数控加工走刀路线图介绍
数控加工工艺及程序编制
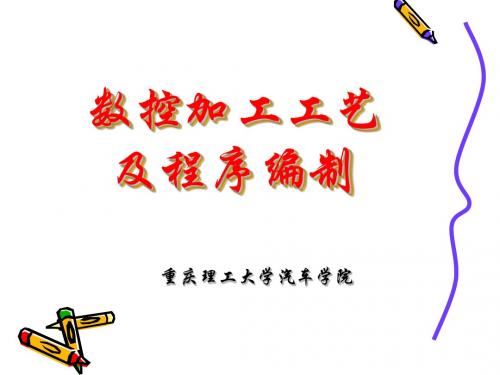
第1章 数控机床加工程序编制基础
一、 选择编程原点 从理论上讲编程原点选在零件上的任何一点都可 以,但实际上,为了换算尺寸尽可能简便,减少计算 误差,应选择一个合理的编程原点。
第1章 数控机床加工程序编制基础
2)编程坐标系
编程坐标系是编程人员根据零件图样及加工工艺等建立的 坐标系。 编程坐标系一般供编程使用,确定编程坐标系时不必考 虑工件毛坯在机床上的实际装夹位置。如下图所示,其中O2 即为编程坐标系原点。
第1章 数控机床加工程序编制基础
编程原点是根据加工零件图样及加工工艺要求选 定的编程坐标系的原点。
其中: X、Y、Z的值是指圆弧 插补的终点坐标值; I、J、K是指圆弧起点 到圆心的增量坐标, 与G90,G91无关; R为指定圆弧半径,当 圆弧的圆心角≤180o 时,R值为正,
G18 G02 X~ Z~ I~ K~ (R~) F~
G18 G03 X~ Z~ I~ K~ (R~) F~ YZ平面:
六、
圆弧插补指令-G02、G03
G02为按指定进给速度的顺时针圆弧插补。G03为按指定进 给速度的逆时针圆弧插补。 圆弧顺逆方向的判别:沿着不在圆弧平面内的坐标轴,由 正方向向负方向看,顺时针方向G02,逆时针方向G03,如下图 所示。
第1章 数控机床加工程序编制基础
程序格式: XY平面: G17 G02 X~ Y~ I~ J~ (R~) F~ G17 G03 X~ Y~ I~ J~ (R~) F~ ZX平面:
。
第1章 数控机床加工程序编制基础
标准机床坐标系中X、Y、Z坐标轴的相互关系用右手笛卡尔 直角坐标系决定: 1)伸出右手的大拇指、食指和中指,并互为90°。则大拇指 代表X坐标,食指代表Y坐标,中指代表Z坐标。 2)大拇指的指向为X坐标的正方向,食指的指向为Y坐标的正方 向,中指的指向为Z坐标的正方向。 3)围绕X、Y、Z坐标旋转的旋转坐标分别用A、B、C表示,根据 右手螺旋定则,大拇指的指向为 X、Y、Z坐标中任意轴的正向, 则其余四指的旋转方向即为旋转坐标A、B、C的正向。
数控铣削加工的走刀路线

数控铣削加工的刀路线反映了工序的加工过程,走刀路线合理与否,关系到工件的加工质量与生产效率。
尤其在数控铣削曲面零件过程中,应认真分析零件的加工要求及其结构特点,找出走刀路线中影响加工效率的因素,在保证零件加工精度和表面粗糙度要求的前提下,应尽量缩短加工路线,从而提高数控机床的加工效率,降低加工成本。
数控加工过程中刀具相对于工件的运动轨迹称为走刀路线。
走刀路线反映了工序的加工过程,确定合理的走刀路线是保证铣削加工精度和表面质量的重要工艺措施之一,也是确定数控编程的前提。
数控铣削加工中走刀路线对工件的加工精度和表面质量有直接的影响,走刀路线合理与否,还关系到加工的生产效率,因此每道工序走刀路线的确定都是非常重要的。
一、走刀路线的确定原则影响走刀路线的因素很多,有工艺方法、工件材料及状态、加工精度及表面粗糙度要求、工件刚度、加工余量、刀具的刚度及耐用度、机床类型和工件的轮廓形状等。
在确定走刀路线时,主要应遵循以下原则:(1)保证产品质量,应将保证工件的加工精度和表面粗糙度要求放在首位。
(2)在保证工件加工质量的前提下,应力求走刀路线最短,并尽量减少空行程时间,提高加工效率。
(3)在满足工件加工质量、生产效率等条件下,尽量简化数学处理的数值计算工作量,以简化编程工作。
此外,在确定走刀路线时,还要综合考虑工件、机床与刀具等多方面因素,确定一次走刀还是多次走刀,以及设计刀具的切入点与切出点,切入方向与切出方向。
在铣削加工中,还要确定是采用顺铣还是逆铣等。
二、铣削方式的选择铣削有顺铣和逆铣两种方式。
铣削加工中是采用顺铣还是逆铣,对工件表面粗糙度有较大的影响。
确定铣削方式应根据工件的加工要求,材料的性质、状态、使用机床及刀具等条件综合考虑。
