过程控制程序
生产过程控制程序

生产过程控制程序在现代化的工业生产中,为了提高生产效率和产品质量,许多企业都引入了生产过程控制程序。
这些程序涉及到多个环节,能够实现对生产过程的全面监控和管理,从而确保产品的稳定性和一致性。
本文将围绕生产过程控制程序展开讨论,探究其相关的概念、原理和应用,旨在为读者提供一些有益的思考和借鉴。
一、什么是生产过程控制程序?生产过程控制程序是一种综合性的管理体系,它的主要目的是实现对生产过程的集中控制和管理,从而实现产品的质量稳定和生产效率提高。
这些程序主要涉及到生产环节的各个方面,包括材料配比、生产设备、产品检测、质量管理等。
通过对这些环节的全面管理和优化,能够有效地提高产品质量、降低生产成本,从而提升企业的市场竞争力。
二、生产过程控制程序的原理生产过程控制程序的实现,需要依靠一系列技术和方法的支持。
其中最核心的原理就是反馈控制系统。
反馈控制是通过将系统的输出量与期望值进行比较,然后根据比较结果采取措施使得输出量逐渐接近期望值的一种自动控制方法。
在生产过程中,反馈控制系统可以实现对每个环节的全面监测,并通过调节各个参数使得生产过程保持稳定和精准。
这个过程需要依靠各种传感器、控制系统和计算机等技术手段来实现。
三、生产过程控制程序的应用生产过程控制程序的应用是非常广泛的。
基本上任何一个生产型企业都可以考虑引入这种管理体系。
其中一些最常见的应用领域包括:1.冶金、化工、石化等行业。
这些行业生产的产品大多数是化学品、合金、金属材料等。
这些产品的生产过程需要高度精确的控制和管理,否则将会导致产品的品质下降、产生安全事故等问题。
2.制造业。
比如汽车、机械、电子等行业。
在这些行业中,生产过程控制程序可以实现对生产流程的全面管理,确保组装质量和一致性,从而提高整体生产效率和质量。
3.医药、食品等行业。
这些行业生产的产品往往是直接涉及人类身体健康和安全的。
而生产过程管理程序可以确保这些产品的稳定性和一致性,消除了质量问题可能带来的潜在风险。
工程项目过程控制程序

工程项目过程控制程序是指通过对项目的各个阶段进行控制、监督和管理,以确保项目能够按时、按质、按量完成的一种管理方案。
在项目管理中,过程控制是非常关键的一环,它能够帮助项目团队及时发现问题、解决问题,从而保证项目的成功实施。
一、项目启动阶段的过程控制1.明确项目的目标和范围:明确项目的目标和范围是项目启动阶段的首要任务,过程控制的目标是确保项目目标的明确,范围的准确定义。
控制措施包括项目目标和范围的验证、修订和确认,以及项目目标和范围的书面文档,如项目章程和项目范围说明书。
2.制定项目计划:项目计划是项目启动阶段的核心内容,它包括项目的时间计划、成本计划、资源计划等。
过程控制的目标是确保项目计划的合理性和可行性。
控制措施包括对项目计划的评审、修订和确认,以及项目计划的书面文档,如项目进度计划和项目资源计划。
3.确定项目组织结构:项目组织结构是项目启动阶段的重要事项,它包括项目组织机构、职责分工、项目团队的组成等。
过程控制的目标是确保项目组织结构的合理性和有效性。
控制措施包括对项目组织结构的评审、修订和确认,以及项目组织结构的书面文档,如项目组织图和职责分工表。
4.制定项目风险管理计划:项目风险管理是项目启动阶段的重要工作,它包括对项目风险的识别、评估、规划和控制等。
过程控制的目标是确保项目风险管理计划的全面和详细。
控制措施包括对项目风险管理计划的评审、修订和确认,以及项目风险管理计划的书面文档,如风险识别表和风险评估报告。
二、项目执行阶段的过程控制1.跟踪项目进展:项目执行阶段的核心工作是跟踪项目的进展情况,及时发现和解决问题。
过程控制的目标是确保项目的按时、按质、按量完成。
控制措施包括对项目进展情况的监控、评估和报告,以及项目进展情况的书面文档,如项目执行报告和项目问题清单。
2.管理项目资源:项目资源管理是项目执行阶段的重要任务,它包括对项目资源的配置、分配和利用等。
过程控制的目标是确保项目资源的合理和有效。
生产过程控制程序

生产过程控制程序1.数据采集:生产过程中需要采集大量的数据,如温度、压力、液位等参数的变化情况。
控制程序可以通过传感器等设备实时采集这些数据,并存储在数据库中。
2.数据分析:控制程序可以对采集到的数据进行分析和处理,以实现对生产过程的监控和管理。
它可以对数据进行统计分析,找出异常数据并进行报警处理,以及对数据进行趋势分析,预测和预警可能出现的问题。
3.过程动态控制:控制程序可以根据数据分析的结果,调整生产过程中的参数和控制设备的工作状态。
它可以自动控制设备的开关、调节阀门的开度、传送带的速度等,以实现对生产过程的精细化控制。
4.故障诊断与维护:控制程序可以自动检测和诊断设备的故障,并进行维护。
它可以通过对设备的实时监测和分析,判断设备是否正常工作,如果出现故障,则及时报警并进行相应的维修和保养操作。
5.过程优化:控制程序还可以通过对生产过程的数据分析和调整,优化生产过程,提高生产效率和产品质量。
它可以利用数据分析的结果,优化设备的运行参数,减少能耗和浪费,提高产品的质量和市场竞争力。
1.实时性:生产过程是动态变化的,控制程序需要实时监测和响应。
它应该能够及时采集数据、进行数据分析和控制调整,并及时报警和处理异常情况。
2.稳定性:生产过程是一个复杂的系统,控制程序需要保持系统的稳定性。
它应该能够对设备的变化和干扰做出正确的响应,避免出现过度调整或频繁切换的情况。
3.可靠性:生产过程是一个关键的环节,控制程序需要具备高度的可靠性。
它应该能够正常工作并处理各种异常情况,避免因程序错误而导致生产中断或产品质量问题。
4.灵活性:生产过程是一个多变的环境,控制程序需要具备一定的灵活性。
