铝合金铸件补焊工艺
铝合金材料焊接工艺方法
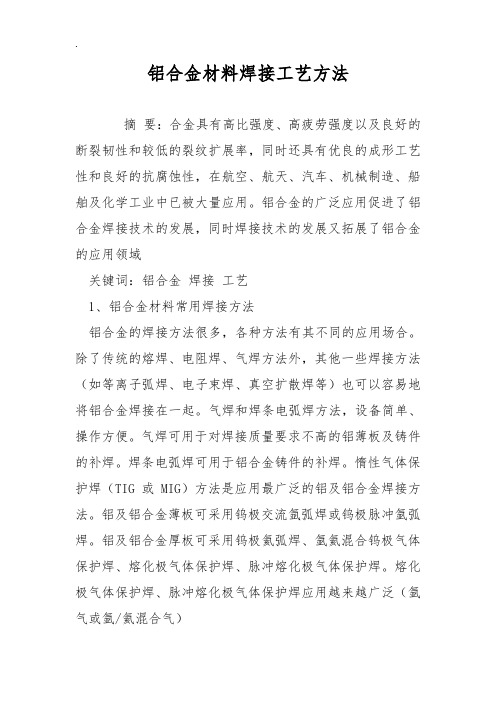
铝合金材料焊接工艺方法摘要:合金具有高比强度、高疲劳强度以及良好的断裂韧性和较低的裂纹扩展率,同时还具有优良的成形工艺性和良好的抗腐蚀性,在航空、航天、汽车、机械制造、船舶及化学工业中已被大量应用。
铝合金的广泛应用促进了铝合金焊接技术的发展,同时焊接技术的发展又拓展了铝合金的应用领域关键词:铝合金焊接工艺1、铝合金材料常用焊接方法铝合金的焊接方法很多,各种方法有其不同的应用场合。
除了传统的熔焊、电阻焊、气焊方法外,其他一些焊接方法(如等离子弧焊、电子束焊、真空扩散焊等)也可以容易地将铝合金焊接在一起。
气焊和焊条电弧焊方法,设备简单、操作方便。
气焊可用于对焊接质量要求不高的铝薄板及铸件的补焊。
焊条电弧焊可用于铝合金铸件的补焊。
惰性气体保护焊(TIG或MIG)方法是应用最广泛的铝及铝合金焊接方法。
铝及铝合金薄板可采用钨极交流氩弧焊或钨极脉冲氩弧焊。
铝及铝合金厚板可采用钨极氦弧焊、氩氦混合钨极气体保护焊、熔化极气体保护焊、脉冲熔化极气体保护焊。
熔化极气体保护焊、脉冲熔化极气体保护焊应用越来越广泛(氩气或氩/氦混合气)2、焊接质量控制2.1焊前预备(1)焊件清洗铝在空气中及焊接时极易氧化,生成的氧化铝(Al2O3)熔点高、非常稳定,不易去除。
阻碍母材的熔化和熔合,氧化膜的比重大,不易浮出表面,易生成夹渣、未熔合、未焊透等缺欠。
在铝合金焊接时,焊前应严格清除工件焊口及焊丝表面的氧化膜和油污。
常采用化学清洗和机械清理两种方法化学清洗化学清洁是运用碱或酸清��工件外表,该法既可去掉氧化膜,还可除油污,化学清洗效率高,质量稳定,适用于清理焊丝及尺寸不大、成批生产的工件。
可用浸洗法和擦洗法两种。
浸洗法详细技术进程如下:体积分数为6%~10%的氢氧化钠溶液,在70℃摆布浸泡0.5min→水洗→体积分数为15%的硝酸在常温下浸泡1min进行中和处理→水洗→温水洗→枯燥。
洗好后的铝合金外表为无光泽的银白色机械清理在工件尺寸较大、生产周期较长、多层焊或化学清洗后又沾污时,常采用机械清理。
铝合金铸件缺陷胶粘修复工艺规范(修补工艺)
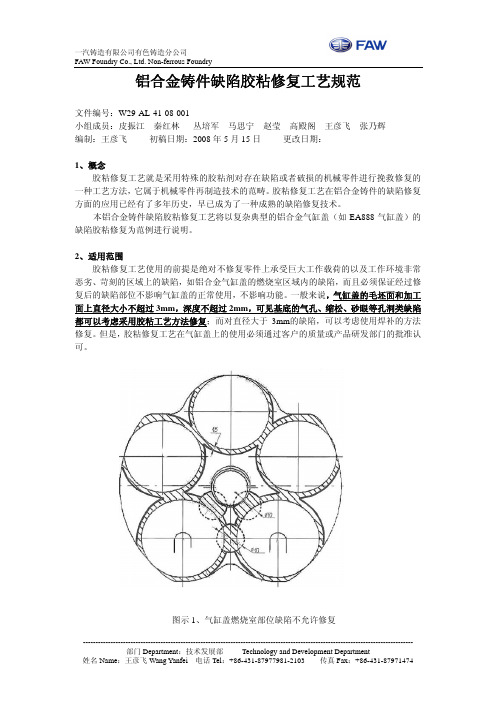
铝合金铸件缺陷胶粘修复工艺规范文件编号:W29-AL-41-08-001小组成员:皮振江秦红林丛培军马思宁赵莹高殿阁王彦飞张乃辉编制:王彦飞初稿日期:2008年5月15日更改日期:1、概念胶粘修复工艺就是采用特殊的胶粘剂对存在缺陷或者破损的机械零件进行挽救修复的一种工艺方法,它属于机械零件再制造技术的范畴。
胶粘修复工艺在铝合金铸件的缺陷修复方面的应用已经有了多年历史,早已成为了一种成熟的缺陷修复技术。
本铝合金铸件缺陷胶粘修复工艺将以复杂典型的铝合金气缸盖(如EA888气缸盖)的缺陷胶粘修复为范例进行说明。
2、适用范围胶粘修复工艺使用的前提是绝对不修复零件上承受巨大工作载荷的以及工作环境非常恶劣、苛刻的区域上的缺陷,如铝合金气缸盖的燃烧室区域内的缺陷,而且必须保证经过修复后的缺陷部位不影响气缸盖的正常使用,不影响功能。
一般来说,气缸盖的毛坯面和加工面上直径大小不超过3mm,深度不超过2mm,可见基底的气孔、缩松、砂眼等孔洞类缺陷都可以考虑采用胶粘工艺方法修复;而对直径大于3mm的缺陷,可以考虑使用焊补的方法修复。
但是,胶粘修复工艺在气缸盖上的使用必须通过客户的质量或产品研发部门的批准认可。
图示1、气缸盖燃烧室部位缺陷不允许修复3、工艺流程3.1缺陷形式和部位确定由质保部检查员对可以采用胶粘工艺进行修复的有缺陷的气缸盖进行判定分离,并在缺陷部位用彩笔明确标识,放在专门的工位器具上,待指定的专业人员进行挽救修复。
图示2、缺陷部位用蓝色彩笔明确标出3.2缺陷部位表面预处理对缺陷部位先采用打磨、钻孔或抛光等方法清理掉缺陷部位处的氧化皮、氧化渣等可能会影响胶粘强度的杂质,然后用压缩空气吹干净,就可准备涂胶。
特别要注意的是,因为油污对胶粘效果的影响非常大,所以操作过程中必须避免缺陷部位粘有油污。
如果缺陷部位的厚度在5mm和8mm之间,则预处理深度不能超过3mm;如果缺陷部位厚度大于8mm,则预处理深度最大可以达到4mm。
铝件人工补焊工艺流程
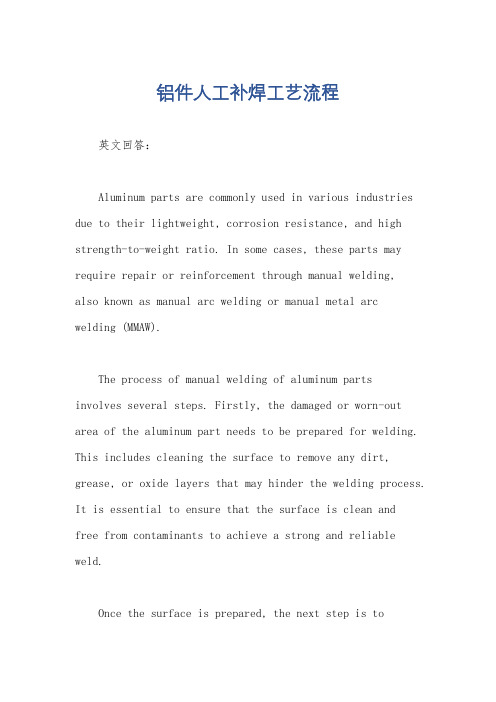
铝件人工补焊工艺流程英文回答:Aluminum parts are commonly used in various industries due to their lightweight, corrosion resistance, and high strength-to-weight ratio. In some cases, these parts may require repair or reinforcement through manual welding,also known as manual arc welding or manual metal arcwelding (MMAW).The process of manual welding of aluminum partsinvolves several steps. Firstly, the damaged or worn-out area of the aluminum part needs to be prepared for welding. This includes cleaning the surface to remove any dirt, grease, or oxide layers that may hinder the welding process. It is essential to ensure that the surface is clean andfree from contaminants to achieve a strong and reliable weld.Once the surface is prepared, the next step is toselect the