铝合金铸件补焊工艺规范 QJ3072-98
铝与铝合金焊接施工工艺标准[详]
![铝与铝合金焊接施工工艺标准[详]](https://img.taocdn.com/s3/m/491598cc6edb6f1afe001f00.png)
铝及铝合金焊接施工工艺标准1 适用围本工艺标准适用于铝及铝合金的手工钨极氩弧焊和熔化极氩弧焊的焊接。
2 施工准备2.1 铝及铝合金的焊接除应执行本工艺标准外,还应符合国家颁布的有关标准、法律法规及规定。
下列文件中的条款通过本标准的引用而成为本标准的条款,凡是不注日期的引用文件其最新版本适用于本标准《铝及铝合金轧制板材》GB/T-3880-1997《铝及铝合金热挤压管》第一部分:无缝圆管GB/T4437.1-2000《铝及铝合金拉(轧)制无缝管》GB/T6893-2000《铝及铝合金焊丝》GB/T10858《铝及铝合金焊接管》GB/T10571《铝制焊接容器》/T4734-20022.2 材料2.2.1 一般规定工程中使用的母材和焊丝应具备出厂质量合格证或质量复验合格报告,并优先选用已列入国家标准或行业标准的母材和焊丝,母材和焊丝应妥善保管,防止损伤、污染和腐蚀。
当选用国外材料时,其使用围应符合相应标准的规定,并应有该材料的质量证明书。
2.2.2 母材2.2.2.1工程选用的母材应符合现行的国家标准规定。
2.2.2.2当对母材有特殊要求时,应在设计图样或相应的技术条件上标明。
2.2.2.3施工单位对设备、容器和管道的材料的代用,必须事先取得原设计单位的设计修改证明文件,并对改动部位作详细记载。
2.2.2.4损伤和锈蚀严重的母材不得在工程中使用。
2.2.3 焊接材料2.2.3.1母材焊接所选用的焊丝应符合现行的国家标准《铝及铝合金焊丝》GB/T10858的规定。
2.2.3.2选用焊丝时应综合考虑母材的化学成分、力学性能及使用条件因素,并应符合下列规定。
(1)焊接纯铝时应选用纯度与母材相同或比母材高的焊丝。
(2)焊接铝锰合金时应选用含锰量与母材相近的焊丝或铝硅合金焊丝。
(3)焊接铝镁合金时应选用含镁量与母材相同或比母材高的焊丝。
(4)异种铝及铝合金的焊接应选用与抗拉强度较高的母材相应的焊丝2.2.3.3焊接时所使用的氩气应符合现行的国家标准《纯氩》GB4842的规定。
焊接材料与焊接工艺标准

焊接材料与焊接工艺标准G983《GB/T983-1995 不锈钢焊条》G984《GB/T984-2001 堆焊焊条》G3131《GB/T3131-2001 锡铅焊料》G3323《GB/T 3323-2005 金属熔化焊焊接接头射线照相》G3429《GB/T3429-2002 焊接用钢盘条》G3669《GB/T3669-2001 铝及铝合金焊条》G3670《GB/T3670-1995 铜及铜合金焊条》G5117《GB/T5117-1995 碳钢焊条》G5118《GB/T5118-1995 低合金钢焊条》G5185《GB/T 5185-2005 焊接及相关工艺方法代号》G5293《GB/T5293-1999 埋弧焊用碳钢焊丝和焊剂》G6417.1《GB/T 6417.1-2005 金属熔化焊接头缺欠分类及说明》G6417.2《GB/T 6417.2-2005 金属压力焊接头缺欠分类及说明》G8012《GB/T8012-2000 铸造锡铅焊料》G8110《GB/T8110-1995 气体保护焊用碳钢、低合金钢焊丝》G9448《GB/T9448-1999 焊接与切割安全》G9491《GB/T9491-2002 锡焊用液态焊剂》G10045《GB/T10045-2001 碳钢药芯焊丝》G10046《GB/T10046-2000 银钎料》G12467《GB/T12467.1~4-1998 焊接质量要求金属材料的熔化焊》G12470《GB/T12470-2003 低合金埋弧焊用焊剂》G14693《GB/T14693-1993 焊缝无损检测符号》G15169《GB/T15169-2003 钢熔化焊手焊工资格考试方法》G15620《GB/T15620-1995 镍及镍合金焊丝》G15747《GB/T15747-1995 正面角焊缝接头拉伸试验方法》G15830《GB/T15830-1995 钢制管道对接环焊缝超声波探伤方法和检验》G16672《GB/T16672-1996 焊缝-工作位置-倾角和转角的定义》G17493《GB/T17493-1998 低合金钢药芯焊丝》G17853《GB/T17853-1999 不锈钢药芯焊丝》G17854《GB/T17854-1999 埋弧焊用不锈钢焊丝和焊剂》G18290.2《GB/T18290.2-2000 无焊连接:无焊压连连接一般要求》G18290.3《GB/T18290.3-2000 无焊连接:可接触无焊绝缘位移连接一般要求》G18290.4《GB/T18290.4-2000 无焊连接:不可接触无焊绝缘位移连接一般要求》G18290.5《GB/T18290.5-2000 无焊连接:无焊压入式连接一般要求》G18591《GB/T18591-2001 焊接预热温度、道间温度及预热维持温度的测量指南》G18762《GB/T18762-2002 贵金属及其合金钎料》G19418《GB/T19418-2003 钢的弧焊接头缺陷质量分级指南》G19419《GB/T19419-2003 焊接管理任务与职责》G19804《GB/T 19804-2005 焊接结构的一般尺寸公差和形位公差》G19805《GB/T 19805-2005 焊接操作工技能评定》G19866《GB/T 19866-2005 焊接工艺规程及评定的一般原则》G19867.1《GB/T 19867.1-2005 电弧焊焊接工艺规程》G19868.1《GB/T 19868.1-2005 基于试验焊接材料的工艺评定》G19868.2《GB/T 19868.2-2005 基于焊接经验的工艺评定》G19868.3《GB/T 19868.3-2005 基于标准焊接规程的工艺评定》G19868.4《GB/T 19868.4-2005 基于预生产焊接试验的工艺评定》G19869.1《GB/T 19869.1-2005 钢、镍及镍合金的焊接工艺评定试验》G19897.1《GB/T 19897.1-2005 自动抄表系统低层通信协议:直接本地数据交换》G19897.3《GB/T 19897.3-2005 自动抄表系统低层通信协议:异步数据交换的物理层服务进程》GJ294A《GJB294A-2005 铝及铝合金熔焊技术条件》GJ607A《GJB607A-1998 金属材料及其焊件的爆炸试验规程》GJ724A《GJB/Z724A-1998 不锈钢电阻点焊和焊缝质量检验》GJ1138《GJB1138-1999 铝及铝合金焊丝规范》GJ1718A《GJB1718A-2005 电子束焊接》GJ3021《GJB 3021-1997 航空用结构钢焊丝规范》GJ3785《GJB3785-1999 