树脂砂工艺
树脂砂工艺流程

树脂砂工艺流程树脂砂工艺是一种常用于铸造行业的工艺,它通过在砂型中加入树脂粘结剂来提高砂型的强度和耐磨性。
树脂砂工艺流程通常包括模具准备、树脂砂制备、模具浇注、模具固化和砂型处理等步骤。
一、模具准备模具准备是树脂砂工艺的第一步,它主要包括选材、设计和制作模具。
首先需要根据铸件的形状和尺寸选择合适的模具材料,常用的有铸铁、钢和铝等。
然后根据铸件的要求进行模具的设计,考虑到铸件的结构和形状,确定模具的形式和尺寸。
最后,根据设计的模具图纸进行模具的制作,包括切割、组装、加工和调整等步骤。
二、树脂砂制备树脂砂制备是树脂砂工艺的核心步骤,它主要包括树脂粘结剂的制备和砂粒的处理。
树脂粘结剂是树脂砂的主要组成部分,它通过提供粘结力来使砂粒聚结在一起。
树脂粘结剂的制备包括将树脂颗粒与固化剂混合,并加热使其固化成块。
砂粒的处理包括清洗、筛分和干燥等步骤,以确保砂粒的质量和干燥度。
三、模具浇注模具浇注是树脂砂工艺的下一步,它主要是将树脂砂填充到模具中,并将铸液浇注到模具中。
在浇注过程中,需要注意树脂砂的填充均匀性和浇注速度的控制。
填充不均匀会导致砂型强度的差异,而浇注速度过快会引起气泡和缺陷的产生。
四、模具固化模具固化是树脂砂工艺的重要步骤,它是指树脂砂在模具中固化成型。
固化的过程中,树脂粘结剂会发生化学反应,使树脂砂变得坚硬并具有一定的强度。
树脂砂的固化时间通常是根据树脂粘结剂的性质和铸件的要求确定的,一般需要在一定的温度和时间条件下进行。
五、砂型处理砂型处理是树脂砂工艺的最后一步,它主要是对固化后的砂型进行处理,以获得符合要求的铸件表面和尺寸。
砂型处理包括除砂、修整和表面处理等步骤。
除砂是将砂型外部的砂粒去除,修整是对铸件的尺寸进行修整,表面处理是对铸件表面进行清理和修饰。
树脂砂工艺流程是一个较为复杂的工艺过程,通过模具准备、树脂砂制备、模具浇注、模具固化和砂型处理等步骤,可以获得质量较好的铸件。
树脂砂工艺具有工艺灵活、生产周期短、成本较低等优点,在铸造行业中得到了广泛的应用。
不锈钢铸件的树脂砂工艺

不锈钢铸件的树脂砂工艺
不锈钢铸件可以采用树脂砂工艺进行制造。
树脂砂工艺是一种常用的铸造工艺,适用于制造复杂形状和高精度要求的铸件。
树脂砂是由石英砂和树脂粘结剂混合而成的一种铸造材料。
树脂砂具有良好的流动性,能够填充铸型中的细小空隙,并能够保持良好的细化性能。
具体的树脂砂工艺流程如下:
1. 铸型制备:根据产品图纸和要求,制备出铸型。
铸型可以通过手工或数控机床加工得到。
2. 涂覆剂处理:在铸型内部涂覆一层涂覆剂,以提高铸件的表面质量并防止树脂与铸型粘结。
3. 砂芯制备:根据需要,在铸型中放置砂芯,用于形成产品的内部空腔或管道。
4. 硬化剂处理:将树脂砂放入铸型中,并在适当的位置注入硬化剂,以固化树脂。
5. 硬化和退模:经过一定的时间后,树脂砂会完全硬化。
然后将铸型反转,从中取出树脂砂,并得到铸件。
6. 铸件加工:对铸件进行切割、修整、打磨等加工工序,使其达到所需的尺寸和表面质量要求。
通过树脂砂工艺,可以制造出高精度、复杂形状的不锈钢铸件。
该工艺具有工艺灵活、成本低廉、生产效率高等优点,适用于中小型不锈钢铸件的生产。
树脂砂工艺流程
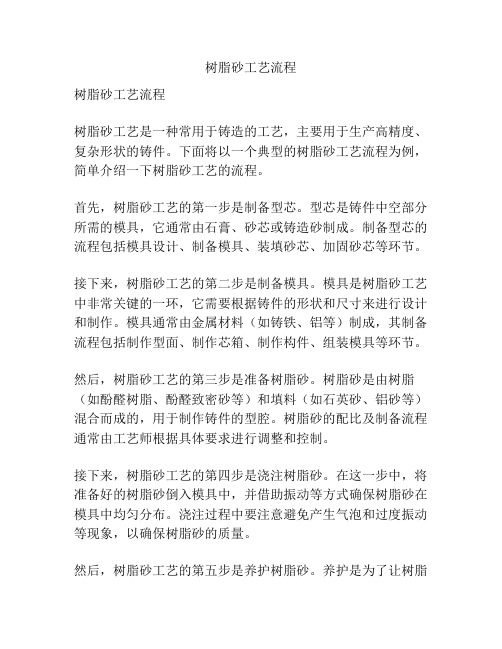
树脂砂工艺流程树脂砂工艺流程树脂砂工艺是一种常用于铸造的工艺,主要用于生产高精度、复杂形状的铸件。
下面将以一个典型的树脂砂工艺流程为例,简单介绍一下树脂砂工艺的流程。
首先,树脂砂工艺的第一步是制备型芯。
型芯是铸件中空部分所需的模具,它通常由石膏、砂芯或铸造砂制成。
制备型芯的流程包括模具设计、制备模具、装填砂芯、加固砂芯等环节。
接下来,树脂砂工艺的第二步是制备模具。
模具是树脂砂工艺中非常关键的一环,它需要根据铸件的形状和尺寸来进行设计和制作。
模具通常由金属材料(如铸铁、铝等)制成,其制备流程包括制作型面、制作芯箱、制作构件、组装模具等环节。
然后,树脂砂工艺的第三步是准备树脂砂。
树脂砂是由树脂(如酚醛树脂、酚醛致密砂等)和填料(如石英砂、铝砂等)混合而成的,用于制作铸件的型腔。
树脂砂的配比及制备流程通常由工艺师根据具体要求进行调整和控制。
接下来,树脂砂工艺的第四步是浇注树脂砂。
在这一步中,将准备好的树脂砂倒入模具中,并借助振动等方式确保树脂砂在模具中均匀分布。
浇注过程中要注意避免产生气泡和过度振动等现象,以确保树脂砂的质量。
然后,树脂砂工艺的第五步是养护树脂砂。
养护是为了让树脂砂在经历一定时间的固化后达到最佳的物理和化学性能。
树脂砂的养护时间通常由具体的树脂类型和环境条件决定。
最后,树脂砂工艺的最后一步是烘烤铸件。
在烘烤过程中,树脂砂中的树脂将会挥发,从而形成空腔,以适应铸造过程中的热胀冷缩等变形。
烘烤的温度和时间通常由具体的树脂类型和铸件的尺寸来决定,以保证铸件的质量。
以上就是一个典型的树脂砂工艺流程介绍。
树脂砂工艺具有制备过程简单、生产效率高、铸件质量好等特点,广泛应用于汽车、航空航天、军工等行业的铸造工艺中。
随着科技的不断发展,树脂砂工艺也在不断创新和改进,以满足更高要求的铸件生产。
树脂砂铸造工艺流程

