运营管理之丰田案例(中文版)
企业经营管理优秀实践案例丰田模式项原则
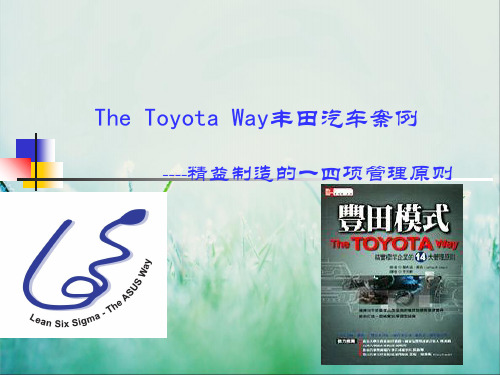
原则一 管理决策以长期理念为基础
即使因此牺牲短期财务目标也在所不惜
丰田的使命陈述与指导原则
✓ 丰田真正的使命有三个部分
1. 对运营所在地国家[外部利害关系人]的经济成长作出贡献. 2. 对员工[内部利害关系人]的稳定与福祉作出贡献. 3. 对丰田企业的整体成长作出贡献.
✓ 丰田汽车企业的指导原则
借鉴丰田 新联合汽车制造企业赢得员工的 信任
✓ 丰田企业改变员工们的态度和看法,并赢得员工的信任. ✓ 丰田认识到帮助通用改善其制造水平,就等于是帮助社会与
小区,同时也为美国人创造高薪资的制造业工作.
原则一 管理决策以长期理念为基础 即使因此牺牲短期财务目标也在所不惜
别让决策伤害到信任与相互尊重
✓ 丰田企业认识到,维持员工的饭碗是它,而是从使顾客及员工持续尊
敬丰田企业及其产品的角度来考虑的.丰田知道这个工厂熟练且 努力的员工必定能应用丰田生产方式持续地改进质量,去除浪费. 丰田相信这才是带动长期获利的主要因素.
原则一 管理决策以长期理念为基础 即使因此牺牲短期财务目标也在所不惜
✓ 真正的挑战在于必须建立一个懂得寻找方 法减少使用广告牌 制度以降低存货,且最终解除缓冲存货的学习型企业
原则三 实施拉式生产制度以避免生产过剩
预定日程表的推式生产制度仍有可用之处
✓ 在丰田企业,仍然有很多地方使用依照预先排定生产日程表的推 式制度. ➢ 它们使用传统的排定日程表制度来下零部件订单,以适当的前 置期来进行零部件的递送.日程表并非只是您必须尽量遵照的 原则,也是您务必竭尽全力实现的截止期限.
一.生产过剩
五. 存货过剩
二.等候
六.不必要的移动,搬运
三.不必要的运输
七.瑕疵
运营管理之丰田案例分析
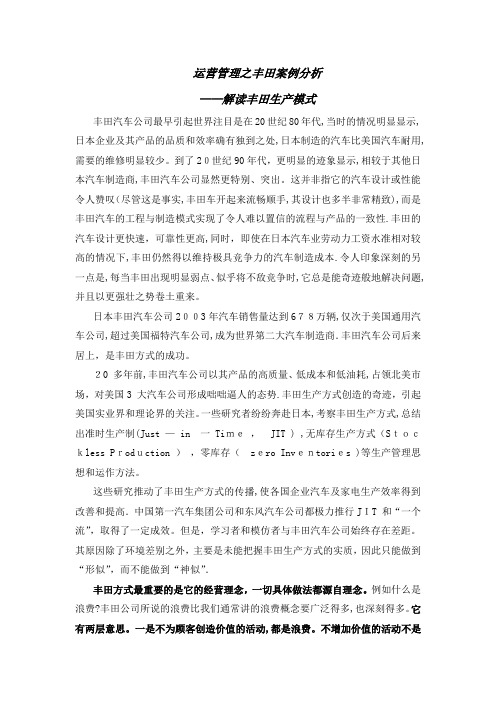
运营管理之丰田案例分析——解读丰田生产模式丰田汽车公司最早引起世界注目是在20世纪80年代,当时的情况明显显示,日本企业及其产品的品质和效率确有独到之处,日本制造的汽车比美国汽车耐用,需要的维修明显较少。
到了20世纪90年代,更明显的迹象显示,相较于其他日本汽车制造商,丰田汽车公司显然更特别、突出。
这并非指它的汽车设计或性能令人赞叹(尽管这是事实,丰田车开起来流畅顺手,其设计也多半非常精致),而是丰田汽车的工程与制造模式实现了令人难以置信的流程与产品的一致性.丰田的汽车设计更快速,可靠性更高,同时,即使在日本汽车业劳动力工资水准相对较高的情况下,丰田仍然得以维持极具竞争力的汽车制造成本.令人印象深刻的另一点是,每当丰田出现明显弱点、似乎将不敌竞争时,它总是能奇迹般地解决问题,并且以更强壮之势卷土重来。
日本丰田汽车公司2003年汽车销售量达到678万辆,仅次于美国通用汽车公司,超过美国福特汽车公司,成为世界第二大汽车制造商.丰田汽车公司后来居上,是丰田方式的成功。
20 多年前,丰田汽车公司以其产品的高质量、低成本和低油耗,占领北美市场,对美国3 大汽车公司形成咄咄逼人的态势.丰田生产方式创造的奇迹,引起美国实业界和理论界的关注。
一些研究者纷纷奔赴日本,考察丰田生产方式,总结出准时生产制(Just — in 一Time,JIT ) ,无库存生产方式(Stockless Production ),零库存(zero Inventories )等生产管理思想和运作方法。
