齿轮摩擦磨损试验机工作原理
摩擦磨损试验机简单介绍

摩擦磨损试验机简介中文名称:摩擦磨损试验机英文名称:friction-abrasion testing machine定义:对材料及润滑剂进行摩擦与磨损性能试验的试验机。
应用学科:机械工程(一级学科);试验机(二级学科);材料试验机-材料试验机名称(三级学科)一、分类根据载荷范围可分为:超纳米摩擦磨损试验机,纳米摩擦磨损试验机,微米摩擦磨损试验机(10N),大载荷摩擦磨损试验机(1000KN)。
根据摩擦运动方式可分为:线性往复摩擦磨损试验机,高速线性往复摩擦磨损试验机(振动摩擦磨损试验机),旋转摩擦磨损试验机,高速旋转摩擦磨损试验机,线性旋转组合摩擦磨损试验机。
根据摩擦副可分为球盘摩擦磨损试验机,销盘摩擦磨损试验机,盘盘摩擦磨损试验机,环块摩擦磨损试验机,四球摩擦磨损试验机,缸套活塞环摩擦磨损试验机,高频摩擦磨损试验机,高温摩擦磨损试验机,真空摩擦磨损试验机。
二、产生的背景摩擦学主要是研究发生在作相对运动的物体表面上的摩擦、磨损与润滑现象及其控制与应用的一门科学与技术。
凡有运动的地方就有摩擦产生,所以摩擦是普遍存在于人类的生产和生活中(包括人体内),具有重大影响和作用的一种自然现象。
世界上如果没有摩擦,人们将寸步难行,车辆行驶失控,房屋无法建造,人类的衣、食、住、行都成问题,显然,人类不能生存在一个没有摩擦的世界,正如无法生存在一个没有万有引力的世界一样。
19世纪以后,随着各种工业,特别是机械制造业的发展,摩擦、磨损与润滑的研究成为众多领域技术进步绕不开的课题。
许多科学家和工程技术人员作了一系列的有关摩擦、磨损与润滑的研究工作,然而这些工作一直是由不同学科领域的学者“各自为战”,有关知识也分散在大学的物理、力学、流体力学、机械设计等不同的课程进行讲授,没有形成一门统一的学科和课程,所以这些知识和技术普及不够,应用不力。
于是在上个世纪60年代中期,英国政府组织了对润滑教育和研究现状的详细调查,发现英国的企业由于对摩擦、磨损和润滑科技知识的了解和应用不够而损失重大。
摩擦磨损试验机的组成及工作原理介绍
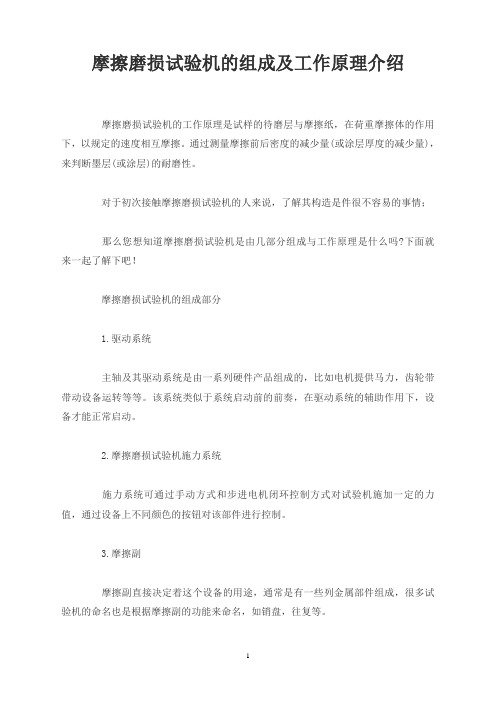
摩擦磨损试验机的组成及工作原理介绍摩擦磨损试验机的工作原理是试样的待磨层与摩擦纸,在荷重摩擦体的作用下,以规定的速度相互摩擦。
通过测量摩擦前后密度的减少量(或涂层厚度的减少量),来判断墨层(或涂层)的耐磨性。
对于初次接触摩擦磨损试验机的人来说,了解其构造是件很不容易的事情;那么您想知道摩擦磨损试验机是由几部分组成与工作原理是什么吗?下面就来一起了解下吧!摩擦磨损试验机的组成部分1.驱动系统主轴及其驱动系统是由一系列硬件产品组成的,比如电机提供马力,齿轮带带动设备运转等等。
该系统类似于系统启动前的前奏,在驱动系统的辅助作用下,设备才能正常启动。
2.摩擦磨损试验机施力系统施力系统可通过手动方式和步进电机闭环控制方式对试验机施加一定的力值,通过设备上不同颜色的按钮对该部件进行控制。
3.摩擦副摩擦副直接决定着这个设备的用途,通常是有一些列金属部件组成,很多试验机的命名也是根据摩擦副的功能来命名,如销盘,往复等。
4.摩擦磨损试验机数据采集系统(1)光电编码器将测得的转速信号分别传至主轴转速测量控制系统和主轴转速测量显示系统;(2)压力传感器转换为电信号传至试验力测量系统,进行试验力数字显示;(3)摩擦力测量传感器将测得的信号传递到摩擦磨损试验机的摩擦力测量显示系统进行数字显示和自动记录。
(4)摩擦磨损试验机微机控制系统摩擦磨损试验机的工作原理1.环盘摩擦:用于研究表面纳米化中碳钢在润滑条件下的磨合性能。
原理:环试样通过专用夹具安装与主轴的下端部,盘试样安装在托盘内并通过托盘下的施力系统对试样加载,主轴在直流电机的驱动下带动销试样做旋转运动。
2.销盘摩擦:用于在干摩擦条件下考察纳米粒子对符合材料摩擦磨损性能的影响。
3.四球摩擦:(1)用于采用硫化异丁烯作为添加剂的微量润滑油摩擦磨损试验。
(2)考察油及含添加剂的油的摩擦磨损性能(3)试验时上钢球旋转,下钢球固定,载荷通过传感器平均加载于3个固定钢球上。
用于超微细磷酸锰转化涂层摩擦磨损性能。
齿轮测量仪器基本工作原理及功能

• • • • • • • • • • •
平行轴齿轮检测软件 轴径参考软件 滚齿刀检测软件 剃刀测量软件 插齿刀测量软件 蜗轮测量软件 蜗杆测量软件 圆形几何元素测量软件 直边花键检测软件 结合齿顶部测量软件 正时关系测量软件
• • • • • • • • • •
