过程审核评分规则
过程审核评分细则
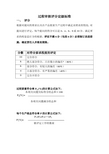
过程审核评分定级标准
一、评分
根据对提问的要求以及在产品批量生产过程中满足该要求的情况,对提问进行评定。
每个提问的得分可以是0、4、6、8或10分,满足要求的程度是打分的根据。
评定不满6分(包括6分)必须制订改进措施,确定责任人并落实期限。
过程要素符合率P n [%]的计算公式如下:
各相关问题实际得分的总和×100
P n[%]=
各相关问题满分的总和
每个生产线总符合率P的计算公式如下:
P1+P2+P3+…+P n
P[%]=
被评定工序的数量
二、定级
注*:
1.若任何一项提问得分为零,而不符合要求可能会给产品质量和过程质量造成严重的影响,则可把被审核部门从A级降到B级或从B级降到C级。
2.若被审核的部门的总符合率超过90%,但其在任何两个或以上提问的符合率只达到6分(60%)或以下,则必须从A级降到B级。
3.必须在审核报告中说明降级的原因。
过程审核评分细则
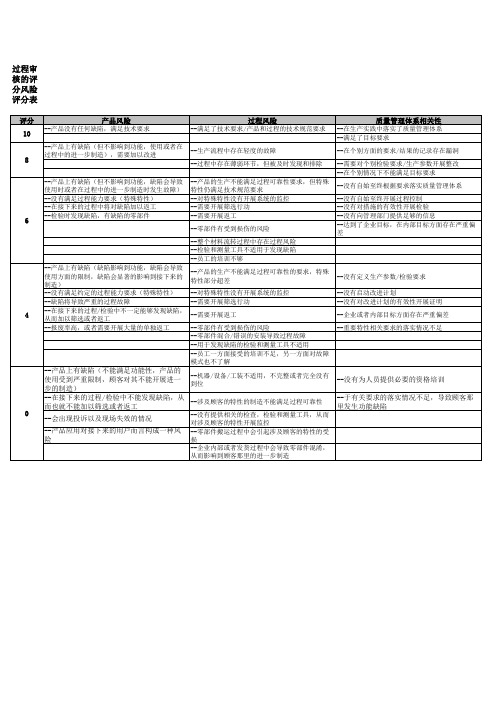
--没有提供相关的检查,检验和测量工具,从而 对涉及顾客的特性开展监控 --零部件搬运过程中会引起涉及顾客的特性的受 --产品应用对接下来的用户而言构成一种风险 损 --企业内部或者发货过程中会导致零部件混淆, 从而影响到顾客那里的进一步制造
--没有为人员提供必要的资格培训 --于有关要求的落实情况不足,导致顾客那 里发生功能缺陷
--没有定义生产参数/检验要求 --没有启动改进计划 --没有对改进计划的有效性开展证明 --企业或者内部目标方面存在严重偏差 --重要特性相关要求的落实情况不足
0
--产品上有缺陷(不能满足功能性,产品的 --机器/设备/工装不适用,不完整或者完全没有 使用受到严重限制,顾客对其不能开展进一 到位 步的制造) --在接下来的过程/检验中不能发现缺陷,从 --涉及顾客的特性的制造不能满足过程可靠性 而也就不能加以筛选或者返工
8
6
--产品上有缺陷(但不影响到功能,缺陷会导致 使用时或者在过程中的进一步制造时发生故障) --没有满足过程能力要求(特殊特性) --在接下来的过程中将对缺陷加以返工 --检验时发现缺陷,有缺陷的零部件
--产品的生产不能满足过程可靠性要求,但特殊 特性仍满足技术规范要求 --对特殊特性没有开展系统的监控 --需要开展筛选行动 --需要开展返工 --零部件有受到损伤的风险 --整个材料流转过程中存在过程风险 --检验和测量工具不适用于发现缺陷 --员工的培训不够
审核评价内容及评分实施细则
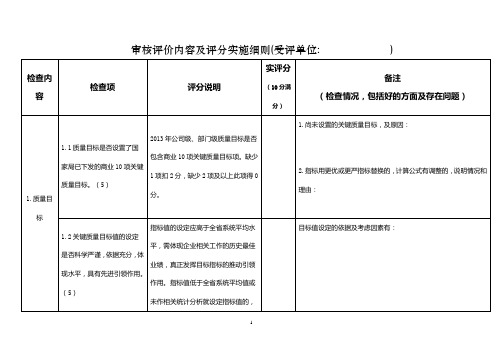
结合现场检查情况,重点关注文件是否够用、好用、管用,是否能够支撑目标绩效的实现,是否体现了过程方法、持续改进的应用要求。以10分为满分,分别对五个过程的文件健全度进行综合评分。健全度检查要点仅作为参考,不能机械地作为过程健全度评分的唯一依据。
文件健全度得分=五个过程得分的算数平均值(结果保留一位小数)
1.文件总体健全度评价得分=
五个过程的健全度得分合计(50分满分)=
2.五个过程的文件健全度得分、检查情况及发现问题:
①()过程得分=
检查情况:
②()过程得分=
检查情况:
③()过程得分=
检查情况:
④()过程得分=
检查情况:
⑤()过程得分=
检查情况:
其中,未按企业文件要求执行的事实项数:
2.企业总体文件执行率=()%(执行率结果保留一位小数)
3.各过程的文件执行率,以及未按文件执行的事实项描述:
①
()过程:文件执行率=
2.3体系文件的健全度。(10)
2.3体系文件的健全度。(10)
参考《文件健全度合规性执行率检查表》,抽查五个过程,细致查看每一个过程的相关文件,看该过程是否按照过程管理的思路对相关内容进行规定和明确,如技术/工作的接收标准或要求、过程及关键控制点的测量方法与周期、纠偏的方法与预案、过程信息的记录与传递要求、工作的职责界定等。
