塑胶模具结构
塑胶模具结构介绍

塑胶模具结构介绍塑胶模具是一种用于制造塑胶制品的工具,它的结构设计对于最终产品的质量和成型效果有着至关重要的影响。
下面是对塑胶模具结构的详细介绍。
1.塑胶模具的基本构造塑胶模具通常由上模、下模和模具座三部分组成。
上模和下模分别位于模具座的上下部,通过模具座的定位孔进行定位,并由模具座的螺母将上模和下模紧固在一起。
上模和下模分别具有模芯和模腔,模芯用于形成产品内部的空腔,模腔则用于形成产品的外形。
2.模芯与模腔模芯和模腔是塑胶模具中最关键的部分,它们决定了产品的形状和尺寸。
在注塑成型过程中,模具中注入熔化的塑料材料,通过模具中的进气系统将塑料材料充填到模芯和模腔中。
模芯和模腔的结构要能保证产品的尺寸精度和形状一致性。
3.模具的冷却系统塑胶模具中的冷却系统非常重要,它决定了产品的冷却速度和质量。
通常,冷却系统由模芯和模腔中的水道组成,通过循环流动的冷却水来降低模具温度,加快产品的冷却时间。
合理的冷却系统设计能够减小产品的变形和缩水,提高产品的强度和表面质量。
4.排气系统塑胶模具中的排气系统是为了排除由于材料流动引起的气泡和气蚀现象,保证产品的质量。
排气系统通常包括排气槽和排气孔,位于模腔或模芯的适当位置,保证气体能够顺畅排出,不影响产品的成型。
5.模具的脱模机构塑胶模具脱模机构主要用于将成品从模具中顺利取出。
脱模机构通常包括顶针、顶出杆和顶出板等部分,通过顶针将成品推出模腔并通过顶出杆和顶出板将成品从模具中顶出。
脱模机构的设计要保证成品从模具中取出时不发生变形、断裂等问题。
6.模具的开合机构塑胶模具的开合机构是为了使上模和下模能够分离和闭合。
开合机构通常由导向柱、导向套和开合杆组成,通过导向柱和导向套使上模和下模保持正确的定位,通过开合杆进行上模和下模的开合动作。
开合机构的设计要确保上模和下模的定位准确性和稳定性。
7.其他辅助结构塑胶模具可能还包括一些辅助结构,如压铭设计、割胎设计和定位销等。
这些辅助结构的设计要根据具体的产品要求和成型工艺进行选择和设计。
图解说明塑胶模具的结构组成

模具采购必备基础知识之二:塑胶模具的结构组成图解说明:模具注塑成型是批量生产某些形状复杂部件时用到的一种加工方法。
具体原理指:将受热融化的塑胶原材料由注塑机螺杆推进高压射入塑胶模具的模腔,经冷却固化后,得到塑胶成形产品。
塑胶模具由动模和定模两部分组成,动模安装在注射成型机的移动模板上,定模安装在注射成型机的固定模板上。
在注射成型时动模与定模闭合构成浇注系统和型腔,开模时动模和定模分离以便取出塑料制品。
塑胶模具的结构虽然由于塑胶品种和性能、塑胶制品的形状和结构以及注射机的类型等不同而可能千变万化,但是基本结构是一致的。
一、塑胶模具结构按功能分,主要由:浇注系统、调温系统、成型零件系统、排气系统、导向系统、顶出系统等组成。
其中浇注系统和成型零件是与塑料直接接触部分,并随塑料和制品而变化,是塑模中最复杂,变化最大,要求加工光洁度和精度最高的部分。
1.浇注系统:是指塑料从射嘴进入型腔前的流道部分,包括主流道、冷料穴、分流道和浇口等。
主流道前模架前模仁塑胶件产品行位油缸定位导柱行位定位导套方铁顶针固定板前模架底板6.顶出系统:一般包括:顶针、前后顶针板、顶针导杆、顶针复位弹簧、顶针板锁紧螺丝等几部分组成。
当产品在模具内成型冷却后,模具前后模分离打开,由推出机构--顶针在注塑机的顶杆推动下将塑料制品及其在流道内的凝料推出或拉出模具开腔和流道位置,以便进行下一个注塑成型工作循环。
二、塑胶模具按结构分一般由模架、模仁、辅助零件、辅助系统、辅助设置、死角处理机构等几个部分组成。
1、模架:一般都不需要我们设计,可以直接从标准模架制造厂商那里订购,大大节约的设计模具所需时间,所以称它为塑胶模具标准模架。
它构成了塑胶模具最基本的框架部分。
2、模仁:模仁部分是塑胶模具的核心部分,它是模具里面最重要的组成部分。
塑胶产品的成形部分就在模仁里面,大部分时间的加工也花费在模仁上。
不过,相对有些比较简单的模具,它没有模仁部分,产品直接在模板上面成形。
塑胶模具结构详解

塑胶模具结构详解塑胶模具是塑胶制品生产中必不可缺的工具,主要用于将熔融状态的塑胶物料注入模具中,通过冷却固化后得到所需要的塑胶制品。
塑胶模具的结构设计直接影响着塑胶制品的成型质量和生产效率,因此塑胶模具的结构设计非常重要。
下面我将详细介绍塑胶模具的结构。
首先,塑胶模具的结构主要包含以下几个部分:模具座、模腔、模芯、导向机构和顶出机构。
1.模具座:模具座是塑胶模具的支撑结构,通常采用钢板焊接而成。
模具座上装有模腔和模芯,通过模具座上的定位孔与注塑机上的模板定位销相连接,保证模具的准确定位。
