盘式制动器的高温裂纹
动车轮装制动盘螺母开裂原因分析及建议

图 1 轮 装 制 动 盘 组 装 不 葸 图
21 0 0年 4 月 1— 2 日 , 公 司 在 轮 装 制 动 盘 6 8 某
化处 理 ( 图纸规定 内孔不 许硬 化 ) 的情况 , 现 有工 对 艺进行 分析 : 球座 热处 理 时 的渗 碳 层深 度 工 艺要 求 为 0 7~10m 实 际一般 为 0 8~ . m, 机加 . . m, . 0 9m 但 工 方面在 淬火前 球座 的底平 面至 内球
的内六 方受力 最大 , 而 使 得材 料 内部 存 在 微观 结 从 构缺 陷的螺母 发生 开裂 。
() 1 目前 动 车 组 产 品 的 进 口 配 件 很 多 , 议 铁 建
道部 动联办 组织 相关 部 门制定 进 口产 品监 督 、 制 控 管理 办法 , 加强对 进 口产 品 的监 督 、 制 , 保 动车 控 确
法, 建议 由主机厂提 供所采 购产 品的人 厂复验 方法 、
检 测 项 点 、 品 图 纸 、 关 标 准 , 业 组 装 时 应 根 据 产 有 企
部 分去 除 , 确保 制动 盘 螺母 使 用 的原 材 料无 形 成 裂
纹 源的条 件 。 ( ) 已 生 产 的 螺 母 , 应 商 进 行 10 螺 母 探 2对 供 0%
孔、 孔、 气 夹渣等 缺 陷 , 把 钢 锭 轧制 成 需要 的规格 在 棒料 过程 中 , 会把 缺陷沿 纵 向拉 长 , 化为 微观缺 陷 转 分布在 一定 长度 的钢材 中 。由于 目前 在棒料 投产前 没有进 行超声 波探 伤 , 以没有 及 时发 现 材 料 中 的 所 微观缺 陷 , 使存 在 缺 陷 的钢 材生 产 的 螺母 混入 合 致
制动盘罩壳开裂分析
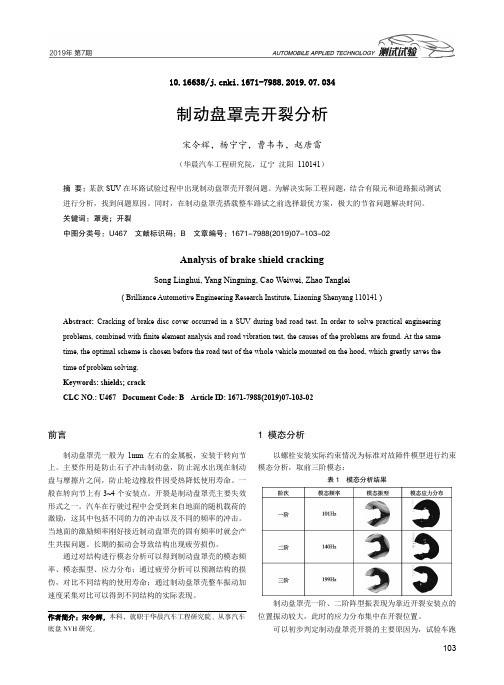
10310.16638/ki.1671-7988.2019.07.034制动盘罩壳开裂分析宋令辉,杨宁宁,曹韦韦,赵唐雷(华晨汽车工程研究院,辽宁 沈阳 110141)摘 要:某款SUV 在坏路试验过程中出现制动盘罩壳开裂问题。
为解决实际工程问题,结合有限元和道路振动测试进行分析,找到问题原因。
同时,在制动盘罩壳搭载整车路试之前选择最优方案,极大的节省问题解决时间。
关键词:罩壳;开裂中图分类号:U467 文献标识码:B 文章编号:1671-7988(2019)07-103-02Analysis of brake shield crackingSong Linghui, Yang Ningning, Cao Weiwei, Zhao Tanglei( Brilliance Automotive Engineering Research Institute, Liaoning Shenyang 110141 )Abstract: Cracking of brake disc cover occurred in a SUV during bad road test. In order to solve practical engineering problems, combined with finite element analysis and road vibration test, the causes of the problems are found. At the same time, the optimal scheme is chosen before the road test of the whole vehicle mounted on the hood, which greatly saves the time of problem solving. Keywords: shields; crackCLC NO.: U467 Document Code: B Article ID: 1671-7988(2019)07-103-02前言制动盘罩壳一般为1mm 左右的金属板,安装于转向节上。
盘式制动器的高温裂纹

盘式制动器的高温裂纹摘要盘式制动器在一般的制动中受到很大的热压力,在紧急制动受到非同寻常的热压力。
大减速度的客车通常每个衬块每秒中产生达900度的高温。
这种高温将产生两种结果:(1)热震动,产生表面裂缝,(2)制动盘产生较大的塑性变性。
在转动圈数相对较少的大减速制动中,如果没有热震动,,将在旋转体的最厚处和盘式制动器的径向产生可见的裂缝。
由此分析发现,制动器失效是短周期热力学疲劳的结果。
用热流方程分析有限元素作出制动器温度纵断面图。
如果得到制动温度,将用这个温度来估计紧急制动时增大的压力。
研究表明,在大减速度制动时由于热压应力较大,而导致塑性变形发生。
算出拉力位移量,然后用Coffin—Manson法则来估计制动失效的圈数。
关键字:热疲劳;热裂缝;制动失效;热压力;疲劳。
1.简介在大减速度制动后,在制动盘上可观察到热裂缝。
热裂缝可分为两类:一类是热裂缝部分的穿过制动盘表面;另一类是透过性热裂缝,他完全透过制动盘体。
虽然热裂缝是由紧急制动引起的,但是仍没办法防止其发生。
本文将对盘水制动器的制动盘热裂缝做一个彻底的分析。
在此,将以载重汽车F-250皮卡的前制动盘热裂缝为例进行分析,如图1所示。
当卡车拖拽的挂车装满货物时,如果频繁的刹车,当听到“嘭”的一声或显著的滴答声,表示制动器失效。
制动盘是由灰铸铁按照图2的几何尺寸制造而成。
选择会铸铁是由于其熔点低,传热和散热较快。
制动盘由连接车轮和轴的头部.内制动片和外制动片组成。
外制动片直接与头部相连,,而内制动片则通过一系列的通风叶片连与外制动片。
在制动盘的头部加工一道沟槽,用以改变该部的应力集中现象。
内制动片不是直接与头部相连,它通过冷却叶片连接。
制动是内外盘面被制动衬块压紧。
频繁的摩擦阻止车轮旋转,同时产生大量的热。
当制动数秒后,制动盘上产生了大量的热而邻近的空间内却与常温无异。
热裂缝在客车上不常见,但是在卡车和动力车辆上却相对常见。
许多车辆还暴露出相当极端的问题。
盘式制动器磨损情况记录

