催化湿式氧化设计案例复习过程
湿式催化氧化法(2018.12.4)

实验装置采用固定床连续鼓 泡式反应器(简称固定床反 应器)。固定床反应器设计 压力为15 MPa,温度< 400℃ , 内径15mm、长度600 mm。
[3]曾经,彭青林.催化湿式氧化技术处理高浓度有机废水催化剂研究[J].环境污染与防 治,2009,31(08):37-40+45.
应用实例2
生物法
通过生物吸附、以空气吹脱 BOD/COD> 0.3 ,可生物 COD去除率60%左右,苯胺,硝基 占地面积大,投资高,受 及微生物新细胞物质合 降解的有机物废水、污泥 苯能基本达标,运行费用低,易管 废水成分和浓度限制,停 成消耗而降解 理 留时间长,脱色差,不适 合盐浓度高的废水 加入混凝剂,减少电荷及双电 废水中以悬浮状或胶体形 COD去除率70%左右,处理费用较低 污泥量大,适用范围窄 层的有效距离,降低电位,通过 式存在的污染物,胶体颗 ,苯胺类,酚类可达标 ,难达标 吸附架桥形成大絮团 粒为0.1~ 1 nm 废水中还原性有机物 少量高浓度废水、污泥 可使一些有机物氧化分解,氧化停留 氧化剂用量大,只对某 时间少 些难降解有机物有效 蒸发液吸收后,污染物基本达标, 能耗高,投资大 能回收盐
(2)链的发展或传递: 自由基与分子相互作用,交替进行使自由基数量迅速增加 的过程。
RH + •OH → R • + H 2O R • +O 2 → ROO • ROO • + RH → ROOH + R •
(3)链的中止: 若自由基之间相互膨胀生成稳定的分子,则链的增长过程 将中断。
R • + R• → R-R ROO • + R• → ROOR ROO • + ROO • + H 2O → ROOH + ROH + O 2
氨水中和法氨水液相催化法湿式氧化法脱硫原理及步骤

S
Cat(O)
Cat(R)
3
再生槽
Cat(R) O2 Cat(O)
4
单质硫的浮选和净化凝固
作用
弱碱性吸收剂, 选择性吸收 H2S,快速 慢速、控制步 骤
空气 、快速
三、湿法氧化脱硫基本步骤与基本原理
H2S(l) +OHCat.(O)+ HS— Cat. (R)+ O2
HS— +H2O
S + Cat. (R) H2O + Cat. (O)
总反应式:
H2S(l) + O2(空气)
S↓+ H2O
氨水中和法 氨水液相催化法 湿式氧化法脱硫原理及步骤
• 一、氨水中和法: • 吸收:
• 用稀氨水在吸收塔内与原料气中的硫化物发生化学反 应,生成NH4HS,以脱除原料气中的H2S。净化后的 半水煤气从塔顶排出。
• NH3.H2O+H2S=NH4HS+H2O+Q
• 再生:
• 吸收H2S的溶液用泵送入再生塔,从塔底吹入空气, 使NH4HS分解。分解出来的H2S和空气一道排人大气, 而氨水循环使用。
半水煤气
氨水
空气
放空气
优点:
• 工艺流程简单,原料来自本厂,容易得到。 • 目前国内不少氮肥厂都采用此法。
缺点:
• 脱硫效率低,氨损失较大 • 解吸出的硫化氢直接排人大气,硫元素不能加以回收利用,
直接造成物料损失和环境污染。
• 二、氨水液相催化法:
• 脱硫液:在氨水中添加少量对苯二酚作为活化剂
• 氨水液相催化法过程总结:
• 用弱碱性溶液吸收原料气中的硫化氢,生成硫氢化物
• 借助溶液中的载氧体(cat.)的氧化作用,将硫氢化物氧 化成元素硫
催化湿式氧化 应用案例
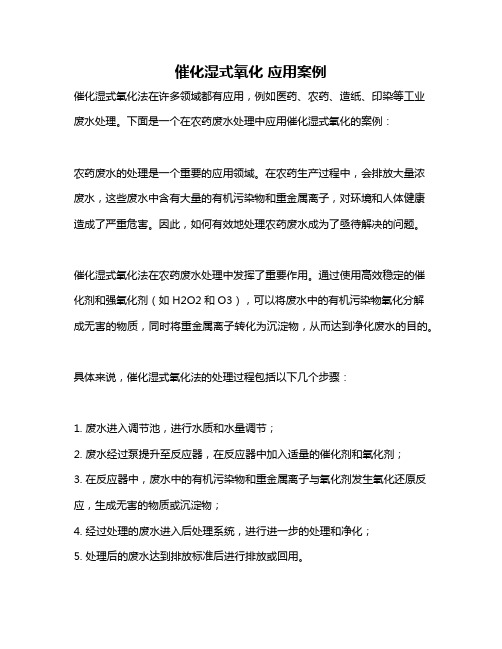
催化湿式氧化应用案例
催化湿式氧化法在许多领域都有应用,例如医药、农药、造纸、印染等工业废水处理。
下面是一个在农药废水处理中应用催化湿式氧化的案例:
农药废水的处理是一个重要的应用领域。
在农药生产过程中,会排放大量浓废水,这些废水中含有大量的有机污染物和重金属离子,对环境和人体健康造成了严重危害。
因此,如何有效地处理农药废水成为了亟待解决的问题。
催化湿式氧化法在农药废水处理中发挥了重要作用。
通过使用高效稳定的催化剂和强氧化剂(如H2O2和O3),可以将废水中的有机污染物氧化分解成无害的物质,同时将重金属离子转化为沉淀物,从而达到净化废水的目的。
具体来说,催化湿式氧化法的处理过程包括以下几个步骤:
1. 废水进入调节池,进行水质和水量调节;
2. 废水经过泵提升至反应器,在反应器中加入适量的催化剂和氧化剂;
3. 在反应器中,废水中的有机污染物和重金属离子与氧化剂发生氧化还原反应,生成无害的物质或沉淀物;
4. 经过处理的废水进入后处理系统,进行进一步的处理和净化;
5. 处理后的废水达到排放标准后进行排放或回用。
催化湿式氧化法在农药废水处理中具有许多优点,例如处理效率高、净化效果好、可回收有价值的物质等。
同时,该方法还可以有效地去除废水中的难降解有机物和重金属离子,实现零排放或近零排放,为环境保护和可持续发展做出了重要贡献。
CWAO湿湿式催化氧化工艺流程

