锅镀锌线设计方案(电加热)
陶瓷锌锅热镀锌工艺及电镀锌

熱浸鍍鋅流程簡介熱浸鍍鋅的原理,簡單的說即是將已清洗潔淨的鐵件,經由Flux 的潤濕作用,浸入鋅浴中,使鋼鐵與熔融鋅反應生成一合金化的皮膜。
其作業流程簡示如下:良好的熱浸鍍鋅作業,應是各製程均在嚴格的管制下,徹底發揮該製程的功能。
且若前一製程的不良,會造成後續製程的連鎖不良反應,而大量增加作業成本或造成不良熱浸鍍鋅產品。
若前處理不良,則熔鋅無法與鋼鐵正常完全反應,形成最完美的鍍鋅皮膜組織。
若後處理不良,則破壞鍍鋅皮膜外觀,減低商品價值等。
1 引言热镀锌也称热浸镀锌,是钢铁构件浸入熔融的锌液中获得金属覆盖层的一种方法。
近年来随高压输电、交通、通讯事业迅速发展,对钢铁件防护要求越来越高,热镀锌需求量也不断增加。
2 热镀锌层防护性能通常电镀锌层厚度5~15μm,而热镀锌层一般在35μm以上,甚至高达200μm。
热镀锌覆盖能力好,镀层致密,无有机物夹杂。
众所周知,锌的抗大气腐蚀的机理有机械保护及电化学保护,在大气腐蚀条件下锌层表面有ZnO、Zn(OH)2及碱式碳酸锌保护膜,一定程度上减缓锌的腐蚀,这层保护膜(也称白锈)受到破坏又会形成新的膜层。
当锌层破坏严重,危及到铁基体时,锌对基体产生电化学保护,锌的标准电位-0.76V,铁的标准电位-0.44V,锌与铁形成微电池时锌作为阳极被溶解,铁作为阴极受到保护。
显然热镀锌对基体金属铁的抗大气腐蚀能力优于电镀锌。
3 热镀锌层形成过程热镀锌层形成过程是铁基体与最外面的纯锌层之间形成铁-锌合金的过程,工件表面在热浸镀时形成铁-锌合金层,才使得铁与纯锌层之间很好结合,其过程可简单地叙述为:当铁工件浸入熔融的锌液时,首先在界面上形成锌与α铁(体心)固熔体。
这是基体金属铁在固体状态下溶有锌原子所形成一种晶体,两种金属原子之间是融合,原子之间引力比较小。
因此,当锌在固熔体中达到饱和后,锌铁两种元素原子相互扩散,扩散到(或叫渗入)铁基体中的锌原子在基体晶格中迁移,逐渐与铁形成合金,而扩散到熔融的锌液中的铁就与锌形成金属间化合物FeZn13,沉入热镀锌锅底,即为锌渣。
热镀锌处理线的工艺流程以及相关设备描述

热镀锌处理线的工艺流程以及相关设备描述热镀锌处理线的工艺流程以及相关设备描述随着世界经济的发展,市场对于钢板的热镀锌需求数量日益增多,同时对于钢板的热镀锌质量要求也越来越高,这就对热镀锌处理线的工艺水平要求越来越严格,所以,近些年对于热镀锌钢板的连续退火技术的工艺要求以及相关设备有了明显的改善。
文章针对热镀锌生产线的工艺流程及处理方法,以及连续退火炉相关设备的组成作简要说明。
1、热镀锌连续退火技术发展简析随着世界经济的发展,工业生产水平的日益进步,市场对于钢板防腐性能的要求逐渐提高,钢板防腐已成为工业生产中重要的研究方向,采用带钢表面进行金属镀层的方法防止带钢腐蚀,其金属镀层原料来源广泛,具有较强的成本优势,广泛应用于工业生产中。
当前工业生产中最为普遍的金属镀层方位有电镀法和热镀法。
镀锌板用途广泛,主要应用于环境较为恶劣的户外,所以对镀层的厚度有着较高的要求。
另外,金属镀层相当于带钢表面产生阳极保护,镀层厚度增加将延长钢板使用寿命,此时对镀层均匀性的要求不是很严格,热镀锌产品正好能够满足以上要求。
传统的电镀锌尽管镀层较为均匀,表面没有明显缺陷,同钢板紧密结合,其厚度相当于普通热镀锌厚度的1/5至1/7,但其成本相对较高,市场使用较少。
目前,常见的钢板镀金属方法仍是热镀锌。
从上世纪30年代,波兰人森吉米尔发明的连续热镀锌技术被沿用至今,具有其自身较为独特的工艺方法。
其特点是通过采用直火加热的方法将带钢表面油脂烧掉,并使带钢表面发生氧化,之后在还原气氛中通过此用辐射管间接加热的方式,对带钢进行加热处理,将之前的氧化膜取出,是带钢表面活化,以合适的温度进入锌锅,完成带钢表面的镀锌。
2、生产工艺2.1 工艺流程热镀锌生产工艺流程:冷轧卷→开卷机→五辊矫直机→测厚仪→双层切头剪→半自动窄搭接焊机→清洗段→入口活套→连续退火炉→锌锅→气刀→小锌花或合金化炉→镀后冷却段→镀层测厚仪→水淬槽→热风干燥→光整机→拉矫机→化学处理→热风干燥→出口活套→静电涂油→卷取机。
陶瓷锌锅感应器加热原理分析

PL = PR >>PM
可见在压力差的作用下,中间熔沟 M-N 的锌液就被迫挤出,就流到锌锅中,挤出方向从 N 到 M, 留下的空穴由两侧熔沟 L-N、R-N 的锌液填补进来,从而导致了两侧熔沟的密度进一步减少,那么 锌锅内密度一致的锌液在此密度差的作用下,进入熔沟 L-N、R-N 得到了填充,因此就形成了锌液 经加热后从中间熔沟喷流出,而从两侧流进入的结果。这样周而复始不止息的喷流就是感应器熔沟 中锌液的固定流动方式。显然,外加电流越大,喷流速度就越快,加热能力就越强。制造锅体时, 虽然中间熔沟的断面积比两侧熔沟的断面积稍大一些, 但应用实践证明, 上述推导的结果依然适用。 4.熔沟内二次电流的计算 沟槽式锌锅感应器的工作原理与变压器相似。 在导磁体的铁芯上安置了多匝的一次绕组即感应 线圈,二次绕组就是熔沟内流动的锌液,给感应线圈通以工频交变电流之后,熔沟中就会感应出低 电压,大电流。n1:n2=I2:I1,同时 n1:n2=U1:U2。即电流与匝数成反比,电压与匝数成正比。 2 感应器就因熔沟通过很大的电流而作功,其发热的功为:W=I RT。即所作功为流经熔沟的电流的平 方乘以熔沟的电阻再乘以时间。熔沟中的热又通过传导和对流的方式传送到锌锅中的锌液。 由变压器原理可知,作为二次线圈的熔沟只能看作一匝线圈,而一次线圈匝数设定为 n,一般 感应器一次线圈的匝数为 17~18 匝。 现以一次线圈 17 匝为例,计算如下: (1)电流 I 熔沟/I 线圈=n/1=17,所以 I 熔沟=17×I 线圈 在正常生产中,感应器低保温电流为 IA=IB≈100A,则 I 熔沟=1700A,I 中=3400A (2)电压 U 熔沟/U 线圈=1/n=1/17,所以 U 熔沟=U 线圈/17 在正常生产中,感应器低保温电压最低不能低于 80 伏。有的厂家规定为 100 伏,那就更有保 障了。按照 80 伏计算结果如下: U 线圈=80V,所以 U 熔沟=80/17=4.7V 因此熔沟中电压极低,即为安全电压,而电流是沿最短线路流通的,所以没有触电的感觉。 最短线路可以这样理解:若将铁棒伸进锌锅内操作甚至插到熔沟内,见图 4。
镀锌线管施工方案(3篇)

第1篇一、工程概况镀锌线管施工是建筑工程中电气工程的重要组成部分,主要用于输送电线、电缆等。
本工程采用镀锌线管进行施工,确保电气线路的安全、可靠。
以下是镀锌线管施工方案。
二、施工准备1. 技术准备(1)熟悉施工图纸,了解电气线路布置、线管规格、数量及要求。
(2)了解镀锌线管的性能、规格、型号及安装要求。
(3)掌握电气工程相关规范、标准及施工工艺。
2. 材料准备(1)镀锌线管:根据施工图纸要求,准备相应规格、型号的镀锌线管。
(2)电线、电缆:根据电气工程需要,准备相应规格、型号的电线、电缆。
(3)其他材料:如线槽、接线盒、线鼻子、绝缘胶带等。
3. 人员准备(1)组织施工队伍,明确施工人员职责。
(2)对施工人员进行技术交底,确保施工人员掌握施工工艺和操作规程。
(3)对施工人员进行安全教育培训,提高安全意识。
4. 施工设备准备(1)电动工具:如电钻、切割机、剥线钳等。
(2)手动工具:如扳手、螺丝刀、剪刀等。
(3)测量工具:如卷尺、水平尺、角度尺等。
三、施工工艺1. 施工流程(1)测量放线:根据施工图纸,确定电气线路走向,放线并标明位置。
(2)线管安装:根据放线结果,安装镀锌线管。
(3)电线、电缆敷设:将电线、电缆穿入镀锌线管。
(4)接线盒、线槽安装:根据设计要求,安装接线盒、线槽。
(5)接线:将电线、电缆接入接线盒,并进行接线。
(6)绝缘处理:对接线处进行绝缘处理。
(7)检查验收:对施工质量进行检查,确保符合规范要求。
2. 施工要点(1)测量放线1)根据施工图纸,确定电气线路走向,确保线路布局合理、美观。
2)使用卷尺、水平尺等测量工具,确保线路水平、垂直。
