品质奖罚制度标准
食品品质奖罚管理制度

食品品质奖罚管理制度一、食品品质奖管理制度:1.食品品质奖的设置:政府可以根据食品行业的发展情况及消费者需求设立食品品质奖,以激励企业加强食品品质管理,鼓励科技创新,提高产品质量和安全水平。
2.评选标准:食品品质奖的评选标准应包括食品安全、品质控制、生产工艺、质量管理体系、市场反馈等方面。
评选委员会应设立评审专家组,对参评企业进行现场评审、抽检等工作,综合评价,最终确定获奖名单。
3.表彰方式:获奖企业可以通过授予荣誉证书、奖杯、奖金等形式进行表彰,同时可以通过宣传推广等方式提高企业知名度和市场竞争力。
4.奖励政策:政府可以制定奖励政策,对获奖企业给予补贴、减免税费等优惠政策,鼓励其持续改进产品质量,提升市场竞争力。
二、食品品质罚管理制度:1.食品品质罚的设定:对于违反食品安全法律法规、生产销售劣质产品、伪劣食品等行为,应依法进行处罚。
主要包括罚款、责令停产、吊销相关许可证等处罚措施。
2.罚款金额:对于生产销售劣质产品、伪劣食品等行为,应根据其违法行为的严重程度和食品安全风险程度,进行罚款处罚。
同时可以对违法企业进行限产、停产等处罚措施。
3.责令整改:一旦发现食品安全问题,相关监管部门应责令企业立即停产、召回产品、整改问题等措施,确保问题得到及时纠正,消费者权益得到保护。
4.通报曝光:对于严重违法企业和行为,应依法进行通报曝光,公开曝光其违法行为,对其进行警示和震慑,敦促其改正错误。
通过建立完善的食品品质奖罚管理制度,可有效引导企业自觉遵守法律法规,提高食品质量和安全水平,保障消费者健康权益,维护国家食品安全和社会和谐稳定。
同时,政府应加强监督检查,保证食品品质奖罚管理制度的有效实施,确保食品质量始终处于安全可控的水平。
供应商品质奖罚制度
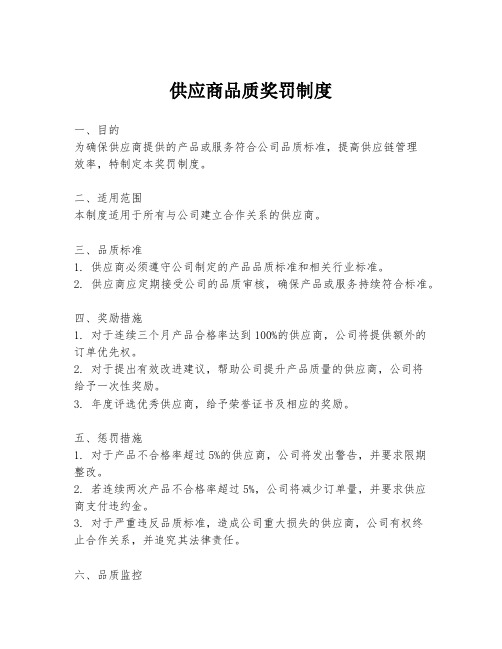
供应商品质奖罚制度一、目的为确保供应商提供的产品或服务符合公司品质标准,提高供应链管理效率,特制定本奖罚制度。
二、适用范围本制度适用于所有与公司建立合作关系的供应商。
三、品质标准1. 供应商必须遵守公司制定的产品品质标准和相关行业标准。
2. 供应商应定期接受公司的品质审核,确保产品或服务持续符合标准。
四、奖励措施1. 对于连续三个月产品合格率达到100%的供应商,公司将提供额外的订单优先权。
2. 对于提出有效改进建议,帮助公司提升产品质量的供应商,公司将给予一次性奖励。
3. 年度评选优秀供应商,给予荣誉证书及相应的奖励。
五、惩罚措施1. 对于产品不合格率超过5%的供应商,公司将发出警告,并要求限期整改。
2. 若连续两次产品不合格率超过5%,公司将减少订单量,并要求供应商支付违约金。
3. 对于严重违反品质标准,造成公司重大损失的供应商,公司有权终止合作关系,并追究其法律责任。
六、品质监控1. 公司将建立完善的品质监控体系,定期对供应商的产品进行抽检。
2. 供应商应配合公司的品质监控工作,提供必要的信息和资料。
七、申诉机制1. 供应商对品质评估结果有异议时,可在接到通知后7个工作日内提出书面申诉。
2. 公司将成立专门的申诉处理小组,对申诉进行公正、客观的调查和处理。
八、制度更新1. 本制度将根据市场变化和公司发展需要进行定期更新。
2. 任何制度的变更都将提前通知供应商,并在下一次合作中生效。
九、其他1. 本制度自发布之日起生效。
2. 本制度的最终解释权归公司所有。
请根据公司实际情况和法律要求,对上述内容进行适当调整和完善。
品质奖罚制度

品质奖罚制度一、目的为提升公司产品及服务质量,确保客户满意度,通过奖罚机制激励员工持续改进工作品质,特制定本制度。
二、适用范围本制度适用于公司全体员工。
三、奖励措施1. 品质卓越奖:对于在产品开发、生产、销售及服务过程中,显著提高产品质量或服务质量的团队或个人,给予一次性奖金。
2. 持续改进奖:鼓励员工提出改进建议,对于被采纳并实施的改进措施,根据成效给予奖励。
3. 零缺陷奖:对于连续一定周期内无品质事故的团队或个人,给予奖励。
四、惩罚措施1. 品质事故责任追究:对于因个人疏忽或违规操作导致的质量问题,根据事故严重程度,给予警告、罚款或记过处分。
2. 重复性错误惩罚:对于同一问题重复发生的品质错误,加倍处罚。
3. 重大品质事故:对于造成重大经济损失或严重损害公司声誉的品质事故,依法依规追究相关责任人的责任。
五、奖罚标准1. 奖励金额根据贡献大小和影响范围确定,具体标准由品质管理部门制定。
2. 惩罚措施的具体标准由品质管理部门根据事故性质和后果严重程度制定。
六、奖罚程序1. 由品质管理部门负责奖罚制度的执行和监督。
2. 对于奖励,由直接上级提名,品质管理部门审核,报公司管理层批准。
3. 对于惩罚,由品质管理部门调查事故原因,提出处理建议,报公司管理层批准。
七、申诉与复核员工对奖罚决定有异议时,可在接到通知后五个工作日内向品质管理部门提出书面申诉,由公司管理层组织复核。
八、附则1. 本制度自发布之日起生效,由品质管理部门负责解释。
2. 本制度如与国家法律法规相抵触,以国家法律法规为准。
3. 本制度由公司管理层负责修订和完善。
九、生效日期本制度自XXXX年XX月XX日起生效。
请根据公司实际情况调整上述内容,确保制度的适用性和有效性。
品质检验质量的奖罚制度
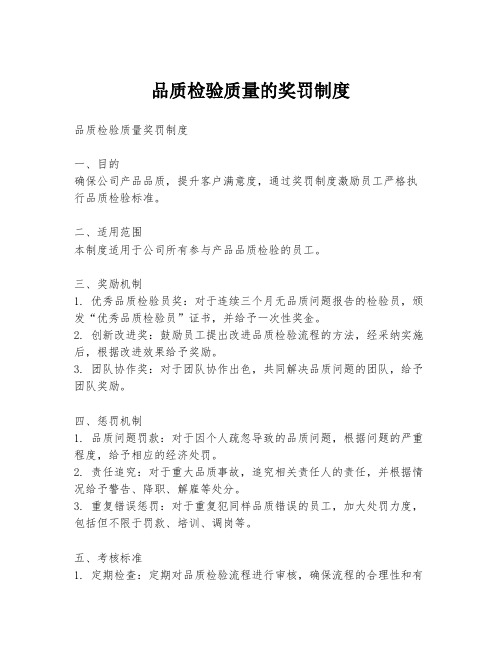
品质检验质量的奖罚制度品质检验质量奖罚制度一、目的确保公司产品品质,提升客户满意度,通过奖罚制度激励员工严格执行品质检验标准。
二、适用范围本制度适用于公司所有参与产品品质检验的员工。
三、奖励机制1. 优秀品质检验员奖:对于连续三个月无品质问题报告的检验员,颁发“优秀品质检验员”证书,并给予一次性奖金。