湿式催化氧化法(CWAO)处理原理与工艺流程/ 点击数:134 发布时间:2011年6月13日来源:湿式催化氧化法(CWAO)是20世纪80年代国际上发展起来的一种治理高浓度有机废水的新技术。
是在一定温度、压力下,在催化剂作用下,经空气氧化使废水中的有机物、氨分别氧化分解成CO2、H2O及N2等无害物质,达到净化目的。
其特点是净化效率高,流程简单,占地面积少。
可使焦化废水中CODc,和NH3 -N 的去除率分别达99.5%和99.8%。
经日本大阪瓦斯公司估算,治理费用与生化法接近,但治理后出水水质,远优于生化法,可达到回用水质。
湿式催化氧化法处理原理与工艺流程湿式催化氧化法(CWAO法)在各种有毒有害和难降解的高浓度有机废水处理中非常有效,具有很高实用价值。
加入适宜的催化剂以降低反应所需温度和压力,提高氧化分解能力,缩短时间,防止设备腐蚀和降低成本。
应用催化剂加快反应速度,主要原因,其一降低了反应的活化能;其二改变反应历程。
废水在高温高压下,在保持液相状态时通人空气,在催化剂的作用下,对焦化废水污染物进行彻底的氧化分解,使之转化为无害物质,从而使废水得到深度净化。
如废水中含氮化合物的氨氮、氰化物、硫氰化物、有机氧化物等经分解后,最终生成N2、CO2、SO42-等。
同时可以查看中国污水处理工程网更多技术文档。
NH3+3/4O2=3/2H2O+1/2N2NH4SCN+7/2O2=N2+ H2O+H2SO4+CO2废水中的酚类、烃类以及一般构成COD的组成,经催化湿式氧化后也生成CO2和H2O等。
C6H5OH+7O2=6CO2+3H20其处理工艺流程如图1所示。
图1 CWAO法工艺流程1-贮存罐;2-分离器;3-健化反应器;4-再沸器;5-分离器;6- 循环泵;7- 透平机;8-空压机;9-热交换器;1O-高压泵其工艺过程为:废水通过贮存罐由高压泵打入热交换器,与反应后的高温氧化液体换热,使温度上升到接近于反应温度后进入反应器。
湿式空气氧化法课件

在化工废水处理中的应用案例
总结词
高效、安全、经济
详细描述
湿式空气氧化法在化工废水处理中具有高效、安全、经济的优势,能够适应不同的化工废水处理需求,同时保障了废 水处理的安全性和经济性。
案例
某化工企业采用湿式空气氧化法处理化工废水,处理后出水水质稳定,有机物去除率高达98%以上,氨 氮和重金属含量也达到排放标准,同时减少了化工生产对环境的影响。
特点
湿式空气氧化法具有反应条件温和、 操作压力适中、适用范围广、选择性 高等优点,但也存在反应过程复杂、 反应速率较慢等缺点。
湿式空气氧化法的应用场景
01
02
03
有机废液处理
湿式空气氧化法可用于处 理含有有机污染物的废液 ,如石油化工、制药、造 纸等行业的废水。
无机废液处理
湿式空气氧化法也可用于 处理含有无机污染物的废 液,如含有重金属离子的 废水。
在垃圾渗滤液处理中的应用案例
总结词
高效、适应性强、环保
详细描述
湿式空气氧化法在垃圾渗滤液处理中表现出高效的处理效果,能够适应不同的污染物组成 和处理规模,同时具有环保优势,减少了对环境的二次污染。
案例
某垃圾填埋场采用湿式空气氧化法处理垃圾渗滤液,处理后出水水质稳定,有机物去除率 高达95%以上,氨氮和重金属含量也达到排放标准,同时减少了垃圾填埋场对周边环境的 影响。
该方法能够在短时间内完成对高浓度、高 粘度废液的处理,显著提高了处理效率。
反应条件温和
能量利用率高
湿式空气氧化法所使用的反应条件相对温 和,通常在常压和中等温度下进行,这降 低了操作的难度和成本。
该方法能够将有机物完全氧化为水和二氧 化碳,实现了能量的高效利用。
缺点分析
催化湿式氧化法
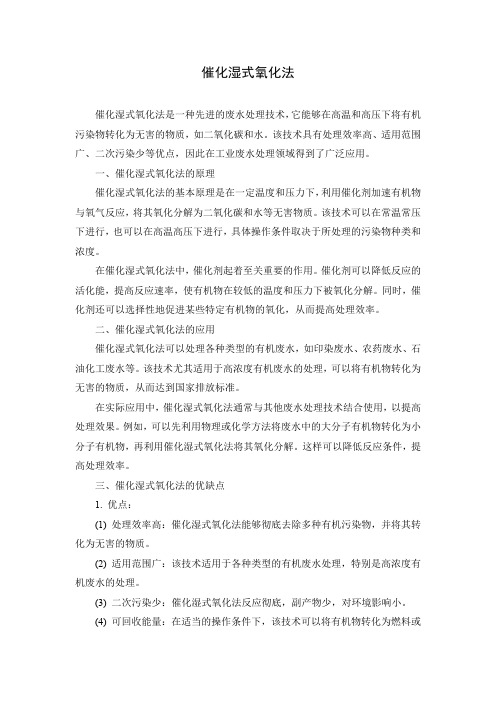
催化湿式氧化法催化湿式氧化法是一种先进的废水处理技术,它能够在高温和高压下将有机污染物转化为无害的物质,如二氧化碳和水。
该技术具有处理效率高、适用范围广、二次污染少等优点,因此在工业废水处理领域得到了广泛应用。
一、催化湿式氧化法的原理催化湿式氧化法的基本原理是在一定温度和压力下,利用催化剂加速有机物与氧气反应,将其氧化分解为二氧化碳和水等无害物质。
该技术可以在常温常压下进行,也可以在高温高压下进行,具体操作条件取决于所处理的污染物种类和浓度。
在催化湿式氧化法中,催化剂起着至关重要的作用。
催化剂可以降低反应的活化能,提高反应速率,使有机物在较低的温度和压力下被氧化分解。
同时,催化剂还可以选择性地促进某些特定有机物的氧化,从而提高处理效率。
二、催化湿式氧化法的应用催化湿式氧化法可以处理各种类型的有机废水,如印染废水、农药废水、石油化工废水等。
该技术尤其适用于高浓度有机废水的处理,可以将有机物转化为无害的物质,从而达到国家排放标准。
在实际应用中,催化湿式氧化法通常与其他废水处理技术结合使用,以提高处理效果。
例如,可以先利用物理或化学方法将废水中的大分子有机物转化为小分子有机物,再利用催化湿式氧化法将其氧化分解。
