密封件定位套设计说明书
密封圈定位套铸件大批量生产答辩记录
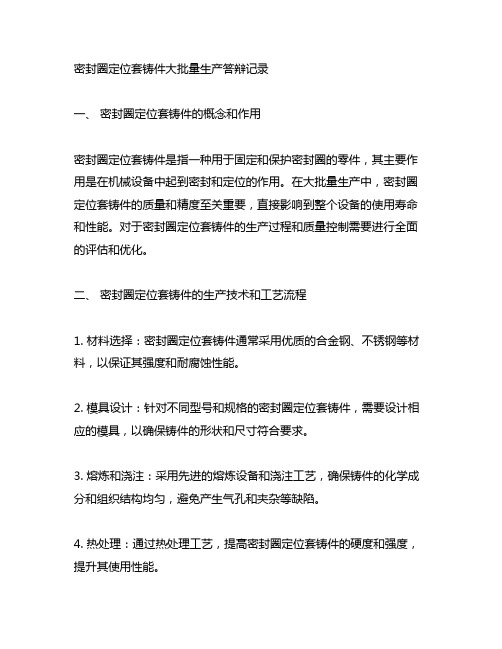
密封圈定位套铸件大批量生产答辩记录一、密封圈定位套铸件的概念和作用密封圈定位套铸件是指一种用于固定和保护密封圈的零件,其主要作用是在机械设备中起到密封和定位的作用。
在大批量生产中,密封圈定位套铸件的质量和精度至关重要,直接影响到整个设备的使用寿命和性能。
对于密封圈定位套铸件的生产过程和质量控制需要进行全面的评估和优化。
二、密封圈定位套铸件的生产技术和工艺流程1. 材料选择:密封圈定位套铸件通常采用优质的合金钢、不锈钢等材料,以保证其强度和耐腐蚀性能。
2. 模具设计:针对不同型号和规格的密封圈定位套铸件,需要设计相应的模具,以确保铸件的形状和尺寸符合要求。
3. 熔炼和浇注:采用先进的熔炼设备和浇注工艺,确保铸件的化学成分和组织结构均匀,避免产生气孔和夹杂等缺陷。
4. 热处理:通过热处理工艺,提高密封圈定位套铸件的硬度和强度,提升其使用性能。
5. 加工和检测:采用精密加工设备对铸件进行精确加工,同时进行严格的检测,以保证产品的质量和精度。
三、密封圈定位套铸件大批量生产的挑战与应对1. 资源配置:对于大批量生产而言,需要充足的人力、物力和财力投入,同时要合理规划生产流程,确保生产效率和质量。
2. 质量控制:大批量生产中,对于每一件产品的质量控制至关重要,需要建立全面的质量管理体系,做好过程控制和产品检验。
3. 成本管理:在大批量生产中,要不断优化生产工艺,控制生产成本,提高资源利用效率,以确保产品价格的竞争力。
四、对于密封圈定位套铸件大批量生产的个人观点和思考针对密封圈定位套铸件大批量生产的挑战,我认为需要从技术、管理和市场等多方面进行综合优化。
在技术方面,要不断引进先进的生产设备和工艺,提高生产效率和产品质量;在管理方面,要建立科学的管理体系,优化生产流程,提高资源利用效率;在市场方面,要深入了解客户需求,不断创新产品,提高市场竞争力。
总结回顾通过本文的综合分析,我们对密封圈定位套铸件大批量生产的相关内容有了全面的了解。
派克液压密封件说明书

派克汉尼汾公司版权所有未经许可不能摘录,翻印。
保留修改权利2021年6月警告销售条件本样本中产品和/或系统或相关产品出现故障,选型不当或使用不当,均可能导致人身伤亡和财产损失。
本文档以及由派克·汉尼汾公司及其子公司和授权经销商提供的其他资料,为具有技术知识的用户提供进一步研究所需的产品和/或系统选项。
重要的是,用户必须对您的应用进行全面的分析,并对当前产品样本中与产品或系统相关的资料进行评估。
由于工作条件以及产品或系统的多样性,用户必须自行分析和测试,并独自承担一切后果,包括:产品和系统的最终选型以及确保满足应用的所有性能、安全和警告等方面的要求。
派克·汉尼汾及其子公司可能会随时对本样本中的产品,包括但不限于:产品的特性、产品的规格、产品的结构、产品的有效性以及产品的价格作出变更而不另行通知.本样本中的所有产品均由派克·汉尼汾公司及其子公司和援权经销商销售。
与派克签订的任何销售合同均按照派克标准条件和销售条件中规定的条款执行(提供复印件备索)。
本公司的密封件,只能在本公司的文件资料述及的应用参数范围与接触介质、压力、温度和存放时间相一致的情况下才能使用。
在规定的应用参数范围外使用以及错误选用不同的材料都可能导致密封件寿命的缩短以及设备的损坏,甚至更严重的后果(如生命安全,环境污染等)。
样本中所列出的工作压力、温度范围、运动速度是极限值,它们之间相互关联、相互影响;在极端的工况下,建议不要同时把各个参数都同时用到极限值。
对于特殊的要求(压力、温度、速度、介质等),请联系派克汉尼汾公司以咨询合适的密封结构、材料、配置、安装建议等。
由于诸多工作参数会影响到流体传动系统及密封元件,这些设备的制造商必须在实际工作条件下测试、验证并批准密封系统的功能与可靠性。
此外,对于不断出现的新的介质(液压油、润滑脂、清洗剂等),用户特别注意它们与目前所用的密封件弹性体材料的兼容性。
我们建议用户在大批量应用之前,在厂内或现场先做密封材料的兼容性能测试,作为密封产品与系统供应商,我们建议用户遵循我们的这些建议。
毕业设计(论文)-D型密封圈的设计说明书
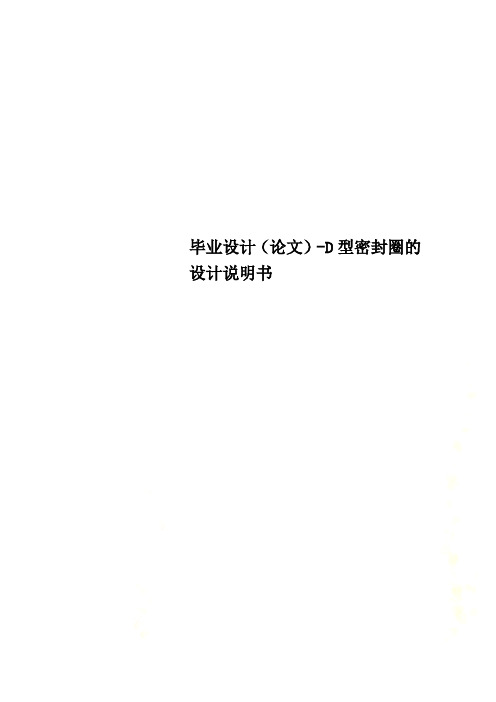
毕业设计(论文)-D型密封圈的设计说明书D型密封圈单腔模设计说明书徐州工业职业技术学院系别:材料工程系班级:高分子应用097姓名:学号:班内序号:09参考目录一、分析D型密封圈 (3)二、模具结构的确定与设计 (3)(1)模具设计的基本要求 (3)(2)模具断面形状及类型的选择 (2)(3)分型面的选择与确定 (4)(4)收缩率的确定及影响因素 (4)(5)型腔尺寸的确定 (5)(6)模具导向与定位 (5)(7)余料槽、启模口 (5)(8)模具外形尺寸的确定 (6)(9)模具型腔内的粗糙度及模具外表面的粗糙度 (6)(10)模具材料的选择 (6)(11)模具设计组合图设计 (7)(12)模具半模图设计 (8)总结 (9)主要参考文献 (9)D型密封圈的设计一、D型密封圈的使用分析D型密封圈再使用过程中不易拧扭损伤,且在低温下起作用时,、其接触压力比O形圈大,不易啃伤,是一种自密性能好的橡胶密封圈,其类型属于异形断面O形圈,其模具与O形圈模具相似,分型面选择在圆弧最大处。
二、模具结构的确定与设计1、设计基本要求提高制品质量,满足外观和尺寸精度等方面的要求,若设计的密封圈其静密封作用,则Ra=6.3~3.2um,动密封时,则Ra<1.6um.。
2、模具的装拆、填料及取出制品,不要损坏制品该模具有上下模与型芯共三部分组成,设有启模口、型芯与上下模用斜面导向槽,型芯与上下模用斜面定位。
上模与型腔之间设有跑气孔,且下模靠近型腔部位开半径为2的半圆形余料槽,保证制品取出方便,模具装拆、填料方便易用。
3、制造容易,成本低廉模具为单腔模,使用的模具的成型方法为一般车雪冰、磨削等方法。
该模具是为丁腈胶模具,无腐蚀性,可选用性能合乎要求的45号钢等一般碳素结构钢,其切削加工性能良好,且该钢可进行调质处理,强度和耐磨性也较高,另外价格较低,有利于降低模具的制造成本,选用45号钢可满足条件。
三、模具的断面形状及类型的选择模具断面为类似长方形,即沿直径方向纵向切开,采用压模类型的开放式结构.四、分型面的选择与确定该胶料密封圈有圆弧,分型面可选择在圆弧最大处,且该圆弧与密封圈上表面相切,可将分型面确定在上表面相平的位置上。
密封件定位套