2. 创新改进奖:鼓励员工提出改进品质检验流程的方法,经采纳实施后,根据改进效果给予奖励。
3. 团队协作奖:对于团队协作出色,共同解决品质问题的团队,给予团队奖励。
四、惩罚机制1. 品质问题罚款:对于因个人疏忽导致的品质问题,根据问题的严重程度,给予相应的经济处罚。
2. 责任追究:对于重大品质事故,追究相关责任人的责任,并根据情况给予警告、降职、解雇等处分。
3. 重复错误惩罚:对于重复犯同样品质错误的员工,加大处罚力度,包括但不限于罚款、培训、调岗等。
五、考核标准1. 定期检查:定期对品质检验流程进行审核,确保流程的合理性和有效性。
2. 问题记录:对所有品质问题进行记录,作为奖罚的依据。
3. 员工反馈:鼓励员工对品质检验流程提出建议和反馈。
六、实施细则1. 奖罚决策:由品质管理部门负责奖罚的决策和执行。
2. 公正透明:奖罚过程必须公正、透明,接受全体员工监督。
3. 持续改进:根据奖罚制度的实施效果,不断优化和调整奖罚标准。
七、附则1. 制度更新:本制度自发布之日起生效,如有更新,将及时通知全体员工。
2. 解释权:本制度的最终解释权归公司所有。
八、生效日期本奖罚制度自XXXX年XX月XX日起生效。
注:具体奖金数额、罚款标准、责任追究的具体措施等,需根据公司实际情况制定。
品质部员工绩效奖罚制度

品质部员工绩效奖罚制度一、绩效奖励制度1. 月度绩效奖励- 根据员工当月的工作表现,包括但不限于质量控制、问题解决能力、团队合作等,评选出优秀员工,给予奖金奖励。
- 绩效评级为A的员工,可获得基本工资的10%作为奖金。
2. 季度绩效奖励- 每季度根据员工的综合表现,评选出季度之星,给予额外奖励。
- 季度之星可获得基本工资的20%作为奖金。
3. 年度绩效奖励- 年度绩效考核中,表现突出的员工将获得年终奖金。
- 根据年度绩效评级,A级员工可获得基本工资的30%作为年终奖金。
4. 特殊贡献奖- 对于在品质控制、流程改进、客户满意度提升等方面做出显著贡献的员工,给予一次性特殊贡献奖励。
- 奖励金额根据贡献大小和影响程度确定。
二、绩效惩罚制度1. 工作失误处罚- 因个人疏忽导致产品质量问题,根据问题的严重程度,给予警告或罚款。
- 轻微失误,给予口头警告;严重失误,根据损失程度,罚款金额为基本工资的5%至10%。
2. 工作态度问题处罚- 工作态度不端正,如迟到、早退、旷工等,根据违规次数和严重程度,给予相应的处罚。
- 首次违规,给予书面警告;再次违规,罚款金额为基本工资的5%。
3. 违反公司规定处罚- 违反公司规定,如泄露公司机密、不遵守安全操作规程等,根据违规行为的严重性,给予相应的处罚。
- 轻微违规,给予书面警告;严重违规,罚款金额为基本工资的10%至20%,并可能面临解雇。
三、绩效考核标准1. 质量控制- 产品合格率、返工率、客户投诉率等作为考核指标。
2. 问题解决能力- 问题发现的及时性、解决方案的有效性、问题解决的效率等。
3. 团队合作- 团队协作精神、沟通能力、对团队目标的贡献等。
4. 创新能力- 工作流程的创新、改进建议的实施效果等。
四、绩效考核流程1. 月度考核- 每月末由直接上级根据员工当月表现进行初步评价。
2. 季度考核- 每季度末由部门负责人对员工进行综合评价。
3. 年度考核- 年末由人力资源部组织,对员工全年表现进行综合评价。
品质部门内部奖罚制度

品质部门内部奖罚制度一、奖励制度1. 质量贡献奖:对于提出有效改进措施,显著提升产品质量的员工,给予一次性奖金。
2. 创新提案奖:鼓励员工提出创新提案,一旦被采纳并实施,根据提案的效益给予奖励。
3. 月度优秀员工:每月评选表现突出的员工,给予物质奖励和荣誉证书。
4. 年度最佳团队:根据团队全年的绩效和贡献,评选最佳团队,给予团队奖金和表彰。
5. 持续改进奖:对于持续提出改进意见并被采纳的员工,给予额外奖励。
二、惩罚制度1. 质量事故责任制:发生质量问题时,根据责任大小,对相关人员进行罚款或降级处理。
2. 工作失误惩罚:对于因个人疏忽导致的工作失误,根据失误的严重程度,给予相应的经济处罚或警告。
3. 违反操作规程:对于不遵守操作规程,导致产品质量问题或生产事故的员工,给予警告或罚款。
4. 工作态度不端:对于工作态度消极、影响团队协作的员工,给予口头警告,情节严重的进行罚款或调岗。
5. 绩效考核不达标:对于连续多次绩效考核不达标的员工,进行岗位培训或岗位调整,仍无改善者,进行降职或解聘。
三、奖罚执行1. 奖罚标准:制定明确的奖罚标准,确保公平公正。
2. 奖罚程序:设立奖罚程序,由品质部门负责人或指定人员执行。
3. 奖罚记录:所有奖罚记录应详细记录,作为员工绩效考核的依据。
4. 申诉机制:员工对奖罚有异议时,可提出申诉,由品质部门负责人或人力资源部门复核。
四、奖罚公示1. 奖罚结果应定期在公司内部公示,以示透明。
2. 公示内容包括获奖或受罚的原因、标准和结果。
五、奖罚制度的更新1. 奖罚制度应根据公司发展和市场变化定期进行评估和更新。
2. 更新后的奖罚制度需经过品质部门和人力资源部门的审核,并得到公司高层的批准。
六、奖罚制度的培训1. 新员工入职时,应接受奖罚制度的培训。
2. 定期对全体员工进行奖罚制度的培训,确保制度的执行。
通过上述奖罚制度的实施,旨在激励员工提高工作质量,增强团队协作,同时对违反规定的行为进行约束,以确保品质部门工作的高效和产品质量的稳定。
品质检验人员奖罚管理制度

品质检验人员奖罚管理制度
一、目的
确保产品质量符合公司标准和客户需求,通过奖罚制度激励品质检验人员提升工作积极性和责任心。
二、适用范围
本制度适用于公司所有从事品质检验工作的员工。
