赛络纺丝/绒纱线与环锭纺棉/绒纱线质量优势分析及探讨
环锭纺和气流纺、赛络纺
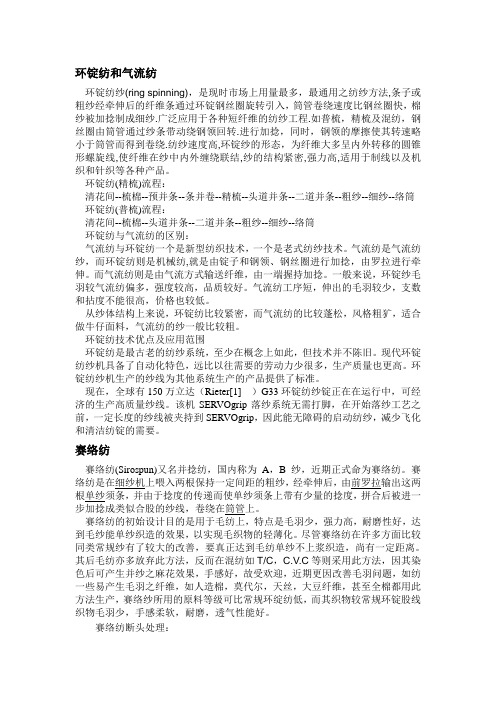
环锭纺和气流纺环锭纺纱(ring spinning),是现时市场上用量最多,最通用之纺纱方法,条子或粗纱经牵伸后的纤维条通过环锭钢丝圈旋转引入,筒管卷绕速度比钢丝圈快,棉纱被加捻制成细纱.广泛应用于各种短纤维的纺纱工程.如普梳,精梳及混纺,钢丝圈由筒管通过纱条带动绕钢领回转.进行加捻,同时,钢领的摩擦使其转速略小于筒管而得到卷绕.纺纱速度高,环锭纱的形态,为纤维大多呈内外转移的圆锥形螺旋线,使纤维在纱中内外缠绕联结,纱的结构紧密,强力高,适用于制线以及机织和针织等各种产品。
环锭纺(精梳)流程:清花间--梳棉--预并条--条并卷--精梳--头道并条--二道并条--粗纱--细纱--络筒环锭纺(普梳)流程:清花间--梳棉--头道并条--二道并条--粗纱--细纱--络筒环锭纺与气流纺的区别:气流纺与环锭纺一个是新型纺织技术,一个是老式纺纱技术。
气流纺是气流纺纱,而环锭纺则是机械纺,就是由锭子和钢领、钢丝圈进行加捻,由罗拉进行牵伸。
而气流纺则是由气流方式输送纤维,由一端握持加捻。
一般来说,环锭纱毛羽较气流纺偏多,强度较高,品质较好。
气流纺工序短,伸出的毛羽较少,支数和拈度不能很高,价格也较低。
从纱体结构上来说,环锭纺比较紧密,而气流纺的比较蓬松,风格粗犷,适合做牛仔面料,气流纺的纱一般比较粗。
环锭纺技术优点及应用范围环锭纺是最古老的纺纱系统,至少在概念上如此,但技术并不陈旧。
现代环锭纺纱机具备了自动化特色,远比以往需要的劳动力少很多,生产质量也更高。
环锭纺纱机生产的纱线为其他系统生产的产品提供了标准。
现在,全球有150万立达(Rieter[1] )G33环锭纺纱锭正在在运行中,可经济的生产高质量纱线。
该机SERVOgrip落纱系统无需打脚,在开始落纱工艺之前,一定长度的纱线被夹持到SERVOgrip,因此能无障碍的启动纺纱,减少飞化和清洁纺锭的需要。
赛络纺赛络纺(Sirospun)又名并捻纺,国内称为A,B纱,近期正式命为赛络纺。
赛络纺棉纱的优缺点及应用创新

赛络纺棉纱的优缺点及应用创新大耀纺织一直致力于为客户提供优质、性价比高的产品,现棉纱常备产品7S-60S常规品种。
近年来对于棉纱的质量尤其重视,开发了一系列的赛络纺产品,如10S/12S/16S都有大量库存,性价比高。
赛络纺相比传统的单纱环锭纺纱有许多优点,如毛羽少、条干更均匀、织物具有较高的抗起球性,手感柔软、抗摩擦性好,织物有更好的透气性。
下面为大家讲解赛络纺棉纱的优缺点及应用创新:一、赛络纺的原理赛络纺是在传统环锭细纱机上纺出类似于股线结构的纱线的一种纺纱方法,是在细纱机上喂入两根保持一定间距的粗纱,经牵伸后,由前罗拉输出这两根单纱须条,并由于捻度的传递而使单纱须条上带有少量的捻度,拼合后被进一步加捻成类似合股的纱线,卷绕在筒管上。
赛络纺又称并捻纺,国内称为A,B纱,近期正式命为赛络纺。
二、赛络纺的优点1、成纱断裂强度较高;2、断裂伸长率较大;3、毛羽大幅度减少;4、耐磨性和抗起球性好;5、粗、细节明显减少;6、车间内飞花减少;7、节约能源与劳动力;8、设备投资少;三、赛络纺与环锭纺之间的比较1、条干的改善是因为赛络纺由双根粗纱喂入,在牵伸区并合,所以条干、粗细节均有不同程度的改善。
2、毛羽的改善是因为在纺纱三角区单纱先轻微加捻,并和后再加捻。
须条在主加捻点处已变成圆柱体,有利于纤维端缠入纱体。
3、强力的增加是因为须条在前罗拉输出处有个三角形加捻区,须条受张力作用捻合在一起,形成类似股线的双中心纱条,在受力时,两个须条相互挤压,使纤维间不易滑脱,且毛羽低,纤维利用率高,因此强力大。
四、赛络纺纱容易出现的问题1、并合前纱条过细,易产生意外牵伸;2、成纱细节增加,纱线越细增加越明显;3、细纱断头增多,生产效率降低。
五、赛络纺断头处理由于赛络纺是由两根有一定间距的须条喂入细纱牵伸区,分别牵伸后加捻成纱,两股须条存在一股断头后另一股跑单纱的情况,并且在纺纱张力稳定的情况下不断头,造成错支纱,为保证纺纱质量,需加装赛络纺单纱打断装置,一股断头后打断装置能将另一股单纱打断。
不同纺纱方法的成纱机理及纱线耐磨性能研究

不同纺纱方法的成纱机理及纱线耐磨性能研究
唐新军;宋均燕;何小东;单小红
【期刊名称】《棉纺织技术》
【年(卷),期】2015(43)7
【摘要】探讨传统环锭纺、集聚纺、赛络纺、集聚赛络纺、喷气涡流纺的成纱机理以及纱线耐磨性能.用这5种方法纺100%新疆长绒棉精梳11.6 tex纱.对比测试了纱线的条干、毛羽、强力和耐磨性.结果表明:集聚赛络纱的各项质量指标和耐磨性均优于其他纺纱.虽然喷气涡流纱的强力和条干不如传统环锭纱,但是耐磨性和毛羽比传统环锭纱好.认为:在集聚纺、赛络纺、集聚赛络纺这样一些环锭纺纱新技术的纺纱过程中,集聚和并合作用都能提高纱线的耐磨性,集聚程度对纱线的耐磨性影响较大,并合作用相对较小.两种同时采用时,改善耐磨性的效果最好.同原料同号棉纱,其耐磨性与条干、强力、毛羽等性能呈现一定的相关关系,条干好、强力高、毛羽少的纱线耐磨性较好.
