环锭纺和气流纺、赛络纺
棉纱知识

1、关于棉纱支数:纱的支数越高,纱就越细,织布越薄,布相对越柔软舒适。
但支数高的布要求原料(棉花)的品质高,而且对纱厂和纺织的织布厂也要求比较高,所以布的成本比较高。
2、活性印花斜纹棉40支:斜纹棉是织物的制造方式,在家纺特别是床上用品大多采用是两上一下或三上一下的斜纹制造工艺,这样面料表面较丰满,在印染过程中易开幅定型,也就是不易缩水.斜纹棉比平纹织物密度大,耗纱量大,耐磨度好,更结实,缩水率好控制。
活性印染是一种染色技术,这种方法印染的色比较细腻,颜色靓丽,不会掉色。
这种印染对机器、水质等硬件环境要求比较高,所以不是一般的小厂能做到的。
3、磨毛印花:是印花的一种,这种面料在后处理的过程中,进行磨毛处理,使面料的表面呈现一定的绒感,提高面料的手感。
磨毛,又叫磨绒。
用砂磨辊(或带)将织物表面磨出一层短而密的绒毛的工艺过程,称为磨绒,又称磨毛。
能使经纬纱同时产生绒毛,且绒毛短而密。
绒面平整,手感丰满、柔软,富于绒感,光泽柔和,无极光。
磨毛面料蓬松、厚实、保暖性能好,在寒夜入睡时,没有了其它棉布与人体刚接触时的冰冷。
同时具有不起球、不褪色等优点。
4、纱支数的计算:5、棉纱的分类(1)按粗细度习惯分:①粗支纱:17“特”(tex)及以下的棉纱均属粗支纱。
主要用于织造粗厚或起绒、起圈棉织物,如粗布、绒布、坚固呢等;②中支纱:18—27支棉纱属中支纱,用于织造平布、斜纹布、贡缎等一般性织物;③细支纱:28支及以上的棉纱,用于织造细布府绸、高档针、机织物。
(3)按照配棉等级分:①普梳纱:系没有经过精梳工序的纺纱工艺纺成的环锭纱,用于一般的针、机织物;②精梳纱:用优良品质的棉纤维作原料,纺制时比普梳纱增加一道精梳工序,纺成的纱质量优良,用于织造高档织物,如高级府绸、细布等;③废纺纱:指全部用纺纱过程中所处理下来的废棉作原料纺成的纱,用于织造低级棉毯、绒布和包皮布等;④新型纺纱:是用新型纺纱系统纺成的纱。
(4)按捻向分:①反手捻(又称Z捻)纱,在各种织物中应用最广;②顺手捻(又称S捻)纱,用于织造绒布的纬纱。
纱线纺制方法鉴别

环锭纺与气流纺的鉴别环锭纺世在细纱机上纺制而得到的,而纺纱的捻向都是Z捻,所以用S捻进行退捻,纤维能分离。
气流纺世通过气流回旋形成涡流,因此纱线表面的纤维相互纠缠,而内部的纤维有一定的捻度,但由于表面纤维相互纠缠,所以不管用Z捻还是S捻解捻,都不能使纤维分离。
因此通过以上方法就能把两者区分开来,且同样纱支的纱线,环锭纺的强力好于气流纺,毛羽、条干气流纺好于环锭纺。
喷气纺与涡流纺的鉴别喷气纱结构分纱芯和外包纤维两部分,纱芯平行且有捻度,结构较紧密,外包纤维松散且无规则缠绕在纱芯外面,故喷气纱结构较蓬松,外观较丰满。
而涡流纱结构也分纱芯和外包纤维,芯纤维呈平行排列、无捻度,外包纤维呈规则螺旋包缠在纱芯表面,且外层规则螺旋包缠纤维比例较高,占总纤维的60%左右,以致于内部未加捻的纤维几乎被完全覆盖,克服了喷气纱露芯问题,表面纤维排列则更接近于传统环锭纺,结构较紧密。
因此只要剥离外层纤维,看里层纤维是否加捻与外层包缠纤维是否有规则就能将两者区别出来。
且喷气纺主要是纺制化纤与棉的混纺、纯化纤纱及其混纺纱,全棉没有喷气纺。
精梳棉与紧密纺纱的鉴别紧密纺纱只要看整个布面的纱线很少有棉结,纱线的条干也很均匀,布面很光洁。
另外也可以看拆出来的纱线,如果是紧密纺,那么整根纱线毛羽很少,而且也很光洁,强力也比精梳棉要好。
整个布面摸起来比精梳棉要薄一些。
因此从以上三个方面我们就能把他们区别开来。
紧密纺纱与赛络紧密纺纱的鉴别紧密纺纱与赛络纺纱的相似之处是都是在传统环锭纺的加捻三角区增加了隔栅板与吸风凝聚装置,因此纱线的条干均匀,强力增加,丝线的毛羽少。
不同之处紧密纺是在细纱机上是单根喂入而赛络纺是在细纱机上喂入两个保持一定间距的粗纱,经牵伸后,由前罗拉输出这两根单纱须条,并由于捻度的传递而使单纱须条上带有少量的捻度,拼合后被进一步加捻成类似合股的纱线,卷绕在筒管上。
环锭纺双股线与赛络纺的鉴别环锭纺是在细纱机上纺制而得到的,而单纱纺纱的捻向都是Z捻,两根单纱并和采用S捻进行并捻。
环锭纺、气流纺、喷气纺、涡流纺、赛络纺、紧密纺简介

环锭纺、气流纺、喷气纺、涡流纺、赛络纺、紧密纺简介环锭纺、气流纺、喷气纺、涡流纺、赛络纺、紧密纺简介环锭纺环锭纺纱是现时市场上用量最多,最通用之纺纱方法,条子或粗纱经牵伸后的纤维条通过环锭钢丝圈旋转引入,筒管卷绕速度比钢丝圈快,棉纱被加捻制成细纱.广泛应用于各种短纤维的纺纱工程.如普梳,精梳及混纺,钢丝圈由筒管通过纱条带动绕钢领回转.进行加捻,同时,钢领的摩擦使其转速略小于筒管而得到卷绕.纺纱速度高,环锭纱的形态,为纤维大多呈内外转移的圆锥形螺旋线,使纤维在纱中内外缠绕联结,纱的结构紧密,强力高,适用于制线以及机织和针织等各种产品。
环锭纺(精梳)流程:清花间--梳棉--预并条--条并卷--精梳--头道并条--二道并条--粗纱--细纱--络筒环锭纺(普梳)流程:清花间--梳棉--头道并条--二道并条--粗纱--细纱--络筒气流纺气流纺不用锭子,主要靠分梳辊、纺杯、假捻装置等多个部件。
分梳辊用来抓取和分梳喂入的棉条纤维,同过他的高速回转所产生的离心力可把抓取的纤维甩出。