目标值设定的依据及考虑因素有:
1.3对关键质量目标的实现是否进行了必要的策划、完善和改进。(7)
VDA6.3过程审核评分准则

--零部件有受到损伤的风险
--零部件混合/错误的安装导致过程故障
--用于发现缺陷的检验和测量工具不适用
--员工一方面接受的培训不足,另一方面对故障
模式也不了解
--产品上有缺陷(不能满足功能性,产品的 使用受到严重限制,顾客对其不能开展进一 步的制造)
--机器/设备/工装不适用,不完整或者完全没有 到位
--没有定义生产参数/检验要求 --没有启动改进计划 --没有对改进计划的有效性开展证明 --企业或者内部目标方面存在严重偏差 --重要特性相关要求的落实情况不足
--没有为人员提供必要的资格培训
--于有关要求的落实情况不足,导致顾客那 里发生功Biblioteka 缺陷过程审核的评分风险评分表
评分 10 8 6
4
0
产品风险 --产品没有任何缺陷,满足技术要求
过程风险 --满足了技术要求/产品和过程的技术规范要求
--产品上有缺陷(但不影响到功能,使用或者在 过程中的进一步制造),需要加以改进
--生产流程中存在轻度的故障
--过程中存在薄弱环节,但被及时发现和排除
--产品上有缺陷(但不影响到功能,缺陷会导致 使用时或者在过程中的进一步制造时发生故障) --没有满足过程能力要求(特殊特性) --在接下来的过程中将对缺陷加以返工 --检验时发现缺陷,有缺陷的零部件
--产品的生产不能满足过程可靠性的要求,特殊 特性部分超差
--没有满足约定的过程能力要求(特殊特性) --对特殊特性没有开展系统的监控
--缺陷将导致严重的过程故障
--需要开展筛选行动
--在接下来的过程/检验中不一定能够发现缺陷, 从而加以筛选或者返工
--需要开展返工
--报废率高,或者需要开展大量的单独返工
最新VDA6.3过程审核检查表及评分标准
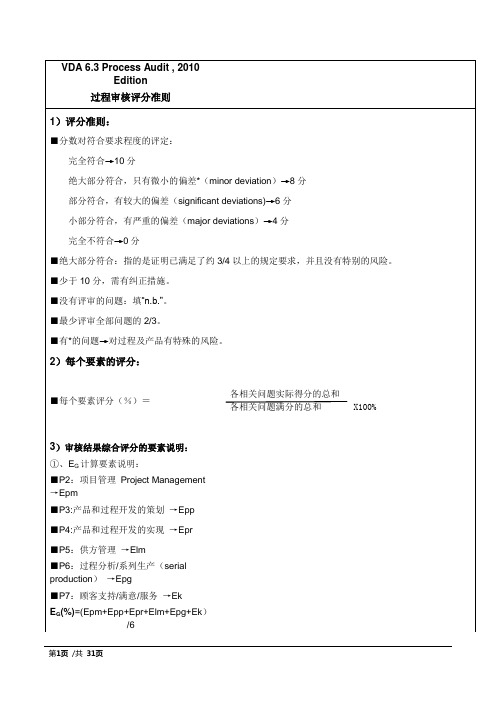
■项目计划=>关键路径则(critical path)
■质量管理计划(QM plan) :项目计划的组成部分。
P2.4
项目组织是否在项目进程中提供了可靠的变更管理?考虑要点,如:
■变更管理需要满足特定的顾客要求。
■变更的可行性检验(manufacturing feasibility check)
EG(%)=(Epm+Epp+Epr+Elm+Epg+Ek)/6
②、过程分析/管理—乌龟图(P6:生产)各要素说明:
■Eu1:输入
■Eu1:工作内容
■Eu3:支持过程
■Eu4:材料、资源
■Eu5:效率
■Eu6:输出/结果
■Eu7:零件运输(Transport/Parts Handling)
4)审核结果的综合评分Overall Assessment:
VDA 6.3 Process Audit , 2010 Ed分数对符合要求程度的评定:
完全符合→10分
绝大部分符合,只有微小的偏差*(minor deviation)→8分
部分符合,有较大的偏差(significant deviations)→6分
小部分符合,有严重的偏差(major deviations)→4分
:记录
■定义的过程[记录所有变更]
■说明变更(highlight)
■和顾客协商沟通、评价
■影响到产品质量的变更=>风险评价
■供方(关键群体)参与
■对变更停止的时间点:明确的定义、遵守
■如果不能遵守,则在顾客和供方之间必须以书面形式加以记录。
■SOP之前的变更时间段:不会影响到产品质量。
过程审核评分标准_20241010
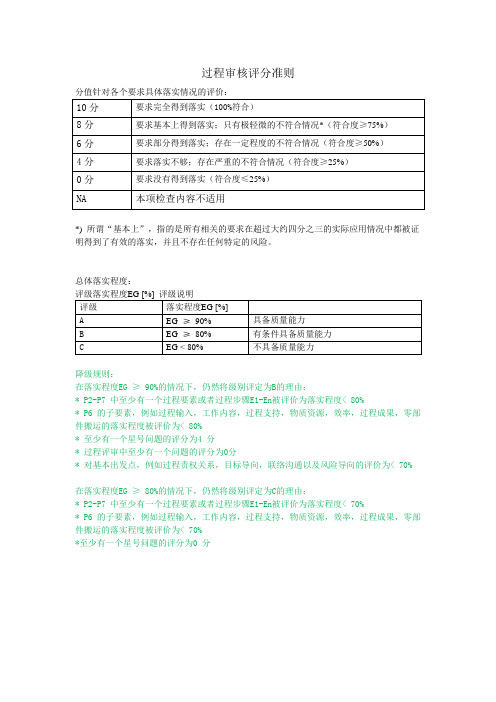
过程审核评分准则
*) 所谓“基本上”,指的是所有相关的要求在超过大约四分之三的实际应用情况中都被证明得到了有效的落实,并且不存在任何特定的风险。
总体落实程度:
降级规则:
在落实程度EG ≥ 90%的情况下,仍然将级别评定为B的理由:
* P2-P7 中至少有一个过程要素或者过程步骤E1-En被评价为落实程度< 80%
* P6 的子要素,例如过程输入,工作内容,过程支持,物质资源,效率,过程成果,零部件搬运的落实程度被评价为< 80%
* 至少有一个星号问题的评分为4 分
* 过程评审中至少有一个问题的评分为0分
* 对基本出发点,例如过程责权关系,目标导向,联络沟通以及风险导向的评价为< 70%
在落实程度EG ≥ 80%的情况下,仍然将级别评定为C的理由:
* P2-P7 中至少有一个过程要素或者过程步骤E1-En被评价为落实程度< 70%
* P6 的子要素,例如过程输入,工作内容,过程支持,物质资源,效率,过程成果,零部件搬运的落实程度被评价为< 70%
*至少有一个星号问题的评分为0 分。
过程审核评分准则

既无规定又未执行--------扣3分
分值计算:
2*被评估项目数-总扣分数
分值(%)=×100%
2*被评估项目数
等级划分:
A级-------分值:≥90%
B级-------分值:≥80%,<90%
C级------分值:≥70%,<80%
D级------分值:<70%
目录
1、产品定义7条
2、外协件质量保证9条
3、生产管理32条
4、成品检验和试验7条
5、成品包装、储存、运输6条
过程审核评分准则
过程审核提问表
本评定标准分为五个章节共61个条款。依据企业规模或所采取的技术及所处的阶段,有些项目可不作评审,但பைடு நூலகம்求有足够的理由。本提问表采取项目扣分制,扣分原则如下:
合适--------扣0分
程序文件没规定但执行的较好--------扣1分
程序文件有规定但执行的不好但对产品质量无直接影响-------扣1分
过程审核的评分标准

0
--产品上有缺陷(不能满足功能性,产品的 --机器/设备/工装不适用,不完整或者完全没有 使用受到严重限制,顾客对其不能开展进一 到位 步的制造) --在接下来的过程/检验中不能发现缺陷,从 --涉及顾客的特性的制造不能满足过程可靠性 而也就不能加以筛选或者返工
--没有提供相关的检查,检验和测量工具,从而 对涉及顾客的特性开展监控 --零部件搬运过程中会引起涉及顾客的特性的受 --产品应用对接下来的用户而言构成一种风险 损 --企业内部或者发货过程中会导致零部件混淆, 从而影响到顾客那里的进一步制造
--没有为人员提供必要的资格培训 --于有关要求的落实情况不足,导致顾客那里 发生功能缺陷
--会出现投诉以及现场失效的情况
过程审核的评分风险评分表
评分 10 产品风险
--产品没有任何缺陷,满足技术要求 --产品上有缺陷(但不影响到功能,使用或者在 过程中的进一步制造),需要加以改进
过程风险
--满足了技术要求/产品和过程的技术规范要求 --生产流程中存在轻度的故障 --过程中存在薄弱环节,但被及时发现和排除
质量管理体系相关性
8
6
--产品上有缺陷(但不影响到功能,缺陷会导致 使用时或者在过程中的进一步制造时发生故障) --没有满足过程能力要求(特殊特性) --在接下来的过程中将对缺陷加以返工 --检验时发现缺陷,有缺要求,但特殊 特性仍满足技术规范要求 --对特殊特性没有开展系统的监控 --需要开展筛选行动 --需要开展返工 --零部件有受到损伤的风险 --整个材料流转过程中存在过程风险 --检验和测量工具不适用于发现缺陷 --员工的培训不够 --产品的生产不能满足过程可靠性的要求,特殊 特性部分超差 --对特殊特性没有开展系统的监控 --需要开展筛选行动 --需要开展返工 --零部件有受到损伤的风险 --零部件混合/错误的安装导致过程故障 --用于发现缺陷的检验和测量工具不适用 --员工一方面接受的培训不足,另一方面对故障 模式也不了解
过程审核评分细则

过程审核评分细则
过程审核是指对一个过程或流程进行全面、系统和全程的评估和分析。
通过审查和评价这个过程,可以发现问题和改进的空间,从而提高过程的
效率和质量。
一、过程目标与规划
1.目标明确性:过程的目标是否明确、具体和可测量?