由于采用顺铣方式,工件加工表面质量较好,刀齿磨损小,因此,一般情况下,尽可能采用顺铣,尤其是精铣内外轮廓、精铣铝镁合金、钛合金或耐热合金时,应尽量按顺铣方式安排走刀路线。
三、铣削曲面类零件走刀路线的确定铣削曲面类零件的走刀路线加工面为空间曲面的零件称为曲面类零件。
数控加工路线的确定

(1)加工路线的确定原则在数控加工中,刀具刀位点相对于工件运动的轨迹称为加工路线。
确定加工路线是编写程序前的重要步骤,加工路线的确定应遵循以下原则。
1.加工路线应保证被加工零件的精度和表面粗糙度,且效率较高。
2.使数值计算简单,以减少编程工作量。
3.应使加工路线最短,这样既可以减少程序段,又可以减少空刀时间。
此外,确定加工路线时,还要考虑工件的加工余量和机床、刀具的刚度等情况,确定是一次走刀,还是多次走刀来完成加工,以及在铣削加工中是采用顺铣还是逆铣等。
(2)辅助程序段的设计1.轮廓加工的进退刀路径设计在对零件的轮廓进行加工时,为了保证零件的加工精度和表面粗糙度符合要求,应合理地设计进退刀路径。
如图1所示,当铣削平面零件外轮廓时,一般采用立铣刀侧刃切削。
刀具切入工件时,应避免沿零件外廓的法向切入,而应沿外廓曲线延长线的切向切入,以避免在切入处产生刀具的刻痕而影响表面质量,保证零件外廓曲线平滑过渡。
同理,在切离工件时,也应避免在工件的轮廓处直接退刀,而应该沿零件轮廓延长线的切向逐渐切离工件。
图1 外轮廓加工刀具的切入切出图2 内轮廓加工刀具的切入和切出1铣削封闭的内轮廓表面时,若内轮廓曲线允许外延,则应沿切线方向切入切出。
若内轮廓曲线不允许外延(见图2),刀具只能沿内轮廓曲线的法向切入切出,此时刀具的切入切出点应尽量选在内轮廓曲线两几何元素的交点处。
当内部几何元素相切无交点时(见图3),为防止刀具在轮廓拐角处留下凹口,刀具切入切出点应远离拐角。
图3 内轮廓加工刀具的切入和切出2如图4所示,用圆弧插补方式铣削外整圆时,当整圆加工完毕时,不要在切点处直接退刀,而应让刀具沿切线方向多运动一段距离,以免取消刀补时,刀具与工件表面相碰,造成工件报废。
铣削内圆弧时也要遵循从切向切入的原则。
最好安排从圆弧过渡到圆弧的加工路线(见图5,这样可以提高内孔表面的加工精度和加工质量。
本篇文章来源于数控网|原文链接:2.孔加工时引伸距离的确定孔加工在确定轴向尺寸时,应考虑一些辅助尺寸,包括刀具的引入距离和超越距离。
数控车床排刀怎么编程【经验分享】
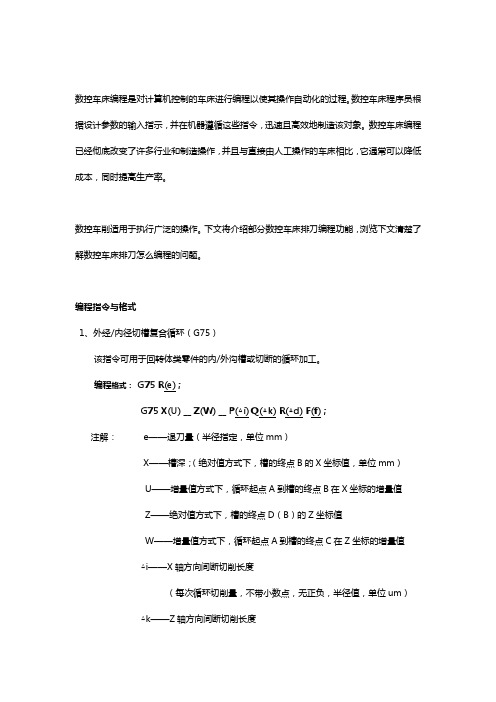
数控车床编程是对计算机控制的车床进行编程以使其操作自动化的过程。
数控车床程序员根据设计参数的输入指示,并在机器遵循这些指令,迅速且高效地制造该对象。
数控车床编程已经彻底改变了许多行业和制造操作,并且与直接由人工操作的车床相比,它通常可以降低成本,同时提高生产率。
数控车削适用于执行广泛的操作。
下文将介绍部分数控车床排刀编程功能,浏览下文清楚了解数控车床排刀怎么编程的问题。
编程指令与格式1、外经/内径切槽复合循环(G75)该指令可用于回转体类零件的内/外沟槽或切断的循环加工。
编程格式:G75 R(e);G75 X(U) __ Z(W) __ P(△i) Q(△k) R(△d) F(f);注解:e——退刀量(半径指定,单位mm)X——槽深;(绝对值方式下,槽的终点B的X坐标值,单位mm)U——增量值方式下,循环起点A到槽的终点B在X坐标的增量值Z——绝对值方式下,槽的终点D(B)的Z坐标值W——增量值方式下,循环起点A到槽的终点C在Z坐标的增量值△i——X轴方向间断切削长度(每次循环切削量,不带小数点,无正负,半径值,单位um)△k——Z轴方向间断切削长度(每次循环切削量,不带小数点,无正负,增量值,单位um ) △d ——为切削至终点的退刀量(半径值),△d 的符号为正,但如果Z(W)和Q(△k)省略,可用正、负符号指定退刀方向。
