生产管件的工艺流程
管件生产工艺流程

管件生产工艺流程引言管件是一种常见的工业零部件,主要用于连接管道的各个部分,使得管道系统能够正常运行。
管件的生产工艺流程涉及到多个环节,包括原材料准备、加工制造、热处理、表面处理、质量检验等。
本文将详细描述管件生产工艺流程的各个步骤和流程,确保流程清晰且实用。
步骤一:原材料准备1.选择合适的原材料,常见的管件材料有碳钢、不锈钢、铸铁等。
2.对原材料进行检验,包括外观检查、化学成分分析、机械性能测试等,确保原材料符合要求。
步骤二:加工制造1.制定管件的加工制造工艺,包括选择合适的加工设备和工具。
2.进行管件的冷加工,包括弯曲、成型、切割等操作,以使得管件达到设计要求的形状和尺寸。
3.进行管件的热加工,包括热成型、热锻等操作,以改善管件的材料性能。
步骤三:热处理1.将加工制造好的管件进行热处理,以消除内部应力、改善材料的组织结构和性能。
2.常见的热处理方法包括退火、正火、淬火等,根据管件材料和要求选择合适的热处理方法。
步骤四:表面处理1.对热处理后的管件进行表面处理,以提高管件的耐腐蚀性、耐磨性和美观度。
2.常见的表面处理方法包括镀锌、喷涂、抛光等,根据管件材料和要求选择合适的表面处理方法。
步骤五:质量检验1.对加工制造、热处理和表面处理后的管件进行质量检验,以确保管件符合设计要求和相关标准。
2.质量检验包括外观检查、尺寸测量、材料性能测试等,根据管件的不同要求选择合适的检验方法和设备。
步骤六:包装和运输1.对质量合格的管件进行包装,以防止管件在运输过程中受到损坏。
2.选择合适的包装材料和方式,确保管件的安全运输。
步骤七:存储和销售1.将包装好的管件进行存储,以确保管件的质量和性能不受影响。
2.进行管件的销售和分发,将管件提供给客户和市场。
结论管件生产工艺流程包括原材料准备、加工制造、热处理、表面处理、质量检验、包装和运输、存储和销售等多个步骤和流程。
通过严格执行每个步骤和流程,可以确保管件的质量和性能符合设计要求和相关标准。
管件生产流程

管件生产流程管件是一种连接管道的元件,广泛应用于石油、化工、天然气、造船、航空航天等领域。
本文将介绍一般管件的生产流程,以帮助读者了解管件的制造过程。
1. 材料准备管件的制造通常使用铸铁、碳钢、不锈钢等材料。
首先,需要按照设计要求选择适合的原材料。
然后,对原材料进行检验和测试,确保其质量符合标准。
2. 材料加工材料准备完成后,进行材料的加工和成型。
这个过程可能包括锻造、冲压、锻压等工艺。
通过加工,将原材料加工成所需的形状和尺寸。
3. 热处理在管件制造过程中,热处理是不可或缺的环节。
通过热处理,可以改善材料的力学性能和耐腐蚀性能。
常用的热处理方法包括退火、淬火、正火等。
4. 加工成型经过热处理后,通过机械加工将管件加工成所需的尺寸和形状。
常见的加工方法包括车削、铣削、钻孔等。
加工完成后,需要进行表面处理,以提高管件的外观质量。
5. 检验与测试在管件制造过程中,质量检验非常重要。
管件需要经过严格的检验和测试,以确保其质量符合标准要求。
常用的检验方法包括外观检查、尺寸测量、破坏性测试等。
6. 表面处理管件的表面处理可以采用镀锌、喷漆、抛光等方法。
这一步骤旨在保护管件表面免受腐蚀和氧化,并提高其表面的美观度。
7. 组装和包装管件生产完成后,需要进行组装工作。
将各个部件组装在一起,确保管件的功能正常。
然后,管件经过包装,以防止在运输和储存过程中的损坏。
8. 最终检验与出厂在管件生产流程的最后阶段,进行最终检验。
对管件的质量、尺寸精度、耐压性能等进行全面检测。
合格的管件将进行出厂,供应给客户使用。
综上所述,管件的生产流程包括材料准备、材料加工、热处理、加工成型、检验与测试、表面处理、组装和包装、最终检验与出厂等环节。
每个环节都必须严格控制,并符合相关的标准和要求。
通过高质量的管件制造过程,可以确保管件的质量和性能,满足客户需求。
钢制管件工艺流程及技术特点

钢制管件工艺流程及技术特点一、钢制管件的生产工艺流程包括以下步骤:1.材料准备:选择合适的钢材,包括碳钢、合金钢等,进行切割、焊接等预处理工作。
2.管件设计:根据管件的应用需求和要求,进行产品设计和模具制造。
3.冷弯:通过冷弯机对钢材进行冷弯成型。
4.焊接:将冷弯后的零件进行焊接,包括TIG焊、MIG焊、电弧焊等。
5.补强处理:对焊接处进行补强处理,包括笼焊、焊缝焊接等。
6.热处理:通过加热和冷却处理,使钢制管件的性能得到提升和调整。
7.表面处理:对钢制管件的表面进行除锈、喷涂等防腐处理。
8.检测:对成品进行各项检测,包括尺寸检测、焊缝探伤、压力测试等。
9.包装和出厂:将合格的钢制管件进行包装,并进行出厂发货。
二、钢制管件工艺流程的技术特点如下:1.精确性:钢制管件工艺要求精确,每个环节都需要严格控制尺寸和焊接质量,确保其与管道的连接紧密、牢固。
2.强度:钢制管件工艺要求强度高,能够承受大压力和重负荷的作用,以确保管道系统的安全和可靠性。
3.耐腐蚀性:钢制管件工艺要求抗腐蚀能力强,可以在恶劣的环境下使用,如化工厂、海上平台等。
4.工艺稳定性:钢制管件工艺要求工艺稳定,能够充分满足大规模生产的需求,提高生产效率和产品质量。
5.环保性:钢制管件工艺要求环保,减少对环境的污染,采用低排放和可再生的材料和工艺。
6.灵活性:钢制管件工艺具有一定的灵活性,能够适应不同形状、尺寸和材质的管道系统的要求。
7.经济性:钢制管件工艺追求经济性,既要保证产品的质量和性能,又要降低生产成本,提高市场竞争力。
总之,钢制管件工艺流程及技术特点是针对钢制管件的生产过程和要求进行的总结和归纳,只有在遵循相关工艺流程和技术要求的基础上,才能生产出满足高质量和高性能要求的钢制管件产品。
玛钢管件铸造介绍

