煤磨动态选粉机使用说明
FM32X6+3风扫煤磨机使用说明书
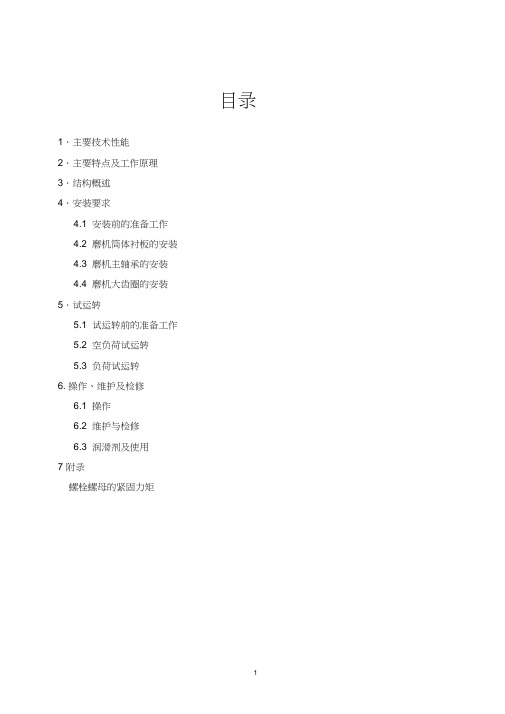
目录1.主要技术性能2.主要特点及工作原理3.结构概述4.安装要求4.1 安装前的准备工作4.2 磨机筒体衬板的安装4.3 磨机主轴承的安装4.4 磨机大齿圈的安装5.试运转5.1 试运转前的准备工作5.2 空负荷试运转5.3 负荷试运转6. 操作、维护及检修6.1 操作6.2 维护与检修6.3 润滑剂及使用7 附录螺栓螺母的紧固力矩1.主要技术性能1.1 规格:© 3.2X( 6+3) m磨机筒体有效内径1仓3120mm2仓3070mm 磨机筒体有效长度1仓3000mm2仓6000mm 1.2 用途:烘干兼粉磨无烟煤1.3 生产能力:24t/h1.4出磨成品细度:80卩m,筛余12%1.5入磨物料粒度(mm): < 25, (95%通过) 1.6入磨物料水份:w 10%1.7煤磨水份:w 1%1.8入磨气体温度:300C( Max400C)1.9出磨气体温度:60〜80E1.10 磨机转速( r/min ):17.81.11 研磨体装载量(t): -46t(max)1.12 填充率: 23.5%1.13 主轴承最大用水量: 2m 3/h1.14 主传动电动机型号:YRKK560-6额定功率: 710kw同步转速: 988r/min额定电压: 6000V1.16 主传动减速机型号: MBY710公称传动比: 7.1额定功率: 710kw输入转速: 988r/min1.17 辅助传动电动机型号: YEJ200L1-6额定功率: 18.5kw满载转速: 970r/min额定电压: 380V1.18 辅助传动减速机型号:ZSY280- I额定功率: 18.5KW公称传动比:100输入转速:970r/min盘磨转速:0.17r/min1.19 主轴承润滑系统型号:GYXZ-25A(两套)高压泵:电动机:型号:Y112M-6功率: 2.2KW公称流量: 2.5L/min公称压力:32Mpa电加热器:型号:SRY2-220/3 功率:3X 3kW 220V冷却水用量: 3.0 m 3/h1.20所有冷却水水温w 28C,水压在0.3〜0.5Mpa之间,水质为“软水”。
煤磨操作说明书

东方红水泥有限责任公司质量管理体系管理文件作业指导书煤磨中控操作说明书编号:版本:发布日期: 2009年月日实施日期: 2009年月日目录1总则2职责权限3操作说明3.1控制回路3.2工艺流程简介4开车前的准备5开、停车顺序6操作参数的调整7常见故障及处理8交接班制度9附设备分组表、规格表1总则1.1本说明书仅适用于东方红水泥厂煤磨系统中控操作岗位。
1.2执行东方红水泥有限责任公司的有关规章制度。
2职责权限2.1接受生产值班经理的指挥,负责煤粉制备系统生产的正常运行所管辖设备的安全;同时负责对煤磨岗位的巡检工的工作和安全的管理。
2.2根据工艺部下达的操作参数标准和质量部下达的质量控制标准控制煤磨系统的操作;确保参数稳定、准确,产品的产量、质量符合公司的要求,从而完成各种经济技术指标。
2.3严格按作业指导书操作,并对过程参数和产品质量及时记录,确保操作规范、记录真实。
2.4负责煤粉制备系统、煤粉输送系统以及所有收尘系统的正常运行,根据情况指挥相关人员对设备进行巡检及维护,确保设备运行正常。
2.5严格按操作规程操作,确保本系统无安全事故发生、并负责对下属进行专业知识培训和安全教育。
2.6负责本系统的卫生和环保,按”5S”要求做好本岗位的工作。
2.7检修期间,指挥、协调本系统人员配合机电维修人员搞好设备检修工作,并参加试车和验收。
3操作说明3.1控制回路3.1.1阀门(2713a)的开度。
通过煤磨出口气体负压来自动调节阀门(2713a)的开度,达到稳定煤磨出口气体负压。
3.1.2定量皮带称(2704、2705、2706)的喂料量。
通过煤磨进出口的压差来自动调节定量皮带称(2704、2705、2706)的喂料量,达到稳定磨内压差。
3.1.3阀门(2618) 的开度。
通过煤磨出口温度来自动调节阀门(2618) 的开度,达到稳定出磨温度。
3.2工艺流程简介3.2.1煤磨工艺流程原煤由汽车运输进厂卸入露天堆场,通过铲车铲入料仓,经板喂机(1201)入环锤式破碎机(1202),破碎后由胶带输送机(1203)、移动堆料机(1602),以连续合成方式堆入原煤圆形预均化堆场。
莱歇分离器-LSKS系列选粉机操作说明书
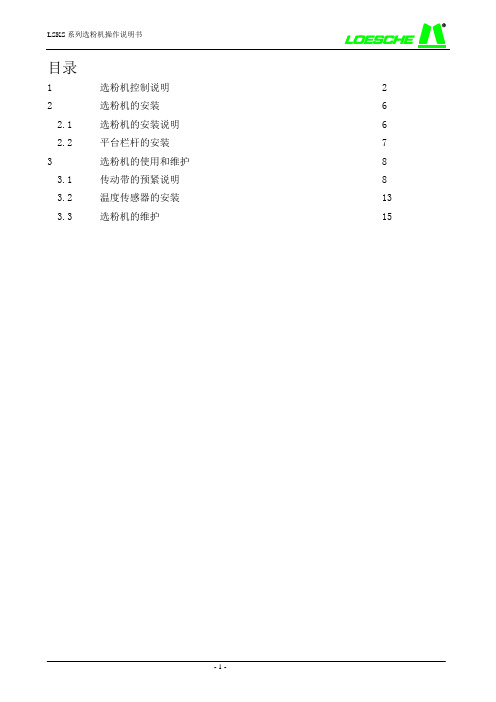
目录1 选粉机控制说明 22 选粉机的安装 6 2.1 选粉机的安装说明 62.2 平台栏杆的安装 73 选粉机的使用和维护 8 3.1 传动带的预紧说明 8 3.2 温度传感器的安装 133.3 选粉机的维护 151. 选粉机的控制说明1.1. 目的莱歇动态选粉机设计用于与磨机协同工作以期获得最佳的颗粒粒度分布,在获得合理的细度特别是减少颗粒分布曲线的粗颗粒端方面已经证实对于煤磨的产量和操作性产生的影响最小。
另外动态选粉机的应用明显地减小了磨机的震动水平。
动态选粉机的使用将帮助弥补燃烧效率低的缺陷,可以通过测量未燃尽炭的水平来衡量。
1.2介绍目前电厂现有大部分煤磨配备静态分离器并且改进这些分离器本身对选粉性能的进一步提升非常有限。
更好的方案是用动态选粉机代替静态分离器,最新一代的动态选粉机证明它是改善煤粉细度的最好方案,且有潜力消除几乎从PF到锅炉所有>300µm粗颗粒。
采用动态选粉机导致NOx产生减少,因为它们可以使锅炉运行在低氧环境。
1.3. 主要部件1.3.1主要设备主要设备包含:✧动态选粉机。
✧动态选粉驱动系统、选粉机电机等。
✧变频器。
✧密封空气系统、密封空气风机、密封风机电机等。
✧选粉机润滑系统、油脂泵、油脂泵电机等。
详细的供货范围见合同要求。
1.3.2计量计量主要指:✧选粉机电机工作时间计量(客户备)。
✧选粉机电机功率计量(客户备)。
✧选粉机变频器界面信号。
