陶瓷注浆成型工艺要点及缺陷分析精选word资料5页
陶瓷注浆成型技术
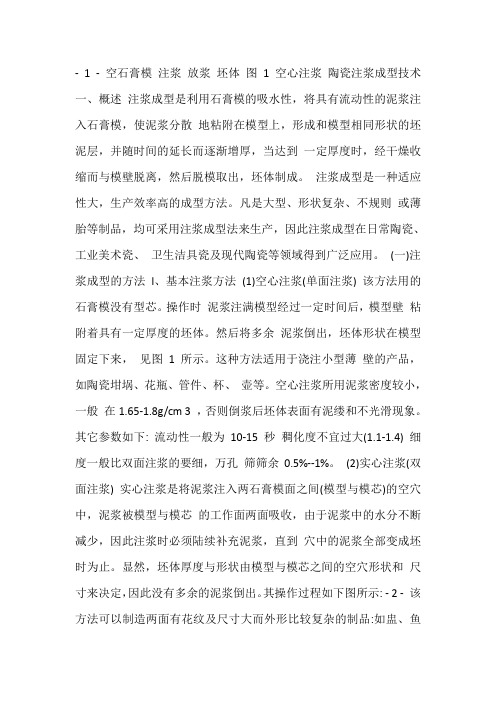
- 1 - 空石膏模注浆放浆坯体图1 空心注浆陶瓷注浆成型技术一、概述注浆成型是利用石膏模的吸水性,将具有流动性的泥浆注入石膏模,使泥浆分散地粘附在模型上,形成和模型相同形状的坯泥层,并随时间的延长而逐渐增厚,当达到一定厚度时,经干燥收缩而与模壁脱离,然后脱模取出,坯体制成。
注浆成型是一种适应性大,生产效率高的成型方法。
凡是大型、形状复杂、不规则或薄胎等制品,均可采用注浆成型法来生产,因此注浆成型在日常陶瓷、工业美术瓷、卫生洁具瓷及现代陶瓷等领域得到广泛应用。
(一)注浆成型的方法l、基本注浆方法(1)空心注浆(单面注浆) 该方法用的石膏模没有型芯。
操作时泥浆注满模型经过一定时间后,模型壁粘附着具有一定厚度的坯体。
然后将多余泥浆倒出,坯体形状在模型固定下来,见图 1 所示。
这种方法适用于浇注小型薄壁的产品,如陶瓷坩埚、花瓶、管件、杯、壶等。
空心注浆所用泥浆密度较小,一般在1.65-1.8g/cm 3 ,否则倒浆后坯体表面有泥缕和不光滑现象。
其它参数如下: 流动性一般为10-15 秒稠化度不宜过大(1.1-1.4) 细度一般比双面注浆的要细,万孔筛筛余0.5%--1%。
(2)实心注浆(双面注浆) 实心注浆是将泥浆注入两石膏模面之间(模型与模芯)的空穴中,泥浆被模型与模芯的工作面两面吸收,由于泥浆中的水分不断减少,因此注浆时必须陆续补充泥浆,直到穴中的泥浆全部变成坯时为止。
显然,坯体厚度与形状由模型与模芯之间的空穴形状和尺寸来决定,因此没有多余的泥浆倒出。
其操作过程如下图所示: - 2 - 该方法可以制造两面有花纹及尺寸大而外形比较复杂的制品:如盅、鱼盘、瓷板等。
实心注浆常用较浓的泥浆,一般密度在1.8g/cm 3 以上,以缩短吸浆时间。
稠化度(1.5 -2.2),细度可粗些,万孔筛筛余1%--2%。
2、强化注浆法为缩短注浆时间,提高注件质量,在两种基本注浆方法的基础上,形成了一些新的注浆方法,这些方法统称为强化注浆。
陶瓷高压注浆成型工艺

陶瓷高压注浆成型工艺陶瓷是一种非常重要的材料,它具有高硬度、高耐磨、高耐腐蚀等优良性能,因此被广泛应用于各种领域,如建筑、电子、化工、医疗等。
而陶瓷的制造过程中,高压注浆成型工艺是一种非常重要的工艺,它可以使陶瓷制品具有更高的密度和更好的性能。
高压注浆成型工艺是一种将陶瓷粉末和液体添加剂混合后,通过高压注入模具中,然后在高温高压下进行成型的工艺。
这种工艺可以使陶瓷制品具有更高的密度和更好的性能,同时还可以大大提高生产效率和降低成本。
高压注浆成型工艺的主要步骤包括:原料制备、混合、注浆、压制、烧结等。
其中,原料制备是非常重要的一步,它直接影响到陶瓷制品的质量和性能。
一般来说,陶瓷粉末的制备需要经过多道工序,如研磨、筛分、干燥等,以保证粉末的均匀性和细度。
而液体添加剂的制备则需要根据不同的陶瓷材料和工艺要求进行选择和调配。
混合是将陶瓷粉末和液体添加剂混合均匀的过程,这一步的目的是使粉末和液体充分结合,形成均匀的浆料。
混合的方法有很多种,如干法混合、湿法混合、球磨混合等,不同的方法适用于不同的陶瓷材料和工艺要求。
注浆是将混合好的浆料注入模具中的过程,这一步需要使用高压注浆机进行操作。
高压注浆机可以将浆料注入模具中,并在一定的时间内保持一定的压力,以保证浆料充分填充模具中的空隙。
压制是将注入模具中的浆料进行压制的过程,这一步需要使用压力机进行操作。
压力机可以将模具中的浆料进行压实,使其具有更高的密度和更好的性能。
烧结是将压制好的陶瓷制品进行高温处理的过程,这一步可以使陶瓷制品具有更高的硬度、密度和耐磨性。
烧结的温度和时间需要根据不同的陶瓷材料和工艺要求进行选择和调整。
总的来说,高压注浆成型工艺是一种非常重要的陶瓷制造工艺,它可以使陶瓷制品具有更高的密度和更好的性能,同时还可以大大提高生产效率和降低成本。
随着科技的不断发展和进步,高压注浆成型工艺也在不断地改进和完善,相信在不久的将来,它将会在更多的领域得到应用。
陶瓷新思维之缺陷分析(含注浆)

大华陶瓷杯类产品缺陷统计
大华陶瓷碟类产品缺陷统计
杯类缺陷分布图
碟类缺陷分布图
大华陶瓷应对措施
预防措施
案例总结
• 在日用陶瓷中陶瓷的装饰缺陷通过提前预防可以 达到较好的改善效果。 • 随着湿度的增大,应加强通风。若温度较低时, 应通过增大湿度以缓和湿度骤减而引起的釉裂等 缺陷的发生。缺陷控制的同时应该结合生产和人 员的管理进行,尤其随着人们环保意识的提高, 会对陶瓷装饰所用的添加剂产生一定的抵触心理 %,会在一定程度上影响产品的合格率,需要结 合一定的生产管理知识进行预防和纠正。
在此录入文字标题
(1)坯体入窑水分过高,加上预热带温度低, 碳素沉积釉中。釉的始熔温度低,釉料玻 化过早,而使沉积在釉层中的碳素不能分 解排出。 (2)坯料中碳酸盐、硫酸盐含量过高. (3)过干过热的坯体施釉,坯体与釉浆温差过 大,不能使釉料被坯体均匀吸收,导致有 些地方釉面过厚,烧成时容易封闭气孔, 使气体无法外逸。
(5)石膏模与模座不吻合
滚压常见缺陷三
产生原因
滚压成型时,滚头转速低,产生下凹花心; 滚压机转速比不合理,转速比过大则产生坯 体底心上凸的花心;滚头与模座停转时间配 合不好;热滚压成型时滚头顶部温度过高; 坯体含水率太低;泥饼在模中放置不正;使 用新模或模型与模座配合太松成型机轴承间 隙过大。
肆 瓷之物语•窑火
解决问题
• 根据结果调整了配方, 烧成有所好转。
• 请问各位问 题解决了吗?