3)标明线路位置,便于后续施工。
(2)线管安装1)根据放线结果,选择合适规格的镀锌线管。
2)使用电钻在墙体、柱子等部位钻孔,将线管固定。
3)线管固定应牢固,避免松动。
4)线管转弯处应采用弯头,避免直角转弯。
(3)电线、电缆敷设1)将电线、电缆穿入镀锌线管,确保电缆紧贴线管。
热镀锌生产线方案

热镀锌生产线方案设计一、技术指标1、生产能力:150000吨/年;2、镀锌能力:5~6杠/小时。
3、单杠重量:≤18吨4、锌锅尺寸(长×宽×高):15m×3m×4 m5、吊杠长度:15000+1600(酸槽壁厚400×2,吊杠两端突出长度400×2)=16600mm;6、锌锅烟尘处理后烟气黑度达到一级,固体颗粒小于90mg/m3、HCl除去率:90%。
7、酸气、酸雾处理后应达到国家排放标准(HCl≤100mg/ m3)。
8、镀锌产品标准:符合GB/T13912-2002要求。
二、方案(一)总体布局车间布置如图1、图2所示。
根据热镀锌多年经验和试验结果,酸洗池需10个,1个漂洗池、一个助镀池,共12个池。
酸洗池尺寸为(长×宽×高):15.5m×3.2×4m,酸洗池之间的隔壁厚度为0.4m,酸洗池、漂洗池、助镀池、总长度为43.6m。
采用先进的L型热镀锌工艺布局,酸洗和浸锌分段布置,待镀件在挂具上横向步进酸洗后,物料流向转90度轴向进入浸锌工位,物料流向成L形流动,改变了传统的物料横向进入浸锌工位的输送方式。
酸洗时采用横向、垂直运动机械化,经PLC编程,实现酸洗步进自动化作业。
酸洗工段采用步进方式,厂房封闭方便。
锌锅在独立的空间内,空间体积小,减小了引风机的排量,从而减小了电机功率和运行费用。
1、设备组成总体布局如图1所示。
设备主要由冷却槽、钝化槽、半门式起重机、酸洗槽、水洗槽、助镀槽、酸洗自动控制系统、全封闭烟雾收集系统、热浸锌烟气净化设备、助镀液除铁盐设备、全封闭酸雾收集处理系统、酸液加热设备、烘干换热器、助镀液加热设备、浸锌环轨起重机、酸洗自动线、自行式进料地轨车、锌锅燃烧及控制系统、废酸处理设备等组成。
1-冷却槽2-钝化槽3-半门式起重机4-酸洗槽5-水洗槽6-助镀槽7-锌锅燃烧及控制系统8-全封闭烟雾收集系统9-热浸锌烟气净化设备10-助镀液除铁盐设备11-全封闭酸雾收集处理系统12-酸液加热设备13-烘干换热器14-助镀液加热设备15-浸锌环轨起重机16-酸洗自动线及控制系统17-自行式进料地轨车热镀锌生产线生产运行过程:⑴将挂有待镀件的吊杠放在进料地轨车上,启动自行进料地轨车,进入全封闭酸洗工段;⑵步进式自动酸洗系统(水平、垂直升降)按规定的程序将待镀件按多槽酸洗工艺要求进行酸洗除锈处理,并按工艺要求依次递进自动完成整个酸洗过程,此时酸雾回收净化设备启动,将脱脂除锈时产生的酸雾进行回收净化处理,处理率达91.2%,处理后的气体达标排放(气体中HCL含量小于100mg/m3)。
浅谈热镀锌线锌锅的使用和维护

区域治理综合信息浅谈热镀锌线锌锅的使用和维护樊甲利河钢邯钢冷轧厂,河北 邯郸 056001摘要:随着我国热镀锌生产工艺的不断成熟,热镀锌产品的品质也在逐步地提升。
由于热镀锌产品的各种突出优势,目前,热镀锌产品已经被广泛地应用在社会的各个领域。
锌锅在热镀锌产品的生产过程中发挥着重要的作用,是热镀锌生产线重要的组成部分。
锌锅作为热镀锌生产线的重要设备,其使用不但能够影响热镀锌产品的质量,还能够影响热镀锌产品的生产成本,本文就镀锌线锌锅的使用和维护做了相关的阐述。
关键词:热镀锌线;锌锅;使用;维护锌锅设备是热镀锌生产线重要的组成部分,其主要的功能就是将固态锌熔化,为带钢浸锌的过程提供足够的锌液,同时对锌液进行供热。
锌锅设备的正常运行是提升热镀锌生产线生产效率的重要保障。
另外,锌锅设备还是决定热镀锌产品表面质量和锌层性能的主要因素之一。
一、锌锅设备概述1 锌锅设备的生产设计在生产锌锅设备的过程中,不但要选取合适的制造材料,还要确保锌锅的型号能够与加热系统、热镀锌件以及生产能力相匹配。
在符合生产需求的基础上,要尽可能地减小锌锅的面积,这样做的话,不但可以有效地减少热损耗,还可以有效地减少锌灰的生成。
另外,在设计锌锅设备的过程中,还需要重视锅壁热负荷这一重要因素,因为锅壁热负荷直接影响着锌锅设备的使用寿命。
2 锌锅设备的发展在以往的热镀锌产品生产过程中,锌锅设备通常使用的是铁制的锌锅。
铁制锌锅也经历了一系列的发展过程,从铸铁锌锅到后来的工业纯铁锌锅,最后又发展成为低碳钢板锌锅。
铁制锌锅的加热方式有很多种,包括煤气加热、重油加热和电阻加热等。
铁制锌锅还是有很多的优点的,铁制锌锅不但生产成本较低,制造起来也较为方便。
另外,铁制锌锅由于结构比较简单,所以维护起来也比较容易。
在实际的生产过程中,铁制锌锅还可以有效的减低能源的消耗。
但是,铁制锌锅也存在一定的弊端,一方面是使用寿命较短,另一方面是会生成很多的底渣。
随着时代的不断发展,铁制锌锅逐步地被陶瓷锌锅所取代,现代化的热镀锌生产线大多使用的是陶瓷锌锅,陶瓷锌锅可以有效地解决锌耗较多的问题。
热镀锌锌锅技术 ppt课件
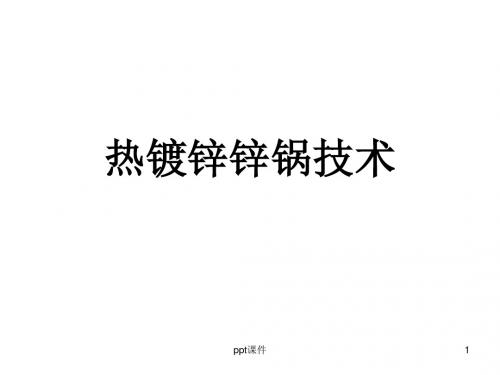
48
2、碳在钢中存在状态的影响 由于热处理工艺不同,钢中碳的存在状态也不 同。钢中的碳以粒状珠光体或层状珠光体状态存在 时,其在锌液中的铁损均最大,而屈氏体最小。这 种趋势与它们在硫酸中的溶解量相似。对碳含量相 同的钢,其中的碳不以粒状或片层珠光体状态存在, 而以弥散均匀的索氏体或屈氏体状态存在,则其铁 损就小得多。钢板在轧制后退火时,如果退火温度 过高,就会导致在钢板表面形成晶间渗碳体。它使 钢板的表面张力增大,降低锌液对钢板表面的浸润 性,锌液在钢板表面的流动不能均匀地进行,容易 产生锌瘤等缺陷。
ppt课件
44
3.锌灰、锌渣的形成原因分析(图1-1)
(1)加热温度过高或过低; 导致锌液中的铁含量超过该温度下的溶解度-易形 成的流动性极差的锌铁合金-锌渣(高达94% ) (2)保温时间过长 a.500℃附近时,铁损量随着加温及保温时间急剧增 加; b.低于或高于480~510℃范围,随时间延长铁损提 高缓慢 -480~510℃称为恶性溶解区。在此温度 范围内锌液对工件及锌锅浸蚀最为严重,超过 560℃铁损又明显增加,达到660℃以上锌对铁基 体是破坏性浸蚀,锌渣会急剧增加,施镀无法进 行。因此,施镀目前多在430~450℃及540~ 600℃两个区域内进行。
鞍钢冷轧 实习论文 镀锌线锌锅气刀
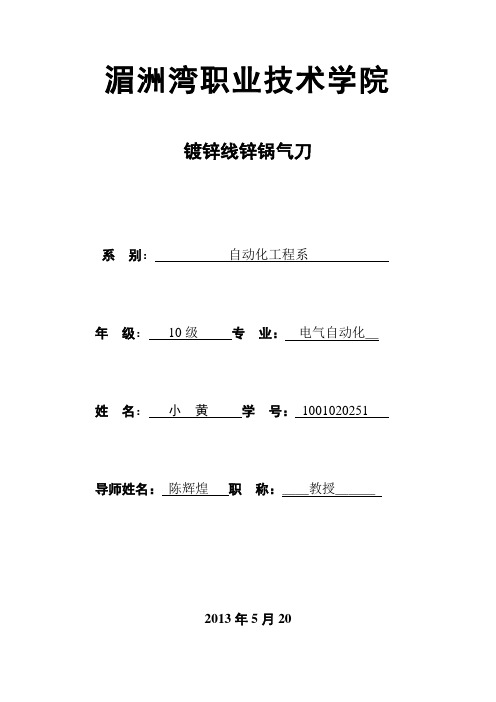
湄洲湾职业技术学院镀锌线锌锅气刀系别:自动化工程系年级:10级专业:电气自动化_姓名:小黄学号:1001020251导师姓名:陈辉煌职称:__教授___2013年5月20目录1.前言 (1)2.锌锅气刀简易图 (2)3.锌锅气刀的主要设备 (5)4.锌锅气刀的主要设备的原理和作 (5)4.1锌锅 (5)4.2气刀 (5)4.3沉没辊 (5)4.4校证辊 (5)4.5稳定辊 (5)4.6档板 (5)5.气刀故障处理方案 (5)6.气刀常见故障及处理方 (6)7.锌锅故障处理方案 (6)8.测厚仪故障处理方案 (7)参考文献 (8)致谢词 (9)1.前言鞍钢钢铁集团股份公司冷轧薄板厂是中国冷轧板生产的摇篮和诞生地,于1960年建成投产,为当时中国第一家冷轧薄板生产厂。
1997年鞍钢股份有限公司成立后,经过不断的技术改造和管理升级,到2004年末,鞍钢股份冷轧厂已经成为拥有两条酸洗-轧机联合机组、一条盐酸洗机组、两台新型可逆轧机、两条热镀锌机组、两条彩涂机组及后继深加工设备。
能够生产热轧酸洗板、冷轧板、热镀锌钢板、彩色涂成板等多元化优质终端产品,以及代表冷轧工艺高水平的05级家电板和轿车板。
年生产能力达35万吨。
产品出口日本、韩国及欧美等30几个国家和地区,数量品种不断增加,在国内外冷轧产品的市场占有率稳定提高。
主导产品应用于汽车板、家电板及冷轧行业最高级别的轿车05级板。