【总页数】5页(P17-21)
【作者】唐新军;宋均燕;何小东;单小红
【作者单位】新疆大学,新疆乌鲁木齐,830046;昌吉溢达纺织有限公司,新疆昌吉,831100;新疆溢达纺织有限公司,新疆乌鲁木齐,830054;新疆大学,新疆乌鲁木齐,830046
【正文语种】中文
【中图分类】TS104.7
【相关文献】
1.2009秋冬纱线展针织纱、色纺纱、新型混纤纱成热点 [J], 研祥
2.赛络纺纱线的成纱特点及应用研究 [J], 刘丽;毛雷
3.新型纱线的成纱机理、纱线结构与产品应用的分析与比较 [J], 田艳红;王键;李玲玲;王建坤
4.环锭纺纱线成纱毛羽的控制措施探讨 [J], 常勇;吴心红
5.不同纺纱方法纺制竹浆纤维纱的成纱质量对比 [J], 张勇
因版权原因,仅展示原文概要,查看原文内容请购买。
紧密纺_赛络纺纺纱经验及其探讨_王方水

紧密纺、赛络纺纺纱经验及其探讨王方水,郭 恒,贾云辉(鲁泰纺织股份有限公司,山东淄博 255100)摘要:介绍了紧密纺、赛络纺等新型纺纱技术原理及紧密纺纱线在色织面料方面的应用;分析紧密纺、赛络纺技术的优点及不足,并将其与普通纺进行对比,指出紧密纺、赛络纺技术生产的纱线质量好、强力高、毛羽少、条干均匀以及下游工序产品质量可进一步提高;加强对设备的日常维护、保养、保持器材部件清洁、运转正常,对充分发挥新型纺纱技术的优势至关重要,但企业要充分考虑其成本因素,应加速研发具有自己特色和自主知识产权,纺织企业能够接受的整机型和改造型的紧密纺细纱机及装置,以提高企业的竞争力。
关键词:紧密纺;塞络纺;优势;不足;器材配置;日常维护;竞争力中图分类号:TS104.7 文献标识码:A 文章编号:1001-9634(2009)03-0057-04收稿日期:2008-10-28作者简介:王方水(1961 ),男,山东淄博人,工程师,主要从事纺纱色织布的研究。
1 紧密纺等新型纺纱自1999年巴黎国际纺织机械展览会,立达(R-ieter )、青泽(Zinser )、绪森(Suessen)等国外纺机公司推出生产紧密纱的环锭细纱机以来,紧密纺纱技术迅速风靡整个纺织界。
紧密纺纱技术对改善纱线品质、提高成纱强力、减少毛羽等方面已经由实践证实,得到了快速发展。
欧洲计划用5a~10a 以紧密纺纱机全部替代普通环锭纺纱机,更有专家预言,未来属于紧密纺。
1.1 紧密纺纱原理紧密纺纱系统多数采用空气动力学原理,在纺纱三角区位置,通过一组集聚元件,使牵伸后的松散纤维须条经过负压吸聚管表面时,利用空气导向作用使纤维紧密地抱合在一起,经导向胶辊输出加捻成纱,纺纱过程中加捻三角区变得很小,基本消失,大大减少浮游外露纤维(即毛羽)的数量。
还有一种紧密纺纱系统不采用吸风而采用机械-磁铁原理工作,如瑞士罗托卡夫特公司生产的罗卡斯(Ro Co S)紧密纺系统装置,其前胶辊和引纱胶辊置于前下罗拉之上,磁性紧密器置于两个胶辊之间,共同形成紧密区。
赛络纺与环锭纺的区别
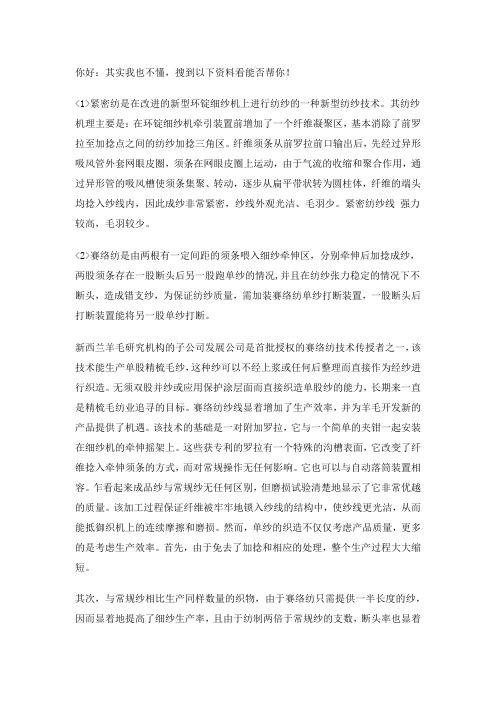
你好:其实我也不懂,搜到以下资料看能否帮你!<1>紧密纺是在改进的新型环锭细纱机上进行纺纱的一种新型纺纱技术。
其纺纱机理主要是:在环锭细纱机牵引装置前增加了一个纤维凝聚区,基本消除了前罗拉至加捻点之间的纺纱加捻三角区。
纤维须条从前罗拉前口输出后,先经过异形吸风管外套网眼皮圈,须条在网眼皮圈上运动,由于气流的收缩和聚合作用,通过异形管的吸风槽使须条集聚、转动,逐步从扁平带状转为圆柱体,纤维的端头均捻入纱线内,因此成纱非常紧密,纱线外观光洁、毛羽少。
紧密纺纱线强力较高,毛羽较少。
<2>赛络纺是由两根有一定间距的须条喂入细纱牵伸区,分别牵伸后加捻成纱,两股须条存在一股断头后另一股跑单纱的情况,并且在纺纱张力稳定的情况下不断头,造成错支纱,为保证纺纱质量,需加装赛络纺单纱打断装置,一股断头后打断装置能将另一股单纱打断。
新西兰羊毛研究机构的子公司发展公司是首批授权的赛络纺技术传授者之一,该技术能生产单股精梳毛纱,这种纱可以不经上浆或任何后整理而直接作为经纱进行织造。
无须双股并纱或应用保护涂层面而直接织造单股纱的能力,长期来一直是精梳毛纺业追寻的目标。
赛络纺纱线显着增加了生产效率,并为羊毛开发新的产品提供了机遇。
该技术的基础是一对附加罗拉,它与一个简单的夹钳一起安装在细纱机的牵伸摇架上。
这些获专利的罗拉有一个特殊的沟槽表面,它改变了纤维捻入牵伸须条的方式,而对常规操作无任何影响。
它也可以与自动落筒装置相容。
乍看起来成品纱与常规纱无任何区别,但磨损试验清楚地显示了它非常优越的质量。
该加工过程保证纤维被牢牢地锁入纱线的结构中,使纱线更光洁,从而能抵御织机上的连续摩擦和磨损。
然而,单纱的织造不仅仅考虑产品质量,更多的是考虑生产效率。
首先,由于免去了加捻和相应的处理,整个生产过程大大缩短。
其次,与常规纱相比生产同样数量的织物,由于赛络纺只需提供一半长度的纱,因而显着地提高了细纱生产率,且由于纺制两倍于常规纱的支数,断头率也显着下降。
环锭纺、气流纺、喷气纺、涡流纺、赛络纺、紧密纺简介

环锭纺、气流纺、喷气纺、涡流纺、赛络纺、紧密纺简介环锭纺环锭纺纱是现时市场上用量最多,最通用之纺纱方法,条子或粗纱经牵伸后的纤维条通过环锭钢丝圈旋转引入,筒管卷绕速度比钢丝圈快,棉纱被加捻制成细纱.广泛应用于各种短纤维的纺纱工程.如普梳,精梳及混纺,钢丝圈由筒管通过纱条带动绕钢领回转.进行加捻,同时,钢领的摩擦使其转速略小于筒管而得到卷绕.纺纱速度高,环锭纱的形态,为纤维大多呈内外转移的圆锥形螺旋线,使纤维在纱中内外缠绕联结,纱的结构紧密,强力高,适用于制线以及机织和针织等各种产品。
环锭纺(精梳)流程:清花间--梳棉--预并条--条并卷--精梳--头道并条--二道并条--粗纱--细纱--络筒环锭纺(普梳)流程:清花间--梳棉--头道并条--二道并条--粗纱--细纱--络筒气流纺气流纺不用锭子,主要靠分梳辊、纺杯、假捻装置等多个部件。
分梳辊用来抓取和分梳喂入的棉条纤维,同过他的高速回转所产生的离心力可把抓取的纤维甩出。
纺杯是个小小的金属杯子,他的旋转速度比分梳辊高出10倍以上,由此产生的离心作用,把杯子里的空气向外排;根据流体压强的原理,使棉纤维进入气流杯,并形成纤维流,沿着杯的内壁不断运动。
这时,杯子外有一根纱头,把杯子内壁的纤维引出来,并连接起来,再加上杯子带着纱尾高速旋转所产生的钻作用,就好像一边“喂”棉纤维,一边加纱线搓捏,使纱线与杯子内壁的纤维连接,在纱筒的旋绕拉力下进行牵伸,连续不断的输出纱线,完成气流纺纱的过程。
气流纺的特征气流纺纱有速度大、纱卷大、适应性广、机构简单和不用锭子、钢领、钢丝圈的优点,可成倍的提高细纱的产量。
气流纺与环锭纺的区别气流纺与环锭纺一个是新型纺织技术,一个是老式纺纱技术。
气流纺是气流纺纱,而环锭纺则是机械纺,就是由锭子和钢铃、钢丝圈进行加捻,由罗拉进行牵伸。
而气流纺则是由气流方式输送纤维,由一端握持加捻。
一般来说,环锭纱毛羽较少,强度较高,品质较好。
气流纺工序短,原料短绒较多,纱线毛,支数和拈度不能很高,价格也较低。
环锭细纱机上开发紧密赛络纺色纺纱的试验分析

ZH ANG Yi
