油管接头注塑模具设计.doc
管接头塑料模设计

前言1塑料注射模具简介1.1 概述模具工业是国民经济的基础工业,被称为“工业之母”。
21世纪模具制造行业的基本特征是高度集成化智能化、柔性化、和网络化,追求的目标是提高产品质量及生产效率,缩短设计及制造周期,降低生产成本,最大限度地提高模具制造业的应变能力,满足用户需求。
近年来我国的模具事业也在不断地飞速向前发展。
1.2 注射模具基本简介注射成型也称为注塑成型,其基本原理就是利用塑料的可挤压性与可模塑性,首先将松散的粒状或粉状成型物料从注射机的料斗送入高温的机筒内加热熔融塑化,使之成为粘流态熔体,然后在柱塞或螺杆的高压推动下,以很大的流速通过机筒前端的喷嘴注射进入温度较低的闭合模具中,经过一段保压冷却定型时间后,开启模具便可以从模腔中脱出具有一定形状和尺寸的塑料制品。
它与挤出和压延成型方法相比,注射成型可以用来生产空间几何形状非常复杂的塑料制品,而挤出和压延则主要用来成型截面尺寸一定长度连续的二维塑料制品。
将注射成型与压缩和压注成型相比,它又具有应用面大、成型周期短、生产效率高、模具工作条件可以得到改善,以及制品精度高和生产条件比较好、生产操作容易实现机械化等多方面的优势。
在中空吹塑成型中,注射成型还常常被用来生产吹塑所用的型坯。
1.3 注射成型的地位注射成型在整个塑料制品生产行业占有非常重要的地位,目前,除少数几种塑料外,几乎所有的塑料品种都可以采用注射成形。
据统计,注射制品约占所有塑料制品总产量的30%,全世界每年生产的注射模数量约占所有塑料成型模具数量的50%。
早期的注射成型方法主要用于生产热塑性塑料制品,随着塑料工业的迅速发展以及塑料制品的应用范围不断扩大,目前的注射成形方法已经推广应用到热固性塑料制品和一些塑料复合材料制品的生产中。
例如,日本的酚醛(热固性塑料)制品生产过去基本上依靠压缩和压注方法生产,但目前已经有70%被注射成型所取代。
注射成型方法不仅广泛应用于通用塑料制品生产,而且就工程塑料而言,它也是一种最为重要的成型方法。
塑料油管注塑模具设计

6 9
塑料 油 管 注 塑 模 具 设 计
朱 华 泽
( 安科技大学理学院 , 安 西 西 705 ) 10 4
摘要
Байду номын сангаас
通 过 分 析 塑料 油 管 的使 用 要 求 和 结 构 特 点 , Po E分 模 的 方 法 完 成 了 塑料 油 管 的 注 塑模 具 设 计 , 用 r/ 阐述
() 3 锁模 力校 核 高 压塑 料熔 体 充 入模 型 腔 时 , 注 塑机 轴 向上 在
() 4 冷却 参 数 : 却 回 路 管 道 直 径 8mm; 却 冷 冷 剂 温度 2 ℃ ; 凝 时间 2 . 5S 5 冷 6 8 。
2 注塑 机 的选择 与 校核
2 1 注塑机 的选 择 .
度要 求 较 高 , 因此 设 计 难 度 较 大 。笔 者 使 用 模 具
C D设 计技 术 , 塑料 油管 注塑 模具 进行 了设 计 。 A 对
了该模 具分型面的选择 、 浇注 系统和成型 零件 的设计 、 侧抽 芯 的设 计及 有关 计算 。生产 实践 证 明, 该模 具结 构 简单
紧凑 , 工作 可靠, 作方便 , 操 成型的塑料件质 量好 。
关 键 词 注 塑 模 具 分 型面 成型零件 抽 芯 机 构
随 着塑 料工 业 的发 展 , 料 在 各 类 产 品 中的应 塑 用越 来越 多 , 涉及 领 域 已从 产 品 的外 壳 制造 延 伸 其 到产 品 的 内部 零 件 , 成 为 制 造 某些 元 器 件 的重 要 并 原料 之一 。塑 料元 件 多为 配合 件 , 结构 比较 复杂 , 精
孔直 径 1 0mm。 0
油管接头的模具设计
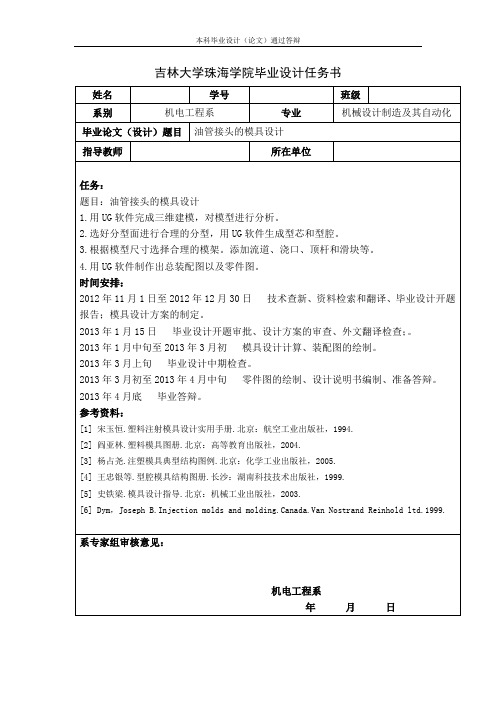
[5] 史铁梁.模具设计指导.北京:机械工业出版社,2003.
[6] Dym,Joseph B.Injection molds and molding.Canada.Van Nostrand Reinhold ltd.1999.
系专家组审核意见:
机电工程系
年 月 日
2013年3月初至2013年4月中旬 零件图的绘制、设计说明书编制、准备答辩。
2013年4月底 毕业答辩。
参考资料:
[1] 宋玉恒.塑料注射模具设计实用手册.北京:航空工业出版社,1994.
[2] 阎亚林.塑料模具图册.北京:高等教育出版社,2004.
[3] 杨占尧.注塑模具典型结构图例.北京:化学工业出版社,2005.