它应该能够适应不同的生产需求和要求,能够扩展和修改,以适应未来的变化和发展。
5.可视化:生产过程控制程序应该具备可视化的界面,方便操作员进行监控和管理。
它应该能够直观地显示生产过程的状态和数据,提供报警和报表功能,以及方便操作员的交互操作。
生产过程控制管理程序

生产过程控制管理程序生产过程控制管理程序是一个重要的系统,用于确保生产过程的高效运行和产品质量的一致性。
该程序涵盖了多个方面,包括原料采购、物流管理、生产计划、质量控制和卫生安全等。
下面是一个关于生产过程控制管理程序的详细说明。
1.原料采购生产过程的第一步是原料采购。
为了保证产品质量,企业应选择可靠的供应商,并在合同中明确规定原料的质量要求。
采购人员应对原材料进行检查,并在接收时核对其质量和数量。
随后,原材料应妥善存储,以确保其不会被污染或变质。
2.物流管理物流管理负责确保原料和成品在生产过程中的顺利运输。
这包括安排适当的运输方式,协调物流时间表,以及保证产品的准时交货。
此外,物流管理还需要考虑库存管理和库房布局,以便最大限度地减少物料的损耗和浪费。
3.生产计划生产计划是一个关键的环节,它决定了生产过程的顺序和时间。
好的生产计划可以有效地利用资源,减少生产周期,并提高生产效率。
生产计划应基于需求预测和产能评估,同时要考虑原料供应和订单交货日期等因素。
为了保证生产计划的顺利实施,企业应建立有效的沟通渠道,并及时调整计划,以应对不可预见的情况。
4.质量控制在生产过程中,质量控制是至关重要的。
它确保产品符合质量标准,减少次品的产生,并提高产品质量的一致性。
质量控制应涵盖整个生产过程,从原料检查到成品检验。
它应包括与产品相关的各个方面,如尺寸、外观、性能等。
企业可以采用各种质量控制工具和技术,如统计过程控制(SPC)、六西格玛等,来确保质量标准的达到。
5.卫生安全卫生安全是生产过程控制管理程序中的另一个重要部分。
企业应确保生产环境清洁卫生,以防止污染和交叉污染。
这包括定期清洁设备和工作区域,培训员工正确的个人卫生措施,提供个人防护装备等。
此外,企业还应建立危险品管理和应急响应计划,以应对可能的事故和灾难。
在生产过程控制管理程序中,以上是一些重要的方面。
当然,不同的企业可能还有其他特定的要求和流程。
因此,企业应根据自身的情况和需求,制定适用的生产过程控制管理程序。
过程控制程序

1.目的
对剪切、冲压、焊接和装配等生产过程控制范围和方法作规定,确保过程受控。
2.适用范围
适用于公司汽车零件所有生产过程的控制,以及涉及的相关区域、场所等。
3.引用文件
ISO/TS16949:2002《质量管理体系汽车行业生产件和相关服务业零件组织应用ISO9001:2000的特定要求》
GB/T24001-1996《环境管理体系规范及使用指南》
OHSAS18001-2001《职业健康安全管理体系规范》
4.定义
无
5.职责
5.1技术开发部负责生产过程策划、产品和过程特殊特性的确定,编制工艺文件,负责工艺纪律检查。
5.2生产装备部负责对生产计划的审核及相关计划的编制;负责对过程控制完备的设备、工装、备件管理;负责现场“5S”管理的监控。
5.3综合管理部负责组织作业人员培训,并对培训效果进行评价;负责为生产过程提供适宜的工作环境。
5.4分厂按照计划,安排各班组严格按工艺文件实施生产,按时生产合格产品;负责监督生产过程的现场管理。
5.5质量部负责产品检验和试验。
6.工作流程
7.支持性文件
产品质量先期策划控制程序人力资源管理程序
数据分析控制程序
设备管理程序
夹具控制程序
模具控制程序
过程控制程序流程图
Y。
生产过程控制程序
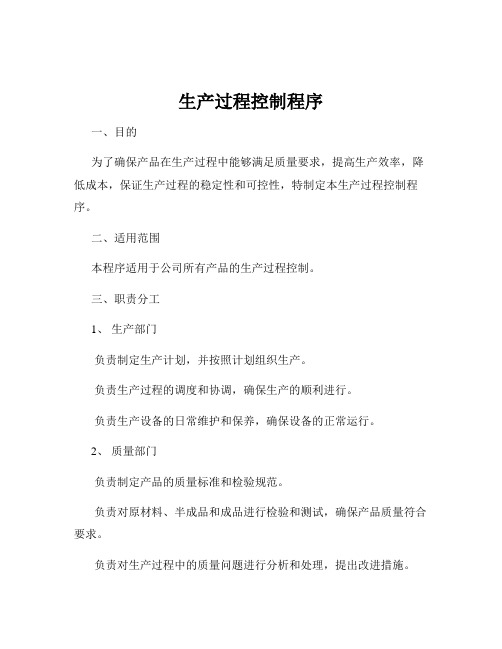
生产过程控制程序一、目的为了确保产品在生产过程中能够满足质量要求,提高生产效率,降低成本,保证生产过程的稳定性和可控性,特制定本生产过程控制程序。
二、适用范围本程序适用于公司所有产品的生产过程控制。
三、职责分工1、生产部门负责制定生产计划,并按照计划组织生产。
负责生产过程的调度和协调,确保生产的顺利进行。
负责生产设备的日常维护和保养,确保设备的正常运行。
2、质量部门负责制定产品的质量标准和检验规范。
负责对原材料、半成品和成品进行检验和测试,确保产品质量符合要求。
负责对生产过程中的质量问题进行分析和处理,提出改进措施。
3、技术部门负责产品的工艺设计和工艺文件的编制。
负责对生产过程中的工艺问题进行技术支持和指导。
4、采购部门负责原材料和零部件的采购,确保采购的物资符合质量要求。
5、仓库部门负责原材料、半成品和成品的收发和保管,确保物资的安全和准确。
四、生产过程控制的流程1、生产计划的制定销售部门根据客户订单和市场预测,向生产部门下达生产任务。
生产部门根据生产任务,结合生产能力和库存情况,制定生产计划。
生产计划应包括生产的产品名称、规格、数量、交货期等内容。
2、原材料的采购采购部门根据生产计划和原材料清单,向供应商下达采购订单。
供应商按照采购订单的要求,按时交付原材料。
原材料到货后,仓库部门进行验收,质量部门进行检验,合格的原材料入库,不合格的原材料退货。
3、生产准备技术部门向生产部门提供产品的工艺文件和作业指导书。
生产部门根据工艺文件和作业指导书,准备生产设备、工装夹具和量具。
生产人员进行培训,熟悉产品的工艺要求和操作方法。
4、生产过程的控制生产部门按照生产计划和工艺文件的要求,组织生产。
生产过程中,操作人员应严格按照作业指导书的要求进行操作,做好生产记录。
质量部门对生产过程中的原材料、半成品和成品进行检验和测试,发现质量问题及时通知生产部门进行处理。
生产部门对生产过程中的设备、工装夹具和量具进行定期维护和保养,确保设备的正常运行。
