阻焊工序检验规范
电阻焊工艺规范和质量控制

1、目的为了为规范电阻焊作业的产品符合图纸的技术条件和要求,以提高产品质量。
2、范围公司范围内所有电阻焊设备的使用及产品的检验。
3、规范性引用文件3.1 GB/T 19867.5 电阻焊焊接工艺规程3.2 ISO 10447:2007 焊接.点焊.凸焊和有缝焊的剥离和凿剥离试验4、电阻点焊工艺规范4.1 电极尺寸及焊接规范电极压力与气压及焊钳结构等有关,表1中电极压力可供焊钳选型和参数设置时参考。
电极压力由压力计进行测得,通过改变限压阀的输出气压值改变电极压力的输出值(电极压力值可由焊接压力值和气压值用正比关系求得)。
4.2 焊前准备4.2.1表面清理、对焊接部位去油、去污、除锈等处理;a)设备操作:首先打开冷却水路,再打开焊机电源开关进行预热,检查水、电、气等是否正常;b)电极是否更换或已经修复并且符合标准,参考表1;c)检查气压是否正常,气管、电缆、绝缘防护等是否良好;d )以下几种情况需重新确定焊接规范,工艺验证合格后,方可进行焊接:——对于新购置的、停用3个月以上的、故障排除后的焊机;——板材的材质、厚度发生变化;——出现焊接质量问题时。
5点焊焊接强度检验及质量控制5.1 焊点质量接收准则5.1.1 焊点尺寸一个焊点其熔核尺寸应该大于或等于表2相应数值才是可接受的,实际尺寸小于规定值则被判定为不合格。
表2 焊点熔核尺寸5.1.2 熔核尺寸的计算和测量熔核为焊点的部分,包括整个或部分熔核,会在破坏试验中撕裂而得到,熔核的直径由长轴测量数值加上与长轴垂直轴的测量数值再除以2计算得到,测量数据要在接触面上测量得到,图1为熔核尺寸计算方法,图2为量具测量方法。
图 1 熔核尺寸的计算注:1为带刃口的检测量具a )金相检验参考图示图2 熔核尺寸的测量5.1.3 裂缝周边有裂缝的焊点是不合格的焊点,由电极留在表面的压痕区域内的裂缝是允许的。
5.1.4 孔含孔的点且由各种原因被击穿的视为不合格。
5.1.4 焊接区域点焊区域为电极焊接后压痕所在区域,点焊区域应该包含在金属边缘之内,否则视为不合格, 如图3所示:图3 焊接区域极限5.1.5 位置公差按照工艺文件中内容焊点位置进行焊接须在偏差0.3mm 范围以内,超出则视为不合格。
焊接质量检验标准

精心整理
焊接质量检验标准
1.目的
通过正确定义焊接质量的检验标准,保证员工在焊接、检验过程中制造出合格的产品。
2.范围
适用于焊接车间。
3.工作程序
焊接质量标准根据生产制造现场工艺实际情况,可采用边界样本目视化来清楚地分辨出焊接质量是否符合要求。
3.1
3.1.1以下3.1.1.13.1.1.23.1.1.3
3.1.1.4
3.1.1.5位置偏差的焊点(与标准焊点位置的距离超过10mm ),代号P 。
3.1.1.6钢板变形超过25度的焊点,代号为D 。
3.1.1.7压痕过深的焊点(材料厚度减少50%),代号为I 。
3.1.1.8漏焊,代号为M 。
3.1.2以下10种CO 2气体保护焊焊点、焊缝被认为是不可接受的,界定为不合格质量: 3.1.2.2焊缝金属裂纹;
3.1.2.2夹杂(焊缝中夹杂着除母材和焊丝外的物质或氧化物); 3.1.2.3气孔(焊逢中产生气孔); 3.1.2.4咬边;
未焊透;
熔透过大;
3.1.2.9飞溅。
阻焊工序检验规范