盘式制动器磨损情况记录近年来,随着汽车的普及和交通运输的发展,盘式制动器在汽车制动系统中扮演着重要的角色。
然而,由于制动器磨损的原因,出现了一系列与安全性相关的问题。
因此,对盘式制动器的磨损情况进行记录和分析,对于车辆的安全性和性能提升至关重要。
我们需要了解盘式制动器的工作原理。
盘式制动器主要由刹车盘、刹车片和刹车卡钳组成。
当驾驶员踩下制动踏板时,刹车油通过主缸传递至刹车卡钳,使刹车片与刹车盘接触,从而产生摩擦力,减速或停止车辆。
然而,随着车辆行驶里程的增加,盘式制动器也会逐渐磨损。
制动器的磨损主要表现在刹车盘和刹车片上。
刹车盘通常由铸铁或复合材料制成,其表面会因为与刹车片的摩擦而磨损。
磨损过程中,刹车盘的厚度会逐渐减小,且表面会出现不均匀的磨损痕迹。
而刹车片通常由摩擦材料和基材组成,当刹车片磨损到一定程度时,需要及时更换,以确保制动效果和安全性。
盘式制动器的磨损情况与多种因素有关。
首先,行驶里程是影响磨损程度的主要因素之一。
通常情况下,行驶里程越长,制动器磨损越严重。
其次,驾驶习惯也会对磨损产生一定影响。
频繁的急刹车和长时间踩住刹车踏板都会导致制动器磨损加剧。
此外,制动器的质量和制动油的性能也会影响磨损情况。
优质的制动器和制动油可以减少磨损,并提高制动效果。
对于盘式制动器的磨损情况,及时的检测和维护是非常重要的。
通常情况下,车辆在保养过程中会进行制动系统的检查,包括刹车盘和刹车片的测量。
刹车盘的测量可以通过测量其厚度和表面磨损痕迹来判断磨损情况。
而刹车片的测量通常通过观察其厚度和摩擦材料的磨损情况来判断。
当刹车盘或刹车片的磨损超过规定的极限值时,需要及时更换。
在使用过程中,我们还可以通过一些现象来判断盘式制动器的磨损情况。
例如,当刹车盘或刹车片磨损严重时,制动过程中会出现刹车抖动、刹车距离增加、制动效果减弱等现象。
此外,还可以通过观察刹车盘和刹车片的外观来判断磨损情况,如刹车盘表面是否出现明显的磨损痕迹,刹车片的厚度是否减小等。
乘用车制动盘性能惯性台架试验研究

引起了整个汽车行业的重视。 制动盘过度磨损或者磨损不均
匀, 会引起制动效能下降、 制动距离增长; 在高温条件下容易
产生变形和裂纹, 影响持续制动力, 有安全隐患; 过度磨损的
制动盘如不及时更换会加剧制动片的磨损, 缩短制动片使用寿
命。 在整车测试过程中对制动盘性能的探究有 一定 难度, 相
试。 根据整车参数的具体要求并结合相关制动盘生产企业的实
。 目前, 国内的乘用车和客车普遍采用盘式
际需要, 通过台架试验的方式模拟制动盘在高温骤冷 ( 水冷方
制动器, 制动盘作为盘式制动器总成的重要组成部分, 其性能
式) 以及高温下连续进行制动试验, 主要考核在不同的极端条
的优劣直接影响到行车安全性和驾驶舒适性。
caeri com cn。
C
M
Y
K
1 1 试验准备
1 1 1 试验台主轴转速的计算
制动器惯性试验台主轴转速与车速按如下关系换算:
n = 2 65v / r
式中: n 为制动器惯性试验台主轴转速, r / min; v 为试验车速,
中图分类号: U463 5 文献标志码: B 文章编号: 1674-1986 (2019) 12-071-07
Study on Inertia Bench Test of Performance of Passenger Vehicle Brake Disc
ZENG Fanzhuo, LEI Wen, ZHOU Yimin, WANG Yingguo
of passenger car brake disc. The setting of test parameters, the realization of test methods and the evaluation and analysis of test results were
汽车制动盘开裂原因分析

AUTO AFTERMARKET I汽车后市场D时代汽车 汽车制动盘幵裂原因分析陈莎罗荣宋泳刘源东风襄阳旅行车有限公司湖北省襄阳市441004摘要:随着经济和科技的不断发达化,路面交通的安全问题越来越受到重视,这就意味着对汽车的制动盘质量的要求也越来越高。
汽车的制动盘是必不可少的一个部件,由于其机械制造的特性,容易出现开裂问题,影响着汽车的驾驶安全。
文章的基本主线就是分析汽车制动盘开裂的原因,首先对制动盘的工作原理和重要作用简单阐述,接下来就系统罗列了造成汽车制动盘开裂的几个主要原因并分析其危害性,最后针对这些原因提出改善的具体措施,希望能够通过科学合理的管理手段减少汽车制动盘的开裂现象,提升我国车辆的生产行驶性能,从而提高路面公共交通安全。
关键词:汽车制动盘;危害性;具体措施;管理手段;公共交通安全1引言汽车的制动盘是汽车的重要组件之一,在汽车的行驶过程中起到制动的作用,由于 刹车也就是紧急制动的过程中主要运用了摩 擦的原理,其阻力很大一部分将会转变成热 量,汽车制动盘的表面会由于热疲劳而出现 开裂现象,因此保证制动盘的通风散热是十 分重要,这是汽车制动盘出现开裂的主要原 因。
良好的耐热性能将会直接决定制动盘的 使用寿命和使用性能,汽车制动盘的耐热 性、结构稳定性等与生产过程中材料的选用 和生产工序是否严格规范是息息相关的,这 些原因都会影响制动盘的质量和性能,决定 其是否能正常起到制动作用,直接构造了车 辆的安全性能。
2汽车制动盘的工作原理和重要作用2.1汽车制动盘的工作原理概述汽车制动盘也可以称作是汽车的盘式制 动器,主要是利用摩擦力起到制动的作用。
制动盘大多为金属材质,安装固定在车桥之 上,与传统的制动器相比,具有一定的优 势,主要可分为以下几方面:制动盘的耐热 性能比较好,结构稳定性较强》汽车制动盘 发生作用时不会受到汽车行驶方向的影响;便于设计双回路的制动系统;制动盘制动器发生作用时压力不集中于同一部位;制动盘尺寸适中,质量轻便且利于散热通风;汽车制动盘安装时制动衬块与制动盘之间距离较短,发生作用需要的时间也较短。
制动器管裂纹原因分析