生产过程控制程序范本
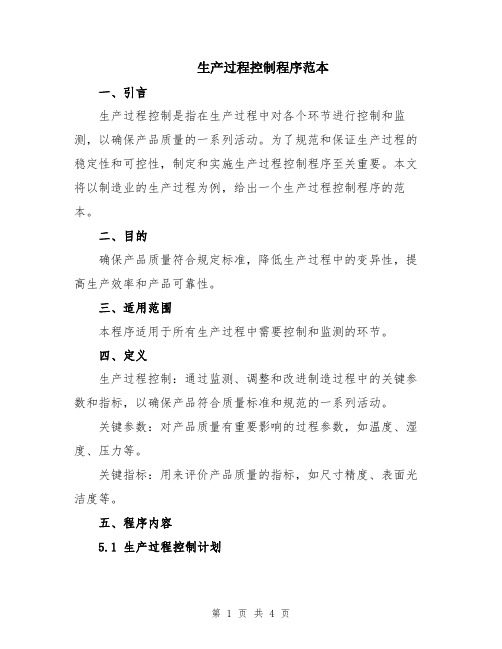
生产过程控制程序范本一、引言生产过程控制是指在生产过程中对各个环节进行控制和监测,以确保产品质量的一系列活动。
为了规范和保证生产过程的稳定性和可控性,制定和实施生产过程控制程序至关重要。
本文将以制造业的生产过程为例,给出一个生产过程控制程序的范本。
二、目的确保产品质量符合规定标准,降低生产过程中的变异性,提高生产效率和产品可靠性。
三、适用范围本程序适用于所有生产过程中需要控制和监测的环节。
四、定义生产过程控制:通过监测、调整和改进制造过程中的关键参数和指标,以确保产品符合质量标准和规范的一系列活动。
关键参数:对产品质量有重要影响的过程参数,如温度、湿度、压力等。
关键指标:用来评价产品质量的指标,如尺寸精度、表面光洁度等。
五、程序内容5.1 生产过程控制计划5.1.1 制定生产过程控制计划,明确需要控制和监测的关键参数和指标。
5.1.2 根据产品要求和工艺流程确定关键参数的合理范围和目标值。
5.1.3 制定关键参数的监测方法和频次。
5.1.4 制定关键指标的测量方法和接受标准。
5.2 生产过程控制执行5.2.1 生产人员按照工艺流程和生产过程控制计划进行操作。
5.2.2 监测和记录关键参数的值,与目标值进行比较,如果超出范围则及时采取措施纠正。
5.2.3 测量和记录关键指标的值,与接受标准进行比较,如果不符合要求则及时采取措施调整。
5.3 数据分析与改进5.3.1 定期对监测数据进行分析,发现问题和异常原因,并制定改进措施。
5.3.2 对改进措施进行验证和评估,确保改进效果。
5.3.3 不断优化生产过程控制计划和方法,加强过程管控能力。
5.4 文件管理5.4.1 对生产过程控制计划、监测记录和改进措施等文件进行管理,确保可追溯性和一致性。
5.4.2 定期对文件进行复查和更新,确保文件有效性。
六、责任与权限6.1 生产经理负责制定和实施生产过程控制计划,并指导生产人员执行。
6.2 生产人员负责按照生产过程控制计划进行操作和记录。
过程控制程序范文
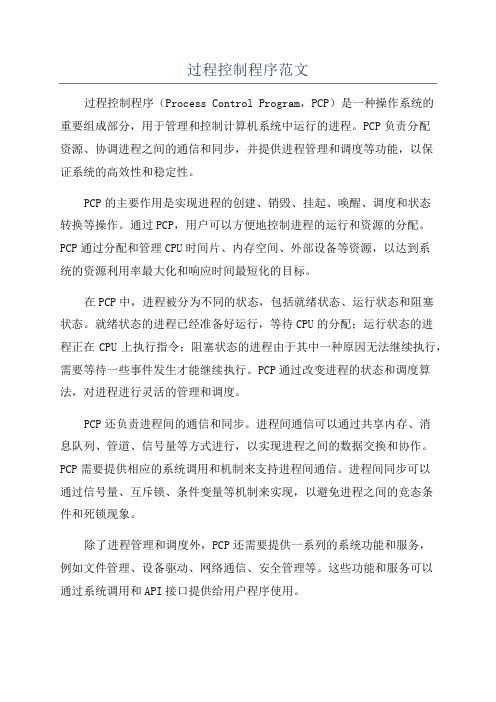
过程控制程序范文过程控制程序(Process Control Program,PCP)是一种操作系统的重要组成部分,用于管理和控制计算机系统中运行的进程。
PCP负责分配资源、协调进程之间的通信和同步,并提供进程管理和调度等功能,以保证系统的高效性和稳定性。
PCP的主要作用是实现进程的创建、销毁、挂起、唤醒、调度和状态转换等操作。
通过PCP,用户可以方便地控制进程的运行和资源的分配。
PCP通过分配和管理CPU时间片、内存空间、外部设备等资源,以达到系统的资源利用率最大化和响应时间最短化的目标。
在PCP中,进程被分为不同的状态,包括就绪状态、运行状态和阻塞状态。
就绪状态的进程已经准备好运行,等待CPU的分配;运行状态的进程正在CPU上执行指令;阻塞状态的进程由于其中一种原因无法继续执行,需要等待一些事件发生才能继续执行。
PCP通过改变进程的状态和调度算法,对进程进行灵活的管理和调度。
PCP还负责进程间的通信和同步。
进程间通信可以通过共享内存、消息队列、管道、信号量等方式进行,以实现进程之间的数据交换和协作。
PCP需要提供相应的系统调用和机制来支持进程间通信。
进程间同步可以通过信号量、互斥锁、条件变量等机制来实现,以避免进程之间的竞态条件和死锁现象。
除了进程管理和调度外,PCP还需要提供一系列的系统功能和服务,例如文件管理、设备驱动、网络通信、安全管理等。
这些功能和服务可以通过系统调用和API接口提供给用户程序使用。
PCP的设计和实现涉及到许多技术和算法,例如进程调度算法、资源分配算法、死锁检测和恢复算法等。
在设计PCP时,需要考虑系统的可靠性、高效性和可扩展性等方面的因素。
此外,PCP还需要适应不同类型的应用场景和需求,如实时系统、分布式系统、并行计算系统等。
总之,过程控制程序是操作系统中重要的一部分,负责管理和控制计算机系统中运行的进程。
它通过分配和管理资源、协调进程间的通信和同步、提供系统功能和服务,以实现系统的高效性、稳定性和可用性。
过程控制程序文件

过程控制程序文件介绍过程控制程序文件是一种用于控制计算机操作系统和应用程序执行的文件。
它包含了一系列的指令和程序代码,用于控制程序的运行和执行过程中的各种行为和条件。
通过编写过程控制程序文件,用户可以自定义和控制计算机的操作,以便满足自己的需求。
过程控制程序文件的结构过程控制程序文件通常由以下几个部分组成:文件头文件头包含了一些描述性的信息,如文件的创建时间、作者、版本号等。
这些信息可以提供给用户和其他程序员参考,以便更好地理解和使用该文件。
导入模块导入模块是过程控制程序文件中的一部分,用于引入其他模块或库,以便在程序中使用它们的功能和特性。
通过导入模块,可以扩展文件的功能和性能,提供更多的工具和方法供程序使用。
主程序主程序是过程控制程序文件的核心部分,它包含了具体的指令和代码,用于实现程序的逻辑和功能。
主程序可以根据需要使用各种数据结构、算法和控制结构,以达到预期的效果和目标。
函数和方法函数和方法是过程控制程序文件的一部分,用于封装并组织可重用的代码。
通过定义函数和方法,可以提高代码的可维护性和可读性,避免代码的重复和冗余。
变量和常量变量和常量是过程控制程序文件中用于存储数据和状态的部分。
变量可以在程序的执行过程中被赋值和修改,而常量的值则是固定不变的。
过程控制程序文件的应用过程控制程序文件可以用于各种不同的应用场景,如:自动化控制系统过程控制程序文件可以用于自动化控制系统,用于监测和控制各种设备和系统。
