紧密纺和赛络纺知识
紧密纺_赛络纺纺纱经验及其探讨_王方水

紧密纺、赛络纺纺纱经验及其探讨王方水,郭 恒,贾云辉(鲁泰纺织股份有限公司,山东淄博 255100)摘要:介绍了紧密纺、赛络纺等新型纺纱技术原理及紧密纺纱线在色织面料方面的应用;分析紧密纺、赛络纺技术的优点及不足,并将其与普通纺进行对比,指出紧密纺、赛络纺技术生产的纱线质量好、强力高、毛羽少、条干均匀以及下游工序产品质量可进一步提高;加强对设备的日常维护、保养、保持器材部件清洁、运转正常,对充分发挥新型纺纱技术的优势至关重要,但企业要充分考虑其成本因素,应加速研发具有自己特色和自主知识产权,纺织企业能够接受的整机型和改造型的紧密纺细纱机及装置,以提高企业的竞争力。
关键词:紧密纺;塞络纺;优势;不足;器材配置;日常维护;竞争力中图分类号:TS104.7 文献标识码:A 文章编号:1001-9634(2009)03-0057-04收稿日期:2008-10-28作者简介:王方水(1961 ),男,山东淄博人,工程师,主要从事纺纱色织布的研究。
1 紧密纺等新型纺纱自1999年巴黎国际纺织机械展览会,立达(R-ieter )、青泽(Zinser )、绪森(Suessen)等国外纺机公司推出生产紧密纱的环锭细纱机以来,紧密纺纱技术迅速风靡整个纺织界。
紧密纺纱技术对改善纱线品质、提高成纱强力、减少毛羽等方面已经由实践证实,得到了快速发展。
欧洲计划用5a~10a 以紧密纺纱机全部替代普通环锭纺纱机,更有专家预言,未来属于紧密纺。
1.1 紧密纺纱原理紧密纺纱系统多数采用空气动力学原理,在纺纱三角区位置,通过一组集聚元件,使牵伸后的松散纤维须条经过负压吸聚管表面时,利用空气导向作用使纤维紧密地抱合在一起,经导向胶辊输出加捻成纱,纺纱过程中加捻三角区变得很小,基本消失,大大减少浮游外露纤维(即毛羽)的数量。
还有一种紧密纺纱系统不采用吸风而采用机械-磁铁原理工作,如瑞士罗托卡夫特公司生产的罗卡斯(Ro Co S)紧密纺系统装置,其前胶辊和引纱胶辊置于前下罗拉之上,磁性紧密器置于两个胶辊之间,共同形成紧密区。
环锭纺、气流纺、喷气纺、涡流纺、赛络纺、紧密纺简介

环锭纺、气流纺、喷气纺、涡流纺、赛络纺、紧密纺简介环锭纺、气流纺、喷气纺、涡流纺、赛络纺、紧密纺简介环锭纺环锭纺纱是现时市场上用量最多,最通用之纺纱方法,条子或粗纱经牵伸后的纤维条通过环锭钢丝圈旋转引入,筒管卷绕速度比钢丝圈快,棉纱被加捻制成细纱.广泛应用于各种短纤维的纺纱工程.如普梳,精梳及混纺,钢丝圈由筒管通过纱条带动绕钢领回转.进行加捻,同时,钢领的摩擦使其转速略小于筒管而得到卷绕.纺纱速度高,环锭纱的形态,为纤维大多呈内外转移的圆锥形螺旋线,使纤维在纱中内外缠绕联结,纱的结构紧密,强力高,适用于制线以及机织和针织等各种产品。
环锭纺(精梳)流程:清花间--梳棉--预并条--条并卷--精梳--头道并条--二道并条--粗纱--细纱--络筒环锭纺(普梳)流程:清花间--梳棉--头道并条--二道并条--粗纱--细纱--络筒气流纺气流纺不用锭子,主要靠分梳辊、纺杯、假捻装置等多个部件。
分梳辊用来抓取和分梳喂入的棉条纤维,同过他的高速回转所产生的离心力可把抓取的纤维甩出。
纺杯是个小小的金属杯子,他的旋转速度比分梳辊高出10倍以上,由此产生的离心作用,把杯子里的空气向外排;根据流体压强的原理,使棉纤维进入气流杯,并形成纤维流,沿着杯的内壁不断运动。
这时,杯子外有一根纱头,把杯子内壁的纤维引出来,并连接起来,再加上杯子带着纱尾高速旋转所产生的钻作用,就好像一边“喂”棉纤维,一边加纱线搓捏,使纱线与杯子内壁的纤维连接,在纱筒的旋绕拉力下进行牵伸,连续不断的输出纱线,完成气流纺纱的过程。
气流纺的特征气流纺纱有速度大、纱卷大、适应性广、机构简单和不用锭子、钢领、钢丝圈的优点,可成倍的提高细纱的产量。
气流纺与环锭纺的区别气流纺与环锭纺一个是新型纺织技术,一个是老式纺纱技术。
气流纺是气流纺纱,而环锭纺则是机械纺,就是由锭子和钢铃、钢丝圈进行加捻,由罗拉进行牵伸。
而气流纺则是由气流方式输送纤维,由一端握持加捻。
一般来说,环锭纱毛羽较少,强度较高,品质较好。
赛络紧密纺资料

3.1 紧密纺纱的原理
为在环锭纺纱机上达到上述要求,需要在牵伸系统 后面加一个凝聚区,它通常由带狭槽的异形截面吸管 和多孔网格皮圈组成或者由多孔辊筒和辊筒内带长糟 的异形截面吸管组成,以及其他的凝聚装置。
