炼钢电炉烟气余热锅炉
饱和蒸汽汽轮机发电技术在电炉炼钢烟气余热回收中的应用

0引言为了改善全球环境资源,各国统一部署,提出二氧化碳减排计划,即要求2030年前二氧化碳排放量达到峰值,2060年前实现二氧化碳超净排放,排放量为零。
我国为适应国际环保政策变化,将废钢资源合理化利用,在15年时间内逐步用电炉炼钢技术取代转炉炼钢技术。
而电炉炼钢生产过程产生的烟气具有一定的热能焓值,可以回收利用,节能减排,降低能耗。
高温烟气通过余热锅炉与水对流换热,锅炉汽包产生饱和蒸汽驱动饱和蒸汽汽轮机发电,降低电炉炼钢流程每吨钢的能耗,产生较大的经济效益和社会效益。
值得深入研究饱和蒸汽汽轮机发电技术在电炉炼钢烟气余热回收的应用。
Abstract:In this paper,the characteristics and process flow of electric furnace steelmaking flue gas are analyzed.The working principle of heat accumulator and its parameter calculation in saturated steam power generation technology are introduced.Measures to improve steam dryness in saturated steam turbines are described.Saturated steam turbine power calculations are described,among other things.Key words:saturated steam,steam turbine,electric furnace steelmaking第一作者简介:刘向东(1979-)男,本科,高级工程师,毕业于长沙理工大学自动化专业,主要从事发电厂调试,检修方面工作。
DOI:10.13808/ki.issn1674-9987.2023.04.004刘向东(中冶南方都市环保工程技术股份有限公司,湖北武汉,430205)摘要:文章分析了电炉炼钢烟气的特点及工艺流程,重点介绍了饱和蒸汽发电技术中蓄热器工作原理及其参数计算,讲述了饱和蒸汽汽轮机提高蒸汽干度措施,描述了饱和蒸汽汽轮机功率计算等内容。
浅谈余热锅炉在40t电弧炉上的应用
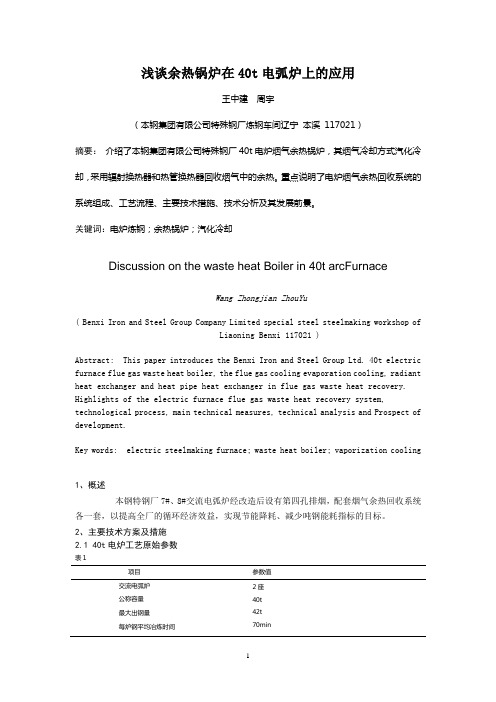
浅谈余热锅炉在40t电弧炉上的应用王中建周宇(本钢集团有限公司特殊钢厂炼钢车间辽宁本溪 117021)摘要:介绍了本钢集团有限公司特殊钢厂40t电炉烟气余热锅炉,其烟气冷却方式汽化冷却,采用辐射换热器和热管换热器回收烟气中的余热。
重点说明了电炉烟气余热回收系统的系统组成、工艺流程、主要技术措施、技术分析及其发展前景。
关键词:电炉炼钢;余热锅炉;汽化冷却Discussion on the waste heat Boiler in 40t arcFurnaceWang Zhongjian ZhouYu( Benxi Iron and Steel Group Company Limited special steel steelmaking workshop ofLiaoning Benxi 117021 )Abstract: This paper introduces the Benxi Iron and Steel Group Ltd. 40t electric furnace flue gas waste heat boiler, the flue gas cooling evaporation cooling, radiant heat exchanger