通过编写过程控制程序文件,可以实现对设备的自动化操作和控制,提高系统的效率和稳定性。
数据处理和分析过程控制程序文件可以用于数据处理和分析,用于处理和分析大量的数据。
通过编写过程控制程序文件,可以实现数据的收集、存储、分析和可视化等功能,以提供对数据的深入理解和洞察。
算法和模拟过程控制程序文件可以用于编写和实现各种算法和模拟,用于解决复杂的数学和科学问题。
通过编写过程控制程序文件,可以实现对算法的实现和优化,以及对模拟的进行和验证。
ISO9001过程质量控制程序
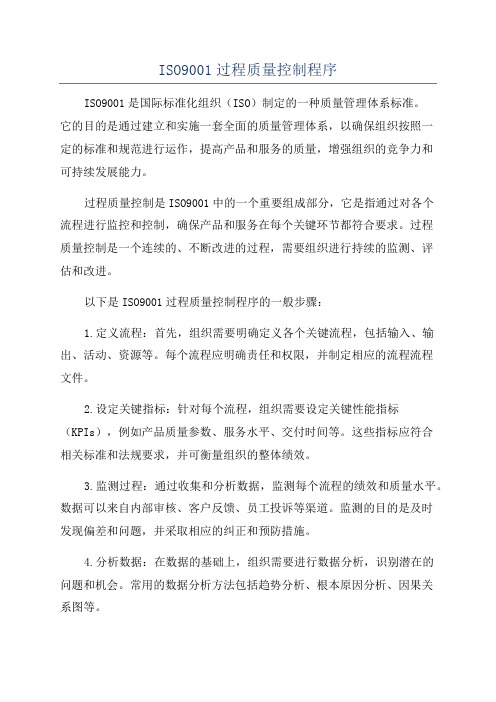
ISO9001过程质量控制程序ISO9001是国际标准化组织(ISO)制定的一种质量管理体系标准。
它的目的是通过建立和实施一套全面的质量管理体系,以确保组织按照一定的标准和规范进行运作,提高产品和服务的质量,增强组织的竞争力和可持续发展能力。
过程质量控制是ISO9001中的一个重要组成部分,它是指通过对各个流程进行监控和控制,确保产品和服务在每个关键环节都符合要求。
过程质量控制是一个连续的、不断改进的过程,需要组织进行持续的监测、评估和改进。
以下是ISO9001过程质量控制程序的一般步骤:1.定义流程:首先,组织需要明确定义各个关键流程,包括输入、输出、活动、资源等。
每个流程应明确责任和权限,并制定相应的流程流程文件。
2.设定关键指标:针对每个流程,组织需要设定关键性能指标(KPIs),例如产品质量参数、服务水平、交付时间等。
这些指标应符合相关标准和法规要求,并可衡量组织的整体绩效。
3.监测过程:通过收集和分析数据,监测每个流程的绩效和质量水平。
数据可以来自内部审核、客户反馈、员工投诉等渠道。
监测的目的是及时发现偏差和问题,并采取相应的纠正和预防措施。
4.分析数据:在数据的基础上,组织需要进行数据分析,识别潜在的问题和机会。
常用的数据分析方法包括趋势分析、根本原因分析、因果关系图等。
5.纠正和预防措施:基于数据分析的结果,组织应制定纠正和预防措施,解决已经发生的问题,并预防未来的问题。
纠正措施是指采取措施来消除问题或纠正不符合和违反的情况。
预防措施是指采取措施来防止问题再次发生。
6.实施措施:组织需要将纠正和预防措施纳入日常运营,并确保其有效实施。
这需要明确责任和时间要求,并通过培训和沟通等手段来确保员工的理解和支持。
7.持续改进:过程质量控制是一个不断改进的过程。
组织需要定期评估流程的效能,并根据评估结果进行改进。
改进可以包括流程的重新设计、流程步骤的优化、资源的调整等。
过程质量控制的核心是持续改进。
施工过程管理控制程序

施工过程管理控制程序
是一种用于监控和管理施工过程的系统或方法。
其目的是确保施工过程按照计划进行,并有效地控制施工过程中的质量、时间、成本和安全等关键要素。
施工过程管理控制程序通常包括以下几个方面的内容:
1. 施工进度控制:确定施工进度计划,并监控施工过程的进展。
可以采用工作分解结构(WBS)和甘特图等方法来展示施工进度,以便及时发现和解决进度延迟等问题。
2. 施工质量控制:制定质量控制措施和标准,并检查施工过程中的质量问题。
可以进行现场巡检、实施非破坏性检测和抽样检验等方法,以确保施工质量符合规定要求。
3. 施工成本控制:预算施工成本,并监控施工过程中的费用支出。
可以制定费用管制措施,比如开展成本审查、制定变更管理程序等,以控制施工成本的增长。
4. 施工安全控制:制定安全管理制度和措施,并执行安全检查和培训。
可以进行安全巡查、实施安全教育和落实安全保护措施等方法,以确保施工过程中的安全。
5. 施工问题解决:及时发现和解决施工过程中的问题和风险。
可以通过开展问题汇报和分析会议、制定问题解决方案等方法,以解决施工过程中的各种困难。
通过施工过程管理控制程序,可以提高施工的效率和品质,减少施工过程中的风险和问题,并确保施工按时完成和符合预期要求。
产品生产过程控制程序
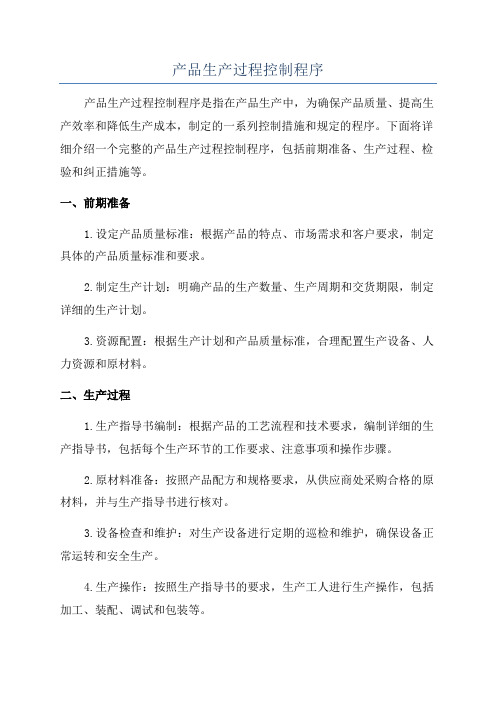
产品生产过程控制程序产品生产过程控制程序是指在产品生产中,为确保产品质量、提高生产效率和降低生产成本,制定的一系列控制措施和规定的程序。
下面将详细介绍一个完整的产品生产过程控制程序,包括前期准备、生产过程、检验和纠正措施等。
一、前期准备1.设定产品质量标准:根据产品的特点、市场需求和客户要求,制定具体的产品质量标准和要求。
2.制定生产计划:明确产品的生产数量、生产周期和交货期限,制定详细的生产计划。
3.资源配置:根据生产计划和产品质量标准,合理配置生产设备、人力资源和原材料。
二、生产过程1.生产指导书编制:根据产品的工艺流程和技术要求,编制详细的生产指导书,包括每个生产环节的工作要求、注意事项和操作步骤。
2.原材料准备:按照产品配方和规格要求,从供应商处采购合格的原材料,并与生产指导书进行核对。
3.设备检查和维护:对生产设备进行定期的巡检和维护,确保设备正常运转和安全生产。
4.生产操作:按照生产指导书的要求,生产工人进行生产操作,包括加工、装配、调试和包装等。
三、检验过程1.过程控制检验:按照生产过程中的关键环节和要求,进行过程控制检验,确保生产过程的稳定性和可控性。
2.成品检验:对生产出来的产品进行成品检验,检验指标包括外观质量、尺寸和性能等,确保产品符合质量标准。
3.抽样检验:通过抽样的方式,对生产过程中的产品进行抽样检验,以控制产品质量稳定。
四、纠正措施1.异常处理:在生产过程中,如出现异常情况,如设备故障、原材料不合格或工艺偏差等,应立即采取纠正措施,并记录异常情况和处理结果。