纺杯是个小小的金属杯子,他的旋转速度比分梳辊高出10倍以上,由此产生的离心作用,把杯子里的空气向外排;根据流体压强的原理,使棉纤维进入气流杯,并形成纤维流,沿着杯的内壁不断运动。
这时,杯子外有一根纱头,把杯子内壁的纤维引出来,并连接起来,再加上杯子带着纱尾高速旋转所产生的钻作用,就好像一边“喂”棉纤维,一边加纱线搓捏,使纱线与杯子内壁的纤维连接,在纱筒的旋绕拉力下进行牵伸,连续不断的输出纱线,完成气流纺纱的过程。
气流纺的特征气流纺纱有速度大、纱卷大、适应性广、机构简单和不用锭子、钢领、钢丝圈的优点,可成倍的提高细纱的产量。
气流纺与环锭纺的区别气流纺与环锭纺一个是新型纺织技术,一个是老式纺纱技术。
气流纺是气流纺纱,而环锭纺则是机械纺,就是由锭子和钢铃、钢丝圈进行加捻,由罗拉进行牵伸。
而气流纺则是由气流方式输送纤维,由一端握持加捻。
一般来说,环锭纱毛羽较少,强度较高,品质较好。
人棉纱的种类
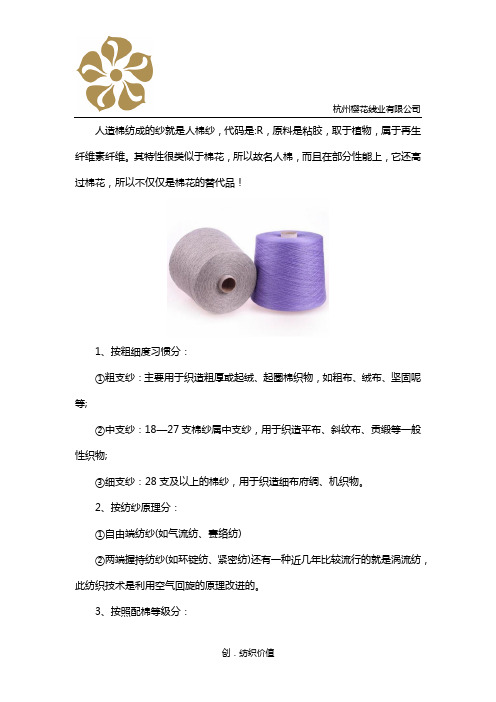
杭州樱花线业有限公司人造棉纺成的纱就是人棉纱,代码是:R,原料是粘胶,取于植物,属于再生纤维素纤维。
其特性很类似于棉花,所以故名人棉,而且在部分性能上,它还高过棉花,所以不仅仅是棉花的替代品!1、按粗细度习惯分:①粗支纱:主要用于织造粗厚或起绒、起圈棉织物,如粗布、绒布、坚固呢等;②中支纱:18—27支棉纱属中支纱,用于织造平布、斜纹布、贡缎等一般性织物;③细支纱:28支及以上的棉纱,用于织造细布府绸、机织物。
2、按纺纱原理分:①自由端纺纱(如气流纺、赛络纺)②两端握持纺纱(如环锭纺、紧密纺)还有一种近几年比较流行的就是涡流纺,此纺织技术是利用空气回旋的原理改进的。
3、按照配棉等级分:杭州樱花线业有限公司①普梳纱:是没有经过精梳工序的纺纱工艺纺成的环锭纱,用于一般的针、机织物;②精梳纱:用优良品质的棉纤维作原料,纺制时比普梳纱增加一道精梳工序,纺成的纱质量优良,用于织造有品质的织物,如有层次的府绸、细布等;③废纺纱:指全部用纺纱过程中所处理下来的废棉作原料纺成的纱,用于织造低级棉毯、绒布和包皮布等;④新型纺纱:是用新型纺纱系统纺成的纱。
4、按捻向分:①反手捻(又称Z捻)纱,在各种织物中应用较广;②顺手捻(又称S捻)纱,用于织造绒布的纬纱。
5、按纱线用途分:①经纱是在机织物中平行布边的方向的纱,有较大的强力,一般捻度较大;②纬纱是在机织物中垂直布边的方向的纱,强力要求较经纱低,捻度一般低杭州樱花线业有限公司于经纱,保持一定的柔软性;③针织用纱是要求洁净、均匀、捻度小,以防在编织弯曲时造成断头;④工业用纱如轮胎帘子线,传送带用纱,卫生医药用纱等。
人棉纱分类细分还可以分,但是常见的人棉纱分类就是如上列出了,除以上外,人棉纱还可以按照规则以及形态区分。
杭州樱花线业有限公司,创建于1992年,占地100多亩,是一家具有20多年制线历史的外商独资企业。
坐落于有中国人间天堂之称的杭州临安,拥有固定资产2.5亿元,在国内同行业中先批通过ISO9001质量管理体系和ISO14001环境管理体系认证,并取得Oeko-Tex standard 100瑞士信心生态纺织品认证。
赛络纺与环锭纺的区别
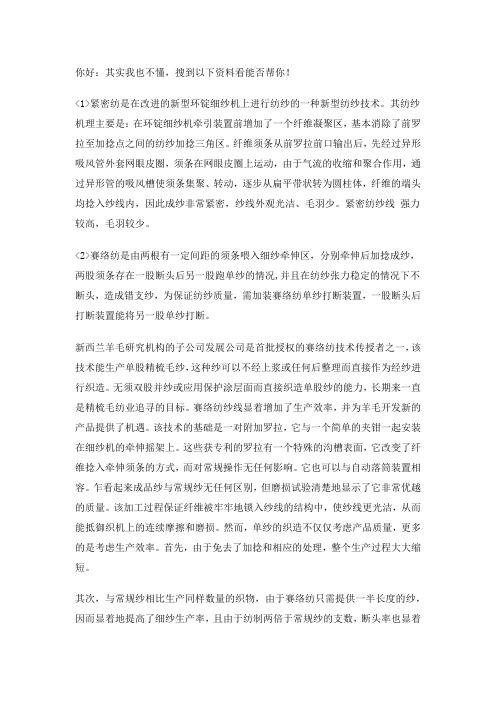
你好:其实我也不懂,搜到以下资料看能否帮你!<1>紧密纺是在改进的新型环锭细纱机上进行纺纱的一种新型纺纱技术。
其纺纱机理主要是:在环锭细纱机牵引装置前增加了一个纤维凝聚区,基本消除了前罗拉至加捻点之间的纺纱加捻三角区。
纤维须条从前罗拉前口输出后,先经过异形吸风管外套网眼皮圈,须条在网眼皮圈上运动,由于气流的收缩和聚合作用,通过异形管的吸风槽使须条集聚、转动,逐步从扁平带状转为圆柱体,纤维的端头均捻入纱线内,因此成纱非常紧密,纱线外观光洁、毛羽少。
紧密纺纱线强力较高,毛羽较少。
<2>赛络纺是由两根有一定间距的须条喂入细纱牵伸区,分别牵伸后加捻成纱,两股须条存在一股断头后另一股跑单纱的情况,并且在纺纱张力稳定的情况下不断头,造成错支纱,为保证纺纱质量,需加装赛络纺单纱打断装置,一股断头后打断装置能将另一股单纱打断。
新西兰羊毛研究机构的子公司发展公司是首批授权的赛络纺技术传授者之一,该技术能生产单股精梳毛纱,这种纱可以不经上浆或任何后整理而直接作为经纱进行织造。
无须双股并纱或应用保护涂层面而直接织造单股纱的能力,长期来一直是精梳毛纺业追寻的目标。
赛络纺纱线显着增加了生产效率,并为羊毛开发新的产品提供了机遇。
该技术的基础是一对附加罗拉,它与一个简单的夹钳一起安装在细纱机的牵伸摇架上。
这些获专利的罗拉有一个特殊的沟槽表面,它改变了纤维捻入牵伸须条的方式,而对常规操作无任何影响。
它也可以与自动落筒装置相容。
乍看起来成品纱与常规纱无任何区别,但磨损试验清楚地显示了它非常优越的质量。
该加工过程保证纤维被牢牢地锁入纱线的结构中,使纱线更光洁,从而能抵御织机上的连续摩擦和磨损。
然而,单纱的织造不仅仅考虑产品质量,更多的是考虑生产效率。
首先,由于免去了加捻和相应的处理,整个生产过程大大缩短。
其次,与常规纱相比生产同样数量的织物,由于赛络纺只需提供一半长度的纱,因而显着地提高了细纱生产率,且由于纺制两倍于常规纱的支数,断头率也显着下降。
