1轮胎模具结构及制造流程介绍
汽车轮胎生产工艺流程
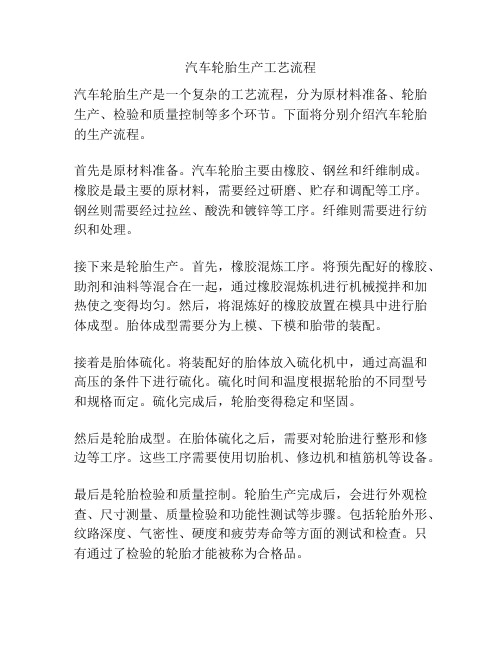
汽车轮胎生产工艺流程
汽车轮胎生产是一个复杂的工艺流程,分为原材料准备、轮胎生产、检验和质量控制等多个环节。
下面将分别介绍汽车轮胎的生产流程。
首先是原材料准备。
汽车轮胎主要由橡胶、钢丝和纤维制成。
橡胶是最主要的原材料,需要经过研磨、贮存和调配等工序。
钢丝则需要经过拉丝、酸洗和镀锌等工序。
纤维则需要进行纺织和处理。
接下来是轮胎生产。
首先,橡胶混炼工序。
将预先配好的橡胶、助剂和油料等混合在一起,通过橡胶混炼机进行机械搅拌和加热使之变得均匀。
然后,将混炼好的橡胶放置在模具中进行胎体成型。
胎体成型需要分为上模、下模和胎带的装配。
接着是胎体硫化。
将装配好的胎体放入硫化机中,通过高温和高压的条件下进行硫化。
硫化时间和温度根据轮胎的不同型号和规格而定。
硫化完成后,轮胎变得稳定和坚固。
然后是轮胎成型。
在胎体硫化之后,需要对轮胎进行整形和修边等工序。
这些工序需要使用切胎机、修边机和植筋机等设备。
最后是轮胎检验和质量控制。
轮胎生产完成后,会进行外观检查、尺寸测量、质量检验和功能性测试等步骤。
包括轮胎外形、纹路深度、气密性、硬度和疲劳寿命等方面的测试和检查。
只有通过了检验的轮胎才能被称为合格品。
总结起来,汽车轮胎生产是一个包含原材料准备、轮胎生产、检验和质量控制等环节的复杂工艺流程。
每一个环节都有严格的工艺要求和操作规范。
只有严格按照流程进行操作,才能生产出合格的汽车轮胎。
轮毂模具制作工艺

轮毂模具制作工艺轮毂模具制作工艺是指将轮毂产品的设计图纸转化为实际零件的过程,它是制造高质量轮毂的关键环节。
以下为轮毂模具制作工艺的主要步骤及流程。
1. 设计轮毂模具:首先,需要根据轮毂产品的设计要求和图纸,设计轮毂模具的结构和形状。
这一步是制作工艺的基础,要根据轮毂的尺寸、形状、孔距和孔径等要求来确定模具的结构参数。
2. 材料准备:根据轮毂模具的设计要求,在选择合适的材料方面,需要考虑模具的耐磨性、强度和硬度等。
常见的材料有优质钢材、合金钢等,根据实际情况进行选择。
3. CNC加工模具:接下来,将轮毂模具的设计图纸输入到计算机数控(CNC)加工机器中,进行模具的加工。
这一步主要是利用机器自动控制削剪、刮削、铣削等工艺,将模具的外形和内部空腔进行加工成型。
4. 精细加工模具:在CNC加工完成后,有时还需要进行一些精细加工工艺,如磨削、抛光等。
这些工艺主要是为了提高模具的表面光洁度和尺寸精度,确保模具加工的质量。
5. 模具组装:模具加工完成后,需要根据设计要求进行模具的组装。
这一步主要是将模具的各个零部件进行拼装,确保模具的结构完整、刚性良好,并能满足后续的使用要求。
6. 模具热处理:某些情况下,为提高模具的硬度和耐磨性,还需要对模具进行热处理。
热处理一般包括淬火、回火、正火等工艺,以增强模具的耐用性和使用寿命。
7. 模具检验:模具制作完成后,需要对模具进行严格的检验。
主要包括尺寸检验、外观检查和功能测试等,以确保模具的质量和性能符合设计要求。
8. 模具调试:模具通过检验后,需要进行调试。
在模具调试过程中,需要根据实际的生产要求进行参数的调整,做好轮毂模具的准备工作。
9. 模具正式投产:经过调试和确认后,模具可以投入正式的生产使用。
在生产过程中,需要进行模具的定期维护和保养,以保证模具的使用寿命和工作效率。
10. 模具改进和优化:一旦模具投入使用,就需要不断对模具进行改进和优化。
根据轮毂产品的实际情况和用户的反馈,可以改进模具的结构和工艺,以提高轮毂产品的质量和效率。
轮胎模具制造工艺流程
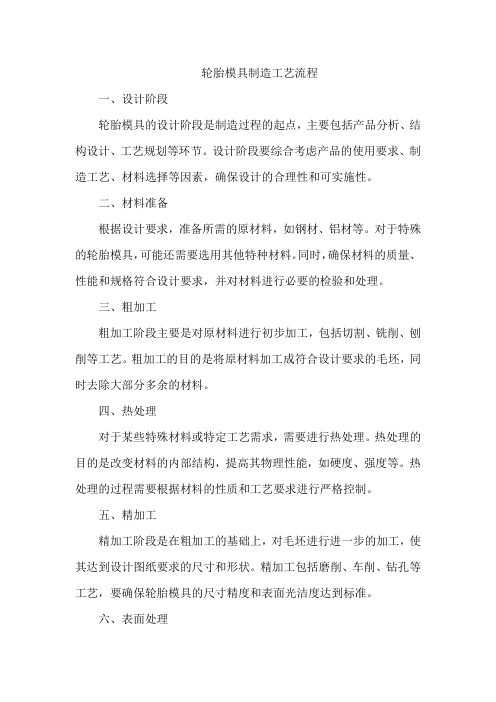
轮胎模具制造工艺流程一、设计阶段轮胎模具的设计阶段是制造过程的起点,主要包括产品分析、结构设计、工艺规划等环节。
设计阶段要综合考虑产品的使用要求、制造工艺、材料选择等因素,确保设计的合理性和可实施性。
二、材料准备根据设计要求,准备所需的原材料,如钢材、铝材等。
对于特殊的轮胎模具,可能还需要选用其他特种材料。
同时,确保材料的质量、性能和规格符合设计要求,并对材料进行必要的检验和处理。
三、粗加工粗加工阶段主要是对原材料进行初步加工,包括切割、铣削、刨削等工艺。
粗加工的目的是将原材料加工成符合设计要求的毛坯,同时去除大部分多余的材料。
四、热处理对于某些特殊材料或特定工艺需求,需要进行热处理。
热处理的目的是改变材料的内部结构,提高其物理性能,如硬度、强度等。
热处理的过程需要根据材料的性质和工艺要求进行严格控制。
五、精加工精加工阶段是在粗加工的基础上,对毛坯进行进一步的加工,使其达到设计图纸要求的尺寸和形状。
精加工包括磨削、车削、钻孔等工艺,要确保轮胎模具的尺寸精度和表面光洁度达到标准。