树脂砂铸造工艺流程树脂砂铸造是一种常见的金属铸造工艺,它使用树脂砂作为型砂,通过模具将熔化的金属注入,然后在型砂中凝固成型。
这种工艺适用于生产各种大小和形状的铸件,具有成本低、生产效率高等优点。
下面将详细介绍树脂砂铸造的工艺流程。
首先,准备模具。
树脂砂铸造的模具通常由两部分组成,分别是上模和下模。
上模和下模的结构要与待生产铸件的形状相适应,可以通过手工或数控机床加工而成。
在模具制作完成后,需要进行表面处理,以保证铸件表面的光洁度和精度。
接下来,准备树脂砂。
树脂砂是由石英砂和树脂粘结剂混合而成的,其比例和配方会根据不同的铸件形状和要求进行调整。
在使用树脂砂前,需要将其加热至一定温度,以提高其流动性和粘结性。
然后,进行模具装配。
将上模和下模分别安装在铸造设备上,然后在上模中放入芯子,再将上下模合并成型。
在合模过程中,需要注意模具的对位和密封,以防止金属液体泄漏。
接着,进行浇注。
将金属熔化后的液态金属倒入模具中,通过重力或压力使其充满整个模腔。
在浇注过程中,需要控制金属液体的温度和流动速度,以确保铸件的质量。
随后,待铸件冷却凝固。
在金属液体充满模腔后,需要等待一定时间,让金属冷却凝固成型。
冷却时间的长短会受到铸件厚度和金属种类的影响。
最后,进行脱模和后处理。
待铸件完全冷却后,可以进行脱模。
脱模后,需要对铸件进行去毛刺、修磨等后处理工艺,以提高其表面粗糙度和尺寸精度。
总的来说,树脂砂铸造工艺流程简单明了,但在实际生产中需要严格控制各个环节,以确保铸件质量和生产效率。
希望本文对树脂砂铸造工艺有所帮助,谢谢阅读。
《树脂砂型成形工艺》课件
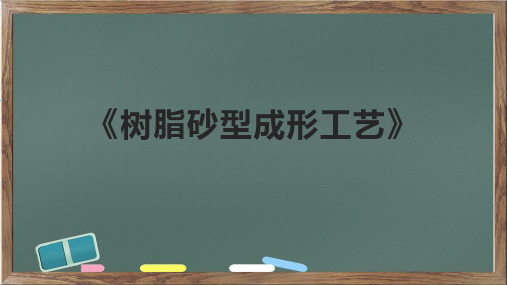
应用: 造型(砂型)—— 中大铸件,质量要求高的小铸件 制芯(砂芯)—— 成批大量生产的铸件
应用: 造型(砂型)—— 中大铸件,质量要求高的小铸件 制芯(砂芯)—— 成批大量生产的铸件
应用: 造型(砂型)—— 中大铸件,质量要求高的小铸件 制芯(砂芯)—— 成批大量生产的铸件
应用: 造型(砂型)—— 中大铸件,质量要求高的小铸件 制芯(砂芯)—— 成批大量生产的铸件
a).湿混:砂 部分水 混匀 粘土 煤粉 混1-2分钟水
b).干混:砂 粘土 煤粉
混1-2分钟 水
混至要求紧实率出碾 调匀 松砂 造型机
湿型砂的制备
混砂效率
起粘结作用的粘土量 有效粘土含量
100 %
ቤተ መጻሕፍቲ ባይዱ测定方法:
型砂预定混碾时间的抗 压强度 型砂预定混碾时间延长 5分钟的抗压强度 100 %
湿型砂的制备 (3) 砂处理工艺流程
以树脂作为粘结剂的型(芯)砂称为树脂砂。 树脂砂成形工艺主要有:
热法覆膜树脂砂(也称壳型 / 壳芯) 热芯盒树脂砂 冷芯盒树脂砂 呋喃树脂自硬砂
应用: 造型(砂型)—— 中大铸件,质量要求高的小铸件 制芯(砂芯)—— 成批大量生产的铸件
应用: 造型(砂型)—— 中大铸件,质量要求高的小铸件 制芯(砂芯)—— 成批大量生产的铸件
应用: 造型(砂型)—— 中大铸件,质量要求高的小铸件 制芯(砂芯)—— 成批大量生产的铸件
应用: 造型(砂型)—— 中大铸件,质量要求高的小铸件 制芯(砂芯)—— 成批大量生产的铸件
应用: 造型(砂型)—— 中大铸件,质量要求高的小铸件 制芯(砂芯)—— 成批大量生产的铸件
应用: 造型(砂型)—— 中大铸件,质量要求高的小铸件 制芯(砂芯)—— 成批大量生产的铸件
树脂固化砂工艺

树脂固化砂工艺工艺, 树脂, 固化1. 加热硬化法此法系指型芯本体经过外部加热源进行加热,使型芯砂在一定温度和时间下固化成型的一种工艺。
目前在铸造生产中广泛应用的有:壳型法和热芯盒法两种。
壳型法是一种开发最早、发展最快、应用甚广的高效造型、制芯工艺。
由于覆膜砂的流动性、充型性和存放性均好,强度大、溃散性好,被汽车行业广泛应用于大批量生产各种结构复杂、质量要求高的型芯。
热芯盒比壳型开发晚15年,由于它的型、芯砂制备简单,成型温度低,硬化速度快,在生产中也得到了应用,鉴于其型砂流动性差、存放性不好,吸湿性很大,含氮量较高,限制了它的应用,目前国外已开发了新型热芯盒树脂,效果较好,国内也在试用。
由于这两种工艺操作方法基本相似,下面仅介绍壳型法。
(1)壳型用原材料及其特性壳型用原材料主要是覆膜砂,它是由硅砂、热塑性酚醛树脂、乌洛托品硬化剂、硬脂酸钙润滑剂及其他附加物等材料,在专门的混制设备上热法混制而成,铸造厂家可根据铸件的种类和不同结构的要求来选用,目前市场上可提供的覆膜砂系列产品的性能见表1。
表1 覆膜砂系列产品的性能(2)壳型、芯的制造工艺及其设备壳型、芯的制作方法一般有两种:翻斗法和吹砂法。
翻斗法适用于壳型制作,而吹砂法多用于壳芯生产。
吹砂法壳芯机又可分为底吹式和项吹式两大类。
底吹式壳芯机制芯时,芯砂由底部吹入芯盒,吹芯压力为0.4~05MPa,吹砂时间为15~35s。
由于芯砂由底部吹入芯盒,充填情况不如顶吹式理想,故一般适用于外形简单的壳芯。
顶吹式壳芯机制芯时,芯砂由芯盒顶部吹入,充填情况较好,但整机结构复杂,常用于结构较复杂的壳芯制造,其吹芯压力为0.l~0.3MPa,吹砂时间为3~8s。