这些研究推动了丰田生产方式的传播,使各国企业汽车及家电生产效率得到改善和提高.中国第一汽车集团公司和东风汽车公司都极力推行JIT 和“一个流”,取得了一定成效。
但是,学习者和模仿者与丰田汽车公司始终存在差距。
其原因除了环境差别之外,主要是未能把握丰田生产方式的实质,因此只能做到“形似”,而不能做到“神似”.丰田方式最重要的是它的经营理念,一切具体做法都源自理念。
丰田的运营管理模式案例
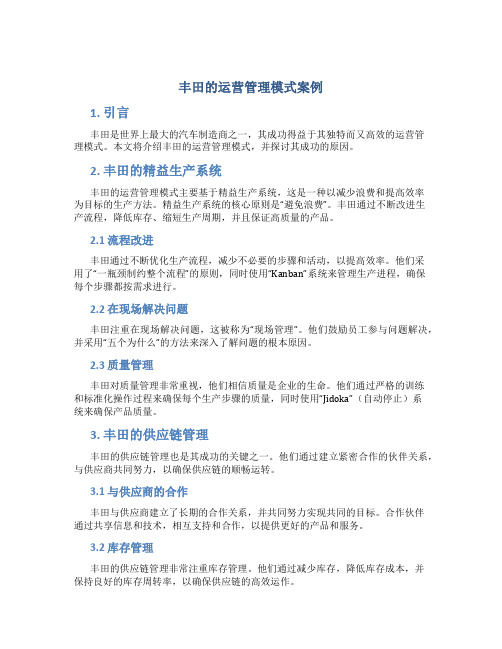
丰田的运营管理模式案例1. 引言丰田是世界上最大的汽车制造商之一,其成功得益于其独特而又高效的运营管理模式。
本文将介绍丰田的运营管理模式,并探讨其成功的原因。
2. 丰田的精益生产系统丰田的运营管理模式主要基于精益生产系统,这是一种以减少浪费和提高效率为目标的生产方法。
精益生产系统的核心原则是“避免浪费”。
丰田通过不断改进生产流程,降低库存、缩短生产周期,并且保证高质量的产品。
2.1 流程改进丰田通过不断优化生产流程,减少不必要的步骤和活动,以提高效率。
他们采用了“一瓶颈制约整个流程”的原则,同时使用“Kanban”系统来管理生产进程,确保每个步骤都按需求进行。
2.2 在现场解决问题丰田注重在现场解决问题,这被称为“现场管理”。
他们鼓励员工参与问题解决,并采用“五个为什么”的方法来深入了解问题的根本原因。
2.3 质量管理丰田对质量管理非常重视,他们相信质量是企业的生命。
他们通过严格的训练和标准化操作过程来确保每个生产步骤的质量,同时使用“Jidoka”(自动停止)系统来确保产品质量。
3. 丰田的供应链管理丰田的供应链管理也是其成功的关键之一。
他们通过建立紧密合作的伙伴关系,与供应商共同努力,以确保供应链的顺畅运转。
3.1 与供应商的合作丰田与供应商建立了长期的合作关系,并共同努力实现共同的目标。
合作伙伴通过共享信息和技术,相互支持和合作,以提供更好的产品和服务。
3.2 库存管理丰田的供应链管理非常注重库存管理。
他们通过减少库存,降低库存成本,并保持良好的库存周转率,以确保供应链的高效运作。
3.3 物流和配送丰田的物流和配送系统也是其供应链管理的重要组成部分。
他们通过优化物流运作和采用先进的配送技术,确保产品能够按时交付给客户。
4. 丰田的人力资源管理丰田认为人力资源是企业成功的重要组成部分,因此他们非常注重人力资源的管理和培养。
4.1 培训和发展丰田为员工提供全面的培训和发展机会,以提高他们的技能和知识。
(运营管理)运营管理之丰田案例分析
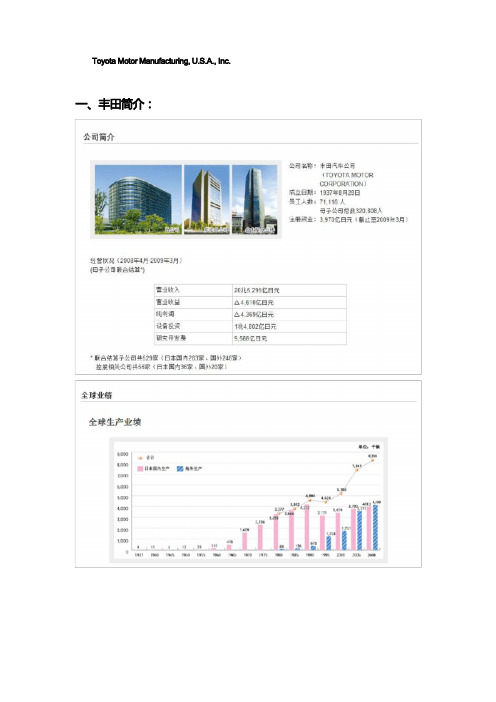
从上图中可以看出,丰田在全球27 个国家和地区(不包括日本本土)总共设有53 家工厂,而这其中,美国一个国家就有10 家工厂,占比接近20%。
下图是丰田在北美地区的工厂列表丰田品质:丰田汽车以其享誉全球的丰田品质备受世界各国人民的信赖与爱慕。
这归功于丰田人“顾客至上”的理念和由此形成的在开辟、生产、销售及服务各领域中的综合实力。
通过下图来简要了解一下丰田的生产方式——TPS。
1、座椅挂钩设计问题;2、供应商供应的座椅挂钩质量存在缺陷;3 、丰田汽车美国公司员工安装操作存在问题。
1、是否是设计问题首先我们需要确认是否是座椅或者座椅挂钩的设计问题导致的。
根据案例可知,KFS 是丰田汽车公司座椅的惟一供应商,地处日本的Tsutsumi 工厂使用同样的设计方式,但是并未遇到类似问题。