这样可以降低反应条件,提高处理效率。
三、催化湿式氧化法的优缺点1. 优点:(1) 处理效率高:催化湿式氧化法能够彻底去除多种有机污染物,并将其转化为无害的物质。
(2) 适用范围广:该技术适用于各种类型的有机废水处理,特别是高浓度有机废水的处理。
(3) 二次污染少:催化湿式氧化法反应彻底,副产物少,对环境影响小。
(4) 可回收能量:在适当的操作条件下,该技术可以将有机物转化为燃料或可回收的物质。
2. 缺点:(1) 成本较高:催化湿式氧化法需要高温高压的条件,因此需要高昂的设备和运行成本。
(2) 对某些特定有机物的处理效果有限:对于某些难以氧化的有机物或特定结构的有机物,催化湿式氧化法的处理效果可能会受到限制。
0107.催化湿式氧化法处理含酚废水
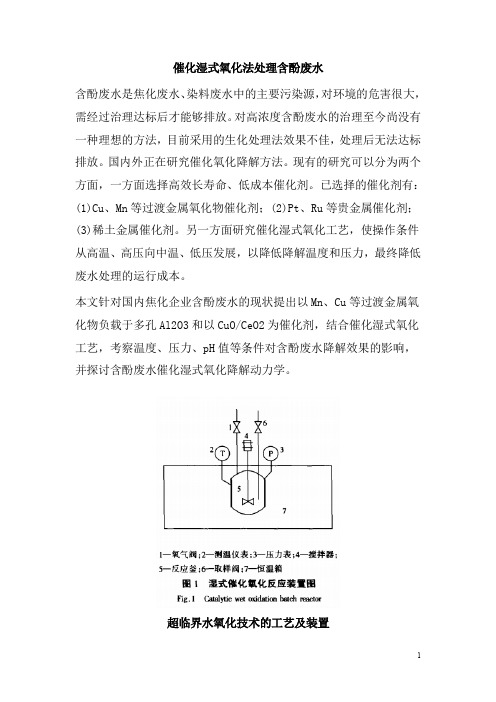
4
图 9 超临界水氧化分批微反应 器
图 9 是 Lee 等人设计的分批微反应器。它由线圈型的管式反应 器、压力传感器、温差热电偶和一个反应器支架组成。反应器用外部 的沙浴加热。
温度/ 压 力浓 度
反应时间 去 除 率
氧化剂
℃ /Mpa /(mg/L)
/min /%
2
压,通过循环用喷射器把上述的循环反应物一并带入反应器。有害有 机物与氧在超临界水相中迅速反应,使有机物完全氧化,氧化释放出 的热量足以将反应器内的所有物料加热至超临界状态,在均相条件 下,使有机物进行反应。离开反应器的物料进入旋风分离器,在此将 反应中生成的无机盐等固体物料从流体相中沉淀析出。离开旋风分离 器的物料一分为二,一部分循环进入反应器,另一部分作为高温高压 流体先通过蒸汽发生器,产生高压蒸汽,再通过高压气液分离器,在 此 N2 及大部分 CO2 以气体物料离开分离器,进入透平机,为空气压缩 机提供动力。液体物料(主要是水和溶在水中的 CO2)经排出阀减压, 进入低压气液分离器,分离出的气体(主要是 CO2)进行排放,液体 则为洁净水,而作补充水进入水槽。反应转化率 R 的定义如下:R=已 转化的有机物/进料中的有机物。
R 的大小取决于反应温度和反应时间。Modell 的研究结果表明, 若反应温度为 550~600 ℃,反应时间为 5s,R 可达 99.99%。延长转 化时间可降低反应温度,但将增加反应器体积,增加设备投资,为获 得 550~600 ℃的高反应温度,污水的热值应有 4000kJ/kg,相当于 含 10%(质量)苯的水溶液。对于有机物浓度更高的污水,则要在进 料中添加补充水。
6
催化湿式氧化法处理含酚废水 含酚废水是焦化废水、染料废水中的主要污染源,对环境的危害很大, 需经过治理达标后才能够排放。对高浓度含酚废水的治理至今尚没有 一种理想的方法,目前采用的生化处理法效果不佳,处理后无法达标 排放。国内外正在研究催化氧化降解方法。现有的研究可以分为两个 方面,一方面选择高效长寿命、低成本催化剂。已选择的催化剂有: (1)Cu、Mn 等过渡金属氧化物催化剂;(2)Pt、Ru 等贵金属催化剂; (3)稀土金属催化剂。另一方面研究催化湿式氧化工艺,使操作条件 从高温、高压向中温、低压发展,以降低降解温度和压力,最终降低 废水处理的运行成本。 本文针对国内焦化企业含酚废水的现状提出以 Mn、Cu 等过渡金属氧 化物负载于多孔 Al2O3 和以 CuO/CeO2 为催化剂,结合催化湿式氧化 工艺,考察温度、压力、pH 值等条件对含酚废水降解效果的影响, 并探讨含酚废水催化湿式氧化降解动力学。
湿式催化氧化脱硫法

体系中S-的氧化为单质硫或多硫化合物。
888(O)X+X S-+XH2O=888+SX↓+2X(OH)-+888(O) NaHS+NaHCO3+S(X-1)=Na2SX+CO2↑+H2O
3. 催化剂再生的化学反应:当888的氧化能力降低时,在再生槽内依靠空气再生。 2 888+O2=2 888(O)
湿法脱硫
化学吸收法脱硫:以稀碱液为脱硫剂,与硫化氢反应形成化合物,从而脱除煤气中
的硫化氢。当吸收富液温度升高,压力降低时,前面形成的化合物分解,释放出硫化 氢,溶液得到了再生。
催化氧化法脱硫
热煤气脱硫
3
湿式催化氧化脱硫法定义
定义:以碱性溶液吸收酸性气体硫化氢,同时选择适当的氧化催化剂,将溶液中被吸收的硫化 氢氧化成单体硫,因而使脱硫溶液得到再生,并获得副产品硫磺。还原态的催化剂可用空气氧 化成氧化态再循环使用。这种方法被称为湿式催化氧化法脱硫。
干法脱硫 大多属于 间歇再生, 氧化铁法 必须在塔 外,活性 炭法需要 过热蒸汽, 再生较困 难
物理吸收法脱硫:高压气化煤气低温甲醇脱硫法就属于这一种它是以有机溶剂-甲醇
为吸收液,它在高压低温状态下对煤气中的硫化氢有良好的吸收能力,达到煤气脱硫的 效果。当吸收液降压升温时,被吸收的硫化氢放出,溶液再生,继续参加脱硫循环。
湿式催化氧化脱硫法
1
目录
一、湿式催化氧化脱硫法定义 二、湿式催化氧化脱硫法工艺流程 二、湿式催化氧化脱硫法原理 三、湿式催化氧化脱硫法指标控制