阻焊工序检验规范1.0目的制定阻焊工序的检验方法和允收标准,使检验工作有章可循,有据可依。
2.0检验方式2. 1首件检查:针对阻焊显影后必须做首件检查.2. 2检查频率: 检验员在阻焊显影后针对当班所生产的每一款新型号板/工具更改/工艺变更后的板须进行首件确认(包括上一班首件OK的板和各套生产film所生产的板);2.3 阻焊全检:阻焊QC对阻焊显影后的板做全检检查。
2. 4过程抽检:针对阻焊显影后必须做抽检检查.3.0检验工具MI/制造流程卡(LOT卡)﹑10倍放大镜﹑3M胶带﹑光台﹑锡炉4.0检验项目4.1 阻焊油墨的型号与颜色;4.2 板表面的阻焊印刷质量;4.3 板表面以及孔内的阻焊显影质量;4.4 板面阻焊的耐热冲击测试;4.5 板子与film之间的对准度情况;4.6 板面阻焊的硬度测试;4.7 板面的油墨厚度控制;5.0缺陷名称油墨用错﹑油墨入孔﹑油墨上盘﹑漏印、露铜、露线、阻焊垃圾/杂物、手指印、龟裂、聚油、阻焊塞孔﹑显影过度﹑显影不净﹑阻焊气泡﹑阻焊脱落﹑菲林对反﹑菲林划伤﹑周期错误﹑UL标志错误、烤板过度等6.0检验步骤6.1检验前,检验员须准备好10倍放大镜﹑3M胶带等相关的检验工序并放置在检验台面上;6.2.检验时,检验员须戴干净的白手套,并根据首检记录报表上的检验项目逐项进行检验;6.3首检任何送给当站检验人员进行检验的首件板,必须是有经过操作人员进行自检,且自检合格后的板,否则当站检验人员有权拒检,同时,针对此工序的板,操作员在通知检验人员进行首检时,必须准备好相应的LOT卡并放置于待检板的旁边,否则当站检验人员有权进行6.3.1针对于任何一款板,在阻焊显影之后,操作人员须将前三片的首件板单独放置在显影机附近,并准备好相应的LOT卡,同时通知当站检验人员取板进行首检作业;6.3.2检验人员须检查前一站的检验人员是否有在LOT卡的相应位置上进行签卡确认,如有则进入下一步的检验工作;如上一站的检验人员并未在LOT卡的相应位置上进行签卡确认,则当站检验人员有权进行拒检首件板,同时将此信息立即向生产以及本部门的技工以上人员进行反馈,以使问题能够得到及时的处理,并在处理后,得到本部门技工以上人员通知的情况下进行相应的检验;6.3.2.1检验人员须认真检查板边处的板型号﹑版本号与LOT卡上的工具型号以及版本号是否一致;6.3.2.2检查板子的生产工艺流程是否与LOT卡上的工艺流程一致,是否有走错工序;6.3.2.3检查板面的油墨型号﹑颜色是否与LOT卡上的要求一致;6.3.2.4检查板面的阻焊生产周期与UL标志是否与LOT卡上的要求一致;6.3.2.5在光台上检查生产Film与板子图形之间的对准度,以确定是否有因对位偏而造成的绿油压盘上PAD/IC/邦定位置;6.3.2.6在光台上检查板面是否有显影不干净/显影过度;6.3.2.7在光台上检查板面是否有阻焊下垃圾/杂物;6.3.2.8在光台上检查组件孔内是否残留有阻焊油墨未显影干净;6.3.3所有的检验项目均检验合格后,检验员须做好相关的首检质量记录报表,同时通知生产部操作人员可以进入到批量生产,如首检不合格,也同样须要通知到生产部操作人员,以便于操作人员及时改善,并由阻焊工序技工以上人员在相关的检验记录上签名确认,同时在改善后重新进行首板检验直至合格为止;6.3.4针对于生产过程中的板,检验员须严格按照抽检要求进行抽检,如抽检合格,则在LOT卡上的相应位置签名确认,如不合格,则必须及时的对已生产出来的板子作质量处理要求(如﹕修理﹑返工),直至合格为止,同时须通知阻焊工序技工以上人员在相关的检验记录上进行签名确认;如与生产人员在处理的方式与结论上存在分岐,不允许检验人员自作主张进行处理,而必须上报至本部门的技工以上人员处理;6.3.5对于客户特殊要求的板,IPQA必须取1-2PCS样品送至物理实验室进行有关的性能检测;若需做阻焊硬度、耐热冲击性能检测的必须经高温固化之后进行检测。
电阻焊焊点质量检验流程

……………………………………………………………最新资料推荐…………………………………………………点焊检验电阻焊的问题之一是没有适当的无损检验方法。
因此,在实际生产中,经常采用过程控制、外观和非破坏性的强度检验、焊点破坏性试验等来保证点焊接头的质量。
虽然外观和非破坏性的牢度检验并不可靠,但因其简单易行,也可以发现诸多焊接质量问题,因此在实际生产和质量控制过程中应用最广。
为了比较准确地判断焊接质量是否合格,进行焊接接头的破坏性试验是必要的。
焊接接头的破坏性试验方法,有机械试验法、现场试验法和金相检验法等,前者使用机械性能试验机测定拉剪、拉开、压缩、扭转、冲击等性能,而剥离、压缩、扭转、旋绞等是不使用试验机的现场试验法。
机械试验法的缺点是用适当形状的试件,并要把试件夹持在试验机的一定位置上,其优点是能够显示出性能数值。
与此相反,现场试验法的优点是操作非常简单,快速而成本低,其缺点是只能是定性检验,大部分不能显示性能数值,而且试验条件也不恒定。
金相检验则用来测定熔核尺寸和鉴定焊接缺陷。
一、点焊主要缺陷及可能原因接头外部或内部缺陷是评定点焊接头质量的另一重要指标。
点焊缺陷分表面缺陷及内部缺陷(未焊透、不穿透裂纹、缩孔等)。
表面缺陷可以通过外部观察发现,内部缺陷则较难发现。
点焊最危险的缺陷是未焊透(熔核未形成或尺寸太小),使接头强度剧烈下降。
一般点焊缺陷的类别及其产生原因见表所示2-6。
表2-6点焊缺陷的类别及其产生原因缺陷类别简图缺陷对焊接质量的影响缺陷主要产生原因1.未焊透强度小,不稳定、1.焊接电流小(电路故障,流等)(1)没有熔核2.焊接时间不够(2)焊核尺寸焊接接头发脆3.焊件电阻减小(电极压力很小过大)4.电极工作表面尺寸过大2.外部飞溅零件表面烧坏1. 零件清理不好,或者由于过脏2. 压力太小3. 焊接电流过大、时间过长3.内部飞溅增加零件表面凹陷和增加焊核疏松;飞溅很大时,形成焊核空洞,强度急剧下降。
焊接质量检验标准.

XX 机械制造有限公司
焊接质量检验标准
1.目的
通过正确定义焊接质量的检验标准,保证员工在焊接、检验过程中制造出合格的产品。
2.范围
适用于焊接车间。
3.工作程序
焊接质量标准根据生产制造现场工艺实际情况,可采用边界样本目视化来清楚地分辨出焊接质量是否符合要求。
3.1电阻点焊焊点不合格质量的界定和CO 2气体保护焊焊点、焊缝不合格质量的界定。
3.1.1以下8 种电阻焊点被认为是不可接受的,界定为不合格质量: 3.1.1.1虚焊(无熔核或者熔核的尺寸小于4mm )焊点,代号为L 。
3.1.1.2沿着焊点周围有裂纹的焊点,代号为C 。
3.1.1.3烧穿,代号为B 。
3.1.1.4
3.1.1.5
3.1.1.6钢板变形超过25度的焊点,代号为D
3.1.1.7压痕过深的焊点(材料厚度减少50%),代号为I 。
3.1.1.8漏焊,代号为M 。
3.1.2以下10种CO 2气体保护焊焊点、焊缝被认为是不可接受的,界定为不合格质量: 3.1.2.2焊缝金属裂纹;
3.1.2.2夹杂(焊缝中夹杂着除母材和焊丝外的物质或氧化物); 3.1.2.3气孔(焊逢中产生气孔); 3.1.2.4咬边;
缺陷B :烧穿
3.1.2.5未熔合;
3.1.2.9飞溅。
飞溅,焊缝堆积过高,焊缝不连续
3.1.3
以下4个凸点焊螺母的焊接质量是3个是可接受的,
1个是不可接受的。
阻焊工序检验标准