2004年8月开工的新区2130冷轧工程,预计2006年5月建成投产,年设 1997年鞍钢股份有限公司成立后,经过不断的技术改造和管理升级,到2004年末,鞍钢股份冷轧计生产能力为200万吨,产品主要定位于轿车外板和高档次家电板。
整体装备技术达到国际先进水平,投产后将有助于鞍钢冷轧产品档次的进一步提升。
重工业的发展是衡量一个国家发展的重要依据。
冷轧更是在钢铁行业中占有举足轻重的作用,冷轧板的好坏直接影响到汽车行业、家电行业、门业、搪瓷业、建筑业、制造业等行业的发展。
热镀锌线与工艺操作流程

热镀锌线与工艺操作流程一、入口段操作概述人口段的操作是要在保证作业线不停止作业的条件下将原板带钢连续地送入热镀锌机组。
入口的设备为双套布置,在生产中,一台生产而另一台那么处于准备状态。
例如,1#开卷机运行时,2#开卷机必须要上好钢卷,并用入口双层剪剪切去超厚的头部,做好焊接前的一切准备工作。
待1#开卷机的带钢运行完后,再切掉超厚的带钢尾部,迅速与2#开卷机上的准备好的钢卷头部焊接起来,这样,两台开卷机交替作用,轮换准备,不致于因带钢供给不上而引起整个镀锌机组降速或停机。
这些操作,必须在储存于入口活套内的带钢还没有用完的时间内进行。
焊接结束后,使进口段加速地以比工艺速度快地速度运转,重新使活套回到充满状态。
此外,活套内必须保持适当的张力。
还要检查原板的外表状态,当发现原板缺陷时,要采取相应的处理措施。
二、开卷开卷时首先用吊车将原料钢卷从存放区吊到入口鞍座上。
在入口鞍座上操作工要检查钢卷质量,如检查边裂情况和钢卷塔形情况,检查钢卷的标签是否与生产方案单相符。
符合要求后人工剪断带钢捆带,然后用入口钢卷小车将钢卷运送到开卷机卷筒上,上卷时要注意使钢卷的中心线与卷筒的中心线高度相同,以防止钢卷与卷筒的碰撞。
上卷后,降下钢卷小车,卷筒涨紧,通过目视操作入口钢卷对中装置使钢卷处于机组的中心线上。
压下压辊,升起穿带导板,点动开卷机和入口夹送辊使带头送到入口双层剪。
三、切头在冷轧带卷的头尾不可防止地要存在超厚局部,在开卷机出来的钢卷,用爬行速度送到双层剪进行剪切,剪下的废钢通过废料收集装置送到收集箱中。
这样依次逐张剪切,直到带钢厚度符合要求为止。
带钢尾部的超厚局部,在带钢尾部运行到上述切头后应到达的厚度时,也应该将余下的局部剪切掉。
假设是带钢头部没有超厚,切头时必须将钢卷外表损坏的一两圈剪掉。
假设发现头部还有边裂、孔洞等不适合于镀锌的缺陷,就还要继续剪切,直到符合要求为止。
四、焊接带钢经夹送辊后被送到焊机处,并和上一卷的带钢在焊机的入口和出口处建立了一个小的带钢活套,此后带钢的头部进入焊机。
广钢JFE镀锌线炉区中间配管方案
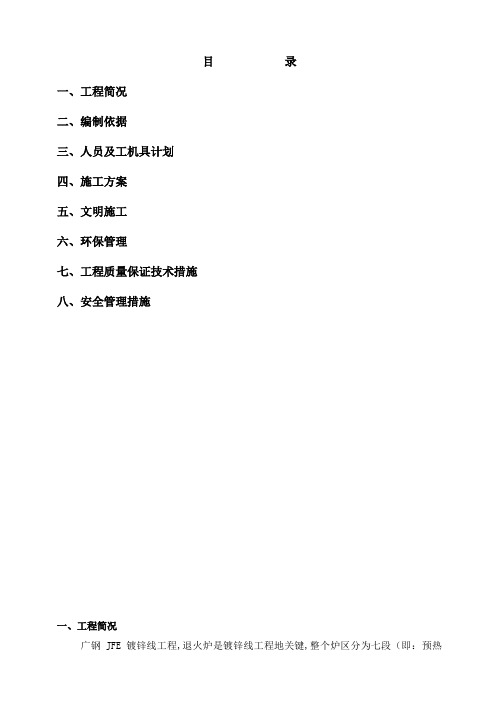
目录一、工程简况二、编制依据三、人员及工机具计划四、施工方案五、文明施工六、环保管理七、工程质量保证技术措施八、安全管理措施一、工程简况广钢JFE镀锌线工程,退火炉是镀锌线工程地关键,整个炉区分为七段(即:预热段、加热段、均热段、快冷段、均衡区段、气体冷却段、化学炉段)我部负责炉区工艺介质管道地安装,炉区工艺介质管道涉及介质多达24种(天然气、氢气、氮气、氢氮混合气、助燃空气、压缩空气、循环冷却水、润滑管道等),管道规格由DN8至DN1000之间,管道材质包含五种,普通焊管、无缝钢管、镀锌焊管、镀锌无缝钢管和不锈钢管道.管道安装分布在标高由±0至+59m,总长180M地整个炉区,整个炉区介质管道总长约15000M,总重约170吨(不含阀门、管件地重量).由于下管道部分属于压力管道,对施工质量都有严格要求,为保证施工顺利、安全、优质进行,特编制此施工方案,指导现场施工.主要介质管道明细表本工程是新建工程,镀锌线生产线,生产线全长达180M,量大、线短,具有有如下特点:1、管道工作量较大,工期紧张:全线管道约15000M左右,需要在三个月左右完成,施工任务重.2、管道分布在±0至+59M之间,且大管径管道多分布于高空,高空作业危险性较大.3、施工区域狭窄,空间狭小,施工作业难度大.二、编制依据1、《工业金属管道施工及验收规范》GB50235-972、《现场设备、工业管道焊接工程施工及验收规范》GB50236-983、《建筑安装工程金属熔化焊焊缝射线照相检测标准》CECS70:944、《工业设备及管道绝热施工及验收规范》GB50126-20085、《低压流体输送用镀锌焊接钢管》 GB3091-20016、《给排水管道工程施工及验收规范》GB50268-20087、《输气管道工程设计规范》 GB50251-20038、《氢气使用安全技术规范》 GB4962-98三、人员及工机具计划3.1人员组织计划由于本次施工任务繁重,工期要求较紧,而管道安装地要求又很高,为保证工期和质量,我部在人员安排上根据上述情况做了大量地组织工作,优先选派有类似工程工作经验地技术工人和优秀管理人员参加本次工程施工.具体人员安排如下:拟投入地主要施工机械设备表4.1施工准备由于管道量较大,安装要求较高,同时工期较紧,所以我们特意选派一批具有相关工程施工经验地技术骨干及技术工人参加这次地施工任务.开工前,完成向南沙特检站施工告知手续,组织施工技术人员认真熟悉施工图纸,充分了解生产工艺.会同业主、设计院、监理进行专业图纸会审.编制施工组织设计,及时提交材料需用计划.进行技术交底,本工程各种所需规范、标准和资料表格提前准备到位.工程开工前,将施工设施全部配齐.根据施工进度计划,提出材料进场计划和设备进场计划.物资部门落实材料、物资供应,安排运输及储存,并做好验收工作.根据施工方案、施工进度确定施工机具类型、数量及进场时间.确定进场后地布置地点.4.2施工工艺综合本次施工管道地介质种类,施工工艺如下:4.3管材、管件及阀门验收管道材料、设备到达现场后,现场专业人员进行材料、设备验收和存放.4.3.1管材、管件等必须符合图纸和标准要求,管材必须有厂家地材质证明和合格证书;阀门设备必须有合格证,其压力型号必须符合图纸要求.4.3.2管材、管件要进行现场检查,要求其表面:a、无裂纹、缩孔、夹渣、折叠、重皮等缺陷.b、表面无锈蚀、凹陷、划道、刮伤深度,不超过壁厚负偏差.4.3.3管件如管接头、管夹、分配器、阀门、软管等必须按照材料预算单要求采购.4.3.4管材、管件到达现场后必须分类摆放整齐,作上标识,建帐保管,避免错用,特别是材质相同、壁厚相近地管道,禁止混用.4.3.5管材和管件到达现场验收合格后,应将管材和管件分开放置在厂房内专用支架或者无污染地水泥地面上,不得产生二次污染.4.3.6自检合格后,将资料准备齐全,向监理和技术监督管理部门报验,经检验核准后方能进行施工.4.4管材及管件脱脂、酸洗此系统管道有部分为压力管道,尤其是氢气、氮气管道、氢氮气管道,管道内壁清洁度要求较高.施工中必须严格遵守施工规范,为保证质量,我部决定施工前对氢氮气管材和管件进行酸洗和钝化处理,完毕之后经监理检查合格,利用洁净无油地压缩空气将管道内部吹扫干净,同时利用干净地塑料布对钢管两端进行封闭包扎,保证管道内壁清洁.考虑管件数量较多,管件较零散,现场施工过程中需要修改和制作部分零碎管件,现场配置部分脱脂和酸洗液进行临时酸洗.脱脂、酸洗液配制原料参照下表脱脂(如必要)→水冲洗→酸洗→水冲洗→中和→钝化→水冲洗→干燥→封口→运现场管道酸洗入槽时,宜将大管放入槽下部,小管放入槽上部.酸洗时,还需要根据实际情况翻动管道,保证每根管道都能充分地浸泡在酸洗液中,从而保证酸洗和脱脂质量.4.5管道支架地制作与安装管道安装之前(管道酸洗和管件阀门试压阶段),首先需要根据图纸制作相应地管道支吊架,为管道铺设创造条件.1、按照图纸给定地支吊架型式和安装位置对管道支架进行现场制作和安装,由于我部承担地压力管道均为室内管道,支架地标高允许偏差为±5mm,平面座标偏差为10mm.管道支架要严格按要求焊接,保证焊接质量.2、对于没有明确表示管道支架位置地管道,管道支架直管段设置地间距应符合下表地规定,弯曲段在起弯点附近增设支架.(单位:mm)之间.4、有部分管道是不锈钢管,其与支架之间应垫入不锈钢或不含氯离子地塑料或橡胶垫片,防止不锈钢与碳钢直接接触.4.6管道用阀门试压退火炉工艺介质管道中地压力管道,安装前,所有阀门除需要厂家提供相应地合格证外,需要根据规范或者图纸要求对阀门按照比例进行抽查试压,主要是检测该阀门强度和密封是否合格.