航空用不锈钢焊丝规范》GJ5162《GJB5162-2003 镍-金基合金高温钎料规范》WJ2613《WJ 2613-2003 兵器铝合金焊接技术要求》QJ2844《QJ2844-1996 铝及铝合金硬钎焊技术条件》QJ2864《QJ2864-1997 铝及铝合金熔焊工艺规范》QJ2868《QJ2868-1997 二氧化碳气体保护半自动焊工艺规范》QJ2845《QJ 2845-1996 铝及铝合金硬钎焊工艺》QJ3040《QJ3040-1998 焊缝建档规定》QJ3071《QJ3071-1998 等离子弧焊技术条件》QJ3072《QJ3072-1998 铝合金铸件补焊工艺规范》QJ3090《QJ3090-1999 焊接材料复验规定》QJ3115《QJ3115-1999 导管熔焊接头角焊缝X射线照相检验方法》QJ3116《QJ3116-1999 金属熔焊内部缺陷X射线照相参考底片》H238《HB/Z238-1993 高温合金电阻点焊和缝焊工艺》H309《HB/Z309-1997 高温合金及不锈钢真空钎焊》H315《HB/Z315-1998 高温合金、不锈钢真空电子束焊接工艺》H328《HB/Z328-1998 镁合金铸件补焊工艺及检验》H345《HB/Z345-2002 铝合金铸件补焊工艺及检验》H346《HB/Z346-2002 熔模铸造钢铸件补焊工艺及检验》H348《HB/Z348-2001 钛及钛合金铸件补焊工艺及检验》H459《HB 459-2004 航空用结构钢焊条规范》H5134《HB/Z 5134-2000 结构钢和不锈钢熔焊工艺》H5135《HB 5135-2000 结构钢和不锈钢熔焊接头质量检验》H5299《HB5299-1996 航空工业手工熔焊焊工技术考核》H5363《HB5363-1995 焊接工艺质量控制》H6771《HB 6771-1993 银基钎料》H6772《HB 6772-1993 镍基钎料》H7052《HB 7052-1994 铝基钎料》H7053《HB 7053-1994 铜基钎料》H7575《HB7575-1997 高温合金及不锈钢真空钎焊质量检验》H7608《HB7608-1998 高温合金、不锈钢真空电子束焊接质量检验》J3168《JB/T3168.1~3-1999 喷焊合金粉末》J3223《JB/T3223-1996 焊接材料质量管理规程》J4291《JB/T4291-1999 焊接接头裂纹张开位移(COD)试验方法》J6963《JB/T6963-1993 钢制熔化焊工艺评定》J6964《JB/T6964-1993 特细碳钢焊条》J6966《JB/T6966-1993 钎缝外观质量评定方法》J6967《JB/T6967-1993 电渣焊通用技术条件》J6975《JB/T6975-1993 自熔合金喷焊技术条件》J7520《JB/T7520.1~6-1994 磷铜钎料化学分析方法》J7524《JB/T7524-1994 建筑钢结构焊缝超声波探伤》J7716《JB/T7716-1995 焊接接头四点弯曲疲劳试验方法》J7717《JB/T7717-1995 焊接接头ECO试验方法》J7853《JB/T7853-1995 铬镍奥氏体不锈钢焊缝金属中铁素体数的测量》J7948《JB/T7948.1~12-1999 熔炼焊剂化学分析方法》J7949《JB/T7949-1999 钢结构焊缝外形尺寸》J8423《JB/T8423-1996 电焊条焊接工艺性能评定方法》J8428《JB/T8428-1996 校正钢焊缝超声检测仪用标准试块》J8931《JB/T8931-1999 堆焊层超声波探伤方法》J9185《JB/T9185-1999 钨极惰性气体保护焊工艺方法》J9186《JB/T9186-1999 二氧化碳气体保护焊工艺方法》J9212《JB/T9212-1999 常压钢质油罐焊缝超声波探伤》J10045《JB/T10045.1~5-1999 热切割》J10375《JB/T10375-2002 焊接物件振动时效工艺参数选择及技术要求》J50076《JB/T50076-1999 气体保护电弧焊用碳钢,低合金钢焊丝产品质量分等》J50193《JB/T50193-1999 银钎料产品质量分等》J50194《JB/T50194-1999 锡铅焊料产品质量分等》J56050《JB/T56050-1999 铜基钎料产品质量分等》J56097《JB/T56097-1999 碳素钢埋弧焊用焊剂产品质量分等》J56098《JB/T56098-1999 铝及铝合金焊丝产品质量分等》J56099《JB/T56099-1999 铜及铜合金焊丝产品质量分等》J56100《JB/T56100-1999 堆焊焊条产品质量分等》J56101《JB/T56101-1999 铸铁焊条产品质量分等》J56102.1《JB/T56102.1-1999 碳钢焊条产品质量分等》J56102.2《JB/T56102.2-1999 低合金钢焊条产品质量分等》J56102.3《JB/T56102.3-1999 不锈钢焊条产品质量分等》TB2374《TB/T2374-1999 铁路机车车辆用耐钢焊条和焊丝》SH3520《SH/T3520-2004 石油化工工程铬钼耐热钢管道焊接技术规程》SH3525《SH/T3525-2004 石油化工低温钢焊接规程》SH3526《SH/T3526-2004 石油化工异种钢焊接规程》SH3527《SH3527-1999 石油化工不锈钢复合钢钢焊接规程》DL678《DL/T678-1999 电站钢结构焊接通用技术条件》DL754《DL/T754-2001 铝母线焊接技术规程》DL816《DL/T816-2003 电力工业焊接操作技能教师资格考核规则》DL819《DL/T819-2002 火力发电厂焊接热处理技术规程》DL833《DL/T833-2003 民用核承压设备焊工资格考核规则》DL868《DL/T 868-2004 焊接工艺评定规程》DL869《DL/T 869-2004 火力发电厂焊接技术规程》JG11《JG11-1999 钢网架焊接球接点》JG3034.1《JG/T3034.1-1996 焊接球节点钢网架焊缝超声波探伤及质量分级法》JG3034.2《JG/T3034.2-1996 螺栓球节点钢网架焊缝超声波探伤及质量分级法》YB5092《YB/T5092-1996 焊接用不锈钢丝》YB9259《YB/T9259-1998 冶金工程建设焊工考试规程》YS458《YS/T458-2003 轨道车辆结构用铝合金挤压型材配用焊丝》SJ10534《SJ/T10534-1994 波峰焊接技术要求》SJ11168《SJ/T11168-1998 免清洗焊接用焊锡丝》SJ11186《SJ/T11186-1998 锡铅膏状焊料通用规范》SJ11216《SJ/T11216-1999 红外/热风再流焊接技术要求》SJ11273《SJ/T11273-2002 免清洗液态助焊剂》SH3520《SH/T3520-2004 石油化工工程铬钼耐热钢管道焊接技术规程》SH3523《SH/T 3523-1999 石油化工铬镍奥氏体钢、铁镍合金和镍合金管道焊接规程》SH3524《SH/T3524-1999 石油化工钢制塔式容器现场组焊施工工艺标准》SH3525《SH/T3525-2004 石油化工低温钢焊接规程》SH3526《SH/T3526-2004 石油化工异种钢焊接规程》SH3527《SH3527-1999 石油化工不锈钢复合钢钢焊接规程》SY0059《SY/T0059-1999 控制钢制设备焊缝硬度防止硫化物应力开裂》焊93《焊接标准汇编》(1993~1995)(96机械版)焊96《焊接标准汇编》(1996~1999)(2000机械版)焊39《焊接材料标准汇编》(1992~1999)(2001机械版)。