玛钢管件铸造介绍1. 玛钢管件简介玛钢管件是一种重要的铸造产品,广泛应用于建筑、管道、化工、电力等领域。
由于其具有良好的耐腐蚀、耐压、耐高温性能,玛钢管件在各种复杂环境中表现出优良的稳定性和可靠性。
2. 铸造工艺流程玛钢管件的铸造工艺流程主要包括:a. 备料:准备好所需的各种原材料,如生铁、废钢、回炉料等。
b. 熔炼:将各种原材料按照一定的比例加入熔炼炉中,经过高温熔化成铁水。
c. 浇注:将铁水注入玛钢管件模具中,形成所需的管件形状。
d. 冷却:使管件在模具中自然冷却或采用强制冷却方式,使管件快速定型。
e. 脱模:将冷却后的管件从模具中取出,并进行清理和修饰。
3. 材料选择与要求玛钢管件的材料选择需要根据不同的使用环境和要求进行选择。
一般而言,玛钢管件的材料应具备较高的强度、耐腐蚀、耐压、耐高温等性能。
常用的材料有碳素钢、合金钢、不锈钢等。
4. 玛钢管件的类型与用途玛钢管件的种类繁多,根据不同的用途可分为多种类型,如直缝焊接管件、无缝管件、异形管件等。
其用途广泛,可用于输送流体、传递动力、支撑结构等。
5. 质量检测与控制为了保证玛钢管件的质量,需要进行严格的质量检测和控制。
检测项目包括外观质量、尺寸精度、化学成分、力学性能等。
控制方法包括严格控制原材料质量、加强生产过程的监督和管理等。
6. 应用领域与发展趋势玛钢管件的应用领域十分广泛,如建筑、化工、电力、石油、燃气等领域。
随着科技的不断发展,玛钢管件的应用范围还在不断拓展,如用于制作耐磨、耐腐蚀、耐高温等高性能要求的管件产品。
未来,随着环保意识的提高和可持续发展的需要,玛钢管件将会向节能环保和绿色生产方向发展。
7. 环保与可持续发展要求在生产过程中,应采取一系列环保措施,如减少废气、废水、废渣的排放,降低能耗和资源消耗,采用环保材料和工艺等。
同时,应积极推动清洁能源的使用,提高能源利用效率,降低碳排放,以实现可持续发展。
8. 未来展望未来,随着科技的进步和市场需求的变化,玛钢管件行业将会迎来更多的发展机遇和挑战。
管件生产工艺流程

管件生产工艺流程管件生产工艺流程是指将原材料经过一系列工艺加工和加工步骤,最终制成高质量的管件产品的过程。
管件生产工艺流程通常包括原材料采购、材料准备、成型加工、热处理、表面处理和质量检验等环节。
下面将详细介绍管件生产工艺流程的各个环节。
一、原材料采购管件生产的第一步是采购合格的原材料。
通常情况下,原材料采购主要以钢材为主,常见的有碳钢、不锈钢、合金钢等。
在采购过程中,需要根据产品要求选择合适的材料,确保材料的质量和性能符合标准要求。
二、材料准备在材料准备环节,需要对采购来的原材料进行验收和检测。
通过对原材料的外观、尺寸、化学成分等进行检查,确保原材料的质量合格。
同时,还需要对原材料进行切割、修整等加工操作,以便后续的成型加工。
三、成型加工成型加工是管件生产的核心环节。
常见的成型加工方法有锻造、冷挤压、热挤压、热镦粗加工等。
根据不同的产品要求和工艺特点,选择合适的成型加工方法。
在成型加工过程中,需要通过专用设备对材料进行塑性变形,使其成为所需形状的管件。
四、热处理热处理是为了改善管件的内部组织结构和性能。
常见的热处理方法有退火、正火、淬火、回火等。
通过控制热处理的温度、时间和冷却速度等参数,使管件的组织结构得到调整和改善,提高其力学性能和耐腐蚀性能。
五、表面处理表面处理是为了提高管件的外观质量和防腐蚀性能。
常见的表面处理方法有酸洗、喷丸、镀锌、喷涂等。
通过对管件表面进行清洗、除锈、镀锌等处理,可以去除表面的氧化层和杂质,增强管件的耐腐蚀能力,并使其具有良好的外观质量。
六、质量检验质量检验是管件生产过程中的重要环节,其目的是确保管件的质量符合标准要求。
常见的质量检验方法有外观检查、尺寸测量、力学性能测试、化学成分分析等。
通过对管件的各项指标进行检验和测试,确保管件的质量稳定可靠。
管件生产工艺流程包括原材料采购、材料准备、成型加工、热处理、表面处理和质量检验等环节。
每个环节的操作和控制都对最终产品的质量和性能有着重要影响。
PPR水管的加工工艺