2.规划合理性:过程的规划是否合理、可行和有效?
二、过程设计与构建
1.结构合理性:过程的结构是否简单、清晰和逻辑?
2.流程完整性:过程的流程是否完整、连贯和无缺漏?
3.任务分配:过程的任务是否明确、分工合理和责任到位?
三、过程执行与管理
1.执行效果:过程的执行是否高效、精确和及时?
2.监控能力:过程的监控是否及时、全面和有效?
3.风险控制:过程的风险管理是否到位、可控和有效?
四、过程改进与优化
1.改进机制:过程的改进机制是否明确、有效和能持续改进?
2.问题识别:过程是否能及时识别和反馈问题?
3.改进措施:过程的改进措施是否切实可行和有效果?
五、过程效果与价值
1.成果达成:过程的目标和成果是否达到预期?
2.价值评估:过程的价值和效益是否被充分认可和评估?
以上仅为过程审核评分细则的一个示例,具体的评分细则可以根据实
际情况进行调整和补充。
在进行过程审核评分时,可以根据上述细则对每
个评分指标进行评估,然后进行得分汇总和综合评价。
通过过程审核的评
分细则,可以帮助组织全面了解和评估过程的状况,进而进行改进和优化。
VDA6.3过程审核评分准则
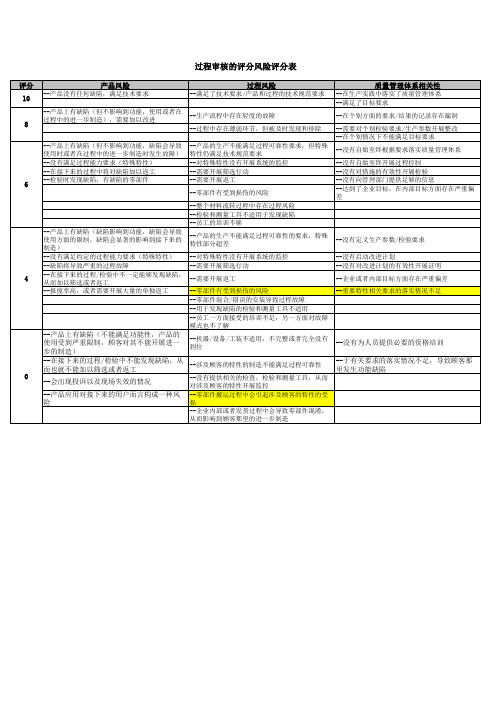
8
6
--产品上有缺陷(但不影响到功能,缺陷会导致 使用时或者在过程中的进一步制造时发生故障) --没有满足过程能力要求(特殊特性) --在接下来的过程中将对缺陷加以返工 --检验时发现缺陷,有缺陷的零部件
--产品的生产不能满足过程可靠性要求,但特殊 特性仍满足技术规范要求 --对特殊特性没有开展系统的监控 --需要开展筛选行动 --需要开展返工 --零部件有受到损伤的风险 --整个材料流转过程中存在过程风险 --检验和测量工具不适用于发现缺陷 --员工的培训不够
--会出现投诉以及现场失效的情况
--没有定义生产参数/检验要求 --没有启动改进计划 --没有对改进计划的有效性开展证明 --企业或者内部目标方面存在严重偏差 --重要特性相关要求的落实情况不足
0
--产品上有缺陷(不能满足功能性,产品的 --机器/设备/工装不适用,不完整或者完全没有 使用受到严重限制,顾客对其不能开展进一 到位 步的制造) --在接下来的过程/检验中不能发现缺陷,从 --涉及顾客的特性的制造不能满足过程可靠性 而也就不能加以筛选或者返工
4
--产品上有缺陷(缺陷影响到功能,缺陷会导致 使用方面的限制,缺陷会显著的影响到接下来的 制造) --没有满足约定的过程能力要求(特殊特性) --缺陷将导致严重的过程故障 --在接下来的过程/检验中不一定能够发现缺陷, 从而加以筛选或者返工 --报废率高,或者需要开展大量的单独返工
VDA6.3 过 程 审 核

二、过程审核概述
过程审核的目的
●对产品/产品组及过程的质量能力进行评定
●识别指出缺陷可能性,以采取措施防止缺陷的首次出现
●对已知的缺陷进行分析,采取措施消除并避免缺陷的再次出现
●优化体系,改进过程
二、过程审核概述
过程审核的时机
●新机种投产 ●增产/减产 ●有重大工程变更 ●品质异常 ●客户抱怨/投诉 8.2.2.4 内部审核计划 当内部/外部不符合或者顾客抱怨时,应适当增加审核频次。
开始进行过程审核的准备工作 确定过程范围 划分过程的工序 过程描述
收集整理资料并 加以考虑
确定影响参数
制定提问表 确定参加人员
制定详细的审核流程
五、审核方式与技巧 审核过程
• 按照事先已制订好的提问表进行审核。既可按照编码顺序也可随机提问 。 • 从“6M”(人、机器、原材料、方法、环境及管理) 着手。 • 提问的方式,例如:5W1H提问方式。 • 实践证明,多次用 “为什么……”提问有利于对过程工艺进行深入的分析 。 • 在审核期间,可以提出新的提问表并增加到提问表里。 • 通过提问把现场的人员也纳入到审核过程中。建议随时记录发现的优点 以及不足之处。 • 为了避免在末次会议上发生冲突,必须尽量在现场澄清不明之处并达成 一致意见。 • 在审核时若发现严重的缺陷,必须与过程负责人共同制订并采取紧急措 施。