2012年1月内蒙古科技与经济Januar y 2012 第2期总第252期Inner Mongolia Science T echnology &Economy No .2Total No .252制动器管裂纹原因分析X魏秋华(内蒙古第一机械制造集团有限公司,内蒙古包头 014032) 摘 要:重型汽车制动器管在潮湿的环境中使用时发生破裂,采用化学成分分析、力学性能试验、断口分析和金相分析等方法对破裂的制动器管进行分析。
结果表明,制动器管的裂纹主要产生于存在加工应力的弯曲部位,应力腐蚀是造成其破裂的主要原因。
同时在选材方面提出建议。
关键词:裂纹;破裂;断口;应力腐蚀;腐蚀产物 中图分类号:U 260.35 文献标识码:A 文章编号:1007—6921(2012)02—0159—03 国内某厂生产的重型汽车在重庆运行3至5个月后,陆续发生刹车系统失灵现象,对不同生产批次的车辆逐一拆卸检查,发现制动器管有裂纹和破裂泄露,实物见图1(a )所示。
该管采用规格为512×1.5mm 的H 62Y 2黄铜管制造,产品加工过程较为简单,采用管料直接进行冷弯成型后装配使用。
制动器管与发动机相连接,工作时管内通入空气介质,工作压力为1兆帕,介质温度为200℃~220℃,由于空气来自发动机,内中含有少量的油和水分。
为分析出现裂纹的原因,笔者对使用中出现裂纹的制动器管(管1)和未经使用的制动器管(管2)进行了对比试验,并提出了改进意见。
1 理化检验及结果1.1 裂纹宏观形貌用美国生产的H 1-SCOPE Advanced KH -3000三维视频显微镜观察制动器管的裂纹及外观质量,管1的裂纹集中分布在两个部位,一处在管的弯臂内侧,并与管的轴线方向垂直,有两条裂纹贯穿管的壁厚,其余为细小裂纹,形似金属挤压变形时产生的褶皱,见图1(b)(c)所示。
另一处与铜管的轴线方向呈一倾斜角,裂纹开口较宽,已贯穿壁厚,见图1(c)所示。
提升绞车制动器盘损剖析及措施

提升绞车制动器盘损剖析及措施提升机制动器盘划伤,使制动力矩减小,制动盘及闸瓦磨损加快,影响提升使用寿命和安全生产,通过采取切实措施修复,恢复正常生产。
标签:制动力矩;划痕;接触面积;贴磨闸瓦;正确操作和维护保养1 故障现象某矿新安装一台JK-2×1.5型矿井提升机,使用不久后出现制动盘表面划出一道道沟槽,拆卸闸瓦检查发现,闸瓦表面也出现了多道沟槽,同时,闸瓦表面镶嵌了大量白色、淡黄色铁屑,制动盘和闸瓦表面产生沟槽后,闸瓦实际接触面积减小,制动力矩减小,对设备的使用寿命和安全产生了严重影响。
分析该现象产生的原因,提出切实可行的解决措施,具有重要意义。
2 原因分析经检查:闸瓦与制动盘的接触面积不足、闸瓦与制动盘的间隙不均匀、闸瓦表面有一层压铸成型的硬皮、使用初期,司机操作不熟练,紧急刹车多,刹车频繁。
刹车时,间隙最小的闸瓦与制动盘先接触,其正压力最大,由于接触面积小,接触应力也最大,当制动盘表面受到很高的接触应力时,在摩擦力的作用下产生大量的热量,使闸瓦表面较高的部位,以及与其接触的制动盘部位,瞬间温度很高(闸瓦表面镶嵌的淡黄色铁屑,表明温度曾经达到400℃),制动盘虽然有一定的硬度,但高温下铁(Fe)原子会氧化成Fe2O3和Fe3O4,碳(C)原子氧化成CO和CO2,破坏了制动盘内部元素分布数量和材料性能,降低了制动盘硬度。
过高的接触应力使制动盘表面受到反复的拉应力而疲劳开裂,并沿锐角方向向内扩展,产生裂纹,麻点剥落或片状剥落,从制动盘上剥落的金属粒子、铁屑有的随制动盘转动带出了闸瓦,有的就在闸瓦正压力的作用下嵌入了闸瓦内部,成为磨粒,这些磨粒对制动盘和闸瓦起到磨损作用,造成制动盘表面粗糙降低,产生沟糟。
在闸瓦表面观察到沟槽是磨粒磨损的主要特征制动盘表面瞬间高温,加上闸瓦与制动盘接触面积小,接触应力大是制动盘表面剥落铁屑的主要原因,剥落的铁镶嵌在闸瓦表面形成磨粒,划伤制动盘。
在盘式制动器运行中,制动油压高、制动盘偏摆,使闸瓦间隙不均匀、提升系统长时间带闸下放重物、不正确的操作,都能引起制动盘表面瞬时高温,使制动盘产生划伤。
动车组转向架车轮制动盘裂纹分析研究

动车组转向架车轮制动盘裂纹分析研究发布时间:2021-01-21T06:07:54.427Z 来源:《中国科技人才》2021年第2期作者:王元[导读] 制动盘表面光滑平整、无异物击打痕迹,闸片状态无异常。
通过对运营过程中的裂纹制动盘进行解刨分析情况如下:中国铁路北京局集团有限公司北京动车段北京 102600摘要:制动盘是轨道交通车辆中的关键零部件,其主要作用是与制动夹钳配合,从而使高速列车停车、降速。
高速列车在频繁的制动力作用下,制动盘和闸片产生制动热负荷使制动盘在短时间内承受很大的温度梯度,长期作用下,这种冷热循环的交变载荷会使盘面出现热斑、磨损甚至裂纹,不仅会大大降低制动盘的使用寿命,甚至会引起灾难性的事故,通过对高速动车组轮盘裂纹的深入调查,对制动盘裂纹发生的原因进行了深入分析,可有效提高制动盘的使用寿命及可靠性。
本文通过对裂纹制动盘的材料及机械性能等进行研究,分析确定裂纹缺陷的产生原因,并根据原因分析提出解决措施,消除安全隐患。
关键词:制动盘;热负荷;裂纹1调查分析选取1套发生裂纹的制动盘进行分析研究,该套制动盘内侧制动盘未见裂纹,外侧轮盘紧固螺栓孔处存在2处裂纹,靠近制动盘外缘裂纹深度约为2mm,靠近螺栓孔附近裂纹深度已延伸至螺栓孔根部。
螺栓防松标记无错位,制动盘表面光滑平整、无异物击打痕迹,闸片状态无异常。
通过对运营过程中的裂纹制动盘进行解刨分析情况如下:1.1断口宏观形貌裂纹超限轮盘其裂纹已基本贯穿盘体厚度,靠近摩擦面表层的断口已明显发黑、被氧化;扩展区氧化程度较低,有明显的撕裂棱,指向裂纹浅表层的氧化区方向,说明表面裂纹形成后并向内继续扩展;压断区为新压开的断口,呈现浅灰色。
图4 内、外侧盘二次枝晶形貌1.3.2同批次无裂纹制动盘金相组织将服役后无裂纹的同批次轮盘作为对照进行解剖观察金相组织,可见制动盘摩擦环内的金相组织存在树枝晶,散热筋内无树枝晶。
1.3.3不同批次无裂纹制动盘金相组织将服役后无裂纹的不同批次轮盘作为对照进行解剖观察金相组织。
轨道车辆制动钳螺栓断裂失效分析与应力腐蚀敏感性评估