未知参数齿轮测绘软件 直齿锥齿轮测量软件 齿面三维拓扑分析软件 螺旋伞齿轮测量软件 凸轮测量软件 扩展齿轮分析软件包 统计分析软件 热处理扭曲变形分析软件 齿根扫描软件 摆线齿轮测量软件
迄今已有美国、德国、日本、瑞士、中国、意大利 等几个国家生产CNC齿轮测量中心,国外的典型产品是 M&M公司的3000系列、Klingelberg的P系列;国产 的典型产品是成都工具研究所的CGW300卧式测量中心 和哈尔滨量具刃具厂的3903型齿轮测量中心。各国的齿 轮测量中心虽然原理上大同小异,但实现方式却存在一定
Hale Waihona Puke (2)在实现测量原理的技术手段上,历经了“以机械为主” 到“机电结合”,直至当今的“光—机—电”与信息技术 综合集成的演变;
(3)在测量结果的表述与利用方面,历经了“指示 表加目视读取”到“记录仪器记录加人工研判”, 直至“计算机自动分析并将测量结果反馈到制造 系统”的飞跃。与此同时,齿轮量仪经历了从单 品种单参数的仪器、单品种多参数的仪器到多品 种 多 参数仪器的演变。 70年代以前的近 50年内,世界上已开发出测 量齿廓、螺旋线、齿距等基本参数的各种类型、 各种规格的机械展成式仪器。这些仪器借助一些 精密机构形成指定标准运动,然后与被测量进行 比较,从而获得被测误差的大小。 1970年是齿
下图是德国克林贝格公司的齿轮测量中心
下图是美国M&M的齿轮测量中心
下图为国内哈量和精达开发的齿轮测量中心
摩擦机工作原理

摩擦机工作原理
摩擦机是一种利用摩擦力来进行工作的设备。
其工作原理可以简单描述为在接触面上施加力,使物体间发生相对运动,并通过摩擦力产生机械能来实现特定的功能。
一般来说,摩擦机由驱动装置、摩擦件和工作部件组成。
驱动装置通过传动装置将动力传递给摩擦件,使其产生相对运动。
摩擦件通常由摩擦盘、摩擦片等组成,可以根据需要选择合适的材料和结构。
工作部件是摩擦机的最终工作目标,可以是任何需要进行摩擦加工、磨削、研磨、切割或压制等操作的物体。
摩擦机的工作过程中,驱动装置提供动力,驱动摩擦件开始运动。
摩擦盘上的摩擦片与工作部件接触,并施加一定的力。
摩擦力的作用下,摩擦盘和工作部件之间产生相对运动。
这种相对运动会导致两个物体间的摩擦发热,一部分机械能将转化为热能而散失。
同时,摩擦力还会进一步产生一系列的摩擦效应,如磨削、研磨、切割等。
工作部件在摩擦力的作用下,根据摩擦机的不同结构和功能,可能会发生形变、磨耗、切削等变化,从而实现特定的工作目标。
最后,通过控制驱动装置的运动和摩擦力的大小,可以调整摩擦机的工作状态和工作效果。
总的来说,摩擦机通过摩擦力产生机械能,将输入的动力转化为实现特定工作目标所需的能量。
其工作原理基于摩擦产生的相对运动和摩擦力所引发的一系列效应,在工程和制造领域中有着广泛的应用。
销盘式摩擦磨损试验机概述 摩擦磨损试验机如何操作

销盘式摩擦磨损试验机概述摩擦磨损试验机如何操作微机掌控的销盘式摩擦磨损试验机可用于球盘或销盘试验,试样间有多种接触类型。
该试验机的紧要特色是销和盘的夹具的刚性很大,适用于盘盘接触测试。
另外,与其他接受固定载荷和负载横梁的球盘试验机相比,该机型的气动加载系统大大削减了高负荷情况下的惯性载荷。
需要指出的是,惯性载荷对测得的摩擦磨损数据有着较大的影响。
该试验机的掌控单元包括串行接口模块和数据采集软件,可自动掌控载荷、速度、温度和测试时间,可设置报警水平,并且数据记录方式快捷。
该试验机的最大优势为可在线测量试样的磨损深度,便于严格筛选材料。
依据所选附件,试验范围也可相应扩展,比如可进行空气加热或润滑剂密闭条件下的测试。
另外,也可选择往复盘配件、线接触配件以及活塞环/汽缸套或环面(止推环)试样配件等,进行相应的试验。
总之,该试验机可用于进行标准ASTM G 99、 DIN 50324 和ISO/DIS 7148—2所指出的销盘或球盘试验,也可用于其它在到导引中列出的试验以及用于ASTM F 732中的往复式试验。
盘和销的夹具组件同轴,均按确定方向固定在机器的框架上,从而保证销和盘试样同轴,便于进行盘盘摩擦磨损。
很多测试方法中都将球面销或者球来做其中一个试样。
盘试样固定在盘夹具内,然后由中心螺栓拧紧即可。
机器下面的矢量掌控交流电机经传动带驱动旋转轴,因带有编码掌控反馈,所以可保证运行速度平稳并且获得充分大的调整比。
若要更改磨痕半径,调整销夹具的位置即可,这样,就可使从多个试验在一个盘上进行了。
磨痕半径可通过一个累计标尺进行设置。
若要进行有润滑的试验,在盘夹具上加一个高沿的环即可。
TE67/LE为高速试验供应了一套全密封系统。
销夹具组件包括绕垂直轴旋转的厚重铝块,可互换的加载单元与铝块前部可相互搭配。