初步结果
• 经过几次调整, 杯把把裂的情况有所好转,但 是生产不过十天又出现反复, 一直没有得到
根治。
• 因此, 技术员就大胆进行新的尝试: 用杯身 泥进行化浆注杯把的试验(行内人称之为:原 泥化浆)。
陶瓷工艺学(4.4)--注浆成型最终
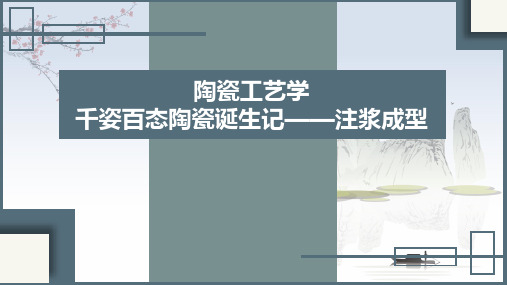
间,还可减少坯体的干燥收
为
缩和脱模后坯体的水分。注
浆压力越高,成型速度越大
生坯强度越高,但是受模型
强度的限制。模型材料可以
采用石膏模型、多孔树脂模
型和无机填料模型。
微压注浆 一般压力在0.05MPa以下 中压注浆 一般压力在0.15MPa——0.20MPa之间 高压注浆 一般压力在0.20MPa以上
单面注浆 双面注浆
压力注浆 真空注浆 离心注浆
其他注浆成型 方法
热压铸成型
成组注浆
热浆注浆
4.4 注浆成型方法
单面注浆
将泥浆注入模型中,待泥浆在模型中停留一段时间,形成所需注件厚度 时,倒出多余泥浆,随后带模干燥,待注件干燥收缩后脱模,取出注件。
单面注浆操作示意图
4.4.1 基本注浆方 法
双面注浆
本节课主要内容
4.1、
注浆过程Leabharlann 4.2、注浆成型的特点
4.3、
注浆成型对泥料的要求
4.4、
注浆方法
4.1 注浆过程
第一阶段
从泥浆注入 石膏模吸入开 始到形成薄泥 层;
第二阶段
形成薄泥层 后,泥层逐渐 增厚,知道形 成注件;
第三阶段
从雏坯成型 后到脱模为收 缩脱模阶段;
4.1 注浆过程
为了提高注浆速率,通常从以下三种方式:
陶瓷工艺学 千姿百态陶瓷诞生记——注浆成型
课程导入
川剧变脸
川剧脸谱,是川剧表演艺术中重要的组成部分,是历代川剧艺人 共同创造并传承下来的艺术瑰宝。
川剧《白蛇传》中的许仙
川剧变脸大师
课程导入
千姿百态陶瓷诞生记
泥浆
石膏模具
百态陶瓷
课程导入
陶瓷注浆成型技术

空石膏模 注浆 放浆 坯体 图1空心注浆陶瓷注浆成型技术一、概述注浆成型是利用石膏模的吸水性,将具有流动性的泥浆注入石膏模内,使泥浆分散 地粘附在模型上,形成和模型相同形状的坯泥层,并随时间的延长而逐渐增厚,当达到 一定厚度时,经干燥收缩而与模壁脱离,然后脱模取出,坯体制成。
注浆成型是一种适应性大,生产效率高的成型方法。
凡是大型、形状复杂、不规则 或薄胎等制品,均可采用注浆成型法来生产,因此注浆成型在日常陶瓷、工业美术瓷、 卫生洁具瓷及现代陶瓷等领域得到广泛应用。
(一)注浆成型的方法l 、基本注浆方法(1)空心注浆(单面注浆)该方法用的石膏模没有型芯。
操作时泥浆注满模型经过一定时间后,模型内壁粘附着具有一定厚度的坯体。
然后将多余泥浆倒出,坯体形状在模型内固定下来,见图1所示。
这种方法适用于浇注小型薄壁的产品,如陶瓷坩埚、花瓶、管件、杯、壶等。
空心注浆所用泥浆密度较小,一般在1.65—1.8g/cm 3,否则倒浆后坯体表面有泥缕和不光滑现象。
其它参数如下:流动性一般为10—15秒稠化度不宜过大(1.1—1.4)细度一般比双面注浆的要细,万孔筛筛余0.5%--1%。
(2)实心注浆(双面注浆)实心注浆是将泥浆注入两石膏模面之间(模型与模芯)的空穴中,泥浆被模型与模芯 的工作面两面吸收,由于泥浆中的水分不断减少,因此注浆时必须陆续补充泥浆,直到穴中的泥浆全部变成坯时为止。
显然,坯体厚度与形状由模型与模芯之间的空穴形状和尺寸来决定,因此没有多余的泥浆倒出。
其操作过程如下图所示:该方法可以制造两面有花纹及尺寸大而外形比较复杂的制品:如盅、鱼盘、瓷板等。
实心注浆常用较浓的泥浆,一般密度在1.8g/cm3以上,以缩短吸浆时间。
稠化度(1.5—2.2),细度可粗些,万孔筛筛余1%--2%。
2、强化注浆法为缩短注浆时间,提高注件质量,在两种基本注浆方法的基础上,形成了一些新的注浆方法,这些方法统称为强化注浆。
强化注浆主要有以下几种:(1)压力注浆采用加大泥浆压力的方法来加速水分扩散,从而加速吸浆速度。
陶瓷注浆成型技术
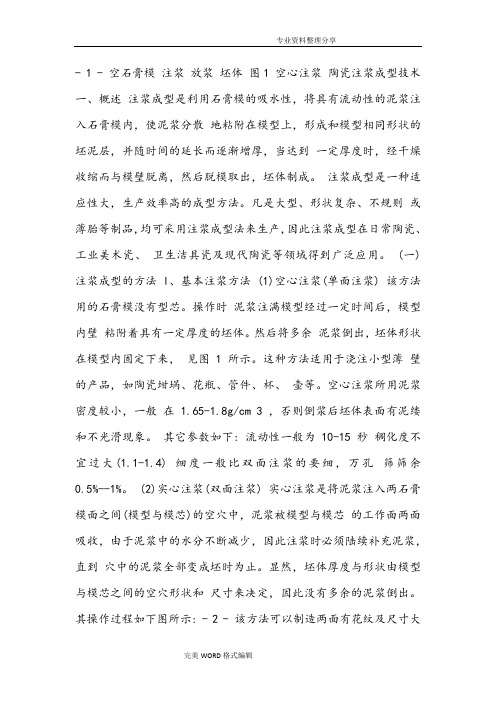
- 1 - 空石膏模注浆放浆坯体图1 空心注浆陶瓷注浆成型技术一、概述注浆成型是利用石膏模的吸水性,将具有流动性的泥浆注入石膏模内,使泥浆分散地粘附在模型上,形成和模型相同形状的坯泥层,并随时间的延长而逐渐增厚,当达到一定厚度时,经干燥收缩而与模壁脱离,然后脱模取出,坯体制成。
注浆成型是一种适应性大,生产效率高的成型方法。
凡是大型、形状复杂、不规则或薄胎等制品,均可采用注浆成型法来生产,因此注浆成型在日常陶瓷、工业美术瓷、卫生洁具瓷及现代陶瓷等领域得到广泛应用。
(一)注浆成型的方法 l、基本注浆方法 (1)空心注浆(单面注浆) 该方法用的石膏模没有型芯。
操作时泥浆注满模型经过一定时间后,模型内壁粘附着具有一定厚度的坯体。
然后将多余泥浆倒出,坯体形状在模型内固定下来,见图 1 所示。
这种方法适用于浇注小型薄壁的产品,如陶瓷坩埚、花瓶、管件、杯、壶等。