轨道车辆制动钳螺栓断裂失效分析与应力腐蚀敏感性评估摘要:制动盘制动也称之为安全制动,该设计即便在外界接触网故障无电时也能够正常使用,确保动车组能够安全停车,是动车组的重要安全部件,其工作原理是制动卡钳抱住制动盘摩擦,达到减速的目的。
每个制动卡钳上由两个M16×120的螺栓固定。
制动钳紧固螺栓断裂,明确其断裂原因的同时,对该部位螺栓应力腐蚀敏感性进行了评估,并提出改进建议。
关键词:轨道车辆;制动钳螺栓;断裂失效分析;应力腐蚀敏感性;评估引言连接螺栓断裂机理可以概括为螺栓盐雾腐蚀与应力共同作用下导致应力腐蚀,主要包括:1)“高温、高湿、高盐雾”的腐蚀环境中,耐腐蚀性能较差的螺栓在热应力作用下萌生裂纹,在热应力和拉应力的作用下进行扩展,发生应力腐蚀开裂,产生延迟脆性断裂。
2)螺栓由于未按规范进行固溶处理,材质部分成分含量偏离标准,致使耐腐蚀性能及韧性下降,导致应力腐蚀加剧。
为防止以后类似情况的发生,应严格进场质量把关,对后续采购的螺栓等紧固件部件严格按照标准进行验收,复检固溶处理等工艺处理情况,并适当采用表面涂层防护措施。
1断口分析宏观断口分析断口的宏观分析法,是一种对断裂件进行直观分析的简便方法,对螺栓断口进行宏观形貌分析,可以迅速而准确地识别出螺栓断裂类型、裂纹源位置,以及裂纹扩展途径和走向。
对断裂螺栓进行宏观目测发现,断裂起源于螺纹牙底区域,断口附近螺栓直径明显变细,该区域螺纹大径相差约0.83mm,出现明显的塑性变形和颈缩现象。
螺栓断口界面呈倾斜状,界面与拉伸轴线呈约30°夹角,表面较粗糙,基本符合拉伸扭转韧性过载断裂特征。
2应力腐蚀断裂指金属构件在静应力和特定的腐蚀环境共同作用下所导致的脆性断裂。
有资料显示,金属构件发生应力腐蚀的首要条件是金属构件在拉应力作用下,其次腐蚀介质与金属构件相接触产生应力腐蚀。
送检螺栓服役过程中承受拉应力作用,满足应力腐蚀开裂的力学条件。
经检测,该列车在维保时采用的清洗剂为酸性溶液,能谱分析腐蚀产物中存在S、Cl腐蚀性元素,提供了应力腐蚀的介质条件,从失效件断裂部位可以看出,腐蚀性介质在螺母旋合部位存在沉积现象,加剧了螺栓局部腐蚀。
浅析气压盘式制动器磨擦片磨损过快的原因

盘式制动作为制动方式的一种,以其制动间隙小、制动响应快、制动强度大、制动距离短、水稳定性强、散热性能好、热衰退少、安全性高、结构紧凑,维修简便等优点而受到推崇。
盘式制动器在客车上的应用,还处于起步阶段,离普及还有相当长的一段距离。
作为一项较新的技术,欧美国家自20世纪90年代初开始将盘式制动器用于公交客车。
至2000年左右,前、后制动均采用盘式制动器已经成为欧美国家城市公交客车的标准配置。
一、盘式制动摩擦片磨损过快问题提出盘式制动技术随着国外的一些车辆带入我国后,在与国内城市道路状况和运载负荷的结合方面还存在着不少问题,制动摩擦片磨损过快的问题是困扰城市客车持续使用这一技术的一大原因。
所谓客车盘式制动器摩擦片磨损过快,是指与前、后桥都采用鼓式制动器而车辆其他配置完全相同的城市客车相比较而言的。
采用盘式制动器的车辆平均行驶25000~27000km就需要更换制动摩擦片,少数车辆甚至在行驶不足2万km的时候,就需要更换制动摩擦片。
盘式制动器的这种表现根本无法满足相关标准中关于公交车辆制动摩擦片使用寿命不得低于3万km的要求。
而前、后桥都采用鼓式制动器的同种类型的城市客车,其制动摩擦片的使用寿命平均为6万km。
经过调查表明,国内几个著名客车生产企业生产的前、后桥全部采用盘式制动器的客车,也不同程度地存在的摩擦片磨损过快的问题。
尤其是在北京、上海等大城市公交市场运行的客车,这种情况表现得更为突出。
二、磨损量与车辆行驶里程之间的关系由摩擦学可知,正常工作期内摩擦片的表面磨损量与车辆行驶里程之间的关系服从一元线性规律,即W=ωL式中:W-总摩损量:ω-单位行程磨损量:L-车辆行驶里程就显得特别重要。
随着车辆的行驶里程的不断增加,盘式制动器摩擦片的磨损越来越大,当厚度接近磨损极限时,对客车的行驶安全来说,就构成一种严重的威胁。
此时,如果驾驶员或技术管理人员稍有疏忽,不认真监控摩擦片的厚度、不及时更换摩擦片,就会致使车辆面临摩擦片被磨光、制动盘被磨坏,进而导致制动功能失效、造成车毁人亡的严重后果。
汽车盘式制动器的研究进展

1 摩擦 衬 片压 力 分 布 规 律
车辆制 动时摩擦 衬 片表面形 成 的压力 分布 不但
状况 下 , 内外两 侧 制动 片的 压力分 布 都不 相 同 。 要完 整分 析制 动压力 分 布 , 将应 力 场 、 移场 应 位 和 温度场 作为统 一 的耦合 问题 来解 决 。可分为 两个 阶段 进行 研究 , 一个 阶段 先 假 设 制 动 压 力 在接 触 第
夫没 有按 摩擦状 态 进 行 划 分 , 出对 于 新 制 动 器而 提
研究 侧重 于试 验研 究 其 摩擦 特 性 , 随着 用户 对 其 制
盲, 制动 压力接 近 于均匀 分 布 。
实 际上 , 制动 衬 片压 力 分 布 受 到多 方 面 因 素 的 影 响 , 制动 气 缸 活塞 的 施 压 位 置 、 动 卡 钳 的结 如 制
面上 均匀 分 布 , 主要 解 决 盘 、 之 间 的 热 流 分 配 问 片
影响制动器的制动转矩容量、 热容 、 磨损 , 而且直接
影 响表面 的工作 温度 , 而影 响热衰 退 、 不稳定 性 从 热
及热 裂纹等一 系列 制动性 能 。 由于盘 式制动 器制 动 过程 中摩擦 副间温 度 沿 半 径方 向分 布不 均 匀 , 部 局
能的好坏和使用寿命 的长短。
在制动 器设计 上 , 根据摩 擦系统 特性 的不 同 , 目 前有 “ 片压 力均 匀分 布” 衬片均 匀磨损 ” 衬 和“ 两种 模
位移 , 以边界 单元 法更 适 合 于此类 问题 , 所 而且 边界
其温 度 比周 围表 面 高 , 它将 膨 胀并 形 成 “ 热点 ” 。局 部热 点的形 成导致 制动 压力不 均匀分 布 的进 一步 发 展, 这反过来 又造 成局 部温度 进一步 升高 , 面 温度 表
分析及检修雪铁龙轿车右前制动盘拖滞发热故障

