差速器壳体铸造工艺设计及改进
汽车差速器壳加工工艺及夹具设计

摘要随着社会的发展,汽车在生产和生活中的越来越广泛,差速器是汽车中的重要部件,其壳体的结构及加工精度直接影响差速器的正常工作,因此研究差速器的加工方法和工艺的编制是十分必要和有意义的。
本次设计主要内容有:差速器的工作原理结构分析,差速器壳体的工艺编制,夹具的设计及加工中对定位基准的选择,工序和工装设计中切削用量,夹紧力的计算等。
机床夹具的种类很多,其中,使用范围最广的通用夹具,规格尺寸多已标准化,并且有专业的工厂进行生产。
而广泛用于批量生产,专为某工件加工工序服务的专用夹具,则需要各制造厂根据工件加工工艺自行设计制造。
本设计的主要内容是设计钻床夹具和铣床夹具,需要对零件上Φ22的孔进行铣削加工端面的铣削加工。
由于某些原因,没有上传完整的毕业设计(完整的应包括毕业设计说明书、相关图纸CAD/PROE、中英文文献及翻译等),此文档也稍微删除了一部分内容(目录及某些关键内容)如需要的朋友,请联系我的叩扣:二二壹五八玖一壹五一关键词:差速器,壳体,工艺规程,夹具设计AbstractAlong with social development motor vehicle production and life in anincreasingly wide differential device is an important vehicle componentsand its interior structure and processing precision differential devicedirectly affect the normal work study differential device case processingmethods and techniques of preparation is necessary andmeaningful. Thecurrent design of the main elements: differential devicestructuresoperating principles of analysis differential device case preparationprocesses design and smooth-bore jig for positioning baseline processingoptions smooth-boredesign processes suits cutting consumption increasedcomputing power.Machine toolfixture of many kinds, among them, the most widely used common fixture, sizespecifications have been standardized, and a professional production plant. While widely used in batch production, designed for a certain workpiece processing services for the fixture, it needs each factory according to workpiece machining technology to design and manufacture. The main contents of this design is the design of drilling jig and milling fixture, the need for parts than22hole milling face milling.Key Words:differential device,case,technological process,jig design致谢目录摘要 (1)Abstract (1)目录 (2)第1章绪论 (4)1.1 课题的背景及意义 (4)1.2 差速器的主要分类 (5)1.2.1 开式差速器 (5)1.2.2 限滑差速器 (5)1.3 差速器结构 (6)1.3论文主要内容 (6)第2章零件的分析 (6)2.1 零件的作用 (6)2.2 零件的工艺分析 (7)第3章工艺规程设计 (8)3.1 基准面的选择 (8)3.1.1 粗基准的选择 (9)3.1.2 精基准的选择 (9)3.2 毛坯的制造形式 (9)3.3 制订工艺路线 (9)3.3.1. 工艺线路方案一 (9)3.3.2 工艺路线方案二 (10)3.3.3. 工艺方案的比较与分析 (10)3.4 机械加工余量、工序尺寸及毛坯尺寸的确定 (11)3.4.1 外圆表面 (11)3.5 内圆表面 (13)3.4.3 端面 (14)3.4.4 凸台 (15)3.4.5 孔类 (15)第4章 确定差速器切削用量及基本工时 (15)4.1 工序1 铣φ200外圆右端面(大头)。
