淬火起重机技术说明
淬火起重机的特点综述

淬火起重机的特点综述李毅鹏【摘要】随着我国机械加工行业的发展,金属热处理量的增加,淬火起重机的使用愈加广泛,淬火起重机的设计、控制、制造方面也有很大发展.文章将对各种淬火起重杌的结构、控制方式、适用性、安全方面进行简述.【期刊名称】《机械管理开发》【年(卷),期】2011(000)003【总页数】3页(P94-96)【关键词】淬火起重机;控制方式;安全;动平衡【作者】李毅鹏【作者单位】太原重工股份有限公司技术中心起重所,山西,太原030024【正文语种】中文【中图分类】TH2181 淬火起重机的概述淬火起重机属于冶金起重机,通常用于热处理立式井淬火工艺中,热处理工部用来对大型工件快速浸入淬火液中。
淬火起重机主要用于冷却介质为盐水、水、矿物油的淬火工艺。
根据淬火工艺要求,炽热工件需要迅速地浸入到淬火池中,以保证工件上下金相组织均匀,并避免油面起火;故淬火起重机应能快速下降,其下降速度常比起升速度大许多倍,最大要达80 m/min。
由于淬火池深度有限,就要求快速下降的工件在极短的时间内停下,下降的制动距离一般控制在300~500 mm范围内[1]。
考虑工件冷却的时间,坑口大小的因素,淬火起重机的运行机构应起、制动运行平稳,并能快速准确停止在要求的工位处。
综上所述,淬火起重机的特点可概括为使用频繁,低速上升,高速下降,急速制动,起升做功,运行快速平稳,准确停车,环境恶劣,安全要求高等。
2 淬火起重机的控制方式淬火起重机的核心是起升机构。
从原理讲,这种起升机构属于多速起升机构,它的起升功率小,下降功率很大;由于下降功率是输出能量,因而可能不用昂贵的电动机来吸收其能量,而用其他简单廉价的方法达到这个目的。
一般采用落重制动的方法,将淬火工件的位能以摩擦功的形式变为热量散发出去。
针对淬火起重机的特点,根据起重量、控制策略、速度、价格、使用习惯等因素,分为以下控制方式。
2.1 电动液压推杆控制方式这种方式是采用频率发送器来控制电动液压推杆的推力,或采用可控硅改变电动液压推杆的供电电压来控制其推力。
ch7500淬火机床作业安全技术操作规程

ch-7500淬火机床作业安全技术操作规程1适用岗位范围本规程适用于公司泵筒ch-7500淬火机床作业安全技术操作2岗位主要危险源2.1机械装置工具造成的挤压碰撞、砸伤等。
2. 2吊装作业时造成起重伤害。
2. 3防护用品使用不当,防护装置缺损造成的机械伤害。
2. 4人体直接接触到高温部位,造成烫伤。
2.5人体直接接触到设备的带电部位、电源,电器漏电造成触电伤害。
3.6机床运转时机械噪南造成伤害。
2.7作业人员操作失误,违章作业造成的人员伤害。
3岗位职责2.1操作人员除遵守《热处理及表面处理类作业安全技术操作规程》有关规定外,必须遵守本规程。
2.2按照工艺规范、技术标准进行生产,做好工件自检和互检工作。
2.3严格遵守安全操作规程,按照设备检查、维护保养制度对安全防护装置进行检查、维护保养,使其保持良好。
2.5按时对生产运行安全情况进行巡回检查,发现异常及时关闭电源,报班组长。
3.6完善现场安全管理、定置管理等工作,使生产现场秩序规范化。
3.7对违反安全生产管理规定的有权拒绝生产。
4工艺安全作业程序和方法及行为规范4.1工作前4.1.1应正确穿戴好个人防护用品,持证上岗。
女工须将长发塞入工作帽中,禁止穿裙子、短裤凉鞋.高跟鞋等便装上机操作。
4.1.2必须对机械传动、电器、防护装置吸尘装置等进行全面检查,确保安全可靠,否则严禁使用。
4.1.3每次开动设备前,要对轴承链条等旋转零部件等进行检查,发现破损要及时更换。
4.1.4机床运转前应对机床各部进行巡回检查,特别应对冷却液系统. 压轮架总成等进行检查,发现有跑、冒、滴、漏现及卡阻或者链条拉长现象时,必须进行处理,待问题解决后才能开始工作。
5.1.5巡回检查无异常后,总电源合闸放电,同时观察各仪表指示情况,如有异常则断电检查排除故障后才能重新启动。
6.1.6清理工作现场,设备周围无无关杂物,确保安全通道畅通。
4. 2.1使用各种设备时严格执行安全生产规章制度和岗位操作规程, 遵守劳动纪律和职业道德。
立式数控淬火机床操作说明
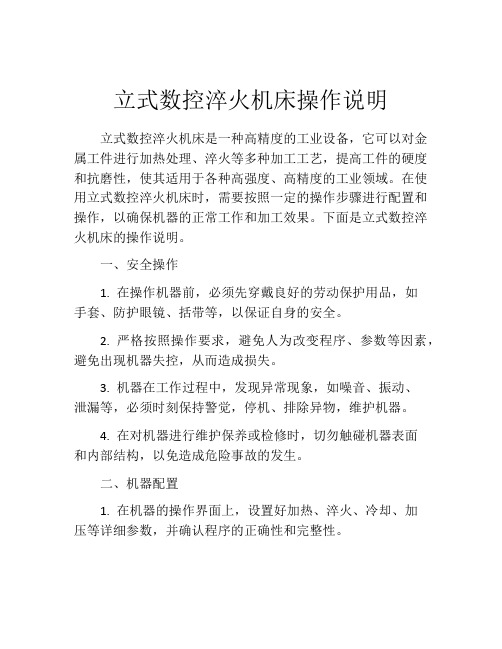