退刀方向与Z 向进给方向相反,通常情况下,因加工槽时,刀两侧无间隙,无退让距离,所以一般△d 取零或省略。
工进切削快速退刀:槽终点坐标):轴终点位置):刀具终点):刀具起点)图2-58 外经/内径切槽复合循环走刀路线说明:(1)执行G75循环加工指令时,应指定循环起点的位置。
即该指令程序段前的X 、Z 坐标就是加工起始位置,也是G74循环加工结束后刀具返回的终点位置。
(2)X 向和Z 向间断切削时,如最后余量小于指定长度值,就按余量值进行间断切削加工。
2、外径切槽切断循环(G75)该指令是上述格式的简化,适合于在外圆面上切削沟槽或切断加工。
数控加工编程及操作习题及答案

数控加工编程与操作习题集一、选择题1、数控系统之所以能进行复杂的轮廓加工,是因为它具有( C )。
A)位置检测功能 B)PLC功能C)插补功能D)自动控制2、数控编程人员在数控编程和加工时使用的坐标系是( C )。
A)右手直角笛卡尔坐标系 B)机床坐标系 C)工件坐标系D)直角坐标系3、在编制加工中心的程序时应正确选择( D)的位置,要避免刀具交换时与工件或夹具产生干涉。
A)对刀点B)工件原点C)参考点 D)换刀点4、一般而言,增大工艺系统的( A )才能有效地降低振动强度。
A)刚度B)强度C)精度D)硬度5、( A )是指机床上一个固定不变的极限点。
A)机床原点B)工件原点C)换刀点D)对刀点6、数控机床的旋转轴之一B轴是绕( B )直线轴旋转的轴。
A)X轴B)Y轴C)Z轴D)W轴7、机床坐标系判定方法采用右手直角的笛卡尔坐标系。
增大工件和刀具距离的方向是( B )。
A)负方向B)正方向C)任意方向D)条件不足不确定8、加工中心用刀具与数控铣床用刀具的区别( A )。
A)刀柄B)刀具材料C)刀具角度D)拉钉9、选择数控机床的精度等级应根据被加工工件( A )的要求来确定的。
A)关键部位加工精度B)一般精度C)长度D)外径10、下列哪项工作不属于数控编程的范畴( D )。
A)数值计算B)键入程序、制作介质C)确定进给速度和走刀路线D)对刀、设定刀具参数11、ISO标准规定增量尺寸方式的指令为( B )。
A) G90 B) G91 C) G92 D)G9312、沿刀具前进方向观察,刀具偏在工件轮廓的左边是 B 指令,刀具偏在工件轮廓的右边是( C ) 指令。
A) G40 B) G41 C) G4213、刀具长度正补偿是( A ) 指令,负补偿是( B ) 指令,取消补偿是( C ) 指令。
A) G43 B) G44 C) G4914、在铣削工件时,若铣刀的旋转方向与工件的进给方向相反称为( B )。
校本华中系统g71g72g73g32g82的编程介绍
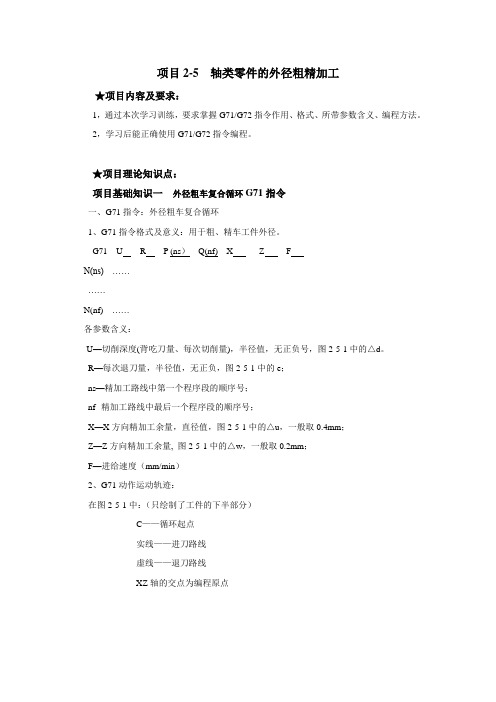
项目2-5 轴类零件的外径粗精加工★项目内容及要求:1,通过本次学习训练,要求掌握G71/G72指令作用、格式、所带参数含义、编程方法。
2,学习后能正确使用G71/G72指令编程。
★项目理论知识点:项目基础知识一外径粗车复合循环G71指令一、G71指令:外径粗车复合循环1、G71指令格式及意义:用于粗、精车工件外径。
G71 U R P (ns)Q(nf) X Z FN(ns) …………N(nf) ……各参数含义:U—切削深度(背吃刀量、每次切削量),半径值,无正负号,图2-5-1中的△d。
R—每次退刀量,半径值,无正负,图2-5-1中的e;ns—精加工路线中第一个程序段的顺序号;nf--精加工路线中最后一个程序段的顺序号;X—X方向精加工余量,直径值,图2-5-1中的△u,一般取0.4mm;Z—Z方向精加工余量, 图2-5-1中的△w,一般取0.2mm;F—进给速度(mm/min)2、G71动作运动轨迹:在图2-5-1中:(只绘制了工件的下半部分)C——循环起点实线——进刀路线虚线——退刀路线XZ轴的交点为编程原点图2-5-13、使用G71编程时的说明:(1)应用G71前必须设一循环起点,图图2-5-1中的C点。