汽车差速器壳体铸造工艺的开发与优化

Found ry Engi nee ri ng
工 艺
汽 车差 速 器 壳体 铸造 工 艺 的开 发 与优化
田迎 新 (上海 圣德 曼铸 造有限公司 ,上海 嘉定 201 805 )
摘 要 :通 过 优 化 边 冒 口位 置 、优 化 过 滤 网位 置 、增 加 进 铁 浇 道 ,坭 芯 工 艺采 用 随形 状 排 气塞 及 设 置 负缩水等措施 ,减少 了汽车差速 器壳体加 工气孔和渣孔缺 陷,消除 了差速 器壳体型腔 多 肉 和 黏 砂 缺 陷 ,解 决 了尺 寸 偏 差 导 致 的加 工 打 刀 问题 ,提 高 了产 品 的质 量 , 降低 了生 产 成 本 。 关键词 :差速 器壳体 ;铸造缺 陷;铸造 工 艺;优化 中图分类号 :TG 242 文献标识码 :B 文章编号 :1 673—3320(201 8)05—001 8—05
缩 孔 缩 松 缺 陷 , 只 是 可 以 剑 减 小 加 缩 孔 缩 松 fjg,趋 势l 。 【人】此 , 埘 材 料 进 行 了 优 化 , 提 岛 碳 “1 进 行 试制 , 检 测 结 果 缩 松 现 象 继 续 , 『]. J J【】r=销 孔 缺 比例 也 未 见 明 的 下 降 。
Developm ent And O ptim ization of Casting Process Used for Autom obile DiferentiaI Case
TIAN Yingxin
(Shanghai Sandmann Foundry Co.,Ltd.,Jiading 201 805,Shanghai China)
1 某 差 速 器 壳 体 开 发 技 术 要 求
某 差 速 器 壳 体 如 图 1所 示 , 产 品 单 重 设 计 为 5.45 kg,法 兰 厚 度 20 mlTl,最 大 壁 厚35 mm,属 于 较 为 厚 大 的 差 速 器 壳 体 。实 践 证 明 , 类 似 差 速 器 壳 体 最 适 合 的造 型 方 式 是 水 平 造 型 浇 注 方 式 …, 因 此 , 该 差 速 器 壳 体 选 择 在HW S线 湿 砂 型 铸 造 。为 节 能 减 排 、 降 低 成 本 及 提 升 产 品 铸 造 工 艺 的 出 品 率 ,开 发 单 冒 口 差 速 器 壳 体 的 铸 造 工 艺 替 代 常 规 的 双 冒 口差 速 器 壳 体 铸 造 工 艺 。原 铸 造 工 艺 图 如
差速器壳零件的机械加工工艺规程及钻端面12孔钻床夹具设计
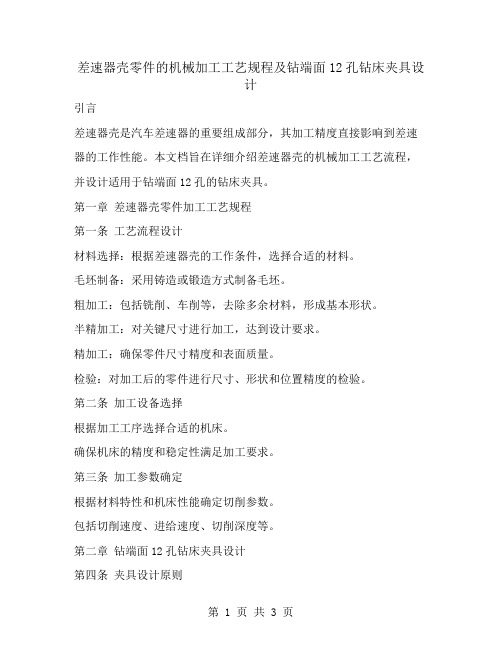
差速器壳零件的机械加工工艺规程及钻端面12孔钻床夹具设计引言差速器壳是汽车差速器的重要组成部分,其加工精度直接影响到差速器的工作性能。
本文档旨在详细介绍差速器壳的机械加工工艺流程,并设计适用于钻端面12孔的钻床夹具。
第一章差速器壳零件加工工艺规程第一条工艺流程设计材料选择:根据差速器壳的工作条件,选择合适的材料。
毛坯制备:采用铸造或锻造方式制备毛坯。
粗加工:包括铣削、车削等,去除多余材料,形成基本形状。
半精加工:对关键尺寸进行加工,达到设计要求。
精加工:确保零件尺寸精度和表面质量。
检验:对加工后的零件进行尺寸、形状和位置精度的检验。
第二条加工设备选择根据加工工序选择合适的机床。
确保机床的精度和稳定性满足加工要求。
第三条加工参数确定根据材料特性和机床性能确定切削参数。
包括切削速度、进给速度、切削深度等。
第二章钻端面12孔钻床夹具设计第四条夹具设计原则保证加工精度:夹具设计要确保加工过程中零件的位置精度。
操作简便:夹具操作要简单快捷,便于工人使用。
安全可靠:夹具结构要牢固,防止加工过程中的意外。
第五条夹具结构设计底座:设计稳定的底座,用于固定夹具。