喷气涡流纺与环锭纺转杯纺三种纺纱方法综合对比分析

差(%) CVb% +0.5 +1.6 +1.7 2.01 1.46 1.38
环锭纺 转杯纺 喷气涡 流纺
从以上对比数据中可以看出: 条干CV%和细节-50%:环锭纺最好,其次喷气涡流纺,转杯 纺最差。 粗节+50%:环锭纺最好,其次喷气涡流纺,转杯纺最差。 棉结+200%:喷气涡流纺最好,其次环锭纺,转杯纺最差。 单纱断裂强度:环锭纺最高,其次涡流纺,转杯纺最低。 条干CVb%:喷气涡流纺最好,其次转杯纺,环锭纺最差。
涡流
切向 开口 进风孔
涡流管
负压装置
2 原料使用
三种纺纱方法由于成纱结构不一样,相同规格 的原料所纺出的纱在强力、条干方面差异较大 针对不同的纺纱方法和纺纱支数,需要选择不同 规格的原料来弥补各自成纱中的不足
环锭纺选用 原料规格为 1.67dtex×3 8mm 100%, 成纱纤维根 数为118根 转杯纺配置 ¢33mm纺杯, 所选原料 1.33dtex×32m m 100%,成纱 纤维根数为148 根 喷气涡流纺 选用原料为 1.33dtex×3 8mm 100%, 成纱纤维根 数为148根
生产效率(%) 97.4 96.0 95.2 94.4 93.1 91.7 90.0 87.8 85.9 每台每小时断头率(根) 204.1 280.2 320.4 370.7 416.1 440.4 455.4 469.8 513.1 折千锭时断头率(根) 2551 3503 4005 4634 5201 5505 5693 5873 6414
3 工艺流程
3 喷气涡流 纺
FA002抓棉机→SFA035混开棉机→FA106A梳针开棉机→FA161振 动棉箱给棉机→A076F成卷机→FA204C梳棉机→FA306A并条机 (二道)→RSB D401自调匀整并条机→种纺纱方法生产的19.7tex粘胶纱成纱质量指标对比 原料 纺纱方 法 ( 条干 细节50% 3 13 6 dtex·mm) CV% 规格 1.67×38 1.33×32 1.33d×38 12.67 13.80 13.39 粗节 +50 % 17 38 29 棉节 +200 % 28 59 23 单纱强 力CV% 9.3 8.9 10.0 单纱断裂 强度 (cN/tex) 15.1 11.5 12.8 百米重 量 CV% 1.8 1.1 0.9 重量偏 条干
环锭纺、气流纺、喷气纺、涡流纺、赛络纺、紧密纺简介

环锭纺、气流纺、喷气纺、涡流纺、赛络纺、紧密纺简介环锭纺环锭纺纱是现时市场上用量最多,最通用之纺纱方法,条子或粗纱经牵伸后的纤维条通过环锭钢丝圈旋转引入,筒管卷绕速度比钢丝圈快,棉纱被加捻制成细纱.广泛应用于各种短纤维的纺纱工程.如普梳,精梳及混纺,钢丝圈由筒管通过纱条带动绕钢领回转.进行加捻,同时,钢领的摩擦使其转速略小于筒管而得到卷绕.纺纱速度高,环锭纱的形态,为纤维大多呈内外转移的圆锥形螺旋线,使纤维在纱中内外缠绕联结,纱的结构紧密,强力高,适用于制线以及机织和针织等各种产品。
环锭纺(精梳)流程:清花间--梳棉--预并条--条并卷--精梳--头道并条--二道并条--粗纱--细纱--络筒环锭纺(普梳)流程:清花间--梳棉--头道并条--二道并条--粗纱--细纱--络筒气流纺气流纺不用锭子,主要靠分梳辊、纺杯、假捻装置等多个部件。
分梳辊用来抓取和分梳喂入的棉条纤维,同过他的高速回转所产生的离心力可把抓取的纤维甩出。
纺杯是个小小的金属杯子,他的旋转速度比分梳辊高出10倍以上,由此产生的离心作用,把杯子里的空气向外排;根据流体压强的原理,使棉纤维进入气流杯,并形成纤维流,沿着杯的内壁不断运动。
这时,杯子外有一根纱头,把杯子内壁的纤维引出来,并连接起来,再加上杯子带着纱尾高速旋转所产生的钻作用,就好像一边“喂”棉纤维,一边加纱线搓捏,使纱线与杯子内壁的纤维连接,在纱筒的旋绕拉力下进行牵伸,连续不断的输出纱线,完成气流纺纱的过程。
气流纺的特征气流纺纱有速度大、纱卷大、适应性广、机构简单和不用锭子、钢领、钢丝圈的优点,可成倍的提高细纱的产量。
气流纺与环锭纺的区别气流纺与环锭纺一个是新型纺织技术,一个是老式纺纱技术。
气流纺是气流纺纱,而环锭纺则是机械纺,就是由锭子和钢铃、钢丝圈进行加捻,由罗拉进行牵伸。
而气流纺则是由气流方式输送纤维,由一端握持加捻。
一般来说,环锭纱毛羽较少,强度较高,品质较好。
气流纺工序短,原料短绒较多,纱线毛,支数和拈度不能很高,价格也较低。
纱线基础知识-图文详解版
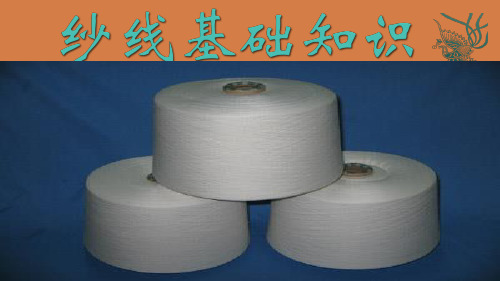
公制支数(Nm)和英制支数(Ne)
公制支数(Nm)
是指在公定回潮率时,一克重的纱线 (或纤维)所具有的长度米数。
公制支数可表示成“20公支、40公支”的 形式,意谓着一克重的纱线具有20m长或 40m长。
b. 英制支数(Ne)
指1磅(454克)重的棉纱线有几个840 码(1码=0.9144米)长。
气流纱: (OPEN END)
也称转杯纺纱,是利用气流将纤维在高速 回转的纺纱杯内凝聚加捻输出成纱。
气流纱特点:
纱线结构比环锭纱蓬松、耐磨、条干均匀、 染色较鲜艳,但强力较低。
