陶瓷注浆模具制作泥浆性能成型方法
陶瓷注浆成型技术
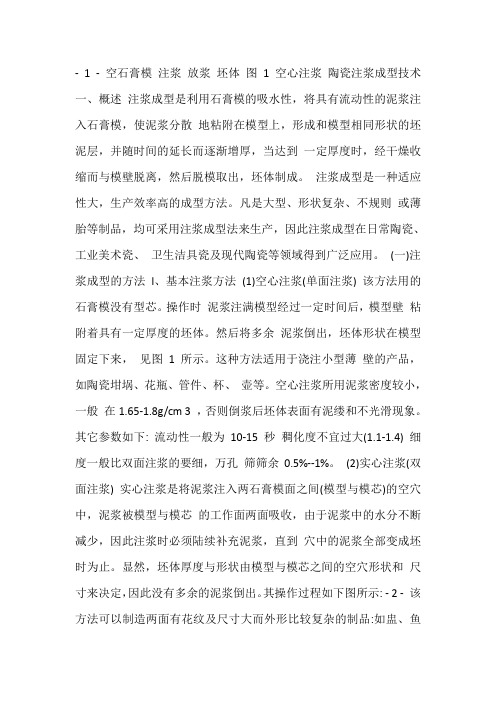
- 1 - 空石膏模注浆放浆坯体图1 空心注浆陶瓷注浆成型技术一、概述注浆成型是利用石膏模的吸水性,将具有流动性的泥浆注入石膏模,使泥浆分散地粘附在模型上,形成和模型相同形状的坯泥层,并随时间的延长而逐渐增厚,当达到一定厚度时,经干燥收缩而与模壁脱离,然后脱模取出,坯体制成。
注浆成型是一种适应性大,生产效率高的成型方法。
凡是大型、形状复杂、不规则或薄胎等制品,均可采用注浆成型法来生产,因此注浆成型在日常陶瓷、工业美术瓷、卫生洁具瓷及现代陶瓷等领域得到广泛应用。
(一)注浆成型的方法l、基本注浆方法(1)空心注浆(单面注浆) 该方法用的石膏模没有型芯。
操作时泥浆注满模型经过一定时间后,模型壁粘附着具有一定厚度的坯体。
然后将多余泥浆倒出,坯体形状在模型固定下来,见图 1 所示。
这种方法适用于浇注小型薄壁的产品,如陶瓷坩埚、花瓶、管件、杯、壶等。
空心注浆所用泥浆密度较小,一般在1.65-1.8g/cm 3 ,否则倒浆后坯体表面有泥缕和不光滑现象。
其它参数如下: 流动性一般为10-15 秒稠化度不宜过大(1.1-1.4) 细度一般比双面注浆的要细,万孔筛筛余0.5%--1%。
(2)实心注浆(双面注浆) 实心注浆是将泥浆注入两石膏模面之间(模型与模芯)的空穴中,泥浆被模型与模芯的工作面两面吸收,由于泥浆中的水分不断减少,因此注浆时必须陆续补充泥浆,直到穴中的泥浆全部变成坯时为止。
显然,坯体厚度与形状由模型与模芯之间的空穴形状和尺寸来决定,因此没有多余的泥浆倒出。
其操作过程如下图所示: - 2 - 该方法可以制造两面有花纹及尺寸大而外形比较复杂的制品:如盅、鱼盘、瓷板等。
实心注浆常用较浓的泥浆,一般密度在1.8g/cm 3 以上,以缩短吸浆时间。
稠化度(1.5 -2.2),细度可粗些,万孔筛筛余1%--2%。
2、强化注浆法为缩短注浆时间,提高注件质量,在两种基本注浆方法的基础上,形成了一些新的注浆方法,这些方法统称为强化注浆。
陶瓷注浆成型技术

空石膏模 注浆 放浆 坯体 图1空心注浆陶瓷注浆成型技术一、概述注浆成型是利用石膏模的吸水性,将具有流动性的泥浆注入石膏模内,使泥浆分散 地粘附在模型上,形成和模型相同形状的坯泥层,并随时间的延长而逐渐增厚,当达到 一定厚度时,经干燥收缩而与模壁脱离,然后脱模取出,坯体制成。
注浆成型是一种适应性大,生产效率高的成型方法。
凡是大型、形状复杂、不规则 或薄胎等制品,均可采用注浆成型法来生产,因此注浆成型在日常陶瓷、工业美术瓷、 卫生洁具瓷及现代陶瓷等领域得到广泛应用。
(一)注浆成型的方法l 、基本注浆方法(1)空心注浆(单面注浆)该方法用的石膏模没有型芯。
操作时泥浆注满模型经过一定时间后,模型内壁粘附着具有一定厚度的坯体。
然后将多余泥浆倒出,坯体形状在模型内固定下来,见图1所示。
这种方法适用于浇注小型薄壁的产品,如陶瓷坩埚、花瓶、管件、杯、壶等。
空心注浆所用泥浆密度较小,一般在1.65—1.8g/cm 3,否则倒浆后坯体表面有泥缕和不光滑现象。
其它参数如下:流动性一般为10—15秒稠化度不宜过大(1.1—1.4)细度一般比双面注浆的要细,万孔筛筛余0.5%--1%。
(2)实心注浆(双面注浆)实心注浆是将泥浆注入两石膏模面之间(模型与模芯)的空穴中,泥浆被模型与模芯 的工作面两面吸收,由于泥浆中的水分不断减少,因此注浆时必须陆续补充泥浆,直到穴中的泥浆全部变成坯时为止。
显然,坯体厚度与形状由模型与模芯之间的空穴形状和尺寸来决定,因此没有多余的泥浆倒出。
其操作过程如下图所示:该方法可以制造两面有花纹及尺寸大而外形比较复杂的制品:如盅、鱼盘、瓷板等。
实心注浆常用较浓的泥浆,一般密度在1.8g/cm3以上,以缩短吸浆时间。
稠化度(1.5—2.2),细度可粗些,万孔筛筛余1%--2%。
2、强化注浆法为缩短注浆时间,提高注件质量,在两种基本注浆方法的基础上,形成了一些新的注浆方法,这些方法统称为强化注浆。
强化注浆主要有以下几种:(1)压力注浆采用加大泥浆压力的方法来加速水分扩散,从而加速吸浆速度。
陶瓷注浆模具制作、泥浆性能、成型方法
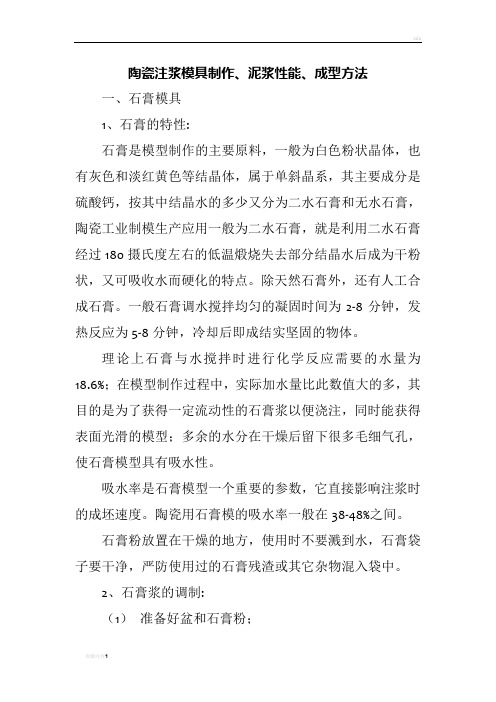
陶瓷注浆模具制作、泥浆性能、成型方法一、石膏模具1、石膏的特性:石膏是模型制作的主要原料,一般为白色粉状晶体,也有灰色和淡红黄色等结晶体,属于单斜晶系,其主要成分是硫酸钙,按其中结晶水的多少又分为二水石膏和无水石膏,陶瓷工业制模生产应用一般为二水石膏,就是利用二水石膏经过180摄氏度左右的低温煅烧失去部分结晶水后成为干粉状,又可吸收水而硬化的特点。
除天然石膏外,还有人工合成石膏。
一般石膏调水搅拌均匀的凝固时间为2-8分钟,发热反应为5-8分钟,冷却后即成结实坚固的物体。
理论上石膏与水搅拌时进行化学反应需要的水量为18.6%;在模型制作过程中,实际加水量比此数值大的多,其目的是为了获得一定流动性的石膏浆以便浇注,同时能获得表面光滑的模型;多余的水分在干燥后留下很多毛细气孔,使石膏模型具有吸水性。
吸水率是石膏模型一个重要的参数,它直接影响注浆时的成坯速度。
陶瓷用石膏模的吸水率一般在38-48%之间。