空心注浆所用泥浆密度较小,一般在 1.65-1.8g/cm 3 ,否则倒浆后坯体表面有泥缕和不光滑现象。
其它参数如下: 流动性一般为10-15 秒稠化度不宜过大(1.1-1.4) 细度一般比双面注浆的要细,万孔筛筛余0.5%--1%。
(2)实心注浆(双面注浆) 实心注浆是将泥浆注入两石膏模面之间(模型与模芯)的空穴中,泥浆被模型与模芯的工作面两面吸收,由于泥浆中的水分不断减少,因此注浆时必须陆续补充泥浆,直到穴中的泥浆全部变成坯时为止。
显然,坯体厚度与形状由模型与模芯之间的空穴形状和尺寸来决定,因此没有多余的泥浆倒出。
其操作过程如下图所示: - 2 - 该方法可以制造两面有花纹及尺寸大而外形比较复杂的制品:如盅、鱼盘、瓷板等。
实心注浆常用较浓的泥浆,一般密度在1.8g/cm 3 以上,以缩短吸浆时间。
稠化度(1.5 -2.2),细度可粗些,万孔筛筛余1%--2%。
2、强化注浆法为缩短注浆时间,提高注件质量,在两种基本注浆方法的基础上,形成了一些新的注浆方法,这些方法统称为强化注浆。
工艺学实验报告-注浆成型制作陶瓷工艺品

工艺学实验报告-注浆成型制作陶瓷工艺品第一篇:工艺学实验报告 - 注浆成型制作陶瓷工艺品注浆成型制作陶瓷工艺品一、实验目的1.应用《无机非金属材料工学》课程中所学的陶瓷工艺理论,认识原料,并确定原料组成及配比范围。
2.掌握简易石膏模具的制做方法,通过注浆成型制作陶瓷工艺品的流程。
3.以小组为单位制作一件陶瓷工艺品。
4.能对烧后制品的缺陷作合理的分析,在此基础上通过改善制备条件,获得优良的工艺品。
二、实验原理及步骤1.原料:建筑石膏:做石膏模具时使用。
钾长石:为肉红色,当块度较大时,经破碎、球磨、过筛后备用。
石英砂:白色,夹杂时带黄色。
经破碎、球磨、过筛后备用。
紫木节:为软质粘土,紫色。
可分散在水中。
大同土:为硬质粘土,白色。
经破碎、球磨、过筛后备用。
滑石:为白色。
无水碳酸钠:白色。
2.仪器及设备:电子天平,振动磨,球磨瓷瓶(带鹅卵石),空桶(陈腐料浆用),比重计,石膏模具(带捆绑绳),烧杯,小刀(或锯条),烧结炉3.步骤:①称料:总量:1kg,石英:25%,长石:27%,紫木节:22%,大同土:24%,滑石:2%,无水碳酸钠(外加):0.4%,料:水=1 :1②球磨:料:水:球=1 :1 :2(24h)③陈腐:陈腐一周。
④测比重:用比重计测定料浆比重。
⑤成型:将石膏模具组装后捆紧,从注浆口倒入搅拌均匀的泥浆,等坯体到达一定厚度后,将多于的泥浆倒出,放置4-8h。
⑥脱模:当湿坯具有一定强度后,解开模具捆绑绳,平放在桌子上,脱模。
⑦干燥:自然干燥湿坯至坯体颜色发白且具有一定强度。
⑧修坯:用小刀或锯条钝面将坯体表面凸凹不平的部分修理平整。
⑨烧成:自定烧成制度。
⑩缺陷分析:分析制品缺陷并提出解决方案以完善制备条件。
石膏模具的制作:①根据成型品的大致形状折纸模型。
②配制少量石膏浆,80%左右水,待粘稠后倒入纸模型中以粘住底部,防止漏浆。
③依据纸模型体积称量石膏粉,85%左右水,混匀并使气泡尽可能少。
粘稠后倒入纸模型内。
陶瓷注浆成型工艺

陶瓷注浆成型工艺嘿,朋友们!今天咱来聊聊陶瓷注浆成型工艺这玩意儿,可有意思啦!你想想看啊,那原本普普通通的泥浆,就像变魔术一样,能变成各种精美的陶瓷制品。
这可不是一般的神奇呀!陶瓷注浆成型呢,就像是给泥浆安了个家。
先得准备好模具,这模具就好比是个小房子,等着泥浆住进去呢。
把泥浆小心翼翼地倒进模具里,看着它慢慢地填满每一个角落,就好像给小房子穿上了一件特别的衣服。
然后呢,就得等啦!等泥浆在模具里安安稳稳地待上一段时间,让它慢慢凝固成型。
这过程就像是在等待一朵花慢慢开放,需要点耐心呢。
等泥浆凝固得差不多了,就可以把模具打开啦!哇哦,这时候你就能看到初步成型的陶瓷啦,虽然还带着点粗糙,但已经有模有样啦!不过,这可还没完事儿呢。
接下来还得给它精心修整一番,把那些不平整的地方打磨打磨,让它变得更加光滑细腻。
这就像是给一个小孩子梳妆打扮,要让它漂漂亮亮的。
你说这陶瓷注浆成型工艺是不是很有趣呀?就好像是在创造一个个小生命一样。
而且啊,通过这种方法可以做出各种各样的形状和图案,那可真是只有你想不到,没有它做不到。
你看那些摆在商店里精美的陶瓷制品,说不定就是通过陶瓷注浆成型工艺做出来的呢。
它们曾经也是普普通通的泥浆呀,经过这么一番奇妙的旅程,就变成了让人爱不释手的宝贝。
咱再想想,要是没有陶瓷注浆成型工艺,那我们的生活得少多少乐趣呀?那些漂亮的花瓶、精致的碗碟,不就都没啦?那多可惜呀!所以说呀,陶瓷注浆成型工艺可真是个了不起的发明呢!它让我们的生活变得更加丰富多彩,让我们能享受到陶瓷带来的美好。
怎么样,朋友们,是不是对陶瓷注浆成型工艺有了更深的了解呀?下次再看到那些漂亮的陶瓷制品,可别忘了它们背后的神奇工艺哦!。
陶瓷注浆
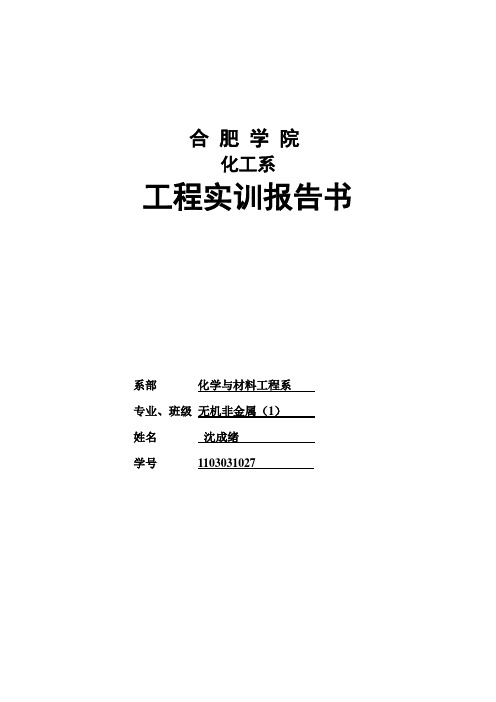