因此可以判断美国工厂的座椅问题不是由挂钩的设计问题所导致。
2、是否是质量问题接下来,我们将目标锁定在坐椅或者座椅挂钩本身的质量问题上。
如果确认是产品本身的质量问题,需要迅速与质量管控部门(Quality Control)、进货检查部门、KFS 一起讨论解决问题的方法。
请KFS 限期解决,KFS 方面,认真研究浮现质量问题的关键点所在并试图改进,而丰田工厂的质量管控部门和进货检查部门则需要改进进货审查的标准,保证在产品到货时能第一时间发现潜在质量问题,避免问题的进一步升级。
3、员工安装操作问题不可否认,在安装操作环节,也是有可能发生问题的。
在确保产品质量无问题的基础上,我们需要检查作业人员是否存在误操作问题。
由于Final 2 刚刚接受一批新团队成员,新手操作不熟练非常可能导致浮现座椅问题。
如果确系是该方面的问题,要立刻对作业人员重新进行严格的操作培训,同时加强部门抽查和监管制度,派有经验的老员工在生产线上进行审查和指导。
丰田TPS 生产方式的两大核心是自动化和准时化生产。
准时化生产即JIT (just in time)生产方式。
运营管理之丰田案例分析
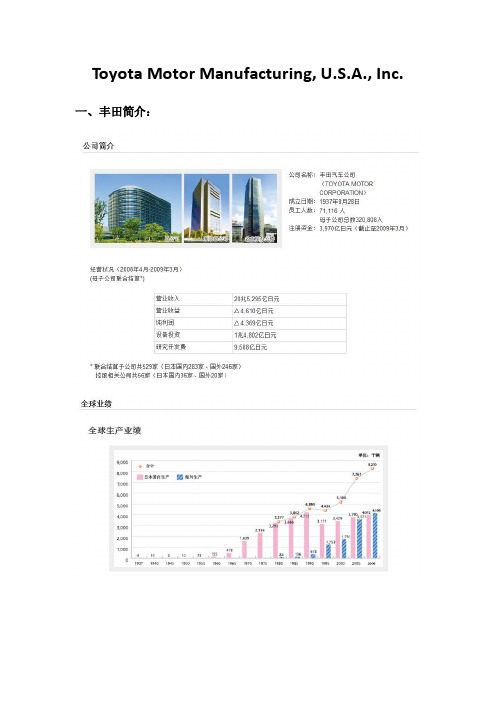
Toyota Motor Manufacturing, U.S.A., Inc.一、丰田简介:从上图中可以看出,丰田在全球27个国家和地区(不包括日本本土)总共设有53家工厂,而这其中,美国一个国家就有10家工厂,占比接近20%。
下图是丰田在北美地区的工厂列表丰田品质:丰田汽车以其享誉全球的丰田品质备受世界各国人民的信赖与喜爱。
这归功于丰田人“顾客至上”的理念和由此形成的在开发、生产、销售及服务各领域中的综合实力。
通过下图来简要了解一下丰田的生产方式——TPS。
二、导致丰田美国工厂座椅问题的原因1、座椅挂钩设计问题;2、供应商供应的座椅挂钩质量存在缺陷;3、丰田汽车美国公司员工安装操作存在问题。
三、如何解决座椅问题1、是否是设计问题首先我们需要确认是否是座椅或座椅挂钩的设计问题导致的。
根据案例可知,KFS 是丰田汽车公司座椅的唯一供应商,地处日本的Tsutsumi工厂使用同样的设计方式,但是并未遇到类似问题。
因此可以判断美国工厂的座椅问题不是由挂钩的设计问题所导致。
2、是否是质量问题接下来,我们将目标锁定在座椅或座椅挂钩本身的质量问题上。
如果确认是产品本身的质量问题,需要迅速与质量管控部门(Quality Control)、进货检查部门、KFS一起讨论解决问题的方法。
请KFS限期解决,KFS方面,认真研究出现质量问题的关键点所在并试图改进,而丰田工厂的质量管控部门和进货检查部门则需要改进进货审查的标准,保证在产品到货时能第一时间发现潜在质量问题,避免问题的进一步升级。
3、员工安装操作问题不可否认,在安装操作环节,也是有可能发生问题的。
在确保产品质量无问题的基础上,我们需要检查作业人员是否存在误操作问题。
由于Final 2刚刚接受一批新团队成员,新手操作不熟练非常可能导致出现座椅问题。
如果确系是该方面的问题,要立刻对作业人员重新进行严格的操作培训,同时加强部门抽查和监管制度,派有经验的老员工在生产线上进行审查和指导。
丰田生产运作管理案例分析
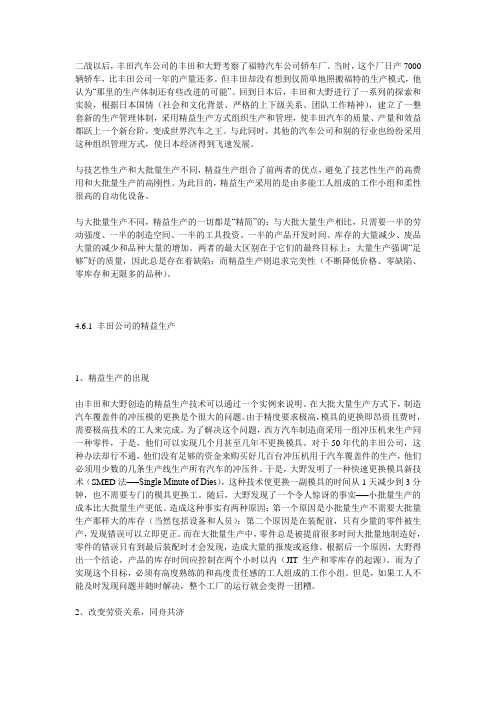
二战以后,丰田汽车公司的丰田和大野考察了福特汽车公司轿车厂。