2
煤气脱硫
干法脱硫 冷煤气脱硫
湿式催化氧化脱硫法

湿法脱硫
化学吸收法脱硫:以稀碱液为脱硫剂,与硫化氢反应形成化合物,从而脱除煤气中
的硫化氢。当吸收富液温度升高,压力降低时,前面形成的化合物分解,释放出硫化 氢,溶液得到了再生。
催化氧化法脱硫
热煤气脱硫
3
湿式催化氧化脱硫法定义
定义:以碱性溶液吸收酸性气体硫化氢,同时选择适当的氧化催化剂,将溶液中被吸收的硫化 氢氧化成单体硫,因而使脱硫溶液得到再生,并获得副产品硫磺。还原态的催化剂可用空气氧 化成氧化态再循环使用。这种方法被称为湿式催化氧化法脱硫。
10
湿式氧化脱硫法指标控制
(3)、溶液循环量:对于填料塔而言,选择液气比应大于保证填料所需的最小湿润流量的液 气比,确保脱硫效率。保持足够的循环量和喷淋密度能提高吸收频率及碱的利用率,而且能将 反应生成的元素硫迅速转移,即解析的硫与随溶液带出的硫要成正比,预防堵塔。因此溶液循 环量的确定,不单是以溶液工作硫容计算出来的,还应兼顾液气比≥20L/Nm3、喷淋密度(4050m3/m2·h)和溶液在再生塔内的停留时间等因素来综合考虑,不能顾此失彼,适当提高循环 量对生产是有利的。
9
湿式氧化脱硫法指标控制
(2)、pH值:pH值是脱硫液的基本组份,随总碱度的增高而上升。pH<8.0时对设备腐蚀严重; 而pH值大于9.3,副反应迅速上升。故pH值最好控制在8.0-9.0之间(正常指标为8.4-8.6)。pH 值高利于吸收而不利于析硫。提高溶液中的碱度和pH值,能增强吸收推动力,利于平衡转移,提 高 脱硫效率。但只要能达标,维持较低碱度对生产长期稳定能起积极作用。其控制高低是以工 艺设备状况、生产负荷和入口煤气中H2S含量及净化度要求而定。
2. 催化氧化的化学反应:由于888特殊的化学结构,具有很强的携氧能力,因而有很强的氧化能力,将
湿式催化氧化法(2018
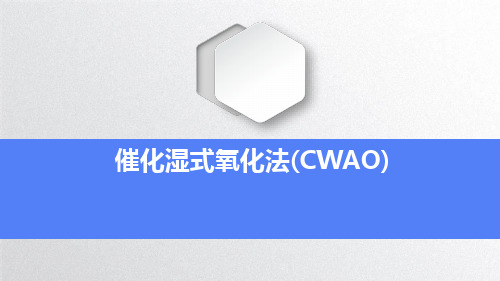
H2O2 + M → 2OH •
(M 为催化剂)
(2)链的发展或传递: 自由基与分子相互作用,交替进行使自由基数量迅速增加
的过程。
RH + •OH → R • +H 2O R • +O2 → ROO • ROO • +RH → ROOH + R •
(3)链的中止: 若自由基之间相互膨胀生成稳定的分子,则链的增长过程
➢ 废水COD达16542 mg/ L,pH 为4.6左右。
➢ 实验装置采用固定床连续鼓 泡式反应器(简称固定床反 应器)。固定床反应器设计 压力为15 MPa,温度< 400℃ , 内径15mm、长度600 mm。
[3]曾经,彭青林.催化湿式氧化技术处理高浓度有机废水催化剂研究[J].环境污染与防 治,2009,31(08):37-40+45.
➢ 催化剂的稳定性和可持续性。连续操作应进一步调查,如何有效地防 止活性组分的损失,提高催化剂的稳定性和可重复性,还有待进一步 研究。
➢ 开发的许多CWAO技术仍处于试验阶段,且大多数是使用模拟废水进 行的,只有少数真正含有工业废水,有必要在大规模水处理中使用而 不只是在实验室中证明它们的应用。
参考文献
[1]丁凯扬,周瑜.催化湿式氧化技术研究进展[J].广东化工,2013,40(12):107-109. [2]Zhang Zhang, Yanshan Gao, Qiang Wang,Fabrication, activity and mechanism studies of transition metal molybdate/molybdenum trioxide hybrids as novel CWAO catalysts,Separation and Purification Technology,Volume 191,2018,354–363. [3]曾经,彭青林.催化湿式氧化技术处理高浓度有机废水催化剂研究[J].环境污染与防 治,2009,31(08):37-40+45. [4]钱仁渊,钱俊峰,云志.催化湿式氧化高浓度SDBS废水的研究[J].水资源保护,2007(06):48-51. [5]魏日出,陈洪林,张小明.湿式催化氧化法处理含高浓度甲醛的草甘膦废水[J].分子催 化,2013,27(04):323-332. [6]邹琳琳,黄冲,潘一,杨双春.催化氧化法处理焦化废水研究[J].当代化工,2013,42(03):319-322. [7]蒋克彬主编,污水处理工艺与应用[M],中国石化出版社,2014.03. [8]Zhaokun Xiong, Heng Zhang, Wenchao Zhang, Bo Lai, Gang Yao,Removal of nitrophenols and their derivatives by chemical redox: A review,Chemical Engineering Journal,Volume 359,2019,Pages 13-31.