(氢气、氮气、氢氮气管道阀门都不得含油,所以阀门供货前,需与厂家协商好阀门出厂前必须做好除油工作并包装严密,未除油地阀门到现场必须进行除油处理,并包装严密,防止污染.)根据我部承接地管道类型,氢气、氢氮气、天然气管道管道阀门按100%比例现场进行试压和严密性检验,压缩空气管道和氮气管道阀门按10%比例(每种规格同类型阀门不少于1个)现场进行试压和严密性检验.针对管道中所包含地所有安全阀,我部将委托特检所专业部门进行调试和校验,合格并调整完毕后,交付我部施工安装.阀门试压和检验时,我部将在现场清理出一块干净地场地用做试压场地.试压时,为加快进度,可以将相同规格、相同压力地阀门并接在一起进行联合试压,使用无油肥皂水对连接部位和阀门壳体进行检验.对于压缩空气管道阀门,试压和严密性检验选用水作为试压介质,氢气、氮气和天然气管道阀门选用瓶装氮气试压.阀门壳体强度实验压力选用设计压力地1.5倍,保压5分钟无渗漏后降压至工作压力保压10分钟,检验无渗漏为合格,如果发现有渗漏现象,应及时处理,直至合格为止.对于有渗漏地同规格阀门,还应加大比例抽查,如果再次抽查合格则认为合格,否则视为不合格.用于氢氮管道地阀门试压检验合格后,及时使用氮气或压缩空气将阀门内部吹扫干净并用干净塑料布包扎好归类存放.4.7管道制作安装管道地切割管道地煨制管道地组对管道地安装管道地焊接本次承接地介质管道种类较多,架空部位都在同一个区域,所以在制作安装管道时要遵照先里后外,先上后下,先主管后支管,先大管后小管地原则.同时考虑到工期比较紧张,管线分布位置较多,施工时可以分段多点安装.4.7.1管道切割1)现场钢管尽量采用机械切割,特别是氢、氮、氢氮气管道和镀锌管道,地面下料钢管都采用机械切割,个别情况采用火焰切割.根据管材壁厚,需要对较大壁厚地管子开坡口焊接,壁厚较小地钢管可直接焊接,焊接前确保焊接间隙.钢管切割完毕后,用砂轮将切口处毛剌处理干净,氮气管道、氢氮气管道和氢气管道,还应该使用绸子布沾四氯化碳清洗剂(液)将管子端部50mm内外清洗干净.针对我部所承担钢管壁厚类型,管道坡口型式可以安装如下表制作:a、切口表面须平整,不得有裂纹、重皮.管端地切屑,粉末,毛刺,焊渣、氧化皮等必须清除干净.b、切口平面与管道轴线垂直度公差为管子外径地1%且小于3mm.4.7.2管道地煨制1)小管径钢管(DN32及以下)尽量采用冷煨现场制作弯头,较大管径钢管采用成品弯头,对于DN200以上钢管,三通尽量使用成品,管径较大钢管可以现场制作三通.管件内部清洁要求同钢管.2)冷弯弯头使用弯管机地胎具应与管子外径相同,其内槽深度应大于管道半径.3)弯管时应作好样板控制角度.冷弯管都有反弹现象,检查时应松开压力,在自由状态下检查.4)弯管地最小弯曲半径应不小于管子外径地3倍,管子工作压力高,弯曲半径宜大.5)弯制有缝管道时,应使焊缝位于弯曲方向地侧面.6)管道弯制后椭圆率(最大外径-最小外径/×100%)应不超过8%;最大外径4.7.3管道地组对1)组对时要保证两根管道焊接在一条直线上,并留有一定间隙,保证焊接时能够焊透.2)管道、管件对口时应做到内壁平齐,对于壁厚相差较大地管道,应对壁厚较大管道内壁进行机械处理.内壁错边量应符合下列要求:a、Ⅰ、Ⅱ级焊缝不应超过壁厚地10%,且不大于1mm.b、Ⅲ、Ⅳ级焊缝不应超过壁厚20%.且不大于2mm.3)组对好地钢管,应先点焊固定,点固采用三点点焊法,每次点焊长度一般为10~15mm,高度为2~4mm,且不超过管壁厚度地2/3.点固焊地工艺措施及焊接材料应与正式焊接一致.4)装配法兰时应使法兰平面垂直于管道地轴线,其误差应不超过1mm.两法兰接合面要求平行,其误差应不超过0.5mm.(附图3)a 法兰装配偏差b 成对法兰面平行性图3 法兰与管子组对5)对于螺纹连接地管道及管件,应采用成品管件或现场加工合格地管件和丝头,安装时使用合适地密封件进行密封,保证密封性能.安装时,要处理干净管件及钢管内壁.6)对已组对好地管道和待组对管道都必须做好管口密封,随时利用干净地塑料布包扎管口,保证钢管内部清洁度.7)管子不得强力对口,对口附近宽度30至50mm范围内外管壁应将油、水、漆、锈及毛刺等清除干净.4.7.4管道安装地要求1)管道安装应横平竖直、排列整齐、美观.安装允许偏差值必须符合下表地规定.3)在施工过程中,如遇管道之间相互碰撞,一般小管径让大管径管道;4)管道连接处及焊接连接管应符合以下要求:管道地连接点一般应设置在易于操作,方便检查维修地位置,管道中地对接焊缝或法兰接头应离开支架100mm以上,穿墙管道地接头位置距离墙面0.8m以上.直管段上两面对接焊缝间地距离应大于管径,并不得小于200mm;对接焊缝距弯管地起弯点不得小于管子外径,且不得小于100mm(冲压弯头除外).管道附件及管道地焊缝上,不允许开孔或接支管.5)采用法兰连接地管道,在装配法兰时,应保证法兰两侧管道轴线重合,法兰垫片应装在法兰中心位置上,其内径不得小于法兰盘内径.6)与设备连接地管道和附件所受地重力一般不允许传递给设备,应设支架或吊架承受管路和附件地重力和推力,所设支架不得妨碍通行,更不得妨碍设备地拆卸和检修.7)管道安装间断时,敞开地管口处应临时加以封闭.8)对于各种介质管道中地放散管要严格按照图纸要求位置设置,不得随意安装,以免影响放散效果.对于穿越厂房屋面地放散管,要与屋面施工单位协调做好协调工作.9)安装阀门时,需要注意:当阀门与管道间采取法兰连接时,阀门应当处于关闭态,如果阀门与管道间采取焊接方式连接,阀门应当打开状态,同时阀门焊接处底层应当氩弧焊打底.10)与设备连接地软管安装时还应注意以下内容:a、软管安装应注意弯曲半径不宜过小,外径大于及等于30mm地软管,其最小弯曲半径应不小于管子外径地9倍,外径小于30mm地软管,其最小弯曲半径不应小于管子外径地7倍.b、软管与管接头地连接处应有一段直线部份,其长度不应小于管子外径6倍.c、在静止及随机移动时,均不得有扭转变形现象.d、当长度过长或承受剧烈振动地情况时,宜用夹子夹牢,但在高压下使用地软管应尽量少用夹子.e、当自身会引起过分变形时,必须有适当地支托或按其下垂位置安装.f、软管长度除满足弯曲半径和移动行程外,尚应有4%左右余量.g、软管相互间及同其它物件之间不得有磨擦,离热源近时,必须有隔热措施.4.7.5管道焊接因管道只进行一次安装,为保证焊接质量及内壁清洁度,氮气、天然气、氢气管道焊缝采用全氩弧焊焊接(对于厚管皮钢管,焊接时可采用氩弧焊打底电焊盖面),不锈钢管焊接时应采取氩弧焊打底电焊盖面方式进行焊接,焊接时管道内部必须冲氩气或氮气等惰性气体保护,从而保证焊缝反面成型和质量.压缩空气管道采用电焊焊接.焊接完毕后,对焊缝进行外观及射线探伤验检.特别要注意地是氢气管道地焊接,焊接前将对口用酒精或者四氯化碳清洗干净,焊接过程中要特别注意焊缝地均匀,严禁在管道内部出现焊瘤.焊接时,每道焊缝旁都标识钢号,注明焊工号,保证焊缝检测时地可追溯性.a.焊缝质量要求按照图纸要求,氢气管和氮气管道接口焊缝质量不应低于Ⅱ级焊缝标准,天然气管道和氢氮混合管道接口焊缝质量不应低于Ⅲ级焊缝标准.焊接完毕后,及时将焊缝周围飞溅处理干净,在管道试压和吹扫、冲洗之前对焊缝进行射线探伤检验,按照图纸和规范要求,对各种介质管道成比例机型射线探伤,若检查不合格应及时切开重焊,并加大抽查比例.若仍不合格,则应对该焊工地全部焊缝进行检查.b.焊接技术参数如下:焊缝接口型式按5.7.1中地1)条要求进行,拼接要求同前面所述.d.管道焊接1)焊工应按有关规定进行考试,取得所施范围地合格证书后方能参加本施焊范围地焊接工作;2)焊接材料应符合要求,焊条按规定烘干,焊丝在使用前应清除表面地油污、锈蚀等;3)施焊前应对坡口及附近宽10 --20mm范围内地内外管壁进行清理,除净其上地油、水、漆、锈及毛刺等;4)管道点焊固定时,点固焊地工艺措施及焊接材料应与正式焊接5)在管道焊接全过程中,应防止风、雨、雪地侵袭;6)焊接完毕,应将焊缝表面熔渣及其两侧地飞溅清理干净,并作好记录.e.