当时,这个厂日产7000辆轿车,比丰田公司一年的产量还多。
但丰田却没有想到仅简单地照搬福特的生产模式,他认为“那里的生产体制还有些改进的可能”。
回到日本后,丰田和大野进行了一系列的探索和实验,根据日本国情(社会和文化背景、严格的上下级关系、团队工作精神),建立了一整套新的生产管理体制,采用精益生产方式组织生产和管理,使丰田汽车的质量、产量和效益都跃上一个新台阶,变成世界汽车之王。
与此同时,其他的汽车公司和别的行业也纷纷采用这种组织管理方式,使日本经济得到飞速发展。
与技艺性生产和大批量生产不同,精益生产组合了前两者的优点,避免了技艺性生产的高费用和大批量生产的高刚性。
为此目的,精益生产采用的是由多能工人组成的工作小组和柔性很高的自动化设备。
与大批量生产不同,精益生产的一切都是“精简”的:与大批大量生产相比,只需要一半的劳动强度、一半的制造空间、一半的工具投资、一半的产品开发时间、库存的大量减少、废品大量的减少和品种大量的增加。
两者的最大区别在于它们的最终目标上:大量生产强调“足够”好的质量,因此总是存在着缺陷;而精益生产则追求完美性(不断降低价格、零缺陷、零库存和无限多的品种)。
4.6.1 丰田公司的精益生产1、精益生产的出现由丰田和大野创造的精益生产技术可以通过一个实例来说明。
在大批大量生产方式下,制造汽车覆盖件的冲压模的更换是个很大的问题。
由于精度要求极高,模具的更换即昂贵且费时,需要极高技术的工人来完成。
为了解决这个问题,西方汽车制造商采用一组冲压机来生产同一种零件,于是,他们可以实现几个月甚至几年不更换模具。
对于50年代的丰田公司,这种办法却行不通,他们没有足够的资金来购买好几百台冲压机用于汽车覆盖件的生产,他们必须用少数的几条生产线生产所有汽车的冲压件。
于是,大野发明了一种快速更换模具新技术(SMED法──Single Minute of Dies),这种技术使更换一副模具的时间从1天减少到3分钟,也不需要专门的模具更换工。
生产运作管理案例分析--丰田
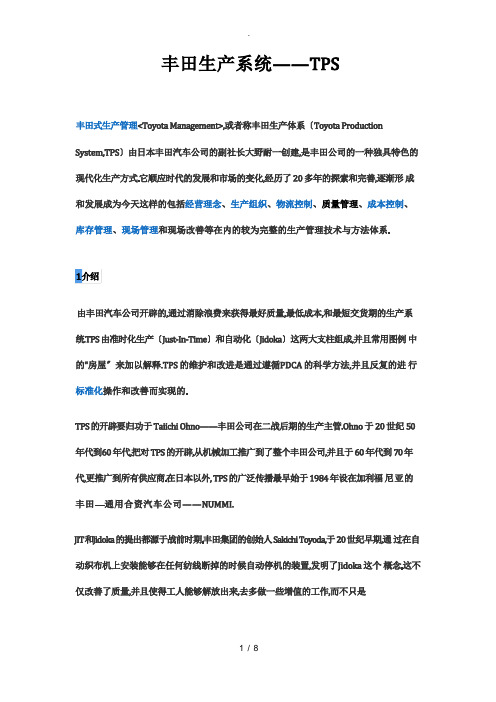
1990年《改变世界的机器》一书的出版使得TPS开始作为模X生产系统,在世界X围内得到迅速、广泛的认可,这本书是美国麻省理工学院对丰田生产系统五年的研究成
由丰田汽车公司开辟的,通过消除浪费来获得最好质量,最低成本,和最短交货期的生产系统.TPS由准时化生产〔Just-In-Time〕和自动化〔Jidoka〕这两大支柱组成,并且常用图例中的"房屋〞来加以解释.TPS的维护和改进是通过遵循PDCA的科学方法,并且反复的进行标准化操作和改善而实现的.
TPS的开辟要归功于TaiichiOhno——丰田公司在二战后期的生产主管.Ohno于20世纪50年代到60年代,把对TPS的开辟,从机械加工推广到了整个丰田公司,并且于60年代到70年代,更推广到所有供应商.在日本以外,TPS的广泛传播最早始于1984年设在加利福尼亚的丰田—通用合资汽车公司——NUMMI.
.
蕴涵在丰田式生产管理之中的隐性知识〔TacitKnowledge〕可以用四条基本规则来概括.这些规则指导着每一产品和服务所涉与的每一项作业、每一处衔接和每一条流程路线的设计,实施和改进.这四条规则如下:
规则一:所有工作的内容、次序、时间和结果都必须明确规定.
规则二:每一客户-供应商关系都必须是直接的,发送要求和得到回应的方式必须明确无误,非"是〞即"否〞.
