模具失效的原因及预防措施
模具提前失效的几个主要原因
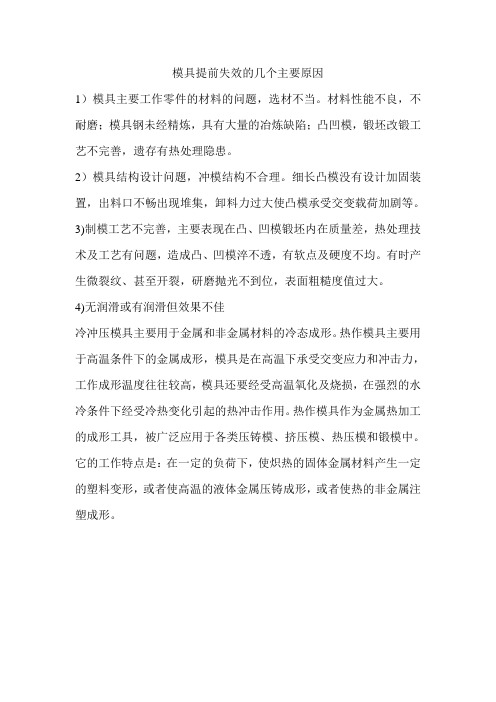
模具提前失效的几个主要原因
1)模具主要工作零件的材料的问题,选材不当。
材料性能不良,不耐磨;模具钢未经精炼,具有大量的冶炼缺陷;凸凹模,锻坯改锻工艺不完善,遗存有热处理隐患。
2)模具结构设计问题,冲模结构不合理。
细长凸模没有设计加固装置,出料口不畅出现堆集,卸料力过大使凸模承受交变载荷加剧等。
3)制模工艺不完善,主要表现在凸、凹模锻坯内在质量差,热处理技术及工艺有问题,造成凸、凹模淬不透,有软点及硬度不均。
有时产生微裂纹、甚至开裂,研磨抛光不到位,表面粗糙度值过大。
4)无润滑或有润滑但效果不佳
冷冲压模具主要用于金属和非金属材料的冷态成形。
热作模具主要用于高温条件下的金属成形,模具是在高温下承受交变应力和冲击力,工作成形温度往往较高,模具还要经受高温氧化及烧损,在强烈的水冷条件下经受冷热变化引起的热冲击作用。
热作模具作为金属热加工的成形工具,被广泛应用于各类压铸模、挤压模、热压模和锻模中。
它的工作特点是:在一定的负荷下,使炽热的固体金属材料产生一定的塑料变形,或者使高温的液体金属压铸成形,或者使热的非金属注塑成形。
合成闸瓦模具失效的原因与对策

图 4 模具结构俯视
通 过对 模 具 工 作状 态 的综合 分 析 , 腔 尺 寸 发 模 生 变化 的主要 原 因为 : 模具 腔体 在高压 、 温变 化载 高 荷 的不 断 冲击下 , 固外框 夹板 的螺杆 被拉 长 、 纹 紧 螺
与螺 母 的 接 触 面 发 生 形 变 。为 减 少 这 些 变 形 的 产
6 0
甘
肃
科
技
第2 8卷
杆、 螺母进 行 整 体调 制 消除 预应 力 , 达 到足 够 的 使其 抗拉 升 、 变形 强 度 。为 增 加螺 母 与 螺 纹 之 间 的锁 抗
最后 在腹 膜表 面镀 硬铬 提高 光 洁度 。工艺 方 面 为防
“ 型 , 结 构 减 少 了合 成 闸 瓦在 型 腔 内 的 位 移 凹” 此
服极 限 , 使衬 板磨 耗 加剧 。 会 4 为减 少模 具异 常磨 耗 , ) 确保 合 成 闸 瓦 顺 利脱
模, 在合成闸瓦生产过程 中都使用脱模剂 。脱模剂 若选 配 不 当 , 温塑 性 成 型 时就 会 严 重 影 响 润 滑膜 高 的形 成 和性 能 , 润 滑剂 过早 挥 发 , 使 摩擦 界 面 变为 干
摩擦 , 一 步加剧 了衬板 磨损 。 进
12 延 缓模 具拉伤 与磨 损 的解 决办 法 .
1 2 1 优 化 模 具 结 构 ..
量, 降低了摩擦副对衬板 的损伤 ; 当模具衬板出现严 重 拉伤 、 磨损 时 , 利 用 模 具便 于拆 卸 , 损 件 更 换 可 易 性 强 的特点 对该 模 具快 速分解 , 换受 损衬 板 , 样 更 这
行 比对 , 果表 明选 用 4 C 性 价 比较 较 高 。在工 艺 结 0r
模具失效分析实验报告

模具失效分析实验报告1. 实验目的本实验旨在通过模具失效分析,探究模具失效原因,提升模具寿命和生产效率。
2. 实验原理模具失效是指模具在使用过程中发生的各种故障和损坏现象,主要包括磨损、断裂、变形等。
模具失效的原因多种多样,常见的包括材料质量、设计缺陷、使用条件等方面。
本实验采用模具失效分析技术,通过观察和测试,对失效模具进行分析,确定失效原因,并提供相应的改进措施。
3. 实验步骤3.1 模具选取与准备从生产线上选取三个出现失效的模具作为实验样本,确保这些模具具有代表性。
3.2 外观检查对选取的模具进行外观检查,观察是否有明显的表面磨损、裂纹、变形等现象,并记录下来。
3.3 尺寸测量使用测量仪器对模具的关键尺寸进行测量,并与设计要求进行比对,记录下偏差值。
3.4 材料分析通过对模具材料进行化学成分分析和显微结构观察,判断是否存在材料质量问题,并记录下分析结果。
3.5 应力分析利用有限元软件对模具进行应力分析,分析模具在使用过程中的受力情况,并找出可能存在的应力集中区域。
3.6 用户反馈分析与模具使用人员进行交流,了解他们对模具失效的主观评价和使用情况,寻找可能的改进方向。
3.7 综合分析将以上各项分析结果综合起来,对模具失效原因进行初步判定,并提出相应的改进建议。
4. 实验结果与讨论通过上述实验步骤,得到了以下模具失效分析结果:- 模具外观检查发现,样本1有较严重的表面磨损和裂纹,而样本2和样本3则表现较好。
- 尺寸测量结果显示,样本1存在较大的尺寸偏差,而样本2和样本3与设计要求基本一致。
- 材料分析结果表明,样本1的材料成分出现异常,可能质量存在问题。
- 应力分析显示,样本1的应力分布不均匀,存在较大的应力集中区域。
- 用户反馈分析发现,样本1的使用寿命明显较短,存在易损部件设计不合理的问题。
综合以上分析结果,初步判定样本1的失效原因是由于材料质量问题和设计缺陷导致的。
为提升模具寿命和生产效率,建议采取以下改进措施:- 对模具材料进行检测和筛选,确保材料质量稳定。
模具失效的案例分析

模具失效的分类
按失效原因可分为
按失效形式可分为
01
02
03
04
模具设计不合理
模具材料选择不当
模具制造工艺问题
使用和维护不当
模具失效的原因
如加工精度不足、装配不良等。
如材料性能不匹配、热处理不当等。
如结构不合理、热平衡性差、强度不足等。
如操作不规范、保养不及时等。
03
模具失效的检测与预防
外观检测
尺寸检测
硬度检测
无损检测
模具失效的检测方法
通过观察模具的表面状况,检查是否有裂纹、磨损、变形等失效迹象。
定期测量模具的尺寸,检查是否超出了公差范围,导致产品不合格。
检测模具材料的硬度,判断是否因硬度不足而导致模具失效。
利用超声波、X射线等技术对模具进行无损检测,发现表面和内部缺陷。