【摘要】:一辆行驶里程超km的东风雪铁龙DC7140 型轿车。
该车在行驶中出现右前轮经常发热现象,制动效果变差,摩擦片磨损过快,增加了车辆运行使用的费用。
由于右前轮制动盘发热,而导致温度升高,甚至有制动盘受热变形,踩制动发抖、爆裂和轮胎爆炸的现象。
1.制动盘发热导致不良的后果东风雪铁龙DC7140 型轿车采用真空助力X 型双回路液压制动系统,带紧急制动助力功能和机械制动2 种系统。
前轮为盘式制动器,后轮为鼓式制动。
制动片的摩擦材料是用无石棉有机材料粘接而成的复合摩擦衬片,一般可经受的最高温度约315°C。
制动盘的材料为铸铁,其直径的公称尺寸为220mm,磨损量≤2mm。
车辆在炎热的夏季使用时,由于天气温度高,右前轮制动盘发热现象越来越严重,特别是在中午时分,或在交通堵塞的路段以及下坡时频繁制动,制动盘发热现象更为突出,以致制动盘冒烟带来一系列不良后果。
1)制动盘发热,超过制动器的耐热极限,制动摩擦片受热变质,表面碳化,摩擦表面间的摩擦系数相应下降,致使制动力矩急剧下滑,制动效能大大减退,制动的稳定性和可靠性降低,使制动距离相应延长,破坏原有的技术性能,从而影响行车安全。
2)制动盘发热,使制动摩擦片膨胀,制动摩擦面间隙减小,导致与制动盘拖滞,产生制动力矩,阻碍汽车的行驶,从而降低了发动机的动力性,增加发动机燃油消耗。
不仅增大运输成本,而且降低了运输效率,影响运输任务的顺利完成。
3)制动盘发热,是汽车制动性能变坏,摩擦片与制动盘间磨损加剧,制动器各机件提前损坏,缩短了维修周期。
增加了维修费用,导致成本加大,影响了经济效益。
4)制动盘发热,温度升高,还会引起制动盘爆裂及轮胎的爆炸。
2.发热的原因分析与排除措施制动盘发热是制动器拖滞的必然结果,而造成拖滞的原因,一般从以下5 个方面去考虑:一是制动踏板无自由间隙;二是制动总泵不回油;三是制动橡胶管路老化内部膨胀,影响制动液的回流;四是制动卡钳活动卡滞,制动缸不回位;五是制动蹄片间隙调整不正确。
动车组转向架车轮制动盘裂纹分析研究

动车组转向架车轮制动盘裂纹分析研究摘要:在动车组的迅速发展下,给其制动装置和材料的耐磨程度、疲劳性能、耐摩擦力等都提出了一定要求。
然而受实际铸造环节和运行环境的影响,制动系统当中常用的制动盘极易出现裂纹,不仅会影响基本的制动效果,还可能会引起严重的制动事故。
对此,为最大程度保证动车组的制动效果,就需从其裂纹样态、产生原因等方面着手进行分析,以此提出相应的解决对策。
关键词:制动盘;裂纹;动车组;转向架引言在动车组中制动盘是非常重要的一项零部件,它能够和制动夹钳相互配合,使列车降速或停止。
但如果制动频繁,其中所产生的热负荷就可能会导致制动盘在短期之内经历极大的温度差,长期下去其盘面势必会被磨损,由此产生热斑甚至裂纹。
如此以来,除了需要及时进行制动盘更换,增加成本,还可能会发生一些重大事故,带来严重的人员伤亡和财产损失。
因此重点对其裂纹原因进行详细分析,提出相应的解决措施具有一定现实意义。
一、动车组制动盘裂纹概述列车在实际制动过程中制动盘会产生巨大的热负荷,同时热量也会渐渐向内扩散,当制动活动完全结束之后就会渐渐冷却。
在这种冷热交替之下,其交变荷载就会导致盘面形成高温蠕变以及热疲劳裂纹[1]。
后续在继续制动操作中,细小的裂纹都可能会在交变荷载的影响下继续扩展,当达到一定限度之后就会给制动性能带来不良影响,直至引发制动事故。
有关研究发现,其摩擦面当中分布着大量径向裂纹与龟裂纹,其中前者在发现的时候深度就已经达到了限度,严重影响使用期限;而后者一般深度较浅,给制动盘使用期限带来的影响并不大。
也有一些研究表明,导致制动盘损坏的主要原因就是压应力和残余热应力。
二、制动盘裂纹分析以某一动车组已经产生裂纹的制动盘为例,其内侧并没有产生裂纹,而外侧在靠近紧固螺栓孔的位置处出现了两道裂纹。
整个制动盘表面平整光滑,没有被锤击过的痕迹,闸片也不存在一场状况,且当中的螺栓防松标记也没有错位。
通过对其进行详解剖解分析之后大致能看出以下几方面内容:(一)形态与面貌分析1.断口整体形态和面貌将该制动盘剖解开之后,发现其裂纹已经贯穿了盘体的整个厚度,特别是邻近摩擦面表层的断口已经出现了十分明显的被氧化以及发黑问题。
洗煤厂机修技术人员题库