主要用于机织物中膨松厚实的平布、手感 良好的绒布。
1.机织用纱: (Weaving)
机织用纱指加工机织物所用纱线,分经纱和 纬纱两种。 经纱:
按照纺纱系统分:
精梳纱 普梳纱 废纺纱
精纺纱 (JC/CJ) (CM combed)
也称精梳纱,是指通过精梳工序纺成 的纱,包括精梳棉纱和精梳毛纱。
精梳纱特点
纤维平行伸直度高,条干均匀、,但 成本较高,纱支较高。
主要用于高级织物及针织品的原料, 如细纺、华达呢、花呢、羊毛衫等。
2.粗纺纱(C) ( CD CARDED) 不经过精梳工序纺成的纱。
捻度 、强力、 纱支 、条干 、细节、 粗节、 棉结 属于乌斯特指标,用乌斯特仪器测出来
捻度: (TWIST)
是指纱线单位长度上的捻回数。
国内: 其计量单位为“捻/10cm” 或“捻 /m”
国外: 用英寸捻度表示:TPI= 捻/INCH 捻 度/英寸
捻度/10cm
捻/10cm
捻度对纱线的影响:
所有的化纤和纤维素纤维都不走精梳工序 普梳纱特点及用途
给我一分钟的时间,告诉你如何区分环锭纺、气流纺、涡流纺和赛络纺

给我⼀分钟的时间,告诉你如何区分环锭纺、⽓流纺、涡流纺和赛络纺今天⼩编教⼤家通过退捻的⽅法
来区分环锭纺、⽓流纺、涡流纺和赛络纺
在这之前,我们要先说⼀下退捻的⽅法,
请看下⾯的视频
⼀、退捻教学视频
(视频有9秒,建议在WIFI下观看,⽆声,⼟豪随意)
学会了退捻之后,我们就可以通过退捻的⽅法来区分四种纱线了
⼆、四种纱线的区分
1.环锭纺纱线
环锭纺整根纱线都能够完全退捻,退完捻后纱线没有强⼒
2.赛络纺纱线
赛络纺整根纱线都能够完全退捻,退完捻后纱线没有强⼒
在这四种纱线中,赛络纺唯⼀⼀个看起来是两根的纱线合成的⼀根单纱
赛络纺就是⾼档环锭纺(是由两根粗纱⼀起并⾏输⼊纺成⼀根细纱)
条⼲好,⽑⽻少,强度⽐环锭纺⼤
3.⽓流纺纱线(转杯纺)
⽓流纺⽆法像环锭纺⼀样整根纱线完全退捻,只能少的局部能完全退捻,所以退捻后被退捻的
节点也没有强⼒,整根纱⼀拉就断
4.涡流纺纱线
涡流纺退捻后外表看起来完全退捻,但纱芯没有退捻,还是有很⼤的强度,
三、纱线的区分流程
第1步:拿到⼀根纱线退捻
没有整根纱线完全退捻,只有部分节点完全退捻,⽓流纺
第2步:看起来完全退捻
第3步:看是否有强⼒
(有→涡流纺,没有→环锭纺)
第4步:观察是否有两根
(有→赛络纺,没有→普通环锭纺)
四、成纱⽐较
(同等原料同样⽀数相⽐)
环锭纺适纺范围最⼴,通常可纺300英⽀以下的纱线,转杯纺⽬前通常适纺40英⽀以下的纱线,涡流纺⽬前适纺60英⽀以下的纱线
END。
气流纺与环锭纺的差别

气流纺与环锭纺的差别气流纺与环锭纺的差别主要体现在以下5个方面:1、气流纺与环锭纺的成纱机理不同。
环锭纺属于握持纺纱,是将牵伸、加捻和卷绕同时进行的一种纺纱方法,粗纱在牵伸系统中被牵伸至所要求纱支的须条,再经钢领、钢丝圈的加捻和卷绕形成一根纱线。
须条在整个成纱过程中没有断开点。
气流纺属于自由端纺纱。
棉条经分梳辊分梳成了单纤维状,纤维在分梳辊的离心力和纺杯内负压气流的作用下,脱离分梳辊表面经输棉管道而进入纺杯,并在凝聚槽中形成纤维环,纤维环随着纺杯高速旋转,在接头纱的作用下,随着捻度不断的传递和连续剥离纤维束而成纱。
须条在成纱过程中是有断开点的。
2、气流纺与环锭纺的加捻方式不同。
环锭纺加捻是两端被握持加捻;气流纺加捻是一段被握持。
3、气流纺与环锭纺的工艺流程不同。
环锭纺形成熟条后,还需要进一步形成粗纱,气流纺直接用熟条就可以生产。
环锭纺成纱后一般还需要进一步经络筒络成筒纱,气流纺直接就可以形成筒纱。
4、气流纺与环锭纺纱线的结构不同。
环锭纺由于牵伸和加捻都是在两端被握持的状态下完成的,因此,纱线中纤维比较顺直,而且由于在加捻时处于三角区外侧的纤维受到的张力最大,而在中心的纤维受到的张力最小,故成纱时这些纤维的初始张力不等,使外层纤维紧紧地包缠住内层纤维,纱线比较紧密。
而气流纺纱由于纤维分离、加捻都是在自由状态下完成,而且在完成纱线抽出和加捻的过程中,不断有纤维沿凝聚槽壁滑向剥取点,因此形成较多的包覆层纤维,纤维取向度较差,纱线蓬松。
气流纺与环锭纺纱线的外观不同。
环锭纱的表面单纤维基本都顺向捻度方向,比较整齐,很少有反捻向纤维缠结,气流纱的表面单纤维有较多的反捻向纤维缠结,故环锭纱很容易退捻,气流纱不容易退捻。
5、气流纺与环锭纺纱线对原料的要求不同。
由于气流纺与环锭纺纱线的成纱机理不同,环锭纺一般相对成纱支数较高,气流纺成纱支数相对较低。
气流纺可以使用长度较短的原料,环锭纺一般要求原料长度要长一些。
来自中国棉纱交易网。
环锭纺纱新技术

1 A
2 赛络纺
和传统的纺纱不同的是 ,赛络纺是双粗纱平
行 喂 入 ,两 股 须 条 在 细 纱 机 上牵 伸 区 内互 不 干
涉,一直到出前箝 口后才汇合一起 。见罔二() 1。
在 汇 合 之 前 两 股 须 条 分 别 在加 捻 力 的 作 用 下 捻 。 当两 股带有 一 定捻 度 的纤 维 束 汇合 后将在 纺
包 芯纱 6 。
说说 我 的看 法 。
、
环 锭 纺 纱 新 技 术
1包 芯纱
在环 锭 细 纱 机 上生 产 包 : ,大都 是 囚弹 芷纱 .