异形截面吸管内呈负压状态, 异形截面吸管的每 个纺纱位置如图有一个长槽。当纤维须条离开钳口时, 它们就被长槽头端的负压气流控制,并被压向带皮圈 多孔辊简的表面;在负压的吸引下,纤维须条沿着长 槽运行至长糟的尾端。纤维须条在整个长槽上都受到 负压控制,使各根纤维紧密排列。
的抖动,加捻平衡受到干扰,因此须条也具有一定捻度。 须条上的平衡捻度大小取决于汇聚点以上须条上的扭矩与 并台加捻时成纱中的扭矩之间的平衡。因而,在平衡状态 下,须条中的捻度,仅仅取决于加捻时的成纱捻度和成纱 须条中的螺旋线半径。
2.1.2 汇聚点位置
双须条纺纱时,只要汇聚点处的加捻平衡受到干扰,在 纱线形成时,须条捻 度被捕获。即使在普通的双须条成纱 过程中(即加捻平衡无抖动),由于须条中的粗、细节和纺 纱张力存在连续随机变化:这导致加捻平衡有细微抖动, 因此,须条捻度也会发生相对较少的随机变异。研究表明, 加捻平衡的周期性抖动,能导致须条位置相当大的变化。
2.3 新发展---赛络菲尔纺
三、紧密纺纱(集聚纺纱)
3.1 紧密纺纱的原理 3.2 紧密纺装置 3.3 紧密纺纱线结构及性能
三、紧密纺纱(集聚纺纱)
毛羽是预测纱线性能的主要指标之一,它是影响纱线后加 工及其产品档次的主要因素。然所有长度超过3mm的毛羽都会 给后续加工和织物质量带来很大危害。
0.1
0
粗节(+50%)/km 10.0
8.0
2.0
棉结(+200%)/km 17
环锭纺、气流纺、喷气纺、涡流纺、赛络纺、紧密纺简介

环锭纺、气流纺、喷气纺、涡流纺、赛络纺、紧密纺简介环锭纺环锭纺纱是现时市场上用量最多,最通用之纺纱方法,条子或粗纱经牵伸后的纤维条通过环锭钢丝圈旋转引入,筒管卷绕速度比钢丝圈快,棉纱被加捻制成细纱.广泛应用于各种短纤维的纺纱工程.如普梳,精梳及混纺,钢丝圈由筒管通过纱条带动绕钢领回转.进行加捻,同时,钢领的摩擦使其转速略小于筒管而得到卷绕.纺纱速度高,环锭纱的形态,为纤维大多呈内外转移的圆锥形螺旋线,使纤维在纱中内外缠绕联结,纱的结构紧密,强力高,适用于制线以及机织和针织等各种产品。
环锭纺(精梳)流程:清花间--梳棉--预并条--条并卷--精梳--头道并条--二道并条--粗纱--细纱--络筒环锭纺(普梳)流程:清花间--梳棉--头道并条--二道并条--粗纱--细纱--络筒气流纺气流纺不用锭子,主要靠分梳辊、纺杯、假捻装置等多个部件。
分梳辊用来抓取和分梳喂入的棉条纤维,同过他的高速回转所产生的离心力可把抓取的纤维甩出。
纺杯是个小小的金属杯子,他的旋转速度比分梳辊高出10倍以上,由此产生的离心作用,把杯子里的空气向外排;根据流体压强的原理,使棉纤维进入气流杯,并形成纤维流,沿着杯的内壁不断运动。
这时,杯子外有一根纱头,把杯子内壁的纤维引出来,并连接起来,再加上杯子带着纱尾高速旋转所产生的钻作用,就好像一边“喂”棉纤维,一边加纱线搓捏,使纱线与杯子内壁的纤维连接,在纱筒的旋绕拉力下进行牵伸,连续不断的输出纱线,完成气流纺纱的过程。
气流纺的特征气流纺纱有速度大、纱卷大、适应性广、机构简单和不用锭子、钢领、钢丝圈的优点,可成倍的提高细纱的产量。
气流纺与环锭纺的区别气流纺与环锭纺一个是新型纺织技术,一个是老式纺纱技术。
气流纺是气流纺纱,而环锭纺则是机械纺,就是由锭子和钢铃、钢丝圈进行加捻,由罗拉进行牵伸。
而气流纺则是由气流方式输送纤维,由一端握持加捻。
一般来说,环锭纱毛羽较少,强度较高,品质较好。
气流纺工序短,原料短绒较多,纱线毛,支数和拈度不能很高,价格也较低。
新型纺纱问答题 整理

新型纺纱12个重点问答题1、紧密纺如何消除加捻三角?紧密纺是在传统牵伸装置前增加一个纤维控制区,利用气流或机械对通过控制区的纤维束进行横向集聚,使纤维束的宽度大大缩小至几乎接近加捻区的宽度,这样,纤维束经过集聚后被加捻卷绕,加捻三角区大大减小,几乎纤维束的每根纤维都能集聚到纱体中,形成的纱条毛羽少,强力高,条干好。
附:加捻三角区:纤维束分布宽度与纺纱三角区之间的差异,加捻三角区不可能把纤维束的所有纤维都聚拢捻合到纱线中。
2、赛络纺的工艺原理赛络纺是在细纱机上喂入2根保持一定间距的粗纱,经过牵伸后由前罗拉输出这2根单纱须条,并由捻度的传递而使单纱须条上带有少量的捻度,并合后被进一步加捻成类似合股的纱线,卷绕在筒管上。
工艺流程:开清棉——梳棉——并条——牵伸——2根单纱(少量捻度)——并合加捻——卷绕3、新型纺纱方法为什么多数能够大卷装?(以一个方法为例说明)传统的环锭细纱机,增大卷装的途径是增加筒管的长度和加大钢领直径,但是筒管加长将加大气圈高度,使小纱时气圈张力增大而导致断头增多,加大钢领直径时,钢丝圈的线速度会增大,断头增多。
因而环锭纺的卷装容量增大受到了严格的限制。