设计说明书目录一、课程设计任务书 (2)二、前言 (4)三、零件的分析 (5)四、工艺规程的设计 (5)(一)确定毛坯的制造形式 (5)(二)基准的选择 (5)(三)工艺路线的拟定 (6)(四)机械加工余量,工序尺寸及毛坯尺寸的确定 (7)五、机械加工余量 (8)六、毛胚图 (9)七、机械加工工艺过程卡片 (10)八、设计总结………………………………………………………………………九、主要参考文献…………………………………………………………………广东轻工职业技术学院机械加工工艺规程设计任务书(五)设计题目设计“二联齿轮”零件的机械加工工艺规程(生产纲领:小批量)设计内容 1产品零件图一张2产品毛坯图一张3机械加工工艺过程综合卡片一份4课程设计说明书一份班级:机电091设计者:林晓新指导老师:陈学文2011年 6月 21日前言本次设计目的经典零部件制造与检验(二)实训是在学习了本课程,进行了金工实习及下厂参观的基础上进行的一个教学环节,要求学生综合运用本课程及其有关的先修课程理论和实践知识,进行经典零件加工工艺规程的设计,机械设计课程设计是机械类专业和部分非机械类专业学生第一次较全面的机械设计训练,是机械设计和机械设计基础课程重要的综合性与实践性教学环节,其目的是:1培养学生运用本课程及有关课程(机械制图、公共材料与热处理、机械设计基础、互换性与测量技术等)的知识,结合个相关的实习中获得的知识,独立的分析和解决机械零件的加工工艺问题,初步具备设计有关中等复杂程度的零件的工艺规程的能力。
2能正确地解决机械零件在加工中的定位、加紧以及工艺路线安排、加工余量及工艺尺寸确定等问题,做到既能保证加工质量,又能满足加工成本合理的要求。
3培养学生熟练的运用有关手册、规范、图表等技术的能力。
4进一步培养学生识图、制图、运算和编写技术文件的能力。
由于时间仓促和水平有限,说明书中难免有不当和欠妥之处,敬请老师不吝批评指正。
全套机械密封件说明

GM37G系列机械密封件本系列属单端面密封,非平衡型符合DIN24960标准适用于水泵、污水泵、油泵、化工泵及潜水泵等。
一、概述:本系列属单端面密封,非平衡型符合DIN24960标准适用于水泵、污水泵、油泵、化工泵及潜水泵等。
二、主要技术参数压力:≤1.2MPa温度:-30℃~200℃转速:≤3000R/min密封介质:水、污水、油及一般腐蚀性液体中使用GM121系列机械密封件本系列适用于污水、油类及一般弱腐蚀介质,静环有石墨环、硬质环、碳化硅环。
概述:本系列适用于污水、油类及一般弱腐蚀介质,静环有石墨环、硬质环、碳化硅环。
如果使用在较强的腐蚀性介质,可以改O型圈为F4V型圈。
本系列机械密封系YM120型改进型,改动环为O型圈调节型,利用弹簧座上的二只肖钉套在叶轮上的传动,使密封的左右旋得已控制,可以任意旋向,可以采用左图中的静环尺寸,安装更简单。
注:静环可以采用左边总图中的形式,且安装长度应为L尺寸减L2尺寸加起H尺寸等于总长。
1.静环O型圈2.静环座3.静环4.动环5.动环O型圈6.动环座7.传动座8.弹簧9.石墨静环或碳化硅静环 10.静环橡胶座主要技术参数适用压力:≤1 Mpa适用温度:-20℃~180℃电机转速:轴径≤45≤3000转/分轴径≥50≤1450转/分GM122系列机械密封件M122系列机械密封件是一种内装内流单端面单弹簧非平衡型结构,符合ISO-3069、JB1472-75。
标准。
广泛应用于各种离心泵、化工泵、管道泵、及各种耐腐蚀泵。
一、概述:M122系列机械密封件是一种内装内流单端面单弹簧非平衡型结构,符合ISO-3069、JB1472-75。
标准。
广泛应用于各种离心泵、化工泵、管道泵、及各种耐腐蚀泵。
本系列机械密封件O型圈分丁腈橡胶、氟橡胶二种。
如果在强腐蚀性介质中使用,可以用四氟V型圈来代替橡胶O型圈,使用V型圈时,先将V型圈放在90。
C 热水中浸泡10分钟。
安装时使V型紧贴密封件内壁和泵轴,以防满泄漏。
密封圈定位套零件的机械加工夹具设计说明书
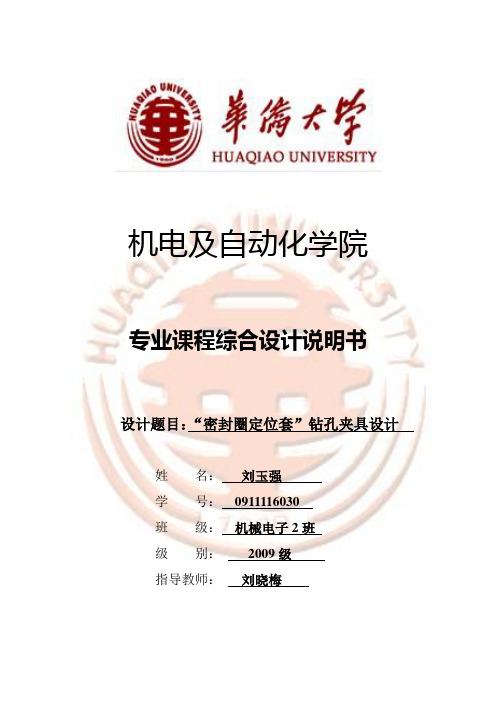
机电及自动化学院专业课程综合设计说明书设计题目:“密封圈定位套”钻孔夹具设计*名:***学号:**********班级:机械电子2班级别:2009级指导教师:***2012 年12月22日前言夹具设计是在我们完成了全部基础课、技术基础课、大部分专业课以及参加了生产实习之后进行的。
这是我们在进行毕业设计之前对所学各课程的一次深入的综合性的复习,也是一次理论联系实际的训练,因此,它在我们四年的大学生活中占有重要的地位。
1. 运用已学过的机床夹具设计及有关课程的理论知识以及生产实习中所获得的实际只是,根据被加工零件的要求,设计既经济合理又能保证加工质量的夹具。
2. 培养结构设计能力,掌握结构设计的方法和步骤3. 学会使用各种手册、图册、设计表格,规范等各种标准技术资料,能够做到熟练运用机械制造技术课程中的基本理论,正确的解决一个零件在加工中的加工基准的选择、定位、夹紧、加工方法选择以及合理安排工艺路线,保证零件的加工质量。
4. 进一步培养机械制图、分析计算、结构设计、编写技术文件等基本技能。
对我而言,此次课程设计是一次难得的实践性环节,是对所学理论知识的又一次更系统更全面的应用、巩固与深化。
从中锻炼着我们的分析问题,解决问题的能力。
尤其对于机械制造方向的学生,为了更好的接触真正的生产加工,步入社会,这次设计是个很好的锻炼机会。
编者2012-10-9目录一.设计课题及任务要求 (4)二.密封圈定位套的分析 (4)1. 零件分析 (4)1-1 零件的作用 (4)1-2零件的工艺分析 (5)1-3确定零件的生产类型 (5)2. 确定毛坯类型和毛坯尺寸 (5)2-1 选择毛坯 (5)2-2 确定毛坯的的尺寸公差和机械加工余量 (5)3. 工艺规程设计 (6)3-1定位基准的选择 (6)3-2拟定工艺路线 (6)3-3加工设备及工艺装备的选用 (8)3-4加工余量、工序尺寸和公差的确定 (9)3-5切削用量的计算 (11)3-6时间定额的计算 (11)三、夹具设计 (11)1.方案的选择 (11)2. 夹紧元件及动力装置确定 (12)3. 钻套、衬套及夹具体零件的选择 (12)4.夹具体中夹紧零件的选择 (14)四、定位误差分析 (14)五、公差配合的选用 (16)六、切削力的计算与夹紧力分析 (16)七、设计小结 (17)四.参考文献 (17)五. 附件 (17)一.设计课题及任务要求:密封圈定位套钻孔3×ø13夹具设计图1定位套工序图二.密封圈定位套的分析:1. 零件分析:1-1.零件的作用:密封圈定位套是机械密封装置中的一个重要零件,它的外圈有凹凸结构,内圈端面凸出一部分保证轴向定位要求。
“密封件定位套”零件的机械加工工艺规程及工序的设计.