二、过程审核概述
过程的定义 过程: 将输入转化输出的一组彼此相关的资源和活动. 包括:人员,资金,设施,设备,技术和方法. 过程审核 对产品/产品组及其过程的质量能力进行评定。 “过程审核”用于检查产品是否符合质量要求, 过程是否受控和有能 力.过程审核的任务:对质量能力进行评定.应该使过程具有能力并受 控,而且在各种因素的影响下仍然稳定地运行. 8.2.2 制造过程审核 组织应对每一个制造过程进行审核,以确定其有效性。
汽车产品VDA6

汽车产品VDA6.3过程审核检查表及评分标准VDA 6.3是一个过程审核评分准则,其中包括了评分准则和每个要素的评分。
评分准则中,完全符合得10分,绝大部分符合得8分,部分符合得6分,小部分符合得4分,完全不符合则不得分。
绝大部分符合指满足了约3/4以上的规定要求,并且没有特别的风险。
少于10分的情况需要采取纠正措施,没有评审问题的填“n.b.”,最少需要评审全部问题的2/3.有特殊风险的问题需要特别注意。
每个要素的评分公式为各相关问题实际得分的总和除以各相关问题满分的总和乘以100%。
审核结果的综合评分要素包括项目管理、产品和过程开发的策划、产品和过程开发的实现、供方管理、过程分析/系列生产和顾客支持/满意/服务。
综合评分公式为各要素得分的平均值。
过程分析/管理中的乌龟图包括了输入、工作内容、支持过程、材料、资源、效率、输出/结果和零件运输。
审核结果的综合评分分为ABCE四个等级,符合率高于90%且各要素得分均高于80%为A级,符合率高于80%且各要素得分均高于70%为B级,否则为C级。
降级规则为如果A级不满足条件,则评为B级,如果B级不满足条件,则评为C级。
P2:项目管理在审核项目/内容审核结果记录评分时,需要考虑是否建立了项目组织并为项目管理者以及团队成员确定了各自的任务及权限。
在组建项目管理的过程中,需要考虑项目管理的能力与顾客要求之间的平衡。
P2.1在确定权限时,需要考虑项目负责人、团队成员、各方面必要的实现权限以及组织机构之间的归口。
同时,需要考虑是否为项目开发而策划并实现了所需的资源,并且通报了变更情况。
在资源策划时,需要考虑项目合同、顾客要求、员工的实际工作负荷以及具备相关资格的专业部门员工。
P2.2在考虑供方时,需要关注关键路径。
同时,需要对项目预算进行管理,并在项目中的变更(时间、开发规模等)发生时及时加以说明,并与顾客进行协商沟通。
变更可分为顾客触发的变更、自身内部的变更以及供方触发的变更。
过程审核评分方法
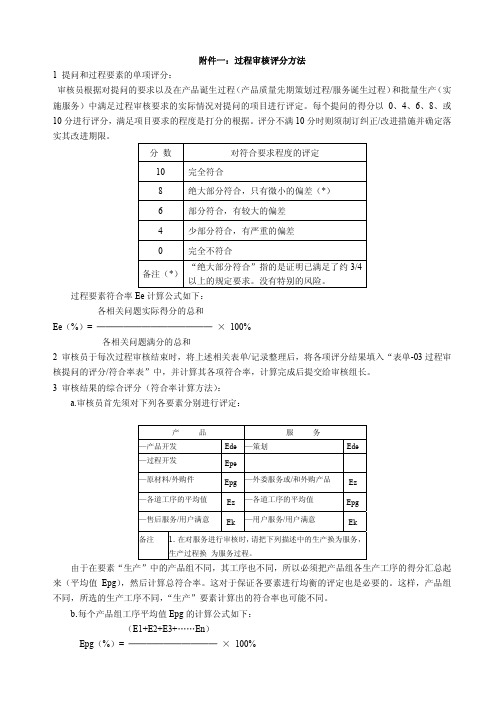
附件一:过程审核评分方法1 提问和过程要素的单项评分:审核员根据对提问的要求以及在产品诞生过程(产品质量先期策划过程/服务诞生过程)和批量生产(实施服务)中满足过程审核要求的实际情况对提问的项目进行评定。
每个提问的得分以0、4、6、8、或10分进行评分,满足项目要求的程度是打分的根据。
评分不满10分时则须制订纠正/改进措施并确定落实其改进期限。
分数对符合要求程度的评定10 完全符合8 绝大部分符合,只有微小的偏差(*)6 部分符合,有较大的偏差4 少部分符合,有严重的偏差0 完全不符合备注(*)“绝大部分符合”指的是证明已满足了约3/4以上的规定要求。
没有特别的风险。
过程要素符合率Ee计算公式如下:各相关问题实际得分的总和Ee(%)= ─────────────× 100%各相关问题满分的总和2 审核员于每次过程审核结束时,将上述相关表单/记录整理后,将各项评分结果填入“表单-03过程审核提问的评分/符合率表”中,并计算其各项符合率,计算完成后提交给审核组长。