而各种新型纺纱方法将加捻和卷绕分开进行,可以直接成筒子纱,卷装容量大大增加。
举例:转杯纺的加捻在转杯内实现,加捻后的纱条经引纱罗拉引导,依靠卷绕罗拉(槽筒)回转成筒子。
4、影响环锭纺纱高速的主要原因(至少2个)A、锭子高速必然引起钢丝圈高速,钢丝圈与钢领间属于干摩擦,钢丝圈极易因过热产生飞圈增加断头。
B、锭速提高,纱线张力和张力波动增加且气圈形态不稳定,使纺纱断头增加。
5、转杯纺喂给分梳机构的作用是什么?喂给机构:喂给喇叭作用:引导条子和防止条子打结。
整理、压缩、均匀棉条。
喂给罗拉和喂给板:两者的合理配合,保证条子的均匀喂给以及分梳辊良好的分梳效果(分梳时,均匀有效地握持条子,供分梳辊分梳)分梳机构:作用:依靠分梳辊(锯条或梳针)打击和刺入纤维层,将纤维束分梳成单纤维状态,依靠气流将纤维输送到转杯内。
紧密纺和赛络纺的区别

紧密纺和赛络纺的区别
紧密纺和赛络纺的区别,紧密纺是在改进的新型环锭细纱机上进⾏纺纱的⼀种新型纺纱技术。
其纺纱机理主要是:在环锭细纱机牵引装置前增加了⼀个纤维凝聚区,基本消除了前罗拉⾄加捻点之间的纺纱加捻三⾓区。
纤维须条从前罗拉前⼝输出后,先经过异形吸风管外套⽹眼⽪圈,须条在⽹眼⽪圈上运动,由于⽓流的收缩和聚合作⽤,通过异形管的吸风槽使须条集聚、转动,逐步从扁平带状转为圆柱体,纤维的端头均捻⼊纱线内,因此成纱⾮常紧密,纱线外观光洁、⽑⽻少。
紧密纺纱线强⼒较⾼,⽑⽻较少。
赛络纺是由两根有⼀定间距的须条喂⼊细纱牵伸区,分别牵伸后加捻成纱,两股须条存在⼀股断头后另⼀股跑单纱的情况,并且在纺纱张⼒稳定的情况下不断头,造成错⽀纱,为保证纺纱质量,需加装赛络纺单纱打断装置,⼀股断头后打断装置能将另⼀股单纱打断。
拓展知识1 紧密纺和赛络纺
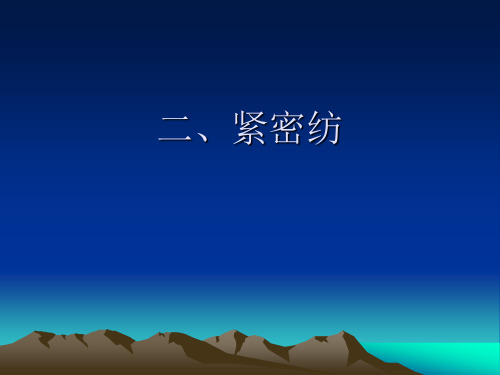
根据紧密纺产生集聚作用的方式不 同,紧密纺系统可分为哪两大类
• 目前较为成熟的集聚环锭纺纱技术的原理主要有 两种:气动式和机械式集聚系统。 • 气动式集聚系统是利用负压气流将纤维收缩、聚 合,使须条边缘快速向须条中心集聚,最终最大 限度地减少纺纱三角区。瑞士Rieter公司、德国 Zinser公司和Sussen公司、意大利Marzoli公司、 日本Toyota公司采用的都是气动式集聚系统,只 是形式各不相同。
• V/F控制不是必选的,可以选用矢量控制变频器, 也可以选用直接转矩控制的变频器啊。V/F控制的 缺点,主要是由两个:第一,是开环控制方式; 第二,是低频扭矩比较小,对于大惯量的负载, 可能造成启动困难,甚至是启动不了。现在风机 水泵类负载,一般还是倾向于使用V/F变频器,这 是一个不争的事实,这是因为,风机水泵类负载, 对于变频器的要求是比较低:第一,风机水泵之 类属于轻载,对低频扭矩不是很关心;第二,风 机水泵的控制是比较简单,无非就是恒压、恒静 压之类的控制,即使不用闭环控制,也能达到较 好的节能效果;第三,相对于矢量控制、直接转 矩控制的变频器来讲,V/F的变频器在价格上还是 有优势的。
5、瑞士罗卡斯公司的紧密纺 (磁铁-机械式紧密纺)
• 在前皮辊和引纱皮辊之间有一个磁性紧密 器,紧密器与下罗拉紧密接触,没有间隙, 上下罗拉一起形成一个完全封闭的负压室, 纤维束与罗拉同步移动,通过紧密器的纤 维通道,被安全地输送到引纱钳口。 • 罗卡斯可确保最佳集聚,简便可靠,不增 加任何纺纱成本。
变频器节能
现环锭细纱机特点及控制电路存在的问题 现有的环锭细纱机纺纱速度主要受细纱断头的约束, 而细纱断头又是细纱生产中的主要危害,也是细 纱生产实现优质、高产、低耗的主要障碍,直接 影响到细纱的质量、产量及生产效率。环锭细纱 机纺纱速度的提高受到纺纱气圈的牵制,气圈张 力变化又受气圈角度速度、卷绕半径、气圈高度 等因素影响,细纱断头的另一个主要原因就是气 圈张力值瞬时超过纱线的抱合强力值造成的,减 少断头率是提高细纱质量和产量主要的关键。
纱线基础知识-图文详解版
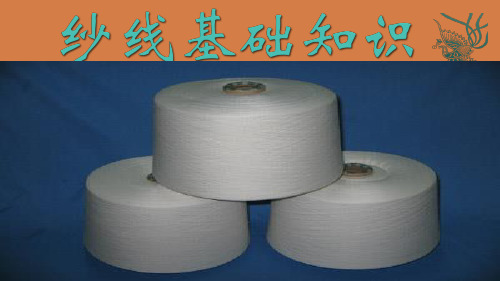
公制支数(Nm)和英制支数(Ne)
公制支数(Nm)
是指在公定回潮率时,一克重的纱线 (或纤维)所具有的长度米数。
公制支数可表示成“20公支、40公支”的 形式,意谓着一克重的纱线具有20m长或 40m长。
b. 英制支数(Ne)
指1磅(454克)重的棉纱线有几个840 码(1码=0.9144米)长。
气流纱: (OPEN END)
也称转杯纺纱,是利用气流将纤维在高速 回转的纺纱杯内凝聚加捻输出成纱。