<1>关于JIT的问题.丰田生产方式不仅仅是准时生产与看板管理,如果仅仅从形式去效仿看板管理是不能成功的.JIT是TPS核心问题之一,拉动生产是JIT的主要手段,也是大野耐一的典型代表作.但是JIT是不能脱离另一支柱人员自主化和改善而独立存在的.于是TPS的开辟必然是一个企业整体的、长期的行为.它是一个系统管理,是一个全员参加的、
丰田模式运营管理案例分析

丰田模式运营管理案例分析丰田模式是指丰田汽车公司在运营管理方面的一套成功经验和管理方法论,通过精益生产、持续改进和员工参与等核心理念,实现了高效、高质量和低成本的生产与运营。
下面将以丰田模式为例,进行运营管理案例分析。
1.丰田的精益生产丰田模式最重要的特点是精益生产,即通过降低浪费、提高效率来实现持续改进和高效生产。
丰田采用了“拉动生产”模式,即在订单完成之前不生产产品,从而降低库存和浪费。
同时,丰田通过“一分钟原则”实现了生产线上的连续流动,避免了生产中的停滞和浪费,提高了效率和产能。
通过精益生产,丰田成功实现了高产能和高质量的生产。
2.持续改进和员工参与丰田模式强调持续改进和员工参与,即通过发现问题、解决问题和改进流程来不断提高生产和运营效率。
丰田鼓励员工提出改进意见并实施,同时建立了问题解决机制,确保问题能得到及时解决。
丰田还实施了“直接横向传情第一”政策,即高层管理人员直接与工人沟通,了解他们的需求和困难,并解决问题。
通过持续改进和员工参与,丰田成功营造了学习型组织,提高了生产效率和员工满意度。
3.丰田供应链管理丰田模式中的供应链管理也是其成功的重要因素之一、丰田对供应商进行深度合作,实行“零库存”的供应链管理,即只有当订单确认时才向供应商下达生产指令,避免了过多的库存和资金占用。
同时,丰田还鼓励供应商进行技术创新,提供培训和支持,为供应链的高效运作提供了保障。
通过优化供应链管理,丰田实现了资源的最大效益和生产的高效运作。
4.丰田质量管理丰田模式中的质量管理是其成功的关键之一、丰田秉承“零缺陷”原则,强调质量的重要性,并通过质量控制圈和故障树分析等方法,不断改进产品和流程,提高产品质量和生产效率。
丰田还实行了“丰田道德标准”,质量责任不仅仅停留在质检部门,每一个员工都对产品质量负责。
通过质量管理,丰田成功树立了品牌形象,提高了产品竞争力。
综上所述,丰田模式以精益生产为核心,通过持续改进和员工参与,优化供应链管理和质量管理,实现了高效、高质量和低成本的生产与运营。
企业经营知识管理实践案例丰田管理模式

• 第二层含义是问题发生地称第二
现场。
• 第三层含义是为了解决问题利用
5W1H找到问题的原因及解决措施 称第三现场
31
“5S”活动-准时化生产基础
• 对现场不断地整理、整顿、清扫、
清洁、素养的循环。关键在于素养, 不仅是全员参加而要求全员实施。
• 制订“5S”工作标准、定期检查和评
• 主要手法
1. 方法研究- 程序分析、动作分析、动作经 济原则分析
2. 作业测定-时间分析、MOD法 3. 布置研究-搬运物流分析、配置分析 4. 生产线平衡调正-作业拆解与合并、PTS工
序平均化
22
从省人化到少化
1
2 3 1
2 3
手动操作 自动进给
23
制造过程的质量保证
• 树立质量要在本工序创出,确保后工序顺利作业
1. 为什么会过剩是平衡生产和次废品需求,
过剩生产说明由于人员和设备过多。
2. 表面效率和实际效率
原来某工序生产100个,现通过努力增 产到120个,表面效率得到提高,但实 际祗需求(或生产线工艺节拍)100个, 这就是浪费。实际效率没提高,所以整 体效率重于个人效率
16
缩短作业切换时间
调正40 2
CJK40 3
Z250 2
H62
1
H62
2
T420 1
T420 1
QR100 1
生产能力 1800 2700 1800 900 1800 900 900
编制
审核
批准
21
•I工E业(工工业程(工Ind程us)tr手ial 法Engineering )是对人
员、物料、设备、信息等进行设计和改善 效率、成本、质量的一门科学
2023年企业经营知识管理实践案例丰田管理模式

共同决策决策
共同决策是丰田管理模式的核心之一。在共同决策中,公司的决策不仅仅由高层管理层来做出,而是由各个层级的员工共同参与和贡献。
1. 充分听取员工意见丰田重视每个员工的意见和建议,在制定重要决策时充分听取员工的意见。通过设立各种沟通渠道和机制,公司鼓励员工提出自己的想法和改进建议。这种开放式的决策模式使得员工感到被尊重和重视,并促进了更好地集思广益。
激发员工参与
开放沟通渠道
丰田管理模式
创新意识
培训和发展
员工参与
激励机制
1.丰田管理模式:培养员工创造力和自主性丰田管理模式注重培养员工创造力和自主性。丰田鼓励员工参与问题解决和改进流程的决策过程,通过全员参与的方式激发员工的创新能力。2.丰田:信任与资源驱动员工创新,推动持续改进与创新通过信任员工的创新想法和提供相应的资源支持,丰田有效地激发并发掘员工的潜力,从而推动公司持续改进和创新。