夹紧机构:设计合理的夹紧机构,确保零件在加工过程中的稳定性。
定位元件:设计定位元件,确保零件在夹具中的准确位置。
钻模板:设计钻模板,用于引导钻头进行钻孔。
第六条夹具操作流程将差速器壳零件放置在夹具的定位元件上。
操作夹紧机构,将零件牢固夹紧。
调整钻模板位置,确保钻头与待钻孔对准。
启动钻床,进行钻孔加工。
加工完成后,松开夹紧机构,取出加工好的零件。
第七条夹具维护与保养定期检查夹具各部件的磨损情况,及时更换损坏部件。
清洁夹具,防止油污和金属碎屑影响夹具性能。
定期对夹具进行润滑,保证其运动部件的顺畅。
第三章加工质量控制第八条加工质量标准制定差速器壳加工的质量标准,包括尺寸精度、表面粗糙度等。
严格按照质量标准进行加工和检验。
第九条质量检验方法采用量具和测量仪器对加工后的零件进行检验。
汽车差壳铸件的铸造工艺探讨

其 是 在 区 域 , 缩孑 L 面 积很 大 。缩松 ( 缩孔 ) 是 该类
中 图分 类号 : T G 2 ห้องสมุดไป่ตู้5 5 . 9; 文献标 识 码 : A; 文 章编 号 : 1 0 0 6 — 9 6 5 8 ( 2 0 l 4 ) 0 1 — 0 0 0 9 — 0 4
D 0 I : l 0. 3 9 6 9 / J. 1 S S n. 1 0 0 6 —9 6 5 8. 2 0 1 4. 0 1 . 0 0 3
口冒口颈p的模数按05cm铁液入水位置改为两为了能够尽可能缩小铸件的缩松缩孑l缺陷须表5铸件实际模数考虑过热影响与补缩通道模数cm区域abcccdddeeefffghp实际模数o5o63o5045o5o704804509609075084o66o181需要的通道模数o4o4o4o404o4o4o4o6057o405o4补缩系统最小的通道模数04504504804505o5o505048045045045054系数12表6铸件实际模数考虑过热影响与补缩通道模数om区域abcccdddeeefffg日fp实际模数o6o7606054o6084o580541151109084o66061需要的通道模数o404o4o404o5oi404o706605705o4补缩系统最小的通道模数054054o58054o6060606058054054054054系数12表7铸件实际模数考虑过热影响与补缩通道模数om区域abcccdddeeefffgp实际模数055069055o5o55077o530511099083o77o610551需要的通道模数o404o4o4o40404o4066o6o5o4o4补缩系统最小的通道模数05o5o5305o55o55o55055053o5o50505系数11提高碳当量尤其是c含量要尽可能高充分利用口必须比较高否则会因为冒口的补缩量不足石墨化膨胀来弥补因补缩通道不畅通导致的缩松导致铸件顶部比如区域b出现缩松缩孔缺陷
新能源汽车差速器壳体的铸造工艺开发和改善
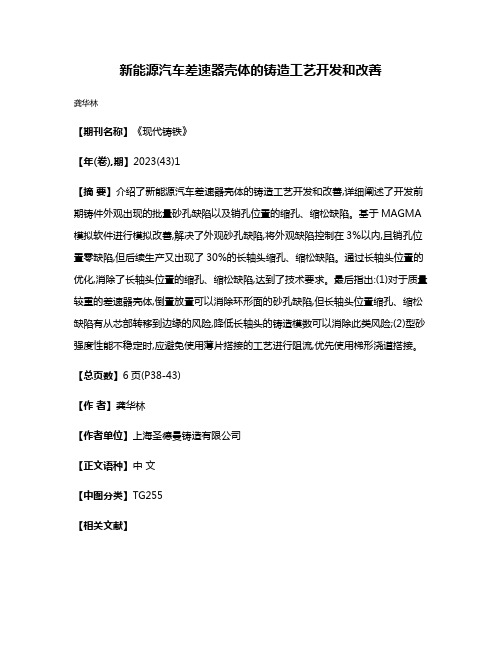
新能源汽车差速器壳体的铸造工艺开发和改善
龚华林
【期刊名称】《现代铸铁》
【年(卷),期】2023(43)1
【摘要】介绍了新能源汽车差速器壳体的铸造工艺开发和改善,详细阐述了开发前期铸件外观出现的批量砂孔缺陷以及销孔位置的缩孔、缩松缺陷。
基于MAGMA 模拟软件进行模拟改善,解决了外观砂孔缺陷,将外观缺陷控制在3%以内,且销孔位置零缺陷,但后续生产又出现了30%的长轴头缩孔、缩松缺陷。
通过长轴头位置的优化,消除了长轴头位置的缩孔、缩松缺陷,达到了技术要求。
最后指出:(1)对于质量较重的差速器壳体,倒置放置可以消除环形面的砂孔缺陷,但长轴头位置缩孔、缩松缺陷有从芯部转移到边缘的风险,降低长轴头的铸造模数可以消除此类风险;(2)型砂强度性能不稳定时,应避免使用薄片搭接的工艺进行阻流,优先使用梯形浇道搭接。
【总页数】6页(P38-43)
【作者】龚华林
【作者单位】上海圣德曼铸造有限公司
【正文语种】中文
【中图分类】TG255
【相关文献】
1.V法铸造工艺生产差速器壳体件
2.汽车差速器壳体铸造工艺的开发与优化
3.差速器壳体铸造工艺适应性结构优化
4.差速器壳体铸造工艺的优化
5.新时代党建带团建促党建的工作创新对策
因版权原因,仅展示原文概要,查看原文内容请购买。
差速器壳的机械加工工艺及工装设计