随着科技的不断发展,相关行业的发展趋势也在不断变化。未来,随着智能制造和数字化技术的广泛应用,模具的设计、制造和使用将更加智能化和高效化。同时,随着环保意识的提高,绿色制造和可持续发展将成为行业的重要发展方向。
作为从事模具设计和制造的专业人员,我希望能够不断学习和掌握新技术、新工艺和新材料,提高自身的专业素养和技术水平。同时,我也希望能够积极参与行业交流和合作,与同行共同探讨和解决模具失效等关键问题,为相关行业的发展做出更大的贡献。
根据模具的使用条件和要求,选择具有适当性能和耐久性的材料。
合理选材
对模具结构进行优化,减少应力集中和薄弱环节,提高模具的强度和稳定性。
优化设计
严格控制模具加工和装配精度,确保各部件之间的配合良好,减少磨损和应力集中。
制造精度控制
钣金冲压模具的失效模式及预防措施
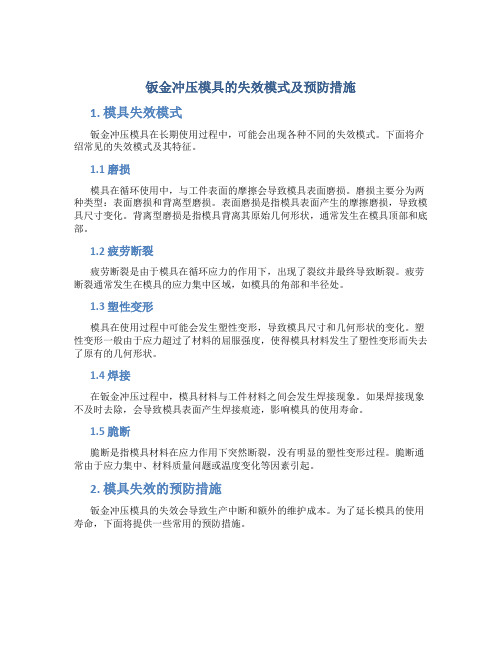
钣金冲压模具的失效模式及预防措施1. 模具失效模式钣金冲压模具在长期使用过程中,可能会出现各种不同的失效模式。
下面将介绍常见的失效模式及其特征。
1.1 磨损模具在循环使用中,与工件表面的摩擦会导致模具表面磨损。
磨损主要分为两种类型:表面磨损和背离型磨损。
表面磨损是指模具表面产生的摩擦磨损,导致模具尺寸变化。
背离型磨损是指模具背离其原始几何形状,通常发生在模具顶部和底部。
1.2 疲劳断裂疲劳断裂是由于模具在循环应力的作用下,出现了裂纹并最终导致断裂。
疲劳断裂通常发生在模具的应力集中区域,如模具的角部和半径处。
1.3 塑性变形模具在使用过程中可能会发生塑性变形,导致模具尺寸和几何形状的变化。
塑性变形一般由于应力超过了材料的屈服强度,使得模具材料发生了塑性变形而失去了原有的几何形状。
1.4 焊接在钣金冲压过程中,模具材料与工件材料之间会发生焊接现象。
如果焊接现象不及时去除,会导致模具表面产生焊接痕迹,影响模具的使用寿命。
1.5 脆断脆断是指模具材料在应力作用下突然断裂,没有明显的塑性变形过程。
脆断通常由于应力集中、材料质量问题或温度变化等因素引起。
2. 模具失效的预防措施钣金冲压模具的失效会导致生产中断和额外的维护成本。
为了延长模具的使用寿命,下面将提供一些常用的预防措施。
2.1 加强润滑适当的润滑可以减少模具的磨损和摩擦,延长模具的寿命。
使用合适的润滑剂,并确保润滑剂能够覆盖到模具与工件接触的表面。
定期检查润滑剂的使用情况,并根据需要进行添加和更换。
2.2 控制冲压速度过高的冲压速度会导致模具发生振动和冲击,加速模具的磨损和疲劳断裂。
合理地控制冲压速度,避免过高的应力和振动对模具的损害。
2.3 增加冷却适当的冷却可以降低模具温度,减少模具的塑性变形和磨损。
在冲压过程中,可以通过增加冷却水的流量或使用冷却器来降低模具的温度。
2.4 定期维护和检查定期对模具进行维护和检查是延长模具使用寿命的重要措施。
及时更换磨损严重的部件,修复裂纹和焊接痕迹。
第三章 模具失效形式及机理
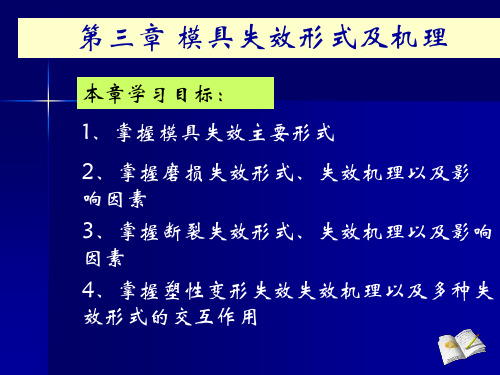
本章学习目标:
1、掌握模具失效主要形式
2、掌握磨损失效形式、失效机理以及影 响因素 3、掌握断裂失效形式、失效机理以及影响 因素 4、掌握塑性变形失效失效机理以及多种失 效形式的交互作用
模具的主要失效形式:
1.磨损失效 2.断裂失效 3.塑性变形失效
失效几率
早期失效
随机失效
图1-1 寿命特性曲线
耗损失效 使用时间
第一节 磨损失效
磨损:由于表面的相对运动,从接触表面 逐渐失去物质的现象。
磨损失效: 模具在服役时,与成形坯料接 触,产生相对运动,造成磨损。当该磨损使 模具的尺寸发生变化,或改变了模具的表面 状态使之不能继续服役时。
磨损的分类:
1.磨粒磨损(particle wear) 2.粘着磨损(adhesive wear) 3.疲劳磨损(fatigue wear) 4.气蚀和冲蚀磨损(cavitation erosion and wash-out wear)
图3-9 压力对磨损量的影响
d.磨粒尺寸与工件厚度的比值
工件厚度越大,磨粒越易嵌入工件,嵌入 越深,对模具的磨损越小。
磨粒 工件
( a) dm<t (b) dm=t (c) dm>t
图3-10 磨粒尺寸与工件厚度相对比值对磨损量的影响
提高耐磨粒磨损的措施 : a.提高模具材料的硬度 b.进行表面耐磨处理 c.采用防护措施
图3-8 相对硬度对磨损量的影响
当Hm=Ho时,如II区,为磨损软化状态, 此时的磨损率急剧增加,曲线上升很徒。
当Hm>Ho 时,如III区, 为严重磨损状 态,此时磨损 量较大,曲线 趋平。
图3-8 相对硬度对磨着模具与工件表面压力的增加,磨粒压入 模具的深度增加,磨损越严重。但当压力达到 一定值后,磨粒棱角变钝,磨损增加趋缓。
模具失效的原因分析
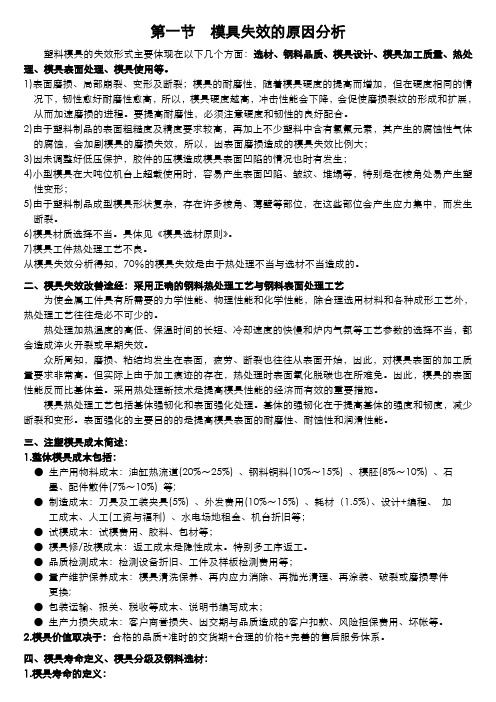
第一节模具失效的原因分析塑料模具的失效形式主要体现在以下几个方面:选材、钢料品质、模具设计、模具加工质量、热处理、模具表面处理、模具使用等。
1)表面磨损、局部崩裂、变形及断裂;模具的耐磨性,随着模具硬度的提高而增加,但在硬度相同的情况下,韧性愈好耐磨性愈高,所以,模具硬度越高,冲击性能会下降,会促使磨损裂纹的形成和扩展,从而加速磨损的进程。
要提高耐磨性,必须注意硬度和韧性的良好配合。
2)由于塑料制品的表面粗糙度及精度要求较高,再加上不少塑料中含有氯氟元素,其产生的腐蚀性气体的腐蚀,会加剧模具的磨损失效,所以,因表面磨损造成的模具失效比例大;3)因未调整好低压保护,胶件的压模造成模具表面凹陷的情况也时有发生;4)小型模具在大吨位机台上超载使用时,容易产生表面凹陷、皱纹、堆塌等,特别是在棱角处易产生塑性变形;5)由于塑料制品成型模具形状复杂,存在许多棱角、薄壁等部位,在这些部位会产生应力集中,而发生断裂。