石膏粉放置在干燥的地方,使用时不要溅到水,石膏袋子要干净,严防使用过的石膏残渣或其它杂物混入袋中。
2、石膏浆的调制:(1)准备好盆和石膏粉;(2)在盆中先加入适量的水,再慢慢把石膏粉沿盆边撒入水中,一定要按照顺序先加水再加石膏。
(3)直到石膏粉冒出水面不再自然吸水沉陷,稍等片刻,就用搅拌棒搅拌,要快速有力、用力均匀。
成糊状即可。
(4)石膏在调制时的比例为:水:石膏=1:1.4-1.8左右。
(5)注意挑除石膏浆里的硬块和杂质。
3、模型翻制操作:常用的材料和工具有:钢锯条、锯条刀,直尺三角板、毛刷、海绵、脱模剂等。
a、清理工作台,把石膏母模清理干净,在石膏母模上均匀涂抹脱模剂,一定注意各个部位必须均匀涂上,不能遗漏。
b、按顺序合模夹紧,并安放好各种模具内配件。
c、调制石膏浆,缓缓注入围好的空腔内,并不断搅动或震动石膏浆,使气泡排出,直至注满母模。
d、静置一段时间,等石膏发热固化后,可开模,如不容易打开,可以用轻敲、气冲、水冲泡等方法打开。
陶瓷注浆模具制作、泥浆性能、成型方法分析
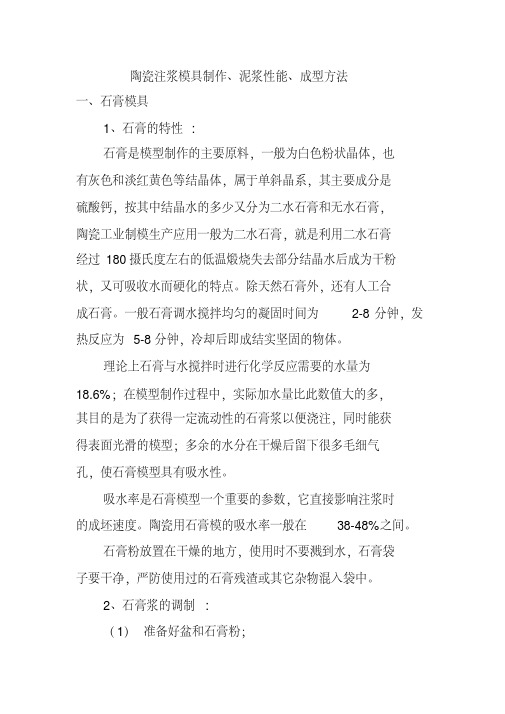
陶瓷注浆模具制作、泥浆性能、成型方法一、石膏模具1、石膏的特性:石膏是模型制作的主要原料,一般为白色粉状晶体,也有灰色和淡红黄色等结晶体,属于单斜晶系,其主要成分是硫酸钙,按其中结晶水的多少又分为二水石膏和无水石膏,陶瓷工业制模生产应用一般为二水石膏,就是利用二水石膏经过180摄氏度左右的低温煅烧失去部分结晶水后成为干粉状,又可吸收水而硬化的特点。
除天然石膏外,还有人工合成石膏。
一般石膏调水搅拌均匀的凝固时间为2-8分钟,发热反应为5-8分钟,冷却后即成结实坚固的物体。
理论上石膏与水搅拌时进行化学反应需要的水量为18.6%;在模型制作过程中,实际加水量比此数值大的多,其目的是为了获得一定流动性的石膏浆以便浇注,同时能获得表面光滑的模型;多余的水分在干燥后留下很多毛细气孔,使石膏模型具有吸水性。
吸水率是石膏模型一个重要的参数,它直接影响注浆时的成坯速度。
陶瓷用石膏模的吸水率一般在38-48%之间。
石膏粉放置在干燥的地方,使用时不要溅到水,石膏袋子要干净,严防使用过的石膏残渣或其它杂物混入袋中。
2、石膏浆的调制:(1)准备好盆和石膏粉;(2)在盆中先加入适量的水,再慢慢把石膏粉沿盆边撒入水中,一定要按照顺序先加水再加石膏。
(3)直到石膏粉冒出水面不再自然吸水沉陷,稍等片刻,就用搅拌棒搅拌,要快速有力、用力均匀。
成糊状即可。
(4)石膏在调制时的比例为:水:石膏=1:1.4-1.8左右。
(5)注意挑除石膏浆里的硬块和杂质。
3、模型翻制操作:常用的材料和工具有:钢锯条、锯条刀,直尺三角板、毛刷、海绵、脱模剂等。
a、清理工作台,把石膏母模清理干净,在石膏母模上均匀涂抹脱模剂,一定注意各个部位必须均匀涂上,不能遗漏。
b、按顺序合模夹紧,并安放好各种模具内配件。
c、调制石膏浆,缓缓注入围好的空腔内,并不断搅动或震动石膏浆,使气泡排出,直至注满母模。
d、静置一段时间,等石膏发热固化后,可开模,如不容易打开,可以用轻敲、气冲、水冲泡等方法打开。
【陶瓷生产】注浆泥料的工艺性能

【陶瓷生产】注浆泥料的工艺性能注浆泥料的工艺性能,主要有如下要求:(1)泥浆的粘度和流动性:注浆成形的泥浆,要求具有良好的流动性,故其含水率比塑性成形的泥料高,即使加入电解质稀释,它的含水率通常也在2836%之间。
如过分减少泥浆的水份,则粘度增大,流动性降低,不仅会造成注浆成形时难以注满模型的所有部位,而且易引起气泡和针孔等缺陷产生,还会减慢注成速度。
若是增加泥浆的含水率,虽可改善泥浆的流动性,但易使泥浆中的粗颗粒沉淀而引起坏体开裂,还会延长模型吸浆时间,降低生产效率。
影响泥浆流动性的因素主要有:①泥浆颗粒的粗细:在同一浓度下,颗粒越细泥浆的粘性大。
②泥浆的温度;如泥浆温度升高,作为泥浆分散介质的水分粘度下降,泥浆的流动性增加。
③泥浆的处理方法:如泥浆经过真空处理,不仅可以提高泥浆的流动性,还能增加坯体的密度和强度。
④稀释剂的种类及用量;如前所述,各种电解质对不同粘土所起的稀释作用是有差别的,其用量也要适宜。
(2)泥浆的稳定性:泥浆的稳定性,是指泥浆在较长时间的存放下,不发生沉淀、分层和触变性变坏的性能。
通常来说,固体颗粒越细,泥浆越稳定,即使泥浆中含有大量的瘠性原料,只要颗粒细度适宜,也会悬浮而不易沉淀。
在泥浆中加入适宜种类和数量的电解质,也可增强泥浆的稳定性。
(3)泥浆的触变性:泥浆的触变性,又称稠化性,是指泥浆在静置后变稠而一经搅拌立即恢复流动的性质。
如泥浆的触变性很大,会影响注浆操作的效率降低,注成的坯体在脱模后稍遇震动就会变形甚至塌陷。
若触变性太小,则泥浆的悬浮性较差,易引起泥浆中的粗颗粒沉淀。
注浆时泥料在模型内难以形成一定的厚度,而且脱模困难。
影响泥浆触变性的因素较多,如泥浆的含水率太低;固体颗粒形状不规则或颗粒太细;电解质加入过多;泥浆的温度太低等,都易使泥浆的触变性增大。
(4)泥浆的渗透性:泥浆的渗透性,是指泥浆中水分的过滤性,即去水性。
如泥浆的渗透性差,会影响在注浆操作过程中泥浆中的水分不易被模型吸出,不仅会延长注浆时间,还易引起实心注浆的坯体内部分层或出现“溏心”,造成坯件开裂、冲泡等缺陷发生。