差速器壳的机械加工工艺及工装设计一、前言毕业设计是我们学完了大学的全部基础课、技术基础课以及大部分专业课之后进行的.这是我们在进行毕业设计之前对所学各课程的一次深入的综合性的总复习,也是一次理论联系实际的训练,因此,它在我们四年的大学生活中占有重要的地位。
就我个人而言,我希望能通过这次课程设计对自己未来将从事的工作进行一次适应性训练,从中锻炼自己分析问题、解决问题的能力,为今后参加祖国的建设打下一个良好的基础。
由于能力所限,设计尚有许多不足之处,恳请各位老师给予指导。
二、零件的分析零件的作用差速器壳是汽车差速器的一个主要零件。
汽车差速器的功用是使左、右驱动轮以不等速旋转,以适应汽车转向运动的需要。
⨯差速器壳以Ф139js6外圆及端面为装配基准装配在大圆锥齿轮上,以4-Ф22R8孔,8-Ф10.3D11孔,M10⨯1.5-6H与零件130-24031012装配。
两短均以Ф50m6为基准由圆锥滚子轴承支承,4-Ф22R8孔用来安装行星轮轴。
差速器壳图样的视图、尺寸、公差和技术要求齐全、正确;零件选用材料为KT350-10,该材料具有良好的强度、韧性和塑性,切削性能良好;结构工艺性比较好。
内圆柱面Ф37、Ф48以及SR54的内球面同轴最好在一次装夹下将三者同时加工; Ф139、Ф133、Ф138、Ф200外圆柱面同轴最好在一次装夹下将四者同时加工。
2.2.2 4-Ф22R8轴线SR54中心点与端面C的不重合度不大于0.05,应予以重视,其本身尺寸精度无特殊要求,较易保证。
2.2.3与基准孔有垂直度要求的端面,其端面圆跳动公差等级为8级,表面粗糙度为Ra≤6.3um。
工艺过程安排应注意保证其位置精度。
2.2.4 12-Ф11、8-Ф≤12.5,两者与与基准孔B的位置度公差为Ф0.30,主要是保证装配时能够互换。
根据各加工方法的经济精度及一般机床所能达到的位置精度,该零件没有很难加工的表面,上述各表面的技术要求采用常规加工工艺均可以保证。
拖拉机差速器壳工艺设计共25页word资料

差速器壳工艺设计设计内容:读零件工作图,绘制毛坯—零件合图,填写机械加工工艺过程卡,填写机械加工工序卡,编写设计说明书。
差速器壳零件图见图2-1,生产纲领为10000件/年。
第一章1.1 分析零件图1.零件的作用差速器示意图如图2-2所示,它是差速器的一个主要零件,其功能是使左,右驱动轮以恒扭矩不等速旋转,以适应机器转向运动的需要。
差速器壳经φ154h7外圆及端面为装配基准装配在大圆锥齿轮2上,经φ130H7内孔及端面为装配基准与差速器盖1装配,两端均以φ50K7为基准由圆锥滚子轴承7支承,2-φ22H8孔用于安装行星轮轴4。
两半轴齿轮6分别与行星齿轮3啮合,并装入差速器壳与差速器盖中形成一个闭合的齿轮传动系统。
2.零件的工艺分析差速器壳零件图如图2-1所示,该零件主要加工表面及技术要求分析如下。
(1)同轴孔φ50H8,φ130H7和同轴外圆φ50k6,φ154h7的同轴度、径向圆跳动公差等级为8~9级,表面粗超度为R a≤1.6μm。
加工时最好在一次装夹下将两孔或两外圆同时加工。
(2)与基准孔有垂直度要求的端面,其端面圆跳动公差等级为8级,表面粗糙度为R a≤3.2μm。
工艺过程安排是应保证其位置精度。
(3)距中心平面74.5mm的两侧面,表面粗糙度为R a≤6.3μm。
(4)2-φ22H8(B1-B2)孔的尺寸精度不难保证,但两孔轴线的同轴度公差等级应为9级及两孔公共轴线对基准孔(A2-A3)位置公差值为0.06μm,应予以重视。
(5)12-φ12.5孔,表面粗糙度R a≤12.5μm,与基准孔(A3)的位置公差为φ0.2mm,主要是保证装配互换性。
(6)改零件选用材料为QT420-10,这种材料具有较高的强度﹑韧性和塑性,切削性能和工艺性均较好。
有各种加工方法的经济精度及一般机床所能达到的精度可知,该零件没有很难加工的表面,各表面的技术要求采用常规加工工艺均可达到。
但是在加工过程中应该注意到该零件属于薄壁零件,刚性较差。
机械工艺夹具毕业设计23差速器壳体工艺及工装设计

机械工艺夹具毕业设计23差速器壳体工艺及工装设计差速器壳体是差速器的主要组成部分之一,它的工艺及工装设计对于差速器的生产质量和效率有着重要的影响。
本文将从工艺流程、工装设计和工艺参数三个方面对差速器壳体的工艺及工装设计进行详细阐述。
一、工艺流程的设计差速器壳体的工艺流程一般包括以下几个环节:材料采购、钣金加工、焊接、表面处理和装配。
首先,根据差速器壳体的制造要求,选择合适的材料,并进行采购。