4.用UG软件制作出总装配图以及零件图。
时间安排:
2012年11月1日至2012年12月30日技术查新、资料检索和翻译、毕业设计开题报告;模具设计方案的制定。
2013年1月15日 毕业设计开题审批、设计方案的审查、外文翻译检查;。
2013年1月中旬至2013年3月初 模具设计计算、装配图的绘制。
2013年3月上旬 毕业设计中期检查。
吉林大学珠海学院毕业设计任务书
姓名
学号
班级
系别
机电工程系
专业
机械设计制造及其自动化
毕业论文(设计)题目
油管接头的模具设计
1.用UG软件完成三维建模,对模型进行分析。
2.选好分型面进行合理的分型,用UG软件生成型芯和型腔。
3.根据模型尺寸选择合理的模架。添加流道、浇口、顶杆和滑块等。
油管接头注射模具设计

油管接头注射模具设计随着各门科学技术的进步和全球化经济的发展,制造业发生了深刻的变革,先进制造技术正在改变着传统的制造业。
进入二十一世纪以来,中国塑料工业取得了令世人瞩目的成就,实现了历史性的跨越。
蓬勃发展的中国塑料工业,在中国现代化经济建设中发挥着越来越大的作用。
塑料制品在人们的日常生活中随处可见,因此其注塑模具的需求也日益增多,市场前景广泛,而且因为不同塑件的外形不同,注塑模具也就有了很大的不同。
本设计是油管接头的注塑模具设计,通过注塑机注塑成形零件。
首先运用UG对塑件进行三维建模,再运用UG软件绘制塑件的模具总装配图。
介绍了注塑机的选用,塑件的选材,浇注系统的设计,分型面及型腔数目的设计,导向、脱模及冷却系统的设计等,以及对模具的校核。
随着塑料加工工业持续快速发展,塑料制品在工业、农业、军事及人民生活的各个领域得到广泛的应用,塑料制品的研究、生成与应用开发得到迅速发展,塑料模具的设计、制造技术也随之不断提高。
塑料制品业是一个新兴大行业。
随着我国国民经济持续高速发展已逐步发展壮大,自上世纪90年代以来,塑料行业一直保持在10%以上的增长速度,已成为轻工业的支柱产业之一。
随着CAD/CAM/CAE技术的引用,更是显著提高了模具设计的效率,减少模具设计过程中的失误,提高了模具和塑件的质量,缩短了生产周期,降低了模具和塑件的成本。
1 绪论1.1设计目的毕业设计是将学生在大学期间所学的知识进行的综合运用,让学生把课本知识与实践问题相结合,在掌握一定的设计方法体系和规范的前提下,进行综合运用的一次实践,是培养学生创新能力的重要环节。
本课题对我们机械制造及其自动化专业学生的基本目的是:通过综合运用塑料成型工艺及模具设计、机械制图、机械设计、机械原理、机械制造技术基础、模具材料及热处理、模具制造工艺、材料成型工艺、计算机辅助设计(UG) 等先修课程的知识,培养我们综合分析和解决塑料模具设计问题的独立工作能力,进一步巩固、加深和拓宽所学的知识。
毕业设计 毕业论文:管接头注塑模具设计说明书

管接头注塑模具设计【摘要】在现代工业中,模具工业已成为制造业的基础,这一观点随着全球制造业向我国转移的过程中以被越来越多的有识之士所意识到。
本论文介绍了管接头的注射模设计过程。
从型腔数量和布局的确定、注射机选择、浇注系统设计、模板及其标准件的选用、脱模及抽芯机构的设计、成型部件的设计等一一进行了详细的介绍。
【关键词】注射模;注塑机;管接头The Design of Union Injecting MoldingAbstract In the modern industry, the die industry has become the foundation of the manufacturing industry, this standpoint was along with the process that world manufacturing industry transfer to our country, which was been aware of by the private who more and more know. This paper introduces the main process of the injection mould designing of the union,recounts the detail as these followed:deciding of the number and the arrangement of the cavity, the detrusion components ,core-pulling outfit,and the feed system; selection of the machine for injection,the moulding boards and the standardized parts .Key words:injection mould;;Injection molding machine;union.目录引言 ............................................................................................................................... - 1 -1 塑件的工艺分析 ....................................................................................................... - 3 -1.1 塑料件的原材料分析 .................................................................................... - 3 -1.2 塑料件的结构、尺寸精度、及表面质量分析 ............................................ - 3 -2 成型设备的选择与模塑工艺参数的编制 ............................................................... - 4 -2.1 计算塑模的体积及浇注系统体积 ................................................................ - 4 -2.2 计算塑模的质量 ............................................................................................ - 4 -2.3 选用注塑机 .................................................................................................... - 5 -2.4 塑件注射成型工艺参数 ................................................................................ - 7 -3 成型零件工作尺寸的计算 ....................................................................................... - 8 -3.1 型腔的工作部位尺寸 .................................................................................... - 8 -3.2 型芯的工作部位尺寸 .................................................................................. - 10 -4模具结构方案的确定 ............................................................................................. - 11 -4.1 分型面的选择 .............................................................................................. - 11 -4.2 型腔的排列方式 .......................................................................................... - 12 -4.3 定模与动模结构的确定 .............................................................................. - 13 -4.4 浇注系统的设计 .......................................................................................... - 13 -4.4.1 主流道的设计 ................................................................................... - 16 -4.4.2 冷料井的设计 ................................................................................... - 17 -4.4.3 分流道的设计 ................................................................................... - 18 -浇口设计 ..................................................................................................... - 18 -4.5 推出方式的选择 .......................................................................................... - 20 -4.6 抽芯机构的设计 .......................................................................................... - 20 -4.6.1 斜导柱设计 ....................................................................................... - 21 -4.6.2 锁紧块的设计 ................................................................................... - 22 -4.6.3 斜顶杆的设计 ................................................................................... - 23 -4.7 冷却系统的设计 .......................................................................................... - 23 -4.8 排气系统的设计 .......................................................................................... - 24 -4.9 标准模架的选用 .......................................................................................... - 24 -4.9.1 模架尺寸的计算 ............................................................................... - 24 -4.9.2 模架的选择 ....................................................................................... - 25 -4.9.3 开模行程的校核 ............................................................................... - 25 -4.9.4 选标准模架 ....................................................................................... - 26 -4.9.5 模具总装图确定 ............................................................................... - 27 -5 注塑机的校核 ......................................................................................................... - 28 -5.1 注塑压力的校核 .......................................................................................... - 28 -5.2 注塑量的校核 .............................................................................................. - 28 -5.3 锁模力校核 .................................................................................................. - 28 -5.4 模具厚度的校核 .......................................................................................... - 29 -5.5 开模行程的校核 .......................................................................................... - 29 -结束语 ......................................................................................................................... - 30 -致谢 ............................................................................................................................. - 31 -参考文献 ..................................................................................................................... - 32 -引言塑料工业包含塑料生产和塑料制品生产(称为塑料加工或塑料成型工业)两个系统。