and heat pipe heat exchanger in flue gas waste heat recovery. Highlights of the electric furnace flue gas waste heat recovery system, technological process, main technical measures, technical analysis and Prospect of development.Key words: electric steelmaking furnace; waste heat boiler; vaporization cooling1、概述本钢特钢厂7#、8#交流电弧炉经改造后设有第四孔排烟,配套烟气余热回收系统各一套,以提高全厂的循环经济效益,实现节能降耗、减少吨钢能耗指标的目标。
余热锅炉试压、煮炉方案
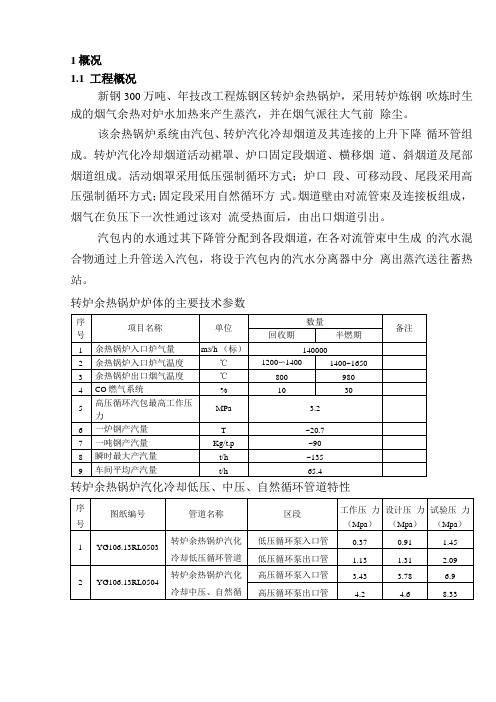
1概况1.1工程概况新钢300万吨、年技改工程炼钢区转炉余热锅炉,采用转炉炼钢吹炼时生成的烟气余热对炉水加热来产生蒸汽,并在烟气派往大气前除尘。
该余热锅炉系统由汽包、转炉汽化冷却烟道及其连接的上升下降循环管组成。
转炉汽化冷却烟道活动裙罩、炉口固定段烟道、横移烟道、斜烟道及尾部烟道组成。
活动烟罩采用低压强制循环方式;炉口段、可移动段、尾段采用高压强制循环方式;固定段采用自然循环方式。
烟道壁由对流管束及连接板组成,烟气在负压下一次性通过该对流受热面后,由出口烟道引出。
汽包内的水通过其下降管分配到各段烟道,在各对流管束中生成的汽水混合物通过上升管送入汽包,将设于汽包内的汽水分离器中分离出蒸汽送往蓄热站。
转炉余热锅炉炉体的主要技术参数转炉余热锅炉汽化冷却低压、中压、自然循环管道特性1.2 工程特点本工程中锅炉管道分低压循环管道、中压循环管道、和自然循环管道。
管道 上泵的进出口前后管道设计压力都不一致。
因此管道压力试验必须分段分级进 行。
1.3 编制依据首钢设备结构制造厂提供的锅炉图纸和说明书 中冶赛迪设计的相关施工图纸 《蒸汽锅炉安全技术监察规程》(1996)《工业锅炉安装工程施工及验收规范》 (GB50273-98) 《压力管道规范》 (GB/T20801-2006) 《工业金属管道设计规范》 (GB50316-2000)《工业金属管道工程施工及验收规范》 (GB 50235-97)《现场设备、工业管道焊接工程施工及验收规范》 (GB 50235-98)2.施工部署 2.1 机构设备本工程设项目负责人、各专业副经理、技术负责人各一名。
项目 负责人全面负责工程从开工到竣工的施工管理协调工作,各专业副经 理负责各专业施工任务的落实和实施,技术负责人负责工程的施工技术管理、质量监督的控制工作,本工程设施工技术、经营、 务部门应明确分工,各负其责,现场施工组织机构图如下: 协调业主监理及其它单位的关系。
供应、质量、安全等业务部门,各业 全力以赴为本工程做好服务工作。
转炉余热锅炉

转炉余热锅炉简介转炉余热锅炉是一种利用钢铁冶炼过程中的转炉废气余热来发电的锅炉设备。
在钢铁冶炼过程中,废气中含有大量热能。
通过利用转炉废气的高温高压特点,将废气中的热能转化为蒸汽,推动汽轮机发电,实现能源的有效回收利用。
工作原理转炉余热锅炉的工作原理可以总结为以下几个步骤: 1. 废气收集:在钢铁冶炼过程中,转炉产生的废气被收集到转炉余热锅炉中,进入余热锅炉进行处理。
2. 燃烧:废气中的燃料在锅炉燃烧室中被燃烧,产生高温高压的烟气。
3. 热交换:烟气通过余热锅炉内的热交换器,与锅炉中的水进行热交换。
烟气中的热能被传递给水,使水变为蒸汽。
4. 蒸汽发电:产生的蒸汽通过蒸汽管道输送到汽轮机中,推动汽轮机转动,从而驱动发电机发电。