其次,对采购的材料进行钣金加工,包括剪切、冲孔、折弯等工艺,以得到相应的壳体零件。
然后,对壳体零件进行焊接,常用的焊接方法有TIG焊、MIG焊等。
接着,对焊接好的壳体进行表面处理,如砂光、喷涂、电镀等,以提高壳体的表面质量。
最后,将各个零件进行装配,形成完整的差速器壳体。
二、工装设计1.材料输送工装:用于将原材料从仓库输送到钣金加工区域,采用传送带或叉车等设备。
2.钣金加工工装:包括剪切机、冲孔机、折弯机等设备,用于对原材料进行各种加工。
3.焊接工装:包括焊接夹具、焊接机器人等设备,用于对壳体零件进行焊接操作。
4.表面处理工装:包括砂光机、喷涂机、电镀设备等,用于对焊接好的壳体进行表面处理。
5.装配工装:包括装配平台、固定夹具等设备,用于将各个零件进行装配。
三、工艺参数的确定1.材料参数:主要包括材料的种类、厚度等。
根据差速器壳体的设计要求和生产经验,选择合适的材料,并确定材料的厚度。
2.加工参数:包括钣金加工的各项参数,如剪切、冲孔、折弯等工艺的刀具选用、切削速度、切削深度等参数。
3.焊接参数:包括焊接的工艺参数和焊接设备的选择。
根据焊接材料和焊接零件的材质选择合适的焊接方法和焊接参数。
4.表面处理参数:包括砂光、喷涂、电镀等工艺的参数。
根据壳体表面的要求选择适当的参数,如砂光的颗粒大小、喷涂的喷枪间距、电镀的电流和时间等。
通过合理设计工艺流程,设计适用的工装和确定合适的工艺参数,可以提高差速器壳体的生产效率和质量,为差速器的整体性能和可靠性提供良好的保障。
差速器壳体工艺设计

摘要随着社会的发展,汽车在生产和生活中的越来越广泛,差速器是汽车中的重要部件,其壳体的结构及加工精度直接影响差速器的正常工作,因此研究差速器的加工方法和工艺的编制是十分必要和有意义的。
本次设计主要内容有:差速器的工作原理结构分析,差速器壳体的工艺编制,夹具的设计及加工中对定位基准的选择,工序和工装设计中切削用量,夹紧力的计算等。
机床夹具的种类很多,其中,使用范围最广的通用夹具,规格尺寸多已标准化,并且有专业的工厂进行生产。
而广泛用于批量生产,专为某工件加工工序服务的专用夹具,则需要各制造厂根据工件加工工艺自行设计制造。
本设计的主要内容是设计镗孔夹具和钻孔夹具。
关键词:差速器,壳体,工艺规程,夹具设计AbstractAlong with social development motor vehicle production and life in anincreasingly wide differential device is an important vehicle componentsand its interior structure and processing precision differential devicedirectly affect the normal work study differential device case processingmethods and techniques of preparation is necessary andmeaningful. Thecurrent design of the main elements: differential devicestructuresoperating principles of analysis differential device case preparationprocesses design and smooth-bore jig for positioning baseline processingoptions smooth-boredesign processes suits cutting consumption increasedcomputing power.Machine toolfixture of many kinds, among them, the most widely used common fixture, sizespecifications have been standardized, and a professional production plant. While widely used in batch production, designed for a certain workpiece processing