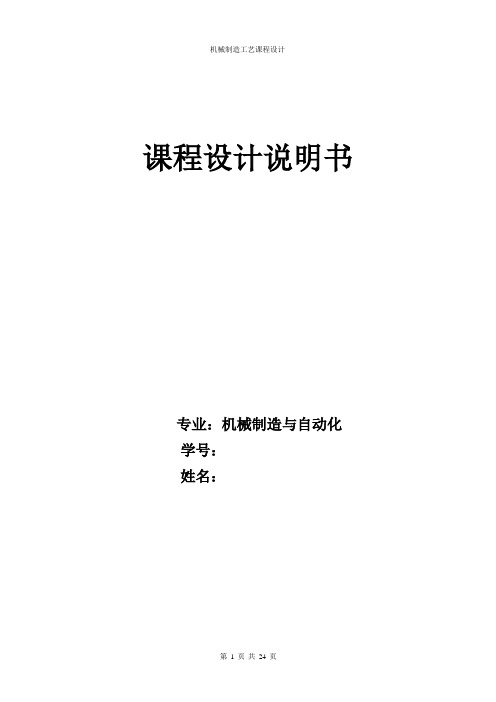
课程设计说明书专业:机械制造与自动化学号:姓名:目录设计任务书 (3)序言 (4)一、零件的分析 (5)二、工艺规程设计 (7)(一)确定毛坯的制造形式 (7)(二)基面的选择 (7)(三)制定工艺路线 (8)(四)机械加工余量、工序尺寸及毛坯尺寸的确定..10 (五)确定切削用量及基本工时 (13)三、总结 (23)参考文献 (24)设计任务书题目:设计“密封件定位套”零件的机械加工工艺规程及工序的设计计算设计内容:1、产品零件图1张;2、产品毛坯图1张;3、机械加工工艺过程卡片1份;4、机械加工工序卡片1张(一道工序);5、课程设计说明书1份(3千字,A4);6、装袋(桂林航院课程设计专用袋、不用档案袋)设计时间:两周序言机械制造工艺学课程设计使我们学完了大学的全部基础课、技术基础课以及大部分专业课之后进行的。
这是我们在进行毕业设计之前对所学各课程的一次深入的综合性的链接,也是一次理论联系实际的训练。
因此,它在我们四年的大学生活中占有重要的地位。
就我个人而言,我希望能通过这次课程设计对自己未来将从事的工作进行一次适应性训练,从中锻炼自己分析问题、解决问题的能力,为今后参加祖国的现代化建设打下一个良好的基础。
由于能力所限,设计尚有许多不足之处,恳请各位老师给予指导。
一、零件的分析(一)零件的作用题目所给定的零件是密封件定位套,其构造成在打开位置和关闭位置之间有选择地定向一密封件。
该组件包括一膨胀器结构,通过转动或其它方式移动到与密封结构的预定部分强制接合和脱开这样的强制接合,该膨胀器结构可设置在一密封件打开或密封件关闭定向。
当密封件定位组件用于实施腹腔镜或类似手术中的套管针组件时,密封件打开定向设置密封结构脱开与通过其间的器械的接合,并可便于充入的气体从充气的体腔内快速地排出。
一偏置组件可连接到密封结构,以在器械不设置在密封结构内的情形下,偏置密封结构到一通常的关闭位置。
构造来打开和关闭一密封结构的密封件定位组件,所述密封件定位组件包括:a)一包括一膨胀器结构的定位装置,膨胀器结构设置成与密封结构保持连通的关系。
“密封件定位套”零件的机械加工工艺规程及工序的设计解读
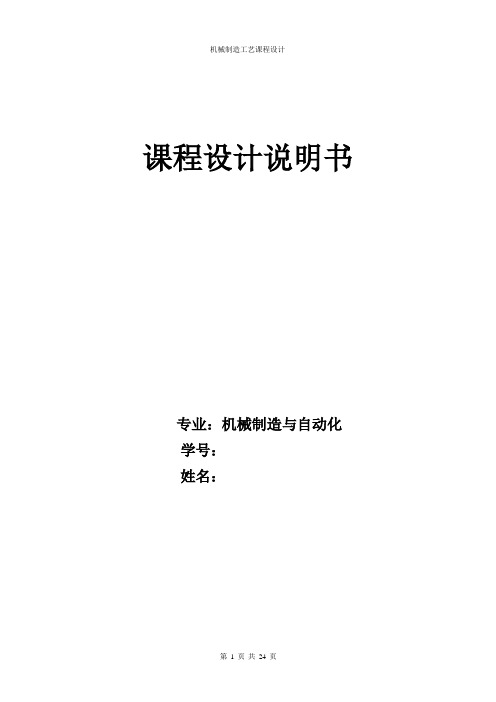
课程设计说明书专业:机械制造与自动化学号:姓名:目录设计任务书 (3)序言 (4)一、零件的分析 (5)二、工艺规程设计 (7)(一)确定毛坯的制造形式 (7)(二)基面的选择 (7)(三)制定工艺路线 (8)(四)机械加工余量、工序尺寸及毛坯尺寸的确定..10 (五)确定切削用量及基本工时 (13)三、总结 (23)参考文献 (24)设计任务书题目:设计“密封件定位套”零件的机械加工工艺规程及工序的设计计算设计内容:1、产品零件图1张;2、产品毛坯图1张;3、机械加工工艺过程卡片1份;4、机械加工工序卡片1张(一道工序);5、课程设计说明书1份(3千字,A4);6、装袋(桂林航院课程设计专用袋、不用档案袋)设计时间:两周序言机械制造工艺学课程设计使我们学完了大学的全部基础课、技术基础课以及大部分专业课之后进行的。
这是我们在进行毕业设计之前对所学各课程的一次深入的综合性的链接,也是一次理论联系实际的训练。
因此,它在我们四年的大学生活中占有重要的地位。
就我个人而言,我希望能通过这次课程设计对自己未来将从事的工作进行一次适应性训练,从中锻炼自己分析问题、解决问题的能力,为今后参加祖国的现代化建设打下一个良好的基础。
由于能力所限,设计尚有许多不足之处,恳请各位老师给予指导。
一、零件的分析(一)零件的作用题目所给定的零件是密封件定位套,其构造成在打开位置和关闭位置之间有选择地定向一密封件。
该组件包括一膨胀器结构,通过转动或其它方式移动到与密封结构的预定部分强制接合和脱开这样的强制接合,该膨胀器结构可设置在一密封件打开或密封件关闭定向。
当密封件定位组件用于实施腹腔镜或类似手术中的套管针组件时,密封件打开定向设置密封结构脱开与通过其间的器械的接合,并可便于充入的气体从充气的体腔内快速地排出。
一偏置组件可连接到密封结构,以在器械不设置在密封结构内的情形下,偏置密封结构到一通常的关闭位置。
构造来打开和关闭一密封结构的密封件定位组件,所述密封件定位组件包括:a)一包括一膨胀器结构的定位装置,膨胀器结构设置成与密封结构保持连通的关系。
密封设计手册
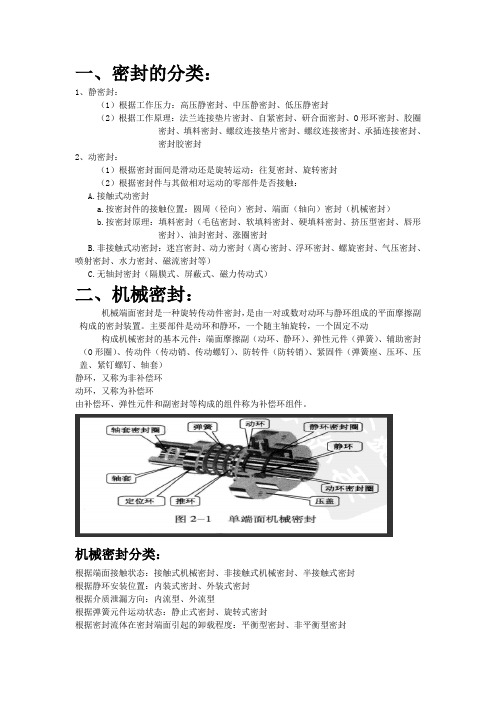
一、密封的分类:1、静密封:(1)根据工作压力:高压静密封、中压静密封、低压静密封(2)根据工作原理:法兰连接垫片密封、自紧密封、研合面密封、O形环密封、胶圈密封、填料密封、螺纹连接垫片密封、螺纹连接密封、承插连接密封、密封胶密封2、动密封:(1)根据密封面间是滑动还是旋转运动:往复密封、旋转密封(2)根据密封件与其做相对运动的零部件是否接触:A.接触式动密封a.按密封件的接触位置:圆周(径向)密封、端面(轴向)密封(机械密封)b.按密封原理:填料密封(毛毡密封、软填料密封、硬填料密封、挤压型密封、唇形密封)、油封密封、涨圈密封B.非接触式动密封:迷宫密封、动力密封(离心密封、浮环密封、螺旋密封、气压密封、喷射密封、水力密封、磁流密封等)C.无轴封密封(隔膜式、屏蔽式、磁力传动式)二、机械密封:机械端面密封是一种旋转传动件密封,是由一对或数对动环与静环组成的平面摩擦副构成的密封装置。
主要部件是动环和静环,一个随主轴旋转,一个固定不动构成机械密封的基本元件:端面摩擦副(动环、静环)、弹性元件(弹簧)、辅助密封(O形圈)、传动件(传动销、传动螺钉)、防转件(防转销)、紧固件(弹簧座、压环、压盖、紧钉螺钉、轴套)静环,又称为非补偿环动环,又称为补偿环由补偿环、弹性元件和副密封等构成的组件称为补偿环组件。
机械密封分类:根据端面接触状态:接触式机械密封、非接触式机械密封、半接触式密封根据静环安装位置:内装式密封、外装式密封根据介质泄漏方向:内流型、外流型根据弹簧元件运动状态:静止式密封、旋转式密封根据密封流体在密封端面引起的卸载程度:平衡型密封、非平衡型密封根据弹性元件的结构和布置:单弹簧式密封、多弹簧式密封、波纹管密封、膜片密封根据密封端面数目:单端面密封、双端面密封、多端面密封根据载荷程度不同:平衡型、非平衡型、过平衡型机械密封计算:1、端面液膜压力:机械密封端面间隙液膜的承载能力。