( h n h n s a xi o , t , h n s a 2 2 0 C i ) Z @a g C a g h nTe t eC . L d C a g h n3 4 0 , hn l a Ab t a t Th s h ss n r d c s t e p l a i n o t e o a t p n i g c mp c S r sr c : i t e i i t o u e h a p i to f h c mp c s i n n , o a t io c s i n n e h o o y t o o p n i g I n l z s t e a v n a e f c mp c p n i g a d pn ig t c n lg o c lr s inn . ta ay e h d a tg so o a ts i nn n
y r e e ne s;harne s a n un v n s ii s
对传 统 的环 锭 纺纱 要 在 激 烈竞 争 中保 持优 势 , 必 须加 快技术 改 造和新 技术 应用 步伐 , 紧密 纺 、 赛络 纺 新颖 纱线 开发 与 生产 , 是 在 传 统环 锭 纺 机 上通 就 过 改造 与创 新获 得 。纺 织 工业“ 十二 五” 发展 规划 提 到棉纺 织 : 重点 推广 紧密 纺 、 扭矩 环锭纺 、 要 低 喷气 、
21 年纪代 饧织校 第 6 02 期
细纱技术进步专题
— —
环锭 细纱 机 上开 发 紧 密赛 络 纺 色 纺纱 的试验 分 析
张 毅
( 江 省 常 山纺 织 有 限责 任 公 司 , 江 常 山 3 4 0 ) 浙 浙 2 2 0
摘
棉纺环锭细纱机的赛络纺改造及成纱质量分析
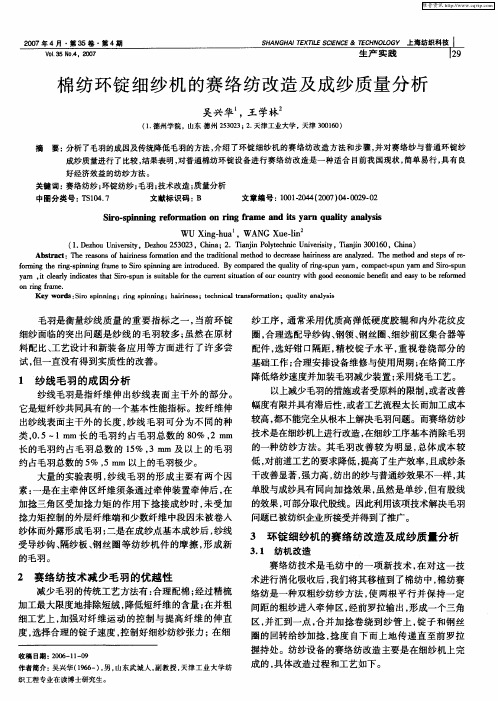
关键词 : 赛络纺纱 ; 环锭纺纱 ; ; 毛羽 技术改造 ; 量分 析 质
中图分类号 : S 0 . T 14 7 文献标识码 :B 文章编号 :( 07)4 0 2 - 2
S r -p n i g r f r a i n o i g f a e a d i a n q a i n l s io s i n n e o m t n rn r m n s y r n l y a a y i o t t s W U Xi g h a ,W ANG Xu - n n —u el i
吴兴华 王学林 ,
(. 1德州学 院, 山东 德州 2 3 2 ; . 5 0 3 2 天津工业 大学 , 天津 3 o6 ) 0 1o
摘
要: 分析 了毛羽 的成 因及 传统 降低 毛羽的方法 , 了环锭 细纱机 的赛 络纺 改造 方法和步 骤 , 对赛络 纱与普 通环锭 纱 介绍 并 成纱质 量进行 了比较 , 结果表明 , 普通棉纺环锭设 备进行赛 络纺 改造是一 种适合 目前我 国现状 , 对 简单 易行 , 具有 良
维普资讯
竺 竺兰 蔓 堂: 塑 星: 苎!
V I 5N . D 3 l o4.2 0 0 7
S HANGHAIT XT L Sc E E IE l NcE& T cHN0L E 0GY
生 产 实 践
棉纺环锭 细纱机 的赛络纺改造及成纱质量分析
Ab t a t h e s n f ar e sfr t n a d t e t dt n lmeh d t e r a e h i n s r n l z d sr c :T e r a 0 s o i n s o mai n r i o a t o d c e s a r e s ae a a y e .T e meh d se so — h i o h a i o i h to a t p f d n e r
赛络纺纱技术在高档针织纱生产中的比较优势
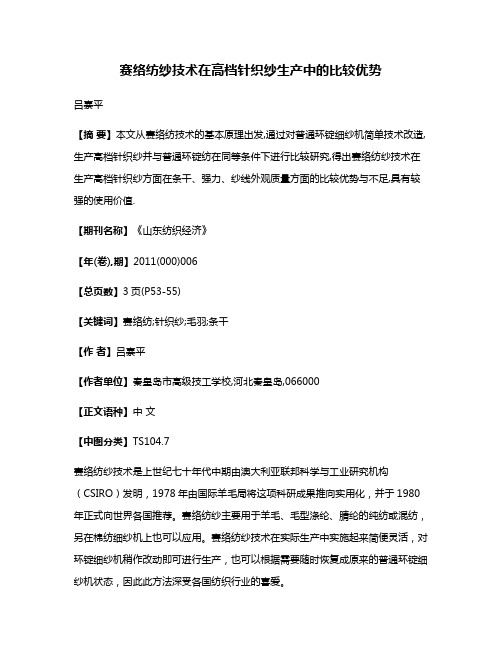
赛络纺纱技术在高档针织纱生产中的比较优势吕寨平【摘要】本文从赛络纺技术的基本原理出发,通过对普通环锭细纱机简单技术改造,生产高档针织纱并与普通环锭纺在同等条件下进行比较研究,得出赛络纺纱技术在生产高档针织纱方面在条干、强力、纱线外观质量方面的比较优势与不足,具有较强的使用价值.【期刊名称】《山东纺织经济》【年(卷),期】2011(000)006【总页数】3页(P53-55)【关键词】赛络纺;针织纱;毛羽;条干【作者】吕寨平【作者单位】秦皇岛市高级技工学校,河北秦皇岛,066000【正文语种】中文【中图分类】TS104.7赛络纺纱技术是上世纪七十年代中期由澳大利亚联邦科学与工业研究机构(CSIRO)发明,1978年由国际羊毛局将这项科研成果推向实用化,并于1980年正式向世界各国推荐。
赛络纺纱主要用于羊毛、毛型涤纶、腈纶的纯纺或混纺,另在棉纺细纱机上也可以应用。
赛络纺纱技术在实际生产中实施起来简便灵活,对环锭细纱机稍作改动即可进行生产,也可以根据需要随时恢复成原来的普通环锭细纱机状态,因此此方法深受各国纺织行业的喜爱。
根据顾客对高档针织产品的需求,我们在传统的环锭细纱机上进行改造,应用赛络纺纱技术,成功地生产5批高档羊绒混纺针织纱,并与普通环锭纱比较,在重量不匀、强力、伸长率等指标方面具有明显优势,且毛羽少,耐磨性好,达到毛纱能单纱织造的效果,以实现毛织物的轻薄化,因此深受顾客欢迎。
下面就此技术做一介绍,与同行共享。
赛络纺纱技术是将两根粗纱以一定的间距平行喂入环锭细纱机的同一牵伸机构,以平行状态同时被牵伸,从前罗拉夹持点出来后形成保持一定间距的两根纤维束,此两根须条由于前罗拉以下的环锭加捻作用自然汇聚,捻合成股线,然后经过导纱钩、钢丝圈卷取到纱管上,成为赛络纱线。
赛络纺纱技术所纺的纱线具有表面纤维排列整齐、毛羽少及外观光洁的特点。
这是由于在纺纱线的过程中,单纱加捻区域的长度低于纤维的平均长度,且施加的捻度又小,这使得单纱中的纤维螺旋线与纱轴的夹角较小,从而使得单纱中的单纤维不致因受到扭曲力的较大影响而横向突出纱的外表面。
环锭纺赛络纺和紧密纺的区别

环锭纺赛络纺和紧密纺的区别1.因为赛络纺是两根粗纱同时被分别牵伸,根据并合理论,CX=CA/√n,公式中CX为并合后的不匀率,CA为并合前的不匀率,n为并合根数,此处n等于2。
所以CX=0.7×CA。
当然上述公式是理论数据,和实际情况有一定差别。
但也说明:用赛络纺工艺方法纺成的纱对改善条干,减少粗、细节有非常明显的效果,这是无数纺纱厂所孜孜以求的。
我公司几年来的试验和众多用户的大量生产实践也充分证明了这一点。
2.赛络纺的纱条从前罗拉输出后,在捻合时,两根弱捻纱条相互为中心卷成一根赛络纱。
在卷绕过程中,把伸出纱条主体的毛羽卷进纱线里面,并得到了良好的握持。
所以,赛络纱的毛羽比其它工艺方法都少,而且因为毛羽被两根纱条卷在细纱内,所以经过络筒工序时,也不会象其它纺纱方法大量增加毛羽,这一点时其它纺纱方法所无法比拟的。
3.赛络纺的纱条在前罗拉钳口处基本不加捻,所以不存在所谓的“加捻三角区”,大大减少了车间的飞花。
4.经过络筒工序后,赛络纱的毛羽比紧密纱更少,所以在上浆、织造、烧毛工序中,有着更加优越的性能。
5.赛络纱在加捻过程中,纤维内、外转移的程度小,成纱后纤维排列规律,其纱线强力优于单纱,比股纱强力低,另外,赛络纱的细节少,这也对增加纱线强力有帮助。