2.模腔:模腔是塑胶模具中用于成型的腔体部分,它的形状和尺寸与最终产品的形状和尺寸一致。
模腔一般由高硬度、高耐磨的钢制成,以保证模具的耐用性。
模腔表面经过抛光和处理,以保证成型产品的光洁度。
3.模芯:模芯是模腔的补充部分。
在注塑过程中,塑胶材料被注入到模腔中,模芯起到的作用是使模腔中的塑胶材料在注射后能够顺利排出,并保证成型产品的尺寸和形状的准确性。
模芯一般用低硬度、低摩擦系数的钢制成,以减少与模腔的磨损。
4.导向机构:导向机构用于保证模腔和模芯的准确定位,以防止注塑过程中的偏移和动作不平衡。
通常采用导柱和导套的组合形式,导柱固定在模具座上,导套安装在模腔和模芯上,实现模腔和模芯的相对运动。
5.顶出机构:顶出机构用于将成型后的产品从模具中弹出,通常采用弹簧和顶出杆的组合形式。
顶出机构应设计合理,力度适中,以保证成型产品的完整和表面的光洁度。
除了上述主要部分之外,塑胶模具还可以根据具体的产品要求加上一些辅助结构,如冷却系统、进胶口和排气口等。
冷却系统用于将模具中的热量迅速带走,以保证模具的温度恒定,提高生产效率;进胶口用于塑胶材料的注入,排气口用于排除模腔内的气体。
总之,塑胶模具是实现塑胶制品生产的关键工具,其结构设计需要综合考虑成型质量、生产效率和模具耐用性等方面的因素。
上述介绍的塑胶模具结构是基础的结构设计,具体的模具结构设计还需要根据不同产品的具体要求进行调整和优化。
塑胶模具基本结构详解

塑胶模具基本结构详解塑胶模具是在塑料制品生产中使用的主要工具,它是将液态塑料注入模具中,经过一定的温度和压力处理后形成的产品。
塑胶模具的基本结构是由模具基板、模具芯、模具腔、模具导板、模具定位销、模具螺栓和注塑系统组成。
1.模具基板模具基板是塑胶模具的主要承载部分,是模具的基础结构,其质量主要决定了整个模具的稳定性和使用寿命。
通常情况下,模具基板是由钢材制造而成,其材质应该具有高强度、高耐磨性、高韧性以及耐高温的特点。
2.模具芯模具芯是模具中用来预留产品中空部分的一个孔,通常直接与注塑系统相连。
在塑料模具的制造中,模具芯的加工难度较大,生产过程中需要高精密度的加工设备和技术,可以利用CNC机床进行加工。
其中,最为常见的模具芯形状包括圆柱形、方形、各种不规则形状等。
3.模具腔模具腔是指模具中用来成型产品的部分,由于涉及到产品的外观、尺寸、表面光洁度等因素,因此模具腔的加工难度也相对较大。
模具腔需要具备高度精密度的尺寸和表面处理,通常要求采用光学除毛刺技术和精密抛光技术来完成。
4.模具导板模具导板是指在塑料模具中,用来固定模具芯和模具腔的位置和方向关系的部件。
通常情况下,模具导板由优质的合金钢、特种材料等制作而成,确保了模具芯和模具腔之间的高度一致性和整体稳定性。
5.模具定位销模具定位销是模具中用来保持模具芯和模具腔对准的重要部件。
其主要作用是确保注塑过程中的模具对位,从而保证了最终产品质量的稳定性和一致性。
模具定位销的数量一般根据模具的大小和复杂度来决定,通常为1~16个。
6.模具螺栓模具螺栓是模具中用来连接、固定模具芯和模具腔的部件。
由于注塑过程中会受到较大的压力和温度冲击,因此模具螺栓的材质必须具有高韧性、高强度和高耐磨性等特点,以保证模具系统的整体稳定性和耐用性。
7.注塑系统注塑系统是塑胶模具中的一个重要部分,其主要作用是将塑料熔化,将熔融塑料注入到模具芯和模具腔中,从而形成最终的产品。
其主要组成部分包括进料系统、加热系统、注塑系统、保压系统、冷却系统和排气系统等。
塑胶模具的结构是什么

塑胶模具的结构是什么
塑胶模具是制造塑料制品的必备工具,其结构是由多个部分组成的,用于将塑料熔化后注入模具中进行形成。
下面将介绍塑胶模具的结构及其各个部分的功能。
模具整体结构
塑胶模具的整体结构通常由注塑机固定板、上模板、下模板和模具基座四个部分组成。
其中,注塑机固定板与模具基座紧密固定,上下模板则可以通过模具底块进行快速拆装。
模具核心与腔
模具核心和模具腔则是模具的核心部分,分别位于上下模板之中,用于容纳塑料材料并将其形成所需要的形状。
模具核心和模具腔的准确度和光洁度对于模具的质量至关重要,一般情况下都需要经过数控加工等精细工艺来保证其精准度和光洁度。
浇口和排气口
塑胶模具的浇口和排气口也是模具不能缺少的部分。
浇口和排气口可以帮助塑料材料在注入模具时均匀流动,并在成型过程中排除内部气体,以达到理想的模具成型效果。
浇口和排气口的设计、尺寸和位置都是需要精心考虑和打磨的。
活削
在一些需要复杂形状或内部结构的模具中,可能会需要使用活削来完整地制造出所需要的产品。
活削也是模具制造中一个重要的工艺环节,需要经过严密的计算和操作。
小结