立式数控淬火机床操作说明立式数控淬火机床是一种高精度的工业设备,它可以对金属工件进行加热处理、淬火等多种加工工艺,提高工件的硬度和抗磨性,使其适用于各种高强度、高精度的工业领域。
在使用立式数控淬火机床时,需要按照一定的操作步骤进行配置和操作,以确保机器的正常工作和加工效果。
下面是立式数控淬火机床的操作说明。
一、安全操作1. 在操作机器前,必须先穿戴良好的劳动保护用品,如手套、防护眼镜、括带等,以保证自身的安全。
2. 严格按照操作要求,避免人为改变程序、参数等因素,避免出现机器失控,从而造成损失。
3. 机器在工作过程中,发现异常现象,如噪音、振动、泄漏等,必须时刻保持警觉,停机、排除异物,维护机器。
4. 在对机器进行维护保养或检修时,切勿触碰机器表面和内部结构,以免造成危险事故的发生。
二、机器配置1. 在机器的操作界面上,设置好加热、淬火、冷却、加压等详细参数,并确认程序的正确性和完整性。
2. 在淬火过程中,需要切换夹具、润滑系统、气源系统等多个配置,确保每个环节的工作正常,以避免因机器配置导致的加工质量降低,并记录工作状态与时间等数据。
3. 根据工件的形状、尺寸和材料,调节淬火温度和加工过程的速度、压力等参数,以保证加工工艺的正确性和精度。
三、加工操作1. 将需要加工的工件,放入夹具中并固定好,用正确的方法进入加工区域,设定好所需加工工艺和加工程序。
2. 按照程序要求进行加热、淬火、冷却等操作,确保每个过程的加工质量稳定可靠,并记录加工数据。
3. 过程中避免干扰机器的正常工作,避免出现振动、泄漏、偏差等问题,以保证加工质量的准确性和稳定性。
四、机器维护1. 机器在工作结束后,必须对机器进行清洁与维护,清除加工残留物、润滑剂、异物等,并检查设备的使用状况和磨损程度等,及时更换损坏的设备部件和润滑器具等。
2. 机器定期进行设备检查和保养,清除累计的油脂和污垢,检查并更换磨损和损坏的部位,以保证机器的正常工作状态。
立式数控淬火机床操作说明
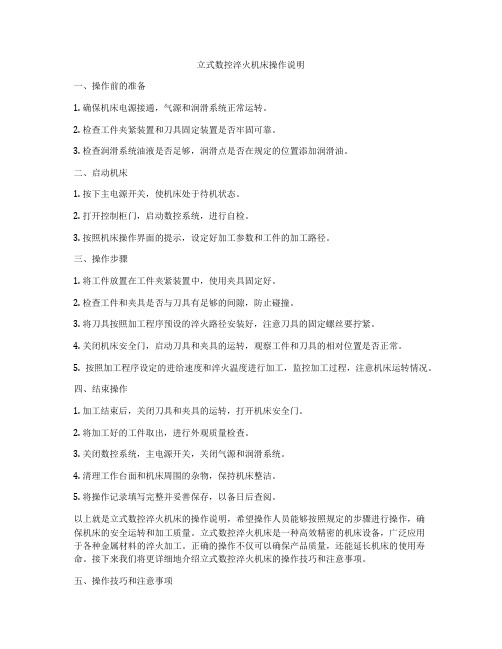
立式数控淬火机床操作说明一、操作前的准备1. 确保机床电源接通,气源和润滑系统正常运转。
2. 检查工件夹紧装置和刀具固定装置是否牢固可靠。
3. 检查润滑系统油液是否足够,润滑点是否在规定的位置添加润滑油。
二、启动机床1. 按下主电源开关,使机床处于待机状态。
2. 打开控制柜门,启动数控系统,进行自检。
3. 按照机床操作界面的提示,设定好加工参数和工件的加工路径。
三、操作步骤1. 将工件放置在工件夹紧装置中,使用夹具固定好。
2. 检查工件和夹具是否与刀具有足够的间隙,防止碰撞。
3. 将刀具按照加工程序预设的淬火路径安装好,注意刀具的固定螺丝要拧紧。
4. 关闭机床安全门,启动刀具和夹具的运转,观察工件和刀具的相对位置是否正常。
5. 按照加工程序设定的进给速度和淬火温度进行加工,监控加工过程,注意机床运转情况。
四、结束操作1. 加工结束后,关闭刀具和夹具的运转,打开机床安全门。
2. 将加工好的工件取出,进行外观质量检查。
3. 关闭数控系统,主电源开关,关闭气源和润滑系统。
4. 清理工作台面和机床周围的杂物,保持机床整洁。
5. 将操作记录填写完整并妥善保存,以备日后查阅。
以上就是立式数控淬火机床的操作说明,希望操作人员能够按照规定的步骤进行操作,确保机床的安全运转和加工质量。
立式数控淬火机床是一种高效精密的机床设备,广泛应用于各种金属材料的淬火加工。
正确的操作不仅可以确保产品质量,还能延长机床的使用寿命。
接下来我们将更详细地介绍立式数控淬火机床的操作技巧和注意事项。
五、操作技巧和注意事项1. 安全第一在操作机床时,安全是首要考虑的因素。
操作人员应穿着合适的工作服和安全帽,严格遵守操作规程,不得违章操作。
同时,机床周围应保持整洁,杂物不得堆积,以防发生危险。
2. 加工参数的设置在进行加工前,操作人员应根据实际情况设定好加工参数,包括进给速度、刀具转速、淬火温度等。
要确保这些参数与加工程序相匹配,以充分发挥机床的效率和准确性。
淬火起重机技术说明
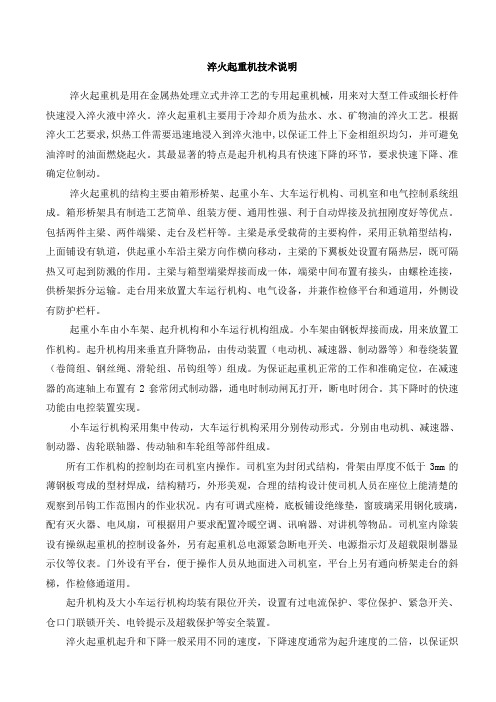