(2)G71程序段本身不进行精加工,粗加工是按后续程序段ns~nf给定的精加工编程轨迹A→A′→B→B′,沿平行于Z轴方向进行。
(3)G71程序段不能省略除F、S、T以外的地址符。
G71程序段中的F、S、T只在循环时有效,精加工时处于ns到nf程序段之间的F、S、T有效。
(4)循环中的第一个程序段(即ns段)必须包含G00或G01指令,即A→A′的动作必须是直线或点定位运动,但不能有Z轴方向上的移动。
(5) ns到nf程序段中,不能包含有子程序。
(6)G71循环时可以进行刀具位置补偿,但不能进行刀尖半径补偿。
因此在G71指令前必须用G40取消原有的刀尖半径补偿。
在ns到nf程序段中可以含有G41或G42指令,对精车轨迹进行刀尖半径补偿。
零件数控车床编程与操作加工

包 头 职 业 技 术 学 院
结构工艺性 几何要素 尺寸标注
该零件的结构工艺性好,便于装夹加工。因此,可选用标准刀具 进行加工。
该零件轮廓几何要素定义完整,尺寸标注符合数控加工要求,有 统一的设计基准,且便于加工、测量。
数控教研室
学习环节一:制定工艺方案
033 该零件外圆面 3000.033 、 4100.04 、 2100.、长度 70 0.1 尺寸 和 20 0.1 尺寸精度要求较高,其中外圆柱面尺寸公差等级 为IT8-IT9级,图中未注尺寸公差按IT12级处理。该零件表面质
零件数控车床编程与操作加工
学习情境8—典型轴类零件车削加工 1.学习情境8.1-典型轴类零件1的车削加工
2.学习情境8.2-典型轴类零件2的车削加工 3.学习情境8.3-典型轴类零件3的车削加工
包头职业技术学院-数控教研室
学习情境8—典型轴类零件车削加工 职业能力
包 1.能对轴类零件进行数控车削加工工艺分析并制定加工工艺路线。 头 2.能正确选择轴类零件数控车削加工所用刀具材料及刀具几何参数,并能 职 正确使用所选刀具进行加工。 业 3.能合理选择加工轴类零件所用切削用量。 技 4.能正确编写轴类零件的数控车削加工程序。 术 5.能合理使用数控车床对类轴零件进行加工。 学 6.能选择并使用相关量具对轴类零件进行质量检测。 院 7.能对轴类零件进行质量评估并能初步分析超差原因。 8.能制定轴类零件数控车削加工工艺规程。 9.能计算轴类零件加工过程尺寸链尺寸。 10.能选择、使用轴类零件加工夹具。
该零件采用外圆柱面进行定位,生产类型为中批生产故在安排 工艺应采用工序集中原则。 该零件要求锐角倒钝,故编程时在锐角处安排1×450的倒角。 该零件生产批量为单件生产,因此,要按单件小批生产类型制 定工艺规程。 数控教研室
数控加工工艺路线设计
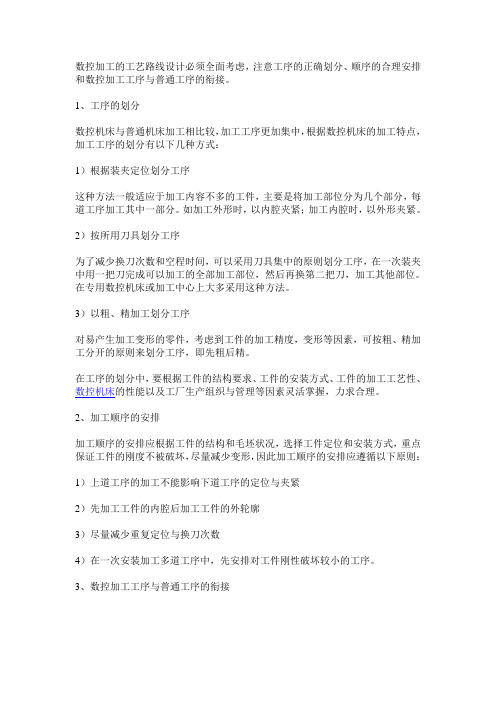
数控加工的工艺路线设计必须全面考虑,注意工序的正确划分、顺序的合理安排和数控加工工序与普通工序的衔接。
1、工序的划分数控机床与普通机床加工相比较,加工工序更加集中,根据数控机床的加工特点,加工工序的划分有以下几种方式:1)根据装夹定位划分工序这种方法一般适应于加工内容不多的工件,主要是将加工部位分为几个部分,每道工序加工其中一部分。
如加工外形时,以内腔夹紧;加工内腔时,以外形夹紧。
2)按所用刀具划分工序为了减少换刀次数和空程时间,可以采用刀具集中的原则划分工序,在一次装夹中用一把刀完成可以加工的全部加工部位,然后再换第二把刀,加工其他部位。
在专用数控机床或加工中心上大多采用这种方法。
3)以粗、精加工划分工序对易产生加工变形的零件,考虑到工件的加工精度,变形等因素,可按粗、精加工分开的原则来划分工序,即先粗后精。
在工序的划分中,要根据工件的结构要求、工件的安装方式、工件的加工工艺性、数控机床的性能以及工厂生产组织与管理等因素灵活掌握,力求合理。
