[汽车零件]汽车零件注塑生产的应用与实践
注塑工艺在汽车零部件制造中的应用

注塑工艺在汽车零部件制造中的应用注塑工艺在汽车零部件制造中的应用汽车零部件制造是汽车工业中至关重要的一部分,注塑工艺作为一种先进而有效的制造方法,在汽车零部件制造中发挥着重要作用。
本文将从注塑工艺的定义、优势以及在汽车零部件制造中的应用等方面进行探讨。
首先,注塑工艺是一种将熔化的塑料材料注入到模具中,通过冷却和固化来制造成型的工艺。
相比传统的制造方法,注塑工艺具有以下几个优势。
首先,注塑工艺可以实现高效生产,通过自动化设备和流水线生产,大大提高了生产效率。
其次,注塑工艺可以制造出形状复杂的零部件,模具可以根据设计要求进行定制,使得产品的制造更加灵活多样化。
此外,注塑工艺还可以实现材料的节约和回收利用,减少了资源浪费和环境污染。
在汽车零部件制造中,注塑工艺的应用广泛而深入。
首先,汽车内饰件的制造离不开注塑工艺。
例如汽车座椅、仪表盘、车门内饰板等零部件,通过注塑工艺可以制造出形状精确、表面光滑的产品,提升了汽车内饰的品质和舒适性。
其次,汽车外观件的制造也离不开注塑工艺。
例如汽车前后保险杠、车灯外壳等零部件,注塑工艺可以制造出具有良好外观质量和抗撞击性能的产品,提高了汽车的安全性和美观性。
此外,注塑工艺还可以应用于汽车动力系统和悬挂系统等零部件的制造,提高了汽车的性能和可靠性。
然而,注塑工艺在汽车零部件制造中也面临一些挑战和难题。
首先,材料选择是一个重要的问题。
汽车零部件需要具备耐高温、耐磨损、耐化学腐蚀等特性,因此需要选择适合的塑料材料。
其次,模具设计和制造也是一个关键环节。
汽车零部件的形状复杂多样,模具需要具备高精度和高耐用性,因此需要投入大量的研发和制造成本。
此外,注塑工艺还需要进行合理的工艺参数设计,以确保产品的质量和性能。
总之,注塑工艺在汽车零部件制造中发挥着重要作用。
通过提高生产效率、制造形状复杂的零部件以及实现材料的节约和回收利用等优势,注塑工艺为汽车零部件的制造提供了先进而有效的方法。
汽车注塑模具基础知识
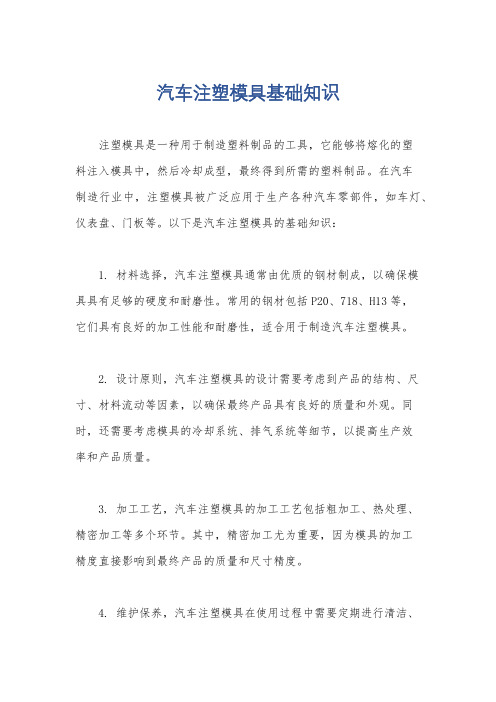
汽车注塑模具基础知识
注塑模具是一种用于制造塑料制品的工具,它能够将熔化的塑
料注入模具中,然后冷却成型,最终得到所需的塑料制品。
在汽车
制造行业中,注塑模具被广泛应用于生产各种汽车零部件,如车灯、仪表盘、门板等。
以下是汽车注塑模具的基础知识:
1. 材料选择,汽车注塑模具通常由优质的钢材制成,以确保模
具具有足够的硬度和耐磨性。
常用的钢材包括P20、718、H13等,
它们具有良好的加工性能和耐磨性,适合用于制造汽车注塑模具。
2. 设计原则,汽车注塑模具的设计需要考虑到产品的结构、尺寸、材料流动等因素,以确保最终产品具有良好的质量和外观。
同时,还需要考虑模具的冷却系统、排气系统等细节,以提高生产效
率和产品质量。
3. 加工工艺,汽车注塑模具的加工工艺包括粗加工、热处理、
精密加工等多个环节。
其中,精密加工尤为重要,因为模具的加工
精度直接影响到最终产品的质量和尺寸精度。
4. 维护保养,汽车注塑模具在使用过程中需要定期进行清洁、
润滑、修复等维护工作,以延长模具的使用寿命和保证生产的稳定性。
总的来说,汽车注塑模具是汽车制造过程中不可或缺的重要工具,它的质量和性能直接关系到汽车零部件的质量和生产效率。
因此,对汽车注塑模具的基础知识的掌握和应用是非常重要的。
注塑模具用途

注塑模具用途注塑模具是一种工业用的设备,广泛应用于制造各种塑料产品,如手机外壳、纺织品用品、家电外壳、汽车零件等。
注塑模具的主要功能是实现塑料制品的量产,样式和质量稳定,从而满足市场的需求。
注塑模具在现代工业生产中的作用越来越重要,下面详细介绍一下注塑模具的用途。
1.制造各种塑料制品注塑模具是制造塑料制品的关键设备之一,可以生产各种形状和尺寸各异的塑料制品,如塑料桶、塑料杯、塑料工具箱、塑料牙刷、塑料毛巾架等。
注塑模具提供了制造塑料制品的高效、低成本和条理性。
通过注塑模具,制造商可以在短时间内批量生产塑料制品,满足市场对产品的需求。
2.生产汽车零件汽车零件是注塑模具的重要应用领域之一。
例如汽车仪表板、前灯、后灯等关键部件,可以采用注塑模具进行生产。
通过模具运用注塑技术,可以快速地生产大量的零件,保证零件质量的统一和称量,从而提高产品的生产效率和降低了成本。
注塑方式还可以保证零件表面的平整度、硬度和透明度,使汽车外观更加美观。
3.制造电子产品注塑模具可为广泛的电子产品提供制造支持,如手机外壳、电视机外壳、音响、收音机和电脑外壳等。
通过模具制造电子产品,可以生产具备美观、高耐用性的产品,并且可以生产大量的产品,保持产品的一致性和稳定性,以满足市场对产品的高需求。
4.定制工业零件模具制造技术可在低成本、高强度、高精度的条件下大规模生产工业零件。
注塑模具可以生产各种规格和形状的金属或塑料零件,如夹具、模头、钢板、封头、瓶塞、塑料标签、电线和电缆绝缘体等。
注塑模具在工业零件制造过程中提供了高质量的制造方案,有效提高了生产效率和工业制品的质量。
总之,注塑模具是制造塑料制品的关键设备之一,在现代工业生产中用途广泛。
模具生产工艺的发展和提高,可以有效提高产品质量和生产效率,提高企业的竞争力。
随着科技的加速发展,注塑模具的应用领域还将更加广泛,对于工业制造和新产品开发都会有更大作用。
薄壁化注塑技术在汽车零件上的应用