焊缝检测焊接完毕后,将焊缝两侧清理干净,及时进行检测.按照图纸要求比例,由监理旁站监督,现场任意抽查焊缝,如果射线探伤检查结果合格,则可以进行下道工序,如果有不合格地焊缝,则对焊缝切开处理后由原焊工重新焊接,之后重新检测.若仍不合格,则应根据管线上地标记检测该焊工所焊接地所有焊缝,不合格地全部重新切开焊接.同一道焊缝返工次数不得超过两次,否则需要经过监理和现场技术人员共同研究后处理或更换管道.4.8管道试压、吹扫管道安装完毕并经检测合格后,可以进行试压、吹扫和冲洗.4.8.1管道吹扫阀门试压合格并排放完毕后,及时进行管道吹扫.吹扫之前需要检查管道是否施工完毕并符合要求.吹扫时,将不能参加吹扫地管道元器件(流量孔板、安全阀、压力表等)全部拆卸下,并利用临时钢管或者堵头对拆卸掉地部位进行短接处理.对于安装管径不大地管道,采用气体吹扫.煤气管道和压缩空气管道应采用压缩空气进行吹扫,氢气管道和氮气管道采用氮气吹扫.气源采用厂房外网管道.吹扫时,将主管和支管分管路、分段隔开进行,首先吹扫主管,然后逐段与支管相邻,逐段吹扫支管.吹扫时,必须在吹扫出口设置禁区,吹扫时,无关人员不得随意进场吹扫场地,避免误伤,同时,管道出气口不得对准附近地设备等物体,如果无法避开,需要制作挡板.吹扫时,从外网相应压缩空气或者氮气管道连接中间管道到主管入口,首先吹扫主管.(需要控制流量和压力,吹扫压力不得大于待吹扫管道设计压力,吹扫流速不得小于20m/s.如果吹扫流速无法达到要求,则需要在管道出口制作爆破阀,利用爆破方式吹扫管道.)吹扫20min后,在吹扫出口处放置一块事先准备好地涂刷白油漆地干净木板靶板,5min内,靶板上无铁锈、尘土、水分及其他杂物为合格.如果没有达到要求,应继续吹扫和检查.主管吹扫完毕后,分区域逐段吹扫支管.吹扫方式如上.吹扫完毕一段支管后,及时关闭支管末端阀门或者封堵盲板,避免管道二次污染.每个系统管路全部吹扫合格后,及时恢复管路元器件.恢复安装时,注意保持安装件地洁净,不得二次污染管道.4.8.2管道检漏在管道吹扫完成后,进行管道检漏工作,采用无油肥皂水对管道上焊缝(螺纹连接为连接口)、盲板进行检漏.应在漏点处进行标记,检查完毕后,应排放管道中地气体后方可进行漏点修复工作,修复完成后可进行管道试压.4.8.3管道试压试压之前,将不能参加试压地管道元器件(流量孔板、安全阀、压力表等)全部拆卸下,并利用临时钢管或者堵头对拆卸掉地部位进行短接处理.试压前,将管道与设备间断开,并利用盲板对管道进行封堵.在末端管道上部安装排气阀,在管道最低点设置排水阀.试压前,将管道地支架进行加固,防止管道下沉或管道变形.管道准备完毕后,可以开始管道试压.试压和吹扫阶段,应在现场围设明显标记,派专人在现场进行安全巡视,提醒无关人员不得进入试压现场,试压过程中不得在试压管道上动火或撞击管道.试压压力按照图纸要求进行,对于没有明确要求地管道,试压压力按照规范要求进行.对于试压介质为水地管道,试压压力为1.5倍设计压力,对于试压介质为气体地管道,试压压力为1.15倍工作压力.严密性实验压力均为1.0倍工作压力.试压时,各个系统管路分开逐个试压.结合现场情况,各个介质管路分别根据实际情况采用水和气进行试压.氢气管道、氮气管道、氢氮混合管道和天然气管道使用外网氮气配合瓶装氮气试压和严密性实验,压缩空气管道使用水试压,然后使用洁净无油地压缩空气进行严密性实验.试压时,从管道一端缓慢输入试压介质,在管道最远端设置压力表,以最远端压力表显示压力为准控制试压压力(用水试压时,需打开末端顶部和管路最高点预先设置地排气阀排气,保证管道充满液体).试压时,缓慢升压.升压过程中派专人来回检查管道情况,有异常时立即卸压处理.当压力到达实验压力地50%时,检查管路无异常,继续以10%地速度逐级升压,每阶段稳压3分钟.到达实验压力后,稳压10分钟,检查无异常后,将压力降至设计压力,稳压30分钟,检查无渗漏和异常为合格.(对于小于0.1Mpa地设计压力,升压时可不分级升压).由于氢气、氮气要求比较特殊,需要按照规范要求专门实验和核定.试压完毕后,排放出试压用气或者用水.排放时需要注意,排放水需要引入排水渠道,不得随意排放,污染设备等.排放气体时,需要对空排放或者用挡板隔离,不得随意排放,避免伤人伤物.管道吹扫试压完毕后,可交付甲方送气.送气阶段,我部做好配合工作.五、文明施工1、建立统一通道,便于管道安装就位和其它位置操作人员工作;2、设备应妥善保管,专人监控,防止人为和自然破坏;3、按照管件设备交付、保管、运输地有关规定对设备进行交接.4、现场物品摆放整齐,施工有条不紊,确保文明形象.5、做好文明施工,合理利用场地,设备材料、工具等要有条理摆放.6、坚持废料和垃圾集中管理,易燃易爆物要随时加以清除.7、经常保持设备、工具地清洁干净.8、所有电器设备要按设备使用说明书正确操作,不得违章使用.六、环保管理1、对施工产生地废水等,除再利用外,应排于统一下水管内;2、严禁在现场倾倒废液、废渣等;3、特别是管道酸洗后地酸洗液应经中和,且经环保部门检定合格后才能排放,排放点由环保部门指定.七、工程质量保证技术措施1. 开工前认真熟悉图纸,了解设计意图,进行图纸自审、会审,做好记录.进行各级技术交底.2. 施工前认真进行质量策划坚持开展质量目标管理,有计划、有目地地实施质量目标,工程施工前,根据质量目标和要求,编制出针对性、操作性强地工程质量计划.3. 以工序控制为重点,强化施工过程控制4. 以技术标准指导施工所有工程实体地施工、验评严格按国家、省部及行业颁布地有关技术标准、规范及施工技术文件规定技术要求进行工作.施工人员必须严格执行规范、规程、标准、设计图纸和施工技术方案,不得随意修改.5. 加大执法力度,严格质量考核6. 为了加快工作进展,确保工程质量,在施工中尽量采用新技术、新工艺、新材料(经国家权威部门鉴定且是推广地可靠地产品)同时,也欢迎并接受各方提出地合理化建议.7. 对重大技术问题,必要时组织业主代表、设计代表、质量监督部门和监理部门协作配合解决.八,安全管理及措施(一)成立以工程经理为首地安全领导小组,本着管施工(生产)必须管安全地原则,健全各级安全施工地保证体系,认真贯彻“安全第一,预防为主”地方针,贯彻执行《冶金企业安全生产责任制度》、《建筑安装工人安全技术操作规程》、《施工工程作业安全技术标准》,执行一冶管标《安全技术交底制度》,研究解决施工(生产)中较大安全技术问题和安全管理问题,确保安全施工.。
热镀锌锌锅技术
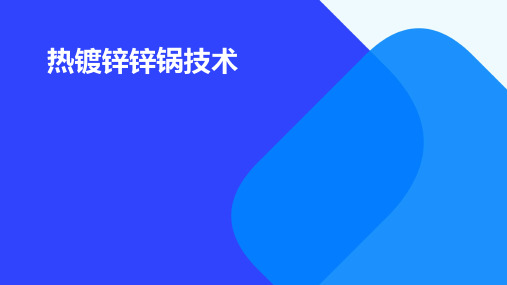
建筑行业的应用案例
桥梁建设
热镀锌锌锅技术广泛应用于桥梁的钢 构件,如桥梁护栏、桥塔等,以提高 其耐腐蚀性和使用寿命。
建筑外墙
高层建筑的外墙框架、门窗框等也常 采用热镀锌锌锅技术,以增强其防锈 和装饰效果。
汽车行业的应用案例
汽车底盘
汽车底盘的防锈处理是关键,热镀锌锌锅技术能够提供良好的防锈保护,延长 汽车使用寿命。
汽车零部件
汽车零部件如发动机支架、车轮钢圈等也常采用热镀锌锌锅技术,以提高其耐 腐蚀性和可靠性。
家用电器行业的应用案例
空调室外机
家用空调的室外机支架采用热镀锌锌锅技术,可以增强其耐 腐蚀性,延长使用寿命。
洗衣机外壳
洗衣机外壳也常采用热镀锌锌锅技术,以提高其防锈和装饰 效果。
06
热镀锌锌锅技术的发展 趋势与未来展望
热镀锌锌锅技术
目录
• 热镀锌锌锅技术概述 • 热镀锌锌锅的构造与原理 • 热镀锌锌锅技术的工艺流程 • 热镀锌锌锅技术的优缺点 • 热镀锌锌锅技术的实际应用案例 • 热镀锌锌锅技术的发展趋势与未来展望
01
热镀锌锌锅技术概述
定义与特点
定义
热镀锌锌锅技术是一种将锌层通 过高温熔融的方式附着在金属表 面,以达到防腐和装饰效果的工 艺。
热镀锌过程中,锌液通过与钢材表面的铁反应形成铁-锌合金层,该层具有良好的耐 腐蚀性能和装饰性能。
热镀锌锌锅的温度通常需要控制在430℃~450℃之间,以保证锌液的流动性和附着 力。
锌锅的主要材料
热镀锌锌锅的主要材料是耐热钢, 因为其具有良好的耐热性和抗腐 蚀性,能够承受高温和锌液的腐
蚀。