六、表面处理表面处理是对加工完成的轮胎模具进行表面处理,以提高其耐腐蚀性、美观性和使用寿命。
表面处理的方法包括喷涂、电镀、氧化等,根据不同的需求选择合适的处理方法。
七、检验阶段检验阶段是对制造完成的轮胎模具进行质量检查,确保其符合设计要求和性能标准。
检验内容包括尺寸精度、表面质量、热处理效果等,检验合格后方可进入下一环节。
八、包装运输最后,对合格的轮胎模具进行包装,以保护其在运输过程中不受损伤。
包装应选用适当的材料和方式,确保轮胎模具在运输过程中保持完好。
同时,要合理规划运输方式,确保产品安全快捷地送达目的地。
全钢轮胎制造工艺流程

全钢轮胎制造工艺流程1.原材料的准备全钢轮胎的主要原材料包括橡胶、纤维材料(如尼龙帘布、钢丝帘布)、化学添加剂和金属配件(如连边和胎圈等)。
在制造过程中,这些原材料需要经过严格的质量检验和筛选,确保其质量符合标准要求。
2.胎面制备胎面是轮胎与地面接触的部分,对轮胎的性能和使用寿命有着重要的影响。
胎面的制备主要包括以下几个步骤:(1)橡胶配方设计:根据轮胎的使用要求和性能指标,确定橡胶的配方,并添加适量的填充剂、增塑剂和硫化剂等。
(2)橡胶热炼:将橡胶混合物在混炼机中进行机械剪切和热能传递,使橡胶分子发生断裂和重组,形成具有一定强度和弹性的橡胶胶料。
(3)成型:将热炼好的橡胶胶料通过滚轮制、挤出法等成型工艺,制备成具有特定花纹和尺寸的胎面。
3.胎体制备胎体是轮胎的骨架,起到支撑、保护和增加刚度等作用。
胎体的制备主要包括以下几个步骤:(1)尼龙帘布预拉伸:将尼龙帘布经过预拉伸处理,使其具有一定的拉伸强度和弹性,提高胎体的整体强度。
(2)帘布预组装:根据轮胎的结构和尺寸要求,将预拉伸好的尼龙帘布和其他纤维材料进行预组装,形成胎体的结构。
同时,胎体中还要安装钢丝帘布和其他金属配件。
4.成型成型是将胎面和胎体组装在一起,形成轮胎整体的过程。
成型工艺主要包括以下几个步骤:(1)帘布胶束嵌入:将预组装的胎体放入成型模具中,调整成型模具的尺寸,使胶束和帘布完全贴合。
(2)封胎:将成型好的轮胎进行封胎处理,使用压力和热力将胎面和胎体之间的空气排出。
同时,确保胎体和帘布之间的胶层能够牢固粘合。
5.硫化硫化是全钢轮胎制造的重要步骤,通过硫化处理可以使橡胶胶料发生化学反应,形成强硬的橡胶网络结构,提高轮胎的强度和弹性。
硫化工艺主要包括以下几个步骤:(1)成型胎的硫化:将成型好的轮胎放入硫化机中,加热至一定温度并施加一定的压力。
在这个过程中,硫化剂和其他化学添加剂会发生反应,使橡胶分子交联,形成硫化胶层。
(2)硫化胎的硫化:将硫化好的轮胎再次放入硫化机中,进行硫化胎的硫化处理。
轮胎生产工艺流程
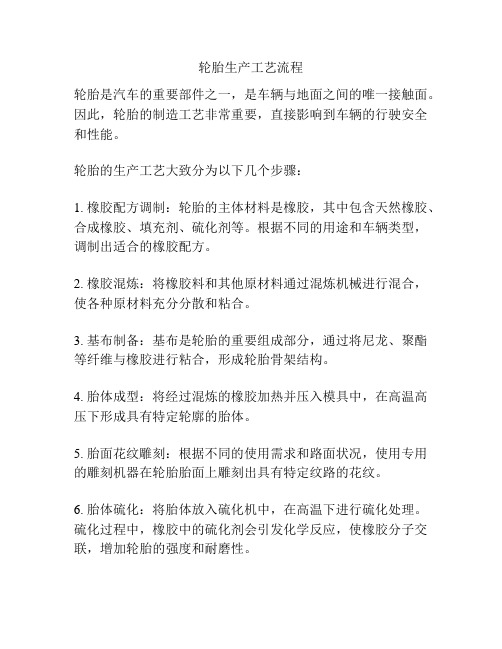
轮胎生产工艺流程轮胎是汽车的重要部件之一,是车辆与地面之间的唯一接触面。
因此,轮胎的制造工艺非常重要,直接影响到车辆的行驶安全和性能。
轮胎的生产工艺大致分为以下几个步骤:1. 橡胶配方调制:轮胎的主体材料是橡胶,其中包含天然橡胶、合成橡胶、填充剂、硫化剂等。
根据不同的用途和车辆类型,调制出适合的橡胶配方。
2. 橡胶混炼:将橡胶料和其他原材料通过混炼机械进行混合,使各种原材料充分分散和粘合。
3. 基布制备:基布是轮胎的重要组成部分,通过将尼龙、聚酯等纤维与橡胶进行粘合,形成轮胎骨架结构。
4. 胎体成型:将经过混炼的橡胶加热并压入模具中,在高温高压下形成具有特定轮廓的胎体。
5. 胎面花纹雕刻:根据不同的使用需求和路面状况,使用专用的雕刻机器在轮胎胎面上雕刻出具有特定纹路的花纹。
6. 胎体硫化:将胎体放入硫化机中,在高温下进行硫化处理。
硫化过程中,橡胶中的硫化剂会引发化学反应,使橡胶分子交联,增加轮胎的强度和耐磨性。
7. 胎体检验:对硫化后的轮胎进行外观检查和功能性测试,确保轮胎符合质量要求。
8. 胎侧编码:在轮胎的侧面编码,编码中包含轮胎的生产日期、尺寸、质量等信息,以供用户查阅。
9. 质量检验:对成品轮胎进行整体检查,包括外观、尺寸、平衡等方面的测试。
10. 包装和运输:将合格的轮胎进行包装,并进行出厂前的最后一次检查,然后装运到销售商或汽车制造商处,进入市场。
轮胎的生产工艺需要严格控制各个环节,确保每一道工序的质量和效率。
现代轮胎生产线往往采用自动化控制系统,利用先进的机器和设备,提高生产效率和产品质量。
总的来说,轮胎的生产工艺是一个复杂而精细的过程。
只有通过严格的生产流程控制和质量监控,才能生产出高质量的轮胎,保障车辆的行驶安全和性能。
轮胎模具侧板加工流程