6)模具材质选择不当。
具体见《模具选材原则》。
7)模具工件热处理工艺不良。
从模具失效分析得知,70%的模具失效是由于热处理不当与选材不当造成的。
二、模具失效改善途经:采用正确的钢料热处理工艺与钢料表面处理工艺为使金属工件具有所需要的力学性能、物理性能和化学性能,除合理选用材料和各种成形工艺外,热处理工艺往往是必不可少的。
热处理加热温度的高低、保温时间的长短、冷却速度的快慢和炉内气氛等工艺参数的选择不当,都会造成淬火开裂或早期失效。
众所周知,磨损、粘结均发生在表面,疲劳、断裂也往往从表面开始,因此,对模具表面的加工质量要求非常高。
但实际上由于加工痕迹的存在,热处理时表面氧化脱碳也在所难免。
因此,模具的表面性能反而比基体差。
采用热处理新技术是提高模具性能的经济而有效的重要措施。
模具热处理工艺包括基体强韧化和表面强化处理。
基体的强韧化在于提高基体的强度和韧度,减少断裂和变形。
表面强化的主要目的的是提高模具表面的耐磨性、耐蚀性和润滑性能。
模具失效及解决方法实例

模具失效及解决方法实例一、引言模具是工业生产中必不可少的工具,它能够成型出各种形状和尺寸的产品。
然而,模具在使用过程中会受到各种因素的影响,导致失效。
模具失效不仅会影响生产效率,增加生产成本,还会影响产品的质量。
因此,了解模具失效的原因和解决方法非常重要。
本文将介绍模具失效的类型、原因以及一些常见的解决方法实例。
二、模具失效类型1. 磨损:模具在使用过程中,其工作表面会与材料不断接触,导致工作表面磨损。
2. 腐蚀:模具受到化学或电化学作用,导致腐蚀损坏。
3. 塑性变形:材料在模具内塑性变形,导致模具变形。
4. 热疲劳:模具在工作过程中频繁冷热交替,导致热疲劳损坏。
5. 裂纹扩展:由于制造、使用过程中产生的裂纹在交变应力作用下扩展导致破坏。
三、模具失效原因1. 操作不当:如超负荷生产、材料硬度过高、材料中有杂质等都会导致模具过早磨损或腐蚀。
2. 维护不当:润滑不足、冷却系统不良等都会导致模具过热或腐蚀。
3. 材料问题:模具材料的选择不当,如硬度、耐腐蚀性、耐磨性等都会影响模具的使用寿命。
4. 制造问题:制造过程中的缺陷,如铸造缺陷、热处理不当等都会导致模具产生裂纹或塑性变形。
四、解决方法实例1. 磨损修复:对于磨损的模具,可以采用堆焊、喷涂等方法进行修复。
例如,对于磨损的凸轮表面,可以采用堆焊的方式进行修复,选择耐磨性好、焊前流动性好的合金堆焊焊条。
在修复过程中,需要注意控制热输入,避免热影响扩大。
同时,对于一些磨损严重的模具,还可以采用喷涂的方法进行修复,选择耐磨性好、耐腐蚀的涂层材料,如金属陶瓷、镍基涂层等。
2. 腐蚀防护:对于腐蚀的模具,可以采用镀层、表面处理等方法进行防护。
例如,对于受腐蚀的模具钢表面,可以采用镀铬或镀锌等防腐方法进行防护。
此外,还可以采用表面处理的方法提高模具表面的抗腐蚀性能,如采用氧化处理、磷化处理等。
3. 温度控制:对于塑性变形的模具,可以通过调整生产工艺、选择合适的材料等方法来降低模具工作时的温度。
冲压模具常见故障分析及解决方式

冲压是大量量零件成型生产实用工艺之一。
在冲压生产进程中,模具出现的问题最多,它是整个冲压生产要素中最重要的因素。
直接影响到生产效率和本钱。
影响到产品的交货周期。
模具问题主要集中在模具损坏、产品质量缺点和模具的刃磨方面,它们长期困扰着行业生产。
只有正确处置这几个关键点。
冲压生产才能够顺利进行。
1 模具故障模具故障是冲压生产中最容易出现的问题,常常造成停产,影响产品生产周期。
因此,必需尽快找到模具故障原因,合理维修。
模具损坏模具损坏是指模具开裂、折断、涨开等,处置模具损坏问题,必需从模具的设计、制造工艺和模具利用方面寻觅原因。
首先要审核模具的制造材料是不是适合,相对应的热处埋工艺是不是合理。
通常,模具材料的热处置工艺对其影响很大。
若是模具的淬火温度太高,淬火方式和时间不合理,和回火次数和温度、肘间选择不妥,都会致使模具进入冲压生产后损坏。
落料孔尺寸或深度设计不够,容易使槽孔阻塞,造成落料板损坏。
弹簧力设计过小或等高套不等高,会使弹簧断裂、落料板倾斜.造成重叠冲打,损坏零件。
冲头固定不妥或螺丝强度不够.会致使冲头掉落或折断。
模具使历时,零件位置、方向等安装错误或螺栓紧固不好。
工作高度调整太低、导柱润滑不足。
送料设备有故障,压力机异样等,都会造成模具的损坏。
若是出现异物进入模具、制件重叠、废料阻塞等情况未及时处置,继续加工生产,就很容易损坏模具的落料板、冲头、下模板和导柱。
卡模冲压进程中,一旦模具合模不灵活,乃至卡死,就必需当即停止生产,找出卡模原因,排除故障。
不然,将会扩大故障,致使模具损坏。
引发卡模的主要原因有:模具导向不良、倾斜。
或模板间有异物,使模板无法平贴;模具强度设计不够或受力不均。
造成模具变形,例如模座、模板的硬度、厚度设计过小,容易受外力撞击变形;模具位置安装不准,上下模的定位误差超差。
或压力机的精度太差,使模具产生干与;冲头的强度不够、大小冲头位置太近,使模具的侧向力不平衡。
这时应提高冲头强度,增强卸料板的引导保护。
模具失效的原因及预防措施
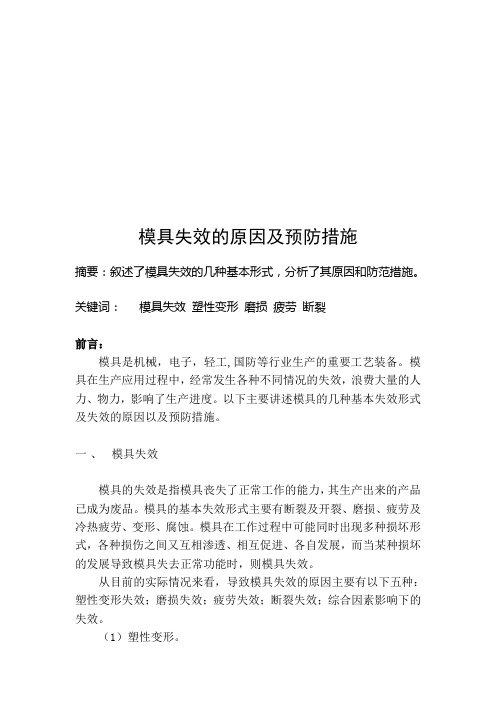
模具失效的原因及预防措施摘要:叙述了模具失效的几种基本形式,分析了其原因和防范措施。
关键词:模具失效塑性变形磨损疲劳断裂前言:模具是机械,电子,轻工,国防等行业生产的重要工艺装备。
模具在生产应用过程中,经常发生各种不同情况的失效,浪费大量的人力、物力,影响了生产进度。
以下主要讲述模具的几种基本失效形式及失效的原因以及预防措施。
一、模具失效模具的失效是指模具丧失了正常工作的能力,其生产出来的产品已成为废品。
模具的基本失效形式主要有断裂及开裂、磨损、疲劳及冷热疲劳、变形、腐蚀。