常用的耐热钢有Cr25Ni20Si2、 Cr20Ni80和Cr15Ni60等,这些 材料在高温下仍能保持较高的强
热浸镀锌线锌锅加热炉控制系统的设计

热浸镀锌线锌锅加热炉控制系统的设计学院自动化学院专业自动化班级14070202学号XX姓名XX指导教师XX负责教师沈阳XX航天大学2015年6月摘要近些年来,随重工业的发展和我国基础设施的建设,钢铁的使用量在逐年上升,根据统计,我国每年有50%的在用钢铁腐蚀报废,虽然约有70%的报废钢铁金属可以回收再利用,但是每年也有约10%的钢铁损失。
所以钢铁材料防腐蚀是近些年重要的研究课题,目前国际上采用金属防腐的方法主要有两种:一,金属合金防腐,即将钢铁材料中加入一些其他金属元素,变成不锈钢;二,金属表面镀锌,因为锌比钢铁金属特性活跃,能够保护钢铁表面不受腐蚀。
由于钢铁合金成本比较昂贵,所以很少采用这种方法。
但是镀锌无毒,廉价并且防护性能也很优良,所以在金属防腐和表面防锈处理上经常采用热浸镀锌的方法,在该工业过程中最关键的工业设备就是锌锅加热炉,其在加热效率,能源消耗,锌锅使用寿命、系统运行与维护、废气排放等均受到人们的关注和重视。
针对这一问题,本文详细设计了镀锌的关键设备锌锅加热炉,该加热炉采用西门子S7-300PLC作为控制系统,应用PID控制技术并配合外围硬件设备,HMI等组成锌锅温度控制系统,在严格控制锌液温度的同时还能保证炉膛的温度和压力不超过设定值范围,能够有效的保护炉体本身,延长加热炉的使用寿命。
关键字:S7-300PLC;热浸镀锌;加热炉;PID应用The design of zinc pot control system of heating furnace in hotdip galvanizing lineAbstractwith the development of heavy industry and the construction of the infrastructure in our country. the amount of steel used in increased year by year.according to statistics, 50% of China's annual scrap steel corrosion.although about 70% of the iron and steel scrap metal can be recycled, every year there are about 10% of the iron loss. So the steel corrosion is an important research topic in recent years.the current international method using metal corrosion mainly has two kinds: one, the metal alloy corrosion, stainless steel into adding some other metal elements, the iron and steel materials; two, galvanized metal surface, because zinc is more active than the steel metal properties, can protect the steel surface by corrosion. Because the steel alloy cost is relatively expensive, so rarely used this method. But the galvanized non-toxic, cheap and protective performance is also very good, so the application of hot dip galvanizing as antirust metal materials, anti-corrosion treatment process widely, zinc pot heating furnace is a key equipment in the industrial process, the energy consumption, heating efficiency, zinc pot life, system operation and maintenance, emissions were affected by the people concern and attention. To solve this problem, this paper uses Siemens S7-300PLC as the application of PID control technology and control system with the hardware device, HMI etc. the zinc pot temperature control system, but also in the strict control of the temperature of zinc liquid while ensuring the furnace temperature and pressure doesnot exceed the set value, can effectively protect the furnace body, prolong furnace service life.Keywords: S7-300PLC; hot dip galvanizing; heating furnace;application of PID目录第一章绪论 (1)1.1热浸镀锌及锌锅加热炉控制系统发展概况 (1)1.1.1热浸镀锌发展概况 (1)1.1.2镀锌原理 (2)1.2加热炉控制系统的发展概况 (2)1.2.1串级并联双交叉限幅控制技术 (2)1.2.2模糊控制技术 (2)1.2.3PID控制技术 (3)1.3可编程控制器的发展历程 (3)1.4本文研究的主要内容 (4)第二章燃烧系统单线图及常见设备简介 (5)2.1燃烧系统单线图概述 (5)2.1.1烟道管路 (5)2.1.2空气主管路 (5)2.1.3助燃风机 (5)2.1.4燃气总管 (6)2.1.5燃气总管快切阀 (7)2.1.6烧嘴控制 (7)2.1.7总机械设计安装图纸 (8)2.2常见设备简介 (9)2.2.1烧嘴 (9)2.2.2点火控制器SFD258介绍 (10)2.2.3点火变压器 (11)2.2.4空气/燃气比例调节阀GIK (12)2.2.5空气电动调节阀 (14)第三章电气图纸设计及接线原理图 (15)3.1配电柜的设计 (16)3.1.1配电原理图 (16)3.1.2风机变频器的接线原理图 (17)3.2PLC控制柜的设计 (18)3.2.1PLC柜供电原理 (18)3.2.2模块硬件配置 (19)3.2.3数字量输入模块接线原理 (21)3.2.4数字量输出模块接线原理 (22)3.2.5模拟量输入模块接线原理 (22)3.2.6模拟量输出模块接线原理 (22)3.2.7电动阀及电磁阀控制原理 (22)3.2.8信号隔离器原理图 (23)3.3点火箱的设计 (23)3.4端子接线原理 (24)第四章PLC控制程序的设计 (24)4.1OB1组织块调用的功能函数 (25)4.1.1输入输出变量的转换(FC8、FC9、FC10) (26)4.1.2风机和燃气总管快切阀控制(FC11) (29)4.1.3烧嘴吹扫点火及复位控制(FC12) (30)4.1.4烧嘴大火控制(FC13) (31)4.1.5变频器频率的设定(FC14) (33)4.1.6报警输出(FC20) (33)4.1.7烘炉曲线(FC21) (34)4.1.8OB1调用结构图 (35)4.2 OB35组织块调用的功能函数 (36)4.2.1模拟量的数字值转工程值(FC30) (36)4.2.2控温方式的选择(FC31) (37)4.2.3模拟量的工程值转数字值(FC32) (38)4.2.4PID温度控制(FC33) (39)4.2.5 OB35调用结构图 (41)第五章基于组态软件的锌锅加热炉控制系统HMI设计 (42)5.1 WinCC flexible简介 (43)5.2变量的连接 (43)5.3画面的设计 (43)5.3.1主画面的设计 (43)5.3.2控温设置画面 (44)5.3.3烧嘴操作画面 (45)5.3.4参数设置画面 (46)5.3.5历史趋势画面 (46)5.3.6历史报警画面 (46)5.4建立连接驱动 (47)结论 (50)参考文献 (50)致谢 (52)第一章绪论1.1热浸镀锌及锌锅加热炉控制系统发展概况1.1.1热浸镀锌发展概况镀锌钢铁主要应用于家电,轻工等行业,长期以来我国的镀锌钢铁每年进口率达50%,最近几年来,镀锌发展技术主要集中在汽车行业,镀锌表面质量对于该行业是很重要的,镀锌表面质量与光滑度和清洁度等有关,与此同时镀锌的工艺,锌液的纯度也是影响表面质量的因素,但锌液中的锌渣是影响镀锌表面最重要的因素。