薄壁化注塑技术在汽车零件上的应用摘要:安全、环保、节能是当下汽车工业发展中三大关键性话题,汽车轻量化是不可忽视的重要策略。
与此同时,保险杠是汽车运行中必不可少的安全件、外观件,要在细化分析的基础上从材料、结构、制造工艺等层面入手,灵活应用薄壁化技术的同时优化汽车保险杠设计,在控制保险杠重量的基础上有着较高的安全性、装饰性、功能性,持续改进汽车质量的同时实现综合效益目标。
本文基于薄壁化注塑技术在汽车零件上的应用展开论述。
关键词:薄壁化注塑技术;汽车零件;应用引言对于非金属材料,使用较成熟和较轻的技术制造薄材料(例如b .保险杠、车门板等。
),用于钢造型(例如。
b .前面板)和低密度材料的应用。
随着新能源汽车越来越普及,电池续航时间尤为重要,连续性与汽车质量密切相关,是汽车行业面临的一个问题。
在开发通过减少建模周期来提高生产效率和降低成本的技术时,压缩薄材料有助于满足性能要求、降低质量和降低成本。
1薄壁注塑成型定义薄壁注射方式,也称为薄壁模具环境,目前在薄壁模具方面定义不一致。
在行业中,塑料部件的厚度小于1mm,塑料投影面大于50cm2称为薄壁形状。
但是,对于汽车行业来说,销认为通过材料和工艺改进,传统抽壳可以打破,并且可以将制造性能视为薄壁形状。
2薄壁化材料测试标准熔体指数:以GB/ T3682. 1-2018测量塑料熔体流动速率(MFR)和熔体流动速率(MVR)。
第1部分:标准方法;密度:经GB/ T103. 1-2008测试,测量塑料非泡沫密度,第1部分:潜水网、液体刻度和滴度规定;拉伸强度:根据GB/ T1040. 2-2006进行测试,测量塑料拉伸性能第2部分:塑料和铸造模具的试验条件;弯曲强度:通过GB/ T9341-2008“塑料弯曲性能”测试;冲击强度:检查塑料的冲击强度(GB/ T1824-2008)。
3薄壁注塑成型技术对于薄壁注塑成型技术来说虽然在业界还没有对其形成一个较为统一定义,但是整体来说,成型塑件的厚度小于1mm,并且塑件的投影面积超过50平方厘米的注塑成型,都可以被称为是薄壁注塑。
汽车配备行业各种零部件生产工艺特点大全(1)

汽车配备行业各种零部件生产工艺特点大全(1)1. 钣金加工工艺- 特点:钣金加工工艺是根据汽车的外形和车身零部件的设计要求,通过对钣金材料的切割、弯曲、冲压、焊接等工艺进行加工制造的一种技术。
- 应用:钣金加工工艺广泛应用于汽车车身、车门、引擎盖等钣金零部件的制造过程中。
2. 塑料注塑工艺- 特点:塑料注塑工艺是将塑料颗粒加热熔化后通过注塑机射入模具中,经冷却固化后得到所需形状的一种制造工艺。
- 应用:塑料注塑工艺广泛应用于汽车内饰件、仪表盘、车灯外壳等塑料零部件的生产过程中。
3. 金属精密铸造工艺- 特点:金属精密铸造工艺是使用铸造机或压铸机将熔化的金属注入经过精密加工的模具中,通过冷却后得到所需的金属零部件。
- 应用:金属精密铸造工艺广泛应用于汽车发动机零部件、传动系统零部件等金属零部件的制造过程中。
4. 焊接工艺- 特点:焊接工艺是将两个或多个金属零部件通过加热、压合或填充金属等方式进行连接的一种制造工艺。
- 应用:焊接工艺广泛应用于汽车车身结构、底盘框架等零部件的制造过程中。
5. 电镀工艺- 特点:电镀工艺是通过电解溶液中的金属离子在金属表面上进行还原沉积,以增加金属零部件的耐腐蚀性和装饰性。
- 应用:电镀工艺广泛应用于汽车车身外部部件、进气格栅、车轮等金属零部件的制造过程中。
6. 热处理工艺- 特点:热处理工艺是通过对金属材料进行加热、保温和冷却等控制过程,改变其组织结构和机械性能的一种处理方法。
- 应用:热处理工艺广泛应用于汽车发动机零部件、传动系统零部件等金属零部件的制造过程中。
以上是汽车配备行业中常见的零部件生产工艺特点,不同工艺在不同的零部件制造过程中发挥着重要的作用,为汽车的性能和品质提供了保障。
浅析双色高光注塑产品的成型工艺和性能及在汽车行业中的应用