科技成果——催化湿式氧化(CWAO)高浓有机废水处理技术

科技成果——催化湿式氧化(CWAO)高浓有机废水处理技术所属行业工业废水治理技术开发单位中国科学院大连化学物理研究所适用范围化工、冶金等行业高浓有机废水处理行业现状辽宁省石油化工、精细化工企业多,污水排放量大,处理技术不过关,出水水质不合格。
化工废水成分复杂,反应原料常为溶剂类物质或环状结构的化合物,增加了废水的处理难度;废水中含有大量有机污染物,COD Cr高、含盐量高,主要是由于原料反应不完全和原料或生产中使用大量溶剂造成的。
化工行业高浓有机废水平均COD Cr排放量为20kg/t。
精细化工废水中有许多有机污染物对微生物是有毒有害的,如卤素化合物、硝基化合物、具有杀菌作用的分散剂或表面活性剂等;生物难降解物质多,B/C比低,可生化性差。
成果简介1、技术原理CWAO反应机理为:在高温(200-280℃)和高压(2-7.5MPa)条件下,空气中的氧气在催化剂表面生成强氧化性的·OH自由基,·OH 将有机污染物及含N、S等的毒物直接氧化为CO2、H2O及N2、SO2-等4无害物排放;在此过程中没有NOx、SO2和HCl等有害气体产生,通常不需要尾气净化系统。
因而在现有的有机废水处理工艺中,CWAO 对大气造成的污染最低。
该技术具有应用范围广、净化效率高、占地面积小、能耗低、二次污染少等优点,具有广阔的应用前景。
2、关键技术及减污技术细节该CWAO废水处理装置主要由储送单元、换热单元、反应单元、尾气吸收单元组成。
(1)储送单元储送单元主要功能为废水与空气的储存及输送、反应后液体和气体的分离及输送。
储送单元将来自工业化装置的高浓度废水收集储存并调整。
废水由工业化装置预处理,经检测达到入口条件后,通过废水来源管线进入废液储罐中储存,储罐出水经过滤后经废水计量泵增压至反应压力。
空气经空压机增压后与废水通过管道混合器混合后送入换热单元。
储送单元同时将反应后的气液混合物进行气液分离后,气体送往尾气吸收单元,液体经地沟去集水井。
氨氮废水的治理---催化湿式

焦化废水组分(以昆钢为例)
氨氮废水处理工艺选择
焦化废水成分复杂多变,对其的处理方法也是多种多样。目前,国
内约有50%焦化厂使用传统的活性污泥法处理废水,虽然出水的酚、氰、 BOD5基本达到排放标准,但对氨氮一直很难达标。A²/O生物脱氮污水处
理技术和催化湿式氧化处理技术是20世纪90年代先后开发出来的焦化废
结论
因为A²/O生物脱氮处理工艺需要废水先经过预处理,预处
理成本较高,而催化湿式氧化处理技术则不需进行蒸氨预处理。
所以CWAO处理技术工艺是在技术上和经济上均具有较强竞争 力的一项技术。
完
案例分析
湿式催化氧化法处焦化废水 焦化废水来源
焦化废水是在原煤高温干馏、煤气净化和化工产品精制过程中产生 的废水,其主要来源有3个:一是剩余氨水,它是在煤干馏及煤气冷 却中产生出来的废水,其水量占焦化废水总量的一半以上,是焦化 废水的主要来源;二是在煤气净化过程中产生出来的废水,如煤气 终冷水和粗苯分离水等;三是在焦油、粗苯等精制过程中及其它场 合产生的废水。
水处理技术,两者均能较好地将焦化废水中的cOD组分和氨氮污染物氧 化降解掉,使水中的各项污染指标达标排放。
A²/O 和 CWAO 技术工艺比较
当采用A²/O生物脱氮处理工艺时,由于废水中的cOD组分和氨 氮浓度均较高,为保证处理工艺的正常运行,废水须先进行蒸氨 等预处理。而催化湿式氧化处理技术则不需进行蒸氨预处理。因 此,在运行费用计算比较时,A²/O生物脱氮处理工艺需要考虑这 部分的费用。A²/O预处理装置包括:包括重力除油池、调节池及 浮选除油池等。
主要来源,大量未被农作物利用的氮化合物绝大部分被农田排水和 地表径流带入地下水和地表水中。氨氮污染源多,排放量大,并且
催化湿式氧化法治理Hfinal

催化湿式氧化法治理H-酸母液废水的研究杜鸿章1王贤高2杨民3杜书4吴鸣5中国科学院大连化学物理研究所辽宁省大连市中山路457号摘要H-酸母液是染料工业急需治理的高浓度有机废水,COD含量高,酸性强,一般的生化法尚不能有效治理.我们研制了具有高氧化活性的含贵金属-稀土金属双活性组份催化剂,对H-酸母液工业废水进行了催化湿式氧化(CWO)治理研究.CWO试验是在固定床鼓泡式反应器连续反应装臵上进行.试验考察了反应温度、反应压力、进水空速、废水PH值和气水比对催化湿式氧化法处理H-酸废水效果的影响.考虑反应工艺条件的影响和工厂实际情况以及对处理费用的要求,选定在248℃,4.0MPa,空速=2.0小时-1,空气/水46391mg/l,色度5600倍的=220:1(体),废水PH=6.0的条件下,处理含CODc rH-酸母液废水,COD和色度的去除率分别达到95.4%和98.2%.处理后的废水c r可生化性有所提高,BOD/COD>0.3,可进一步用生化法降解排放。
催化剂运转稳定性良好.根据小试结果初步估算治理H-酸废水费用为每治理1公斤COD 约0.6-0.7元.催化湿式氧化法处理H-酸母液废水有很好的应用前景.关键词:催化湿式氧化、H酸废水治理、贵金属催化剂壹、前言H酸(1-氨基-8-萘酚-3,6-二磺酸)是重要的染料中间体,在生产过程中排出的H酸母液,含有大量萘的各种取代衍生物,具有强烈的生物毒性,COD含量高达4×105-6×105,色度深(~1万倍),酸性强(PH=1-2),是一种典型的高浓度难降解的工业有机废水,常规的生化治理方法无能为力.清华大学祝万鹏[1] 与王永仪[2]曾经分别用光催化氧化法和湿式空气氧化法(WAO)对H酸盐配制的溶液进行了初步的处理研究,结果表明前者只适用于低COD浓度(~50mg/l) ,不能用于处理H酸工业废水;后者COD去除率仅50%,效果亦不理想.催化湿式氧化(CWO)是国际上八十年代在WAO基础上发展起来的一种处理高浓度有机废水的先进技术,具有净化效率高,无二次污染,占地面积小等特点,引起各国环保科技工作者关注[3,4,5].我们研制的高氧化活性的含贵金属-稀土金属双活性组份催化剂在焦化废水治理中已取得良好的效果[6],本文用催化湿式氧化技术直接处理染料厂H酸母液工业废水,考察各种反应工艺条件对治理效果的影响,为CWO技术处理H酸母液废水工业应用提供依据.贰、试验方法1.试验污水H-酸母液由吉林某染料厂提供。