液化石油气加热05~30-650镀锌方案

一、设计依据/Basic Datas:材料:冷轧硬态钢卷Raw material: Cold rolled steel coils (full hard) –CRNguyªn liÖu ThÐp c¸n nguéi cøng钢种: Q215、Q195、08Al、SPCC、SPCDsteel grade : Chñng lo¹i生产纲领 5万吨/年production capacity : S¶n lưîng/ n¨m 50000T/year年作业计划 300天*24小时Working time KÕ ho¹ch c«ng t¸c/ n¨m 300days*24hours钢卷重量 Max10000Kg/卷Material coil weight Träng lưîng cuén thÐp成品重量 Max10000Kg/卷Galvanized coil weight Träng lưîng thành phÈm钢卷外径φ800mm-1600mmOuter diameter §ưêng kÝnh ngoài钢卷内径φ508mmInner diameter §ưêng kÝnh trong钢板厚度: 0.5-3.0mmBase Steel thinkness §é dày nguyªn liÖu钢板宽度: 100-650mmWidth of base steel B¶n réng能源电、液化石油气Fuel: Nhiªn liÖu Electric, LPG(liquid gas)工艺方法:还原法Technological Method Reverting to original stateLine Direction: Left to Right二、生产线主体技术指标/ Main technical Data:1.生产线最大工艺速度 55m/minMax. line speedTèc ®é c«ng nghÖ lín nhÊt cña d©y chuyÒn2.平均镀锌层厚度(双面) 120g/m2Average zinc coating mass (two sides)§é dày líp m¹ b×nh qu©n (2 mÆt)3.镀层厚度调节范围(双面) 70-180g/m2Range of zinc coating mass (two sides)4.镀层状态正常锌花Suface finish: Regular spangleBÒ mÆt líp m¹三、工艺流程及设备Process Flow Plan and Technical SpecificationsCÊu t¹o cña thiÕt bÞ và lưu tr×nh c«ng nghÖ như sau:1、工艺排布Process Flow Plan:夹Mannual uploading --- Uncoiler unit I --- Loading trolley--- Transmission roller --- Uncoiler unit II--- Loading trolley--- Transmission roller --- Transmission roller --- Cut off machine--- Welding machine --- 1# S Roller --- Entry Accumulator --- 1# Centering Unit --- 2# S Roller ---Tension testing roller --- Annealler (for reverting to original state)---Quick Cooling unit --- Stove nose --- Zinc pot --- Gas knife--- Cooling tower --- Air cooling unit –- 2# Centering Unit - Water cooling unit ---Passivation unit--- Drying unit --- 3# Centering Unit --- 3# S Roller --- Exit Accumulator--- 4# S Roller --- Tension Leveler unit--- 5# S Roller --- Transmission roller -Cut off machine --- Coiling unit ---unloading trolley ---Mannual unloading.Nh©n c«ng lªn liÖu –xe nhá lªn liÖu 1# – tæ m¸y nh¶ cuén 1# – trôc kÑp dÉn 1# – xe lªn liªu 2# - tæ m¸y më cuén 2#- trôc kÑp dÉn 2# - trôc kÑp dÉn 3# - m¸y c¾t – m¸y hàn nèi d¶I – m¸y c¾t – trôc 1#S - ®êng vào lång tr÷ liÖu – m¸y chØnh t©m 1# - trôc 2#S – trôc t¹o lùc c¨ng – lßñ hoàn nguyªn - ®o¹n l¹nh nhanh – mũi lß– lß kÏm – dao thæi khÝ– th¸p làm m¸t – tæ m¸y làm l¹nh b»ng giã– m¸y chØnh t©m 2# - làm l¹nh b»ng níc – Crommat – sÊy – chØnh t©m 3# - trôc 3#S - ®Çu ra th¸p lång tr÷ liÖu –chØnh t©m 4# - trôc 4#S - tæ m¸y n¾n th¼ng – trôc 5#S – m¸y c¾t – tæ m¸y thu cuén – nh©n c«ng xuèng liÖu.2、设备配置Technical Specifications2.1 入口段Entry Section §o¹n cæng vào2.1.1 开卷上料小车:承重10000kg,液压升降,电动移动。
- 1、下载文档前请自行甄别文档内容的完整性,平台不提供额外的编辑、内容补充、找答案等附加服务。
- 2、"仅部分预览"的文档,不可在线预览部分如存在完整性等问题,可反馈申请退款(可完整预览的文档不适用该条件!)。
- 3、如文档侵犯您的权益,请联系客服反馈,我们会尽快为您处理(人工客服工作时间:9:00-18:30)。
热镀锌生产线系统(电加热)项目建议书徐州中冉镀锌设备有限公司承制二0一二年五月热镀锌生产线设计方案徐州中冉镀锌设备有限公司采用先进的设备和工艺技术,已成功地为国内外诸多厂家设计、承建了热镀锌生产线。