2、加工顺序的安排加工顺序的安排应根据工件的结构和毛坯状况,选择工件定位和安装方式,重点保证工件的刚度不被破坏,尽量减少变形,因此加工顺序的安排应遵循以下原则:1)上道工序的加工不能影响下道工序的定位与夹紧2)先加工工件的内腔后加工工件的外轮廓3)尽量减少重复定位与换刀次数4)在一次安装加工多道工序中,先安排对工件刚性破坏较小的工序。
3、数控加工工序与普通工序的衔接由于数控加工工序穿插在工件加工的整个工艺过程之中,各道工序需要相互建立状态要求,如加工余量的预留,定位面与孔的精度和形位公差要求,矫形工序的技术要求,毛坯的热处理等要求,各道工序必须前后兼顾综合考虑。
4、数控机床加工工序和加工路线的设计数控机床加工工序设计的主要任务:确定工序的具体加工内容、切削用量、工艺装备、定位安装方式及刀具运动轨迹,为编制程序作好准备。
其中加工路线的设定是很重要的环节,加工路线是刀具在切削加工过程中刀位点相对于工件的运动轨迹,它不仅包括加工工序的内容,也反映加工顺序的安排,因而加工路线是编写加工程序的重要依据。
数控加工走刀路线图(完整版)
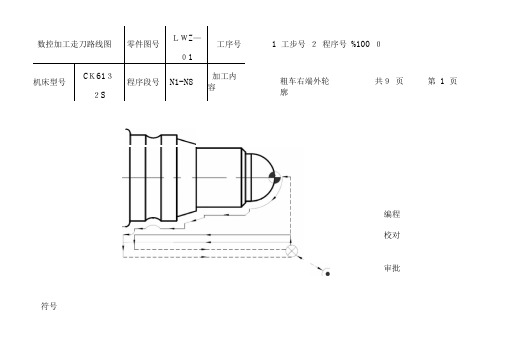
CK6132
程序段号
N22
加工内容
粗车左端内轮廓
共9页
第7页
S
-N29
校对
审批
换刀点
进给走刀方向
含义
循环点
编程原点
符号
编程
数控加工走刀路线图
零件图号
LWZ—
工序号
2
工步号
6
程序号
%2000
快速走刀方向
01
机床型号
CK613
2S
程序段号
N3
0-N41
加工内容
精车左端内轮廓
编程
校对
符号
含义
循环点
程序段号
N9-
N31
加工内容
精车右端外轮廓
共9页
第2页
编程
校对
审批
校对
审批
符号
含义
循环点
编程原点
换刀点
快速走刀方向
进给走刀方向
数控加工走刀路线图
零件图号
LWZ—
01
工序号
2
工步号
3
程序号
%2000
机床型号
CK613
2S
程序段号
N1—N8加工内容来自粗车左端外轮廓共9页
第5页
编程
校对
审批
符号
含义
循环点
编程原点
编程原点
换刀点
快速走刀方向
进给走刀方向
数控加工走刀路线图
零件图号
LWZ-0
1
工序号
2
工步号
7
机床型号
CK61
32S
程序段号
N42—N
51
典型零件数控加工工艺分析实例

说明:表格中刀尖半径和备注栏可以不要;25×25 指车刀刀柄的截面尺寸。
(5)切削用量选择
一般情况下,粗车:恒转速 n=800r/min 恒线速 v=100m/min
进给量 f=0.2mm/r 以下
vf=120m/min
背吃刀量 ap=2mm 以下
精车:恒转速 n=1100r/min 恒线速 v=150m/min
以零件右端面和中心轴作为 坐标原点建立工件坐标系。
根据零件尺寸精度及技术要 求,零件从右向左加工,将粗、 精加工分开来考虑。
加工工艺顺序为:车削右端面→复合型车削固定循环粗、精加工右端需要加工的所有轮 廓(粗车Φ44、Φ40.5、Φ34.5、Φ28.5、Φ22.5、Φ16.5 外圆柱面→粗车圆弧面 R14.25→ 精车外圆柱面Φ40.5→粗车外圆锥面→粗车外圆弧面 R4.75→精车圆弧面 R14→精车外圆锥 面→精车外圆柱面Φ40→精车外圆弧面 R5)。 (4)选择刀具
所选定刀具参数如表 1-2 所示。 说明:铣削内、外轮廓时,铣刀直径受槽宽限制,可选择φ6 的立铣刀;精铰的量通常 小于 0.2mm;刀刃和长度通常要比切削的深度大。 5.切削用量选择 一般情况下,粗铣:恒转速 n=600r/min
进给量 f=180mm/min 以下 背吃刀量 ap=5mm 以下 精车:恒转速 n=800r/min 进给量 f=120mm/min 以下
零件的底面和外部轮廓已经加工,本工序是在铣床上加工槽与孔。 1.零件图分析
凸轮内外轮廓由直线和圆弧组成。凸轮槽侧面和
20
0.021 0
、
12
0.018 0
两个内孔尺寸精
度要求较高,表面粗糙度要求也较高,Ra1.6;内孔
20
数控铣削加工编程图例
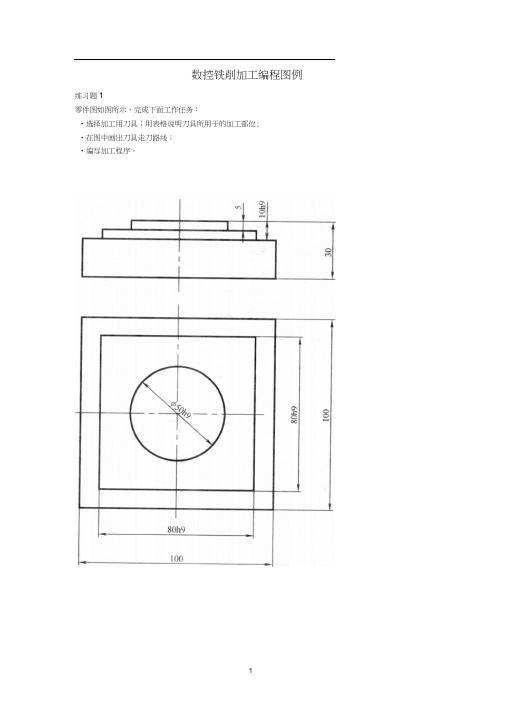