✧选粉机密封空气系统、密封空气系统压差等。
详细的供货范围见合同要求。
1.3.3控制单元关于控制的详细信息请查阅设备控制描述。
详细的供货范围见合同要求。
1.4. 系统描述动态分选粉机被设计可以直接安装在煤磨上。
选粉机配有中心管及PF出口法兰与PF分配管路相连,分离器设计可以根据客户要求与新设备连接及检测相容。
莱歇动静态高效选粉机 (LSKS) 是一种可控离心式选粉机,设计耐压能力为3.5bar(表压)。
原煤经磨辊碾压粉磨烘干后随气流输送到LSKS分离器。
新疆博东MD1800AY说明书
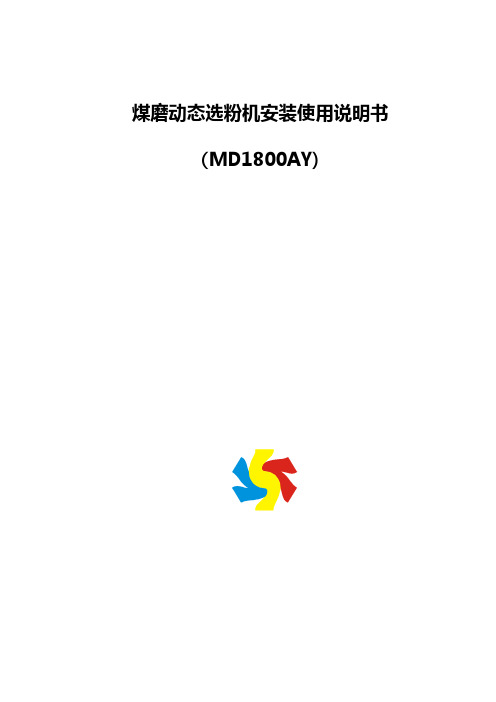
煤磨动态选粉机安装使用说明书(MD1800AY)绵阳西金科技发展有限公司MianYang Seeker Science&Technology Development Co.Ltd.1、用途2、主要技术参数3、结构及工作原理4、安装与试运转5、操作、维护及检修6、备件清单7、注意事项1、用途本煤磨动态选粉机主要适用于煤粉制造过程中的煤粉的分级。
2、主要技术参数转速 100~264 r/min空气量 95000~125000m3/h转子直径φ2100mm产量 43~52t/h(R80μm筛余2%-5%)电机型号 YPT280S-4功率 75KW减速器型号 MC2VSF04速比 5.6稀油站型号 XYZ-10G3、结构及工作原理3.1结构本高效选粉机主要有传动装置、回转体、壳体部分、重锤翻板阀、润滑系统组成。
结构如图(一)3.1.1传动装置由卧式电机、直交轴齿轮减速器及联轴器等组成,电机通过弹性联轴器水平安装在减速器中心平面上,整个传动装置安置在传动支架上。
减速器的润滑采用浸油润滑。
传动装置如图(二)3.1.2回转体回转体由卧式电机通过卧式减速器直接驱动,为了轴承的密封和防止立轴的磨损,在主轴外设有主轴套,并在主轴套外表面粘接耐磨瓷砖。
为了保证工作的平稳性,回转体已经进行动平衡试验。
回转体如图(三)3.1.3壳体壳体是由钢板和型钢组焊的焊接件。
壳体上设计了检修门,以便维护和检修。
壳体内部在圆周方向装有均匀间隔的导流叶片,使选粉空气均匀地进入选粉室,导流叶片采用耐磨钢板。
壳体如图(四)密封套3.1.4润滑系统本系统采用46#机械润滑油进行润滑,设有稀油站TBJ-16,向主轴的轴承供润滑油,对主轴轴承进行润滑。
稀油站数据表15 过滤器面积M216 油箱容积630L17 工作介质46#机械润滑油18 润滑站重量120 Kg 图(五)润滑管路图3.2工作原理粉磨后的物料随磨内气体,从壳体下部进风口进入壳体,在沿壳体上升过程中,由于气流速度的减慢,大量的粗粉沉积下来,由壳体排料口排出。
煤磨现场操作规程1

Xx水泥有限公司部门标准煤磨现场操作规程1 范围本规程适用于煤磨系统现场设备巡检操作,即从煤取料机至煤粉仓所有设备。
2 目的本规程意在规范巡检制度,提高工作质量和工作效率,以“安全第一”为原则,指导职员有条不紊地进行生产巡检操作。
3 开机前的准备为了确保本系统设备的安全运行,避免人身和设备事故的发生,在每次开机前,都应对本系统的全部设备与管道进行认真、全面的检查。
要对煤粉取料系统、压缩空气、冷却水供应、燃料储存、原煤仓料位、煤粉仓、定量给料机、喂煤秤、袋收尘等情况逐一检查,并确认灭火系统随时可以投入使用,与中控操作员密切配合,共同完成开机前的协调准备工作。
4 桥式刮板取料机巡检规程4.1设备参数物料粒度 0-30mm 堆积容重0.9t/m3取料刮板尺寸:1700×300物料水份8% 运行速度0.4m/s取料能力200t/h 取料行走速度0.2-2m/min电机功率75 KW 额定电流137.6 A电机转速1470 r/min 电压380 V4.2巡检规程4.2.1 运转前的检查a.减速机润滑油油位是否正常;b.链传动系统液力偶合器是否完好,有无漏油现象;c.链滴油润滑系统油量是否充足;d.刮板机链头尾轮是否完好,特别是对头轮圈的检查;e.行走驱动装置的减速机油位是否正常,联轴器是否良好;f.取料机是否在要求位置,料耙的耙架倾角是否合适,与料面接触是否良好;g.耙架的钢索有无断股和严重磨损,有无油脂、异物;h.轨道上有无异物,若有予以清除;j.取料机与堆料机是否在同一料堆中;h.各螺栓是否松动、脱落;I.开关是否在中控位置。
4.2.2 运转中的检查a.各传动部位有无异振、异音、异温;b.各电机、减速机有无异振、异温、异音、异味;c.检查刮板是否松动、脱落,刮板的防偏轮转动是否灵活,运转是否平稳,张紧是否合适;d.检查刮板滴油润滑是否正常;e.检查轨道上有无异物及钢丝绳有无明显断股现象;f.检查取料量是否适中,皮带上有无异物;g.检查各螺栓是否松动、脱落;4.2.3 维护与保养a.对磨损严重的部件要更换,特别是对变形严重的刮板必须更换;b.认真检查保养刮板链润滑装置,确保润滑正常;c.对传动减速机润滑油、油脂泵润滑点定期更换和补充;d.检查耙架与料面接触角度是否合适,运行是否平衡,并及时调整;e.耙车运行是否平稳,有无振动现象,换向装置是否灵活;f.检查各螺栓是否松动、脱落,并及时紧固、更换;5 皮带输送机巡检规程5.1 出煤堆场1#皮带输送机设备参型式: TD75槽形规格: B800179400 mm(右装)输送能力: 200 t/h 输送距离: 水平178.1 m倾斜角度: 13胶带速度: 1.25h拉紧型式: 垂直拉紧电动机型号 Y180M-4电动机功率 18.5 kW 减速机型号: ZQ65速比405.2 出煤堆场2#皮带输送机设备参数型式 TD75槽形输送能力 200t/h规格 B800142160 mm(右装)输送距离: 水平142.16 m 倾斜角度: 4.8911胶带速度: 1.25 m/s 拉紧型式: 垂直拉紧电动机型号Y180L-4 功率: 22 kW减速机型号:ZQ75 速比: 405.3出煤堆场3#皮带输送机设备参数型式: TD75槽形规格: B800133150 mm(左装)输送能力: 200 t/h 输送距离: 水平133.15 m倾斜角度: 7.9463胶带速度: 1.25 m/s拉紧型式: 垂直拉紧电动机型号: Y200L-4 功率: 30 kW减速机型号: ZQ85 速比: 505.3巡检规程5.3.1 运转前的检查a.