合肥学院化工系工程实训报告书系部化学与材料工程系专业、班级无机非金属(1)姓名沈成绪学号1103031027陶瓷注浆成型实验一、工程实训的目的和意义坯体的制备方面1、掌握石膏的用量,不要太多,造成浪费;也不能太少,太少会造成坯体的露底。
2、掌握石膏模具的制作方法。
泥浆的制作方面1、掌握泥浆的制备方法;2、掌握泥浆流动性的表示方法和测定方法;3、掌握影响泥浆流动性的因素及调整泥浆流动性的措施;4、了解泥浆流动性对注浆成形性能的影响。
注浆方面1、掌握陶瓷注浆成型的工艺流程。
2、掌握陶瓷烧成过程中的方法。
总体来说,锻炼学生动手能力、综合运用专业知识的能力和团队合作能力。
二、工程实训内容所涉及的理论知识概述陶瓷注浆是基于多孔石膏模具能够吸收水分的物理特性,将陶瓷粉料配成具有流动性的泥浆,然后注入多孔模具内(主要为石膏模),水分在被模具(石膏)吸入后便形成了具有一定厚度的均匀泥层,脱水干燥过程中同时形成具有一定强度的坯体,此种方式被称为注浆成型。
三、工程实训内容1、原料石膏、水、陶瓷原料、高岭土2、仪器和设备盆、盒子、玻璃杯、搅拌器、恩格拉(恩氏)流量计3、方案、方法和步骤石膏浆的调制:(1)准备好盆和石膏粉;(2)在盆中先加入适量的水,再慢慢把石膏粉沿盆边撒入水中,一定要按照顺序先加水再加石膏。
(3)直到石膏粉冒出水面不再自然吸水沉陷,稍等片刻,就用搅拌棒搅拌,要快速有力、用力均匀。
成糊状即可。
(4)石膏在调制时的比例为:水:石膏=1:1.4-1.8左右。
(5)注意挑除石膏浆里的硬块和杂质。
模具的制作:(1)、清理工作台,把石膏母模清理干净,在石膏母模上均匀涂抹脱模剂,一定注意各个部位必须均匀涂上,不能遗漏。
(2)、按顺序合模夹紧,并安放好各种模具内配件。
(3)、静置一段时间,等石膏发热固化后,可开模,如不容易打开,可以用轻敲、气冲、水冲泡等方法打开。
(4)、每块模具做完,都要及时用钢锯条刮平修整,模具子口要吻合。
(完整word版)陶瓷注浆成型技术

—1 - 空石膏模注浆放浆坯体图1 空心注浆陶瓷注浆成型技术一、概述注浆成型是利用石膏模的吸水性,将具有流动性的泥浆注入石膏模内,使泥浆分散地粘附在模型上,形成和模型相同形状的坯泥层,并随时间的延长而逐渐增厚,当达到一定厚度时,经干燥收缩而与模壁脱离,然后脱模取出,坯体制成。
注浆成型是一种适应性大,生产效率高的成型方法。
凡是大型、形状复杂、不规则或薄胎等制品,均可采用注浆成型法来生产,因此注浆成型在日常陶瓷、工业美术瓷、卫生洁具瓷及现代陶瓷等领域得到广泛应用. (一)注浆成型的方法l、基本注浆方法(1)空心注浆(单面注浆) 该方法用的石膏模没有型芯。
操作时泥浆注满模型经过一定时间后,模型内壁粘附着具有一定厚度的坯体。
然后将多余泥浆倒出,坯体形状在模型内固定下来,见图1 所示。
这种方法适用于浇注小型薄壁的产品,如陶瓷坩埚、花瓶、管件、杯、壶等。
空心注浆所用泥浆密度较小,一般在1.65-1。
8g/cm 3 ,否则倒浆后坯体表面有泥缕和不光滑现象。
其它参数如下: 流动性一般为10-15 秒稠化度不宜过大(1.1-1.4)细度一般比双面注浆的要细,万孔筛筛余0.5%——1%。
(2)实心注浆(双面注浆)实心注浆是将泥浆注入两石膏模面之间(模型与模芯)的空穴中,泥浆被模型与模芯的工作面两面吸收,由于泥浆中的水分不断减少,因此注浆时必须陆续补充泥浆,直到穴中的泥浆全部变成坯时为止。
显然,坯体厚度与形状由模型与模芯之间的空穴形状和尺寸来决定,因此没有多余的泥浆倒出。
其操作过程如下图所示:— 2 —该方法可以制造两面有花纹及尺寸大而外形比较复杂的制品:如盅、鱼盘、瓷板等。
实心注浆常用较浓的泥浆,一般密度在1。
8g/cm 3 以上,以缩短吸浆时间。
稠化度(1。
5 —2。
2),细度可粗些,万孔筛筛余1%-—2%. 2、强化注浆法为缩短注浆时间,提高注件质量,在两种基本注浆方法的基础上,形成了一些新的注浆方法,这些方法统称为强化注浆。
瓷器注浆工艺

瓷器注浆工艺瓷器是我国传统的文化瑰宝之一,其精美的工艺和独特的艺术价值一直以来受到人们的喜爱。
而其中的注浆工艺更是瓷器制作过程中不可或缺的一环。
注浆工艺是指在瓷器成型前,将液态瓷浆注入模具中,经过一定的处理后,形成瓷器的基础形状。
下面我们就来详细了解一下瓷器注浆工艺的具体步骤和注意事项。
瓷器注浆工艺的第一步是准备瓷浆。
瓷浆是由瓷土和一定比例的水混合而成,其中的瓷土是由石英、长石和高岭土等原料经过精细研磨而成。
在准备瓷浆的过程中,需要根据不同的瓷器种类和工艺要求,控制好瓷土的配比和研磨时间,以确保瓷浆的质量和流动性。
接下来,将准备好的瓷浆注入模具中。
模具是用来塑造瓷器形状的工具,通常由石膏或金属制成。
在注浆过程中,需要将瓷浆缓慢而均匀地注入模具中,以免产生气泡或不均匀的厚度。
同时,需要控制好注浆的速度和压力,以确保注入的瓷浆能够填满整个模具,并且与模具表面贴合紧密。
注浆完成后,需要进行瓷器的初步成型。
这个过程通常包括振动、压实和脱模。