0114.多相催化湿式氧化法处理高浓度难降解有机废水
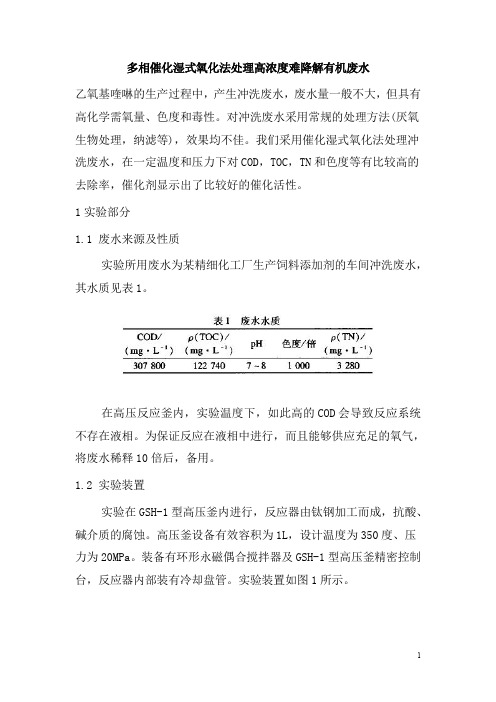
多相催化湿式氧化法处理高浓度难降解有机废水乙氧基喹啉的生产过程中,产生冲洗废水,废水量一般不大,但具有高化学需氧量、色度和毒性。
对冲洗废水采用常规的处理方法(厌氧生物处理,纳滤等),效果均不佳。
我们采用催化湿式氧化法处理冲洗废水,在一定温度和压力下对COD,TOC,TN和色度等有比较高的去除率,催化剂显示出了比较好的催化活性。
1实验部分1.1废水来源及性质实验所用废水为某精细化工厂生产饲料添加剂的车间冲洗废水,其水质见表1。
在高压反应釜内,实验温度下,如此高的COD会导致反应系统不存在液相。
为保证反应在液相中进行,而且能够供应充足的氧气,将废水稀释10倍后,备用。
1.2实验装置实验在GSH-1型高压釜内进行,反应器由钛钢加工而成,抗酸、碱介质的腐蚀。
高压釜设备有效容积为1L,设计温度为350度、压力为20MPa。
装备有环形永磁偶合搅拌器及GSH-1型高压釜精密控制台,反应器内部装有冷却盘管。
实验装置如图1所示。
1.3催化剂的制备催化剂载体采用改性后的普通陶粒。
直径3mrn 的普通陶粒经盐酸清洗后,于120度干燥12h,采用液相沉积法在其表面负载一定量的TiO2,于650度马弗炉中焙烧3h,备用。
先用Mn(NO)溶液浸渍改性后的催化剂载体20h,于650度焙烧3h,再用RuC13,溶液浸渍20h,于350℃焙烧3h,即得负载型颗粒催化剂。
1.4分析方法COD 采用GB11914-89重铬酸盐法测定;TOC 采用日本岛津TOC 分析仪测定;TN 采用GB11894-89碱性过硫酸钾消解紫外分光光度法测定;色度采用GB11903-89稀释倍数法测定。
1.5实验方法每次取废水500mL,加热到设定温度,通人高压氧气,记为反应零点,反应时间为3h。
在有催化剂的条件下,研究不同温度、压力下各种污染物的去除率、催化剂的耐酸性能、进水pH 对污染物去除率和出水pH 的影响。
2结论a)采用自制贵金属催化剂催化湿式氧化饲料抗氧化剂合成废水,取得了比较好的处理效果。
湿式催化氧化

一.背景水质分类:香料生产过程废水,经膜法分盐预处理后得到低盐度高有机物浓度废水,主要污染物为芳香环结构。
水质:外观,深色,一般性粘度,含盐7000mg/L,COD140000mg/L,pH8-9.含有机氮3000mg/L,无机氮2000mg/L,不含磷硫元素和其它无机物。
水量:120tpd处理目的:此水不能直接生化,焚烧费用昂贵,拟采取中温CWO 工艺进行有机污染物开环降解脱色脱氮,达到生化重整的目的,为后续高效生化降解处理奠定物料基础条件。
二.APO设计工艺方案:1.备料技术条件:将标的废水直接收集存放在APO原料收集池内即可,无需任何调整。
2.配置一套处理能力120tpd的中温APO降解系统,集成撬装式设计。
实现以下工艺目的:(1) COD去除率>60% (2) 有机氮脱除率>80%,氨氮输出<500mg/L.(3)脱色率>80% (4) B/C由处理前0.2提高到0.4以上,达到良好生化水平23.设计工艺条件:氧化塔运行最高温度210℃,系统运行压力3.0Mpa 。
设计系统最高温度230℃,设计系统最高压力4.5Mpa 。
4. 流程框图:三.120t/d Bi-CWO 全系统配置条件1. 中压段非标静设备(系核心主装备,称APO 组件)A 单元:热能回收组件,数量1套,3.3m (宽)*6m(长)*3.3m (高),整体撬装。
内置:中压特制结构高效换热器5台,副反应器1台,控制阀,PLC 控制器等。
B 单元:主催化氧化塔,数量,1套,DN900*13m (H ),内置固定式催化床,填料总量不低于1m3.A/B 制造材质:镍铬特种合金/钛钼镍特种合金/锆合金(限特殊部位)。
换热器和反应器接液金属内表面全部采用纳米级材料进行350℃高温烧结陶瓷化涂装覆盖防腐处理。
全部整体保温。
保温厚度100-150mm。
A:空气压缩机:15Nm3/h,最大输出压力4.5Mpa。
1套B:三柱塞泵:5m3/h,最大输出4.5Mpa,接液材质双相钢,变频,1套C:热油炉:30万大卡/h,最大输出260℃,1套D:闪蒸罐:接液材质304,2000L,1套E:尾气洗涤罐:玻璃钢,2000L,2套。
湿式催化氧化脱硫法
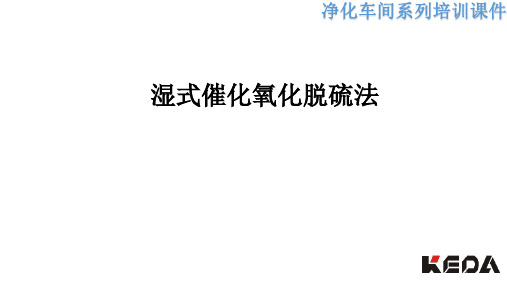
压篦子丝网太密造成塔内积硫
12
湿式氧化脱硫法指标控制
(4)、操作温度:提高温度可以加速化学反应速度,但脱硫吸收是放热反应,降低温度对 H2S的吸收有利。而在再生中溶液温度稍高对解析再生,副盐分解等有利。再生反应随着温度 升高而加快,但温度过高对硫颗粒聚合不利,影响溶液粘度和表面张力;不利于硫泡沫的浮 选,还会使副反应急剧上升。再者溶液温度过高,也会使溶液解O2能力下降,不利催化剂吸 氧再生。而且,以自产氨为碱源的工艺,只有控制好温度才能控制好碱度。并且溶液对设备 的腐蚀也是随温度的升高而加剧。
5
湿式催化氧化脱硫法工艺流程
氧化吸收
浮选再生
循环回收
6
湿式催化氧化脱硫法工艺流程
故此整个脱硫工艺包括氧化吸收、浮选再生、循环回收三大环节,他们之间相互依存,相互影响。 第一步氧化吸收。气液逆流接触,通过传质(填料)H2S从气相界面向液相界面转移,进入液相主体。酸碱中和反应