(1)液膜静压力:当密封间隙有微量泄漏时,由于密封环内外径压差促使流体流动,而流体通过缝隙受到密封面的节流作用,使压力逐步降低Pm=λpPm -------端面上平均液膜静压力,Paλ----液膜反压系数p---密封流体压力(2)液膜动压力:机械密封环端面即使经过精细的研磨加工,在微观上仍存在一定的波动,当两个端面彼此相对摩擦时,由于液膜作用会产生动压效应。
专科课程设计之 密封件定位套课程设计
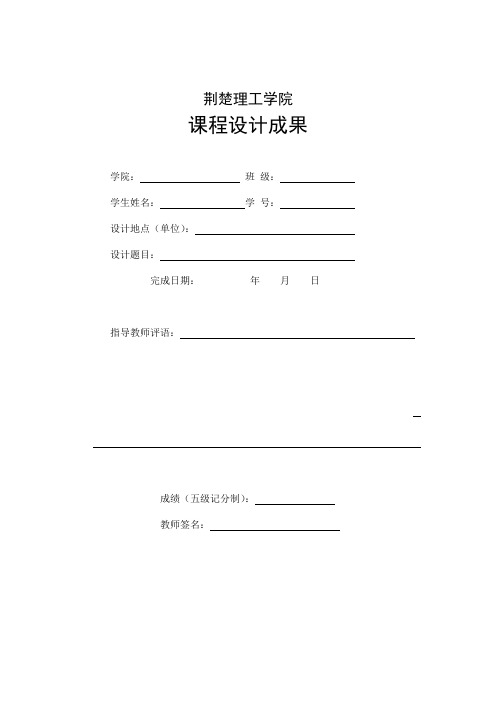
荆楚理工学院课程设计成果学院:班级:学生姓名:学号:设计地点(单位):设计题目:完成日期:年月日指导教师评语:_________________________________________________________________ _________________________________________________________________ ________________________________________________________________成绩(五级记分制):教师签名:荆楚理工学院课程设计任务书设计题目:密封件定位套零件的机械加工工艺规程及工序的设计计算教研室主任:指导教师:年月日目录1零件的工艺分析1.1零件的功用、结构及特点1.2主要加工表面及其要求2毛坯的选择2.1确定毛坯的类型、制造方法和尺寸及其公差2.2确定毛坯的技术要求2.3绘制毛坯图3基准的选择4拟订机械加工工艺路线4.1确定各表面的加工方法4.2拟定加工工艺路线4.3工艺路线方案的分析与比较5确定机械加工余量、工序尺寸及公差6选择机床及工艺装备6.1选择机床6.2选择刀具6.3选择夹具6.4选择量具7确定切削用量及基本工时8填写工艺文件总结参考文献附图附表1零件的工艺分析1.1 零件的功用、结构及特点1.1.1 零件的作用:密封件定位套,它位于传动轴的端部,主要作用是支撑和定位传动轴及密封作用。
它的外圈有凹凸结构,内圈端面凸出一部分保证轴向定位要求。
两者都可以作为密封件的辅助元件达到定位密封,保证密封工作稳定的要求。
1.1.2零件的工艺分析:由零件图可知,其材料为HT200。
该材料具有一定的强度、耐磨性、耐热性及减震性,适用于承受较大应力、要求耐磨的零件。
定位套孔壁较薄,在各道加工工序加工时,应注意选择用合理的夹紧力,以防止工件变形。
定位套内外圆有同轴度要求,为保证加工精度,工艺安排过程应保证工艺基准和设计基准统一。
特瑞堡密封系统产品说明书
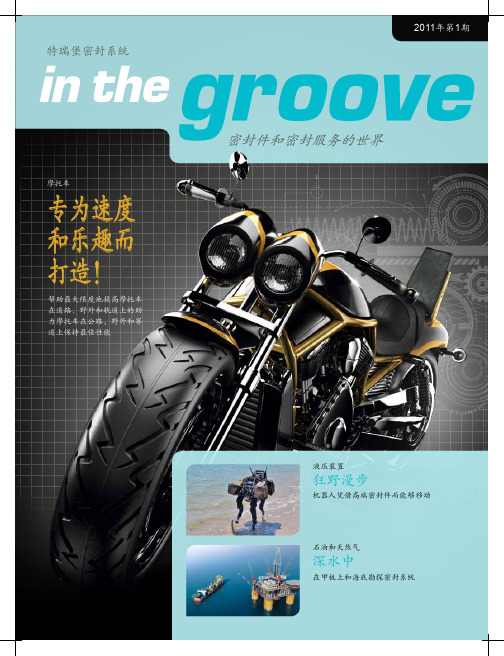
密封件和密封服务的世界液压装置石油和天然气深水中狂野漫步机器人凭借高端密封件而能够移动在甲板上和海底勘探密封系统帮助最大限度地提高摩托车在道路、野外和轨道上的助力摩托车在公路,野外和赛道上保持最佳性能专为速度和乐趣而打造!摩托车2011年第1期特瑞堡密封系统目录3034714中国的扩张提高了特殊处理印度天然气储量展563817294凭借特瑞堡的高端密封件,波士顿动力公司的机器人才得以移动。
想象一下,一个机械化驮骡能够跋涉多岩地带、淌过泥坑、滑过冰层、钻过灌木丛并攀上陡峭的山丘。
它能看到并绕过障碍,经受风吹雨淋,遵照人的指示或自动根据预设的程序行进,始终背负着重达50公斤的负荷。
这听起来像科幻小说中的生物,实际上是称为大狗的四腿机器人, 已经在美国马萨诸塞州的乡村留下了足迹。
大狗及其第二代LS3(Legged Squad Support System 的缩写,步兵班组支援系统)是由波士顿动力公司开发并制造的。
该公司虽小,但拥有尖端技术,其资金由五角大楼的研究机构国防高级研究规狂野漫步123石油天然气大会暨展览会2011年9月6日至8日英国阿伯丁巴西水电展2011年9月20日至22日 巴西里约热内卢印度能源展2011年9月29日至10月1日 印度孟买巴西近海技术会议(OTC)2011年10月4日至6日巴西里约热内卢全球风能大会2011年10月19日至21日 中国北京煤炭采矿博览会2011年10月28日至31日 中国北京瑞典国际工业配件展2011年11月8日至11日 瑞典延雪平国际工程机械展览会2011年11月23日至27日 印度班加罗尔国际工作艇展2011年11月30日至12月2日美国新奥尔良、洛杉矶789456恶劣环境下执行侦查、救援和消防方案的载重机器人20英里以上范围内优异的承载能力由麻省理工学院的前教授用美国五角大楼提供的资金而开发特瑞堡为液压腿部机构提供最佳的高耐用性密封件特瑞堡和波士顿动力公司就第二代人形机器人进行合作简言之…液 压 装 置看到了他这个灵活的机器人的广泛应用,从运载物质到恶劣环境下的侦查、救援和消防任务等各种应用。
密封件定位套设计说明书
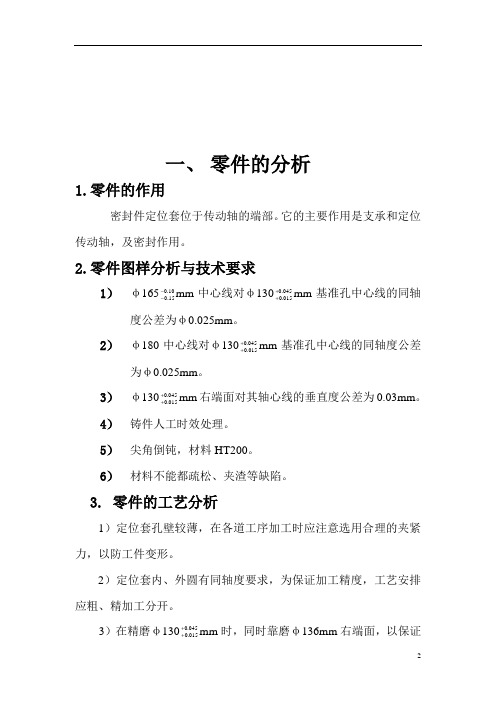
一、 零件的分析1.零件的作用密封件定位套位于传动轴的端部。
它的主要作用是支承和定位传动轴,及密封作用。
2.零件图样分析与技术要求1) φ16510.015.0--mm 中心线对φ130045.0015.0++mm 基准孔中心线的同轴度公差为φ0.025mm 。
2) φ180中心线对φ130045.0015.0++mm 基准孔中心线的同轴度公差为φ0.025mm 。
3) φ130045.0015.0++mm 右端面对其轴心线的垂直度公差为0.03mm 。
4) 铸件人工时效处理。
5) 尖角倒钝,材料HT200。
6) 材料不能都疏松、夹渣等缺陷。
3. 零件的工艺分析1)定位套孔壁较薄,在各道工序加工时应注意选用合理的夹紧力,以防工件变形。
2)定位套内、外圆有同轴度要求,为保证加工精度,工艺安排应粗、精加工分开。
3)在精磨φ130045.0015.0++mm 时,同时靠磨φ136mm 右端面,以保证φ130045.0015.0++mm 右端面对其轴心线的垂直度公差0.03mm 。
4)密封件定位套零件结构特点和技术要求如下:内孔φ130和退刀槽端面粗糙度值较小为Ra1.6um 。
φ180﹑φ160与φ130的同轴度的要求为0.025,固定位要求高。
该零件的主要加工表面是内孔φ130﹑外圆φ180﹑φ165及退刀槽端面。