铝及铝合金熔焊通用焊接工艺规范探析
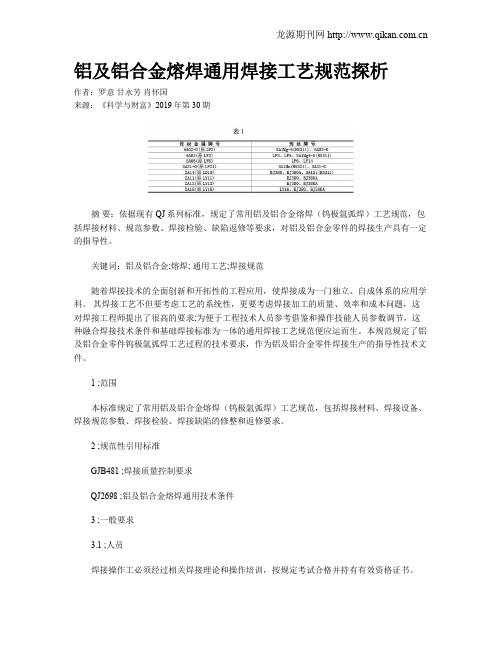
铝及铝合金熔焊通用焊接工艺规范探析作者:罗意甘永芳肖怀国来源:《科学与财富》2019年第30期摘要:依据现有QJ系列标准,规定了常用铝及铝合金熔焊(钨极氩弧焊)工艺规范,包括焊接材料、规范参数、焊接检验、缺陷返修等要求,对铝及铝合金零件的焊接生产具有一定的指导性。
关键词:铝及铝合金;熔焊; 通用工艺;焊接规范随着焊接技术的全面创新和开拓性的工程应用,使焊接成为一门独立、自成体系的应用学科。
其焊接工艺不但要考虑工艺的系统性,更要考虑焊接加工的质量、效率和成本问题,这对焊接工程师提出了很高的要求;为便于工程技术人员参考借鉴和操作技能人员参数调节,这种融合焊接技术条件和基础焊接标准为一体的通用焊接工艺规范便应运而生。
本规范规定了铝及铝合金零件钨极氩弧焊工艺过程的技术要求,作为铝及铝合金零件焊接生产的指导性技术文件。
1 ;范围本标准规定了常用铝及铝合金熔焊(钨极氩弧焊)工艺规范,包括焊接材料、焊接设备、焊接规范参数、焊接检验、焊接缺陷的修整和返修要求。
2 ;规范性引用标准GJB481 ;焊接质量控制要求QJ2698 ;铝及铝合金熔焊通用技术条件3 ;一般要求3.1 ;人员焊接操作工必须经过相关焊接理论和操作培训,按规定考试合格并持有有效资格证书。
3.2 ;设备3.2.1 ;焊接设备应符合GJB481第6条规定。
3.2.2 ;氩弧焊焊接电源应选用能方便调节焊接参数,并能在所需焊接参数下稳定工作。
3.2.3 ;焊接设备应在有效的鉴定使用期内。
3.3 ;焊接环境铝合金零件焊接一般要求在:温度≥15℃,相对湿度≤65%,且环境洁净的条件下进行。
3.4 ;场地焊接场地不允许有穿堂风,且有足够照明。
3.5 ;焊接材料3.5.1 ;填充焊丝设计文件有规定的按设计文件执行,设计文件未规定的可参照表1选择。
3.5.2 ;焊丝的保管焊丝应按牌号、规格分类保管;使用不同标记以便区别,保证在使用中不用错。
3.5.3 ;保护气体焊接用气体采用高纯氩气,纯度99.999%;当瓶装气体的压力低于0.2MPa时不允许使用。
铝合金铸件缺陷胶粘修复工艺规范(修补工艺)
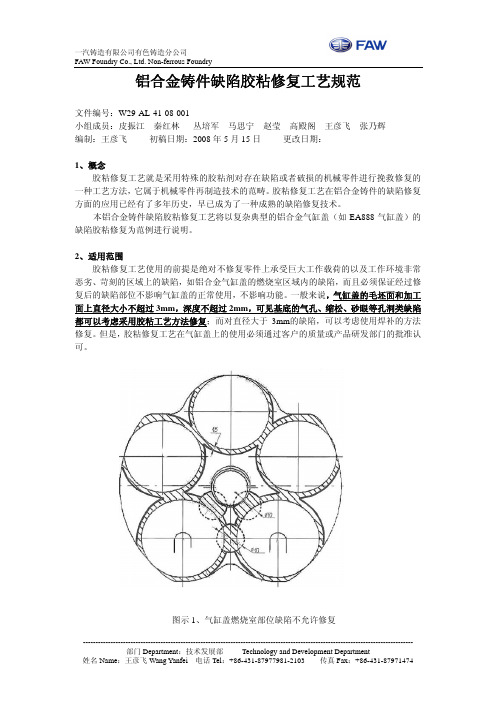
铝合金铸件缺陷胶粘修复工艺规范文件编号:W29-AL-41-08-001小组成员:皮振江秦红林丛培军马思宁赵莹高殿阁王彦飞张乃辉编制:王彦飞初稿日期:2008年5月15日更改日期:1、概念胶粘修复工艺就是采用特殊的胶粘剂对存在缺陷或者破损的机械零件进行挽救修复的一种工艺方法,它属于机械零件再制造技术的范畴。
胶粘修复工艺在铝合金铸件的缺陷修复方面的应用已经有了多年历史,早已成为了一种成熟的缺陷修复技术。
本铝合金铸件缺陷胶粘修复工艺将以复杂典型的铝合金气缸盖(如EA888气缸盖)的缺陷胶粘修复为范例进行说明。
2、适用范围胶粘修复工艺使用的前提是绝对不修复零件上承受巨大工作载荷的以及工作环境非常恶劣、苛刻的区域上的缺陷,如铝合金气缸盖的燃烧室区域内的缺陷,而且必须保证经过修复后的缺陷部位不影响气缸盖的正常使用,不影响功能。
一般来说,气缸盖的毛坯面和加工面上直径大小不超过3mm,深度不超过2mm,可见基底的气孔、缩松、砂眼等孔洞类缺陷都可以考虑采用胶粘工艺方法修复;而对直径大于3mm的缺陷,可以考虑使用焊补的方法修复。
但是,胶粘修复工艺在气缸盖上的使用必须通过客户的质量或产品研发部门的批准认可。
图示1、气缸盖燃烧室部位缺陷不允许修复3、工艺流程3.1缺陷形式和部位确定由质保部检查员对可以采用胶粘工艺进行修复的有缺陷的气缸盖进行判定分离,并在缺陷部位用彩笔明确标识,放在专门的工位器具上,待指定的专业人员进行挽救修复。
图示2、缺陷部位用蓝色彩笔明确标出3.2缺陷部位表面预处理对缺陷部位先采用打磨、钻孔或抛光等方法清理掉缺陷部位处的氧化皮、氧化渣等可能会影响胶粘强度的杂质,然后用压缩空气吹干净,就可准备涂胶。
特别要注意的是,因为油污对胶粘效果的影响非常大,所以操作过程中必须避免缺陷部位粘有油污。
如果缺陷部位的厚度在5mm和8mm之间,则预处理深度不能超过3mm;如果缺陷部位厚度大于8mm,则预处理深度最大可以达到4mm。
GB标准汇总
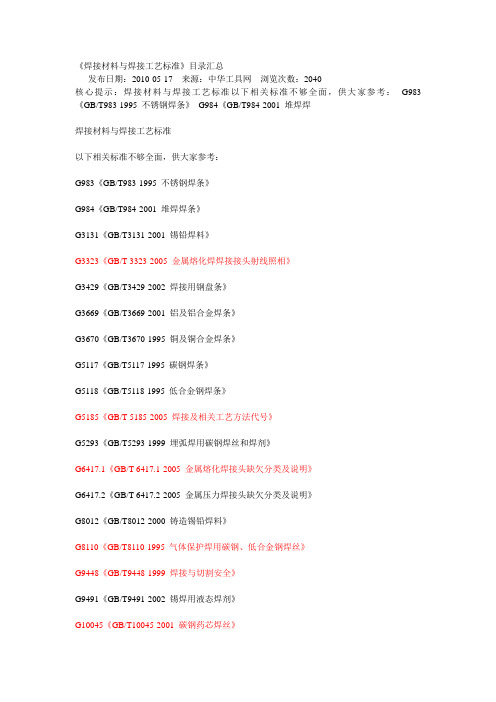
《焊接材料与焊接工艺标准》目录汇总发布日期:2010-05-17 来源:中华工具网浏览次数:2040核心提示:焊接材料与焊接工艺标准以下相关标准不够全面,供大家参考:G983《GB/T983-1995 不锈钢焊条》G984《GB/T984-2001 堆焊焊焊接材料与焊接工艺标准以下相关标准不够全面,供大家参考:G983《GB/T983-1995 不锈钢焊条》G984《GB/T984-2001 堆焊焊条》G3131《GB/T3131-2001 锡铅焊料》G3323《GB/T 3323-2005 金属熔化焊焊接接头射线照相》G3429《GB/T3429-2002 焊接用钢盘条》G3669《GB/T3669-2001 铝及铝合金焊条》G3670《GB/T3670-1995 铜及铜合金焊条》G5117《GB/T5117-1995 碳钢焊条》G5118《GB/T5118-1995 低合金钢焊条》G5185《GB/T 5185-2005 焊接及相关工艺方法代号》G5293《GB/T5293-1999 埋弧焊用碳钢焊丝和焊剂》G6417.1《GB/T 6417.1-2005 金属熔化焊接头缺欠分类及说明》G6417.2《GB/T 6417.2-2005 金属压力焊接头缺欠分类及说明》G8012《GB/T8012-2000 铸造锡铅焊料》G8110《GB/T8110-1995 气体保护焊用碳钢、低合金钢焊丝》G9448《GB/T9448-1999 焊接与切割安全》G9491《GB/T9491-2002 锡焊用液态焊剂》G10045《GB/T10045-2001 碳钢药芯焊丝》G10046《GB/T10046-2000 银钎料》[page]G12467《GB/T12467.1~4-1998 