气流纱特点:
纱线结构比环锭纱蓬松、耐磨、条干均匀、 染色较鲜艳,但强力较低。
主要用于机织物中膨松厚实的平布、手感 良好的绒布。
1.机织用纱: (Weaving)
机织用纱指加工机织物所用纱线,分经纱和 纬纱两种。 经纱:
按照纺纱系统分:
精梳纱 普梳纱 废纺纱
精纺纱 (JC/CJ) (CM combed)
也称精梳纱,是指通过精梳工序纺成 的纱,包括精梳棉纱和精梳毛纱。
精梳纱特点
纤维平行伸直度高,条干均匀、,但 成本较高,纱支较高。
主要用于高级织物及针织品的原料, 如细纺、华达呢、花呢、羊毛衫等。
2.粗纺纱(C) ( CD CARDED) 不经过精梳工序纺成的纱。
捻度 、强力、 纱支 、条干 、细节、 粗节、 棉结 属于乌斯特指标,用乌斯特仪器测出来
捻度: (TWIST)
是指纱线单位长度上的捻回数。
国内: 其计量单位为“捻/10cm” 或“捻 /m”
国外: 用英寸捻度表示:TPI= 捻/INCH 捻 度/英寸
捻度/10cm
捻/10cm
捻度对纱线的影响:
所有的化纤和纤维素纤维都不走精梳工序 普梳纱特点及用途
环锭纺、气流纺、喷气纺、涡流纺、赛络纺、紧密纺简介
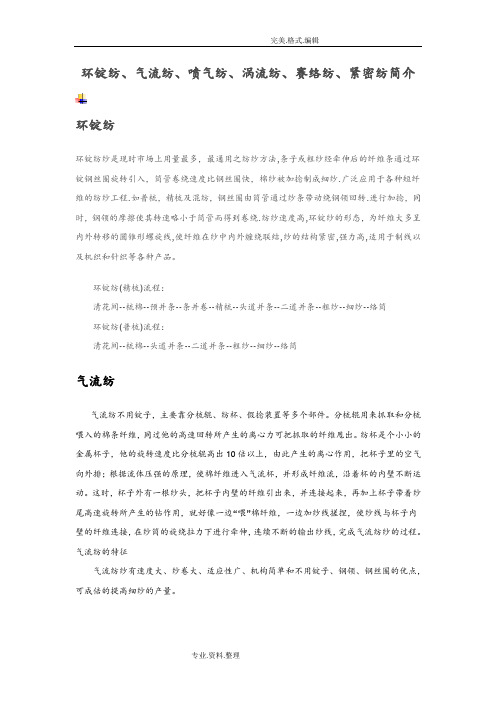
环锭纺、气流纺、喷气纺、涡流纺、赛络纺、紧密纺简介环锭纺环锭纺纱是现时市场上用量最多,最通用之纺纱方法,条子或粗纱经牵伸后的纤维条通过环锭钢丝圈旋转引入,筒管卷绕速度比钢丝圈快,棉纱被加捻制成细纱.广泛应用于各种短纤维的纺纱工程.如普梳,精梳及混纺,钢丝圈由筒管通过纱条带动绕钢领回转.进行加捻,同时,钢领的摩擦使其转速略小于筒管而得到卷绕.纺纱速度高,环锭纱的形态,为纤维大多呈内外转移的圆锥形螺旋线,使纤维在纱中内外缠绕联结,纱的结构紧密,强力高,适用于制线以及机织和针织等各种产品。
环锭纺(精梳)流程:清花间--梳棉--预并条--条并卷--精梳--头道并条--二道并条--粗纱--细纱--络筒环锭纺(普梳)流程:清花间--梳棉--头道并条--二道并条--粗纱--细纱--络筒气流纺气流纺不用锭子,主要靠分梳辊、纺杯、假捻装置等多个部件。
分梳辊用来抓取和分梳喂入的棉条纤维,同过他的高速回转所产生的离心力可把抓取的纤维甩出。
纺杯是个小小的金属杯子,他的旋转速度比分梳辊高出10倍以上,由此产生的离心作用,把杯子里的空气向外排;根据流体压强的原理,使棉纤维进入气流杯,并形成纤维流,沿着杯的内壁不断运动。
这时,杯子外有一根纱头,把杯子内壁的纤维引出来,并连接起来,再加上杯子带着纱尾高速旋转所产生的钻作用,就好像一边“喂”棉纤维,一边加纱线搓捏,使纱线与杯子内壁的纤维连接,在纱筒的旋绕拉力下进行牵伸,连续不断的输出纱线,完成气流纺纱的过程。
气流纺的特征气流纺纱有速度大、纱卷大、适应性广、机构简单和不用锭子、钢领、钢丝圈的优点,可成倍的提高细纱的产量。
气流纺与环锭纺的区别气流纺与环锭纺一个是新型纺织技术,一个是老式纺纱技术。
气流纺是气流纺纱,而环锭纺则是机械纺,就是由锭子和钢铃、钢丝圈进行加捻,由罗拉进行牵伸。
而气流纺则是由气流方式输送纤维,由一端握持加捻。
一般来说,环锭纱毛羽较少,强度较高,品质较好。
气流纺工序短,原料短绒较多,纱线毛,支数和拈度不能很高,价格也较低。
紧密纺的原理
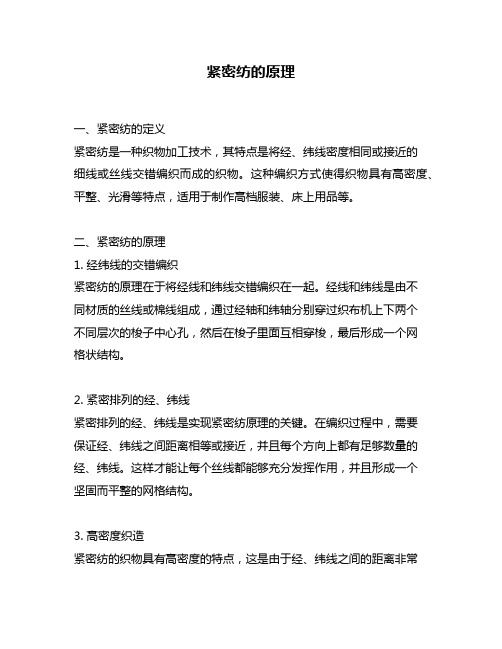
紧密纺的原理一、紧密纺的定义紧密纺是一种织物加工技术,其特点是将经、纬线密度相同或接近的细线或丝线交错编织而成的织物。
这种编织方式使得织物具有高密度、平整、光滑等特点,适用于制作高档服装、床上用品等。
二、紧密纺的原理1. 经纬线的交错编织紧密纺的原理在于将经线和纬线交错编织在一起。
经线和纬线是由不同材质的丝线或棉线组成,通过经轴和纬轴分别穿过织布机上下两个不同层次的梭子中心孔,然后在梭子里面互相穿梭,最后形成一个网格状结构。
2. 紧密排列的经、纬线紧密排列的经、纬线是实现紧密纺原理的关键。
在编织过程中,需要保证经、纬线之间距离相等或接近,并且每个方向上都有足够数量的经、纬线。
这样才能让每个丝线都能够充分发挥作用,并且形成一个坚固而平整的网格结构。
3. 高密度织造紧密纺的织物具有高密度的特点,这是由于经、纬线之间的距离非常短,每个方向上都有足够数量的经、纬线。
这种高密度织造使得织物更加平整、光滑,并且可以有效地防止织物表面出现毛刺、起球等现象。
4. 特殊的织造方式紧密纺的原理还包括一些特殊的织造方式,例如采用双层或多层编织技术、采用不同材质丝线交错编织等。