壳芯制造过程如下:把芯盒加热至210~250℃,吹入覆膜砂,这时覆膜砂上树脂受热融化、结壳后,翻转180º,使芯盒自动左右摇摆数次,排放出未固化的砂子,翻斗复位,壳型、芯继续硬化2~3min,便可顶出制好的壳型、芯。
树脂砂生产工艺

树脂砂生产工艺
树脂砂生产工艺是一种常用于铸造行业的铸造材料,具有良好的流动性和压实性能,可用于生产各种铸件。
下面介绍一下树脂砂的生产工艺。
树脂砂生产工艺主要包括原料准备、砂型制备和固化等步骤。
首先是原料准备。
树脂砂的主要原料包括树脂、固化剂和填充料。
树脂一般选择无毒无味且具有一定黏度的树脂,如酚醛树脂、酚醛树脂酚醛相间树脂等。
固化剂一般选择硫酸铵或氯化胺等,填充料一般选择细砂或锆砂等。
接下来是砂型制备。
首先将树脂和固化剂混合均匀,然后将填充料加入到树脂中,搅拌均匀。
接着将混合好的砂料放入模具中,通过震动或振动来排气和压实,使砂型紧密结实。
在制备过程中还需要设置好适当的温度和湿度,以确保砂型的质量。
最后是固化。
将制备好的砂型放置在恒温恒湿的环境下,树脂和固化剂通过化学反应进行固化。
此时需要根据不同的树脂砂,控制好固化时间,一般在几十分钟到几小时之间。
固化后的砂型具有一定的强度和硬度,可以用于铸件的生产。
树脂砂生产工艺具有许多优点。
首先,树脂砂具有良好的流动性,能够完全填充模具的细小空腔,使得铸件表面光滑均匀。
其次,树脂砂具有压实性能,能够形成较为坚固的砂型,不易发生变形和破裂。
另外,树脂砂的固化时间短,生产效率高,适用于大批量生产。
总之,树脂砂生产工艺是一种常用于铸造行业的铸造材料,具有良好的流动性和压实性能,通过原料准备、砂型制备和固化等步骤可以生产出质量可靠的砂型,用于铸件的生产。
它的应用方便,生产效率高,被广泛应用于汽车、机械、航空等领域。
树脂砂工艺流程

树脂砂工艺流程一、树脂砂概述树脂砂是一种常用于铸造的模具材料,由树脂和填充料组成。
其优点包括制备简单、成本低、表面光滑、精度高等,因此在工业生产中得到广泛应用。
下面将介绍树脂砂的工艺流程。
二、原料准备1.树脂选择:树脂砂的主要成分是树脂,常用的有酚醛树脂、酚醇树脂和酚甲醛树脂等。
选择树脂时需要考虑铸件的材质、形状、质量要求等因素。
2.填充料选择:填充料主要用于增加树脂砂的强度和耐热性。
常用的填充料有石英砂、石英粉、锆砂等。
填充料的选择要根据铸件的特点和使用环境来确定。
3.添加剂选择:树脂砂中还需要添加一些辅助材料,如固化剂、抗氧化剂、润滑剂等。
这些添加剂的选择要根据树脂砂的具体要求来确定。
三、树脂砂制备1.树脂与填充料的混合:将树脂和填充料按照一定比例混合,可以采用手工搅拌或机械搅拌的方式。
混合的目的是使树脂和填充料充分均匀地混合在一起。
2.添加剂的加入:根据需要,将适量的固化剂、抗氧化剂、润滑剂等添加到树脂砂中,并进行充分搅拌,使其均匀分散。
3.加水调湿:树脂砂在使用前需要进行湿润处理,以提高其粘结性和塑性。
通常是将适量的水加入到树脂砂中,然后搅拌直至均匀吸湿。
四、模具制备1.模具设计:根据铸件的形状和尺寸,设计相应的模具。
模具的设计要考虑铸件的缩短率、浇注系统、冷却系统等因素。
2.模具制作:根据模具设计图纸,选择合适的材料进行模具制作。
常用的模具材料有铁、铝、石膏等。
制作过程包括模板制作、模具拼装、模具修整等环节。
3.模具涂覆:树脂砂需要涂覆在模具表面,以便更好地复制铸件的形状。
涂覆的方式可以是手工涂覆或机械涂覆,涂覆的厚度要根据铸件的要求来确定。
五、铸造操作1.模具准备:将涂覆好树脂砂的模具准备好,包括清理模具表面、涂抹脱模剂等。
2.浇注铸件:将熔融金属倒入模具中,填充整个空腔,保持一定的冷却时间,待金属凝固后,即可取出铸件。
3.清理铸件:将铸件从模具中取出后,进行去砂、去毛刺、修整等工序,使其达到要求的尺寸和表面质量。
铸造树脂砂工艺流程

铸造树脂砂工艺流程一、树脂砂的原料准备。
树脂砂的主要原料那就是树脂和砂啦。
砂的话,得选择合适的粒度和形状的哦。
就像我们挑东西一样,不能随便抓一把砂就用。
砂要干净,不能有太多杂质,要是砂里面混着乱七八糟的东西,那铸造出来的东西质量可就没法保证啦。
树脂呢,它可是很关键的成分,就像做菜的调料一样重要。
不同类型的树脂有不同的性能,要根据具体的铸造要求来选。
而且树脂的比例也要调配好,多了少了都不行,多了可能会太黏,少了又可能粘不住砂,这就像我们做蛋糕放面粉和鸡蛋一样,比例得刚刚好。
二、混砂过程。
把树脂和砂混在一起可是个技术活。
这就好比把两种不同性格的小伙伴凑在一起玩,得让它们和谐相处。
混砂的时候,设备得运作得恰到好处。
要是混得不均匀,那有些地方的砂可能树脂多,有些地方树脂少,这就像我们穿衣服,一块厚一块薄的,多不舒服呀。
在混砂过程中,还得注意温度和湿度的影响。
温度太高或者湿度太大,都可能影响树脂和砂的混合效果。
比如说在夏天特别热的时候,树脂可能变得太稀,就不容易均匀地裹在砂粒上了。
而湿度大的时候,砂可能会吸收太多水分,这就像砂喝饱了水,就不想跟树脂好好配合了。
三、造型过程。
混好的树脂砂就要用来造型啦。
这就像是用沙子堆城堡一样,不过要比堆城堡复杂得多。
工人师傅得把树脂砂按照模具的形状填进去,要填得紧实又均匀。