性纱 而起 的。让 纱线 有 弹性 的力‘ 有好 多 。但不 法
很 明显采用 这样 的装 置虽 然可 以达到 包芯 的 效 果 ,但 要 有 良好 的包 芯 效 果 还 需 1艺 的 配
调 整 长 丝 和 纤 维 须 条 的位 置 和 张 力 .可 以
产 生 不 同 的包缠 方 法 ,或长 丝 和 纤 维相 互包 缠 ,
打破 ,在纺 纱 张 力的作 用下 B O须 条纱 线将 向右 偏移 到 B E位 置 _ ,在移 动过程 中 ,具 有一 定 张 _ I
或长 丝包缠纤 维 ,或 者纤 维包 缠长 丝 。在纺 制纤
间有 一个 _角 区( 『 ) 随着纺 纱 的进 行 ,长 二 见冬 1 。
囤 二 | 群络 纺 1 ) 1粗纱须条 2 前集合器
丝呈螺旋 状地包 复在羊 毛纤 维的外 1 。长丝乖 j 6 = 『 ¨毛
3 前罗拉
4 纱 线
纤 维 都 有… 定 的 捻 度 。 m于 纱 线 中有 长丝 的存 一 在 ,纱线 的强力和仲 长明显增加 ,还有 闪色效. 。
新型纺纱

新型纺纱当前棉纺领域中有五种实用的、倍受关注的纺纱方法,即环锭纺、转杯纺、喷气纺(包括喷气涡流纺),摩擦纺和紧密纺。
环锭纺纱方法已有100多年的历史,故又称传统纺纱,而后4种纺纱方法都是在近几十年甚至是近几年发展起来的,故统称为新型纺纱方法。
(1) 紧密纺是纺纱的新概念,新技术,主要在细纱机上作改良,牵伸系统与传统细纱机不同,在输出罗拉后多加一套令纤维会集的装置,使有效地让经过了两次牵伸的粗纱棉条,在进入加捻区前会聚,利用一股气流把条子从罗拉牵伸系统的夹持点拉出,集合在一个多孔的表面上,因吸力作用下条子被压缩,缩小钳口处粗纱宽度,大幅降低纺纱三角的高度,棉纱加捻效果增加,棉纤维抱合更加有序,更加紧密,令棉纱毛羽数量大幅下降。
(2)赛络纺又命并捻纺,中国大陆称为A,B纱,近期正式命为赛络纺。
是在细纱机上喂入两根保持一定间距的粗纱,经牵伸后,由前罗拉输出这两根单纱须条,并由于捻度的传递而使单纱须条上带有少量的捻度,拼合后被进一步加捻成类似合股的纱线,卷绕在筒管上。
赛络纺的初始设计目的是用于毛纺上,该纱存在:毛羽少,强力高,耐磨性好。
达到毛纱能单纱织造的效果,以实现毛织物的轻薄化,但尽管赛络纺在许多方面比较同类常规纱有了较大的改善,要真正达到毛纺单纱不上浆织造,尚有一定距离,其后毛纺亦多放弃此方法,反而在混纺如T/C,C.V.C等则采用此方法,因其染色后可产生并纱之麻花效果,手感好,故受欢迎,近期更因改善毛羽问题,如纺一些易产生毛羽之纤维,如人造棉,莫代尔,天丝,大豆纤维,甚至全棉都用此方法生产,赛络纱所用的原料等级可比常规环绽纺低,而其织物较常规环锭股线织物毛羽少,手感柔软,耐磨,透气性能好。
(可参考本人:SIRO YARN 工艺及注意事项一文)。
(3)赛络菲纺,与赛络纺类似,亦是在赛络纺基础上变化,不同之处是将一根粗纱改为一根细旦长丝,与另一根粗纱(毛,棉或麻,绢丝等)在环锭细纱机上加装一个长丝喂入装置,使长丝与正常牵伸的须条,保持一定距离平等喂入,并在前罗拉钳口下游汇合,交捻成纱。
技术环锭纺包芯纱和赛络纺包芯纱的对比

技术环锭纺包芯纱和赛络纺包芯纱的对比包芯纱又称复合纱或包覆纱,它是由两种或两种以上的纤维组合而成的一种新型纱线。
最初的包芯纱是以棉纤维为皮、涤纶短纤纱为芯开发的短纤维与短纤维包芯纱。
对于高强耐用、免烫、尺寸稳定又抗起球、吸湿透气、美观舒适的纺织品,如缝纫线和军服等,包芯纱比一般的纯纺纱和混纺纱优越,更能满足要求。
但传统的环锭纺包芯纱包覆效果欠佳,有时其结构就象把长丝和外包纤维须条并捻在一起的股线,没有适宜后序机械加工的抗剥离强度,因而降低了包芯纱的附加值,限制了包芯纱的潜在用途。
赛络纺包芯纱是一种具有股线性质的单纱,其强力、伸长、均匀度优于环锭纺包芯纱,且手感柔软、包覆效果好。
为了能经济地生产出质量优良、符合客户要求的包芯纱,结合本厂的生产实际,比较了传统和赛络纺锦纶长丝包芯纱的生产设备和成纱性能,分析了二者的差异,指出了应采取的合理纺纱工艺等。
1设备改造1.1 环锭纺包芯纱的设备改装传统环锭纺包芯纱可在普通改装过的细纱机上生产。
首先在一般的细纱机上加装芯丝喂入机构和预牵伸机构。
筒子长丝在导丝罗拉的牵引下退绕,不经过细纱机的牵伸机构,而是经过加装的预牵伸机构和V形槽导轮,自前罗拉皮辊后的集合器喂入,与牵伸后的须条合并,再通过前罗拉和导纱钩,由环锭回转加捻为长丝包芯纱。
接着改装粗纱架。
由于所用的锦纶长丝外形尺寸大于200mm×500mm,一台粗纱架由六列单层吊锭,改为四列单层吊锭,锭距由原来的210mm改为130mm。
芯丝喂入装置位于粗纱架上方,因而粗纱架下降30mm,以便腾出空间加装长丝立柱、托架和插丝锭子。
考虑到可操作性,只在立柱上加装二排长丝托架和锭子,利用粗纱前的空间,加装一排长丝托架和锭子。
这样,可以合理分布粗纱和长丝,长丝由导丝杆引出,喂入牵伸区前钳口,粗纱则经由导纱杆和分纱棒引出,喂入牵伸后区。
将横动杆固定,确保从喇叭口喂入经牵伸区输出的粗纱须条不产生移动。
在摇架位置加装导丝轮,有效控制长丝在前罗拉输出时始终位于粗纱须条中央,减少露芯等包芯纱缺陷,提高包覆效果。