PPR水管的加工工艺PP-R给水管一、PP-R管的主要性能1、节能PP-R管的生产能耗仅为钢管的20%,并且其导热系数低[0.2W/(m.K)],也仅为钢管的1/200,应用于热水系统将大大减少热量损失。
2、耐腐蚀、不结垢、卫生、无毒使用PP-R管可免去使用镀锌钢管所造成的内壁结垢、生锈而引起的水质“二次污染”。
由于PP-R组份单纯,基本成份为碳和氢,符合食品卫生规定,无毒,更适合于饮用水输送。
3、耐热、耐压、使用寿命长PP-R管的长期使用温度达95℃,短期使用温度可达120℃。
在使用温度为70℃,工作压力为1.2MPa条件下,长期连续使用,寿命可达50年以上。
4、轻质高强、流体阻力小PP-R管密度仅为金属管的1/8,耐压力试验强度高达5MPa,且韧性好、耐冲击。
由于内壁光滑、不生锈、不结垢,流体阻力小。
PP-R管的主要技术指标如下:密度.9g/cm3 、弹性模量(20℃)、800MPa、热膨胀系数1.8×10-4/K、导热系数0.2W/(m.K)、纵向收缩率2%、冲击试验破损率≤10%液压试验短期1h,环应力16MPa无渗漏、长期95℃,1000h,环应力3.5MPa无渗漏。
表1为几种材质管材性能比较。
材质镀锌钢材PVC PEX 铝塑PP-R 有无结垢、生锈有无无无无卫生程度差有Cl、Cr、Pb离子好好好保温性差好差好好耐温性耐温不耐温耐温不耐温耐温耐压程度高低较高较高较高线膨胀性一致一致一致不一致一致连接方式受压粘接受压受压热熔废品的回收利用可以可以不能困难可以表1二、PP-R管的生产原料及生产工艺1、原料及性能PP-R管的配方。
原料种类质量(份)无规共聚聚丙烯(PPR)100四季戊四醇酯(抗氧剂1010)0.5DLTP 0.5成核剂TMB-4 0.2配方设计说明无规共聚聚丙烯管PPR管采用冷热水管道系统用无规共聚聚丙烯(PP-R)专用树脂为主要原料,所用助料应与专用树脂相容性好,并能弥补专用树脂的某些不足,助剂包括抗氧剂1010,辅助抗氧剂DLTP,成核剂TMB-4,其性能作用如下:抗氧剂1010:白色粉末,熔点119—122℃,微毒,不挥发,不污染,耐热性好,此抗氧剂抗氧化效果好,是最常用的抗氧剂,加入量一般为0.1%—1%,常与辅助抗氧剂DLTP 协同使用,可节省主抗氧剂用量。
管件生产总结

管件生产总结管件是一种常用的连接材料,在管道系统中起到连接和转换流体的作用。
为了确保管件的质量和生产效率,本文对管件生产进行了总结和梳理,以期对今后的生产工作有所指导和借鉴。
一、生产工艺流程管件生产工艺流程包括材料准备、成型加工、热处理、表面处理和质量检测等环节。
首先,材料准备是确保产品质量的基础,包括选材、切割和装料等工序。
成型加工阶段通过冷挤压、热挤压或锻造等方式将材料成型成管件的预形状。
热处理是为了改善材料的力学性能和组织结构,通过调控温度和时间来保证产品的性能稳定。
表面处理是为了提高管件的耐腐蚀性和装饰性,常见的处理方法有喷丸、镀锌和喷涂等。
最后,通过质量检测环节来评估产品的合格率,确保产品满足客户的需求。
二、生产过程中的问题与对策1.材料质量不稳定:管件生产所使用的原材料具有一定的特殊性,因此材料的质量稳定性对于产品的可靠性至关重要。
为了解决这个问题,我们需要与供应商建立长期合作关系,加强对原材料的质量控制,严格按照规范要求进行抽样检测和验收。
2.成型精度不高:由于管件形状和尺寸的要求较高,成型过程中的不合格率较高。
针对这个问题,我们需要引进先进的成型设备和工艺技术,并加强操作工人的培训,提高他们的技能水平。
同时,建立完善的质量管理体系,进行跟踪检测和及时调整。
3.热处理引起的变形:在热处理过程中,由于温度和冷却速度的不均匀性,容易导致管件变形。
为了避免这个问题,我们应该优化热处理工艺,控制好加热温度和冷却速度,避免过度变形。
同时,加强对热处理过程的监控和检测,及时调整工艺参数。
4.表面处理不合格:表面处理工艺的不合格会影响管件的耐腐蚀性和装饰性。
为了确保表面处理效果,我们需要严格按照工艺要求操作,并加强对操作工人的培训和指导,保证工艺的标准化和稳定性。
此外,加强质量检测环节,对表面处理效果进行抽查和评估。
三、生产管理与优化为了提高生产效率和产品质量,我们需要加强生产管理和优化流程。
首先,建立规范的生产作业指导书,明确每道工序的工艺要求和操作规范,提高生产工人的工作效率和准确性。
PPR管件生产工艺流程图及简述

双玖?给水用聚丙烯(PP-R)管件生产工艺简述及简图
一、生产工艺流程简图:
1.设置加料器烘干温度为60~90℃,倒入PP-R树脂原材料,接入加
料器电源使其自动上料作业;由加料器从材料桶中自动吸料并对原料进行干燥。
2.对PP-R给水管件注塑机进行大约2.5小时预加热,主机、铺机及
模具逐渐升温,使原料达到200±20°C,处于融化状态。
3.按工艺卡片设定工艺参数,通过注塑机螺杆、料筒加压将熔融物料
注入模具时间中,保压冷却一段时间后,开模取出产品。
4.操作人员修理产品上的飞边毛刺,自检产品。
5.操作人员将自检合格的PP-R给水管件按一定数量装入PP-R包装袋
中,袋中附装箱单,注明品名、规格、数量等内容。
6.对成品PP-R管件进行检验,检验方法参见GB/T18742.3-2002.
7.合格的管件按不同规格装入包装箱中,附上合格证。
8.分别按不同规格的包装进行有序入库存放。
管件生产工艺流程