轮胎模具侧板加工流程Title: Tire Mould Side Plate Machining ProcessTitle: 轮胎模具侧板加工流程English:The tire mould side plate machining process involves several critical steps to ensure the precision and durability of the final product.Initially, the raw material, typically high-quality steel, is selected for its strength and resistance to wear.The side plate"s design must align with the tire"s specifications to provide an accurate fit.中文:轮胎模具侧板的加工流程包括几个关键步骤,以确保最终产品的精确度和耐用性。
首先,选择优质的钢材作为原材料,因其具有足够的强度和耐磨性。
侧板的设计必须与轮胎的规格相符,以提供准确的配合。
English:ext, the side plate undergoes blanking to create the required shape and size.This step may involve laser cutting or mechanical stamping, depending on the complexity of the design.After blanking, the side plate is subjected to milling and turning operations to achieve the precise dimensions and smooth finish required for the tire mould.中文:接下来,侧板将进行空白处理,以形成所需的形状和尺寸。
轮胎是怎么加工的原理
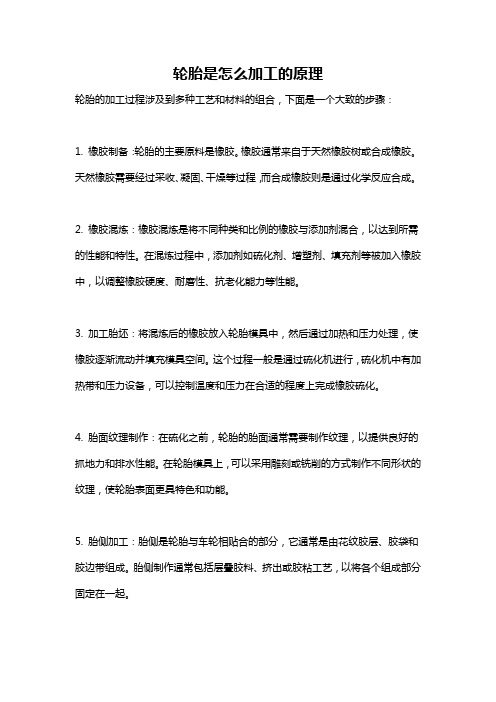
轮胎是怎么加工的原理轮胎的加工过程涉及到多种工艺和材料的组合,下面是一个大致的步骤:1. 橡胶制备:轮胎的主要原料是橡胶。
橡胶通常来自于天然橡胶树或合成橡胶。
天然橡胶需要经过采收、凝固、干燥等过程,而合成橡胶则是通过化学反应合成。
2. 橡胶混炼:橡胶混炼是将不同种类和比例的橡胶与添加剂混合,以达到所需的性能和特性。
在混炼过程中,添加剂如硫化剂、增塑剂、填充剂等被加入橡胶中,以调整橡胶硬度、耐磨性、抗老化能力等性能。
3. 加工胎坯:将混炼后的橡胶放入轮胎模具中,然后通过加热和压力处理,使橡胶逐渐流动并填充模具空间。
这个过程一般是通过硫化机进行,硫化机中有加热带和压力设备,可以控制温度和压力在合适的程度上完成橡胶硫化。
4. 胎面纹理制作:在硫化之前,轮胎的胎面通常需要制作纹理,以提供良好的抓地力和排水性能。
在轮胎模具上,可以采用雕刻或铣削的方式制作不同形状的纹理,使轮胎表面更具特色和功能。
5. 胎侧加工:胎侧是轮胎与车轮相贴合的部分,它通常是由花纹胶层、胶袋和胶边带组成。
胎侧制作通常包括层叠胶料、挤出或胶粘工艺,以将各个组成部分固定在一起。
6. 胎壁构建:胎壁是连接轮胎胎面和胎侧的部分。
它通常有多个层次和不同的构造,以提供更好的耐磨性、支撑性和稳定性。
胎壁的构建过程中,需要将各种橡胶层、钢丝帘子层、尼龙帘子层和帘子胶层等材料按照一定的顺序和结构贴合在一起。
7. 花纹图案压花:硫化前,轮胎的胎面通常需要通过压花技术制作更复杂的花纹特征。
这通常是通过将轮胎模具上的花纹设计压在胎面上,以使花纹更加鲜明和具有良好的抓地力和排水性能。
8. 硫化:硫化是轮胎加工中最重要的一个步骤,也是决定轮胎最终性能的关键环节。
硫化是指将模具中的轮胎胎坯加热到一定的温度,并在高压下与硫化剂反应,使橡胶永久性地交联,以提高轮胎的强度、耐磨性和弹性。
9. 后处理:硫化后的轮胎需要经过多道工序进行后处理。
这包括拆模、胶料修整、质检、修补、刮除多余橡胶等环节。
轮胎生产工艺流程
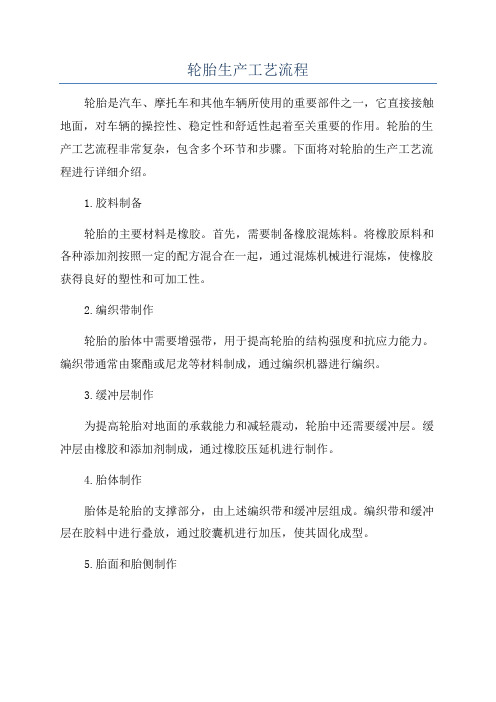
轮胎生产工艺流程轮胎是汽车、摩托车和其他车辆所使用的重要部件之一,它直接接触地面,对车辆的操控性、稳定性和舒适性起着至关重要的作用。
轮胎的生产工艺流程非常复杂,包含多个环节和步骤。
下面将对轮胎的生产工艺流程进行详细介绍。
1.胶料制备轮胎的主要材料是橡胶。
首先,需要制备橡胶混炼料。
将橡胶原料和各种添加剂按照一定的配方混合在一起,通过混炼机械进行混炼,使橡胶获得良好的塑性和可加工性。
2.编织带制作轮胎的胎体中需要增强带,用于提高轮胎的结构强度和抗应力能力。
编织带通常由聚酯或尼龙等材料制成,通过编织机器进行编织。
3.缓冲层制作为提高轮胎对地面的承载能力和减轻震动,轮胎中还需要缓冲层。
缓冲层由橡胶和添加剂制成,通过橡胶压延机进行制作。
4.胎体制作胎体是轮胎的支撑部分,由上述编织带和缓冲层组成。