不能这边松松垮垮,那边又硬邦邦的。
如果填得不好,铸造出来的东西就会变形。
而且在造型的时候,还得考虑到排气的问题。
就像我们住在房子里要通风一样,树脂砂里面要是有空气排不出去,在铸造的时候就会产生气泡,那铸造出来的产品表面就不光滑,像长了痘痘一样,多难看呀。
四、硬化过程。
造型完成后,就要让树脂砂硬化啦。
这个过程就像是让刚刚捏好的泥人变得坚固起来。
硬化的速度和质量取决于很多因素呢。
比如树脂的种类、环境温度、硬化剂的用量等等。
如果硬化得太快,可能内部还没完全干透,要是硬化得太慢,那就会影响生产效率。
就像我们等蛋糕烤熟一样,时间长了烤焦了,时间短了又没熟,这可得把握好度。
树脂砂工艺很全
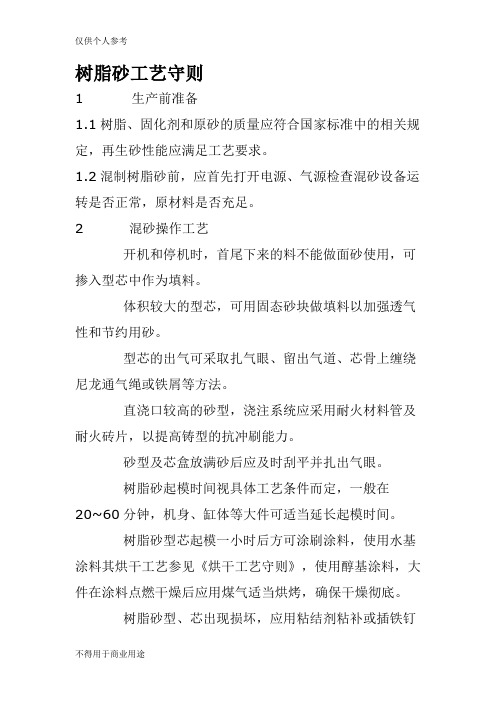
树脂砂工艺守则1 生产前准备1.1树脂、固化剂和原砂的质量应符合国家标准中的相关规定,再生砂性能应满足工艺要求。
1.2混制树脂砂前,应首先打开电源、气源检查混砂设备运转是否正常,原材料是否充足。
2 混砂操作工艺开机和停机时,首尾下来的料不能做面砂使用,可掺入型芯中作为填料。
体积较大的型芯,可用固态砂块做填料以加强透气性和节约用砂。
型芯的出气可采取扎气眼、留出气道、芯骨上缠绕尼龙通气绳或铁屑等方法。
直浇口较高的砂型,浇注系统应采用耐火材料管及耐火砖片,以提高铸型的抗冲刷能力。
砂型及芯盒放满砂后应及时刮平并扎出气眼。
树脂砂起模时间视具体工艺条件而定,一般在20~60分钟,机身、缸体等大件可适当延长起模时间。
树脂砂型芯起模一小时后方可涂刷涂料,使用水基涂料其烘干工艺参见《烘干工艺守则》,使用醇基涂料,大件在涂料点燃干燥后应用煤气适当烘烤,确保干燥彻底。
树脂砂型、芯出现损坏,应用粘结剂粘补或插铁钉用树脂砂填补固化后磨平。
型芯起模后,一般应经6小时达到一定强度后方可浇注。
每个工作班结束后必须清理搅拌槽和叶片。
不定期检查混砂设备定量是否准确。
3 树脂砂工艺性能检查树脂型、芯砂性能检验规定为每班一次,每周可检查四次,在常温下要求:一小时抗拉强度≥0.08Mpa,两小时抗拉强度>0.2 Mpa,二十四小时抗拉强度>0.4 Mpa.再生砂性能检验为每周一次,要求灼减度<2.5%,含泥量<1.5%,发气量<15ml。
树脂砂铸件生产操作工艺规程1 目的为规范树脂砂铸件的生产操作过程,严格执行操作工艺,减少因违反工艺或操作不当产生的废品和降低的铸件生产成本,特制定本生产操作工艺规程。
2 适用范围本工艺规程适用于公司内所有树脂砂铸件的生产全过程和与之相关的各类操作人员。
3 工艺规程3.1 主要原材料的技术要求或规格粒度:40/70目(中大件)或50/100目(一般件);化学成分:SiO2 >90% 、含泥量< 0.2%~0.3% 、含水量<0.1~0.2%;微粉含量(140目筛以下) ≤0.5~1.0%、耗酸值<5ml 、灼减量<5、粒型:圆形或多角形。
树脂砂造型工艺流程

树脂砂造型工艺流程1.模具准备:首先,需要准备模具,这可以通过两种方式完成。
一种是使用现有的模具,另一种是制作新的模具。
在使用现有的模具之前,需要对其进行检查和修复,以确保其完好无损。
如果需要制作新的模具,可以使用准确的模型来制作模具,也可以使用3D打印技术来制作模具。
2.填充树脂砂:接下来,将树脂砂填充到模具中。
树脂砂通常是一种具有良好流动性和一定强度的粘稠液体。
将树脂砂倒入模具时,可以采用手动或自动的方式。
填充树脂砂时需要注意均匀填充,并且要避免气泡和缺陷的产生。
3.模具振动:填充树脂砂后,需要对模具进行振动。
振动可以帮助树脂砂在模具中均匀分布,并排除可能存在的气泡。
振动时间和频率应根据树脂砂的特性和模具的尺寸来确定。
4.硬化:填充和振动后,树脂砂需要在适当的温度下进行硬化。
硬化的温度和时间取决于所使用的树脂砂的类型。
通常情况下,树脂砂会在几分钟到几小时内变硬。
5.模具分离:硬化后,树脂砂和模型一起形成了模具。
模具通常需要经过分离过程,以分离出模具和模型。
分离可以通过手工或机械的方式完成。
在分离过程中,需要小心操作,以避免损坏树脂砂模具和模型。
6.模型清理:在模具分离后,需要对模型进行清理。
这包括去除可能附着在模型表面的多余树脂砂和任何其他杂质。
清理可以采用机械或化学的方式进行。
清理后的模型应该是干净和光滑的。
7.烘烤:清理后的模型需要经过烘烤过程。
烘烤有两个主要目的:一是去除树脂砂中的残余水分,二是增加模型的强度和耐磨性。
烘烤的温度和时间也取决于所使用的树脂砂的类型。
8.铸造:经过烘烤的模型可以进入下一阶段-铸造。
铸造是将熔化的金属倒入模具中,使其在模型中形成所需的形状。
铸造可以通过多种方式来完成,常见的方法包括重力浇注、压力浇注和真空浇注。
9.冷却和固化:铸造完毕后,需要让模具中的金属冷却和固化。
冷却和固化时间根据所使用的金属的类型和尺寸而有所不同。
在冷却期间,模具应妥善保护,以防止变形或损坏。
树脂砂铸造工艺流程(3篇)
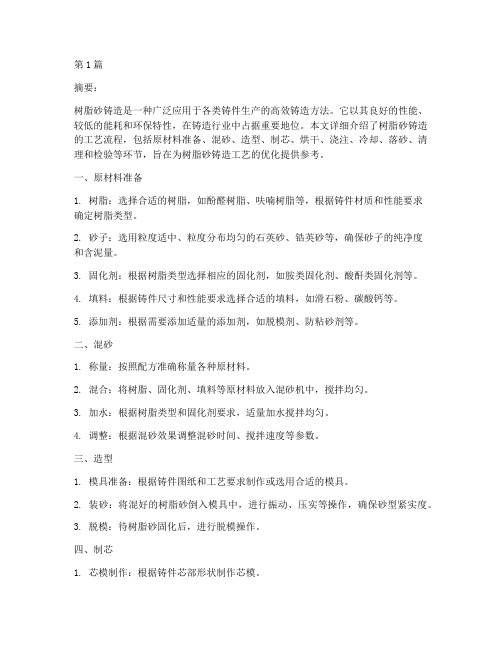
第1篇摘要:树脂砂铸造是一种广泛应用于各类铸件生产的高效铸造方法。