淬火起重机技术说明淬火起重机是用在金属热处理立式井淬工艺的专用起重机械,用来对大型工件或细长杅件快速浸入淬火液中淬火。
淬火起重机主要用于冷却介质为盐水、水、矿物油的淬火工艺。
根据淬火工艺要求,炽热工件需要迅速地浸入到淬火池中,以保证工件上下金相组织均匀,并可避免油淬时的油面燃烧起火。
其最显著的特点是起升机构具有快速下降的环节,要求快速下降、准确定位制动。
淬火起重机的结构主要由箱形桥架、起重小车、大车运行机构、司机室和电气控制系统组成。
箱形桥架具有制造工艺简单、组装方便、通用性强、利于自动焊接及抗扭刚度好等优点。
包括两件主梁、两件端梁、走台及栏杆等。
主梁是承受载荷的主要构件,采用正轨箱型结构,上面铺设有轨道,供起重小车沿主梁方向作横向移动,主梁的下翼板处设置有隔热层,既可隔热又可起到防溅的作用。
主梁与箱型端梁焊接而成一体,端梁中间布置有接头,由螺栓连接,供桥架拆分运输。
走台用来放置大车运行机构、电气设备,并兼作检修平台和通道用,外侧设有防护栏杆。
起重小车由小车架、起升机构和小车运行机构组成。
小车架由钢板焊接而成,用来放置工作机构。
起升机构用来垂直升降物品,由传动装置(电动机、减速器、制动器等)和卷绕装置(卷筒组、钢丝绳、滑轮组、吊钩组等)组成。
为保证起重机正常的工作和准确定位,在减速器的高速轴上布置有2套常闭式制动器,通电时制动闸瓦打开,断电时闭合。
其下降时的快速功能由电控装置实现。
小车运行机构采用集中传动,大车运行机构采用分别传动形式。
分别由电动机、减速器、制动器、齿轮联轴器、传动轴和车轮组等部件组成。
所有工作机构的控制均在司机室内操作。
司机室为封闭式结构,骨架由厚度不低于3mm的薄钢板弯成的型材焊成,结构精巧,外形美观,合理的结构设计使司机人员在座位上能清楚的观察到吊钩工作范围内的作业状况。
内有可调式座椅,底板铺设绝缘垫,窗玻璃采用钢化玻璃,配有灭火器、电风扇,可根据用户要求配置冷暖空调、讯响器、对讲机等物品。
起重机吊臂的热处理工艺

起重机吊臂的热处理工艺
起重机吊臂的热处理工艺主要包括回火和淬火。
下面是具体步骤:
1. 预处理:将起重机吊臂的工件进行清洗或研磨处理,确保表面无杂质和氧化皮。
2. 加热:将起重机吊臂工件放入炉内,进行加热。
加热温度根据吊臂材料的不同而有所不同。
3. 保温:在达到加热温度后,将炉温保持一段时间,以让材料内部达到均匀的温度。
4. 淬火:淬火是热处理工艺中的重要步骤。
将加热好的起重机吊臂迅速浸入水或油中进行淬火。
淬火温度和淬火介质根据工件材料的不同而有所不同。
5. 回火:淬火后的起重机吊臂显著增加了硬度,但也会变得非常脆。
因此需要进行回火处理,以降低硬度并增强韧性。
回火温度和时间根据工件材料和要求的性能而有所不同。
6. 精加工:经过热处理后,起重机吊臂需要进行一些精加工工艺,如切割、钻孔、铣削等,以满足其应用要求。
总之,起重机吊臂的热处理工艺是一个复杂的过程,需要根据具体情况选择合适的工艺参数和方法。
淬火起重机技术说明(YH)

淬火起重机技术说明淬火起重机适用于吊运机械工件进行淬火工艺处理,起重机能够快速将工件从加热炉吊运至淬火池,下降时要求以相应的速度快速下降(根据工件的大小、长短及相应的材质等),如处理长度在8m以上的大型棒料工件时,起重机垂直吊运工件从井式加热炉快速平稳准确吊运至井式淬火池,然后快速下降将工件放入淬火池,进行处理。
基于淬火工艺的特殊性,起升机构能够实现任意设定快速下降速度,并能在快速状态下准确停车,不产生溜钩现象。
1. 环境条件1.1 起重机的工作环境温度最低为-10℃,最高不超过+60℃。
1.2 起重机的电源为三相交流,频率为50HZ,电压为380V。
电动机和电器上允许电压波动的上限为额定电压的+10%,下限(尖峰交流时)为额定电压的-15%。
1.3 起重机安装使用地点的海拔高度2000m以下。
2. 使用性能2.1 起升机构起吊物品在下降制动时的制动距离应不大于每分钟额定起升速度的1/65。
2.2 起升机构采用变频调还控制,保证了在(0.2~1.0)G范围内下降,且电动机转速降至同步转速的1/3以下时,能够平稳制动。
3. 主要零部件3.1 起重横梁3.1.1起重机主梁、司机室、横梁下翼缘板下设有隔热装置。
3.1.2起升机构双限位,并有下限位装置,铸钢滑轮、钢板卷制卷筒。