检查电机减速箱油量、油质是否正常;b.检查皮带各档皮是否完好;c.确认各托辊是否有掉槽、缺少,运转是否灵活;d.检查皮带机进、出料口是否有异物;e.检查各辅助设施是否良好;f.控制开关是否在中控位置;5.3.2 运转中的检查a.检查、确认所送物料是否正确;b.检查下料是否均匀、适量,出料口是否有异物卡住;c.检查皮带是否有跑偏现象,托辊是否灵活;d.检查皮带接头是否良好,是否有划痕;e.检查电机总成是否有异音、异振、异温、异味;f.检查皮带张紧力是否在合适范围;g.检查皮带机进料罩挡板是否损坏、漏料;h.检查各润滑部位的润滑状况;5.3.3 维护与保养a.不允许带料停机;b.定期补充和更换各润滑点润滑油(脂);c.保持托辊、滚筒的清洁;d.对磨损、旋转不灵的托辊应及时更换;e.及时调整清扫器、保证清扫效果;f.检查调整张紧装置,保持拉绳开关灵活可用;g.紧固各部位松动螺栓;6 原煤仓巡检规程6.1原煤仓设备参数规格:6000 mm 容积: 120m36.2巡检规程6.2.1运转前的检查a.检查原煤仓内有无异物、大块、仓壁积料状况;b.确认原煤仓的料位,根据料位及时组织进煤;c.检查原煤仓上人孔门是否关闭密封好,原煤仓下闸阀是否打开;d.确认原煤温度,以防自燃;;6.2.2 运转中的检查a.确认原煤仓料位状况;b.检查原煤仓下料是否通畅、有无异物卡住;6.2.3 维护与保养a.检查原煤仓内的原煤,注意温度变化,防止自燃;b.长时间停机应放空原煤仓,紧急停机时应注意煤仓温度;c.检查仓壁磨损情况;d.经常检查料位的准确性和灵活性;e.停机进仓检查时,必须正确佩戴安全绳,上方有人加以看护并携带安全灯照明;7 定量给料机巡检规程7.1给煤机设备参数给煤机规格: DPG50 进出料口中心距:3500 mm 给料能力: 6.8_68t/h(正常:46t/h)电动机 (变频调速) 功率: 2.2 kW清扫电动机功率: 0.37kW7.2巡检规程7.2.1 运转前的检查a.检查各润滑点的润滑状况;b.检查皮带清扫器与皮带的接触情况;c.检查皮带有无起毛、开裂、划痕、裙边现象;d.检查皮带张紧状况;e.检查皮带机上有无杂物;f.检查皮带传感器上有无积灰、变形、有无异物接触现象;g.检查各螺栓是否松动、脱落、各辅助设施是否完好;h.检查给煤机密封情况。
磨粉机的操作规程

磨粉机的操作规程磨粉机是一种常用于进行粉磨处理的机械设备,操作磨粉机需要注意一些规程,以确保工作效率和安全。
本文将介绍磨粉机的操作规程。
1. 设备检查在操作磨粉机前,需要检查设备的安全状态和运行状况。
具体操作如下:1.检查电源及电器线路是否正常,确保接地良好,并且电压稳定。
2.检查机器的传动部分是否有轴承松动、带轮偏心和链传动松动等现象,及时予以调整、紧固或更换。
3.打开各部位的检查口,查看进出口管道、研磨室内清洁情况,以及各运动部位润滑情况;同时检查密封处是否正常,避免粉尘泄漏。
2. 开机操作1.在设备运行前,要保证电机无负荷旋转3-5分钟,检查磨盘无顶向和偏心。
2.检查磨盘间隙是否过小,磨盘是否摩擦,切勿强行开机,避免设备受损或事故发生。
3.首次加料需要适当控制,增加料量和开机时磨料的水分比例。
注意向磨盘缓慢加入料后,逐渐调整到正常料量。
4.成品粉经过各部位排出,确认流速和粒度达到要求后,方可达到目标。
5.在完成磨粉任务后,逐渐减小吸风量,避免因收尘过滤板堵塞导致操作难度增大。
3. 关机操作1.关机时先逐渐减小吸风量,清洗各部位残余粉尘后再关机。
2.关机后清理机台内部和周围环境,并对机台本身进行擦拭、调整、保养。
3.对磨盘、滚筒、轴承、密封圈、传动链等设备维护进行松动、更换、润滑。
4. 安全注意事项在操作磨粉机的过程中,需要注意如下安全事项:1.操作前要检查电源及电器线路是否正常,确保接地良好,并且电压稳定。
2.操作过程中要随时关注设备录音,发现任何异常情况要及时停机、排查修复。
3.在设备运行前,要保证电机无负荷旋转3-5分钟,检查磨盘无顶向和偏心。
4.关注磨盘间隙、磨料比例,不得暴力开机,检查各部位状态并进行适当控制。
5.关机后要清理吸尘板,擦拭机台,定期对设备各部位进行更换、润滑和维护。
总之,磨粉机是一项高效、安全的机械设备,操作磨粉机需要注意一些规程以确保工作效率和安全。
人们需要根据实际需求进行操作,加强日常维护,不断提高工作水平和设备效率。
浅谈中速磨煤机动态分离器的使用和分析

浅谈中速磨煤机动态分离器的使用和分析中速磨煤机动态分离器是煤磨系统中的重要设备之一,其主要作用是对磨煤机出口的煤粉进行分级和分离,以提高煤粉的粒度控制和燃烧效率。
本文将从使用和分析两个方面对中速磨煤机动态分离器进行浅谈。
一、使用1. 装置:中速磨煤机动态分离器通常由静动态叶片、分级筛、调整齿轮、分配器等组成。
静动态叶片可根据煤粉颗粒大小的需要进行调整,实现不同粒度的煤粉分离。
分级筛用于筛分出不同粒度的煤粉,以便根据需要进行再磨和再分级。
调整齿轮用于调整分离器的转速,以控制分离效果。
分配器用于将分离后的煤粉送入对应的筒仓或输送系统中。
2. 工作原理:中速磨煤机动态分离器通常与煤磨机同步工作,由煤磨机的排煤口将磨好的煤粉送入分离器中,经过分级筛的筛分后,根据颗粒大小分为粗粉和细粉两部分。
细粉通过调整齿轮控制的转速再进行一次细化磨煤,而粗粉则通过分配器分配到对应的筒仓或输送系统中,以供后续使用。
3. 优势:中速磨煤机动态分离器具有煤粉粒度控制范围广、分离效果好、燃烧效率高等优势。
由于静动态叶片和分级筛的作用,可以将煤粉粒度控制在较为合适的范围内,减少煤粉的堆积和粘连现象,提高燃烧效率。
动态分离器的自动控制装置可以实现对煤粉分离过程的实时监控和调节,提高分离效果和稳定性。
二、分析1. 优化参数:中速磨煤机动态分离器的分离效果和性能受到多种参数的影响,如静动态叶片的角度、颗粒分布、分级筛的开孔率等。