这些特殊的技术可以进一步增强织物的强度、耐久性和美观性。
三、紧密纺与其他编织方式的比较1. 与平纹比较平纹是最基本的编织方式之一,其原理是将经线和纬线交错编织在一起,但是经、纬线之间距离较大。
相比之下,紧密纺更加致密,可以形成更加坚固和平整的网格结构。
2. 与斜纹比较斜纹是一种斜向交错编织方式,其原理是将经线和斜向交错的纬线编织在一起。
相比之下,斜纹的织物更加柔软、透气,但是强度和耐久性较差,不适合制作高档服装等。
3. 与针织比较针织是一种由单根或多根丝线按照特定方式交织而成的编织方式。
相比之下,针织的织物更加柔软、弹性好,但是密度较低,容易出现毛刺和变形等问题。
四、紧密纺的应用紧密纺可以用于制作各种高档服装、床上用品、鞋帽等产品。
其优点在于具有高密度、平整、光滑等特点,可以有效地提升产品的品质和价值。
紧密赛络纺技术的特点及在牛仔纱生产中的应用

紧密赛络纺技术的特点及在牛仔纱生产中的应用随着消费者对牛仔服装的热爱和生活水平不断提高,牛仔布面料的要求也越来越高,新的纺纱原料和纺纱方法正逐渐应用在生产实践中。
一、前言1、赛络纺是在传统环锭细纱机上纺出类似于股线结构的纱线的一种纺纱方法。
赛络纺技术最早在毛纺上得到应用,后逐步应用到棉纺上。
赛络纺纱是采用两根粗纱从喇叭口喂入,在前后牵伸区仍然保持两根须条的分离状态,从前钳口输出一定长度后合并,并由同一个锭子加捻,形成有双股结构特征的赛络纱。
赛络纺的同向同步加捻使其纱线具有特殊的结构,赛络纺纱表面纤维排列整齐,纱线结构紧密,毛羽少,抗起毛起球好。
赛络纺织物和股线织物相比,手感柔软,比较平滑。
赛络纺纱可用于机织物及针织物,也可替代股线用于高支高密织物。
2、紧密纺技术是基于传统环锭纺的一种新型环锭纺纱技术。
简单地说就是使细纱机牵伸后输出的纤维致密化的纺纱技术,即通过在须条加捻前增加吸风装置,通过负压的控制,使松散纤维集聚、抱合,纤维在受控制区域内充分伸直,缩小传统纺纱机上的加捻三角区,便纤维在平行紧密的状态下实现加捻。
由于须条中各纤维受力均匀,抱合紧密,使成纱结构和质量得到全面提升,毛羽、强力、条干,耐磨性,纱线外观有了显著的改善。
3、紧密赛络纺是紧密纺和赛络纺相结合的一种组合工艺纺纱方法,该技术所纺制的纱线,结合了两种纺纱法的优异特性和品质,与传统环锭纺单纱及赛络纱相比,紧密赛络纱毛羽更少,强力更高,更具有赛络纺合股的效果,是纺制高档织物的理想原料,具有良好的发展前景。
二、我国牛仔布的起源及发展现状牛仔以其粗犷、豪放、洒脱大方、自然的风格以及结构紧密厚实,穿着柔软,质地耐磨结实的特点,广受人们的青睐。
我国作为牛仔布生产的大国,年产能力已达15亿平方米以上,但并非产销强国,其产品主要是以量取胜的传统大路货品种,其品牌,价格在国际上普遍缺乏竞争力。
提升产品的质量档次,开发出更多高附加值的新产品是产业升级的重要方法。
紧密纺和赛络纺知识

紧密纺和赛络纺知识近年来,关于紧密纺及赛络纺两种新型纺纱方法的报道很多,这两种新型纺纱工艺对于提高成纱质量的效果也是大家所公认的,本文将根据我公司4年多来的研究结果及用户的使用情况,对两种纺纱工艺的特点及成纱质量进行分析。
紧密纺纱工艺尽管在机械结构上有所不同,但有一点是相同的,即在完成工艺要求的牵伸之后,在加捻之前,把从前罗拉钳口输出的较宽的纱条进行聚集,使得纱条宽度变的很窄,单纤维之间排列更加紧密,并且尽量保持在这种状态下进入加捻区。
虽然有的报道说是此举消灭了“加捻三角区”,但实际上纱条在加捻前后的宽度是不一样的。
所以,紧密纺的加捻罗拉钳口处仍然有一个极小的所谓“加捻三角区”,当然其危害性已降低到最小。
正是由于上述成纱机理,用紧密纺工艺纺成的细纱具有以下特点:1.由于在加捻前,纱条中单纤维充分伸直,相互平行,而且排列紧密,所以在加捻罗拉钳口处(也叫阻捻罗拉,因为其有阻止捻度传递的作用),纱条直径变得很小,所以基本消除了“加捻三角区”,由于加捻前单纤维充分伸直、平行,没有毛羽伸出纱条主体,所以成纱毛羽很少,特别是3毫米以上毛羽极少。
2.在细纱中由于各单纤维是在伸直、平行的状态下加捻,在单纱受到拉力时,各单纤维受力基本一致,所以紧密纺强力比传统单纱高。
而且由于紧密纱中的单纤维排列紧密,相互间抱合力大,这也有助于提高纱线的强力。
3.在紧密纺工艺中,纱条是在完成了工艺规定的牵伸之后再进行聚集,所以其条干不匀的指标没有大的改善,但在其聚集区有对纱条的整理作用,且在加捻罗拉钳口处加捻时纤维的内、外层转移没有传统工艺强烈,所以紧密纱的条干不匀,粗、细节指标比传统纱要好。