试验时,先将销/球托塞进夹头内,而后旋紧加载单元的一个精密活塞内,这样就可直接给接触点施加载荷了。
在工作压力位7.5 bar时,气动组件的加载范围为25—1,000 N。
精密型din磨耗试验机原理
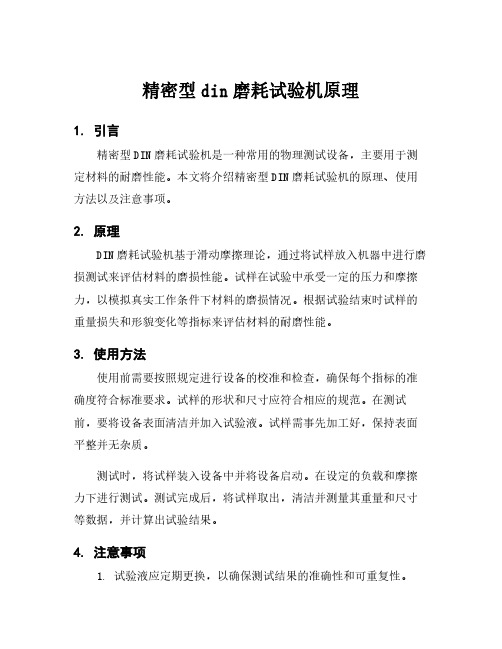
精密型din磨耗试验机原理
1.引言
精密型DIN磨耗试验机是一种常用的物理测试设备,主要用于测定材料的耐磨性能。
本文将介绍精密型DIN磨耗试验机的原理、使用方法以及注意事项。
2.原理
DIN磨耗试验机基于滑动摩擦理论,通过将试样放入机器中进行磨损测试来评估材料的磨损性能。
试样在试验中承受一定的压力和摩擦力,以模拟真实工作条件下材料的磨损情况。
根据试验结束时试样的重量损失和形貌变化等指标来评估材料的耐磨性能。
3.使用方法
使用前需要按照规定进行设备的校准和检查,确保每个指标的准确度符合标准要求。
试样的形状和尺寸应符合相应的规范。
在测试前,要将设备表面清洁并加入试验液。
试样需事先加工好,保持表面平整并无杂质。
测试时,将试样装入设备中并将设备启动。
在设定的负载和摩擦力下进行测试。
测试完成后,将试样取出,清洁并测量其重量和尺寸等数据,并计算出试验结果。
4.注意事项
1.试验液应定期更换,以确保测试结果的准确性和可重复性。
2.试样必须保持干燥并避免受潮,以保证测试结果的准确性。
3.操作时要严格按照要求进行,避免操作失误导致试验失败。
4.长时间的使用可能导致设备的磨损和老化,应定期进行维护和保养。
5.结论
精密型DIN磨耗试验机是一种可靠、准确的物理测试设备,可用于评价材料的磨损性能。
正确的使用和维护可以确保设备的性能和测试结果的准确性。
【摩擦磨损试验机】摩擦磨损试验机三个常见问题

【摩擦磨损试验机】摩擦磨损试验机三个常见问题1.四球摩擦磨损试验机的使用方法四球摩擦试验机紧要用于滑动、转动工况下润滑油的润滑性能讨论,其摩擦副由3个固定球和1个与之压紧的旋转球构成。
除去了因操不同造成的测量误差和操作中的空回误差,同时也削减了对四球磨损试验机的反复调整,加快了测量速度。
使用方法:1.首先在确保接线正确的前提下,接通电源,打开设备左侧空气开关;2.按下四球摩擦试验机电源开关,接通系统电源,按下计算机开按钮,启动计算机掌控系统;3.进入系统后打开四球摩擦试验机专用掌控系统,检查各参数是否显示正常;4.检查试样装夹情况,保持空载状态,选择摩擦副,设置较低转速,启动设备,注意察看设备运转是否正常;5.用溶剂汽油清洗油盒、试验用钢球、夹具及其它试验过程中与试样接触的零部件,再用石油醚洗两次,清洗完成吹干,清洗后钢球应无残渣干净无锈斑。
依据现场情况及试验要求选择清洗方式及清洗次数,每次试验工况保持一致;6.四球摩擦试验机使用专用工具装夹试样,将钢球分别固定在四球机的上球座和油盒内,把试样倒入油盒中,让试样盖过钢球到达压环与螺帽结合处。
假如是试验润滑脂,则先在油盒中充分数量的润滑脂,把求嵌入润滑脂中,放上压环,拧紧螺帽固定油盒,抹平表面的润滑脂并调整到压环与螺帽的结合处,试样中不能有空穴存在;7.安装好上钢球,然后把装好试样和球的油盒正中地安置在力矩轮上面;8.四球摩擦试验机依据PB点注2的补偿表设定试验力值,设定时间为10s,转速为1450r/min,开始试验。
2.摩擦磨损试验机的原理介绍摩擦磨损试验机由主轴驱动系统、摩擦副承载系统、试验力传感器、摩擦力测量系统、全自动加载系统、计算机掌控系统(包括各个主参数的设定、掌控、报警等单元)等部分构成。
它们都安装在以焊接机座为主体的机架中。
主轴及其驱动系统主轴是由伺服电动机通过调速系统驱动,速度无级调速。
通过圆弧齿同步带调速系统把电机的功率传递到主轴上。
摩擦磨损试验

实验四 摩擦学基础实验(1学时)一.实验目的1.通过实验了解不同材料配副摩擦系数的变化及磨损量的不同。
2.掌握摩擦学实验的基本方法及有关仪器设备的使用方法。
二.实验原理 1.概述摩擦表面上的物质,由于表面相对运动而不断损失的现象称磨损。
在一般正常工作状态下,磨损可分三个阶段:(1).跑合(磨合)阶段:轻微的磨损,跑合是为正常运行创造条件。
(2).稳定磨损阶段:磨损更轻微,磨损率低而稳定。
(3).剧烈磨损阶段:磨损速度急剧增长,零件精度丧失,发生噪音和振动,摩擦温度迅速升高,说明零件即将失效。
(如图4.1)机件磨损是无法避免的。
但是如何缩短跑合期、延长稳定磨损阶段和推迟剧烈磨损的到来,是研究者致力的方向。
伯韦尔(Burwell)根据磨损机理的不同,把粘着磨损,磨粒磨损、腐蚀磨损和表面疲劳磨损列为磨损的主要类型,而把表面侵蚀,冲蚀等列为次要类型。