5. 回收利用:通过发电实现废气中的热能回收利用,提高能源利用效率,减少能源浪费。
优势与应用1. 能源回收利用转炉余热锅炉利用了钢铁冶炼过程中产生的废气中的高温高压热能,将其转化为蒸汽发电。
这种方式实现了废气中热能的回收利用,提高了能源的利用效率。
同时,通过减少能源的浪费,也能降低钢铁企业的能源消耗和生产成本。
2. 环保减排转炉余热锅炉的运行过程中,能够减少钢铁冶炼过程中排放的废气和固体废物。
废气经过处理后,烟尘排放得到有效控制,减少了对大气环境的污染。
此外,转炉余热锅炉通过回收废气中的热能发电,还能减少温室气体的排放,对于缓解温室效应和减少碳排放具有积极的意义。
3. 应用领域广泛转炉余热锅炉在钢铁冶炼行业得到了广泛应用。
钢铁生产过程中,转炉冶炼是一项重要工序,产生大量的废气。
通过利用废气中的热能,实现能源回收利用,不仅可以节约能源和降低生产成本,还能提高钢铁企业的竞争力。
此外,转炉余热锅炉也逐渐在其他行业得到应用,如石化、化工、纸浆等领域。
结语转炉余热锅炉作为一种能源回收利用设备,在钢铁冶炼过程中发挥了重要的作用。
通过将废气中的高温高压热能转化为蒸汽发电,转炉余热锅炉实现了对废气中热能的有效回收利用,提高了能源利用效率,减少了能源浪费。
110吨电炉余热锅炉操作规程
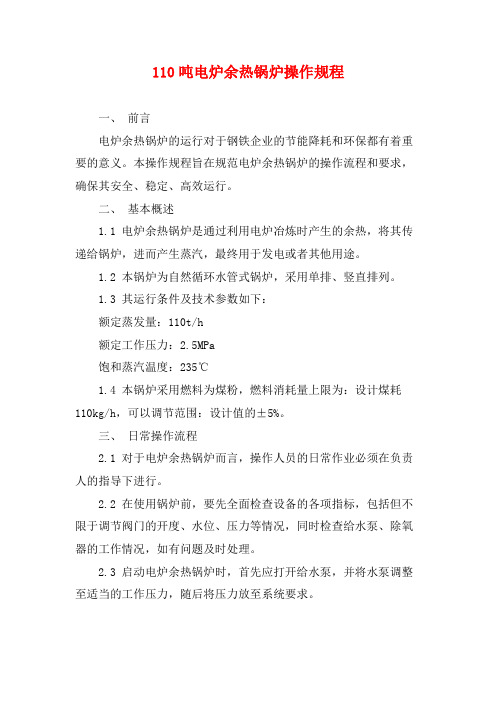
110吨电炉余热锅炉操作规程一、前言电炉余热锅炉的运行对于钢铁企业的节能降耗和环保都有着重要的意义。
本操作规程旨在规范电炉余热锅炉的操作流程和要求,确保其安全、稳定、高效运行。
二、基本概述1.1 电炉余热锅炉是通过利用电炉冶炼时产生的余热,将其传递给锅炉,进而产生蒸汽,最终用于发电或者其他用途。
1.2 本锅炉为自然循环水管式锅炉,采用单排、竖直排列。
1.3 其运行条件及技术参数如下:额定蒸发量:110t/h额定工作压力:2.5MPa饱和蒸汽温度:235℃1.4 本锅炉采用燃料为煤粉,燃料消耗量上限为:设计煤耗110kg/h,可以调节范围:设计值的±5%。
三、日常操作流程2.1 对于电炉余热锅炉而言,操作人员的日常作业必须在负责人的指导下进行。
2.2 在使用锅炉前,要先全面检查设备的各项指标,包括但不限于调节阀门的开度、水位、压力等情况,同时检查给水泵、除氧器的工作情况,如有问题及时处理。
2.3 启动电炉余热锅炉时,首先应打开给水泵,并将水泵调整至适当的工作压力,随后将压力放至系统要求。
2.4 开启点火器,引燃炉膛中的火焰,快速升温至设计温度,调整好阀门。
2.5 检查炉膛中的火焰和尾部的排烟情况,确保其正常燃烧。
2.6 建议在设备使用前进行两次清洗,以确保其干净,同时有效防止污垢对锅炉的损伤或者不良影响。
2.7 在锅炉运行时,要时刻关注水位的变化情况,保持其稳定在正常范围内,以确保系统正常供水。
2.8 当锅炉或其他设备发现问题时,要及时报告,设备维修完毕后需经过负责人的验收才可进行使用。
四、安全操作要求3.1 在使用电炉余热锅炉前,必须对锅炉进行全面检查。
3.2 在启动锅炉前,要确保清洁和冲洗工作已经做好,以及有足够的水和燃料。
3.3 在启动过程中,必须对锅炉进行全面检验,排查其是否存在异常。
3.4 对于操作人员而言,需要明确自己的职责,确保自己的工作安全。
3.5 运行过程中,必须时刻观察水位、压力等指标,绝不能放松,以免意外事件的发生。
热管余热锅炉在炼钢电弧炉烟气余热回收系统中的应用
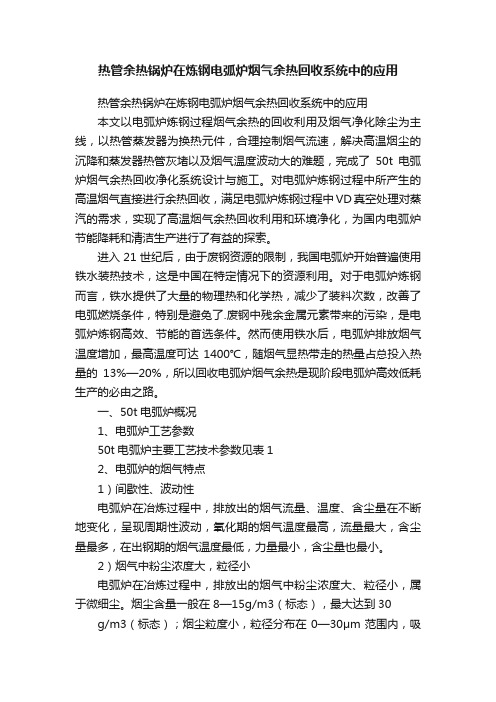