编织带和缓冲层在胶料中进行叠放,通过胶囊机进行加压,使其固化成型。
5.胎面和胎侧制作胎面和胎侧是轮胎的外层,负责与地面接触和提供额外的保护。
它们由多层橡胶和纤维材料组成,通过胎面部分和胎侧部分的制作工艺进行制作。
6.胎圈组装胎圈是连接轮胎和车轮的部分,它由金属材料制成。
将胎圈与胎体组装在一起,通过机械设备将胎圈固定在胎体上。
7.胎纹制作胎纹是轮胎表面的花纹,其作用是提高轮胎的附着力和排水性能。
胎纹由专门的胎纹机制作,通过胎纹模具将花纹压制到轮胎表面。
8.钢帘线加工轮胎中的钢帘线主要用于加强轮胎的抗张能力。
钢帘线是经过特殊处理的钢丝,通过机械设备进行加工和成形。
9.胎垫制作胎垫是轮胎内部的一层橡胶垫,用于防止气体泄漏。
胎垫由橡胶原料制成,通过模具压制和硫化固化。
10.胶带涂布和硫化在胎体和胎面胎侧的制作过程中,需要将各种胶带涂布在轮胎的不同部位。
涂布后的轮胎经过硫化设备进行硫化,使胶料固化并获得最终的物理和化学性能。
11.质检和包装经过上述工艺流程后,轮胎进行质量检测,如外观检查、尺寸检查、力学性能测试等。
合格的轮胎将进行包装和打包,准备发货到客户。
轮胎模具加工工艺
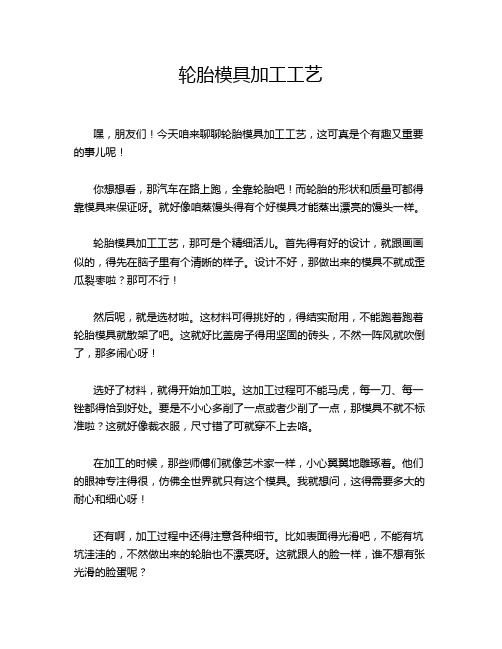
轮胎模具加工工艺嘿,朋友们!今天咱来聊聊轮胎模具加工工艺,这可真是个有趣又重要的事儿呢!你想想看,那汽车在路上跑,全靠轮胎吧!而轮胎的形状和质量可都得靠模具来保证呀。
就好像咱蒸馒头得有个好模具才能蒸出漂亮的馒头一样。
轮胎模具加工工艺,那可是个精细活儿。
首先得有好的设计,就跟画画似的,得先在脑子里有个清晰的样子。
设计不好,那做出来的模具不就成歪瓜裂枣啦?那可不行!然后呢,就是选材啦。
这材料可得挑好的,得结实耐用,不能跑着跑着轮胎模具就散架了吧。
这就好比盖房子得用坚固的砖头,不然一阵风就吹倒了,那多闹心呀!选好了材料,就得开始加工啦。
这加工过程可不能马虎,每一刀、每一锉都得恰到好处。
要是不小心多削了一点或者少削了一点,那模具不就不标准啦?这就好像裁衣服,尺寸错了可就穿不上去咯。
在加工的时候,那些师傅们就像艺术家一样,小心翼翼地雕琢着。
他们的眼神专注得很,仿佛全世界就只有这个模具。
我就想问,这得需要多大的耐心和细心呀!还有啊,加工过程中还得注意各种细节。
比如表面得光滑吧,不能有坑坑洼洼的,不然做出来的轮胎也不漂亮呀。
这就跟人的脸一样,谁不想有张光滑的脸蛋呢?而且,模具的尺寸得精确到毫米级别的,这要求得多高呀!这就跟射击比赛一样,得瞄得特别准才能打中靶心。
咱再说说模具的纹路,那也是很有讲究的。
纹路得设计合理,能让轮胎有足够的摩擦力,这样汽车才能跑得稳呀。
这就像人的鞋底,纹路不好走在冰面上不就滑倒啦?加工完了还不算完,还得检查检查再检查。
可不能让有问题的模具流出去呀,那不是砸了招牌嘛。
总之,轮胎模具加工工艺可不是那么简单的事儿。
它需要技术、耐心、细心,还有对质量的严格把控。
这可不是随随便便就能做好的,得下大功夫呢!所以说呀,咱在路上开车的时候,可得感谢那些在背后默默付出的模具加工师傅们。
他们就像幕后英雄一样,让我们的出行更加安全、顺畅。
你们说,是不是这个理儿呀?。
轮胎成型工艺

轮胎成型工艺轮胎成型是指将橡胶材料经过一系列工艺加工,最终形成轮胎的过程。
轮胎的成型工艺是一个复杂的过程,涉及到大量的机械设备和工艺操作。
下面将介绍轮胎成型的主要工艺流程。
首先,轮胎的成型工艺通常开始于制作胎圈的环节。
胎圈是固定轮胎上的橡胶材料,使其固定在车辆的车轮上。
制作胎圈的工艺一般是将钢带卷成圆形,并通过焊接或者胶水固定在一起。
接下来,橡胶材料被制作成花纹模具,以便形成轮胎的花纹部分。
这一过程需要用到一些特殊的机械设备,如挤出机和模具。
挤出机将加热的橡胶材料通过模具挤出,形成花纹部分的轮胎。
然后,橡胶材料被放入一个成型机中,通过加热和加压的方式,使其完全填充轮胎的花纹部分。
成型机中的加热和加压过程可确保橡胶材料与花纹模具紧密结合,并使轮胎在使用过程中能够有较好的强度和耐磨性。
最后,成型的轮胎通过冷却装置进行冷却,以固化橡胶材料。
冷却后的轮胎会脱离成型机,并进一步进行质量检验和后续加工,如胶合和热补等。
最终,轮胎会被送往成品库存,准备出售给客户或安装在车辆上。
轮胎成型工艺中需要格外关注的是每个工艺环节的温度、压力和时间等参数的控制。
这些参数的合理控制可以有效提高轮胎的质量和可靠性,使轮胎具有良好的抓地力、耐磨性和耐久性。
总而言之,轮胎成型工艺是一个复杂而严谨的过程,需要严格控制各个工艺环节。
只有通过科学的工艺流程和专业的技术操作,才能制造出高质量的轮胎,满足人们对于安全和舒适行驶的需求。
轮胎成型工艺是指将橡胶材料通过一系列的加工工艺,进行成型和固化,最终形成一个结实耐用的轮胎的过程。