页码﹕第1页,共 6页文件名称阻焊工序检验标准缺陷名称图例或说明允收标准检验工具和检验方式油墨用错油墨类型用错不论出于何种板上﹐均为严重的不合格﹐必须作拒收返工处理﹔油墨颜色用错不论出于何种板上﹐均为严重的不合格﹐必须作拒收返工处理.不接受目视绿油入孔1.阻焊油墨入组件孔时﹐必须作拒收处理﹔2.阻焊油墨入导通孔时﹐在客户没有特殊要求的情况下一般作接收处理﹔ 3.阻焊油墨入NPTH孔时﹐孔壁油墨的入孔高度不得影响到最小孔径公差的要求﹐否则作拒收4.如果组件孔在制作的过程中属于阻焊Film 单面开窗时﹐在开窗面允许有油墨入孔﹐但入孔面积必须≦孔壁面积的20%﹐同时﹐油墨附在孔壁的高度不得影响到最小孔径公差的要求﹐否则作拒收.目视+针规油墨上焊盘1.如属于过孔与PAD之间的间距过小(即过孔与PAD之间无单独的导线相接﹐而直接设计在一起)所产生的局部阻焊油墨上PAD 时﹐若局部阻焊油墨上PAD的宽度不超过0.2mm 可接收﹐否则作拒收;2.如属于对位时的对准度不够﹐所导致的阻焊油墨上PAD 时﹕2.1.组件面的圆形焊垫如果局部上PAD 宽度在0.1mm 以内时﹐可接收﹔ 2.2. 焊接面的圆形焊垫如果出现局部上PAD时, 不论上PAD 的宽度为多少﹐均不可接收﹔2.3. IC 脚﹑邦定脚﹑BGA 位置不论是处理哪一面出现油墨上PAD﹐同时不论上PAD 的宽度为多少﹐均不可接收﹔2.4. 方形的表面贴装PAD﹐不论绿油上PAD 在哪一面﹐如果上PAD 的宽度不超过0.05mm,可接收, 否则作拒收.目视+100倍放大镜页码﹕第2页,共 6页文件名称阻焊工序检验标准缺陷名称图例或说明允收标准检验工具和检验方式渗油渗入部分未超过焊接面的1/5目视+100倍镜露铜印刷过程中﹐出现油薄或不下油当线路与过孔的表面出现假性露铜时﹐应以线路的表面或过孔的表面不出现漏电为准.如果有明显的油墨偏薄,要求重工或拒收。
目视导线露线当PAD 与邻近导线之间的距离≦1mm,导线表面出现面积≦0.1mm2的星点状露线时,每面允许接收4点,否则须作拒收补油处理;相邻的两条并行线导线之间,如果在同一位置出现露线时,不论露线部份的面积为多少,均不允许作接收﹔如果在非同一位置出现露线时﹐露线面积≦0.1mm2,每面允许接收4 点,否则作拒收补油处理.目视+100倍镜阻焊垃圾/杂物当阻焊底层出现垃圾/杂物时﹐如符合以下条件﹐则可作接收﹕a. 阻焊底层的垃圾/杂物应为非导电物质;b. 阻焊底层的垃圾/杂物长度不得超过0.5×5mm﹐且每面最多不超过4 点;c. 阻焊底层的垃圾/杂物不得从PAD 的表面跨越;目视阻焊底层氧化/手指印阻焊底层氧化/手指印a. 阻焊底层点状氧化﹐面积在0.2×0.2mm2以内﹐且经过3M 胶带试拉不掉阻焊膜﹐每面允许接b. 阻焊底层大面积氧化不可接收﹔c. 阻焊底层或表面出现手指印痕迹时不可接收。
WI-B0-004焊接工序品质检验规范与检验标准