2.问题分析和改善措施:定期分析和评估生产过程中的问题,制定改善方案和措施,以确保生产过程的稳定性和持续改进。
五、记录和汇总1.产品生产记录:对每个生产批次进行记录,包括生产日期、生产数量、生产人员和质量检验结果等,以便追溯产品质量。
2.统计分析:对产品生产过程中的关键指标进行统计和分析,并制定改进措施,以提高生产效率和降低生产成本。
生产过程质量控制程序
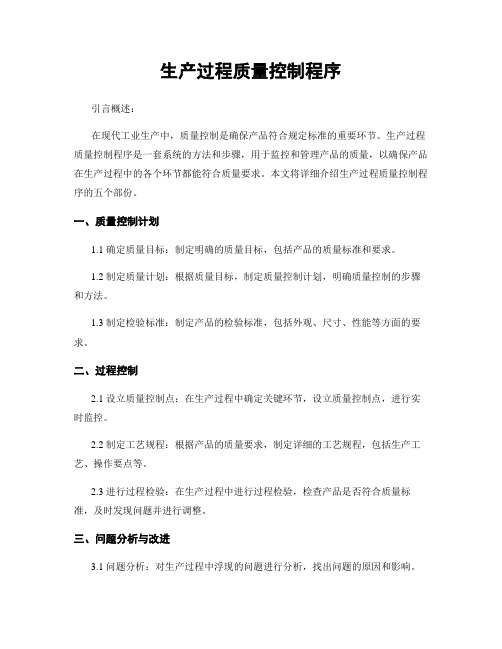
生产过程质量控制程序引言概述:在现代工业生产中,质量控制是确保产品符合规定标准的重要环节。
生产过程质量控制程序是一套系统的方法和步骤,用于监控和管理产品的质量,以确保产品在生产过程中的各个环节都能符合质量要求。
本文将详细介绍生产过程质量控制程序的五个部份。
一、质量控制计划1.1 确定质量目标:制定明确的质量目标,包括产品的质量标准和要求。
1.2 制定质量计划:根据质量目标,制定质量控制计划,明确质量控制的步骤和方法。
1.3 制定检验标准:制定产品的检验标准,包括外观、尺寸、性能等方面的要求。
二、过程控制2.1 设立质量控制点:在生产过程中确定关键环节,设立质量控制点,进行实时监控。
2.2 制定工艺规程:根据产品的质量要求,制定详细的工艺规程,包括生产工艺、操作要点等。
2.3 进行过程检验:在生产过程中进行过程检验,检查产品是否符合质量标准,及时发现问题并进行调整。
三、问题分析与改进3.1 问题分析:对生产过程中浮现的问题进行分析,找出问题的原因和影响。
3.2 制定改进措施:根据问题分析的结果,制定相应的改进措施,解决问题并避免再次发生。
3.3 实施改进措施:将改进措施付诸实施,在实际生产中进行改进,并进行监控和评估。
四、培训与沟通4.1 培训员工:培训生产人员,使其了解质量控制程序的要求和操作方法。
4.2 沟通与协作:加强与各个部门的沟通与协作,共同推动质量控制工作的开展。
4.3 建立反馈机制:建立反馈机制,及时采集员工的意见和建议,改进质量控制程序。
五、持续改进5.1 定期评估:定期对质量控制程序进行评估,检查程序的有效性和可行性。
5.2 改进措施:根据评估结果,提出改进措施,进一步完善质量控制程序。
5.3 持续优化:持续优化质量控制程序,不断提高产品的质量和生产效率。
结论:生产过程质量控制程序是确保产品质量的重要手段,通过制定质量控制计划、进行过程控制、问题分析与改进、培训与沟通以及持续改进等五个部份的工作,可以有效地控制产品的质量,提高生产效率,满足市场需求。
生产过程控制程序
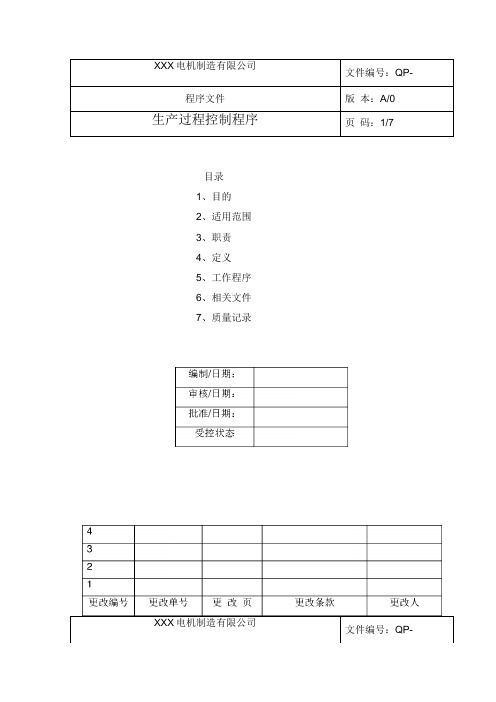
目录1、目的2、适用范围3、职责4、定义5、工作程序6、相关文件7、质量记录1目的对影响质量的生产过程进行有效控制,确保生产过程在受控状态下进行,使工序质量受控。
2适用范围适用于本公司生产过程的控制。
3职责3.1 制造部负责生产过程控制的归口管理。
3.2 质量部负责过程结果的验证工作。
3.3 技术部负责过程所需的有关技术标准的提供。
3.4 采购部负责所需原材料、外协件、外购件及辅料的采购。
3.5 人力资源部负责员工的招聘、培训、考核等。
4定义4.1特殊工序:工序的加工质量不易或不能通过其后的检验和试验得到验证,这种工序属于特殊工序。
5工作程序5.1 年度生产计划控制5.1.1 制造部根据当年公司生产经营情况并结合销售部提供的顾客订货情况和市场预测,在年底制订下年度生产计划并报请生产副总经理批准后分发总经理副总经理和相关部门。
5.2 月度生产计划控制5.2.1 制造部根据公司库存量及销售公司提供的顾客订单于当月25日前作出下月生产计划报生产副总经理批准后下发各相关部门。
5.2.2 制造部在发生下列情况时可对当月生产计划进行调整。
5.2.2.1 顾客临时增加或取消定单。
1.1.1.1 性生产量与实际销售量有差异时。
1.1.1.3 制造过程及其它变动因素导致计划变化时。
1.1.1.4 原物料供应无法配合时。
1.1.3 生产变更1.1.3.1 制造部收到销售公司通知有关数量、交期、质量上变动时,应根据实际情况进行处理。
1.1.3.2 生产计划变动时,生产部应制订“生产调整计划”,将变动内容详载后,通知生产单位及相关部门。
1.1.4 生产管理、统计1.1.4.1 生产车间应每周填报《生产周报表》,星期一上午9时前交制造部。
1.1.4.2 制造部统计、物流调度员依据《生产周报表》进行统计、分析,以便掌握生产进度,及时协调安排。
1.1.4.3 制造部统计员每月5日前应作出上月生产月报并报送制造部部长和生产副总经理。
生产过程控制程序

生产过程控制程序
生产过程控制程序是指一种能够对生产过程进行持续、准确地
监控、调控和管理的程序,为生产过程的流程、质量、效率等各个
方面提供有效的保障。
在一个企业的生产过程中,控制程序是非常
关键的一环,对于生产的质量和效率都有着重要的影响。
下面是一个完整的生产过程控制程序:
1. 设定目标和标准
首先,需要确立生产目标和生产质量标准。
这个环节是非常重
要的,因为只有明确了目标和标准,后续的操作才有依据。
2. 制定计划
根据生产目标和标准,制定详细的生产计划,包括生产时间表、质量控制计划、人员配备计划等。
3. 生产试验
对新的设备、材料、产品进行试验。
试验包括质量控制、设备
性能测试、产品性能测试等。
4. 生产过程监控
监控生产过程中的各个环节,包括生产设备的运行状态、工人
的作业状态、生产产品的数量和质量等。
5. 数据分析
对收集到的数据进行分析,找出问题点和改进方案。
6. 操作改进
根据数据分析的结果,对生产过程进行控制和改进。
这包括生
产设备的维护和更新、工人的培训和技能提升、产品质量的提升等。
