电子束焊要求
电子束焊接

1.3.1 焊前准备
焊前清理:真空电子束焊前必须对焊件表面
进行严格清理,否则将导致焊缝产生缺陷, 接头的力学性能降低,不清洁的表面还会延 长抽真空时间,影响电子枪工作的稳定性, 降低真空泵的使用寿命。
1.3.1 焊前准备
观察窗口通常由三重玻璃组成,里层为普通玻璃;中层 的铅玻璃是防护X射线的作用;外层的钢化玻璃是承受 真空室内外压力差的。
采用工业电视可以使操作者能连续观察焊接过程,防止 肉眼受强烈光线刺激的危害。
1.2.2 电子束焊机的选用
选用电子束焊机通常考虑以下几个方面: 焊接化学性能活泼的金属(如W、Ta、Mo等)及其合金应
零件装配: 对于无锁底的对接接头,板厚δ<1.5mm时,局部最
大间隙不应超过0.07 mm;随板厚增加,间隙略增。 板厚超过3.8mm时,局部最大间隙可到0.25 mm。
焊薄工件时,一般装配间隙不应大于0.13mm。
1.3.1 焊前准备
非真空电子束焊时,装配间隙可以放宽到0.75mm。 深熔焊时,装配不良或间隙过大,会导致过量收缩、 咬边、漏焊等缺陷。
1.1.2 电子束焊的特点及分类
2.电子束焊的缺点 设备比较复杂,投资大,费用较昂贵; 电子束焊要求接头位置准确,间隙小而且均匀,
焊前对接头加工、装配要求严格; 真空电子束焊接时,被焊工件尺寸和形状常常受到
工作室的限制; 电子束易受杂散电磁场的干扰,影响焊接质量; 电子束焊接时产生X射线,需要操作人员严加防护。
由电子枪、工作室(也 称真空室)、电源及电 气控制系统、真空系统、 工作台以及辅助装置等 几大部分组成。
1.2.1 电子束焊机的组成
JB_T11062_2010_电子束焊接工艺指南_介绍_赵霞

GB/T 19867.3—2008 《电子束焊接工艺规 程 》、 GB/T 22085.1—2008 《电 子 束 及 激 光 焊 接接头 缺欠质量分级指南 第 1 部分: 钢》、 GB/T 22085.2—2008 《电子束及激光焊接接头
缺欠质量分级指南 第 2 部分: 铝及铝合 金》、 ISO 14744-1∶2008 《焊接 电 子束焊 接 机的验收检验 第 1 部分: 原理和验收条件》 和 ISO 15614-11∶2002 《金属材料焊接程序的 规范 和鉴定 焊 接 程 序 试 验 第 11 部 分 电 子和激光束焊接》 等标准所确立的术语和定义 适 用 于 JB/T 11062—2010, 同 时 JB/T 11062—2010 中 还 补 充 规 定 了 加 速 电 压 、 束 流、 束流摆动、 修饰焊道、 离焦量、 焦距、 工 作距离、 透镜电流、 斜坡下降、 斜坡上升、 钉 尖、 排气孔、 工作压力、 夹层材料、 过渡材料 等术语。
JB/T 11062—2010 中 还 规 定 了 焊 接 工 艺 评定、 接头制备、 接头设计、 排气孔、 定位焊 及修饰焊、 焊前及焊后热处理及文件记录等的 技术要求。
5 附录
JB/T 11062—2010 中 列 有 资 料 性 附 录 A、 附录 B、 附录 C 及附录 D。
(1) 附录 A 附录 A 中阐述了金属材料焊接性。 聚焦的 电子束可以熔化所有的金属材料, 所以几乎所 有纯金属和合金都可以成功焊接。 附录 A 基于 金属材料主要元素, 对黑色金属、 镍及镍合金、 铝镁合金、 铜及铜合金、 难熔金属和活性金属、 异种金属等不同材料的焊接特性逐一阐述。 (2) 附录 B 附录 B 以列表的方式阐明钢、 铝及铝合 金、 铜及铜合金、 镍及镍合金、 钛及钛合金、 锆及锆合金、 铸铁等各种金属材料的电子束焊 接性, 并就不同材料按其特性规定了Ⅰ为焊接 性良好、 Ⅱ为焊接性一般及Ⅲ为焊接性较差 等, 也标出了 N 为焊接性未知的金属材料。 (3) 附录 C 附录 C 中以表格的方式列出焊接缺欠产生 的原因及防止措施, 规定根据使用标准或按合同 规定选择防止、 消除不当焊接缺欠的方法和设备。 (4) 附录 D 附录 D 列出了环缝接头设计示例。
电子束焊接机的操作流程与注意事项介绍
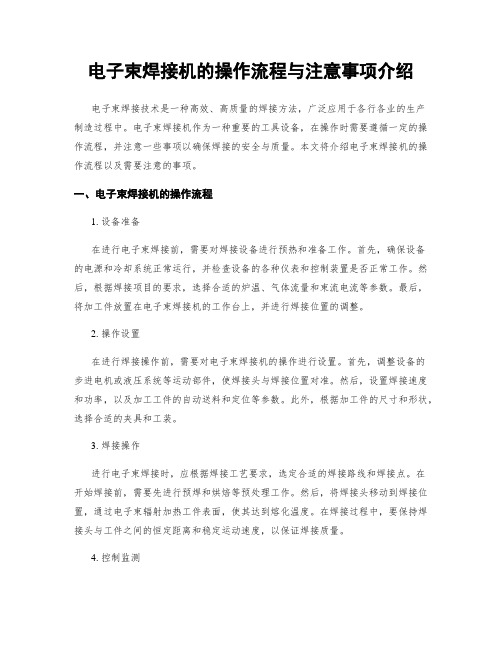
电子束焊接机的操作流程与注意事项介绍电子束焊接技术是一种高效、高质量的焊接方法,广泛应用于各行各业的生产制造过程中。
电子束焊接机作为一种重要的工具设备,在操作时需要遵循一定的操作流程,并注意一些事项以确保焊接的安全与质量。
本文将介绍电子束焊接机的操作流程以及需要注意的事项。
一、电子束焊接机的操作流程1. 设备准备在进行电子束焊接前,需要对焊接设备进行预热和准备工作。
首先,确保设备的电源和冷却系统正常运行,并检查设备的各种仪表和控制装置是否正常工作。
然后,根据焊接项目的要求,选择合适的炉温、气体流量和束流电流等参数。
最后,将加工件放置在电子束焊接机的工作台上,并进行焊接位置的调整。
2. 操作设置在进行焊接操作前,需要对电子束焊接机的操作进行设置。
首先,调整设备的步进电机或液压系统等运动部件,使焊接头与焊接位置对准。
然后,设置焊接速度和功率,以及加工工件的自动送料和定位等参数。
此外,根据加工件的尺寸和形状,选择合适的夹具和工装。
3. 焊接操作进行电子束焊接时,应根据焊接工艺要求,选定合适的焊接路线和焊接点。
在开始焊接前,需要先进行预焊和烘焙等预处理工作。
然后,将焊接头移动到焊接位置,通过电子束辐射加热工件表面,使其达到熔化温度。
在焊接过程中,要保持焊接头与工件之间的恒定距离和稳定运动速度,以保证焊接质量。
4. 控制监测在焊接过程中,需要对焊接参数进行实时监测和控制。
通过检测焊接电流、电压、功率和焊缝的温度等参数,可以判断焊接的稳定性和质量。
如发现异常情况,应及时调整焊接参数,保证焊接质量。
同时,还需要对设备的冷却系统和气体供应系统等进行监控,确保其正常运行。
5. 焊后处理在焊接完成后,需要进行焊后处理工作。
首先,检查焊接缺陷和质量问题,并进行必要的修复和整形。
然后,对焊接部位进行冷却和固定,以保证焊缝的稳定性和强度。
最后,对焊接设备进行清洁和维护,以延长其使用寿命。
二、电子束焊接机的注意事项1. 安全操作电子束焊接是一项高温高能的焊接工艺,操作人员需要特别注意安全。
电子行业电子束焊接

电子行业电子束焊接简介电子束焊接是一种常用于电子行业的高精度焊接技术。
它利用电子束的高能量特性,将焊接材料加热至高温,快速融化并连接在一起。
电子束焊接具有精度高、焊接速度快和热影响区小等优点,广泛应用于半导体、电子元件和电路板的制造过程中。
工艺流程电子束焊接的工艺流程包括以下几个步骤:1.准备工作:对焊接材料进行清洁处理,确保表面不含杂质和氧化物。
同时,需要根据焊接要求确定焊接参数,包括电子束功率、聚焦电压和聚焦电流等。
2.对焊接材料进行定位和夹持:将待焊接的材料放置在焊接台上,并使用夹具进行固定,以确保焊接过程中的稳定性和准确性。
3.开始焊接:启动电子束装置,将电子束聚焦并瞄准焊接位置。