陶瓷高压注浆成型工艺

陶瓷高压注浆成型工艺
陶瓷高压注浆成型工艺是一种将陶瓷粉末和粘合剂混合后,通过高压
注射机将混合物注入模具中进行成型的工艺。
具体工艺流程如下:
1.准备原料:将陶瓷粉末和粘合剂按一定比例混合。
2.注浆:将混合物倒入高压注射机中,通过高压将混合物注入模具中。
在注入过程中,需要控制注入速度和压力,以保证成型品的质量。
3.固化:注浆完成后,待陶瓷材料固化后,即可将成型品取出。
4.烧结:成型品经过固化后需要进行烧结,以使其获得更高的密度和
硬度。
5.加工处理:烧结后的陶瓷成型品需要进行加工处理,如磨光、抛光等,以使其表面光滑。
陶瓷高压注浆成型工艺具有成品的尺寸精度高、表面光滑、强度高、
耐磨性好等优点,广泛应用于电子、机械、化工等领域的制造。
陶瓷注浆成型技术

空石膏模 注浆 放浆 坯体 图1空心注浆陶瓷注浆成型技术一、概述注浆成型是利用石膏模的吸水性,将具有流动性的泥浆注入石膏模内,使泥浆分散 地粘附在模型上,形成和模型相同形状的坯泥层,并随时间的延长而逐渐增厚,当达到 一定厚度时,经干燥收缩而与模壁脱离,然后脱模取出,坯体制成。
注浆成型是一种适应性大,生产效率高的成型方法。
凡是大型、形状复杂、不规则 或薄胎等制品,均可采用注浆成型法来生产,因此注浆成型在日常陶瓷、工业美术瓷、 卫生洁具瓷及现代陶瓷等领域得到广泛应用。
(一)注浆成型的方法l 、基本注浆方法(1)空心注浆(单面注浆)该方法用的石膏模没有型芯。
操作时泥浆注满模型经过一定时间后,模型内壁粘附着具有一定厚度的坯体。
然后将多余泥浆倒出,坯体形状在模型内固定下来,见图1所示。
这种方法适用于浇注小型薄壁的产品,如陶瓷坩埚、花瓶、管件、杯、壶等。
空心注浆所用泥浆密度较小,一般在1.65—1.8g/cm 3,否则倒浆后坯体表面有泥缕和不光滑现象。
其它参数如下:流动性一般为10—15秒稠化度不宜过大(1.1—1.4)细度一般比双面注浆的要细,万孔筛筛余0.5%--1%。
(2)实心注浆(双面注浆)实心注浆是将泥浆注入两石膏模面之间(模型与模芯)的空穴中,泥浆被模型与模芯 的工作面两面吸收,由于泥浆中的水分不断减少,因此注浆时必须陆续补充泥浆,直到穴中的泥浆全部变成坯时为止。
显然,坯体厚度与形状由模型与模芯之间的空穴形状和尺寸来决定,因此没有多余的泥浆倒出。
其操作过程如下图所示:该方法可以制造两面有花纹及尺寸大而外形比较复杂的制品:如盅、鱼盘、瓷板等。
实心注浆常用较浓的泥浆,一般密度在1.8g/cm3以上,以缩短吸浆时间。
稠化度(1.5—2.2),细度可粗些,万孔筛筛余1%--2%。
2、强化注浆法为缩短注浆时间,提高注件质量,在两种基本注浆方法的基础上,形成了一些新的注浆方法,这些方法统称为强化注浆。
强化注浆主要有以下几种:(1)压力注浆采用加大泥浆压力的方法来加速水分扩散,从而加速吸浆速度。
注浆成型

注浆成型的应用
注浆成型是一种传统的陶瓷成型方法, 也是一种经典的流法成型方法。由于采用流 动充模,可以制备复杂形状的型坯。一般而 言,凡形状复杂、不规则、薄壁、体积较大且 尺寸要求不严的器件都可用注浆法成型,如日 用陶瓷中的花瓶、茶壶、杯把、椭圆形盘等 都可采用此法成型。
注浆成型基本工艺流程为: 粉末→浆料→注浆→脱模→干燥→型坯
原料
浆料是固相颗粒在水中的分散体系。 浆料的基本成分是固相颗粒和水。一般在满足 浆料各种性能要求的基础上,固相的体积分数愈大 愈好。通常固相的体积分数在30-65%范围内。 根据最终性能,制品的成分结构应有一定的要 求。该要求对烧结前的成型坯的成分结构提出相应 的要求,进而对用于制备浆料的固相原料也提出了 要求。
即泥浆的粘度要小,能保证泥浆在输送管道内畅 流并可分流注以模型的各个部位。 2)稳定性要好 稳定性的含义是指浆料长期放置时不产生分层现象。
3)具有适当的触变性 泥浆在存放一定时间后粘度变化不宜过大,这样泥 浆就便于输送和储存,同时又要求脱模后的坯体不 致于受到轻微振动而软塌。注浆用泥浆的触变性太 大易稠化,不便浇注,而触变性太小则生坯易软塌, 所以要有适当的触变性。
1. 压力注浆。
对于大型的制品来说,因为制品较大,注浆时间就必 然很长,又因为注件壁厚,当石膏模吸水能力不够 时,就不易干涸,多余泥浆倒出后,有时注件内壁 还很潮湿,注件容易损坏。为了加速水分扩散,加 快吸浆速度,提高注件的致密度,缩短注浆时间, 并避免大型或异型注件发生缺料现象,必须在压力 下将泥浆注入石膏模。一般加压方法是将注浆斗提 高,加大注浆压力,或用压缩空气将泥浆压入模型。
陶瓷工艺基础_陶瓷制品的注浆成形

陶瓷工艺基础 陶瓷制品的注浆成形 使用石膏模具的现代式陶瓷制品注浆成形法产生于200多年之前。
今天,注浆仍是一些日用陶瓷、卫生陶瓷和美术陶瓷制品的主要成形方法。
恰恰是这种成形方法,可以制得结构均匀的复杂形状制品。
与可塑成形法(滚压、挤压)不同,采用注浆法可以生产出深浮雕、独特曲线、薄壁不定截面的制品。
该种方法的优点还在于简单易行,成本低廉。
注浆是一条从模型到成品的捷径,这首先在新型制品的设计阶段是非常重要的。
模型、雏模、母模和易加工石膏工作模的制作占用时间少,同时顾及了因空气收缩和烧缩而引起的制品尺寸变化。
必要时,可改变制品形状,消除会使裂纹产生和发育的作为应力集中区的部位。