这些不同类型的磨损,可以单独发生,相继发生或同时发生(称为复合磨损形式)。
2磨损的检测与评定研究磨损要通过各种摩擦磨损试验设备,检测摩擦过程中的摩擦系数及磨损量(或磨损率)。
摩擦过程中从表面上脱落下来的材料(磨屑),记录了磨损的发展历程,反映了磨损机理,描述了表面磨损的程度。
发生磨损后的表面,同样有着磨损机理、磨损严重程度及其发展过程的记载。
因此研究磨屑和磨损后表面磨损量跑合稳定磨损阶段剧烈图4.1 磨损三个阶段的示意图摩擦行程(时间)上的信息是研究磨损的重要一环。
2.1摩擦磨损试验机磨损试验的目的在于研究各种因素对摩擦磨损的影响,从而合理地选择配对材料,采用有效措施降低摩擦、磨损,正确设计摩擦副的结构尺寸及冷却设施等等。
摩擦磨损试验大体上可分为实验室试验,模拟试验或台架试验,以及使用试验或全尺寸试验三个层次,各层次试验设备的要求各不相同。
(1)实验室评价设备实验室设备主要用于摩擦磨损的基础研究,研究工作参数(载荷、速度等)对摩擦磨损的影响。
可以得到单一参量变化与摩擦磨损过程之间的关系。
往复式摩擦磨损试验机的工作原理

往复式摩擦磨损试验机是一种用于模拟物体表面往复摩擦磨损情况的专用设备,广泛应用于材料磨损性能评价和材料磨损机理研究等领域。
本文将从工作原理、结构特点和应用领域等方面对往复式摩擦磨损试验机进行介绍。
一、工作原理往复式摩擦磨损试验机的工作原理主要基于摩擦和磨损的物理过程。
在试验中,样品与摩擦副之间采用往复摩擦方式,在一定载荷和速度的作用下,样品表面会产生不同程度的磨损,通过对磨损量、磨损形貌、摩擦系数等参数的监测和分析,可以评价材料的耐磨性能和磨损机理。
往复式摩擦磨损试验机采用电机驱动,通过控制电机的转速和载荷大小,实现样品之间的往复摩擦运动,同时利用多种传感器对摩擦副的运动状态和试验参数进行实时监测和记录,以获取精确的试验数据。
二、结构特点1. 样品夹持装置:通常采用气动或液压夹持方式,保证样品稳固牢固地固定在磨损试验机上,避免试验过程中的误差。
2.试验载荷装置:通过加载装置对样品施加一定大小的载荷,模拟实际工况下的磨损情况,使试验结果更具可靠性。
3. 高精度运动控制系统:试验机配备高精度的运动控制和数据采集系统,可实现多种摩擦运动方式的模拟和控制,如往复摩擦、旋转摩擦等。
4. 数据采集与分析系统:试验机配备强大的数据采集与分析系统,能够实时记录试验过程中的摩擦系数、磨损量、磨损形貌等参数,并对试验数据进行深入分析和处理,为后续的磨损机理研究提供可靠的数据支持。
三、应用领域1. 材料耐磨性能评价:往复式摩擦磨损试验机可对不同材料的耐磨性能进行定量分析和评价,为材料的选择和设计提供科学依据。
2. 磨损机理研究:通过对试验结果的分析和研究,可以深入了解材料磨损的机理和规律,为改进材料性能和延长材料使用寿命提供理论支持。
3. 润滑剂研究:通过模拟不同润滑条件下的摩擦磨损试验,评价不同润滑剂对材料表面磨损的影响,为润滑剂的优选和应用提供技术参考。
总结:往复式摩擦磨损试验机具有良好的稳定性和精确性,能够模拟多种实际工况下的摩擦磨损情况,广泛应用于材料磨损性能评价和磨损机理研究等领域,对于促进材料科学研究和工程实践具有重要意义。
多功能摩擦磨损试验机

多功能摩擦磨损试验机多功能摩擦磨损试验机是一种可以控制测试参数的设备,用于评估材料或涂层在摩擦或磨损过程中的性能。
它可以用于各种材料和涂层的磨损性能测试,如金属材料、陶瓷材料、聚合物材料等。
多功能摩擦磨损试验机是由电机、传动装置、试验夹具、控制系统等组成。
电机通过传动装置带动试件和对试件施加力,控制系统可以控制试验参数,如试验时间、载荷大小等。
试件被夹在试验夹具中,通过试夹具与试验机构进行摩擦,用于评估材料在实际使用中的磨损性能。
多功能摩擦磨损试验机的应用广泛,并可以根据不同的测试需求进行调整。
例如,在评估不同涂层材料的耐磨性时,可以使用不同形状、尺寸的磨损头和试样,以模拟不同使用条件下的磨损情况。
在评估金属材料的耐磨性时,可以根据不同的应用需求,调整试验参数,如载荷大小、滑动速度等,以模拟不同使用环境下的磨损情况。
多功能摩擦磨损试验机的优点是具有高度的自动化和精确控制的能力。
它可以通过控制系统精确地控制试验参数,从而准确评估材料的磨损性能。
此外,它还可以通过计算机系统进行数据采集和分析,以获得更详细的测试结果。
多功能摩擦磨损试验机在实际应用中有很大的价值。
例如,在汽车行业中,它可以用于评估汽车发动机零部件的耐磨性能,以提高发动机的使用寿命和可靠性。
在航空航天领域,它可以用于评估航空发动机涂层材料的耐磨性能,以提高飞机的安全性和性能。
在材料科学领域,它可以用于评估新材料的磨损性能,以指导新材料的研发和应用。