3.1.3封闭滑轮、车轮材质65SiMn,起升电机H级绝缘及加超速开关、耐高温电缆。
3.2 采用封闭式司机室,并符合GB/T14407中的有关规定。
3.3小车电缆内翻、走台加宽。
3.4起升制动器有松闸装置,在工作当中以防停电。
3.5电气防护等级为H级。
4.起重机重要金属结构件的材料采用GB700规定的碳素结构钢,板厚小于或等于20mm时,选用力学性能不低于Q235-B,钢板厚大于20mm时。
注:重要金属结构件系指主梁、端梁、小车架、起重横梁。
4.2 焊接构件用焊条、焊丝和焊剂应与被焊接件的材料相适应。
5. 缓冲装置5.1 起重机大、小车运行机构采用弹簧缓冲器,采用弹簧缓冲器时按GB1614.1的规定执行。
淬火吊技术要求

太原重型机械(集团)有限公司起重机招标内容、技术、质量要求一、工程项目介绍:本项目标的为太原重型机械(集团)有限公司所属铸锻公司热处理分公司电动双梁桥式淬火起重机,安装在上述单位新建化学热处理中心生产场地。
二、现场条件2.1 电源参数:电压:AC 380V ± 10 %,电源频率:50Hz。
2.2 轨顶标高:(车间地面± 0.00)+12 m2.3 轨道中心距:22.5 m 。
2.4 生产用途:工件的起吊等。
2.5 生产类型:三班制。
2.6 工件类型:车轮及圆柱形钢锭等。
2.7 工作环境:室内热工环境(-5~50℃)三、设备主要技术参数和规格:3.1 主要技术参数3.1.1 主钩起重量:32 t3.1.2 主钩起升速度:25m/min3.1.3 主钩下降速度:50m/min3.1.4 主钩扬高:15m3.1.5 付钩起重量: 5 t3.1.6 付钩起升速度:25m/min3.1.7 付钩扬高:18m3.1.8 主钩下降:失电松闸安全装置(司机室手动操作)3.1.9 主钩下降:满载下降4档回零后,最大减速及制动距离小于600mm 3.1.10 大车运行速度:10~70m/min3.1.11 小车运行速度:10~48m/min3.1.12 大车供电方式:安全滑导3.1.13 小车供电方式:悬挂船用拖缆3.1.14 大车轨道:QU803.1.15 供电位置:司机室对面3.1.16 司机室形式:封闭空调式3.1.17 操纵方式:车上司机和地面遥控两用3.1.18 制动器类型:液力推动3.1.19 工作制度:A63.1.20 轨上高度:3100mm3.1.21 轨外尺寸:240mm3.1.22 外形尺寸(长×宽×高):≯23100×7000×2300(宽度含两缓冲器,高度指大车轨面至小车最高点)3.1.23 面漆色泽:橘红四、标的物技术要求(设计、制造、配套的基本要求):4.1 标的物技术要求4.1.1 按照通用标准车型设计、制造;主梁采用箱形结构,小车架要求整体加工,主梁和小车架要求必须采用Q345B;大小车轴箱首选圆弧形式;桥架结构及轨道形式采用偏轨梁和中轨梁两种;小车架振动时效或整体退火;整机钢板必须经前后两道抛丸处理后才能涂装。
淬火起重机的伤害类型及安全防护措施

淬火起重机的伤害类型及安全防护措施随着我国机械加工行业的迅速发展,金属热处理量日益增加,淬火起重机的使用也愈加广泛。
淬火起重机属于冶金类起重机的一种,即:用于淬火工序时,将工件快速浸入淬火液中的起重机。
它具有冶金类起重机工作环境温度高、启(制)动频繁和工作负荷大的共性,同时还具有主起升机构下降速度快、起降不同速的特点,其安全措施和安全装置的定期检验要求特别严格。
一、淬火起重机伤害类型根据冷却方法,淬火工艺分为单液淬火、双介质淬火、马氏体分级淬火和贝氏体等温淬火等四类。
常用的淬冷介质有盐水、水、矿物油、空气等。
而淬火起重机主要用于冷却介质为盐水、水和矿物油的淬火工艺,其在工作中存在如下伤害类型:(一)工件坠落及挤压碰撞专用卡具中吊物脱落、吊挂不牢、起升钢丝绳破断、吊装钢丝绳脱钩、吊物零乱或捆扎不牢、吊具损坏、吊挂位置摆动过大、设备缺陷、调运不稳等均可造成工件坠落。
另外,钢丝绳不耐高温、吊钩滑轮组没有防溅罩等都有可能烧断钢丝绳而造成坠落。
吊运现场混乱、操作空间狭窄以及操作不熟练等也可能造成吊运中的工件与其它物体、人员挤压碰撞。
(二)火灾油淬过程中火灾危险尤为突出。