制作石膏模型、注浆模具和其它需用装具的费用大大低于压制用金属装具的制作费用。
制备泥浆需用的设备比制备塑性坯料少,坯料制备阶段能源消耗小。
泥浆输运距离长短皆可,并可利用低塑性料制取。
注浆成形法的缺点是:注浆模具的配置和注件的干燥占用场地大;因产品成形和干燥过程长,生产效率低;手工劳动量大;石膏模具消耗大;注件含水多,空气收缩大。
这样,就对产品结构有一定的要求,首先是对空心制品(器皿、花瓶等),其孔口周边和底足应设支骨。
注浆法的另一缺点是废渣量高,二次利用时尚需解散。
注浆过程就是石膏模具开口气孔的小毛细管从陶瓷泥浆中吸收水的过程。
在该过程中,于模具内面形成部分脱水的致密硬质塑性沉淀物层。
该层的形成过程称为坯料吃浆。
坯料吃浆的速度决定成形的效率,而吃浆速度又受泥浆性能(浇注性能)、石膏模具性能及外部条件(如注浆车间的温度)的制约。
有空心注浆和实心注浆法之分。
采用空心注浆法时,在一定厚度的坯料层吃浆后,要排除模内的多余泥浆。
实心注浆法要求根据模壁两面的吸水和坯料填充整个模腔的情况制作模具,采用此方法时泥浆由浇口进入。
空心注浆法用于成形壁厚相同的薄胎制品;实心注浆法用于成形壁厚不同的厚胎及实心制品。
空心注浆法的缺点是:坯料吃浆缓慢,泥浆耗量大,不能保持制品绝对的均一壁厚。
陶瓷注浆成型工艺

陶瓷注浆成型工艺注浆成型工艺是陶瓷制作中一个重要手段,其工艺流程是首先按照设计图纸用石膏块制作一件未来所需瓷器形状相同的造型,如瓶、罐、壶等圆形器物使用车削方法制成,四方六方等非圆形器物用雕塑方法完成,这个过程称之为“制种”种制好后,再用水将石膏粉调成糊状将“种”全部包裹,并预留石膏凝固后取出“种”的开合缝,待石膏硬结后,取出“种”,石膏就成为模具,石膏模具彻底干燥后用橡胶带捆好,在模具的顶部开一孔,由此孔向模具内注入特别配制的泥浆,这种泥浆加入了化学制剂,使得泥沙在一定的时间内保持悬浮状态,干燥的石膏模具接触到泥浆后立刻会吸收水份,悬浮的泥沙会均匀的吸附在模具内壁上,随着时间长短不同,吸附的泥沙厚度也不同,需要薄胎时间就短一些,需要胎厚一些时间就长一些,待达到需要的厚度以后,将泥浆从模具中倒出,再等吸附在模具内壁上的泥沙稍干燥后,即可打开模具取出制好的泥坯;瓷器的成型工序完成。
其工艺原理是利用石膏模具的吸水性能,将悬浮在水中的泥沙吸附在内壁上,达到一定厚度的泥沙吸附后,再将剩余的泥浆倒出,既形成中空的器皿泥坯,其优点是工艺简单、方便的制作各种非圆形不能使用辘轳车旋转制作的泥坯如方形,菱形,等以及壶嘴、瓶耳等,使用注浆工艺成型使得镶器类、小器类瓷器成本大大下降,质量大幅度提高。
但是由于其工艺特点,又有些影响产品质量的问题无法解决,一是合缝线残留,由于两块或更多块模具的相接处的缝隙影响泥沙的吸附,造成接缝处泥坯密度与其他处不同,高温烧成时其收缩率不同,烧成的瓷器胎体上会留下隆起或下凹的线状痕迹,俗称“合缝线”,明显时用肉眼可以看到器皿相对两侧的合缝线,不明显时用手抚摸可以感觉到,合缝线影响瓷器外观质量,为了解决这一问题圆形器皿一般采用上下开模,将合缝线留在器皿的腹部,经过车削后,在车削痕的掩盖下,基本找不到合缝线,如果器皿上下两头凸出,则采用三开、四开模减少合缝线,棱角造型器皿尽量把合缝线留在棱角处;其二由于依靠吸附所以壁厚基本相同如果底部有足,在足部位的内底有一圈下凹沟,其形成原因是足部占用了吸附的泥沙,而下凹无法用泥补平,因为补上去的泥和原来坯上的泥密度不同高温烧成时会出现收缩不均的问题,一般解决办法是尽量采用无足造型。
陶瓷注浆成型工艺流程

陶瓷注浆成型工艺流程
陶瓷注浆成型是陶瓷制品生产过程中的重要环节,其工艺流程的合理性和稳定性直接影响着陶瓷制品的质量和性能。
在陶瓷注浆成型工艺中,需要经过原料准备、注浆、成型、烘干等多个环节,下面将详细介绍陶瓷注浆成型工艺的流程。
首先,原料准备是陶瓷注浆成型的第一步。
在原料准备阶段,需要将陶瓷原料进行配比,并进行搅拌混合。
通常情况下,陶瓷原料主要包括粘土、瓷石、瓷釉等,不同种类的陶瓷制品所需的原料配比也会有所不同。
在搅拌混合过程中,需要确保原料的均匀性和稳定性,以保证后续工艺的顺利进行。
其次,注浆是陶瓷注浆成型的关键环节。
在注浆过程中,需要将搅拌好的陶瓷浆料注入模具中,以形成所需的产品形状。
注浆需要控制浆料的流动速度和压力,以确保产品成型的精度和一致性。
同时,还需要注意避免浆料中的气泡和杂质,以防影响产品的质量和外观。
接下来是成型环节。
在成型过程中,需要对注浆后的产品进行振实和压实,以提高产品的密实度和强度。
成型过程中需要注意控
制振实和压实的力度和时间,以确保产品的内部结构和外观质量。
最后是烘干环节。
在烘干过程中,需要将成型后的产品进行适当的干燥处理,以去除产品中的水分。
烘干过程需要根据产品的材质和厚度来确定时间和温度,以避免产品出现开裂或变形的情况。
综上所述,陶瓷注浆成型工艺流程包括原料准备、注浆、成型和烘干四个主要环节。
在实际生产中,需要严格控制每个环节的工艺参数,以确保产品质量和生产效率。
同时,还需要根据不同产品的要求和特点,对工艺流程进行合理调整和优化,以满足市场需求和提高竞争力。
陶瓷注浆成型工艺