综合以上的内容,可以看出塑胶模具是由多个部分组成的,每个部分都扮演着重要的角色。
在塑胶模具制造过程中,为了避免由于材料、工艺等原因引起的模具失效,需要对模具进行细致、严谨的设计和制造。
希望本文能够对大家了解塑胶模具的结构有所帮助。
塑胶模具结构简介

1.4 顶出系统与成型机构
扁顶针:成型空间小、加强筋深度较深,不好布置 比较合适的圆顶针的时候采用。
入子
W
為參考 規格
图-24 扁顶针顶出
简单推出机构——推杆推出机构.exe
1.4 顶出系统与成型机构
顶管(司筒):一般用来作为螺丝柱较深的顶出。
成品 套筒内芯
套筒外壁
压板形式
螺钉锁紧形式
简单推出机构——推管推出机构.exe
塑胶模具结构简介
目录
1.塑胶模具的结构
1.1 塑胶模具的基本结构 1.1-1 模板编号规则 1.1-2 塑胶模具零件编号标准 1.2 浇注系统 1.3 成型系统 1.4 顶出系统及成型机构 1.5 排气系统 1.6 冷却系统 1.7 导向与定位系统
1.1塑胶模具的结构
塑胶模具,一种用于压塑、挤塑、注射、吹塑和低发泡成型的组合式 塑料模具的简称
1.4 顶出系统与成型机构
顶出系统:当制品在模具中固化后,需要有一套优先的方
式将其从模具中顶出,而且在顶出中不能出现顶白、制品变形、 破裂等损坏制品的现象,这套系统被称为顶出系统。
顶出的主要形式:圆顶针(推杆)、扁顶针(推杆)、
顶管(司筒)、顶出块、脱料板、斜顶等。
圆顶针:
制品
胶位面 顶杆
图-23 圆顶针顶出
B3
B2
B4
1.1-1-1 模板的区分
C101
1 浇口 2 顶杆孔 3 斜顶孔 4 镶芯孔
C201
1 1
2
3 1 4
1.1-圾钉
撑头孔
回程杆杯头
顶杆杯头
1.1-1-2零件的编号规则
镶块→C; 镶芯→P; 前模→1; 后模→2; 行位,斜顶→3; 其他→4,5 零件序号: 1)前模零部件: C101→C1××(主镶件) P101→P1××(镶芯) C101-1→C1××-1(次镶件) 2)后模零部件: C201→C2××(主镶件) P201→P2××(镶芯) C201-1→C2××-1(次镶件) 3)滑块零部件: C3A01→C3××(滑块或滑块座) C3A01-1→C3A××-1(滑块头或C3A××上复杂组件部件) 4)斜顶、直顶零部件: C3B01→C3B××(斜顶头、斜顶、直顶块、带形状的方顶等) C3B01-1→C3B××-1(C3B××上的组件部件) 5)压板,固定块,滑块安装座,导滑块,T型块,固定板类部件: C401→C4×× 6)耐磨板,承压板,镶块锁紧块需热处理类部件: C501→C5××
塑胶模具结构设计

塑胶模具结构设计塑胶模具结构设计是制造业中至关重要的环节,它直接关系到产品的质量、生产效率和成本。
本文将围绕塑胶模具结构设计的基本原则、设计流程及注意事项进行详细阐述。
一、塑胶模具结构设计的基本原则1. 确保产品精度在设计塑胶模具时,要保证产品的尺寸精度和形状精度。
这要求设计师充分了解塑胶材料的收缩率、流动性等特性,并在模具设计中予以充分考虑。
2. 易于加工与装配模具结构应尽量简单,便于加工和装配。
复杂的设计不仅会增加制造成本,还可能影响模具的可靠性。
在设计过程中,要充分考虑模具零件的加工工艺性和装配顺序。
3. 高效生产塑胶模具结构设计应考虑生产效率,尽量减少生产过程中的辅助时间。
例如,通过优化流道设计、缩短冷却时间等措施,提高生产效率。
4. 安全可靠5. 维护方便模具在使用过程中难免会出现磨损、损坏等问题,设计时应考虑模具的维修便捷性,降低维护成本。
二、塑胶模具结构设计流程1. 分析产品结构在设计模具前,要对产品结构进行分析,了解产品的尺寸、形状、技术要求等,为模具设计提供依据。
2. 确定模具类型根据产品结构特点和生产要求,选择合适的模具类型,如单腔模具、多腔模具、热流道模具等。
3. 设计分型面分型面是模具闭合时,分离塑胶制品和浇注系统的界面。
设计分型面时要考虑产品的脱模斜度、外观质量等因素。
4. 设计浇注系统浇注系统包括主流道、分流道、浇口等部分,其设计直接影响到塑胶制品的质量。
设计时应关注流道截面积、长度、浇口位置等因素。
5. 设计冷却系统冷却系统对塑胶制品的质量和生产效率具有重要影响。
设计时要考虑冷却水路的布局、冷却水流量、冷却水温度等因素。
6. 设计顶出系统顶出系统的作用是在模具开模时,将制品从模具中顺利取出。
设计时要确保顶出力均匀、可靠,避免产品变形或损坏。
7. 绘制模具零件图及装配图三、塑胶模具结构设计注意事项1. 充分考虑塑胶材料的特性,如收缩率、流动性、热稳定性等。
2. 优化模具结构,提高生产效率,降低生产成本。
塑胶模具结构设计注意点