振动可以帮助瓷浆在模具中排除多余的气泡,并增加瓷器的密实度。
压实是为了进一步增加瓷器的密度和硬度,通常通过在模具上施加一定的压力来实现。
脱模是指将初步成型的瓷器从模具中取出,这一步需要注意轻拿轻放,以免损坏瓷器的形状。
经过初步成型后,瓷器还需要进行干燥和烧制。
干燥是为了去除瓷器中的水分,通常采用自然风干或低温烘干的方式。
烧制是最后一个环节,也是最关键的一步。
在烧制过程中,瓷器需要经历一系列的温度变化,从而使其逐渐变得坚硬和耐用。
同时,还需要控制好烧制温度和时间,以保证瓷器的质量和色泽。
总结起来,瓷器注浆工艺是瓷器制作中不可或缺的一环,它决定了瓷器的基本形状和质地。
在注浆工艺中,需要准备好瓷浆,并将其缓慢而均匀地注入模具中。
注浆完成后,还需要进行初步成型、干燥和烧制等环节,以最终完成一件美丽的瓷器作品。
瓷器注浆工艺的传承和创新是瓷器制作过程中的重要环节。
在传统的基础上,我们可以结合现代科技和工艺,不断提高瓷浆配比的准确性和瓷器成型的精细度,以满足不同人们对瓷器的需求。
浅析卫生陶瓷的压力注浆工艺
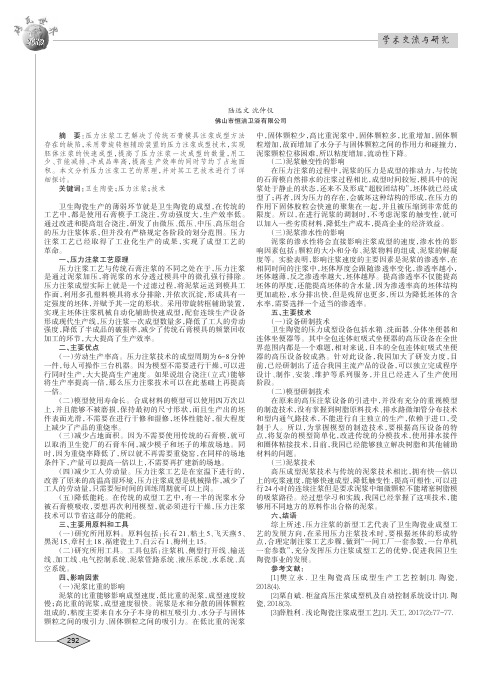
2019浅析卫生陶瓷的压力注浆工艺陆远文沈仲仪佛山市恒洁卫浴有限公司实现提高了压力注浆一次成型的数量,用工提高生产效率的同时节约了占地面并对其工艺技术进行了详压力注浆;技术在传统的劳动强度大,生产效率低。
研发了由微压、低压、中压、高压组合但并没有严格规定各阶段的划分范围。
压力实现了成型工艺的压力注浆将泥浆的水分透过模具中的微孔强行排除。
将泥浆运送到模具工并依次沉淀,形成具有一并赋予其一定的形状。
采用带旋转框辅助装置,配套连续生产设备压力注浆一次成型数量多,降低了工人的劳动减少了传统石膏模具的频繁回收6-8分钟可以进(立式)能够那么压力注浆技术可以在此基础上再提高保持最初的尺寸形状,而且生产出的坯坯体性能好,很大程度就可减少模子和坯子的堆放场地。
同所以就不再需要重烧窑,在同样的场地不需要再扩建新的场地。
压力注浆成型是机械操作,减少了只需要短时间的训练周期就可以上岗。
有一半的泥浆水分要想再次利用模型,就必须进行干燥,压力注浆长石21、粘土5、飞天燕5、18、福建瓷土7、白云石1、梅州土15。
注浆机、侧型打开线、输送泥浆管路系统、液压系统、水系统、真低比重的泥浆,成型速度较成型速度很快。
泥浆是水和分散的固体颗粒水分子与固体固体颗粒之间的吸引力。
在低比重的泥浆中,固体颗粒少,高比重泥浆中,固体颗粒多,比重增加,固体颗粒增加,故而增加了水分子与固体颗粒之间的作用力和碰撞力,泥浆颗粒位移困难,所以粘度增加,流动性下降。
(二)泥浆触变性的影响在压力注浆的过程中,泥浆的压力是成型的推动力,与传统的石膏模自然排水的注浆过程相比,成型时间较短,模具中的泥浆处于静止的状态,还来不及形成“超胶团结构”,坯体就已经成型了;再者,因为压力的存在,会破坏这种结构的形成,在压力的作用下固体胶粒会快速的聚集在一起,并且被压缩到非常低的限度。
所以,在进行泥浆的调制时,不考虑泥浆的触变性,就可以加入一些劣质材料,降低生产成本,提高企业的经济效益。
陶瓷注浆模具制作、泥浆性能、成型方法重点讲义资料
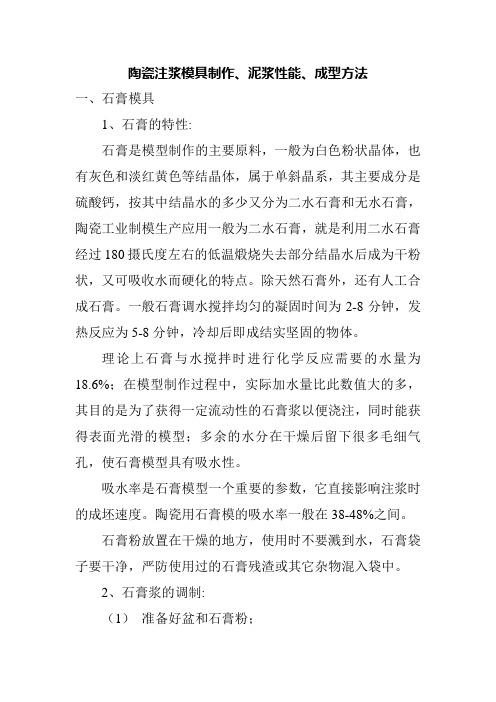
陶瓷注浆模具制作、泥浆性能、成型方法一、石膏模具1、石膏的特性:石膏是模型制作的主要原料,一般为白色粉状晶体,也有灰色和淡红黄色等结晶体,属于单斜晶系,其主要成分是硫酸钙,按其中结晶水的多少又分为二水石膏和无水石膏,陶瓷工业制模生产应用一般为二水石膏,就是利用二水石膏经过180摄氏度左右的低温煅烧失去部分结晶水后成为干粉状,又可吸收水而硬化的特点。
除天然石膏外,还有人工合成石膏。
一般石膏调水搅拌均匀的凝固时间为2-8分钟,发热反应为5-8分钟,冷却后即成结实坚固的物体。
理论上石膏与水搅拌时进行化学反应需要的水量为18.6%;在模型制作过程中,实际加水量比此数值大的多,其目的是为了获得一定流动性的石膏浆以便浇注,同时能获得表面光滑的模型;多余的水分在干燥后留下很多毛细气孔,使石膏模型具有吸水性。
吸水率是石膏模型一个重要的参数,它直接影响注浆时的成坯速度。
陶瓷用石膏模的吸水率一般在38-48%之间。
石膏粉放置在干燥的地方,使用时不要溅到水,石膏袋子要干净,严防使用过的石膏残渣或其它杂物混入袋中。
2、石膏浆的调制:(1)准备好盆和石膏粉;(2)在盆中先加入适量的水,再慢慢把石膏粉沿盆边撒入水中,一定要按照顺序先加水再加石膏。
(3)直到石膏粉冒出水面不再自然吸水沉陷,稍等片刻,就用搅拌棒搅拌,要快速有力、用力均匀。
成糊状即可。
(4)石膏在调制时的比例为:水:石膏=1:1.4-1.8左右。
(5)注意挑除石膏浆里的硬块和杂质。
3、模型翻制操作:常用的材料和工具有:钢锯条、锯条刀,直尺三角板、毛刷、海绵、脱模剂等。
a、清理工作台,把石膏母模清理干净,在石膏母模上均匀涂抹脱模剂,一定注意各个部位必须均匀涂上,不能遗漏。