它以其良好的性能、较低的能耗和环保特性,在铸造行业中占据重要地位。
本文详细介绍了树脂砂铸造的工艺流程,包括原材料准备、混砂、造型、制芯、烘干、浇注、冷却、落砂、清理和检验等环节,旨在为树脂砂铸造工艺的优化提供参考。
一、原材料准备1. 树脂:选择合适的树脂,如酚醛树脂、呋喃树脂等,根据铸件材质和性能要求确定树脂类型。
2. 砂子:选用粒度适中、粒度分布均匀的石英砂、锆英砂等,确保砂子的纯净度和含泥量。
3. 固化剂:根据树脂类型选择相应的固化剂,如胺类固化剂、酸酐类固化剂等。
4. 填料:根据铸件尺寸和性能要求选择合适的填料,如滑石粉、碳酸钙等。
5. 添加剂:根据需要添加适量的添加剂,如脱模剂、防粘砂剂等。
二、混砂1. 称量:按照配方准确称量各种原材料。
2. 混合:将树脂、固化剂、填料等原材料放入混砂机中,搅拌均匀。
3. 加水:根据树脂类型和固化剂要求,适量加水搅拌均匀。
4. 调整:根据混砂效果调整混砂时间、搅拌速度等参数。
三、造型1. 模具准备:根据铸件图纸和工艺要求制作或选用合适的模具。
2. 装砂:将混好的树脂砂倒入模具中,进行振动、压实等操作,确保砂型紧实度。
3. 脱模:待树脂砂固化后,进行脱模操作。
四、制芯1. 芯模制作:根据铸件芯部形状制作芯模。
2. 装砂:将混好的树脂砂倒入芯模中,进行振动、压实等操作。
3. 脱模:待树脂砂固化后,进行脱模操作。
五、烘干1. 烘干设备:选用合适的烘干设备,如隧道式烘干炉、电热烘干炉等。
2. 烘干温度:根据树脂类型和固化剂要求,设定合适的烘干温度。
3. 烘干时间:根据烘干温度和树脂砂性能要求,确定烘干时间。
六、浇注1. 浇注设备:选用合适的浇注设备,如地坑浇注、半自动浇注机等。
2. 浇注温度:根据铸件材质和性能要求,设定合适的浇注温度。
3. 浇注速度:根据铸件形状和浇注设备能力,确定浇注速度。
七、冷却1. 冷却方式:采用自然冷却或强迫冷却,如风冷、水冷等。
树脂砂铸造工艺流程
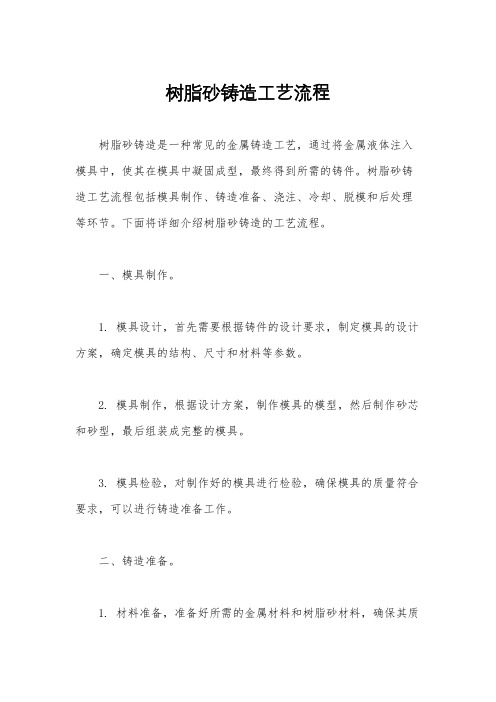
树脂砂铸造工艺流程树脂砂铸造是一种常见的金属铸造工艺,通过将金属液体注入模具中,使其在模具中凝固成型,最终得到所需的铸件。
树脂砂铸造工艺流程包括模具制作、铸造准备、浇注、冷却、脱模和后处理等环节。
下面将详细介绍树脂砂铸造的工艺流程。
一、模具制作。
1. 模具设计,首先需要根据铸件的设计要求,制定模具的设计方案,确定模具的结构、尺寸和材料等参数。
2. 模具制作,根据设计方案,制作模具的模型,然后制作砂芯和砂型,最后组装成完整的模具。
3. 模具检验,对制作好的模具进行检验,确保模具的质量符合要求,可以进行铸造准备工作。
二、铸造准备。
1. 材料准备,准备好所需的金属材料和树脂砂材料,确保其质量符合要求。
2. 设备准备,检查铸造设备的状态,确保设备正常运转,准备好所需的浇注工具和保护设备。
3. 工艺参数确定,根据铸件的要求,确定浇注温度、浇注速度、浇注压力等工艺参数。
三、浇注。
1. 砂型装配,将模具放置在浇注设备上,进行砂型的装配,确保砂型的完整性和稳定性。
2. 预热模具,对模具进行预热处理,以提高模具的表面硬度和耐磨性。
3. 浇注金属,将预热好的金属液体倒入模具中,控制浇注过程中的温度和速度,确保金属液体充分填充模具。
四、冷却。
1. 自然冷却,待金属液体充分填充模具后,等待一定时间,让金属液体在模具中自然冷却凝固。
2. 辅助冷却,对于一些大型或厚壁铸件,可以采用辅助冷却设备,加快冷却速度,避免产生热裂纹。
五、脱模。
1. 模具拆卸,待金属铸件完全冷却后,将模具拆卸,取出铸件和砂芯。
2. 清理铸件,对铸件进行清理和修整,去除表面的砂粒和氧化皮,确保铸件的表面光洁。
六、后处理。
1. 热处理,根据铸件的材料和要求,进行热处理,提高铸件的硬度和强度。
2. 检测,对铸件进行尺寸和质量的检测,确保铸件的质量符合要求。
3. 表面处理,对铸件进行表面处理,如喷砂、喷丸、镀层等,提高铸件的表面质量和耐腐蚀性能。
以上就是树脂砂铸造工艺流程的详细介绍,树脂砂铸造是一种常见的金属铸造工艺,具有生产效率高、成本低、适用范围广等优点,被广泛应用于机械制造、汽车制造、航空航天等领域。
树脂砂工艺流程

树脂砂工艺流程
《树脂砂工艺流程》
树脂砂工艺是一种常用于铸造工艺中的重要方法,它通常用于制造精密铸件和大型铸件。
树脂砂是一种具有优良流动性和耐高温性能的材料,因此在铸造工艺中得到广泛应用。
树脂砂工艺的流程通常包括以下几个主要步骤:模具制备、模型制备、树脂砂制备、浇注和冷却、脱模和后处理。
首先是模具制备,这一步骤通常包括模具设计、模具制造和模具组装。
模具设计是根据铸件的形状和大小来确定模具的结构和尺寸,通常使用CAD软件进行设计。
模具制造则是根据设计图纸来进行,通常使用铸造用砂模具来制作。
接下来是模型制备,这通常包括铸造型芯制备和模型粘接。
铸造型芯是用于形成铸件内部空腔的部分,而模型则是用于形成铸件外部形状的部分。
然后是树脂砂制备,这一步骤通常包括树脂砂配比、混合和造型。
树脂砂通常由树脂、固化剂和填料组成,需要按照一定的配比进行混合,在制备好的树脂砂中进行造型。