近年来,随着汽车工业的快速发展和技术的不断进步,轮胎的成型工艺也在不断创新与改进。
本文将深入探讨轮胎成型工艺的相关内容。
首先,轮胎的成型工艺在整个轮胎制造过程中起着至关重要的作用。
一个优质的轮胎需要经历多个工艺步骤,包括胎圈制作、橡胶花纹挤出、花纹成型和固化等。
在这些步骤中,每一个环节的控制都对最终轮胎的质量和性能有着直接的影响。
轮胎的生产流程是什么样的(轮胎生产过程详解)
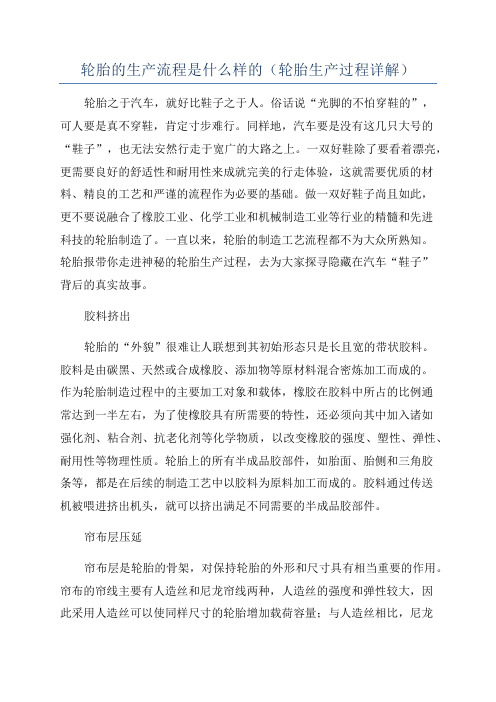
轮胎的生产流程是什么样的(轮胎生产过程详解)轮胎之于汽车,就好比鞋子之于人。
俗话说“光脚的不怕穿鞋的”,可人要是真不穿鞋,肯定寸步难行。
同样地,汽车要是没有这几只大号的“鞋子”,也无法安然行走于宽广的大路之上。
一双好鞋除了要看着漂亮,更需要良好的舒适性和耐用性来成就完美的行走体验,这就需要优质的材料、精良的工艺和严谨的流程作为必要的基础。
做一双好鞋子尚且如此,更不要说融合了橡胶工业、化学工业和机械制造工业等行业的精髓和先进科技的轮胎制造了。
一直以来,轮胎的制造工艺流程都不为大众所熟知。
轮胎报带你走进神秘的轮胎生产过程,去为大家探寻隐藏在汽车“鞋子”背后的真实故事。
胶料挤出轮胎的“外貌”很难让人联想到其初始形态只是长且宽的带状胶料。
胶料是由碳黑、天然或合成橡胶、添加物等原材料混合密炼加工而成的。
作为轮胎制造过程中的主要加工对象和载体,橡胶在胶料中所占的比例通常达到一半左右,为了使橡胶具有所需要的特性,还必须向其中加入诸如强化剂、粘合剂、抗老化剂等化学物质,以改变橡胶的强度、塑性、弹性、耐用性等物理性质。
轮胎上的所有半成品胶部件,如胎面、胎侧和三角胶条等,都是在后续的制造工艺中以胶料为原料加工而成的。
胶料通过传送机被喂进挤出机头,就可以挤出满足不同需要的半成品胶部件。
帘布层压延帘布层是轮胎的骨架,对保持轮胎的外形和尺寸具有相当重要的作用。
帘布的帘线主要有人造丝和尼龙帘线两种,人造丝的强度和弹性较大,因此采用人造丝可以使同样尺寸的轮胎增加载荷容量;与人造丝相比,尼龙帘线在耐用性方面表现更佳。
目前,大部分汽车上都已采用子午线轮胎,其帘布层帘线排列的方向与轮胎的子午断面一致,这样排列使帘线的强度能得到充分利用,帘布层数也可减少40%~50%,提高了轮胎散热性能。
帘布穿过压延机和胶料紧密贴合,就构成了轮胎的帘布层。
轮胎成型生产轮胎需要的所有半成品在成型机上被组装成生胎。
这时的生胎从外观上已经初步具有轮胎的外形和尺寸,只是在内部构造上还需要经过进一步加工处理。
轮胎模具制作流程

轮胎模具制作流程
1、将轮胎模型用脱模剂涂抹均匀后,用吹干。
处理好的轮胎模型四周用钢板围住,钢板也应用脱模剂处理。
2、硅胶与固化剂搅拌均匀.模具硅胶外观是流动的液体,A组份是硅胶,B组份是固化剂。
例:取100克硅胶,加入2克固化剂(注:硅胶与固化剂一定要搅拌均匀,如果没有搅拌均匀,模具会出现一块已经固化,一块没有固化,硅胶会出现干燥固化不均匀的状况就会影响硅胶模具的使用寿命及翻模次数,甚至造成模具报废状况。
3、抽真空排气泡处理:硅胶与固化剂搅拌均匀后,进行抽真空排气泡环节,抽真空的时间不宜太久,正常情况下,不要超过十分钟,抽真空时间太久,硅胶马上固化,产生了交联反映,使硅胶变成一块一块的,无法进行涂刷或灌注,这样就浪费了硅胶,只能把硅胶倒入垃圾桶,重新再取硅胶来做。
3、将配好的胶沿一固定灌注点缓慢浇注,并不时震荡以排除里面的空气。
4、120分钟胶固化完全后,将石膏粉1000g兑水后注入木条框内,注满为止(木条框应用塑胶片分为两部分以利拆模)。
5、20分钟后拆除木条,模具即做完成。
轮胎生产流程生产工艺

轮胎生产流程生产工艺轮胎是车辆的重要组成部分,其质量和性能直接关系到车辆的操控性、安全性和舒适性。
轮胎的生产流程主要包括原材料准备、胶料混炼、制胶、成型和后续工艺处理等几个关键环节。
下面将对轮胎的生产工艺进行详细介绍。
首先是原材料准备。
轮胎的主要原材料包括橡胶、布线、化学添加剂等。
橡胶是轮胎的主要组成部分,常用的有天然橡胶和合成橡胶。
布线主要用于增强轮胎的强度和耐磨性,常用的有尼龙线和钢丝线。
化学添加剂包括硫化剂、填充剂、加工油、防老化剂等,用于改变橡胶的性能。
接下来是胶料混炼。
将橡胶、布线和化学添加剂等原材料按一定配方投入到混炼机中进行混炼。
混炼机通过摩擦和加热将各种原料混合均匀,并使之发生化学反应,形成胶料。
混炼的时间、温度和转速等参数对胶料的性能起到重要影响。
然后是制胶。
将混炼好的胶料传送到制胶机上进行制胶。
制胶机通过预压、挤压和挤出等过程,将胶料压制成所需的带状胶片。
制胶机采用的工艺可分为多层制胶和单层制胶两种。
多层制胶可以产生带有纹理结构的胶片,可提高轮胎的抓地性能。
单层制胶则适用于更加平整的轮胎表面,可提高车辆的舒适性。
接下来是成型。
将制胶好的胶片堆叠成轮胎的花纹层,并装入成型模具中。
