赛络纺与环锭纺的区别
赛络纺棉纱的优缺点及应用创新

赛络纺棉纱的优缺点及应用创新大耀纺织一直致力于为客户提供优质、性价比高的产品,现棉纱常备产品7S-60S常规品种。
近年来对于棉纱的质量尤其重视,开发了一系列的赛络纺产品,如10S/12S/16S都有大量库存,性价比高。
赛络纺相比传统的单纱环锭纺纱有许多优点,如毛羽少、条干更均匀、织物具有较高的抗起球性,手感柔软、抗摩擦性好,织物有更好的透气性。
下面为大家讲解赛络纺棉纱的优缺点及应用创新:一、赛络纺的原理赛络纺是在传统环锭细纱机上纺出类似于股线结构的纱线的一种纺纱方法,是在细纱机上喂入两根保持一定间距的粗纱,经牵伸后,由前罗拉输出这两根单纱须条,并由于捻度的传递而使单纱须条上带有少量的捻度,拼合后被进一步加捻成类似合股的纱线,卷绕在筒管上。
赛络纺又称并捻纺,国内称为A,B纱,近期正式命为赛络纺。
二、赛络纺的优点1、成纱断裂强度较高;2、断裂伸长率较大;3、毛羽大幅度减少;4、耐磨性和抗起球性好;5、粗、细节明显减少;6、车间内飞花减少;7、节约能源与劳动力;8、设备投资少;三、赛络纺与环锭纺之间的比较1、条干的改善是因为赛络纺由双根粗纱喂入,在牵伸区并合,所以条干、粗细节均有不同程度的改善。
2、毛羽的改善是因为在纺纱三角区单纱先轻微加捻,并和后再加捻。
须条在主加捻点处已变成圆柱体,有利于纤维端缠入纱体。
3、强力的增加是因为须条在前罗拉输出处有个三角形加捻区,须条受张力作用捻合在一起,形成类似股线的双中心纱条,在受力时,两个须条相互挤压,使纤维间不易滑脱,且毛羽低,纤维利用率高,因此强力大。
四、赛络纺纱容易出现的问题1、并合前纱条过细,易产生意外牵伸;2、成纱细节增加,纱线越细增加越明显;3、细纱断头增多,生产效率降低。
五、赛络纺断头处理由于赛络纺是由两根有一定间距的须条喂入细纱牵伸区,分别牵伸后加捻成纱,两股须条存在一股断头后另一股跑单纱的情况,并且在纺纱张力稳定的情况下不断头,造成错支纱,为保证纺纱质量,需加装赛络纺单纱打断装置,一股断头后打断装置能将另一股单纱打断。
第十部分纱线的分类与结构特征

复合与结构纺
(20 世纪 80 年代至今)
?可拓展
复合纺纱技术(包芯纺、长/短复合纺)、
结构纺纱技术(以环锭纺为基础和特征)
(始于 20 世纪 60 年代)
组份连续与非连续、渐变与突变技 术、有引入纺纱其他工序趋势
(始于 20 世纪 80 年代)
图10-4 纺纱技术的演变进程
(1)自由端纺纱
把纤维分离为单根并使其凝聚,在一端非机械握持状态 下加捻成纱
炭化 惰性气氛(N2)
1200℃~1600℃ 几~几十分钟 碳纤维(CF)
石墨化 惰性气氛
2000℃~3000℃ 几~几十秒 石墨纤维(GrF)
表面处理、深加工 CF 产品
图10-6 PAN纤维的炭化加工流程示意图
3. 线加工的发展
集中体现在外观与性能的变化、赋予功能性以 及向织物合成品靠拢
第三节 纱线的结构特征与主要性能
短纤维的粘合纱为无捻纱
(6)新型复合结构纱
主要指在环锭纺纱机上通过短/短、短/长纤维加捻成的 复合纱和通过单须条分束或须条集聚方式得到的纱
赛络纺(Sirospun)、短/长复合纺(如Sirofil)、分束 纺(Solospun)和集聚纺纱(Compact yarn)
①赛络纺(sirospun)
④、摩擦纺纱
利用尘笼内的负压气流吸附纤维和尘笼回转对须条摩 擦加捻成纱
广泛用于地毯、衬布和粗厚装饰织物
(2)自捻纱
利用搓辊的往复运动对两根须条实施同向加捻,靠须条 自身的退捻力矩相互反卷在一起,形成一个双股的稳定 结构的纱,属非自由端纺纱
(3)包芯纱
以长丝为芯,短纤维为皮的包缠结构的纱,属复合纱 可在环锭纺纱机或捻线机,转杯纺,涡流纺,尘笼纺,
纱线纺制方法鉴别

环锭纺与气流纺的鉴别环锭纺世在细纱机上纺制而得到的,而纺纱的捻向都是Z捻,所以用S捻进行退捻,纤维能分离。
气流纺世通过气流回旋形成涡流,因此纱线表面的纤维相互纠缠,而内部的纤维有一定的捻度,但由于表面纤维相互纠缠,所以不管用Z捻还是S捻解捻,都不能使纤维分离。
因此通过以上方法就能把两者区分开来,且同样纱支的纱线,环锭纺的强力好于气流纺,毛羽、条干气流纺好于环锭纺。
喷气纺与涡流纺的鉴别喷气纱结构分纱芯和外包纤维两部分,纱芯平行且有捻度,结构较紧密,外包纤维松散且无规则缠绕在纱芯外面,故喷气纱结构较蓬松,外观较丰满。
而涡流纱结构也分纱芯和外包纤维,芯纤维呈平行排列、无捻度,外包纤维呈规则螺旋包缠在纱芯表面,且外层规则螺旋包缠纤维比例较高,占总纤维的60%左右,以致于内部未加捻的纤维几乎被完全覆盖,克服了喷气纱露芯问题,表面纤维排列则更接近于传统环锭纺,结构较紧密。
因此只要剥离外层纤维,看里层纤维是否加捻与外层包缠纤维是否有规则就能将两者区别出来。
且喷气纺主要是纺制化纤与棉的混纺、纯化纤纱及其混纺纱,全棉没有喷气纺。
精梳棉与紧密纺纱的鉴别紧密纺纱只要看整个布面的纱线很少有棉结,纱线的条干也很均匀,布面很光洁。
另外也可以看拆出来的纱线,如果是紧密纺,那么整根纱线毛羽很少,而且也很光洁,强力也比精梳棉要好。
整个布面摸起来比精梳棉要薄一些。
因此从以上三个方面我们就能把他们区别开来。