services for the fixture, it needs each factory according to workpiece machining technology to design and manufacture. The main contents of this design is the design of drilling jig and milling fixture, the need for parts than22hole milling face milling.Key Words:differential device,case,technological process,jig design目录摘要 (1)Abstract (2)目录 (3)第1章绪论 (5)1.1 课题的背景及意义 (5)1.2 差速器的主要分类 (5)1.2.1 开式差速器 (5)1.2.2 限滑差速器 (6)1.3 差速器结构 (6)1.3论文主要内容 (7)第2章零件的分析 (7)2.1 零件的作用 (7)2.2 零件的工艺分析 (8)第3章工艺规程设计 (9)3.1 基准面的选择 (9)3.1.1 粗基准的选择 (10)3.1.2 精基准的选择 (10)3.2 毛坯的制造形式 (10)3.3 制订工艺路线 (10)3.3.1. 工艺线路方案一 (10)3.3.2 工艺路线方案二 (11)3.3.3. 工艺方案的比较与分析 (11)3.4 机械加工余量、工序尺寸及毛坯尺寸的确定 (12)3.4.1 外圆表面 (12)3.5 内圆表面 (14)3.4.3 端面 (15)3.4.4 凸台 (16)3.4.5 孔类 (16)第4章 确定差速器切削用量及基本工时 (16)4.1 工序1 铣φ200外圆右端面(大头)。
差速器壳体工艺改进
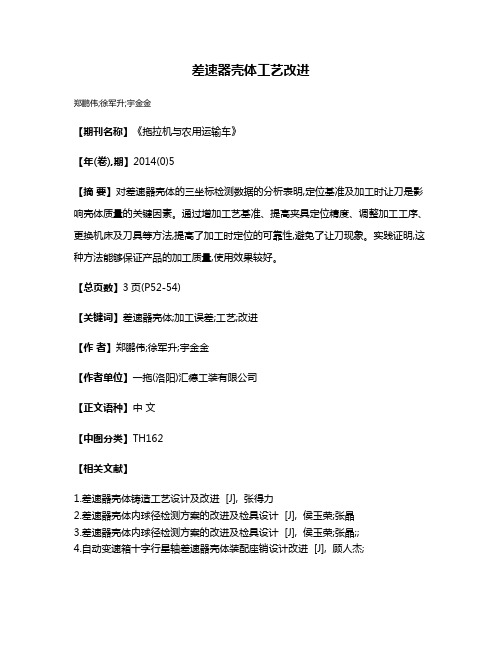
差速器壳体工艺改进
郑鹏伟;徐军升;宇金金
【期刊名称】《拖拉机与农用运输车》
【年(卷),期】2014(0)5
【摘要】对差速器壳体的三坐标检测数据的分析表明,定位基准及加工时让刀是影响壳体质量的关键因素。
通过增加工艺基准、提高夹具定位精度、调整加工工序、更换机床及刀具等方法,提高了加工时定位的可靠性,避免了让刀现象。
实践证明,这种方法能够保证产品的加工质量,使用效果较好。
【总页数】3页(P52-54)
【关键词】差速器壳体;加工误差;工艺;改进
【作者】郑鹏伟;徐军升;宇金金
【作者单位】一拖(洛阳)汇德工装有限公司
【正文语种】中文
【中图分类】TH162
【相关文献】
1.差速器壳体铸造工艺设计及改进 [J], 张得力
2.差速器壳体内球径检测方案的改进及检具设计 [J], 侯玉荣;张晶
3.差速器壳体内球径检测方案的改进及检具设计 [J], 侯玉荣;张晶;;
4.自动变速箱十字行星轴差速器壳体装配座销设计改进 [J], 顾人杰;
5.某变速器差速器壳体圆柱度超差分析与改进研究 [J], 张天梁;庞世松;马保仁;王世杰;黄祖思
因版权原因,仅展示原文概要,查看原文内容请购买。
球铁前轮毂和差速器壳体铸造工艺
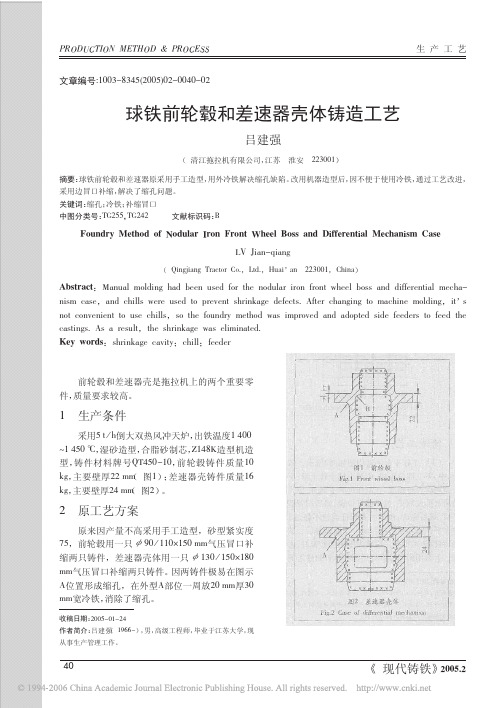
前轮毂和差速器壳是拖拉机上的两个重要零 件, 质量要求较高。
!
生产条件
采用" # $ %倒大双热风冲天炉, 出铁温度! &’’ (! &"’ ), *!&+,造型机造 湿砂造型, 合脂砂制芯, 型, 铸件材料牌号 -.&"’/!’, 前轮毂铸件质量 !’ 01, 主要壁厚22 33 ( 图!) ; 差速器壳铸件质量 !4 01, 2& 33 2 主要壁厚 ( 图 ) 。
!"#$%&’(#) *+’,#$ - !"#&+.. 文章编号:!’’8/+8&";2’’"<’2/’’&’/’2
生 产 工 艺
球铁前轮毂和差速器壳体铸造工艺
吕建强
( 清江拖拉机有限公司, 江苏 淮安 228’’!) 摘要: 球铁前轮毂和差速器原采用手工造型, 用外冷铁解决缩孔缺陷。 改用机器造型后, 因不便于使用冷铁, 通过工艺改进, 采用边冒口补缩, 解决了缩孔问题。 关键词: 缩孔; 冷铁; 补缩冒口 .=2"", .=2&2 中图分类号: > 文献标识码:
2’’"/’!/2& 收稿日期: 作者简介: 吕建强 ( !644/) , 男, 高级工程师, 毕业于江苏大学, 现 从事生产管理工作。
!"