数控铣削加工编程图例练习题1零件图如图所示,完成下面工作任务:•选择加工用刀具;用表格说明刀具所用于的加工部位;•在图中画出刀具走刀路线;•编写加工程序。
练习题2零件图如图所示,编写加工程序。
•粗加工用φ 30平底铳刀,刀具长度130mm,留Imm精加工余量; •精加工用φ 10平底铳刀,刀具长度110mm技术要求未注尺寸公差按照ITl2加工和检验匚练习题3如图所示,完成下面任务:•对零件加工进行工艺设计•编写零件加工程序⅛⅛ I 80x i 50∣45mJ W列45*i练习题4如图所示,完成下面任务: •对零件加工进行工艺设计 •编写零件加工程序13*±L ¢5「LS占十Wl练习题5如图所示,完成下面任务:•对零件加工进行工艺设计•编写零件加工程序20⅛a 140x100x46mm练习题6如图所示,完成下面任务:•对零件加工进行工艺设计•编写零件加工程序如图所示,完成下面任务:•对零件加工进行工艺设计•编写零件加工程序如图所示,完成下面任务:•对零件加工进行工艺设计•编写零件加工程序A-A编写零件加工程序«0+0.03 2×^10H8其余穿80 -0()s -≡^ 0.03」册一25 _ IKa材料:45钢92h9 IOOP l ( -30 902 P 0) P l { -y. 549. -29. 379) 巴(25,3 K. 153)P t (25 J 8. 153) P S ( -9.549,29,379)技术姿求未注尺寸公劳按照n ∣2加丄和检验编写零件加工程序月F16q s=0_。
数控程序铣削加工走刀路线的改善

其 中要 点是 : (1)精加 工为顺铣 ,切削力稳定 ,表 面质量
好 。 (2)去除余量 ,由毛坯 中部 向零件 型腔轮 廓
层 次 剥离 。 (3)确 保 精 加 工 余 量 均 匀覆 盖 于 型 腔 轮 廓 ,
使 精加 工 过 程平 稳 ,不 产 生 突兀 的振 刀现 象 。 (4)粗 加 工 时 ,深 度 方 向分 层 ,a ≤3mm,
图 4
(1)精加工为顺铣 ,切 削力稳定 ,表面 质量 好 。
(2)去除余量 ,由毛坯 边缘 向零件轮廓 层次 剥 离 。
(3)确保精JJ ̄T_余量于 凸台轮廓均匀覆 盖 , 使精 加 工 过程 平 稳 ,不产 生 突 兀 的振 刀现 象 。
而红线走刀方式 ,先吃满刀JJ ̄T_轮廓 ,再 去除 余量。但缺点是 :满 刀加工产生振刀 ,不易满足所 需精度 ;使被去除的余量与主体分离 ,局部材料 刚 性 下降,在切 削去除过程中产生振动 ,损伤刀具 , 降低 使 用 寿命 。
图 1
如 图2所示 ,零件表面粗糙 度值尺 ≤3.2 nl, 非 配合 型面 ,选 择整 体硬 质合金铣 刀或可转 位端 铣 刀 ,往复走 刀时零 件较长 方 向作 为进给 方 向 , 等 间距 覆 盖 ,步 距 刀具 直 径 ×2/3;有 三 种转 向方 式 :第一种方式 为每一次进给完全穿过零件 ,适 合 普 铣 手 工 操 作及 初 级 编 程 使 用 ;第 二 种 方 式 为不 出 零 件 ,边 切 削进 给 边 直 折 线 转 向 ,这 种 方 式切 削效 率 大 幅 提 高 ,但 对 机 床 冲 击 大 ;第 三 种 方 式 为不 出 零件 ,边切削进给边 圆弧线转向,切削效率同样提 高 ,对 机 床 冲击 小 。
数控铣削加工编程图例

如图所示,完成下面任务:
·对零件加工进行工所示,完成下面任务:
·对零件加工进行工艺设计
·编写零件加工程序
练习题5
如图所示,完成下面任务:
·对零件加工进行工艺设计
·编写零件加工程序
练习题6
如图所示,完成下面任务:
·对零件加工进行工艺设计
·编写零件加工程序
练习题7
数控铣削加工编程图例
练习题1
零件图如图所示,完成下面工作任务:
·选择加工用刀具;用表格说明刀具所用于得加工部位;
·在图中画出刀具走刀路线;
·编写加工程序.
练习题2
零件图如图所示,编写加工程序.