7. 操作记录
对生产过程中的各个环节进行记录,包括操作员记录、设备运
行记录、质量检测记录等。
8. 总结评估
定期对生产过程进行总结评估,找出优缺点和改进措施。
以上是一个完整的生产过程控制程序,需要注意的是,生产过
程控制程序需要不断地进行调整和改进,以确保生产目标的顺利达成。
生产过程控制程序

生产过程控制程序一、导言生产过程控制程序是指用于监控和控制生产过程的软件程序。
它主要负责监视和控制机械设备、仪器仪表和工艺参数等,确保生产过程的正常运行和产品质量的稳定。
本文将从以下几个方面介绍生产过程控制程序的设计和实现。
二、需求分析在设计生产过程控制程序之前,我们首先需要进行需求分析,明确程序需要具备的功能和性能要求。
1. 监控功能:实时监控设备状态、工艺参数和产品质量等信息,并能够通过图形界面显示。
2. 控制功能:根据设定的工艺参数,控制机械设备的运行和材料的输送,确保生产过程的稳定性。
3. 报警功能:当设备出现异常状态或超出工艺参数范围时,及时发出警报,并采取相应的措施。
4. 数据分析功能:对生产过程中的数据进行记录和分析,生成报表和统计图表,帮助管理人员进行决策。
5. 操作界面:提供友好的操作界面,方便操作人员使用和操作。
6. 可靠性和稳定性:保证程序的稳定运行和信息的准确性,尽量避免故障和误操作。
7. 可扩展性:程序能够适应不同的工艺和生产环境,并具备一定的扩展性,方便后续的升级和扩展。
三、系统设计根据需求分析的结果,我们可以着手进行生产过程控制程序的系统设计。
1. 硬件设计:根据具体的生产过程和设备需求,选择相应的硬件设备,包括传感器、执行器和控制器等。
同时,还需要设计合适的硬件连接和接口,确保程序可以与硬件设备进行通信和控制。
2. 软件设计:软件设计是生产过程控制程序的核心内容,要保证程序具备所需的功能和性能。
a. 数据采集模块:负责从传感器、仪表和设备中采集实时数据,并进行处理和转换,确保数据的准确性和完整性。
b. 控制模块:根据设定的工艺参数,控制机械设备的运行和材料的输送,以实现生产过程的稳定性和优化。
c. 显示模块:通过图形界面显示实时监控数据和报警信息,方便操作人员进行观察和判断。
d. 报警模块:当设备出现异常状态或超出工艺参数范围时,及时发送报警信息,并采取相应的措施。
生产运行过程控制程序

生产运行过程控制程序生产运行过程控制程序是一种用于对生产过程进行控制和监控的软件程序,其主要功能是通过对各个环节的数据采集、分析和控制,并根据预定的规则和参数进行自动化操作,以提高生产效率和质量。
在以下内容中,将会详细介绍生产运行过程控制程序的原理、架构、功能和优势。
一、原理和架构生产运行过程控制程序基于先进的计算机技术、网络技术和传感器技术,通过多种传感器采集生产过程中的各种数据和信号,并将其传输给控制程序进行处理。
控制程序根据预设的规则和参数,对生产过程进行分析和判断,并进行相应的控制操作。
整个过程基于客户端-服务器架构,通过网络连接实现数据的传输和指令的下达。
二、功能和应用1.数据采集与监控:生产运行过程控制程序可以实时采集各个环节的数据,并通过可视化界面实时展示,以便工作人员了解生产情况。
2.数据分析与预测:控制程序能够对采集到的数据进行分析和处理,利用统计学和机器学习算法,提取关键指标和规律,预测潜在问题,并提供相应的报警或建议。
3.过程控制:控制程序可以根据预设的规则和参数对生产过程进行实时控制,例如调整生产速度、温度、压力等参数,以保证生产过程的稳定和高效。
4.品质检测与质量控制:通过采集和分析关键产品参数,控制程序能够对产品质量进行实时监控和控制。
对于不合格品或异常情况,控制程序会及时报警并采取相应措施。
5.计划与排程:控制程序可以根据生产订单和设备状态,进行生产计划的制定和排程的优化,提高生产效率和资源利用率。
三、优势和效果1.提升生产效率:生产运行过程控制程序能够自动化地实时监控和控制生产过程,快速进行决策和调整,避免了人为因素的干扰和延误,提高了生产效率。
2.提高产品质量:通过对关键过程参数的实时监控和控制,控制程序能够及时发现和纠正质量问题,减少次品率和废品率。
3.资源优化和成本控制:控制程序能够对生产过程进行优化,提高资源利用率,减少能源和原材料的浪费,从而降低生产成本。
工程项目过程控制程序
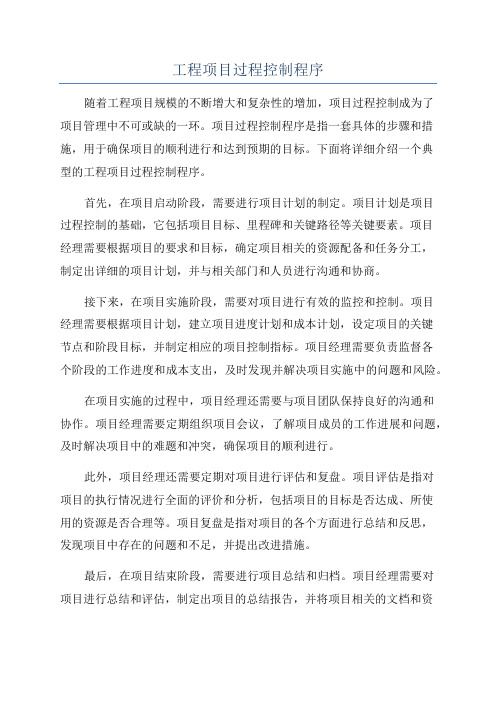
工程项目过程控制程序随着工程项目规模的不断增大和复杂性的增加,项目过程控制成为了项目管理中不可或缺的一环。
项目过程控制程序是指一套具体的步骤和措施,用于确保项目的顺利进行和达到预期的目标。
下面将详细介绍一个典型的工程项目过程控制程序。
首先,在项目启动阶段,需要进行项目计划的制定。
项目计划是项目过程控制的基础,它包括项目目标、里程碑和关键路径等关键要素。
项目经理需要根据项目的要求和目标,确定项目相关的资源配备和任务分工,制定出详细的项目计划,并与相关部门和人员进行沟通和协商。
接下来,在项目实施阶段,需要对项目进行有效的监控和控制。
项目经理需要根据项目计划,建立项目进度计划和成本计划,设定项目的关键节点和阶段目标,并制定相应的项目控制指标。
项目经理需要负责监督各个阶段的工作进度和成本支出,及时发现并解决项目实施中的问题和风险。
在项目实施的过程中,项目经理还需要与项目团队保持良好的沟通和协作。
项目经理需要定期组织项目会议,了解项目成员的工作进展和问题,及时解决项目中的难题和冲突,确保项目的顺利进行。
此外,项目经理还需要定期对项目进行评估和复盘。
项目评估是指对项目的执行情况进行全面的评价和分析,包括项目的目标是否达成、所使用的资源是否合理等。