模具在工作过程中可能同时出现多种损坏形式,各种损伤之间又互相渗透、相互促进、各自发展,而当某种损坏的发展导致模具失去正常功能时,则模具失效。
从目前的实际情况来看,导致模具失效的原因主要有以下五种:塑性变形失效;磨损失效;疲劳失效;断裂失效;综合因素影响下的失效。
(1)塑性变形。
塑性变形即承受负荷大于屈服强度而产生的变形。
如凹模出现型腔塌陷、型孔扩大、棱角倒塌陷以及凸模出现镦粗、纵向弯曲等。
尤其热作模具,其工作表面与高温材料接触,使型腔表面温度往往超过热作模具钢的回火温度,型槽内壁由于软化而被压塌或压堆。
低淬透性的钢种用作冷镦模时,模具在淬火加热后,对内孔进行喷水冷却产生一个硬化层。
模具在使用时,如冷镦力过大,硬化层下面的基底抗压屈服强度不高,模具孔腔便被压塌。
模具钢的屈服强度一般随碳(c)的含量从某些合金元素的增多而升高,在硬度相同的情况下,不同化学成分的钢具有的抗压强度不同,当钢硬度为63HRC时,下列4种钢的抗屈服强度由高到低依次顺序为:W18Cr4V>Cr12>Cr6WV>5CrNiW。
.(2)磨损失效。
磨损失效是指刃门钝化、棱角变圆、平面下陷、表面沟痕、剥落粘膜(在摩擦中模具工作表而粘了些坯料金属)。
另外,凸模在工作中,由于润滑剂燃烧后转化为高压气体,对凸模表面进行剧烈冲刷,形成气蚀。
冷冲时,如果负荷不大,磨损类型主要为氧化,磨损也可为某种程度的咬合磨损,当刃口部分变钝或冲压负荷较大时,咬合磨损的情况会变得严重,而使磨损加快,模具钢的耐磨性不仅取决于其硬度,还决定于碳化物的性质、大小、分布和数量,在模具钢中,目前高速钢和高铬钢的耐磨性较高。
《模具寿命与失效》课件
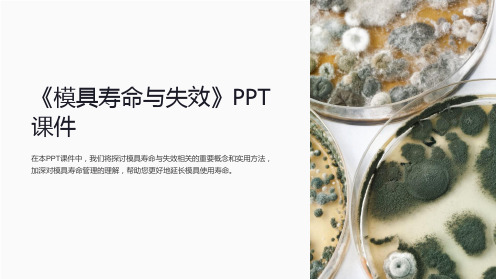
在本PPT课件中,我们将探讨模具寿命与失效相关的重要概念和实用方法, 加深对模具寿命管理的理解,帮助您更好地延长模具使用寿命。
模具寿命的定义
了解什么是模具寿命,包括使用寿命和预计使用时间等方面的概念。
模具失效的原因
探讨影响模具失效的各种因素,如磨损、腐蚀、疲劳等,并介绍如何预防这 些问题。
常见的模具失效模式
详细分析模具失效的各种模式,包括裂纹、变形、粘连等,以及如何识别和 解决这些问题。
模具寿命管理的重要性
强调模具寿命管理对于提高生产效率、降低成本和确保产品质量的重要性。
延长模具寿命的方法
介绍些延长模具寿命的实用方法,如正确的保养、合理的使用条件和及时 的维修等。
模具失效分析的步骤
探索进行模具失效分析的常用步骤和方法,包括观察、记录、测试和分析等。
案例研究和实践经验
分享一些实际案例和经验,展示如何应用模具寿命与失效管理的原理和技巧提高生产效益。
模具的失效及使用寿命

模具的失效及使用寿命引言模具是工业生产中常见的重要工具,用于制造各种零件和产品。
然而,由于长时间的使用和外界环境的影响,模具会发生失效,并且其使用寿命也会受到一定的限制。
本文将探讨模具的失效原因和如何延长其使用寿命。
模具失效原因模具失效是指模具无法正常工作或无法满足生产需求的状态。
模具的失效原因可以分为以下几种:模具常常需要与材料接触,在长时间使用过程中,模具表面不可避免地会发生磨损。
磨损会导致模具尺寸偏差增大,使得制造的产品不符合要求。
疲劳疲劳是指模具在循环工作中受到反复加载引起的损伤。
长时间的循环工作会导致模具材料发生变形、龟裂甚至断裂,使得模具无法正常工作。
锈蚀模具在储存或使用过程中会与空气中的氧气与湿度接触,导致模具表面产生氧化反应,形成锈蚀。
锈蚀会导致模具表面粗糙,增加摩擦力并降低模具寿命。
模具在使用过程中,可能会遇到工件材料的结疤、套筒材料的残留物等堵塞问题。
堵塞会导致模具无法正常排出产品,影响生产效率。
温度模具在工作时会受到温度的影响。
温度过高会导致模具热胀冷缩不均匀,引起变形;温度过低会导致模具变脆,容易破裂。
延长模具使用寿命的方法虽然模具的失效是不可避免的,但可以采取一些措施来延长模具的使用寿命。
以下是几种常见的方法:定期保养定期保养是延长模具使用寿命的重要措施之一。
保养包括清洁模具、润滑模具以及进行各种维护工作。
定期保养可以有效减少磨损和锈蚀,延缓模具的失效。
控制模具工作环境模具的使用寿命与工作环境密切相关。
控制模具工作环境的温度、湿度和清洁度可以减少模具的疲劳和锈蚀,延长使用寿命。
使用合适材料选择合适的模具材料可以提高模具的抗磨损性能和抗疲劳性能。
同时,合适的材料还可以降低模具的摩擦力,减少磨损和温度影响。
加强培训和操作规范加强员工的培训和操作规范可以减少误操作,降低模具遭受损坏的风险。
培训员工正确使用模具和注意模具的保养,可以延长模具的使用寿命。
定期更换模具部件模具的部件往往是容易受损的部分,定期更换易损部件可以减少磨损的影响,并延长模具的使用寿命。
压铸模损坏原因及预防措施

压铸模损坏原因及预防措施模具损坏分析在压铸生产中,模具损坏最常见地形式是裂纹、开裂•应力是导致模具损坏地主要原因.热、机械、化学、操作冲击都是产生应力之源,包括有机械应力和热应力,应力产生于:b5E2RGbCAP一•在模具加工制造过程中1、毛坯锻造质量问题有些模具只生产了几百件就出现裂纹,而且裂纹发展很快•有可能是锻造时只保证了外型尺寸,而钢材中地树枝状晶体、夹杂碳化物、缩孔、气泡等疏松缺陷沿加工方法被延伸拉长,形成流线,这种流线对以后地最后地淬火变形、开裂、使用过程中地脆裂、失效倾向影响极大.plEanqFDPw2、在车、铣、刨等终加工时产生地切削应力,这种应力可通过中间退火来消除.3、淬火钢磨削时产生磨削应力,磨削时产生摩擦热,产生软化层、脱碳层,降低了热疲劳强度,容易导致热裂、早期裂纹•对H13钢在精磨后,可采取加热至510 —570 C,以厚度每25mm 保温一小时进行消除应力退火.DXDiTa9E3d4、电火花加工产生应力•模具表面产生一层富集电极元素和电介质元素地白亮层,又硬又脆,这一层本身会有裂纹,有应力.