成型模具将胶片和模具内的空气排出,并使胶片承受一定的压力和温度。
在成型过程中,胶片经过拉伸、挤压和压缩等多个步骤,最终形成具有花纹和轮胎轮廓形状的成品轮胎。
最后是后续工艺处理。
成型后的轮胎需要进行硫化和修整等工艺处理。
硫化是将轮胎置于硫化炉中进行加热和硫化处理,使胶料中的硫化剂发挥作用,使胶料交联成胶弹性体,并提高轮胎的强度和耐磨性。
修整是将硫化好的轮胎进行修整、切割和打磨等工艺处理,使其表面光滑、尺寸精确,并进行质检和包装。
总的来说,轮胎的生产流程涉及到多个关键的工艺环节,包括原材料准备、胶料混炼、制胶、成型和后续工艺处理等。
每个环节的技术参数和操作方法对轮胎质量和性能具有重要影响。
轮胎制造厂通过严格控制每个环节的工艺参数和质量检测标准,可以生产出高质量的轮胎,满足不同车辆和道路条件的需求。
轮胎工艺流程
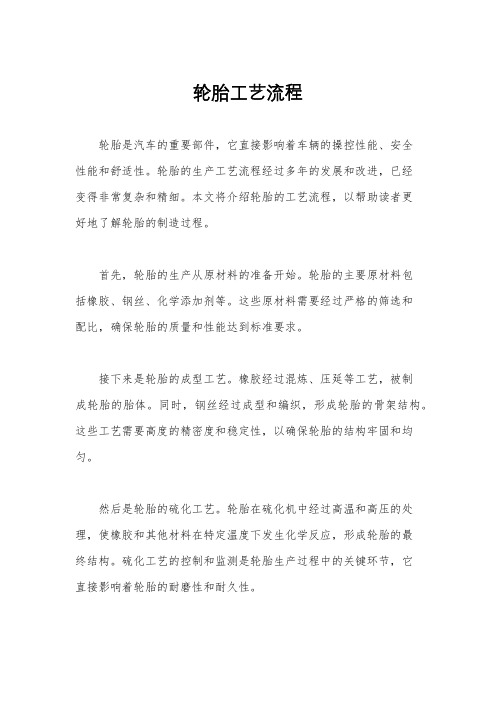
轮胎工艺流程轮胎是汽车的重要部件,它直接影响着车辆的操控性能、安全性能和舒适性。
轮胎的生产工艺流程经过多年的发展和改进,已经变得非常复杂和精细。
本文将介绍轮胎的工艺流程,以帮助读者更好地了解轮胎的制造过程。
首先,轮胎的生产从原材料的准备开始。
轮胎的主要原材料包括橡胶、钢丝、化学添加剂等。
这些原材料需要经过严格的筛选和配比,确保轮胎的质量和性能达到标准要求。
接下来是轮胎的成型工艺。
橡胶经过混炼、压延等工艺,被制成轮胎的胎体。
同时,钢丝经过成型和编织,形成轮胎的骨架结构。
这些工艺需要高度的精密度和稳定性,以确保轮胎的结构牢固和均匀。
然后是轮胎的硫化工艺。
轮胎在硫化机中经过高温和高压的处理,使橡胶和其他材料在特定温度下发生化学反应,形成轮胎的最终结构。
硫化工艺的控制和监测是轮胎生产过程中的关键环节,它直接影响着轮胎的耐磨性和耐久性。
最后是轮胎的检测和包装。
经过硫化工艺的轮胎需要经过严格的质量检测,包括外观检查、尺寸测量、性能测试等。
合格的轮胎被包装成最终成品,准备发往市场销售。
总的来说,轮胎的工艺流程包括原材料准备、成型、硫化、检测和包装等环节。
每个环节都需要高度的技术和管理水平,以确保轮胎的质量和性能达到标准要求。
随着科技的不断进步,轮胎生产工艺也在不断改进和创新,以满足市场对轮胎的不断提高的需求。
通过本文的介绍,相信读者对轮胎的工艺流程有了更深入的了解。
轮胎作为汽车的重要组成部分,其制造工艺的精细程度和复杂性不容小觑。
只有经过严格的工艺流程和质量控制,才能生产出安全、可靠、耐用的轮胎产品,为汽车行驶提供保障。
轮胎工艺流程
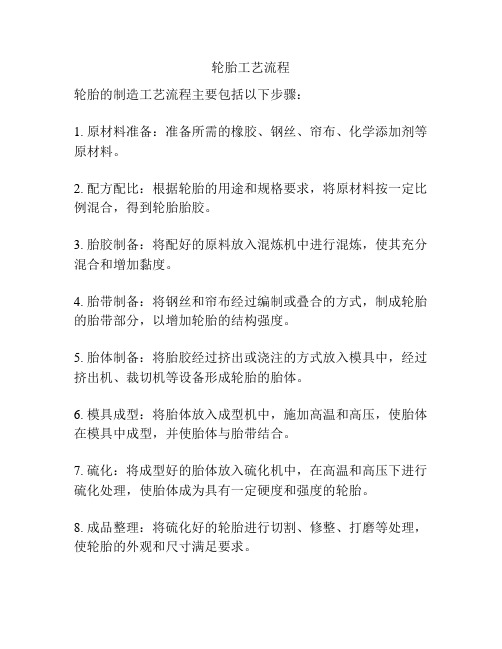
轮胎工艺流程
轮胎的制造工艺流程主要包括以下步骤:
1. 原材料准备:准备所需的橡胶、钢丝、帘布、化学添加剂等原材料。
2. 配方配比:根据轮胎的用途和规格要求,将原材料按一定比例混合,得到轮胎胎胶。
3. 胎胶制备:将配好的原料放入混炼机中进行混炼,使其充分混合和增加黏度。
4. 胎带制备:将钢丝和帘布经过编制或叠合的方式,制成轮胎的胎带部分,以增加轮胎的结构强度。
5. 胎体制备:将胎胶经过挤出或浇注的方式放入模具中,经过挤出机、裁切机等设备形成轮胎的胎体。
6. 模具成型:将胎体放入成型机中,施加高温和高压,使胎体在模具中成型,并使胎体与胎带结合。
7. 硫化:将成型好的胎体放入硫化机中,在高温和高压下进行硫化处理,使胎体成为具有一定硬度和强度的轮胎。
8. 成品整理:将硫化好的轮胎进行切割、修整、打磨等处理,使轮胎的外观和尺寸满足要求。
9. 质量检测:对成品轮胎进行外观检查、尺寸检测、性能测试等,确保轮胎的质量符合标准要求。
10. 包装和出厂:对合格的轮胎进行包装,并进行质量追溯和出厂记录,最后将轮胎出厂。
轮胎制造工艺流程

轮胎制造工艺流程轮胎是汽车的重要组成部分,是汽车行驶的基础保障之一。
轮胎的制造过程从原材料的加工开始,经过多个工序完成最终的成品。
以下是轮胎制造的大致工艺流程。
1. 原材料的准备:轮胎制造的原材料主要包括橡胶、纤维材料和钢丝等。
这些原材料需要经过加工处理,以达到符合轮胎制造过程的要求。
橡胶是轮胎最主要的原材料之一,需要在橡胶混炼机中将各种添加剂和硫化药剂加入到橡胶中,经过混合、摇匀、切割和挤压等工序,最终制成符合要求的橡胶条。
2. 胎体和胎面的制造:车胎的主要结构部分是胎体和胎面,它们是轮胎性能的决定因素。
胎体是由一层层的帘子布通过缠绕、融合而成,而胎面则是采用硫化面层和胶料进行压制而成的。
制造胎体和胎面需要使用专门的机器设备,并且需要根据每个车型的要求进行设计、调整。
3. 胎面加工和组装:制成的胎体和胎面需要进行进一步的加工和组装。
其中,胎面需要进行花纹图案打印、切割、冲孔、铆钉等加工工序,以达到良好的抓地性和耐用性。