电子束穿过电子枪并聚焦在工件上,加热焊接材料达到融化温度并实现焊接。
4.焊接结束:完成焊接后,关闭电子束装置,等待焊接区域冷却。
同时,对焊接区域进行检查,确保焊接质量符合要求。
特点和优势电子束焊接在电子行业中得到广泛应用,主要受益于以下几个特点和优势:•高精度:电子束焊接能够提供非常精确的焊接结果,焊接位置和焊缝的尺寸控制非常准确,有助于保证电子产品的稳定性和可靠性。
•焊接速度快:电子束焊接的加热速度非常快,因为电子束本身具有高能量,能够迅速将焊接材料加热至融化温度。
相比传统焊接方法,电子束焊接能够大大缩短焊接时间,提高生产效率。
•热影响区小:电子束焊接时,焊接区域受热的时间非常短,因此在焊接过程中产生的热量对材料周围的影响非常小。
这意味着电子束焊接可以避免或减少由于热应力引起的变形和损坏,提高焊接质量。
•适用范围广:电子束焊接可以应用于各种材料的焊接,包括金属、陶瓷和非金属材料。
它在不同类型的电子元件、半导体和电路板的制造过程中都有重要的应用价值。
•自动化程度高:电子束焊接可以与自动化设备相结合,实现工艺的自动化和智能化。
通过编程和机器控制,可以实现焊接参数的精确控制和焊接过程的自动化控制。
应用案例LED封装在LED封装过程中,电子束焊接被广泛应用于焊接LED芯片和良好导热性能的基座之间的连接。
焊接工艺的电子束焊接技术要点
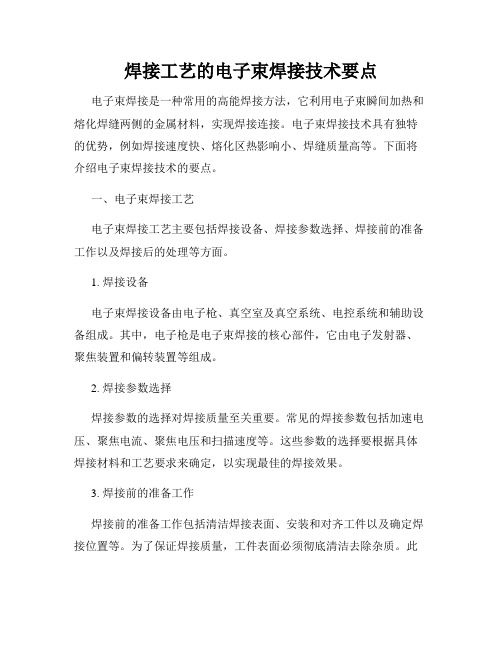
焊接工艺的电子束焊接技术要点电子束焊接是一种常用的高能焊接方法,它利用电子束瞬间加热和熔化焊缝两侧的金属材料,实现焊接连接。
电子束焊接技术具有独特的优势,例如焊接速度快、熔化区热影响小、焊缝质量高等。
下面将介绍电子束焊接技术的要点。
一、电子束焊接工艺电子束焊接工艺主要包括焊接设备、焊接参数选择、焊接前的准备工作以及焊接后的处理等方面。
1. 焊接设备电子束焊接设备由电子枪、真空室及真空系统、电控系统和辅助设备组成。
其中,电子枪是电子束焊接的核心部件,它由电子发射器、聚焦装置和偏转装置等组成。
2. 焊接参数选择焊接参数的选择对焊接质量至关重要。
常见的焊接参数包括加速电压、聚焦电流、聚焦电压和扫描速度等。
这些参数的选择要根据具体焊接材料和工艺要求来确定,以实现最佳的焊接效果。
3. 焊接前的准备工作焊接前的准备工作包括清洁焊接表面、安装和对齐工件以及确定焊接位置等。
为了保证焊接质量,工件表面必须彻底清洁去除杂质。
此外,工件的安装和对齐对焊接结果也有重要影响,需要严格按照工艺要求进行操作。
4. 焊接后的处理焊接完成后,需要对焊接接头进行检查和处理。
可以采用非破坏性检测方法,例如X射线检测和超声波检测等,来评估焊接接头的质量。
同时,还可以对焊接接头进行后续处理,例如涂敷防腐剂、热处理和机械加工等,以提高焊缝的性能和外观。
二、电子束焊接技术的要点1. 选择合适的焊接参数电子束焊接的焊接参数选择十分重要。
加速电压和聚焦电流的组合将决定电子束的能量密度,从而影响着焊缝的形态和质量。
同时,聚焦电压和扫描速度的设置也会影响焊接接头的宽度和深度。
因此,在实际操作中,需要根据具体要求进行合理的参数选择。
2. 确保较好的真空环境在电子束焊接过程中,要保持较好的真空环境,以确保电子束的稳定和焊接质量的提高。
真空度的要求根据具体工艺和焊接材料而变化,但通常要求真空度在10^-4至10^-5 Pa之间。
3. 控制焊接速度和扫描模式焊接速度的选择需要综合考虑焊接材料的熔化温度、热导率以及焊缝的质量要求等因素。
电子束焊接机的操作技巧与维护注意事项
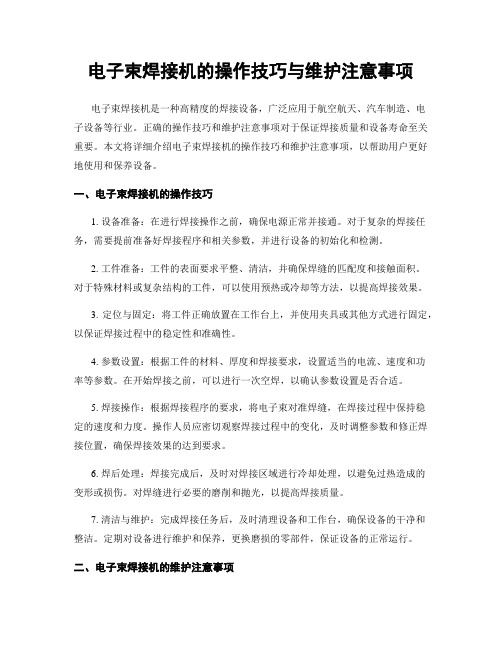
电子束焊接机的操作技巧与维护注意事项电子束焊接机是一种高精度的焊接设备,广泛应用于航空航天、汽车制造、电子设备等行业。
正确的操作技巧和维护注意事项对于保证焊接质量和设备寿命至关重要。
本文将详细介绍电子束焊接机的操作技巧和维护注意事项,以帮助用户更好地使用和保养设备。
一、电子束焊接机的操作技巧1. 设备准备:在进行焊接操作之前,确保电源正常并接通。
对于复杂的焊接任务,需要提前准备好焊接程序和相关参数,并进行设备的初始化和检测。
2. 工件准备:工件的表面要求平整、清洁,并确保焊缝的匹配度和接触面积。
对于特殊材料或复杂结构的工件,可以使用预热或冷却等方法,以提高焊接效果。
3. 定位与固定:将工件正确放置在工作台上,并使用夹具或其他方式进行固定,以保证焊接过程中的稳定性和准确性。
4. 参数设置:根据工件的材料、厚度和焊接要求,设置适当的电流、速度和功率等参数。
在开始焊接之前,可以进行一次空焊,以确认参数设置是否合适。
5. 焊接操作:根据焊接程序的要求,将电子束对准焊缝,在焊接过程中保持稳定的速度和力度。
操作人员应密切观察焊接过程中的变化,及时调整参数和修正焊接位置,确保焊接效果的达到要求。
6. 焊后处理:焊接完成后,及时对焊接区域进行冷却处理,以避免过热造成的变形或损伤。
对焊缝进行必要的磨削和抛光,以提高焊接质量。
7. 清洁与维护:完成焊接任务后,及时清理设备和工作台,确保设备的干净和整洁。
定期对设备进行维护和保养,更换磨损的零部件,保证设备的正常运行。
二、电子束焊接机的维护注意事项1. 定期检查:定期对焊接机进行全面的检查,包括电源、电路、接线等。
特别注意焊接枪和电子束发射器的磨损情况,及时更换磨损的部件,以保证焊接质量和设备寿命。
2. 清洁保养:保持设备的干净和整洁,避免灰尘和异物进入机器内部。
使用专门的清洁工具和清洁剂,定期清洁设备的外壳、缝隙和散热器等。
3. 温度控制:在使用电子束焊接机时,要注意环境温度的控制。
电子束焊接注意事项
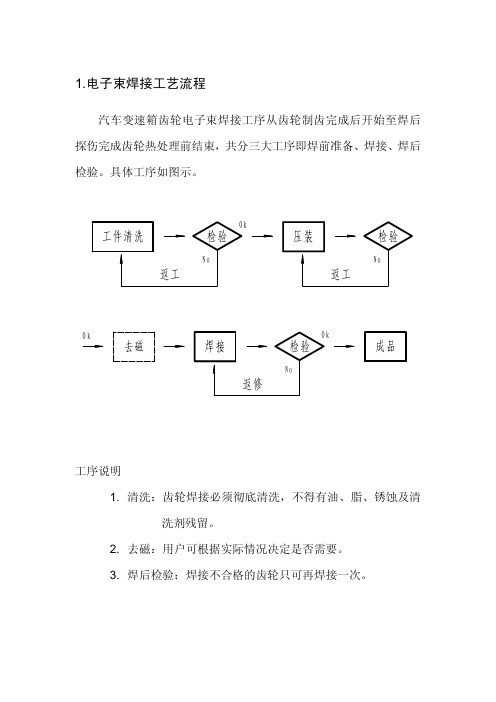
1.电子束焊接工艺流程汽车变速箱齿轮电子束焊接工序从齿轮制齿完成后开始至焊后探伤完成齿轮热处理前结束,共分三大工序即焊前准备、焊接、焊后检验。
具体工序如图示。
工序说明1. 清洗:齿轮焊接必须彻底清洗,不得有油、脂、锈蚀及清洗剂残留。
2. 去磁:用户可根据实际情况决定是否需要。
3. 焊后检验:焊接不合格的齿轮只可再焊接一次。
2.焊接结构齿轮的设计要求3.电子束焊对工件的特殊要求一.对焊件焊接接头的技术要求(图样见上页):1.电子5.电子确规定,二. 对焊件的去2.清洗4. 清洗束焊缝至凸起边缘距离(L 、l )为:h :焊缝的表面宽度,一般为1.5~2.5mm 突起高度(b 、B )其中a 与b 及A 与B 之间关系应满足:a:b ≤1:10、A:B ≤1:10;A h L +=2a h l +=22.压配面底部要求清根或准确地设计过渡圆弧与倒角的配合,以保证压配到位和避免焊缝内部出现气孔;3. 保持压配深度等高,压配端面平整,上端面高度差允许范围0.3mm 。
压配结合上端面允许有倒角,允许最大值为0.5×450;4.要求零件的配合间隙最大为0.03mm ,最大过盈除特殊情况外一般不超过0.03mm ,通常取H7/k6或H7/n6过渡配合; 束焊透深度,视零件所需承受扭矩与疲劳强度而定,图纸应有明一般是压配深度大于焊透深度。