纺纱方法比较及预氧丝纯纺和混纺
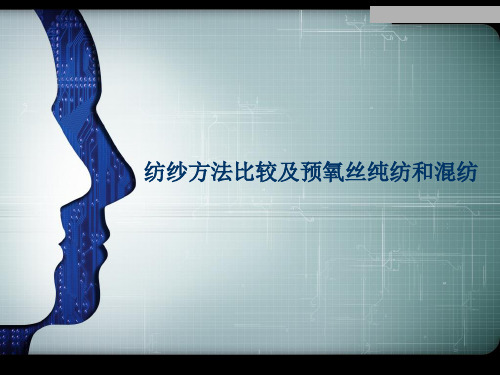
纺纱方法比较及预氧丝纯纺和混纺
大连工业大学
目录
1 2
环锭纺之赛络纺和赛罗菲尔纺
转杯纺
3 4
各种纺纱方式的区别和联系
PANOF纯纺和混纺 纯纺和混纺
5 结论
大连工业大学
1 环锭纺之赛络纺和赛罗菲尔纺
一 赛络纺原理 Siro纺是在细纱机上喂入两根 保持一定间距的粗纱,经牵伸 后,由前罗拉输出这两根单纱 须条,并由于捻度的传递而使 单纱须条上带有少量的捻度, 这两根须条回合后被进一步加 捻成类似股线的赛罗纱并被卷 绕在筒管上。
Hale Waihona Puke 大连工业大学2 转杯纺
纺纱杯是转杯纺最重要的部件,其 基本形状是由两个中空的截头圆锥 体联接而成,在两个圆锥体的交界 处(最大直径处)形成一个凝聚纤维 的凹槽,称为凝聚槽。
大连工业大学
2 转杯纺
转杯纺适纺纱线密度 —般为 般为388.7—13tex。 般为 。 例如, 例如,Autocoro-240 型适纺纱线密度为 125—12.5tex, , FA601型适纺纱线密度 型适纺纱线密度 为100—14.7tex。 。 国内实际常纺纱线密度 为97.2-36.4tex。 。 当纱线密度小于16tex 当纱线密度小于 时纺纱就比较困难。 时纺纱就比较困难。 其它纱种 在转杯纺机上 开发各种麻棉混纺纱、 开发各种麻棉混纺纱、 纳丝纯(混 纺纱 纺纱、 纳丝纯 混)纺纱、毛型纯 (混)纺纱、化纤纯 混)纺 混 纺纱 化纤纯(混 纺 纺纱、 纱 (涤、腈、粘等),往往有 涤 粘等 , 可能比环锭纺具有更好的 可纺性和更高的经济效益 。 转杯纱适合开发各类 牛仔布、绒类织物、装饰 牛仔布、绒类织物、 用布及工业用布等。 用布及工业用布等。
大连工业大学
常见纱线的结构形态与鉴别

常见纱线的结构形态与鉴别纺纱是人类非常古老的生产活动,大约在公元前9000年,人们就开始用双手搓捻的方式,搓出了最原始的羊毛纱。
西方工业革命后,纺纱由手工生产转变为工业化生产,尤其是环锭细纱机的发明,极大地提高了生产效率,加快了纺织工业化的步伐。
目前,纺纱技术主要有传统环锭纺、紧密纺、赛络纺、转杯纺、喷气纺和涡流纺等,除了传统环锭纺之外,其它几种纺纱技术都是在近几十年甚至是近几年发展起来的,统称为新型纺纱技术。
不同纺纱方式的成纱机理不同,纤维在纱线中的排列形态以及纱线的紧密度以不同,如图所示。
(1) 传统环锭纺环锭纱中纤维基本上呈螺旋线排列,由于存在纺纱加捻三角区,纤维不能全部被加捻到纱体中去,较多边缘纤维一端被捻入纱体,另一端露在纱条外面形成毛羽,因而虽然环锭纱结构较为紧密,但纱条表面相对来说显得杂乱无序,光洁度较差。
(2) 紧密纺紧密纺亦称集聚纺,是在环锭纺纱机牵伸机构之后的加捻三角区位置加装了纤维集聚装置,减小加捻三角区,从而改善纱线机构的一种纺纱方法。
纱线外观光洁、加捻螺旋结构清晰可见,纤维排列整齐清晰、毛羽少,纤维几乎没有内外转移,从一定意义上讲,可能是纱线中理想化的纤维排列方式。
(3) 赛络纺赛络纺是在传统环锭细纱机上纺出类似于股线结构的纱线的一种纺纱方法。
两根粗纱以一定的间距平行喂入环锭纺纱机的同一牵伸机构,以平行状态同时被牵伸,从前罗拉夹持点输出的这两根单纱须条,由于捻度的传递而使单纱须条上带有少量的捻度,拼合后被进一步加捻成类似合股的纱线,然后经过导纱钩、钢丝圈卷取到纱管上,成为赛络纺纱线。
(4) 转杯纺转杯纱,亦称气流纺,属于自由端纺纱方法。
在加捻过程中,加捻区的纤维缺乏积极握持,呈松散状态,因而纤维伸直度差,纤维内外转移程度低。
纱的结构分纱芯和外包纤维两部分。
纱芯结构与环锭纱相似,比较紧密;外包纤维结构松散,无规则地缠绕在纱芯外面。
因此与传统环锭纱相比,转杯纱结构比较蓬松,外观较丰满。
13种纺纱方法的介绍

13种纺纱方法简介气流纺纱, 杯, 金币本帖最后由 kpjiesen 于 2011-11-12 14:18 编辑(1)环锭纺纱(RING SPINNING) (2)无捻纺纱(TWISTLESS YARN PROCESSING) (3)自捻纺纱(SELF-TWIST SPINNING) (4)离心纺纱(CENTR FUGAL SPINNING) (5(帽锭纺纱(CAP SPINNING) (6)走绽纺纱(MULE SPINNING) (7)自由端纺纱(OPEN-END SPINNING) (8)气流纺纱(转杯纺纱)(ROTOR SPINNING) (9)静电纺纱(ELECTRO STATIC SPINNING) (10)涡流纺纱VORTEX SPINNING (11)喷气纺纱 JET SPINNING. (12)摩擦纺纱FRICTION SPINNING (13)尘笼纺纱(德雷夫纺纱)DREF SPINNING (1) 环锭纺纱(ring spinning),是现时市场上用量最多,最通用之纺纱方法,条子或粗纱经牵伸后的纤维条通过环锭钢丝圈旋转引入,筒管卷绕速度比钢丝圈快,棉纱被加拈制成细纱.广泛应用于各种短纤维的纺纱工程.如普梳,精梳及混纺,钢丝圈由筒管通过纱条带动绕钢领回转.