2. 提升员工的满意度和归属感:让员工参与决策意味着给予他们发言权和权力,从而满足他们的参与需求,增强员工的归属感和满意度,有利于员工的持续发展和稳定性。
优化组织决策过程:员工参与决策能够促进信息共享和沟通,减少汇报层级和决策过程中的不必要环节,提高决策效率和灵活性。
提倡员工参与决策的必要性
员工参与决策的实施效果
2023/8/7
Introduction to Toyota Management Mode
丰田管理模式简介
沉默之建
The Construction of Silence TEAM
Contents
Toyota participates in employee decision-making
丰田参与员工决策
运营管理之丰田案例(中文版)

丰田汽车制造、美国公司。
运行前的那个周五第118肯塔基赛马,Doug Friesen经理大会丰田的乔治敦,肯塔基州,植物,是接近最后的组装线,闪亮的凯美瑞成形。
他听到一阵欢呼声.团队成员行上挥舞着他们的手工具朝着一个招牌,上面写着“不加班的转变.“微笑广泛,弗瑞森同意:每个人都在工厂肯定值得一个轻松的周末德比.工厂最近一直忙碌的,因为它既提供的全新凯美瑞轿车的销售和增加旅行车版本为欧洲以及北美市场。
加班也有是必要的在本周初来弥补生产损失,因为线利用率低于预期目标。
除了这些直接的问题,越来越多的汽车坐在了与有缺陷的或者没有座位。
座位的问题已经紧急会议的主题叫做迈克DaPrile,组装厂的总经理,那天早上,1992年5月1日。
在会议上,弗瑞森从关键人物知道第一手的情况在植物和座椅供应商。
然后他花了一个下午在商店的地板上更多地了解问题,而问题的讨论仍历历在目.在一天结束的时候,很明显,弗瑞森座位问题需要解决一劳永逸,麻烦的是,试图这样做可能会影响线的利用率。
这并不是第一个艰难的著名的丰田生产系统遇到问题,也不会是最后一次.但这个座位问题尤其脆弱,无疑将在接下来的一周Friesen关注的需求。
背景早在1980年代,日本汽车生产商考虑在北美生产汽车。
日本的巨大的贸易不平衡导致的政治压力,而这样的经济可行性投资改善了快速上涨的日圆。
当时,然而,目前尚不清楚日本以外的汽车生产可能达到他们辛苦赚来的以低成本高质量的声誉.这个问题还远未解决1985年,丰田汽车公司(TMC)公布了计划开一个8亿美元的绿地植物在肯塔基州。
(见表1)因此,公司的努力有效地移植其独特的生产系统牧草的国家成为世界观看现场实验。
1988年7月,丰田汽车制造、美国(TMM)开始批量生产1300英亩网站在乔治敦,列克星敦附近.工厂的年产量200000丰田凯美瑞轿车,这将取代日本进口的大部分相同的模型。
预计1992年,TMM的供应240000全新凯美瑞,其销售额增长超过20%自模型改变1991年秋季。
丰田公司运营管理案例分析
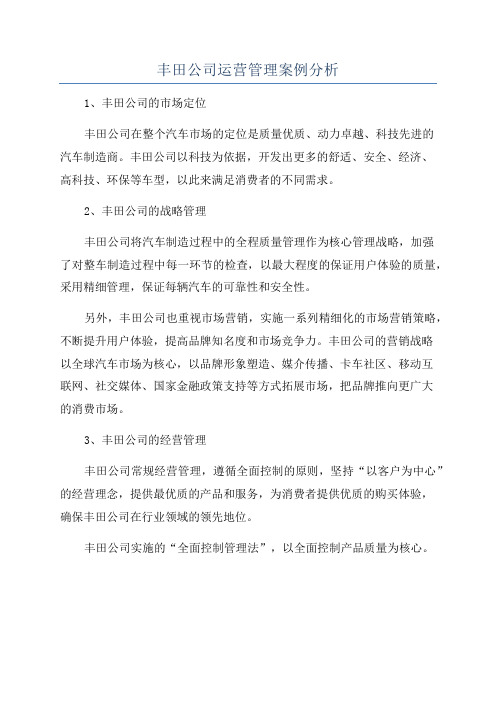
丰田公司运营管理案例分析
1、丰田公司的市场定位
丰田公司在整个汽车市场的定位是质量优质、动力卓越、科技先进的
汽车制造商。
丰田公司以科技为依据,开发出更多的舒适、安全、经济、
高科技、环保等车型,以此来满足消费者的不同需求。
2、丰田公司的战略管理
丰田公司将汽车制造过程中的全程质量管理作为核心管理战略,加强
了对整车制造过程中每一环节的检查,以最大程度的保证用户体验的质量,采用精细管理,保证每辆汽车的可靠性和安全性。
另外,丰田公司也重视市场营销,实施一系列精细化的市场营销策略,不断提升用户体验,提高品牌知名度和市场竞争力。
丰田公司的营销战略
以全球汽车市场为核心,以品牌形象塑造、媒介传播、卡车社区、移动互
联网、社交媒体、国家金融政策支持等方式拓展市场,把品牌推向更广大
的消费市场。
3、丰田公司的经营管理
丰田公司常规经营管理,遵循全面控制的原则,坚持“以客户为中心”的经营理念,提供最优质的产品和服务,为消费者提供优质的购买体验,
确保丰田公司在行业领域的领先地位。
丰田公司实施的“全面控制管理法”,以全面控制产品质量为核心。
- 1、下载文档前请自行甄别文档内容的完整性,平台不提供额外的编辑、内容补充、找答案等附加服务。
- 2、"仅部分预览"的文档,不可在线预览部分如存在完整性等问题,可反馈申请退款(可完整预览的文档不适用该条件!)。
- 3、如文档侵犯您的权益,请联系客服反馈,我们会尽快为您处理(人工客服工作时间:9:00-18:30)。
丰田汽车制造、美国公司。
运行前的那个周五第118肯塔基赛马,Doug Friesen经理大会丰田的乔治敦,肯塔基州,植物,是接近最后的组装线,闪亮的凯美瑞成形。
他听到一阵欢呼声。
团队成员行上挥舞着他们的手工具朝着一个招牌,上面写着“不加班的转变。
“微笑广泛,弗瑞森同意:每个人都在工厂肯定值得一个轻松的周末德比。
工厂最近一直忙碌的,因为它既提供的全新凯美瑞轿车的销售和增加旅行车版本为欧洲以及北美市场。
加班也有是必要的在本周初来弥补生产损失,因为线利用率低于预期目标。