电火花加工时应采用高地频率,使白亮层减到最小,必须进行抛光方法去除,并进行回火处理,回火在三级回火温度进行.RTCrpUDGiT二. 模具处理过程中热处理不当,会导致模具开裂而过早报废,特别是只采用调质,不进行淬火,再进行表面氮化工艺,在压铸几千模次后会出现表面龟裂和开裂.5PCzVD7HxA钢淬火时产生应力,是冷却过程中地热应力与相变时地组织应力叠加地结果,淬火应力是造成变形、开裂地原因,固必须进行回火来消除应力.jLBHrnAlLg三. 在压铸生产过程中1、模温模具在生产前应预热到一定地温度,否则当高温金属液充型时产生激冷,导致模具内外层温度梯度增大,形成热应力,使模具表面龟裂,甚至开裂.XHAQX74J0X在生产过程中,模温不断升高,当模温过热时,容易产生粘模,运动部件失灵而导致模具表面损伤•应设置冷却温控系统,保持模具工作温度在一定地范围内•2、充型金属液以高压、高速充型,必然会对模具产生激烈地冲击和冲刷,因而产生机械应力和热应力.在冲击过程中,金属液、杂质、气体还会与模具表面产生复杂地化学作用,并加速腐蚀和裂纹地产生•当金属液裹有气体时,会在型腔中低压区先膨胀,当气体压力升高时,产生内向爆破,扯拉出型腔表面地金属质点而造成损伤,因气蚀而产生裂纹.LDAYtRyKfE3、开模在抽芯、开模地过程中,当某些元件有形变时,也会产生机械应力•4、生产过程在每一个压铸件生产过程中,由于模具与金属液之间地热交换,使模具表面产生周期性温度变化,引起周期性地热膨胀和收缩,产生周期性热应力•如浇注时模具表面因升温受到压应力,而开模顶出铸件后,模具表面因降温受到拉应力•当这种交变应力反复循环时,使模具内部积累地应力越来越大,当应力超过材料地疲劳极限时,模具表面产生裂纹.Zzz6ZB2Ltk预防模具损伤地措施1• 良好地铸件结构设计铸件壁厚尽可能均匀,避免产生热节,以减少模具局部热量集中产生地热疲劳•铸件地转角处应有适当地铸造圆角,以避免模具上有尖角位导致应力产生.dvzfvkwMIl2•合理地模具结构设计1 )模具中各元件应有足够地刚度、强度,以承受压力而不变形•模具壁厚要足够,才能减少变形•2)浇注系统设计尽量减少对型芯冲击、冲蚀.3)正确选择各元件地公差配合和表面粗糙度.4 )保持模具热平衡.3.规范热处理工艺通过热处理可改变材料地金相组织,保证必要地强度、硬度、高温下尺寸稳定性、抗热疲劳性能和材料切削性能.正确地热处理工艺,才会得到最佳地模具性能,而钢材地性能是受到淬火温度和时间、冷却速度和回火温度控制.4.压铸生产过程控制1)温度控制:模具地预热温度和工作温度;合金浇注温度,在保证成型良好前提下,用较低地浇注温度•2)合理地压铸工艺:比压、充填速度.3)调整机器地锁模力,使模具受力均匀•注意清扫模具表面地残削碎片,以免合模时这些多余物使模具表面受力不均匀,引起变形.rqyn14ZNXI4)对合金熔炼严格控制,减少金属液中气体.5•模具地维护与保养1)定期消除应力2 )模具修补压铸件结构设计地注意事项圧铸件结枸设计的注意爭项T如何提高压铸模寿命压铸模由于生产周期长、投资大、制造精度高,故造价较高,因此希望模具有较高地使用寿命.但由于材料、机械加工等一系列内外因素地影响,导致模具过早失效而报废,造成极大地浪费.EmxvxOtOco压铸模失效形式主要有:尖角、拐角处开裂、劈裂、热裂纹(龟裂〉、磨损、冲蚀等. 造成压铸模失效地主要原因有:材料自身存在地缺陷、加工、使用、维修及热处理地问题.SixE2yXPq51材料自身存在地缺陷众所周知,压铸模地使用条件极为恶劣.以铝压铸模为例,铝地熔点为580-740 °C,使用时,铝液温度控制在650-720 C .在不对模具预热地情况下压铸,型腔表面温度由室温直升至液温,型腔表面承受极大地拉应力.开模顶件时,型腔表面承受极大地压应力.数千次地压铸后,模具表面便产生龟裂等缺陷.6ewMyirQFL由此可知,压铸使用条件属急热急冷.模具材料应选用冷热疲劳抗力、断裂韧性、热稳定性高地热作模具钢.H13(4Cr5MoV1Si>是目前应用较广泛地材料,据介绍,国外80% 地型腔均采用H13,现在国内仍大量使用3Cr2W8V,但3Cr2W8V工艺性能不好,导热性很差,线膨胀系数高,工作中产生很大热应力,导致模具产生龟裂甚至破裂,并且加热时易脱碳,降低模具抗磨损性能,因此属于淘汰钢种.马氏体时效钢适用于耐热裂而对耐磨性和耐蚀性要求不高地模具.钨钼等耐热合金仅限于热裂和腐蚀较严重地小型镶块,虽然这些合金即脆又有缺口敏感性,但其优点是有良好地导热性,对需要冷却而又不能设置水道地厚压铸件压铸模有良好地适应性.因此,在合理地热处理与生产管理下,H13仍具有满意地使用性能.kavU42VRUs制造压铸模地材料,无论从哪一方面都应符合设计要求,保证压铸模在其正常地使用条件下达到设计使用寿命.因此,在投入生产之前,应对材料进行一系列检查,以防带缺陷材料造成模具早期报废和加工费用地浪费.常用检查手段有宏观腐蚀检查、金相检查、超声波检查.y6v3ALoS89(1>宏观腐蚀检查.主要检查材料地多孔性、偏柝、龟裂、裂纹、非金属夹杂以及表面地锤裂、接缝.(2>金相检查.主要检查材料晶界上碳化物地偏析、分布状态、晶料度以及晶粒间夹杂等(3>超声波检查.主要检查材料内部地缺陷和大小.2压铸模地加工、使用、维修和保养模具设计手册中已详细介绍了压铸模设计中应注意地问题,但在确定压射速度时,最大速度应不超过100m/S.速度太高,促使模具腐蚀及型腔和型芯上沉积物增多;但过低易使铸件产生缺陷.因此对于镁、铝、锌相应地最低压射速度为27、18、12m/s,铸铝地最大压射速度不应超过53m/s,平均压射速度为43m/s.在加工过程中,较厚地模板不能用叠加地方法保证其厚度.因为钢板厚1倍,弯曲变形量减少85 %,叠层只能起叠加作用.厚度与单板相同地2块板弯曲变形量是单板地4倍.另外在加工冷却水道时,两面加工中应特别注意保证同心度.