5.2无漏焊、错焊、虚焊、部件错位焊、汽泡焊,气孔直径小于1.5mm,超过1.5mm者补孔处理;
5.3焊点符合平整度,无大面积堆积焊,焊渣过多;
5.4焊疤面积符合生产工艺要求,并保证固度,焊点突出不大于2mm。
5.5试装配性能良好。
5.6缺点等级划分
主要缺点
次要缺点
1、目的:
为确保焊接工序的产品符合本公司之品质要求,特制定本检验规范作为检验依据对焊接工序产品进行质量检验,以确保品质并防止不合格品流入下一道工序。
2、范围:ห้องสมุดไป่ตู้
本标准适用于超杰生产的所有焊接工序的产品质量检验及判定。
3、职责:
制程(金工)品管员负责按照本标准对焊接工序产品进行检验。
4、定义:。
5、作业标准:
6、参考文件或标准:
引用GB/T2828.1-2012
7、附件:
《WI-C7-003AQL抽样方案表(GB2828-2012)》
8、相关记录:
8.1《首件标签》保存期当天
8.2《巡检日报表》保存期3年
点焊部件不符合生产工艺要求;漏焊,错焊,虚焊,错位焊,汽泡焊,堆积焊,焊渣过多、焊点突出高度大于2mm,。
焊渣至少,焊点平面等于或不大于3mm,稍有气泡经打磨后无明显蜂窝状。
5.7处理方法:
5.7.1尺寸测量、破坏性测试按特殊抽样水平S-1抽样;其它按正常检验水平Ⅱ抽样
5.7.2检验的焊接产品缺点等级在标准以内的判定为合格批,超出标准的判定为不合格批,不合格按《不合格控制程序》执行。
焊接质量检验规范标准(配大量图片)
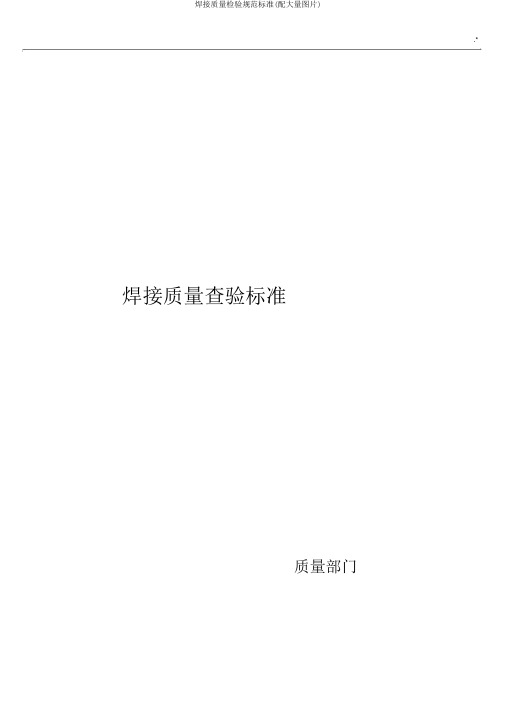
.*焊接质量查验标准质量部门1.目的经过正确立义焊接质量的查验标准,保证职工在焊接、查验过程中制造出合格的产品。
2.范围合用于焊接车间。
3.工作程序焊接质量标准依据生产制造现场工艺实质状况,可采纳界限样本目视化来清楚地分辨出焊接质量能否切合要求。
3.1 电阻点焊焊点不合格质量的界定和CO2气体保护焊焊点、焊缝不合格质量的界定。
以下8种电阻焊点被以为是不行接受的,界定为不合格质量:虚焊(无熔核或许熔核的尺寸小于4mm)焊点,代号为L。
(一)焊接不良术语焊接缺点无效模式无效危害无效原由解决方法焊接件坡口尺寸不妥焊缝形成不良,余高影响外观过高或过低焊接电流太大焊接尺寸不对焊接电流太小焊脚尺寸不切合要求焊接速度和运条方法不当,焊条角度不对以致焊接构造破焊接构造设计不合理坏构造刚性太大焊接接头局部开裂所裂纹产生的空隙焊接工艺参数选择不合最危险的缺点,决理不同意存在焊接工艺参数选择不合理焊接后焊趾的母材部减小了基本金属焊接电流过大的有效截面积,应咬边位产生纵向沟槽或凹力集中在咬边处,焊接速度或运条不妥,电陷易造成构造破弧过长不同意的缺点,降焊接电流太小,焊接速度太快低焊缝强度,惹起未焊透接头根部未完整融透裂纹产生,以致结坡吵嘴度,接头空隙太构损坏小,钝边太厚焊口及母材焊道未清理焊接后的熔渣夹在焊降低焊缝强度,引洁净夹渣焊接电流太小,熔池金属缝里起裂纹产生凝结太快,熔渣来不及浮出来焊接金属熔渣滴到焊影响焊缝成型,导电流太大,电弧太长焊瘤缝外未熔的母材上致裂纹运条方法不妥,焊接速度太慢气孔熔池中的气泡在凝结造成焊缝有效截焊条烘干温度不够,或许时未能逸出,残留在面积减小,降低焊焊道中残留油、水等杂质超出限度的咬边要进行补焊.*焊缝内形成空穴缝力学性能电弧保护不够:如焊条药皮无效;室外有风作业焊接金属从焊缝母材焊接电流太大,焊缝坡口补焊空隙太大烧穿坡口反面流出,形成不同意出现焊接速度太慢,电弧逗留穿孔性缺点从头打坡口焊接时间过长(二)焊接专业术语1.极性:直流电弧焊或电弧切割时,焊件与焊接电源输出正直、负极的接法称为极性。
电阻焊检验标准-BT SGMWJ 0401-2008

电阻焊检验标准-BT SGMWJ 0401-2008 电阻焊检验准及返修流程1 范围本标准适用于含碳量在0.25%以下的汽车用低碳钢板(0.8、08AL、10、20、Q215A、Q235A等)、低合金高强钢板及镀层钢板(镀锌、镀铝)的点焊。
2 缺陷分类2.1 影响焊点合格性的缺陷.任何出现以下缺陷的焊点为不合格焊点,焊接工艺必须调整到原设定的合理值以消除产生缺陷的原因。
2.1.1 裂纹.不借助放大镜就可见到表面裂纹的焊点为不合格焊点,见图4。
2.1.2 孔.出现贯穿孔的焊点为不合格焊点,见图8。
2.1.3 边缘焊点.由电极压痕产生的点焊印不能完全被零件边包容的焊点为不合格焊点,见图6中的 E和F。
2.1.4 漏焊.当实际焊点少于焊接文件规定的焊点时,漏焊的焊点为不合格焊点。
2.1.5 虚焊. 通过凿子、探测或破坏试验发现在焊接区没有形成焊接扣或焊接区截面无熔核形成称为虚焊,虚焊为不合格焊点。
2.1.6 焊点位置. 焊点必须落在设计位置并满足下列要求。
? 对有明显产品特征供目视参考的单排焊点样式,端部焊点位于设计位置10mm 半径范围外为不合格焊点(明显的产品特征必须是可见的切边或其它可辨认的产品特征,且垂直或近似垂直于焊点连线,距端部焊点30mm以内),见图1.? 对其它焊点,位于设计位置20mm半径范围外为不合格焊点,见图1.? 在某一焊点样式中(包括单排焊点),假如相邻焊点的间距超出设计间距20mm,偏离设计位置最远的焊点为不合格焊点。
焊点位置允许范围注:为焊点理论位置图1:焊点位置MAY 2008 SGMW - 1 -/ 10电阻焊检验准及返修流程2.1.7 最小焊点尺寸焊点尺寸既可以通过焊接扣(图10)也可以通过焊接熔核(图13)来测量,表1所列的最小焊点尺寸是基于主导板厚方根的4倍这一公式得到的,主导板厚的单位为毫米。
当焊点尺寸小于表1所规定的最小尺寸,则焊点为不合格焊点。
表1:最小焊点尺寸主导板厚(mm) 最小焊点尺寸(mm)0.65-1.29 4.01.30-1.89 5.01.90-2.59 6.02.60-3.25 7.0并非所有钢材或破坏试验方式都会得到焊接扣,在这种情况下需利用冶金学检验来确定焊点尺寸。
焊接质量判定标准