试题内容装载点应保持货载在胶带正中不允许在( )上直接装载。
装配输送机机尾拉紧装置的丝杆、丝母机构时,应将丝杆、丝母的起点与终点处不完整部分的铸铁冷焊时选用( )焊条,焊缝抗裂性较好。
整齐、清洁、润滑、安全是设备( )的基本要求。
( )振动筛筛框、筛箱对角线允许偏差是( )。
振动筛筛缝磨损极限规定:小于3mm的筛缝,其最大磨损不超过原规格的( )。
振动筛两侧的两台激振器要求振幅( )。
张紧装置的作用就是将胶带张紧,使胶带与驱动滚筒具备足够的( ),使带式输送机正常运转。
窄轨轨道路线质量等级评定为优良时,主要检查项目单项合格率应在( )以上。
在同样的张紧力下V带产生的的摩擦是平带的( )左右。
在双轨运输巷道中(包括弯道)两条轨道中心线之间的距离必须使两列对开列车最突出部分之间的距离大于( )。
在熔池结晶过程中,沿各个方向均匀长大的颗粒晶体称为( )。
在焊缝根部未完全熔透的现象称为( )在干燥状态下,同样材质的两物料,其滑动摩擦的摩擦系数和滚动摩擦的摩擦系数相比较而言( )。
在带式输送机的减速器中,如果( )不符合要求,需更换新油。
在带式输送机的减速器中,除了油包水齿轮油外,油中水含量高于( )时,需更换新润滑油。
运用压缩空气时,其气流方向绝不能朝向( )。
预防维修的简称是( )有人触电导致呼吸停止心脏停跳,此时在场人员应( )。
有挠性牵引构件的输送机常见的有( )。
由于运动部件磨损,所引起的故障为( )。
用游标卡尺测量钢丝绳实际直径时( )。
硬齿面齿轮,齿面磨损达硬化层的( )时需要更换齿轮。
一般情况下,最高安全电压是( )。
一般减速机的工作环境温度可适用于( )。
液压油换油标准,机械杂质超过( )更换。
液压系统中使用的液压油,多为( )油。
液压系统的最大压力为10MPa,安全阀的调定压力应为( )。
液压系统的工作压力是指元件或系统工作时的( )压力。
液压系统常用的过滤器有烧结式、磁性式等共( )类。
汽车制动盘开裂原因分析
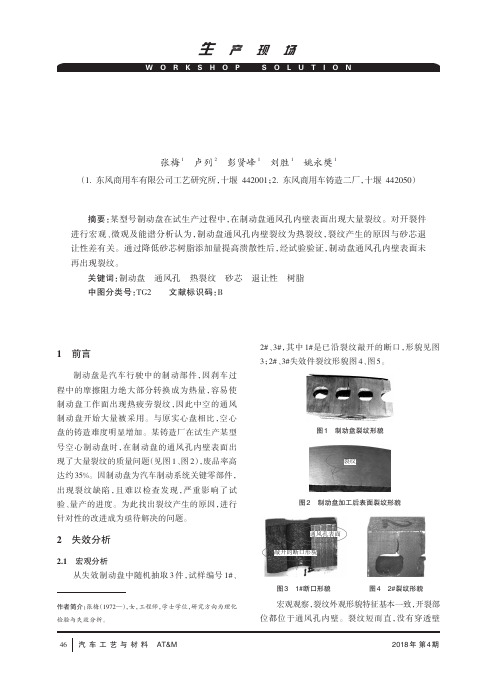
摘要:某型号制动盘在试生产过程中,在制动盘通风孔内壁表面出现大量裂纹。
对开裂件进行宏观、微观及能谱分析认为,制动盘通风孔内壁裂纹为热裂纹,裂纹产生的原因与砂芯退让性差有关。
通过降低砂芯树脂添加量提高溃散性后,经试验验证,制动盘通风孔内壁表面未再出现裂纹。
关键词:制动盘通风孔热裂纹砂芯退让性树脂中图分类号:TG2文献标识码:B汽车制动盘开裂原因分析张梅1卢列2彭贤峰1刘胜1姚永樊1(1.东风商用车有限公司工艺研究所,十堰442001;2.东风商用车铸造二厂,十堰442050)作者简介:张梅(1972—),女,工程师,学士学位,研究方向为理化检验与失效分析。
1前言制动盘是汽车行驶中的制动部件,因刹车过程中的摩擦阻力绝大部分转换成为热量,容易使制动盘工作面出现热疲劳裂纹,因此中空的通风制动盘开始大量被采用。
与原实心盘相比,空心盘的铸造难度明显增加。
某铸造厂在试生产某型号空心制动盘时,在制动盘的通风孔内壁表面出现了大量裂纹的质量问题(见图1、图2),废品率高达约35%。
因制动盘为汽车制动系统关键零部件,出现裂纹缺陷,且难以检查发现,严重影响了试验、量产的进度。
为此找出裂纹产生的原因,进行针对性的改进成为亟待解决的问题。
2失效分析2.1宏观分析从失效制动盘中随机抽取3件,试样编号1#、2#、3#,其中1#是已沿裂纹敲开的断口,形貌见图3;2#、3#失效件裂纹形貌图4、图5。
宏观观察,裂纹外观形貌特征基本一致,开裂部位都位于通风孔内壁。
裂纹短而直,没有穿透壁图1制动盘裂纹形貌图2制动盘加工后表面裂纹形貌裂纹图31#断口形貌图42#裂纹形貌通风孔表面敲开的断口形貌厚。
将2#、3#制动盘沿裂纹敲开,断口形貌与1#相同,即开裂部位均呈灰色,表明裂纹在高温下就已产生,以至于断口在铸型中就已被氧化,见图6、图7。
2.2微观分析三件样品宏观形貌一致,仅对2#、3#样品进行了微观分析。
垂直断口取样,样品经磨制抛光后,在光学显微镜下,2#开裂部位的断口表面存在厚度约15μm 的灰色层即氧化层(图8),在垂直断口截面处还发现一条裂纹,裂纹由断口表面向内部延伸(图9),裂纹内部也被灰色物质覆盖(图10)。
盘式制动器磨损情况记录
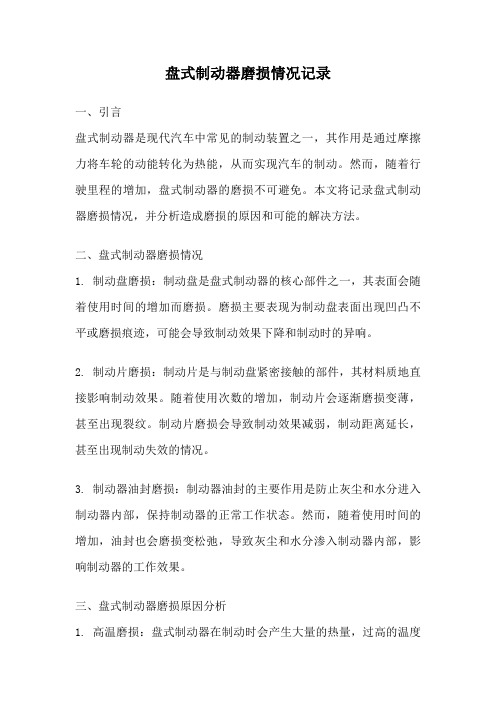
盘式制动器磨损情况记录一、引言盘式制动器是现代汽车中常见的制动装置之一,其作用是通过摩擦力将车轮的动能转化为热能,从而实现汽车的制动。
然而,随着行驶里程的增加,盘式制动器的磨损不可避免。
本文将记录盘式制动器磨损情况,并分析造成磨损的原因和可能的解决方法。
二、盘式制动器磨损情况1. 制动盘磨损:制动盘是盘式制动器的核心部件之一,其表面会随着使用时间的增加而磨损。
磨损主要表现为制动盘表面出现凹凸不平或磨损痕迹,可能会导致制动效果下降和制动时的异响。
2. 制动片磨损:制动片是与制动盘紧密接触的部件,其材料质地直接影响制动效果。
随着使用次数的增加,制动片会逐渐磨损变薄,甚至出现裂纹。
制动片磨损会导致制动效果减弱,制动距离延长,甚至出现制动失效的情况。
3. 制动器油封磨损:制动器油封的主要作用是防止灰尘和水分进入制动器内部,保持制动器的正常工作状态。
然而,随着使用时间的增加,油封也会磨损变松弛,导致灰尘和水分渗入制动器内部,影响制动器的工作效果。
三、盘式制动器磨损原因分析1. 高温磨损:盘式制动器在制动时会产生大量的热量,过高的温度会导致制动盘和制动片的材料发生变化,从而造成磨损。
2. 金属疲劳:长时间的制动会导致金属材料的疲劳,使制动盘和制动片的表面出现磨损和裂纹。
3. 环境因素:盘式制动器经常暴露在恶劣的环境中,如雨水、灰尘等,这些因素会加速制动盘和制动片的磨损。
四、盘式制动器磨损的解决方法1. 定期检查和更换制动盘和制动片:根据汽车制造商的建议,定期检查盘式制动器的磨损情况,并在必要时更换制动盘和制动片,以确保制动器的正常工作。
2. 注意制动方式:避免长时间连续制动,尽量采用间歇制动的方式,以减少盘式制动器的磨损。
3. 定期清洁制动器:定期清洁制动器表面的灰尘和污垢,防止其积聚在制动盘和制动片上,影响制动效果。
4. 定期更换制动器油封:定期更换制动器油封,以保持制动器内部的清洁和干燥,延长制动器的使用寿命。
汽车盘式制动器分析