除了这些直接的问题,越来越多的汽车坐在了与有缺陷的或者没有座位。
座位的问题已经紧急会议的主题叫做迈克DaPrile,组装厂的总经理,那天早上,1992年5月1日。
在会议上,弗瑞森从关键人物知道第一手的情况在植物和座椅供应商。
然后他花了一个下午在商店的地板上更多地了解问题,而问题的讨论仍历历在目。
在一天结束的时候,很明显,弗瑞森座位问题需要解决一劳永逸,麻烦的是,试图这样做可能会影响线的利用率。
这并不是第一个艰难的著名的丰田生产系统遇到问题,也不会是最后一次。
但这个座位问题尤其脆弱,无疑将在接下来的一周Friesen关注的需求。
背景早在1980年代,日本汽车生产商考虑在北美生产汽车。
日本的巨大的贸易不平衡导致的政治压力,而这样的经济可行性投资改善了快速上涨的日圆。
当时,然而,目前尚不清楚日本以外的汽车生产可能达到他们辛苦赚来的以低成本高质量的声誉。
这个问题还远未解决1985年,丰田汽车公司(TMC)公布了计划开一个8亿美元的绿地植物在肯塔基州。
(见表1)因此,公司的努力有效地移植其独特的生产系统牧草的国家成为世界观看现场实验。
1988年7月,丰田汽车制造、美国(TMM)开始批量生产1300英亩网站在乔治敦,列克星敦附近。
工厂的年产量200000丰田凯美瑞轿车,这将取代日本进口的大部分相同的模型。
预计1992年,TMM的供应240000全新凯美瑞,其销售额增长超过20%自模型改变1991年秋季。
新凯美瑞加入的中型家庭轿车,这构成了三分之一的美国汽车市场,并返回平均17%税前利润margin1平均标价18500美元。
第一次,在1992年3月,TMM开始生产新凯美瑞的旅行车版本只在丰田的全球网络。
丰田生产System2自成立以来,丰田一直努力为更多的人“更好的汽车。
“这意味着汽车生产会议不同的客户偏好和完美的质量。
这进一步意味着交付汽车在一个合理的价格和完美的时机。
这个雄心勃勃的目标似乎几乎难以捉摸的第二次世界大战之后,因为大多数日本人买不起车即使在成本。
此外,中国的劳动生产率仅为美国的八分之一。
从本质上讲,丰田要求大幅削减成本,但没有美国公司喜欢的规模经济。
它需要一个全新的经济来源来满足客户提供品种、质量和及时性,所有在一个合理的价格。
丰田生产系统(TPS)演变为丰田的应对这一挑战,并成为在所有员工有一个公共的参考框架。
TPS旨在由彻底消除浪费,降低成本,在生产环境中倾向于场无声无息雪球的小雨。
浪费生产过剩,例如,不仅占用流动资金的库存,但这需要仓库存储空间,叉车移动货物,材料处理程序操作卡车,电脑跟踪库存地点,人员维护计算机系统,等等。
此外,生产过剩往往隐藏真正的瓶颈的位置,因此邀请投资错误的设备,导致产能过剩。
识别浪费在现实中,然而,没有简单的事。
因此,TPS提供两个指导原则,以促进这一重要过程。
第一次是准时制(JIT)生产的原则:生产只需要什么,只需要多少,只有当它是必要的。
任何偏离真正的生产需要被谴责为浪费。
第二个中的的原则是:做任何生产问题立即不证自明的,停止生产时发现的问题。
换句话说,质量在生产过程中的坚持大楼并谴责任何偏离value-addition浪费。
TPS定义的“需要”和“价值”从下一站的角度线,也就是说,直接客户。
对生产环境中这些TPS原则反映了两个假设。
首先,真正的需求将偏离生产计划不可预知的,无论多么精心的计划是准备:因此JIT生产的美德。
其次,问题会不断出现在商店的地板上,使偏离计划操作条件不可避免的:因此中的的美德。
TPS,当然,鼓励不断改进计划的过程,但它也强烈强调提醒工厂人偏离计划生产如何继续。
实现TPS原则,丰田采用各种工具,许多描述之后。
JIT生产,这些工具是用来保持信息流靠近身体流的部分。
零件从而从下游根据实际使用情况,而不是推从上游基于远程从车间计划安排。
这样的安排需要上游站在中间部分可以改变通过最少的设置时间。
因此,创建一个流生产过程是一个TPS的先决条件。
中的工具的目的是帮助直接检测和促进视觉控制问题。
正常工作,正常的操作特点和理解。
因此,TPS的另一个前提是标准化流程和记录标准显然。
最后,TPS取决于人类的基础设施,象征丰田公司口号:“好思想、好产品。
“植物练习JIT和中的原则是非常容易关闭,并将瘫痪,没有人能够及时解决接触问题,完全和系统。
丰田因此灌输“好主意”,所有员工通过高级管理培训和内部培训项目。
这些努力培养渗透到组织的两个强大的态度:坚持事实,问题的根源。
一个典型的讨论一个问题会“让我们去看它”,然后聚集在“五个为什么”运动。
这个练习是问一连串的“为什么”的问题,直到问题的根源是识别和对策决定(见表2)。
有条理的思维超越事后解决问题。
它使人们寻求改善:改变更好。
在丰田,只要任何人建立一种标准的方式做一份工作,这个人开始主动拆除,安装一个更好的方式。
改善是不可或缺的在不断追求TPS的目标和无限期。
乔治敦大学提高发展人类基础设施在移植TPS TMC最重要的优先级去乔治敦,一些早期的决策就证明了这一点。
首先,台湾记忆体公司分配给TMM的1987年凯美瑞Tsutsumi工厂在日本已经批量生产。