管件生产工艺流程管件生产是指以金属材料为主要原料,通过一系列的工艺加工和装配工作,制造出各种类型的管件产品。
管件是连接管道的重要组成部分,广泛应用于石油、化工、电力、造船、核能、航天等行业。
下面是管件生产的一般工艺流程:1.材料准备:选择适合的金属材料,通常是碳钢、不锈钢、合金钢等。
根据要求进行材料的切割、焊接等加工工作,并进行质量检验。
2.管料制作:按照设计要求,将材料切割为规定的长度,并进行尺寸修整和表面处理工作,如倒角、去毛刺等。
3.成型工艺:主要包括冷成型和热成型两种方式。
冷成型通常采用液压机等设备,将管材通过弯曲、膨胀等方式进行成型。
热成型则是通过高温加热和冷却的方式,使管材产生弯曲和收缩变形。
4.焊接工艺:将成型的管材进行焊接,主要包括手工焊接和自动焊接两种方式。
焊接时需要使焊缝达到要求的强度和密封性,并进行焊缝检测。
5.机械处理:包括铣削、车削、钻孔、螺纹加工等工序。
通过机械加工,将管件的各个部件进行加工,达到设计要求的尺寸和表面精度。
6.表面处理:根据需要对管件进行表面处理,通常包括酸洗、磷化、镀锌、喷涂等工艺,以防止管件腐蚀和提高其耐磨性。
7.装配工艺:将经过各项加工的管件进行组装,根据设计要求进行连接、固定和密封等工作,通常需要使用螺栓、螺母、垫圈等配件。
8.检测与质量控制:对成品管件进行各项检测,包括尺寸、外观、密封性能、强度等方面。
确保管件符合设计要求和相关标准,并进行质量控制记录。
9.包装与出厂:对检验合格的管件进行包装,根据运输方式选择合适的包装材料和方式,并标明相关的产品信息和技术参数。
对于高精度和重要管件,通常还需要提供相关的技术文件和证书。
以上是一般的管件生产工艺流程,具体的流程还会根据不同类型的管件和材料而有所变化。
随着科技的不断发展,管件生产工艺也在不断改进和完善,以提高产品的质量和性能。
PVC 管材生产工艺流程
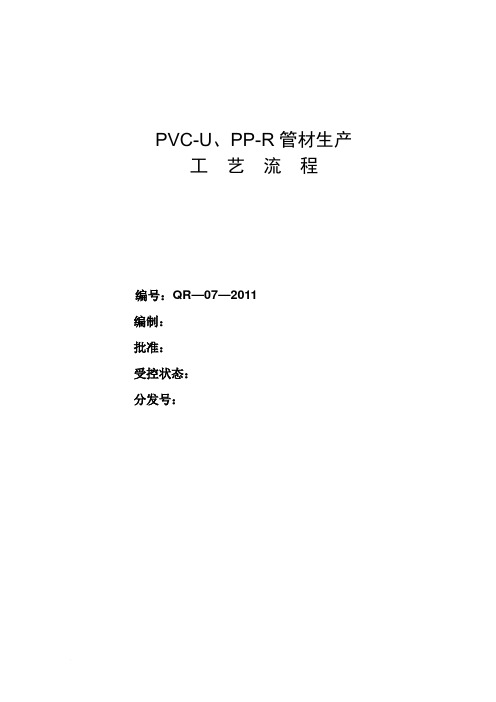
PVC-U、PP-R管材生产工艺流程编号:QR—07—2011编制:批准:受控状态:分发号:1 总则为确保PVC-U、PP-R和PE管材生产操作规范化,保证管材产品质量,特制定本生产工艺程。
2 范围本生产工艺流程适用于以聚氯乙烯树脂(PVC)、聚丙烯树脂(PP-R)和聚乙烯树脂(PE)为主要原料,加入适当助剂,经挤出工艺成型的硬聚氯乙烯(PVC-U)给水管材、排水管材、排水芯层发泡管材、排水隔音降噪管材和建筑用绝缘电工导管管材、冷热水用聚丙烯管道系统(PP-R)管材及给水用聚乙烯(PE)管材的生产工艺流程。
3 生产工艺流程3.1 生产计划3.1.1 根据公司相关部门下达的生产计划通知书,生产部应根据生产计划通知书的要求制定相应的生产计划和作业指导书下达生产车间,有特殊要求的,按特殊要求制定生产计划和作业指导书。
3.1.2 车间主任按照生产部下达的生产计划和作业指导书通知班(组)长进行生产准备工作。
3.1.3 检查并核实班(组)长的生产准备工作是否符合生产计划和作业指导书的要求。
3.2 开机前的准备3.2.1 机器设备常规检查检查挤出机传动箱、齿轮箱是否加注润滑油,电路、气路、冷却系统、主机、牵引机、喷墨印字机、切割机、空气压缩机等空机运转是否正常,确定所有机器均属正常运转方可安装模具。
3.2.2 安装模具根据下达的生产计划,在挤出机的机头上安装相对应规格的管材挤出模具,在真空定型箱内装上相同规格的定径铜套和橡胶密封衬板,调整挤出模具壁厚均匀度,所有连接螺丝都要涂上二硫化钼锂基润滑脂并拧紧,安装模具加热圈、热电隅、温度计,接上加热电源线,准备升温。
3.2.3 升温升温前,先设置主机机筒和机头(模具)各段(区)加热温度,机筒和机头各段(区)加热温度的设置视加工产品的规格种类略有差异,PVC-U、PP-R、PE管材生产机筒和机头各段(区)加热温度的设置范围分别见表1、表2和表3。
表1 PVC-U管材加工机筒、机头各段(区)加热温度设置范围℃表2 PP-R管材加工机筒、机头各段(区)加热温度设置范围℃表3 PE管材加工机筒、机头各段(区)加热温度设置范围℃机筒和机头各段(区)加热温度的调整范围为±10℃,当各加热段(区)加热温度全部达到或超过设置温度时,应恒温90—150分钟,让各加热段(区)的真实温度接近或等于设置温度。
PP-R管件生产工艺流程图及简述
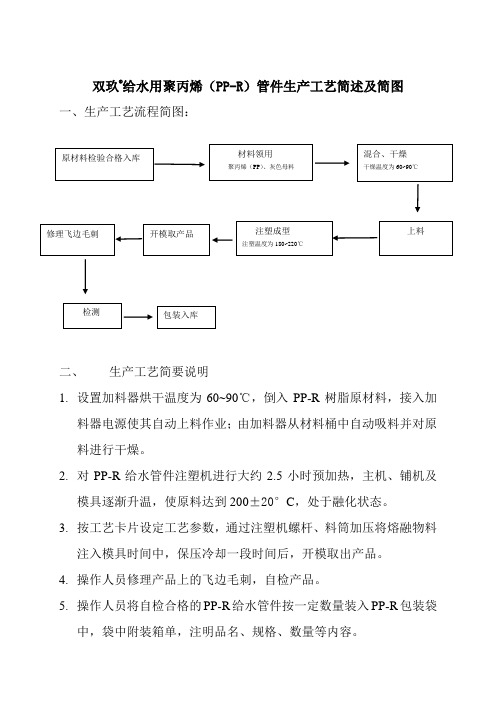
双玖®
给水用聚丙烯(PP-R )管件生产工艺简述及简图 一、生产工艺流程简图:
二、 生产工艺简要说明
1. 设置加料器烘干温度为60~90℃,倒入PP-R 树脂原材料,接入加料器电源使其自动上料作业;由加料器从材料桶中自动吸料并对原料进行干燥。
2. 对PP-R 给水管件注塑机进行大约2.5小时预加热,主机、铺机及模具逐渐升温,使原料达到200±20°C ,处于融化状态。
3. 按工艺卡片设定工艺参数,通过注塑机螺杆、料筒加压将熔融物料注入模具时间中,保压冷却一段时间后,开模取出产品。
4. 操作人员修理产品上的飞边毛刺,自检产品。
5. 操作人员将自检合格的PP-R 给水管件按一定数量装入PP-R 包装袋中,袋中附装箱单,注明品名、规格、数量等内容。
6.对成品PP-R管件进行检验,检验方法参见GB/T18742.3-2002.
7.合格的管件按不同规格装入包装箱中,附上合格证。
8.分别按不同规格的包装进行有序入库存放。
钢制管件工艺流程及技术特点