AUTO TIME115MANUFACTURING AND PROCESS | 制造与工艺时代汽车 1 引言随着当今科学技术的发展,生产制造水平的提升,以及人们对汽车外观品质、性能追求的不断提高,双色高光注塑产品被广泛的应用在汽车内外饰产品中。
这种先进的注塑成型方式,为汽车零部件的生产制造提供了全新的可能性。
双色高光注塑工艺,不仅可以实现在同一产品上呈现出两种不同感知颜色的视觉美感,还可在同一个产品上实现其中一种材料呈现外观品质,另一种材料实现内部结构性能的优势,从而使得产品在外观品质与结构性能上结合互补,表现出卓越的综合性能。
常见的双色高光注塑原材料粒子搭配有“PC-Red+PC-White”,“PMMA+ABS”,“PMMA+ TPE”,“ASA+PMMA”,“ASA+ EPDM”等。
“双色”原材料粒子的配对,取决于造型设计师对产品外观和性能的要求,但是其配对的前提是必须能够满足两种材料粒子本身性能的两个兼容性,即为粘合相容和加工相容。
其中,PMMA 与ABS 既是具有很好的相容性的两种原材料,两者的混合搭配,可以取长补短,提高的产品的硬度和光泽度[1]。
2 原材料的组成2.1 PMMA 材料聚甲基丙烯酸甲酯(polymethyl methacrylate),简称 PMMA。
属于长链高浅析双色高光注塑产品的成型工艺和性能及在汽车行业中的应用赵兴旺江铃控股有限公司 江西省南昌市 330052摘 要: 本文主要以“PMMA-Piano Black +ABS-G10 Black”两种原材料粒子的搭配为例,对双色高光注塑的汽车前后门窗框装饰盖板产品的成型工艺和性能进行分析介绍,以及浅析采用双色高光注塑工艺成型的多种产品在汽车内外饰零件中的应用。
关键词:双色高光注塑;PMMA/ABS;前后门窗框装饰盖板;汽车分子聚合物,主链为—C—C—单键结构,链性柔软。
具有高机械强度,表面高光泽度,优异的耐候性、耐划擦性、耐化学性等杰出的综合性能[2]。
注塑件包覆工艺__解释说明以及概述

注塑件包覆工艺解释说明以及概述1. 引言1.1 概述注塑件包覆工艺是一种将注塑件表面涂覆或包裹一层特定材料的加工方法,以实现增强结构强度、改善外观质量、提升耐用性和保护性能等目的。
该工艺在汽车制造、电子产品生产以及医疗器械行业等领域得到广泛应用,并且其技术特点逐渐被人们重视和认可。
1.2 文章结构本文将全面阐述注塑件包覆工艺的定义、原理、应用领域以及关键技术特点。
接着,对注塑件包覆工艺进行详细概述,包括历史背景、工艺流程简介和关键技术。
随后,通过分析主要应用案例,探讨该工艺在汽车零部件、电子产品外壳和医疗器械领域的实践与发展趋势。
最后,在结论与展望中总结当前注塑件包覆工艺的优缺点及存在问题,探讨未来发展方向和研究重点,并对其应用前景进行展望。
1.3 目的本文旨在系统性地介绍和分析注塑件包覆工艺,为相关领域的制造企业和研究人员提供有用的参考和指导。
通过对该工艺的深入探讨,能够增进对其定义、原理、应用领域和关键技术的理解,并促进业界对注塑件包覆工艺发展的思考与创新。
最终,希望推动该工艺在各个行业中的更广泛应用,并为相关产业链的发展做出贡献。
2. 注塑件包覆工艺解释说明2.1 注塑件包覆工艺定义注塑件包覆工艺是一种在已完成注塑成型的零部件表面上附着一层特殊材料的技术。
该技术利用各种粘结剂和涂料,通过不同的涂装方法,将附加材料牢固地覆盖在注塑零部件的表面上,以实现外观装饰、功能增强或保护作用。
这种工艺能够提供物理性能改善、耐磨损、防腐蚀和防UV等功能,为注塑产品赋予更高的价值。
2.2 注塑件包覆工艺原理注塑件包覆工艺基于几个基本原理来实现:- 表面处理:在进行包覆前,需要对注塑零部件表面进行清洁和处理以去除污垢和氧化物,并确保与涂层之间有足够的附着力。
- 选择合适数量和类型的粘接剂:根据需要,在注塑零部件表面应用适当类型和数量的粘接剂。
常见粘接剂包括聚氨酯、丙烯酸酯、环氧树脂等,其选择通常取决于底材和涂层材料的特性以及作用要求。
汽车模内镶件注塑成型( IMD )技术

汽车模内镶件注塑成型(IMD )技术塑料加工商们正在将可成型彩色薄膜视为一个经济、耐用、环境友好的装饰手段,它可使零件在脱模时即已完成装饰。
模内镶件注塑成型(IMD )技术,利用的就是这种可成型薄膜,可替代传统的、在零件脱模后采用的涂漆、印刷、热模锻、镀铬工艺。
该技术的首次成功应用是制成了一些小型的、相对较平的汽车内外饰零部件和手机零件。
今天,IMD技术有了更进一步的发展,可以制成更大的三维零件,例如整个仪表板、汽车保险杠、托板、汽车顶盖,甚至汽车、卡车的发动机罩。
据说,第一个实现商业化的、无需涂漆的水平车身板已经应用在Smart双座敞篷轿车上了。
IMD技术可节省再加工的费用,这对汽车工业极具诱惑力。
GE Plastics的Lexan SLX(一种聚碳酸酯共聚物)车身零件生产经理Venkata-krishnan Umamaheswaran说:“汽车上最贵的就是油漆了,涂漆生产线是汽车装配车间最大的投资,会占据车间一半的地面空间,而且一年内会产生1500多吨VOCs(挥发性有机物)。
”IMD技术的优势还包括:边角料产率低;可在同一地点完成零件的成型和装饰;回收性更好。
IMD技术可获得A级表面,且无流痕,更不会像流痕那样造成“模内驻色”。
但是如果零件本身就有很多孔,必须在脱模后进行装饰,那么IMD技术的经济效益则会大打折扣。
IMD技术的倡导者们宣称:利用最新一代的可成型薄膜制成的车身板,具有与涂漆金属板相媲美的甚至更高的抗划伤性和抗冲击性。
但是,假设汽车制造商们对涂漆生产线仍然施以巨额投资,则IMD在近期内还是无望完全取代涂漆工艺。
不过,工业观察家们相信:在美国,今后即使有投资,也很少会出现建造大型涂漆生产线的情况。
IMD技术首先将一块已经被印刷、涂覆或染色过的塑料薄板经冲切成坯料后,热成型成最终产品的形状。
修正后,把它放入注射腔内,从型腔后面注入一种与其相容的基体材料,最后得到成品。
成品的表面可以是纯色的,也可具有金属外观或木纹效果,还可印有图形符号。
实现汽车保险杠快速化注塑成型的研究与应用