总之,多功能摩擦磨损试验机是一种重要的测试设备,用于评估材料的磨损性能。
它具有高度自动化和精确控制的能力,并可根据不同的测试需求进行调整。
它在实际应用中具有广泛的应用前景,对于提高材料和涂层的磨损性能,具有重要意义。
摩擦磨损试验机的工作原理和操作方法 摩擦磨损试验机常见问题解决方法
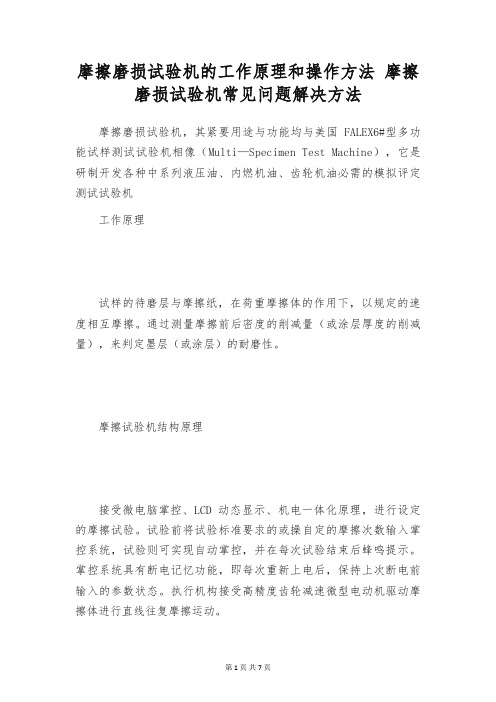
摩擦磨损试验机的工作原理和操作方法摩擦磨损试验机常见问题解决方法摩擦磨损试验机,其紧要用途与功能均与美国FALEX6#型多功能试样测试试验机相像(Multi—Specimen Test Machine),它是研制开发各种中系列液压油、内燃机油、齿轮机油必需的模拟评定测试试验机工作原理试样的待磨层与摩擦纸,在荷重摩擦体的作用下,以规定的速度相互摩擦。
通过测量摩擦前后密度的削减量(或涂层厚度的削减量),来判定墨层(或涂层)的耐磨性。
摩擦试验机结构原理接受微电脑掌控、LCD动态显示、机电一体化原理,进行设定的摩擦试验。
试验前将试验标准要求的或操自定的摩擦次数输入掌控系统,试验则可实现自动掌控,并在每次试验结束后蜂鸣提示。
掌控系统具有断电记忆功能,即每次重新上电后,保持上次断电前输入的参数状态。
执行机构接受高精度齿轮减速微型电动机驱动摩擦体进行直线往复摩擦运动。
操作方法立式摩擦磨损试验机是由主轴驱动系统,摩擦副专用夹具,油盒与加热器,试验力传感器,摩擦力矩测定系统,摩擦副下副盘升降系统,弹簧式微机施力系统,操纵面板系统等部分构成。
它们都安装在以焊接机座为主体的机架内。
机座的右上方是试验机操作显示系统,左上方是主轴驱动系统和油盒,摩擦副,各种传感仪器等,机座的左下部是试验机弹簧式施力系统和微机自动加荷系统,右下部是工具箱,机座的前后及左侧有门,打开时能清楚看到内部机构,以便进行调试检修。
1 主轴及其驱动系统主轴(1)是由松下交流电机(2)和PWMC 脉宽调速掌控系统构成,该系统电机的额定力矩为9.545Nm,脉宽调速范围为10—2000r/min,无级恒扭矩,高速精度为1%.该电机较大功率约 1.5Kw,在主轴(1)和电机(2)上部,分别装有从动和自动特制的圆弧齿形带轮(3)、(4),通过圆弧齿同步带(5)把电机的功率传递到主轴上。
由于应用了脉宽调速系统使其在低转速下具有高的传动力矩,它完全更改了可控硅无级变速系统在低转速下传动力成倍递减的特点。
摩擦磨损试验机
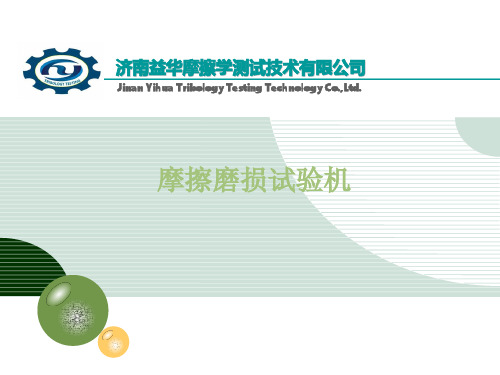
环块摩擦磨损试验机
MRH-3高速环块摩擦磨损试验机 一、主要用途 该机主要以滑动摩擦形式,在浸油润滑条件 下,评定各种润滑剂的润滑性能,尤其适用于 中高档汽车齿轮油的抗擦伤性能的模拟评定, 也可用于各种金属、非金属材料及涂层的磨损 性能研究。采用框架式结构,由直流电机控制 杠杆加载,各试验参数实现单元化设置,操作 方便,试验读数准确可靠,该机采用一体化结 构设计,将计算机、软件、工业控制模块、执行 器组合在一个框架中,完成对整个实验过程的 控制,可实时采集试验数据并可绘制相应的试 验曲线, 适用标准: GB/T 12444-2006 《金属材料磨 损试验方法:试环-试块滑动磨损试验》
往复摩擦磨损试验机
MGW-02 高速往复摩擦磨损试验机 一、主要用途与功能 主要用于往复运动的工况下实现材料或涂层 间的摩擦磨损性能检测。该机可动态检测各试 验参数,并实时绘制各参数曲线,设有主要参 数超预置停机或报警保护。还可做长时间疲劳 摩擦试验,可连续工作1000小时。 二、技术参数与指标 1)行程范围:1 ~ 12mm,精度±0.01mm; 2)摩擦力测量范围:0 ~ 100N,精度3% ; 3)试验力范围:1 ~ 200N,精度0.1N; 4)摩擦副形式:销-盘、球-盘、柱-瓦 5)最大行程:40mm,精度±0.01mm; 6)往复频率:1~ 60Hz(无级可调); 7)温度控制范围:室温~200℃;精度±2℃;
四球摩擦磨损试验机
MRS-10P 杠杆式四球摩擦磨损试验机(触摸屏式) 一、主要用途 该试验机采用滑动摩擦的形式,在极高的点接触压 力条件下,评定润滑剂的承载能力,包括最大无卡咬负 荷PB,烧结负荷PD,综合磨损值ZMZ等三项指标。该 机还可以做润滑剂的长时抗磨损试验,测定摩擦系数。 该机采用彩色触摸屏控制方式,可设置并实时显示主轴 的转速、转数、试验力、摩擦力矩、摩擦系数、试验时 间、温度等试验参数,可实时采集试验数据并可绘制相 应的试验曲线。 适用标准:GB 3142-82《润滑剂承载能力测定法》、 GB/T 12583-98 《润滑剂极压性能测定法》、SH/T 018992 《润滑油抗磨性能测定法》、SH/T 0202-92 《润滑 脂极压性能测定法》、SH/T 0204-92 《润滑脂抗磨性能 测定法》。