热管余热锅炉在炼钢电弧炉烟气余热回收系统中的应用热管余热锅炉在炼钢电弧炉烟气余热回收系统中的应用本文以电弧炉炼钢过程烟气余热的回收利用及烟气净化除尘为主线,以热管蒸发器为换热元件,合理控制烟气流速,解决高温烟尘的沉降和蒸发器热管灰堵以及烟气温度波动大的难题,完成了50t电弧炉烟气余热回收净化系统设计与施工。
对电弧炉炼钢过程中所产生的高温烟气直接进行余热回收,满足电弧炉炼钢过程中VD真空处理对蒸汽的需求,实现了高温烟气余热回收利用和环境净化,为国内电弧炉节能降耗和清洁生产进行了有益的探索。
进入21世纪后,由于废钢资源的限制,我国电弧炉开始普遍使用铁水装热技术,这是中国在特定情况下的资源利用。
对于电弧炉炼钢而言,铁水提供了大量的物理热和化学热,减少了装料次数,改善了电弧燃烧条件,特别是避免了.废钢中残余金属元素带来的污染,是电弧炉炼钢高效、节能的首选条件。
然而使用铁水后,电弧炉排放烟气温度增加,最高温度可达1400℃,随烟气显热带走的热量占总投入热量的13%—20%,所以回收电弧炉烟气余热是现阶段电弧炉高效低耗生产的必由之路。
一、50t电弧炉概况1、电弧炉工艺参数50t电弧炉主要工艺技术参数见表12、电弧炉的烟气特点1)间歇性、波动性电弧炉在冶炼过程中,排放出的烟气流量、温度、含尘量在不断地变化,呈现周期性波动,氧化期的烟气温度最高,流量最大,含尘量最多,在出钢期的烟气温度最低,力量最小,含尘量也最小。
2)烟气中粉尘浓度大,粒径小电弧炉在冶炼过程中,排放出的烟气中粉尘浓度大、粒径小,属于微细尘。
烟尘含量一般在8—15g/m3(标态),最大达到30 g/m3(标态);烟尘粒度小,粒径分布在0—30μm范围内,吸附力大。
电弧炉烟尘化学成分见表2.3电弧炉能量平衡50t电弧炉爱配加30%铁水冶炼时的能量平衡表如图1所示由图1可知,在50t电弧炉的能量平衡中,高温烟气带走的热量一般约占电弧炉总热量的11%,冶炼强度增加,单位时间内高温烟气带走的热量增加。
电炉炼钢节能措施

电炉炼钢节能措施引言随着环保意识的增强和能源成本的上升,节能已经成为了各行各业的重要议题。
在钢铁行业中,电炉炼钢是一种常见的钢铁生产工艺。
然而,传统的电炉炼钢过程存在着能源浪费的问题,需要采取节能措施来提高能源利用效率。
本文将介绍一些有效的电炉炼钢节能措施,以帮助钢铁企业减少能源消耗,提高盈利能力。
1. 优化电炉操作参数合理的电炉操作参数对节能至关重要。
以下是一些常见的优化措施:•温控系统优化:通过对电炉的温度控制系统进行优化,可以实现更精确的温度控制,避免能源的过度消耗。
•母线电压优化:对电炉的母线电压进行优化,可以实现更高效的电能转换,降低能源浪费。
•电炉功率控制:合理控制电炉的功率,避免过高或过低的功率消耗,提高能源利用效率。
2. 废气余热回收利用电炉炼钢过程中产生的废气中含有大量的热能,如果能有效利用这些余热,就可以减少能源的消耗。
以下是一些常见的废气余热回收利用措施:•废气余热锅炉:通过安装废气余热锅炉,将废气中的热能转化为蒸汽或热水,供给其他工艺过程使用或供热。
•废气余热发电:通过废气余热发电系统,将废气中的热能转化为电能,提供给电网使用,达到能源的再生利用。
•废气余热回采:通过热交换器等设备,将废气中的热能回收,供给其他工艺过程使用,减少能源的浪费。
3. 电炉热保护措施电炉炼钢过程中,合理的热保护措施可以降低能源消耗,延长设备的使用寿命。
以下是一些常见的电炉热保护措施:•保温材料优化:优化电炉的保温材料,减少热量的散失,提高能源的利用效率。
•空气冷却系统优化:通过对电炉的空气冷却系统进行优化,减少冷却的能量损失,提高能源利用效率。
•炉衬维护:定期检查和维护电炉的炉衬,保证其完整性,减少热量的散失,延长设备的使用寿命。
4. 电炉技术改进通过技术改进,可以进一步提高电炉的能源利用效率。
以下是一些常见的技术改进措施:•高效炼钢工艺:采用先进的电炉炼钢工艺,如负压炼钢等,提高炼钢效率,减少能源消耗。