通过合理调整和优化这些参数,可以提高分离器的工作效率和性能,降低能耗和磨损。
2. 故障排除:中速磨煤机动态分离器的使用过程中可能会出现各种故障,如煤粉分离不彻底、过细或过粗煤粉比例偏大等。
针对这些故障,可以通过对分离器内部结构的检查和维护、清理防堵物等方法进行排除和修复。
3. 维护保养:中速磨煤机动态分离器的长期运行需要进行定期的维护保养工作,包括清理煤粉积聚、检查叶片磨损情况、润滑轴承等。
保持设备的良好状态和正常工作是确保其高效稳定运行的前提。
MX煤磨动态选粉机主要技术性能参数表

性能特点
本磨机为边缘传动,由电动机通过减速机及大小齿轮副带动磨机传动。
磨机采用带有烘干仓的风扫式结构,使磨机对原煤的水分有较大的适应性,粉磨仓内依次采用阶梯衬板、双阶梯衬板、波纹衬板等组合式排列布置,提高了磨机的粉磨能力。
进料装置采用斜进风的百叶窗式结构,增强了磨机的热交换能力,可以有效地防止煤磨进口的堵料现象。
工作原理
原煤由喂料设备进入到磨机的进料装置中,温度为300℃左右的热风也通过进风管进入进料装置,烘干仓
内设有特制的扬料板将原煤扬起,使得原煤在此处进行强烈的热交换而得到烘干,烘干后的煤块通过设有扬料板的双层隔仓板进入粉磨仓。
粉磨仓内装有研磨体(钢球),煤块在此仓内被粉碎、研磨成煤粉。
在煤块被粉碎的同时,由专用的引风机经过磨机的出料装置将已粉碎的煤粉及气体一同带出磨机,较粗的颗粒会经过出料装置的返料螺旋返回到粉磨仓内进行再次粉磨。
相关文章:。
浅谈中速磨煤机动态分离器的使用和分析

浅谈中速磨煤机动态分离器的使用和分析
中速磨煤机动态分离器是目前广泛应用于煤炭生产过程中的一种设备,具有磨煤、干燥、粉煤分离等多种功能,能够对煤炭进行有效的分级处理,提高煤炭品质和利用价值。
下面将对中速磨煤机动态分离器的使用和分析进行浅谈。
一、使用方法
1.开机前先检查整机的各个部件是否正常,特别是动态分离器的转子和定子是否有异常。
2.开机时需先启动进料鼓器,确保煤炭平稳进入磨煤机,防止因进料不平稳而引起的设备故障。
3.根据生产需要调节进料量和磨煤机的转速,逐渐加大煤炭的进料量,并根据磨煤机的输出粉煤质量进行微调,确保粉煤质量达标。
4.开机后要定期清理磨煤机内部的积煤和灰尘,防止因积煤或灰尘过多而影响设备的工作效率和粉煤质量。
5.当设备出现异常情况时,要及时停机检查,并进行必要的维修或更换。
二、分析
1.磨煤效果
中速磨煤机动态分离器能够有效的磨碎煤炭,提高煤炭的可燃性和热值,同时通过动态分离器的分离作用可以将煤炭中的杂质和水分等物质分离出来,确保粉煤的质量和利用价值。
2.设备运行稳定性
3.节能环保性
中速磨煤机动态分离器具有高效节能的特点,能够有效降低煤炭加工过程中的能耗和排放量,提高生产效益和环境保护效益,符合绿色低碳的生产理念。
同时,设备还能够将煤炭中的杂质和污染物分离出来,减少环境污染的风险和危害。
总之,中速磨煤机动态分离器在煤炭生产过程中扮演着重要的角色,需要通过科学合理的使用和分析,充分利用其优点,提高煤炭的利用价值和生产效益,为保障人们能源需求和环境保护做出贡献。
使用煤炭磨样机安全操作规程

使用煤炭磨样机安全操作规程一、前言煤炭磨样机是煤炭行业中常用设备之一,其主要功能是对各种煤样进行磨损操作,制作出符合要求的煤样。
安全操作是煤炭磨样机正常工作的基础,本文旨在对煤炭磨样机的安全操作规程进行详细介绍,以提高煤炭磨样机的使用效率和工作安全性。
二、安全操作规程1.之前要做好维护工作,包括清洁、调整、润滑等,互锁、限位等机构的联锁应调整到位。
2.煤炭磨样机使用前应认真检查,检查应包括煤样料斗和煤炭磨样机内部是否有异物,是否存在外泄的部位等。
3.操作煤炭磨样机时,应穿好工作服和安全帽,管理工作人员应对其进行细致的工作安全培训。
4.在操作煤炭磨样机时,人员要对机器所处的环境进行认真检查,防止发生冲击、振动等危险情况,并注意观察机器运行情况。
5.在操作时,必须熟悉操作步骤,按照操作要求进行工作,不得随意更改或加入新操作步骤。
6.煤炭磨样机在工作中应注意闸门、传送带、输送鼓和机壳等部位是否正常运行,不得操作故障或不正常的机器。
7.禁止有任何其他机器或设备靠近煤炭磨样机工作区,更不能在机器内部堆积过多的煤炭,以免引起事故。
8.当煤炭磨样机运行异常或有异常响应时,应及时关闭电源,并通知有关管理者进行处理。
9.在煤样真空状态下,磨损器内部产生气氛时,请避免引燃静电等情况,以免发生事故。
10.使用完煤炭磨样机后,及时将其清洁干净,并进行维护保养,以确保下一次使用时的安全性和使用效率。
三、结语煤炭磨样机为煤炭企业的生产和开采提供了便利,同时也给工作人员的安全带来了一定的威胁。
为保障工作人员的安全,提高煤炭磨样机的使用效率,应建立完善的安全运行规则和操作规程,并加强人员安全培训,这样既可以保障煤炭磨样机的正常使用,又可以在工作过程中不断提高人员安全意识。
煤磨操作规程
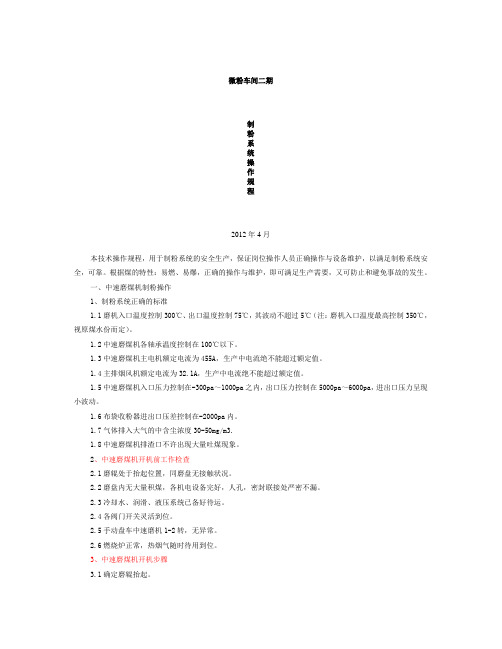
微粉车间二期制粉系统操作规程2012年4月本技术操作规程,用于制粉系统的安全生产,保证岗位操作人员正确操作与设备维护,以满足制粉系统安全,可靠。
根据煤的特性:易燃、易爆,正确的操作与维护,即可满足生产需要,又可防止和避免事故的发生。
一、中速磨煤机制粉操作1、制粉系统正确的标准1.1磨机入口温度控制300℃、出口温度控制75℃,其波动不超过5℃(注:磨机入口温度最高控制350℃,视原煤水份而定)。
1.2中速磨煤机各轴承温度控制在100℃以下。
1.3中速磨煤机主电机额定电流为455A,生产中电流绝不能超过额定值。
1.4主排烟风机额定电流为32.1A,生产中电流绝不能超过额定值。
1.5中速磨煤机入口压力控制在-300pa~1000pa之内,出口压力控制在5000pa~6000pa,进出口压力呈现小波动。
1.6布袋收粉器进出口压差控制在-2000pa内。