次要加工表面是其它外圆及径向孔加工。
5)该密封件定位套因为是铸件,采用先铸造出中心孔,以减少加工余量。
6)定位套螺纹孔宽,大径、小径尺寸及等分精度的检查,采用符合量规进行检查。
二、 工艺规程设计(一)确定毛坯的制造形式毛坯成形方法选择的合理与否直接影响到零件的质量、使用性能、成本和生产率;零件的材料选定以后,其毛坯成形方法也大致确定了。
机械零件毛坯选择的原则是既满足零件的使用要求,又使零件在制造过程中具有良好的工艺性和经济性,以利于降低成本和提高生产率。
零件材料为HT200。
密封件定位套零件的生产类型为大批量生产,考虑零件在机床运行过程中所受冲击不大,零件有多个通孔,零件结构又比较简单,生产类型为中等批量生产,故选择铸件毛坯。
密封件定位套工艺过程卡

机械加工工艺过程卡片产品型号零件图号产品名称密封件定位套零件名称共 2 页第 1 页材料牌号HT200毛坯种类铸造毛坯外形尺寸227mmX265mm每毛坯件数 1 每台件数 1 备注工序号工名序称工序内容车间工段设备工艺装备工时准终单件1 备料2 铸造铸件各部留加工余量7mm3 清砂清砂4 热处理人工时效处理5 粗车夹工件右端外圆,照顾铸件壁厚均匀,车内径各部尺寸以及左端面和φ260外圆,留加工余量2mm,法兰盘壁厚23mm,其余各部留余量3mmCA61406 粗车倒头,以内径定位装夹工件,法兰盘外圆找正,车外圆各部,及右端面和右端总长199mm,留加工余量2mmCA61407 精车夹工件右端外圆,车内径至尺寸φ1308.06.0++mm,深195mm处车内槽φ136mm×4mm,车外端面,保证工件总长221mm,车φ260mm法兰盘厚度20mmCA61408 精车倒头,以内径定位装夹工件,精车右端外圆各部尺寸,留磨量0.8mm(注φ160mm不留加工余量),车内径φ905.02.0++mm至尺寸φ90mm,切各环槽至图样尺寸CA61409 磨夹工件右端外圆,内径找正,磨削内径至图样尺寸φ130045.0015.0++mm,靠磨φ136mm端面M1432A10 磨以内径定位装夹工件,磨φ16510.015.0--mm外圆,磨φ18010.015.0--mm外圆至图样尺寸M1432A11 钳划φ175mm中心圆上3×M8孔线,划φ222mm中心圆上3×φ13mm孔线Z52512 钳钻3×φ13mm孔,钻3×M8底孔φ6.7mm、攻螺纹M8、深15mmZ52513 检验桉图样检查各部尺寸和精度摇臂钻床14 入库入库高频感应加热淬火设备设计(日期)校对(日期)审核(日期)标准化(日期)会签(日期)标记处数更改文件号签字日期标记处数更改文件号签字日期。
定位圈的设计与加工制造说明书
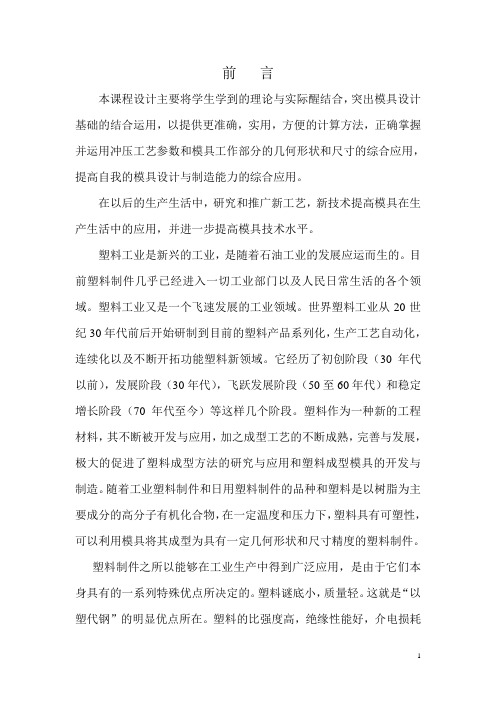
前言本课程设计主要将学生学到的理论与实际醒结合,突出模具设计基础的结合运用,以提供更准确,实用,方便的计算方法,正确掌握并运用冲压工艺参数和模具工作部分的几何形状和尺寸的综合应用,提高自我的模具设计与制造能力的综合应用。
在以后的生产生活中,研究和推广新工艺,新技术提高模具在生产生活中的应用,并进一步提高模具技术水平。
塑料工业是新兴的工业,是随着石油工业的发展应运而生的。
目前塑料制件几乎已经进入一切工业部门以及人民日常生活的各个领域。
塑料工业又是一个飞速发展的工业领域。
世界塑料工业从20世纪30年代前后开始研制到目前的塑料产品系列化,生产工艺自动化,连续化以及不断开拓功能塑料新领域。
它经历了初创阶段(30年代以前),发展阶段(30年代),飞跃发展阶段(50至60年代)和稳定增长阶段(70年代至今)等这样几个阶段。
塑料作为一种新的工程材料,其不断被开发与应用,加之成型工艺的不断成熟,完善与发展,极大的促进了塑料成型方法的研究与应用和塑料成型模具的开发与制造。
随着工业塑料制件和日用塑料制件的品种和塑料是以树脂为主要成分的高分子有机化合物,在一定温度和压力下,塑料具有可塑性,可以利用模具将其成型为具有一定几何形状和尺寸精度的塑料制件。
塑料制件之所以能够在工业生产中得到广泛应用,是由于它们本身具有的一系列特殊优点所决定的。
塑料谜底小,质量轻。
这就是“以塑代钢”的明显优点所在。
塑料的比强度高,绝缘性能好,介电损耗低,所以塑料是现代电工行业和电器行业中不可缺少的原材料。
塑料的化学稳定性最高,减磨耐磨性能好。
此外,塑料的减振和隔音性能也很好。
许多塑料还具有透光性能和绝热性能以及防水,防透气和防辐射等特殊性能。
因此,塑料已成为各行各业中不可缺少的一种重要材料。
需求量的日益增加,这些产品的更新换代的周期愈来愈短。
因此对塑料的品种,产量和质量都提出了越来越高的要求。
从而充分体现了所学的专业知识实际生产的应用。
因此,本课程设计说明说具有以下的优点:一、本课程设计计算说明书结合了塑料模具图册的若干图列,并突出性和实用性的对每一幅模具进行详细的对比分析与学习,然后再结合相应的实践知识进行的设计计算。
机械制造课程设计——密封件定位套说明书

课程设计
课程名称 专业、班级 学生姓名 指导教师 日期
课程设计成绩评定表
班级
学号
设计题目:密封件定位套
个人设计总结:
姓名
成绩评定项目
A
B
C
D
E
完成设计任务情况
工艺过程
工序设计 说明书表达情况
(精炼、流畅、排版正确)
答辩回答问题情况
很好
正确 正确
很好 很好
好
比较好 一般
基本正确 有个别错误 多处错误
为 A4 幅面(可打印)。
5、设计某一个加工工序的机械加工工序卡片,格式参照《机械制造技术基础课程设计指南》,
P113 表 4-9,幅面大小为 A4 幅面(可打印),卡片中的参数、工时定额及辅助时间等参阅指南中相
关内容确定。
6、设计某工序的夹具,用 A1 图纸画出夹具的装配图。包括定位设计、辅助元件设计等。