余热锅炉的热源
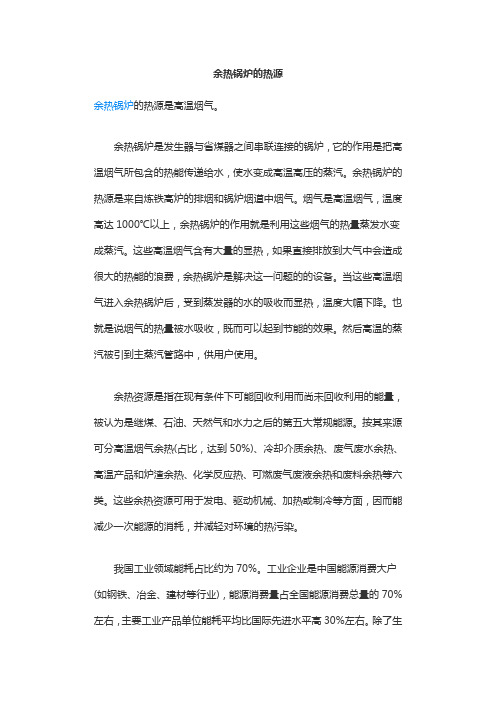
余热锅炉的热源余热锅炉的热源是高温烟气。
余热锅炉是发生器与省煤器之间串联连接的锅炉,它的作用是把高温烟气所包含的热能传递给水,使水变成高温高压的蒸汽。
余热锅炉的热源是来自炼铁高炉的排烟和锅炉烟道中烟气。
烟气是高温烟气,温度高达1000℃以上,余热锅炉的作用就是利用这些烟气的热量蒸发水变成蒸汽。
这些高温烟气含有大量的显热,如果直接排放到大气中会造成很大的热能的浪费,余热锅炉是解决这一问题的的设备。
当这些高温烟气进入余热锅炉后,受到蒸发器的水的吸收而显热,温度大幅下降。
也就是说烟气的热量被水吸收,既而可以起到节能的效果。
然后高温的蒸汽被引到主蒸汽管路中,供用户使用。
余热资源是指在现有条件下可能回收利用而尚未回收利用的能量,被认为是继煤、石油、天然气和水力之后的第五大常规能源。
按其来源可分高温烟气余热(占比,达到50%)、冷却介质余热、废气废水余热、高温产品和炉渣余热、化学反应热、可燃废气废液余热和废料余热等六类。
这些余热资源可用于发电、驱动机械、加热或制冷等方面,因而能减少一次能源的消耗,并减轻对环境的热污染。
我国工业领域能耗占比约为70%。
工业企业是中国能源消费大户(如钢铁、冶金、建材等行业),能源消费量占全国能源消费总量的70%左右,主要工业产品单位能耗平均比国际先进水平高30%左右。
除了生产工艺相对落后和产业结构不合理的因素外,工业余热利用率低,能源没有得到充分综合利用是造成能耗高的重要原因,我国能源利用率仅约为33%,较发达国家低10%左右,至少50%的工业耗能以各种形式的余热被直接废弃。
因此余热利用具备较大提升潜力。
余热锅炉是利用各种工业过程中的废气、废料或废液中的显热或其可燃物质燃烧后产生的热量的锅炉。
与常规锅炉的区别在于加热的热源不同。
余热锅炉的热源可以是高温烟气余热、化学反应余热、可燃废气余热,甚至可以利用高温产品余热。
余热锅炉一方面能够利用工业生产中的废气、废能等产生蒸汽用于发电、供热,同时还能将废气中的粉尘等环境污染物沉降下来,减少固态、液态或气态有害物质的排放。
钢铁企业发电锅炉尾部烟气余热利用技术研究

管理及其他M anagement and other钢铁企业发电锅炉尾部烟气余热利用技术研究孙振巍摘要:在我国容量大且高效的钢铁企业中,机组的最高有效率只有45%,大部分的热能都没有被利用就直接排放到了周围的环境。
通常情况下,钢铁企业的三大设备是损失热能最多的。
其中包括:发电锅炉排烟热损失、主凝器冷却水损失以及辅机循环水热损失。
由于发电锅炉排放的烟气比热低,而且流动速度快,成分过于复杂,有时甚至会对受热面产生腐蚀,为了使排烟的温度降低,燃煤发电锅炉需要提高它的换热量。
基于此,本文探讨了钢铁企业发电锅炉尾部烟气余热利用技术,仅供参考。
关键词:钢铁企业;发电锅炉尾部烟气;余热利用技术;应用分析钢铁企业排烟热损失是钢铁企业发电锅炉各项热损失中最大的一项,一般占比在5%~8%,占发电锅炉总热损失的80%,甚至更高。
影响排烟热损失的主要因素是发电锅炉排烟温度,一般情况下,排烟温度每升高20℃,排烟热损失就会增加0.6%~1.0%。
中国钢铁企业排烟温度控制受到燃烧煤质含硫量导致的酸露点温度影响,现役火电机组中发电锅炉排烟温度普遍维持在125℃~150℃,排烟温度高是一种普遍现象。
因此,发电锅炉排烟余热回收利用技术是节约能源、降低能耗、减少污染排放的有效举措。
1 烟气余热的相关概述1.1 烟气余热利用价值当烟气离开发电锅炉时都会存在较高的温度,对这些高温烟气进行排放时,会使大部分热量被流失掉,为了能够使排烟热被充分得到利用,就要加大对其的研究力度,目前,存在热损失最大的要属钢铁企业中排烟热,而造成热损失的主要原因就是排烟的温度,排烟的温度越高,说明排烟热损失也就越大,因此,要提高对其的利用率,才能有效的解决钢铁企业热损失这个问题,进而使钢铁企业机组的运行效率得到显著的提高。