焊接质量要求金属材料的熔化焊》G12470《GB/T12470-2003 低合金埋弧焊用焊剂》G14693《GB/T14693-1993 焊缝无损检测符号》G15169《GB/T15169-2003 钢熔化焊手焊工资格考试方法》G15620《GB/T15620-1995 镍及镍合金焊丝》G15747《GB/T15747-1995 正面角焊缝接头拉伸试验方法》G15830《GB/T15830-1995 钢制管道对接环焊缝超声波探伤方法和检验》G16672《GB/T16672-1996 焊缝-工作位置-倾角和转角的定义》G17493《GB/T17493-1998 低合金钢药芯焊丝》G17853《GB/T17853-1999 不锈钢药芯焊丝》G17854《GB/T17854-1999 埋弧焊用不锈钢焊丝和焊剂》G18290.2《GB/T18290.2-2000 无焊连接:无焊压连连接一般要求》G18290.3《GB/T18290.3-2000 无焊连接:可接触无焊绝缘位移连接一般要求》G18290.4《GB/T18290.4-2000 无焊连接:不可接触无焊绝缘位移连接一般要求》G18290.5《GB/T18290.5-2000 无焊连接:无焊压入式连接一般要求》G18591《GB/T18591-2001 焊接预热温度、道间温度及预热维持温度的测量指南》G18762《GB/T18762-2002 贵金属及其合金钎料》G19418《GB/T19418-2003 钢的弧焊接头缺陷质量分级指南》G19419《GB/T19419-2003 焊接管理任务与职责》G19804《GB/T 19804-2005 焊接结构的一般尺寸公差和形位公差》G19805《GB/T 19805-2005 焊接操作工技能评定》G19866《GB/T 19866-2005 焊接工艺规程及评定的一般原则》G19867.1《GB/T 19867.1-2005 电弧焊焊接工艺规程》G19868.1《GB/T 19868.1-2005 基于试验焊接材料的工艺评定》G19868.2《GB/T 19868.2-2005 基于焊接经验的工艺评定》G19868.3《GB/T 19868.3-2005 基于标准焊接规程的工艺评定》G19868.4《GB/T 19868.4-2005 基于预生产焊接试验的工艺评定》G19869.1《GB/T 19869.1-2005 钢、镍及镍合金的焊接工艺评定试验》G19897.1《GB/T 19897.1-2005 自动抄表系统低层通信协议:直接本地数据交换》[page]G19897.3《GB/T 19897.3-2005 自动抄表系统低层通信协议:异步数据交换的物理层服务进程》图书中国机械工业标准汇编(第二版):金属无损检测与探伤卷(上)目录: —、通用与综合GB/T5616—1985常规无损探伤应用导则GB/T6417—1986金属熔化焊焊缝缺陷分类及说明GB/T9445—1999无损检测人员资格鉴定与认证GB/T12469—1990焊接质量保证钢熔化焊接头的要求和缺陷分级GB/T14693—1993焊缝无损检测符号JB4730—1994压力容器无损检测JB/T5000.14—1998重型机械通用技术条件铸钢件无损探伤JB/T5000.15—>998重型机械通用技术条件锻钢件无损探伤JB/T7406.2—1994试验机术语无损检测仪器JB/T9095—1999离心机、分离机锻焊件常规无损探伤技术规范二、表面方法GB/T5097—1985黑光源的间接评定方法GB/T9443—1988铸钢件渗透探伤及缺陷显示迹痕的评级方法GB/T9444—1988铸钢件磁粉探伤及质量评级方法GB/T10121—1988钢材塔形发纹磁粉检验方法GB/T12604.3—1990无损检测术语渗透检测GB/T12604.5—1990无损检测术语磁粉检测GB/T15147—1994核燃料组件零部件的渗透检验方法GB/T15822—1995磁粉探伤方法GB/T16673—1996无损检测用黑光源(UV—A)辐射的测量GB/T17455—1998无损检测表面检查的金相复制件技术GB/T18851—2002无损检测渗透检验标准试块JB/T5391—1991铁路机车车辆滚动轴承零件磁粉探伤规程JB/T5442—1991压缩机重要零件的磁粉探伤JB/T6061—1992焊缝磁粉检验方法和缺陷磁痕的分级JB/TGJ294A《GJB294A-2005 铝及铝合金熔焊技术条件》GJ607A《GJB607A-1998 金属材料及其焊件的爆炸试验规程》GJ724A《GJB/Z724A-1998 不锈钢电阻点焊和焊缝质量检验》GJ1138《GJB1138-1999 铝及铝合金焊丝规范》GJ1718A《GJB1718A-2005 电子束焊接》GJ3021《GJB 3021-1997 航空用结构钢焊丝规范》GJ3785《GJB3785-1999 航空用不锈钢焊丝规范》GJ5162《GJB5162-2003 镍-金基合金高温钎料规范》WJ2613《WJ 2613-2003 兵器铝合金焊接技术要求》QJ2844《QJ2844-1996 铝及铝合金硬钎焊技术条件》QJ2864《QJ2864-1997 铝及铝合金熔焊工艺规范》QJ2868《QJ2868-1997 二氧化碳气体保护半自动焊工艺规范》QJ2845《QJ 2845-1996 铝及铝合金硬钎焊工艺》QJ3040《QJ3040-1998 焊缝建档规定》QJ3071《QJ3071-1998 等离子弧焊技术条件》QJ3072《QJ3072-1998 铝合金铸件补焊工艺规范》QJ3090《QJ3090-1999 焊接材料复验规定》QJ3115《QJ3115-1999 导管熔焊接头角焊缝X射线照相检验方法》QJ3116《QJ3116-1999 金属熔焊内部缺陷X射线照相参考底片》H238《HB/Z238-1993 高温合金电阻点焊和缝焊工艺》H309《HB/Z309-1997 高温合金及不锈钢真空钎焊》H315《HB/Z315-1998 高温合金、不锈钢真空电子束焊接工艺》[page] H328《HB/Z328-1998 镁合金铸件补焊工艺及检验》H345《HB/Z345-2002 铝合金铸件补焊工艺及检验》H346《HB/Z346-2002 熔模铸造钢铸件补焊工艺及检验》H348《HB/Z348-2001 钛及钛合金铸件补焊工艺及检验》H459《HB 459-2004 航空用结构钢焊条规范》H5134《HB/Z 5134-2000 结构钢和不锈钢熔焊工艺》H5135《HB 5135-2000 结构钢和不锈钢熔焊接头质量检验》H5299《HB5299-1996 航空工业手工熔焊焊工技术考核》H5363《HB5363-1995 焊接工艺质量控制》H6771《HB 6771-1993 银基钎料》H6772《HB 6772-1993 镍基钎料》H7052《HB 7052-1994 铝基钎料》H7053《HB 