!""#$! 《 现代铸铁》
!"#"$% & $’()%"*+", -(*" 文章编号!"##$%&$’()*##(+#*%##’"%#$
缺 陷 与 对 策
差速器壳体工艺及镗工装设计

差速器壳体工艺及镗工装设计一、引言差速器壳体是汽车差速器的重要组成部分,具有支撑和固定齿轮和轴的功能,因此其工艺和装配对差速器的稳定性和运行性能起着重要作用。
本文将介绍差速器壳体的工艺流程和镗工装设计。
二、差速器壳体的工艺流程差速器壳体的制造工艺一般包括以下几个步骤:1. 材料准备选择合适的材料是制造高质量差速器壳体的前提。
常用的材料有铝合金、铸铁等。
合理选择材料可以提高差速器壳体的强度和耐磨性。
2. 零件加工差速器壳体一般由多个零件组成,需要进行零件加工。
零件加工包括铣削、钻孔、车削等工序,以形成壳体的基本形状和孔洞。
3. 焊接将加工好的零件进行焊接,焊接工艺应选用适当的焊接方式和焊接材料,以确保焊接强度和密封性。
4. 表面处理对焊接好的壳体进行表面处理,一般包括清洗、喷涂、烤漆等工序,以提高壳体的美观度和耐腐蚀性。
5. 检测和装配对制造好的壳体进行严格的检测和质量控制,包括尺寸测量、焊接质量检验等。
通过合格的检测后,进行差速器齿轮和轴的装配。
三、镗工装设计差速器壳体的镗工装设计是为了保证差速器壳体内部孔洞的精度和相互位置的精确度。
以下是镗工装设计的步骤:1. 镗工装的选择根据差速器壳体的孔洞形状和尺寸,选择合适的镗工装。
常用的镗工装有手动镗床、数控镗床等。
应根据生产量和精度要求选择最合适的镗工装。
2. 差速器壳体的夹紧方式差速器壳体在镗工装上进行夹紧,夹紧方式应能保证壳体的稳定性和刚性,以减少加工误差。
常用的夹紧方式有机械夹紧和液压夹紧等。
3. 加工路径的设计根据差速器壳体的几何形状和孔洞布局,设计加工路径,以保证镗工的精度和效率。
在设计加工路径时应考虑刀具的刚性和切削力等因素。
4. 刀具的选择和切削参数的确定根据差速器壳体材料和孔洞尺寸,选择合适的刀具,并确定切削速度、进给量和切削深度等切削参数,以提高加工效率和镗工质量。
5. 加工过程的监控和调整在镗工过程中,应定期检查加工质量,对镗削刀具进行监控和调整,以保证壳体孔洞的尺寸精度和表面质量。
差速器壳体铸造工艺设计及改进

( a a n gm n (h n hiC . t. h g a 2 0 3 , hn ) D n ae e tS a g a o Ld, a h i 0 2 5 C ia Ma ) , Sn
Ab ta t I rv me t f a t gp o e s o i aeu e r o s u t nma hn r nrd c di sr c: mp o e n s n rc s r fc s sdf n t ci c ieyi it u e oc i f d oc r o s o n ti a e. u h p r a i a ei l ey t a ep rst u igc t gb c u eo sc mpe t cu e hsp p r S c at sdf c s s i l oh v oo i d rn a i e a s f t o lxsr tr k y s n i u
a d i n e ma e tr ; n a d t n i t r l sn d lri n T ep r st s e l u d i t f n s t ma y t r l n e s i d i o , t mae i o u a o . h o o i wa a l f n l so h c i s ai r y r yo n o p r n s f p rs w r c a p d l n t g p r s y i r aie h o g h a t g p c s a t a d a ma s o a t e e s r p e .E i ai o o i s e l d t r u h t e c si r e s s mi n t z n o i r v me t wh c r vd s ee e c r t e i l a t c s n . mp o e n , i hp o i e f r n ef h r mi p rs a t g r o o s r a i
- 1、下载文档前请自行甄别文档内容的完整性,平台不提供额外的编辑、内容补充、找答案等附加服务。
- 2、"仅部分预览"的文档,不可在线预览部分如存在完整性等问题,可反馈申请退款(可完整预览的文档不适用该条件!)。
- 3、如文档侵犯您的权益,请联系客服反馈,我们会尽快为您处理(人工客服工作时间:9:00-18:30)。
差速器壳体铸造工艺设计及改进
张得力
【摘要】主要介绍工程机械差速器壳体铸件的工艺改进过程.此零件由于结构复杂,零件本身存在较多热节处,零件材料又是球墨铸铁,所以出现缩松的倾向较大.在生产过程中确实发现大量零件出现缩松,从而导致零件报废,给企业造成了较大的损失.通过工艺方案的逐渐改进,最终消除了缩松缺陷的过程,为相关零件的铸造提供了经验依据.