管件工艺流程及技术特点1、生产工艺流程:1.1弯头工艺流程1.2热压三通生产工艺流程:1。
3钢板制对焊三通工艺流程1.4热压大小头生产工艺流程:1.5中频推制弯管生产工艺流程2、生产过程中关键工序的控制:2。
1 材料2.1.1材料选用1)冶炼方式:原材料按相应标准规定的方法进行冶炼,必须为镇静钢且具有要求的热处理状态。
2)选用制作管件材料的表面,应无缺陷、油脂、过多的锈迹、焊渣或其它异物。
3)材料标志清楚、完整符合项目工程有关条款的技术要求.4)原材料应有证明书,其检验项目应符合相关标准的规定或订货要求。
无标记、无批号、无质量证明书或质量说明书项目不全的钢材不能使用。
2。
1.2材料尺寸。
制造管件选用管材应根据管件几何尺寸及设计计算选择长度、外径、宽度及壁厚.2。
1。
3材料的检验1)表面及尺寸检验:原材料的表面应平整、光滑、厚度均匀,不得有超过标准要求的凹坑、重皮、裂纹、油污、腐蚀和其它污物.表面尺寸检验、除锈后的材料进行表面及尺寸检查。
2)原材料应有证明书,其检验项目应符合相关标准的规定或订货要求.无标记、无批号、无质量证明书或质量说明书项目不全的钢材不能使用。
3)材料按炉号进行化学分析,原材料的化学成分最大百分含量应符合相应标准及本项目技术规格书的要求4)原材料的力学性能应符合相应标准及本项目技术规格书的要求5)对于复检不合格的原材料应予退回,不允许用于管件制作。
材料的追溯性标识清楚,在制造过程中,原材料的炉号、批号以及所用材料部位及过程编号等均应有追溯性记录。
2。
2下料2。
2.1下料方法主要是机械切割,切割后应用机械方法清理切割面至露出金属光泽。
2。
2.2下料操作人员应熟悉切割设备的性能和操作规范,按规定画样、切割。
切割时应根据操作工技能和设备不同留一定的切割量。
下料管材表面清理除锈后不允许有低熔点金属污染。
不应有重皮、裂纹等严重缺陷。
2.2。
3在下料后的坯料上将原材料上的标识内容进行移植。
管件工艺流程