紧密纺纱与赛络紧密纺纱的鉴别紧密纺纱与赛络纺纱的相似之处是都是在传统环锭纺的加捻三角区增加了隔栅板与吸风凝聚装置,因此纱线的条干均匀,强力增加,丝线的毛羽少。
不同之处紧密纺是在细纱机上是单根喂入而赛络纺是在细纱机上喂入两个保持一定间距的粗纱,经牵伸后,由前罗拉输出这两根单纱须条,并由于捻度的传递而使单纱须条上带有少量的捻度,拼合后被进一步加捻成类似合股的纱线,卷绕在筒管上。
环锭纺双股线与赛络纺的鉴别环锭纺是在细纱机上纺制而得到的,而单纱纺纱的捻向都是Z捻,两根单纱并和采用S捻进行并捻。
第六章环锭纺纱新技术

第四节 集聚纺纱
二. 集聚纺纱工艺原理与类型 (二)B型集聚纺纱
1. 代表 德国青泽(Zinser)公司
COMPACT3 2. 集聚装置 带孔皮圈、一对输出罗拉
A型集聚纺中纤维束的集聚
A型集聚纺原理示意图
A型集聚纺滚筒罗拉
A型集聚纺滚筒罗拉
第四节 集聚纺纱
二. 集聚纺纱工艺原理与类型 (一)A型集聚纺纱
3. 特点 (1) 在31至32区域内滚筒罗拉借助空气 负压对纤维进行集聚。 (2) 可纺纤维的最短长度,即皮圈控制 钳口线R到前罗拉钳口线3-31之间的距离, 受到滚筒罗拉直径的限制。
成纱断裂强度高,耐磨性好,毛羽少。
第四节 集聚纺纱
一. 集聚纺纱技术的产生背景 (一)传统环锭纺纱技术的缺陷
加捻三角区不可能聚拢喂给的所有纤 维,许多边缘纤维或者散失掉,或者以 毛羽形式从纱体中突出,对成纱强度贡 献很小,而且影响成纱条干。
传统环锭纺纱线的形成
第四节 集聚纺纱
一. 集聚纺纱技术的产生背景 (二)集聚纺纱技术的产生
第四节 集聚纺纱
三. 成纱结构与性能 (二)成纱性能
5. 加工性能 (3) 比同规格普通环锭纱节省化学浆料 50%。 (4) 整经断头率比同规格普通环锭纱低 30%。
The End
距离平行喂入,在前罗拉钳口下游汇合, 加捻成纱。
赛络菲尔纺纱工艺原理
第二节 赛络菲尔纺纱
二. 成纱结构与性能 (一)成纱结构
短纤维须条与长丝抗弯刚度和抗扭刚 度不同,造成两者在成纱结构中位置分 布有差异,长丝呈螺旋状包覆在短纤维 须条外。
环锭纺、气流纺、喷气纺、涡流纺、赛络纺、紧密纺简介

环锭纺、气流纺、喷气纺、涡流纺、赛络纺、紧密纺简介环锭纺环锭纺纱是现时市场上用量最多,最通用之纺纱方法,条子或粗纱经牵伸后的纤维条通过环锭钢丝圈旋转引入,筒管卷绕速度比钢丝圈快,棉纱被加捻制成细纱.广泛应用于各种短纤维的纺纱工程.如普梳,精梳及混纺,钢丝圈由筒管通过纱条带动绕钢领回转.进行加捻,同时,钢领的摩擦使其转速略小于筒管而得到卷绕.纺纱速度高,环锭纱的形态,为纤维大多呈内外转移的圆锥形螺旋线,使纤维在纱中内外缠绕联结,纱的结构紧密,强力高,适用于制线以及机织和针织等各种产品。
环锭纺(精梳)流程:清花间--梳棉--预并条--条并卷--精梳--头道并条--二道并条--粗纱--细纱--络筒环锭纺(普梳)流程:清花间--梳棉--头道并条--二道并条--粗纱--细纱--络筒气流纺气流纺不用锭子,主要靠分梳辊、纺杯、假捻装置等多个部件。
分梳辊用来抓取和分梳喂入的棉条纤维,同过他的高速回转所产生的离心力可把抓取的纤维甩出。
纺杯是个小小的金属杯子,他的旋转速度比分梳辊高出10倍以上,由此产生的离心作用,把杯子里的空气向外排;根据流体压强的原理,使棉纤维进入气流杯,并形成纤维流,沿着杯的内壁不断运动。
这时,杯子外有一根纱头,把杯子内壁的纤维引出来,并连接起来,再加上杯子带着纱尾高速旋转所产生的钻作用,就好像一边“喂”棉纤维,一边加纱线搓捏,使纱线与杯子内壁的纤维连接,在纱筒的旋绕拉力下进行牵伸,连续不断的输出纱线,完成气流纺纱的过程。
气流纺的特征气流纺纱有速度大、纱卷大、适应性广、机构简单和不用锭子、钢领、钢丝圈的优点,可成倍的提高细纱的产量。
气流纺与环锭纺的区别气流纺与环锭纺一个是新型纺织技术,一个是老式纺纱技术。
气流纺是气流纺纱,而环锭纺则是机械纺,就是由锭子和钢铃、钢丝圈进行加捻,由罗拉进行牵伸。
而气流纺则是由气流方式输送纤维,由一端握持加捻。
一般来说,环锭纱毛羽较少,强度较高,品质较好。
气流纺工序短,原料短绒较多,纱线毛,支数和拈度不能很高,价格也较低。
紧密纺和赛络纺的区别

紧密纺和赛络纺的区别
紧密纺和赛络纺的区别,紧密纺是在改进的新型环锭细纱机上进⾏纺纱的⼀种新型纺纱技术。
其纺纱机理主要是:在环锭细纱机牵引装置前增加了⼀个纤维凝聚区,基本消除了前罗拉⾄加捻点之间的纺纱加捻三⾓区。
纤维须条从前罗拉前⼝输出后,先经过异形吸风管外套⽹眼⽪圈,须条在⽹眼⽪圈上运动,由于⽓流的收缩和聚合作⽤,通过异形管的吸风槽使须条集聚、转动,逐步从扁平带状转为圆柱体,纤维的端头均捻⼊纱线内,因此成纱⾮常紧密,纱线外观光洁、⽑⽻少。
紧密纺纱线强⼒较⾼,⽑⽻较少。
赛络纺是由两根有⼀定间距的须条喂⼊细纱牵伸区,分别牵伸后加捻成纱,两股须条存在⼀股断头后另⼀股跑单纱的情况,并且在纺纱张⼒稳定的情况下不断头,造成错⽀纱,为保证纺纱质量,需加装赛络纺单纱打断装置,⼀股断头后打断装置能将另⼀股单纱打断。
拓展知识1 紧密纺和赛络纺
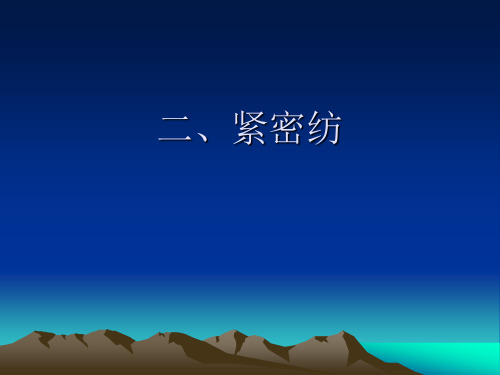