【期刊名称】《柴油机设计与制造》
【年(卷),期】2012(018)002
【总页数】4页(P24-26,33)
【关键词】差速器壳体;缩松;工艺改进
【作者】张得力
【作者单位】美国德纳管理(上海)有限公司,上海200235
【正文语种】中文
差速器壳体是我公司供应商为我公司生产的零件之一。
在加工螺栓孔时,在孔中发现存在大量的缩松孔洞,有时缩孔较大时直径可达到20 mm的孔洞,并且一件零件中可出现2到3个这样的缩孔,从而造成大量的报废。
废品率最多可达95%,几乎没有合格品,根本无法组织生产。
虽然在工艺设计时运用了凝固模拟软件进行了模拟,并且模拟时并未发现存在较大的缩松缺陷,但在实际生产中由于各种因素的影响,使得实际的工艺结果并不能完全符合设计时的工艺思路,所以还需经过在
生产实践中的不断探索改进,从而达到理想的工艺目的。
其实,我公司针对缩松缺陷并不是不允许存在,而是有一定的接收标准,即在用X 光无损探伤的情况下给出的缩松或疏松缺陷的最大尺寸接收准则。
图1为缩松缺陷接收等级(Category CD-Shrinkage),1到3级可接收,也即最大接收等级为3级,就是在边长为38.10 mm的正方形内,缩松的最大尺寸不超过12.70 mm。
图2疏松缺陷接收等级(Category CC-Shrinkage),同样1到3级可接收,最大接收等级为3级,也是在边长为38.10 mm的正方形内,疏松的最大尺寸不超过25.4 mm。
此零件的材料要求是美国标准,材料牌号为MS-75B。
材料基体组织为珠光体与铁素体,并没有明确的比例标准。
抗拉强度为550 MPa,屈服强度为380 MPa,延伸率为6%,硬度为187~255 HB。
根据以上材料性能,对应的我国标准应该是牌号为QT550-6的球墨铸铁。
对铸件的工艺设计,一般流程如图3所示。
在初始工艺设计及经过凝固模拟未出现严重的铸造缺陷的情况下,要进行模具设计及制作,之后进行工艺验证,若工艺存在严重缺陷,则需进行进一步的改进。
3.1 初始工艺设计及试制
3.1.1 初始工艺设计
由于此零件材料是球墨铸铁,所以在设计工艺时首先要考虑将来可能会出现的缩松缺陷。
针对此零件的特点,不但要考虑浇冒口的设计,还需考虑到如何分型才能便于生产。
因为此零件一头直径较小又有一个直径较大的法兰,而另一头直径较大且壁厚较厚,并且在零件内部又有四组铸出的齿,如图4所示。
在法兰面与底部大直径处存在较大的壁厚,所以此处必定就是整个零件的热节,也即是最有可能存在缩松的位置。
在设计工艺时此一点是必须要考虑的,又考虑到此零件泥芯需要拼装且下芯方便,
现将分型面设在法兰面于大径端的一侧,并大径端为下箱,小径端为上相,如图5所示。
鉴于4组厚壁热节的存在,增设4个冒口,然后再在上箱的小径端增设一
个发热冒口以避免此处的缩松,如图5所示。
而最下面的厚大处设在下箱,有足
够的压力可以在凝固时形成自补缩能力,所以出现缩松的可能性相对较小。
由于此零件工艺复杂,产量也不是很大,故采用树脂砂造型方式进行生产。
3.1.2 样件试制
工艺设计完成后进行模具设计及制作,之后进行试生产。
其他工艺参数为:C-3.8,Si-2.5,Mn-0.5,S、P控制在0.02以下,并添加适当的Cu。
首批试制10件,其中3件进行X光无损探伤,3件进行解剖试验,4件进行机加工试生产。
X光检测没有发现大的缩孔,缩松级别亦在接受范围内,即最大缩松为3级。
经过切片分析也没有发现缩松缺陷及其他缺陷,如图6所示。
并且在其他4件加工时也未发现有大量缩松存在,仅在加工通过热节处的螺栓孔时发现个别螺孔存在疏松缺陷,但均在3级缺陷之内。
但在接下来的小批试制200件样件时却发现了大量的缩松缺陷,缺陷率达到95%以上,且缩孔较大,并且大部分位置处在法兰面下面的热节处的螺栓孔内,其他位置如下箱的大径端的底部厚大处也有少量疏松,比例在10%左右,其他部位未发
现任何疏松或其他类型的缺陷,如图7所示。
一般情况下,球墨铸铁形成缩松或疏松的倾向都较大,常用的改进方法一般有以下4种方法:
(1)加大铸型的刚度,以帮助球墨铸铁件较软的外壳抵抗由于石墨化膨胀所产生的外壳胀大的倾向,使铸件外壳保持原有的形状。
这样,铸件需要补缩的体积不致于因外壳的胀大而增加。
这一措施可使石墨化膨胀所产生的巨大的膨胀力作用于正在生长的共晶团,从而有效地消除共晶团件的微观缩松。
(2)增加石墨化膨胀的体积。
通过适当增加碳量,并配合以有效的孕育处理,使
球墨铸铁中石墨的数量增加而尽量避免自由渗碳体的产生,从而可提高铸件的自补缩能力。
(3)采用合适的浇注温度,以减少液态收缩值。
(4)结合生产实际,合理地选用冒口或冒口加冷铁的方式防止缩松产生[1,2]。
鉴于上述出现的缩松缺陷,再结合实际工艺参数来看,上述的工艺参数及之后的检测并未发现其他问题,化学成分都在所规定的范围之内,球化率达到90%以上,
机械性能合格,珠光体80%,残余镁0.05%,均未发现异常现象;所用沙箱刚度
足够,并且上下箱均用锁扣锁死,不存在抬箱的可能;并且浇注温度也在合理的范围内,孕育处理也未出现异常;并且从缺陷的部位来看,经统计,出现缩孔的位置均发生在与浇道一起的冒口所对应的热节处的螺栓孔内,另外两个冒口处的热节处未发现有缩松,所以,出现这样大的缩孔缺陷的原因很可能是由于此处为浇道口,砂型烘烤时间长,导致局部过热,而边冒口对此处不能实现有效的补缩所致。
所以,现考虑采用冷铁加冒口的工艺进行改进,即在出现缩松的热节处分别加两个冒口,将另外两个冒口及定部的发热冒口去掉,再在底箱的大径端面加上一块冷铁。
改进后的方案如图8所示。