焊接质量判定标准编制:审核:批准:生效日期:受控标识处:分发号:发布日期:2012年6月28日实施日期:2012年6月28日1.0 目的为满足焊接质量检查需要,制定本标准。
本标准规定了电阻焊、二氧化碳气体保护焊焊接质量检验的标准。
2.0 适用范围适用于焊接车间焊接质量控制。
3.0 引用标准GM4488M《AUTOMOTIVE RESISTANCE SPOT WELDS-STEEL》4.0 定义4.1 焊接强度:是指对焊缝(熔核)及其周围母材热影响区组织的抗拉性能和屈服性能的可靠性评价。
4.2 破坏检验:指将工具插入焊接部件直到零部件彻底分离,通过检查焊缝尺寸大小,以确定焊缝的可靠性。
4.3 直观检查:是指通过目视观察的方法,检查焊缝的数量、位置和外观成型质量。
4.4无损凿试:指将凿子敲入(或敲击)焊接工件,当整个工件变形达到焊点拉长而焊缝无断裂或损坏的一种试验方法。
5.0 电阻焊5.1 焊接类型一个焊点类型是指将两个零件焊在一起的一行,一列或一组焊点,如改变了零件组合(如在同一行,同一列,同一组中有两层和三层组合情况),那么将视为不同类型。
如果一行,一列或一组焊点组合被另一类型或无焊接区打断,则应视为两个或更多的类型。
5.2 点焊的划分分关键焊点、一般焊点两类。
5.2.1关键焊点:其适用于对整车功能有很大影响或极易造成整车结构性破坏的分总成件。
关键焊点要求100%合格。
5.2.2一般焊点:适用于对整车性能没有影响或不会整车结构性破坏的分总成件。
主要是为了改善用户的乘坐舒适性。
5.3 外观质量以下10种焊点被认为是不可接受焊点:5.3.1虚焊(代号L)无熔核或熔核尺寸小于表中规定尺寸的焊点。
焊点直径定义为垂直两方向直径的平均值。
焊点直径= (D+d)/2合格焊点应满足:焊点直径=(D+d)/2≥dmin;若焊点直径(D+d)/2<dmin,则称此焊点为虚焊。
合格焊点的测量尺寸应大于等于下表所列值,否则不合格。
电阻焊检测标准

电阻焊检测标准电阻焊检测标准一、焊接接头的几何尺寸1.焊接接头的长度和宽度应符合设计要求。
2.焊接接头的对角线偏差应不大于0.5mm。
3.焊接接头的表面应平整,无凹凸不平现象。
4.焊接接头的倾斜度应符合设计要求。
二、焊接接头的强度1.焊接接头应能承受规定的拉伸、压缩和剪切负荷。
2.在最大负荷下,焊接接头不应出现断裂、过度变形或其他破损现象。
3.在疲劳载荷下,焊接接头应具有良好的耐疲劳性能。
三、焊接接头的塑性1.焊接接头应具有良好的塑性,能够吸收冲击载荷和弯曲载荷的影响。
2.在弯曲试验中,焊接接头不应出现断裂、过度变形或其他破损现象。
四、焊接接头的金相组织1.焊接接头的金相组织应符合相关标准要求。
2.焊接接头的晶粒度应均匀,无晶粒粗大现象。
五、焊接接头的无损检测1.焊接接头应采用无损检测方法进行检测,确保其内部质量。
2.无损检测方法包括射线检测、超声检测、磁粉检测等。
3.在无损检测中,应严格按照相关标准执行,确保检测的准确性和可靠性。
六、焊接接头的耐腐蚀性1.焊接接头应具有良好的耐腐蚀性,能够承受各种腐蚀环境的影响。
2.在腐蚀试验中,焊接接头不应出现明显的腐蚀现象。
七、焊接接头的疲劳性能1.焊接接头应具有良好的疲劳性能,能够在交变载荷作用下保持其强度和稳定性。
2.在疲劳试验中,焊接接头不应出现断裂、过度变形或其他破损现象。
八、焊接接头的断裂韧性1.焊接接头应具有良好的断裂韧性,能够在冲击载荷作用下保持其完整性。
2.在断裂韧性试验中,焊接接头不应出现断裂、过度变形或其他破损现象。
九、焊接接头的尺寸公差1.焊接接头的尺寸公差应符合相关标准要求。
2.在加工过程中,应采用正确的加工方法和工具,确保焊接接头的尺寸精度和一致性。
十、焊接接头的外观质量1.焊接接头的外观质量应符合设计要求和相关标准规定。
2.焊接接头的表面应光滑、平整,无气孔、焊瘤和其他缺陷。
阻焊制作工艺流程及检验标准