油管接头注塑模具设计.doc

油管接头注塑模具设计前言塑料制品在日常生活中是常常见到的,如在家用电器、仪器仪表、建筑器材、汽车工业、日用五金、通信器材以及医疗器械等众多领域,塑料制品的使用比例正迅猛增加。
这主要是因为以下原因:第一,塑料与金属材料相比有许多优点:容易加工,生产效率高;节约能源,绝缘性能好;质量轻,相对密度为1.0~1.4,比铝轻一半,比钢轻3/4,比强度高,具有突出的耐磨、耐腐蚀性等;第二,在日用和工业产品中,一个设计合理的塑料制品往往能代替多个传统金属结构件,加上利用工程塑料特有的性质,可以一次成型非常复杂的形状,并且还能设计成卡装结构,从而减少产品中装配的各种紧固件,降低了金属材料消耗量和加工及装配工时;第三,注塑加工是塑料加工中普遍采用的方法之一。
该方法使用与全部热塑性塑料和部分热固性塑料,制品数量比其他常规的金属成型方法要大得多。
由于注塑成型加工不仅产量多,而且适用于多种原料,能够成批、连续的生产,并且具有稳定的尺寸,容易实现生产的自动化和高速化,具有极高的经济效益。
因此目前工业产品非金属化、金属制品塑料化的趋势日益明显。
获得注塑制品的过程,称之为注塑成型或者注射成型,或者简单的称之为注塑。
注塑成型的基本过程是:颗粒状的高分子材料(以下简称为塑料)经过注塑机螺杆的挤压和加热,成为熔融状态的可以流动的熔体。
在螺杆的推动下,塑料熔体通过注塑机的喷嘴、模具的主流道、分流道和浇口进入模具型腔,成型出具有一定形状和尺寸制品的过程。
注塑的结果是生产出符合用户要求的塑料制品。
要想取得合格的制品,必须要有设计合理、制造精良的模具,还需要有何该模具配套的先进的注射设备(注塑机)以及合理的加工工艺。
因此人们常将,模具、注塑机以及工艺称之为注塑过程得以顺利进行的三个基本要素。
作为注塑成型加工的主要工具之一的注塑模具,在质量、精度、制造周期以及注塑成型过程中的生产效率等方面的恶水平高低,直接影响产品的质量、产量、成本及产品的更新换代,并最终决定着企业在市场竞争中的反映能力和速度。
塑料成型工艺与注射模具设计 (14)
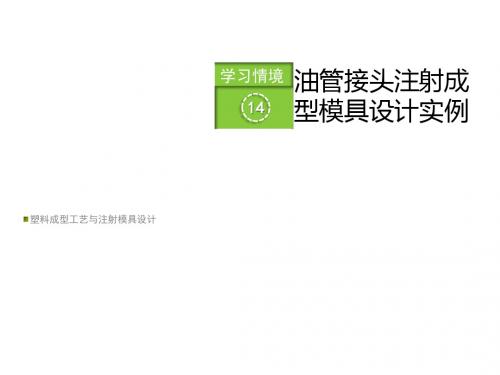
图14-3 油管接头零件图
2
确定模具结构方案
2.型腔数量的确定与排列形式 由于塑件的外形不很规则,各方向尺 寸也不一样,且右端螺纹需要侧向分型, 故采用图14-4所示的型腔排列方式。即 一模两腔,侧抽芯机构分布在右侧。
5
6 7 8 9 10
模具温度/℃
注射压力/ MPa 注射时间/s 高压时间/s 冷却时间/s 成型周期/s
90~120
80~130 20~90 0~5 20~60 50~160
1
拟定成型工艺方案、初选成型设备
2.计算塑件体积和质量 通过计算可知塑件体积单个约 32.11cm3,查相关手册知聚甲醛 (POM)的密度为1.41g/cm3,故塑 件单件重量为 32.11×1.41g=45.2751g≈45.28g。 本设计中的塑件的生产批量为大批 量生产,为尽量提高生产率,决定采 用一模两件的模具结构。2个塑件的总 质量为90.56g。考虑浇注系统的质量, 按经验公式计算得出总的塑料质量为 1.6×90.56g=144.90g。 根据以上数据,初选XS-ZY-125A 注射机,其主要技术参数,见表14-3。
1
拟定成型工艺方案、初选成型设备
2.塑料成型特征 聚甲醛(POM)的吸水性比聚酰胺 和ABS等塑料小,成型前可不必进行 干燥,其制品尺寸稳定性好,可以制 造较精密的零件。但聚甲醛熔融温度 范围小,熔融和凝固速度快,其制品 容易产生毛斑、折皱、熔接痕等表面 缺陷,并且收缩率大,热稳定性差。 这些都应在设备调整和工艺参数及模 具温度控制等方面采取相应措施。 综合来看,该塑件结构简单,无特 殊的结构要求和精度要求。在注射成 型生产时,只要工艺参数控制合适, 该塑件是比较容易成型的。
1
拟定成型工艺方案、初选成型设备
管接头注射模设计

管接头注射模设计通过对内外螺纹接头的结构特点和成型工艺的分析,阐述了该制件的模具设计思路。
该模具采用一模四腔的结构形式,主要特点为同时具备内外螺纹抽芯,成型内螺纹采用齿轮驱动自动脱螺纹机构,外螺纹采用哈夫块成型,并用斜导柱驱动脱模。
标签:塑料模具;成型工艺;螺纹抽芯1 塑件分析图1所示塑件为管类零件之间的管接头。
材料采用的是增强聚甲醛(POM+30%GF)。
聚甲醛性能:表面光滑,有光泽,表面硬度大,吸水率低,刚性好,韧性好,弯曲强度,耐疲劳性强度高,良好的滑动性,耐磨性非常优异,电性能优良,尺寸稳定性好,产品的尺寸精度高。
玻纤的加入使制品的刚性和高温机械性能大大提高,同时,线膨胀系数、成型收缩率及蠕变性能降低,从而提高了产品的尺寸稳定性,扩大了POM的使用范围,且保持了POM原有的耐磨性、耐疲劳性和耐药性。
该制件总体形状为圆筒形,塑件为内外螺纹接头,外侧壁有一段外螺纹(1.4375-16UN-2A),内侧壁有一段内螺纹(Tr30x1.6),均要求与接头配合良好。
设计时对模具结构设计和脱模方式要求较高,本设计的难点是总体模具结构的设计和内外螺纹的成型设计,同时还要兼顾考虑冷却系统的设计。
2 模具总体结构的设计2.1 模具分型面的选择该制件为壳体类零件,拐角处都是圆弧过渡。
考虑内螺纹的脱模问题,选择垂直于轴线的截面作为分型面,同时考虑到脱螺纹的止转,以及模具制造的问题,应将带有三个槽的φ41.5×2.5mm的凸缘设计在动模上,以保证脱螺纹的止转问题,便于成型后的脱模。
综上所述,确定该塑件的分型面如图2:2.2 确定型腔的数量及流道方式考虑该制件大批量生产,本塑件在注射时采用“一模四腔”。
塑件的外螺纹采用哈夫块的形式,因此四个型腔应排成一行。
考虑到动模设置滑块的问题,为了便于加工及顺利脱模,因此将分流道设置在定模,并且选用截面形状为半圆形分流道,并且采用圆弧过渡的流道,因此将分流道设计成S型,综合考虑浇注系统、模具结构的复杂程度等因素,拟采取如图3的流道及型腔布局方式:2.3 抽芯机构设计该塑件包含内外螺纹,这會阻碍成型后塑件从模具中脱出。
注塑模具毕业设计(四通管接头)

前言模具工业是国民经济的基础工业,被称为“工业之母”。
传统的模具制造技术,主要是根据设计图纸,用仿型加工、成形磨削以及电火花加工方法来制造模具。
而现代模具不同,它不仅形状与结构十分复杂,而且技术要求更高,用传统的模具制造方法显然难于制造,必须借助于现代科学技术的发展,采用先进制造技术,才能达到它的技术要求。
当前,整个工业生产的发展特点是产品品种多、更新快、市场竞争剧烈,因此提出了以数字化为主要因素的数字化塑性成形技术体系,设计和制造模具的数字化技术是实施数字化的关键,以便适应市场对模具制造的短交货期、高精度、低成本的迫切要求。
塑料模具又是整个模具行业中的一支独秀,发展极为迅速。
作为机械专业的学生,对模具设计的了解是必须的。
本设计就是利用课本中的理论,和毕业实习基地(湘潭塑料二厂)的所见,及前辈的宝贵经验设计出来的一套工用塑件的模具。
通过对塑件的分析,确定用一模一腔注射成型该塑件。