·粗加工用φ30平底铣刀,刀具长度130mm,留1mm精加工余量;
·精加工用φ10平底铣刀,刀具长度110mm
如图所示,完成下面任务:
·对零件加工进行工艺设计
·编写零件加工程序
练习题8
如图所示,完成下面任务:
·对零件加工进行工艺设计
·编写零件加工程序
练习9
编写零件加工程序
练习10
编写零件加工程序
数控加工工艺培训(共42张PPT)
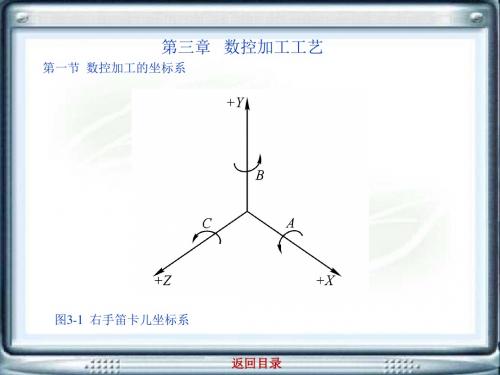
第三章 数控加工工艺
第二节 数控加工的工艺处理
图3-9 非敞开部位的沟槽加工 返回目录
第三章 数控加工工艺
第二节 数控加工的工艺处理
图3-10 普通机床上用成形刀加工沟槽 返回目录
第三章 数控加工工艺
第二节 数控加工的工艺处理
图3-11 数控机床上加工对应的沟槽 返回目录
第三章 数控加工工艺
图3-26 车削中心加工类型 返回目录
第三章 数控加工工艺
第四节 数控车床加工工艺
图3-27 可转位车刀 返回目录
第三章 数控加工工艺
第四节 数控车床加工工艺
图3-28 可转位刀片的紧固方式 返回目录
第三章 数控加工工艺
第四节 数控车床加工工艺
图3-29 用圆形刀片进行仿形加工 返回目录
第三章 数控加工工艺
图3-19 型腔区域加工走刀路线 返回目录
第三章 数控加工工艺
第三节 数控加工工艺的制订
图3-20 三坐标曲面行切法加工 返回目录
第三章 数控加工工艺
第三节 数控加工工艺的制订
图3-21 曲面加工走刀路线 返回目录
第三章 数控加工工艺
第三节 数控加工工艺的制订
图3-22 进给速度的确定 返回目录
第三章 数控加工工艺
第一节 数控加工的坐标系
图3-5 三坐标加工 返回目录
第三章 数控加工工艺
第一节 数控加工的坐标系
图3-6 车削零件图 返回目录
第三章 数控加工工艺
第一节 数控加工的坐标系
图3-7 G92刀具调整位置 返回目录
第三章 数控加工工艺
第二节 数控加工的工艺处理
图3-8 数控车床上加工的典型零件 返回目录
数控加工走刀路线图说明

数控加工走刀路线图
零件图号
工序号
2
工步号
2
程序号
O0002
机床型号
KV650
程序段号
加工内容
铣心型轮廓
共6页
第2页
编程
校对
审批
符号
含义
抬刀
下刀
编程原点
起刀点
走刀
方向
走刀线
相交
爬斜坡
铰孔
行切
数控加工走刀路线图
零件图号
工序号
3工Biblioteka 号3程序号O0003
机床型号
KV650
程序段号
加工内容
下刀
编程原点
起刀点
走刀
方向
走刀线
相交
爬斜坡
铰孔
行切
工序号
5
工步号
5-8
程序号
O0005
机床型号
KV650
程序段号
加工内容
钻孔
共6页
第5页
编程
校对
审批
符号
含义
抬刀
下刀
编程原点
起刀点
走刀
方向
走刀线
相交
爬斜坡
铰孔
行切
数控加工走刀路线图
零件图号
工序号
6
工步号
13
程序号
O0006
机床型号
KV650
程序段号
加工内容
加工内球面
共6页
第6页
编程
校对
审批
符号
含义
抬刀
挖槽
共6页
第3页
编程
校对
审批
符号
含义
机械制造及自动化专业毕业论文--数控铣床加工工艺设计
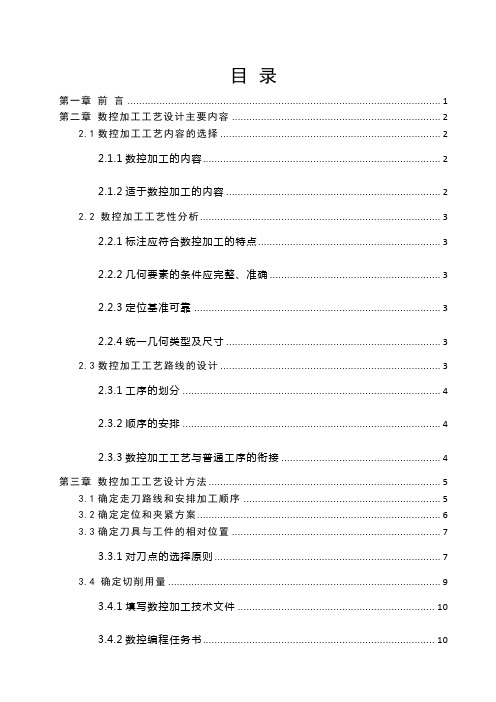
目录第一章前言 (1)第二章数控加工工艺设计主要内容 (2)2.1数控加工工艺内容的选择 (2)2.1.1数控加工的内容 (2)2.1.2适于数控加工的内容 (2)2.2 数控加工工艺性分析 (3)2.2.1标注应符合数控加工的特点 (3)2.2.2几何要素的条件应完整、准确 (3)2.2.3定位基准可靠 (3)2.2.4统一几何类型及尺寸 (3)2.3数控加工工艺路线的设计 (3)2.3.1工序的划分 (4)2.3.2顺序的安排 (4)2.3.3数控加工工艺与普通工序的衔接 (4)第三章数控加工工艺设计方法 (5)3.1确定走刀路线和安排加工顺序 (5)3.2确定定位和夹紧方案 (6)3.3确定刀具与工件的相对位置 (7)3.3.1对刀点的选择原则 (7)3.4 确定切削用量 (9)3.4.1填写数控加工技术文件 (10)3.4.2数控编程任务书 (10)3.4.3数控加工工件安装和原点设定卡片(简称装夹图和零件设定卡)113.4.4数控加工工序卡片 (12)3.4.5数控加工走刀路线图 (13)3.5数控刀具卡片 (14)第四章数控铣床加工的基本特点 (15)第五章数控铣床刀具的选择 (16)5.1数控铣床对刀具的要求及铣刀的种类 (16)5.1.1对刀具的要求 (16)5.1.2常用铣刀种类 (17)5.2孔加工刀具的选用 (17)5.3铣削加工刀具选用 (18)结论 (18)结束语 (18)参考文献 ........................................... 错误!未定义书签。