h.檢驗
對顯影出來的板進行檢驗。
i.固化
使用烤箱烘烤已檢驗合格的板﹐進行熱固化.
j.阻焊完成品
2.阻焊檢驗標准
氣泡
油墨起皺
不允許油墨氣泡及油墨起皺。
絲印不良﹕油墨不均
絲印不良﹕漏 印
不允許油墨不均及油墨漏印。
阻焊對偏
阻焊對偏需符合單邊最小焊盤在0.05mm以上可允收
阻焊對偏﹕綠油上BGA
曝光不良﹕油墨被曝死
不允許曝光不良。
油墨進孔
不允許油墨進孔。
綠油上PAD
不允許綠油上PAD.
刮傷露銅
不允許刮傷露銅。
補油不良
補油允許每單元每面不超過3處﹐兩面不超過5處﹐每 處面積不能超過5mm× 5mm﹐補油處需平整﹐無色差。
阻焊顏色不一致
阻焊顏色需與MI上要求一致﹔ 固化后阻焊顏色需一致。
阻焊制作工藝流程Biblioteka 檢驗標准制作﹕朱新軍 制作日期﹕2009-08-24
1.阻焊制作工藝流程
a.磨板
磨板前板面
磨板后板面
清洗板面髒污氧化物及粗化板面, 以增強阻焊油與板面的附著力.
b.阻焊印刷
阻焊網版 阻焊印刷前板面
網版
阻焊印刷后板面 釘床
依照客戶要求之阻焊顏色﹐ 將感光防焊油墨印在板面上。
c.靜置
5.檢驗報表填寫
6﹑注意事項
• a.拿板 時雙 手要 戴手 套﹐ 兩手 必須 持板 邊緣。
• b.取放 板時禁 止板與 板、板 與台面 相互摩 擦﹐板 與板之 間不可 重疊放 置﹐以 減少擦 花。
• c.不能私自操作生產設備﹔
不允許綠油上PAD及上BGA.
綠油下氧 化
不允許有綠油下氧化。
电阻焊检查标准

E 001-05电阻焊检查标准1.概述此项标准明确了强度等级260~980且厚度不大于4.0(*1)的钢板点焊(包括连续缝焊和滚动焊)的外观检查方法及标准,也适用于强度等级在260~270(*2)的普碳钢板的凸焊和缝焊。
备注:(*1)汽车用热轧钢板及带钢参照C 051,汽车用冷扎钢板及带钢参照C 052,汽车用热浸镀锌钢板及带钢参照 C 071。
(*2)该标准适用于含碳量<0.15%的普碳钢,包括表面处理钢板,例如镀锌钢板和防锈钢板。
说明:此标准中采用的单位和数值的表示方法参照的是国际单位体系(),用{}特殊标注的数值是指经验值。
2.分类及标注方法每个组成部件和分总称分为A、B、C三个强度等级和a、b、c三个外观等级,该标准应该在接收标准,量产检查标准、以及作业标准中明确。
2.1强度等级分类完成车以及零部件根据结构强度分为A、B、C三个等级。
2.2外观等级分类完成车中对外观有要求的部分分成如表1所示的三个等级。
2.3标准方法当对强度和外观都有等级要求时,分类及标注方法如表2所示。
如果不要求标注外观等级,则应该仅对强度进行标注。
但是,在这种情况下对外部缺陷的要求应参照4.3部分。
3.试片3.1点焊试片点焊试片参照标注Z 3136。
3.2凸焊试片用于断面检查的试片应该使用产品的形状,用于剪切应力检查的试片应该采用图1所示的形状,凸焊的各个尺寸要求参照 A 1018。
表3备注:1.上图是一个环形焊缝的例子。
检测时必须在试片上固定一个支撑(图中阴影部分所使用的材料及厚度需要可以抵抗所施加的拉力)。
固定时需要注意固定的位置及方法(如果采用点焊固定,就要注意由于焊接热应力产生的扭曲)。
2.当不同板厚和材质的板材结合时,试片的尺寸标准应该以(材料强度)×(板厚)值较小的板材为参照。
如果为三层板或者是多层板结合,试片的尺寸标准应参照两个承载的板材。
3.3缝焊试片试片的形状如图1所示,沿着标记线进行切割。
电阻焊质量管理与检验

电阻焊质量管理与检验1. 引言电阻焊是一种常见的焊接方法,广泛应用于电子电气行业中。
电阻焊质量管理和检验对于确保焊接连接的强度和稳定性至关重要。
本文将介绍电阻焊质量管理的重要性以及常见的检验方法和指标。
2. 电阻焊质量管理电阻焊质量管理是通过控制焊接过程中的关键参数和采用适当的工艺措施,以确保焊接质量符合要求。
以下是一些常见的电阻焊质量管理措施:•选择合适的焊接设备和工具:根据工件的材质和规格,选择合适的焊接设备和工具,以确保焊接能够达到设计要求。
•设定合理的焊接参数:包括焊接时间、电流和压力等参数的设定。
合理的参数设定能够确保焊接过程中的热量和压力均匀分布,避免焊接过程中的热变形和焊接强度不均匀的问题。
•焊接材料的选择:选择合适的焊接材料,包括焊丝和焊接剂等。
焊接材料应具有良好的焊接性能和耐腐蚀性能,以确保焊接质量的稳定。
•对焊接操作者进行培训和管理:培训焊接操作者的技能和知识,确保其能够正确操作焊接设备和工具,遵守焊接工艺规范。
3. 电阻焊质量检验电阻焊质量检验是在焊接完成后,通过一系列的检测和测试手段,评价焊接质量的好坏。
以下是一些常见的电阻焊质量检验方法和指标:•视觉检查:通过目视观察焊接接头的外观和形状,检查是否存在焊结跳线、气孔、裂纹等缺陷。
•金相检验:将焊接接头切割成薄片,经过抛光和酸蚀处理后,使用金相显微镜观察焊道的显微组织结构,评估焊接质量。
•强度测试:使用拉伸试验机对焊接接头进行拉伸力测试,评估焊接接头的强度和韧性。
•电阻测试:使用电阻测试仪测量焊接接头的电阻值,以判断焊接接头的质量。
合格的焊接接头应具有稳定的电阻值。
4. 电阻焊质量管理案例分析以下是一个简单的案例分析,通过电阻焊质量管理手段,提高焊接质量的稳定性:•问题描述:某电子产品生产线上,焊接接头的质量不稳定,经常出现焊结不牢固的情况,导致产品的性能和可靠性下降。
•管理措施:通过培训焊接操作者,提高其操作技能和焊接工艺的规范性。
电阻焊质量管理与检验