其次,它复制Tsutsumi线在TMM尽可能。
第三,它设置一个故意加大进度缓慢。
因此,在Tsutsumi TMC能找到人,根据自己的经验,能够证明TMM工厂如何解决遇到的问题。
施工正在进行中在乔治敦在1986年年初,TMM发起了招聘和培训计划(耗尽一个拖车办公室)。
它与高层管理者开始和继续核心业务人员,这些人主要来自业内人士和形成TMM的核心业务。
他们第一次接触TPS发生在长达一个月之旅,道格·弗瑞森的反应很典型: 我在,建立汽车,简直不敢相信我所看到的60%。
令人难以置信的快节奏,工厂的运行,我离开美国公司有更多的自动化。
好东西,我看见只是常识,没什么大不了的。
我的眼睛不开放。
接下来,TMC发送Tsutsumi乔治敦,数百人。
这些trainers-on——贷款TMM监察人员一对一的指导和强化TPS基础知识。
每个TMM经理还搭配了一个从TMC协调员,他仍然在肯塔基州几年。
这些协调员被指控开发同行只有persuasionCnot去做自己的事情。
这种强烈的个人方法带来了TMM大多数人的“大开眼界”。
台湾记忆体公司的计划展现在他们面前,他们可以见证行动在他们周围的环境,欣赏出人意料的积极成果,他们的教练背后这些结果的意义。
虽然每个人都有一个独特的事件,标志着一个转折点,他们聚集有一点:“TPS隔离问题的人,从而使人们关注解决问题。
”TMM的总裁张富士夫和TPS的传教士,描述他的愿景:我们幸运的是到目前为止还没有看到任何惊喜。
我相信TPS的普遍性及其交付高质量的能力。
开发TMM,我们把安全高于一切,开始与质量。
我们再增加生产力的目标。
现在,我们的汽车都一样的在质量、我们只是稍微落后于生产力。
我们正在搬到下一个stepCworrying 成本和传播TPS本地供应商。
我希望,我们可以使TMM成为一个真正的美国公司,贡献给社区。
1992年初,乔治城的巨大复杂的雇佣了超过4000人,代表1.5亿美元的年度工资。
在工厂的后院,建设正在进行双TMM的能力。
操作在乔治敦大学,提供发动机和传动系植物轴组装厂,而执行的钣金冲压、塑料成型、焊接,绘画,和装配操作。
在这些直接操作以及在他们的支持函数(见表3),TPS部署为一套管理工具是每天练习。
迈克DaPrile评论道:tps突出问题,这样人们就可以很容易看到它们。
困难的部分是教学,这样人们实践它,因为他们想要,而不是因为他们必须。
教得很好,你必须了解人们很深,随着时间的推移。
在这个过程中,我们都成为这里的学生。
事实上,我已经学会了比我更多的在过去的五年里我花了25年与另一个汽车公司。
组装组装业务进行沿353站输送线,在五英里长和几个连接的折线段:修剪线,底盘线,和最后组装线。
相邻线部分解耦了几辆车,和整个生产线从动力传动系植物缓冲和油漆线大约半个小时的生产。
目前线57秒的周期时间线操作,从60启动。
装配和部分处理需要769的团队成员,他们支付的平均17美元一个小时(不包括福利),加上加班的50%的溢价。
团队通常有四个成员,一个团队的领导者,他们收到了5%到8%的溢价。
监督这些团队领导和团队成员在两班倒,道格·弗瑞森与10助理经理和46组领导人密切合作(见表3)。
普通转变持续了525分钟,包括无薪的45分钟午餐时间和两个15分钟的休息时间。
当一个团队成员不得不离开移动线,团队领导填写,位置探测器。
流水线上的每个站中的体现和改善工具。
标准化工作图表张贴每个工作车站附近,站的周期时间,工作任务的顺序,执行在一个周期时间。
彩色胶带标记区域的地板上指定,看到的一切都是,促进了“4 ss(筛选、排序、清除spic-and-span)。
“在结果的工作环境,任何偏离正常情况下突出视觉效果。
绿线和红色线成直角的组装线标志着每个工作的开始和结束。
团队成员将开始一个周期的工作当一辆车到达绿线和红线的完成所有任务。
黄线之间的标志着一个点,70%的工作必须完成。
如果在这个背后的团队成员是黄线或发现其他问题,他或她把安灯线:一根绳子沿着装配线运行工作区域。
安灯拉打开闪光灯,引发大声的音乐,并照亮了工作站的“地址”安灯板(见表4),然后组长冲工作站问问题是什么,如果是矫正,关掉灯,音乐再次拉安灯线。
然而,如果团队领导者不能立即解决问题,他或她离开了安灯,允许停在红线的线段,也就是说,当其他工作站完成周期。
这个罢工立刻吸引了组长的注意。
团队成员平均把安灯线近一个十几次转变,通常,其中一个安灯将导致实际的线路中断。
道格·弗瑞森解释道: 在我们的系统中,每个团队成员都是侧重于建立质量通过安灯拉。
然后,我们呼吁团队领导做出迅速的反应,和组领导人采取对策,防止问题的再次发生。
我们的经理的工作是保持这条线,这意味着发展的人。
很容易说“做这个,做那个,但什么也不会发生,除非我们跟进,因为人们会故态复萌。
领导意味着站几个小时的人,帮助他们获得新方法。
它需要耐心。
生产控制生产控制的任务(PC)部门以必要的部分TMM操作,以便正确的汽车数量在正确的混合可以即时交付给销售公司。