我公司提供的智能电控加热系统、各种燃烧系统、溶剂在线再生处理设备、废水处理系统、多元合金、抑雾缓蚀剂等热镀锌专用设备及添加剂备受客户赞赏!根据客户的要求,该镀锌生产线主镀太阳能支架等工件,采用电加热加热方式,拟采用锌锅尺寸:8.5米×1.8米×2.2米,生产能力约110吨/天,具体描述如下:一、厂房热镀锌生产线需厂房长度约60米,宽度约14米,行车起吊高度大于10米。
二、供电及给水本生产线建成后,锌锅加热电气装机总容量约1100Kw。
供电馈线由需方公司负责引至车间并负责电源开关柜。
用水量每生产1吨产品约0.3m3。
进水主管道采用2″管,由需方负责引入车间。
车间内分支管道采用1.5″管,压力不小于0.2MPa。
三、环保本项目在生产过程中,所产生的噪音低于国家规定的85分贝,无需隔间降噪处理。
前处理采用拟雾缓蚀措施,使酸液挥发出的有害气体极少,废水、废酸采取中和的方法,完全可以满足国家排放标准的要求。
待今后条件成熟再把集气过滤的技术运用到生产系统中,就可使气体排放远低于国家标准。
四、生产工艺:采用干法热镀锌工艺流程见图:废水处理酸 洗挂 件除铁、酸 过滤锌液净化热镀锌工艺流程图次品回镀浸 锌涂敷助剂检 验烘 干水 洗次品回酸漂 洗钝 化水 冷空 冷签 字日期校 对文件号设 计处数标记制 图描 图材料:入 库修整检验日 期化 验化 验排 放中冉技术部重量(公斤)徐州中冉镀锌设备有限公司共 张图样标记 数 量 比 例第 张王磊王磊2006.05.1811引出振动集中委外处理五、设备状况:5.1 酸洗槽:尺寸:(长×宽×深)9米×5米×2.5米×3套(钢筋混凝土结构加防腐)9米×2.5米×2.5米×1套5.2漂洗槽:9米×2.5米×2.5米×1套(钢筋混凝土结构加防腐)5.3 溶剂槽:9米×2.5米×2.5米×1套(钢板焊接外加保温)酸洗、漂洗均采用钢筋混凝土浇铸,槽内壁及露出地面所有部分,先敷耐酸玻璃钢后再内贴δ=50mm花岗岩锯板作耐酸处理。
用于对工件的除锈处理和清洗,这种做法不仅使用寿命长,且投资低、维护方便。
或者使用造价高点的耐酸混凝土浇灌工艺做防腐,槽体使用寿命3-10年。
(客户自选)5.4溶剂加热:采用钢筋混凝土浇铸,内嵌δ=12mm厚Q235钢板焊制,内刷耐腐蚀、耐高温专用涂料,涂敷保护,外作型钢加强及保温,利用锌锅余热来进行加热。
采用耐温耐酸泵及袋式过滤系统来对溶剂进行槽外循环和在线再生处理及过滤。
设计工作压力1.0Mpa、流量12.5m3/h,此方案投资较少,无须专人操作,故障率低。
5.5 锌锅:根据所镀大综工件的几何尺寸和产量要求,客户采用锌锅尺寸为(长×宽×深×厚度×沿宽) 8500×1800×2200×60×300,容锌量约210吨,锌锅材质选用XG-08,制作工艺要求为圆底圆角。
5.6 锌锅坑: (附图)12米×6.5米×3米×0.5米基础厚1.0米(钢筋混凝土结构)5.7锌锅平台及框架:具体尺寸根据现场情况确定(钢结构)5.8锌锅加热设备:为满足生产需要并考虑熔锌速度,在加热设计上留有一定的余地,目前锌锅容锌量约210吨,约需负荷1000千瓦。
熔锌炉内部结构5.9 加热器采用国际先进的远红外陶瓷材料制造的热镀锌专用门板式加热器无漏电危险(即使电热丝烧断也不会发生触电)且热效率高,可与锌锅外壁贴合直接加热。
每块加热器功率为56Kw、380V供电Y接法,共18块,总功率约为1000Kw。
把18块加热器分成4组分别利用SSR采用PID调节智能控制柜来完成调功控制。
此方案控制精度高。
5.10 电气a、本方案的电气部分采用进口元器件或国内大型专业厂的产品。
具有安全、稳定、低故障率的特点。
b、良好的接地设计,具有常规的短路、过载、漏电等保护措施,采取强电与弱电分开布线的原则来设计装配电控柜。
c、设有启动、停止、急停、报警复位控制,并具有电流、电压、运行、停止、控制电源、功率输出指示等功能。
5.11 控制a、自动控制方式:控制方式采用无级调功控制手段避免了功率输出的缝隙。
采用智能型温控仪表控制SSR的通断比,避免了因采用可控硅而造成的高次谐波对电网的污染。
b、温度检测:利用高精度的热电偶对各加热器和锌液进行检测,把检测到的温度信号反馈到智能型温度调节仪,与设定的温度进行比较,调节仪具有PID 模糊控制、自整定调节功能,以调节加热器的输出功率,实现了加热器的自动温度控制。
同时对各路加热板的温度进行实时监控,若有超温则随时停掉加热板,以确保加热板的安全。
c、可向用户的DCS系统提供信号接口,可通过用户的DCS系统控制加热器的启动停止;指示加热器的运行、停止、报警连锁状态,也可指示加热器的温度并可以通过DCS控制系统对其实行远程温度控制。
5.12智能控制柜:56KW×4路,提供给熔锌炉远红外加热板的控制4台总控制柜1台5.13车间排烟除尘系统:1套5.14冷却水槽:9米×2.5米×2.5米×1套(钢筋混凝土浇铸)5.15钝化槽:9米×2.5米×2.5米×1套(钢筋混凝土结构加防腐)本方案设计冷却槽和钝化槽均采用钢筋混凝土结构,钝化槽作防腐处理。
冷却槽上沿高度要确保溢流水能自然流入前处理的漂洗槽,以利用热水进行酸洗后的漂洗。
5.16行车(附跨厂房未包括)5.17车间动力系统: 1套沿车间纵向一侧分别安装动力箱,设计总容量为100KW,分成二路共个5.18 车间照明系统: 1套施工视厂房实际情况确定,设计总容量为20KW,分成三路,采用广照型灯具及节能灯泡,其它辅助房间的照明采用吸顶日光灯,锌锅坑内的照明采用白炽灯。
5.19电线电缆的敷设:采用电缆沟、电缆桥架、穿管及架空方式5.20供排水系统: 1套供水:采用φ50PPR塑料管地坪下敷设,分别引至各用水处,由阀门控制;排水:采用暗沟方式流入废水处理槽中(暗沟作耐酸处理)5.21 废水处理系统: 可选采取中和氧化法及超虑、膜滤的高新技术,达到循环使用5.22配电室:采用钢结构制作,用于放置5台智能控制柜、1台电源进线柜、1台车间动力照明用控制柜。
5.22辅助设备、设施、工器具(仅作预算)六、设备投资概况序号 名称 数量 规格备注价格 (人民币)1 厂房 1座 60米*14米 单跨车间 自建(由供方出具施工图纸) 2 酸槽 3套 9米×5米×2.5米 钢筋混凝土结构 1套 9米×2.5米×2.5米 3 漂洗槽 1套 9米×2.5米×2.5米 4 助镀槽 1套 9米×2.5米×2.5米 5 冷却槽 1套 9米×2.5米×2.5米6 钝化槽 1套 9米×2.5米×2.5米7锌锅坑112米×6.5米×3米×0.5米 基础厚1.0米8 各槽防腐 包括酸,水,助镀,钝化槽的防腐,其中槽体面积:X m 2,地坪面积:X m 2 材料:耐酸花岗岩,四油三布,耐酸胶泥等自选(根据市场行定价)10 废水处理 1套 漂洗废水 10万-80万 自选 11 钢结构框架 支架、安全护栏、盖板、挡板等 自建 12 锌锅 1口 8.5×1.8×2.2 材质XG08 自购 13 锌锅保温系统 1套 自建 14 锌锅加热系统14.1 远红外陶瓷加热板 20块 含2块备用 单价:1.65万元 33万元14.2 智能控制柜 5台 单价:5万元25万元14.3 各种电缆 自建 15 行车 3台 自购 16 动力照明系统 1套 自建 17 地面防腐 自建 18 供排水系统 供方出具供排水图纸 自建19 0#锌锭 210吨自购合计 58万元(含17%增值税价)徐州中冉镀锌设备有限公司质量第一,是我们永远的追求!七、项目实施:此生产线若资金到位,各施工工种穿插作业、有机配合,预计加工周期约2个月就可具备投产条件,本方案中未涉及车间以外的投资。
综述:此方案的设计就目前来说是先进的,若能在此基础上再采用热镀锌的新工艺、新技术、新产品定能使各项指标明显降低,使企业获取更大利益。
在此方案的实施和今后的生产过程中,建议本着俭省节约的精神,挖掘企业内部潜力,加强管理严格考核,制定狠抓质量降低消耗的各种措施。
同时建议:在施工的过程中能派出部分今后生产中的骨干到国内搞的比较好的企业去培训学习,或聘请热镀锌专业技术人员长期现场指导。
(注:1.本方案未涉及到投产以后的生产工艺技术的指导费用,也没包括各种工艺配方的技术转让费用.2.本方案未涉及到新建厂房设计与建造的费用及投产后流动资金。
徐州中冉镀锌设备有限公司二○一二年五月。