清洗、磁技术要求:1. 焊件在压装前应进行彻底清洗;后焊接面应干燥、无油脂、无锈蚀、无清洗剂残留;3. 单个焊件清洗方法是以100#汽油清洗,再用丙酮擦拭,干燥后压配;后,焊件要干燥、压配、塑料袋包装密封好;5.焊件在焊接前要进行去磁处理,剩磁小于3高斯,否则由于磁场的作用,会使电子束偏移开焊缝,乃至出现废品。
ISO15609-3:2004_金属材料焊接工艺规程及评定-第三部分:电子束焊

国际标准 ISO 15609-32004金属材料焊接工艺规程及评定——焊接工艺规程——第3部分:电子束焊标准号ISO15609-3:2004(E)© ISO目录1 范围 (3)2 规范性引用文件 (3)3 术语和定义 (3)4 焊接工艺规程(WPS)的技术内容 (5)金属材料焊接工艺规程及评定——焊接工艺规程——第3部分:气焊1 范围本标准规定了电子束焊焊接工艺规程的内容要求。
本标准是一套系列标准的组成部分,ISO15607:2003的附录A提供了该系列标准的详细说明。
本标准所列出的参数对焊接接头的质量有影响。
2 规范性引用文件下列标准所包含的条文,通过在本国国际标准中引用而构成本国际标准的条文。
标准出版时,所示标准均为有效。
所有的标准都可能被修订,因此使用本国际标准的各方应探讨使用下列标准最新版本的可能性。
IEC及ISO的成员保持着现行有效国际标准的目录。
ISO4063:1998,金属的焊接、硬钎焊、软钎焊及钎接焊-用于图样上符号表示的工艺术语及参照代号ISO6947,焊缝—焊接工作位置—倾角和转角的定义ISO15607,金属材料焊接工艺规程及评定—一般原则3 术语和定义出于本标准的目的,采用了ISO15607中的术语和定义。
3.1 上升 slope up焊接开始时,电子束功率的控制增加。
3.2 下降 slope down焊接结束时,电子束功率的控制减少。
电子束功率下降的区域就是工件上有束流减少现象发生的区域。
该区域在不同焊接状态下,可能由一或两部分区域组成。
a)全熔透焊接:——焊缝完全熔透的区域;——焊缝布完全熔透的区域或者是熔深减少的区域。
b)部分熔透的焊接:——熔深持续减少的区域。
3.3工作距离 working distance工件表面与设备标准基准面(在实际聚焦镜中心处)之间的距离。
注:这仅是实际参照距离。
3.4 定位焊道 tacking pass为将被焊部件固定在合适位置,而在最终焊接之间焊制的焊道。
电子束焊接

电子束焊接原理电子束焊接(EBW)是利用电子枪所产生的电子在阴阳极间的高电场作用下被拉出,并加速到很高速度,经一级或二级磁透镜聚焦后,形成密集的高速电子流,当其撞击在工件接缝处,其动能转化为热能,使材料迅速熔化而达到焊接的目的。
高速电子在金属中的穿透能力非常弱,如在100kV加速电压下仅能穿透1/40mm,但电子束焊接所以能一次焊透甚至达数百毫米,这是因焊接过程中一部分材料迅速蒸发,其气流强大的反作用力迫使底面液体向四周排开,让出新的底面,电子束继续作用,过程连续不断进行,最后形成一又深又窄的焊缝。
电子束焊接特点电子束焊接是一种先进的焊接方法,其特点和要求主要表现在如下几方面:(1)由于电子束的能量密度很高,焊接速度快,焊件的热影响区和焊接变形极小,可作为零件的终加工工序。
(2)电子束焊缝的深宽比大,可达10∶1~40∶1,而一般电弧焊的深宽比约为1∶1. 5,因此,可以实现大厚度、不开坡口的焊接场合。
(3)可控性好。
电子束焊接参数(电压、电流、焊接速度等)能够被精确控制,焊接时参数的重复性及稳定性好,能确保焊件的焊接质量。
(4)可将难于整体加工的零件分解为容易加工的几部分,再用电子束焊的方法将其焊成整体,使复杂工序变得简单。
(5)可用于不加填充焊丝的对接、角接、T形接等多种焊接场合。
(6)因电子束焊焦点小而能量集中,对组焊件配合处的机械加工精度及装配质量有严格要求,对接焊缝的两边缘要求平整、贴紧,一般不留间隙。
(7)为防止出现焊接裂纹等缺陷,对采用电子束焊接的零件材料,一般要求其碳当量小于0. 4%, 当材料的碳当量大于0. 6%时,裂纹就很难避免,且对焊接工艺的要求也特别高。
电子束焊接的应用日本电子束焊接在压力容器中的实际应用电子束焊接具有焊接热输入量小,焊缝非常窄,几乎没有热影响区,因此焊接接头的性能很好,在焊接过程中工件几乎没有收缩与变形;在真空中焊接,避免了氮、氢、氧的有害作用,可防止低合金高强度钢产生延迟裂纹,同时,由于在真空中避免了氮与氧的有害作用,使较活泼的金属也易于焊接等优点。
电子束焊工艺

电子束焊接焊接工艺收藏此信息打印该信息添加:用户投稿来源:未知(1)薄板的焊接板厚在0.03~2.5mm的零件多用于仪表、压力或真空密封接头、膜盒、封接结构、电接点等构件中。
薄板导热性差,电子束焊接时局部加热强烈。
为防止过热,应采用夹具。
图8示出薄板膜盒零件及其装配焊接夹具,夹具材料为纯铜,对极薄厂件可考虑使用脉冲电子束流。
图8膜盒及其焊接夹具1-顶尖2-膜盒3-电子束4-纯铜夹具电子束功率密度高,易于实现厚度相差很大的接头的焊接。
焊接时薄板应与厚度紧贴,适当调节电子束焦点位置,使接头两侧均匀熔化。
(2)厚板的焊接电子束可以一次焊透300mm的钢板,焊道的深宽比可以高达50:1。
当被焊钢板厚度在60mm以上时,应将电子枪水平放置进行横焊,以利焊缝成形。
电子束焦点位置对熔深影响很大,在给定的电子束功率下,将电子束焦点调节在工件表面以下,熔深的0.5—0.75mm处电子束的穿透能力最强。
根据实践经验,焊前将电子束焦点调节在板材表面以下,板厚的1/3处,可以发挥电子束的熔透效力并使焊缝成形良好。
焊接厚板时,保持良好的真空度有利于增大电子束焊缝的熔深。
(3)添加填充金属只有在对接头有特殊要求或者因接头准备和焊接条件的限制不能得到足够的熔化金属时,才添加填充金属,其主要作用是:1)在接头装配间隙过大时可防止焊缝凹陷。
2)在焊接裂纹敏感材料或异种金属接头时可防止裂纹的产生。
3)在焊接沸腾钢时,加入少量含脱氧剂(铝、锰、硅等)的焊丝,或在焊接铜时加入镍,均有助于消除气孔。
添加填充金属的方法是在接头处放置填充金属。
箔状填充金属可夹在接缝的间隙处,丝状填充金属可用送丝机构送入或用定位焊固定。
送丝机构应保证焊丝准确地送入电子束的作用范围内。
送丝嘴应尽可能靠近熔池,其表面应有涂层以防金属飞溅物的沾污。
应选用耐热钢来制造送丝嘴。
应能方便地对送丝机构进行调节,以改变送丝嘴到熔池的距离、送丝方向以及与工件的夹角等。
焊丝应从熔池前方送入。
真空电子束焊接安全管理要求
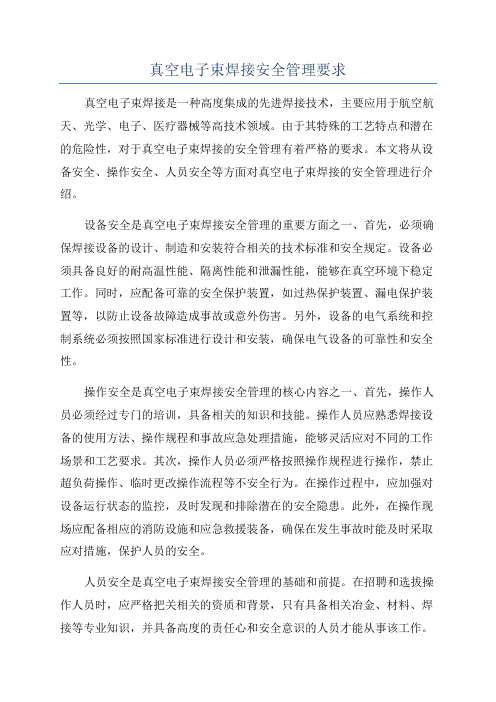
真空电子束焊接安全管理要求真空电子束焊接是一种高度集成的先进焊接技术,主要应用于航空航天、光学、电子、医疗器械等高技术领域。