模具结构设计1.滑块导轨的高至少要为滑块高的1/32.有滑动摩擦的位置注意开设润滑槽,为了防止润滑油外流,不宜把槽开成“开式”,而应该为“封闭式”,一般可以用单片刀在铣床上直接铣出。
3.固定模仁的型腔,对小模一般用线割,这样可以提高模具的精度;而较大模的模腔一般铣削的形式加工出来,加工时注意其垂直度,并且为了防止装配时,模仁不到位,模框的四周应该用铣刀铣深0.2。
4.入子与模仁,模仁与模仁,模仁与模框的相互穿插一般要加1°的斜度,以防装配时碰伤。
5.入子的靠位部分长度公差为-0.02,大小公差为-0.10,模仁相对应的靠位公差为+0.02。
6.有C角的入子最底端到C角部位的公差为+0.01,以防跑毛边。
7.本体模具的主体部分用NAK80的材料,入子、梢等用SKH9、SKH51(材料处理:室化处理,也可以不要)的材料,必要时可以使用VIKING材料。
8.画好部品之后,应先定滑块的位置、大小,防止发生干涉、及强度不够的现象,然后才定模仁寸法。
9.入子大小公差设为-0.01,模仁上入子孔对应的公差为+0.01。
10.模仁上的线割方孔尖角部分用R0.20过度,对应的入子部分也为R0.20,以对应线切割时的线径影响,同时可以防止尖角部分磨损,而产生益边。
11.与定位珠相对应的小凹坑寸法一般为底径φ3夹角90°-120°的圆锥孔。
12.固定侧的拔模角应该大于可动侧,以便离型留在可动侧;而且可以防止部品变形,尤其是壁薄,件长容易变形的零件,固定侧对它的拉力不均容易使部品翘曲,或留在固定侧。
13.对于侧面抽芯力大而部品精度要求又严的零件,最好采用二次抽芯结构。
14.斜梢的斜度+2°=压紧块的斜度(一般为18°或20°或22°).15.模具组立时,应该养成如下习惯:a.用空气枪清理模仁、模腔、入子、流道板、分模面的表面。
b.装配前用油石打光模仁、模腔、入子、分模面的表面,以便装配时顺tang。
塑胶模具结构设计要点
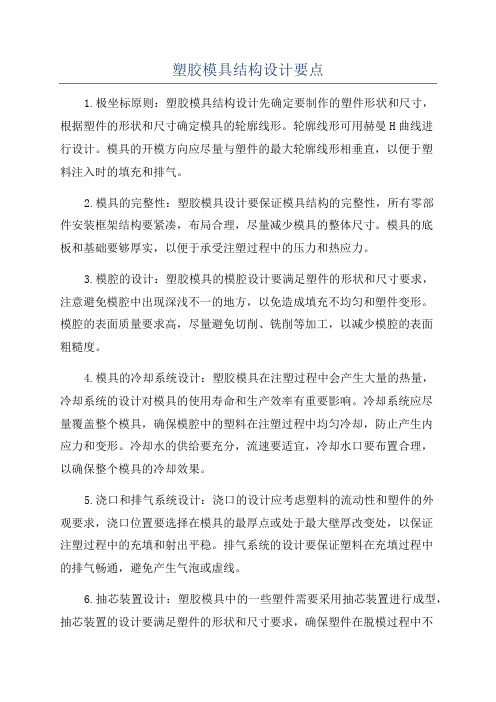
塑胶模具结构设计要点1.极坐标原则:塑胶模具结构设计先确定要制作的塑件形状和尺寸,根据塑件的形状和尺寸确定模具的轮廓线形。
轮廓线形可用赫曼H曲线进行设计。
模具的开模方向应尽量与塑件的最大轮廓线形相垂直,以便于塑料注入时的填充和排气。
2.模具的完整性:塑胶模具设计要保证模具结构的完整性,所有零部件安装框架结构要紧凑,布局合理,尽量减少模具的整体尺寸。
模具的底板和基础要够厚实,以便于承受注塑过程中的压力和热应力。
3.模腔的设计:塑胶模具的模腔设计要满足塑件的形状和尺寸要求,注意避免模腔中出现深浅不一的地方,以免造成填充不均匀和塑件变形。
模腔的表面质量要求高,尽量避免切削、铣削等加工,以减少模腔的表面粗糙度。
4.模具的冷却系统设计:塑胶模具在注塑过程中会产生大量的热量,冷却系统的设计对模具的使用寿命和生产效率有重要影响。
冷却系统应尽量覆盖整个模具,确保模腔中的塑料在注塑过程中均匀冷却,防止产生内应力和变形。
冷却水的供给要充分,流速要适宜,冷却水口要布置合理,以确保整个模具的冷却效果。
5.浇口和排气系统设计:浇口的设计应考虑塑料的流动性和塑件的外观要求,浇口位置要选择在模具的最厚点或处于最大壁厚改变处,以保证注塑过程中的充填和射出平稳。
排气系统的设计要保证塑料在充填过程中的排气畅通,避免产生气泡或虚线。
6.抽芯装置设计:塑胶模具中的一些塑件需要采用抽芯装置进行成型,抽芯装置的设计要满足塑件的形状和尺寸要求,确保塑件在脱模过程中不变形或损坏。
抽芯装置的操作要方便,可靠,要考虑到抽芯力和脱模力的大小,以确保抽芯的顺畅和模具的寿命。
7.快速更换系统设计:塑胶模具在生产过程中需要频繁更换不同的模腔,快速更换系统的设计能够极大地提高模具的使用效率和生产效率。
快速更换系统要求模腔结构尽量简单,易于拆卸和装配,以及固定方式的可靠性。
8.模具的加工工艺:塑胶模具的制作工艺要选择合适的材料和加工工艺,以确保模具的成型精度和表面质量。
塑胶模具的基本结构

流道系統-示意圖與實品 浇注系统
尽短原则 平衡进入原则. 大与小的综合考量(阻力、殘余应力、 材料、保压、冷却时间)
浇注系统
流道设计考虑因素:
浇注系統-澆口形式
直接澆口 方形邊緣澆口 搭接澆口 扇形澆口 薄膜澆口 圓盤澆口 點狀澆口 潛狀澆口
普通滑块抽蕊结构
1.8.4 成型零件系统
后模HALF滑块结构
1.8.4 成型零件系统
前模HALF滑块结构
1.8.5 成型零件系统
1.8.4 成型零件系统
常见分型面处理方法
分型面应沿产品的外形拉伸,尽量避免线或点封胶
1.8.5 成型零件系统
常见分型面处理方法
如果沿产品外形拉伸会产生尖角,可采用以下的方法避免.