appropriate welding electrode or filler material. Aluminum welding electrodes are usually made of aluminum alloy and are available in various compositions to matchthe base metal being welded. The choice of electrode depends on factors such as the alloy type, thickness of the aluminum part, and the desired mechanical properties of the weld joint.After selecting the electrode, the welding equipment needs to be set up. This includes adjusting the welding current, polarity, and arc length to achieve the desired weld penetration and heat input. It is important to strikea stable arc and maintain a consistent welding speed to ensure a uniform and defect-free weld.During the welding process, it is crucial to protectthe molten weld pool from atmospheric contamination. Aluminum is highly reactive and readily forms oxide layers when exposed to air. To prevent oxidation, a shielding gasor flux is used. In manual welding of aluminum, a shielding gas such as argon or helium is commonly used to create an inert atmosphere around the weld pool, preventing oxidationand ensuring a clean weld.Once the welding is complete, the weld joint needs to be properly cooled and post-weld treated. This may involve processes such as heat treatment, stress relieving, or surface finishing, depending on the specific requirements of the aluminum part and the intended application.In summary, the manual welding process for aluminum parts involves surface preparation, electrode selection, equipment setup, welding with proper shielding gas, and post-weld treatment. By following these steps and ensuring proper technique, high-quality welds can be achieved, providing the necessary repair or reinforcement to the aluminum part.中文回答:铝件由于其轻质、耐腐蚀性和高强度重量比,在各个行业中得到广泛应用。
铝合金缺陷修复新工艺

铝合金缺陷修复新工艺:1、概述批量生产的低压薄壁容器,零件大部分采用ZL115压差铸造毛坯。
虽然铸件经过X光探伤检测,但是由于结构特征的限制和铸造缺陷的大小与分布的敏感方向不同,有些缺陷在X光片上不能明显呈现出来,常常在机械加工之后发现,有些直径微小的穿透性气孔只能在压力试验之后发现。
这严重影响到产品质量和生产进度,甚至造成巨大经济损失。
一些常规焊补方法均不能很好地满足技术要求。
为了验证该项新工艺对解决铸铝零件机加后所出现的密封性和外观缺陷修复的有效性,寻找出一种铸铝件缺陷修复新途径,我们进行了大量工艺试验和必要的检测,并形成一套正确的铸铝件缺陷修复工艺规程。
2、金属表面修补机的缺陷修复机理由于铝及其合金的化学活泼性很强,表面极易形成氧化膜,且多属于难熔性质(如Al2O3的熔点约为2050℃,MgO的熔点约为2500℃)加之铝及其合金导热性强,焊接时容易造成不熔合现象。
由于氧化膜比重同铝的比重极其接近,所以也容易成为焊缝金属的夹杂物。
同时铝及其合金的线胀系数大,导热性又强,焊接时容易产生翘曲变形。
这是铝及其合金焊接时颇感困难的问题。
目前熔化焊中最常用的氩弧焊是靠“阴极雾化”作用,将氧化膜破碎,在氩气的保护下,使氧化膜不能重新产生。
但是在焊接热处理强化处理后的铝合金时,近缝区存在强度大大削弱的现象,也不可避免的会产生翘曲变形。
金属表面修补机主要用于修复铸造缺陷,它有逆变式高频+脉冲电源、可使焊丝高速旋转的焊枪和控制部分组成。
其修复缺陷的机理为:利用高频+脉冲电压将气体击穿形成等离子气,从而产生温度可达6000℃以上的电火花,电火花将可熔性旋转电极(即焊丝)瞬间(10-5—10-6秒)和与其接触的母材同时熔化,依靠瞬间高温和旋转焊丝与母材的机械摩檫及旋转电场力的综合作用,使氧化膜破碎,在氩气的保护下,使氧化膜不能重新产生,从而完成焊丝与母材的冶金结合。
由于电火花作用时间短,与焊丝直接接触的母材局部熔化,铝的导热性很好,瞬间将输入的热量扩散并散失到空气中,基体几乎不产生温升,从而基体不会变形,精密铸铝件机械加工后进行缺陷的修复,而不会影响尺寸精度。