三、奖励机制
1. 月度品质检验优秀员工奖:对当月工作表现突出,发现重大质量问题并及时上报的员工给予奖励。
2. 年度品质贡献奖:对全年工作表现优异,对提升产品质量有显著贡献的员工给予年度奖励。
3. 创新改进奖:鼓励员工提出改进检验流程、方法或工具的建议,对被采纳并实施的建议给予奖励。
四、惩罚机制
1. 错误报告惩罚:对因疏忽大意导致错误报告的员工,根据错误严重性给予警告或经济处罚。
2. 质量问题隐瞒惩罚:对故意隐瞒质量问题,不按规定上报的员工,给予严厉处罚,包括但不限于罚款、降级或解雇。
3. 工作失职惩罚:对因个人原因导致检验工作失误,影响产品质量的员工,根据失误程度给予相应的处罚。
五、考核标准
1. 检验准确性:检验结果与实际产品质量的一致性。
2. 报告及时性:发现问题后,报告的及时性。
3. 工作态度:工作认真负责,遵守公司规章制度。
4. 团队协作:与团队成员协作,共同提升工作效果。
六、奖罚执行
1. 奖罚决定由品质管理部门提出,经人力资源部门审核后执行。
2. 奖罚结果应公开透明,确保公平公正。
七、申诉机制
员工对奖罚决定有异议时,可向人力资源部门提出申诉,由公司管理层组织复审。
八、制度修订
本制度由品质管理部门负责修订,每年至少审查一次,确保制度的时效性和适应性。
九、附则
本制度自发布之日起生效,由公司管理层负责解释。
制衣厂品质奖罚制度

制衣厂品质奖罚制度一、品质奖励制度:1. 品质优秀员工奖励:- 月度品质标兵:对连续三个月无品质问题,且工作表现突出的员工,给予奖金奖励。
- 年度品质之星:对全年无品质问题,且在品质管理方面有显著贡献的员工,给予年终奖金。
2. 品质改进提案奖励:- 对提出有效品质改进措施,并被采纳实施的员工,根据改进效果给予一次性奖励。
3. 团队品质奖励:- 对于团队整体品质表现优异,连续三个月品质合格率达到98%以上的部门,给予团队奖励。
二、品质惩罚制度:1. 品质问题处罚:- 轻微品质问题:对导致轻微品质问题的员工,给予口头警告,并要求立即改正。
- 严重品质问题:对导致严重品质问题的员工,根据问题的严重程度,给予罚款或降职处理。
2. 重复品质问题处罚:- 对于同一员工在一个月内出现两次及以上相同品质问题的,除罚款外,还将进行岗位培训。
3. 重大品质事故处罚:- 对于造成重大品质事故,给公司带来严重损失的员工,将根据事故严重程度,给予解除劳动合同等处罚。
三、品质监督制度:1. 品质监督小组:- 成立由管理层和员工代表组成的品质监督小组,负责监督品质奖罚制度的执行。
2. 定期品质检查:- 定期对生产线进行品质检查,确保员工遵守品质标准。
3. 品质问题追踪:- 对发现的品质问题进行追踪,确保问题得到及时解决,并防止问题再次发生。
四、品质培训制度:1. 新员工品质培训:- 对新入职员工进行品质意识和操作规范的培训。
2. 定期品质培训:- 定期对全体员工进行品质标准和操作技能的培训。
3. 品质改进培训:- 对于品质问题频发的部门,组织专项品质改进培训。
五、品质反馈机制:1. 员工反馈:- 鼓励员工对品质问题提出反馈,并对积极反馈的员工给予奖励。
2. 管理层反馈:- 管理层需定期收集员工对品质制度的意见和建议,不断优化制度。
3. 客户反馈:- 重视客户对产品品质的反馈,及时调整生产流程和品质标准。
通过上述奖罚制度,旨在提高员工的品质意识,确保制衣厂产品的品质稳定,提升客户满意度,同时激励员工积极参与品质管理,共同推动企业持续发展。
品质部品质奖罚制度

品质部品质奖罚制度一、目的为了提升公司产品品质,确保客户满意度,通过奖罚机制激励员工积极参与品质管理和改进活动。
二、适用范围本制度适用于公司品质部全体员工。
三、奖励机制1. 品质贡献奖:对于提出有效改进措施,显著提升产品质量的员工,给予一次性奖励。
2. 零缺陷奖:连续三个月无品质事故的团队或个人,给予奖金及表彰。
3. 创新奖:鼓励员工进行工艺创新,对于成功实施并带来显著效益的创新项目,给予奖励。
4. 优秀团队奖:每季度评选出表现最优秀的品质管理团队,给予团队奖励。
四、惩罚机制1. 品质事故罚款:对于因个人疏忽导致的质量问题,根据事故严重程度进行罚款。
2. 重复错误惩罚:对于重复出现相同错误的员工,除罚款外,还需进行额外培训。
3. 严重违规解雇:对于严重违反操作规程,造成重大品质事故的员工,将予以解雇。
五、奖罚标准1. 奖励金额根据贡献大小和效益提升比例确定。
2. 罚款金额根据事故造成的损失和影响范围确定。
六、奖罚程序1. 由品质部经理提出奖罚建议。
2. 奖罚决定需经部门会议讨论通过。
3. 奖罚结果需向全体员工公示。
七、申诉机制员工对奖罚决定有异议时,可在决定公布后5个工作日内向人力资源部提出申诉。
八、附则1. 本制度自发布之日起生效,由品质部负责解释。
2. 对于本制度未尽事宜,按照公司相关规章制度执行。
九、修订记录1. 制度发布日期:XXXX年XX月XX日2. 最后修订日期:XXXX年XX月XX日请根据公司实际情况和法律法规要求,对上述内容进行适当调整和完善。
品质奖惩管理制度

品质奖惩管理制度•相关推荐品质奖惩管理制度(通用10篇)随着社会一步步向前发展,接触到制度的地方越来越多,制度是各种行政法规、章程、制度、公约的总称。
那么相关的制度到底是怎么制定的呢?下面是小编为大家整理的品质奖惩管理制度,仅供参考,希望能够帮助到大家。
品质奖惩管理制度篇11、总则1.1为了加强对产品质量的监督管理,提高产品质量,明确质量责任,维护企业和员工利益,特制定本规定。
1.2本公司员工依照本规定承担产品工作质量责任。
1.3本公司鼓励员工钻研业务知识,不断提高岗位技能,对在质量方面做出成绩的部门或个人给予奖励。
