
在精益评估流程中,还有一些关键的步骤和原则需要被注意和遵循。
以下是其中一些重要的内容:1. 持续改进:精益评估流程是一个持续改进的过程,不仅仅是一次性的评估和改进工作。
- 1、下载文档前请自行甄别文档内容的完整性,平台不提供额外的编辑、内容补充、找答案等附加服务。
- 2、"仅部分预览"的文档,不可在线预览部分如存在完整性等问题,可反馈申请退款(可完整预览的文档不适用该条件!)。
- 3、如文档侵犯您的权益,请联系客服反馈,我们会尽快为您处理(人工客服工作时间:9:00-18:30)。
3A Operator Flexibilty
3B Versatility & Multi skills Training
3C 5 S
3D Visual Management / Communicaton Boards
FLV&IC SPS Deployment Dept.
PRODUCT / PROCESS ENGINEERING
G&I / Industrial Deployment Schneider Production System
SPS Assessment
Training
(FLV & IC)
FLV&IC SPS Deployment Dept.
SPS Assessment training page 1
Icons & meanings
2A SIM Support Functions Implementation
2B SIM Support Functions Efficiency
2C Suggestion System / Needs Expression Board
3
CONTINUOUS IMPROVEMENT in people commitment
7C
Lean Six Sigma Kaizen (See/Do)
7D Total Productive Maintenance
7E Process Control (Part - Product)
MANAGEMENT OF MANUFACTURING & LOGISTICAL PROCESSES
8 PRODUCTION PLANNING & SCHEDULING 8A Master Production Scheduling 8B CDO / OFO Process 8B' Queue Management 8C Inventory management 9 PULL PRODUCTION 9A Single Point Scheduling / Pull system 9B Single Piece Flow Assembly / WIP Management 9C KANBAN Methodology 9D Value Stream Management 10 SUPPLY CHAIN & QUALITY MANAGEMENT 10A Supplier Quality Management 10B Supply Chain (upstream) Management 10C Down Stream Supply Chain Management 10D Shared Quality Management 10E Customer Focus
2 – SPS Basic
3. Operators were trained using the work instructions
Ask the trainers how they fulfill the training tasks
PEOPLE COMMITMENT
1 SIM PRODUCTION
1A Work Instructions
1B Short Interval Production Quality Tracking
1C SIM Production Implementation
2 SIM SUPPORT FUNCTION
4D Late Differentiation / Adaptation
5 ERGONOMICS / ENVIRONMENT - BAT
5AB Ergonomics / Work station
5C Environment - BAT
5D Safety
6 MATERIAL HANDLING
6A Reception / Warehouse Architecture
Explanation
Checking point
Question Good example Bad example
FLV&IC SPS Deployment Dept.
SPS Assessment training page 2
Introduction: 3 Domains,10 Categories, 38 Lines
6B MPAH Material Providing and Handling Internal
6C Water Spider
7
CONTINUOUS IMPROVEMENT in process engineering
7A Poka-Yoke
7B Changeover Time Minimization
Safety instruction could be combined with other work instructions, it must be posted (for critical machines/stations)
Observe whether the operator respects the safety instructions
SPS Assessment training page 3
People Commitment - SIM Production
1a - Work Instructions - P1 - Q
1 – SPS Notion
1. Work instructions exist for: a. Manufacturing. b. Quality.
4 PROCESS ARCHITECTURE / LEAN DESIGN
4A Manufacturing Time Definition
4A'
Manufacturing Time Definition (auto workshop / line)
4B Process Design / Lean Concept
Standard work has been defined for each station
2. Work instructions for Safety (based on risk analysis) are posted. (instruction board / workstation).