6.赛络纺纱设备比紧密纺机构简单,设备投资少,宜于维护。
在老机上进行改造容易实现。
7.赛络纱有类似股纱的性能,在许多情况下,可以代替股纱。
但赛络纺纱不需经过并捻机,工艺流程比常规工艺短,节省能源和劳动力。
综上所述,赛络纺工艺有着其它纺纱工艺所无法比拟的优点,但也有其不足之处,如下所述:1.络纺工艺是双粗纱喂入,纺同号细纱时,如果粗纱定量不减少,细纱机的总牵伸倍数就要增加一倍。
现有细纱机的配置可能不适应,牵伸倍数过大,也要恶化细纱的条干水平。
如果降低粗纱定量,势必增加粗纱工序的负担。
为解决这个矛盾,我公司研制出细纱机三罗拉四皮圈超大牵伸机构,即在原有的三罗拉双皮圈牵伸机构的基础上,在后区增加上、下肖和上、下皮圈,使原来后区的简单罗拉牵伸区变成皮圈牵伸区,大大加强了对纤维的控制。
给我一分钟的时间,告诉你如何区分环锭纺、气流纺、涡流纺和赛络纺

给我⼀分钟的时间,告诉你如何区分环锭纺、⽓流纺、涡流纺和赛络纺今天⼩编教⼤家通过退捻的⽅法
来区分环锭纺、⽓流纺、涡流纺和赛络纺
在这之前,我们要先说⼀下退捻的⽅法,
请看下⾯的视频
⼀、退捻教学视频
(视频有9秒,建议在WIFI下观看,⽆声,⼟豪随意)
学会了退捻之后,我们就可以通过退捻的⽅法来区分四种纱线了
⼆、四种纱线的区分
1.环锭纺纱线
环锭纺整根纱线都能够完全退捻,退完捻后纱线没有强⼒
2.赛络纺纱线
赛络纺整根纱线都能够完全退捻,退完捻后纱线没有强⼒
在这四种纱线中,赛络纺唯⼀⼀个看起来是两根的纱线合成的⼀根单纱
赛络纺就是⾼档环锭纺(是由两根粗纱⼀起并⾏输⼊纺成⼀根细纱)
条⼲好,⽑⽻少,强度⽐环锭纺⼤
3.⽓流纺纱线(转杯纺)
⽓流纺⽆法像环锭纺⼀样整根纱线完全退捻,只能少的局部能完全退捻,所以退捻后被退捻的
节点也没有强⼒,整根纱⼀拉就断
4.涡流纺纱线
涡流纺退捻后外表看起来完全退捻,但纱芯没有退捻,还是有很⼤的强度,
三、纱线的区分流程
第1步:拿到⼀根纱线退捻
没有整根纱线完全退捻,只有部分节点完全退捻,⽓流纺
第2步:看起来完全退捻
第3步:看是否有强⼒
(有→涡流纺,没有→环锭纺)
第4步:观察是否有两根
(有→赛络纺,没有→普通环锭纺)
四、成纱⽐较
(同等原料同样⽀数相⽐)
环锭纺适纺范围最⼴,通常可纺300英⽀以下的纱线,转杯纺⽬前通常适纺40英⽀以下的纱线,涡流纺⽬前适纺60英⽀以下的纱线
END。
【技术】赛络纺纱线性能分析及工艺实践

【技术】赛络纺纱线性能分析及工艺实践赛络纺;加捻三角区;捻幅;细节;纤维散失;集合器赛络纺工艺是从毛纺工艺中移植到棉纺工艺的一种纺纱工艺。
该工艺方法是将两根粗纱以一定的间距,平行喂入细纱牵伸区,两根粗纱在前钳口外,加捻三角区处加捻聚合成纱(见图1)。
图1 赛络纺加捻三角区一赛络纺纱线的优点分析由于特殊的工艺方法,使赛络纺纱具备一些优点。
(1)条干均匀度好。
主要是由于两根须条的粗、细节互补作用,使成纱条干较为均匀。
(2)纱线强力高。
由于两根须条聚合后成纱,分别带有一定的捻回,同向捻回的叠加使外层纤维具有了更大的捻幅。
使成纱强力有所提高。
(3)纱线毛羽少。
加捻三角区是形成毛羽的主要区域,此处边缘纤维与须条轴线形成一定的夹角,使边缘纤维受力拉伸幅度较大,而须条芯部的纤维受力较少,边缘纤维就会挤压芯部纤维,边缘纤维进入芯部,芯部纤维被挤压到边缘,须条内纤维不断地发生内外转移。
而一端露出纱体的边缘纤维由于不再承受斜向拉力,向心压力变为零,不再参与内外转移,露出纱体的一端便形成毛羽。
而赛络纺中加捻三角区处两根须条上的表面毛羽在加捻点聚合成纱时,又有机会重新捻入纱体成为纱线内部纤维(见图2)。
加上单根须条和聚合成纱捻幅的叠加作用。
使得赛络纺纱线毛羽减少。
另外两根须条具有一定的间距,使加捻三角区变宽,边缘纤维到达捻合点的距离变长,相对较短的边缘纤维头端还没到达捻合点,而尾端已经脱离前钳口的有效握持区而提前散失,使得纱线外层短纤维减少,毛羽相对较少。
在一定范围内,随着两根粗纱间距的增加,赛络纺纱线的毛羽减少趋势更加明显。
图2 赛络纺加捻三角区示意图捻幅的叠加使纱线毛羽减少、强力增加,不仅表现在成纱上,而且在后期整理和织造过程中也会表现出比环锭纺单纱更大的优越性。
由于赛络纺纱具有类似股线的特点,复合捻度的作用使纱线内的纤维呈现复杂的空间螺旋曲线,几乎不存在捻幅为零的芯部纤维,这就使纱线中的纤维都能够承担轴向应力,纤维强力利用系数高,使纱线在后期整理和织造时反复拉伸的过程中强力损失较小。
基于几何模型的赛络纱与环锭纱毛羽分析 霍亮袁马崇启
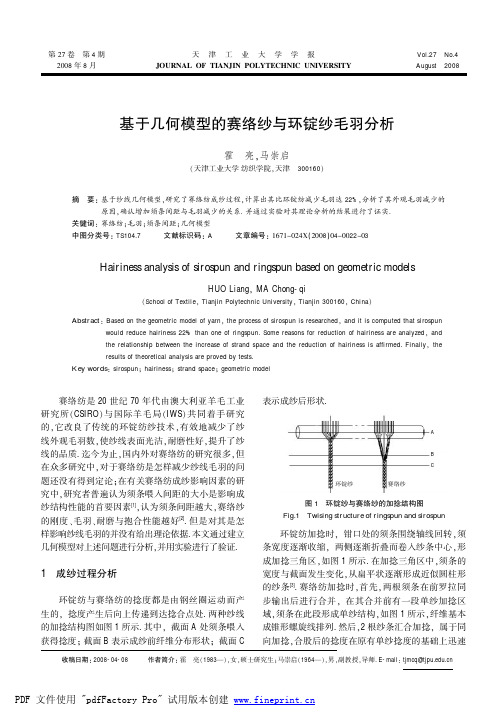
第27卷第4期2008年8月天津工业大学学报JOURNAL OF TIANJIN POLYTECHNIC UNIVERSITYVol.27No.4August 2008基于几何模型的赛络纱与环锭纱毛羽分析霍亮袁马崇启(天津工业大学纺织学院,天津300160)摘要:基于纱线几何模型,研究了赛络纺成纱过程,计算出其比环锭纺减少毛羽达22%,分析了其外观毛羽减少的原因,确认增加须条间距与毛羽减少的关系.并通过实验对其理论分析的结果进行了证实.关键词:赛络纺;毛羽;须条间距;几何模型中图分类号:TS104.7文献标识码:A文章编号:1671-024X (2008)04-0022-03Hairiness analysis of sirospun and ringspun based on geometric modelsHUO Liang ,MA Chong-qi(School of Textile ,Tianjin Polytechnic University ,Tianjin 300160,China )Abstract :Based on the geometric model of yarn ,the process of sirospun is researched ,and it is computed that sirospunwould reduce hairiness 22%than one of ringspun.Some reasons for reduction of hairiness are analyzed ,and the relationship between the increase of strand space and the reduction of hairiness is affirmed.Finally ,theresults of theoretical analysis are proved by tests.Key words :sirospun ;hairiness ;strand space ;geometric model收稿日期:2008-04-08作者简介:霍亮(1983—),女,硕士研究生;马崇启(1964—),男,副教授,导师.E-mail :tjmcq@赛络纺是20世纪70年代由澳大利亚羊毛工业研究所(CSIRO )与国际羊毛局(IWS )共同着手研究的,它改良了传统的环锭纺纱技术,有效地减少了纱线外观毛羽数,使纱线表面光洁,耐磨性好,提升了纱线的品质.