根据紧密纺产生集聚作用的方式不 同,紧密纺系统可分为哪两大类
• 目前较为成熟的集聚环锭纺纱技术的原理主要有 两种:气动式和机械式集聚系统。 • 气动式集聚系统是利用负压气流将纤维收缩、聚 合,使须条边缘快速向须条中心集聚,最终最大 限度地减少纺纱三角区。瑞士Rieter公司、德国 Zinser公司和Sussen公司、意大利Marzoli公司、 日本Toyota公司采用的都是气动式集聚系统,只 是形式各不相同。
• V/F控制不是必选的,可以选用矢量控制变频器, 也可以选用直接转矩控制的变频器啊。V/F控制的 缺点,主要是由两个:第一,是开环控制方式; 第二,是低频扭矩比较小,对于大惯量的负载, 可能造成启动困难,甚至是启动不了。现在风机 水泵类负载,一般还是倾向于使用V/F变频器,这 是一个不争的事实,这是因为,风机水泵类负载, 对于变频器的要求是比较低:第一,风机水泵之 类属于轻载,对低频扭矩不是很关心;第二,风 机水泵的控制是比较简单,无非就是恒压、恒静 压之类的控制,即使不用闭环控制,也能达到较 好的节能效果;第三,相对于矢量控制、直接转 矩控制的变频器来讲,V/F的变频器在价格上还是 有优势的。
5、瑞士罗卡斯公司的紧密纺 (磁铁-机械式紧密纺)
• 在前皮辊和引纱皮辊之间有一个磁性紧密 器,紧密器与下罗拉紧密接触,没有间隙, 上下罗拉一起形成一个完全封闭的负压室, 纤维束与罗拉同步移动,通过紧密器的纤 维通道,被安全地输送到引纱钳口。 • 罗卡斯可确保最佳集聚,简便可靠,不增 加任何纺纱成本。
变频器节能
现环锭细纱机特点及控制电路存在的问题 现有的环锭细纱机纺纱速度主要受细纱断头的约束, 而细纱断头又是细纱生产中的主要危害,也是细 纱生产实现优质、高产、低耗的主要障碍,直接 影响到细纱的质量、产量及生产效率。环锭细纱 机纺纱速度的提高受到纺纱气圈的牵制,气圈张 力变化又受气圈角度速度、卷绕半径、气圈高度 等因素影响,细纱断头的另一个主要原因就是气 圈张力值瞬时超过纱线的抱合强力值造成的,减 少断头率是提高细纱质量和产量主要的关键。
纱线基础知识-图文详解版
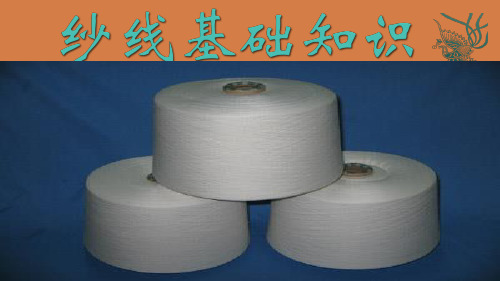
公制支数(Nm)和英制支数(Ne)
公制支数(Nm)
是指在公定回潮率时,一克重的纱线 (或纤维)所具有的长度米数。
公制支数可表示成“20公支、40公支”的 形式,意谓着一克重的纱线具有20m长或 40m长。
b. 英制支数(Ne)
指1磅(454克)重的棉纱线有几个840 码(1码=0.9144米)长。
气流纱: (OPEN END)
也称转杯纺纱,是利用气流将纤维在高速 回转的纺纱杯内凝聚加捻输出成纱。
气流纱特点:
纱线结构比环锭纱蓬松、耐磨、条干均匀、 染色较鲜艳,但强力较低。
主要用于机织物中膨松厚实的平布、手感 良好的绒布。
1.机织用纱: (Weaving)
机织用纱指加工机织物所用纱线,分经纱和 纬纱两种。 经纱:
按照纺纱系统分:
精梳纱 普梳纱 废纺纱
精纺纱 (JC/CJ) (CM combed)
也称精梳纱,是指通过精梳工序纺成 的纱,包括精梳棉纱和精梳毛纱。
精梳纱特点
纤维平行伸直度高,条干均匀、,但 成本较高,纱支较高。
主要用于高级织物及针织品的原料, 如细纺、华达呢、花呢、羊毛衫等。
2.粗纺纱(C) ( CD CARDED) 不经过精梳工序纺成的纱。
捻度 、强力、 纱支 、条干 、细节、 粗节、 棉结 属于乌斯特指标,用乌斯特仪器测出来
捻度: (TWIST)
是指纱线单位长度上的捻回数。
国内: 其计量单位为“捻/10cm” 或“捻 /m”
国外: 用英寸捻度表示:TPI= 捻/INCH 捻 度/英寸
捻度/10cm
捻/10cm
捻度对纱线的影响:
所有的化纤和纤维素纤维都不走精梳工序 普梳纱特点及用途
环锭纺、气流纺、喷气纺、涡流纺、赛络纺、紧密纺简介
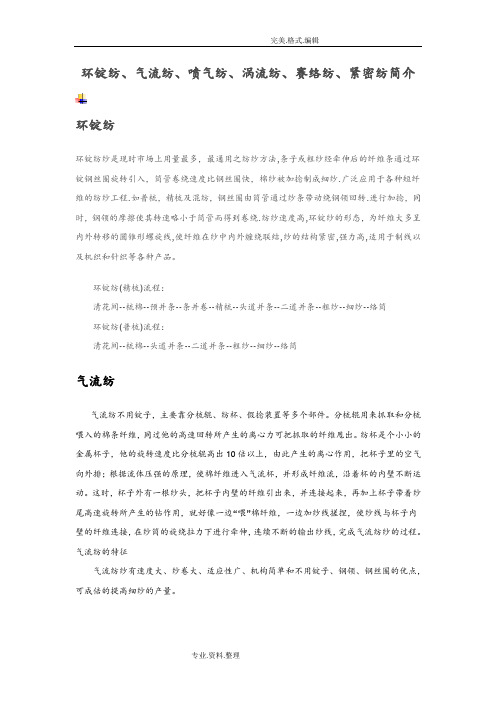
环锭纺、气流纺、喷气纺、涡流纺、赛络纺、紧密纺简介环锭纺环锭纺纱是现时市场上用量最多,最通用之纺纱方法,条子或粗纱经牵伸后的纤维条通过环锭钢丝圈旋转引入,筒管卷绕速度比钢丝圈快,棉纱被加捻制成细纱.广泛应用于各种短纤维的纺纱工程.如普梳,精梳及混纺,钢丝圈由筒管通过纱条带动绕钢领回转.进行加捻,同时,钢领的摩擦使其转速略小于筒管而得到卷绕.纺纱速度高,环锭纱的形态,为纤维大多呈内外转移的圆锥形螺旋线,使纤维在纱中内外缠绕联结,纱的结构紧密,强力高,适用于制线以及机织和针织等各种产品。
环锭纺(精梳)流程:清花间--梳棉--预并条--条并卷--精梳--头道并条--二道并条--粗纱--细纱--络筒环锭纺(普梳)流程:清花间--梳棉--头道并条--二道并条--粗纱--细纱--络筒气流纺气流纺不用锭子,主要靠分梳辊、纺杯、假捻装置等多个部件。
分梳辊用来抓取和分梳喂入的棉条纤维,同过他的高速回转所产生的离心力可把抓取的纤维甩出。
纺杯是个小小的金属杯子,他的旋转速度比分梳辊高出10倍以上,由此产生的离心作用,把杯子里的空气向外排;根据流体压强的原理,使棉纤维进入气流杯,并形成纤维流,沿着杯的内壁不断运动。