由于其特殊的工艺特点和潜在的危险性,对于真空电子束焊接的安全管理有着严格的要求。
本文将从设备安全、操作安全、人员安全等方面对真空电子束焊接的安全管理进行介绍。
设备安全是真空电子束焊接安全管理的重要方面之一、首先,必须确保焊接设备的设计、制造和安装符合相关的技术标准和安全规定。
设备必须具备良好的耐高温性能、隔离性能和泄漏性能,能够在真空环境下稳定工作。
同时,应配备可靠的安全保护装置,如过热保护装置、漏电保护装置等,以防止设备故障造成事故或意外伤害。
另外,设备的电气系统和控制系统必须按照国家标准进行设计和安装,确保电气设备的可靠性和安全性。
操作安全是真空电子束焊接安全管理的核心内容之一、首先,操作人员必须经过专门的培训,具备相关的知识和技能。
操作人员应熟悉焊接设备的使用方法、操作规程和事故应急处理措施,能够灵活应对不同的工作场景和工艺要求。
其次,操作人员必须严格按照操作规程进行操作,禁止超负荷操作、临时更改操作流程等不安全行为。
在操作过程中,应加强对设备运行状态的监控,及时发现和排除潜在的安全隐患。
此外,在操作现场应配备相应的消防设施和应急救援装备,确保在发生事故时能及时采取应对措施,保护人员的安全。
人员安全是真空电子束焊接安全管理的基础和前提。
在招聘和选拔操作人员时,应严格把关相关的资质和背景,只有具备相关冶金、材料、焊接等专业知识,并具备高度的责任心和安全意识的人员才能从事该工作。
开展定期的安全培训和教育,提高操作人员的安全防范意识和应急处理能力,加强对焊接安全管理政策和行业标准的宣传和贯彻。
此外,在工作场所要加强作业人员的管理和监督,严禁酒后上岗、疲劳作业、违规操作等不安全行为。
综上所述,真空电子束焊接安全管理要求设备安全、操作安全和人员安全的综合管理。
只有严格执行相关的安全规定和标准,提高整体的安全意识和安全管理水平,才能确保真空电子束焊接作业的安全性和可靠性。
电子束焊接标准专题汇编
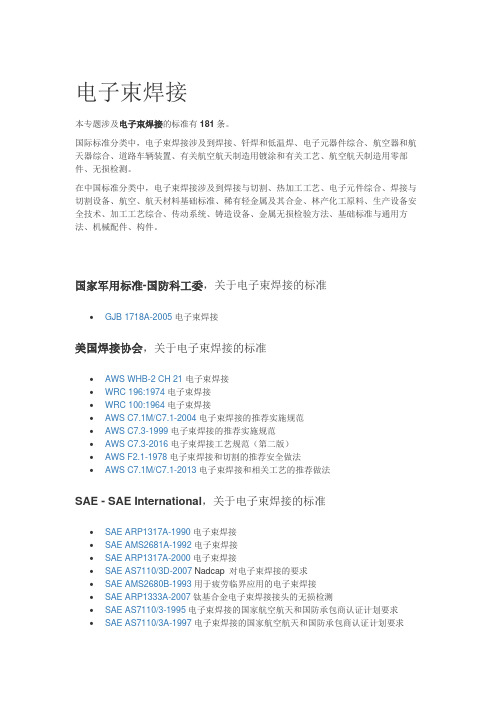
电子束焊接本专题涉及电子束焊接的标准有181条。
国际标准分类中,电子束焊接涉及到焊接、钎焊和低温焊、电子元器件综合、航空器和航天器综合、道路车辆装置、有关航空航天制造用镀涂和有关工艺、航空航天制造用零部件、无损检测。
在中国标准分类中,电子束焊接涉及到焊接与切割、热加工工艺、电子元件综合、焊接与切割设备、航空、航天材料基础标准、稀有轻金属及其合金、林产化工原料、生产设备安全技术、加工工艺综合、传动系统、铸造设备、金属无损检验方法、基础标准与通用方法、机械配件、构件。
国家军用标准-国防科工委,关于电子束焊接的标准•GJB 1718A-2005电子束焊接美国焊接协会,关于电子束焊接的标准•AWS WHB-2 CH 21电子束焊接•WRC 196:1974电子束焊接•WRC 100:1964电子束焊接•AWS C7.1M/C7.1-2004电子束焊接的推荐实施规范•AWS C7.3-1999电子束焊接的推荐实施规范•AWS C7.3-2016电子束焊接工艺规范(第二版)•AWS F2.1-1978电子束焊接和切割的推荐安全做法•AWS C7.1M/C7.1-2013电子束焊接和相关工艺的推荐做法SAE - SAE International,关于电子束焊接的标准•SAE ARP1317A-1990电子束焊接•SAE AMS2681A-1992电子束焊接•SAE ARP1317A-2000电子束焊接•SAE AS7110/3D-2007 Nadcap 对电子束焊接的要求•SAE AMS2680B-1993用于疲劳临界应用的电子束焊接•SAE ARP1333A-2007钛基合金电子束焊接接头的无损检测•SAE AS7110/3-1995电子束焊接的国家航空航天和国防承包商认证计划要求•SAE AS7110/3A-1997电子束焊接的国家航空航天和国防承包商认证计划要求•SAE AS7110/3B-2000电子束焊接的国家航空航天和国防承包商认证计划要求美国机动车工程师协会,关于电子束焊接的标准•SAE ARP1317A-1994电子束焊接•SAE AMS2681-1982电子束焊接•SAE ARP1317-1975电子束焊接•SAE AMS2680C-2001疲劳关键应用的电子束焊接•SAE AMS2680-1981用于疲劳临界应用的电子束焊接•SAE AMS2680A-1981用于疲劳临界应用的电子束焊接•SAE AMS2680C-2019用于疲劳临界应用的电子束焊接•SAE ARP1333-1991钛基合金电子束焊接接头的无损检测•SAE ARP1333-1974在钛基合金R中对电子束焊接接头进行的无损检测R(1991) WRC - Welding Research Council,关于电子束焊接的标准•BULLETIN 100-1964电子束焊接•BULLETIN 196-1974电子束焊接国家军用标准-总装备部,关于电子束焊接的标准•GJB 1718-1993电子束焊接规范德国机械工程师协会,关于电子束焊接的标准•DVS 3202-1990电子束焊接机控制•DVS 3202-2013电子束焊接机控制•DVS 2702-1974电子束焊接机束电流的测量•DVS 3202-2004电子束焊接系统的控制•DVS 3213-2010电子束焊接接合区清洁建议•DVS 3213-1998清洁电子束焊接缝槽的建议•DVS 3201-1986电子束焊接部件的构造原理•DVS 2701-1973电子束焊接机进给率的测量•DVS 2803-1974显微镜下的电子束焊接(调查)•DVS 2706-1979电子束焊接机操作人员内部培训•DVS 3201-2001高真空电子束焊接元件的构造原理•DVS 2704-1976电子束焊接金属建筑构件的构造指南•DVS 3201-2010高真空电子束焊接元件设计的基本原理•DVS 2703-1975航空航天中的电子束焊接;方法和机器的调查•DVS 3220-2007非真空电子束焊接应用的基本原则技术和设计相关说明•DVS 1199-2012 DVS® 课程用于工程师、技术员和专家级别的电子束焊接基础和高级培训行业标准-机械,关于电子束焊接的标准•JB/T 11062-2010电子束焊接工艺指南AWS - American Welding Society,关于电子束焊接的标准•C7.3-1999电子束焊接工艺规范•C7.1M/C7.1-2004电子束焊接的推荐做法•C7.1-1992电子束焊接的推荐做法•C7.1-1999电子束焊接的推荐做法•C7.3-2016电子束焊接工艺规范(第二版)•F2.1-1978推荐的电子束焊接和切割安全实践•C7.1M/C7.1-2013电子束焊接和相关工艺的推荐做法美国国家标准学会,关于电子束焊接的标准•ANSI/AWS C7.3:1999电子束焊接工艺规范•ANSI/AWS C7.3:2016电子束焊接工艺规范•ANSI/AWS C7.1:1992电子束焊接的推荐实施规程行业标准-航天,关于电子束焊接的标准•QJ 