1.4本公司不允许不注重质量的现象和行为存在,对因此而造成质量事故者将给予处罚。
1.5本规定适用于本公司所有部门的工作(生产)场所的所有人员。
2、质量事故的定性范围及类别2.1质量事故的定性范围,下列行为/现象均属于质量事故:2.1.1违反工艺和操作规程,造成重大后果的;2.1.2违反标准/合同规定,编制工艺造成严重后果的;2.1.3因错检、漏检,致使不合格原材料进厂或不合格产品出厂,造成经济损失的;2.1.4生产工序间没有按规定进行三检(专检、互检、自检)而出现质量问题,造成损失的;2.1.5因物资/产品保管不善,造成报废/降级/返工/退货的;2.1.6因错发产品/材料,对销售/生产产生影响的;2.1.7因运输维护不当,造成产品/材料受损,而延误交付/生产的;2.1.8因核算失误,下错生产通知单,而造成物资/产品积压的;2.1.9不具备上岗条件,擅自开动生产设备的;2.1.10生产现场物品未按规定摆放,造成标识混乱/不全,致使错用的;2.1.11生产记录填写不规范,影响产品质量/不符合程序文件规定的;2.1.12各类统计报表,台帐和原始记录不真实、不完整的;2.1.13纠正措施没有按期整改的;2.1.14一次交验合格率没有达到规定要求的。
2.2质量事故的类别质量事故按造成损失的大小和对本公司声誉影响的不同程度划分为:重大质量事故;严重质量事故;一般质量事故。
品质部奖罚管理制度
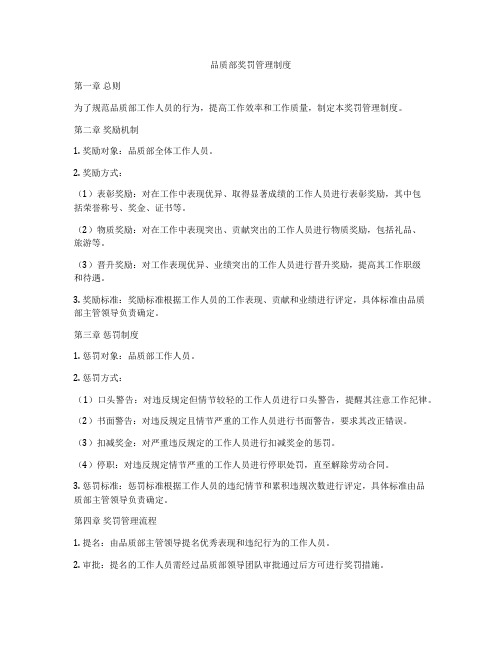
品质部奖罚管理制度第一章总则为了规范品质部工作人员的行为,提高工作效率和工作质量,制定本奖罚管理制度。
第二章奖励机制1. 奖励对象:品质部全体工作人员。
2. 奖励方式:(1)表彰奖励:对在工作中表现优异、取得显著成绩的工作人员进行表彰奖励,其中包括荣誉称号、奖金、证书等。
(2)物质奖励:对在工作中表现突出、贡献突出的工作人员进行物质奖励,包括礼品、旅游等。
(3)晋升奖励:对工作表现优异、业绩突出的工作人员进行晋升奖励,提高其工作职级和待遇。
3. 奖励标准:奖励标准根据工作人员的工作表现、贡献和业绩进行评定,具体标准由品质部主管领导负责确定。
第三章惩罚制度1. 惩罚对象:品质部工作人员。
2. 惩罚方式:(1)口头警告:对违反规定但情节较轻的工作人员进行口头警告,提醒其注意工作纪律。
(2)书面警告:对违反规定且情节严重的工作人员进行书面警告,要求其改正错误。
(3)扣减奖金:对严重违反规定的工作人员进行扣减奖金的惩罚。
(4)停职:对违反规定情节严重的工作人员进行停职处罚,直至解除劳动合同。
3. 惩罚标准:惩罚标准根据工作人员的违纪情节和累积违规次数进行评定,具体标准由品质部主管领导负责确定。
第四章奖罚管理流程1. 提名:由品质部主管领导提名优秀表现和违纪行为的工作人员。
2. 审批:提名的工作人员需经过品质部领导团队审批通过后方可进行奖罚措施。
3. 公示:经过审批通过的奖励和惩罚决定将在全体员工面前公示。
4. 执行:根据审批通过的奖罚决定,品质部将执行相应的奖罚措施。
第五章监督机制1. 本奖罚管理制度由品质部全体工作人员遵守,不得有人擅自修改或违反规定。
2. 品质部主管领导需负责监督奖罚执行情况,发现问题及时处理。
3. 对于严重违纪的工作人员,品质部主管领导有权提出严厉处罚意见。
第六章附则1. 本奖罚管理制度自颁布之日起执行,如有不当之处,可根据实际情况进行调整。
2. 工作人员对于奖罚决定有异议时,可向品质部主管领导提出申诉,品质部主管领导将进行再审定。
品质奖罚制度规定
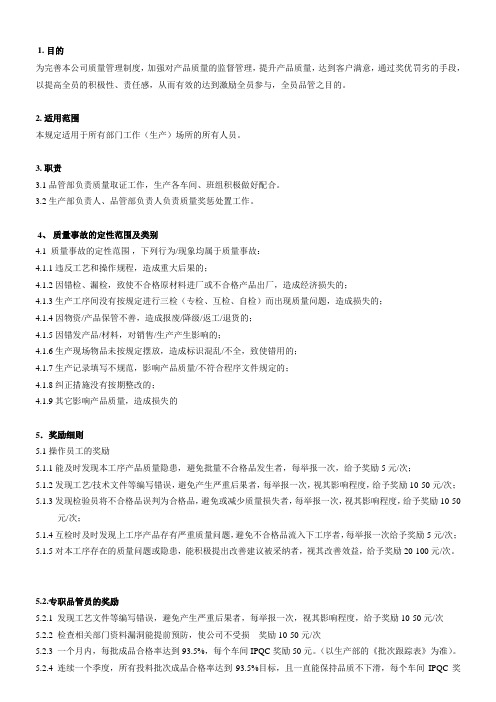
1. 目的为完善本公司质量管理制度,加强对产品质量的监督管理,提升产品质量,达到客户满意,通过奖优罚劣的手段,以提高全员的积极性、责任感,从而有效的达到激励全员参与,全员品管之目的。
2. 适用范围本规定适用于所有部门工作(生产)场所的所有人员。
3. 职责3.1品管部负责质量取证工作,生产各车间、班组积极做好配合。
3.2生产部负责人、品管部负责人负责质量奖惩处置工作。
4、质量事故的定性范围及类别4.1 质量事故的定性范围,下列行为/现象均属于质量事故:4.1.1违反工艺和操作规程,造成重大后果的;4.1.2 因错检、漏检,致使不合格原材料进厂或不合格产品出厂,造成经济损失的;4.1.3 生产工序间没有按规定进行三检(专检、互检、自检)而出现质量问题,造成损失的;4.1.4 因物资/产品保管不善,造成报废/降级/返工/退货的;4.1.5 因错发产品/材料,对销售/生产产生影响的;4.1.6生产现场物品未按规定摆放,造成标识混乱/不全,致使错用的;4.1.7生产记录填写不规范,影响产品质量/不符合程序文件规定的;4.1.8 纠正措施没有按期整改的;4.1.9 其它影响产品质量,造成损失的5.奖励细则5.1操作员工的奖励5.1.1能及时发现本工序产品质量隐患,避免批量不合格品发生者,每举报一次,给予奖励5元/次;5.1.2发现工艺/技术文件等编写错误,避免产生严重后果者,每举报一次,视其影响程度,给予奖励10-50元/次;5.1.3发现检验员将不合格品误判为合格品,避免或减少质量损失者,每举报一次,视其影响程度,给予奖励10-50元/次;5.1.4互检时及时发现上工序产品存有严重质量问题,避免不合格品流入下工序者,每举报一次给予奖励5元/次;5.1.5对本工序存在的质量问题或隐患,能积极提出改善建议被采纳者,视其改善效益,给予奖励20-100元/次。