同时为了锻炼一下自己的能力,以后更加复杂的设计打点基础。
本设计严格按照模具设计的步骤,及模具设计中的要求来设计的:塑件工艺性的分析、型腔数量的确定、分型面的确定、浇注系统的设计、成型零件的设计等,这一整套的程序下来,感觉自己这方面的知识丰富了不少。
同时在设计中也要求对机械的相关知识有相当的了解:机械制图、公差与配合、机械制造、材料成型、数控技术等。
总之,在这次毕业设计过程中,我感觉充实了不少。
希望能为自己的研究生学习打下更好的基础。
1 概述1.1 塑料工业简介塑料工业是当今世界上增长最快的工业门类之一。
自从聚氯乙烯塑料问世以来,随着高分子化学技术的发展以及高分子合成技术、材料改进技术的进步、愈来愈多的具有优异性能的高分子材料不断涌现,从而促进塑料工业的发展。
模居室利用其特定形状去成型具有一定形状和尺寸的制品的工艺装备或工具,它属于型腔模的范畴。
通常情况下,塑件质量的优劣及生产效率的高低,其模具的因素占80%。
然而模具的质量的好坏又直接与模具的设计与制造有很大关系。
输油管接头注射模具设计

第一章绪论1.1 输油管接头造型展示图1.1 三维图图1.2 三维图1.2 课题研究的意义和目的目前,世界模具市场仍供不应求。
近年来,世界模具市场总量已超过700亿美元,其中美国、日本、瑞士等国一年的出口模具约占本国模具总产值的三分之一。
因此,研究和发展模具技术,提高模具技术水平,对于促进国民经济的发展有着特别重要的意义。
美国工业界认为“模具工业是美国工业的基石”,日本把模具誉为“进入富裕社会的原动力”,德国则冠之为“加工工业中的帝王”,在欧洲其他一些发达国家模具被认为“磁力工业”由此可见模具在各国国民经济中的重要地位[1]。
经过本次毕业设计可以掌握机械工艺装备设计的一般方法及基本工序。
巩固和加强机械零件设计、机械制造工艺与装备、机械制图、模具设计和模具制造工艺等专业理论知识在实际生产中应用的能力。
巩固和加深对机械二维、三维的制图能力。
设计过程中锻炼查阅文献和资料自我设计的能力,培养和提升我们的创新能力,增强我们独立思考问题和解决问题的能力。
所以认真完成本次设计非常重要。
1.3 本课题国外发展概况1.3.1 国塑料模具发展概况及趋势1)新材料、新技术、新工艺的研制、开发和应用。
随着塑料成型技术的不断发展,模具新材料、模具加工新技术和模具新工艺方面的开发己成为当前模具工业生产和科研的主要任务之一[2]。
随着技术的发展,气体辅助注射成型和热流道技术随之出现。
气体辅助注射成型可在保证产品质量的前提下,大幅度降低成本。
目前在汽车和家电行业中正逐步推广使用。
气体辅助注射成型比传统的普通注射工艺有更多的工艺参数需要确定和控制,而且其常用于较复杂的大型制品,模具设计和控制的难度较大,因此,开发气体辅助成型流动分析软件,显得十分重要。
采用热流道技术的模具可提高制件的生产率和质量,并能大幅度节省塑料制件的原材料和节约能源,所以广泛应用这项技术是塑料模具的一大变革[3-7]。
2)我国模具标准件水平和模具标准化程度仍较低,与国外差距甚大,在一定程度上制约着我国模具工业的发展,为提高模具质量和降低模具制造成本,模具标准件的应要大力推广[8]。
模具毕业设计82外螺纹液压管四通管接头注塑模具设计

5.1 分型面的设计 ......................................................... 13 5.1.1 分型面的分类 ....................................................... 13 5.1.2 分型面的选择原则 ................................................... 13 5.1.3 分型面的确定 ....................................................... 13 5.2 型腔的分布 ........................................................... 14 5.3 凹模的结构设计 ....................................................... 14 5.4 模具型零成件的工作尺寸计算 ........................................... 15 5.4.1 塑件的收缩率波动误差s ............................................. 15 5.4.3 模具成型零件的磨损c ............................................... 16 5.4.4 模具安装配合误差j ................................................. 16 5.5 型腔和型芯径向尺寸的计算 ............................................. 17 5.5.1 型腔径向尺寸的计算 ................................................. 18 5.5.2 型芯径向尺寸的计算 ................................................. 18 5.5.3 型腔深度和型芯高度尺寸的计算 ....................................... 18 6 排气系统的设计 ........................................................ 19 6.1 排气不良的危害 ....................................................... 19 6.2 排气系统的设计方法 ................................................... 19 7 导向与脱模机构的设计 .................................................. 20 7.1 导向机构的作用和设计原则 ............................................. 20 7.1.1 导向机构的作用 ..................................................... 20 7.1.2 导向机构的设计原则 ................................................. 20 7.2 导柱、导套的设计 ..................................................... 21 7.2.1 导柱的设计 ......................................................... 21 7.2.2 导套的设计 ......................................................... 21 7.2.3 导向孔的总体布局 ................................................... 22 7.3 推出机构设计 ......................................................... 22 7.4 脱模力的计算 ......................................................... 