在此基础上,胎体和胎面经过组装粘接、裁切、堆叠、卷曲等工序,最终形成半成品轮胎。
4. 硫化:硫化是轮胎制造过程中最重要的工序之一。
半成品轮胎通过进入硫化胶压机,经过热压、硫化、降温等复杂的物理和化学反应,最终形成具有强度、柔韧性、耐磨性等性能的成品轮胎。
硫化的温度、时间和压力等参数需要进行精密的控制,以满足不同车型、用途和环境的要求。
5. 最后的质检和包装:制成的成品轮胎需要进行严格的质量检验和测试,以确保轮胎的性能和使用寿命。
轮胎的外观、尺寸、硬度、强度等多个参数需要进行检测,并制定相关标准和规范。
最后,符合质量要求的轮胎将进行包装和运输,以便在全球范围内进行销售和使用。
总的来说,轮胎制造是一项技术要求很高的工艺,需要经历多个工序进行组装和加工。
其专业化程度较高,除了对原材料的品质要求较高外,对设备、技术和环境等方面也有较高的要求。
当前,随着汽车行业的发展和需求的变化,轮胎制造技术和工艺也在不断更新和发展,以迎合市场和用户的需求。
轮胎模具培训教材全解
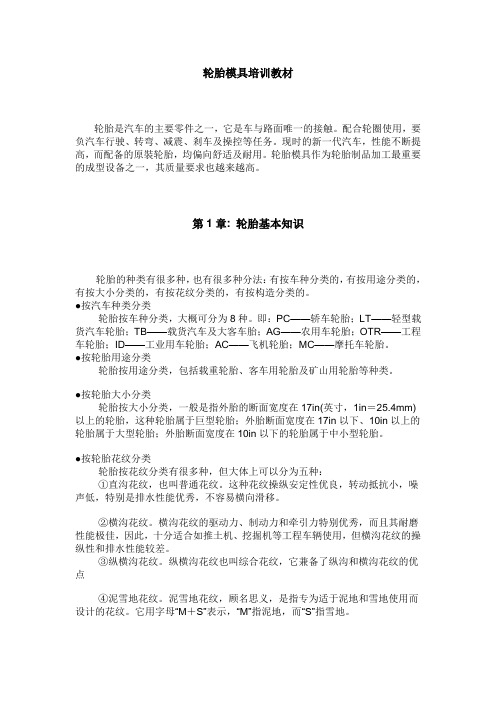
轮胎模具培训教材轮胎是汽车的主要零件之一,它是车与路面唯一的接触。
配合轮圈使用,要负汽车行驶、转弯、减震、剎车及操控等任务。
现时的新一代汽车,性能不断提高,而配备的原裝轮胎,均偏向舒适及耐用。
轮胎模具作为轮胎制品加工最重要的成型设备之一,其质量要求也越来越高。
第1章: 轮胎基本知识轮胎的种类有很多种,也有很多种分法:有按车种分类的,有按用途分类的,有按大小分类的,有按花纹分类的,有按构造分类的。
●按汽车种类分类轮胎按车种分类,大概可分为8种。
即:PC——轿车轮胎;LT——轻型载货汽车轮胎;TB——载货汽车及大客车胎;AG——农用车轮胎;OTR——工程车轮胎;ID——工业用车轮胎;AC——飞机轮胎;MC——摩托车轮胎。
●按轮胎用途分类轮胎按用途分类,包括载重轮胎、客车用轮胎及矿山用轮胎等种类。
●按轮胎大小分类轮胎按大小分类,一般是指外胎的断面宽度在17in(英寸,1in=25.4mm)以上的轮胎,这种轮胎属于巨型轮胎;外胎断面宽度在17in以下、10in以上的轮胎属于大型轮胎;外胎断面宽度在10in以下的轮胎属于中小型轮胎。
●按轮胎花纹分类轮胎按花纹分类有很多种,但大体上可以分为五种:①直沟花纹,也叫普通花纹。
这种花纹操纵安定性优良,转动抵抗小,噪声低,特别是排水性能优秀,不容易横向滑移。
②横沟花纹。
横沟花纹的驱动力、制动力和牵引力特别优秀,而且其耐磨性能极佳,因此,十分适合如推土机、挖掘机等工程车辆使用,但横沟花纹的操纵性和排水性能较差。
③纵横沟花纹。
纵横沟花纹也叫综合花纹,它兼备了纵沟和横沟花纹的优点④泥雪地花纹。
泥雪地花纹,顾名思义,是指专为适于泥地和雪地使用而设计的花纹。
它用字母“M+S”表示,“M”指泥地,而“S”指雪地。
⑤越野花纹。
越野花纹是专门为适应干、湿、崎岖山路和泥泞、沙路而设计的花纹。
●按轮胎结构分类轮胎按照构造分类,以目前广泛使用的情况来分,可分为斜交轮胎和子午线轮胎两大类。
1轮胎模具结构及制造流程介绍

轮胎模具结构及制造流程介绍一般轮胎模具按制造的工艺大致分两种:半钢,全钢。
半钢主要用于轮胎直接较小,花纹比较复杂的轿车轮胎模具,全钢相对于半钢主要用于卡车,工程车等等。
一套轮胎模具按结构一般分为两大部分:壳体和型腔。
轮胎模具的壳体部分对于同一厂家,相对比较固定,而型腔部分涉及到花纹曲线部则经常变化。
壳体部大致分:中套镶环,上盖,上盖开滑板,上盖闭滑板,T型块,中套,进出气嘴,中套滑板,导向条,弓形座,弓形座底板,底座滑板,底座,限位块等型腔部大致分:上侧模,花纹圈,上夹盘,副钢圈,下夹盘,下钢圈,下侧模等。
半钢与全钢轮胎模具的生产流程大体分设计,编程,加工,修花以及装配。
半钢模具工艺以型腔部分流程为例说明:设计---根据厂家要求设计出模具的壳体,型腔,壳体部分对于同一厂家基本就几个统一规格,不会有太大变化;型腔部分则根据厂家花纹进行设计,主要是对侧模字体的排列,花纹块的分块。
编程---根据厂家图纸要求利用软件做出花纹,上下侧模三维造型,并做出加工操作,最后生产NC代码(半钢型腔部分编程,主要是基准模编程,侧模刻字编程)加工---1.花纹块加工:五轴加工基准模(A,C轴摇篮式双摆台机床),利用基准模制作出硅胶,硅胶在反做成石膏,拼圆并铸造出铝花纹圈。