1.7气体排入大气的中含尘浓度30-50mg/m3.1.8中速磨煤机排渣口不许出现大量吐煤现象。
2、中速磨煤机开机前工作检查2.1磨辊处于抬起位置,同磨盘无接触状况。
2.2磨盘内无大量积煤,各机电设备完好,人孔,密封联接处严密不漏。
2.3冷却水、润滑、液压系统已备好待运。
2.4各阀门开关灵活到位。
2.5手动盘车中速磨机1-2转,无异常。
2.6燃烧炉正常,热烟气随时待用到位。
3、中速磨煤机开机步骤3.1确定磨辊抬起。
3.2各设备润滑系统开始润滑,主减速机回油畅通。
3.3各电动机开始送电。
3.4投入联锁状置。
3.5启动布袋收粉器,星型卸料器运转。
3.6螺旋输送机运行。
入仓插板开关状态到位,进入相应煤粉仓。
3.7起动中速磨机分离器运转正常。
3.8启动主排烟风机,调整系统负压。
3.9系统送热烟气并兑入自循环风量,控制磨机出口小于75℃,准备主磨机启动。
3.10调整系统各位置压力、温度满足生产要求。
3.11起动磨煤机3.12起动密封式给煤机,并同时落辊轻载运行。
3.13调整下煤量,调整热烟气量,观察磨机振动及吐煤情况,调整液压系统压力。
煤磨操作手册
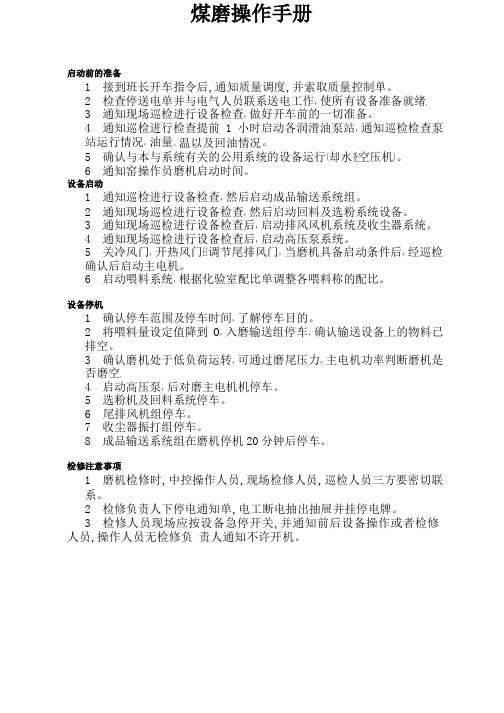
煤磨操作手册启动前的准备1 接到班长开车指令后,通知质量调度,并索取质量控制单。
2 检查停送电单并与电气人员联系送电工作,使所有设备准备就绪.3 通知现场巡检进行设备检查,做好开车前的一切准备。
4 通知巡检进行检查提前1小时启动各润滑油泵站,通知巡检检查泵站运行情况,油量、温以及回油情况。
5 确认与本与系统有关的公用系统的设备运行(却水尧空压机)。
6 通知窑操作员磨机启动时间。
设备启动1 通知巡检进行设备检查,然后启动成品输送系统组。
2 通知现场巡检进行设备检查,然后启动回料及选粉系统设备。
3 通知现场巡检进行设备检查后,启动排风风机系统及收尘器系统。
4 通知现场巡检进行设备检查后,启动高压泵系统。
5 关冷风门,开热风门曰调节尾排风门,当磨机具备启动条件后,经巡检确认后启动主电机。
6 启动喂料系统,根据化验室配比单调整各喂料称的配比。
设备停机1 确认停车范围及停车时间,了解停车目的。
2 将喂料量设定值降到0,入磨输送组停车,确认输送设备上的物料已排空。
3 确认磨机处于低负荷运转,可通过磨尾压力,主电机功率判断磨机是否磨空.4 启动高压泵,后对磨主电机机停车。
5 选粉机及回料系统停车。
6 尾排风机组停车。
7 收尘器振打组停车。
8 成品输送系统组在磨机停机20分钟后停车。
检修注意事项1 磨机检修时,中控操作人员,现场检修人员,巡检人员三方要密切联系。
2 检修负责人下停电通知单,电工断电抽出抽屉并挂停电牌。
3 检修人员现场应按设备急停开关,并通知前后设备操作或者检修人员,操作人员无检修负责人通知不许开机。
4 检修时,巡检人员及时与检修人员加强联系,通知操作人员及时调整磨里负压。
5 检修完时,先检查有无遗留物,由检修负责人下送电通知单,电工送电,巡检人员恢复急停开关。
6 确认无误后,检修人员与巡检人员在现场观察,中控人员起动设备。
煤磨动态选粉机说明书
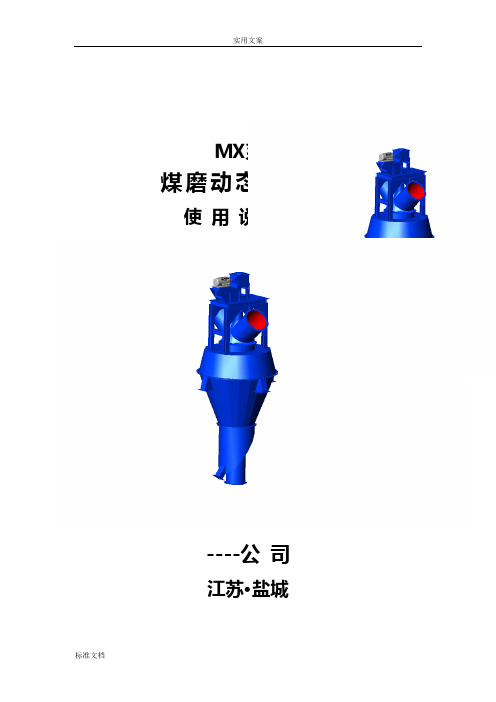
实用文案MX 系列煤磨动态选粉机 使 用 说 明 书----公 司 江苏·盐城目录一、概述二、结构工作原理三、技术性能表四、设备结构及各部位功能五、技术革新及特点六、安装要求七、调试及运行八、维护及维修一、概述我公司生产的MX系列高效动态煤粉选粉机是我公司2000年引进天津院图纸。
它是在日本小野田公司O-Sepa原版图纸的基础上,成功应用国际先进水平的TSV4高效、低阻、节能涡轮转子技术,笼型转子选粉机和粗粉分离器组合为一体的新型高效动态选粉机,我公司引进该设备的生产技术以后,成功的嫁接了法国FCB公司国际选进TSV4选粉机涡轮转子技术及机翼状导流叶片。
其分离的粒径范围为25μm至150μm,可以根据煤质变化和烧成情况的需要很方便的进行调节。
是当前最为理想和可靠的煤粉分选设备。
二、工作原理MX系列高效动态煤粉选粉机是将笼形转子选粉机和粗粉分离器组合为一体的设备,分为上、下两部分。
上部为笼形转子选粉机;下部为粗粉分离器。
出磨物料由气体携带着进入选粉机下部的粗料套筒的立式内筒,气体中的物料在反击锥出受到碰撞作用而转向,由于上升风速的降低、提升气力的变小,粗颗粒向下降落并通过粗料出口离开选粉机;细颗粒由混合气体继续带到上部。
到达位于导向风环与旋转着的笼形转子之间的选粉区,进行分选。
细粉(即成品)由于气力的驱动,穿过笼形转子上的笼条并离开壳体上部的出风口进入(料、气)分离设备。
粗粉从选粉区降落下来进入内锥体,通过内锥体与反击锥之间的环形缝隙来实现物料的均匀分撒。
这样,上升的混合气体可对此部分物料进行再分选,形成选粉机内部循环分选,以提高选粉机的效率。
含尘气体携带着细粉从位于顶部的壳体上部的出风口进入分离设备。
成品从分离设备卸出,经由输送设备进入煤粉仓。
含尘气体进入收尘器,过滤后的气体通过系统风机后排入大气或部分在循环到系统中。
MX煤磨动态选粉机分级性能好,能提高煤磨系统产量10-15%,单产电耗降低5%-8%。
浅谈中速磨煤机动态分离器的使用和分析

浅谈中速磨煤机动态分离器的使用和分析中速磨煤机是燃煤工业中常见的设备之一。
其主要作用是将煤炭磨碎,提高燃烧效率。
在磨煤的过程中,煤炭与空气混合,产生大量的粉尘。
这些粉尘对于环境和工作安全都是有害的。
为了解决磨煤过程中产生的粉尘污染问题,使用动态分离器作为磨煤机的配套设备,能够有效地解决这个问题。
动态分离器是一种利用离心力对颗粒物进行分离的设备。
在磨煤机内部,动态分离器是安装在磨盘下方的。
煤粉进入到磨盘中间区域进行磨碎。
在磨碎的过程中,由于转子高速旋转产生的离心力,煤粉会被向上抛出,而重质的物质则会下沉到磨盘下部分离心罩内。
这样,煤粉中的粉尘即可被分离出来,而煤粉则继续向外输送。
通过动态分离器的作用,磨煤机的出料口产生的粉尘浓度可降至原有的1/10以下。