陶瓷注浆成型工艺嘿,朋友们!今天咱来聊聊陶瓷注浆成型工艺这玩意儿,可有意思啦!你想想看啊,那原本普普通通的泥浆,就像变魔术一样,能变成各种精美的陶瓷制品。
这可不是一般的神奇呀!陶瓷注浆成型呢,就像是给泥浆安了个家。
先得准备好模具,这模具就好比是个小房子,等着泥浆住进去呢。
把泥浆小心翼翼地倒进模具里,看着它慢慢地填满每一个角落,就好像给小房子穿上了一件特别的衣服。
然后呢,就得等啦!等泥浆在模具里安安稳稳地待上一段时间,让它慢慢凝固成型。
这过程就像是在等待一朵花慢慢开放,需要点耐心呢。
等泥浆凝固得差不多了,就可以把模具打开啦!哇哦,这时候你就能看到初步成型的陶瓷啦,虽然还带着点粗糙,但已经有模有样啦!不过,这可还没完事儿呢。
接下来还得给它精心修整一番,把那些不平整的地方打磨打磨,让它变得更加光滑细腻。
这就像是给一个小孩子梳妆打扮,要让它漂漂亮亮的。
你说这陶瓷注浆成型工艺是不是很有趣呀?就好像是在创造一个个小生命一样。
而且啊,通过这种方法可以做出各种各样的形状和图案,那可真是只有你想不到,没有它做不到。
你看那些摆在商店里精美的陶瓷制品,说不定就是通过陶瓷注浆成型工艺做出来的呢。
它们曾经也是普普通通的泥浆呀,经过这么一番奇妙的旅程,就变成了让人爱不释手的宝贝。
咱再想想,要是没有陶瓷注浆成型工艺,那我们的生活得少多少乐趣呀?那些漂亮的花瓶、精致的碗碟,不就都没啦?那多可惜呀!所以说呀,陶瓷注浆成型工艺可真是个了不起的发明呢!它让我们的生活变得更加丰富多彩,让我们能享受到陶瓷带来的美好。
怎么样,朋友们,是不是对陶瓷注浆成型工艺有了更深的了解呀?下次再看到那些漂亮的陶瓷制品,可别忘了它们背后的神奇工艺哦!。
陶艺注浆的正确方法
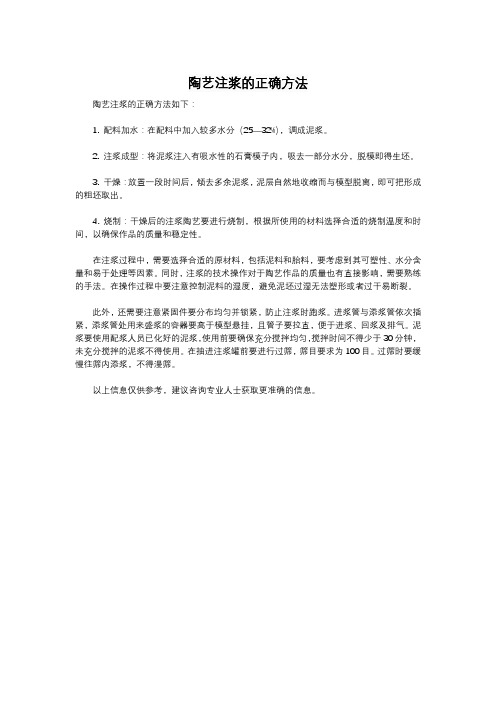
陶艺注浆的正确方法
陶艺注浆的正确方法如下:
1. 配料加水:在配料中加入较多水分(25—32%),调成泥浆。
2. 注浆成型:将泥浆注入有吸水性的石膏模子内,吸去一部分水分,脱模即得生坯。
3. 干燥:放置一段时间后,倾去多余泥浆,泥层自然地收缩而与模型脱离,即可把形成的粗坯取出。
4. 烧制:干燥后的注浆陶艺要进行烧制,根据所使用的材料选择合适的烧制温度和时间,以确保作品的质量和稳定性。
在注浆过程中,需要选择合适的原材料,包括泥料和胎料,要考虑到其可塑性、水分含量和易于处理等因素。
同时,注浆的技术操作对于陶艺作品的质量也有直接影响,需要熟练的手法。
在操作过程中要注意控制泥料的湿度,避免泥坯过湿无法塑形或者过干易断裂。
此外,还需要注意紧固件要分布均匀并锁紧,防止注浆时跑浆。
进浆管与添浆管依次插紧,添浆管处用来盛浆的容器要高于模型悬挂,且管子要拉直,便于进浆、回浆及排气。
泥浆要使用配浆人员已化好的泥浆,使用前要确保充分搅拌均匀,搅拌时间不得少于30分钟,未充分搅拌的泥浆不得使用。
在抽进注浆罐前要进行过筛,筛目要求为100目。
过筛时要缓慢往筛内添浆,不得漫筛。
以上信息仅供参考,建议咨询专业人士获取更准确的信息。
陶瓷注浆成型工艺-【浆胎瓷器】DM
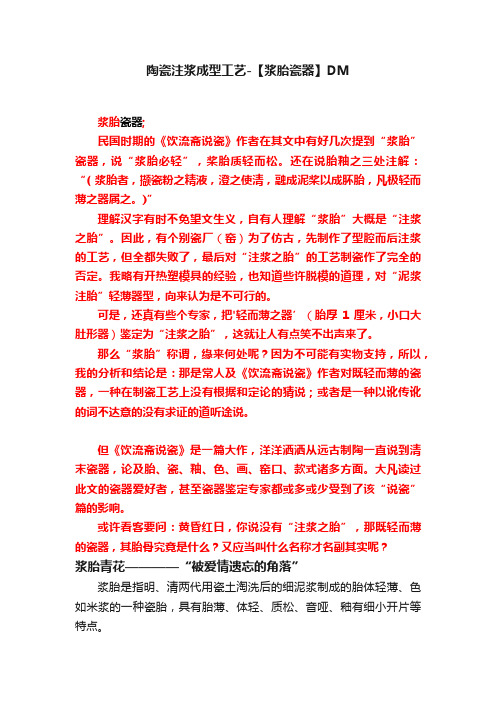
陶瓷注浆成型工艺-【浆胎瓷器】DM浆胎瓷器;民国时期的《饮流斋说瓷》作者在其文中有好几次提到“浆胎”瓷器,说“浆胎必轻”,桨胎质轻而松。
还在说胎釉之三处注解:“( 浆胎者,撷瓷粉之精液,澄之使清,融成泥桨以成肧胎,凡极轻而薄之器属之。
)”理解汉字有时不免望文生义,自有人理解“浆胎”大概是“注浆之胎”。
因此,有个别瓷厂(窑)为了仿古,先制作了型腔而后注浆的工艺,但全都失败了,最后对“注浆之胎”的工艺制瓷作了完全的否定。
我略有开热塑模具的经验,也知道些许脱模的道理,对“泥浆注胎”轻薄器型,向来认为是不可行的。
可是,还真有些个专家,把'轻而薄之器’(胎厚1厘米,小口大肚形器)鉴定为“注浆之胎”,这就让人有点笑不出声来了。
那么“浆胎”称谓,缘来何处呢?因为不可能有实物支持,所以,我的分析和结论是:那是常人及《饮流斋说瓷》作者对既轻而薄的瓷器,一种在制瓷工艺上没有根据和定论的猜说;或者是一种以讹传讹的词不达意的没有求证的道听途说。
但《饮流斋说瓷》是一篇大作,洋洋洒洒从远古制陶一直说到清末瓷器,论及胎、瓷、釉、色、画、窑口、款式诸多方面。
大凡读过此文的瓷器爱好者,甚至瓷器鉴定专家都或多或少受到了该“说瓷”篇的影响。
或许看客要问:黄昏红日,你说没有“注浆之胎”,那既轻而薄的瓷器,其胎骨究竟是什么?又应当叫什么名称才名副其实呢?浆胎青花————“被爱情遗忘的角落”浆胎是指明、清两代用瓷土淘洗后的细泥浆制成的胎体轻薄、色如米浆的一种瓷胎,具有胎薄、体轻、质松、音哑、釉有细小开片等特点。
康、雍、乾浆胎青花自成一体。
康熙时胎体微泛土黄色,釉面多为粉白或浆白色,有细碎纹片,纹饰较一般青花细腻。
雍正、乾隆时浆胎青花胎釉与康熙无大差别,少数有釉面不太平整的,青花纹饰则渐趋规矩图案化。
乾隆晚期的浆胎青花,其胎质较松软细致,叩之有瓦声,胎色微黄,青花呈色有浓有淡,但都较为明艳,略带紫色倾向,白釉带乳白色,开细纹,莹润明亮。
注浆成型的主要工艺流程
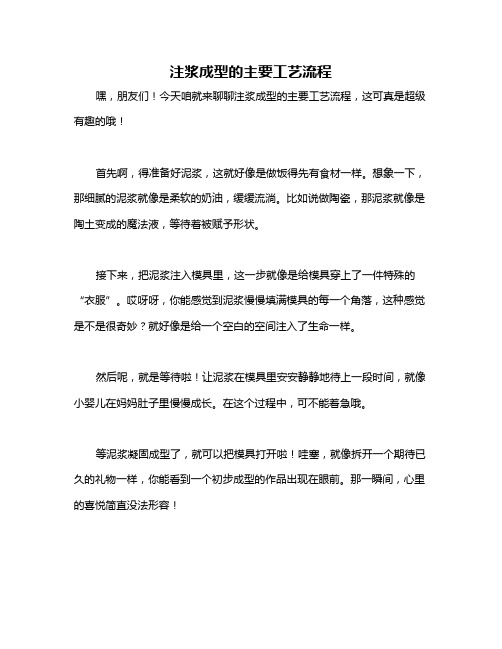
注浆成型的主要工艺流程
嘿,朋友们!今天咱就来聊聊注浆成型的主要工艺流程,这可真是超级有趣的哦!