972-1986电子束焊接技术条件国家质检总局,关于电子束焊接的标准•GB/T 19867.3-2008电子束焊接工艺规程•GB/T 36232-2018焊缝无损检测电子束焊接接头工业计算机层析成像(CT)检测方法•GB/T 35085-2018金属材料焊缝破坏性试验激光和电子束焊接接头的维氏和努氏硬度试验行业标准-电子,关于电子束焊接的标准•SJ/Z 3202-1989电子工业典型焊接工艺电子束焊接AIA/NAS - Aerospace Industries Association of America Inc.,关于电子束焊接的标准•NAS976-2012电子束焊接机高真空(Rev 5)•NAS976-1975电子束焊接机高真空(修订版4)美国航空工业协会/国家航天工业标准,关于电子束焊接的标准•AIA/NAS NAS976-2012高真空电子束焊接机Rev 5•AIA/NAS NAS 976-1975 (Rev. 4)高度真空电子束焊接机行业标准-航空,关于电子束焊接的标准•HB/Z 198-1991钛及钛合金电子束焊接工艺•HB 5484-1991钛及钛合金电子束焊接质量检验•HB/Z 315-1998高温合金、不锈钢真空电子束焊接工艺•HB/Z 198-2011钛及钛合金电子束焊接工艺及质量检验•HB 7608-1998高温合金、不锈钢真空电子束焊接质量检验•HB 20118-2012航空发动机用电子束焊接接头工业射线层析成像(CT)检测方法美国航空工业协会,关于电子束焊接的标准•AIA NAS 976-1975电子束焊接机高真空(修订版4)英国标准学会,关于电子束焊接的标准•BS EN ISO 14744-4:2001焊接.电子束焊接机的验收检验.焊接速度的测量•BS EN ISO 14744-3:2001焊接.电子束焊接机的验收检验.电子束电流特性的测量•BS EN ISO 14744-5:2001焊接.电子束焊接机的验收检验.偏转精度的测量•BS EN ISO 14744-2:2001焊接.电子束焊接机的验收检验.加速电压特性测量•BS EN ISO 14744-1:2008焊接.电子束焊接机器的验收检验.原则和验收条件•BS EN ISO 14744-6:2001焊接.电子束焊接机的验收检验.现场位置稳定性的测量•BS EN 4677-001:2012航空航天系列.航空航天结构用焊接和钎焊装配组件.电子束焊接金属材料接头.焊接部件质量RO-ASRO,关于电子束焊接的标准•STAS 13066-1992钢材中的电子束焊接接缝.质量等级韩国科技标准局,关于电子束焊接的标准•KS B 0911-2001焊接.电子束焊接机验收检查.第4部分:焊接速度测定•KS B 0910-2001焊接.电子束焊接机验收检查.第3部分:电子束电流特性测定•KS B 0908-2001焊接.电子束焊接机验收检查.第1部分:原理及验收条件•KS B 0912-2001焊接.电子束焊接机验收检查.第5部分:偏离精确度测定•KS B 0909-2001焊接.电子束焊接机验收检查.第2部分:加速电压特性测定•KS B ISO 14744-1:2021焊接.电子束焊接机的验收检验.第1部分:原理和验收条件•KS B ISO 14744-1:2016焊接电子束焊接机的验收检验第1部分:原理和验收条件•KS B 0913-2001焊接.电子束焊接机验收检查.第6部分:焦点位置稳定度测定•KS B ISO 9956-10-2003(2013)金属材料焊接工艺规程和认可第10部分:电子束焊接工艺规程•KS B ISO 9956-10:2003金属材料焊接方法的批准和规范.第10部分:电子束焊接方法规范•KS B ISO 9956-10:2015金属材料焊接方法的批准和规范第10部分:电子束焊接方法规范•KS B ISO 15609-3:2018金属材料焊接程序的规范和资格- 焊接程序规范- 第3部分:电子束焊接丹麦标准化协会,关于电子束焊接的标准•DS/EN 1011-7:2004焊接金属材料焊接建议第7部分:电子束焊接•DS/EN ISO 14744-3:2000焊接电子束焊接机的验收检验第3部分:束电流特性的测量•DS/EN ISO 14744-4:2000焊接电子束焊接机的验收检验第4部分:焊接速度的测量•DS/EN ISO 14744-5:2000焊接电子束焊接机的验收检验第5部分:跳动精度的测量•DS/EN ISO 14744-2:2000焊接电子束焊接机的验收检验第2部分:加速电压特性的测量•DS/EN ISO 14744-6:2000焊接电子束焊接机的验收检验第6部分:光斑位置稳定性的测量•DS/EN ISO 15609-3:2004金属材料焊接工艺规范和评定焊接工艺规范第3部分:电子束焊接•DS/EN 4677-001:2012航空航天系列航空航天结构用焊接和钎焊组件电子束焊接金属材料接头第001部分:焊接组件的质量立陶宛标准局,关于电子束焊接的标准•LST EN 1011-7-2004焊接金属材料焊接建议第7部分:电子束焊接•LST EN ISO 14744-3:2000焊接-电子束焊接机的验收检验-第3部分:束流特性的测量(ISO 14744-3:2000)•LST EN ISO 14744-4:2000焊接-电子束焊接机的验收检验-第4部分:焊接速度的测量(ISO 14744-4:2000)•LST EN ISO 14744-5:2000焊接-电子束焊接机的验收检验-第5部分:跳动精度的测量(ISO 14744-5:2000)•LST EN ISO 14744-1:2008焊接-电子束焊接机的验收检验-第1部分:原则和验收条件(ISO 14744-1:2008)•LST EN ISO 14744-2:2000焊接-电子束焊接机的验收检验-第2部分:加速电压特性的测量(ISO 14744-2:2000)•LST EN ISO 14744-6:2000焊接-电子束焊接机的验收检验-第6部分:光斑位置稳定性的测量(ISO 14744-6:2000)•LST EN ISO 15609-3:2004金属材料焊接工艺规范和评定焊接工艺规范第3部分:电子束焊接(ISO 15609-3:2004)•LST EN 4677-001-2012航空航天系列航空航天结构用焊接和钎焊组件电子束焊接金属材料接头第001部分:焊接组件的质量行业标准-汽车,关于电子束焊接的标准•QC/T 982-2014汽车变速器齿轮激光焊接和电子束焊接技术规范国际标准化组织,关于电子束焊接的标准•ISO/TR 17671-7:2004焊接.金属材料焊接的推荐.第7部分:电子束焊接•ISO 14744-4:2000焊接电子束焊接机的验收检验第4部分:焊接速度的测量•ISO 14744-3:2000焊接电子束焊接机的验收检验第3部分:电子束电流特性的测量•ISO 14744-1:2000焊接电子束焊接机的验收检验第1部分:原理和验收条件•ISO 14744-5:2000焊接电子束焊接机的验收检验第5部分:偏转精度的测量•ISO 14744-1:2008焊接.