这时,杯子外有一根纱头,把杯子内壁的纤维引出来,并连接起来,再加上杯子带着纱尾高速旋转所产生的钻作用,就好像一边“喂”棉纤维,一边加纱线搓捏,使纱线与杯子内壁的纤维连接,在纱筒的旋绕拉力下进行牵伸,连续不断的输出纱线,完成气流纺纱的过程。
气流纺的特征气流纺纱有速度大、纱卷大、适应性广、机构简单和不用锭子、钢领、钢丝圈的优点,可成倍的提高细纱的产量。
气流纺与环锭纺的区别气流纺与环锭纺一个是新型纺织技术,一个是老式纺纱技术。
气流纺是气流纺纱,而环锭纺则是机械纺,就是由锭子和钢铃、钢丝圈进行加捻,由罗拉进行牵伸。
而气流纺则是由气流方式输送纤维,由一端握持加捻。
一般来说,环锭纱毛羽较少,强度较高,品质较好。
气流纺工序短,原料短绒较多,纱线毛,支数和拈度不能很高,价格也较低。
环锭纺赛络纺和紧密纺的区别

环锭纺赛络纺和紧密纺的区别1.因为赛络纺是两根粗纱同时被分别牵伸,根据并合理论,CX=CA/√n,公式中CX为并合后的不匀率,CA为并合前的不匀率,n为并合根数,此处n等于2。
所以CX=0.7×CA。
当然上述公式是理论数据,和实际情况有一定差别。
但也说明:用赛络纺工艺方法纺成的纱对改善条干,减少粗、细节有非常明显的效果,这是无数纺纱厂所孜孜以求的。
我公司几年来的试验和众多用户的大量生产实践也充分证明了这一点。
2.赛络纺的纱条从前罗拉输出后,在捻合时,两根弱捻纱条相互为中心卷成一根赛络纱。
在卷绕过程中,把伸出纱条主体的毛羽卷进纱线里面,并得到了良好的握持。
所以,赛络纱的毛羽比其它工艺方法都少,而且因为毛羽被两根纱条卷在细纱内,所以经过络筒工序时,也不会象其它纺纱方法大量增加毛羽,这一点时其它纺纱方法所无法比拟的。
3.赛络纺的纱条在前罗拉钳口处基本不加捻,所以不存在所谓的“加捻三角区”,大大减少了车间的飞花。
4.经过络筒工序后,赛络纱的毛羽比紧密纱更少,所以在上浆、织造、烧毛工序中,有着更加优越的性能。
5.赛络纱在加捻过程中,纤维内、外转移的程度小,成纱后纤维排列规律,其纱线强力优于单纱,比股纱强力低,另外,赛络纱的细节少,这也对增加纱线强力有帮助。
6.赛络纺纱设备比紧密纺机构简单,设备投资少,宜于维护。
在老机上进行改造容易实现。
7.赛络纱有类似股纱的性能,在许多情况下,可以代替股纱。
但赛络纺纱不需经过并捻机,工艺流程比常规工艺短,节省能源和劳动力。
综上所述,赛络纺工艺有着其它纺纱工艺所无法比拟的优点,但也有其不足之处,如下所述:1.络纺工艺是双粗纱喂入,纺同号细纱时,如果粗纱定量不减少,细纱机的总牵伸倍数就要增加一倍。
现有细纱机的配置可能不适应,牵伸倍数过大,也要恶化细纱的条干水平。
如果降低粗纱定量,势必增加粗纱工序的负担。
为解决这个矛盾,我公司研制出细纱机三罗拉四皮圈超大牵伸机构,即在原有的三罗拉双皮圈牵伸机构的基础上,在后区增加上、下肖和上、下皮圈,使原来后区的简单罗拉牵伸区变成皮圈牵伸区,大大加强了对纤维的控制。
给我一分钟的时间,告诉你如何区分环锭纺、气流纺、涡流纺和赛络纺

给我⼀分钟的时间,告诉你如何区分环锭纺、⽓流纺、涡流纺和赛络纺今天⼩编教⼤家通过退捻的⽅法
来区分环锭纺、⽓流纺、涡流纺和赛络纺
在这之前,我们要先说⼀下退捻的⽅法,
请看下⾯的视频
⼀、退捻教学视频
(视频有9秒,建议在WIFI下观看,⽆声,⼟豪随意)
学会了退捻之后,我们就可以通过退捻的⽅法来区分四种纱线了
⼆、四种纱线的区分
1.环锭纺纱线
环锭纺整根纱线都能够完全退捻,退完捻后纱线没有强⼒
2.赛络纺纱线
赛络纺整根纱线都能够完全退捻,退完捻后纱线没有强⼒
在这四种纱线中,赛络纺唯⼀⼀个看起来是两根的纱线合成的⼀根单纱
赛络纺就是⾼档环锭纺(是由两根粗纱⼀起并⾏输⼊纺成⼀根细纱)
条⼲好,⽑⽻少,强度⽐环锭纺⼤
3.⽓流纺纱线(转杯纺)
⽓流纺⽆法像环锭纺⼀样整根纱线完全退捻,只能少的局部能完全退捻,所以退捻后被退捻的
节点也没有强⼒,整根纱⼀拉就断
4.涡流纺纱线
涡流纺退捻后外表看起来完全退捻,但纱芯没有退捻,还是有很⼤的强度,
三、纱线的区分流程
第1步:拿到⼀根纱线退捻
没有整根纱线完全退捻,只有部分节点完全退捻,⽓流纺
第2步:看起来完全退捻
第3步:看是否有强⼒
(有→涡流纺,没有→环锭纺)
第4步:观察是否有两根
(有→赛络纺,没有→普通环锭纺)
四、成纱⽐较
(同等原料同样⽀数相⽐)
环锭纺适纺范围最⼴,通常可纺300英⽀以下的纱线,转杯纺⽬前通常适纺40英⽀以下的纱线,涡流纺⽬前适纺60英⽀以下的纱线
END。
赛络纺乃呙流纺廊锭纺竹纤维成纱质量对比分析

赛络纺乃呙流纺廊锭纺竹纤维成纱质量对比分析赛络纺、乃呙流纺、廊锭纺是目前常见的纺纱工艺,它们各自有其适用的纺纱原料和工艺特点。
本文将从纤维成纱的质量角度对这三种工艺进行对比分析。
赛络纺是一种较新的纺纱工艺,其主要特点是纤维成纱过程中无需揉搓和拧紧,纤维在纱锭旋转时自由地络合成纱。
这一工艺在生产上的优点是纺纱速度较快、梳棉系统相对简单,纤维破损较少,成纱品质较好。
赛络纺适用于长纤维、细纱纺纱,如棉、麻等。
乃呙流纺是一种传统的纺纱工艺,其特点是纤维成纱过程中需要经过揉搓和拧紧。
这一工艺在生产上的优点是纱线的强度较高、纤维的整齐度好,适用于纤维长度较短、粗纱纺纱,如羊毛、粗棉等。