这对于环境治理具有非常重要的作用。
动态分离器使用的效果与其结构设计密切相关。
其主要结构包括转子、离心罩和分离筒。
离心罩和分离筒由多个分叶构成,分叶之间有缝隙。
转子以高速旋转,离心罩和分离筒亦随之旋转。
在运转过程中,被处理的气体流经离心罩和分离筒,其中的大颗粒物因惯性作用被分离出来并落入离心罩的内腔,而小颗粒物则被带走而不易沉积,从而实现逐步清除颗粒物的目的。
在实际使用中,动态分离器的效果非常稳定,而且使用寿命较长。
其主要优点在于,具有的离心力比静态设备大,可以更好地实现对粉尘的分离效果。
特别是在大风量和较高的粉尘浓度下,其效果更加显著,这也是其他分离设备无法比拟的。
此外,动态分离器还具有操作简单、维护方便等优点。
总之,动态分离器作为中速磨煤机的配套设备,除了能够有效地降低粉尘污染,还能够提高磨煤机的磨煤效率,减少了能源消耗。
在燃煤工业中,其作用非常重要,对于提高生产效率、保障工人身体健康都具有重要的意义。
煤磨系统中控操作规程

煤磨系统是重要的煤炭粉碎设备,它的稳定运行直接关系到生产效率和产品质量。
为了确保煤磨系统的正常运行和安全生产,制定一套煤磨系统中控操作规程至关重要。
本规程旨在规范操作流程、标准作业程序、安全操作要求等方面的细节,以确保操作人员能够安全、高效地操作煤磨系统,实现生产目标。
本规程适用于所有煤磨系统的中控操作人员,必须在系统投入使用前进行培训并掌握相关操作技能。
任何违反规程的行为将会被认为是严重的违规,对生产安全和企业形象均会造成不良影响。
因此,本规程应该认真遵守和执行。
1范围本规程适用于烧成煤粉制备系统中控操作,即从原煤预均化堆场到煤粉仓部分。
2总则本规程旨在统一操作思想,树立安全第一的观点,力求做到优质、稳产、高产、低耗、生产出合格的煤粉,确保合格煤粉供应。
现场出现问题时,现场班组长确认后,汇报中控操作员,(较大的问题同时汇报主管部门领导)。
然后由中控操作员通知相关部门解决。
所有信息,现场与中控之间要及时反馈和协调。
3工艺流程3. 1工艺流程简介首先由原煤预均化堆场的取料机(06/18.03)从堆场取到原煤,再由输送皮带机(06/18.07、06/18.08、06/18.09)输送至原煤仓。
原煤仓的原煤,经过仓下棒形阀(19.01),再落到定量给料机(19.02),由电动双翻板锁风阀(19.03)喂入煤磨(19.04),并在回转的磨内,受研磨体的粉磨。
由窑头废气来的热风,将磨内物料烘干并将粉料带此经动态选粉机(19.05),将较粗的颗粒料分选出来经螺旋输送机(19.07)返回磨内再次粉磨,合格的细粉和废气进入袋收尘器(19.09),由袋收尘收集下来的煤粉,经过回转下料器(19.09-1)由可逆螺旋输送机(19.11),经过气动推杆平板闸阀(19.12、19.13)分别卸入窑头煤粉仓(19.15-1)和分解炉煤粉仓(19.15-2)中,再经罗茨风机(19.18、19.19)送风,由申克秤计量被连续送入窑头燃烧器和分解炉中。
第一篇磨煤机使用和操作说明

第一篇磨煤机使用和操作说明1. 代号和技术数据1.1 代号分K、N、G三个型号,N型,不表示磨环滚道平均半径(cm)磨煤机辊式中速1.2 技术数据1.2.1 煤种范围煤种烟煤,部分贫煤和部分褐煤发热量16~31MJ/kg表面水份≤18%可磨性系数HGI=40~80(哈氏)可燃质挥发份16~40%原煤颗粒0~40mm煤粉细度R90=15~40%1.2.2 磨煤机技术数据标准研磨出力78.7 (当R90=16%,HGI=80,W Y=4%)额定功率512 kW电动机额定功率650 kW电动机电压6000 V电动机转速990 r/min电动机旋转方向逆时针(正对电机输入轴)磨煤机磨盘转速24.4 r/min磨煤机旋转方向顺时针(俯视)通风阻力≤6410 Pa磨机额定空气流量25.14 kg/s磨煤机磨煤电耗量6~10 kW·h/t (100%磨煤机出力)2. 工作原理ZGM113磨煤机是一种中速辊盘式磨煤机,其碾磨部分是由转动的磨环和三个沿磨环滚动的固定且可自转的磨辊组成。
原煤从磨机的中央落煤管落到磨环上,在离心力作用下将原煤运动至碾磨滚道上,通过磨辊进行碾磨。
三个磨辊沿圆周方向均布于磨盘滚道上,碾磨力则由液压加载系统产生,通过静定的三点系统,碾磨力均匀作用至三个磨辊上,这个力是经磨环、磨辊、压架、拉杆、传动盘、减速机、液压缸后通过底板传至基础(见图1―1)。
原煤的碾磨和干燥同时进行,一次风通过喷嘴环均匀进入磨环周围,将从磨环上切向甩出的煤粉吹送至磨机上部的分离器,在分离器中进行分离,粗粉被分离出来返回磨环重磨,合格的细粉被一次风带出分离器。
图1―1 磨煤机加载传递系统“受力状态图”难以粉碎且一次风吹不起的较重石子煤、黄铁矿、铁块等通过喷嘴环落到一次风室,被刮板刮进排渣箱,由人工(或由自动排渣装置排走)定时清理。
(见图1―2)。
ZGM113型磨煤机采用鼠笼型异步电动机驱动。
通过立式伞齿轮行星齿轮减速机传递力矩。
煤磨操作说明书
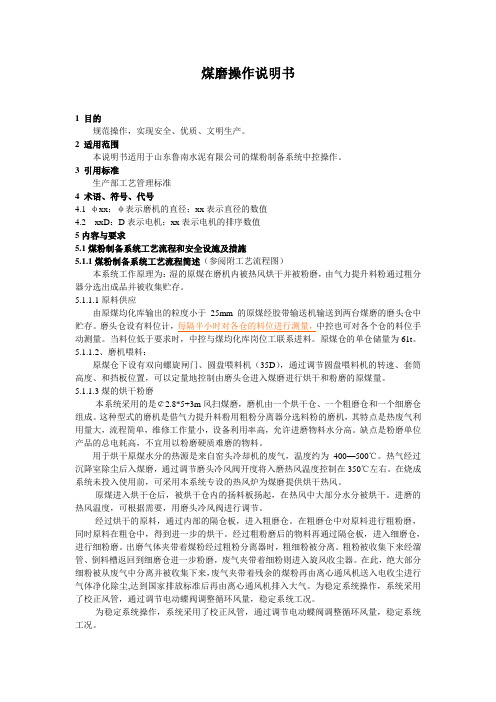
煤磨操作说明书1 目的规范操作,实现安全、优质、文明生产。
2 适用范围本说明书适用于山东鲁南水泥有限公司的煤粉制备系统中控操作。
3 引用标准生产部工艺管理标准4 术语、符号、代号4.1 φxx:φ表示磨机的直径;xx表示直径的数值4.2 xxD:D表示电机;xx表示电机的排序数值5内容与要求5.1煤粉制备系统工艺流程和安全设施及措施5.1.1煤粉制备系统工艺流程简述(参阅附工艺流程图)本系统工作原理为:湿的原煤在磨机内被热风烘干并被粉磨,由气力提升料粉通过粗分器分选出成品并被收集贮存。
5.1.1.1原料供应由原煤均化库输出的粒度小于25mm的原煤经胶带输送机输送到两台煤磨的磨头仓中贮存。
磨头仓设有料位计,每隔半小时对各仓的料位进行测量,中控也可对各个仓的料位手动测量。
当料位低于要求时,中控与煤均化库岗位工联系进料。
原煤仓的单仓储量为61t。