7053-1994 铜基钎料》H7575《HB7575-1997 高温合金及不锈钢真空钎焊质量检验》H7608《HB7608-1998 高温合金、不锈钢真空电子束焊接质量检验》J3168《JB/T3168.1~3-1999 喷焊合金粉末》J3223《JB/T3223-1996 焊接材料质量管理规程》J4291《JB/T4291-1999 焊接接头裂纹张开位移(COD)试验方法》J6963《JB/T6963-1993 钢制熔化焊工艺评定》J6964《JB/T6964-1993 特细碳钢焊条》J6966《JB/T6966-1993 钎缝外观质量评定方法》J6967《JB/T6967-1993 电渣焊通用技术条件》J6975《JB/T6975-1993 自熔合金喷焊技术条件》J7520《JB/T7520.1~6-1994 磷铜钎料化学分析方法》J7524《JB/T7524-1994 建筑钢结构焊缝超声波探伤》J7716《JB/T7716-1995 焊接接头四点弯曲疲劳试验方法》J7717《JB/T7717-1995 焊接接头ECO试验方法》J7853《JB/T7853-1995 铬镍奥氏体不锈钢焊缝金属中铁素体数的测量》J7948《JB/T7948.1~12-1999 熔炼焊剂化学分析方法》J7949《JB/T7949-1999 钢结构焊缝外形尺寸》[page]J8423《JB/T8423-1996 电焊条焊接工艺性能评定方法》J8428《JB/T8428-1996 校正钢焊缝超声检测仪用标准试块》J8931《JB/T8931-1999 堆焊层超声波探伤方法》J9185《JB/T9185-1999 钨极惰性气体保护焊工艺方法》J9186《JB/T9186-1999 二氧化碳气体保护焊工艺方法》J9212《JB/T9212-1999 常压钢质油罐焊缝超声波探伤》J10045《JB/T10045.1~5-1999 热切割》J10375《JB/T10375-2002 焊接物件振动时效工艺参数选择及技术要求》J50076《JB/T50076-1999 气体保护电弧焊用碳钢,低合金钢焊丝产品质量分等》J50193《JB/T50193-1999 银钎料产品质量分等》J50194《JB/T50194-1999 锡铅焊料产品质量分等》J56050《JB/T56050-1999 铜基钎料产品质量分等》J56097《JB/T56097-1999 碳素钢埋弧焊用焊剂产品质量分等》J56098《JB/T56098-1999 铝及铝合金焊丝产品质量分等》J56099《JB/T56099-1999 铜及铜合金焊丝产品质量分等》J56100《JB/T56100-1999 堆焊焊条产品质量分等》J56101《JB/T56101-1999 铸铁焊条产品质量分等》J56102.1《JB/T56102.1-1999 碳钢焊条产品质量分等》J56102.2《JB/T56102.2-1999 低合金钢焊条产品质量分等》J56102.3《JB/T56102.3-1999 不锈钢焊条产品质量分等》TB2374《TB/T2374-1999 铁路机车车辆用耐钢焊条和焊丝》SH3520《SH/T3520-2004 石油化工工程铬钼耐热钢管道焊接技术规程》SH3525《SH/T3525-2004 石油化工低温钢焊接规程》SH3526《SH/T3526-2004 石油化工异种钢焊接规程》SH3527《SH3527-1999 石油化工不锈钢复合钢钢焊接规程》DL678《DL/T678-1999 电站钢结构焊接通用技术条件》DL754《DL/T754-2001 铝母线焊接技术规程》DL816《DL/T816-2003 电力工业焊接操作技能教师资格考核规则》DL819《DL/T819-2002 火力发电厂焊接热处理技术规程》[page]DL833《DL/T833-2003 民用核承压设备焊工资格考核规则》DL868《DL/T 868-2004 焊接工艺评定规程》DL869《DL/T 869-2004 火力发电厂焊接技术规程》JG11《JG11-1999 钢网架焊接球接点》JG3034.1《JG/T3034.1-1996 焊接球节点钢网架焊缝超声波探伤及质量分级法》JG3034.2《JG/T3034.2-1996 螺栓球节点钢网架焊缝超声波探伤及质量分级法》YB5092《YB/T5092-1996 焊接用不锈钢丝》YB9259《YB/T9259-1998 冶金工程建设焊工考试规程》YS458《YS/T458-2003 轨道车辆结构用铝合金挤压型材配用焊丝》SJ10534《SJ/T10534-1994 波峰焊接技术要求》SJ11168《SJ/T11168-1998 免清洗焊接用焊锡丝》SJ11186《SJ/T11186-1998 锡铅膏状焊料通用规范》SJ11216《SJ/T11216-1999 红外/热风再流焊接技术要求》SJ11273《SJ/T11273-2002 免清洗液态助焊剂》SH3520《SH/T3520-2004 石油化工工程铬钼耐热钢管道焊接技术规程》SH3523《SH/T 3523-1999 石油化工铬镍奥氏体钢、铁镍合金和镍合金管道焊接规程》SH3524《SH/T3524-1999 石油化工钢制塔式容器现场组焊施工工艺标准》SH3525《SH/T3525-2004 石油化工低温钢焊接规程》SH3526《SH/T3526-2004 石油化工异种钢焊接规程》SH3527《SH3527-1999 石油化工不锈钢复合钢钢焊接规程》SY0059《SY/T0059-1999 控制钢制设备焊缝硬度防止硫化物应力开裂》焊93《焊接标准汇编》(1993~1995)(96机械版)焊96《焊接标准汇编》(1996~1999)(2000机械版)焊39《焊接材料标准汇编》(1992~1999)(2001机械版)[page]本篇文章来源于中华工具网(/) 原文链接:/news/show-21785.html。
铝合金熔炼与铸造工艺规范与流程

铝合金熔炼与铸造工艺规范与流程Revised by Chen Zhen in 2021铝合金熔炼与铸造工艺规范与流程资料来源:全球铝业网铝业知识频道一、铝合金熔炼规范(1)总则①按本文件生产的铸件,其化学成分和力学性能应符合GB/T 9438-1999《铝合金铸件》、JISH 5202-1999《铝合金铸件》、ASTM B 108-03a《铝合金金属型铸件》、GB/T 15115-1994《压铸铝合金》、JISH 5302-2006《铝合金压铸件》、ASTM B 85-03《铝合金压铸件》、EN1706-1998《铸造铝合金》等标准的规定。
②本文件所指的铝合金熔炼,系在电阻炉、感应炉及煤气(天然气)炉内进行。
一般采取石墨坩埚或铸铁坩埚。
铸铁坩埚须进行液体渗铝。
(2)配料及炉料1)配料计算①镁的配料计算量:用氯盐精炼时,应取上限,用无公害精炼剂精炼时,可适当减少;也可根据实际情况调整加镁量。