b、按顺序合模夹紧,并安放好各种模具内配件。
c、调制石膏浆,缓缓注入围好的空腔内,并不断搅动或震动石膏浆,使气泡排出,直至注满母模。
d、静置一段时间,等石膏发热固化后,可开模,如不容易打开,可以用轻敲、气冲、水冲泡等方法打开。
注浆陶艺经验总结范文
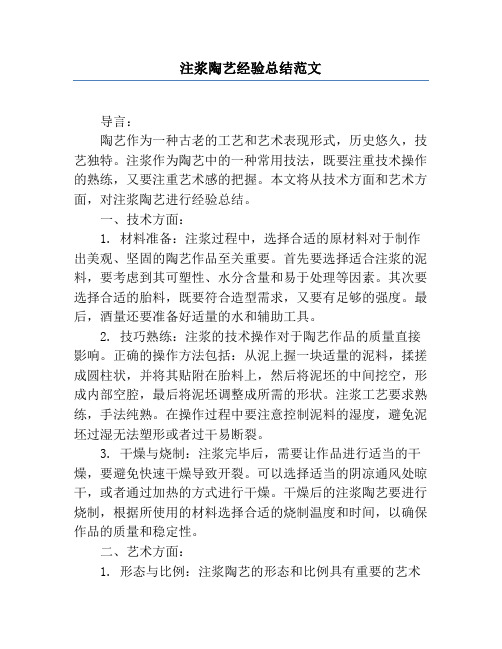
注浆陶艺经验总结范文导言:陶艺作为一种古老的工艺和艺术表现形式,历史悠久,技艺独特。
注浆作为陶艺中的一种常用技法,既要注重技术操作的熟练,又要注重艺术感的把握。
本文将从技术方面和艺术方面,对注浆陶艺进行经验总结。
一、技术方面:1. 材料准备:注浆过程中,选择合适的原材料对于制作出美观、坚固的陶艺作品至关重要。
首先要选择适合注浆的泥料,要考虑到其可塑性、水分含量和易于处理等因素。
其次要选择合适的胎料,既要符合造型需求,又要有足够的强度。
最后,酒量还要准备好适量的水和辅助工具。
2. 技巧熟练:注浆的技术操作对于陶艺作品的质量直接影响。
正确的操作方法包括:从泥上握一块适量的泥料,揉搓成圆柱状,并将其贴附在胎料上,然后将泥坯的中间挖空,形成内部空腔,最后将泥坯调整成所需的形状。
注浆工艺要求熟练,手法纯熟。
在操作过程中要注意控制泥料的湿度,避免泥坯过湿无法塑形或者过干易断裂。
3. 干燥与烧制:注浆完毕后,需要让作品进行适当的干燥,要避免快速干燥导致开裂。
可以选择适当的阴凉通风处晾干,或者通过加热的方式进行干燥。
干燥后的注浆陶艺要进行烧制,根据所使用的材料选择合适的烧制温度和时间,以确保作品的质量和稳定性。
二、艺术方面:1. 形态与比例:注浆陶艺的形态和比例具有重要的艺术价值。
在注浆前,要对作品的形态进行规划和设计,考虑到作品所要表达的主题和意境,确定形状、大小和比例等方面。
要注重整体感和动态美,根据作品的需要灵活运用线条和曲面等造型元素,使作品更具美感。
2. 表面处理:注浆陶艺的表面处理也是关键。
可以运用各种表面处理技法,如刻划、雕花、上釉等,使作品更加生动、有层次感。
在选择处理方式时要根据作品风格和主题进行合理选择,避免琐碎和过度装饰,保持作品与自然、自然的的关系。
3. 色彩运用:色彩是注浆陶艺中不可忽视的部分。
注浆作品可以通过采用色浆和釉料进行涂抹,可以在焙烧后呈现出丰富的色彩变化。
在使用色彩时要注重色彩的搭配和运用技巧,使作品呈现出丰富而和谐的色彩效果。
陶瓷注浆工艺技术
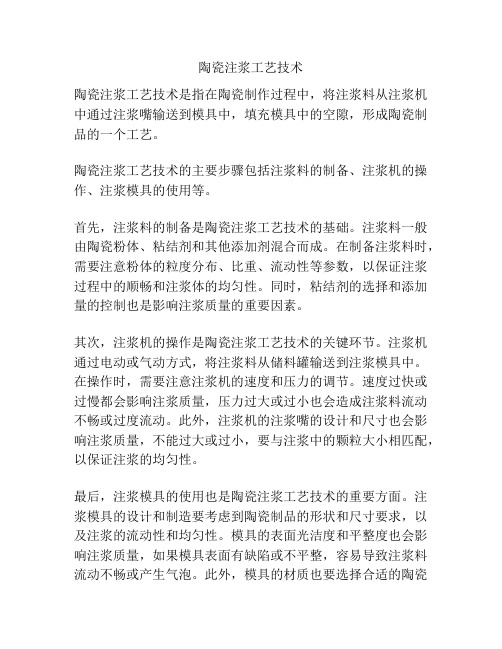
陶瓷注浆工艺技术陶瓷注浆工艺技术是指在陶瓷制作过程中,将注浆料从注浆机中通过注浆嘴输送到模具中,填充模具中的空隙,形成陶瓷制品的一个工艺。
陶瓷注浆工艺技术的主要步骤包括注浆料的制备、注浆机的操作、注浆模具的使用等。
首先,注浆料的制备是陶瓷注浆工艺技术的基础。
注浆料一般由陶瓷粉体、粘结剂和其他添加剂混合而成。
在制备注浆料时,需要注意粉体的粒度分布、比重、流动性等参数,以保证注浆过程中的顺畅和注浆体的均匀性。
同时,粘结剂的选择和添加量的控制也是影响注浆质量的重要因素。
其次,注浆机的操作是陶瓷注浆工艺技术的关键环节。
注浆机通过电动或气动方式,将注浆料从储料罐输送到注浆模具中。
在操作时,需要注意注浆机的速度和压力的调节。
速度过快或过慢都会影响注浆质量,压力过大或过小也会造成注浆料流动不畅或过度流动。
此外,注浆机的注浆嘴的设计和尺寸也会影响注浆质量,不能过大或过小,要与注浆中的颗粒大小相匹配,以保证注浆的均匀性。
最后,注浆模具的使用也是陶瓷注浆工艺技术的重要方面。
注浆模具的设计和制造要考虑到陶瓷制品的形状和尺寸要求,以及注浆的流动性和均匀性。
模具的表面光洁度和平整度也会影响注浆质量,如果模具表面有缺陷或不平整,容易导致注浆料流动不畅或产生气泡。
此外,模具的材质也要选择合适的陶瓷材料,以确保注浆过程中不会与注浆料发生化学反应或产生颜色变化。
陶瓷注浆工艺技术的发展使得陶瓷制品的生产效率和质量得到了较大的提高。
通过不断改进注浆料的成分和配比,优化注浆机的结构和性能,设计和制造高精度的注浆模具,可以生产出形状复杂、尺寸精确、表面光洁度高的陶瓷制品。
同时,陶瓷注浆工艺技术也有助于减少生产过程中的废品率和能源消耗,降低成本,提高生产效益。
总之,陶瓷注浆工艺技术是陶瓷制品生产过程中不可缺少的一部分。
只有掌握和应用好注浆工艺技术,才能生产出高质量的陶瓷制品。
浅论耀州瓷注浆成型中的缺陷及解决方法
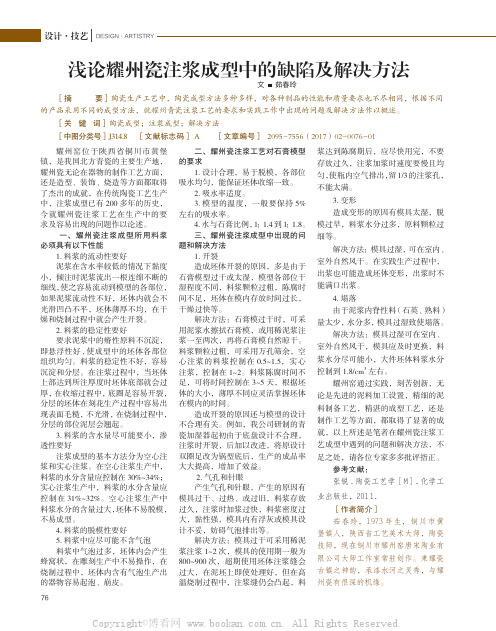
76DESIGN·ARTISTRY设计·技艺浅论耀州瓷注浆成型中的缺陷及解决方法[摘 要]陶瓷生产工艺中,陶瓷成型方法多种多样,对各种制品的性能和质量要求也不尽相同,根据不同的产品采用不同的成型方法,就耀州青瓷注浆工艺的要求和实践工作中出现的问题及解决方法作以概述。