首先啊,得准备好泥浆,这就好像是做饭得先有食材一样。
想象一下,那细腻的泥浆就像是柔软的奶油,缓缓流淌。
比如说做陶瓷,那泥浆就像是陶土变成的魔法液,等待着被赋予形状。
接下来,把泥浆注入模具里,这一步就像是给模具穿上了一件特殊的“衣服”。
哎呀呀,你能感觉到泥浆慢慢填满模具的每一个角落,这种感觉是不是很奇妙?就好像是给一个空白的空间注入了生命一样。
然后呢,就是等待啦!让泥浆在模具里安安静静地待上一段时间,就像小婴儿在妈妈肚子里慢慢成长。
在这个过程中,可不能着急哦。
等泥浆凝固成型了,就可以把模具打开啦!哇塞,就像拆开一个期待已久的礼物一样,你能看到一个初步成型的作品出现在眼前。
那一瞬间,心里的喜悦简直没法形容!
这时还没完哦,还得把成型的作品进行修整和加工。
这就像是给一个已经很漂亮的人再精心打扮一番,让它更加完美。
比如把一些不平整的地方磨平,让它变得光滑细腻,就好像给它披上了一件顺滑的外衣。
最后就是烧制啦!把作品放入高温炉中烧制,让它变得坚固耐用。
这就像是给它进行一场蜕变之旅,经过烈火的洗礼,它变得更加坚韧和美丽。
总之啊,注浆成型的工艺流程就像是一场神奇的魔法表演,从泥浆到最后的精美作品,每一步都充满了惊喜和期待!
我的观点就是,注浆成型真的是一种超级棒的工艺,能创造出那么多让人惊叹的作品!大家一定要去感受感受它的魅力呀!。
陶瓷注浆成型工艺流程

陶瓷注浆成型工艺流程陶瓷是一种古老而又精美的艺术品,它经历了千百年的发展,如今已成为人们生活中不可或缺的一部分。
陶瓷制品的制作过程中,注浆成型是其中非常重要的一个环节。
本文将为您介绍陶瓷注浆成型的工艺流程。
首先,我们需要准备好原料。
陶瓷制品的原料主要包括粘土、瓷石、石英、长石等。
这些原料需要经过混合、研磨等工序,最终形成适合注浆成型的陶瓷浆料。
接下来,是模具的制作。
模具是用来给陶瓷制品定型的工具,通常由石膏或硅胶制成。
制作模具需要根据设计图纸,将模具分割成若干个部分,然后用模具胶将其粘合在一起,最终形成完整的模具。
然后,是注浆成型的过程。
首先,将准备好的陶瓷浆料倒入模具中,然后用振动台将浆料振实,以确保模具内部充满浆料并且没有气泡。
接着,将模具放置在震动台上,震动台会以一定的频率和幅度进行震动,使得浆料在模具内部均匀分布并且排除气泡。
经过一定时间的震动,浆料逐渐凝固成型,最终形成陶瓷制品的初步形态。
随后,是脱模和修整。
经过一定时间的凝固,陶瓷制品可以从模具中取出,但此时制品还不完整,需要经过修整工序。
通常会使用刀具对制品进行修整,去除多余的浆料和修复表面的瑕疵,最终使制品达到设计要求的形态和质量。
最后,是烧制工序。
经过注浆成型和修整后的陶瓷制品需要进行烧制,以使其达到一定的硬度和耐用性。
烧制的温度和时间需要根据具体的陶瓷材料和制品设计要求来确定,一般来说,烧制温度在1000℃以上,时间在几小时到几十小时不等。
综上所述,陶瓷注浆成型是陶瓷制品制作过程中非常重要的一个环节。
通过精心的原料准备、模具制作、注浆成型、脱模修整和烧制工序,我们可以制作出各种精美的陶瓷制品,为人们的生活增添更多的艺术和美感。
希望通过本文的介绍,您对陶瓷注浆成型工艺流程有了更深入的了解。
简述陶瓷注浆成型的过程

简述陶瓷注浆成型的过程一、引言陶瓷注浆成型是一种重要的陶瓷成型工艺,它是指将陶瓷粉末和液体粘结剂混合后,在模具内进行注浆成型,然后经过干燥和烧结等工艺步骤,最终制成各种形状的陶瓷制品。
本文将从原料准备、注浆成型、干燥和烧结等方面详细介绍陶瓷注浆成型的过程。
二、原料准备在进行陶瓷注浆成型之前,需要准备好一定比例的陶瓷粉末和液体粘结剂。
通常情况下,陶瓷粉末可以选择氧化铝、氧化锆、碳化硅等材料,并且需要对其进行筛分处理以保证其颗粒大小均匀。
液体粘结剂可以选择有机胶水或者无机胶水等材料,并且需要根据具体情况调整其比例以保证混合后的浆料流动性适中。
三、注浆成型1. 模具设计:在进行注浆成型之前,需要根据所需制品形状设计相应的模具。
通常情况下,模具可以选择金属或者硅胶等材料制作,其内部需要具有所需制品的形状和尺寸。
2. 浆料混合:将陶瓷粉末和液体粘结剂混合后,需要进行搅拌处理以保证其均匀性。
通常情况下,可以选择机械搅拌或者手动搅拌等方式进行。
3. 注浆成型:将混合后的浆料注入到模具内部,然后通过震动或者压实等方式使浆料充分填充模具内部。
在注浆成型过程中需要注意控制注浆速度和压力,以保证制品质量。
四、干燥在完成注浆成型之后,需要将制品取出并进行干燥处理。
通常情况下,可以选择自然风干或者烘干等方式进行。
在干燥过程中需要注意控制温度和湿度,以避免制品出现开裂等问题。
五、烧结在完成干燥之后,需要将制品进行烧结处理。
通常情况下,可以选择电子束烧结、高温气氛固相反应等方式进行。
在烧结过程中需要注意控制温度和时间,以保证制品的致密性和强度。
六、总结陶瓷注浆成型是一种重要的陶瓷成型工艺,其过程包括原料准备、注浆成型、干燥和烧结等步骤。
在进行注浆成型时需要注意控制浆料比例、注浆速度和压力等因素,以保证制品质量。
在干燥和烧结过程中需要注意控制温度和湿度等因素,以避免制品出现开裂等问题。
(完整word版)注浆成型

注浆成型注浆成型,亦称浇注成型定义及原理:是基于多孔石膏模具能够吸收水分的物理特性,将陶瓷粉料配成具有流动性的泥浆,然后注入多孔模具内(主要为石膏模),水分在被模具(石膏)吸入后便形成了具有一定厚度的均匀泥层,脱水干燥过程中同时形成具有一定强度的坯体,此种方式被称为注浆成型.其完成过程可分为三个阶段:1。
泥浆注入模具后,在石膏模毛细管力的作用下吸收泥浆中的水,靠近模壁的泥浆中的水分首先被吸收,泥浆中的颗粒开始靠近,形成最初的薄泥层。
2。
水分进一步被吸收,其扩散动力为水分的压力差和浓度差,薄泥层逐渐变厚,泥层内部水分向外部扩散,当泥层厚度达到注件厚度时,就形成雏坯.3。
石膏模继续吸收水分,雏坯开始收缩,表面的水分开始蒸发,待雏坯干燥形成具有一定强度的生坯后,脱模即完成注浆成型。