1.9.10 浇注系统
1.4 环形浇口:环绕型芯均匀进入型腔,充模状态较好。但环形浇口的凝料切除比较困难。
浇注系统
1.5 盘形浇口:适用于管状或扁平和浅的环形塑件。 优点:进料点对称、充模均匀、能 消除熔接线。 缺点:浇口凝料常用冲切法切除;
1.9.11 浇注系统
环形入口的自动化结构实例
此小端取D2.0~3.0 此大端取D-0.5(D指流道直径) 应用图例 牛角澆口应用
此型号的牛角镶件适用于常用的以下胶料:PP,ABS,PC,PA+GF等。浇口大小根据不同胶料的胶厚相应取值, T指胶位厚度: PP=0.6T,ABS=0.6T,PC=0.7T,PA+GF15~30%=0.6T, 浇注系统
1
2
合模导向系统
3
部分零﹑部件的功能﹑材質介紹
場合二﹕成品有插破角而插破角 較小時使用﹐防止精度 破壞插破面。這是 我們設計中最常見的場 合。
塑胶模具结构解析

塑胶模具结构解析
塑胶模具是生产塑料制品的重要工具,它的结构对于塑料制品的形状、尺寸和质量起着至关重要的作用。
本文将从塑胶模具的结构组成、工作原理、常见问题及优化改进等方面进行解析。
塑胶模具的结构组成通常包括模具底板、上下模板、滑块、导柱导套
和顶出机构等。
模具底板是模具的支撑结构,上下模板是塑胶制品的成型腔,滑块用于造型复杂的塑胶制品,导柱导套用于定位工作,顶出机构用
于将成型后的塑胶制品顶出模具。
塑胶模具的工作原理是通过注塑机将熔化的塑料料料注入到模具腔中,经过一定的冷却和固化后,取出成型的塑料制品。
在注塑过程中,模具必
须具备合理的进料通道,以保证熔化塑料的顺畅流动,并避免熔料在模具
中的堆积产生缺陷。
塑胶模具在使用过程中可能会遇到一些常见问题,如模具磨损、变形、断裂等。
针对这些问题,可通过增加模具的冷却系统来解决模具温度过高
引起的变形问题,增加模具材料的硬度和韧性来改善模具的耐用性,合理
设置模具的出料槽,避免模具断裂。
为了提高塑胶模具的使用寿命和生产效率,可进行优化改进。
首先,
对模具进行维护保养,定期清理模具内部的残留物和杂质,以保证模具的
流畅运行。
其次,可以采用高强度耐磨材料制作模具,提高模具的抗磨性能。
还可以优化模具的结构设计,减少模具的开合力,提高模具的开模速
度和生产效率。
总之,塑胶模具的结构对于塑料制品的成型质量和生产效率起着至关重要的作用。
通过合理的结构设计、优化改进和定期维护保养,可以提高模具的使用寿命和生产效率,进而降低生产成本,提高经济效益。
塑胶模具结构基础知识

塑胶模具结构基础知识塑胶模具是塑料制品生产过程中不可或缺的一部分,它是制定塑料制品形状和尺寸的工具。
塑胶模具结构基础知识是了解塑胶模具的重要基础,本文将从塑胶模具的分类、主要构件和工作原理等方面进行介绍。
一、塑胶模具的分类1.根据模具制作材料的不同,塑胶模具可以分为金属模具和非金属模具两大类。
金属模具通常由钢、铝等材料制成,具有高强度、高硬度和高耐磨性等优点;非金属模具通常由塑料和树脂等材料制成,具有成本低、加工方便等优点。
2.根据模具结构的复杂程度,塑胶模具可以分为单一模具和组合模具两大类。
单一模具是一种简单的模具,用于生产单一形状的塑料制品;组合模具是由多个模块组合而成的复杂模具,可以生产多种形状的塑料制品。
3.根据塑料制品的生产方式,塑胶模具可以分为压力成型模具和注射成型模具两大类。
压力成型模具适用于塑料在一定温度和压力下通过模具的压力形成制品;注射成型模具适用于将塑料熔化后注入模具腔中,并通过压力使其充满整个模具腔,然后冷却成型。
二、塑胶模具的主要构件1.模具基础部分:包括底板、底座、定位销等。
底板是模具的主要支撑部分,通常由钢板制成;底座用于固定模具和机器,保证模具的稳定性;定位销用于定位模具的上下左右方向,以确保模具的精度。
2.模具腔部分:模具腔是塑胶模具的主要工作部分,它是塑料制品形状和尺寸的表现。
模具腔通常由上模腔和下模腔组成,通过上下闭合实现对塑料的成型。
模具腔的形状和尺寸应与最终塑料制品的要求相匹配。
3.模具动作系统:用于实现模具的开合和脱模动作。
包括模具开合机构、模具顶针机构、模具顶针回程机构等。
模具开合机构通常由导柱和导套组成,用于使上、下模腔之间产生相对运动;模具顶针机构用于在模具开合过程中对塑料制品进行顶出。
4.模具温控系统:用于控制模具的温度,以确保塑料熔化和冷却的过程。
模具温控系统通常包括模具加热和冷却装置,通过控制加热和冷却介质的流动和温度,可以控制模具的温度。
塑胶模具的基本结构.