项目复盘是指对项目的各个方面进行总结和反思,发现项目中存在的问题和不足,并提出改进措施。
最后,在项目结束阶段,需要进行项目总结和归档。
项目经理需要对项目进行总结和评估,制定出项目的总结报告,并将项目相关的文档和资料进行整理和归档。
项目经理还需要与项目团队进行项目庆功会,以表彰团队成员的努力和贡献。
综上所述,一个完整的工程项目过程控制程序应包括项目计划的制定、项目实施的监控和控制、与团队的沟通和协作、项目评估和复盘以及项目总结和归档等环节。
通过这些措施,可以确保项目的顺利进行和达到预期的目标,提高项目的成功率和管理效果。
因此,在工程项目管理中,合理制定并执行过程控制程序是非常重要的。
生产过程控制工作程序

生产过程控制工作程序生产过程控制工作程序一、目的生产过程控制是保证产品质量和生产效率的重要环节,本程序旨在规范生产过程控制工作,确保生产流程的顺利进行。
二、范围本程序适用于公司所有生产工艺的过程控制。
三、责任1. 生产部负责制定和执行生产过程控制方案,并监督实施情况。
2. 生产车间负责实施生产过程控制,按照方案进行操作。
四、流程1. 计划阶段- 生产部根据订单和需求量制定生产计划,并编制生产过程控制方案。
- 生产部与生产车间沟通交流,确保方案可以顺利执行。
2. 准备阶段- 生产部提供所需原材料和设备,并确保其合格。
- 生产车间根据生产过程控制方案进行设备调试和人员培训。
3. 运行阶段- 生产车间按照生产过程控制方案进行生产,确保每个工序按时完成。
- 每个工序结束后,负责人员进行产品检验,确保质量符合要求。
4. 监控阶段- 生产部设立生产过程监控中心,对生产车间的生产过程进行实时监控,确保生产按照计划执行。
- 生产车间设立岗位巡检制度,及时发现和解决生产过程中的问题。
5. 调整阶段- 如果生产过程中出现问题,生产车间及时停止生产并报告生产部。
- 生产部根据情况调整生产过程控制方案,并向生产车间进行指导。
6. 结束阶段- 生产车间完成生产任务后,进行设备清洗和维护,并做好记录。
- 生产车间向生产部提交生产报告,说明生产过程中的问题和改进措施。
五、记录- 生产部和生产车间应做好生产计划、过程控制方案、设备调试记录等相关文件的记录和归档。
- 生产车间应做好生产报告、产品检验记录、设备清洗和维护记录等相关文件的记录和归档。
六、改进- 生产部和生产车间应对生产过程中的问题和改进措施进行总结和分析,并及时反馈给相关部门。
- 生产部和生产车间应定期评估和优化生产过程控制方案,提高生产效率和产品质量。
七、文件- 生产计划表、过程控制方案、设备调试记录、生产报告、产品检验记录、设备清洗和维护记录等相关文件。
八、培训- 生产部应对生产车间的负责人员进行培训,提高其生产过程控制的能力。
工程项目过程控制程序
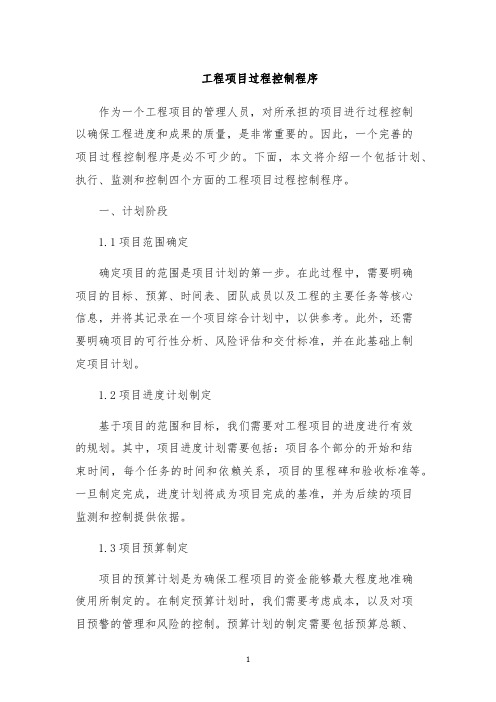
工程项目过程控制程序作为一个工程项目的管理人员,对所承担的项目进行过程控制以确保工程进度和成果的质量,是非常重要的。
因此,一个完善的项目过程控制程序是必不可少的。
下面,本文将介绍一个包括计划、执行、监测和控制四个方面的工程项目过程控制程序。
一、计划阶段1.1项目范围确定确定项目的范围是项目计划的第一步。
在此过程中,需要明确项目的目标、预算、时间表、团队成员以及工程的主要任务等核心信息,并将其记录在一个项目综合计划中,以供参考。
此外,还需要明确项目的可行性分析、风险评估和交付标准,并在此基础上制定项目计划。
1.2项目进度计划制定基于项目的范围和目标,我们需要对工程项目的进度进行有效的规划。
其中,项目进度计划需要包括:项目各个部分的开始和结束时间,每个任务的时间和依赖关系,项目的里程碑和验收标准等。
一旦制定完成,进度计划将成为项目完成的基准,并为后续的项目监测和控制提供依据。
1.3项目预算制定项目的预算计划是为确保工程项目的资金能够最大程度地准确使用所制定的。
在制定预算计划时,我们需要考虑成本,以及对项目预警的管理和风险的控制。
预算计划的制定需要包括预算总额、资金使用计划、项目资金需求计划,并在项目执行结束时对项目支出进行审核和审批。
二、执行阶段2.1任务分配和时间表分配合适的任务和完成时间表格是一个有效的项目实施的基础。
任务分配和时间表的制定是工程项目进一步推进的具体落实,而不是空洞的计划。
在任务分配中,我们需要使团队成员明确自己的职责和任务,明确工作内容和交付目标,并将其嵌入到整个项目的时间线中去。
2.2任务执行和监督在项目执行阶段,我们需要对任务的执行和监测进行有效的管理。
在任务执行中,领导者需要确保任务按计划按时完成,并对团队成员进行有效的指导和帮助。
在任务监督中,我们需要对完成情况进行持续跟踪和记录,及时发现并处理异常情况,并在确认任务执行结果有效后在进一步推进的项目执行中获得更高的控制经验。
- 1、下载文档前请自行甄别文档内容的完整性,平台不提供额外的编辑、内容补充、找答案等附加服务。
- 2、"仅部分预览"的文档,不可在线预览部分如存在完整性等问题,可反馈申请退款(可完整预览的文档不适用该条件!)。
- 3、如文档侵犯您的权益,请联系客服反馈,我们会尽快为您处理(人工客服工作时间:9:00-18:30)。
1.目的
对影响产品质量形成过程中各种因素进行有效控制,确保过程在受控状态下进行产品质量符合规定要求。
2.适用范围
适用于本公司生产制造全部必要活动的策划和实施.
3.定义
3.1 机器能力――由公差与生产设备的加工离散之比得出.通常采用数理统计的方法进行测
算和证明,此时只考虑短期的离散,尽可能排除对过程有影响而非机器的因素.
3.2 过程能力――在考虑影响过程的参数的情况下考察长期离散,人们称之为“过程能力”.