浅析铝合金CMT补焊工艺研究

应用技术在铝合金焊接中,对焊接结构设计、焊接工艺水平以及材料质量都有很高的要求,若没有控制和掌握焊接工艺,尤其是厚板铝合金焊接中,其温度或是焊道布置没有处理得当,会在实际焊接生产中会出现一些气孔或是焊接热裂纹,存在微小缺陷,而针对重要产品,就必须进行补焊,控制修复次数,不断提高补焊质量,降低重要产品的报废率,进而达到最大的经济效益。
对此,在铝合金焊接中,要不断优化CMT补焊工艺,根据铝合金产品缺陷特征,合理补焊和维修,保证补焊质量,使得产品符合质量标准,以谋求最大的利润空间。
在这样的环境背景下,探究铝合金CMT补焊工艺具有非常重要的现实意义。
1 CMT焊接技术综合分析■1.1 焊接机理CMT焊接技术是依托于MIG/MAG技术的一种崭新焊接技术,在传统焊接短路中,焊丝端部金属会受到焊接电弧热的影响而熔化,在熔滴不断变大后会和焊接熔池相接触,造成短路问题引起焊丝爆断,继而电弧熄灭,形成大飞溅现象。
在CMT焊接技术应用中,焊机电源收集到短路电流信号后,会立即切断电流,焊枪送丝系统会进行回抽焊丝,协助熔滴快速进入到熔池中,以达到无电流状态时的熔滴过渡,防止焊接飞溅问题。
在实际焊接中,CMT焊接技术把熔滴金属朝着焊接熔池进行过渡,融合送丝机构中的送丝运动,焊接开始阶段,向前送丝会点燃电弧,焊丝由于受热熔化而形成熔滴,过渡到焊接熔池中,随后焊接熔池电弧被熄灭,不断降低电流直至短路。
一旦发生短路,CMT焊机电源中的DSP处理器会立即接收到短路信号,并将该信号传输到送丝机构,接收短路信号后,送丝机构会立即响应,开展焊丝回抽运动,使得熔滴完全脱离于焊丝端部,而熔滴可以在无电流环境下进入焊接熔池 ,送丝结构继续进行向前送丝,重新引燃电弧焊接,循环往复这一过程。
■1.2 技术特征相比于传统短路过渡焊接技术而言,CMT焊接技术具有以下特征 :第一,送丝过程与过程控制有效结合。
在CMT焊接技术应用中,焊丝送丝运动和焊接过程控制联系紧密,送丝运动会影响整个焊接过程,而焊接中熔滴过渡也会影响焊丝运动效果,可以说明二者属于相辅相成的关系,相互关联、相互影响。
zl114a铝合金铸件补焊工艺研究
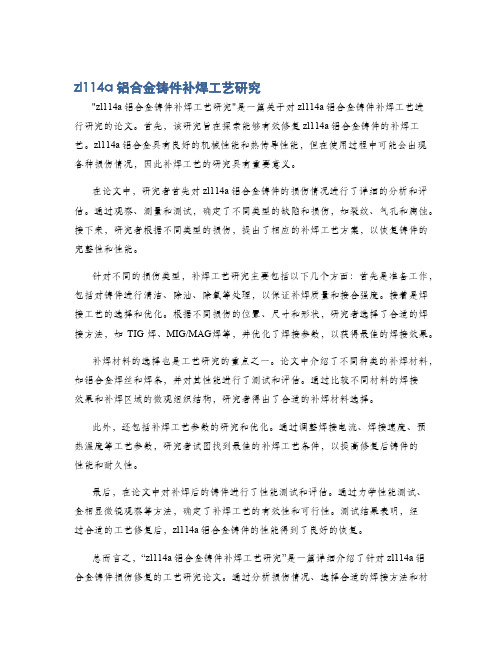
zl114a铝合金铸件补焊工艺研究"zl114a铝合金铸件补焊工艺研究"是一篇关于对zl114a铝合金铸件补焊工艺进行研究的论文。
首先,该研究旨在探索能够有效修复zl114a铝合金铸件的补焊工艺。
zl114a铝合金具有良好的机械性能和热传导性能,但在使用过程中可能会出现各种损伤情况,因此补焊工艺的研究具有重要意义。
在论文中,研究者首先对zl114a铝合金铸件的损伤情况进行了详细的分析和评估。
通过观察、测量和测试,确定了不同类型的缺陷和损伤,如裂纹、气孔和腐蚀。
接下来,研究者根据不同类型的损伤,提出了相应的补焊工艺方案,以恢复铸件的完整性和性能。
针对不同的损伤类型,补焊工艺研究主要包括以下几个方面:首先是准备工作,包括对铸件进行清洁、除油、除氧等处理,以保证补焊质量和接合强度。
接着是焊接工艺的选择和优化。
根据不同损伤的位置、尺寸和形状,研究者选择了合适的焊接方法,如TIG焊、MIG/MAG焊等,并优化了焊接参数,以获得最佳的焊接效果。
补焊材料的选择也是工艺研究的重点之一。
论文中介绍了不同种类的补焊材料,如铝合金焊丝和焊条,并对其性能进行了测试和评估。
通过比较不同材料的焊接效果和补焊区域的微观组织结构,研究者得出了合适的补焊材料选择。
此外,还包括补焊工艺参数的研究和优化。
通过调整焊接电流、焊接速度、预热温度等工艺参数,研究者试图找到最佳的补焊工艺条件,以提高修复后铸件的性能和耐久性。
最后,在论文中对补焊后的铸件进行了性能测试和评估。
通过力学性能测试、金相显微镜观察等方法,确定了补焊工艺的有效性和可行性。
测试结果表明,经过合适的工艺修复后,zl114a铝合金铸件的性能得到了良好的恢复。
总而言之,“zl114a铝合金铸件补焊工艺研究”是一篇详细介绍了针对zl114a铝合金铸件损伤修复的工艺研究论文。
通过分析损伤情况、选择合适的焊接方法和材料,以及优化工艺参数,研究者成功地提出了一套有效的补焊工艺方案,并通过测试证明了其修复效果。
铸钢件缺陷判断及焊补工艺
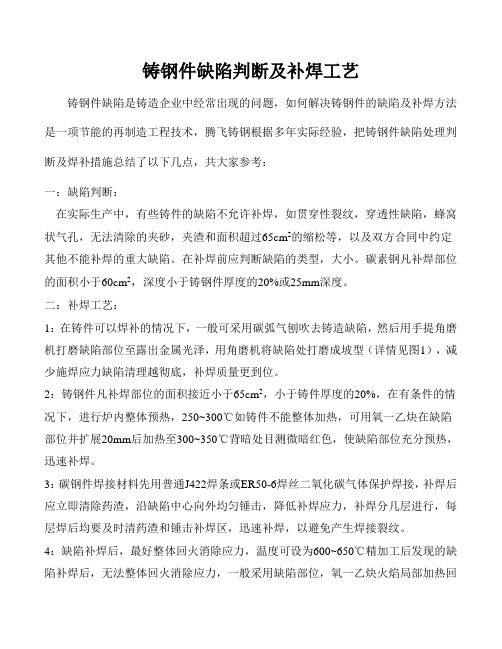
铸钢件缺陷判断及补焊工艺铸钢件缺陷是铸造企业中经常出现的问题,如何解决铸钢件的缺陷及补焊方法是一项节能的再制造工程技术,腾飞铸钢根据多年实际经验,把铸钢件缺陷处理判断及焊补措施总结了以下几点,共大家参考:一:缺陷判断:在实际生产中,有些铸件的缺陷不允许补焊,如贯穿性裂纹,穿透性缺陷,蜂窝状气孔,无法清除的夹砂,夹渣和面积超过65cm2的缩松等,以及双方合同中约定其他不能补焊的重大缺陷。
在补焊前应判断缺陷的类型,大小。
碳素钢凡补焊部位的面积小于60cm2,深度小于铸钢件厚度的20%或25mm深度。
二:补焊工艺:1:在铸件可以焊补的情况下,一般可采用碳弧气刨吹去铸造缺陷,然后用手提角磨机打磨缺陷部位至露出金属光泽,用角磨机将缺陷处打磨成坡型(详情见图1),减少施焊应力缺陷清理越彻底,补焊质量更到位。
2:铸钢件凡补焊部位的面积接近小于65cm2,小于铸件厚度的20%,在有条件的情况下,进行炉内整体预热,250~300℃如铸件不能整体加热,可用氧一乙炔在缺陷部位并扩展20mm后加热至300~350℃背暗处目测微暗红色,使缺陷部位充分预热,迅速补焊。
3:碳钢件焊接材料先用普通J422焊条或ER50-6焊丝二氧化碳气体保护焊接,补焊后应立即清除药渣,沿缺陷中心向外均匀锤击,降低补焊应力,补焊分几层进行,每层焊后均要及时清药渣和锤击补焊区,迅速补焊,以避免产生焊接裂纹。
4:缺陷补焊后,最好整体回火消除应力,温度可设为600~650℃精加工后发现的缺陷补焊后,无法整体回火消除应力,一般采用缺陷部位,氧一乙炔火焰局部加热回火方法,采用大割把中性火焰来回缓慢摆动,将铸件表面加热到目视暗红色。
(约740℃)保温(2min/mm但不少于30min)消除应力处理后立即在缺陷处盖上石棉板,防止产生裂纹。