进行加拈同时,钢领的摩擦使其转速略小于筒管而得到卷绕.纺纱速度高,环锭纱的形态,为纤维大多呈内外转移的圆锥形螺旋线,使纤维在纱中内外缠绕联结,纱的结构紧密,强力高,适用于制线以及机织和针织等各种产品. 环锭纺(精梳)流程:清花间--梳棉--预并条--条并卷--精梳--头道并条--二道并条--粗纱--细纱--络筒环锭纺(普梳)流程:清花间--梳棉--头道并条--二道并条--粗纱--细纱--络筒 (2)无拈纺纱(twistless processing) 使用粘合剂使纤维条中的纤维互相粘合成纱的一种纺纱方法.粗纱经牵伸装置牵伸后,须条被送到加捻滚筒上,回滚筒上来自槽箱中的薄层粘合剂接触.纤维条由数根回转的小压辊与滚筒一起向前输送,其中一根小压辊还同时作轴向往复运动,将纤维条搓成圆形截面,并使每根纤维都能均匀地接触到粘合剂.圆形纤维条通过加热器烘燥,纤维互相粘牢成纱.纺纱速度可比常规纺纱方法大2~4倍,制成的纱可供织造用. (3)自拈纺纱(self-twist spinning) 一种非传统纺纱方法.(siro yarn类同)将两根纤维条经牵伸装置拉细,由前罗拉、搓捻辊输出,在导纱钩处合.搓捻辊除回转外,并快速轴向往复运动,搓转纱条,使搓捻辊前后的纱条获得方向相反的捻回.在导纱钩处 合后的两根纱条,依靠它们本身的抗扭力矩自行拈合成双股自拈纱(ST 纱),卷绕成筒子.自拈纱的形态特点是相邻纱段交替地呈正反方向的捻回,交替处为无捻回.在捻线机上加一个方向的捻度,制成加捻自捻线(STT纱).两组自捻纱以无捻区相位差90°配置并合而成的四股纱,简称“2ST纱”,再在捻线机上低捻并制成(2ST)T纱.两次自并称为“(ST)2”纱.用一根长丝代替自捻中一根单纱条时,可以相应地制成STM和 (STM)T纱.此纺法专用于多股纱线上,如毛纺或仿毛化纤产品.高质量的自捻纱可直接用于纬编针织,但机织用经纱,须使用加捻自捻线,改善强力性能. (4)离心纺纱(centrifugal spinning) 以高速离心罐(杯)和升降导纱管实施加捻卷绕的连续纺纱方法.粗纱经牵伸装置后由前罗拉连续输出纤维条,经导纱钩、导纱管进入高速回转的圆柱形离心罐中,纱条在离心力作用下紧贴于罐内壁而与罐子同转,使导纱管下端与前罗拉间的纱条受到加捻作用,并用导纱管下水平方向纱条转动速度落后于离心罐而产生卷绕.导纱管按一定规律升降,形成交叉卷绕的纱饼,卷绕达到一定长度要求时,前罗拉停止输出纤维条,导纱管上升退出离心罐,将空筒管急速下降到离心罐内,纱头钩住筒管下部的钩纱器,使纱饼上的纱退绕到筒管上,退绕完毕,取下满管.同环锭纺纱比较,功率消耗大,回丝多,断头难处理,纱重绕到纱管上,前罗拉需停转,影响生产率.现时很少人使用。
气流纺生产工艺

气流纺生产工艺气流纺是一种较新的纺纱工艺,相比传统的锭子纺、环锭纺等工艺,具有生产效率高、成本低、纤维质量好等优点。
下面将从纺纱原理、设备构成和生产工艺流程三个方面介绍气流纺的生产工艺。
一、纺纱原理气流纺利用高速的气流使纤维悬浮在空气中,并将悬浮的纤维拉伸、扭转成纱线。
在气流纺纺纱过程中,纤维经过剑刺或钳口的牵引而进入气流,纺纱时纤维沿气流的方向进行拉伸、扭转,最终形成纱线。
其纺纱原理是利用气流的动能、摩擦力和表面张力等作用于纤维上,使纤维产生捻度、撑直、扩散,从而形成纱线。
二、设备构成气流纺纺纱机主要由纤维缸、气流缸、引纱器、驱动装置等组成。
其中,纤维缸是纺纱机的核心部分,负责将纤维进给到气流缸中,经过加热并添加接枝剂等预处理;气流缸则是气流纺纺纱机中最关键的部分,通过喷射气流、卷辊速度的控制等手段,将纤维牵引、伸长、扭转,形成纱线;引纱器是将纱线引入传感器或层架的装置;驱动装置则是驱动气流缸和引纱器等组件工作的动力来源。
三、生产工艺流程气流纺生产工艺的主要流程包括:预处理、纤维进给、纺纱和整理。
预处理阶段主要是对纤维进行处理,包括清洗、张力调整、加湿、加热等工序。
其中,清洗是将原料纤维中的杂质去除,以保证纤维的纯净度;张力调整则是通过调整预处理设备的张力,降低纤维的弹性和扭曲度,以便于后续的纺纱工序进行;加湿和加热则是为了提高纤维的柔软性和伸长性,使其更易于纺制成纱线。
纤维进给阶段是将经过预处理的纤维送入纺纱机内部。
通常情况下,纤维以卷轴的形式放在纤维缸中,通过张力辊、优化纤维台等装置将纤维送入气流缸中。
纤维进入气流缸后,由高速的气流将纤维牵引、伸长、扭转,形成纱线。
纺纱阶段是气流纺的核心工序,也是整个生产工艺中最关键的环节。
在纺纱过程中,纤维不断接受气流的力量,得到拉伸、扭转和沉重力的作用,最终形成纱线。
纺纱速度、接送张力、压力等参数的控制对于纱线质量、纺纱效率等都有重要影响。
整理阶段是对纱线进行整形,主要包括卷绕、拉伸、整理等工序。
环锭纺赛络纺和紧密纺的区别

环锭纺赛络纺和紧密纺的区别1.因为赛络纺是两根粗纱同时被分别牵伸,根据并合理论,CX=CA/√n,公式中CX为并合后的不匀率,CA为并合前的不匀率,n为并合根数,此处n等于2。
所以CX=0.7×CA。
当然上述公式是理论数据,和实际情况有一定差别。
但也说明:用赛络纺工艺方法纺成的纱对改善条干,减少粗、细节有非常明显的效果,这是无数纺纱厂所孜孜以求的。