5.4.1 钻 3 个∅ 孔的切削用量和基本时间............................................................................... 18 5.4.2、钻 3 个∅ . 螺纹底孔切削用量和基本时间 ........................................................... 19 5.4.3、确定工序基本时间 ........................................................................................................... 19 5.5、机械加工工艺过程卡片和工序卡片 ...................................................................................... 19 6、设计小结......................................................................................................................................... 26 7、参考文献......................................................................................................................................... 27 附件零件图和毛坯图各一张
密封设计安装使用说明书
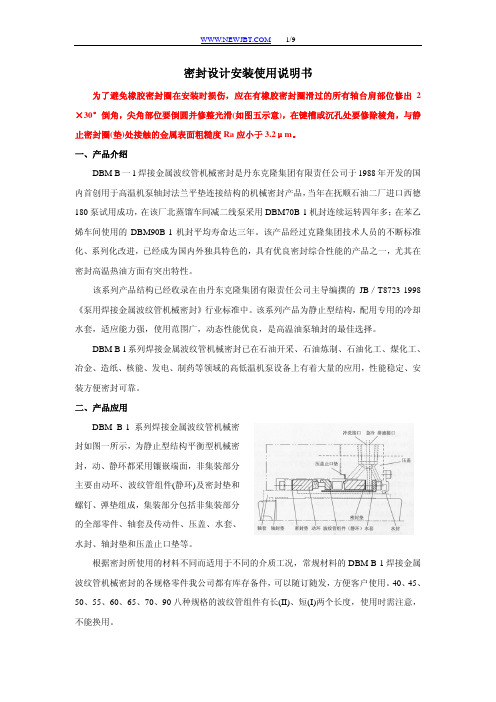
DBM B-l 系列焊接金属波纹管机械密封已在石油开采、石油炼制、石油化工、煤化工、 冶金、造纸、核能、发电、制药等领域的高低温机泵设备上有着大量的应用,性能稳定、安 装方便密封可靠。 二、产品应用
DBM B-1 系列焊接金属波纹管机械密 封如图一所示,为静止型结构平衡型机械密 封,动、静环都采用镶嵌端面,非集装部分 主要由动环、波纹管组件(静环)及密封垫和 螺钉、弹垫组成,集装部分包括非集装部分 的全部零件、轴套及传动件、压盖、水套、 水封、轴封垫和压盖止口垫等。
根据密封所使用的材料不同而适用于不同的介质工况,常规材料的 DBM B-1 焊接金属 波纹管机械密封的各规格零件我公司都有库存备件,可以随订随发,方便客户使用。40、45、 50、55、60、65、70、90 八种规格的波纹管组件有长(II)、短(I)两个长度,使用时需注意, 不能换用。
3/9
高黏稠的介质及易结晶、易结焦、易聚合的介质可以阻塞波纹管,使其失弹,DBM B-1 系列焊接金属波纹管机械密封不宜用于此类的介质中。 三、安装
准备 1.对所要安装的密封进行核实,查看密封包装盒上标注泵位号或泵型号是否与所要安 装的机泵相符合,查阅密封装配图,掌握密封结构和安装位置。 2.按照机泵相关的拆卸顺序和要求,拆下机泵的轴承箱等相关部件,拆下旧的密封装 置。 3.对泵的密封腔各相关部件进行外观检查和尺寸检查,包括各配合尺寸、空间尺寸、 形位公差等,并做相应处理。 3.1校核密封腔体中旋转轴相对于静止腔体的轴向及径向跳动值,确保不超过国家相 关标准规定的极限值。 轴端部检查,跳动量小于 0.1mm(如图二示意) 轴径向检查,跳动量小于 0.05mm(如图三示意) 密封腔止口端面与轴的垂直度检查,允差小于 0.05mm(如图四示意) 如果不能达到 上述要求,应检修调整相关部件。
Y型密封圈模具设计说明书

第一章塑件及材料的工艺性分析1.1 设计任务的原始依据本次设计是由指导老师以样件的形式为我们下达的设计任务,要求我们设计一套成型自选样件注射模具。
我所设计Y型密封圈样件的塑料制品图如图1-1所示。
该塑件的材料为TPU,塑件的使用精度为一般精度要求,塑件外表面光滑、无飞边毛刺及明显的熔接痕,侧面不允许有浇口痕迹。
塑件的强度和刚度要满足装配及其他方面的使用要求。
该塑件的生产属于较大批生产。
生产条件为卧式中小型注射机。
图1-1Y形密封圈塑料制品图1.2 塑件的工艺性分析1. 塑件的材料特性和成型性能分析塑件材料为TPU,查手册知TPU塑料的收缩率为1%。
热塑性聚氨酯弹性体,具有高张力、高拉力、强韧和耐老化,抗撕裂性的特性。
挤出级系列(硬度75A-64D)以表面光泽度分为光面及雾面两种,成形性良好,表面无麻点、应用于弹性肩带、各种线材、装饰材料、运动器材、服装辅料、密封材料等领域。
2. 材料的工艺性分析TPU塑料可以使用螺杆注射机。
一般使用螺杆注射机时得工艺条件如下:料筒温度后段130~180℃;中段,前段150~210℃;注射压力80~120Mpa;模具温度20~40℃;注射时间15~20s;保压时间15~20s;冷却时间20~40s。
成型TPU90塑料时,熔融粘度对温度依存性大。
温度过高则粘度降低,树脂一流动,容易产生溢料孔隙、凹凸收缩等不良现象;3. 浇口的选择TPU在浇口、方面没有特别的限制,用浇口粗、倾角大的模具在脱模时十分方便。
比通用树脂的大些。
但须注意采用点状空隙节流孔时孔直径要大于Φ0.7mm,否则树脂填充不好得不到好的制品。
4. 成型零件的结构设计为了方便加工和热处理,型芯、型腔均采用整体式结构。
1.3 型腔数目的确定根据塑件形状简单,但形状较大,生产批量较大及尺寸精度要求,应使用单型腔注射模具,故模具采用一模一腔。
按照塑料件图所示(小沟、槽等部位简化)近似计算:单件塑件体积为: VS≈14.539cm³查手册知塑料LDPE的密度为1.10~1.25g/cm³(取平均密度为1.175g/cm³) 由制品尺寸计算出单件塑件重量为ms=14.539 x 1.175 = 17g1.4 塑件推出方式确定的由于塑件形状为圆环形,由于是高端密封件所以使用推杆推出容易在塑件上留下推出痕迹,不宜采用;由于塑件柔软,单独使用推件板推出时容易使塑件变形。
D型密封圈的设计说明书概述

D型密封圈的设计说明书概述D型密封圈单腔模设计说明书徐州工业职业技术学院系别:材料工程系班级:高分子应用097姓名:李贵学号:930207013班内序号:09参考目录一、分析D型密封圈 (3)二、模具结构的确定与设计 (3)(1)模具设计的基本要求 (3)(2)模具断面形状及类型的选择 (2)(3)分型面的选择与确定 (4)(4)收缩率的确定及影响因素 (4)(5)型腔尺寸的确定 (5)(6)模具导向与定位 (5)(7)余料槽、启模口 (5)(8)模具外形尺寸的确定 (6)(9)模具型腔内的粗糙度及模具外表面的粗糙度 (6)(10)模具材料的选择 (6)(11)模具设计组合图设计 (7)(12)模具半模图设计 (8)总结 (9)主要参考文献 (9)D型密封圈的设计一、D型密封圈的使用分析D型密封圈再使用过程中不易拧扭损伤,且在低温下起作用时,、其接触压力比O形圈大,不易啃伤,是一种自密性能好的橡胶密封圈,其类型属于异形断面O形圈,其模具与O形圈模具相似,分型面选择在圆弧最大处。