电子束焊接机器的验收检验.第1部分:原则和验收条件•ISO 14744-2:2000焊接电子束焊接机的验收检验第2部分:加速电压特性的测量•ISO 14744-6:2000焊接电子束焊接机的验收检验第6部分:焊点位置稳定性的测量•ISO 9956-10:1996金属材料焊接工艺规程及认可第10部分:电子束焊接工艺规程法国标准化协会,关于电子束焊接的标准•NF A89-101-7*NF EN 1011-7:2004焊接焊接金属材料的建议第7部分:电子束焊接•NF EN 1011-7:2004焊接焊接金属材料的建议第7部分:电子束焊接•NF A89-030:1993焊接结构金属材料焊接工艺的认可电子束焊接案例•NF A89-700-4*NF EN ISO 14744-4:2000焊接电子束焊接机的验收检验第4部分:焊接速度的测量•NF A89-700-3*NF EN ISO 14744-3:2000焊接.电子束焊接机的验收检验.第3部分:电子束电流特性的测量•NF L06-388:1991航空航天结构件的焊接和钎焊组件.电子束焊接机.鉴定规范•NF A89-700-1*NF EN ISO 14744-1:2008焊接电子束焊接机器的验收检验第1部分:原则和验收条件•NF A89-700-2*NF EN ISO 14744-2:2000焊接电子束焊接机的验收检验第2部分:加速电压特性的测量•NF A89-700-6*NF EN ISO 14744-6:2000焊接电子束焊接机的验收检验第6部分:焊点位置稳定性的测量•NF A89-700-5*NF EN ISO 14744-5:2000焊接.电子束焊接机的验收检验.第5部分:电子束径向跳动精确度的测量•NF A89-010-10:1996金属材料焊接工艺规范和批准.第10部分:电子束焊接工艺规范•NF L06-387:1991航空航天结构件的焊接和钎焊组件.用电子束焊接金属材料连接件.焊接件质量•NF EN ISO 15609-3:2004金属材料焊接工艺的描述和鉴定焊接工艺的描述第3部分:电子束焊接•NF L06-387:2007航空航天结构用焊接和铜焊的组装件.用电子束焊接金属材料接缝.焊接的组装件质量•NF EN 4677-001:2013航空航天系列航空航天结构用焊接和钎焊组件电子束焊接金属材料组件第001 部分:焊接组件质量德国标准化学会,关于电子束焊接的标准•DIN EN 1011-7:2004焊接.焊接金属材料的建议.第7部分:电子束焊接•DIN EN 1011-7:2004-10焊接-金属材料焊接的建议-第7部分:电子束焊接•DIN EN ISO 14744-5:2000焊接.电子束焊接机验收检验.第5部分:偏转精度的测量•DIN EN ISO 14744-4:2000焊接.电子束焊接机的验收检验.第4部分:焊接速度的测量•DIN EN ISO 14744-3:2000焊接.电子束焊接机的验收检验.第3部分:电子束电流特性的测量•DIN EN ISO 14744-1:2008焊接.电子束焊接机的验收检验.第1部分:原则和验收条件•DIN EN ISO 14744-6:2000焊接.电子束焊接机验收检验.第6部分:焊点位置稳定性的测量•DIN EN ISO 14744-2:2000焊接.电子束焊接机的验收检验.第2部分:加速电压特性的测量•DIN EN ISO 15609-3:2004-10金属材料焊接工艺规范和评定-焊接工艺规范-第3部分:电子束焊接•DIN EN ISO 15609-3:2004金属材料焊接程序的规范和合格评定.焊接程序规范.第3部分:电子束焊接子束焊接金属材料接头- 第001 部分:焊接组件的质量•DIN EN 4677-001:2013-02航空航天系列-航空航天结构用焊接和钎焊组件-电子束焊接金属材料接头-第001部分:焊接组件的质量•DIN EN 4677-001:2022航空航天系列航空航天结构用焊接和钎焊组件电子束焊接金属材料接头第001部分:焊接组件的质量AENOR,关于电子束焊接的标准•UNE-EN 1011-7:2005焊接金属材料焊接的建议第7部分:电子束焊接•UNE-EN ISO 14744-4:2001焊接电子束焊接机的验收检查第4部分:焊接速度的测量(ISO 14744-4:2000)•UNE-EN ISO 14744-3:2001焊接电子束焊接机的验收检查第3部分:射束电流特性的测量(ISO 14744-3:2000)•UNE-EN ISO 14744-5:2001焊接电子束焊接机的验收检查第5部分:跳动精度的测量(ISO 14744-5:2000)•UNE-EN ISO 14744-1:2009焊接-电子束焊接机的验收检验-第1部分:原则和验收条件(ISO 14744-1:2008)•UNE-EN ISO 14744-2:2001焊接电子束焊接机的验收检查第2部分:加速电压特性的测量(ISO 14744-2:2000)•UNE-EN ISO 14744-6:2001焊接电子束焊接机的验收检查第6部分:斑点位置稳定性的测量(ISO 14744-6:2000)•UNE-EN ISO 15609-3:2005金属材料焊接工艺规范和评定焊接工艺规范第3部分:电子束焊接(ISO 15609-3:2004)欧洲标准化委员会,关于电子束焊接的标准•EN 1011-7:2004焊接.焊接金属材料的建议.第7部分:电子束焊接•EN ISO 14744-1:2000焊接.电子束焊接机的验收检验.第1部分:原理和验收条件•EN ISO 14744-1:2008焊接.电子束焊接机的验收检验.第1部分:原理和验收条件•EN ISO 14744-4:2000焊接.电子束焊接机的验收检验.第4部分:焊接速度的测量ISO 14744-4-2000•EN 9956-10:1996金属材料焊接法规范和认可.第10部分:电子束焊接的焊接说明ISO 9956-10-1996•EN ISO 14744-3:2000焊接.电子束焊接机的验收检验.第3部分:电子束电流特性的测量ISO 14744-3-2000•EN ISO 14744-5:2000焊接.电子束焊接机的验收检验.第5部分:停机精确度的测量ISO 14744-5-2000•EN ISO 14744-2:2000焊接.电子束焊接机的验收检验.第2部分:加速电压特性的测量ISO 14744-2-2000•EN ISO 14744-6:2000焊接.电子束焊接机的验收检验.第6部分:焊点位置稳定性的测量ISO 14744-6-2000接金属材料接头第001部分:焊接组件的质量KR-KS,关于电子束焊接的标准•KS B ISO 14744-4-2016焊接- 电子束焊接机的验收检验- 第4部分:焊接速度的测量•KS B ISO 14744-5-2016焊接- 电子束焊接机的验收检验- 第4部分:焊接速度的测量•KS B ISO 14744-1-2016焊接- 电子束焊接机的验收检验- 第1部分:原理和验收条件•KS B ISO 14744-1-2021焊接.