4职责
4.1技术课负责生产过程控制的技术归口管理工作:包括技术标准的制订,操作规程的编制,
工装夹具的设计,工艺技术文件的审核及批准。
4.2质保部负责产品质量的控制和检验作业指导书搞好相关过程的产品的检验和试验控制。
4.3制造部负责组织协调各车间及各部门的生产技术活动,组织实施批次管理,定置管理和
相关生产活动的协调安排,并负责模具和工装夹具的周期检验计划的制订,模具的修理及工装夹具的制作。
5 工作程序
5.1过程策划
由新产品开发项目小组按《产品先期质量策划控制程序》进行工艺,设备,工装,生产,检验等方面的策划,并制订过程流程图和控制计划以及PFMEA风险评估。
根据过程流程图和控制计划编制相应的各类工艺卡,操作规程,检验指导书和其他作业指导书,现场使用的各类作业指导书和用于指导生产的各种样件,缺陷照片等须放置在相应工位处,使操作人员易得到。
涉及到顾客确定的特殊特性项目(包括注明存档责任)须在相应作业指导书中按顾客规定的符号予以标识,并且标明更改和实施时间以及工程更改等级。
当顾客要求较高或较低的过程能力或性能要求时,须在控制计划中“产品过程规范/公差”
栏中作相应注释。
5.2原料控制
5.2.1质保部负责对原料的进厂入库检验控制,按《进货检验和试验程序》执行,坚决杜绝不
合格的原材料投入生产和使用。
5.2.2原材料仓库管理人员严格按照相关的程序文件和管理制度的规定做好批次管理,注意原
材料的贮存和防护,具体按照《产品标识和可追溯性控制程序》和《搬运、贮存、包装、防护和交付》。
5.2.3原料在搬运过程中必须注意防潮,防止阳光暴晒,防止受强热等不利因素的破坏。
5.2.4原料进车间后须按照定置区域和相关规定分批堆放整齐。
5.2.5车间严格按工艺规定的原料名称,供应商,牌号进行生产。
5.3过程监视和作业指导书
5.3.1由技术课制订工艺卡,其内容可包括:
1)对应过程流程图的工序名称和编号;
2)零件名称和零件号及现行工程等级,实施日期;
3)该工序所需工具,量具,生产设备,模具名称或型号,编号;
4)如顾客确认或公司确认的特殊特性(重要特性),须按顾客要求标识特定符号;
5)根据控制计划,要求采用控制图时,在工艺卡中注明并注明工艺参数监控频次;
6)如工艺卡已修改须注明修订/实施日期及批准;
7)注明所使用材料的名称或代号;
8)注明该工序使用的材料处理,工程规范,检验指导书(自检时须注明职责)名称和编号以及反应计划;
9)工艺卡中工艺参数原则上须注明公差;
10)注明材料处理,工装模具更换周期。
5.3.2在每班开工前或材料/工艺变更和较长时间停机后须进行作业准备验证,只有经负责该
工序的检验员认可后方可开始,验证流程如下:
5.3.2.1冲压件每班开始生产前由模具工根据《工艺操作规程》内容正确,安全地安装工装模
具,准备好夹具。
严格按工艺卡内容设定工艺参数。
泡沫件每班开始生产前由操作工在车间主管指导下,设定工艺参数.
5.3.2.2设定好工艺参数后,生产出第一只完整产品并自检合格,同时由质保部检验员及时对
首件进行检验,填写《首件检验结论单》和《作业准备验证检查单》检验员签名,合格的方可交班组成员开始生产,不合格的,由模具工或车间主管按调整工艺参数,直到生产出合格的产品为止,如确系技术原因或模具故障造成生产不能正常进行的,由车间主管填写10-11《质量信息反馈单》交生产部,由生产部协调技术课,进行工艺
更改或其他方式处理。
如有其它原因未及时做好作业作业验证,则由操作工将生产出产品隔离,直到验证合格后放行。
5.3.2.3 《首件检验结论单》随着首件流入下一班次,操作工记录下工艺参数,作为原始记录
务必做到真实可靠,按月交生产部存档备查,具体按《质量记录控制程序》执行。
5.3.4 在生产过程须按控制计划中规定的控制方法进行过程控制,如控制中规定的接收准则,
所使用的测量器具,产品检验的抽样水平/频次,反应计划。
确保过程流程图控制计划得到有效实施。
5.3.4.1操作工须严格按工艺操作规程上规定工序工步内容进行操作,并工艺参数按工艺卡规
定的频次进行监控并作记录,对于自动监控的工艺参数则通过过程质量审核时来检查,如发现有异常则按控制计划中反应计划执行。
5.3.4.2质保部专职检验员和生产员工负责对生产过程中产品质量进行巡回检验并作好相关
记录,填写《巡回检验(工人自检)检验记录单》。
5.3.4.3每批最后一只产品由操作工负责配合专检人员,对末件进行检验,并出具《末件检验
结论单》,挂到工装模具上,随同工装模具一同入库。
5.3.4.4由车间按控制计划要求或对重要特性采用控制图进行控制,对于设备故障,工装更换,
材料变更,测量器具变更,工艺变更等均须在控制图上标明,发现控制图出现异常波动或能力不足时,须执行控制计划中规定的反应计划,必要时进行100%检验。
5.3.4.5在过程控制图显示过程无异常时,由质保部负责每月对涉及特殊特性的项目进行过程
能力测定,确保过程能力充足。
如果过程能力低于额定值须进行产品的100%检验,以便剔除不合格产品,并由质保部负责分析,制订纠正措施明确进度和负责部门,措施须有过程的持续改进内容,顾客要求对经其认可后执行,若由于原设计时公差过紧,在不影响产品功能前提下可放松公差,必要时须经顾客认可。
5.3.5当过程/产品的数据表明过程能力很高时,技术课可修订控制计划和相应作业指导书,
顾客要求时须经重新认可。
任何工艺变更均按《技术文件和资料控制程序》规定注明更改原因,并对相应文件一同进行更改,并在控制计划,过程流程图和相应作业指导书中注明更改修改/实施日期以及工程更改等级,涉及到特殊性项目更改时须重新进行过程能力调查。
5.3.6外观件控制
对于顾客指定的外观件须按以下要示进行控制。
5.3.
6.1在外观件作业区域,生产车间必须配备必要的照明设施,对于有严格的颜色要求工位
处必须使用自然光或白光,防止灯光反射造成颜色失真。
5.3.
6.2在外观件加工和检验处,须放置标样,并得操作人员易于看到。
5.3.
6.3对外观件检验人员必须进行资格确认,有视力和辨色能力要求时须经体验证明有能力
从事该工作。
5.3.
6.4对标样以及检测设备须按《检验、测量和试验控制程序》,《设备控制程序》规定实施,
确保生产过程中所使用设备,工具,模具受控。
5.3.7产品成型后的成品处理控制由技术课在新产品开发阶段试验并确定解决办法。
5.3.8所有操作工及设备维护人员均按《培训控制程序》进行培训,持证上岗,严禁无证上岗操
作,包括模具的装卸和行车的安全使用。
5.3.9生产现场环境控制
由制造部负责对生产现场实施5S管理绘制定置图,保持生产设施处于清洁,有序状态并清理生产现场,应达到以下要求:
1)由生产部组织车间人员定期清洗工位器具,发现破损工位器具及时修补或报废;
2)生产完毕后各员工及时清扫生产现场,保养设备和工模具;
3)生产现场物流须按规定物流流程进行,并在现场标识运输线路;
4)生产现场放置物品或产品须按定置图规定放置并堆放整齐;
5)各生产工位处须放置废品箱。
5.4应急计划
为保障对顾客及时供应,防止因意外情况影响供货及时,由公司办组织各相关部门针对可能出现的停电,停水,原材料/外购件短缺,劳动力短缺,关键设备故障,装运前通知系统故障等非自然灾害造成的偶发性事故制订应急计划。
应急计划须注明计划的具体实施部门/人,具体应急措施及相应控制要求,确保计划的可行性,并经主管部门审核,副总经理批准。
5.5生产过程有效性评价
由技术课负责组织质保部,生产部和车间在关人员分季度对生产工艺进行有效性评价,填写《生产过程有效性检查表》。
5.6对于涉及产品安全性的过程要求按《产品安全性控制程序》规定按批号分类保存。
5.7所有生产中的各项质量记录按《质量记录控制程序》规定按批号分类保存。
5.8对于特殊过程(如:热板焊接,焊管工序等)须制订较详细的作业指导书,并对过程参数
严格监控,所有过程,设备均须作能力测定,人员经培训上岗。