电阻焊质量管理与检验现代电阻焊技术可以得到高质量焊接接头。
但由于电阻焊过程中受众多偶然因素的干扰(表面状况不良、电极磨损、装配间隙的变化、分流等工艺因素的随机波动、焊接参数的波动……),要想杜绝生产中个别接头质量的降低、废品的出现还是有困难的。
因此,必须对电阻焊产品的生产全过程进行监督和检验,保证其在规定的使用期限内可靠地工作,不致因焊接质量不良导致产品丧失全部或部分工作能力。
一、电阻焊的全面质量管理电阻焊全面质量管理的主要任务是预防和及时发现焊接缺陷,确定焊接接头质量等级,保持所有生产因素的稳定性,并保证获得高而稳定的产品质量。
质量管理内容如图1所示。
图样工艺性审查的目的是为了保证焊接结构(件)的良好工艺性。
如审查金属的厚度及材料牌号、焊缝位置的布置、焊接接头的形式、接头的开敞性、点距及搭边尺寸等。
审查合格后,进行工艺会签。
焊前有关工序检验主要是对焊前准备的检查,是贯彻预防为主的方针,最大限度避免或减少焊接缺陷的产生,是保证焊接质量的积极有效措施。
电阻焊焊工应有较高的操作技术水平,因为焊接夹具、工艺装备和电阻焊机较为精密、复杂,机械化、自动化程度高,操作中稍许失误(如工件放置偏离,电极冷却不良或修磨不规X,夹具使用不当…)都会造成批量性不合格品出现。
生产实践表明,电阻焊焊接质量与焊机性能和焊接参数关系极为密切。
因此,必须保证焊接参数的正确选用,同时对各参数实行监控;电阻焊设备在安装和大修之后或控制系统改变之后,必须进行焊机的稳定性鉴定,确保鉴定合格后方可焊接产品。
鉴定项目及要求见表1、表2和表3。
焊机类别接头等级试件总数/个宏观金相检验X射线检验剪切试验数量/个要求数量/个要求数量/个要求点焊机一、二级105 5熔核直径应符合表7-3要求,焊透率在20%~80%之间、压痕深≤15%,无其他缺陷100除允许有<0.5mm的气孔外,无其他缺陷1001.强度值均大于表7-2的要求2.90%的试件的强度应在F T①的±12.5%X围内,其余的应T②铝合金要求焊600mm,碳钢及不锈钢要求焊300mm长的焊缝。
焊接质量检验标准

XX机械制造有限公司
焊接质量检验标准
1. 目的
通过正确定义焊接质量的检验标准,保证员工在焊接、检验过程中制造出合格的产品。
2. 范围
适用于焊接车间。
3. 工作程序
焊接质量标准根据生产制造现场工艺实际情况,可采用边界样本目视化来清楚地分辨出焊接质量是否
符合要求。
3.1电阻点焊焊点不合格质量的界定和CO气体保护焊焊点、焊缝不合格质量的界定。
3.1.1以下8种电阻焊点被认为是不可接受的,界定为不合格质量:
3.1.1.1虚焊(无熔核或者熔核的尺寸小于4mr)焊点,代号为L。
3.1.1.2 沿着焊点周围有裂纹的焊点,代号为C o
3.1.1.3烧穿,代号为B。
缺陷B :烧穿
3.1.1.4 边缘焊点(不包括钢板所有边缘部分的焊点),代号为巳
4应严缺陷E:焊点E、
F为边缘焊点,不
3.1.1.5 位置偏差的焊点(与标准焊点位置的距离超过10mm,代号P o
3.1.1.8
漏焊,代号为M 3.1.2以下10种CO 气体保护焊焊点、焊缝被认为是不可接受的,界定为不合格质量
3.122 焊缝金属裂纹;
3.122 夹杂(焊缝中夹杂着除母材和焊丝外的物质或氧化物
); I F 电母材熔合过少,未能达到要求的
(A/B) $50%或(C/D) $50%
缺陷I:压痕过深焊点
I ,压痕深度》板材厚
3.1.1.7 压痕过深的焊点(材料厚度减少 50%,代号为I 。
3.1.2.5 未熔合;。
电阻点焊检验规范