2015—20
20—3020—30
30—4030—40
﹥4050
五、藏CORE(内模料深度28mm以上,前后模内模料厚度与制品的平面投影面积有关,一般制品可参考下表,经验数值选定。CORE料边至回针应有10mm距离。
制品平面投影面积前模内模料厚度A+型腔深度后模内模料厚度B+型腔深度
C.分流道的斷面形狀及尺寸大小﹐應根據塑件的成型體積﹐塑件壁厚﹐塑件形狀﹐所用塑
料工藝特性﹐注射速率﹐分流道長度等因素來確定。
2.分流道的布置形式有平衡式進料和非平衡式進料兩種形式。平衡式進料就是保証各個進料口同時均衡地進料﹐非平衡式進料就是各個進料口不能同時均衡地進料﹐一般要做模流分析來進行評估。
(1.其作用主要為﹕
A.使模具安裝時進入定位孔方便而在注塑機上很好地定位與注塑機噴嘴孔吻合﹐并能經受塑料的反壓力﹐不致被推出模具
B.作為澆注系統的主流道﹐將料筒內的塑料過渡到模具內﹐保証料流有力暢通地到達型腔﹐在注射過程中不應有塑料溢出﹐同時保証主流道凝料脫出方便。
(2結構形式有整體式和分體式
整體式﹕即台肩與構成主流道部份做成一體
当模胚阔度在250mm(包括250mm以下时,用工字型模胚口型,模胚阔度在250—350 mm时,用直力有面板模胚(T型。模胚阔度在400mm以上并且有行位时用直力有面板模胚T型,没有行位时用直力无面板模胚(H型有力模胚必须加工W25mm×H20mm码
模坑,底面板必须有码模孔(中心距为“7、10、14”,中心“7、10”
(三.澆口
1.定義﹕澆口又稱進料口或內流道。它是分流道與塑件之間狹窄的部份﹐也稱澆注系統最短小的部份﹔
2.作用﹕能使分流道輸送過來的熔融塑料的流速產生加速度﹐形成理想的流態﹐順序﹐并速速地充滿型腔﹐同時還起著封閉型腔防止熔料倒流的作用﹐并在成型后便于使澆口與塑件分離。
塑胶模具结构基础知识

塑胶模具结构基础知识一、引言塑胶模具是工业生产中常用的一种工具,用于制造各种塑胶制品。
它的结构是非常重要的,直接影响到塑胶制品的成型效果和质量。
本文将介绍塑胶模具结构的基础知识,包括模具的组成部分、常见的模具结构形式以及模具的工作原理等。
二、塑胶模具的组成部分1. 模具座:模具座是模具的基础部分,用于支撑和固定模具的其他部分。
它通常由铸铁或铝合金等材料制成,具有足够的强度和刚性。
2. 上模板:上模板是模具的上部,用于承受注塑机的顶出力和模具的各种动作力。
它通常由优质的工具钢制成,具有高硬度和耐磨性。
3. 下模板:下模板是模具的下部,用于承受注塑机的射出力和模具的各种定位力。
它的结构和材料与上模板类似。
4. 滑块:滑块是模具中的一个可移动部件,用于实现模具的顶出动作。
它通常由铜合金或钢制成,具有良好的耐磨性和低摩擦系数。
5. 模腔:模腔是模具中的一个空腔,用于形成塑胶制品的外形。
它的形状和尺寸应与所需的塑胶制品相匹配。
6. 模芯:模芯是模具中的另一个空腔,用于形成塑胶制品的内部结构。
它的形状和尺寸也应与所需的塑胶制品相匹配。
7. 导柱和导套:导柱和导套用于实现模具的定位和导向,以确保模具的准确定位和运动的精度。
8. 射嘴:射嘴是连接注塑机和模具的部件,用于将熔化的塑胶注入模腔或模芯中。
9. 冷却系统:冷却系统用于控制模具温度,以确保塑胶制品成型的质量。
它通常由冷却水道组成,通过冷却水的流动来吸收和带走热量。
三、常见的模具结构形式1. 单模:单模是最简单的模具结构形式,只有一个模腔和一个模芯。
它适用于制造单个塑胶制品。
2. 多腔模:多腔模具具有多个模腔和模芯,可以同时制造多个塑胶制品。
它的生产效率高,但模具结构复杂。
3. 套模:套模由一对上下模组成,上模具有模腔,下模具有模芯。
它适用于制造中空或多层塑胶制品。
4. 滑动模:滑动模具的模腔和模芯都可以在模具中滑动,以实现复杂形状的塑胶制品的成型。
5. 侧拉模:侧拉模具的模腔和模芯可以在模具中侧向移动,以实现带有侧壁的塑胶制品的成型。
塑胶模具结构设计要点

塑胶模具结构设计要点塑胶模具是用于制造塑料制品的工具,其结构设计关系到产品的质量、生产效率和成本。
下面是塑胶模具结构设计的要点。
1.模具基座设计:模具基座是模具的基础,承载着整个模具的重量,并提供模具的稳定性。
在设计模具基座时,需要考虑模具的尺寸、重量和运输方式,选择适当的材料和结构,保证模具在使用过程中能够稳定运行。