但是这里我们要强调一点,就是当排烟温度降低以后,会提高能源的利用率,如果利用传热学对其进行分析后发现,当传热温差较少时会降低热交换的效率,因此,就要扩大热传面积和烟道面积。
电炉炼钢余热回收技术

电炉炼钢余热回收技术摘要:在电炉炼钢过程中烟气流量、温度周期性波动较大。
针对电炉炼钢过程中烟气周期性波动大,余热利用不足造成能量损失的现状,从电炉炼钢余热回收的理论计算出发,通过在电炉水冷烟道后加装一台余热锅炉,将烟气中热能转化为电能。
电炉炼钢行业属于高能耗行业,炼钢中排出废气热量高,含尘量大,不回收利用,不符合环保要求。
特别在能源紧缺、碳达峰、碳中和的倡导下,电炉炼钢余热回收利用的经济效益和环境效益显著。
基于此,本文对电炉炼钢余热回收技术进行了简要的分析。
关键词:电炉;炼钢;余热回收;技术1电炉炼钢余热回收原理1.1电炉炼钢烟气分析电炉在炼钢过程中烟气流量和温度波动幅度大,而且成周期性变化。
电炉炼钢主要分为3个阶段,分别为融化期、氧化期、出钢期。
融化期为燃烧废钢中的可燃物产生大量高温黑褐色烟气。
氧化期为氧化脱碳,因吹氧或加矿石而产生大量高温赤褐色浓烟,且烟气中携带CO。
在冶炼的氧化阶段烟、尘排放量很大,此时期烟气温度高达1200~1600℃,烟气含尘量高达30g/Nm³。
出钢期为倾倒钢业液,此阶段电炉停止通电,不产生烟气。
电炉炼钢一般出钢周期为42min,其中融化期26min、氧化期6min、出钢期10min。
电炉炼钢废钢种类庞杂,烟气中含尘量大,根据收集电炉烟气灰分分析,灰分的颗粒粒径基本在微米级,成分主要含Fe2O3、CaO、MgO、ZnO、SiO2、K2O、SO3、MnO、Na2O、CL、AL2O3、、PbO、P2O5、Cr2O3、CuO、TiO2。
1.2余热回收利用电炉炼钢过程中会产生大量的高温烟气,这部分烟气热量占总能耗的21%,传统的余热利用是将这部分烟气用于加热废钢+极速水冷后与顶部烟罩吸收空气混合后直接排放,不能很好利用这部分热量。
在电炉冷却烟道后加装一台余热锅炉,并通过蒸汽发电技术把这部分热能转化为电能,能更好的回收这部分热能,而且电炉在炼钢中需要消耗大量的电能,可以减少电炉对电能的消耗,也能带来很好的经济和环保效应。
炼钢转炉烟气余热饱和蒸汽发电分析

炼钢转炉烟气余热饱和蒸汽发电分析摘要:当前炼钢转炉烟气余热饱和蒸汽发电技术已经比较成熟,在很多钢铁企业已经得到了良好的应用,本文结合案例简单分析了炼钢转炉烟气余热回收以及饱和蒸汽发电技术的应用方法。
关键词:炼钢转炉;烟气余热;饱和蒸汽发电对饱和蒸汽发电技术进行研究,分析目前依然存在的不足,强调在实际应用中需要注意的事项,争取通过不断优化来达到更好的发电效果,同时延长汽轮机服务寿命,降低高温蒸汽与汽轮机运行状态的不利影响。
一、炼钢转炉烟气余热资源分析炼钢转炉的吹炼环节会有大量温度在1400~1600℃的含尘撸起产生,随着吹氧强度的增加,加上花费时间越短,每小时所对应产生的炉气量越大。
以及在吹炼期的不同时间段,碳氧化速度的不同,决定了熔池排出的炉气量以及路气成分也会有较大的差异。
转炉烟气可以提供大量的高热显热,大部分的钢铁企业均是通过余热锅炉进行蒸汽回收,整个流程比较简单,将冶炼环节产生的高温烟气通入到余热锅炉内达到降温目的,会有大量的热会释放出来,并由锅炉内的饱和水吸收,促使其转变成饱和蒸汽。
需要注意的是,转炉炼钢产生的高温烟气并不稳定,吹炼期的烟气往往存在着较大的波动,因此30min的吹炼期本质上只有15min左右会有饱和蒸汽形成,并且还会在烟气量变化的影响下,蒸汽量产生剧烈波动。