然而,乃呙流纺的纺纱速度较慢,机器复杂,纤维易受损,产量相对较低。
廊锭纺是一种介于赛络纺与乃呙流纺之间的工艺。
其特点是纤维成纱过程中既有一定程度的揉搓和拧紧,又有自由络合的环节。
廊锭纺的生产速度介于赛络纺与乃呙流纺之间,其整齐度和强度也介于两者之间。
该工艺适用于各种纤维类型。
在纤维成纱质量方面的对比分析中,赛络纺相对于乃呙流纺和廊锭纺,具有更好的颗粒度和纤维长度分布,纺纱后的纱线质地更加柔软,纺织品的手感更好。
然而,赛络纺的生产成本较高,设备维护及操作复杂,长时间生产易造成机器故障。
乃呙流纺由于需要经过揉搓和拧紧的步骤,纺纱后的纱线强度较高,纤维的整齐度也更好,适用于粗纺细织产品的制造。
然而,乃呙流纺的生产速度较慢,耗能较大,且纤维易受损,纺纱产量限制较大。
而廊锭纺则兼具了赛络纺和乃呙流纺的优点。
其纺纱速度相对较快,纺织品的品质也较高。
同时,廊锭纺还具有较低的故障率和维护成本,使得其在纤维成纱工艺中得到广泛应用。
综上所述,赛络纺、乃呙流纺和廊锭纺是三种常见的纺纱工艺,各自适用于不同类型的纤维和织物产品。
赛络纺在纺织品的柔软度和颗粒度上更具优势,而乃呙流纺则在强度和整齐度方面更出色。
廊锭纺则兼具两者的优点,且维护成本较低。
在选择纺纱工艺时,需要根据不同的需求和实际情况进行权衡。
技术环锭纺包芯纱和赛络纺包芯纱的对比

技术环锭纺包芯纱和赛络纺包芯纱的对比包芯纱又称复合纱或包覆纱,它是由两种或两种以上的纤维组合而成的一种新型纱线。
最初的包芯纱是以棉纤维为皮、涤纶短纤纱为芯开发的短纤维与短纤维包芯纱。
对于高强耐用、免烫、尺寸稳定又抗起球、吸湿透气、美观舒适的纺织品,如缝纫线和军服等,包芯纱比一般的纯纺纱和混纺纱优越,更能满足要求。
但传统的环锭纺包芯纱包覆效果欠佳,有时其结构就象把长丝和外包纤维须条并捻在一起的股线,没有适宜后序机械加工的抗剥离强度,因而降低了包芯纱的附加值,限制了包芯纱的潜在用途。
赛络纺包芯纱是一种具有股线性质的单纱,其强力、伸长、均匀度优于环锭纺包芯纱,且手感柔软、包覆效果好。
为了能经济地生产出质量优良、符合客户要求的包芯纱,结合本厂的生产实际,比较了传统和赛络纺锦纶长丝包芯纱的生产设备和成纱性能,分析了二者的差异,指出了应采取的合理纺纱工艺等。
1设备改造1.1 环锭纺包芯纱的设备改装传统环锭纺包芯纱可在普通改装过的细纱机上生产。
首先在一般的细纱机上加装芯丝喂入机构和预牵伸机构。
筒子长丝在导丝罗拉的牵引下退绕,不经过细纱机的牵伸机构,而是经过加装的预牵伸机构和V形槽导轮,自前罗拉皮辊后的集合器喂入,与牵伸后的须条合并,再通过前罗拉和导纱钩,由环锭回转加捻为长丝包芯纱。
接着改装粗纱架。
由于所用的锦纶长丝外形尺寸大于200mm×500mm,一台粗纱架由六列单层吊锭,改为四列单层吊锭,锭距由原来的210mm改为130mm。
芯丝喂入装置位于粗纱架上方,因而粗纱架下降30mm,以便腾出空间加装长丝立柱、托架和插丝锭子。
考虑到可操作性,只在立柱上加装二排长丝托架和锭子,利用粗纱前的空间,加装一排长丝托架和锭子。
这样,可以合理分布粗纱和长丝,长丝由导丝杆引出,喂入牵伸区前钳口,粗纱则经由导纱杆和分纱棒引出,喂入牵伸后区。
将横动杆固定,确保从喇叭口喂入经牵伸区输出的粗纱须条不产生移动。
在摇架位置加装导丝轮,有效控制长丝在前罗拉输出时始终位于粗纱须条中央,减少露芯等包芯纱缺陷,提高包覆效果。
纺纱方法比较及预氧丝纯纺和混纺
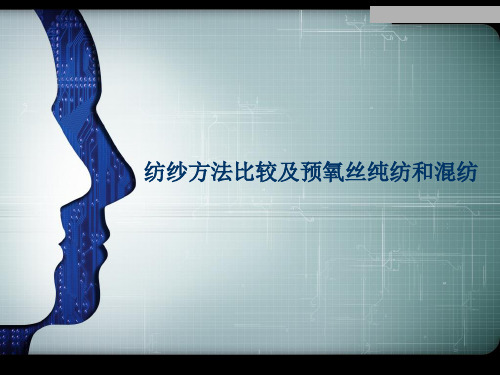
纺纱方法比较及预氧丝纯纺和混纺
大连工业大学
目录
1 2
环锭纺之赛络纺和赛罗菲尔纺
转杯纺
3 4
各种纺纱方式的区别和联系
PANOF纯纺和混纺 纯纺和混纺
5 结论
大连工业大学
1 环锭纺之赛络纺和赛罗菲尔纺
一 赛络纺原理 Siro纺是在细纱机上喂入两根 保持一定间距的粗纱,经牵伸 后,由前罗拉输出这两根单纱 须条,并由于捻度的传递而使 单纱须条上带有少量的捻度, 这两根须条回合后被进一步加 捻成类似股线的赛罗纱并被卷 绕在筒管上。
Hale Waihona Puke 大连工业大学2 转杯纺
纺纱杯是转杯纺最重要的部件,其 基本形状是由两个中空的截头圆锥 体联接而成,在两个圆锥体的交界 处(最大直径处)形成一个凝聚纤维 的凹槽,称为凝聚槽。
大连工业大学
2 转杯纺
转杯纺适纺纱线密度 —般为 般为388.7—13tex。 般为 。 例如, 例如,Autocoro-240 型适纺纱线密度为 125—12.5tex, , FA601型适纺纱线密度 型适纺纱线密度 为100—14.7tex。 。 国内实际常纺纱线密度 为97.2-36.4tex。 。 当纱线密度小于16tex 当纱线密度小于 时纺纱就比较困难。 时纺纱就比较困难。 其它纱种 在转杯纺机上 开发各种麻棉混纺纱、 开发各种麻棉混纺纱、 纳丝纯(混 纺纱 纺纱、 纳丝纯 混)纺纱、毛型纯 (混)纺纱、化纤纯 混)纺 混 纺纱 化纤纯(混 纺 纺纱、 纱 (涤、腈、粘等),往往有 涤 粘等 , 可能比环锭纺具有更好的 可纺性和更高的经济效益 。 转杯纱适合开发各类 牛仔布、绒类织物、装饰 牛仔布、绒类织物、 用布及工业用布等。 用布及工业用布等。