接下来是浇注和冷却,这一步骤通常是将熔化的金属倒入树脂砂模具中,并在一定时间内进行冷却,使金属凝固成型。
最后是脱模和后处理,脱模是将铸件从树脂砂模具中取出,然
后进行去除余砂、修磨和清洁等后处理步骤,最终得到成型的铸件。
树脂砂工艺流程,是一个复杂的工艺流程,需要各个步骤之间紧密配合,以保证最终铸件的质量和形状达到要求。
在实际应用中,还需要根据具体铸件的要求和工艺条件来进行相应的调整和优化,以确保生产出满足客户需求的高质量铸件。
树脂砂生产工艺步骤

树脂砂生产工艺步骤嘿,朋友们!今天我要给你们唠唠树脂砂的生产工艺步骤,这可真是个挺有趣的事儿呢。
一、原材料准备这树脂砂生产啊,就像盖房子打地基一样,原材料准备那是相当重要的。
咱先来说说树脂吧。
树脂就像是这个小世界里的胶水,它得是质量好的。
我曾经见过一个小作坊,图便宜买了劣质树脂,那做出的树脂砂啊,简直就是一团糟,就像一个病恹恹的人,啥力气也没有。
所以啊,我们得精心挑选优质的树脂。
再说说砂子,砂子就像是大楼的砖头,它得干净、粒度合适。
要是砂子不干净,里面夹杂着乱七八糟的东西,那做出来的树脂砂就像饭菜里混进了沙子,口感极差,在使用的时候就会出现各种各样的问题。
这时候,就需要有经验的工人师傅来把关了。
我认识的王师傅,他那眼睛就像老鹰一样,一眼就能看出砂子的好坏。
他会抓起一把砂子,在手里搓一搓,然后摇摇头或者点点头。
要是他摇摇头,那这砂子肯定是不行啦。
二、混砂过程原材料准备好了,就开始混砂啦。
这混砂啊,就像是一场热闹的聚会。
把树脂、固化剂还有砂子一股脑儿地放到混砂机里。
这时候,机器就开始轰隆隆地响起来,就像在唱歌一样。
不过这歌可不能乱唱,得按照一定的比例来。
如果树脂放多了,那树脂砂就会太黏,就像糖放多了的糖浆,流都流不动;要是树脂放少了呢,又会像一盘散沙,没有一点凝聚力。
在混砂的时候,操作人员可得小心啦。
小李就是负责混砂的一个年轻小伙子,他每次操作的时候都特别认真。
他会时不时地打开混砂机的观察窗看看里面的情况,嘴里还嘟囔着:“哎呀,这情况看起来还不错呢。
”旁边的老张就会笑着说:“小李啊,可别掉以轻心,这事儿就像走钢丝一样,得时刻保持警惕。
”三、造型和制芯混好的树脂砂就可以进行造型和制芯啦。
这就像是雕塑家开始创作一样。
工人师傅们把树脂砂填充到模具里,然后用工具把它捣实,就像把蛋糕面糊填满蛋糕模具一样。
这个过程可需要耐心了。
我看到过赵师傅做这个,他就像对待自己的孩子一样,轻轻地、慢慢地把树脂砂弄好。
旁边的学徒小王好奇地问:“赵师傅,为啥要这么小心啊?”赵师傅就会笑着说:“这就好比你绣花,一针错了,那整幅画可就毁了。
铸造树脂砂工艺流程

铸造树脂砂工艺流程一、树脂砂是啥呀。
咱先来说说树脂砂是个啥玩意儿。
树脂砂呢,就是在铸造的时候用到的一种特殊的砂。
它可不是那种普通的沙子哦,这里面可是加了树脂这种东西的。
树脂就像是胶水一样,把沙子都黏在一起,这样就可以做出各种形状的模具啦。
你想啊,铸造就是要做出各种形状的东西,像一些机械零件啊什么的,树脂砂就能很好地满足这个要求呢。
二、准备工作可不能少。
在开始整个工艺流程之前,准备工作那是相当重要的。
咱得先把要用的材料都准备好。
这树脂砂的材料主要就是沙子和树脂啦,还有一些添加剂之类的东西。
沙子得选那种颗粒大小合适的,太粗了或者太细了都不行。
就好像我们做饭,米要是选得不好,那做出来的饭肯定也不好吃。
这沙子也是这个道理。
树脂呢,也要根据具体的铸造要求来选,不同的树脂有不同的性能。
添加剂就像是调料一样,虽然用得不多,但是能让整个树脂砂的性能变得更好呢。
然后就是设备的准备啦。
铸造的时候需要用到混砂机,这个机器就是把沙子、树脂和添加剂混合在一起的。
在使用之前,得检查一下混砂机有没有什么问题,就像我们出门之前要检查一下车子一样。
要是混砂机不好好工作,那树脂砂的质量可就没法保证啦。
三、混合的小秘密。
接下来就是把沙子、树脂和添加剂混合在一起的过程啦。
这可有点像我们做蛋糕的时候把面粉、鸡蛋和糖混合在一起的感觉呢。
不过这个过程要更加精确一些。
把这些材料按照一定的比例放进混砂机里面,然后让混砂机开始工作。
这时候,沙子就会和树脂还有添加剂充分地混合在一起。
这个比例可是很重要的,如果比例不对,那做出来的树脂砂可能就太硬或者太软啦。
太软的话,在铸造的时候就没办法保持形状,太硬的话,又可能会出现裂缝之类的问题。
四、造型的时候到喽。
混合好的树脂砂就可以用来造型了。
这个造型的过程就像是我们小时候玩泥巴,把泥巴捏成各种形状一样。
不过树脂砂可不像泥巴那么好捏,得用专门的工具。
工人师傅们会根据要铸造的零件的形状,用模具或者直接用手把树脂砂塑造成合适的形状。
- 1、下载文档前请自行甄别文档内容的完整性,平台不提供额外的编辑、内容补充、找答案等附加服务。
- 2、"仅部分预览"的文档,不可在线预览部分如存在完整性等问题,可反馈申请退款(可完整预览的文档不适用该条件!)。
- 3、如文档侵犯您的权益,请联系客服反馈,我们会尽快为您处理(人工客服工作时间:9:00-18:30)。
树脂砂工艺我要打印 IE收藏放入公文包我要留言查看留言第一章/ 概论1 — 1 自硬呋喃树脂砂的概念自硬呋喃树脂砂的命名来源于英语的Furan No-Bake process,它表示以呋喃树脂为粘结剂,并加入催化剂混制出型砂,不需烘烤或通硬化气体,即可在常温下使砂型自行固化的造型方法。