生成相应的盐( NaHS)转化为富液,同时盐在催化剂作用下转化成单质硫。
湿式催化氧化脱硫法
1
目录
一、湿式催化氧化脱硫法定义 二、湿式催化氧化脱硫法工艺流程
二、湿式催化氧化脱硫法原理
三、湿式催化氧化脱硫法指标控制
2
氧化铁脱硫 干法脱硫 活性炭脱硫 冷煤气脱硫
脱硫过程:Fe2O3· H2O+3H2S→Fe2S3· H2O+3H2O Fe2O3· H2O+3H2S→2FeS+1/8S8+4H2O 再生过程:2Fe2S3+3O2+6H2O→4Fe(OH)3+6S 4FeS+3O2+6H2O→4Fe(OH)2+4S 脱硫过程:活性炭脱硫主要是利用活性炭的催化和吸 附作用,活性炭的催化活性很强,煤气中的H2S在活性 炭的催化作用下,与煤气中少量的O2发生氧化反应。 再生过程:一般利用450-500℃左右的过热蒸汽对活性 炭脱硫剂进行再生。
催化湿式氧化设计案例
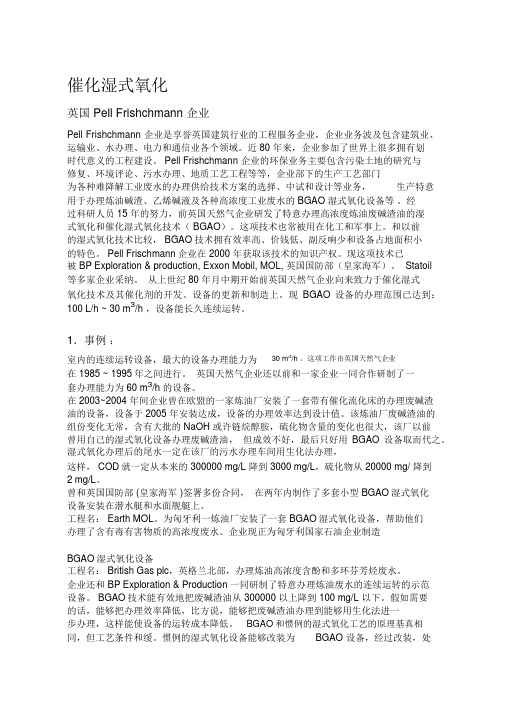
催化湿式氧化英国 Pell Frishchmann 企业Pell Frishchmann 企业是享誉英国建筑行业的工程服务企业,企业业务波及包含建筑业、运输业、水办理、电力和通信业各个领域。
近 80 年来,企业参加了世界上很多拥有划时代意义的工程建设。
Pell Frishchmann 企业的环保业务主要包含污染土地的研究与修复、环境评论、污水办理、地质工艺工程等等,企业部下的生产工艺部门为各种难降解工业废水的办理供给技术方案的选择、中试和设计等业务,生产特意用于办理炼油碱渣、乙烯碱液及各种高浓度工业废水的 BGAO 湿式氧化设备等。
经过科研人员 15 年的努力,前英国天然气企业研发了特意办理高浓度炼油废碱渣油的湿式氧化和催化湿式氧化技术( BGAO)。
这项技术也常被用在化工和军事上。
和以前的湿式氧化技术比较, BGAO技术拥有效率高、价钱低、副反响少和设备占地面积小的特色。
Pell Frischmann企业在 2000 年获取该技术的知识产权。
现这项技术已被 BP Exploration & production, Exxon Mobil, MOL, 英国国防部(皇家海军)、 Statoil等多家企业采纳。
从上世纪 80 年月中期开始前英国天然气企业向来致力于催化湿式氧化技术及其催化剂的开发、设备的更新和制造上。
现BGAO 设备的办理范围已达到:100 L/h ~ 30 m3/h ,设备能长久连续运转。
1.事例:室内的连续运转设备,最大的设备办理能力为30 m3/h 。
这项工作由英国天然气企业在 1985 ~ 1995年之间进行。
英国天然气企业还以前和一家企业一同合作研制了一套办理能力为 60 m3/h 的设备。
在 2003~2004 年间企业曾在欧盟的一家炼油厂安装了一套带有催化流化床的办理废碱渣油的设备,设备于 2005 年安装达成,设备的办理效率达到设计值。
该炼油厂废碱渣油的组份变化无常,含有大批的 NaOH 或许链烷醇胺,硫化物含量的变化也很大,该厂以前曾用自己的湿式氧化设备办理废碱渣油,但成效不好,最后只好用BGAO 设备取而代之。
湿式氧化技术演示幻灯片

(Technology of Wet Air Oxidation)
1
主要内容
◎ 湿式氧化技术及特点 ◎ 湿式氧化技术作用机理 ◎ 影响湿式氧化处理效果的主要因素 ◎ 湿式氧化工艺和设备 ◎ 湿式氧化处理技术的应用 ◎ 催化湿式氧化技术
2
湿式氧化技术及特点
1. 湿式氧化法:指在高温(125-320℃)和高压 (0.5-20MPa)条件下,以空气中的氧气为氧化剂, 在液相体系中,将废水中的有机物氧化分解为无机 物或小分子有机物的过程。相应的技术称之为湿式 氧化技术(wet air oxidation,WAO)。
35
(3)空气压缩机:为了减少费用,常采用空气作为 氧化剂,当空气进入高温﹑高压的反应器之前,需要 使空气通过热交换器升温和通过压缩机提高空气压 力,以达到需要的温度和压力。通常使用复式压缩 机,根据压力要求选定段数,一般选3~4段。 (4)气液分离器:压力容器。氧化后的液体经过热 交换器后温度降低,使液相中的O2、CO2和易挥发 的有机物从液相进入气相分离。分离器内的液体再 经过生物处理或直接排放。
27
3. Vertech工艺(深井反应器)
28
组成:由一个垂直在地面下1200~1500m的反应 器及两个管道组成,内管为入水管,外管为出水 管。 操作条件:井的深度在1200~1500m之间,反应 器底部的压力在8.5~11MPa,反应器内的温度可 达550K,停留时间约为1h。 优点:高压可以部分由重力转化,减少了物料进 入高压反应器所需要的能量。 缺点:深井的腐蚀;反应器长,停留时间长。
2. WAO最初由美国的F. J. Zimmermann在1944年 研究提出的,并于1958年首次用于处理造纸黑液, 也称齐默尔曼法。
- 1、下载文档前请自行甄别文档内容的完整性,平台不提供额外的编辑、内容补充、找答案等附加服务。
- 2、"仅部分预览"的文档,不可在线预览部分如存在完整性等问题,可反馈申请退款(可完整预览的文档不适用该条件!)。
- 3、如文档侵犯您的权益,请联系客服反馈,我们会尽快为您处理(人工客服工作时间:9:00-18:30)。
催化湿式氧化设计案
例
催化湿式氧化
英国Pell Frishchmann 公司
Pell Frishchmann 公司是享誉英国建筑行业的工程服务公司,公司业务涉及包括建筑业、运输业、水处理、电力和通讯业各个领域。
近80年来,公司参与了世界上许多具有划时代意义的工程建设。