火灾的潜在原因大致分为:淬火油本身老化;外来污染,例如淬火油中含有水分或低闪点成分的其它物资;系统设计缺陷,例如淬火槽的冷却、搅拌系统效果不好等;违章作业,如起重机带病运行、淬火油面过低等。
1、淬火油中含有水分:淬火油中的水分受热汽化体积急剧增加,出现泡沫和突沸,火灾危险性加大。
2、淬火油过热及含有低闪点成份:油槽冷却装置故障、油量过少以及淬火温度过高、工件体积过大等均可导致淬火油过热起火;油中混入低闪点组份可导致淬火油闪点降低,而淬火油使用温度高于闪点60℃就容易发生火灾。
3、工件未完全人油:工件入油时,如果起重机出现机械或电气故障,而使之不能完全、迅速入油,炽热的工件可使油表面温度迅速增高,达到闪点后可引燃油品表面,进而引燃所有油品。
值得注意的是:如果起重机驾驶室设在油槽的上方,一旦油槽起火将对司机造成严重伤害。
淬火机床使用操作说明书

淬火机床使用操作说明书一.机床操作说明1、性能特点立式数控淬火机床采用框架式焊接床身结构,双层精密工作台,上工作台移动,该机床上工作台移动采用滚珠丝杠传动,步进电机驱动,移动速度无级可调,零件旋转采用变频调速控制,速度无级可调。
零件夹持长度可电动调整,以适应淬火零件长度的变化,便于调整。
采用数控系统实现自动控制,可存储二十多种零件工艺程序。
该机床具有手动操作及全自动操作功能,适用于单件及批量零件生产,广泛应用于拖拉机、汽车、工程机械、机床行业的感应热处理领域。
结构合理、功能齐全、安装调试方便。
该机床具有连续淬火、同时淬火、分段连续淬火、分段同时淬火、等功能,主要用于半轴、传动轴、凸轮轴等各种轴类零件表面淬火,齿轮类、环类及平面类零件的感应淬火。
2、结构特点该机床主机由床身、双层精密工作台、上顶尖座调整滑动机构、上顶尖总成、工作台移动及传动系统、主轴旋转及传动系统、零件旋转与上顶尖调整机构,配种平衡,罩框、电气数控部分等组成。
1、床身部分:机床采用焊接床身结构,整体进行去应力退火。
主要外露件表面经特殊处理,具有良好的防锈抗蚀性能。
2、上顶尖调整机构:上顶尖调整采用电动调整,可实现不同长度工件的装夹。
3、工作台系统:采用步进电机通过变速机构驱动滚珠丝杠实现上工作台的升降运动,移动速度无级可调,传动轻快,导向精度高,定位准确。
4、主轴旋转系统:由异步电机通过变速机构和传动轴驱动主轴旋转。
采用变频调速实现零件转速无级调节。
5、罩框:罩框用厚钢板制成。
制作精良,外观美观,色泽大方。
罩框上部设有玻璃窗及推拉门,既可防止冷却水外溅,又便于装卸零件及监控淬火过程。
6、电气控制部分:电气控制部分由数控系统、变频调速器、中间继电器等组成,电源进线:3相,380V,1.5Kw;可存储二十种以上零件的淬火工艺,通过数控键盘可对各种程序进行编程存储。
机床设置有失电保护、越位保护等功能,具有较高的安全可靠性。
3、主要技术参数4. 机床操作使用方法1)开机:首先合上电源开关,检查数控系统各功能开关位置是否正常,若数控系统一切正常,选择相应主功能。
曲轴机械手自动淬火-概述说明以及解释

曲轴机械手自动淬火-概述说明以及解释1.引言1.1 概述曲轴机械手是一种自动化设备,广泛应用于汽车制造、机械制造等行业。
其主要功能是将曲轴从一工位转移到另一工位,以完成不同的加工工序。
在曲轴生产过程中,淬火是一个关键环节,能够提高曲轴的硬度和强度,从而提高其使用寿命和工作性能。
自动淬火技术作为现代制造业中的一项重要技术,可以使淬火过程更加稳定、自动化、高效。
传统的淬火操作不仅需要大量人工劳动,而且存在一定的操作难度和品质不稳定的问题。
而曲轴机械手自动淬火技术的出现,为曲轴淬火操作带来了很大的改变和便利。
曲轴机械手自动淬火主要依靠先进的传感器和控制系统,可以实时监测曲轴的温度和位置,并根据设定的工艺参数进行自动化控制。
同时,曲轴机械手还可以根据曲轴的形状和尺寸进行自适应调整,使得淬火的效果更加均匀和稳定。
通过自动化操作,曲轴机械手可以提高淬火的一致性和重复性,从而提高产品的质量和品质稳定性。
曲轴机械手自动淬火技术具有广阔的应用前景。
它不仅可以提高生产效率,减少人力成本,还可以提高产品的质量稳定性和一致性,降低了产品的缺陷率,提高了企业的竞争力。
在现代制造业中,曲轴机械手自动淬火已经成为曲轴生产过程中重要的一环,并得到了广泛的应用。
综上所述,曲轴机械手自动淬火技术是一项具有重要意义和广泛应用前景的技术。