2.模具导向设计:模具导向是指对模具零件进行定位和导向的设计。
在塑胶模具中,通常采用导柱和导套的方式进行导向。
导向设计的关键是准确的位置和良好的刚性。
导向结构的设计需要考虑模具的复杂程度、精度要求和生产效率,确保模具在成型过程中能够准确地进行导向。
3.模具分型设计:模具分型是指模具零件的分离方式。
在塑胶模具中,常用的分型方式包括平移分型、拉伸分型和旋转分型等。
分型设计的目的是实现模具零件的准确分离和快速排料,避免产品变形和损坏。
在进行分型设计时,需要考虑产品的形状、尺寸和壁厚等因素,并合理选择分型面和顶针的位置和数量。
4.模具冷却设计:塑胶制品的成型过程中需要消耗大量的热量,模具的冷却系统是为了控制模具温度,提高生产效率和产品质量。
在进行冷却设计时,需要合理确定冷却通道和冷却介质的位置和数量,以及冷却器的尺寸和布置方式。
冷却通道的设计应该保证冷却效果良好且均匀,同时尽量减少冷却介质的消耗和时间。
5.模具出产口设计:模具出产口是指产品从模具中取出的通道,也是模具的关键部分之一、在进行出产口设计时,需要考虑产品的形状、结构和尺寸,确定合理的出产口位置和尺寸。
出产口的设计应该保证产品的完整和光滑,避免产品形状的畸变和损伤。
6.模具加工工艺设计:模具加工工艺是指模具零件的加工方式和工艺步骤。
在进行加工工艺设计时,需要考虑模具材料的性质和加工难度,选择适当的机械加工方法和工艺流程。
加工工艺的设计应该保证模具零件的精度和质量,以及加工周期和成本的控制。
7.模具耐磨性设计:塑胶模具在使用过程中会受到摩擦和冲击力的作用,需要具备良好的耐磨性。
塑胶模具结构详解
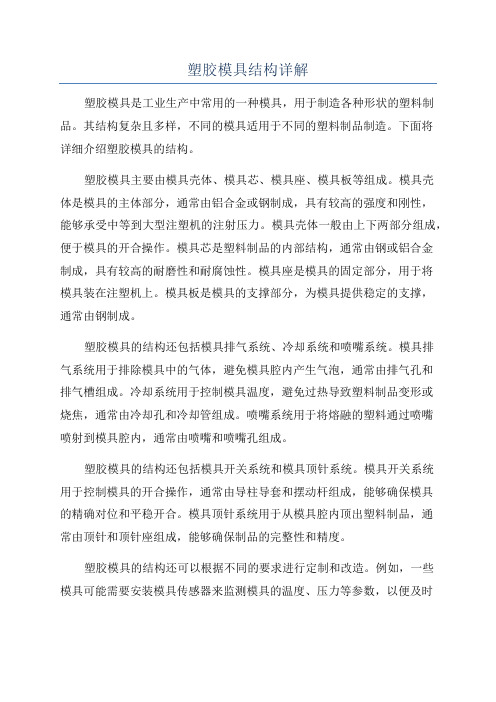
塑胶模具结构详解塑胶模具是工业生产中常用的一种模具,用于制造各种形状的塑料制品。
其结构复杂且多样,不同的模具适用于不同的塑料制品制造。
下面将详细介绍塑胶模具的结构。
塑胶模具主要由模具壳体、模具芯、模具座、模具板等组成。
模具壳体是模具的主体部分,通常由铝合金或钢制成,具有较高的强度和刚性,能够承受中等到大型注塑机的注射压力。
模具壳体一般由上下两部分组成,便于模具的开合操作。
模具芯是塑料制品的内部结构,通常由钢或铝合金制成,具有较高的耐磨性和耐腐蚀性。
模具座是模具的固定部分,用于将模具装在注塑机上。
模具板是模具的支撑部分,为模具提供稳定的支撑,通常由钢制成。
塑胶模具的结构还包括模具排气系统、冷却系统和喷嘴系统。
模具排气系统用于排除模具中的气体,避免模具腔内产生气泡,通常由排气孔和排气槽组成。
冷却系统用于控制模具温度,避免过热导致塑料制品变形或烧焦,通常由冷却孔和冷却管组成。
喷嘴系统用于将熔融的塑料通过喷嘴喷射到模具腔内,通常由喷嘴和喷嘴孔组成。
塑胶模具的结构还包括模具开关系统和模具顶针系统。
模具开关系统用于控制模具的开合操作,通常由导柱导套和摆动杆组成,能够确保模具的精确对位和平稳开合。
模具顶针系统用于从模具腔内顶出塑料制品,通常由顶针和顶针座组成,能够确保制品的完整性和精度。
塑胶模具的结构还可以根据不同的要求进行定制和改造。
例如,一些模具可能需要安装模具传感器来监测模具的温度、压力等参数,以便及时调整生产过程。
一些模具还可能需要添加模穴和浇口,以便制造具有复杂形状的塑料制品。
总之,塑胶模具的结构复杂且多样,根据不同的塑料制品和生产要求,模具的结构也会有所不同。
了解和掌握塑胶模具的结构对于生产和使用塑料制品具有重要意义,可以提高生产效率和产品质量。
- 1、下载文档前请自行甄别文档内容的完整性,平台不提供额外的编辑、内容补充、找答案等附加服务。
- 2、"仅部分预览"的文档,不可在线预览部分如存在完整性等问题,可反馈申请退款(可完整预览的文档不适用该条件!)。
- 3、如文档侵犯您的权益,请联系客服反馈,我们会尽快为您处理(人工客服工作时间:9:00-18:30)。
塑料模具结构
一.设计注射模具应考虑的问题:
1.了解塑料熔体的流动行为,考虑塑料在流道和型腔各流动的阻力,流动速度,校验最大流动长度.根据塑料在模具内流动方向(即充模顺序),考虑塑料在模具内重新熔合和模腔原有空气导出的问题.
2.考虑冷却过程中塑料收缩及补缩问题.
3.通过模具设计来控制塑料在模具内结晶.取向和改善制品的内应力.