实现汽车保险杠快速化注塑成型的研究与应用赵理罗毅黄冬东风本田汽车合成树脂科【摘要】目前汽车保险杠的生产要紧采纳PP(聚丙烯)树脂,通过成型机与模具一次注塑成型。
本文通过详细研究保险杠成型各道工序与工艺条件,提出了缩短注塑成型周期的具体方式,采纳模具开合,制品顶出与退回,掏出机夹取制品三个步骤最大化重叠实现节拍快速化,并成功应用于实际生产。
【关键词】汽车保险杠注塑成型工艺优化1.汽车保险杠加工工艺简介汽车保险杠历史沿革20世纪70年代以前汽车的前后保险杠都仍是以金属材料为主,用厚度为3毫米以上的钢板冲压成U形槽钢,表面处置镀铬,与车架纵梁铆接或焊接在一路,与车身有一段较大地间隙,像是一件附加上去的部件。
车与树脂的关系开始于1926年福特distributor汽车利用的爱惜罩,HONDA于1958年开始利用树脂材料成型摩托车的爱惜罩,而且在内外装部品上也利用了树脂材料。
可是树脂材料在汽车中的普及还只是处于起步时期。
随着工业技术的进展,汽车保险杠作为一种重要的平安装置也走向了革新的道路,专门是以小轿车为主的小型汽车和微型汽车,前后保险杠除维持原有的爱惜功能之外,还要追求与车体造型的和谐和统一,追求本身轻量化。
而塑料被用做汽车保险杠就容易实现以上诸多要求,塑料的结构特性使其具有缓冲性好,重量轻,比金属材料更易加工制造等。
同时,塑料保险杠具有本钱低、耐侵蚀、成设计自由度大等优势。
通过量年的进展,汽车保险杠目前形成了以PP(聚丙烯)材料为主材,并加入必然比例的橡胶或弹性体材料、无机填料(滑石粉为主)、色母粒、助剂等,通过注塑成型进行生产的模式。
保险杠注塑成型简介注塑成型是将粒状或粉状塑料加入注塑成型机机料筒,通过加热融化呈流动状态,然后在注塑机的移动螺杆快速而又持续的压力下,从料筒前端喷嘴中以很高的压力和专门快的速度注入闭合的模具内,经冷却固化后,开模取得与模具型腔相应的制品。
注塑成型机大体结构如图1。
图1 成型机结构成型机要紧由材料供给料筒、塑化和射出螺杆、模具(包括动模和定模)、顶出机构、锁模机构和驱动机构组成,依驱动机构不同又分为油压型成型机和电动型成型机。
浅谈嵌件注塑技术及其自动化生产在汽车内饰零件中的发展趋势

不同材质各有的特性可以在同一个产品 上充分结合并展现;
不同材质的物理性能优势能够满足一些 新产品设计的特殊性能需求;
缩短产品制造生产工序,避免大量的且 复杂的装配作业;
相对于几道直接装配生产模式,嵌件注 塑使得复合产品的可靠性更加高;
2 嵌件注塑工艺的嵌入方式
纯人工放置:人工放置模式局限性较大, 不适合大型吨位注塑机(一般超过 350 吨以 上),仅限一些简单且结构较小的嵌件产品 生产,生产效率相对较低,且安全性不足,
AUTO TIME 123
Copyright©博看网 . All Rights Reserved.
AUTO PARTS | 汽车零部件
图2
开始 start
顶杆 / 抽芯返回 ejector&core back
放置嵌件在模具内 put insert in the mould
合模 clamp close
注射 injection
保压 hold
取件 take out
顶出 / 抽芯 ejector&core out
开模 clamp open
冷却 cooling
朔化 / 计量 charge
复循环。 为了实现上述术细节问题需特 别关注 ;
(1)机械抓手设计复杂性:由于嵌件注 塑工艺相对传统注塑工艺增加了一步嵌件放 置环节,对于机械抓手的设计需要兼备嵌件 以及注塑成品取件的两个部分,注塑成品的 取件部分,设计与应用已非常成熟,没什么 特殊,一般都是吸盘吸取,夹具夹取或两者 结合形式为主;其复杂性在于嵌件部分,由于 嵌物有些是单一材料简单构造(见图 3),也 有些是多种材质复合型的复杂构造(见图 4)。
为了确保嵌物放入模具型腔时就能精确 放置,在抓取时就需要精确抓取定位,故导 向,限位与感应判断是该部分必不可少的三 大设计要素,之前做过的一个实例项目,其 嵌件抓取要求特别高,主要分成了两块细节, 一是应用插片机构来定位气囊门总成中网布 折叠槽,保证该产品结构功能性(气囊爆破 时网布该折叠部分拉住气囊门总成),二是 应用了三个直径 10mm 的吸盘来真空吸附金 属螺钉,在此项目开发初期,最不稳定的就 是插片机构,由于插片机构是由齿牙排布而 成,开发初期经常性的出现部分齿牙未插入, 或者齿牙插入后又松开,或者齿牙偏移角度 过大将网布冲破等等异常情况,也是通过不 断的调整,优化设计构造,固化设计数据, 将所有齿牙的宽度,长度,间隔及偏移角度 等等要素都完全与网布折叠槽匹配好,最终 确定了最优方案,实现了稳定且精确的连续 抓取要求。
双色注塑技术在汽车零件制造中的应用

双色注塑技术在汽车零件制造中的应用摘要:国家经济的迅速发展促进了工业水平的不断提高,各类新型材料涌入工业生产当中,其中塑料制品作为优势较多的材料应用于工业和生产生活当中,大型塑料制品厂及相关企业蓬勃发展,越来越多技术人员投入到塑料制造和成型技术研究当中,随着技术研究的不断深入与成熟,双色注塑成型技术受到广大生产上的高度关注。
作为新兴的塑料制造成型技术具有传统技术无法比拟的高效便捷优势,目前双色注塑技术在各类生产中均有应用,文章注重双色注塑技术在汽车零件制造中的实际应用,结合实际进行了深入分析探讨,提出理论观点,以供后续汽车零件制造参考。
关键词:双色注塑成型技术;汽车零件制造;应用引言双色注塑技术是现阶段最为先进的一种塑料加工工艺,传统注塑工艺模型单一,加工过程复杂,而先进的双色注塑技术拥有两套注塑系统,两套模板作业,施工时间大大压缩,塑料成型技术显著提高。
除此之外,双色注塑技术形成的产品外观更加美观高档,结合了两种物料特性的材料结构更加牢固,客户体验感更好,因此在汽车零件制造中广受欢迎。
1双色注塑成型技术工艺和技术类型双色注塑加工过程中能够分别将两种高分子材料塑化,具体工作流程如下:首先,将第一材料注射到单色模具中以创建主注射产品,然后通过移动模具将主注射产品转换为双色模具,然后将第二材料转换为双色模具,轻按盖子或先折叠以创建辅助注射产品。
注塑产品是由两种材料的组合形成的,从而产生具有两种材料特性的双色最终产品。
1.1型芯旋转式双色注塑技术型芯旋转术双色注塑技术也可称为转模芯双色注塑技术,在汽车零件制造中应用广泛,具体工作流程和原理如下:首先,使用注射装置将第一种原材料塑料注入模具中的小孔中,成型后成为第一种塑料,然后将模具旋转180度,使用相同的注射装置注射第二原料塑料。
在第二种塑料成型后,制成最终的封套,并完成最基本的双色注塑成型。
整体来讲,技术流程并不复杂,操作简单易上手,经过培训的技术人员都可以进行自由操作,遇到设计感较强的住宿产品也能通过简便工具进行加工。
铝合金注塑在汽车零部件中的应用