迄今为止,国内外对赛络纺的研究很多,但在众多研究中,对于赛络纺是怎样减少纱线毛羽的问题还没有得到定论;在有关赛络纺成纱影响因素的研究中,研究者普遍认为须条喂入间距的大小是影响成纱结构性能的首要因素[1],认为须条间距越大,赛络纱的刚度、毛羽、耐磨与抱合性能越好[2].但是对其是怎样影响纱线毛羽的并没有给出理论依据.本文通过建立几何模型对上述问题进行分析,并用实验进行了验证.1成纱过程分析环锭纺与赛络纺的捻度都是由钢丝圈运动而产生的,捻度产生后向上传递到达捻合点处.两种纱线的加捻结构图如图1所示.其中,截面A 处须条喂入获得捻度;截面B 表示成纱前纤维分布形状;截面C表示成纱后形状.环锭纺加捻时,钳口处的须条围绕轴线回转,须条宽度逐渐收缩,两侧逐渐折叠而卷入纱条中心,形成加捻三角区,如图1所示.在加捻三角区中,须条的宽度与截面发生变化,从扁平状逐渐形成近似圆柱形的纱条[3].赛络纺加捻时,首先,两根须条在前罗拉同步输出后进行合并,在其合并前有一段单纱加捻区域,须条在此段形成单纱结构,如图1所示,纤维基本成锥形螺旋线排列.然后,2根纱条汇合加捻,属于同向加捻,合股后的捻度在原有单纱捻度的基础上迅速图1环锭纱与赛络纱的加捻结构图Fig.1Twising structure of ringspun and sirospun环锭纱赛络纱A B C第4期增加,使股线中的单纱及纤维螺旋线更加明显,纤维倾斜程度增加,使股线截面成圆形结构[4].赛络纺中,由于单股纱加捻区域短,所获得的捻度少,纤维排列相对顺直,纤维两头外伸机会少,使得毛羽少.而在随后的合股中,单纱的一部分毛羽被捻入纱线体内,也减少了毛羽.所以,赛络纺的毛羽会少于环锭纺的毛羽.2毛羽分析为了研究赛络纱较环锭纱在毛羽方面的不同,设计一个赛络纺理想状态下的几何模型.由参考文献[4~6]分析可知:赛络纱截面形状是与普通环锭纱相同的圆形.并且,赛络纱内部两股单纱各占一半,互不交涉,有明显的分界线.通过电子显微镜观测所得的赛络纱横截面如图2所示,由黑白单纱经过加捻后组成的赛络纱中,两股单纱各占一半,有明显的分界线.据此设计如图3所示的赛络纱结构模型.假设:没形成赛络纱前,两股单纱在图1中的截面B 处的形状是两个标准的圆形.用圆O 1、O 2表示,它们细度相同,半径为r ;成型后,赛络纱与环锭纱的截面形状均为标准的圆形O ,半径为R ,即图1中截面C 处的成纱形状;两股纱的分界线为直线,如图3直径BC .理想状态下,由于成纱支数相同,在截面B 上,赛络纱与普通环锭纱的面积相同,即πR 2=2πr 2.所以R =2√r (1)经过加捻,两根单纱向中心汇合,单纱上一部分毛羽被捻入纱线内部,体现在图3上即圆O 1、O 2一段弧上的毛羽被捻入纱线内部BC 上.而剩下的弧上毛羽会存在于纱线的表面,形成赛络纱的毛羽.假设纱线的毛羽在纱线外表面均匀分布,那么就可以用纱截面的弧长来表示纱线毛羽的相对数量.由圆的周长公式得单纱O 1周长L O 1=2πr(2)由于两股单纱被相互挤压,向中心汇合,故可理解为圆O 1、O 2圆周上各自的一段弧长不断向中心贴近,最后被挤压成直线BC 存在于加捻后的单纱中.由于向中心贴近后长度不变,故线段BC 的长度L BC 等于圆O 1、O 2上各自被捻入纱线内部的弧长.所以单纱O 1没有被捻入股线内的外表弧长L D =L O 1-L BC (3)由(1)、(2)、(3)式得L D =3.452r (4)在模型中,两股细纱细度相同,且理解为完全对称状态.那么,赛络纱外表面周长L S =2L D =6.904r (5)而环锭纺横截面周长L H =2πR =8.880r (6)所以,赛络纱的外观毛羽N s 与环锭纱外观毛羽N H 的比值τ=N S /N H =L S /L H =0.78(7)据此可以看出,赛络纺较传统环锭纺可减少毛羽22%.但实际上赛络纱中两股单纱的分界线BC 并不一定以直线状态存在.研究表明,加捻后的赛络纱中单纱截面基本属于圆形或椭圆形,其分界线会以曲线形式存在[6],纱线的横截面显微镜图(图2)也证明了这一点.那么上面以BC 为直线计算得到的值就是一个最小值.即赛络纺较传统环锭纺最小可减少毛羽22%.3须条间距对赛络纺毛羽的影响为了研究须条间距对赛络纺毛羽的影响,基于前面理论分析,进一步建立几何模型,如图4所示.在前面的分析中,假设在聚合点上的纤维截面为图2赛络纱的横截面图Fig.2Cross-section of sirospun344μm图3理想状态赛络纱结构图Fig.3Idealized structure of sirospunBARO 1rOO 2Cd截面A截面B图4赛络纺成纱三角区分析图Fig.4Analysis of sirospun in twisting triangular spacerl O 2O ′2O ′1O 1a a霍亮,等:基于几何模型的赛络纱与环锭纱毛羽分析23——天津工业大学学报第27卷圆形.而实际上由于赛络纺两须条间有一定距离,所以在聚合点上存在一个角度,而且在聚合点处的纤维之间有挤压作用,这些原因使得在截面B 处的纤维聚合形成非标准的圆形,如图4所示.图4中,两个圆柱体表示形成的两股细纱.在截面A 上,d 表示两须条间的距离;α表示须条与中心轴的夹角;椭圆O 1′、O 2′表示形成的两股细纱横截面O 1、O 2在截面B 上的投影形状,为实际上通过截面B 时纱线的形状,它们的长径为r 、短径为r ′,如图5所示.由图4的对应关系得r ′=r cos α(8)椭圆的周长公式:L O 1=2πr′+4(r -r ′)(9)根据(1)、(3)、(8)、(9)式得出:L D ′=1.172r +2.28r cos α(10)由(5)、(6)、(7)、(10)式得出,赛络纱与环锭纱外观毛羽的比值τ′=0.264+0.514cos α(11)由实验观察α∈(0°,45°).所以,τ′是关于α的减函数.随着d 增加,α增大,τ′减小.也就是说,随着两须条间的距离d 增加,赛络纺毛羽减少的百分比增加.当α=0时,这时模型与理想状态模型一致,代入公式(11),得τ′=0.78,与前面结论相同.4验证实验在电子小样赛络纺细纱机上,采用双喇叭喂入的方法,通过调整两个喇叭口的中心距离纺出不同间距的赛络纱.利用测试仪比较相同支数的赛络纱与环锭纱毛羽指数的差异.实验所用粗纱原料为羊绒50%、0.17tex 粘胶50%;捻度为30捻/m ,锭重7.5g/10m ;细纱号数76tex ,捻度为420捻/m.采用YG172型纱线毛羽测试仪测试5次,片段长度10cm ,数据见表1.由表1可以看出,赛络纺纱线的各种毛羽长度的毛羽指数均明显小于环锭纺.其中3mm 长毛羽赛络纱较环锭纱减少毛羽百分比范围达到22%~48%.从表中也可以看出,随着赛络纺须条间距的增大,各长度的毛羽指数是成减小趋势,毛羽减少百分比增加,验证了上面模型中得出的结果.5结束语赛络纺因为其特殊的加捻方式,使得更多的毛羽被捻入纱线内部,从而使得纱线外观毛羽减少.假设纱线外观毛羽在纵向以及截面圆周上分布均匀,用几何图形表示赛络纱的截面形态,从而可用截面毛羽分布弧长来代表整根纱线的毛羽情况.运用此方法得出:在支数相同的情况下,赛络纱较环锭纱可以有效减少毛羽22%以上;赛络纺中两须条间的距离是影响成纱的主要因素之一,理论分析及实验表明随着间距的增加,加捻三角区成角增大,纠缠于纱线内部的毛羽更多,从而使赛络纺毛羽减少百分比增加.