22 7.5 推杆的设计 ........................................................... 24 7.5.1 推杆长度及强度计算 ................................................. 24 7.5.2 推杆的形状及固定形式 ............................................... 24 7.2.3 推杆位置的选择 ..................................................... 25 8 侧向分型与抽芯机构的设计 ............................................... 26 8.1 抽芯机构设计原则 ..................................................... 26 8.2 抽芯机构的确定 ....................................................... 26 8.3 抽芯距 S ............................................................. 26
油管接头注塑模设计

目录摘要 (1)关键词 (1)1 前言 (2)1.1 选题的背景目的和意义 (2)1.2 我国模具技术的发展现状及发展趋势 (2)1.2.1 发展现状 (2)1.2.2 发展趋势 (2)1.3 对选题的设计设想和研究方法 (4)2 塑件分析和成型材料特性 (4)2.1 塑件分析 (4)2.2 成型材料的特性 (5)2.3 脱模斜度的选择 (7)2.4 本章小结 (7)3 注射机选择 (7)3.1 常用的注射机分类 (7)3.2 注射机的选择 (8)3.3 本章小结 (9)4 分型面设计与型腔布置 (9)4.1 分型面设计 (10)4.2 型腔布置设计 (10)4.2.1 型腔数目的确定 (10)4.2.2 标准模架的选取 (11)4.3 本章小结 (11)5 浇注系统设计 (12)5.1 浇注系统的设计原则 (12)5.2 浇注系统的设计 (12)5.3.1 概述 (13)5.3.2 排气系统的设计要点 (13)5.3.3 排气槽的位置和形式 (13)5.4 本章小结 (14)6 成型零部件和导向机构的设计 (14)6.1 成型零件的结构设计 (14)6.2 成型钢材的选用 (14)6.2.1 塑料模材料的性能要求 (14)6.2.2 塑料模常用材料 (15)6.3 成型零件工作尺寸计算 (15)6.4 型腔壁厚的计算 (18)6.5 模架与板厚的确定 (18)6.6 导向机构的设计 (19)6.7 本章小结 (19)7 脱模机构设计 (20)7.1 脱模机构的设计 (20)7.1.1 推管的设计 (20)7.1.2 复位装置设计 (20)7.1.3 顶出距离 (20)7.2 脱模力计算 (20)7.3 本章小结 (21)8 侧向分型与抽芯机构设计 (21)8.1 抽芯距的计算 (21)8.2 斜导柱的设计 (21)8.3 滑块的设计 (22)8.4 本章小结 (22)9 温度调节系统设计 (22)9.1 温度调节对塑件的影响 (23)9.2.1 冷却系统计算 (23)9.2.2 冷却回路布置 (24)9.3 本章小结 (25)10 模具校核 (25)10.1 注射机校核 (25)10.2 本章小结 (26)结论 (26)参考文献 (27)致谢 (27)附录 (28)油管接头注塑模设计摘要:简要介绍了一种油管接头注塑成型模具的结构方案。
四通管接头注塑模具毕业设计

XXXX大学本科毕业论文(设计)四通管接头注塑模设计院系名称:XXXX学院专业:网络技术学生姓名:Docer学号: 123456789指导老师:DocerXXXX大学教务处制2018年3月1日前言此毕业设计课题的制品名称为“四通管接头”,用于部件的连接。
制品材料为:ABS(丙烯腈—丁二烯—苯乙烯共聚物),此材料有良好的耐化学腐蚀、表面硬度、加工性和染色性。
制品的壁厚、熔料温度对收缩率影响极小。
ABS有较强的抗冲击强度,且在低温下也不迅速下降。
ABS有一定的硬度和尺寸稳定性,易于成型加工,经过调色可配成任何颜色。
此制品是批量生产,所以我将设计一套塑料成型模具。
在设计模具时需要考虑制品的一些特点。
制品的主要特点是其有一个上下贯穿孔,两侧也有一个贯穿孔,且上下孔相对比较大且深,复杂。
塑件的尺寸精度有一定的要求,外型需光洁不得有划伤,总体尺寸大小适中。
取塑件的最大截面为分型面,大小两孔分别上下放置,左右相同孔位于两侧,需要抽芯。
由于塑件尺寸较小,采用一模两件,能够适应生产的需要,侧浇口去除方便,模具结构孔不复杂,容易保证塑件的质量。
开模后,塑件包紧动模型芯的力比较大,采用推管推出,推出力比较平稳,塑件不易发生变形。
目录前言 (3)一.塑件分析 (4)二.分型面的设计 (6)三.注射机的选择 (7)四.根据制品尺寸,设计成型零部件 (11)五.型腔壁厚计算 (18)六.浇注系统的设计 (21)七.推出机构的设计 (24)八.导柱导向机构的设计 (25)九.侧向分型与抽芯机构 (27)十.温度调节系统的设计与计算 (31)十一.模架的选择 (33)十二.设计说明 (34)十三.模具的装配 (34)十四.试模 (36)十五.修模 (37)后记 (38)参考文献 (39)前言时光转瞬即逝,我在扬州职业大学求学也即将历满三个寒暑,虽不敢说学业有成,却有幸得到诸多师长的殷殷教诲,这是我最大的收获。
尤其在毕业设计期间,在校内指导老师:徐美银,以及各位系领导和老师的指导帮助下完成了这次毕业设计的任务。
快速接头注塑模具设计

摘要本设计针对快换接头进行该产品的模具设计,通过对塑件进艺分行工析和比较,最终设计出一副注塑模。
从产品结构工艺性和模具结构出发,对模具的浇注系统、模具成型部分的结构、分型面的选择、冷却系统、注塑机的选择及有关参数的校核都有详细的分析设计说明。
通过完成该课题设计,熟悉了塑料模具设计的一般方法和流程。
通过完成该课题设计,熟悉了塑料模具设计的一般方法和流程,较好的完成了任务,实现了无纸化设计。
塑料工业是当今世界上增长最快的工业门类之一,而注塑模具是其中发展较快的种类,因此,研究注塑模具对了解塑料产品的生产过程和提高产品质量有很大意义。
模具是工业生产的基础工艺装备,被称为“工业之母”。
80%的家电产品零部件、70%的机电产品零部件都由模具成型,汽车、仪表等产品有60%-90%的零部件制作也要依靠模具来完成。
近几年,各地政府也都意识到了模具业的重要性,纷纷通过建设模具工业园来提升竞争力。