5.2.专职品管员的奖励5.2.1 发现工艺文件等编写错误,避免产生严重后果者,每举报一次,视其影响程度,给予奖励10-50元/次5.2.2 检查相关部门资料漏洞能提前预防,使公司不受损奖励10-50元/次5.2.3 一个月内,每批成品合格率达到93.5%,每个车间IPQC奖励50元。
服装品质奖罚制度

服装品质奖罚制度一、目的为了提升公司服装产品的质量,确保消费者满意度,同时激发员工的工作积极性和责任感,特制定本奖罚制度。
二、适用范围本制度适用于公司所有参与服装生产、质检、物流等环节的员工。
三、奖励机制1. 品质优秀奖:对于在服装品质控制中表现突出的团队或个人,根据其贡献程度,给予现金奖励或职位晋升机会。
2. 创新改进奖:鼓励员工提出改进服装品质的创新建议,一经采纳并实施有效,给予相应的奖励。
3. 无差错奖:对于连续一定周期内无品质问题发生的团队或个人,给予奖金或荣誉证书。
四、惩罚机制1. 品质问题惩罚:对于因个人疏忽导致服装品质问题,根据问题的严重程度,给予警告、罚款或降职处理。
2. 重复错误惩罚:对于重复出现相同品质错误的员工,加重惩罚力度,包括但不限于罚款、停职或解雇。
3. 隐瞒问题惩罚:对于隐瞒品质问题不报的行为,一经查实,将给予严厉的纪律处分。
五、奖罚标准1. 奖励标准:根据员工在品质控制、创新改进等方面的具体表现,由质量管理部和人力资源部共同评定。
2. 惩罚标准:依据品质问题的严重性、发生频率以及对公司造成的损失,由质量管理部和人力资源部共同确定。
六、奖罚程序1. 提名:由直接上级或同事提名,提交相关证明材料。
2. 审核:由质量管理部和人力资源部进行审核,确保奖罚公平、公正。
3. 决定:审核通过后,由公司管理层做出最终奖罚决定。
4. 通知:奖罚决定将以书面形式通知相关人员,并在公司内部进行公示。
七、申诉机制员工对奖罚决定有异议时,可在接到通知后5个工作日内向人力资源部提出申诉,公司将组织相关部门进行复审。
八、附则1. 本制度自发布之日起生效,由质量管理部负责解释。
2. 本制度如与国家法律法规冲突,以法律法规为准。
3. 本制度定期进行评审和更新,以适应公司发展和市场变化的需要。
九、生效日期本奖罚制度自XXXX年XX月XX日起生效。
品质管理奖惩制度 (共5篇)
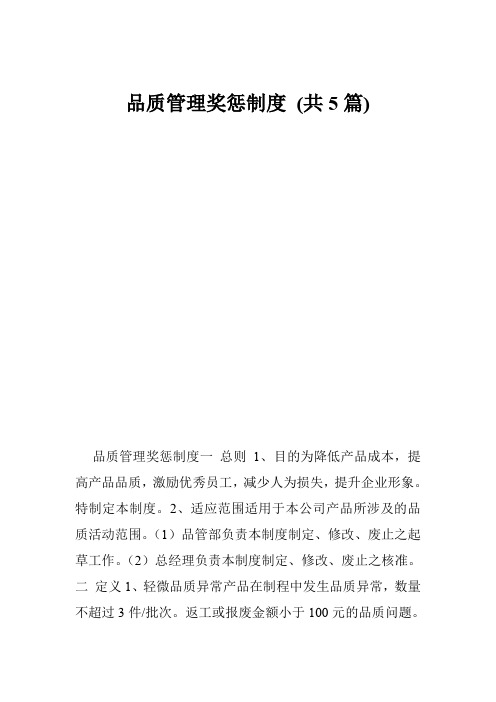
品质管理奖惩制度(共5篇)品质管理奖惩制度一总则1、目的为降低产品成本,提高产品品质,激励优秀员工,减少人为损失,提升企业形象。
特制定本制度。
2、适应范围适用于本公司产品所涉及的品质活动范围。
(1)品管部负责本制度制定、修改、废止之起草工作。
(2)总经理负责本制度制定、修改、废止之核准。
二定义1、轻微品质异常产品在制程中发生品质异常,数量不超过3件/批次。
返工或报废金额小于100元的品质问题。
2、一般品质异常(返工数量大于3件小于5件/批次;损失金额大于100元、小于1000元)。
或出厂后3、重大品质事故(1)被客户严重警告或罚款。
(2)退货或返修(数量大于3件/批次)。
(3)产品报废(报废金额大于5000元)。
(4)违规操作造成设备损坏延误交期。
4、特大品质事故(1)因品质问题而被客户取消供应商资格。
僅发现不良被客户让步接收,未造成返工或退货的品质问题。
限指产品未出厂,下工序发现上工序造成返工或报废的品质问题;不良率大于20%,內部使用3、权责单位三责任划分1、各生产小组必须对所加工、装配、自检的产品品质负责。
2、品管部应对经检验(来料检验、制程检验、成品检验、出货调试检验)后的产品品质负责。
3、工程技术、研发人员应对设计图纸、工艺的准确性,产品设计的稳定性,工程技术改善的有效性负责。
4、仓库人员应对仓储的物料保存品质负责。
5、制造总监负有对制造产品品质的自主监督权,部门负责人负有自主品质监督责任。
6、送检人应确认产品为自检合格品后,方可送品管部检验,若品管部抽检不合格,送的产品,后工序或客户发现不良,且不良率高于10%,品管部承担80%责任。
其上级部门承担20%责任。
7、若责任暂时无法划分,经品管部调查后开品质会讨论并报总经理裁决。
四品质指标1、来料:一次送检合格率>95%(每月)2、制程:一次送检合格率>97%(每月)3、成品:一次送检合格率>98% (每月)3、出货:一次送检合格率>98%(每月)4、一般客户投诉(外观投诉)≤5%(每月)重大客户投诉(功能投诉)≤1%(每月)客户投诉次数≤1次(每月)五处罚条例1、流程异常处罚细则:(1)多次送检不合格(连续三次,每次3个轻微不合格点以上者),生产人员应负有不自检或自检不到位责任,处罚20元。
生产部品质奖罚制度
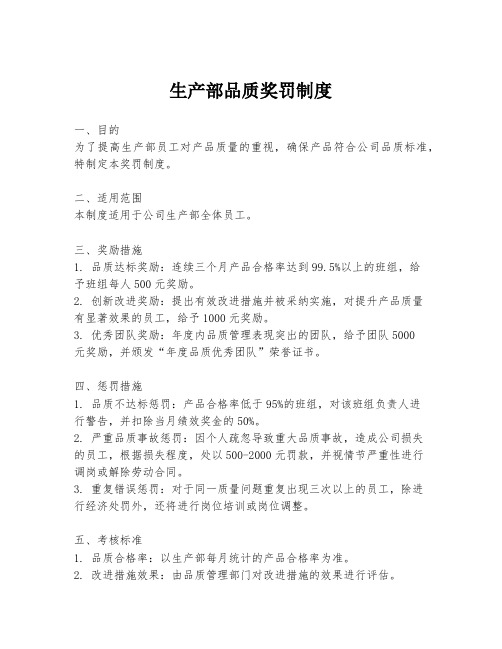
生产部品质奖罚制度一、目的为了提高生产部员工对产品质量的重视,确保产品符合公司品质标准,特制定本奖罚制度。
二、适用范围本制度适用于公司生产部全体员工。
三、奖励措施1. 品质达标奖励:连续三个月产品合格率达到99.5%以上的班组,给予班组每人500元奖励。
2. 创新改进奖励:提出有效改进措施并被采纳实施,对提升产品质量有显著效果的员工,给予1000元奖励。
3. 优秀团队奖励:年度内品质管理表现突出的团队,给予团队5000元奖励,并颁发“年度品质优秀团队”荣誉证书。
四、惩罚措施1. 品质不达标惩罚:产品合格率低于95%的班组,对该班组负责人进行警告,并扣除当月绩效奖金的50%。
2. 严重品质事故惩罚:因个人疏忽导致重大品质事故,造成公司损失的员工,根据损失程度,处以500-2000元罚款,并视情节严重性进行调岗或解除劳动合同。
3. 重复错误惩罚:对于同一质量问题重复出现三次以上的员工,除进行经济处罚外,还将进行岗位培训或岗位调整。
五、考核标准1. 品质合格率:以生产部每月统计的产品合格率为准。