大连工业大学
常见纱线的结构形态与鉴别

常见纱线的结构形态与鉴别纺纱是人类非常古老的生产活动,大约在公元前9000年,人们就开始用双手搓捻的方式,搓出了最原始的羊毛纱。
西方工业革命后,纺纱由手工生产转变为工业化生产,尤其是环锭细纱机的发明,极大地提高了生产效率,加快了纺织工业化的步伐。
目前,纺纱技术主要有传统环锭纺、紧密纺、赛络纺、转杯纺、喷气纺和涡流纺等,除了传统环锭纺之外,其它几种纺纱技术都是在近几十年甚至是近几年发展起来的,统称为新型纺纱技术。
不同纺纱方式的成纱机理不同,纤维在纱线中的排列形态以及纱线的紧密度以不同,如图所示。
(1) 传统环锭纺环锭纱中纤维基本上呈螺旋线排列,由于存在纺纱加捻三角区,纤维不能全部被加捻到纱体中去,较多边缘纤维一端被捻入纱体,另一端露在纱条外面形成毛羽,因而虽然环锭纱结构较为紧密,但纱条表面相对来说显得杂乱无序,光洁度较差。
(2) 紧密纺紧密纺亦称集聚纺,是在环锭纺纱机牵伸机构之后的加捻三角区位置加装了纤维集聚装置,减小加捻三角区,从而改善纱线机构的一种纺纱方法。
纱线外观光洁、加捻螺旋结构清晰可见,纤维排列整齐清晰、毛羽少,纤维几乎没有内外转移,从一定意义上讲,可能是纱线中理想化的纤维排列方式。
(3) 赛络纺赛络纺是在传统环锭细纱机上纺出类似于股线结构的纱线的一种纺纱方法。
两根粗纱以一定的间距平行喂入环锭纺纱机的同一牵伸机构,以平行状态同时被牵伸,从前罗拉夹持点输出的这两根单纱须条,由于捻度的传递而使单纱须条上带有少量的捻度,拼合后被进一步加捻成类似合股的纱线,然后经过导纱钩、钢丝圈卷取到纱管上,成为赛络纺纱线。
(4) 转杯纺转杯纱,亦称气流纺,属于自由端纺纱方法。
在加捻过程中,加捻区的纤维缺乏积极握持,呈松散状态,因而纤维伸直度差,纤维内外转移程度低。
纱的结构分纱芯和外包纤维两部分。
纱芯结构与环锭纱相似,比较紧密;外包纤维结构松散,无规则地缠绕在纱芯外面。
因此与传统环锭纱相比,转杯纱结构比较蓬松,外观较丰满。
纤维、纱线、面料鉴别大全!

纤维、纱线、面料鉴别大全!导读:随着面料生产技术的不断进步,越来越多的新型纤维成为纺织品的原料,由此带来了对纺织品面料纤维进行鉴别的问题。
常用的纤维鉴别方法有显微镜观察法、燃烧法、试剂显色法、染色法等。
显微镜观察法在显微镜下观察纤维的纵向及横向形态,根据形态特征差异来鉴别纤维。
Tencel纤维:纵向形态光滑,截面形态较规则圆形或椭圆形,有皮芯层。
Modal纤维:纵向形态有1~2根沟槽,截面形态是不规则类似腰圆形,较圆滑,有皮芯。
大豆纤维:纵向形态表面有不规则沟槽和海岛状凹凸,截面形态呈扁平状哑铃型和腰圆形。
竹纤维:纵向形态表面有沟槽,截面形态锯齿型,有皮芯层。
甲壳素纤维:纵向形态表面有明显沟槽,截面形态边缘锯齿型,芯层有明显的细小空隙。
粘胶纤维:纵向形态表面有沟槽,截面形态锯齿型,有皮芯层。
棉纤维:纵向形态有天然转曲,截面形态腰圆形,有中腔。
蚕丝:纵向形态表面平滑,截面形态不规则三角形。
毛纤维:纵向形态表面有鳞片,截面形态圆形。
涤纶纤维:纵向形态棒状,截面形态表面光滑,圆形。
燃烧法不同的纤维在燃烧的过程中,火焰、烟雾、气味、残渣等会有所不同,因此根据纤维燃烧时和燃烧后的特征可以区分纤维种类。
Tencel纤维:接近火焰不熔不收缩,火焰中迅速燃烧,离开火焰继续燃烧,产生烧纸味,其残渣形态为灰黑色的灰。
Modal纤维:接近火焰不熔不收缩,火焰中迅速燃烧,离开火焰继续燃烧,产生烧纸味,其残渣形态为灰黑色的灰。
大豆蛋白纤维:接近火焰收缩,火焰中燃烧不熔融,有黑烟,离开火焰不易延烧,产生烧毛发味,其残渣形态为松脆黑灰。
竹纤维:接近火焰不熔不收缩,火焰中迅速燃烧,离开火焰继续燃烧,产生烧纸味,其残渣形态为灰黑色的灰。
甲壳素纤维:接近火焰不熔不收缩,火焰中迅速燃烧,离开火焰继续燃烧,产生烧纸味,其残渣形态为灰黑色的灰。
粘胶纤维:接近火焰不熔不收缩,火焰中迅速燃烧,离开火焰继续燃烧,产生烧纸味,其残渣形态为少量灰白色的灰。
环锭纺纱新技术 上海市毛麻纺织科学技术研究所 何春泉 - 的捻向是
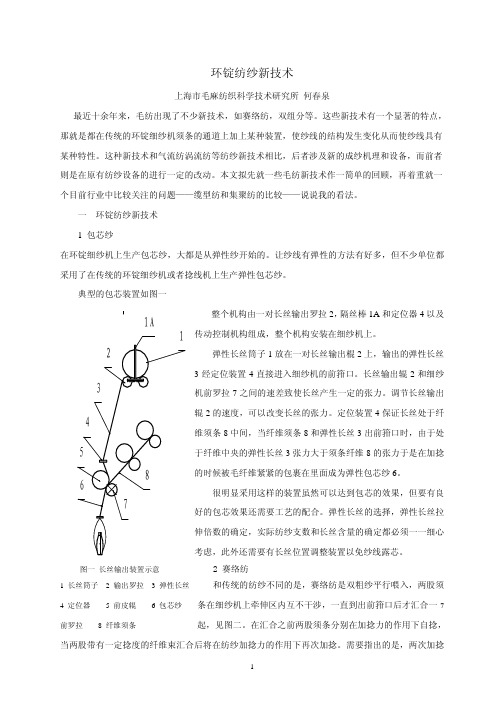
环锭纺纱新技术上海市毛麻纺织科学技术研究所何春泉最近十余年来,毛纺出现了不少新技术,如赛络纺,双组分等。
这些新技术有一个显著的特点,那就是都在传统的环锭细纱机须条的通道上加上某种装置,使纱线的结构发生变化从而使纱线具有某种特性。
这种新技术和气流纺涡流纺等纺纱新技术相比,后者涉及新的成纱机理和设备,而前者则是在原有纺纱设备的进行一定的改动。
本文拟先就一些毛纺新技术作一简单的回顾,再着重就一个目前行业中比较关注的问题——缆型纺和集聚纺的比较——说说我的看法。
一环锭纺纱新技术1 包芯纱在环锭细纱机上生产包芯纱,大都是从弹性纱开始的。
让纱线有弹性的方法有好多,但不少单位都采用了在传统的环锭细纱机或者捻线机上生产弹性包芯纱。
整个机构由一对长丝输出罗拉2,隔丝棒1A和定位器4以及传动控制机构组成,整个机构安装在细纱机上。
弹性长丝筒子1放在一对长丝输出棍2上,输出的弹性长丝3经定位装置4直接进入细纱机的前箝口。