它可以改变传统的曲轴淬火操作方式,提高生产效率和产品质量稳定性。
随着科技的不断进步和自动化技术的不断发展,相信曲轴机械手自动淬火技术将迎来更加美好的未来。
1.2文章结构1.2 文章结构本文主要分为引言、正文和结论三个主要部分,下面将对每个部分的内容进行介绍。
引言部分概述了本篇文章的主题——曲轴机械手自动淬火,并简要介绍了文章的结构。
通过引言,读者可以初步了解文章的主要内容和目的。
正文部分主要包括曲轴机械手的作用、自动淬火技术的重要性以及曲轴机械手自动淬火的原理。
首先,我们将详细介绍曲轴机械手在工业生产中的作用,包括提高生产效率、改善产品品质等方面的优势。
立式数控淬火机床操作说明

立式数控淬火机床操作说明1. 介绍立式数控淬火机床是一种先进的金属热处理设备,用于对金属工件进行淬火处理。
本文档将详细介绍立式数控淬火机床的操作步骤和注意事项,以确保安全、高效地进行淬火处理。
2. 操作步骤步骤1:开机准备在进行任何操作之前,请确保机床的电源已经连接,并检查电源开关和控制系统是否正常工作。
同时,检查冷却系统的工作状态,并确保冷却液和润滑油的供应充足。
步骤2:加载工件将待处理的工件放置在机床的工作台上,并使用夹具固定,以确保工件在淬火过程中的稳定性。
步骤3:设置淬火参数根据工件的具体要求,设置淬火的温度和时间参数。
这些参数可以通过机床的控制系统进行调整,确保淬火过程的准确控制。
步骤4:开始淬火确认设置参数后,按下启动按钮,机床开始进行淬火处理。
此时,机床会自动将工件加热至设定温度,并在温度达到后保持一段时间。
步骤5:冷却处理在保持工件温度一段时间后,机床会自动进行冷却处理。
冷却过程可以通过控制系统进行调整,以确保工件达到所需的硬度和强度。
步骤6:卸载工件待淬火处理完成后,将工件从机床上卸载,并进行必要的后续处理,如淬火工件表面的清洁、抛光等。
3. 注意事项•在操作机床之前,请确保穿戴好个人防护装备,如手套、护目镜等。
•严禁在机床运行时触摸工件或机床的移动部件。
•在操作机床时,请保持注意力集中,严禁分心或玩弄手机等物品。
•在设置淬火参数时,请确保参数的准确性和合理性,以避免损坏工件或机床。
•在进行冷却处理时,要确保冷却液和润滑油的供应充足,并注意冷却液的安全使用。
•在卸载工件时,要格外小心,并使用必要的工具和夹具以确保安全。
4. 结论本文档介绍了立式数控淬火机床的操作步骤和注意事项。
通过遵循正确的操作流程和注意事项,可以确保安全地进行淬火处理,提高工件的硬度和强度。
在操作过程中,请始终保持注意力集中,并妥善保养机床,以确保其正常和高效的工作。
YH型200/50t淬火起重机

地
邮
址 :湖南省长沙市雨花 区东二环一段 5 6 号湖南长重 机器股份有限公 司技术开发部
编 :4 1 0 0 1 4
斗轮机 的上线 ,取得 良好 的综合 效果。可 为斗轮
《 起重运输机械》 2 0 1 3( 2 )
收稿 日期 :2 0 1 2— 0 3— 0 7
态 一直 处 于可控 范 围之 内。
2 适 用 工 况
该 机适 用 的 环 境 温 度 为 一2 0℃ 一6 0 q C,高
温 、油蒸汽、烟尘等有害气体侵蚀环境 。
域处于领先水平 。总结大 吨位 、高 下降速度 、高
安全 性 的淬 火 起 重 机 的研 发 经 验 ,对 于 淬 火 起 重 机 的设 计 ,甚 至 类 似 铸 造 起 重 机 行 星 设 计 ,具 有 十分 重 要 的现 实意义 。
在热 加 工 过 程 中 ,为 保 证 细 长 工 件 热 处 理 性 能 均 匀 ,避 免 淬 火 液 着 火 ,起 重 机 应 具 有 快 速 下 降
功能 。
1 主 要技术 参数
Y H型 2 0 0 / 5 0 t 淬 火 起 重 机 的起 重 量 为 2 0 0 / 5 0 t ,跨 度 为 3 4 m,起 升 高 度 为 3 6 / 3 8 m,工 作制 度为 A 6( 重级 ) ,起 升 速度 为常 规 升 降 0—1 2 m / m i n ,淬火 下 降 0~ 2 4 m / m i n 。
方式及 其 装 置 :中 国 ,2 0 1 1 1 0 2 5 0 3 2 5 . 1[ P] . 2 0 1 1—
08 —2 9.