2. 改进措施效果:由品质管理部门对改进措施的效果进行评估。
3. 团队表现:由生产部管理层根据团队整体表现进行评定。
六、奖罚执行1. 奖励发放:由人力资源部根据奖罚制度规定,每季度对符合条件的员工或团队进行奖励发放。
2. 惩罚执行:由生产部管理层根据奖罚制度规定,对违规员工进行处罚,并记录在员工个人档案中。
七、制度修订本制度自发布之日起执行,如有需要,由生产部和人力资源部共同提出修订意见,经公司管理层审批后实施。
八、附则本制度最终解释权归公司所有。
所有员工必须遵守本制度,如有异议,可通过正当途径向人力资源部反映。
九、生效日期本制度自XXXX年XX月XX日起生效。
请根据公司实际情况调整上述内容,以确保制度的适用性和有效性。
车间员工品质奖罚规章制度
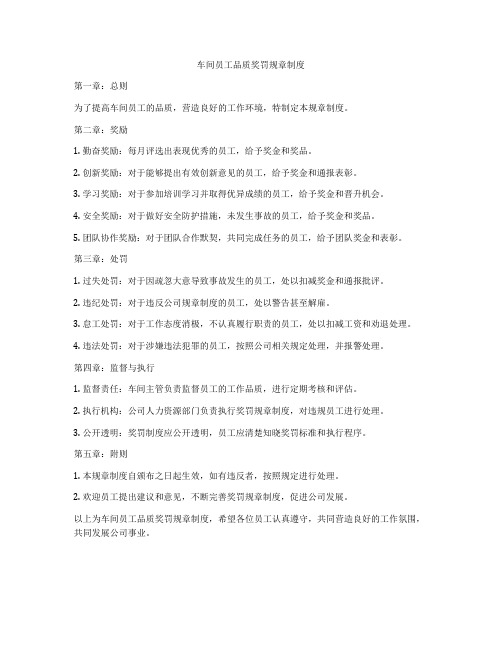
车间员工品质奖罚规章制度
第一章:总则
为了提高车间员工的品质,营造良好的工作环境,特制定本规章制度。
第二章:奖励
1. 勤奋奖励:每月评选出表现优秀的员工,给予奖金和奖品。
2. 创新奖励:对于能够提出有效创新意见的员工,给予奖金和通报表彰。
3. 学习奖励:对于参加培训学习并取得优异成绩的员工,给予奖金和晋升机会。
4. 安全奖励:对于做好安全防护措施,未发生事故的员工,给予奖金和奖品。
5. 团队协作奖励:对于团队合作默契,共同完成任务的员工,给予团队奖金和表彰。
第三章:处罚
1. 过失处罚:对于因疏忽大意导致事故发生的员工,处以扣减奖金和通报批评。
2. 违纪处罚:对于违反公司规章制度的员工,处以警告甚至解雇。
3. 怠工处罚:对于工作态度消极,不认真履行职责的员工,处以扣减工资和劝退处理。
4. 违法处罚:对于涉嫌违法犯罪的员工,按照公司相关规定处理,并报警处理。
第四章:监督与执行
1. 监督责任:车间主管负责监督员工的工作品质,进行定期考核和评估。
2. 执行机构:公司人力资源部门负责执行奖罚规章制度,对违规员工进行处理。
3. 公开透明:奖罚制度应公开透明,员工应清楚知晓奖罚标准和执行程序。
第五章:附则
1. 本规章制度自颁布之日起生效,如有违反者,按照规定进行处理。
2. 欢迎员工提出建议和意见,不断完善奖罚规章制度,促进公司发展。
以上为车间员工品质奖罚规章制度,希望各位员工认真遵守,共同营造良好的工作氛围,共同发展公司事业。
品质部的奖罚制度
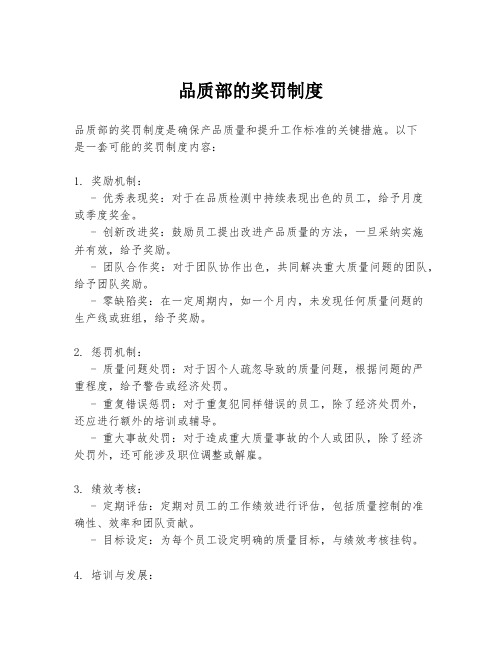
品质部的奖罚制度品质部的奖罚制度是确保产品质量和提升工作标准的关键措施。
以下是一套可能的奖罚制度内容:1. 奖励机制:- 优秀表现奖:对于在品质检测中持续表现出色的员工,给予月度或季度奖金。
- 创新改进奖:鼓励员工提出改进产品质量的方法,一旦采纳实施并有效,给予奖励。
- 团队合作奖:对于团队协作出色,共同解决重大质量问题的团队,给予团队奖励。
- 零缺陷奖:在一定周期内,如一个月内,未发现任何质量问题的生产线或班组,给予奖励。
2. 惩罚机制:- 质量问题处罚:对于因个人疏忽导致的质量问题,根据问题的严重程度,给予警告或经济处罚。
- 重复错误惩罚:对于重复犯同样错误的员工,除了经济处罚外,还应进行额外的培训或辅导。
- 重大事故处罚:对于造成重大质量事故的个人或团队,除了经济处罚外,还可能涉及职位调整或解雇。
3. 绩效考核:- 定期评估:定期对员工的工作绩效进行评估,包括质量控制的准确性、效率和团队贡献。
- 目标设定:为每个员工设定明确的质量目标,与绩效考核挂钩。
4. 培训与发展:- 技能提升:为员工提供定期的质量控制和相关技能培训,以提升整体工作水平。
- 职业发展:表现优秀的员工将获得更多的职业发展机会,包括晋升和转岗。
5. 透明度与公正性:- 公开透明:确保奖罚制度的公开透明,让所有员工都清楚奖罚标准和流程。
- 公正执行:奖罚决策应基于事实和数据,避免任何形式的偏见和不公。
6. 反馈与申诉:- 反馈机制:建立一个反馈机制,让员工可以对奖罚决策提出疑问或申诉。
- 申诉处理:设立一个公正的申诉处理流程,确保员工的疑虑得到妥善解决。
7. 持续改进:- 定期审查:定期审查奖罚制度的有效性,并根据公司发展和市场变化进行调整。
- 员工参与:鼓励员工参与到奖罚制度的改进过程中,以确保制度的适应性和公平性。
这套制度旨在通过正面激励和必要的惩罚措施,提升品质部门的整体工作效率和产品质量,同时确保制度的公正性和透明性。
品质客诉奖罚制度模板
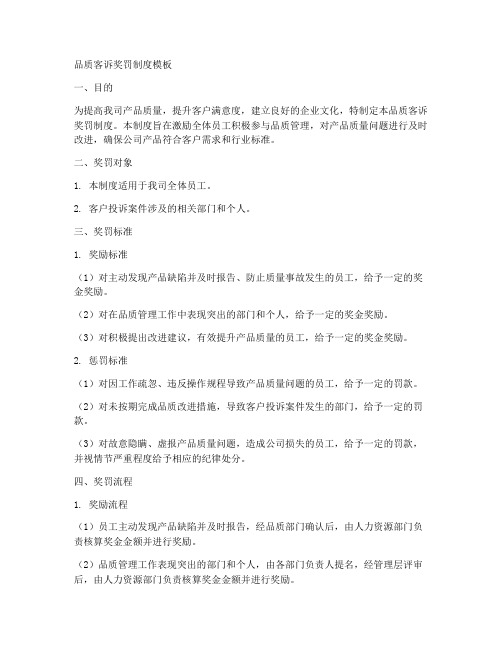
品质客诉奖罚制度模板一、目的为提高我司产品质量,提升客户满意度,建立良好的企业文化,特制定本品质客诉奖罚制度。
本制度旨在激励全体员工积极参与品质管理,对产品质量问题进行及时改进,确保公司产品符合客户需求和行业标准。
二、奖罚对象1. 本制度适用于我司全体员工。
2. 客户投诉案件涉及的相关部门和个人。
三、奖罚标准1. 奖励标准(1)对主动发现产品缺陷并及时报告、防止质量事故发生的员工,给予一定的奖金奖励。
(2)对在品质管理工作中表现突出的部门和个人,给予一定的奖金奖励。
(3)对积极提出改进建议,有效提升产品质量的员工,给予一定的奖金奖励。
2. 惩罚标准(1)对因工作疏忽、违反操作规程导致产品质量问题的员工,给予一定的罚款。
(2)对未按期完成品质改进措施,导致客户投诉案件发生的部门,给予一定的罚款。
(3)对故意隐瞒、虚报产品质量问题,造成公司损失的员工,给予一定的罚款,并视情节严重程度给予相应的纪律处分。
四、奖罚流程1. 奖励流程(1)员工主动发现产品缺陷并及时报告,经品质部门确认后,由人力资源部门负责核算奖金金额并进行奖励。