3 审核结果的综合评分(符合率计算方法):a.审核员首先须对下列各要素分别进行评定:产品服务—产品开发 Ede—策划 Ede—过程开发Epe—原材料/外购件Epg—外委服务或/和外购产品Ez—各道工序的平均值Ez —各道工序的平均值Epg—售后服务/用户满意Ek —用户服务/用户满意Ek备注1.在对服务进行审核时,请把下列描述中的生产换为服务,生产过程换为服务过程。
由于在要素“生产”中的产品组不同,其工序也不同,所以必须把产品组各生产工序的得分汇总起来(平均值Epg),然后计算总符合率。
这对于保证各要素进行均衡的评定也是必要的。
这样,产品组不同,所选的生产工序不同,“生产”要素计算出的符合率也可能不同。
b.每个产品组工序平均值Epg的计算公式如下:(E1+E2+E3+……En)Epg(%)= ──────────× 100%被评定工序数量c.整个过程的总符合率计算如下:(Ede+Epe+Ez+Epg+Ek)Ep(%)=───────────× 100%被评定过程要素的数量①.此外,作为对整个过程的评定的补充,也可以另外对“生产”要素中的各分要素进行评定,来反映质量管理体系的情况。
汽车行业VDA6.3过程审核检查表及评分标准
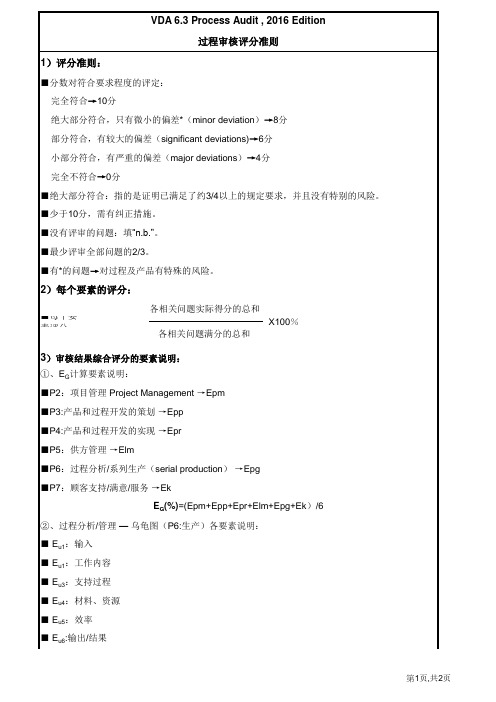
第2页,共2页
完全不符合→0分
■绝大部分符合:指的是证明已满足了约3/4以上的规定要求,并且没有特别的风险。
■少于10分,需有纠正措施。
■没有评审的问题:填“n.b."。
■最少评审全部问题的2/3。
■有*的问题→对过程及产品有特殊的风险。
2)每个要素的评分:
■每个要 素评分
各相关问题实际得分的总和
X100% 各相关问题满分的总和
3)审核结果综合评分的要素说明: ①、EG计算要素说明: ■P2:项目管理 Project Management →Epm ■P3:产品和过程开发的策划 →Epp ■P4:产品和过程开发的实现 →Epr ■P5:供方管理 →Elm ■P6:过程分析/系列生产(serial production) →Epg ■P7:顾客支持/满意/服务 →Ek
过程审核评分准则
■ Eu7:零件运输(Transport/Parts Handling) 4)审核结果的综合评分Overall Assessment:
总符合率EG(%) EG>=90
对过程的评定 符合
级别名称 A
80=<EG<90
有条件符合
B
EG<80
不符合
C
■审核结果的综合评分-降级规则
如果EG≥90%, 且P2…P7、E1…En、EU1…Eu7都>80%,评为A级;反之,则评为B级(A→B)
VDA 6.3 Process Audit , 2016 Edition
过程审核评分准则
1)评分准则:
内审方案评分标准
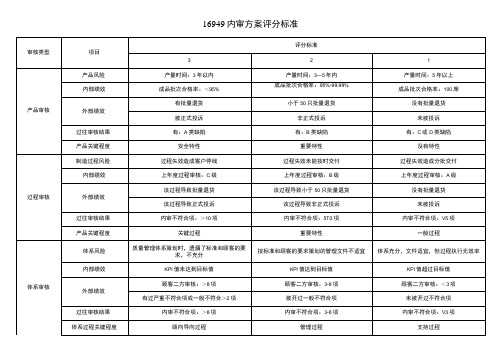
2
1
顾客特殊要求抽样
每年针对顾客要求的抽样W3项
供应商审核供应商质量管源自体系水平无:IS09001证书和IATF证书
只有:IS09001证书
有IATF证书
产品安全
安全特性
重要特性
没有特性
供应商绩效得分
85分以上
70-85分
70分以下
过往审核结果
有过严重不符合项或一般不符合>8项
一般不符合项:3-8项
有:B类缺陷
有:C或D类缺陷
产品关键程度
安全特性
重要特性
没有特性
过程审核
制造过程风险
过程失效造成客户停线
过程失效未能按时交付
过程失效造成分批交付
内部绩效
上年度过程审核:C级
上年度过程审核:B级
上年度过程审核:A级
外部绩效
该过程导致批量退货
该过程导致小于50只批量退货
没有批量退货
该过程导致正式投诉