通常被简称为“冷硬树脂砂”,甚至“树脂砂”。
以下介绍两个基本概念。
一、呋喃树脂的概念由碳原子和其它元素原子(如O、S、N等)共同组成的环叫做杂环、组成杂环的非碳原子叫杂原子。
含有杂环的有机化合物叫做杂环化合物。
所谓“呋喃”,是含有一个氧原子的五员杂环有机化合物,它是表示一族化合物的基本结构总称。
在呋喃系中不带取代基的杂环作为母体,叫做“呋喃”,它的衍生物则根据母体来命名。
呋喃本身在互业上并无什么用途,但它的衍生物——糠醛和糠醇,却是互业上的重要原料,它们是最重要的呋喃衍生物,糠醛学名叫α——呋喃甲醛,糠醇学名叫呋喃甲醇。
它们的分子结构如下:含有糠醇的树脂称为呋喃树脂。
作为铸造粘结剂用的呋喃树脂一般是用糠醇(FA)与尿素、甲醛或苯酚等缩合而成的,如尿醛呋喃树脂(UF/FA)、酚醛呋喃树脂(PF/FA)、酚脲醛呋喃树脂(UPF-FA)和甲醛——糠醇树脂(F/FA)等。
二、呋喃树脂的硬化机理根据呋喃树脂的组成不同,分别可以通过加热、通入硬化气体或添加酸催化剂等方法使其固化。
酸催化(即“自硬”)的呋喃树脂一般糠醇含量都超过50%。
其硬化机构很复杂,现在还未完全弄清楚,但基本的树脂化反应包括了糠醇的第一醇基和呋喃环的第五位氢之间的脱水缩合,此外呋喃环的断裂生成乙酰丙酸,第一醇基间脱水生成醚和醛等等的反应。
图1-1为呋喃树脂粘结剂的成分和代表性的呋喃自硬树脂结构的一例。
•初期阶段1 — 2自硬呋喃树脂砂的优缺点一、自硬呋喃树脂砂具有以下优点:1 .铸件表面光洁、棱角清晰、尺寸精度高。
这是由于树脂砂造型可以排除许多使型(芯)变形的因素。
如:(1)型砂流动性好,不需捣固机紧实,减少了模样(芯盒)的伤损和变形;(2)砂型(芯)固化后起模,减少了因起模前松动模样和起模时碰坏砂型(芯)引起的变形;(3)无需修型,减少了修型时引起的变形;(4)无需烘烤,减少了因烘烤造成的铸型(芯)变形;(5)铸型强度高、表面稳定性好,故芯头间隙小、分型负数小,减少了下芯、配模过程中铸型的破损和变形,保证了配模精度;(6)铸型(芯)硬度高,热稳定性好,可以有效地抵御浇注时的型壁退让、迁移现象,减少了铸型的热冲击变形(如胀砂等);(7)型砂的溃散性好,清理、打磨容易,从而减少了落砂清铲修整工序中对铸件形状精度的损害。
综上所述,由于在各个工序中都最大限度地排除了影响铸型、铸件变形和损坏的因素,所以树脂砂铸件的铸件表面质量、铸件几何尺寸精度方面比粘土烘模砂可以提高1—2级,达到CT7-9级精度和1-2mm / 600mm的平直度,表面粗糙度更大有改观。
2 .造型效率高,提高了生产率和场地利用率,缩短了生产周期。
这是由于(1)、型砂流动性好,不需捣固机紧实,节省了大量的捣固工作量,使造型操作大为简化;(2)铸型强度高,节约了起模后修型工作量;(3)型(芯)上醇基涂料点干后可省去烘干工序,节约了工时和场地;(4)旧砂回收后干法机械再生,使砂处理为封闭系统,便于机械化,可以节约大量旧砂处理,型砂混制、运输等辅助劳动;(5)型砂的溃散性好,落砂容易,修整工作量少、(6)节约了一些造型(芯)前的准备工作量。
如插芯固等。
根据一般统计,用自硬呋喃树脂砂代替粘土烘模砂后,生产效率可提高40—100%,单位造型面积产量可提高20—50%。
3 .减轻劳动强度,大大改善了劳动条件和工作环境,尤其是减轻了噪音、矽尘等,减少了环境污染。
4 .节约能源。
这表现在取消了烘窑和水力清砂,提高了铁水成品率,大大降低了压缩空气消耗,从而在节水、节电、节煤(焦)等方面效果显著。
5 .树脂砂型(芯)强度高(含高温强度高)、成型性好、发气量较其它有机铸型低、热稳定性好、透气性好,可以大大减少铸件的粘砂、夹砂、砂眼、气孔、缩孔、裂纹等铸件缺陷,从而降低废品率,可以制造出用粘土砂难以做出的复杂件、关键件。
6 .旧砂回收再生容易,可以达到90—95%的再生回收率。
在节约新砂、减少运输、防止废弃物公害等方面效果显著。
二、自硬呋喃铸型有一些缺点,应采取相应对策。
1 .对原砂要求较高,如粒度、粒形、SI0 2含量、微粉含量、碱金属盐及粘土含量等都有较严格要求;2 .气温和湿度对硬化速度和固化后强度的影响较大;3 .与无机类粘结剂的铸型相比,树脂砂发气量较高,如措施不当,易产生气孔类缺陷;4 .由于硬化机理是脱水缩合型,故硬化反应需一定时间,模样的周转率较低,不易适应于大批量铸件的生产;5 .与粘土砂相比,成本仍较高;6 .对球铁件或低C不锈钢等铸件,表面因渗硫或渗碳可能造成球化不良或增碳,薄壁复杂铸钢件上易产生裂纹等缺陷;7 .浇注时有剌激性气味及一些有害气体发生,CO气发生量较大,需有良好的通风条件。
1 — 3 自硬呋喃树脂砂的发展概况呋喃树脂最早作为铸型用粘结剂是1958年在美国开始使用的,当时是作为热芯盒粘结剂使用的。
把它作为自硬性铸型进行研究是1963年-1971年在英国进行的。
这个期间从基础研究到生产大铸件都作了扎实的实用化研究。
其结果,报导了用少量粘结剂能获得很高的强度,铸型溃散性好,铸件尺寸精度高,生产效率提高等一系列优点。