铝合金注塑在汽车零部件中的应用随着汽车工业的迅猛发展和环保意识的逐渐提高,铝合金注塑在汽车工业中的应用越来越广泛。
铝合金注塑是一种将熔化的铝合金注入模具中,通过模具的冷却和硬化,最终得到所需的汽车零部件的制造工艺。
铝合金注塑具有成本低、强度高、重量轻、耐磨性好等优点,因此在汽车制造领域有着广泛的应用。
首先,铝合金注塑在汽车发动机零部件中的应用非常广泛。
发动机是汽车的重要组成部分,而铝合金注塑可以生产出高强度、轻质、耐磨损和高温耐受性的零部件,比如缸盖、曲轴箱、活塞等。
铝合金注塑发动机零部件相比于传统的铸铁零部件,具有更好的散热性能和更低的噪音水平,提高了发动机的工作效率和可靠性。
其次,铝合金注塑在汽车底盘零部件中也有重要应用。
底盘是汽车的骨架,承受着车身的重量和动力传递的力量。
铝合金注塑可以制造出高强度、轻质、耐腐蚀和抗疲劳的底盘零部件,比如悬挂臂、横梁和稳定杆等。
与传统的钢制零部件相比,铝合金注塑底盘零部件具有更好的刚性和吸能性能,提高了驾驶的稳定性和安全性。
另外,铝合金注塑在汽车车身零部件中也有广泛的应用。
车身是汽车的外部保护罩,直接关系到汽车的外观和安全性。
铝合金注塑可以生产出高强度、轻质、耐腐蚀和耐撞击的车身零部件,比如车门、车顶和车厢等。
与传统的钢制零部件相比,铝合金注塑车身零部件具有更好的抗腐蚀性和减震性能,提高了汽车的耐用性和驾乘舒适性。
此外,铝合金注塑还可以应用在汽车电子零部件中。
随着汽车电子化水平的提高,电子零部件在汽车中的重要性越来越突出。
铝合金注塑可以制造出轻质、高强度、导电性良好的电子零部件,比如控制面板、仪表盘和电池盒等。
铝合金注塑电子零部件相比于传统的塑料零部件,具有更好的机械性能和导热性能,提高了电子设备的稳定性和可靠性。
总的来说,铝合金注塑在汽车零部件中的应用具有明显的优势和潜力。
铝合金注塑制造的零部件具有高强度、轻质、耐磨损、耐腐蚀等特点,可以提高汽车的性能、安全性和可靠性。
注塑成型应用

注塑成型应用注塑成型是一种常见的塑料加工方法,广泛应用于各个领域。
它通过将熔化的塑料注入到模具中,然后冷却硬化成为所需的形状,从而实现塑料制品的生产。
注塑成型具有成型速度快、生产效率高、产品精度高等优点,因此被广泛应用于汽车、电子、家电、医疗器械等领域。
注塑成型在汽车行业中扮演着重要的角色。
汽车零部件的注塑成型可以将塑料制品制造成具有复杂结构的零部件,如仪表板、车门饰板、中控台等。
注塑成型可以满足汽车行业对于零部件质量、外观和性能的要求,同时具有较低的生产成本,因此受到了汽车制造商的青睐。
注塑成型在电子行业中也有广泛的应用。
随着电子产品的不断更新换代,对于电子产品外壳的要求也越来越高。
注塑成型可以生产出精细、高精度的电子产品外壳,如手机壳、电脑键盘等。
注塑成型可以满足电子行业对于外观质量、产品精度和生产效率的要求,推动了电子产品的不断发展。
注塑成型在家电行业中也占据重要地位。
家电产品通常需要具备良好的耐用性和外观效果,而注塑成型技术可以满足这些要求。
通过注塑成型,可以生产出具有复杂形状和结构的家电产品,如洗衣机外壳、冰箱把手等。
注塑成型可以保证家电产品的质量和性能,提高了产品竞争力。
注塑成型在医疗器械行业中也得到了广泛应用。
医疗器械对于安全性和卫生要求非常高,注塑成型技术可以满足这些要求。
通过注塑成型,可以生产出符合医疗器械标准的产品,如注射器、输液器等。
注塑成型可以确保医疗器械的质量和可靠性,保障了患者的健康。
注塑成型应用广泛且多样化,涵盖了汽车、电子、家电、医疗器械等多个行业。
注塑成型技术以其成型速度快、生产效率高、产品精度高等优点,为各个行业的产品制造提供了重要的支持。
随着科技的不断进步和创新,相信注塑成型技术将会在更多领域得到应用,并为各行各业的发展带来新的机遇和挑战。
汽车注塑工艺(3篇)

第1篇随着汽车工业的飞速发展,汽车零部件的需求量越来越大,注塑工艺作为汽车零部件制造的重要工艺之一,其在汽车制造中的应用越来越广泛。
注塑工艺是一种将塑料原料通过加热、熔化、注射成型等过程,使其成为具有一定形状和尺寸的塑料制品的工艺。
本文将详细介绍汽车注塑工艺的原理、流程、设备以及注意事项。
一、注塑工艺原理注塑工艺的基本原理是利用塑料的流动性和可塑性,将塑料原料在高温、高压下注入模具腔内,经过冷却、固化、脱模等过程,最终得到具有一定形状和尺寸的塑料制品。
注塑工艺主要包括以下步骤:1. 塑料原料的预热:将塑料原料在注塑机料筒内加热至熔融状态。
2. 注射:将熔融塑料通过注射筒注入模具腔内。
3. 冷却、固化:模具腔内的熔融塑料在冷却水或冷却空气的作用下逐渐固化。
4. 脱模:将固化后的塑料制品从模具中取出。
5. 后处理:对塑料制品进行表面处理、尺寸检验等。
二、注塑工艺流程1. 塑料原料的准备:根据塑料制品的性能要求,选择合适的塑料原料。
2. 模具设计:根据塑料制品的形状、尺寸、结构等因素,设计模具结构。
3. 模具制造:根据模具设计图纸,制造模具。
4. 注塑机调试:对注塑机进行调试,确保其正常运行。
5. 注塑成型:将塑料原料预热、注射、冷却、固化、脱模等。
6. 后处理:对塑料制品进行表面处理、尺寸检验等。
7. 产品检验:对塑料制品进行性能、尺寸等方面的检验。
三、注塑设备1. 注塑机:注塑机是注塑工艺的核心设备,其主要功能是将塑料原料加热、熔化、注射成型。
注塑机的主要参数包括注射量、锁模力、注射速度等。
2. 模具:模具是注塑工艺的关键设备,其质量直接影响到塑料制品的形状、尺寸和性能。
模具主要由动模、定模、导向柱、冷却水道等组成。
3. 辅助设备:辅助设备包括预热装置、冷却装置、脱模装置、检验设备等。
四、注意事项1. 塑料原料的选择:根据塑料制品的性能要求,选择合适的塑料原料。
2. 模具设计:合理设计模具结构,确保塑料制品的形状、尺寸和性能。
2024年汽车注塑模具市场发展现状