二、模具结构的确定与设计1、设计基本要求提高制品质量,满足外观和尺寸精度等方面的要求,若设计的密封圈其静密封作用,则Ra=6.3~3.2um,动密封时,则Ra<1.6um.。
2、模具的装拆、填料及取出制品,不要损坏制品该模具有上下模与型芯共三部分组成,设有启模口、型芯与上下模用斜面导向槽,型芯与上下模用斜面定位。
上模与型腔之间设有跑气孔,且下模靠近型腔部位开半径为2的半圆形余料槽,保证制品取出方便,模具装拆、填料方便易用。
3、制造容易,成本低廉模具为单腔模,使用的模具的成型方法为一般车雪冰、磨削等方法。
该模具是为丁腈胶模具,无腐蚀性,可选用性能合乎要求的45号钢等一般碳素结构钢,其切削加工性能良好,且该钢可进行调质处理,强度和耐磨性也较高,另外价格较低,有利于降低模具的制造成本,选用45号钢可满足条件。
三、模具的断面形状及类型的选择模具断面为类似长方形,即沿直径方向纵向切开,采用压模类型的开放式结构.四、分型面的选择与确定该胶料密封圈有圆弧,分型面可选择在圆弧最大处,且该圆弧与密封圈上表面相切,可将分型面确定在上表面相平的位置上。
- 1、下载文档前请自行甄别文档内容的完整性,平台不提供额外的编辑、内容补充、找答案等附加服务。
- 2、"仅部分预览"的文档,不可在线预览部分如存在完整性等问题,可反馈申请退款(可完整预览的文档不适用该条件!)。
- 3、如文档侵犯您的权益,请联系客服反馈,我们会尽快为您处理(人工客服工作时间:9:00-18:30)。
一、 零件的分析1.零件的作用密封件定位套位于传动轴的端部。
它的主要作用是支承和定位传动轴,及密封作用。
2.零件图样分析与技术要求1) φ16510.015.0--mm 中心线对φ130045.0015.0++mm 基准孔中心线的同轴度公差为φ0.025mm 。
2) φ180中心线对φ130045.0015.0++mm 基准孔中心线的同轴度公差为φ0.025mm 。
3) φ130045.0015.0++mm 右端面对其轴心线的垂直度公差为0.03mm 。
4) 铸件人工时效处理。
5) 尖角倒钝,材料HT200。
6) 材料不能都疏松、夹渣等缺陷。
3. 零件的工艺分析1)定位套孔壁较薄,在各道工序加工时应注意选用合理的夹紧力,以防工件变形。
2)定位套内、外圆有同轴度要求,为保证加工精度,工艺安排应粗、精加工分开。
3)在精磨φ130045.0015.0++mm 时,同时靠磨φ136mm 右端面,以保证φ130045.0015.0++mm 右端面对其轴心线的垂直度公差0.03mm 。
4)密封件定位套零件结构特点和技术要求如下:内孔φ130和退刀槽端面粗糙度值较小为Ra1.6um 。
φ180﹑φ160与φ130的同轴度的要求为0.025,固定位要求高。
该零件的主要加工表面是内孔φ130﹑外圆φ180﹑φ165及退刀槽端面。
次要加工表面是其它外圆及径向孔加工。
5)该密封件定位套因为是铸件,采用先铸造出中心孔,以减少加工余量。
6)定位套螺纹孔宽,大径、小径尺寸及等分精度的检查,采用符合量规进行检查。
二、 工艺规程设计(一)确定毛坯的制造形式毛坯成形方法选择的合理与否直接影响到零件的质量、使用性能、成本和生产率;零件的材料选定以后,其毛坯成形方法也大致确定了。
机械零件毛坯选择的原则是既满足零件的使用要求,又使零件在制造过程中具有良好的工艺性和经济性,以利于降低成本和提高生产率。
零件材料为HT200。
密封件定位套零件的生产类型为大批量生产,考虑零件在机床运行过程中所受冲击不大,零件有多个通孔,零件结构又比较简单,生产类型为中等批量生产,故选择铸件毛坯。
(二)基面的选择基面选择是工艺规程设计中的重要工作之一。
基面选择的正确与合理,可以使加工质量得到保证,生产效率得以提高。
否则,加工工艺过程中会问题百出,更有甚者,还会造成大批报废,使生产无法正常进行。
1) 粗基准的选择:按有关基准的选择原则,即当零件有不加工表面时,应以这些不加工表面作粗基准;若零件有若干不加工表面时,则应以与加工表面要求相对位置精度高的不加工表面作粗基准。
对本零件而言,则应以φ260mm 的外圆为主要的定位粗基准。
2) 精基准的选择:考虑要保证零件的加工精度和装夹准确方便,依据“基准重合”原则和“基准统一”原则。
对本零件而言,φ16510.015.0--mm孔与φ130045.0015.0++mm 的孔、φ18010.015.0--mm 的孔与φ130045.0015.0++mm 的孔同轴度误差为0.025mm ,则应以φ130045.0015.0++mm 中心孔为精基准。
(三)制定工艺路线制订工艺路线的出发点,应当是使零件的几何形状、尺寸精度及位置精度等技术要求能达到合理的保证。
在生产纲领确定为大批量生产的情况下,可以考虑采用万能性机床配以专用工夹具,并尽量使工序集中来提高生产率。
除此之外,还应当考虑经济效果,以便降低生产成本。
1. 工艺路线方案一:工序1:备料,检查毛坯是否合格。
工序2:热处理,人工时效处理。
工序3:车左端面,车内径φ130孔深195mm工序4:深195mm处车内槽φ136mm×4mm工序5:车右端面到φ220mm,车法兰盘至壁厚20mm。
车外圆至φ180mm,车内孔至φ90mm。
车左边环槽。
工序6:车外圆至φ165mm,车右边环槽至图样尺寸。
工序7:车外圆至φ160mm至如图尺寸。
工序8:φ165孔外圆倒角1×45°工序9:钻孔:利用钻模定位,钻出3Xφ13和3XM8工序10:攻出3XM8的螺纹孔工序11:检验2.工艺路线方案二:工序1:备料,检查毛坯是否合格。
工序2:热处理,人工时效处理。
工序3:车左端面,粗车内径φ130孔深195mm工序4:深195mm处车内槽φ136mm×4mm工序5:车右端面到φ220mm,车法兰盘至壁厚20mm。
粗车外圆至φ180mm,车外圆至φ160mm、φ165mm。
工序6:车所有外圆环槽。
工序7:,粗磨内径φ130至图样尺寸,靠磨φ136mm端面,磨φ90至图样尺寸。