关键词:快换接头;注塑模具;模具设计AbstractThis design for quick change connector for the product mold design, plastic parts to process through analysis and comparison of the final design an injection mold.From the product structure processing and mold structure that, the casting mold system, mold forming part of the structure, parting the choice of cooling systems, injection molding machine of choice and check all the parameters of a detailed analysis of design specifications.Design through the completion of the subject, familiar with the general method of plastic mold design and process.Plastics industry in the world today one of the fastest growing industry category, while the injection mold is one of the types of rapid development, and therefore the study of plastic injection molds for understanding the production process and improving product quality is very significant.Mould and die are the essential equipment in the industry manufacturing, so as called “the mother of industry”. 80% parts of family appliance and 70% parts of mechanical and electrical facilities use mould and die in the production. 60%-90% parts of automobiles and instruments make use of mould and die. These years, the importance of mould and die are convinced by local governments, and so many mould industrial districts and parks are constructed to strengthen the competitiveness.Design through the completion of the subject, familiar with the general method of plastic mold design and process, the better to complete the tasks and achieve a paperless design.Keywords:Quick joint injection mold;Injection mold;Mold Design.目录目录 (I)第1章绪论 (1)1.1国内外研究现状 (1)1.2本文研究的内容和意义 (2)1.3本文主要研究内容 (2)第2章塑料制品及工艺分析 (3)2.1制件图 (3)2.2塑件的工艺分析 (4)2.3塑件材质工艺性 (4)2.4ABS注射成型工艺参数 (5)第3章确定注塑机类型 (6)3.1注塑机的初选 (6)3.2选择注射机 (8)第4章模具结构分析与设计 (10)4.1结构分析 (10)4.2模具零部件设计 (11)4.3凸、凹模的确定 (14)4.4脱模方式的确定 (15)4.5冷却系统的结构设计 (15)4.6排气方式的确定 (17)4.7标准模架的选择 (17)第5章设计计算 (18)5.1成型零件的尺寸的计算 (18)5.1.2型腔深度尺寸 (18)5.2冷却系统水管孔径的计算 (17)5.3浇注系统尺寸的计算 (21)5.4型腔的计算 (21)5.5脱模机构相关计算 (22)5.6模架的确定 (23)5.7各模板的尺寸的确定 (23)5.8校核模具平面尺寸 (24)第6章 PRO/E所示图 (25)6.1零件图 (25)6.2导套 (26)6.3导柱 (27)6.4垫块 (28)6.5定模板 (29)6.6演示动画 (30)结论 (31)致谢 (32)参考文献 (33)第1章绪论1.1国内外研究现状我国加入世贸组织(WTO)后,将获得一个更加稳定的国际经贸环境,从而有利于我国与各国、各地区的经济贸易合作,有利于世界经济的稳定发展,我国的利用外资领域将进一步扩大,国内和国外模具企业都可以从中得到更多的机会和收益。
- 1、下载文档前请自行甄别文档内容的完整性,平台不提供额外的编辑、内容补充、找答案等附加服务。
- 2、"仅部分预览"的文档,不可在线预览部分如存在完整性等问题,可反馈申请退款(可完整预览的文档不适用该条件!)。
- 3、如文档侵犯您的权益,请联系客服反馈,我们会尽快为您处理(人工客服工作时间:9:00-18:30)。
油管接头注塑模具设计前言塑料制品在日常生活中是常常见到的,如在家用电器、仪器仪表、建筑器材、汽车工业、日用五金、通信器材以及医疗器械等众多领域,塑料制品的使用比例正迅猛增加。
这主要是因为以下原因:第一,塑料与金属材料相比有许多优点:容易加工,生产效率高;节约能源,绝缘性能好;质量轻,相对密度为1.0~1.4,比铝轻一半,比钢轻3/4,比强度高,具有突出的耐磨、耐腐蚀性等;第二,在日用和工业产品中,一个设计合理的塑料制品往往能代替多个传统金属结构件,加上利用工程塑料特有的性质,可以一次成型非常复杂的形状,并且还能设计成卡装结构,从而减少产品中装配的各种紧固件,降低了金属材料消耗量和加工及装配工时;第三,注塑加工是塑料加工中普遍采用的方法之一。
该方法使用与全部热塑性塑料和部分热固性塑料,制品数量比其他常规的金属成型方法要大得多。
由于注塑成型加工不仅产量多,而且适用于多种原料,能够成批、连续的生产,并且具有稳定的尺寸,容易实现生产的自动化和高速化,具有极高的经济效益。
因此目前工业产品非金属化、金属制品塑料化的趋势日益明显。
获得注塑制品的过程,称之为注塑成型或者注射成型,或者简单的称之为注塑。
注塑成型的基本过程是:颗粒状的高分子材料(以下简称为塑料)经过注塑机螺杆的挤压和加热,成为熔融状态的可以流动的熔体。
在螺杆的推动下,塑料熔体通过注塑机的喷嘴、模具的主流道、分流道和浇口进入模具型腔,成型出具有一定形状和尺寸制品的过程。
注塑的结果是生产出符合用户要求的塑料制品。
要想取得合格的制品,必须要有设计合理、制造精良的模具,还需要有何该模具配套的先进的注射设备(注塑机)以及合理的加工工艺。
因此人们常将,模具、注塑机以及工艺称之为注塑过程得以顺利进行的三个基本要素。
作为注塑成型加工的主要工具之一的注塑模具,在质量、精度、制造周期以及注塑成型过程中的生产效率等方面的恶水平高低,直接影响产品的质量、产量、成本及产品的更新换代,并最终决定着企业在市场竞争中的反映能力和速度。
与其他机械行业相比,模具制造业主要有以下三个特点:第一,模具不能像其他机械产品那样可作为基本定型的商品随时都可以在机电市场上买到。
这是因为每副模具都是针对特定的塑料制品的规格而产生的,由于塑料制品的形状、尺寸各异,差距甚大,其模具结构也是大相径庭,所以模具制造不可能形成批量生产。
换句话说,模具是单件生产的,重复加工的可能性很小。
因此,模具的设计、制造成本都较高。
第二,因为注塑模具是为产品中的塑料制品而订制的,作为产品,除质量、价格等因素之外,很重要的一点就是需要尽快地投放市场,所以对于为塑料制品而特殊订制的模具来说,其制造周期一定要短。
第三,模具制造时一项技术性很强的工作,其加工过程集中了机械制造中的诸多先进技术的部分精华与钳工技术的手工技巧,因此要求模具工人具有较高的文化技术水平,特别是对于企业来说要求培养“全能工人”(即多面手),使其适应多工种的要求,这种技术工人对模具单件生产方式组织均衡生产来说是非常重要的。