5:JB/T5263-2005标准中规定,重缺陷补焊后应进行射线或超声波检测,即对于重缺陷和重要补焊,必须进行有效的无损检查,证明合格后方能使用。
铸件补焊通用作业指导书【最新版】

铸件补焊通用作业指导书冷焊非加工面加工面高强度铸铁球墨铸铁22.5 3.2<45~20铸116、铸117、铸308铸116、铸117、铸408铸238、铸408、铸116、铸117(1)焊条直径按待焊补铸件壁厚根据下表选用;(二)焊补程序(2)各类型焊条的冷焊机电流按下表选用;2、缺陷原有形状边缘应适当加工或打磨成坡口形式;1、对铸件待焊部位进行清理;3、选用适合的电焊机和电焊工具;4、根据铸件材质、缺陷大小及焊后要求按下表选用焊条。
焊补特点一般灰铸铁结422、铸100、铸208可选用焊条铸件补焊通用作业指导书焊条直径(mm)铸件壁厚(mm)410~30在客户允许和规定的铸件修补要求的范围内,对铸件出现的砂眼、气孔、缩孔等缺陷,在不影响原铸件的使用性能、寿命和外观的情况下,均可进行修补。
修补工作必须对不同的缺陷和要求,选择适当的方法,按照规定的工艺规程进行。
二、补焊方法(一)焊前准备一、补焊条件铸件补焊通用作业指导书22.53.2456钢芯电焊条80~100100~120130~150铸铁芯电焊条200~280250~350300~420热焊焊条直径(mm)4567电流(A)200~240250~300300~360350~4201、对补焊部位补焊质量进行检查,是否符合要求,不符合时应重新补焊。
2、对补焊部位进行打磨平整。
编制: 审核: 会签: 批准:三、焊后检查及修整(3)钢芯焊条冷焊时,采用“小电流、短路、断续、分散焊”方式操作;(4)铸铁焊条冷焊时,采用“大电流、连续、集中式”方式操作;(5)当焊补厚壁铸件时,可用多层堆焊方式操作;焊条类型焊条直径(mm)(6)当焊补有裂纹倾向的缺陷时,可采用热态锤击法,以减轻初应力。
(一)焊前准备(1)缺陷清理和加工与冷焊基本相同;(2)对于边角部位及穿透缺陷,可用石墨板、石棉布或造型材料等进行塑型;(3)缺陷处预热至500~700℃。
(二)焊补程序(1)热焊用电流按下表选用;8400~480(2)由缺陷最低处开始引弧、引弧后摆动电焊条,用长弧依次熔化缺陷四周,交界处必须熔合良好,对于堆积的熔渣要及时清理掉;(3)当铁水已经超过缺陷顶平面时,应将电弧略为拉长,并沿交界处走几圈。
铝合金的三种焊接方法

铝合金的三种焊接方法铝合金被广泛的运用在工业产品上,因为它具有很好的物理性能,几乎各种焊接方法都可以用于焊接铝及铝合金,但是铝及铝合金对各种焊接方法的适应性不同,各种焊接方法有其各自的应用场合。
由于焊接方法及焊接工艺参数的选取不当,造成铝合金零件焊接后产生严重变形,或因为焊缝气孔、夹渣、未焊透等缺陷,导致焊缝金属裂纹或材质疏松,严重影响了产品质量及性能。
以下小编就带您分析铝合金焊接的方法以及注意事项。
铝合金的三种焊接方法钨极氩弧焊钨极氩弧焊法主要用于铝合金,是一种较好的焊接方法,不过钨极氩弧焊设备较复杂,不合适在露天条件下操作。
电阻点焊、缝焊这种焊接方法可以用来焊接厚度在5mm以下的铝合金薄板。
但是在焊接时用的设备比较复杂,焊接电流大、生产率较高,特别适用于大批量生产的零、部件。
脉冲氩弧焊脉冲氩弧焊可以很好的改善在焊接过程中的稳定性可以调节参数来控制电弧功率和焊缝成形。
焊件变形小、热影响区小,特别适用于薄板、全位置焊接等场合以及对热敏感性强的锻铝、硬铝、超硬铝等的焊接。
铝合金的焊接注意事项1 焊接铝合金前先要清理铝合金表面,不能有油污,尘埃等存在,可以用丙酮清洗铝合金焊接处的表面,厚板铝合金要用钢丝刷清理,之后再加丙酮清洗。
2 在焊接铝合金的时候要先清理铝合金表面,不能有油烟,灰尘等,另外厚板铝合金要用钢丝刷清理,然后再加丙酮清洗。
3 如果板材比较后可以对板材预热,这样可以防止预热不够造成成焊不透,在收弧时要用小电流收弧填坑。
4 焊接时一定要规范,要根据板材的厚度来焊接。
5 焊枪的电缆不要太长,要是太长会造成送丝稳定。
一、焊接材料要求:01 保护气体的选择焊接时所用的保护气体有惰性气体氩气(Ar)和氦气(He),生产上普遍使用氩气。
用于焊接铝及铝合金的氩气必须满足下列纯度(体积分数)要求:氩气大于99.99%,氦气小于0.04%,氧气小于0.03%,水的质量分数小于0.07%。
目前国内生产的氩气,其纯度一般能达到此要求,故在使用前不需再进行提纯处理。
铝合金铸件补焊
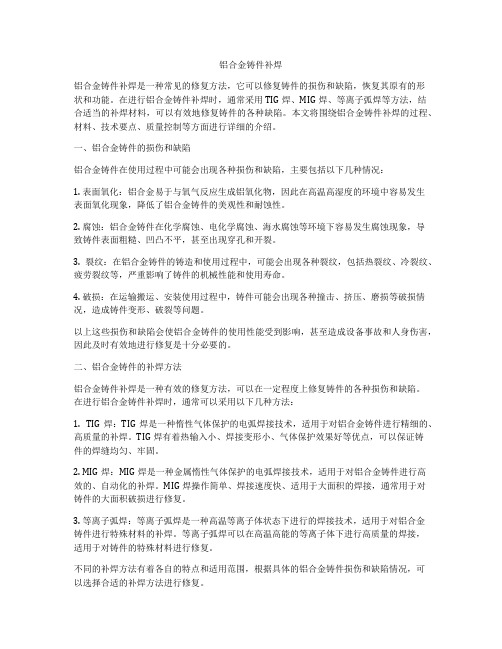
铝合金铸件补焊铝合金铸件补焊是一种常见的修复方法,它可以修复铸件的损伤和缺陷,恢复其原有的形状和功能。
在进行铝合金铸件补焊时,通常采用TIG焊、MIG焊、等离子弧焊等方法,结合适当的补焊材料,可以有效地修复铸件的各种缺陷。
本文将围绕铝合金铸件补焊的过程、材料、技术要点、质量控制等方面进行详细的介绍。
一、铝合金铸件的损伤和缺陷铝合金铸件在使用过程中可能会出现各种损伤和缺陷,主要包括以下几种情况:1. 表面氧化:铝合金易于与氧气反应生成铝氧化物,因此在高温高湿度的环境中容易发生表面氧化现象,降低了铝合金铸件的美观性和耐蚀性。
2. 腐蚀:铝合金铸件在化学腐蚀、电化学腐蚀、海水腐蚀等环境下容易发生腐蚀现象,导致铸件表面粗糙、凹凸不平,甚至出现穿孔和开裂。
3. 裂纹:在铝合金铸件的铸造和使用过程中,可能会出现各种裂纹,包括热裂纹、冷裂纹、疲劳裂纹等,严重影响了铸件的机械性能和使用寿命。
4. 破损:在运输搬运、安装使用过程中,铸件可能会出现各种撞击、挤压、磨损等破损情况,造成铸件变形、破裂等问题。
以上这些损伤和缺陷会使铝合金铸件的使用性能受到影响,甚至造成设备事故和人身伤害,因此及时有效地进行修复是十分必要的。
二、铝合金铸件的补焊方法铝合金铸件补焊是一种有效的修复方法,可以在一定程度上修复铸件的各种损伤和缺陷。
在进行铝合金铸件补焊时,通常可以采用以下几种方法:1. TIG焊:TIG焊是一种惰性气体保护的电弧焊接技术,适用于对铝合金铸件进行精细的、高质量的补焊。
TIG焊有着热输入小、焊接变形小、气体保护效果好等优点,可以保证铸件的焊缝均匀、牢固。