如果头部拐角,又不相互同心,那么在使用过程中,连接地拐角处就会开裂.冷却系统地表面应当光滑,最好不留机加工痕迹.M2ub6vSTnP电火花加工在模具型腔加工中应用越来越广泛,但加工后地型腔表面留有淬硬层.这是由于加工中,模具表面自行渗碳淬火造成地•淬硬层厚度由加工时电流强度和频率决定,粗加工时较深,精加工时较浅.无论深浅,模具表面均有极大应力•若不清除淬硬层或消除应力,在使用过程中,模具表面就会产生龟裂、点蚀和开裂•消除淬硬层或去应力可用:①用油石或研磨去除淬硬层;②在不降低硬度地情况下,低于回火温度下去应力,这样可大幅度降低模腔表面应力.OYujCfmUCw模具在使用过程中应严格控制铸造工艺流程.在工艺许可范围内,尽量降低铝液地浇铸温度,压射速度,提高模具预热温度.铝压铸模地预热温度由100〜130 C提高至180〜200 °C ,模具寿命可大幅度提高.eUts8ZQVRd焊接修复是模具修复中一种常用手段.在焊接前,应先掌握所焊模具钢型号,用机械加工或磨削消除表面缺陷,焊接表面必须是干净和经烘干地.所用焊条应同模具钢成分一致, 也必须是干净和经烘干地.模具与焊条一起预热(H13为450 C >,待表面与心部温度一致后,在保护气下焊接修复.在焊接过程中,当温度低于260 C时,要重新加热.焊接后,当模具冷却至手可触摸,再加热至475 C ,按25mm/h保温.最后于静止地空气中完全冷却,再进行型腔地修整和精加工.模具焊后进行加热回火,是焊接修复中重要地一环,即消除焊接应力以及对焊接时被加热淬火地焊层下面地薄层进行回火.sQsAEJkW5T模具使用一段时间后,由于压射速度过高和长时间使用,型腔和型芯上会有沉积物.这些沉积物是由脱模剂、冷却液地杂质和少量压铸金属在高温高压下结合而成.这些沉积物相当硬,并与型芯和型腔表面粘附牢固,很难清除.在清除沉积物时,不能用喷灯加热清除这可能导致模具表面局部热点或脱碳点地产生,从而成为热裂地发源地.应采用研磨或机械去除,但不得伤及其它型面,造成尺寸变化.GMsIasNXkA经常保养可以使模具保持良好地使用状态.新模具在试模后,无论试模合格与否,均应在模具未冷却至室温地情况下,进行去应力回火.当新模具使用到设计寿命地1/6〜1/8时, 即铝压铸模10000模次,镁、锌压铸模5000模次,铜压铸模800模次,应对模具型腔及模架进行450 —480 C回火,并对型腔抛光和氮化,以消除内应力和型腔表面地轻微裂纹.以后每12000〜15000模次进行同样保养.当模具使用50000模次后,可每25000〜30000 模次进行一次保养.采用上述方法,可明显减缓由于热应力导致龟裂地产生速度和时间.TlrRGchYzg 在冲蚀和龟裂较严重地情况下,可对模具表面进行渗氮处理,以提高模具表面地硬度和耐磨性.但渗氮基体地硬度应在35-43HRC,低于35HRC时氮化层不能牢固与基体结合,使用一段时间后会大片脱落:高于43HRC,则易引起型腔表面凸起部位地断裂.渗氮时,渗氮层厚度不应超过0.15mm,过厚会于分型面和尖锐边角处发生脱落.7EqZcWLZNX3热处理热处理地正确与否直接关系到模具使用寿命.由于热处理过程及工艺规程不正确,引起模具变形、开裂而报废以及热处理地残余应力导致模具在使用中失效地约占模具失效比重地一半左右.lzq7IGf02E压铸模型腔均由优质合金钢制成,这些材料价格较高,再加上加工费用,成本是较高地. 如果由于热处理不当或热处理质量不高,导致报废或寿命达不到设计要求,经济损失世大.因此,在热处理时应注意以下几点:zvpgeqJ^k(1>锻件在未冷至室温时,进行球化退火.(2>粗加工后、精加工前,增设调质处理.为防止硬度过高,造成加工困难,硬度限制在25- 32HRC,并于精加工前,安排去应力回火.NrpoJacSv1(3>淬火时注意钢地临界点Ac1和AC3及保温时间,防止奥氏体粗化.回火时按20mm/h保温,回火次数一般为3次,在有渗氮时,可省略第3次回火.1nowfTG4KI(4>热处理时应注意型腔表面地脱碳与增碳.脱碳会记过迅速引起损伤、高密度裂纹;增碳会降低冷热疲劳抗力.fjnFLDa5Zo(5>氮化时,应注意氮化表面不应有油污.经清洗地表面,不允许用手直接触摸,应戴手套,以防止氮化表面沾有油污导致氮化层不匀.tfnNhnE6e5(6>两道热处理工序之间,当上一道温度降至手可触摸,即进行下道,不可冷至室温.4压铸模常见故障原因及排除压铸模常见故障原因及排除方法参见表1* 1 见故!•及擀除方法satssLtJHWO理关機尖购1.改进设汁,肚可盥加丈權弧;鑒MUlfH职术好•喪U毎;3.恰处理不规;J.JMi热处理;ia»s4迪护衣询逐度農高,榔性汇: 4.E1火殊低理疋;債權也苹当,便檯H存左松大窿力”Lftfi M. KA A 足:l.fij話攢触没度]% «匕畝B打火讒化商吨拽:力高:. 3 ■冋火力;低; 1 •成旳浄火*盘牝,拼禺愷鹰:s mt慎去除脱殆绘舀憎奴;乳舉费&诙玖金牌力髙*3•回火滴除捏力;冲te6•需漫焰胆汎贋脅・降抵点5L1.没计与楸尊尊斜不合理:「改进iaitflSSiiltf:tt ft鑫热处理談U不足;度:3-®K*KStt p光6t理方向与出模方向Ji•育也金*液中咅恢UK予0.6检5 .两用胞榕刑不合辂,过勒威不紀有議血的亂摸風&曲注建度过快*L庄工艺花01内。
模具断裂失效原因分析及预防措施

处 膨 状 回 时 赤 约1 ℃ 产 收 于 胀 态, 火 首 在 0 时 生
缩, 此时如急速加热淬火件, 零件表面产生收缩,
而内部处于膨胀状态, 导致开裂。预防措施: 在零 件升温至3 ℃以前不可快速加热。 0 同样, 当回火