Pell Frishchmann 公司的环保业务主要包括污染土地的研究与修复、环境评价、污水处理、地质工艺工程等等,公司下属的生产工艺部门为各类难降解工业废水的处理提供技术方案的选择、中试和设计等业务,生产专门用于处理炼油碱渣、乙烯碱液及各类高浓度工业废水的BGAO湿式氧化设备等。
通过科研人员15年的努力,前英国天然气公司研发了专门处理高浓度炼油废碱渣油的湿式氧化和催化湿式氧化技术(BGAO)。
这项技术也常被用在化工和军事上。
和之前的湿式氧化技术比较,BGAO技术具有效率高、价格低、副反应少和设备占地面积小的特点。
Pell Frischmann公司在2000年获得该技术的知识产权。
现这项技术已被BP Exploration & production, Exxon Mobil, MOL, 英国国防部(皇家海军)、Statoil等多家公司采用。
从上世纪80年代中期开始前英国天然气公司一直致力于催化湿式氧化技术及其催化剂的开发、设备的更新和制造上。
现BGAO设备的处理范围已达到:100 L/h ~ 30 m3/h,设备能长期连续运行。
1.案例:
(1)室内的连续运行设备,最大的设备处理能力为30 m3/h。
这项工作由英国天然气
公司在1985 ~ 1995年之间进行。
英国天然气公司还曾经和一家公司一起合作研制了一套处理能力为60 m3/h的设备。
(2)在2003~2004年间公司曾在欧盟的一家炼油厂安装了一套带有催化流化床的处
理废碱渣油的设备,设备于2005年安装完成,设备的处理效率达到设计值。
该炼油厂废碱渣油的组份变化多端,含有大量的NaOH或者链烷醇胺,硫化物含量的变化也很大,该厂之前曾用自己的湿式氧化设备处理废碱渣油,但效果不好,最后只能用BGAO设备取而代之。
湿式氧化处理后的尾水必须在该厂的污水处理车间用生化法处理,这样,COD就必须从原来的300000 mg/L降到3000 mg/L,硫化物从20000 mg/降到2 mg/L。
(3)曾和英国国防部(皇家海军)签订多份合同,在两年内制作了多套小型BGAO湿
式氧化设备安装在潜水艇和水面舰艇上。
(4)工程名:Earth MOL。
为匈牙利一炼油厂安装了一套BGAO湿式氧化设备,帮
助他们处理了含有毒有害物质的高浓度废水。
公司现正为匈牙利国家石油公司制造
BGAO湿式氧化设备
(5)工程名:British Gas plc,英格兰北部,处理炼油高浓度含酚和多环芳香烃废
水。
(6)公司还和BP Exploration & Production一起研制了专门处理炼油废水的连续运行
的示范设备。
BGAO技术能有效地把废碱渣油从300000以上降到100 mg/L以下。
如果需要的话,可以把处理效率降低,比方说,可以把废碱渣油处理到可以用生化法进一步处理,这样能使设备的运行成本降低。
BGAO和常规的湿式氧化工艺的原理基本相同,但工艺条件缓和。
常规的湿式氧化设备可以改装为
BGAO设备,通过改装,处理能力和处理效率都将大大提高,而运行成本大大降低。
2. 设计参数
BGAO工艺和设备是根据相似组份的废碱渣油的运行参数设计的,或者根据中试实验结果获取参数。
设计参数可以通过处理要求和出水参数优化。
废碱渣油的有机物和碱的含量、它的pH缓冲能力、HS-/S2-和HCO3-/CO32-的平衡以及H2S气体的分压对工艺和设备的优化尤其重要。
主要工艺参数有:温度、压力、停留时间、气流速度和催化剂用量。
典型废碱渣油的工艺条件如下:
反应釜温度: 200 ~ 2700C;压力 35~80大气压
停留时间: 10~60 分钟气流速度0.05 – 2.5 m3 (处理能力1 m3/h)
4 – 12 m3 (处理能力10 m3/h) 对于特种废碱渣油,需要定量加酸(H2SO4或者HNO3)或者碱(NaOH)。
工艺控制
BGAO设备系全自动的,无需专人照看和管理。
它主要由反应釜、开机设施、控制关机设施和紧急关机设施构成。
自动进料和废碱渣油监控设施能对处理后尾水组份的变化进行自动调节,也能对尾气组分的变化进行自动调节。
设备的大小
处理设备基本和一个车道差不多大,它在运送到用户之前全部装配好,并通过厂内检验。
设备的大小可按照用户的要求变化,比方说,如果需要安装在室内,高度可以减小。
一般设备都安装在室外的硬质地面上运行。
3. BGAO和常规湿式氧化比较的优点
BGAO的主要优点如下:
(1)BGAO的操作温度和压力都比较低,所以设备成本和运行成本都比较低。
(2)BGAO的处理效率高。
COD去除率在标准运行条件下达到99%(COD包括无
机和有机硫化物)。
处理后尾水可以回用,灌溉等。
(3)设备的处理效率可以根据用户需要降低,从而使运行成本降低。
(4)BGAO工艺首先氧化废碱渣油中的硫化物、高分子有机物、芳香烃和带双键的
有机物,破坏对生物有毒有害物质,大大提高处理后尾水的BOD5/COD比例,改善尾水的可生化性能。
(5)停留时间比较短,所以设备的体积大大减小。
(6)氮有机物和氨被转化为N2去除(在常规湿式氧化过程中它们被转化为硝酸
盐)。
(7)反应条件缓和,所以反应釜可以用比较便宜的材料制造,设备成本较低。
4. BGAO工艺性能
典型的运行参数见图1~3。
BGAO设备在可以一定处理范围内根据用户的特殊要求设计。
排放的尾气组份如下:
氮气(包括空气中余留下来的氮气) 79% Mol
氧气 0~3 Mol
二氧化碳 18-21 Mol
水蒸汽饱和(25~400C)
易挥发性物质 < 35 mg/m3
总硫 <0.1 ppm
压力 0~2 大气压
温度 20~30 0C
图1:处理废碱渣油的BGAO运行参数:COD的去除
图2:处理废碱渣油的BGAO运行参数:特殊组份
图3:处理废碱渣油的BGAO运行参数:特殊组份
图4:设备图纸
图5:BGAO示范设备
图6:BGAO废碱液处理设备
图7:BGAO废碱液处理设备
表1 湿式氧化工艺的性能比较。