数控铣床加工工艺设计摘要目的数控机床作为一种高效率的设备,欲充分发挥其高性能、高精度和高自动化的特点,除了必须掌握机床的性能、特点及操作方法外,还应在编程前进行详细的工艺分析和确定合理的加工工艺,以得到最优的加工方案。
方法本文通过理论上的论述和实例的说明,得到数控铣床加工工艺的基本过程为:零件图分析,加工工艺路线的设计,夹具和刀具的选择,切削用量的选择和划分工序及拟定加工顺序等步骤。
浅述数控车床加工中走刀路线的合理确定

浅述数控车床加工中走刀路线的合理确定作者:杨艳华来源:《中国新技术新产品》2011年第15期摘要:在数控加工中,刀具刀位点相对于工件运动的轨迹称为进给路线,也称走刀路线。
它不但包括了工步的内容,而且也反映出工步的顺序。
在数控加工中,进给路线是由数控系统控制的。
它对零件的加工质量、加工效率有直接影响,因此,工序设计时必须拟定好刀具合理的进给路线。
关键词:数控车床;走刀路线;原则;确定方法中图分类号:TG659 文献标识码:A1确定走刀路线的原则工步的划分与安排一般可随走刀路线来进行,在确定走刀路线时,主要遵循以下几点原则:1.1加工路线应保证被加工工件的精度和表面粗糙度;1.2应使加工路线最短,以减少空行程时间,提高加工效率;1.3尽量简化数学处理时的数值计算工作量,以简化编程工作;1.4当进给路线重复时,为了简化编程,缩短程序长度,应使用子程序。
此外,确定加工路线时,还要考虑工件的形状与刚度、加工余量的大小,机床与刀具的刚度,合理的切入与切出方向等。
2走刀路线的确定方法走刀路线的确定原则是在保证加工质量的前提下,使加工程序具有最短的走刀路线,这样不仅可以节省整个加工过程的执行时间,还能减少一些不必要的刀具消耗及机床进给滑动部件的磨损等。
2.1粗车走刀路线2.1.1外圆粗车G71适于切削区轴向余量较大的细长轴套类零件的粗车,使用该方式加工可减少径向分层次数,使走刀路线变短2.1.2端面粗车G72用于切削区径向余量较大的轮盘类零件的粗车加工,并使得轴向分层次数少。
2.1.3环状粗车G73适合周边余量较均匀的铸锻坯料的粗车加工,对从棒料开始粗车加工,则会有很多空行程的切削进给路线。
如图1所示。
图1粗车走刀路线若按图2(a)所示,从右往左由小到大逐次车削,由于受背吃刀量不能过大的限制,所剩的余量就必然过多;按图2(b)所示,从大到小依次车削,则在保证同样背吃刀量的条件下,每次切削所留余量就比较均匀,是正确的阶梯切削路线。
- 1、下载文档前请自行甄别文档内容的完整性,平台不提供额外的编辑、内容补充、找答案等附加服务。
- 2、"仅部分预览"的文档,不可在线预览部分如存在完整性等问题,可反馈申请退款(可完整预览的文档不适用该条件!)。
- 3、如文档侵犯您的权益,请联系客服反馈,我们会尽快为您处理(人工客服工作时间:9:00-18:30)。
14.4 数控加工走刀路线图
数控加工走刀路线图零件图号工序号 2 工步号 2 程序号O0002 机床型号KV650 程序段号加工内容铣心型轮廓共 6 页第 2 页
编程
校对
审批
符号
含义抬刀下刀编程原点起刀点
走刀
方向
走刀线
相交
爬斜坡铰孔行切数控加工走刀路线图零件图号工序号 3 工步号 3 程序号O0003 机床型号KV650 程序段号加工内容挖槽共 6 页第 3 页
编程
校对
审批符号
含义抬刀下刀编程原点起刀点走刀
方向
走刀线
相交
爬斜坡铰孔行切
数控加工走刀路线图零件图号工序号 5 工步号5-8 程序号O0005
钻孔
编程
校对
审批符号
含义抬刀下刀编程原点起刀点走刀
方向
走刀线
相交
爬斜坡铰孔行切
数控加工走刀路线图零件图号工序号 6 工步号13 程序号O0006 机床型号KV650 程序段号加工内容加工内球面共 6 页第 6 页
编程
校对
审批。