2. MIG焊:MIG焊是一种金属惰性气体保护的电弧焊接技术,适用于对铝合金铸件进行高效的、自动化的补焊。
MIG焊操作简单、焊接速度快、适用于大面积的焊接,通常用于对铸件的大面积破损进行修复。
3. 等离子弧焊:等离子弧焊是一种高温等离子体状态下进行的焊接技术,适用于对铝合金铸件进行特殊材料的补焊。
焊工必备资料-常用的铸铁补焊方法
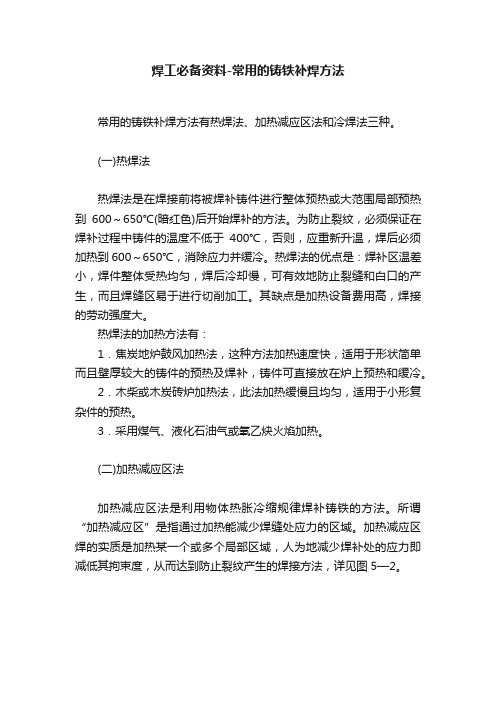
焊工必备资料-常用的铸铁补焊方法常用的铸铁补焊方法有热焊法、加热减应区法和冷焊法三种。
(一)热焊法热焊法是在焊接前将被焊补铸件进行整体预热或大范围局部预热到600~650℃(暗红色)后开始焊补的方法。
为防止裂纹,必须保证在焊补过程中铸件的温度不低于400℃,否则,应重新升温,焊后必须加热到600~650℃,消除应力并缓冷。
热焊法的优点是:焊补区温差小,焊件整体受热均匀,焊后冷却慢,可有效地防止裂缝和白口的产生,而且焊缝区易于进行切削加工。
其缺点是加热设备费用高,焊接的劳动强度大。
热焊法的加热方法有:1.焦炭地炉鼓风加热法,这种方法加热速度快,适用于形状简单而且壁厚较大的铸件的预热及焊补,铸件可直接放在炉上预热和缓冷。
2.木柴或木炭砖炉加热法,此法加热缓慢且均匀,适用于小形复杂件的预热。
3.采用煤气、液化石油气或氧乙炔火焰加热。
(二)加热减应区法加热减应区法是利用物体热胀冷缩规律焊补铸铁的方法。
所谓“加热减应区”是指通过加热能减少焊缝处应力的区域。
加热减应区焊的实质是加热某一个或多个局部区域,人为地减少焊补处的应力即减低其拘束度,从而达到防止裂纹产生的焊接方法,详见图5—2。
加热减应区法与热焊法的区别是:热焊法须将铸件全部或大部分预热,并且焊补区也被预热;而加热减应区法只用气焊火焰预热某一个或几个不大的局部(加热减应区),而焊补区有时不作预热。
加热减应区部位选择的原则是:1.阻碍焊缝金属自由膨胀和收缩的部位,即当该局部加热后,就可使焊缝金属及其它部位有自由膨胀和收缩的可能。
2.加热减应区应与铸件的其它部位联系不多,而且比较牢固。
如边、角部位。
且与焊补区共同受热后冷却时,能够比较自由地与焊补区一同收缩。
减应区可根据需要选择一处或多处。
采取加热减应区法施焊时应注意:加热减应区的加热温度不宜过高,一般不高于750℃,以免使该区性能降低;应在室内避风处焊接;气焊火焰在不焊时要对着空间或减应区,严禁对着其它未焊区域。
铝合金铸件与型材焊接工艺及性能

铝合金铸件与型材焊接工艺及性能摘要:随着国家碳中和、碳达峰要求的提出,在汽车制造工业中,很多大型结构件由传统的黑色金属整体铸造被铝合金、分体式焊接构件所代替。
这是因为焊接零件可以快速地将零散件加工成复杂的结构件,可以显著降低复杂结构件的制造成本;其次,尽管在焊缝处会出现强度软化、存在缺陷等现象,但经过大量的静态疲劳试验及理论验证,焊接件的力学性能优良,完全可以代替复杂整体成形结构件。
关键词:铝合金铸件;型材焊接;工艺;性能1铝合金MIG焊接工艺1.1MIG焊接特点熔化极惰性气体保护焊(MeltInert-gasWelding,MIG焊接)的优点是焊接品质好,因为有保护气体的作用,焊缝品质稳定,焊接件的变形小;MIG焊接还可以采用大的焊接电流,使得焊丝熔化速度快,得到较好的母材熔深,提高焊接速度。
其缺点是没有脱氧去氢,焊缝内部会存在气孔。
因此,MIG焊接对母材及焊丝的洁净度及生产环境要求比较严格。
1.2铝合金MIG焊接工艺采用TPS-4000型焊机,焊丝直径为1.2mm,A356和6082铝合金板材厚度分别为5mm和3mm,坡口为V型,MIG焊接电流为140~160A,焊接速度为0.1~0.15m/s,推进角为15°。
焊接电流是铝合金MIG焊接中最重要的参数。
MIG焊接时,焊接电流一般根据焊件厚度、焊缝位置以及焊丝直径来选择。
当焊丝直径确定后,焊接关键工艺参数还有焊接电流、焊接速度及脉冲强度。
2试验2.1A356及6082铝合金A356铝合金,其Si元素含量较高,铸造性能良好,具有较好的强度与机械加工性能,被广泛应用于铸造领域;6082铝合金属于Al-Mg-Si系合金,主要适用于板材高温冲压领域。
试验中,焊接母材A356铝合金、6082铝合金及ER5356焊丝的化学成分。
2.2试验方案设计为了验证焊接工艺的可靠性,应通过一系列试验方法进行验证。
首先,应先进行焊缝熔透试验、拉伸试验和静态疲劳试验;然后,通过动态疲劳试验,获得准确的焊接件疲劳寿命曲线,并建立A356铸件和6082型材焊接件疲劳寿命曲线的数学模型,预测焊接件的疲劳寿命。
铝合金的焊工工艺步骤

铝合金的焊工工艺步骤
铝合金的焊接工艺步骤如下:
1. 准备工作:首先要将铝合金零件清洗干净,去除表面油污和氧化物,使其表面干燥,然后根据焊接零件的设计要求进行加工和安装。
2. 选择焊接方法:根据铝合金零件的材质、形状、大小和焊接要求等,选择适合的焊接方法,如TIG、MIG、氢气焊等。
3. 确定焊接参数:根据所选择的焊接方法和一系列焊接因素,确定焊接电流、焊接速度、焊接温度、气体流量、焊接杆等参数。
4. 装配电极:根据焊接要求,选用适当规格的电极,并将其装配到焊接设备上。
5. 开始焊接:启动设备,进入焊接程序,开始焊接。
在焊接的过程中要注意电极与焊接材料之间的距离和角度,保持焊接电弧稳定,焊接位置和焊接质量的一致性。
6. 检查焊接质量:焊接完成后,对焊缝进行检查。
包括焊缝的均匀性、焊缝的强度、气孔、缺陷等的检查。
7. 收尾工作:修剪焊接余料,清理焊接面,保持环境清洁,将设备归位或存放
好。
以上是铝合金的一般焊接工艺步骤,具体步骤可能会因不同的情况而有所不同。
焊接铝合金需要技术要求较高,需要有丰富的经验和专业技能。
补焊操作规程
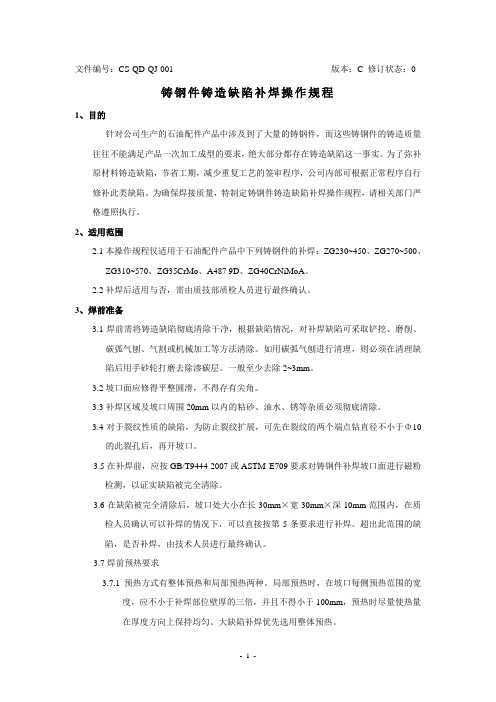
文件编号:CS-QD-QJ-001 版本:C 修订状态:0铸钢件铸造缺陷补焊操作规程1、目的针对公司生产的石油配件产品中涉及到了大量的铸钢件,而这些铸钢件的铸造质量往往不能满足产品一次加工成型的要求,绝大部分都存在铸造缺陷这一事实。