(2)品质管理工作表现突出的部门和个人,由各部门负责人提名,经管理层评审后,由人力资源部门负责核算奖金金额并进行奖励。
(3)提出改进建议,有效提升产品质量的员工,由品质部门负责人提名,经管理层评审后,由人力资源部门负责核算奖金金额并进行奖励。
2. 惩罚流程(1)因工作疏忽、违反操作规程导致产品质量问题的员工,由品质部门进行调查核实,报请管理层批准后,由人力资源部门负责执行罚款。
(2)未按期完成品质改进措施,导致客户投诉案件发生的部门,由品质部门进行调查核实,报请管理层批准后,由财务部门负责执行罚款。
(3)故意隐瞒、虚报产品质量问题,造成公司损失的员工,由品质部门进行调查核实,报请管理层批准后,由人力资源部门负责执行罚款,并视情节严重程度给予相应的纪律处分。
五、奖罚制度的执行与监督1. 本制度由品质部门负责解释和执行,各部门应积极配合。
服装车间奖罚制度品质
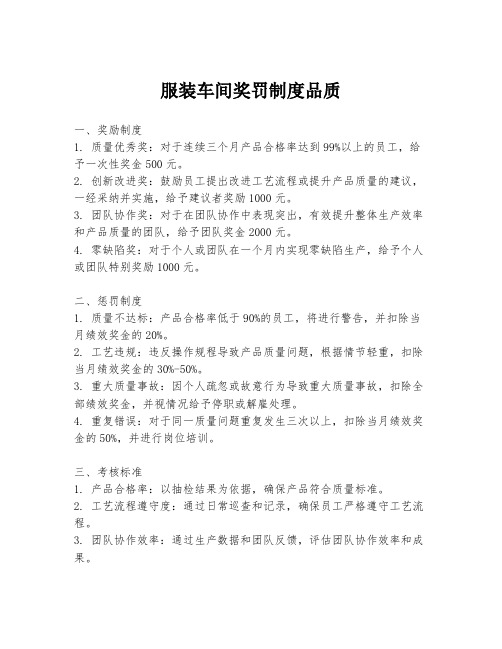
服装车间奖罚制度品质一、奖励制度1. 质量优秀奖:对于连续三个月产品合格率达到99%以上的员工,给予一次性奖金500元。
2. 创新改进奖:鼓励员工提出改进工艺流程或提升产品质量的建议,一经采纳并实施,给予建议者奖励1000元。
3. 团队协作奖:对于在团队协作中表现突出,有效提升整体生产效率和产品质量的团队,给予团队奖金2000元。
4. 零缺陷奖:对于个人或团队在一个月内实现零缺陷生产,给予个人或团队特别奖励1000元。
二、惩罚制度1. 质量不达标:产品合格率低于90%的员工,将进行警告,并扣除当月绩效奖金的20%。
2. 工艺违规:违反操作规程导致产品质量问题,根据情节轻重,扣除当月绩效奖金的30%-50%。
3. 重大质量事故:因个人疏忽或故意行为导致重大质量事故,扣除全部绩效奖金,并视情况给予停职或解雇处理。
4. 重复错误:对于同一质量问题重复发生三次以上,扣除当月绩效奖金的50%,并进行岗位培训。
三、考核标准1. 产品合格率:以抽检结果为依据,确保产品符合质量标准。
2. 工艺流程遵守度:通过日常巡查和记录,确保员工严格遵守工艺流程。
3. 团队协作效率:通过生产数据和团队反馈,评估团队协作效率和成果。
四、申诉机制1. 对于奖罚结果有异议的员工,可在接到通知后三个工作日内向人力资源部门提出申诉。
2. 人力资源部门应在收到申诉后五个工作日内组织复核,并给出处理意见。
五、制度更新1. 本奖罚制度自发布之日起生效,每年至少进行一次审查和更新,以适应生产和管理的需要。
六、其他1. 本制度的最终解释权归公司所有。
2. 所有员工应认真阅读并遵守本奖罚制度,以确保生产质量和效率的持续提升。
l品质部奖罚制度

l品质部奖罚制度一、总则1. 本制度旨在提升公司产品质量,确保品质管理的有效性,通过奖罚机制激励员工积极参与品质改进。
2. 本制度适用于公司品质部全体员工。
二、奖励机制1. 质量改进奖:对于提出有效质量改进建议并被采纳实施的员工,给予一次性奖励。
2. 零缺陷奖:在连续三个月内,负责的产品无重大质量问题发生的团队或个人,给予奖金奖励。
3. 优秀团队奖:每季度评选品质管理优秀团队,根据团队整体表现和贡献,给予团队奖金。
三、惩罚机制1. 质量事故处罚:因个人疏忽导致的质量事故,根据事故严重程度,给予警告、罚款或记过处分。
2. 违规操作处罚:违反操作规程导致质量问题的,除按规定赔偿损失外,还将给予相应的行政处分。
3. 隐瞒不报处罚:对于发现质量问题隐瞒不报的员工,一经发现,将给予严重警告,并根据情况严重性追加罚款。
四、奖罚标准1. 奖励金额根据建议的实施效果和节省成本的额度来定,具体由品质部经理和人力资源部共同评估。
2. 罚款金额根据问题的严重程度和造成的损失来定,具体标准参照公司《员工手册》相关规定。
五、奖罚程序1. 奖励和惩罚的提议由品质部经理提出,经人力资源部门审核后,报公司管理层审批。
2. 所有奖罚决定需书面通知相关人员,并记录在员工个人档案中。
六、申诉与复核1. 员工对奖罚决定有异议的,可在接到通知后5个工作日内向人力资源部门提出书面申诉。
2. 人力资源部门负责组织复核,并在收到申诉后10个工作日内给予答复。
七、附则1. 本制度自发布之日起生效,由品质部负责解释。
2. 对本制度的修改和补充,由品质部提出建议,经管理层审批后执行。
请根据公司实际情况和法律法规,对上述内容进行适当调整和完善。
- 1、下载文档前请自行甄别文档内容的完整性,平台不提供额外的编辑、内容补充、找答案等附加服务。
- 2、"仅部分预览"的文档,不可在线预览部分如存在完整性等问题,可反馈申请退款(可完整预览的文档不适用该条件!)。
- 3、如文档侵犯您的权益,请联系客服反馈,我们会尽快为您处理(人工客服工作时间:9:00-18:30)。
1.目的
为提升产品质量,通过奖优罚劣的手段,以提高全员的积极性、责任感,从而有效的达到激励全员参与,全员品管之目的。
2.适用范围
本制度适用于本厂所有部门工作(生产)场所的所有人员。
3.定义;
3.1质量:一组固有的特性满足要求的程度.
3.2品质异常:本制度所异常是在日常生产活动中,依据客户提供的资料和公司的规范工艺文件作业标准可以避免非预期的质量不良,且该不良判定责任为岗位工作人员,或其它可经目视或检验工具发现而未发觉的质量事件.
3.3质量事故的[定义
3.3.1按事故损失分:
A)一般质量事故:事故给公司带来的经济损失小于或等于500元的.
B)严重质量事故:事故给公司带来的经济损失大于500元而小于1000元的.
C)重大质量事故: 事故给公司带来的经济损失在1000元以上的或严重影响公司声誉的
经济损失计算时,包括材料成本和返修人工.工具.电费等所有估算值.