摩擦磨损实验机的原理及使用说明

1.1摩擦磨损实验机的原理及使用说明1.1.1实验机机械部分的原理图3-64为HIT-1型球盘式摩擦磨损实验机原理图。
电动机2经带传动1驱动托盘3回转,下试件4安装在托盘3上并随托盘3一起回转,上试件5装在夹头6中。
载荷P由砝码7的重量W产生,摆杆8在摩擦力F作用下摆动,摆杆的另一端压在压力传感器9上,压在压力传感器上的力Q可经数据采集测量系统获得。
工作时,托盘3中可加入润滑油或在下试件4表面上滴润滑油(边界润滑),也可不加润滑油(干摩擦)。
1带传动2电动机3托盘4下试件5上试件6夹头7砝码8摆杆9压力传感器图3-64 HIT-1型球盘式摩擦磨损实验机原理图试验机主要技术指标:转速:100~500r/m最大载荷:W=10N1.1.2摩擦系数测试原理如图3-64所示,本实验机作用在试件上的载荷P由砝码重量W产生,P与W的关系为:P=W(N)(3-4)图3-65 试件结构及尺寸作用在上试件5上的摩擦力F 与作用在压力传感器9上的力Q 的关系为:QL 1=FL 2 (3-5)本试验机 L 1=L 2=100mm 则:Q=F (3-6)摩擦系数:P W f F Q== (3-7) 所以,只要预先确定加载砝码W 的重量再测出传感器受力Q 的大小,即可计算出摩擦系数f 。
1.1.3 数据采集处理系统本试验机配有自动数据采集处理系统,图3-66为数据处理系统框图,系统的硬件有:传感器、数据采集卡、计算机等。
图3-66 数据处理系统框图数据的结果有两种形式:一是由计算机直接做出摩擦系数随时间的变化曲线。
在屏幕上显示,并在打印机上打印出曲线。
二是计算机只记录实验数据,并通过计算机打印出数据,由学生手工绘图。
1.1.4 本试验机的应用范围(1) 改变上下试件材料,研究不同材料配副的摩擦、磨损情况。
(2) 改变速度快慢,研究不同速度下的摩擦,磨损情况。
(3) 改变载荷大小,研究不同载荷下的摩擦、磨损情况。
(4) 改变试件的表面加工质量,研究表面质量不同时的摩擦、磨损情况。
摩擦磨损试验机的组成及工作原理介绍
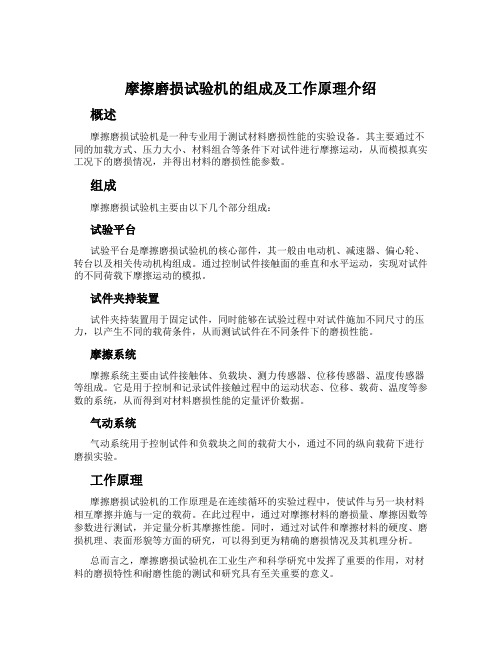
摩擦磨损试验机的组成及工作原理介绍
概述
摩擦磨损试验机是一种专业用于测试材料磨损性能的实验设备。
其主要通过不同的加载方式、压力大小、材料组合等条件下对试件进行摩擦运动,从而模拟真实工况下的磨损情况,并得出材料的磨损性能参数。
组成
摩擦磨损试验机主要由以下几个部分组成:
试验平台
试验平台是摩擦磨损试验机的核心部件,其一般由电动机、减速器、偏心轮、转台以及相关传动机构组成。
通过控制试件接触面的垂直和水平运动,实现对试件的不同荷载下摩擦运动的模拟。
试件夹持装置
试件夹持装置用于固定试件,同时能够在试验过程中对试件施加不同尺寸的压力,以产生不同的载荷条件,从而测试试件在不同条件下的磨损性能。
摩擦系统
摩擦系统主要由试件接触体、负载块、测力传感器、位移传感器、温度传感器等组成。
它是用于控制和记录试件接触过程中的运动状态、位移、载荷、温度等参数的系统,从而得到对材料磨损性能的定量评价数据。
气动系统
气动系统用于控制试件和负载块之间的载荷大小,通过不同的纵向载荷下进行磨损实验。
工作原理
摩擦磨损试验机的工作原理是在连续循环的实验过程中,使试件与另一块材料相互摩擦并施与一定的载荷。
在此过程中,通过对摩擦材料的磨损量、摩擦因数等参数进行测试,并定量分析其摩擦性能。
同时,通过对试件和摩擦材料的硬度、磨损机理、表面形貌等方面的研究,可以得到更为精确的磨损情况及其机理分析。
总而言之,摩擦磨损试验机在工业生产和科学研究中发挥了重要的作用,对材料的磨损特性和耐磨性能的测试和研究具有至关重要的意义。
摩擦磨损试验机工作原理

摩擦磨损试验机工作原理摩擦磨损试验机是一种用于测试材料表面摩擦磨损性能的设备。
它的工作原理是通过施加一定的负荷和摩擦力,使试样与摩擦副相互作用,并模拟实际工作条件下的摩擦磨损过程。
摩擦磨损试验机主要由负荷系统、摩擦系统、运动控制系统和数据采集系统等组成。
负荷系统是摩擦磨损试验机的核心部分,它的作用是施加一定的力或负荷到试样上。
负荷系统通常包括负荷传感器、负荷调节装置和负荷控制系统。
负荷传感器用于测量施加在试样上的力或负荷大小,负荷调节装置用于调节施加在试样上的负荷大小,负荷控制系统用于控制负荷的施加方式和施加时间。