长丝输出辊2和细纱机前罗拉7之间的速差致使长丝产生一定的张力。
调节长丝输出辊2的速度,可以改变长丝的张力。
定位装置4保证长丝处于纤维须条8中间,当纤维须条8和弹性长丝3出前箝口时,由于处于纤维中央的弹性长丝3张力大于须条纤维8的张力于是在加捻的时候被毛纤维紧紧的包裹在里面成为弹性包芯纱6。
很明显采用这样的装置虽然可以达到包芯的效果,但要有良好的包芯效果还需要工艺的配合。
弹性长丝的选择,弹性长丝拉伸倍数的确定,实际纺纱支数和长丝含量的确定都必须一一细心考虑,此外还需要有长丝位置调整装置以免纱线露芯。
图一 长丝输出装置示意 2 赛络纺1 长丝筒子2 输出罗拉3 弹性长丝和传统的纺纱不同的是,赛络纺是双粗纱平行喂入,两股须4 定位器5 前皮辊6 包芯纱条在细纱机上牵伸区内互不干涉,一直到出前箝口后才汇合一7 前罗拉8 纤维须条起,见图二。
在汇合之前两股须条分别在加捻力的作用下自捻,当两股带有一定捻度的纤维束汇合后将在纺纱加捻力的作用下再次加捻。
- 1、下载文档前请自行甄别文档内容的完整性,平台不提供额外的编辑、内容补充、找答案等附加服务。
- 2、"仅部分预览"的文档,不可在线预览部分如存在完整性等问题,可反馈申请退款(可完整预览的文档不适用该条件!)。
- 3、如文档侵犯您的权益,请联系客服反馈,我们会尽快为您处理(人工客服工作时间:9:00-18:30)。
你好:其实我也不懂,搜到以下资料看能否帮你!
<1>紧密纺是在改进的新型环锭细纱机上进行纺纱的一种新型纺纱技术。
其纺纱机理主要是:在环锭细纱机牵引装置前增加了一个纤维凝聚区,基本消除了前罗拉至加捻点之间的纺纱加捻三角区。
纤维须条从前罗拉前口输出后,先经过异形吸风管外套网眼皮圈,须条在网眼皮圈上运动,由于气流的收缩和聚合作用,通过异形管的吸风槽使须条集聚、转动,逐步从扁平带状转为圆柱体,纤维的端头均捻入纱线内,因此成纱非常紧密,纱线外观光洁、毛羽少。
紧密纺纱线强力较高,毛羽较少。
<2>赛络纺是由两根有一定间距的须条喂入细纱牵伸区,分别牵伸后加捻成纱,两股须条存在一股断头后另一股跑单纱的情况,并且在纺纱张力稳定的情况下不断头,造成错支纱,为保证纺纱质量,需加装赛络纺单纱打断装置,一股断头后打断装置能将另一股单纱打断。
新西兰羊毛研究机构的子公司发展公司是首批授权的赛络纺技术传授者之一,该技术能生产单股精梳毛纱,这种纱可以不经上浆或任何后整理而直接作为经纱进行织造。
无须双股并纱或应用保护涂层面而直接织造单股纱的能力,长期来一直是精梳毛纺业追寻的目标。
赛络纺纱线显着增加了生产效率,并为羊毛开发新的产品提供了机遇。
该技术的基础是一对附加罗拉,它与一个简单的夹钳一起安装在细纱机的牵伸摇架上。
这些获专利的罗拉有一个特殊的沟槽表面,它改变了纤维捻入牵伸须条的方式,而对常规操作无任何影响。
它也可以与自动落筒装置相容。
乍看起来成品纱与常规纱无任何区别,但磨损试验清楚地显示了它非常优越的质量。
该加工过程保证纤维被牢牢地锁入纱线的结构中,使纱线更光洁,从而能抵御织机上的连续摩擦和磨损。
然而,单纱的织造不仅仅考虑产品质量,更多的是考虑生产效率。
首先,由于免去了加捻和相应的处理,整个生产过程大大缩短。
其次,与常规纱相比生产同样数量的织物,由于赛络纺只需提供一半长度的纱,因而显着地提高了细纱生产率,且由于纺制两倍于常规纱的支数,断头率也显着
下降。
在可织单纱计划的中试阶段,意大利、澳大利亚和新西兰的工厂将该罗拉各安装了一台细纱机,生产出商业批量的纱,接着将这些纱织入一系列的织物中。
所有的报告都反映出纺纱和织造的效率都是令人满意的。
在强力、伸长和均匀度方面,赛罗纺纱与传统的双股纱没有明显的差别。
纺纱后赛络纺纱将以普通的单股纱同样的方式进行自动蒸压定形、络筒、清纱和捻接。
采用赛罗纺纱技术纺股线可以省却两股并合和加捻的工序而降低生产成本。
它在环锭精纺机上平行喂入两根粗纱,经牵伸后在前罗拉输出再将两股须条加捻成纱。
印度纺织科学技术研究院对涤毛混纺比为55/45的赛罗纺纱工艺参数作了研究,并且与同等纱支的单纱和双纱作了对比。
在梳毛纺纱工艺系统中,采用3d涤纶和22.5μm羊毛以55/45混纺比纺Nm20赛络纱,用2.2d涤纶和20μm羊毛以55/45混纺比纺Nm35赛络纱,采用6、8、10、12、14mm五种不同的须条间距和75、85、95三种不同的捻系数分别进行试验。
成纱进行CV、纱疵、毛羽、单纱强力和断裂伸长以及
耐磨性和压缩系数的对比。
同时与同等纱支的单纱和双纱进行对比。
试验结果表明,涤毛混纺的赛络纱的特性可以通过工艺参变数的选择而优化。
须条间距为
10mm时成纱CV和耐磨性较好,然而间距增大会使细节增多。
当须条间距为12mm 时强力和断裂伸长最大。
须条间距不同对成纱毛羽因纱支而异,间距增加到10mm,则长短毛羽趋向减少。
须条间距对成纱压缩系数没有影响。
一般捻系数较大则成纱不匀,毛羽和压缩系数较低,强力和耐磨性较好。
除CV、纱疵和断裂伸长外,赛络纱的其他性能比同等纱支的单纱或双纱更好。
在赛络纺纱线结构中成纱与单股均有一定的捻度,其成纱过程中实际进行了二次加捻,其单股与成纱具有同向