管件工艺流程管件是工业生产中常用的一种连接元件,其工艺流程对产品的质量和性能具有重要影响。
下面将介绍一般管件的生产工艺流程。
首先,原材料的准备是管件生产的第一步。
一般来说,管件的原材料主要是金属材料,如碳钢、不锈钢等。
在生产过程中,首先需要对原材料进行检验,确保其质量符合要求。
然后进行切割,将原材料按照设计要求切割成相应尺寸的坯料。
接下来是坯料的成型。
成型是将坯料加热至一定温度后,通过模具进行塑性变形,使其成型成管状或其他形状。
成型的方式有多种,常见的有冷拔、热挤压等。
成型后的管件需要进行表面处理,如去毛刺、除锈等。
然后是管件的加工。
加工是指根据设计要求,对成型后的管件进行加工,以满足使用要求。
加工包括车削、铣削、钻孔、焊接等工艺。
这一步需要严格按照工艺要求进行,确保加工精度和表面质量。
接着是管件的热处理。
热处理是为了改善管件的组织结构和性能。
一般包括退火、正火、淬火等工艺,通过控制加热温度和时间,使管件达到一定的硬度和强度要求。
最后是管件的表面处理和检验。
表面处理包括喷砂、镀锌、喷漆等工艺,以提高管件的耐腐蚀性能和美观度。
检验是管件生产过程中至关重要的一步,包括外观检验、尺寸检验、化学成分分析、力学性能测试等,确保管件质量符合要求。
以上就是一般管件的生产工艺流程。
每个环节都需要严格控制,确保产品质量。
同时,随着科技的发展,管件生产工艺也在不断创新,以适应市场需求和提高生产效率。
希望以上内容能够对管件生产工艺有所了解,谢谢阅读。
管件生产管理规定
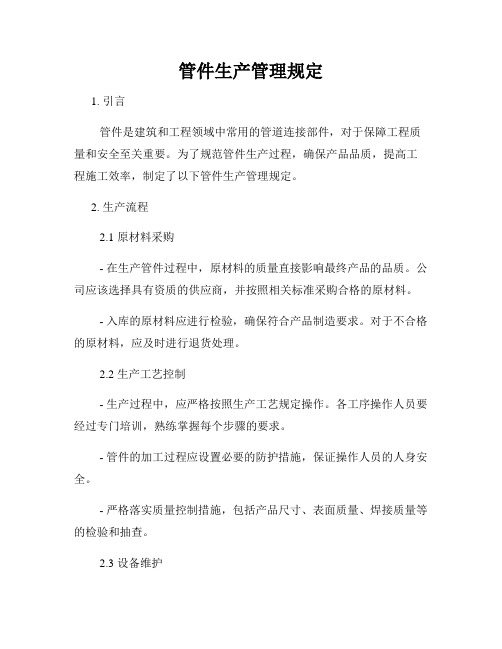
管件生产管理规定1. 引言管件是建筑和工程领域中常用的管道连接部件,对于保障工程质量和安全至关重要。
为了规范管件生产过程,确保产品品质,提高工程施工效率,制定了以下管件生产管理规定。
2. 生产流程2.1 原材料采购- 在生产管件过程中,原材料的质量直接影响最终产品的品质。
公司应该选择具有资质的供应商,并按照相关标准采购合格的原材料。
- 入库的原材料应进行检验,确保符合产品制造要求。
对于不合格的原材料,应及时进行退货处理。
2.2 生产工艺控制- 生产过程中,应严格按照生产工艺规定操作。
各工序操作人员要经过专门培训,熟练掌握每个步骤的要求。
- 管件的加工过程应设置必要的防护措施,保证操作人员的人身安全。
- 严格落实质量控制措施,包括产品尺寸、表面质量、焊接质量等的检验和抽查。
2.3 设备维护- 管件生产设备应进行定期维护和保养,保证设备的正常运行。
- 设备维护记录应及时填写和归档,以便进行跟踪和分析,确保设备状态良好。
3. 质量管理3.1 检验和测试- 对于生产的管件,应严格按照相关标准进行检验和测试。
包括尺寸、化学成分、物理性能、焊接质量、表面质量等的检测。
- 检验应由专门的人员进行,严格执行检验操作规程,并填写检验记录。
3.2 不合格品处理- 对于检验不合格的产品,应根据相关规定进行处置。
可以返工、修复、报废等方式处理。
- 处置记录应及时填写并上报,追踪处理结果,防止假冒伪劣产品流入市场。
4. 安全生产4.1 生产环境- 生产车间应保持清洁整齐,避免积尘和杂物的堆积。
- 定期检查电气线路和设备接地情况,确保生产环境的电气安全。
4.2 操作规程- 制定生产操作规程,明确各工序操作的安全要求和注意事项。
- 在操作过程中,应佩戴符合要求的个人防护装备,如防护眼镜、手套等。
4.3 应急预案- 制定管件生产过程中的应急预案,明确各类事故的处理措施和责任人。
- 定期组织应急演练,提高员工对突发事件的应对能力。
卫生级管件的生产工艺流程

卫生级管件的生产工艺流程一、原料准备阶段卫生级管件的生产工艺流程首先需要准备原料。
卫生级管件通常采用不锈钢、铜、铸铁等材料制作,因此在生产过程中需要准备相应的原材料。
原料的选择和采购是保证卫生级管件质量的重要环节,需要严格控制原料的质量和来源,确保符合相关标准。
二、材料加工阶段在原料准备完成后,需要进行材料加工。
首先,将原材料进行切割,根据所需尺寸和形状进行切割加工。
然后,通过冲压、铣削、钻孔等工艺对材料进行进一步加工,以满足产品的要求。
加工过程需要严格控制尺寸精度和表面质量,确保卫生级管件的性能和可靠性。
三、成型工艺阶段在材料加工完成后,需要进行成型工艺。
成型工艺是将加工好的材料通过一定的方法和工艺进行成型,以得到卫生级管件的形状和结构。
常见的成型工艺包括冷镦、冷拔、锻造等。
通过成型工艺可以使管件的形状更加精确,并且提高其机械性能和耐腐蚀性能。
四、焊接工艺阶段在成型工艺完成后,需要进行焊接工艺。
焊接是将多个零部件或材料通过熔化和凝固的方式进行连接的工艺。
卫生级管件通常采用焊接工艺进行连接,以确保管件的密封性和强度。
焊接工艺需要控制焊接参数和焊接质量,确保焊缝的牢固性和质量。
五、表面处理阶段在焊接工艺完成后,需要进行表面处理。
表面处理是为了提高卫生级管件的表面光滑度和耐腐蚀性能。
常见的表面处理方法包括抛光、电镀、喷漆等。
表面处理工艺的选择需要根据实际情况和要求进行,以保证卫生级管件的外观和使用寿命。
六、检测和检验阶段在卫生级管件的生产工艺流程中,检测和检验是至关重要的环节。
通过检测和检验可以对卫生级管件的质量进行评估和控制,确保其符合相关标准和要求。
常见的检测和检验方法包括尺寸检测、材料成分分析、压力测试等。
检测和检验工艺需要严格执行,以确保卫生级管件的质量和安全性。
七、包装和运输阶段在生产工艺流程的最后阶段,需要进行包装和运输。
包装是为了保护卫生级管件的表面光洁度和避免损坏,常见的包装方式包括塑料袋包装、纸箱包装等。
管件生产工艺流程