工序8:磨φ165外圆至图样尺寸,磨φ180外圆至图样尺寸工序9:钻孔:利用钻模定位,钻出3X φ13和3XM8工序10:攻出3XM8的螺纹孔工序11:检验3、工艺方案的比较与分析上述两种工艺方案的特点有:方案一工序太分散不利于提高加工精度及生产率,而且全部用车床加工孔,外圆表面,在精加工的时候会出现对车床精度要求过高,对工人技术要求高,精度难以保证。
方案二工序集中减少了装夹次数有利于提高加工精度及生产率,同时采用磨削加工重要表面,磨削能获得高的加工精度和小的表面粗糙度,对工人要求不高,效益好。
综上两种加工工艺,最终的加工路线确定如下:工序1:铸:铸件各部留加工余量7mm工序2:清砂工序3:热处理:人工时效处理工序4:夹工件右端外圆,照顾铸件壁厚均匀,车内径各部尺寸,留加工余量5mm ,车右端面,保证工件总长为226mm ,法兰盘壁厚23mm ,其余各部留余量5mm工序5:倒头,以内径定位装夹工件,法兰盘外圆找正,车外圆各部,留加工余量5mm工序6: 夹工件右端外圆,车内径至尺寸φ1308.06.0++mm ,深195mm 处车内槽φ136mm ×4mm ,车外端面,保证工件总长222mm ,车φ260mm 法兰盘厚度22mm工序7:倒头,以内径定位装夹工件,精车右端外圆各部尺寸,留磨量0.8mm (注φ160mm 不留加工余量),车端面保证工件总长220mm ,车内径φ905.02.0++mm 至尺寸φ9020.012.0++mm ,切各环槽至图样尺寸。
工序8:夹工件右端外圆,内径找正,粗磨内径至图样尺寸φ130045.0015.0++mm ,靠磨φ136mm 端面,磨φ905.02.0++mm工序9:以内径定位装夹工件,磨φ16510.015.0--mm 外圆,磨φ18010.015.0--mm 外圆至图样尺寸工序10:划φ175mm 中心圆上3×M8孔线,划φ222mm 中心圆上3×φ13mm 孔线工序11:钻3×φ13mm 孔,钻3×M8底孔φ6.7mm 、攻螺纹M8、深15mm工序12:桉图样检验各部尺寸和精度工序13:涂油入库(四)机械加工余量、工序尺寸及毛胚尺寸的确定“密封件定位套”零件材料为HT200,硬度为HB180~HB210。
生产类型为大批量生产可使用铸造模铸造毛胚。
根据以上原始资料及加工工艺,分别确定各加工表面的机械加工余量、工序尺寸及毛坯尺寸如下。
1.外圆表面(φ180mm 、φ160mm 、φ165mm 以及260mm )其加工长度为227mm ,与其连接的法兰盘外圆表面直径为φ260mm 。
表面粗糙度值要求为0.8,要求精加工,此时直径余量2Z=7mm 已能满足加工要求。
2.外圆表面沿轴线长度方向的加工余量及公差两端面的精度等级为IT10,所以,长度方向的加工余量查《机械制造工艺设计简明手册》,现取2mm。
3.内槽φ136х4, 此时的直径余量2Z=4mm4. 法兰盘φ260mm, 法兰盘的长度为20mm,留加工余量为2Z=7mm,采用切削加工。
5.环槽Ⅰ4xφ174mm, 参照《工艺手册》取直径余量2Z=6mm环槽Ⅱ4xφ159mm,参照《工艺手册》取直径余量2Z=6mm 由于本设计的零件为中等批量生产,应采用调整法加工,因此在计算最大、最小加工余量时,应按调整法加工方式予以确定。
(五)确定切削用量确定每一工步的切削用量------背吃刀量ap,进给量f及切削速度Vc。
确定方法是:先确定切削深度和进给量再确定切削速度,用《现代制造工艺设计方法》公式Vc=πdn/1000(m/min)查表或计算所得转速nc,根据nc在选择的机床的实有的主轴转速表中选取接近的主轴转速n作为所得的转速nc。
用公式Vc=πdn/1000(m/min)再换算出实际的切削速度Vc填入工艺文件中。
对粗加工,选取实际Vc,实际进给量f和背吃刀量ap之后,还要验证机床功率是否足够等,才能作为最后的切削用量填入工艺文件中。
(一)加工条件工件材料:HT200,最低抗拉强度为200MPa的灰铸铁加工要求粗车端面,粗车外圆、内径,精车外圆、内径,磨外圆、内径,钻孔。
机床为CA6140型车床,M1432A型外圆磨床,Z525型钻床。
工件装夹车床夹具上,专用夹具上。
(二)切削用量1.粗车右端面1)选取刀具:选择45°弯头外圆车刀,按《切削手册》表中选取刀杆尺寸为16X25,刀片厚度为4.5mm;选择车刀几何形状等2)确定切削用量:(a)确定背吃刀量ap 由于单边余量Z=1mm,可分1次走刀完成即ap=1mm。
(b)确定进给量f:根据《切削手册》,在加工材料HT200,车刀刀杆尺寸为16*25,ap≤1mm,工件直径为200以下时的f 范围,再按CA6140车床查得纵向进给量取:f=0.94mm/r(c)选择车刀磨钝标准及耐用度:根据《切削手册》取车刀后刀面磨损量为1mm,焊接车刀耐用度T=60min(d)确定切削速度Vc:根据《切削手册》当用硬质合金车刀加工HT200材料,ap≤3mm,f ≤0.94mm/r时,切削速度为Vc=460m/min。
由于实际车削过程使用条件的改变,根据《切削手册》切削速度的修正系数为Ktv=1,Kmv=1,ksv=0.8,ktv=0.65,kkv=1,kkrv=1故Vc=460*0.8*0.65*1*1*1*1=239m/minn=1000Vc/(πd)=422r/min根据CA6140车床,选择n=400r/min则实际的切削速度为:Vc=πnd/1000=π400*165/1000=207m/min最后确定的切削用量为:ap=asp=1mm,f=0.94mm/r,n=400r/mm,vc=207m/min2. 粗车φ180的外圆.1)选择刀具:与粗车端面同一把刀。
2)确定切削用量:(a)确定背吃刀量ap 由于单边余量Z=1mm,可分1次走刀完成即ap=1mm。
(b)确定进给量f:根据《切削手册》,在加工材料HT200,车刀刀杆尺寸为16*25,ap≤1mm,工件直径为200以下时的f 范围,再按CA6140车床查得纵向进给量取:f=0.94mm/r(c)选择车刀磨钝标准及耐用度:根据《切削手册》取车刀后刀面磨损量为1mm,焊接车刀耐用度T=60min(d)确定切削速度Vc:根据《切削手册》当用硬质合金车刀加工HT200材料,ap≤3mm,f≤0.94mm/r时,取切削速度为Vc=460m/min。