为了弥补原材料铸造缺陷,节省工期,减少重复工艺的签审程序,公司内部可根据正常程序自行修补此类缺陷。
为确保焊接质量,特制定铸钢件铸造缺陷补焊操作规程,请相关部门严格遵照执行。
2、适用范围2.1本操作规程仅适用于石油配件产品中下列铸钢件的补焊:ZG230~450、ZG270~500、ZG310~570、ZG35CrMo、A487 9D、ZG40CrNiMoA。
2.2补焊后适用与否,需由质技部质检人员进行最终确认。
3、焊前准备3.1焊前需将铸造缺陷彻底清除干净,根据缺陷情况,对补焊缺陷可采取铲挖、磨削、碳弧气刨、气割或机械加工等方法清除。
如用碳弧气刨进行清理,则必须在清理缺陷后用手砂轮打磨去除渗碳层。
一般至少去除2~3mm。
3.2坡口面应修得平整圆滑,不得存有尖角。
3.3补焊区域及坡口周围20mm以内的粘砂、油水、锈等杂质必须彻底清除。
3.4对于裂纹性质的缺陷,为防止裂纹扩展,可先在裂纹的两个端点钻直径不小于Φ10的此裂孔后,再开坡口。
3.5在补焊前,应按GB/T9444-2007或ASTM E709要求对铸钢件补焊坡口面进行磁粉检测,以证实缺陷被完全清除。
3.6在缺陷被完全清除后,坡口处大小在长30mm×宽30mm×深10mm范围内,在质检人员确认可以补焊的情况下,可以直接按第5条要求进行补焊。
超出此范围的缺陷,是否补焊,由技术人员进行最终确认。
3.7焊前预热要求3.7.1预热方式有整体预热和局部预热两种。
局部预热时,在坡口每侧预热范围的宽度,应不小于补焊部位壁厚的三倍,并且不得小于100mm,预热时尽量使热量在厚度方向上保持均匀。
大缺陷补焊优先选用整体预热。
铝件人工补焊工艺流程
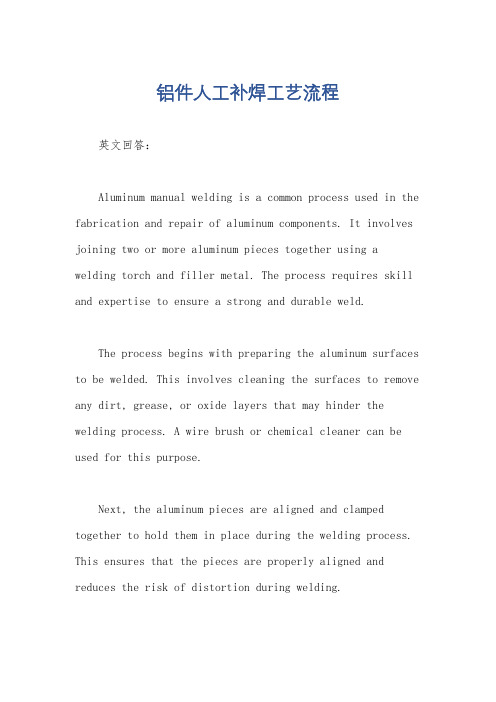
铝件人工补焊工艺流程英文回答:Aluminum manual welding is a common process used in the fabrication and repair of aluminum components. It involves joining two or more aluminum pieces together using a welding torch and filler metal. The process requires skill and expertise to ensure a strong and durable weld.The process begins with preparing the aluminum surfaces to be welded. This involves cleaning the surfaces to remove any dirt, grease, or oxide layers that may hinder the welding process. A wire brush or chemical cleaner can be used for this purpose.Next, the aluminum pieces are aligned and clamped together to hold them in place during the welding process. This ensures that the pieces are properly aligned and reduces the risk of distortion during welding.The welding torch is then used to heat the aluminum pieces and the filler metal. The torch is moved along the joint, melting the filler metal and creating a pool of molten metal. The torch is carefully controlled to maintain the desired temperature and prevent overheating or burning of the aluminum.Once the molten pool is formed, the filler metal is added to the joint. The filler metal is chosen based on the composition of the aluminum pieces being welded. It is added to the molten pool, where it fuses with the base metal to create a strong bond.During the welding process, it is important to maintain a stable arc and proper heat input. This ensures that the weld is of high quality and free from defects such as porosity or cracks. The welder must have good control over the torch and filler metal to achieve the desired results.After the welding is complete, the weld is inspectedfor quality. This can be done visually or using non-destructive testing methods such as ultrasonic testing orX-ray inspection. Any defects or imperfections are repaired, and the weld is re-inspected to ensure it meets therequired standards.In conclusion, the manual welding of aluminum involvesa series of steps including surface preparation, alignment, heating, filler metal addition, and inspection. It requires skill, control, and expertise to achieve a strong and durable weld. With practice and experience, a welder can master this process and produce high-quality aluminum welds.中文回答:铝件人工补焊是铝制零件制造和修复中常用的工艺流程。