参考文献院[1]李玮茹.赛络纺成纱机理的研究[D].上海:东华大学,2003.[2]CHENG K P S ,SUN M N.Effect of spacing and twist multiplier on cotton sirospun yarn[J].Textile Res J ,1998,7:520-527.[3]CHENG Long ,FU Peihua ,YU Xiuye .Relationship between hairiness and the twisting principles of solospun and ring spun yarns [J].Textile Res J ,2004,9:763-766.[4]张进武.赛络纺纱线捻度结构分析[J].棉纺织技术,2006,34(7):16-19[5]SUN M N ,CHENG K P S.Structure and properties of cottonsirospun yarn[J].Textile Res J ,2000,3:261-268.[6]张同华,韩光亭,王成君,等.关于赛络纺纱线捻度的探讨[J].青岛大学学报,2003,18(4):14-16.表1环锭纺与赛络纺纱线毛羽指数Tab.1Hairiness indexes of ringspun and sirospun毛羽长度/mm 23456环锭纺纱线/(根·m -1)45.015.1 6.0 2.6 1.2d =0mm 赛络纱/(根·m -1)毛羽减少百分比/%37.01811.126 4.229 1.9270.835d =3mm 赛络纱/(根·m -1)毛羽减少百分比/%37.31711.822 5.114 2.311 1.23d =6mm 赛络纱/(根·m -1)毛羽减少百分比/%33.42610.431 5.0162.0231.110d =11mm 赛络纱/(根·m -1)毛羽减少百分比/%33.9259.140 3.739 1.4460.839d =13mm 赛络纱/(根·m -1)毛羽减少百分比/%32.2288.842 3.344 1.5440.745d =15mm 赛络纱/(根·m -1)毛羽减少百分比/%30.9318.047 3.247 1.0620.465d =17mm 赛络纱/(根·m -1)毛羽减少百分比/%29.5347.8482.8541.1600.468图5赛络纱结构图Fig.5Yarn structure of sirospunCBAR O 1′rr ′OO 2′′24——。
赛络纺乃呙流纺廊锭纺竹纤维成纱质量对比分析
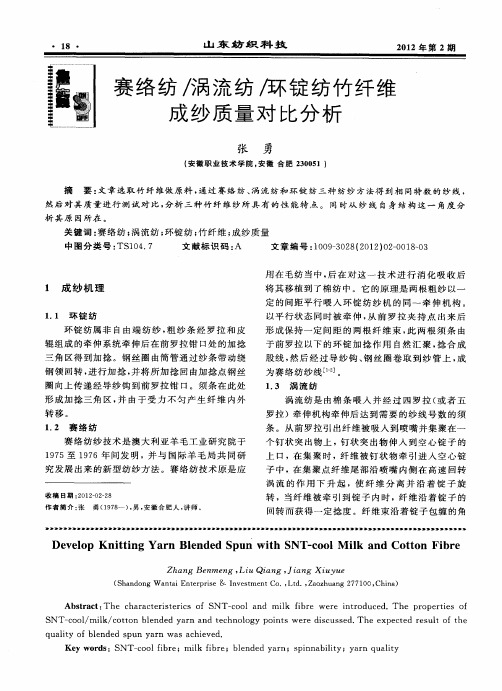
Ab t a t The ha a t rs e i s f SN T— o a m ik i e sr c : c r c e it rc o c ol nd l fbr we e ntodu e r i r c d.The pr pe te o o r is f
S NT—o lmi / o t n b e d d y r n e h oo y p i t r ic se . e e p ce e u to h c o/ l c to ln e a n a d t c n lg o n swe ed s u s d Th x e t d r s l ft e k
21 0 2年 第 2期
山 东 纺 织 科 技
.1 . 9
度及 回转 角度 均 可控 制 , 现 了高速 度 纺纱 并 获 实
得真 捻 。 由于涡 流 纺 具 有 纺 纱 速 度 高 、 程 短 特 流
3 3 成 纱质 量测 试对 比分 析 .
成纱 强伸 度测 试结 果见 表 1 。
赛 络 纺纱 技 术是 澳 大利 亚羊 毛 工业 研究 院于 17 9 5至 1 7 9 6年 间发 明 ,并 与 国际 羊 毛 局 共 同 研 究 发展 出来 的新 型纺 纱 方法 。赛 络 纺技 术原 是 应
收 稿 日期 :0 20 — 8 2 1-22
上 口,在 集 聚 时 ,纤 维 被 钉状 物 牵 引 进入 空心 锭 子 中 ,在集 聚 点纤 维尾 部 沿 喷 嘴 内侧 在 高速 回转
紧密赛络纺纱技术在棉纺中的应用探讨_杨丽丽 (1)

紧密赛络纺纱技术在棉纺中的应用探讨杨丽丽谢春萍王兰兰黄晶全江南大学纺织服装学院(中国)摘要:介绍了紧密赛络纺技术的原理及其特点。
将自行研制的具有不同吸风双槽的紧密赛络纺集聚装置应用于国产棉纺细纱机,分别纺制相同线密度的棉纱,并与相同工艺条件下的紧密纺和赛络纺纱线进行纱线结构与性能的比较分析。
最后,用模糊数学的方法对结构不同的吸风双槽进行综合性能评判。
关键词:紧密赛络纺纱技术,棉纺,纱线结构,纱线性能,模糊数学纱线性能主要受纤维的性能和纱线结构的影响,而纱线结构主要是由纺纱过程所决定的。
事实上,每种纺纱过程都会生产出不同于其他纱线的结构。
近些年来,纺纱技术的改良使纱线质量有了很大的进步,赛络纺、紧密纺等新纺纱工艺的出现,为环锭纺纱技术在扩大品种适应性、改善纱线结构、提高纱线质量等方面起到了有力的促进作用。
赛络纺纱工艺,是对传统细纱机加以改进而直接纺出类似于双股线结构纱线的一种纺纱方法,赛络纺纱线条干均匀、毛羽少、手感柔软、透气性好;紧密纺纱工艺,通过有效缩小纱线成形区的纤维须条宽度,缩小或消除加捻三角区,从而进一步改善纱线结构,大幅度提高纱线品质,紧密纺成纱结构最为紧密,纱线外观光洁、毛羽少[1~3]。
因此,两者的结合可获得符合特定使用要求、性能优越、具有全新效果的低线密度纱线,紧密赛络纺纱技术也正是在此基础上应运而生,具有良好的发展前景。
1紧密塞络纺纺纱原理如图1所示,两根粗纱以一定的间距经过双喇叭口平行喂入环锭细纱机的同一牵伸机构,以平行状态同时被牵伸,从前罗拉夹持点出来后进入气动集聚区。
在每个纺纱部位开有双槽且内部处于负压状态的异型管表面套有网格圈,网格圈受输出罗拉摩擦传动。
由前罗拉输出的两根须条受负压作用吸附在网格圈表面对应双槽的位置,须条在受集聚控制的同时随网格圈向前运动,由输出钳口输出。
集聚后的两束纤维获得较为紧密的结构,分别经轻度初次加捻后,在结合点处结合,然后再加强捻,卷曲到纱管上,成为具有类似股线结构的紧密赛络纱。
赛络纺乃呙流纺廊锭纺竹纤维成纱质量对比分析

赛络纺乃呙流纺廊锭纺竹纤维成纱质量对比分析赛络纺、乃呙流纺、廊锭纺是目前常见的纺纱工艺,它们各自有其适用的纺纱原料和工艺特点。
本文将从纤维成纱的质量角度对这三种工艺进行对比分析。
赛络纺是一种较新的纺纱工艺,其主要特点是纤维成纱过程中无需揉搓和拧紧,纤维在纱锭旋转时自由地络合成纱。
这一工艺在生产上的优点是纺纱速度较快、梳棉系统相对简单,纤维破损较少,成纱品质较好。
赛络纺适用于长纤维、细纱纺纱,如棉、麻等。
乃呙流纺是一种传统的纺纱工艺,其特点是纤维成纱过程中需要经过揉搓和拧紧。
这一工艺在生产上的优点是纱线的强度较高、纤维的整齐度好,适用于纤维长度较短、粗纱纺纱,如羊毛、粗棉等。
然而,乃呙流纺的纺纱速度较慢,机器复杂,纤维易受损,产量相对较低。
廊锭纺是一种介于赛络纺与乃呙流纺之间的工艺。