加捻的效果,从而纱线外表光洁、平滑、毛羽少、耐磨性能好,虽然是单纱但有股线的效果,可部分取代股线,因而减少了工序,降低了成本,增加了企业经济效益。
赛络纺与普通环锭纱相比,毛羽大大减少,为后道工序的织造提供了良好的条件。
由于双粗纱喂入,细纱机上的吊锭需要增加一倍,另外每一股粗纱的定重要比同实纺支数的传统单纱的粗纱轻一半,而且赛络纺必须有切断装置,在纺纱过程中,万一有一股纤维束断裂,必须及时将另一股纤维束切断,否则会造成纱疵。
有不少文章讨论赛络纺粗纱间距大小问题,笔者认为粗纱间距确实对纺纱质量有很大
的<BR>关系,但却不能有一个定值。
为什么?因为这粗纱间距的确定还受原料情况的制约。
假设粗纱间距定14毫米,如果你的原料强力较差,或者段毛较多,设备状态较差那就很容易产生条干不匀以及断头增加,相反地你适当将开档缩小一点,那纱线条干质量断头数量就会有所改善。
反过来说,你定了粗纱间距以后,你必须控制你的原料物理指标使其符合纺纱要求。
赛络纺一般都配置打断器,打断器都依据粗纱间距来设计的,当须条间距变小后,纱线断头时打断器可能检测不出(无断头信号)从而不能打搅断另一股纤维束以致产生跑单纱的纱疵。
介绍了赛络纺纱技术的原理,在棉纺细纱机上的实现方法,赛络纺纯棉精梳纱、混纺纱和涤粘复合纱的纺纱工艺,对比分析了赛络纺成纱质量与环锭纺成纱质量。
认为赛络纱的成纱毛羽、条干、强力优于环锭纱,但细节差于环锭纱。
传统环锭纺纱成纱毛羽多,毛羽不仅影响纱线本身的表面光洁度和纤维强力利用系数,而且影响后工序加工的顺利进行。
另一方面随着织造技术进步,无梭织机对成纱质量的要求越来越高,毛羽问题更为突出。
为了减少成纱毛羽,可以在原料选配、工艺优化、器材选择和操作管理等方面采取措施。
同时,也可以应用纺纱新技术,如紧密纺纱技术、络筒机吹捻装置。
此外,赛络纺纱技术也可以减少成纱毛羽。
该纺纱原理是1975年~1976年由澳大利亚联邦科学与工业研究机构(CSIRO)发明,最初的目的是要减少毛纱毛羽。
1978年国际羊毛局将这项科研成果推向实用化,1980年正式向世界各国推荐。
赛络纺纱主要用于羊毛、毛型涤纶、腈纶的纯纺或混纺,在棉纺细纱机上也可以应用。
赛络纺纱技术在实际生产中实施起来非常简便,对环锭细纱机稍作改动即可,改造后的纺纱机既可纺制赛络纱线,也可以根据需要随时方便地恢复成原来的普通环锭细纱机。
1 赛络纺纱方法:
赛络纱可以用于机织或针织,其工艺是将两根具有一定间距的粗纱平行喂人到细纱机同一牵伸区进行牵伸,然后在同一个锭子上加捻卷绕。
具体地说,需要进行以下几方面的改造:(1)改装粗纱架,增加一倍的粗纱吊锭,托锭加吊锭改装更方便些;(2)将原来牵伸机构中的横动喇叭口调换为双眼形式;(3)导纱
横动装置固定在中央位置或作小动程横动;(4)增加断头自停装置,其作用是防止纺单纱现象,即当一根粗纱条断头时,为避免产生长片段细节纱疵,必须将另一根纱条也及时打断。
近年来,棉纺行业也开始引用这种纺纱方法。
一般棉纺所纺纱线多为本色纱,只要减少挡车工的看台数,可以不采用价格昂贵的断头自停装置。
2 赛络纺纱实践
2.1纯棉精梳产品
在改造过的细纱机上纺CJ 14.5 tex赛络纱,采用两种不同的纺纱工艺流程。
赛络纺CJ 14.5 tex与环锭纺CJ 14.5 tex成纱质鼍对比见表1。
从表1可以看出,赛络纱的条干CV值、单纱断裂强力、断裂伸长率等指标优于环锭纱,但细节偏多。
方案一所纺赛络纱的条干、细节、粗节、单强、伸长率等指标优于方案二,综合性能最佳。
参照2001年乌斯特公报,方案一的成纱条干、粗节、棉结都相当于5%~25%的水平,细节相当于25%~50%的水平。
2.2混纺产品
在相同条件下纺制T/CJ 65/35 13.1 tex赛络纱和普通环锭纱,赛络纺纱工艺为:粗纱号数330tex,牵伸倍数(前×后)39.6倍×1.25倍,捻度34.5捻/m;细纱机前罗拉速度229 r/min,锭速17278 r/min。
成纱质量对比见表2。
同细度的赛络纱与环锭纱相比,赛络纱单强高,百米重量CV小,毛羽减少,条干质量基本相当,细节多,粗节、棉结数量相当。
2.3 复合纱
当喂入两根粗纱为不同原料时,纺出纱为复合纱,又称AB纱。
利用赛络纺纱技术纺制T/R55/45 18.5 tex复合纱,细纱工艺为:涤纶粗纱定量3.9g/10 m,
粘胶粗纱定量3.2g/10 m,细纱捻系数314,罗拉隔距19 mm×33 mm,后区牵伸倍数1.25倍,钳口隔距3.0 mm,钢丝圈型号FU5/0,前罗拉速度230 r/min,锭速14 400 r/min。
成纱质量为:条干CV 13.46%,细节5个/km,粗节46个/km,棉结59个/km,单强23.3 cN/tex,单强CV值5.72%,断裂伸长率10.86%,断裂伸长CV5.09%。
由此可以看出,赛络纺复合纱的质量指标比较理想。
3 结束语
赛络纱质量较好,尤其是成纱毛羽、条干、强力指标优于环锭纱,可以满足机织和针织用纱要求。
赛络纱的缺点是细节偏多,主要是由于从前钳口输出两根纱条的汇聚点在纺纱过程中上下不断波动,引起汇聚点至前钳口一段纱条上的捻度大小发生变化,捻度小、意外牵伸大造成细节偏多。
同时赛络纺加工时要求细纱大牵伸、粗纱小定量,又影响到了经济效益,这方面需要进一步改进提高。