铝件人工补焊工艺流程
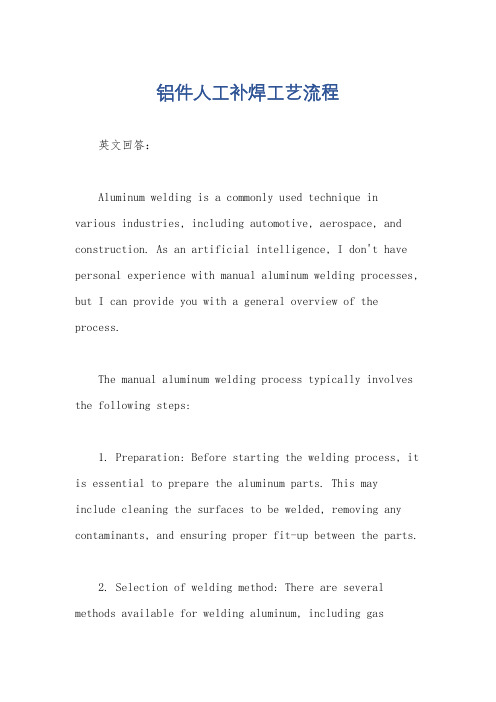
铝件人工补焊工艺流程英文回答:Aluminum welding is a commonly used technique in various industries, including automotive, aerospace, and construction. As an artificial intelligence, I don't have personal experience with manual aluminum welding processes, but I can provide you with a general overview of the process.The manual aluminum welding process typically involves the following steps:1. Preparation: Before starting the welding process, it is essential to prepare the aluminum parts. This may include cleaning the surfaces to be welded, removing any contaminants, and ensuring proper fit-up between the parts.2. Selection of welding method: There are several methods available for welding aluminum, including gastungsten arc welding (GTAW), gas metal arc welding (GMAW), and oxy-fuel welding. The choice of method depends on factors such as the thickness of the aluminum, the desired weld quality, and the available equipment.3. Preheating (if necessary): In some cases, preheating the aluminum parts may be required to reduce the risk of cracking and improve the weldability. The preheating temperature and duration depend on the specific aluminum alloy being welded.4. Welding: Once the preparation is complete, the actual welding process begins. The welder uses a welding torch or gun to melt the aluminum filler material and create a weld pool. The filler material is added to the pool to create a solid joint between the parts. The welder controls the heat input, travel speed, and other parameters to ensure a high-quality weld.5. Post-weld treatment: After the welding is complete, some post-weld treatments may be necessary. This can include removing any slag or spatter, grinding the weld toachieve the desired surface finish, and conducting non-destructive testing to check for any defects.It is important to note that aluminum welding requires skill and experience to achieve good results. The welder needs to have a good understanding of the aluminum alloys being used, as well as the specific welding process and equipment. Practice and training are crucial for mastering the art of aluminum welding.中文回答:铝件人工补焊是各个行业常用的技术之一,包括汽车、航空航天和建筑等领域。
2195铝锂合金的补焊工艺
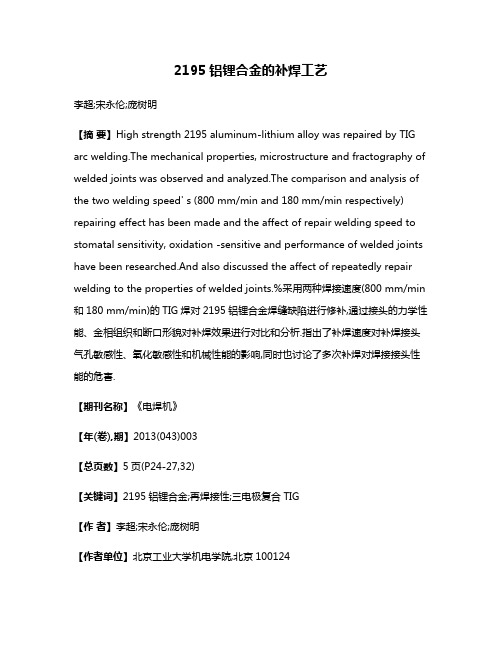