摩擦系统是摩擦磨损试验机的另一个重要组成部分,它的作用是通过施加摩擦力使试样与摩擦副发生相对运动。
摩擦系统通常包括摩擦副、摩擦力传感器和摩擦力调节装置。
摩擦副是指试样与摩擦副之间的接触面,它可以是两个试样之间的接触面,也可以是试样与摩擦副之间的接触面。
摩擦力传感器用于测量试样与摩擦副之间的摩擦力大小,摩擦力调节装置用于调节试样与摩擦副之间的摩擦力大小。
运动控制系统是摩擦磨损试验机的另一个关键部分,它的作用是控制试样与摩擦副之间的相对运动。
运动控制系统通常包括电机、减速器和传动装置等。
电机提供驱动力,减速器用于调节电机的转速和转矩,传动装置用于将电机的运动传递给试样和摩擦副。
数据采集系统是摩擦磨损试验机的重要组成部分,它的作用是采集和记录试样与摩擦副之间的摩擦磨损数据。
数据采集系统通常包括传感器、数据采集卡和计算机等。
传感器用于测量试样与摩擦副之间的各项物理量,数据采集卡用于将传感器采集到的数据转换为计算机可识别的信号,计算机用于接收和处理数据,并生成相应的测试结果。
摩擦磨损试验机的工作过程一般包括以下几个步骤:首先,将试样和摩擦副装入试验机;然后,通过负荷系统施加一定的负荷到试样上;接下来,通过摩擦系统施加一定的摩擦力使试样与摩擦副发生相对运动;同时,运动控制系统控制试样与摩擦副之间的相对运动方式和运动速度;最后,数据采集系统采集和记录试样与摩擦副之间的摩擦磨损数据,并生成相应的测试结果。
摩擦机工作原理

摩擦机工作原理
摩擦机是一种常见的机械设备,它通过利用摩擦力来完成工作。
摩擦机的工作原理如下:
1. 摩擦产生摩擦力:摩擦机内部通常有两个摩擦面,它们之间会产生摩擦力。
摩擦力是两个物体之间相互接触并相对运动时产生的力。
2. 摩擦力推动工作物体:摩擦机通常会有一个工作物体,例如一个物体表面上的零件。
当摩擦力作用在工作物体上时,它会推动工作物体产生运动。
3. 控制摩擦力大小:摩擦力的大小可以通过摩擦机的设计和控制来调节。
例如,可以通过调整摩擦面之间的接触压力或改变摩擦面材料的性质来控制摩擦力的大小。
4. 实现工作效果:通过控制摩擦力的大小和方向,摩擦机可以实现不同的工作效果。
例如,可以用摩擦力夹持工件,将工件移动到所需位置;也可以用摩擦力将两个物体连接在一起。
总的来说,摩擦机利用摩擦力完成工作。
通过控制摩擦力的大小和方向,它可以实现不同的工作效果。
摩擦磨损性能测试试验
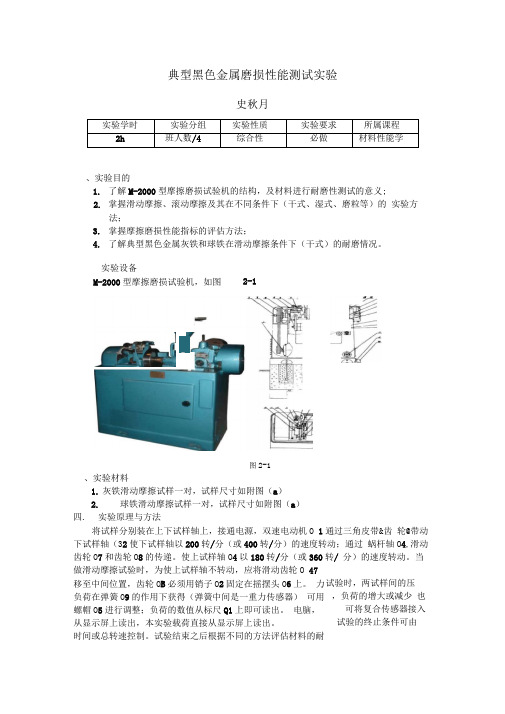
典型黑色金属磨损性能测试实验史秋月 实验学时 实验分组 实验性质 实验要求 所属课程 2h班人数/4 综合性 必做 材料性能学 、实验目的1. 了解M-2000型摩擦磨损试验机的结构,及材料进行耐磨性测试的意义;2. 掌握滑动摩擦、滚动摩擦及其在不同条件下(干式、湿式、磨粒等)的 实验方法;3. 掌握摩擦磨损性能指标的评估方法;4. 了解典型黑色金属灰铁和球铁在滑动摩擦条件下(干式)的耐磨情况。
、实验材料1. 灰铁滑动摩擦试样一对,试样尺寸如附图(a )2. 球铁滑动摩擦试样一对,试样尺寸如附图(a )四. 实验原理与方法将试样分别装在上下试样轴上,接通电源,双速电动机O 1通过三角皮带&齿 轮@带动下试样轴(32使下试样轴以200转/分(或400转/分)的速度转动;通过 蜗杆轴O 4,滑动齿轮O 7和齿轮O 8的传递。
使上试样轴O 4以180转/分(或360转/ 分)的速度转动。
当做滑动摩擦试验时,为使上试样轴不转动,应将滑动齿轮O 47移至中间位置,齿轮O B 必须用销子O 2固定在摇摆头O 6上。
力负荷在弹簧O 9的作用下获得(弹簧中间是一重力传感器) 可用螺帽O 5进行调整;负荷的数值从标尺Q1上即可读出。
电脑,从显示屏上读出,本实验载荷直接从显示屏上读出。
时间或总转速控制。
试验结束之后根据不同的方法评估材料的耐实验设备M-2000型摩擦磨损试验机,如图 试验时,两试样间的压 ,负荷的增大或减少 也可将复合传感器接入 试验的终止条件可由 2-1图2-1—rba磨情况。
五、实验内容将加工好的滑动摩擦试样装在实验机上,在给定的条件下(干式、滑动摩擦、压力:200N、时间60min)进行试验,试验结束后将试样取下,评估耐磨性能。
根据所选取磨损试验方法的不同以及材料本质的差异,可以选择不同的耐磨性能评定方法,以期获得精确的试验数据,现简单例举下述几种方法以供参考。
1、称重法:采用试样在试验前后重量之差,本表示耐磨性能的方法,由于两试样之间的摩擦所引起的磨损量,可以采用精度达万分之一的分析天平称量出试样试验前后重量之差非凡获得。
摩擦磨损与润滑实验