5.1.1.2、磨机喂料:原煤仓下设有双向螺旋闸门、圆盘喂料机(35D),通过调节圆盘喂料机的转速、套筒高度、和挡板位置,可以定量地控制由磨头仓进入煤磨进行烘干和粉磨的原煤量。
5.1.1.3煤的烘干粉磨本系统采用的是¢2.8*5+3m风扫煤磨,磨机由一个烘干仓、一个粗磨仓和一个细磨仓组成。
这种型式的磨机是借气力提升料粉用粗粉分离器分选料粉的磨机,其特点是热废气利用量大,流程简单,维修工作量小,设备利用率高,允许进磨物料水分高。
缺点是粉磨单位产品的总电耗高,不宜用以粉磨硬质难磨的物料。
用于烘干原煤水分的热源是来自窑头冷却机的废气,温度约为400—500℃。
热气经过沉降室除尘后入煤磨,通过调节磨头冷风阀开度将入磨热风温度控制在350℃左右。
在烧成系统未投入使用前,可采用本系统专设的热风炉为煤磨提供烘干热风。
原煤进入烘干仓后,被烘干仓内的扬料板扬起,在热风中大部分水分被烘干。
进磨的热风温度,可根据需要,用磨头冷风阀进行调节。
经过烘干的原料,通过内部的隔仓板,进入粗磨仓。
- 1、下载文档前请自行甄别文档内容的完整性,平台不提供额外的编辑、内容补充、找答案等附加服务。
- 2、"仅部分预览"的文档,不可在线预览部分如存在完整性等问题,可反馈申请退款(可完整预览的文档不适用该条件!)。
- 3、如文档侵犯您的权益,请联系客服反馈,我们会尽快为您处理(人工客服工作时间:9:00-18:30)。
MX系列煤磨动态选粉机使用说明书江苏·盐城目录一、概述二、结构工作原理三、技术性能表四、设备结构及各部位功能五、技术革新及特点六、安装要求七、调试及运行八、维护及维修一、概述我公司生产的MX系列高效动态煤粉选粉机是我公司2000年引进天津院图纸。
它是在日本小野田公司O-Sepa原版图纸的基础上,成功应用国际先进水平的TSV4高效、低阻、节能涡轮转子技术,笼型转子选粉机和粗粉分离器组合为一体的新型高效动态选粉机,我公司引进该设备的生产技术以后,成功的嫁接了法国FCB公司国际选进TSV4选粉机涡轮转子技术及机翼状导流叶片。
其分离的粒径范围为25μm至150μm,可以根据煤质变化和烧成情况的需要很方便的进行调节。
是当前最为理想和可靠的煤粉分选设备。
二、工作原理MX系列高效动态煤粉选粉机是将笼形转子选粉机和粗粉分离器组合为一体的设备,分为上、下两部分。
上部为笼形转子选粉机;下部为粗粉分离器。
出磨物料由气体携带着进入选粉机下部的粗料套筒的立式内筒,气体中的物料在反击锥出受到碰撞作用而转向,由于上升风速的降低、提升气力的变小,粗颗粒向下降落并通过粗料出口离开选粉机;细颗粒由混合气体继续带到上部。
到达位于导向风环与旋转着的笼形转子之间的选粉区,进行分选。
细粉(即成品)由于气力的驱动,穿过笼形转子上的笼条并离开壳体上部的出风口进入(料、气)分离设备。
粗粉从选粉区降落下来进入内锥体,通过内锥体与反击锥之间的环形缝隙来实现物料的均匀分撒。
这样,上升的混合气体可对此部分物料进行再分选,形成选粉机内部循环分选,以提高选粉机的效率。
含尘气体携带着细粉从位于顶部的壳体上部的出风口进入分离设备。
成品从分离设备卸出,经由输送设备进入煤粉仓。
含尘气体进入收尘器,过滤后的气体通过系统风机后排入大气或部分在循环到系统中。
MX煤磨动态选粉机分级性能好,能提高煤磨系统产量10-15%,单产电耗降低5%-8%。
产品的细度主要靠调节回转部分的转速来控制。
为了保证足够的提升气力,只有在极特殊的情况下,才可改变风量来调整产品的细度。
如果在允许的转速范围内,仍达不到细度要求的情况下,可以调整导板的开度来满足细度要求。
如果把导板的开度增大,成品将变粗,反之,成品将变细。
三、技术性能:四、设备构造及各部位功能该选粉机外壳体均采用16Mn钢板,关键部位加耐磨衬板或粘贴高铝耐磨陶瓷,其配套部件选用国际名牌。
本选粉机主机主要由下述部件组成:传动装置、传动支座、支架、回转部分、壳体、支座、反击锥。
现分别描述如下:1、传动装置:由变频调速电机驱动减速机垂直向下输出轴构成的传动装置。
高速轴端为弹性联轴器,低速轴端为梅花联轴器。
2、传动支座:由于传动装置座落于其上要求有足够的刚度,用钢板拼焊而成。
3、支架:由于回转部分及传动装置均要安装在传动支架上,应对其考虑要有足够的强度及刚度,主要由工字钢拼焊制成。
4、回转部分:主要由笼形转子、涡流打散器、主轴、轴套、轴承、气封装置等组成。
(1)笼形转子:通过主轴与减速器连接。
在柱体状的转子外圆周上装有可更换的叶片。
由于该部分属较大重量的转动部件,因此,在制造厂要求对其进行动平衡实验(2)涡流打散器:在笼形转子内部插入涡流打散器。
(3)主轴:材质为45号优质钢,调质处理,硬度BHN=217~255。
(4)轴承:选用瑞典SKF或日本NSK。
(5)气封装置:用钢板焊接一组放射形同心圆导板的空穴式箱形结构以形成气隙密封。
用螺栓固定在笼形转子的顶部。
5、导向叶片:采用机翼形结构,在上壳体的空腔内沿圆周设置,形成导向风环。
在与笼形转子之间内形成选粉区。
6、支座:由钢板拼焊而成的结构件。
保证有足够的刚度和强度来支撑整个选粉机。
7、壳体:由出风管、上壳体、下壳体、内锥体、粗料套筒组成。
(1)出风管:由钢板拼焊而成,内砌高铝耐磨陶瓷。
由于本选粉机用于煤粉,故在风管对称位置上设有防暴装置。
(2)上壳体:由钢板拼焊而成并设有检查门。
在其内表面上设有可更换的耐磨衬板。
在其空腔内沿圆周设置了机翼状的导向叶片。
导向叶片插入上壳体空腔内。
这些导向叶片可以进行调整,来改变气流的速度和方向。
使料气混合能力大大提高,流体阻力大大减小,从而有助于选粉能力提高。
每个叶片都是通过专门的销轴与上壳体连接,只要松动销轴上的固定螺母,就可以对导板进行调整。
考虑到气流中含有的颗粒物质对导板会产生严重的磨损,导板采用了特殊的耐磨钢板制成。
(3)下壳体:由钢板拼焊而成并设有检查门。
在气内表面上设有可更换的耐磨衬板。
(3)内锥体:由钢板拼焊而成。
这装在笼形转子底部和反击锥之间。
要求内锥体与反击锥之间的环形缝隙为25-30mm(4)粗料套筒:由钢板拼焊而成。