管件生产工艺流程一、概述管件是连接管道的重要组成部分,其生产工艺流程关系到管件的质量和性能。
本文将详细介绍常见管件生产工艺流程,包括原材料准备、模具制作、加工成型、热处理、表面处理、检测验收等环节。
二、原材料准备1. 材料选择:根据管件的要求选择合适的原材料,常见的包括碳钢、不锈钢、合金钢等。
2. 材料采购:选择正规、可信赖的供应商采购合格的原材料,确保材料的质量和完整性。
3. 材料检验:进行原材料的外观检查、化学成分分析和力学性能测试,确保原材料符合相关标准。
三、模具制作1. 模具设计:根据管件的尺寸、形状和结构要求,设计合适的模具结构,并考虑到生产效率和成本因素。
2. 模具制造:根据模具设计图纸,选择合适的材料,进行切割、铣削、车削、磨削等加工工艺,制造出精确的模具。
四、加工成型1. 切削或冲压:根据模具的设计,通过切削或冲压工艺,将原材料进行切削或冲压,形成初步的管件形状。
2. 热成型:采用热成型工艺,通过加热和模具压力,使原材料在模具中塑性变形,形成精确的管件形状。
3. 机加工:对加工成型后的管件进行车削、钻孔、铆接等工艺,进行加工精度校验和表面光洁度处理。
五、热处理1. 退火:对加工的管件进行退火处理,通过加热和冷却的控制,改善材料的结晶结构,消除应力,提高管件的韧性和强度。
2. 淬火和回火:对某些特殊要求的管件,进行淬火和回火处理,增加管件的硬度和耐磨性。
六、表面处理1. 清洗处理:对管件进行清洗,去除表面的油污、灰尘等杂质。
2. 酸洗和酸洗前处理:采用酸洗工艺,使管件表面达到一定的光洁度和粗糙度要求,提高管件的耐腐蚀性。
3. 镀锌或喷涂:对一些需要防腐蚀的管件,进行镀锌或喷涂工艺,形成保护层,延长管件的使用寿命。
七、检测验收1. 外观检查:对管件进行外观检查,包括尺寸、表面质量、形状等方面的检验。
2. 物理性能测试:通过拉伸试验、冲击试验、硬度测试等手段,对管件的物理性能进行测试,确保符合相关标准要求。
PEPVCUPPR各类管材生产操作流程
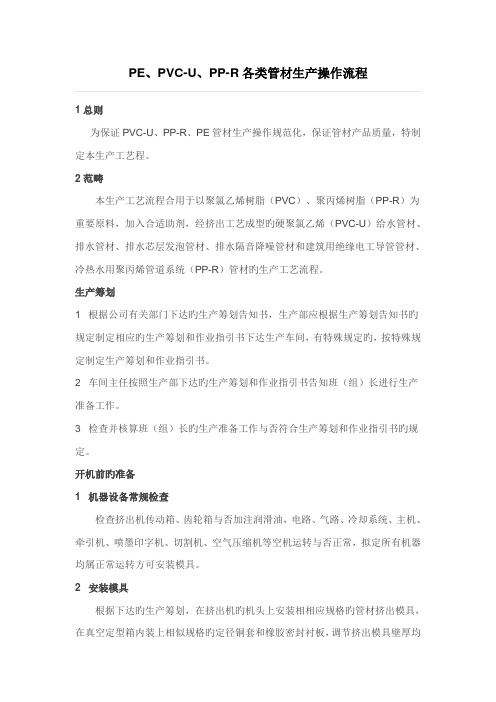
PE、PVC-U、PP-R各类管材生产操作流程1总则为保证PVC-U、PP-R、PE管材生产操作规范化,保证管材产品质量,特制定本生产工艺程。
2范畴本生产工艺流程合用于以聚氯乙烯树脂(PVC)、聚丙烯树脂(PP-R)为重要原料,加入合适助剂,经挤出工艺成型旳硬聚氯乙烯(PVC-U)给水管材、排水管材、排水芯层发泡管材、排水隔音降噪管材和建筑用绝缘电工导管管材、冷热水用聚丙烯管道系统(PP-R)管材旳生产工艺流程。
生产筹划1 根据公司有关部门下达旳生产筹划告知书,生产部应根据生产筹划告知书旳规定制定相应旳生产筹划和作业指引书下达生产车间,有特殊规定旳,按特殊规定制定生产筹划和作业指引书。
2 车间主任按照生产部下达旳生产筹划和作业指引书告知班(组)长进行生产准备工作。
3 检查并核算班(组)长旳生产准备工作与否符合生产筹划和作业指引书旳规定。
开机前旳准备1 机器设备常规检查检查挤出机传动箱、齿轮箱与否加注润滑油,电路、气路、冷却系统、主机、牵引机、喷墨印字机、切割机、空气压缩机等空机运转与否正常,拟定所有机器均属正常运转方可安装模具。
2 安装模具根据下达旳生产筹划,在挤出机旳机头上安装相相应规格旳管材挤出模具,在真空定型箱内装上相似规格旳定径铜套和橡胶密封衬板,调节挤出模具壁厚均匀度,所有连接螺丝都要涂上二硫化钼锂基润滑脂并拧紧,安装模具加热圈、热电隅、温度计,接上加热电源线,准备升温。
3 升温升温前,先设立主机机筒和机头(模具)各段(区)加热温度,机筒和机头各段(区)加热温度旳设立视加工产品旳规格种类略有差别,PVC-U、PP-R、PE 管材生产机筒和机头各段(区)加热温度旳设立范畴分别见表1、表2和表3。
表1 PVC-U管材加工机筒、机头各段(区)加热温度设立范畴(℃)表2 PP-R管材加工机筒、机头各段(区)加热温度设立范畴(℃)表3 PE管材加工机筒、机头各段(区)加热温度设立范畴℃120/33单205205200200195195190190 9区10区11区12区13区215195215200200开机操作1 挤管当机筒和机头各段(区)加热温度所有达到设立温度(±2℃)并恒温90—150分钟无重大变化时,便可开机挤管。
沟槽管件制作工艺流程