我公司几年来的试验和众多用户的大量生产实践也充分证明了这一点。
2.赛络纺的纱条从前罗拉输出后,在捻合时,两根弱捻纱条相互为中心卷成一根赛络纱。
在卷绕过程中,把伸出纱条主体的毛羽卷进纱线里面,并得到了良好的握持。
所以,赛络纱的毛羽比其它工艺方法都少,而且因为毛羽被两根纱条卷在细纱内,所以经过络筒工序时,也不会象其它纺纱方法大量增加毛羽,这一点时其它纺纱方法所无法比拟的。
3.赛络纺的纱条在前罗拉钳口处基本不加捻,所以不存在所谓的“加捻三角区”,大大减少了车间的飞花。
4.经过络筒工序后,赛络纱的毛羽比紧密纱更少,所以在上浆、织造、烧毛工序中,有着更加优越的性能。
5.赛络纱在加捻过程中,纤维内、外转移的程度小,成纱后纤维排列规律,其纱线强力优于单纱,比股纱强力低,另外,赛络纱的细节少,这也对增加纱线强力有帮助。
6.赛络纺纱设备比紧密纺机构简单,设备投资少,宜于维护。
在老机上进行改造容易实现。
7.赛络纱有类似股纱的性能,在许多情况下,可以代替股纱。
但赛络纺纱不需经过并捻机,工艺流程比常规工艺短,节省能源和劳动力。
综上所述,赛络纺工艺有着其它纺纱工艺所无法比拟的优点,但也有其不足之处,如下所述:1.络纺工艺是双粗纱喂入,纺同号细纱时,如果粗纱定量不减少,细纱机的总牵伸倍数就要增加一倍。
现有细纱机的配置可能不适应,牵伸倍数过大,也要恶化细纱的条干水平。
如果降低粗纱定量,势必增加粗纱工序的负担。
为解决这个矛盾,我公司研制出细纱机三罗拉四皮圈超大牵伸机构,即在原有的三罗拉双皮圈牵伸机构的基础上,在后区增加上、下肖和上、下皮圈,使原来后区的简单罗拉牵伸区变成皮圈牵伸区,大大加强了对纤维的控制。
- 1、下载文档前请自行甄别文档内容的完整性,平台不提供额外的编辑、内容补充、找答案等附加服务。
- 2、"仅部分预览"的文档,不可在线预览部分如存在完整性等问题,可反馈申请退款(可完整预览的文档不适用该条件!)。
- 3、如文档侵犯您的权益,请联系客服反馈,我们会尽快为您处理(人工客服工作时间:9:00-18:30)。
环锭纺和气流纺
环锭纺纱(ring spinning),是现时市场上用量最多,最通用之纺纱方法,条子或粗纱经牵伸后的纤维条通过环锭钢丝圈旋转引入,筒管卷绕速度比钢丝圈快,棉纱被加捻制成细纱.广泛应用于各种短纤维的纺纱工程.如普梳,精梳及混纺,钢丝圈由筒管通过纱条带动绕钢领回转.进行加捻,同时,钢领的摩擦使其转速略小于筒管而得到卷绕.纺纱速度高,环锭纱的形态,为纤维大多呈内外转移的圆锥形螺旋线,使纤维在纱中内外缠绕联结,纱的结构紧密,强力高,适用于制线以及机织和针织等各种产品。
环锭纺(精梳)流程:
清花间--梳棉--预并条--条并卷--精梳--头道并条--二道并条--粗纱--细纱--络筒环锭纺(普梳)流程:
清花间--梳棉--头道并条--二道并条--粗纱--细纱--络筒
环锭纺与气流纺的区别:
气流纺与环锭纺一个是新型纺织技术,一个是老式纺纱技术。
气流纺是气流纺纱,而环锭纺则是机械纺,就是由锭子和钢领、钢丝圈进行加捻,由罗拉进行牵伸。
而气流纺则是由气流方式输送纤维,由一端握持加捻。
一般来说,环锭纱毛羽较气流纺偏多,强度较高,品质较好。
气流纺工序短,伸出的毛羽较少,支数和拈度不能很高,价格也较低。
从纱体结构上来说,环锭纺比较紧密,而气流纺的比较蓬松,风格粗犷,适合做牛仔面料,气流纺的纱一般比较粗。
环锭纺技术优点及应用范围
环锭纺是最古老的纺纱系统,至少在概念上如此,但技术并不陈旧。
现代环锭纺纱机具备了自动化特色,远比以往需要的劳动力少很多,生产质量也更高。
环锭纺纱机生产的纱线为其他系统生产的产品提供了标准。
现在,全球有150万立达(Rieter[1] )G33环锭纺纱锭正在在运行中,可经济的生产高质量纱线。
该机SERVOgrip落纱系统无需打脚,在开始落纱工艺之前,一定长度的纱线被夹持到SERVOgrip,因此能无障碍的启动纺纱,减少飞化和清洁纺锭的需要。
赛络纺
赛络纺(Sirospun)又名并捻纺,国内称为A,B纱,近期正式命为赛络纺。
赛络纺是在细纱机上喂入两根保持一定间距的粗纱,经牵伸后,由前罗拉输出这两根单纱须条,并由于捻度的传递而使单纱须条上带有少量的捻度,拼合后被进一步加捻成类似合股的纱线,卷绕在筒管上。
赛络纺的初始设计目的是用于毛纺上,特点是毛羽少,强力高,耐磨性好,达到毛纱能单纱织造的效果,以实现毛织物的轻薄化。
尽管赛络纺在许多方面比较同类常规纱有了较大的改善,要真正达到毛纺单纱不上浆织造,尚有一定距离。
其后毛纺亦多放弃此方法,反而在混纺如T/C,C.V.C等则采用此方法,因其染色后可产生并纱之麻花效果,手感好,故受欢迎,近期更因改善毛羽问题,如纺一些易产生毛羽之纤维,如人造棉,莫代尔,天丝,大豆纤维,甚至全棉都用此方法生产,赛络纱所用的原料等级可比常规环绽纺低,而其织物较常规环锭股线织物毛羽少,手感柔软,耐磨,透气性能好。
赛络纺断头处理:
由于赛络纺是由两根有一定间距的须条喂入细纱牵伸区,分别牵伸后加捻成纱,两股须条存在一股断头后另一股跑单纱的情况,并且在纺纱张力稳定的情况下不断头,造成错支纱,为保证纺纱质量,需加装赛络纺单纱打断装置,一股断头后打断装置能将另一股单纱打断。