3 结 论不
作
者 :万正喜
足,提出了一种新 的 回转上线方法并设 计 了一 种
- 1、下载文档前请自行甄别文档内容的完整性,平台不提供额外的编辑、内容补充、找答案等附加服务。
- 2、"仅部分预览"的文档,不可在线预览部分如存在完整性等问题,可反馈申请退款(可完整预览的文档不适用该条件!)。
- 3、如文档侵犯您的权益,请联系客服反馈,我们会尽快为您处理(人工客服工作时间:9:00-18:30)。
淬火起重机技术说明淬火起重机是用在金属热处理立式井淬工艺的专用起重机械,用来对大型工件或细长杅件快速浸入淬火液中淬火。
淬火起重机主要用于冷却介质为盐水、水、矿物油的淬火工艺。
根据淬火工艺要求,炽热工件需要迅速地浸入到淬火池中,以保证工件上下金相组织均匀,并可避免油淬时的油面燃烧起火。
其最显著的特点是起升机构具有快速下降的环节,要求快速下降、准确定位制动。
淬火起重机的结构主要由箱形桥架、起重小车、大车运行机构、司机室和电气控制系统组成。
箱形桥架具有制造工艺简单、组装方便、通用性强、利于自动焊接及抗扭刚度好等优点。
包括两件主梁、两件端梁、走台及栏杆等。
主梁是承受载荷的主要构件,采用正轨箱型结构,上面铺设有轨道,供起重小车沿主梁方向作横向移动,主梁的下翼板处设置有隔热层,既可隔热又可起到防溅的作用。
主梁与箱型端梁焊接而成一体,端梁中间布置有接头,由螺栓连接,供桥架拆分运输。
走台用来放置大车运行机构、电气设备,并兼作检修平台和通道用,外侧设有防护栏杆。
起重小车由小车架、起升机构和小车运行机构组成。
小车架由钢板焊接而成,用来放置工作机构。
起升机构用来垂直升降物品,由传动装置(电动机、减速器、制动器等)和卷绕装置(卷筒组、钢丝绳、滑轮组、吊钩组等)组成。
为保证起重机正常的工作和准确定位,在减速器的高速轴上布置有2套常闭式制动器,通电时制动闸瓦打开,断电时闭合。
其下降时的快速功能由电控装置实现。
小车运行机构采用集中传动,大车运行机构采用分别传动形式。
分别由电动机、减速器、制动器、齿轮联轴器、传动轴和车轮组等部件组成。
所有工作机构的控制均在司机室内操作。
司机室为封闭式结构,骨架由厚度不低于3mm的薄钢板弯成的型材焊成,结构精巧,外形美观,合理的结构设计使司机人员在座位上能清楚的观察到吊钩工作范围内的作业状况。
内有可调式座椅,底板铺设绝缘垫,窗玻璃采用钢化玻璃,配有灭火器、电风扇,可根据用户要求配置冷暖空调、讯响器、对讲机等物品。
司机室内除装设有操纵起重机的控制设备外,另有起重机总电源紧急断电开关、电源指示灯及超载限制器显示仪等仪表。
门外设有平台,便于操作人员从地面进入司机室,平台上另有通向桥架走台的斜梯,作检修通道用。
起升机构及大小车运行机构均装有限位开关,设置有过电流保护、零位保护、紧急开关、仓口门联锁开关、电铃提示及超载保护等安全装置。
淬火起重机起升和下降一般采用不同的速度,下降速度通常为起升速度的二倍,以保证炽热工件可迅速地浸入到淬火池中,进而保证工件上下金相组织调质均匀。
其速度控制通常有以下几种方式:晶闸管闭环能耗制动式,摇摆电动机式、直流电动机式、变频电动机式等。
本设计按招标文件要求,采用晶闸管闭环能耗制动式。
采用晶闸管闭环能耗制动是采用由晶闸管(可控硅)整流出的直流电通入运转中的异步电动机,通过改变电动机转子的电阻或改变等效励磁电流的大小来实现起升机构的快速下降。
即电动机转子电阻增大而等效直流电流不变时,产生最大转矩的转速也增大。
因此速度的控制与载荷无关,即在不增加起升电动机容量的前提下就可以满足淬火起重机快速下降的工艺要求。
此方法电动机容量较小,既节能,控制装置的结构又成熟、简单、可靠。
是目前用得最广泛的淬火起重机控制方式。
一.设计、制造遵守的主要标准及规范GB 3811 《起重机设计规范》GB 6067 《起重机械安全规程》GB 5905 《起重机试验规范和程序》GB/T14405 《通用桥式起重机》JB5898 《淬火起重机》GB/T14407 《通用桥式和门式起重机司机室技术条件》GB 10183 《桥式和门式起重机制造及轨道安装公差》GB 700 《碳素结构钢》GB 8918 《优质钢丝绳》GB 5972 《起重机械用钢丝绳检验和报废实用规范》GB 8923 《涂装前钢材表面锈蚀等级和除锈等级》GB 9286 《色漆和清漆漆膜的规划试验》JB 4315 《起重机电控设备》GB 232 《电气装置安装工程施工及验收规范》TJ 231 《机械设备安装工程施工及验收规范》二.主要性能参数及说明1.性能参数:详见方案图2.设备技术说明:2.1主梁为正轨箱型结构,满载垂直静挠度 < S/800;满载自振频率≥2Hz。
跨中上拱度=(0.9/1000~1.4/1000)S,最大上拱度值控制在跨中S/10的范围内。
2.2主要承载构件如主梁、端梁、小车架等材质均为Q235-B钢,非受力件如走台、栏杆等采用Q235-A钢。
2.3重要金属结构件的材料均进行表面抛丸的除锈处理并达到GB8923中规定的Sa221级,其它构件达到Sa2级或St2级。
主梁腹板一次成型下料,无对接焊缝(适用于起重量≤50t,跨度≤30m)。
气体保护焊及埋弧焊,下料采用自动切割。
焊缝坡口符合GB9852.4主要构件焊接采用CO2和GB986标准,焊缝外部检查没有目测可见的明显缺陷。
2.5主梁上下盖板的对接焊缝采用超声波探伤或X射线探伤。
2.6电动机为YZR型冶金及起重用三相异步电动机,额定电压380V,额定频率50Hz,绝缘等级H级,防护等级IP54。
2.7减速机为ZQA和ZSC系列起重机专用中硬齿面圆柱齿轮减速器。