电子束焊接机的验收检验.第1部分:原理和验收条件•KS B ISO 15609-3-2023金属材料焊接工艺规范和评定焊接工艺规范第3部分:电子束焊接•KS B ISO 15609-3-2018金属材料焊接程序的规范和资格- 焊接程序规范- 第3部分:电子束焊接未注明发布机构,关于电子束焊接的标准•BS EN ISO 9956-10:1997金属材料焊接工艺规范和认可第10部分:电子束焊接焊接工艺规范•BS EN ISO 15609-3:2004(2009)金属材料焊接工艺规范和评定焊接工艺规范第3部分:电子束焊接RU-GOST R,关于电子束焊接的标准•GOST R ISO 5817-2021焊接钢材、镍、钛及其合金的电容焊(不包含电子束焊)接点缺陷质量级别•GOST R ISO 5817-2009焊接.钢材,镍,钛及其合金的电容焊(不包含电子束焊)接点.缺陷质量级别GOSTR,关于电子束焊接的标准•GOST ISO 15609-3-2020金属材料焊接程序的规范和鉴定焊接工艺规范第3部分电子束焊接ZA-SANS,关于电子束焊接的标准•SANS 15609-3:2009金属材料焊接程序的规范和鉴定.焊接程序规范.第3部分:电子束焊接美国机械工程师协会,关于电子束焊接的标准•ASME N-452-2001专业外包焊接工艺.(电子线束焊接) 第III节,第1部分ES-UNE,关于电子束焊接的标准•UNE-EN 4677-001:2012航空航天系列航空航天结构用焊接和钎焊组件电子束焊接金属材料接头第001部分:焊接组件质量CEN - European Committee for Standardization,关于电子束焊接的标准•EN 4677-001:2012航空航天系列航空航天结构用焊接和钎焊组件电子束焊接金属材料接头第001部分:焊接组件的质量。
非真空电子束焊接
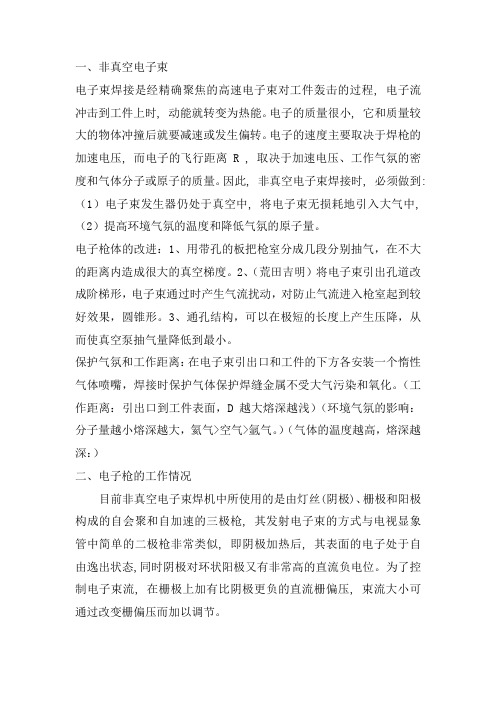
一、非真空电子束电子束焊接是经精确聚焦的高速电子束对工件轰击的过程, 电子流冲击到工件上时, 动能就转变为热能。
电子的质量很小, 它和质量较大的物体冲撞后就要减速或发生偏转。
电子的速度主要取决于焊枪的加速电压, 而电子的飞行距离R , 取决于加速电压、工作气氛的密度和气体分子或原子的质量。
因此, 非真空电子束焊接时, 必须做到:(1)电子束发生器仍处于真空中, 将电子束无损耗地引入大气中,(2)提高环境气氛的温度和降低气氛的原子量。
电子枪体的改进:1、用带孔的板把枪室分成几段分别抽气,在不大的距离内造成很大的真空梯度。
2、(荒田吉明)将电子束引出孔道改成阶梯形,电子束通过时产生气流扰动,对防止气流进入枪室起到较好效果,圆锥形。
3、通孔结构,可以在极短的长度上产生压降,从而使真空泵抽气量降低到最小。
保护气氛和工作距离:在电子束引出口和工件的下方各安装一个惰性气体喷嘴,焊接时保护气体保护焊缝金属不受大气污染和氧化。
(工作距离:引出口到工件表面,D越大熔深越浅)(环境气氛的影响:分子量越小熔深越大,氦气>空气>氩气。
)(气体的温度越高,熔深越深:)二、电子枪的工作情况目前非真空电子束焊机中所使用的是由灯丝(阴极)、栅极和阳极构成的自会聚和自加速的三极枪, 其发射电子束的方式与电视显象管中简单的二极枪非常类似, 即阴极加热后, 其表面的电子处于自由逸出状态,同时阴极对环状阳极又有非常高的直流负电位。
为了控制电子束流, 在栅极上加有比阴极更负的直流栅偏压, 束流大小可通过改变栅偏压而加以调节。
电子束功率损耗:它在电子枪内部通道上的动能损失很小。
当穿过最下面的阻尼孔后, 由于和周围大气中气体原子或分子间的散射碰撞所造成的漂移, 使电子束立即发散而降低功率密度。
不过, 其总功率并无明显损失。
电子束与周围气体碰撞并使其电离后所摄得的照片, 但实际上使周围气体电离的电子乙束比照片中所显示的要细得多。
电子束在离开最下面的阻尼孔后不同距离处的功率密度分布表明,其总功率在一个较大的距离范围内相当稳定, 但距离增加时, 束径随之增大, 功率密度相应降低。
电子束焊接工艺简介

电子束焊接工艺简介电子束焊接是一种高效、精密的焊接技术,由于其在电子工业、航空航天等领域的广泛应用,成为热门研究和关注的焦点。
本文将对电子束焊接的工艺流程、特点以及应用进行简要介绍。
一、电子束焊接的工艺流程电子束焊接是一种高能量密度激光焊接方法,通过电子束束流的聚焦,将热能集中在焊缝上,使焊缝迅速熔化并形成牢固的焊接接头。
其工艺流程如下:1. 设定焊接参数:包括功率、电流、加速电压等,根据工件材料和所需焊接强度确定最佳参数。
2. 准备工件:将待焊接的工件进行清洁处理,确保表面没有灰尘、油污等杂质。
3. 定位工件:将工件安装在焊接平台上并进行精确定位,确保焊缝位置准确。
4. 开启真空系统:电子束焊接需要在真空环境下进行,确保焊接过程没有气体干扰。
5. 聚焦电子束:打开电子束发射装置,聚焦束流到焊缝上,形成高能量密度。
6. 进行焊接:启动电子束焊接机,控制焊接速度和焊接时间,实现焊缝的熔化和焊接。
7. 冷却焊接接头:焊接完成后,对焊接接头进行冷却处理,使焊缝达到最佳的强度和连接性。
二、电子束焊接的特点电子束焊接具有许多独特的特点,使其在高精度焊接领域具有广泛的应用前景。
1. 高能量密度:电子束焊接采用高能量密度的电子束进行焦点聚焦,能够在瞬间将焊接区域加热到极高温度,实现快速熔化和焊接。
2. 焊缝精度高:电子束焊接具有非常小的焊缝宽度和热影响区,焊缝几乎没有变形和气孔等缺陷,保证了焊接接头的精密度和可靠性。
3. 适用于多种材料:电子束焊接适用于各种金属材料的焊接,包括不锈钢、铝合金、镍合金等,广泛应用于汽车、航空航天等行业。
4. 环境友好:电子束焊接不需要使用焊接剂和填充材料,避免了焊接过程中的气体污染和材料浪费问题,对环境更加友好。
5. 自动化程度高:电子束焊接可以实现自动化和机器人化操作,提高生产效率,降低人工成本。
三、电子束焊接的应用电子束焊接广泛应用于电子元件、航空航天、汽车制造等领域。
以下为部分应用案例:1. 电子元件焊接:电子束焊接适用于焊接微小尺寸的电子元件,如电子芯片、连接器等,确保接头的高精密度和稳定性。
真空电子束焊安全技术

真空电子束焊安全技术除遵守焊条电弧焊的有关安全规定外,还应注意以下几点。
(1)焊机应安装在用高密度混凝土建造的X射线屏蔽室内,还需备有在焊机运行时防止误入或被关闭在屏蔽室内的安全措施。
(2)设备接地系统要可靠,不可将接地线直接接入电网零线上,要接设备专用地线,接地电阻不大于2Ω。
(3)电子束焊机应安装电压报警或其他电子联动装置,以便在出现故障时自动断电。
(4)保证高压电源和电子枪有足够的绝缘,耐压试验应为额定电压的1.5偌。