然后经过粗车,半精车,分块,铣立面,打气孔,修花,镶气孔套,拼圆,车口,拆胎,表面处理等完成对花纹加工;2.侧模加工:粗车,热处理,半精车,开槽,铣活字块,研块,车块,刻字(B,C四轴机床),打气孔,镶气孔套,精抛,表面处理等;3.上下钢圈,上下夹盘:粗车,热处理,半精车,刻气线,精车等全钢模具工艺型腔部分流程工艺:设计---根据厂家要求设计出模具的壳体,型腔,壳体部分对于同一厂家基本就几个统一规格,不会有太大变化;型腔部分则根据厂家花纹进行设计,主要是对侧模字体的排列,花纹块的分块编程---根据厂家图纸要求利用软件做出花纹,上下侧模三维造型,并做出加工操作,最后生产NC代码(全钢型腔编程主要根据不同工艺对花纹进行编程,以及侧模编程)加工---1.花纹块加工:根据工艺路线加工花纹,以整圈粗铣后电打为例说明,将环形锻件毛坯经过粗车,热处理,半精车,粗铣,电打,分块,铣立面,打气孔,修花,镶气孔套,拼圆,车口,拆胎,表面处理等;2.侧模加工:基本同半钢侧模加工路线。
轮胎成型工序的流程

轮胎成型工序的流程
轮胎成型工序是轮胎制造过程中的一个关键环节,其流程包括以下几个步骤:
1. 混合原材料:将23种常用配方材料和各种橡胶材料按照一定的比例进行混合,就像将各种材料搅拌在一起制成包子的馅料一样。
2. 准备胶部件:这是轮胎制造过程的第二步,就像准备好组成包子的面皮一样,工作人员将混合好的材料压延成条状,形成半成品的胶部件。
3. 组装成生胎:工作人员将条状胶部件组装成轮胎的半成品,这就相当于把包子包好,就差最后一步发酵了。
4. 硫化成成品轮胎:经过硫化过程,轮胎的半成品被压紧并形成最终形状,就像把包子煮熟一样,轮胎被硫化成了成品轮胎。
5. 最终检验:检查轮胎的外观、均匀性和动平衡等特性,相当于检查包子的口感是否均匀,外观是否美观。
6. 破坏性能抽检:为了确保轮胎的性能和寿命,厂家会进行破坏性能的抽检,检测轮胎的承受负荷和抵抗冲击的能力,这就像测试包子是否能够承受重压一样。
这些步骤完成后,轮胎就可以进行最终的测试和销售了。
- 1、下载文档前请自行甄别文档内容的完整性,平台不提供额外的编辑、内容补充、找答案等附加服务。
- 2、"仅部分预览"的文档,不可在线预览部分如存在完整性等问题,可反馈申请退款(可完整预览的文档不适用该条件!)。
- 3、如文档侵犯您的权益,请联系客服反馈,我们会尽快为您处理(人工客服工作时间:9:00-18:30)。
轮胎模具结构及制造流程介绍
一般轮胎模具按制造的工艺大致分两种:半钢,全钢。
半钢主要用于轮胎直接较小,花纹比较复杂的轿车轮胎模具,全钢相对于半钢主要用于卡车,工程车等等。
一套轮胎模具按结构一般分为两大部分:壳体和型腔。
轮胎模具的壳体部分对于同一厂家,相对比较固定,而型腔部分涉及到花纹曲线部则经常变化。
壳体部大致分:中套镶环,上盖,上盖开滑板,上盖闭滑板,T型块,中套,进出气嘴,中套滑板,导向条,弓形座,弓形座底板,底座滑板,底座,限位块等
型腔部大致分:上侧模,花纹圈,上夹盘,副钢圈,下夹盘,下钢圈,下侧模等。
半钢与全钢轮胎模具的生产流程大体分设计,编程,加工,修花以及装配。
半钢模具工艺以型腔部分流程为例说明:
设计---根据厂家要求设计出模具的壳体,型腔,壳体部分对于同一厂家基本就几个统一规格,不会有太大变化;型腔部分则根据厂家花纹进行设计,主要是对侧模字体的排列,花纹块的分块。
编程---根据厂家图纸要求利用软件做出花纹,上下侧模三维造型,并做出加工操作,最后生产NC代码(半钢型腔部分编程,主要是基准模编程,侧模刻字编程)
加工---1.花纹块加工:五轴加工基准模(A,C轴摇篮式双摆台机
床),利用基准模制作出硅胶,硅胶在反做成石膏,拼圆并铸造出铝花纹圈。
然后经过粗车,半精车,分块,铣立面,打气孔,修花,镶气孔套,拼圆,车口,拆胎,表面处理等完成对花纹加工;
2.侧模加工:粗车,热处理,半精车,开槽,铣活字块,研块,车块,刻字(B,C四轴机床),打气孔,镶气孔套,精抛,表面处理等;
3.上下钢圈,上下夹盘:粗车,热处理,半精车,刻气线,精车等
全钢模具工艺型腔部分流程工艺:
设计---根据厂家要求设计出模具的壳体,型腔,壳体部分对于同一厂家基本就几个统一规格,不会有太大变化;型腔部分则根据厂家花纹进行设计,主要是对侧模字体的排列,花纹块的分块编程---根据厂家图纸要求利用软件做出花纹,上下侧模三维造型,并做出加工操作,最后生产NC代码(全钢型腔编程主要根据不同工艺对花纹进行编程,以及侧模编程)
加工---1.花纹块加工:根据工艺路线加工花纹,以整圈粗铣后电打为例说明,将环形锻件毛坯经过粗车,热处理,半精车,粗铣,电打,分块,铣立面,打气孔,修花,镶气孔套,拼圆,车口,拆胎,表面处理等;2.侧模加工:基本同半钢侧模加工路线。
3.上下钢圈及上下夹盘加工路线也基本同半钢。
中套,弓形座,上盖,底座,导向条等壳体部分,生产加工相对简单且单一
最后将所有组件装配成一副轮胎模具,并通过试压,测量间隙
达到厂家标准。
在整个工艺流程中,我的团队共有5人,涉及到编程,钢片设计,工艺。
对半钢,全钢花纹编程,上下侧模编程以及壳体部都能独立完成。
钢片设计人员,能独立完成对钢片的设计以及加工指导。
工艺部分,有熟悉轮胎模具加工的工艺安排人员。
不足的是,对于半钢铸造,质检涉及不多,对其中的操作规程,标准等不太了解。