[关 键 词]陶瓷成型;注浆成型;解决方法[中图分类号]J314.8 [文献标志码] A [文章编号] 2095-7556(2017)02-0076-01文 茹春玲耀州窑位于陕西省铜川市黄堡镇,是我国北方青瓷的主要生产地,耀州瓷无论在器物的制作工艺方面,还是造型、装饰、烧造等方面都取得了杰出的成就,在传统陶瓷工艺生产中,注浆成型已有200多年的历史,今就耀州瓷注浆工艺在生产中的要求及容易出现的问题作以论述。
一、耀州瓷注浆成型所用料浆必须具有以下性能1.料浆的流动性要好泥浆在含水率较低的情况下黏度小,倾注时泥浆流出一根连绵不断的细线,使之容易流动到模型的各部位,如果泥浆流动性不好,坯体内就会不光滑凹凸不平,坯体薄厚不均,在干燥和烧制过程中就会产生开裂。
2.料浆的稳定性要好要求泥浆中的瘠性原料不沉淀,即悬浮性好,使成型中的坯体各部位组织均匀。
料浆的稳定性不好,容易沉淀和分层。
在注浆过程中,当坯体上部达到所注厚度时坯体底部就会过厚,在收缩过程中,底圈足容易开裂,分层的坯体在刻花生产过程中容易出现表面毛糙,不光滑,在烧制过程中,分层的部位泥层会翘起。
3.料浆的含水量尽可能要小,渗透性要好注浆成型的基本方法分为空心注浆和实心注浆。
在空心注浆生产中,料浆的水分含量应控制在30%~34%;实心注浆生产中,料浆的水分含量应控制在31%~32%。
空心注浆生产中料浆水分的含量过大,坯体不易脱模,不易成型。
4.料浆的脱模性要好5.料浆中应尽可能不含气泡料浆中气泡过多,坯体内会产生蜂窝状,在雕刻生产中不易操作,在烧制过程中,坯体内含有气泡生产出的器物容易起泡、崩皮。
工艺学实验报告-注浆成型制作陶瓷工艺品
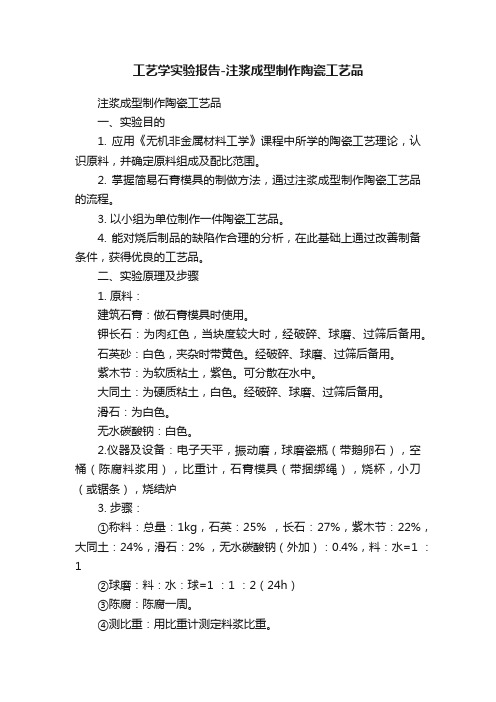
工艺学实验报告-注浆成型制作陶瓷工艺品注浆成型制作陶瓷工艺品一、实验目的1. 应用《无机非金属材料工学》课程中所学的陶瓷工艺理论,认识原料,并确定原料组成及配比范围。
2. 掌握简易石膏模具的制做方法,通过注浆成型制作陶瓷工艺品的流程。
3. 以小组为单位制作一件陶瓷工艺品。
4. 能对烧后制品的缺陷作合理的分析,在此基础上通过改善制备条件,获得优良的工艺品。
二、实验原理及步骤1. 原料:建筑石膏:做石膏模具时使用。
钾长石:为肉红色,当块度较大时,经破碎、球磨、过筛后备用。
石英砂:白色,夹杂时带黄色。
经破碎、球磨、过筛后备用。
紫木节:为软质粘土,紫色。
可分散在水中。
大同土:为硬质粘土,白色。
经破碎、球磨、过筛后备用。
滑石:为白色。
无水碳酸钠:白色。
2.仪器及设备:电子天平,振动磨,球磨瓷瓶(带鹅卵石),空桶(陈腐料浆用),比重计,石膏模具(带捆绑绳),烧杯,小刀(或锯条),烧结炉3. 步骤:①称料:总量:1kg,石英:25% ,长石:27%,紫木节:22%,大同土:24%,滑石:2% ,无水碳酸钠(外加):0.4%,料:水=1 :1②球磨:料:水:球=1 :1 :2(24h)③陈腐:陈腐一周。
④测比重:用比重计测定料浆比重。
⑤成型:将石膏模具组装后捆紧,从注浆口倒入搅拌均匀的泥浆,等坯体到达一定厚度后,将多于的泥浆倒出,放置4-8h。
⑥脱模:当湿坯具有一定强度后,解开模具捆绑绳,平放在桌子上,脱模。
⑦干燥:自然干燥湿坯至坯体颜色发白且具有一定强度。
⑧修坯:用小刀或锯条钝面将坯体表面凸凹不平的部分修理平整。
⑨烧成:自定烧成制度。
⑩缺陷分析:分析制品缺陷并提出解决方案以完善制备条件。
石膏模具的制作:①根据成型品的大致形状折纸模型。
②配制少量石膏浆,80%左右水,待粘稠后倒入纸模型中以粘住底部,防止漏浆。
③依据纸模型体积称量石膏粉,85%左右水,混匀并使气泡尽可能少。
粘稠后倒入纸模型内。
④将事先抹好肥皂的模型浸入石膏中,留少许边缘以方便取出。
陶瓷注射成型混料工艺及坯体产生缺陷研究
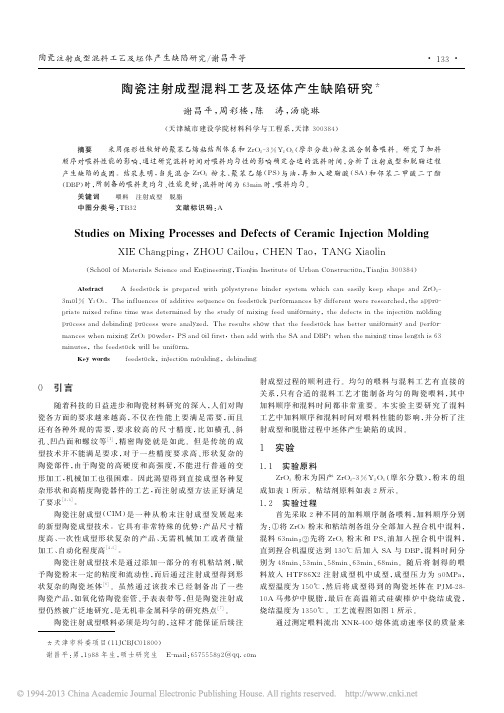
2 结 果 与 讨 论
2.1 加 料 顺 序 对 陶 瓷 喂 料 性 能 的 影 响 通过表3可以看 出,加 料 顺 序 为 ② 时,制 得 的 坯 体 与 烧
结体的密度都比加料顺序为① 时高,这是因为加 料 顺 序 为 ② 时,ZrO2 粉末与有机粘 结 剂 混 合 更 均 匀,粘 结 剂 能 有 序 地 包 裹 ZrO2 颗粒。
影响注射成型过程的因素有很多,如 注 射 温 度 ﹑ 注 射 压 力﹑保压压力及时间和注射速度等,往往缺陷 的 产 生 不 仅 仅 是单一因素 影 响 的 结 果,更 多 的 是 几 种 因 素 共 同 作 用 造 成 的。下面是几种注射成型过程产生的缺陷及其成因分析。
表 2 粘 结 剂 组 成 及 性 能
Table 2 Constitutions and functions of binding
粘结剂组成
密 度/(g/cm3)
熔 点/℃
PS
1.05
240
SA
0.94
72
DBP 油
1.042~1.048 0.94
图 1 陶 瓷 注 射 成 型 流 程 图 Fig.1 Ceramic injection molding flow chart