其特点是纤维成纱过程中既有一定程度的揉搓和拧紧,又有自由络合的环节。
廊锭纺的生产速度介于赛络纺与乃呙流纺之间,其整齐度和强度也介于两者之间。
该工艺适用于各种纤维类型。
在纤维成纱质量方面的对比分析中,赛络纺相对于乃呙流纺和廊锭纺,具有更好的颗粒度和纤维长度分布,纺纱后的纱线质地更加柔软,纺织品的手感更好。
然而,赛络纺的生产成本较高,设备维护及操作复杂,长时间生产易造成机器故障。
乃呙流纺由于需要经过揉搓和拧紧的步骤,纺纱后的纱线强度较高,纤维的整齐度也更好,适用于粗纺细织产品的制造。
然而,乃呙流纺的生产速度较慢,耗能较大,且纤维易受损,纺纱产量限制较大。
而廊锭纺则兼具了赛络纺和乃呙流纺的优点。
其纺纱速度相对较快,纺织品的品质也较高。
同时,廊锭纺还具有较低的故障率和维护成本,使得其在纤维成纱工艺中得到广泛应用。
综上所述,赛络纺、乃呙流纺和廊锭纺是三种常见的纺纱工艺,各自适用于不同类型的纤维和织物产品。
赛络纺在纺织品的柔软度和颗粒度上更具优势,而乃呙流纺则在强度和整齐度方面更出色。
廊锭纺则兼具两者的优点,且维护成本较低。
在选择纺纱工艺时,需要根据不同的需求和实际情况进行权衡。
赛络纺的纺纱工艺
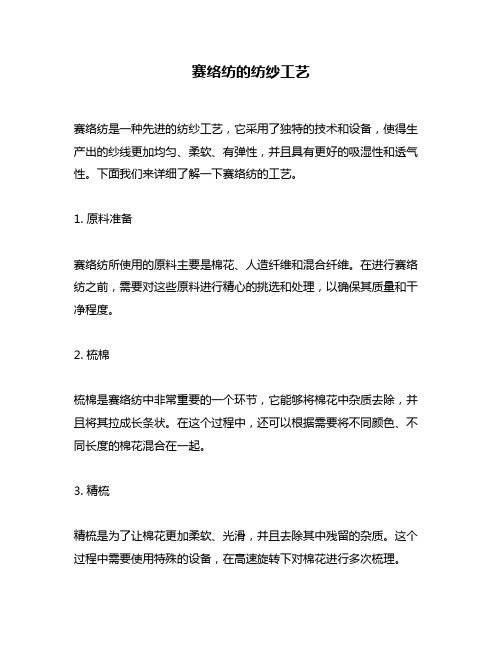
赛络纺的纺纱工艺
赛络纺是一种先进的纺纱工艺,它采用了独特的技术和设备,使得生产出的纱线更加均匀、柔软、有弹性,并且具有更好的吸湿性和透气性。
下面我们来详细了解一下赛络纺的工艺。
1. 原料准备
赛络纺所使用的原料主要是棉花、人造纤维和混合纤维。
在进行赛络纺之前,需要对这些原料进行精心的挑选和处理,以确保其质量和干净程度。
2. 梳棉
梳棉是赛络纺中非常重要的一个环节,它能够将棉花中杂质去除,并且将其拉成长条状。
在这个过程中,还可以根据需要将不同颜色、不同长度的棉花混合在一起。
3. 精梳
精梳是为了让棉花更加柔软、光滑,并且去除其中残留的杂质。
这个过程中需要使用特殊的设备,在高速旋转下对棉花进行多次梳理。
4. 赛络
赛络是指将经过梳理后的棉花进行拉伸,然后再将其紧密地卷成一根纱线。
这个过程中需要使用赛络机,它能够对纱线进行不断地拉伸和卷曲,从而使得纱线更加均匀、柔软、有弹性。
5. 捻合
捻合是为了让纱线更加牢固,并且增加其强度。
在这个过程中,需要将两根或多根纱线捻合在一起,从而形成一个更加稳定的结构。
6. 包装
最后,经过上述工艺处理后的纱线需要进行包装,并且标明其规格、颜色等信息。
这个过程中需要使用自动化包装设备,并且进行质量检测,以确保每一批产品都符合要求。
总之,赛络纺是一种非常先进的纺织工艺,在生产出高品质的棉纱、混纺纱等方面具有很大优势。
通过精心的原料准备、梳棉、精梳、赛络、捻合和包装等环节,可以生产出各种优质的产品,满足不同客户的需求。
技术环锭纺包芯纱和赛络纺包芯纱的对比

技术环锭纺包芯纱和赛络纺包芯纱的对比包芯纱又称复合纱或包覆纱,它是由两种或两种以上的纤维组合而成的一种新型纱线。
最初的包芯纱是以棉纤维为皮、涤纶短纤纱为芯开发的短纤维与短纤维包芯纱。
对于高强耐用、免烫、尺寸稳定又抗起球、吸湿透气、美观舒适的纺织品,如缝纫线和军服等,包芯纱比一般的纯纺纱和混纺纱优越,更能满足要求。
但传统的环锭纺包芯纱包覆效果欠佳,有时其结构就象把长丝和外包纤维须条并捻在一起的股线,没有适宜后序机械加工的抗剥离强度,因而降低了包芯纱的附加值,限制了包芯纱的潜在用途。
赛络纺包芯纱是一种具有股线性质的单纱,其强力、伸长、均匀度优于环锭纺包芯纱,且手感柔软、包覆效果好。
为了能经济地生产出质量优良、符合客户要求的包芯纱,结合本厂的生产实际,比较了传统和赛络纺锦纶长丝包芯纱的生产设备和成纱性能,分析了二者的差异,指出了应采取的合理纺纱工艺等。
1设备改造1.1 环锭纺包芯纱的设备改装传统环锭纺包芯纱可在普通改装过的细纱机上生产。
首先在一般的细纱机上加装芯丝喂入机构和预牵伸机构。
筒子长丝在导丝罗拉的牵引下退绕,不经过细纱机的牵伸机构,而是经过加装的预牵伸机构和V形槽导轮,自前罗拉皮辊后的集合器喂入,与牵伸后的须条合并,再通过前罗拉和导纱钩,由环锭回转加捻为长丝包芯纱。
接着改装粗纱架。
由于所用的锦纶长丝外形尺寸大于200mm×500mm,一台粗纱架由六列单层吊锭,改为四列单层吊锭,锭距由原来的210mm改为130mm。
芯丝喂入装置位于粗纱架上方,因而粗纱架下降30mm,以便腾出空间加装长丝立柱、托架和插丝锭子。
考虑到可操作性,只在立柱上加装二排长丝托架和锭子,利用粗纱前的空间,加装一排长丝托架和锭子。
这样,可以合理分布粗纱和长丝,长丝由导丝杆引出,喂入牵伸区前钳口,粗纱则经由导纱杆和分纱棒引出,喂入牵伸后区。
将横动杆固定,确保从喇叭口喂入经牵伸区输出的粗纱须条不产生移动。
在摇架位置加装导丝轮,有效控制长丝在前罗拉输出时始终位于粗纱须条中央,减少露芯等包芯纱缺陷,提高包覆效果。
紧密纺和赛络纺知识

紧密纺和赛络纺知识近年来,关于紧密纺及赛络纺两种新型纺纱方法的报道很多,这两种新型纺纱工艺对于提高成纱质量的效果也是大家所公认的,本文将根据我公司4年多来的研究结果及用户的使用情况,对两种纺纱工艺的特点及成纱质量进行分析。
紧密纺纱工艺尽管在机械结构上有所不同,但有一点是相同的,即在完成工艺要求的牵伸之后,在加捻之前,把从前罗拉钳口输出的较宽的纱条进行聚集,使得纱条宽度变的很窄,单纤维之间排列更加紧密,并且尽量保持在这种状态下进入加捻区。
虽然有的报道说是此举消灭了“加捻三角区”,但实际上纱条在加捻前后的宽度是不一样的。
所以,紧密纺的加捻罗拉钳口处仍然有一个极小的所谓“加捻三角区”,当然其危害性已降低到最小。
正是由于上述成纱机理,用紧密纺工艺纺成的细纱具有以下特点:1.由于在加捻前,纱条中单纤维充分伸直,相互平行,而且排列紧密,所以在加捻罗拉钳口处(也叫阻捻罗拉,因为其有阻止捻度传递的作用),纱条直径变得很小,所以基本消除了“加捻三角区”,由于加捻前单纤维充分伸直、平行,没有毛羽伸出纱条主体,所以成纱毛羽很少,特别是3毫米以上毛羽极少。
2.在细纱中由于各单纤维是在伸直、平行的状态下加捻,在单纱受到拉力时,各单纤维受力基本一致,所以紧密纺强力比传统单纱高。
而且由于紧密纱中的单纤维排列紧密,相互间抱合力大,这也有助于提高纱线的强力。
3.在紧密纺工艺中,纱条是在完成了工艺规定的牵伸之后再进行聚集,所以其条干不匀的指标没有大的改善,但在其聚集区有对纱条的整理作用,且在加捻罗拉钳口处加捻时纤维的内、外层转移没有传统工艺强烈,所以紧密纱的条干不匀,粗、细节指标比传统纱要好。
4.由于紧密纱的上述特点,为下道工序提供了非常好的条件,紧密纱毛羽少,所以减轻了上浆、烧毛等工序的压力,在无梭织机的纬纱使用紧密纱时大大减少了引纬的阻力,提高了织机效率。
5.由于紧密纱纤维排列紧密,和相同号数的传统纱线相比直径小,所以用相同经、纬密织成的布透气性好,布面平整、光滑,是高档纺织品的理想用纱。
赛络纺纱的纱线特点及产品开发
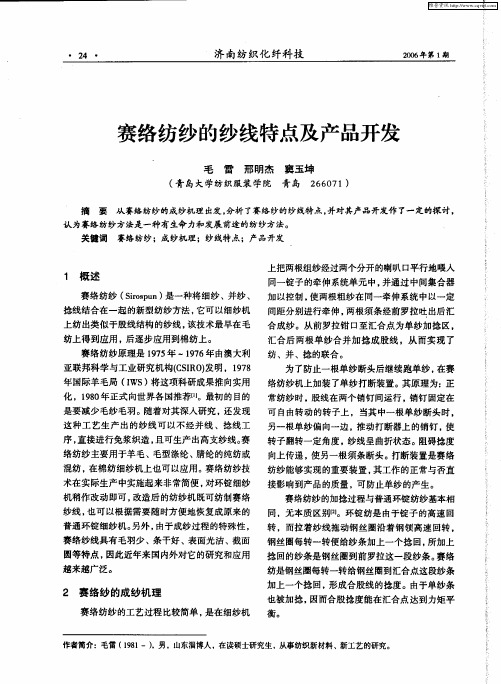
亚联邦科学与工业研究机构(SR ) C I O 发明 ,17 98 年国际羊毛局 (WS) I 将这项科研成果推 向实用