(5)更换阴极组件或维修时,应切断高压电源,并用接地良好的放电棒接触准备更换的零件或需要维修的地方,放完电后才可以操作。
(6)工作场所的面积一般不小于40m2,室高不小于3.5m,对于高压大功率电子束设备,可将高压电源设备和抽气装置与工作人员的操作室分开。
(7)电子束焊机的真空室必须加强对X射线的防护,其措施如下:①加速电压低于60kV的焊机,一般靠焊机外壳的钢板厚度来防护。
①加速电压高于60kV的焊机,外壳应附加足够厚度的铅板加强防护。
①电子束焊机在高电压下运行,观察窗应选用铅玻璃,铅玻璃的厚度可按相应的铅当量选择(见下表)。
国产铅玻璃牌号和相应的铅当量注:铅当量指1个单位厚度的铅玻璃相当于表中示出厚度的铅板。
(8)对设备要定期进行X射线辐射剂量的检测,以确保设备操作现场符合国家有关X射线辐射防护的规定。
(9)设备周围应通风良好,工作场所应安装抽气装置,以便将真空室排出油气、烟尘等及时排出。
(10)穿戴好规定的劳动防护用品,如工作帽、工作服、脚盖、绝缘鞋、长筒皮手套等,选用合适的面罩及滤光镜片。
(11)焊接过程中不准用肉眼观察熔池,必须要时应佩戴铅玻璃防护眼镜。
(12)操作者通过光学系统或工业电视系统在屏蔽室外监控。
操作者站立处的地面上应铺绝缘垫,并检查设备、工具、附具等,使之达到正常、完好和方便操作的状态。
(13)先打开通风设备,再接通焊接设备。
(14)要严格检查真空室的一切缝隙是否密闭,防止X射线逸出。
电子束焊作业指导书
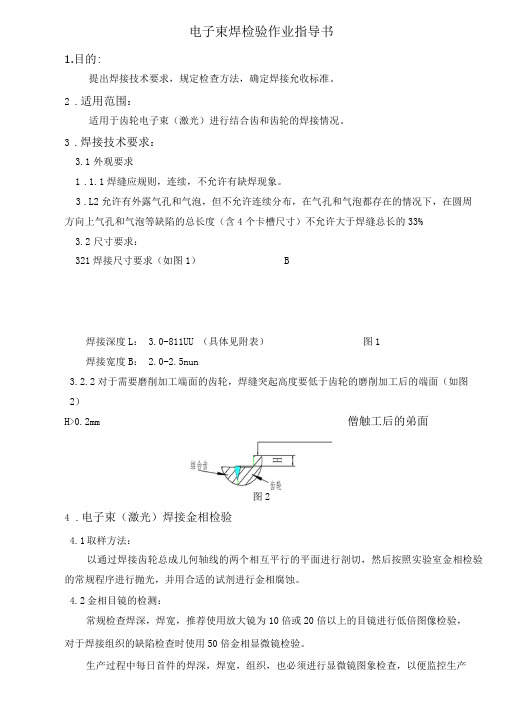
电子束焊检验作业指导书1.目的:提出焊接技术要求,规定检查方法,确定焊接允收标准。
2.适用范围:适用于齿轮电子束(激光)进行结合齿和齿轮的焊接情况。
3.焊接技术要求:3.1外观要求1.1.1焊缝应规则,连续,不允许有缺焊现象。
3.L2允许有外露气孔和气泡,但不允许连续分布,在气孔和气泡都存在的情况下,在圆周方向上气孔和气泡等缺陷的总长度(含4个卡槽尺寸)不允许大于焊缝总长的33%3.2尺寸要求:321焊接尺寸要求(如图1) B焊接深度L: 3.0-811UU (具体见附表)图1焊接宽度B: 2.0-2.5nun3.2.2对于需要磨削加工端面的齿轮,焊缝突起高度要低于齿轮的磨削加工后的端面(如图2)H>0.2mm 僧触工后的弟面图24.电子束(激光)焊接金相检验4.1取样方法:以通过焊接齿轮总成儿何轴线的两个相互平行的平面进行剖切,然后按照实验室金相检验的常规程序进行抛光,并用合适的试剂进行金相腐蚀。
4.2金相目镜的检测:常规检查焊深,焊宽,推荐使用放大镜为10倍或20倍以上的目镜进行低倍图像检验,对于焊接组织的缺陷检查时使用50倍金相显微镜检验。
生产过程中每日首件的焊深,焊宽,组织,也必须进行显微镜图象检查,以便监控生产设备是否稳定合理。
5.电子束(激光)焊接探伤:采用超声波技术进行焊接部位的100%无损探伤。
5.1探伤标准:图35.1.1探伤深度要求:热前L=2.75mm 热后L=2.5mm5.1.2探伤伤长要求:焊接圆周伤长不大于33% (含4个卡槽尺寸)为合格(即:累计缺陷值 W116)6.焊接缺陷接收标准6.1裂纹及空洞(50倍下观察)在L>2mm处有裂纹,可以接收。
通过显微镜图像观察在L<lnun有细裂纹,可以接收。
中部贯通裂纹,不可接收。
顶部裂纹,延伸至融合区,不可接收。
6.2焊偏如下图8情况可以接收,此进L满足第3.2节焊深要求。
图86.3 探伤不合格在探伤深度要求为热前2.75mm,热后2.5mm,伤长大于33% (含4个卡槽尺寸)不可接收 6.4 外观缺陷641不允许有焊缝不连续,焊渣,表面下陷,咬边等缺陷。
- 1、下载文档前请自行甄别文档内容的完整性,平台不提供额外的编辑、内容补充、找答案等附加服务。
- 2、"仅部分预览"的文档,不可在线预览部分如存在完整性等问题,可反馈申请退款(可完整预览的文档不适用该条件!)。
- 3、如文档侵犯您的权益,请联系客服反馈,我们会尽快为您处理(人工客服工作时间:9:00-18:30)。
检查时间段
检查内容
检查标准
注意事项
焊前
温度、湿度检查
温度20±10°C
湿度<70%
如果数值不在规定范围内,严禁继续加工,用空调调整温度与湿度至合格后方可加工。
设备点检
点检卡内容逐项点检
出现异常及时向班长反馈
产品名称与其相配夹具
认清产品,查阅焊缝直径,找出相应夹具。
注意产品标识与实际是否相符
全过程
焊缝检查
焊缝宽度
达到2+0.50mm。
自检100%
外观检查
焊缝是否均匀,是否有裂纹、凹陷、气孔等。
自检100%、用记号笔确认
探伤检查
(着色探伤抽检5%,超声波探伤10%)
着色检查焊缝一圈没有明显裂纹状;超声波探伤合格。
在记录表上填写相关数据
换灯丝
灯丝安装正确到位
换好灯丝后打点检查焊缝位置正确
更换灯丝前必须先净手;更换时把灯丝座取出,用金相砂纸去除表面氧化物和赃物,再将内腔清洁干净
电子束焊作业要求
产品在束焊过程,要认真做好以下工作流程:
总要求:
1.产品清洗后工件表面无油污、铁末、清洗液残留物(碱粉结晶颗粒)、尘埃等,工件表面要求干燥不潮湿,并且所有产品压配后24小时内全部焊接完毕。
2.每逢冬季和梅雨季节时,压配后的待焊产品应立即推到束焊室内恒温1~2小时并保持干燥方可焊接,焊接好的产品必须放在束焊室保温0.5~1小时才能进热,避免急冷急热;
焊缝深度
4mm厚钢板试焊,要求焊穿并每产品至少试焊3次
外观检查
焊缝是否均匀,是否有裂纹、凹陷、气孔等。
探伤检查
着色检查焊缝一圈没有明显裂纹状;超声波探伤合格。
焊接
过程
首件打点,第5件打点,合格后每20件(四工位每60件)打点一次,末件必须打点检查
三点必须位于焊缝中心并且目测三点大致均分圆周
需放置打点工件于规定位置待查,保留至最后焊接,并做好记录
校束焊夹具外圆/内孔跳动
≤0.05mm
夹具擦拭干净并上紧
焊接参数
焊缝直径
参阅相应束焊机
(注意机床编号)
焊接参数表
/
焊接电流
尽量设定为标准值中差
焊接时间
工件转速
用秒表测量时间,确定转速
是否要求
预热、封焊
预热件按照规定要求达到预热温度及保温30-60分钟后方可焊接;封焊电流采用小束流(7-10mA)
焊接
产品摆放
焊接和未焊接的产品分开存放在不同的流转车上,防止混料和磕碰。
产品要求不接触,不落地,不合格品及时隔离,处理
关机
清扫焊室
焊接室干净、门圈清洁
每半个班清扫一次,关机前焊接室抽成真空后,退出全自动程序,每个星期进行一次全面保养
编制:徐敏2012.4.9校对:批准:
首件
产品
调焦
焊缝调焦时观察出现最亮点,实现焊缝表面聚焦;以焊后产品不出现散焦、保证焊缝宽度为准。
采用小束流,焊接时间调为无穷大。
打点
三点必须位于焊缝中心
焊点直径约0.50mm。
需放置打点首件于规定位置待查。
焊缝检查
伤件需放置首件待查;在记录表上填写相关数据,发现异常及缺陷,及时向班长及工艺反馈。