想要实现饱和蒸汽发电,往往还需要设置蓄热器系统来提高汽轮机进汽流量的稳定性与连续性[1]。
另外,正常情况下即便是采取了多种防护措施,汽轮机入口部位的蒸汽干度也只是在0.995以内,饱和蒸汽不可避免的会对汽轮机产生影响,使其可使用寿命缩短。
为进一步提高饱和蒸汽发电效率,缩短投资回收期,还可以对饱和蒸汽发电系统增设蒸汽过热系统,通过进一步优化达到更高效的发电状态。
二、饱和蒸汽发电系统组成饱和蒸汽发电系统运行具有较高的安全性与可靠性高,整个发电过程无需额外的使用其他燃料或者能源,比较容易操作。
(1)蒸汽产生系统通入到余热锅炉中的转炉高温烟气,由锅炉内的饱和水来吸收释放出的大量热量,由此可得到饱和蒸汽。
钢厂加热炉烟气余热发电工程技术方案提纲

钢厂加热炉烟气余热发电工程技术方案提纲目 录1、总论 .....................................................错误!未定义书签。
错误!未定义书签。
1.1项目背景及项目概况 .............................................................1.2项目承担企业产品质量、技术水平、生产工艺及装备现状,与国内外先进水平的比错误!未定义书签。
较 ....................................................................................错误!未定义书签。
1.3项目建设必要性 ....................................................................2、产品市场预测 .............................................错误!未定义书签。
错误!未定义书签。
2.1产品市场供需分析 ................................................................错误!未定义书签。
2.2价格现状与预测 ....................................................................2.3市场竞争力及风险分析 .........................................................错误!未定义书签。
3、建设规模与产品方案 .......................................错误!未定义书签。
错误!未定义书签。
3.1建设规模 ...........................................................................错误!未定义书签。
炼钢电炉热管型烟气余热回收锅炉

炼钢电炉热管型烟气余热回收锅炉概述:一、工艺方案1.烟气系统来自电弧炉的烟气温度高达1600℃,高温烟气从滑套管流入沉降室(燃烧室),在此进行预除尘和除去CO,烟气进入水冷烟道,经过进一步冷却到850℃,进入热管软水器,在此将20℃软水加热到104℃进热力除氧器,烟气进一步被冷却后,进入热管余热锅炉中,产生高压饱和蒸汽。
烟气再进入热管省煤器,将除氧软水由104℃加热到200℃进入汽液分离器(汽包),烟气降到200℃进入布袋系统,经引风机排入大气。
高压饱和蒸汽送到蓄热器变成低压蒸汽连续供生产、生活或低压发电使用。
2.水汽系统外来20℃水经过软化水处理系统,到软化水箱,由软化水箱经水泵进入除氧器;除氧后,一部分除氧水由补水泵补入省煤器,将软水预热,然后进入蒸发器,蒸发器和汽包进行自然循环;在汽包内蒸汽与水分离产生1.6MPa饱和蒸汽,饱和蒸汽进入蓄热器,用于VD炉抽真空;另一部分进入低压蒸发器,产生0.2MPa的饱和蒸汽供除氧器使用。