②铝合金压铸时,为了减少压铸时粘模现象,允许适当提高铁含量,但不得超过有关标准的规定。
2)金属材料及回炉料①新金属材料铝锭:GB/T 1196-2002《重熔用铝锭》铝硅合金锭:GB/T 8734-2000《铸造铝硅合金锭》镁锭: GB 3499-1983《镁锭》铝铜中间合金:YS/T 282-2000《铝中间合金锭》铝锰中间合金:YS/T 282-2000《铝中间合金锭》各牌号的预制合金锭:GB/T 8733-2000《铸造铝合金锭》、JISH 2117-1984《铸件用再生铝合金锭》、ASTM B 197-03《铸造铝合金锭》、JISH 2118-2000《压铸铝合金锭》、EN1676-1996《铸造铝合金锭》等。
②回炉料包括化学成分明确的废铸件、浇冒口和坩埚底剩料,以及溢流槽和飞边等破碎的重熔锭。
回炉料的用量一般不超过80%,其中破碎重熔料不超过30%;对于不重要的铸件可全部使用回炉料;对于有特殊要求(气密性等)的铸件回炉料用量不超过50% 。
超高韧铝镁合金铸件焊补技术研究

超高韧铝镁合金铸件焊补技术研究发布时间:2022-05-05T01:38:09.014Z 来源:《中国科技信息》2022年1月2期作者:王德峰[导读] 对于某超高韧铝镁合金工件补焊易出现热裂纹现象,经金相研究王德峰中国航发哈尔滨东安发动机有限公司,黑龙江哈尔滨 150066摘要:对于某超高韧铝镁合金工件补焊易出现热裂纹现象,经金相研究,根据相关理论全面探究其产生机理,且组织了多种焊补方法测试,最后选择热处理后焊补工艺,处理了工件补焊缺陷,增大了焊补合格率。
关键词:超高韧镁铝材料;焊补工艺;力学性能铝镁合金是目前应用最广的轻金属结构材料,具有密度低、比强度和刚强度高、阻尼减震性好、导热性好、机加工性能优良、零件尺寸稳定、易回收等优点。
在航空航天、汽车等领域有着广泛的应用。
随着对零配件总体性与复杂性要求的提升,大量镁铝合金复杂整体结构件选择采取铸造工艺生产。
但是因为铝镁合金存在收缩率高、补缩性差等特征,导致在铸造完成后经常出现气孔、缩松、氧化、冷隔等缺陷。
由于铝镁合金存在易氧化,收缩率大等特征,导致铝镁合金工件焊补困难,容易出现热裂纹,经常由于一个较小的问题焊补不达标而造成产品废弃。
1、合金性能特征1.1化学成分这种铝镁合金工件的化学成分范围标准与测试成分如表1所示。
通过表1得知,合金对主元素镁及铜成分范围标准很高,镁成分范围标准仅有0.6%,但镁在熔炼环节容易烧损,所以很难控制。
1.2材料力学性能超高韧铝镁合金最大的性质即具备良好的韧性,其伸展率在铸态就能超过20%,T4态、T6态加工后还能提升3%-8%,但其他铝合金通常伸展率均小于5%,极少有超出10%的。
而超高韧铝镁合金的防拉强度与屈服强度相较于其他合金毫不逊色。
2、缺陷分析超高韧铝镁合金是总体厚壁1.5cm的薄壁繁琐结构工件,铸造困难,经多次电脑模拟与实际测试工艺调节,铸造方法基本固定,处理了工件疏松、夹渣、气孔与偏析等缺陷,但有些铸件依旧出产生砂孔、夹渣、单一气孔等小问题[1]。
铝合金焊接通用工艺规范(定版)
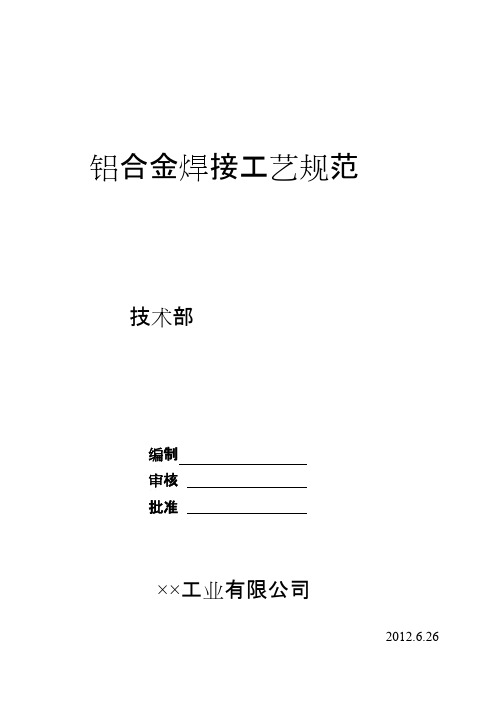
12~14
8~10
Ⅰ形
3
1~2
4
4
1~2
5
5
2
5
2 2~3 2~3
150~180 180~200 180~240
14~18 14~18 16~20
10~14
10~14
12~16
Y形
6~8 2~3
5~6
3
260~320
18~24
14~18
8~12 2~3
6
3~4
300~360
18~24
14~18
、、 预防焊接缺陷,获得优质焊接接头的措施
相变时产生较多的脆性相,还要使熔池保护足够的时间,有利于氢气的逸出。
5.5采用适当的夹具、压板,同时选择合理的焊接顺序(如对称焊、跳焊、逐步退焊等),
以防止和减少变形。
5.6当焊件从中心向外进行焊接时,具有大收缩量的焊缝宜先施焊,整条焊道应连续焊
完。必要时采取反变形方法,并应留有收缩余量。
5.7电弧擦伤处的弧坑需经打磨,使其均匀过渡到母材表面,当打磨后的母材厚度小于规
定值时,则需补焊。
5.8接弧处应保证焊透和熔合。
六、焊缝检验
-5-
6.1焊接结束,清理焊缝表面的飞溅和污物后,所有焊缝进行100%外观检查。 6.2焊缝表面不得有裂纹、未熔合、夹渣、气孔、未焊透、咬边等缺陷。 6.3焊缝表面余高不低于母材,一般余高为0~1.0mm,焊缝宽度比坡口每侧增宽0.5~1.5m
铝合金焊接工艺规范
技术部
编制 审核 批准
××工业有限公司
2012.6.26
-1-
前言
本规范根据××工业有限公司,定制与实施设计规范、工艺规范、试验规范的要 求,按《企业标准编写的一般规定》,为明确铝合金焊接的工艺要求而制定。
铝合金焊接通用工艺规范定版
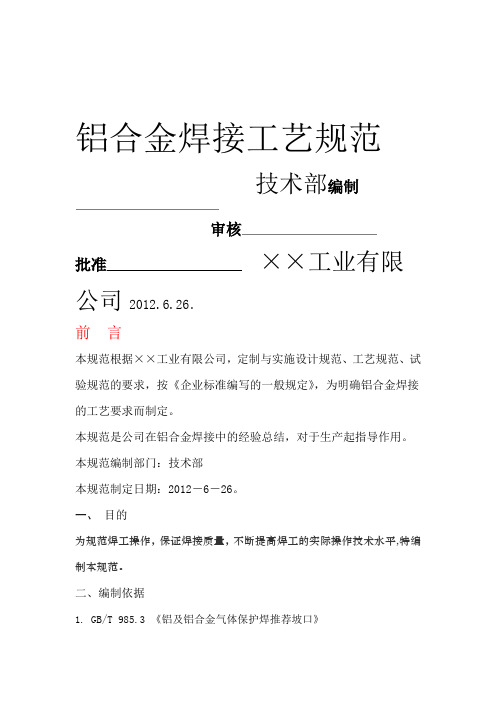
铝合金焊接工艺规范技术部编制审核批准××工业有限公司2012.6.26.前言本规范根据××工业有限公司,定制与实施设计规范、工艺规范、试验规范的要求,按《企业标准编写的一般规定》,为明确铝合金焊接的工艺要求而制定。
本规范是公司在铝合金焊接中的经验总结,对于生产起指导作用。
本规范编制部门:技术部本规范制定日期:2012-6-26。
一、目的为规范焊工操作,保证焊接质量,不断提高焊工的实际操作技术水平,特编制本规范。
二、编制依据1. GB/T 985.3 《铝及铝合金气体保护焊推荐坡口》2. GB/T10858-2008《铝及铝合金焊丝》3. GB/T24598-2009《铝及铝合金熔化焊焊工技能评定》4. GBT3199-2007 《铝及铝合金加工产品贮存及包装》5. GBT22087-2008《铝及铝合金弧焊接头缺欠质量》6.有关产品设计图纸三、焊前准备3.1 焊接材料铝板 3A21(原LF21)及铝合金型材。
焊丝:S311铝硅焊丝 ER4043 直径φ2,φ3,焊丝应有制造长的质量合格证,领取和发放由管理员统一管理。
铝硅焊丝抗裂性好,通用性大。
氩气3.2氩气瓶上应贴有出厂合格标签,其纯度≥99.99%,所用流量8-16升/分钟,气瓶中的氩气不能用尽,瓶内余压不得低于0.5MPa ,以保证充氩纯度。
氩气应符合GB/T4842-1995。
3.3 焊接工具①采用交流电焊机,本厂用WSME-315(J19)。
②选用的氩气减压流量计应开闭自如,没有漏气现象。
切记不可先开流量计、后开气瓶,造成高压气流直冲低压,损坏流量计;关时先关流量计而后关氩气瓶。
③输送氩气的胶皮管,不得与输送其它气体的胶皮管互相串用,可用新的氧气胶皮管代用,长度不超过30米。
3.4 其它工器具焊工应备有:手锤、砂纸、扁铲、钢丝刷、电磨工具等,以备清渣和消除缺陷。
3.5 焊前清理①化学清理:效率高,清理质量稳定,焊件清理范围一般为坡口及其两边各100mm区域,用干净棉纱蘸丙酮溶液擦拭或用8%-10%的NaOH溶液浸泡,去除油污并干燥。
铸件修补操作工艺规程

福 田 雷 沃 重 工