2011届毕业生毕业设计(论文)汽车盘式制动器分析Analysis of automotive disc brake系别:汽车工程系专业:班级:学号:姓名:指导教师:完成日期:2010年12月14日河北交通职业技术学院摘要汽车制动简单来讲,就是利用摩擦将动能转换成热能,使汽车失去动能而停止下来。
汽车上使用最多的制动器就是盘式制动器,盘式制动器各部件在如此高温的状况下磨损非常严重,为了保证制动器的工作性能就需要定期的对盘式制动器进行检测,如果发现问题就需要及时进行维修与更换。
本文通过对盘式制动器结构的了解,提出了对各项部件维护前的准备和注意事项,然后利用举升机或千斤顶将车举起,用专用工具进行拆卸和检测,对制动器摩擦衬片的厚度是否合格,制动卡钳是否大修,以及对制动盘的精整和更换进行了系统的描述,确保了盘式制动器的正常工作性能。
关键词:盘式制动器检测维修AbstractAutomobile brake simple speaking, is to use friction at converting kinetic energy into heat energy, that car losing kinetic energy and stop. Car use most of the brake is disc brakes, disc brake parts in such high temperature condition wear very serious, in order to guarantee the brakes work performance is needs regular to disc brakes for testing, if found that the problem will need timely maintenance and replacement. This article through to disc brakes structure understanding, proposed to the various components maintenance preparation before and attention, then use lift or jack will raise, use a special tool car dismantled and testing, the brake friction facing the thickness is unqualified, brake calipers whether overhaul, and brake disc of finishing and replace the system are described, and ensure the normal work of disc brake performance.Keywords: disc-brake test and maintenance【目录】1.引言 (1)2. 盘式制动器概述 (1)3. 钳盘式制动器结构 (3)3.1 定钳盘式制动器 (3)3.2 浮钳盘式制动器 (3)4. 盘式制动器的检测与维修 (4)4.1 维修时的注意事项和诊断参数 (4)4.2 盘式制动器的故障检测和维修方法 (5)4.3 典型车型案例分析 (6)5. 结论 (7)参考文献: (8)致谢 (9)附录 (10)1.引言汽车制动系统是汽车行驶的一个重要主动安全系统,其性能的好坏对汽车的行驶安全有着重要影响。
- 1、下载文档前请自行甄别文档内容的完整性,平台不提供额外的编辑、内容补充、找答案等附加服务。
- 2、"仅部分预览"的文档,不可在线预览部分如存在完整性等问题,可反馈申请退款(可完整预览的文档不适用该条件!)。
- 3、如文档侵犯您的权益,请联系客服反馈,我们会尽快为您处理(人工客服工作时间:9:00-18:30)。
盘式制动器的高温裂纹摘要盘式制动器在一般的制动中受到很大的热压力,在紧急制动受到非同寻常的热压力。
大减速度的客车通常每个衬块每秒中产生达900度的高温。
这种高温将产生两种结果:(1)热震动,产生表面裂缝,(2)制动盘产生较大的塑性变性。
在转动圈数相对较少的大减速制动中,如果没有热震动,,将在旋转体的最厚处和盘式制动器的径向产生可见的裂缝。
由此分析发现,制动器失效是短周期热力学疲劳的结果。
用热流方程分析有限元素作出制动器温度纵断面图。
如果得到制动温度,将用这个温度来估计紧急制动时增大的压力。
研究表明,在大减速度制动时由于热压应力较大,而导致塑性变形发生。
算出拉力位移量,然后用Coffin—Manson法则来估计制动失效的圈数。
关键字:热疲劳;热裂缝;制动失效;热压力;疲劳。
1.简介在大减速度制动后,在制动盘上可观察到热裂缝。
热裂缝可分为两类:一类是热裂缝部分的穿过制动盘表面;另一类是透过性热裂缝,他完全透过制动盘体。
虽然热裂缝是由紧急制动引起的,但是仍没办法防止其发生。
本文将对盘水制动器的制动盘热裂缝做一个彻底的分析。
在此,将以载重汽车F-250皮卡的前制动盘热裂缝为例进行分析,如图1所示。
当卡车拖拽的挂车装满货物时,如果频繁的刹车,当听到“嘭”的一声或显著的滴答声,表示制动器失效。
制动盘是由灰铸铁按照图2的几何尺寸制造而成。
选择会铸铁是由于其熔点低,传热和散热较快。
制动盘由连接车轮和轴的头部.内制动片和外制动片组成。
外制动片直接与头部相连,,而内制动片则通过一系列的通风叶片连与外制动片。
在制动盘的头部加工一道沟槽,用以改变该部的应力集中现象。
内制动片不是直接与头部相连,它通过冷却叶片连接。
制动是内外盘面被制动衬块压紧。
频繁的摩擦阻止车轮旋转,同时产生大量的热。
当制动数秒后,制动盘上产生了大量的热而邻近的空间内却与常温无异。
热裂缝在客车上不常见,但是在卡车和动力车辆上却相对常见。
许多车辆还暴露出相当极端的问题。
值得注意的是,这些情况不是所谓的滥用,而是显示了制动技术的局限。
虽然这篇文章是由卡车的制动器失效的例子引出的,接下来就这个问题作一个人和车辆都使用的一般性论述。
图1图22.车辆力学制动就是以及时和重复的方式消耗掉车辆的动能。
为了估计制动中升高的温度,就必须算出施加于制动盘上的力。
图3展示了车辆的解析图,求质心的瞬时平衡,得如下公式:()()()212 12 1sincosxxlVghVKhxbmgFG GZ∆+∆+---∆-=•αα(1a)()()()212 22 2sincosxxlVghVKhxamgFG GZ∆+∆+---∆+=•αα(1b)图3这里:()[]Z M G x C x b lC h C mgS K y 212∆-+-⨯=ρ (2a) ()[]Z M G x C x a lC h C mg S K y 122∆++-⨯=ρ (2b) 和是有效制动系数,其他符号在图3中已标定。
假设制动发生在完全平坦的地面上(α=0),公式(1)可被进一步简化。
再者,Δx 向克认为是轮胎从中心的正常受力位移。
由于它相对于其他尺寸很小,可以把这些项从公式(1),(2)中忽略掉。
相当于每个轮胎上稍少于1%重量的制动系数也被忽略掉了。