摩擦磨损与润滑实验实验目的23通过实验了解不同材料配副、不同摩擦(润滑)状态时的摩擦系数与磨损量的变化;了解不同材料配副对摩擦磨损的影响;学会摩擦学实验的基本方法,学会有关仪器设备的使用方法。
102 实验设备及原理实验机设备的名称是球盘式摩擦磨损实验机,其实物照片如图所示设备的原理图如下图所示,实验机由如下9部分组成1.带传动2.电动机3.托盘4.下试件5.上试件6.夹头7.砝码8.摆杆9.压力传感器试验机的工作过程电动机2经带传动1驱动托盘3回转;Array下试件4安装在托盘3上并随托盘3一起回转;上试件5装在夹头6中;载荷P由砝码7的重力W产生;摆杆的另一端压在压力传感器9上;传感器上检测的力Q可由数据采集测试系统测得。
设备的技术指标与参数实验机参数:转速范围:n=100-500(r/min);最大载荷:Wmax=10N;试件的结构尺寸与材料尺寸球的尺寸为Ф11.113mm ;圆盘直径为Ф60mm ,厚度为8mm 。
材料上试件:GCr15钢、Si3N4陶瓷下试件:钢、铸铁、铜、PTFE等材料摩擦系数测试原理P=W (N )QL 1=FL 2L 1=L 2Q=F预先确定加载砝码的重力W ,再由测试系统测出传感器受力Q 的大小,进而计算出摩擦系数f 。
F Q f P W==数据采集系统原理测试系统的硬件:传感器、信号放大器、数据采集卡、计算机等。
下图为数据测试采集系统框图。
数据采集AD转换数据存储数据处理信号放大摩擦磨损实验测试系统软件是实验室自己开发的,这是主界面。
这是输入实验参数的界面。
计算机屏幕实时显示摩擦系数的变化曲线,可以直接存储成图片文件格式。
还可以把摩擦系数以数据文件格式输出,便于后处理。
这是后处理的摩擦系数随时间变化的曲线。
这是实验结束时的界面,点击“保存数据”可存成数据格式文件,击“保存曲线”可存成图片格式文件。
磨痕观察测量原理磨痕观察测量系统包括:金相数码显微镜、二维图像测量软件两部分,这是金相数码显微镜;这是二维图像测量软件主界面。
- 1、下载文档前请自行甄别文档内容的完整性,平台不提供额外的编辑、内容补充、找答案等附加服务。
- 2、"仅部分预览"的文档,不可在线预览部分如存在完整性等问题,可反馈申请退款(可完整预览的文档不适用该条件!)。
- 3、如文档侵犯您的权益,请联系客服反馈,我们会尽快为您处理(人工客服工作时间:9:00-18:30)。
齿轮摩擦磨损试验机工作原理
工作原理是齿轮摩擦磨损试验机的灵魂,只有掌握工作原理,才能熟练地掌握,应用。
下面简单介绍一下几个重要部件的工作原理。
1,加载方式
该机是一种动力闭环结构,加载方式采用加载杆挂砝码的方式。
加载杆挂在加载离合器的槽轮上,加挂砝码后,通过紧固加载离合器的螺母,将加载离合器上的两个槽轮拧紧,取下砝码及加载杆,在扭矩测量离合器上可读出扭矩。
2,温度控制
试样的加热及温度的控制,都通过温度控制表和调功器来实现。
在温度控制表的右侧有一个纽子开关,掰到“开”的一边,温度控制表接通电源,掰到“关”的一边,温度控制表断开电源。
调功器开关操作相同,通过对温控表的设置和调功器的操作,可以实现对试验温度的控制。
3,电器部分
插上电源线后,按下电源部分的“开”按钮,整个机器处于通电状态;按下电源部分的“关”按钮,整个机器处于断电状态;按下电源部分的“开”按钮后,按“低速”按钮,电机将以1450r/min的转速运转;按下“电机停”按钮,电机将停止运转。
产品用途:
CL-100齿轮摩擦磨损试验是一种多用途试验机。
即可用于润滑剂承载能力的评定,也可根据用户需要,特殊定货,用于齿轮副的胶合承载能力和齿轮接触承载能力的试验。
相关标准:
GB/T13672-92《润滑剂承载能力测定法(CL-100齿轮机法)》
SH/T0306-92《齿轮胶合承载能力试验方法》
主要技术性能指标:
1.最大扭矩:1kN.m;
2.最大载荷级:13级;
3.温度控制精度:±2%;
4.驱动电机功率:6.5/8kw;
5.驱动电机转速:1450/2880r/min,无级可调;
6.试验齿轮箱容量(轴中心线至箱底面的部分):1.25L;
7.加热功率:0.5×3=1.5kw;
8.主机外型尺寸(长×宽×高)1390×705×1082mm。
9.可增加试验箱体、驱动箱体冷却器,可实现试验介质冷却保温。
10.可增加循环油箱,可实现试验介质的动态循环。
工作环境:
试验机应在下列条件下工作:
1、电源电压的波动范围不应超过额定值的±10%,频率的波动范围不应超过额定值的2%;
2、试验机应水平安装,安装基础须平稳,主机工作台纵横方向水平误差应不超过0.2/1000;
3、室温10℃-35℃;
4、环境无震动,无强磁场干扰,无腐蚀性介质;
5、相对湿度不大于80%。