该过程导致非正式投诉
4、供应商审核原则:单项得分为3分或总得分大于12分时,每年审核一次;总分在7—11之间每两年审核一次;总分小于7每三年审核一次。
5、本审核方案每年提交管理评审会议,评审其有效性。
编制:
审核
批准:
KPl值超过目标值
外部绩效
顾客二方审核:>8项
顾客二方审核:3-8项
顾客二方审核:<3项
有过严重不符合项或一般不符合>2项
被开过一般不符合项
未被开过不符合项
过往审核结果
内审不符合项:>8项
内审不符合项:3-8项
内审不符合项:V3项
体系过程关键程度
顾向导向过程
管理过程
支持过程
过程审核评分方法

附件一:过程审核评分方法1 提问和过程要素的单项评分:审核员根据对提问的要求以及在产品诞生过程(产品质量先期策划过程/服务诞生过程)和批量生产(实施服务)中满足过程审核要求的实际情况对提问的项目进行评定。
每个提问的得分以0、4、6、8、或10分进行评分,满足项目要求的程度是打分的根据。
评分不满10分时则须制订纠正/改进措施并确定落实其改进期限。
分数对符合要求程度的评定10 完全符合8 绝大部分符合,只有微小的偏差(*)6 部分符合,有较大的偏差4 少部分符合,有严重的偏差0 完全不符合备注(*)“绝大部分符合”指的是证明已满足了约3/4以上的规定要求。
没有特别的风险。
过程要素符合率Ee计算公式如下:各相关问题实际得分的总和Ee(%)= ─────────────× 100%各相关问题满分的总和2 审核员于每次过程审核结束时,将上述相关表单/记录整理后,将各项评分结果填入“表单-03过程审核提问的评分/符合率表”中,并计算其各项符合率,计算完成后提交给审核组长。
3 审核结果的综合评分(符合率计算方法):a.审核员首先须对下列各要素分别进行评定:产品服务—产品开发 Ede—策划 Ede—过程开发Epe—原材料/外购件Epg—外委服务或/和外购产品Ez—各道工序的平均值Ez —各道工序的平均值Epg—售后服务/用户满意Ek —用户服务/用户满意Ek备注1.在对服务进行审核时,请把下列描述中的生产换为服务,生产过程换为服务过程。
由于在要素“生产”中的产品组不同,其工序也不同,所以必须把产品组各生产工序的得分汇总起来(平均值Epg),然后计算总符合率。
这对于保证各要素进行均衡的评定也是必要的。
这样,产品组不同,所选的生产工序不同,“生产”要素计算出的符合率也可能不同。
b.每个产品组工序平均值Epg的计算公式如下:(E1+E2+E3+……En)Epg(%)= ──────────× 100%被评定工序数量c.整个过程的总符合率计算如下:(Ede+Epe+Ez+Epg+Ek)Ep(%)=───────────× 100%被评定过程要素的数量①.此外,作为对整个过程的评定的补充,也可以另外对“生产”要素中的各分要素进行评定,来反映质量管理体系的情况。
最新过程审核评分规则
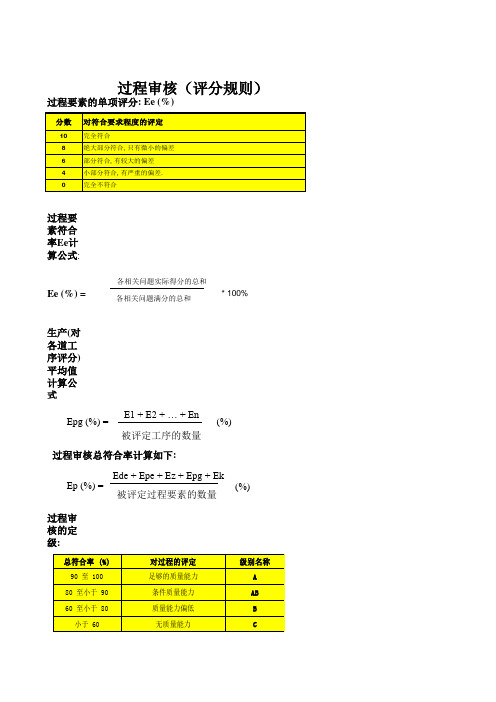
过程要素符合率Ee 计算公式:
Ee (%) =* 100%
生产(对各道工序评分)平均值计算公式
过程审核的定级:
降级原因说明:
1.若总符合率超过90%或80%,但其在一个或多个要素上符合率只达到75%以下,则从A 降到AB 或从AB 降到B ;
2.若有的提问得分为0,此不符合要求可能会给产品质量和过程绘制量造成严重的影响,则可从A 降到AB 或从AB 降到B 级。
在特别情况下,也可降为C 级。
3.须说明降级的原因。
过程审核(评分规则)
过程要素的单项评分: Ee (%)各相关问题实际得分的总和各相关问题满分的总和Epg (%) =被评定工序的数量E1 + E2 + … + En
(%)
过程审核总符合率计算如下:
Ep (%) =Ede + Epe + Ez + Epg + Ek 被评定过程要素的数量(%)。