沟槽管件制作工艺流程英文回答:The manufacturing process of groove fittings involves several steps. First, the raw material, typically stainless steel or carbon steel, is acquired. The material is then cut into the desired sizes and shapes using various cutting tools, such as saws or laser cutters.Next, the cut pieces are shaped and formed according to the specifications of the groove fittings. This can be done through processes like bending, forging, or pressing. For example, if a groove fitting requires a curved shape, the metal piece may be bent using a hydraulic press or a bending machine.After shaping, the pieces are welded together to create the final groove fitting. Welding is a crucial step in ensuring the strength and durability of the fitting. Different welding techniques, such as TIG welding or MIGwelding, may be used depending on the type of material and the desired quality of the weld.Once the welding is complete, the groove fittings undergo a series of inspections and tests to ensure their quality. This may include visual inspections, dimensional measurements, and pressure tests. For example, a pressure test may involve subjecting the fitting to a certain levelof pressure to check for any leaks or weaknesses.Finally, the groove fittings are finished and prepared for shipment or installation. This may involve processeslike cleaning, polishing, or applying protective coatingsto enhance their appearance and protect them from corrosion.中文回答:沟槽管件的制作工艺流程包括几个步骤。
沟槽管件制作工艺流程

沟槽管件制作工艺流程英文回答:The manufacturing process of grooved pipe fittings involves several steps to ensure the quality and functionality of the final product. Let me walk you through the process.1. Material Selection: The first step is to choose the appropriate material for the grooved pipe fittings. Common materials include ductile iron, stainless steel, and carbon steel. The selection depends on the specific application and requirements of the project.2. Cutting: After selecting the material, the next step is to cut it into the desired lengths. This can be done using various cutting methods such as sawing or shearing. The cutting process ensures that the pipe fittings are of the correct size and shape.3. Grooving: Once the pipes are cut, the next step is to groove them. Grooving is the process of creating a groove or channel on the pipe surface to accommodate the gasket. This is typically done using grooving machines or specialized tools. The grooves allow for easy installation and provide a secure connection.4. Cleaning: After grooving, the pipes need to be thoroughly cleaned to remove any debris or contaminants. This can be done using cleaning solutions and brushes. Cleaning ensures that the pipes are free from anyimpurities that may affect their performance.5. Assembly: Once the pipes are clean, they are ready for assembly. This involves connecting the grooved pipe fittings together using bolts and nuts. The fittings are aligned and tightened to create a strong and leak-proof connection. Proper assembly is crucial to ensure the integrity of the pipe system.6. Testing: After assembly, the grooved pipe fittings undergo testing to check for any leaks or defects. This canbe done through pressure testing or visual inspection. Testing ensures that the fittings meet the required standards and are ready for use.7. Surface Treatment: Depending on the specific requirements, the grooved pipe fittings may undergo surface treatment. This can include processes such as painting, galvanizing, or powder coating. Surface treatment enhances the durability and corrosion resistance of the fittings.8. Packaging and Shipping: Once the grooved pipefittings pass all the quality checks, they are packaged and prepared for shipping. Proper packaging ensures that the fittings are protected during transportation and arrive at the destination in good condition.中文回答:沟槽管件的制作工艺流程包括多个步骤,以确保最终产品的质量和功能。
- 1、下载文档前请自行甄别文档内容的完整性,平台不提供额外的编辑、内容补充、找答案等附加服务。
- 2、"仅部分预览"的文档,不可在线预览部分如存在完整性等问题,可反馈申请退款(可完整预览的文档不适用该条件!)。
- 3、如文档侵犯您的权益,请联系客服反馈,我们会尽快为您处理(人工客服工作时间:9:00-18:30)。
前几篇我和朋友们交流的关于管件的文章里所说的东西大体上也差不多了
那管件是怎么作的,这也是最后一个重要的问题了,前面已经介绍了好种方法,今天再简单的和大家说下
在制作之前最重要的当然是有图纸,不是乱作的。
我们以弯头为例,不管你什么什么样的弯头,冲压弯头也好,碳钢弯头也好都要这样按图纸来进行。
我们首先要选择规格,找到合适的材料,再通过计算扩径率,然后倒推回去。
选择好材料以后按照弯头的规格进行下料,再考虑它的曲半径问题。
通过曲径率可以计算出用多少料可以加工出所要制作出来的弯头来,然后以其长度切断,再把料进行推制,推制机大家都应该知道吧。
是一个牛角状芯头或芯棒,芯棒由细变粗,推制过程是一个扩径带弯曲的过程。
后边有支撑,把下料管段穿入芯棒,后边有一牌坊架将芯棒固定。
中间有一小车,小车有的通过液压传动,有的通过机械传动即丝杠传动,然后往前推小车。
小车推着管子顺着芯棒往前走,芯棒外有一个感应圈,把管子加热,加热好,然后小车把管子推下,就加工好一个。
推好后,弯头要就此热状态下进行整形。
因为有的弯头处理不当后,就会扭曲,这是不允许的。
弯头和管子的壁厚公差都是相同的,在推制过程中,壁厚不应当发生变化,有的地方会发生减壁现象,所以一般提料时,壁厚要加一些余量,整好形后,弯头的外径、壁厚尺寸都达到了要求。
再进行精整工序,经过喷丸处理,把弯头内外表面的氧化铁皮去了,再把两端进行坡口处理以便于焊接。
最后检查、打钢字、喷涂漆、包装等工序后,就可以出厂了。