粗料筒有两个功能:其一,内套筒是出磨的混合气体进选粉机的入口。
其二,是粗料的出口,为了防止漏风,粗料出口要求设有翻板阀。
8、反击锥:主要由顶盖、锥体等组成。
(1)顶盖:由钢板拼焊而成。
外表面设有以便与安装及检修的入孔门。
其内部要求填满矿渣棉。
(2)锥体:为耐磨铸件。
五、技术革新及特点1.技术革新:(1)笼形转子内部经过技术革新。
转子叶片嫁接国际先进水平TSV4高效涡轮转子叶片技术。
转子叶片内侧进风口的横截面积增大,选粉空气的径向速度朝着转子轴的方向减小,选粉区不局限于叶片转子的周边而是延伸进入转子叶片间的开口处,大大提高了选粉效率;涡流系统被引入到叶片转子的中心,提高了选粉机分选细粉的能力。
细粉累积产量Tromp曲线表明几乎全部细粉被回收,无重聚现象。
避免了涡流产生的压降,气流的旋转产生的能量传给转子,降低了驱动装置的电耗,同时避免了涡流产生的能耗。
由于通过转子叶片内侧的流体切向速度降低,使流体阻力减小、磨损大大减小。
(3)导向叶片采用机翼形构造,使料气混合能力大大提高,流体阻力大大减小,从而有助于选粉能力提高。
2.改进后选粉机具有以下特点:(1)具有高单位风量载尘量的处理能力,当喂料量增大时切割粒径几乎不变,因此成品相当均匀一致;当单位风量含尘量达到3.2kg/m3而分级效率不会降低。
(2)分级精度从第三代选粉机的0.5提高到0.7。
(3)成品颗粒均齐均匀、改善水泥产品性能,提高水泥早期强度。
(4)粉磨工艺改善,电耗更低,可使整个粉磨回路有很好的节能效果。
六、安装要求:对于如此大规格的选粉机,有许多的零、部件,为此,需要大量的安装工作。
由于本选粉机可用于不同的场合或不同的工厂,因此,其安装空间及安装工具亦可能不同,为此,本说明书规定的安装顺序,仅供参考。
支座→临时安放下壳体→笼形转子→上壳体→出风管→支架→主轴→反击锥→粗粉套筒→传动支座→联轴器→减速器→联轴器→电动机。
1.支座:安装底座并用调整垫板进行调整,使其平面度公差为0.25mm。
2.下壳体:暂时用临时架子固定,将笼形转子放置在内锥体内。
3.上壳体:将上壳体放置在支座上,用螺栓松套上,并用调整垫板进行调整,要求上壳体上部支撑传动支架的两条工字钢的平面度公差值为0.1mm。
调整好后紧固螺母固定,并将调整垫板与支座焊成一体。
由于采用了非机械接触气仓式正压密封装置,安装要求非常严格,有需要到现场安装时组焊的零部件。
(具体位置请查阅壳体部分图纸)4.出风管:注意方向应与图纸方向一致。
5.支架:注意方向性,通过调整上壳体与支架之间的调整垫板来保证支架上表面的平面度公差值为0.05mm。
6.主轴:安装回转部分时,应严格按照图纸要求,确保回转部分与支架间的配合尺寸要求。
把带有主轴套的主轴调整好油管、气管的要求方位,将其整体从支架上端的轴孔中落下,要求准确的将轴落入笼轮的轴套中,然后拧紧下部的锁紧螺母。
为了确保回转部分的垂直度要求,在轴套的圆周上设置了四个拉板。
为了防止拉板被物料冲刷,拉板采用耐磨板。
在回转部分安装完毕并调整好达到垂直度要求后,方可将四个拉板与壳体上部用螺母固定。
气封装置用螺栓固定在笼型转子的顶部。
安装气封装置时,要对其进行精确的调整,使气封装置的每一块导板与壳体上部之间的间隙均为5mm。
(具体位置请查阅回转部分图纸)安装后,用手转动笼轮,气封装置与壳体上部之间不得有金属接触和刮撞现象。
按图纸要求安装油管、气管。
安装前要求对管路进行除锈、酸洗,油管内注满油脂。
进行有关各部位陶瓷片的粘贴。
7.反击锥:反击锥用吊环螺栓固定在壳体顶盖上。
安装前,应严格校正反击锥底部的圆度,使其达到要求。
安装反击锥时,要求对其进行精确的调整,使内锥体与反击锥之间的环形缝隙均匀,相等。
8.粗料套筒:注意方向性,粗料出口要求安装翻板阀,防止漏风。
七、调试及运行:1.准备调试:在次调试之前,应对选粉机及传动装置按以下顺序进行全面检查。
(1)应认真查阅传动装供货商提供的电动机、减速器及联轴器的有关技术文件,并检查是否按其要求进行安装。
(2)是否按图纸及说明书中有关要求进行组装;为了方便运输及现场组装所设置的辅助零部件是否已经全部拆除。
(3)选粉机及传动装置的全部连接件是否牢固。
(4)粗料出口翻板阀的功能是否正常。
(5)轴承润滑脂、减速器润油是否以加到合适的量。
(6)笼型转子转动是否自如。
(7)导板的位置是否均匀、相等。
上述各项检查均达到要求后,可以进行短时间的空负荷试车。
2.空负荷试车:在转子最高转速下,连续进行2-4小时空负荷运转,应满足下述要求:(1)回转部分运行平稳,笼型转子既不能碰撞壳体,主轴也不能有噪声。
(2)各轴承温升不超过30℃。
(3)润滑油、油脂不得有任何污迹,油管通畅,润滑良好。
(4)所有监视检测仪表及控制系统,均应灵敏准确。
(5)观察、检测并记录电流波动情况。
(6)检查并拧紧各部连接螺栓。
完成上述工作后,方可进行投料试车。
3.负荷试车:(1)对首次投料试车的选粉机,要求必须保证物料连续、均匀的喂入选粉机。
(2)避免系统漏风。
粗料出口的翻板阀重锤重量或位置应调节为使得阀板每分钟大约开启6至10次。
(3)只有在选粉机的电动机达到其运行速度之后,才能投料。
反之亦然,即必须在已经停止喂料后,选粉机的电动机才能停止运行。
(4)传动装置的润滑系统必须在选粉机启动之前启动。
(5)成品细度的控制:选粉机的转速和导板的位置变化,必须根据选粉机的进料粒径和成品细度的要求来调节。
(6)于改变成品细度,可采取下述方法:4.成品细度调节方法:(1)成品细度变的更细:逐渐加快笼型转子的转速。
如果转速达到最大,仍达不到要求的细度时,可将导板关紧些。
(2)成品细度变的更粗:逐渐减慢笼型转子的转速。
如已调至笼型转子最高转速的35%时,仍未达到所要求的成品细度,可将导板开得更宽些。
改变导板的位置时,磨机系统必须停止工作,鉴于本系统具有一定的相互关联性这一特点,上述改变成品细度的工作必须一次完成。
八、日常维护:应该指出,日常性的维护工作远比故障性的维修工作更为重要,为此,必须加强平时的维护工作。