注浆成型的特点:优点:(1)适用性强,不需复杂的机械设备,只要简单的石膏模就可成型;(2)能制出任意复杂外形和大型薄壁注件;(3)成型技术容易掌握,生产成本低.(4)坯体结构均匀。
缺点:(1)劳动强度大,操作工序多,生产效率低;(2)生产周期长,石膏模占用场地面积大;(3)注件含水量高,密度小,收缩大,烧成时容易变形.(4)模具损耗大。
(5)不适合连续化、自动化、机械化生产。
常规注浆成型方法:单面注浆:泥浆与模型的接触只有一面,称为单面注浆。
双面注浆:泥浆与模型和模芯的工作面两面接触,双面吸水,称为双面注浆。
1.粉料浆料的性能。
如安定性,流动性,触变性,含水量的多少,脱模性好坏,料浆含气泡情况.2。
注浆成型的方法的影响.如实心,空心,离心,压力,真空注浆等.3。
浆料设备的影响.4。
吸浆速度的影响.因素有模型的阻力,坯料的阻力。
5一、陶瓷注浆成型工艺要点注浆成型是一种适应性广、生产效率高的成型方法,凡是形状复杂或不规则、不能用其他方法成型以及薄胎制品都可用注浆成型来生产但是由于温、湿度对坯体成型影响较大,直接关系到半成品的质量和成品率的高低,所以生产时必须对环境温度、湿度进行严格的控制以及季节的变化采取相应的措施。
- 1、下载文档前请自行甄别文档内容的完整性,平台不提供额外的编辑、内容补充、找答案等附加服务。
- 2、"仅部分预览"的文档,不可在线预览部分如存在完整性等问题,可反馈申请退款(可完整预览的文档不适用该条件!)。
- 3、如文档侵犯您的权益,请联系客服反馈,我们会尽快为您处理(人工客服工作时间:9:00-18:30)。
陶瓷注浆模具制作、泥浆性能、成型方法一、石膏模具1、石膏的特性:石膏是模型制作的主要原料,一般为白色粉状晶体,也有灰色和淡红黄色等结晶体,属于单斜晶系,其主要成分是硫酸钙,按其中结晶水的多少又分为二水石膏和无水石膏,陶瓷工业制模生产应用一般为二水石膏,就是利用二水石膏经过180摄氏度左右的低温煅烧失去部分结晶水后成为干粉状,又可吸收水而硬化的特点。
除天然石膏外,还有人工合成石膏。
一般石膏调水搅拌均匀的凝固时间为2-8分钟,发热反应为5-8分钟,冷却后即成结实坚固的物体。
理论上石膏与水搅拌时进行化学反应需要的水量为%;在模型制作过程中,实际加水量比此数值大的多,其目的是为了获得一定流动性的石膏浆以便浇注,同时能获得表面光滑的模型;多余的水分在干燥后留下很多毛细气孔,使石膏模型具有吸水性。
吸水率是石膏模型一个重要的参数,它直接影响注浆时的成坯速度。
陶瓷用石膏模的吸水率一般在38-48%之间。
石膏粉放置在干燥的地方,使用时不要溅到水,石膏袋子要干净,严防使用过的石膏残渣或其它杂物混入袋中。
2、石膏浆的调制:(1)准备好盆和石膏粉;(2)在盆中先加入适量的水,再慢慢把石膏粉沿盆边撒入水中,一定要按照顺序先加水再加石膏。
(3)直到石膏粉冒出水面不再自然吸水沉陷,稍等片刻,就用搅拌棒搅拌,要快速有力、用力均匀。
成糊状即可。
(4)石膏在调制时的比例为:水:石膏=1:左右。
(5)注意挑除石膏浆里的硬块和杂质。
3、模型翻制操作:常用的材料和工具有:钢锯条、锯条刀,直尺三角板、毛刷、海绵、脱模剂等。
a、清理工作台,把石膏母模清理干净,在石膏母模上均匀涂抹脱模剂,一定注意各个部位必须均匀涂上,不能遗漏。
b、按顺序合模夹紧,并安放好各种模具内配件。
c、调制石膏浆,缓缓注入围好的空腔内,并不断搅动或震动石膏浆,使气泡排出,直至注满母模。
d、静置一段时间,等石膏发热固化后,可开模,如不容易打开,可以用轻敲、气冲、水冲泡等方法打开。
e、每块模具做完,都要及时用钢锯条刮平修整,模具子口要吻合。
f、做好的模具要烘干后用,烘干时温度不得高于60摄氏度,以免模具粉化报废。
注意:整个制作模具的过程要求胆大心细,必须牢记涂抹脱模剂、开牙口、刮平。
要求模具整体光滑,表面平整,内部光洁,不允许有飞棱和毛边。
二、注浆泥浆的质量要求1. 细度有恰当的细度并有一定的颗粒级配,泥浆细度是涉及泥浆流动性、制品收缩、高温液相、产品吸水率等的重要因素。
它将会影响泥浆的悬浮性、渗透性及坯体的抗折强度,注浆成型所要求的泥浆细度比较严格。
泥浆细度过粗,抗折强度低,造成较多的半成品破损,加工性能差。
待别是双面吃浆产品及立浇座便器等在双面吃浆部位,易造成接触不实,分层而在烧成中出现分层或凸起等现象,同时在烧成过程中,颗粒间接触面少,瓷化不完全,产品吸水率大,易出现风惊、炸裂。
泥浆细度的控制,首先是入磨前控制硬质原料的粒度。
它不仅影响到球磨的时间,而且影响到球磨后泥浆中的颗粒级配。
目前我国在卫生陶瓷的实际生产中,对粒度的控制普通用万孔筛(250目)筛余来表示。
其实是不科学的。
因为我们从有关资料及实践中得知,卫生陶瓷泥浆中350目筛筛余量在5-10%,小于10微米颗粒占44-55%的泥浆性能优良。
为达此目的,一方面要从配方上着手,另一方面要设法控制球磨前硬质原料粒度。
对泥浆粒度的检验也应按上述方法进行。
这对泥浆性能的稳定较有好处。
2.水分在保证流动性及成型性能的前提下,水分越少越好,通常为28%~35%,生产上习惯用控制泥浆密度来控制含水率,泥浆密度一般为~1.85g/cm3,一般小件制品可取下限,而大件制取其上限。
3.流动性泥浆的流动性要好,保证注浆时泥浆能充满整个模型。
生产上习惯用控制相对粘度即流动度来控制流动性。
要求涂-4粘度计30s,陈腐后达到45s左右,相对粘度主要与泥浆的含水率和稀释用电解质的种类和数量有关,生产上通过加入电解质来获得含水率低、流动性好的浓泥浆。
4.触变性用稠化度来衡量,它等于100ml泥浆在恩氏粘度计中静置30min后流出时间与静置30s 后流出时间的比值。
一般希望泥浆稠化度较小,以便于管道输送又能保证成坯。
触变性是指泥浆在静止时粘性会增加,一经搅拌或振动,稠化的泥浆又获得流动性,如再恢复静止状态,则又重新稠化,这种可逆变化的性能称为触变性。
泥浆的触变性主要来源于黏土性能及杂质的我少,触变性的测定方法,一般都有是测定两次流动时间,一次是搅拌后静止一分钟的流动时间a,一次是静止30分钟后的流动时间b,b/a叫做厚化系数。
稍有触变性的泥浆,坯体的加工性能要好些。