4.由于紧密纱的上述特点,为下道工序提供了非常好的条件,紧密纱毛羽少,所以减轻了上浆、烧毛等工序的压力,在无梭织机的纬纱使用紧密纱时大大减少了引纬的阻力,提高了织机效率。
5.由于紧密纱纤维排列紧密,和相同号数的传统纱线相比直径小,所以用相同经、纬密织成的布透气性好,布面平整、光滑,是高档纺织品的理想用纱。
解释紧密纺和赛络纺

解释紧密纺和赛络纺
嘿,咱今儿个就来唠唠紧密纺和赛络纺!你知道啥是紧密纺不?就好比那精密的仪器,把纤维紧紧地拢在一起,织出来的布那叫一个细腻光滑!比如说吧,就像你做一件精细的手工活儿,每一个步骤都得特别仔细,紧密纺就是这样,把纤维梳理得特别整齐,纺出来的纱线质量可高啦!
再来说说赛络纺,这赛络纺就像是一场精彩的团队合作!两根纱线并在一起,互相配合,就像两个好朋友一起努力完成一件大事儿。
你想想看,是不是感觉特别神奇?比如说咱平时和朋友一起搭积木,两个人齐心协力搭出来的城堡肯定更稳固更好看呀,赛络纺也是这个道理。
紧密纺织出来的布啊,那手感,啧啧,简直绝了!就像摸着丝滑的巧克力一样。
而赛络纺的布呢,有着独特的纹路和质感,就如同那有着独特风格的艺术品。
你说,这两种纺织方法是不是各有千秋?
在实际应用中,紧密纺常用于制作高档的衣物,让你穿上身就感觉自己特别有范儿。
赛络纺呢,则在一些需要特殊效果的纺织品中大放异彩,给人带来不一样的视觉和触觉感受。
咱生活中很多漂亮的衣服可都是靠它们呢!紧密纺和赛络纺,就像是纺织世界里的两颗璀璨明星,各自闪耀着独特的光芒,为我们的生
活增添了无尽的色彩和美好。
它们就是纺织工艺里的宝贝呀,让我们的穿着更加丰富多彩!。
新纺紧密纺及名词解释

紧密纺纱(Compact Spinning)紧密纺又称:集聚纺,卡摩纺、依丽纺二、紧密纺纱设计原理(一) 环锭纺纱强力高的原因环锭纱中纤维形态转杯纱中纤维形态环锭纱形成圆锥形螺旋线的原因:加捻三角区F1=Fsinα使纱线向中间转移F2=Fcosα使纱线沿纱轴运动(二) 加捻三角区引起的问题1.毛羽的形成头端毛羽形成尾端毛羽形成2.飞花的形成细纱车间85%的飞花是加捻三角区产生的。
3.纤维张力不匀边缘纤维形成纱线表面纤维,预张力大,拉伸时先断裂飞花形成中间纤维形成纱芯校外,预张力小,拉伸时后断裂纤维不同时断裂,纱线强力低(三) 紧密纺纱的设计理念紧密纺设计理念:缩小甚至去掉加捻三角区三、紧密纺纱的机构及原理(一)瑞士立达Comforspin1. 瑞士立达Comforspin 纺纱装置示意图2. 瑞士立达Comforspin 纺纱装置照片3. 瑞士立达Comforspin 纺纱装置吸风内胆4. 瑞士立达Comforspin 纺纱装置成纱过程5. 瑞士立达Comforspin 纺纱装置纺纱效果6. 瑞士立达Comforspin 纺纱装置纺纱效果环锭纺纱线紧密纺纱线(二)德国Sussen Elite 纺纱装置1.机构示意图2.德国Sussen Elite 纺纱装置照片3.德国Sussen Elite 纺纱装置纺纱效果(三)德国青泽Zinser 纺纱装置1.机构示意图2.德国青泽Zinser 纺纱装置照片3.德国青泽Zinser 纺纱装置纺纱效果(四)德国Rocos 纺纱装置德国Rocos 纺纱装置纺纱效果四、德国青泽Zinser 纺纱装置录像五、紧密纺纱的优点1.纱线毛羽少:3mm以上毛羽减少70%-80%。
2.纤维平行取向度好,纤维整体结构好,取向规则,纤维利用率高,纤维张力均匀,拉伸时同时断裂纤维多,纱线强力高,伸长率大,耐磨性大。
强力提高10%-20%,伸长率提高20%。
3.减少了络筒、整经、织布、针织等工序的断头,提高了经济效益。
紧密纺和赛络纺知识

紧密纺和赛络纺知识近年来,关于紧密纺及赛络纺两种新型纺纱方法的报道很多,这两种新型纺纱工艺对于提高成纱质量的效果也是大家所公认的,本文将根据我公司4年多来的研究结果及用户的使用情况,对两种纺纱工艺的特点及成纱质量进行分析。
紧密纺纱工艺尽管在机械结构上有所不同,但有一点是相同的,即在完成工艺要求的牵伸之后,在加捻之前,把从前罗拉钳口输出的较宽的纱条进行聚集,使得纱条宽度变的很窄,单纤维之间排列更加紧密,并且尽量保持在这种状态下进入加捻区。
虽然有的报道说是此举消灭了“加捻三角区”,但实际上纱条在加捻前后的宽度是不一样的。
所以,紧密纺的加捻罗拉钳口处仍然有一个极小的所谓“加捻三角区”,当然其危害性已降低到最小。
正是由于上述成纱机理,用紧密纺工艺纺成的细纱具有以下特点:1.由于在加捻前,纱条中单纤维充分伸直,相互平行,而且排列紧密,所以在加捻罗拉钳口处(也叫阻捻罗拉,因为其有阻止捻度传递的作用),纱条直径变得很小,所以基本消除了“加捻三角区”,由于加捻前单纤维充分伸直、平行,没有毛羽伸出纱条主体,所以成纱毛羽很少,特别是3毫米以上毛羽极少。