结果,公式(1)简化为如下形式:⎪⎪⎭⎫ ⎝⎛=•V g h b l mg F G Z 1 (3a) ⎪⎪⎭⎫ ⎝⎛=•V g h b l mg F G Z 2 (3b) 公式(3)表明,重量的分布取决于每个轮胎距离质心的距离和车的加速度。
在减速时,重量转移到前轮,因此,大部分制动工作由前轮承担。
大多数汽车专有比例阀,用控制前后轮液压力的分配,形成前后轮负荷分配比例为60/40。
这种分配用于随后的制动分析。
图4位前制动盘-轮胎的受力图,得出如下的等式:0==-=∑y y ma W N F (4a)x tire rotor axel x ma F F F F =+-=∑2 (4b)αrotor tire tire rotor rotor I F r F r M =+=∑)()2(0 (4c)图4由于60%的载荷由前制动器承担,单个制动盘的动力由公式(5)给出:()()()⎰⎰==•dt t v F dt t P M rotor rotor disipated 2213.020 (5) 消耗与制动盘的能量等价于实际流入制动盘的热量,用这一关系可以预测制动盘上的温度变化量。
对于恒加速度,可以得出如下的动力学关系式:(6)F rotor 不随时间变化,而V rotor 随时间呈现性变化。
因此,能量平衡可变为:()()()⎪⎪⎭⎫ ⎝⎛⎪⎭⎪⎬⎫⎪⎩⎪⎨⎧-==•⎰2000202122213.0stop stop stop tire rotor rotor t rotor rotor t t v t v r r F dt t v F Mv stop (7) 工业标准明确规定:紧急制动是在6秒内把车速从45m/s 降至0。
实验表明,300圈这样的制动足以是制动盘产生热裂缝。
汽车制动一般用表1所时的数据进行计算:表1:汽车数据汽车质量 M 1500Kg初速度 V 0 45m/s制动时间t stop 6s有效制动盘半径 r rotor 0.10m轮胎半径 r tire 0.38m()⎪⎪⎭⎫ ⎝⎛⎪⎭⎪⎬⎫⎪⎩⎪⎨⎧-••••=2002021221%30stop stop stop tire rotorrotor t t v t v r r Mv F (8) 瞬间热流量直接用下式计算: ()t s w W t Q in ⎪⎭⎫ ⎝⎛-=•656.12938.75 (9) 最后,制动盘所需的总制动力是由制动钳夹紧使车停止所需的力来计算。
二家尽力可以用摩擦公式来计算,这里μ=0.4:N F F pad rotorcaliper 000,16≈=μ (10)这个力在制动盘上产生夹紧力,同时制动力产生剪切力。
制动衬块的中心角一般是60度。
现在接触面积是A=53cm 。
利用已知的面积和压力代入公式(8)和(10),制动盘压力如下:MPa 2.1=τ (11)2.1 材料性质在制动应用中,工业用薄片灰铸铁。
对图1种描述的制动盘进行硬度检验已确定铁的纯度。
分别测量头部,外制动面,内制动面。
出现以下几种情况:首先,最硬的是内制动盘面(97HRB ),其次是外制动盘(94HRB ),最后是头部(88HRB )。
统计比较这些数据表明:没出的硬度明显不同于别处。
这种硬度的不同是由于浇铸过程中仍却速度不同造成的,而不是制动盘的热过渡现象。
Rockwell-B 硬度属于Brinell 硬度的范围,170-220HB 。
通过与手册的数据比较,表明这种的合金为GG25铸铁,其主要材料组成列于表2:表2:材料的疲劳极限参量材料 Brinnel 硬度 σ(Mpa ) E (Gpa ) σf b εf cGG25#4 174 215 90 241 -0.115 0.008 -0.360从外制动盘上靠内侧用油冷锯取下一部分作为样品观察其微观组织。
缺血样本是可以看到剩余张应力:第一次切割时可以看到制动盘上有的部分约有1cm 宽的裂缝。
当锯子在内径时,伴随着“蓬”的一声,裂缝分开数毫米(图5),这个切口显示了制动盘上最初的组成。
第二次切示了切割的真实宽度,因为第一次的切口包括了环形剩余张力在内的位移。
把样品擦亮,并用5%的溶液浸蚀,在多个点检查样品的微观组织,如图5指示的1,2,3位置。
微观组织证明制动盘的材料是片状石磨(图6),除了石磨片外,图6的低倍放大图也发现了在浇铸时坚硬的球状矿渣杂质,这些杂质对制动盘热性能有显著的影响。
不同的位置硬度不同,符合图6所示的微观组织图。
硬度较高的地方有较好的耐磨性。
图53.估计制动温度分析有限元素用以估计制动盘上温度的分布。
假设制动盘径向对称,选择性质相同的部分作为代表性体积,分成50个单元。
是与衬块接触的制动盘面逐渐升温,而接近头部的表面和横断面由于径向对称而被绝热。
其他表面进行缓慢的传热,热产地系数从30W/m ·k在每个连续的时间段内以单一的速度递减,并且快于制动转速。
制动盘的初始温度定为300K 。
现以6s 为时间间隔进行瞬态分析,在0.5秒内运用以给定的热流公式(9),结果曲线有一系列的0.5秒的时间间隔组成。
哲学之别衬块面积均分后输入热流表(J/m )。
图7展示了制动2.5s 后制动盘的宽度方向上的纵断面温度曲线图6图74.估计制动盘寿命制动引起制动盘面温度迅速上升,从而导致其热震动。
这个问题可以由计算表面压力来解决。
制动使盘体的温度迅速上升而头部只有少许的变化,从而限制了制动面。
另一种办法是忽略热震动而集中考虑制动盘头部的热压力。
假设头部仍然保持室温,限制外盘面的热转移,在此我们集中考虑制动盘的热压力。
头部是一个几何模型,而不是开口圆柱。
头部产生的约束似与外盘体环形面上产生的内压力,并且大体等于约束压力。
我们忽略内盘体和与他相连的叶片的影响,虽然这只是一个近似的简化,但是得到的结果与实验很吻合。
轮毂限制了制动盘的大小,如图8所示。
如果没有这个限制,制动盘半径可以按公式随意扩展:Δb=b αΔT (12)图8尽管如此,总的偏移量是由头部的弹性向外位移和制动盘的向内位移组成。
在此受力体的向内偏移量为:⎭⎬⎫⎩⎨⎧+⎪⎪⎭⎫ ⎝⎛++⎪⎭⎫ ⎝⎛=∆v b a b a b E P b 2222 (13) 图8给出了个符号代表的意义。
头部的向外位移为:()v c EP c -••=∆1 (14) 这两个位移的和必须等于制动盘总的热位移量,即:b c Tb ∆+∆=∆α (15)在头部和盘体相互作用时,b=c ,因此()⎥⎦⎤⎢⎣⎡+⎪⎪⎭⎫ ⎝⎛+++-••=•∆v b a b a b E P v b E P b T 22221α (16) 在此限制压力为:122221-⎥⎦⎤⎢⎣⎡+⎪⎪⎭⎫ ⎝⎛-+∆=b a b a TE P α (17) 为了达到与头部相当的限制压力,去盘体的厚度内的平稳温度,即t=2.5s 时的温度。
当制动盘的温度达到200度时,平均温度在圆周和径向产生的压力为:()()2222221b a r r a Pb -+-=σ (18) ()()2222222b a r r a Pb --=σ (19) 这里,σ1为周向压力,σ2为径向压力。
把这些点联成线和Mises 等价曲线一起展示在图9中,从中可以看到平均压力大约为180Mpa,而GG25铸铁合金的屈服强度是215Mpa ,弹性模数为90GPa ,图9表明,制动温度产生的热压力几乎超过屈服强度,接近中心,延长了1cm 。
再者制动盘的屈服与压缩取决于制动,而环形剩余拉力取决于冷却。