4.奖励细则
4.1操作员工的奖励
4.1.1能及时发现本工序产品质量隐患,避免质量事故发生者,每举报一次,给予奖励10-50元/次;
4.1.2发现工艺/技术文件BOM表以及装箱清单等编写错误,避免质量故发生者,每举报一次,视其影响程度,给予奖励10-50元/次;
4.1.3发现检验员将不合格品误判为合格品,避免或减少质量损失者,每举报一次,视其影响程度,给予奖励10-50元/次;
4.1.4互检时及时发现上工序产品存有严重质量问题,避免不合格品流入下工序者,每举报一次,给予奖励10元/次;
4.1.5对本工序存在的质量问题或隐患,能积极提出改善建议被采纳者,视其改善效益,给予奖励20-100元/次。
4.1.6月度质量统计中,员工在本职工作上未造成质量事故的,且配合质量工作者;由所属部门的主管及质检员共同评选出1-3名人员,并推举为“质量标兵”经审查确定后;给予奖励30-50元/人。
4.2关键工序的奖励
4.2.1成品入库前检测:月度质量统计中,未造成后工序或客户投诉(退货)附件缺失、给予奖励20-100元/人;
4.3专职品管员的奖励
4.3.1 月度质量统计,IQC当月检验误判次数为0次时(零星不良不计其内,失误次数以不良比率超过其允收水准值为准,误判次数小于3%为准给予奖励200元/人. 4.3.2 月度质量统计,IPQC当月度检验误判次数为0次时,成品抽检或客户验货通过给予奖励200元/人
4.3.3 月度质量统计,当月客户验货通过或没有客诉及被内部抽检通过者, 给予奖励200元/人
4.3.4对本岗位工作存在的质量问题或隐患,能积极提出改善建议被采纳者,视其改善效益,给予奖励20-100元/次。
4.4各职能人员的奖励(仓库/采购/技术等)
4.4.1月度总结中,在本职工作上从未发生因人为失误而造成质量事故者;由其部门主管推举表现优异者向厂部申请奖励,视其职务重要度给予奖励10-100元/人。
4.4.2对本职工作上存在的质量问题或隐患,能积极提出改善建议被采纳者,视其改善效益,给予奖励20-100元/次。
4.4.3在质量改进工作上有重大突出贡献者,由公司副总经理或总经理助理颁发特别奖,并召开表彰会进行表彰。
4.5干部层的奖励
4.5.1月度统计中,本单位/部门未因人为失误产生批量不合格,且制程抽检合格率及成品不良率均达成目标者;给予其负责人奖励10-100元/人。
4.5.2干部层其它形式的奖励按条款3.4.2及3.4.3之规定办理。
5.处罚
5.1原则
5.1.1当出现的不合格,属于非批量一般性质的质量事故,对相应岗位的责任按10-20元/次处罚
5.1.2当出现的不合格,属于批量一般性质的质量事故,对相应岗位的责任按20-100元/ 次处罚
5.1.3当出现的不合格, 属于非批量严重性质的质量事故, 对相应岗位的责任按50-200元/次处罚
5.1.4当出现的不合格, 属于批量严重性质的质量事故, 对相应岗位的责任按80-300
元/次处罚,或开除和调离岗位.
5.2操作员工的处罚
5.2.1未送首件产品(指公司新开发产品、客户打样产品及生产车间批量生产试装产品)确认,造成批量不合格者,给予处罚30元/次,并承担相应的返工或赔偿责任。
5.2.2未落实自检,造成批量不合格者(不良率超10%时),给予处罚20元/次,并承担相应的返工或赔偿责任。
5.2.3未落实互检,造成批量不合格流入下工序或客户者(与本工序有相关性的),给予处罚10元/次,并承担相应的返工或赔偿责任。
5.2.4未落实自检/互检,造成个别产品存有严重缺陷而流入下工序或客户者(如、网布破裂、孔位不对等影响性能的不合格),给予处罚5-10元/次,并承担相应的返工或赔偿责任。
5.2.5当发现异常,品管员要求改善而未停止改善,继续生产造成不合格品,对车间主管及生产部经理处以50-100元以上的罚款.
5.2.6 故意将不合格品混入到合格品当中或私自报废处理不合格品给当事人以100-200元的罚款.
5.3关键工序的处罚
5.3.1成品入库前检测:月度质量统计中,造成后工序或客户投诉(退货)附件缺失、
未按作业标准操作/检测,造成后工序或客户投诉(退货)给予处罚10-200元并无偿返检不合格批.
5.4专职品管员的处罚
5.4.1未按有关标程序及标准作业,造成首检错误、批量不合格、后工序或客户反馈不合格,不良比率超过1%者;视其造成损失程度,给予处罚10~100元/次。
5.5各职能人员的处罚(仓库/采购/技术等)
5.5.1在本职工作上因人为失误而造成质量事故者(包括开错单、发/领错料、使用或管理不善…违反有关程序/制度文件作业);视其造成损失程度,给予处罚10~50元/次,并承担相应的返工或赔偿责任。
5.6干部层的处罚
5.6.1现场发生较严重的批量性不合格时,车间主管应承担连带责任,并视其情节扣罚10~50元。
5.6.2发生重大品质事故(或客户退货)造成严重损失时,生产经理、质检、副总助理等应承担连带责任,并视其情节扣罚50~500元。
5.7不合格品返工或赔偿责任说明
5.7.1返工责任:因故而造成不合格品产生,不合格品可通过挑选/返修等方式加工为合格品时;由此而产生之人力(或费用)损失,由直接责任人按相应比例无偿返工。
5.7.2赔偿责任:因故而造成不合格品产生,且致使不合格品无法使用,须作报废处理或改料以作它用时,由此而产生之原材料、工时的损失,由责任人按损失总额的10%并按员工5:主管2:生产经理2:副总助理1的比例承担。
5.8不合格品返工或赔偿的责任分配比例
5.8.1本工序/岗位产生的批量性不合格
5.8.2车间主管未送首件产品试装确认产生批量性不合格时,半天(4小时)内产生之不合格,由车间主管100%承担相应的返工或赔偿责任;半天之后(4小时)之后产生之不合格,责任分配比例则为:操作员30%,车间主管20%,品管员50%。
5.8.3品管首件试装确认错误产生的批量性不合格时,其责任分配比例为:车间主管20%,品管员80%。
5.8.4首件确认合格,但车间员工及车间主管未落实自检产生的批量性不合格时,其责任是车间主管80%,车间员工20%。
5.8.5各职能人员因人为失误而造成产品批量性不合格,由当事人100%承担相应的返工或赔偿责任,其部门自行协调处理。
5.9流入次工序/工程发现的不合格
5.9.1操作员未落实自检/互检,造成批量不合格流入次工序时(指流出两个或两个以上工序的不合格),其责任分配比例为:直接操作员30%,间接操作员20%,车间主管30%,生产经理20%。
5.9.2操作员未落实自检/互检,造成个别产品存有严重缺陷而流入次工序或客户者,其责任分配比例为:直接操作员30%,间接操作员30%,车间主管20%,生产经理10%,品检10%。
5.9.3品管人员因批量误判,造成不合格流入次工序时(指流出本单位的不合格),若为来料不合格,则由责任品管员及供应商共同承担;若为制程不合格或客户退货不合格,其责任分配比例品管80%,生产单位20%,具体细分方式由各单位自行协调。
6、奖罚程序
6.1属日常作业中突发而产生的质量奖罚信息,由其部门/单位于事发后24小时内填写《质量奖罚处理单》,并及时知会品管进行调查、核实,之后再逐级呈送至副总经理助理审核,最后转财务部实施奖罚。
6.2属月度质量统计后而产生的质量奖罚信息,由品管部负责按月收集、统计,并将有关质量原始数据汇总后以书面形式通知各部门/单位,再由其部门/单位根据实际情况填写《质量奖罚处理单》,逐级呈送至副总经理处批准,最后转财务部实施奖罚。
6.3有关部门/单位人员所产生的奖罚金额,均于当事人当月薪资中体现,并在公告栏上加以公布。
7、执行奖罚的原则
7.1具备充分的理由和清晰的证据。
7.2奖罚的轻重程度应与所产生的经济效益或损失相符合。
7.3实施处罚时,应提前确认程序/流程/标准的合理性、可操作性及人员资格等,仅在因人为因素(未落实有关标准/无责任感/粗心大意等)造成的不合格时,则执行质量处罚。
7.4员工对质量处罚不满意时,有上诉的权利,申诉至副总助理调查。
8、本制度未尽事宜,由生产经理或以上级临时决定奖罚办法。
9、本制度自批准之日起生效,修正时亦同。
制定:生产部核准:。