2.8制动器为YWZ型液压推杆常闭式,当机构不工作时制动器闭合,机构工作时由松闸装置将制动器打开,起升机构制动安全系数不低于1.75。
2.9卷筒为钢板卷制卷筒,材质Q235-B。
2.10采用起重机专用6W(19)瓦林吞线接触型钢芯钢丝绳,强度高、寿命长。
2.11吊钩材料为DG20#钢,并经热处理,钩口有防止钢丝绳脱落的安全卡。
2.12大小车缓冲装置为聚氨酯缓冲器,具有耐冲击,吸收能量大,反弹小,无噪声等特点。
2.13选用我公司生产的V法铸造的车轮,材料ZG55,车轮轴材料45#钢。
车轮踏面和轮缘内侧面硬度HB≥330~380,最小淬硬层的深度20mm处硬度HB≥260,车轮踏面和轮缘内侧面上无铸造缺陷。
2.14制动轮材料ZG340-640,表面热处理硬度HRC45-55,深2mm处硬度不低于HRC40。
2.15油漆标准符合GB9286标准,漆膜厚度为每层20~30μm,总厚度为60~90μm,漆膜附着力符合GB9286中的一级质量要求,设备经长期使用后,无漆面的退色、脱落等现象,油漆颜色由用户自定。
三.电气控制设计、制造遵守的主要标准及规范:GB3811 《起重机设计规范》GB6067 《起重机械安全规程》GB5905 《起重机试验规范和程序》JB4315 《起重机电控设备》GB1497 《低压电器基本标准》JB/ZQ20070 《起重机电气制图》【控制方式】●起升机构:通过起重机专用联动控制台操作晶闸管能耗制动装置来实现起升机构上升或下降的启动、制动与调速,该系统具备常规的过载、短路、失压及零位保护。
●大小车运行机构:采用切换转子电阻与联动台控制器配合,实现电动机的起动、制动及调速。
控制器档位:5-0-5。
大小车运行机构转子串电阻采用一相开路形式,使起动、运行更平稳。
【安全保护】●过流保护——每个机构的电动机单独设有两相过流继电器,另一相通过保护箱内的总过流继电器进行保护,各继电器的动作电流为被保护电动机总额定电流的2.5倍。
●零位保护——起重机开始工作及失压后重新工作时,必须将各控制器手柄置于零位后才能启动总接触器,使各机构电动机工作。
●限位及行程保护——主、副起升机构均设有DXZ型起升高度限位器,当吊钩上升到规定的极限位置时,能自动切断起升电动机电源,此时只能反向下降;设有下降深度限位器,当下降到下极限位置时,除能自动切断电动机电源外,缠绕在卷筒上的钢丝绳除固定圈外,至少保留两圈,此时起升机构只能作上升动作。
大、小车运行机构均设置LX10-12型限位开关,运行到极限位置时,即可断开控制回路,只有反方向操作时,机构才能动作。
●紧急保护——司机室内设有自锁式紧急开关,在紧急情况下可迅速切断起重机总控制电源。
●进入司机室的门和司机室到桥架上的门均设有LX6-10Q型限位开关,当任何一个门打开时,起重机所有机构均不能工作。
【照明信号及通讯】●司机室内采用照度不低于100LX的照明灯,电压为220V。
●起重机走台下设有2个以上GC-29型防震灯(数量由跨度而定),照度不低于20LX。
●司机室内设有警示电铃或声光报警器脚踏开关,并可根据用户需要配置对讲机。
【操纵形式】采用司机室内联动控制器操纵。
【馈电装置】●小车馈电装置采用电缆滑车、扁平电缆供电。
●大车馈电装置采用型钢滑触线或安全滑触线两种(供用户选择)。
【导线型号及敷设】●整机室内采用BVR-500V铜芯塑料线,室外采用BXR-500V铜芯橡皮线。
所有布线均采用截面积不小于1.5mm²的单芯铜线。
●导线通过线槽及线管来敷设。
【接地】起重机所有电气设备、正常不带电的金属外壳、金属线管、安全照明变压器低压侧一端等均通过专用接地线与金属结构可靠连接,再由金属结构通过车轮、大车轨道接地。
四.防护设备1. 起重机走台上通道的宽度不小于500mm,铺设有防滑花纹板。
走台及端梁栏杆高度为1050mm,间距350mm处设两道水平横杆,底部设高度70mm的围护板。
2. 起重机外露的旋转零部件均装设有防护罩。
3. 靠近大车导电滑线端设有检修吊笼;当导电滑线和司机室同侧时司机室配有防护网。
主要配套件厂家起重机主要部件加工工艺一. 起重机主梁的制作1.主梁盖板、腹板由ZQ—10数控切割机下料,一般构件采用半自动切割机下料,尺寸较小件采用仿形切割机下料。
2.主梁盖板及腹板在施焊前均由Q6920抛丸机进行表面除锈处理,达到Sa221级,并立即涂环氧富锌底漆。
3.主梁腹板下料预制上拱度按二次抛物线原理,利用计算机辅助设计,计算各相应高点,由数控切割机切割下料。
4.主梁拼焊在专用工作平台上进行,为减小焊接筋板对盖板和腹板造成变形,通过实行二人或四人对焊、正确选择焊接电流和速度等办法来保证。
5.主梁上下盖板的对接焊缝采用CO2气体保护焊,腹板和盖板连接四条纵焊缝采用埋弧自动焊焊接。
6.受拉翼缘板对接焊缝按规定实施超声波或X射线探伤。
7.桥架翻转采用特制工装,定位、起吊翻转,保证加工尺寸精度,控制箱体变形。
8.工序根据作业指导书进行,自检、专检合格后方能转入下道工序。
9.各种检验均有记录备查。
二. 起重机大车运行机构的制作与安装1.大车运行机构的加工件有齿轮联轴器、补偿轴和车轮组。
2.齿轮联轴器所采用的45#钢坯料及车轮(ZG50siMn)坯料,均由经我公司评价确定的合格分承包方协作供应并提供材质证明,并由我公司进行进厂检验。
3.齿轮联轴器坯料经车削后,由Y54A插齿机(内齿)或Y38—1滚齿机(外齿)进行齿加工,加工后的联轴器,齿形经Q—12、QZ—150齿轮检查仪检查合格后,转入SR的高频电炉对齿面进行高频处理。