通过测定喂料流出 XNR-400熔 体 流 动 速 率 仪 的 质 量 来
* 天 津 市 科 委 项 目 (11JCBJC01800) 谢 昌 平 :男 ,1988 年 生 ,硕 士 研 究 生 E-mail:657555892@qq.com
· 134 ·
材料导报 B:研究篇
2012 年 8 月 (下 )第 26 卷 第 8 期
different load at 130℃
载 重/N m/g
- 1、下载文档前请自行甄别文档内容的完整性,平台不提供额外的编辑、内容补充、找答案等附加服务。
- 2、"仅部分预览"的文档,不可在线预览部分如存在完整性等问题,可反馈申请退款(可完整预览的文档不适用该条件!)。
- 3、如文档侵犯您的权益,请联系客服反馈,我们会尽快为您处理(人工客服工作时间:9:00-18:30)。
陶瓷注浆成型工艺要点及缺陷分析
一、陶瓷注浆成型工艺要点
注浆成型是一种适应性广、生产效率高的成型方法,凡是形状复杂或不规则、不能用其他方法成型以及薄胎制品都可用注浆成型来生产但是由于温、湿度对坯体成型影响较大,直接关系到半成品的质量和成品率的高低,所以生产时必须对环境温度、湿度进行严格的控制以及季节的变化采取相应的措施。
1、对石膏模型的要求
(1)设计合理,易于脱模,各部位及吸水均匀,能保证坯体收缩一致。
(2)孔隙率和吸水率适度,比可塑成型模型略大。
(3)模型的湿度要严格控制,一般应保持5%左右的吸水率,过干会引起坯体开裂;过湿会延长注浆时间,甚至难于成型。
2、对泥浆性能的要求
为了提高注浆生产效率,并获得高质量的坯件,要求泥浆具有良好的性能。
(1)流动性好,要求泥浆在含水率较低的情况下粘度小,倾注时泥浆流出一根连绵不断的细线,使之容易流动到模型的各部位。
(2)稳定性好,要求泥浆中的瘠性原料不沉淀,即悬浮性好,使成型后的坯体各部位组织均匀。
(3)触变性适宜,即粘度不宜过大。
(4)渗透性好,即过滤性好,要求泥浆中的水分能顺利通过粘附在模壁上的泥层而被石膏吸收。
(5)不含气泡,以利于增加坯体的强度。
一、注浆成型生产对环境温度、湿度的要求
3、对环境温度、湿度的要求
注浆成型的卫生瓷操作的温度一般控制在25度—37度为好,夜间的温度可以提高一些,但也不能超过50度,因为超过50度,一方面坯体的外表面干燥速度过快,而坯体内表面的干燥速度则相对较慢,造成坯体在干燥过程中内外收缩不均,导致坯体在干燥过程中开裂;另一方面温度超过50度容易使石膏模过干、过热,而且石膏模形状复杂,各部分干湿度不均,在成型过程中很容易造成吃浆过快以及成型后坯体气孔率增大等缺陷。
成型操作的湿度一般控制在50-70%,过高则坯体的干燥速度太慢,影响下道工序的正常进行,过低坯体干燥速度加快,收缩速度也在加快,容易产生开裂,特别是成型复杂的产品在应力集中的部位,开裂更加严重。
4.注浆成型的坯体对季节的要求
注浆成型的坯体质量对季节的变化比较敏感,特别是春秋季节对坯体成型影响最大。
因为春秋季节风比较大,空气又比较干燥,在这样的条件下,如果不采取合理的措施,坯体在成型阶段就造成大面积的风裂,严重影响坯体的收成率。
主要原因是风不可能均匀地吹到坯体的各个部位,造成坯体各个部位干燥不均匀,局部收缩过快而产生开裂。
因此,春秋季节坯体成型要注意的问题是:
(1)成型车间不能开窗户,门上要挂门帘,避免外面的风直接吹到室内的坯体上,必要时可以用薄膜全部将坯体盖起来,这样在干燥过程中收缩均匀。
(2)春秋季节要经常在成型操作室内四周喷洒一些水,喷水的目的是增加室内的湿度。
喷洒水量要求刚进入春秋季节时少喷洒,慢慢地增多,在接近夏季和冬季时慢慢减少,但要注意阴、雨天要少喷洒甚至不洒水。
夏季风比较小,湿度较大,室内不要喷洒水可以开窗户。
冬季一定要把窗户缝糊好,保证室内温度。
因此,在生产过程中根据季节的变化采取相应的保护措施以及控制好生产环境的温度和湿度,对提高产品质量和收成率是十分有益的。
二、陶瓷注浆成型缺陷分析
1、气孔与针眼
(1)泥浆的流动性差,粘度大,致使泥浆中的气泡不易排出。
(2)泥浆未经陈腐,或电解质种类及用量不当。
(3)搅拌泥浆太剧烈,或注浆速度太快,使泥浆中夹有气泡,或泥浆真空脱泡处理不严。
(4)石膏模过湿、过干、过旧,或模型表面沾有灰尘。
2、泥缕
主要原因是泥浆的粘度大,流动性差,或因倾浆操作不当,或模型工作面沾有浆滴。
还有一种情况,因进浆时集中于模型内某一局部,由于泥浆的冲击而形成这一局部颗粒取向排列不同,致使干燥收缩时隆起成筋状,即使经过车修或用刀削平,烧后仍有明显的泥缕。
3、开裂
(1)泥浆配方不当;
(2)陈腐不足、不均;
(3)操作不当、厚薄坯;
(4)脱模太早或太迟;
(5)接坯的双部分干湿不一致。
4、变形
(1)泥浆水分太高,干燥收缩过大。
(2)泥浆混合不匀,干燥收缩不一。
(3)倾浆操作不当,坯体厚薄不匀。
(4)模型过湿,或脱模过早,出模操作不当,湿坯没有放平、放正。