为获得今天这样的发展奠定了基础。
在欧美,70—80年代是自硬呋喃砂取得飞跃发展的时期。
在日本将自硬呋喃砂用于生产一般铸件是从1973年开始的,约十年左右,全国多品种小批量的中、大铸件生产中有一大半过渡到用自硬呋喃铸型来生产。
这种发展趋势至今方兴未艾,尽管其他有机自硬铸型开发了更多种类,然而现在占首位的仍然是自硬呋喃树脂砂。
在我国,七十年代开始研究自硬树脂砂,但仅限于个别厂家和研究单位搞试验。
从八十年代初,尤其是1982年以后,随着改革开放政策的贯彻,我国与国外合作生产的工厂增多,不少合作生产的外国厂家都对铸件生产提出来用自硬树脂砂的要求,否则无法合作。
对国内来说,以出口产品为主,对铸件质量的要求也越来越高。
于是在这种社会生产发展的新形势下,在国外树脂砂热的推动下,迫使我国广大铸造工作者们认识到应用自硬树脂砂是造型工艺上的一场革命,是提高铸件和机械产品质量的重要途径,是振兴铸造行业改变后面貌的必由之路,是机械产品跃入国际市场的基本保证。
因此八十年代我国铸造生产战线上形成了“树脂砂热”。
由于自硬树脂砂最适合于多品种小批量的中大铸件生产,所以机床行业、水泵行业、阀门行业和造船、石化等行业在树脂砂推广应用中走在最前面。
迄今为止,据不完全统计,我国已引进树脂砂处理生产线不下五十家,国内有三大铸机厂(重庆、保定、漯河)已正式生产成套树脂砂设备。
另外,生产原辅助材料的厂家遍布各省,原辅助材料的质量进步很快,有些已接近或达到国外同类产品的水平。
事实表明用树脂砂工艺取代粘土烘模砂生产多种小批量中大铸件是今后国内铸造业界的发展方向之一。
第二章自硬呋喃树脂砂的原辅材料组成自硬呋喃树脂砂的主要原材料有作为型砂骨料的原砂,作为粘结剂用的呋喃树脂,作为催化剂用的酸类固化剂和作为添加剂的硅烷偶联剂等,树脂砂造型中必须的辅助材料有涂料、脱模剂、粘合剂、浇口陶管、分型剂等。
原辅材料的好坏对树脂砂铸件质量的影响很大,本章对以上主要原辅材料作一简单介绍。
2 — 1 原砂一般仍选用天然石英砂。
对于部分高合金钢铸件或特殊需要的情况下,也有选用铬矿砂或锆砂等特殊骨料的。
这里我们主要讨论树脂砂对石英砂的要求。
一、矿物成分与化学成分原砂的主要矿物成分是石英(即SiO 2)、长石和云母,还有一些铁的氧化物和碳化物。
石英比重 2.55,莫氏硬度七级,熔点1713℃,具有耐高温、耐磨损等优点。
若原砂中石英(SiO 2)含量高,则原砂的耐火度和复用性都好。
长石是铝硅酸盐,常见的有钾长石(K 2O、AI 2O 3、SiO 2)钠长石(Na 2 O、AI 2O 3 SiO 2)和钙长石(2CaO、AI 2O 3、SiO 2),长石比重 2. 54-2.76,莫氏硬度6- 6.5级,熔点1100-1250℃,因其熔点低、硬度低、不耐磨、易粉碎,会降低树脂砂的复用性和耐火度。
云母是种含铝硅酸盐,有黑白云母之分,白云母的成分为(3AI 2O 3、6SiO 2、H 2O)。
云母的熔点为1145-1270℃,比重 2.7-3.2。
硬度很低,极易破碎,它在砂中的含量多少对原砂的复用性很有影响。
总之,在选择原砂时,SiO 2含量应尽量高一些,不纯物要少,当然还与金属的熔点和浇注温度,铸件壁厚等因素有关。
一般来说,铸钢用原砂SiO 2含量应大于95%,铸铁应大于92%,有色金属可以低一些。
杂质允许含量还与旧砂是否再生回用以及下面谈到的耗酸量有关。
二、粒形和表面光滑度对于粒形,要求园形或类园形,砂粒表面应光洁平整,没有孔洞或裂纹。
这样的砂粒表面积小,砂粒表面涂上一层薄膜所需的树脂量少些。
一般用角形系数表示砂粒形园整度,人造石英砂虽然SiO 2含量高,但粒形为多角形甚至尖角形,角形系数太大,需经研磨处理,一般不采用。
天然砂中角形系数最小的要算风积砂,如内蒙通辽一带的大林标准砂,角形系数小于 1.2,呈圆形。
为了改善粒形,对原砂最好进行擦磨处理。
目前我国唯一生产擦磨砂的是江西星子砂矿。
该矿对原砂经擦磨处理后,角形系数从 1.47减少到 1.35,与此同时,SiO 2含量也从93%(水洗砂)提高到95%(45/75目)砂样抗拉强度也由12.2Kg /cm 2增加到16.3Kg / Cm 2。
原砂的粒形不仅影响树脂砂加入量,同时还影响到树脂砂的流动性及紧实程度,砂粒表面空洞裂纹不仅无效消耗树脂,而且砂粒易碎,影响复用性及粒度保持性。
三、粒度分布及微粉含量粒形相同的原砂,以粒度较粗的总表面积小,树脂用量少,透气性好,耐火度高。
粗砂的缺点是抗机械粘砂能力低。
一般多选用30/50目、40/70目为宜,为提高综合性能,本厂采用30/70目的多筛号分布的砂。
微粉及含泥量严重恶化树脂砂性能。
由于微粉表面积很大,消耗树脂及固化剂影响透气性及强度,原砂中的泥份中碱土金属含量较高,据介绍细粉状比粒状耗酸值要大3—10倍。
一般要求原砂含泥量应小于0.3%。
四、含水量树脂砂的硬化是放热反应,原砂含水量严重影响树脂的固化强度与固透性,实验证明,含水量由0.2%升高到0.4%,型砂的抗拉强度可从13.2kg /cm 2降低到8.6kg /c m 2,固化时间也从30分钟延长到70分钟。
国外一般要求原砂含水量小于0.1%,国内一般要求小于0.2%。