2024年汽车注塑模具市场发展现状简介汽车注塑模具是指用于汽车制造及相关行业中的模具,用于注塑成型汽车零部件的生产工艺。
随着汽车产业的快速发展,汽车注塑模具市场也呈现出良好的发展势头。
本文将探讨汽车注塑模具市场的发展现状,并分析相关问题。
市场规模汽车注塑模具市场的规模逐年增长。
据统计,全球汽车注塑模具市场规模在过去十年中持续增长,预计到2025年将达到X亿美元。
不仅如此,中国市场也是全球汽车注塑模具市场的重要组成部分,中国汽车注塑模具市场规模不断扩大。
发展趋势1.技术创新:随着汽车制造技术的不断革新,汽车注塑模具的技术水平也在不断提高。
新材料的应用以及模具制造技术的进步,使得汽车注塑模具能够更好地满足汽车制造工艺的需求。
2.自动化生产:自动化生产技术的应用使得汽车注塑模具的生产效率大幅提升。
自动化生产线的使用不仅可以降低劳动力成本,还能提高产品质量和制造效率,进一步促进汽车注塑模具市场的发展。
3.环保意识:环保意识的提高使得汽车制造行业对注塑模具的要求更高。
在选择模具供应商时,企业更倾向于选择环保型材料和制造工艺,以降低对环境的影响。
4.智能制造:随着人工智能和大数据技术的不断发展,智能制造逐渐在汽车注塑模具领域应用。
智能化的注塑模具制造可以实现生产数据实时监控、故障预警和远程控制,提高模具生产的智能化水平。
市场竞争汽车注塑模具市场竞争激烈,主要由几家大型企业垄断。
这些企业具有强大的研发实力和生产能力,可以为汽车制造商提供高质量的注塑模具产品。
此外,进口模具的竞争也对国内厂商造成了一定压力。
为了在市场中保持竞争力,企业应注重产品质量、技术创新和服务质量。
此外,与汽车制造商建立长期合作关系、拓展海外市场等策略也有助于企业在竞争中获得更多机会。
挑战与机遇汽车注塑模具市场面临的挑战与机遇并存。
挑战主要来自于金融风险、技术壁垒、市场需求波动等方面。
然而,随着全球汽车产业链的调整和升级,市场机遇也在增加。
注塑成型工艺论文汽车座椅塑料件力学性能论文
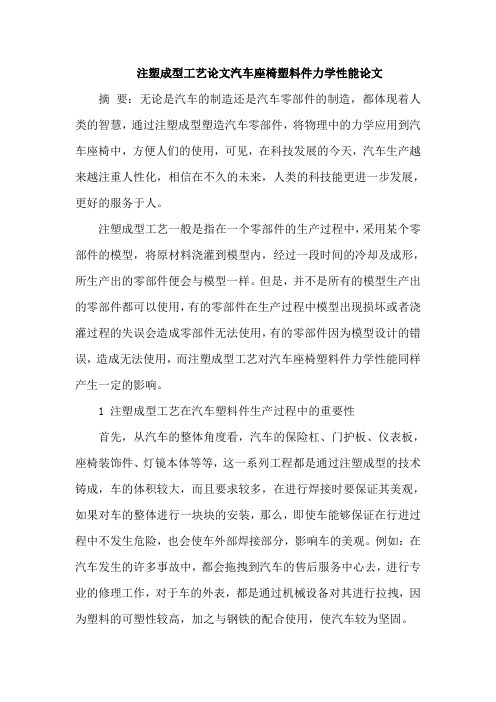
注塑成型工艺论文汽车座椅塑料件力学性能论文摘要:无论是汽车的制造还是汽车零部件的制造,都体现着人类的智慧,通过注塑成型塑造汽车零部件,将物理中的力学应用到汽车座椅中,方便人们的使用,可见,在科技发展的今天,汽车生产越来越注重人性化,相信在不久的未来,人类的科技能更进一步发展,更好的服务于人。
注塑成型工艺一般是指在一个零部件的生产过程中,采用某个零部件的模型,将原材料浇灌到模型内,经过一段时间的冷却及成形,所生产出的零部件便会与模型一样。
但是,并不是所有的模型生产出的零部件都可以使用,有的零部件在生产过程中模型出现损坏或者浇灌过程的失误会造成零部件无法使用,有的零部件因为模型设计的错误,造成无法使用,而注塑成型工艺对汽车座椅塑料件力学性能同样产生一定的影响。
1 注塑成型工艺在汽车塑料件生产过程中的重要性首先,从汽车的整体角度看,汽车的保险杠、门护板、仪表板,座椅装饰件、灯镜本体等等,这一系列工程都是通过注塑成型的技术铸成,车的体积较大,而且要求较多,在进行焊接时要保证其美观,如果对车的整体进行一块块的安装,那么,即使车能够保证在行进过程中不发生危险,也会使车外部焊接部分,影响车的美观。
例如:在汽车发生的许多事故中,都会拖拽到汽车的售后服务中心去,进行专业的修理工作,对于车的外表,都是通过机械设备对其进行拉拽,因为塑料的可塑性较高,加之与钢铁的配合使用,使汽车较为坚固。
其次,从汽车的载体来看,汽车注塑成型的工艺可以说是汽车零部件的载体工艺。
因为汽车零部件无法组装且成型,仅靠塑料材料本身无法成为汽车零部件的一部分,利用注塑成型的方式制造汽车的零部件,美观且实用。
例如:汽车的照明灯罩,汽车因为其自身的重量较重,所以要减轻其零部件的重量,采用塑料生产,汽车的前照灯会影响人的视野也会影响行车安全,在汽车的修理部门,我们经常看到,当汽车灯罩坏掉后,不是进行专业的焊接,而是直接更换,许多爱车人士可以根据车的灯罩形状判断车的品牌,所以,车的每一个部分都会影响汽车的美观,注塑成型工艺使车的灯罩在制造过程中美观、独一无二。
双色注塑技术在汽车零件制造中的应用朱秀锋