注塑机也是注塑成型必需的要素之一。
一般来说,市场上供应的各种形式和规格的注塑机,但是在实践中,必须根据模具的实际情况和注塑厂家的设备情况进行选择。
对于采用注塑成型加工方法生产塑料制品来说,合理的成型工艺既是三个基本要素中的加工工艺。
所谓成型工艺,简单来说就是将压力、温度、时间(速度)三大要素组成最合理的搭配。
在成型过程中,尤其是精密制品的成型,要想确立一组最佳的成型条件决非易事,因为影响成型条件的因素很多,除制品的形状、模具结构、注塑设备、原材料等之外,电压的波动、环境温度的变化对成型都有一定的影响。
到目前为止,建立最佳的成型工艺尚无简便可靠的办法,大多需要操作者具有很丰富的实践经验与耐心,根据塑料制品在成型过程出现的具体文言体认真调查,才能确立一个理想的成型工艺,高效率、高质量地生产出合格的塑料制品。
如前所述,注塑过程得以实现的三个基本要素是:注塑机、注塑模具以及加工工艺,它们缺一不可。
随之市场竞争的激烈化,客户对于产品的质量要求越来越高,生产速度要求越来越快。
这些要求推动人们不断设计技术更加先进,生产效率更加高的注塑机,同时设计结构更加合理,性能更加稳定的注塑模具,并寻求更为合理的注塑工艺,以满足这方面的要求。
但是要做到上述三个方面并不容易。
因为从制品质量方面讲,塑料模具以及注塑成型工艺对其影响甚大;从制品的生产效率方面讲,注塑机、模具以及生产工艺则发挥着巨大的作用。
而整个注塑的工艺又是有制品的形状和大小、塑料的种类、模具的结构以及注塑机的类型来决定的。
为了能够使我们在毕业后的工作过程中能够独立分析和解决实际问题,在三年的学习将要结束的时候,学校安排了“毕业设计”这个环节。
本设计题目为“油管接头注塑模”,在设计中经过分析选用了“一模两腔”的型腔排列方式,能够满足中等批量的生产任务;浇口的设计中根据模具结构选择了潜伏式浇口,在开模过程中能够自动切断浇口凝料,提高了生产效率;由于制件有侧孔,需要设置侧向分型抽芯机构,本模具中采用了斜导柱抽芯机构;在顶出机构的设计中,由于制件包紧在型芯上造成脱模力较大,为保证塑件质量,采用了顶管脱模;顶管必须在侧型芯滑块回位时提前退会复位,为避免侧型芯与顶管在合模过程中发生干涉,设置了弹簧式优先复位机构,需要注意的是选用的弹簧要有迫使顶出机构复位的足够力矩.毕业设计是塑料模设计课程重要的综合性和实践性教学环节。
通过这个环节使我能够综合运用塑料模具设计课程和其他先修课程的知识,分析和解决塑料模具设计问题,进一步巩固、加深和拓宽所学知识,逐步树立正确的设计思想,增强创新意识和竞争意识,熟悉掌握塑料模具设计的一般规律,培养分析问题和解决问题的能力;通过设计计算、绘图以及运用技术规范、标准、设计手册等有关设计资料,进行全面的塑料模具设计基本技能的训练。
在设计过程中得到了杨占尧老师的大力指导与帮助,此外还参考了有关同学的设计内容和资料,他们为我的设计提供了许多宝贵意见,在此我表示衷心的感谢!第1章模塑工艺规程的编制塑件的工艺性分析塑件的原材料分析塑件的材料采用聚甲醛(POM),属热塑性塑料,是一种具有优异综合性能的工程塑料。
从使用性能上看,该塑料具有硬度大、耐磨性强、弹性好、化学稳定性高、尺寸稳定性好,其耐油性能与温度、湿度等外界条件无关等优点,并且具有突出的耐溶剂性和良好的耐热性【2】。
从成型性能上看,该塑料熔料的流动性较好,受温度变化的影响较小,而受压力的影响比较敏感,在注塑成型时只要控制压力的大小就可获得适合的流动性,使得成型较容易。
但是制件的成型收缩率较大,使得成型后制件上易产生折皱、凹痕、斑纹、熔接痕等缺陷,因此应注意注塑工艺的合理控制,例如在成型时应采用较高注射压力,适当延长保压时间以减小收缩率等。
塑件的结构和尺寸精度及表面质量分析(1)结构分析。
从零件图上分析,该零件总体形状类示一个三通管道,在下端有一个直径为φ35mm,深度为3mm的凹坑。
在上端有一个外径为φ40mm,内径为φ30mm,高度为3mm的凸缘。
在三通的一端是一段M12mm的螺纹,其长度为10mm。
因此,模具设计时必须设置侧向分型抽芯机构,该零件属于中等复杂程度。
(2)尺寸精度分析。
从零件图可知,该零件各个尺寸均未注明公差,为提高经济效益,则按未注明公差尺寸来处理。
根据表2—15【1】查得POM材料的适用未注公差等级为MT6级(GB/T14486-1993)。
从以上分析可见,该零件的尺寸精度等级不高,对应的模具相关零件的尺寸加工容易保证。
从塑件的壁厚上来看,壁厚最大处为9mm,最小处为5mm,壁厚差为4mm,相差较大,成型时可能会在塑件内部产生缩孔和残余应力,应在成型工艺上采取措施,比如延长保压时间和冷却时间,改善浇注系统,开设冷却水道,使模具冷却均匀等,防止缺陷的产生。
(3)表层质量分析。
该零件的表面要求没有缺陷、毛刺,内部表面应光洁,以利于液体的流动。
除此之外没有特别的表面质量要求,故比较容易实现。
综上分析可以看出,注塑时在工艺参数控制的较好的情况下,零件的成型要求可以得到保证。
计算塑件的体积和重量为了选用注塑机型号及确定模具型腔数,应该先确定塑件的质量。
mm(具体过程略)。
计算塑件的体积:用分割法求得塑胶体积V= 256803ρ,故塑计算塑件的质量:根据设计手册【3】查得POM的密度为3=g1.41cm/件的质量为:ρ10-W== 25680×1.41×3V= 36.2g采用一模两件的模具结构,考虑其外形尺寸,注塑时所需压力等情况,初选用注塑机XS—ZY—250型。
塑件注塑工艺参数的确定由于聚甲醛塑料的热稳定性较差,在210℃下停留时间不得超过20min,在正常加工温度范围内受热时间稍长也会发生分解。
所以在保证物料流动性的前提下,尽量采用较低的成型温度和较短的停留时间。
查相关文献资料,聚甲醛的成型工艺参数可作如下选择【2】:(试模时,可根据实际情况作适当调整)注塑温度:包括料筒温度和喷嘴温度。
t选用165℃;料筒温度:后段温度1中段温度t选用175℃;2t选用185℃;前段温度3喷嘴温度:选用175℃;注塑压力:选用100Mpa;注塑时间:选用40s;保压:选用40Mpa;保压时间:选用10s;冷却时间:选用35s。
另外,为了提高制品的尺寸稳定性和减少内应力,可将注塑成型后获得的制件置于120℃~130℃的环境中进行空气浴,停留时间约4小时,然后缓慢冷却至室温。
第2章注塑模的结构设计2.1分型面的选择根据分型面选择原则和塑件的成型要求选择分型面。
该塑件为油管接头,表面质量无特殊要求,分析后可取如下图所示的分型面,它是塑件最大截面,大孔在开模方向上成型,而小孔在侧面,便于抽芯。
若选图1所示的分型方式即可降低模具的复杂程度,减少模具加工难度又便于成型后取件。
故选用如图1所示的分型方式较为合理。
图1 分型面的选择(1)图 2 分型面的选择(2)若采用图2所示的分型方式,虽然侧向抽芯距大大减小,但要想使制件脱模,模具的开模行程将增加很多,模具结构也成倍增大,所需设备要有很大的开模行程才行,势必降低生产效率。
2.2确定型腔的排列方式本塑件在注塑时采用一模两件,即模具需要两个型腔。
综合考虑浇注系统、模具结构的复杂程度等因素,拟采取如图3所示的型腔排列方式。
图 3 型腔排列方式(1)采用图3所示的型腔排列方式能够适应生产批量的需求,模具结构也不复杂,容易保证塑件的质量。
若采用图4所示的型腔排列方式,虽然较图3在模具结构上少了一侧的抽芯机构,但将两个侧型芯放在同一侧,由于侧型芯较细小,并且抽芯距较长,造成抽芯力大,抽芯机构相对复杂,并且模具纵向尺寸将随之增大,模具制造成本提高。