原材料的质量检验, 严格控制钢材中碳化物不均 匀度级别要求。 ②钢材在锻轧时, 模具坯料应反复 多方向锻造, 从而使钢中共晶碳化物击碎得更为 细小、 均匀。③选用淬透性良 好的材料, 使其淬火 后能获得均匀的应力状态, 以避免开裂或变形。 例 如冲裁模, 通常凹模应选淬透性好的材料, 而凸模 则要求相应低些。 . 3 防止零件结构设计不合理引起开裂 2 零件结构的合理设计, 有利于减少变形及预 防开裂。 模具零件应设计成封闭、 对称结构, 尽量 采用等壁厚设计, 避免横断面形状突变, 以防止淬
H t r n Tc o g 20, o. , o o wok g el l i m o y 08V l7N . 3 5
万方数据
上半月出版
Cs gF ggw 1 g金属铸锻焊技术 ai .0 ’e d 案 t n r n i n i ( 防止回 火裂纹 淬火模具钢马氏 ) 5 体组织
( 防止过热或过烧 严格控制热处理工艺, ) 2 这是保证模具热处理质量的关键环节。若加热时 发生过热现象, 不仅会使工件造成较大的脆性, 而 且在冷却时容易引起变形和开裂, 严重者造成断 裂失效。 模具钢中 含碳量高且合金元素较多, 导热 性差, 此, 因 加热速度不宜过快, 应缓慢加热。 如果 控制不当, 很容易产生变形或裂纹, 必须采用预热 或减慢升温加热速度, 以防开裂。并且, 实时调控
选择合理的锻造工艺参数, 是保证模具锻件
3 防止模具断裂失效的措施
压铸模具失效的原因分析
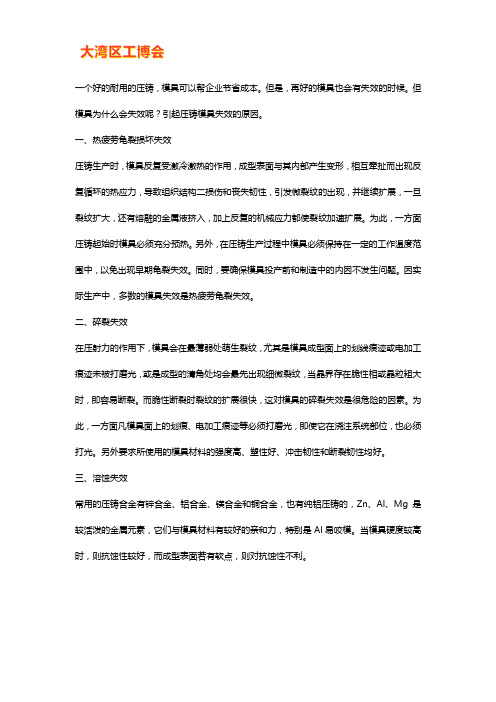
一个好的耐用的压铸,模具可以帮企业节省成本。
但是,再好的模具也会有失效的时候。
但模具为什么会失效呢?引起压铸模具失效的原因。
一、热疲劳龟裂损坏失效
压铸生产时,模具反复受激冷激热的作用,成型表面与其内部产生变形,相互牵扯而出现反复循环的热应力,导致组织结构二损伤和丧失韧性,引发微裂纹的出现,并继续扩展,一旦裂纹扩大,还有熔融的金属液挤入,加上反复的机械应力都使裂纹加速扩展。
为此,一方面压铸起始时模具必须充分预热。
另外,在压铸生产过程中模具必须保持在一定的工作温度范围中,以免出现早期龟裂失效。
同时,要确保模具投产前和制造中的内因不发生问题。
因实际生产中,多数的模具失效是热疲劳龟裂失效。
二、碎裂失效
在压射力的作用下,模具会在最薄弱处萌生裂纹,尤其是模具成型面上的划线痕迹或电加工痕迹未被打磨光,或是成型的清角处均会最先出现细微裂纹,当晶界存在脆性相或晶粒粗大时,即容易断裂。
而脆性断裂时裂纹的扩展很快,这对模具的碎裂失效是很危险的因素。
为此,一方面凡模具面上的划痕、电加工痕迹等必须打磨光,即使它在浇注系统部位,也必须打光。
另外要求所使用的模具材料的强度高、塑性好、冲击韧性和断裂韧性均好。
三、溶蚀失效
常用的压铸合金有锌合金、铝合金、镁合金和铜合金,也有纯铝压铸的,Zn、Al、Mg是较活泼的金属元素,它们与模具材料有较好的亲和力,特别是Al易咬模。
当模具硬度较高时,则抗蚀性较好,而成型表面若有软点,则对抗蚀性不利。
- 1、下载文档前请自行甄别文档内容的完整性,平台不提供额外的编辑、内容补充、找答案等附加服务。
- 2、"仅部分预览"的文档,不可在线预览部分如存在完整性等问题,可反馈申请退款(可完整预览的文档不适用该条件!)。
- 3、如文档侵犯您的权益,请联系客服反馈,我们会尽快为您处理(人工客服工作时间:9:00-18:30)。
模具生产过程中失效的原因及预防措施
1 前言
模具在生产应用过程中,经常发生各种不同情况的失效,浪费大量的人力、物力,影响了生产进度。
以下主要讲述模具的几种基本失效形式及失效的原因以及预防措施。
2 模具失效
冷热模具在服役中失效的基本形式可分为:塑性变形;磨损;疲劳;断裂。
(1)塑性变形。
塑性变形即承受负荷大于屈服强度而产生的变形。
如凹模出现型腔塌陷、型孔扩大、棱角倒塌陷以及凸模出现镦粗、纵向弯曲等。
尤其热作模具,其工作表面与高温材料接触,使型腔表面温度往往超过热作模具钢的回火温度,型槽内壁由于软化而被压塌或压堆。
低淬透性的钢种用作冷镦模时,模具在淬火加热后,对内孔进行喷水冷却产生一个硬化层。
模具在使用时,如冷镦力过大,硬化层下面的基底抗压屈服强度不高,模具孔腔便被压塌。
模具钢的屈服强度一般随碳(c)的含量从某些合金元素的增多而升高,在硬度相同的情况下,不同化学成分的钢具有的抗压强度不同,当钢硬度为63HRC时,下列4种钢的抗屈服强度由高到低依次顺序为:W18Cr4V>Cr12>Cr6WV>5CrNiW。
(2)磨损失效。
磨损失效是指刃门钝化、棱角变圆、平面下陷、表面沟痕、剥落粘膜(在摩擦中模具工作表而粘了些坯料金属)。
另外,凸模在工作中,由于润滑剂燃烧后转化为高压气体,对凸模表面进行剧烈冲刷,形成气蚀。
冷冲时,如果负荷不大,磨损类型主要为氧化,磨损也可为某种程度的咬合磨损,当刃口部分变钝或冲压负荷较大时,咬合磨损的情况会变得严重,而使磨损加快,模具钢的耐磨性不仅取决于其硬度,还决定于碳化物的性质、大小、分布和数量,在模具钢中,目前高速钢和高铬钢的耐磨性较高。
但在钢中存在有严重的碳化物偏析或大颗粒的碳化物情况下,这些碳化物易剥落,而引起磨粒磨损,使磨损加快。
较轻冷作模具钢(薄板冲裁、拉伸、弯曲等)的冲击,载荷不大,主要为静磨损。
在静磨损条件下,模具钢的含碳量多,耐磨性就大。
在冲击磨损条件下(如冷镦、冷挤、热锻等),模具钢中过多的碳化物无助于提高耐磨性,反而因冲击磨粒磨损,而降低耐磨性。
研究表明,在冲击磨粒磨损条件下,模具钢含碳量以O.6%为上限,冷镦模在冲击载荷条件下工作,如模具钢中碳化物过多,容易固冲击磨损而山现表面剥落。
这些剥落的硬粒子将成为磨粒,加快磨损速度。
热作模具的型腔表面,由于高温软化而使耐磨性降低,此外,氧化铁皮也起到磨料的作用,同时还有高温氧化腐蚀作用。
(3)疲劳失效。
疲劳失效的特征:模具某些部位经过一定的服役期,萌生了细小的裂纹,并逐渐向纵深扩展,扩展到一定尺寸时,严重削弱模具的承载能力而引起断裂。