农业装备事业本部
铸件修补操作工艺规程
T-01-2040-079 共5页
第1页
适用范围:此工艺规范适用于拖拉机发动机缸体、飞轮壳体、变速箱壳体、后桥壳体等各类铸造件毛坯缺陷修补的具体操作及注意事项。
1、铸件可修补性分析
序号 缺陷类型 实物图片
可修补性分析 备注 1
砂眼、夹砂
修补时,清砂困难,杂物难以清除,修补效果不好,不建议进行修补。
2 裂纹
裂纹修补,由于焊补溶深
浅,可能对后期壳体使用带来安全隐患,不建议进行修补。
3 气孔
气孔是最常见的毛坯缺陷,所占比例较大,修补便于操作,效果好,确定为主要修补对象。
4 缩孔、缩松
缩松往往面积大而分散,无法进行修补。
标记 处数 更改文件号 签字
日期 标记 处数 更改文件号 签字 日期 编制/日期 校对/日期
审核/日期 标准化/日期 批准/日期
缩松
缩孔。
铝合金焊接通用工艺规范标准
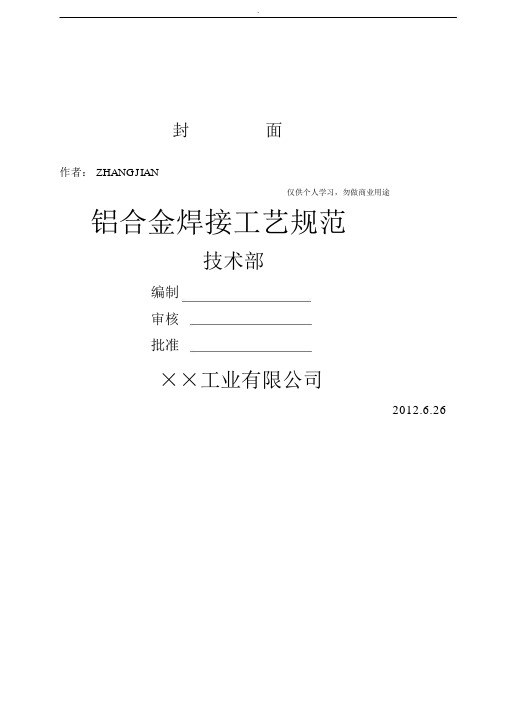
.封面作者: ZHANGJIAN仅供个人学习,勿做商业用途铝合金焊接工艺规范技术部编制审核批准××工业有限公司2012.6.26. . ..前言本规范根据××工业有限公司,定制与实施设计规范、工艺规范、试验规范的要求,按《企业标准编写的一般规定》,为明确铝合金焊接的工艺要求而制定。
文档来自于网络搜索本规范是公司在铝合金焊接中的经验总结,对于生产起指导作用。
本规范编制部门:技术部本规范制定日期: 2012-6-26。
.一、目的为规范焊工操作,保证焊接质量,不断提高焊工的实际操作技术水平 , 特编制本规范。
二、编制依据1.GB/T 985.3 《铝及铝合金气体保护焊推荐坡口》2.GB/T10858-2008 《铝及铝合金焊丝》3.GB/T24598-2009 《铝及铝合金熔化焊焊工技能评定》4.GBT3199-2007 《铝及铝合金加工产品贮存及包装》5.GBT22087-2008《铝及铝合金弧焊接头缺欠质量》6.有关产品设计图纸三、焊前准备3.1 焊接材料铝板 3A21( 原LF21)及铝合金型材。
焊丝: S311铝硅焊丝 ER4043直径φ 2,φ 3,焊丝应有制造长的质量合格证,领取和发放由管理员统一管理。
铝硅焊丝抗裂性好,通用性大。
3.2 氩气氩气瓶上应贴有出厂合格标签,其纯度≥99.99%,所用流量 8-16 升 / 分钟,气瓶中的氩气不能用尽,瓶内余压不得低于 0.5MPa ,以保证充氩纯度。
氩气应符合GB/T4842-1995。
3.3焊接工具①采用交流电焊机,本厂用WSME-315(J19)。
②选用的氩气减压流量计应开闭自如,没有漏气现象。
切记不可先开流量计、后开气瓶,造成高压气流直冲低压,损坏流量计;关时先关流量计而后关氩气瓶。
③输送氩气的胶皮管,不得与输送其它气体的胶皮管互相串用,可用新的氧气胶皮管代用,长度不超过 30米。
3.4其它工器具焊工应备有:手锤、砂纸、扁铲、钢丝刷、电磨工具等,以备清渣和消除缺陷。
铝及铝合金焊接施工工艺标准.doc
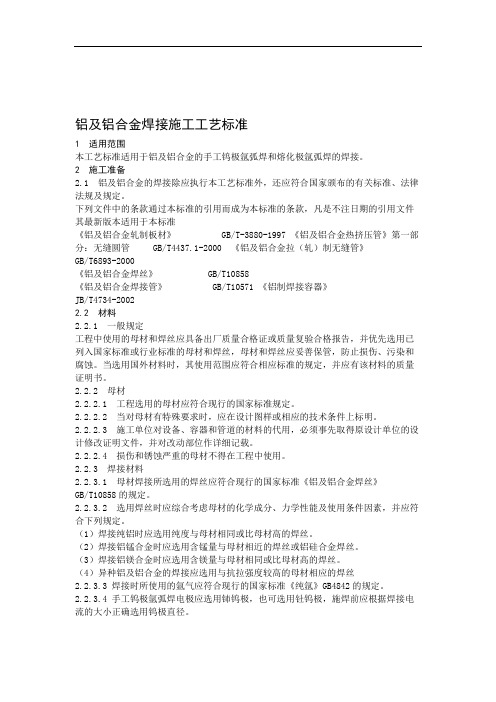
铝及铝合金焊接施工工艺标准1 适用范围本工艺标准适用于铝及铝合金的手工钨极氩弧焊和熔化极氩弧焊的焊接。
2 施工准备2.1 铝及铝合金的焊接除应执行本工艺标准外,还应符合国家颁布的有关标准、法律法规及规定。
下列文件中的条款通过本标准的引用而成为本标准的条款,凡是不注日期的引用文件其最新版本适用于本标准《铝及铝合金轧制板材》 GB/T-3880-1997 《铝及铝合金热挤压管》第一部分:无缝圆管 GB/T4437.1-2000 《铝及铝合金拉(轧)制无缝管》GB/T6893-2000《铝及铝合金焊丝》 GB/T10858《铝及铝合金焊接管》 GB/T10571 《铝制焊接容器》JB/T4734-20022.2 材料2.2.1 一般规定工程中使用的母材和焊丝应具备出厂质量合格证或质量复验合格报告,并优先选用已列入国家标准或行业标准的母材和焊丝,母材和焊丝应妥善保管,防止损伤、污染和腐蚀。
当选用国外材料时,其使用范围应符合相应标准的规定,并应有该材料的质量证明书。
2.2.2 母材2.2.2.1 工程选用的母材应符合现行的国家标准规定。
2.2.2.2 当对母材有特殊要求时,应在设计图样或相应的技术条件上标明。
2.2.2.3 施工单位对设备、容器和管道的材料的代用,必须事先取得原设计单位的设计修改证明文件,并对改动部位作详细记载。
2.2.2.4 损伤和锈蚀严重的母材不得在工程中使用。
2.2.3 焊接材料2.2.3.1 母材焊接所选用的焊丝应符合现行的国家标准《铝及铝合金焊丝》GB/T10858的规定。
2.2.3.2 选用焊丝时应综合考虑母材的化学成分、力学性能及使用条件因素,并应符合下列规定。
(1)焊接纯铝时应选用纯度与母材相同或比母材高的焊丝。
(2)焊接铝锰合金时应选用含锰量与母材相近的焊丝或铝硅合金焊丝。
(3)焊接铝镁合金时应选用含镁量与母材相同或比母材高的焊丝。
(4)异种铝及铝合金的焊接应选用与抗拉强度较高的母材相应的焊丝2.2.3.3 焊接时所使用的氩气应符合现行的国家标准《纯氩》GB4842的规定。
铝及铝合金焊接-规范文件-

+ 铝及铝合金在液态能溶解大量的氢,固态几乎不溶解氢。在 焊接熔池凝固和快速冷却的过程中,氢来不及溢出,极易形 成氢气孔。
几乎各种焊接方法都可以用于焊接铝及铝合金,但是铝 及铝合金对各种焊接方法的适应性不同,各种焊接方法有其 各自的应用场合。
+ 焊后热处理
铝容器一般焊后不要求热处理。如果 所用铝材在容器接触的介质条件下确有明 显的应力腐蚀敏感性,需要通过焊后热处 理以消除较高的焊接应力,来使容器上的 应力降低到产生应力腐蚀开裂的临界应力 以下,这时应由容器设计文件提出特别要 求,才进行焊后消除应力热处理。
+ 坡口的处理 板厚在3 mm 以下的对接焊缝可不开坡口,只需在焊缝背
面倒一0. 5~1 mm 的角即可,这样有利于气体的排放和避 免背面凹槽。背面是否倒角对焊缝的影响。
铝合金厚板的坡口角度较 钢板的要大。单边坡口一般采用
55°坡口,双边坡口采用每边35°坡 口。这样可以使焊接的可达性提
高,同时可降低未熔合缺陷的产生
+ 铝及铝合金的焊接特点 + 铝及铝合金焊接方法 + 铝及铝合金焊接材料 + 焊前准备 + 焊后处理
+ 铝在空气中及焊接时极易氧化,生成的氧化铝(Al2O3)熔 点高、非常稳定,不易去除。
+ 铝及铝合金的热导率和比热Байду номын сангаас均约为碳素钢和低合金钢的两 倍多。
+ 铝及铝合金的线膨胀系数约为碳素钢和低合金钢的两倍。
+ 保护气体 保护气体为氩气、氦气或其混合气。交流加高频
铝及铝合金焊接规程

铝及铝合金焊接规程用。
铝及铝合金焊接规程是为了确保铝及铝合金焊接的质量,适用于铝及铝合金制单层、衬铝的铝焊接工艺。
在焊接前需要注意以下几点:首先,焊接用氩气的纯度应≥99.99%,露点≤-55℃,符合GB/T4842或GB的规定。