4.进浇点分型面的选择问题
5.制件的横向分型抽芯及顶出的问题.
6.模具的冷却或加热问题.
7.模具有关尺寸与所用注射机的关系,包括与注射机的最大注射量.锁模力.装模部分的尺寸等的关系.
8.模具总体结构和零件形状要简单合理,模具应具有适当的精度.光洁度.强度和刚度,易于制造和装配
二.注射模具的典型结构
1.成型零件
型腔是直接成型,塑料制件的部分通常由公模仁,母模仁组成.
2.浇注系统.
将塑料由少射机喷嘴引向型腔的流道称为浇注系统,由主流道.分流道.浇口.
冷料井所组成.
3.导向部分
为确保动模与定模合模时准确对中面设导向零件.通常有:导柱(GP).定位块.顶出导柱(EGP)等
4.分型抽芯机构
带有外侧凹或侧孔塑件在被顶出之前,必须先进行侧向分型,才能顺利脱模.常见机构有:滑块(包括母模抽芯滑块,母模爆炸式滑块),斜销等.
5.顶出装置
在开模过程中,将塑件从模具中顶出的装置.常见机构有:顶针.顶管.顶出块.斜销等.
6.冷却加热系统
为了满足注射工艺对模具温度的要求,模具设有冷却或加热系统.一般在模具内开设冷却水道,加热或油类物质.
※水孔直径选取Φ4.Φ6.Φ8.Φ10.Φ12.Φ16… …
※”○”型环(见图6 )
A内压式B外压式
对于较大或大型模具,为防止公模板变形而加设支撑柱.一般要求支撑柱高出模脚0.10~~0.15mm以补偿支撑柱本身受压变形.
9.回位机构
为使上下顶出板回位面设有回位机构
回位机构除回位销(RP)外,还有强制拉回的机构,急回机构
(1)通常RP上装有弹簧(见图#) 装此弹簧的作用就是在弹簧弹力的作用下让上下顶出板迅速回位
弹簧规格一般选轻小荷重或轻重荷重
(2)有时当斜销有靠破或顶针有靠破时而加弹簧于回位销底部.目的是保护顶针或斜销, 或者顶针和斜销碰伤母模面(见图2)选择型号一般为中荷重或重荷重
1 ‧GP的作用:
1.使固定侧与可动侧精确定位。
2.支承模具重量。
3.保护模仁
2‧GP材质SUJ2;热处理HRC60°±2(高频淬火)。
3.GP规格及配合要求。
(超级链接GP标准件)
4.GP直径及位置的选取。
(超级链接GP直径及位置)
5.GP配置形式及使用场合。
(如下图)
使用A型衬套使用B型衬套公模板深及大型便于取成品
一般场合下模板深减小衬模具母模仁落差大
套配合长度增加模具强度防止导注油污沾上成品
6.GP长度的确定。
(如下图)
高出成品面
15~25MM左右高出斜撑销※RP的配置要求:(RP的作
用:使顶出板回位)
1.模具需自动生产
时一般要在RP下装弹簧,如图一所示:弹簧规
格为TR型。
(超级链接TR弹簧规格)
注:弹簧安装要求
A‧在作动前状态下,弹簧预压量取5~10MM。
B‧如需先回位情况下,弹簧预压量取10MM以上。
2.模具有斜销机构且斜销无靠破时,RP下可不装弹簧,以防止成品被
斜销拉回。
如图二所示:
3.模具有斜销机构且斜销有靠破时,RP底部装弹簧以保护斜销靠破面。
如图三所示:
4.模具装有顶板导柱(EGP)时,RP在各板之间均逃料。
如图四所示:
3‧RP材质------SUJ2;热处理HRC60°±2(高频淬火)。
4‧RP规格(超级链接RP标准件)。
图一图二图三图※EFP的配置要求
1‧EGP的作用:
导向顶出板运动,防止顶出板受力不均而顶出不平衡。
2‧EGP的材质------SUJ2;热处理HRC60°±2(高频淬火)。
3‧EGP规格及配合要求。
(超级链接EGP标准件)
4‧EGP直径的选取。
EGP直径大小与RP直径大小一致。
5‧
EGP的装配形式及使用场合。
(如
下图)
一般模具小模具模温高及压铸模6‧当模具装有EGP时,RP在各模板均逃料。
(超级链接RP配置要求)※STP的配置要求
1‧STP的作用。
1.减少顶出板与下固定板接触面积,易条整顶出板平面度。
2.防止顶出板与下固定板直接接触。
2‧STP材质-----S45C,热处理HRC40°~45°
3‧STP规格(超级链接)。
4‧STP位置的确定。
A回位梢(RP)下必装STP,因受力最大,防止变形。
(如图一):
B STP避免与其它零件干涉,如SP、EGP、K.0孔及顶管。
5‧STP数量的确定。
(如图二)
图
1 图
2 图三
注:大型模具需在中间加STP ,以增加下顶出板的支点,防止顶板变形。
(如图三) 6‧STP 安装形式。
(如下图):
易取下,可 单独
加
工,
不易取下,一般用在小
大型模具建义使用此STP 。
型
模具中可整体加工。
※KO 孔的规格 1‧K.O 孔平面布
置图如下:
注:A 型K.O 孔=Φ40; B 型K.O 孔=Φ60
2‧K.O 孔的中心位置要与注口中心一致。
3‧模具较大且斜销时要装拉回机构
五.三板模
1. 三板模结构介绍(见附图)
2. 三板模的开模顺序
合模
射出成型
保压 开模 B 与C 分开A 与B 分开
C 与
D 分开.
3. 小拉杆的行程确定
4. 大拉杆的行程确定。