2.在细纱中由于各单纤维是在伸直、平行的状态下加捻,在单纱受到拉力时,各单纤维受力基本一致,所以紧密纺强力比传统单纱高。
而且由于紧密纱中的单纤维排列紧密,相互间抱合力大,这也有助于提高纱线的强力。
3.在紧密纺工艺中,纱条是在完成了工艺规定的牵伸之后再进行聚集,所以其条干不匀的指标没有大的改善,但在其聚集区有对纱条的整理作用,且在加捻罗拉钳口处加捻时纤维的内、外层转移没有传统工艺强烈,所以紧密纱的条干不匀,粗、细节指标比传统纱要好。
4.由于紧密纱的上述特点,为下道工序提供了非常好的条件,紧密纱毛羽少,所以减轻了上浆、烧毛等工序的压力,在无梭织机的纬纱使用紧密纱时大大减少了引纬的阻力,提高了织机效率。
5.由于紧密纱纤维排列紧密,和相同号数的传统纱线相比直径小,所以用相同经、纬密织成的布透气性好,布面平整、光滑,是高档纺织品的理想用纱。
紧密纺和赛络纺知识

紧密纺和赛络纺知识近年来,关于紧密纺及赛络纺两种新型纺纱方法的报道很多,这两种新型纺纱工艺对于提高成纱质量的效果也是大家所公认的,本文将根据我公司4年多来的研究结果及用户的使用情况,对两种纺纱工艺的特点及成纱质量进行分析。
紧密纺纱工艺尽管在机械结构上有所不同,但有一点是相同的,即在完成工艺要求的牵伸之后,在加捻之前,把从前罗拉钳口输出的较宽的纱条进行聚集,使得纱条宽度变的很窄,单纤维之间排列更加紧密,并且尽量保持在这种状态下进入加捻区。
虽然有的报道说是此举消灭了“加捻三角区”,但实际上纱条在加捻前后的宽度是不一样的。
所以,紧密纺的加捻罗拉钳口处仍然有一个极小的所谓“加捻三角区”,当然其危害性已降低到最小。
正是由于上述成纱机理,用紧密纺工艺纺成的细纱具有以下特点: 1.由于在加捻前,纱条中单纤维充分伸直,相互平行,而且排列紧密,所以在加捻罗拉钳口处(也叫阻捻罗拉,因为其有阻止捻度传递的作用),纱条直径变得很小,所以基本消除了“加捻三角区”,由于加捻前单纤维充分伸直、平行,没有毛羽伸出纱条主体,所以成纱毛羽很少,特别是3毫米以上毛羽极少。
2.在细纱中由于各单纤维是在伸直、平行的状态下加捻,在单纱受到拉力时,各单纤维受力基本一致,所以紧密纺强力比传统单纱高。
而且由于紧密纱中的单纤维排列紧密,相互间抱合力大,这也有助于提高纱线的强力。
3.在紧密纺工艺中,纱条是在完成了工艺规定的牵伸之后再进行聚集,所以其条干不匀的指标没有大的改善,但在其聚集区有对纱条的整理作用,且在加捻罗拉钳口处加捻时纤维的内、外层转移没有传统工艺强烈,所以紧密纱的条干不匀,粗、细节指标比传统纱要好。
4.由于紧密纱的上述特点,为下道工序提供了非常好的条件,紧密纱毛羽少,所以减轻了上浆、烧毛等工序的压力,在无梭织机的纬纱使用紧密纱时大大减少了引纬的阻力,提高了织机效率。
5.由于紧密纱纤维排列紧密,和相同号数的传统纱线相比直径小,所以用相同经、纬密织成的布透气性好,布面平整、光滑,是高档纺织品的理想用纱。
- 1、下载文档前请自行甄别文档内容的完整性,平台不提供额外的编辑、内容补充、找答案等附加服务。
- 2、"仅部分预览"的文档,不可在线预览部分如存在完整性等问题,可反馈申请退款(可完整预览的文档不适用该条件!)。
- 3、如文档侵犯您的权益,请联系客服反馈,我们会尽快为您处理(人工客服工作时间:9:00-18:30)。
紧密纺和赛络纺知识
近年来,关于紧密纺及赛络纺两种新型纺纱方法的报道很多,这两种新型纺纱工艺对于提高成纱质量的效果也是大家所公认的,本文将根据我公司4年多来的研究结果及用户的使用情况,对两种纺纱工艺的特点及成纱质量进行分析。
紧密纺纱工艺尽管在机械结构上有所不同,但有一点是相同的,即在完成工艺要求的牵伸之后,在加捻之前,把从前罗拉钳口输出的较宽的纱条进行聚集,使得纱条宽度变的很窄,单纤维之间排列更加紧密,并且尽量保持在这种状态下进入加捻区。
虽然有的报道说是此举消灭了“加捻三角区”,但实际上纱条在加捻前后的宽度是不一样的。
所以,紧密纺的加捻罗拉钳口处仍然有一个极小的所谓“加捻三角区”,当然其危害性已降低到最小。
正是由于上述成纱机理,用紧密纺工艺纺成的细纱具有以下特点: 1.由于在加捻前,纱条中单纤维充分伸直,相互平行,而且排列紧密,所以在加捻罗拉钳口处(也叫阻捻罗拉,因为其有阻止捻度传递的作用),纱条直径变得很小,所以基本消除了“加捻三角区”,由于加捻前单纤维充分伸直、平行,没有毛羽伸出纱条主体,所以成纱毛羽很少,特别是3毫米以上毛羽极少。