瓶装氩气的压力≤0.5Mpa时不宜使用,因为氩气内含氮量≥0.04%会导致焊缝表面上产生氮化镁及气孔,含氧量≥0.03%会导致熔池表面上出现密集的黑点、电弧不稳和飞溅较大,含水量≥0.07%会导致熔池沸腾并产生气孔。
其次,手工钨极氩弧焊电极采用铈钨电极。
电极直径应根据焊接电流大小来选择,电极端部应为半球形。
如果钨极被铝污染,则必须重新打磨或更换钨极;轻微污染时,可增大电流使电弧在试板燃烧一会,即能烧掉污染物。
铝及铝合金焊接规程中提供了铈钨电极直径和对应的焊接电流。
第三,MIG焊铝合金时,不允许使用带齿轮的送丝轮和推丝式,送丝软管应使用聚四氟乙烯或尼龙制品,以免磨削污染或堵塞软管。
MIG通常使用直流反极性。
第四,焊剂主要作用是去除氧化膜和其它一些杂质,使用时可用无水酒精调成糊状或直接将焊剂粉放在坡口和两侧。
在焊接角焊缝时应选用那些焊后容易清除熔渣的焊剂;铝镁合金用焊剂不宜含有钠的组成物。
最后,不同牌号的铝材相焊时,按耐腐蚀性能较好和强度级别较低的母材去选择焊丝材料。
在焊接铝镁合金或铝锰合金等耐蚀铝合金时,宜采用含镁量或含锰时与母材相近或比母材稍高的焊丝。
焊丝可从GB/T《铝及铝合金焊丝》选用。
本文介绍了如何选择适合的铝焊接用焊丝。
选择焊丝时可以参考GB/T3190和GB/T3197标准。
表格中列出了同牌号铝焊接用焊丝、异种铝焊丝、针对不同材料和性能要求推荐的焊丝以及一般用途焊接时焊丝的选择。
这些表格可以帮助焊接工程师选择适合的焊丝,以确保焊接质量和性能。
应用丙酮或其他合适的清洗剂清洗干净。
5.焊接前应根据铝材的不同种类、厚度、形状和用途选择合适的焊接方法、焊接位置、焊接工艺和焊接参数,并进行试焊,以确定最佳的焊接工艺参数。
铸件焊补工安全操作规程范文

铸件焊补工安全操作规程范文第一章总则第一条为了保证铸件焊补工作安全,保障工人的生命财产安全,提高工作效率和质量,制定本规程。
第二条本规程适用于所有进行铸件焊补工作的人员。
第三条铸件焊补工是指对铸件进行修补、补焊或加固等工艺操作。
第四条铸件焊补工作应符合国家相关法律法规和标准的要求。
第五条铸件焊补工作应遵守安全第一的原则,操作人员要时刻保持高度的安全意识。
第六条所有从事铸件焊补工作的人员必须参加相关的安全培训,了解本规程的内容,并遵守规程中的各项要求。
第七条对于违反本规程的行为将给予相应的纪律处分,严重者将追究法律责任。
第二章工作环境安全第八条铸件焊补工作场所应具备良好的通风条件,确保工人的健康和安全。
第九条铸件焊补工作场所应保持清洁干燥,杂物堆放整齐,防止滑倒或其他意外伤害的发生。
第十条铸件焊补工作场所应配备必要的物品,如灭火器、眼镜、工作手套、护目镜等。
并定期检查这些物品的有效性。
第十一条铸件焊补工作场所应设置明显的安全警示标志,提醒工人注意安全。
第十二条铸件焊补工作场所应保持良好的照明条件,以确保工人的正常操作和观察。
第十三条铸件焊补工作场所应设置明显的从业人员进出口,严禁无关人员进入。
第三章个人防护措施第十四条所有从事铸件焊补工作的人员必须穿戴个人防护装备,包括工作服、安全帽、隔热防护手套、防护眼镜等。
第十五条在进行高温焊接操作时,必须佩戴隔热手套和防护面具,并采取隔离措施,防止烧伤。
第十六条在进行电焊作业时,必须佩戴防护眼镜,防止眼睛受到明火和碎屑的伤害。
第十七条焊补工人必须随时保持清醒状态,不得饮酒或服用药物。
第十八条任何情况下,焊接操作人员都不得穿过焊丝或割断焊丝电源线。
第十九条工作结束时,焊接操作人员必须将电源开关关闭,并拔掉电源插头。
第二十条焊接操作人员在工作过程中应根据需要穿戴防护服装,防止外界物质对身体的伤害。
第四章设备安全第二十一条铸件焊补工作所使用的设备必须符合国家安全标准,经过合格的检验,杜绝设备故障引发的事故。
铝合金焊接工艺设计规范

铝合金电弧焊工艺设计规范2014- - 发布 2015- - 实施目录前言 (2)范围 (3)规范性引用文件 (3)铝合金电弧焊主要工艺参数及影响因素 (3)钎焊主要工艺参数的设计规范 (6)1范围本标准规范了公司铝交换器(铝散热器、中冷器)铝合金电弧焊焊接参数对焊接质量的影响因素、及焊接参数工艺设计的选择和调节方向。
2规范性引用文件下列文件对于本文件的应用是必不可少的。
凡是注日期的引用文件,仅注日期更改的版本适用于本文件。
凡是不注日期的引用文件,其最新版本(包括所有的修改单)适用于本文件。
GBT3375-1994 焊接术语GBT3669-2001T 铝及铝合金焊条GBT10858-89铝及铝合金焊丝GBT22086-2008 铝及铝合金弧焊推荐工艺JBT9185-1999钨极惰性气体保护焊工艺方法4.钨极惰性气体保护焊主要工艺参数的影响因素4.1电流种类与极性4.1.1钨极惰性气体保护焊使用的电流种类可分为直流正接、直流反接电流种类直流交流(对称的)直流正接直流反接示意图熔深特点深、窄浅、宽中等电极热量分布工件70% 钨极30% 工件30% 钨极70% 工件50%钨极50% 钨极许用电流最大小较大阴极清理作用无有有(工件为负时)适用材料除铝、镁外金属一般不采用铝、镁、铝青铜等4.1.2.1直流正极性的特点:钨极发射电子,带走大量的逸出功,钨极本身温度不高,烧损小,同样直径钨极可使用较大电流,电弧稳定而集中,熔深大,焊接质量好,4.1.2.2直流反极性的特点:钨极吸收电子,钨极本身温度高,烧损大,同样大小直径的钨极许用电流要小的多,电流密度小,熔深浅而宽。
但在质量很大的氩正离子的高速撞击下可清除铝、镁等易氧化金属表面形成的氧化膜,有阴极清理即“清洁”作用。
4.1.3清洁作用通常情况下,铝板或镁板表面有一层很明显的氧化膜。
即使工件金属熔化后,此膜也呈固体状浮在表面上(既不熔化),为达到良好的焊接效果,就需要清除此膜。
铝合金的焊工工艺步骤

铝合金的焊工工艺步骤
铝合金的焊接工艺步骤如下:
1. 准备工作:首先要将铝合金零件清洗干净,去除表面油污和氧化物,使其表面干燥,然后根据焊接零件的设计要求进行加工和安装。
2. 选择焊接方法:根据铝合金零件的材质、形状、大小和焊接要求等,选择适合的焊接方法,如TIG、MIG、氢气焊等。
3. 确定焊接参数:根据所选择的焊接方法和一系列焊接因素,确定焊接电流、焊接速度、焊接温度、气体流量、焊接杆等参数。
4. 装配电极:根据焊接要求,选用适当规格的电极,并将其装配到焊接设备上。
5. 开始焊接:启动设备,进入焊接程序,开始焊接。
在焊接的过程中要注意电极与焊接材料之间的距离和角度,保持焊接电弧稳定,焊接位置和焊接质量的一致性。
6. 检查焊接质量:焊接完成后,对焊缝进行检查。
包括焊缝的均匀性、焊缝的强度、气孔、缺陷等的检查。
7. 收尾工作:修剪焊接余料,清理焊接面,保持环境清洁,将设备归位或存放
好。
以上是铝合金的一般焊接工艺步骤,具体步骤可能会因不同的情况而有所不同。
焊接铝合金需要技术要求较高,需要有丰富的经验和专业技能。