双色注塑技术在汽车零件制造中的应用朱秀锋发布时间:2021-09-08T06:21:36.213Z 来源:《中国科技人才》2021年第17期作者:朱秀锋[导读] 目前在汽车零件制造中,双色注塑技术已逐渐成为主流技术,对其应用进行分析探讨无疑有着重要的现实意义。
为此,本文对双色注塑技术在汽车零件制造中的应用进行了探讨,并结合实际案例,对双色注塑技术的应用要点进行了详细分析和总结,以期为今后的相关工作提供参考。
昌辉汽车电器(黄山)股份公司 245436摘要:目前在汽车零件制造中,双色注塑技术已逐渐成为主流技术,对其应用进行分析探讨无疑有着重要的现实意义。
为此,本文对双色注塑技术在汽车零件制造中的应用进行了探讨,并结合实际案例,对双色注塑技术的应用要点进行了详细分析和总结,以期为今后的相关工作提供参考。
关键词:双色注塑技术;汽车零件;零件制造前言:目前,双色注塑技术已经在汽车零件制造中得到了较为广泛的应用,其通过两套注塑系统的同时运作,能够得到由两种材料组合而成且兼具两种材料的优点的汽车零件成品。
采用这种技术制备的汽车零件成品具有外形高档美观、结构牢固合理、使用感受良好和附加值高等诸多优点,因此这种技术的应用范围仍在进一步扩展。
1汽车零件制造中双色注塑技术的发展现状目前,在部分汽车零件中,其采用的双色(多组分)注塑技术主要通过以下两种方法加以表现:一是“包胶法”,这种方法使用两副模具,分别在两台普通注塑机上分别进行注塑成型,第一次主要针对成型嵌件进行注塑,第二次则对另一种颜色或材料的塑料进行注塑,第二次注塑的材料将包裹在注塑后的成型嵌件上,以完成最终的双色注塑。
这种方法对于生产设备的要求较低,目前很多企业的双色注塑技术都采用此种方法进行应用,但这种方式较为繁琐,且效率和成型质量相对较低[1]。
二是“一次注塑成型”法,这种方法直接采用专用的双色注塑机,将两个或更多种颜色的塑料同时或按顺序注入到模具当中,其又可细分为双色单模注塑成型或是双色多模注塑成型两种方法。
汽车塑料部件低成本解决方案与实例

汽车塑料部件低成本解决方案与实例摘要:本文主要介绍汽车塑料部件的低成本解决方案以及实例。
首先,我们将讨论低成本解决方案的重要性和应用场景。
然后,我们将详细介绍几种常见的汽车塑料部件低成本解决方案,并提供实际案例作为说明。
最后,我们将总结本文的主要观点和结论。
1.引言在汽车制造业中,降低成本是一项重要的任务。
汽车塑料部件作为汽车生产过程中不可或缺的组成部分,对于降低整车成本起着关键作用。
因此,寻找汽车塑料部件的低成本解决方案是汽车制造商和供应商的一项重要任务。
2.汽车塑料部件低成本解决方案的重要性和应用场景降低汽车塑料部件的成本对于提高汽车制造商的竞争力至关重要。
低成本解决方案可以帮助汽车制造商降低生产成本,提高利润率,并在市场上获得价格竞争优势。
此外,低成本解决方案还可以促进创新和技术发展,在设计和生产过程中寻找更有效和经济的方法。
3.1材料选择选择合适的塑料材料可以降低成本。
例如,汽车塑料部件可以采用更便宜的塑料材料,如聚丙烯或聚乙烯,而不是更昂贵的塑料材料,如聚酰胺。
此外,可以使用回收塑料材料,以降低原材料成本。
案例:一汽丰田在其车身部件中使用聚碳酸酯(PC)材料,代替传统的聚酰胺材料,降低了材料成本,并在汽车质量和性能方面没有降低。
3.2设计优化通过优化设计,可以降低汽车塑料部件的生产成本。
例如,可以减少零部件数量,简化生产工艺。
此外,可以通过优化零部件结构和形状,减少材料损耗。
案例:大众汽车将其汽车内饰件的设计进行优化,通过减少零部件数量和材料使用量,降低了生产成本。
3.3自动化生产采用自动化生产技术可以降低人工成本,提高生产效率。
例如,使用自动化机器人进行注塑成型过程,可以提高生产效率,并降低零部件的生产成本。
案例:特斯拉公司使用自动化生产技术生产其塑料零件,包括注塑成型和装配过程,从而实现了低成本生产。
4.结论汽车塑料部件的低成本解决方案对于降低汽车制造商的生产成本,提高市场竞争力至关重要。
注塑成型实习报告