2195铝锂合金的补焊工艺李超;宋永伦;庞树明【摘要】High strength 2195 aluminum-lithium alloy was repaired by TIG arc welding.The mechanical properties, microstructure and fractography of welded joints was observed and analyzed.The comparison and analysis of the two welding speed' s (800 mm/min and 180 mm/min respectively) repairing effect has been made and the affect of repair welding speed to stomatal sensitivity, oxidation -sensitive and performance of welded joints have been researched.And also discussed the affect of repeatedly repair welding to the properties of welded joints.%采用两种焊接速度(800 mm/min 和180 mm/min)的TIG焊对2195铝锂合金焊缝缺陷进行修补,通过接头的力学性能、金相组织和断口形貌对补焊效果进行对比和分析.指出了补焊速度对补焊接头气孔敏感性、氧化敏感性和机械性能的影响,同时也讨论了多次补焊对焊接接头性能的危害.【期刊名称】《电焊机》【年(卷),期】2013(043)003【总页数】5页(P24-27,32)【关键词】2195铝锂合金;再焊接性;三电极复合TIG【作者】李超;宋永伦;庞树明【作者单位】北京工业大学机电学院,北京100124【正文语种】中文【中图分类】TG457.110 前言铝锂合金具有低密度、高强度、高弹性模量、耐高温、优良的超低温性能及良好的抗蚀性等优点。
2A14 铝合金返修焊技术

2A14 铝合金返修焊技术根据2A14 铝合金的冶金特点,针对对接接头和锁底焊缝的不同要求,提出了相应的采用缺陷槽的补焊工艺。
分析了焊接位置、补焊层数及两面补焊、预热和缓冷、补焊的收/ 起弧及长度、电源选择、环境控制、补焊顺序和方向,以及装配等因素的影响。
由不同运载贮箱补焊的结果可知,该工艺措施有效,补焊质量较好,提高了补焊的一次合格率。
0 引言焊接过程中的可变因素较多,常因出现一些技术条件不允许的焊接缺陷而造成焊缝的返修补焊(以下简称补焊) 。
一些重要的航天器构件,如运载贮箱,往往因补焊质量不高而导致重大事故和经济损失。
因此,研究和探索补焊的机理,采用合适的工艺,对确保补焊质量具有十分重要的意义。
2A14 铝合金为铝铜系可热处理强化材料,是运载贮箱的主材料。
其抗拉强度较高,但焊接性较差,焊缝的伸长率较小(3 %~5 %) ,会影响补焊质量。
为此,本文对2A14 铝合金钨极惰性气体( TIG)保护焊的补焊技术进行了研究。
1 补焊原因和目的导致补焊的主要原因是存在技术条件不允许的焊接缺陷。
它们主要有两大类:一是裂纹,包括焊缝中的凝固裂纹、焊趾的液化裂纹,以及校正过程中出现的表面裂纹;二是气孔,如密集气孔、链状气孔和尖锐尾状气孔。
另外,在液压、气密试验过程中,当压力升至一定量值或在压力达到设计指标后的保压过程中,贮箱(或单底) 有时会出现渗漏或破裂。
在贮箱(或单底) 通过液压、气密检验后进行目视检查(10 倍放大镜) 时,也会在焊接接头处发现裂纹。
焊接过程是非均匀加热,其焊缝为铸造组织。
根据2A14 铝合金的冶金特点和产品厚度,焊接经过正面二层、反面一层三道工序。
补焊时,即使是一条很短的焊缝,同样要经过多次引弧2正常焊接2收弧的过程,因此补焊区的非均匀加热较为严重。
另外,接头还存在一定程度的成分偏析和结构应力。
因此,补焊时要采取合适的工艺,将加热的非均匀化程度减至最小,成分偏析和结构应力的峰值不致过高,从而使接头的伸长率得以保持或不会大幅减小。
- 1、下载文档前请自行甄别文档内容的完整性,平台不提供额外的编辑、内容补充、找答案等附加服务。
- 2、"仅部分预览"的文档,不可在线预览部分如存在完整性等问题,可反馈申请退款(可完整预览的文档不适用该条件!)。
- 3、如文档侵犯您的权益,请联系客服反馈,我们会尽快为您处理(人工客服工作时间:9:00-18:30)。
铝合金铸件补焊工艺
补焊铸件的确定:
1、由检验人员确定补焊铸件,补焊部位应在铸件上标出。
2、允许补焊的缺陷如下:a)夹杂、砂眼、缩孔、气孔、冷隔等。
b)机械加工产生的机械损
伤。
补焊材料:
1、补焊用的焊丝应与铸件材料相同。
(以后采用铸造浇注的焊丝)
2、焊丝使用时的表面应干净,无氧化物、油污和锈蚀。
铸件缺陷的清理:
1、补焊前应用风动铣刀或其它工具对铸件缺陷部位进行打磨或扩修成坡口。
2、铸件缺陷部位开坡口应将缺陷完全排除,并保证坡口面光滑。
3、较大的穿透性缺陷清理后,应在背面垫上不锈钢或耐火砖片垫片,垫片应留有3-4mm
的间隙,便于完全焊透。
4、对需要补焊的部位,应在离坡口边界10-30mm的范围清除掉铸皮、氧化物和其他污物,
在开穿透性坡口的情况下,可从两面进行清理。
5、表面清理过的铸件应及时进行补焊,停放时间一般不超过5h.
铸件补焊前的预热
1、整体预热;适合各类型的铸件。
2、局部预热:
局部预热可用氧—乙炔焰进行,应用中性焰进行,预热时应避免穿堂风。
局部预热的铸件,加热面积应距离缺陷坡口边界不小于200mm的地方。
3、不预热
对单个的小缺陷和不易变形的铸件,可不预热。
预热要求预热温度一般为250-350度
补焊手工氩弧焊补焊时,应尽量小电流,短弧焊、小直径焊丝和小体积熔敷金属,补焊过程中,焊枪与零件表面的夹角60-70度。
补焊过程的控制
1、补焊时,焊缝均应有3-4mm的余高。
2、为防止铸件产生冷裂纹,补焊后应采用石棉布将其覆盖。
3、补焊时不允许近焊缝金属过热。
4、铸件的同一处允许补焊次数不超过三次。
补焊后的热处理
允许补焊后的铸件余同一牌号合金同炉热处理。
2011年6月26日。