2.在细纱中由于各单纤维是在伸直、平行的状态下加捻,在单纱受到拉力时,各单纤维受力基本一致,所以紧密纺强力比传统单纱高。
而且由于紧密纱中的单纤维排列紧密,相互间抱合力大,这也有助于提高纱线的强力。
3.在紧密纺工艺中,纱条是在完成了工艺规定的牵伸之后再进行聚集,所以其条干不匀的指标没有大的改善,但在其聚集区有对纱条的整理作用,且在加捻罗拉钳口处加捻时纤维的内、外层转移没有传统工艺强烈,所以紧密纱的条干不匀,粗、细节指标比传统纱要好。
4.由于紧密纱的上述特点,为下道工序提供了非常好的条件,紧密纱毛羽少,所以减轻了上浆、烧毛等工序的压力,在无梭织机的纬纱使用紧密纱时大大减少了引纬的阻力,提高了织机效率。
5.由于紧密纱纤维排列紧密,和相同号数的传统纱线相比直径小,所以用相同经、纬密织成的布透气性好,布面平整、光滑,是高档纺织品的理想用纱。
紧密纺工艺虽然有许多优点,但也有一些不足之处,如下所述:
1.紧密纺设备的造价较高,增加了纺纱厂的设备投资。
2.和每根纱线对应有一个吸气口,其吸气口处的负压锭间差异较大,如想提高其一致性,则需在每个吸管(或每个锭位)处加装能自动调节风量的控制阀。
这样做不但成本大,而且维护较困难。
3.除了毛羽指标有很大的改善之处,纱线的其它指标如条干、粗、细节等改善幅度不大。
4.紧密纱在经过络筒工序后,还会增加较多的毛羽。
赛络纺是在同一个锭位上以一定的间距喂入两根粗纱,两根粗纱分别被牵伸,纱条从前罗拉输出后,由于加捻的作用,两根纱条被捻合在一起,形成一根细纱。
实践证明,纱条在从前罗拉输出后到捻合之前,也形成较少的捻度,两根存在弱捻的纱条互为中心捻合在一起,形成风格独特的赛络纱。
赛络纺的特点如下所述:
1.因为赛络纺是两根粗纱同时被分别牵伸,根据并合理论,CX=CA/√n,公式中CX为并合后的不匀率,CA为并合前的不匀率,n为并合根数,此处n等于2。
所以CX=0.7×CA。
当然上述公式是理论数据,和实际情况有一定差别。
但也说明:用赛络纺工艺方法纺成的纱对改善条干,减少粗、细节有非常明显的效果,这是无数纺纱厂所孜孜以求的。
我公司几年来的试验和众多用户的大量生产实践也充分证明了这一点。
2.赛络纺的纱条从前罗拉输出后,在捻合时,两根弱捻纱条相互为中心卷成一根赛络纱。
在卷绕过程中,把伸出纱条主体的毛羽卷进纱线里面,并得到了良好的握持。
所以,赛络纱的毛羽比其它工艺方法都少,而且因为毛羽被两根纱条卷在细纱内,所以经过络筒工序时,也不会象其它纺纱方法大量增加毛羽,这一点时其它纺纱方法所无法比拟的。
3.赛络纺的纱条在前罗拉钳口处基本不加捻,所以不存在所谓的“加捻三角区”,大大减少了车间的飞花。
4.经过络筒工序后,赛络纱的毛羽比紧密纱更少,所以在上浆、织造、烧毛工序中,有着更加优越的性能。
5.赛络纱在加捻过程中,纤维内、外转移的程度小,成纱后纤维排列规律,其纱线强力优于单纱,比股纱强力低,另外,赛络纱的细节少,这也对增加纱线强力有帮助。
6.赛络纺纱设备比紧密纺机构简单,设备投资少,宜于维护。
在老机上进行改造容易实现。
7.赛络纱有类似股纱的性能,在许多情况下,可以代替股纱。
但赛络纺纱不需经过并捻机,工艺流程比常规工艺短,节省能源和劳动力。
综上所述,赛络纺工艺有着其它纺纱工艺所无法比拟的优点,但也有其不足之处,如下所述:
1.络纺工艺是双粗纱喂入,纺同号细纱时,如果粗纱定量不减少,细纱机的总牵伸倍数就要增加一倍。
现有细纱机的配置可能不适应,牵伸倍数过大,也要恶化细纱的条干水平。
如果降低粗纱定量,势必增加粗纱工序的负担。
为解决这个矛盾,我公司研制出细纱机三罗拉四皮圈超大牵伸机构,即在原有的三罗拉双皮圈牵伸机构的基础上,在后区增加上、下肖和上、下皮圈,使原来后区的简单罗拉牵伸区变成皮圈牵伸区,大大加强了对纤维的控制。
使原细纱机的总牵伸倍数增加50%~100%,此项技术已在2002年获国家专利。
使用三罗拉四皮圈牵伸机构与赛络纺工艺配套,大大减轻了因赛络纺的工艺特点对粗纱工序造成的压力。
2.在赛络纺工艺中,单根粗纱的牵伸状态是所纺细纱支数的两倍,即如果纺30支纱,那么单根粗纱就相当于在纺60支纱,这样在前罗拉钳口至捻合点段的纱条中,纤维数量是所纺细纱截面上纤维根数的一半,如果原料太差或工艺参数选择不当,在这一段断头可能会增多,甚至无法正常纺纱。
在捻合点以后,由于由于赛络纱的强力比传统工艺高,所以不会产生断头。
3.一般来说,为提高成纱质量,赛络纺工艺的粗纱定量通常比传统纺纱工艺小一些,这在一定程度上增加了粗纱工序的压力。