注塑成型实习报告注塑成型实习报告注塑成型实习报告前言近年来,随着科学技术的不断进步和工业生产的迅速发展,中国塑料模具发展速度相当快。
汽车、家电、办公用品、工业电器、建筑材料、电子通信等塑料制品需求旺盛,带动了塑料模具的快速发展。
模具作为重要的工艺装备,在消费品、电器电子、汽车、飞机制造等工业,占有举足轻重的地位。
工业产品零件粗加工的75%,精加工50%及塑料零的90%将由模具完成。
中国模具工业发展迅速,模具制造业产值年平均增长14%,201*年增长25%。
201*年我国模具产值为450亿人民币。
总产量位居世界第三,出口模具3.368亿美元,比上年增长33.5%。
但是,我国技术含量低的模具已供过于求,精密、复杂的高档模具很大部分依靠的是进口。
每年进口模具超过10亿美元,出口超过1亿美元。
面对市场的变化,有着高技术含量的模具正在市场上崭露头角。
随着工业发展,工业产品的品种、数量越来越多;对产品质量和外观的要求,更是日趋精美,华气。
因此,结合中国具体情况,学习国外模具工业建设和模具生产的经验,宣传、推行科学合理化的模具生产,才能推进模具技术的进步。
摘要本文叙述了本人在厂实习的经历及体会,学习理解产品的实际生产流程,分析和掌握产品在设计和生产过程中存在的问题以及如何改善和优化产品的性能,同时了解工厂的管理体制及其经营的基本规律,并通过撰写实习报告,学会综合应用所学知识,提高应用专业知识的能力。
为了更多地了解社会,在实践中接收教育,锻炼解决生产等实际问题的能力,通过在相关模具部门的实习,进一步理解了注射模的结构、设计以及生产,这对我的人生有很大的帮助。
关键词:生产流程注射模注塑成型实习报告时间过得真快,为期四周的实习转眼就过去了,在这次生产实习中,我很认真的去接触每一件事情,抱着满腔的热情和好奇,认真的去对待。
对于一些平常理论的东西,或遇到不懂的方面,我都认真去了解和充实接触,然而使我的知识有了质的飞越,感觉到受益匪浅。
- 1、下载文档前请自行甄别文档内容的完整性,平台不提供额外的编辑、内容补充、找答案等附加服务。
- 2、"仅部分预览"的文档,不可在线预览部分如存在完整性等问题,可反馈申请退款(可完整预览的文档不适用该条件!)。
- 3、如文档侵犯您的权益,请联系客服反馈,我们会尽快为您处理(人工客服工作时间:9:00-18:30)。
汽车零件注塑生产的应用与实践
1 前言
汽车用塑料量的多少已成为衡量汽车设计和制造水平高低的重要标志,目前国内汽车的材料约10%以上由塑料构成,塑料在汽车中的应用范围正在由汽车内部装饰扩展到汽车外部结构,除聚烯烃材料近来在汽车领域的应用量大增外,聚氨酯、增强复合材料等在汽车的运用也日益增加。
注塑件在汽车零部件所占的比例越来越高,注塑产业也成为汽车产业供应链上最为关键的环节。
2 车用塑件成型重点要素
由于汽车复杂零件的塑料件有与众不同的特殊性,所以其注塑成型在设计上需要充分考虑到如下因素,材料的干燥处理、玻纤增强材料对螺杆的新要求、驱动形式及合模结构等。
首当汽车保险杠、仪表板等常用的树脂材料为改性PP和改性ABS等改性树脂时,树脂材料有不同的吸湿性,为满足成型时的水份含量要求(一般要求0.2%),树脂原料在进入注塑机螺杆预塑计量之前,都要经过热风干燥或除湿干燥处理。
改性PP(PPEPDM)树脂的吸湿性较小,一般采用热风干燥机在80100℃的条件下23h即可。
改性ABS(PC/ABS)的吸湿性较强,在成型干燥前,应用除湿干燥机进行除湿干燥处理。
我们在设计汽车复杂塑料零件成型系统上充分考虑了除湿干燥系统功能运用。
目前国内汽车用塑料件基本上为无玻璃纤维增强的塑料制品,与使用含有短切玻璃纤维增强的树脂相比,成型无玻璃纤维增强塑料件所用注塑机的螺杆的材质和结构有较大的不同。
注塑机在设计时,要注意螺杆料筒的合金材质和特殊的热处理加工工艺,保证它的耐腐性和强度。
由于汽车零部件与常规产品不同,它的型腔面十分复杂,受力不等、应力分布不均,在设计中重点考虑它所需的加工能力。
注塑机的加工能力体现在合模力和注塑能力(以最大理论注射容积来表示)两方面。
注塑机在成型制品时,合模力必须大于模具型腔压力产生的开模力,否则模具分型面将会分开而成产生溢料。
确定注塑机合模力的公式如下:P合模P型腔F/100。
式中:P合模为注塑机的合模力(或称锁模力)KN;P型腔为模腔平均压力,MPa,与制品结构形状、精度要求和每模型腔数等有关,取值范围一般在25-40MPa之间;F为模具型腔,浇道和进料口的水平重叠投影面积CM3。
为保证可靠的锁模、注塑成型时的工艺锁模力必须小于注塑机的额定锁模力。
注塑机的最大理论注射容积与注塑机合模力吨位相匹配,是注塑机在出厂前以聚苯乙烯(PS)为基准树脂标称出来的注射容量。
3 车用塑料零部件优势
3.1 汽车复杂塑料零部件的优势
塑料可以一次加工成型,加工时间短,精度有保证。
塑料制品的弹性变形特性能吸收大量的碰撞能量,对强烈撞击有较大的缓冲作用,对车辆和乘员起到保护作用。
现代汽车上都采用塑化仪表板和方向盘,以增强缓冲作用。
前后保险杠、车身装饰条都采用塑料材料,以减轻车外物体对车身的冲击力。
塑料还具有吸收和衰减振动和噪声的作用,可以提高乘坐的舒适性。
塑料耐腐蚀性强,局部受损不会腐蚀。
通过添加不同的填料、增塑剂和硬化剂来制出所需性能的塑料,以适应车上不同部件的用途要求。
更方便的是塑料颜色可以通过添加剂调出不同颜色,省去喷漆的麻烦。
有些塑料件还可以电镀。
另一方面,汽车复杂零部件的注塑件特殊的外观和尺寸要求提高了汽车注塑件的开发门槛和风险。
Moldflow三维软件帮助企业在产品设计阶段分析塑件的成型可行性,通过对部品的变形及成型工艺的分析,评估并优化产品设计,同时指导了下游厂商的模具及注塑优化。
4 专用注塑机潜力大
泰瑞已推出新一代D系列汽车复杂塑料零部件专用注塑生产线。
早在2013广州CHINAPLAS国际橡塑展上已展示部份产品和技术。
现在,泰瑞提供的汽车复杂塑料零部件专用注塑生产线注重能耗及速度,不仅能缩短循环周期,相应提高产能;还能降低能耗,直接减低成本,实现节能环保、高响应速度、高重复精度等。
该生产线可生产的外装饰件主要部件有保险杠、挡泥板、车轮罩、导流板等,内装饰件的主要部件有仪表板、车门内板、副仪表板、杂物箱盖、座椅、后护板等。
锁模力从600至3000吨,射胶量从1848克至47601克,直正二板设计,比一般大型注塑机约少于30%以上长度,快速15秒调模、节省换模时间,多项专利授权技术,特快开模行程,达700mm/s,以8秒完成开锁模,自主研发计算器控制器。
一般注塑成型汽车前后保险杠、仪表板等大型汽车塑料件的成型周期为60100秒不等。
采用制作精良、冷却系统好的注塑模具以及配合取件机械手会缩短成型周期。
5 结论
全球车用塑料消耗量正逐年增加,车用塑料部件已从内饰件到外饰件、结构件到功能件、动力系统到转向制动系统等方向发展,特别是模块化制件,因此开发汽车复杂零部件塑料件专用注塑成型系统仍将具有很大的发展空间。