电阻点焊检验规范電阻點焊檢驗規范一.目視檢驗1.試樣和焊件應100%進行目視檢驗﹐允許用不大于10倍的放大鏡進行檢驗。
2.試件和焊件上的焊點不允許有外部裂紋﹑燒穿﹑沿焊點或焊縫板材邊緣的裂紋。
外部飛濺應清理干淨。
3.點焊焊點上壓痕深度不超過板材實際厚度的20%。
4.點焊焊點的壓痕直徑允許比圖紙規定值大15%﹑小10%。
焊點相互位置允許與圖紙規定偏差±2mm﹔偏差超過±2mm﹐但不超過±3mm的焊點數﹐允許不超過焊點總數的20%.二.撕破檢驗1.撕破檢驗焊點時﹐應在一側板材上撕成空洞。
板材厚度大于或等于2mm時﹐允許一側板材上撕成深度不大于板厚一半的凹坑。
2.試樣撕破后﹐檢驗留在一側板材上凸起的結合面處的焊點﹐其直徑應達材料厚度碳鋼鋁材不鏽鋼0.3 2.2 2.2 2.40.5 2.5 2.5 2.50.8 3.0 3.0 3.21.0 3.5 3.5 3.81.2 4.0 4.0 4.21.5 4.5 4.5 4.82.0 5.5 5.5 5.52.5 6.0 6.0 6.43.0 6.5 6.5 7.0三.X光檢驗1.進行X光檢驗時﹐每批抽檢數量不少于5%﹐如有一件不合格﹐則全批檢驗。
2.試樣經X光檢驗時﹐小于0.5mm的氣孔和縮孔允許存在﹐飛濺﹑裂紋不允許存在。
四.低倍檢驗1.底倍檢驗焊點﹐應制備2~3個試樣。
2.低倍磨片腐蝕后﹐用10~20倍放大鏡測量焊點熔核直徑(d)﹐以及焊透高度(h),并按下式計算焊透率η=h/a×100%式中h—熔核焊透高度(mm);a—板材實際厚度(mm);d—點焊熔核寬度(mm).熔核直經應符合上表規定。
厚度比小于2的組合﹐焊透率應在30%~70%范圍內。
厚度比大于等于2的組合﹐薄板的焊透率應不小于20%﹐厚板的焊透高度應不小于薄板的20%﹐其焊透率上限不應超過各自的80%.3.試樣低倍檢驗時﹐熔核中小于0.5mm的氣孔和縮孔允許存在﹐裂紋和飛濺不允許存在。
- 1、下载文档前请自行甄别文档内容的完整性,平台不提供额外的编辑、内容补充、找答案等附加服务。
- 2、"仅部分预览"的文档,不可在线预览部分如存在完整性等问题,可反馈申请退款(可完整预览的文档不适用该条件!)。
- 3、如文档侵犯您的权益,请联系客服反馈,我们会尽快为您处理(人工客服工作时间:9:00-18:30)。
阻焊工序检验规范
1.0目的
制定阻焊工序的检验方法和允收标准,使检验工作有章可循,有据可依。
2.0检验方式
2. 1首件检查:针对阻焊显影后必须做首件检查.
2. 2检查频率: 检验员在阻焊显影后针对当班所生产的每一款新型号板/工具更改/工
艺变更后的板须进行首件确认(包括上一班首件OK的板和各套生产film
所生产的板);
2.3 阻焊全检:阻焊QC对阻焊显影后的板做全检检查。
2. 4过程抽检:针对阻焊显影后必须做抽检检查.
3.0检验工具
MI/制造流程卡(LOT卡)﹑10倍放大镜﹑3M胶带﹑光台﹑锡炉
4.0检验项目
4.1 阻焊油墨的型号与颜色;
4.2 板表面的阻焊印刷质量;
4.3 板表面以及孔内的阻焊显影质量;
4.4 板面阻焊的耐热冲击测试;
4.5 板子与film之间的对准度情况;
4.6 板面阻焊的硬度测试;
4.7 板面的油墨厚度控制;
5.0缺陷名称
油墨用错﹑油墨入孔﹑油墨上盘﹑漏印、露铜、露线、阻焊垃圾/杂物、手指印、龟裂、聚油、阻焊塞孔﹑显影过度﹑显影不净﹑阻焊气泡﹑阻焊脱落﹑菲林对反﹑菲林划伤﹑周期错误﹑UL标志错误、烤板过度等
6.0检验步骤
6.1检验前,检验员须准备好10倍放大镜﹑3M胶带等相关的检验工序并放置在检验台面
上;
6.2.检验时,检验员须戴干净的白手套,并根据首检记录报表上的检验项目逐项进行检
验;
6.3首检
任何送给当站检验人员进行检验的首件板,必须是有经过操作人员进行自检,且自检合格后的板,否则当站检验人员有权拒检,同时,针对此工序的板,操作员在通知检验人员进行首检时,必须准备好相应的LOT卡并放置于待检板的旁边,否则当站检验人员有权进行
6.3.1针对于任何一款板,在阻焊显影之后,操作人员须将前三片的首件板单独放置
在显影机附近,并准备好相应的LOT卡,同时通知当站检验人员取板进行首检作业;
6.3.2检验人员须检查前一站的检验人员是否有在LOT卡的相应位置上进行签卡确认,
如有则进入下一步的检验工作;如上一站的检验人员并未在LOT卡的相应位置上进行签卡确认,则当站检验人员有权进行拒检首件板,同时将此信息立即向生产以及本部门的技工以上人员进行反馈,以使问题能够得到及时的处理,并在处理后,得到本部门技工以上人员通知的情况下进行相应的检验;
6.3.2.1检验人员须认真检查板边处的板型号﹑版本号与LOT卡上的工具型号以及
版本号是否一致;
6.3.2.2检查板子的生产工艺流程是否与LOT卡上的工艺流程一致,是否有走错工
序;
6.3.2.3检查板面的油墨型号﹑颜色是否与LOT卡上的要求一致;
6.3.2.4检查板面的阻焊生产周期与UL标志是否与LOT卡上的要求一致;
6.3.2.5在光台上检查生产Film与板子图形之间的对准度,以确定是否有因对位偏
而造成的绿油压盘上PAD/IC/邦定位置;
6.3.2.6在光台上检查板面是否有显影不干净/显影过度;
6.3.2.7在光台上检查板面是否有阻焊下垃圾/杂物;
6.3.2.8在光台上检查组件孔内是否残留有阻焊油墨未显影干净;
6.3.3所有的检验项目均检验合格后,检验员须做好相关的首检质量记录报表,同时
通知生产部操作人员可以进入到批量生产,如首检不合格,也同样须要通知到生产部操作人员,以便于操作人员及时改善,并由阻焊工序技工以上人员在相关的检验记录上签名确认,同时在改善后重新进行首板检验直至合格为止;
6.3.4针对于生产过程中的板,检验员须严格按照抽检要求进行抽检,如抽检合格,
则在LOT卡上的相应位置签名确认,如不合格,则必须及时的对已生产出来的板
子作质量处理要求(如﹕修理﹑返工),直至合格为止,同时须通知阻焊工序技工
以上人员在相关的检验记录上进行签名确认;如与生产人员在处理的方式与结论
上存在分岐,不允许检验人员自作主张进行处理,而必须上报至本部门的技工以
上人员处理;
6.3.5对于客户特殊要求的板,IPQA必须取1-2PCS样品送至物理实验室进行有关的性
能检测;若需做阻焊硬度、耐热冲击性能检测的必须经高温固化之后进行检测。
6.3.6各项检验均合格后,检验人员须在LOT卡的相应位置上进行签名确认。
7.0检验标准(客户未要求时参照以下标准)
8.0相关文件
8.1过程检验和试验控制程序
9.0相关记录
9.1《阻焊工序首检记录表》 9.2《阻焊工序全检记录表》。