如果触变性太强,会使泥浆漏浆困难,排浆性不好,坯体还会出现糖心,易变形,模型的狭窄部位容易出现存浆裂,同时给操作带来困难,根据有关资料介绍及证明肥复实践。
5.悬浮性浆料中的固体颗粒能较长时间呈悬浮状态,这样便于泥浆的输送及贮存,在成型过程中也不易分层。
6.、泥浆的真空处理泥浆在制备、储存和输送过程中,难免会混入一定数量的空气。
为了使制品表面光洁平具有较高的机械强度、良好的物理性能,在浇注前一般要对泥浆进行真空脱气处理,另外泥浆经真空脱气处理后还可以改善其流动性。
在盛满泥浆的封闭式浆塔中,先用压缩空气进行搅拌,作用是使泥浆的组合成均匀并保持悬浮状态,减少分层现象,并使电解质的作用更加完全。
在搅拌过程中有一些细小的气泡可以随同压缩空气溢出,但是有大部分气体仍残留在泥浆中。
如果不使用真空脱气处理,泥浆中的大量气体就无法排除这样就容易使坯体产生气泡、棕眼等缺陷。
为保证制品的质量,应进行真空脱气处理,根据资料介绍,利用真空脱气装置,将50升泥浆经真空处理10-15分钟,可使干坯及制品的强度提高15-20%。
实践证明,通常要用700-720mmHg的真空度进行脱气并保持一定时间,才能起到真空脱气的作用,从而使干坯及制品的强度提高。
三、注浆料的制备流程及选择注浆料的制备流程大致与可塑料制备流程中泥浆压滤前的流程相似。
所不同的是注浆料中必须加入电解质以稀释泥浆,获得流动性好、含水率低的浓泥浆。
泥浆稀释泥浆的稀释要控制下列工艺参数。
1.合理控制泥浆的密度和颗粒细度。
当泥浆的容积密度过大,或颗粒太细时,颗粒间距较小,颗粒间引力较大,泥浆的流动阻力就大,当引力大于胶粒间的斥力时就会聚沉,反之,如果泥浆的密度过小,或颗粒太粗,则会降低成坯密度和坯体强度,泥浆也会因颗粒沉淀而破坏稳定性。
2.添加电解质及其稀释机理根据泥浆的组成和性质,选用合适的电解质作稀释剂是泥浆制备的重要措施之一。
在粘土—水系统中,粘土颗粒由于断键、同晶取代(如硅氧四面体中的Si4+被Al3+所取代,铝氧八面体中的Al+被二价的Mg+、Ca+所取代),总是带有电荷的(通常为负电荷)。
由于化水化作用,被粘土颗粒吸附的只能是水化阳离子。
距离粒子表面越远,引力也越弱,吸附阳离子浓度就越小,粘土颗粒周围形成包括吸附层和扩散层的水化膜。
粘土胶团开成了三个不同层次:胶核(粘土颗粒本身)、胶粒(胶核加吸附层)、胶团(胶粒加扩散层),胶团结构见图3-4-11。
当粘土颗粒移动时,只有吸附层随之移动。
吸附层表面对溶液存在电位差,称之为ζ电位。
胶粒的ζ电位大,则胶粒间的斥力大,不易相互聚合产生絮凝从而使泥浆稳定,流动性也好。
ζ电位主要取决于扩散层厚度和胶核表面电荷密度并与它们成正比关系。
电解质中的一价阳离子(H+除外)的电价比二价、三价的要小,但水化离子的半径却比二价三价阳离子的大,因此在泥浆中加入由一价阳离子(Na+)组成的电解质后,由于一价离子(H+除外)吸附能力弱,所以进入胶团吸附层的离子数少,使整个胶粒呈现的负电荷较多。
同时,一价离子水化能力强,进入扩散层厚度增加,水化膜加厚,导致ζ电位增加使泥浆的稳定性、流动性增强。
此外,泥浆的pH值对泥浆的稳定也有重要意义,因为粘土颗粒是片状的,一般边上带正电,面上带负电,如果加入电解质后使溶液呈碱性OH-过剩)则可使部分颗粒边上也带负电,从而防止颗粒的边-面之间因带不同电荷而相互吸引导致凝聚,促使泥浆稀释。
陶瓷工业用电解质分无机和有机两大类(多为相应钠盐),其中最常用字的有水玻璃\纯碱(Na2CO3)三聚磷酸钠、六偏磷酸钠、腐殖酸钠等。
生产是常常同时使用水玻璃和纯碱作电解质以调整吸浆速度和坯体强度。
水玻璃与纯碱的质量比可取1:3。
单用水玻璃的泥浆成坯时泥浆渗水性差,易粘模,坯体致密,强度较大;而单用纯碱的泥浆成坯体疏松吸浆速度快、脱模快,但干坯强度小。
在使用水玻璃时要选用适当的模数,即SiO2/Na2O的比值,通常取3左右。
纯碱必须防止受潮,变成NaHCO3,从而使泥浆絮凝。
电解质的用量要合适,太少不能充分置换H+、Ca2+等,太多则会使部分扩散层离子压入吸附层,使胶粒的净电荷减少,扩散层厚度减少,导致颗粒ζ电位减小,泥浆发生絮凝。
四、注浆成型操作:注浆成型主要是利用石膏模具吸收水分的特性,使泥浆吸附在模具壁上而形成均匀的泥层,在一定时间内达到所需的厚度,再倾倒出多余的泥浆,在模具中的其余泥层水分继续受石膏模具吸收而逐渐硬化,经干燥并产生体积收缩与模具脱离,即获得完好的粗坯。
(1)模具的准备和清理包括:按标准对新模型进行检查,模型内表面有油污及残缺的地方必须清除干净,新模型的水分一般为6—8%,但形状复杂小而薄的可以高一些,反之则可低一些,最低不小于4%;模型的烘干,一般控制在室温28~35℃温度,防止因干燥不均而使制品变形:使用前要将模型上附着的灰土等杂质清除干净,使模型能对合严实以避免跑浆漏泥;增强坯体在模型上的附着力,有利于防止杂质对坯体造成污染。
(2)对模型吃浆面根据脱模情况刷模,分刷滑石粉和刷水(包括清水和泥浆水)。
当脱模困难时刷滑石粉,用细纱布包裹滑石粉在吃浆面上轻轻拍打;如脱模时发现模具不挂坯,则可少刷滑石粉或者不刷滑石粉,不刷滑石粉仍不挂坯的就要用清水或者泥浆水擦模。
(3)正确进行组装对已处理好需要组合使用的模型,对正合严、夹紧、塞紧注浆管和微气压管准备注浆。
(4)泥浆要做到浆内无泥块、杂质,不可随意加水。
经真空滤气后打入注浆管道。
(5)将泥浆轻缓地注满模型,应避免“泥浆冲击”造成斑点、圈纹等缺陷。
(6)使用试验浇注杯,判断正确的放浆浆时间,从而达到要求的浇注件厚度。
(7)回浆时应预先敞开气孔,避免“抽吸”现象。
目前有三种空浆方法:自然压力回浆,即利用管道的坡度,将放出的泥浆在自然压力下流回泥浆池;利用泥浆泵,通过回浆管道,将管道及模型里多余的泥浆抽回泥浆池,这种方法往往因管道漏气影响效果;气压回浆,即利用注浆线上的微压气管打入压缩空气,压出泥浆,回浆压力控制在-。
(8)判断脱模所要求达到的固化程度(巩固时间)。
太早,注件会塌下来:太迟,注件收缩并且在受到模子束缚的地方会自行裂开,造成废品。