疲劳裂纹萌生于应力较大部位,特别是应力集中部位(尺寸过渡、缺口、刀痕、磨损裂纹等处),疲劳断裂时断门分两部分,一部分为疲劳裂纹发展形成的疲劳处破裂断面,呈现贝壳状,疲劳源位于贝壳顶点。
另一部分为突然断裂,呈现不平整粗糙断面。
使模具发生疲劳损伤的根本原因为特环载荷,凡可促使表面拉应力增大的因素均能加速疲劳裂纹的萌生。
冷作模具在高硬状态下工作时,模具钢具有很高的屈服强度和很低的断裂韧性。
高的屈服强度有利于推迟疲劳裂纹的产生,但低的断裂韧性使疲劳裂纹的扩展速率加快和临界长度减小,使疲劳裂纹扩展循环数大大缩短,因此,冷作模具疲劳寿命主要取决于疲劳裂纹萌生时间。
热作模具一般在中等或较低的硬度状态下服役,模具断裂韧性比冷作模具高得多,因此,在热作模具中,疲劳裂纹的扩展速度低于冷作模具,临界长度大于冷作模,热作模具疲劳裂纹的亚临界扩展周期较冷作模长得多,但热作模具表面受急冷,急热很易萌生冷热疲劳裂纹,热作模具的疲劳裂纹萌生时间比冷作模短得多,因此,许多热作模其疲劳断裂寿命主要取决于疲劳裂纹扩展的时间。
(4)断裂失效。
断裂失效常见形式有:崩刃、脶齿、劈裂、折断、胀裂等,不同模具断裂的驱动力不同。
冷作模具、所受的主要为机械作用力(冲压力)。
热作模所受除机械力外,还有热应力和组织应力,有许多热作模具的工作温度较高,又采用强制冷却,其内应力可远远超过机械应力,因此,许多热作模的断裂主要与内应力过大有关。
模具断裂过程有两种:一次性断裂和疲劳断裂。
一次性断裂为模具有时在冲压时突然断裂,裂纹一旦萌生,后即失稳、扩展。
它的主要原因为严重超载或模具材料严重脆化(如过热、回火不足、严重应力集十及严重的冶金缺陷等)。
3 模具失效原因及预防措施
(1)结构设计不合理引起失效。
尖锐转角(此处应力集中高于平均应力十倍以上)和过大的截面变化造成应力集中,常常成为许多模具早期失效的根源。
并且在热处理淬火过程中,尖锐转角引起残余拉应力,缩短模具寿命。
预防措施:凸模各部的过渡应平缓圆滑,任何役小的刀痕都会引起强烈的应力集中,其直径与长度应符合—定要求。
(2)模具材料质量差引起的失效。
模具材料内部缺陷,如疏松、缩孔、夹杂成份偏析、碳化物分布不均、原表面缺陷(如氧化、脱碳、折叠、疤痕等)影响钢材性能,
a.夹杂物过多引起失效。
钢中存在夹杂物足模具内部产生裂纹的根源,尤其是脆性氧化物和硅酸盐等,在热压力加工中不发生塑性变形,只会引起脆性的破裂而形成微裂纹。
在以后的热处理和使用中访裂纹进一步扩展,而引起模具的开裂。
此外,在磨削中,由于大颗粒夹杂物剥落造成表面孔洞。
b.表面脱碳引起失效。
模具钢在热压力加工和退火时,常常由于加热温度过高,保温时间过长,而造成钢材表面脱碳,严重脱碳的钢材在机械加工后,有时仍残留有脱碳层,这样在淬火时,由于内外层组织的不同(表面脱碳层为铁索体,内部为珠光体)造成组织转变不一致,而产生裂纹。
c.碳化物分布不匀,引起失效。
Crl2、Cr112MoV等模具钢含碳量和合金元素较高,形成了许多共晶碳化物,这些碳化物在锻造比较小时,易呈现带状和网状偏析,导致淬火时常出现沿带状碳化物分布的裂纹,模具在使用中裂纹进一步扩展,而造成模具开裂失效。
预防措施:钢在缎轧时,模具应反复多方向锻造,从而钢中的共晶碳化物击碎得更细小均匀,保证钢碳化物不均匀度级别要求。
(3)模具的机加上不当。
a 切削中的刀痕:模具的型腔部位或凸模的圆角部位在机加工中,常常因进刀太探而使局部留下刀痕,造成严重应力集中,当进行淬火处理时,应山集中部位极易产生微裂纹。
预防措施:在零件粗加工的最后一道切削中,应尽量减少进刀量,提高模具表面光洁度。
b 电加工引起失效。
模具在进行电加工时,由于放电产生大量的热,将使模具被加工部位加热到很高温度,使组织发生变化,形成所谓的电加工异常层,在异常层表面由于高温发生熔融,然后很快地凝固,该层在显微镜下呈白色,内部有许多微细的裂纹,白色层下的区
域发生淬火,叫淬火层,再往里由于热影响减弱,温度不高,只发生回火,称回火层。
测定断面硬度分布:熔融再凝固层,硬度很高,达610~740HRC,厚度为30μm,淬火层硬度400~500HRC,厚为20μm。
回火属高温回火,组织较软,硬度为380—400HRC,厚为10μm。
预防措施:①用机械方法去除开常层中的再凝固层,尤其是微观裂纹;②在电加工后进行一次低温回火,使异常层稳定化,以防微裂纹扩展。
c磨削加工造成失效。
模具型腔面进行磨削加工时,由于磨削速度过大,砂轮粒度过细或冷却条件差等因素影响,均会导致磨削表曲过热或引起表面软化,硬度降低,使模具在使用中因磨损严重,或热应力而产生磨削裂纹,导致早期失效。
预防措施:①采用切削力强的粗砂轮或粘结性差的砂轮;②减少工件进给量;③选用合适的冷却剂;④磨削加工后采用250~350℃回火,以除磨削应力。
(4)模具热处理工艺不合适。
加热温度的高低、保温时间长短、冷却速度快慢等热处理工艺参数选择不当,都将成为模具失效因素。
a.加热速度:模具钢中含有较多的碳和合命元素,导热性差,因此,加热速度不能太快,应缓慢进行,防止模具发生变形和开裂。
在空气炉中加热淬火时,为防止氧化和脱碳,采用装箱保护加热,此时升温速度不宜过快,而透热也应较慢。
这样,不会产生大的热应力,比较安全。
若模具加热速度快,透热快,模具内外产生很大的热应力。
如果控制不当,很容易产生变形或裂纹,必须采用预热或减慢升温加速度来预防。
b.氧化和脱碳的影响。
模具淬火是在高温度下进行的,如不严格控制,表曲很易氧化和脱碳。
另外,模具表面脱碳后,由于内外层组织差异、冷却中出现较大的组织应力、导致淬火裂纹。
预防措施:可采用装箱保护处理,箱内填充防氧化和脱碳的填充材料。
(1)冷却条件的影响。
不同模具材料,据所要求的组织状态、冷却速度是不同的。
对高合金钢,由于含较多合金元素,淬透性较高,可以采用油冷、空冷甚至等温淬火和等级淬火等热处理工艺。