化 ,1 8 年正式 向世界各 国推荐【 90 l J 。最初 的目的
为了防止一根单纱断头后继续跑单纱 , 在赛
络纺纱机上加装了单纱打断装置。其原理为: 正
常纺纱时 , 股线在两个销钉问运行 。 销钉 固定在
纱的结构紧密 。 截面形状较圆。 表面毛羽少 , 纱 线较光洁 ;耐磨程度高。 33 强力较高 、耐磨程度好 -
5 结 语 5 赛络纺与常规的股线生产相 比, . 1 省去了单纱
络筒 、 并纱及捻线工序 , 节约了机器设备 , 相应 减少了占地面积和能量 消耗 , 因此 , 赛络纺纱方 法 以其技术实现 的简易性 、工艺流程 的简便性 、
维普资讯
.2 . 4
济 南纺 织化 纤科 技
26 0 年第1 0 期
赛络纺纱的纱线特点及产 品开发
毛 雷 邢明杰 窦玉坤 ( 岛 大学纺 织服 装 学 院 青 岛 2 6 7 ) 青 6 0 1
摘 要 从赛络纺纱的成纱机理 出发, 分析 了赛络纱的纱线特点, 并对其产品开发作了一定的探讨 , 赛络纺纱;成纱机理;纱线特点;产品开发 上把两根组纱经过两个分开的喇叭 口平行地喂人
2 赛 络纱 的成 纱机理
加上一个捻 回, 形成合股线 的捻度。由于单纱条
也被加捻 , 因而合股捻度能在汇合点达到力矩平
赛络纺纱 的工艺过程 比较简单 , 是在细纱机 衡 。
作者简介:毛雷 ( 9 1 。 18 一) 男,山东淄博人 , 在读硕士研究生 。 从事纺织新材料、新工艺的研究。
高支纱线的可纺性等特点 , 越来越受到纺织界的
- 1、下载文档前请自行甄别文档内容的完整性,平台不提供额外的编辑、内容补充、找答案等附加服务。
- 2、"仅部分预览"的文档,不可在线预览部分如存在完整性等问题,可反馈申请退款(可完整预览的文档不适用该条件!)。
- 3、如文档侵犯您的权益,请联系客服反馈,我们会尽快为您处理(人工客服工作时间:9:00-18:30)。
K e wo ds c t n c s m e e; sl /c s me e; p y ia p o e t s a ay i o c u e ; t e y r : ot / a h r o i k ah r h sc l r p ri ; n l ss f a s s e h
Ac o d n o t e a l ss,1 7 tx ×2 sl /c s me e 8 /1 io s u anss a e l b e y p p a c r i g t h nay i 6. e i k a h r 5 5 sr -p n y r we trwil e v r o ulr
毛 纺 科 技
一
第4 O卷
第 1 0期
1 一 0
W O lTe tl o r a O x i J u n l e
21 0 2年 1 0月
赛 络纺 丝/ 纱 线 与 环锭 纺棉/ 纱线 绒 绒 质 优 势 分 析及 探 讨 量
刘 月玲
( 原 理 工 大 学轻 纺 工 程 与 美 术 学 院 , 西 榆 次 太 山 000 ) 3 6 0
sr n t te gh,h ii e s t s , b a in r ssa e we e t se a d c n r se a h o h r Th rs l ho d a rn s ,wit a r so e itnc r e td n o ta td e c t e . e e u t s we t a h r p ri s o ik a h r io-p n y r s we e s pe irt h s f c to / a h e e rn —p n h tt e p o ete fsl /c s me e sr - u a n r u ro o t o e o ot n c s m r i g- u s s y r s 1 7 tx ×2 sl/c s m e e 8 /1 sr -p ans c n b e o e hg g a e k ti g fb i . a n . 6. e ik a h r 5 5 io s un y r a e us d m r ih—r d ni n a rc t
t c n l g fs i ni g e h o o y o p n n
LI Yu ・i g U e ln
( olg fLg t n et eE gn ei ga d Ar T iu n Unv ri f C l e o ih d T xi n ie r n t, ay a iest o e a l n y
T cn l y Y c 0 0 0 , hn )Байду номын сангаасeh oo , u i 3 6 0 C ia g
果 表 明 : 络 纺 丝 / 纱线 的所 有测 试 性 能均 优 于 环 锭 纺 棉/ 纱 线 。 1. e 赛 绒 绒 67txx 2丝/ 8 / 5赛 络 混 纺 纱 线 可 用 绒 51 于生产高档针织面料 , 针织衫预计会受到消费者的青睐。 其
关 键 词 : / ; / ; 理 性 能 ; 因分 析 ; 纱 工 艺 棉 绒 丝 绒 物 原 纺
摘
要 : 究 赛 络 纺 丝 / 纱线 与环 锭纺 棉 / 纱 线 的 主 要 性 能 质 量 指 标 , 讨 新 型 纺 纱 与 传 统 纺 纱 工 艺 及 设 研 绒 绒 探
备, 以及 不 同纤 维 材 料 对 纱 线 质 量 的 影 响 。测 试 并 对 比 了 2种 纱线 的 条 干 均 匀 度 、 度 、 羽 数 、 度 、 磨 性 。结 强 毛 捻 耐
q a i fsr p n i g a d ta i o a p n i g tc n lg n i e e tfb rma e il. Ya n e e n s u lt o io s i n n n r dt n ls i n n e h o o y a d df r n e tras y i f i r v n e s,
Absr c s:M an p o e t fsl /c s me e sr —p ansa d t e c t n c s ta t i r p ry o i k a h r io s un y r n h ot / a hme ern —p n y r s o r i g s u a n we e su e r tdid. Th p r o e f t e r s n t y wa o x lr t e fc o s t t n u n e n t e a ns e u p s o h p e e t sud s t e p o e h a tr ha if e c o h y r l
中 图分 类 号 :S0 . 1 T 14 5
文 献标 识码 : A
文 章 编 粤 :0 315 《0 2 1 -000 10 — 6 2 1 )00 1-3 4
An l ss a s u so n t ua iy s pe i r t f sl / a hm e e a y i nd dic s i n o he q lt u ro iy o ik c s r sr s un y r s a h o t n a h e e r n s n y r s i o-p a n nd t e c to /c s m r i g-pu a n