产品审核、过程审核推荐标准
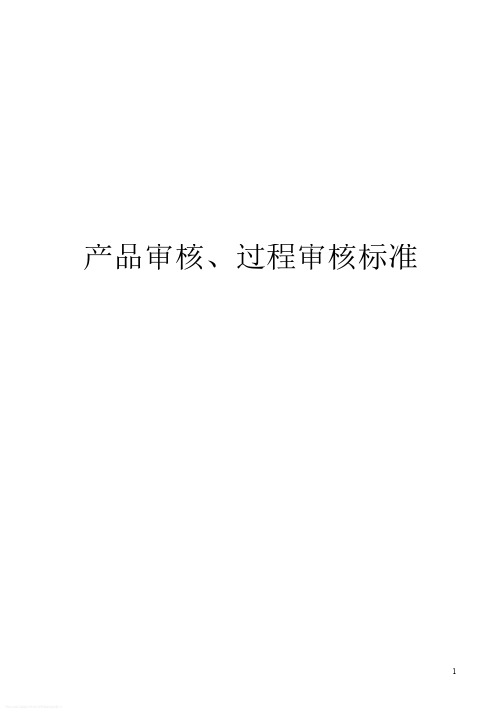
产品审核、过程审核标准一、供应商质量能力审核1 2 范围本标准规定了供应商质量能力审核评价方法及评级原则、审核要素、审核报告等内容。
本标准适用于中国一汽红旗品牌汽车零部件供应商质量能力审核,其它自主品牌整车公司汽车零部件供应商质量能力审核可参照执行。
审核要素对供应商质量能力审核分为以下三个要素:供应商管理;生产过程控制;顾客关怀、顾客满意度、服务。
3 评价方法及评级原则3.1 评价方法依据现场审核、资料查阅、双方沟通等确认的结果,按审核要素评价打分。
3.2 评级原则3.2.1 审核要素评分原则3.2.1.1 单项要素评分原则单项要素评分原则见表1。
表1 单项审核要素评分原则序号分数单项审核要素的符合程度1 2 3 4 5 108完全符合要求绝大部分*符合要求;小的偏差部分符合要求;大的偏差符合程度不足;严重偏差不符合要求64对“绝大部分”应理解是,有效的符合大于3/4的要求,没有特别的风险。
3.2.2.2 单项要素(E)审核符合率计算方法E审核要素的实得分E [%]=E×100% 该审核要素的满分3.2.2.3 审核要素的符合率供应商管理(E ),生产过程控制(E ),顾客关怀、顾客满意、服务(E )。
由于各个产品组具 Z PGK 有不同的工序,对于“生产过程控制”这个要素的评价必须将不同工序的评价结果汇总起来从而得到 E 。
要素供应商管理(E )和顾客关怀、顾客满意、服务(E )将各自得到评分。
PGZ K 3.2.2.4 生产过程控制审核要素的计算方法对每一道工序进行审核,根据产品组将各道工序的审核结果汇总起来,确保各个要素的同等重要 性。
因此,在“生产过程控制”这个大组中,对具体的产品组来说,由于工序是每一次审核时选定的, 故得到的符合率可能相同。
每个产品组的平均值E 的计算方法:PG E1+ E2+…+EnE [%]= PG ×100%已评价的工序数其中,E1和En 分别为各产品组生产的第一道工序和最后一道工序的单项要素(E )审核符合率。
- 1、下载文档前请自行甄别文档内容的完整性,平台不提供额外的编辑、内容补充、找答案等附加服务。
- 2、"仅部分预览"的文档,不可在线预览部分如存在完整性等问题,可反馈申请退款(可完整预览的文档不适用该条件!)。
- 3、如文档侵犯您的权益,请联系客服反馈,我们会尽快为您处理(人工客服工作时间:9:00-18:30)。
E1 + E2 + … + En
Epg (%) =
ቤተ መጻሕፍቲ ባይዱ
(%)
被评定工序的数量
过程审核总符合率计算如下:
(%)
Ede + Epe + Ez + Epg + Ek Ep (%) =
被评定过程要素的数量
过程审核的定级:
总符合率 (%) 90 至 100
80 至小于 90 60 至小于 80
小于 60
对过程的评定 足够的质量能力
过程审核评分规则
过程要素的单项评分: Ee (%)
分数 对符合要求程度的评定
10
完全符合
8
绝大部分符合, 只有微小的偏差
6
部分符合, 有较大的偏差
4
小部分符合, 有严重的偏差.
0
完全不符合
过程要素符合率Ee计算公式:
Ee (%) =
各相关问题实际得分的总和 各相关问题满分的总和
* 100%
生产(对各道工序评分)平均值计算公式
条件质量能力 质量能力偏低
无质量能力
降级原因说明: 1.若总符合率超过90%或80%,但其在一个或多个要素上符合率只达到75%以下,则从A降到AB 或从AB降到B; 2.若有的提问得分为0,此不符合要求可能会给产品质量和过程绘制量造成严重的影响,则可从 A降到AB或从AB降到B级。在特别情况下,也可降为D级。 3.须说明降级的原因。