3.工艺参数额定烟尘流量:80000Nm3/h烟尘进口温度:750℃-200℃烟尘出口温度:-200℃烟尘含尘浓度:-8g/m3设计蒸汽产能:5-8t/h蒸汽输出压力:-1.2MPa锅炉出口蒸汽压力:1.6MPa二、设计要求1.考虑设备占地与安装方便,热管余热锅炉紧凑的安装在出口烟道上。
余热锅炉本体长16米宽8米。
2.为了保证蒸汽余热锅炉耐压性能好,热管与水接触处采用套管式连接,在蒸汽侧产生很小单元,这样增加了水的流速,提高了热换效率,又增加了整体的受压效果,保证蒸汽锅炉的正常使用,每根热管又是一个独立的整体,即使有几根热管损坏也不会影响整个锅炉的使用。
3.因列管式换热器是两头焊接,存在应力、易损坏和单根列管损坏后,电弧炉烟气与水串通,生产过程中需紧急停车等问题造成的经济损失较大,因此此设备不能采用。
而热管型设备克服了以上多种弊端。
热管是一种新型高效的传热元件,按较精确的定义应称之为“封闭的两相传热系统”,即在一个抽成真空的封闭的体系内,依赖装入内部的流体的相态变化(液态变为汽态和汽态变为液态)来传递热量的装置。
炼钢工程电炉余热锅炉系统
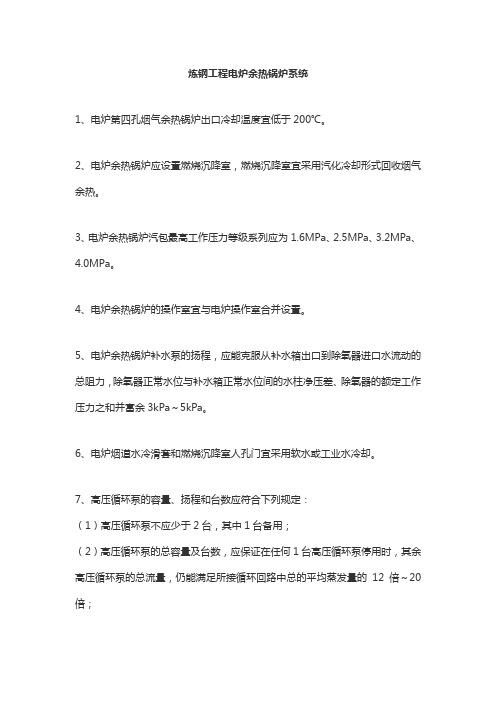
炼钢工程电炉余热锅炉系统1、电炉第四孔烟气余热锅炉出口冷却温度宜低于200℃。
2、电炉余热锅炉应设置燃烧沉降室,燃烧沉降室宜采用汽化冷却形式回收烟气余热。
3、电炉余热锅炉汽包最高工作压力等级系列应为1.6MPa、2.5MPa、3.2MPa、4.0MPa。
4、电炉余热锅炉的操作室宜与电炉操作室合并设置。
5、电炉余热锅炉补水泵的扬程,应能克服从补水箱出口到除氧器进口水流动的总阻力,除氧器正常水位与补水箱正常水位间的水柱净压差、除氧器的额定工作压力之和并富余3kPa~5kPa。
6、电炉烟道水冷滑套和燃烧沉降室人孔门宜采用软水或工业水冷却。
7、高压循环泵的容量、扬程和台数应符合下列规定:(1)高压循环泵不应少于2台,其中1台备用;(2)高压循环泵的总容量及台数,应保证在任何1台高压循环泵停用时,其余高压循环泵的总流量,仍能满足所接循环回路中总的平均蒸发量的12倍~20倍;(3)高压循环泵的扬程应为锅筒下降管出口到锅筒上升管进口循环水经循环水泵流动的总阻力并另加10%的余量;(4)高压循环泵应采用热水泵。
8、高压循环泵应布置在锅筒以下的平台上,且锅筒的最低水位面到高压循环泵中心线的水柱,不应小于下列各项的代数和:(1)高压循环泵进口处水的汽化压力和锅筒额定工作压力之差;(2)高压循环泵的汽蚀余量;(3)高压循环泵进水管的流动阻力;(4)高压循环泵安全运行必需的富余量3kPa~5kPa。
9、在高压强制循环回路中应设流量检测装置。
10、电炉余热锅炉锅筒容积在低水位时,锅筒的有效水容积,应保证在给水系统出现故障时,使锅炉安全工作到炼完一炉钢水;在高水位时,锅筒的蒸汽空间应满足锅炉最大瞬时蒸发量时蒸汽空间负荷强度不超过450m3/(m3·h)。
11、锅炉应设定期排污扩容系统,排污扩容器的容量应满足锅炉事故放水的需要。
12、排污管路、取样管应符合下列要求:(1)每台余热锅炉的定期排污应从锅筒底部和余热锅炉各段的下联箱接出。
炼钢工程转炉余热锅炉系统
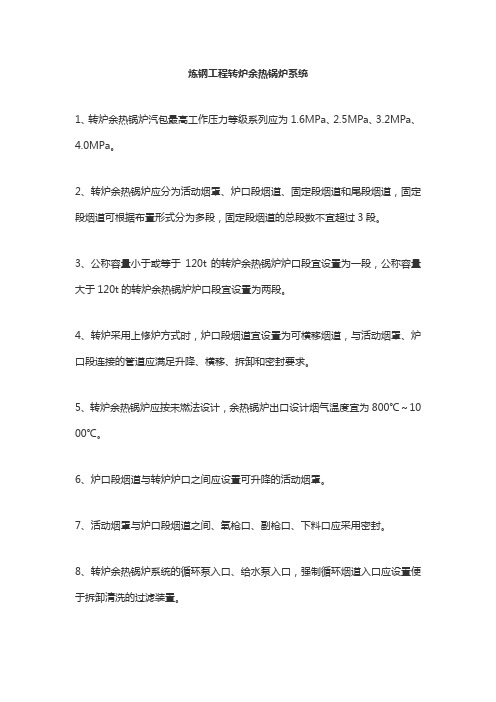
炼钢工程转炉余热锅炉系统
1、转炉余热锅炉汽包最高工作压力等级系列应为1.6MPa、2.5MPa、3.2MPa、4.0MPa。
2、转炉余热锅炉应分为活动烟罩、炉口段烟道、固定段烟道和尾段烟道,固定段烟道可根据布置形式分为多段,固定段烟道的总段数不宜超过3段。
3、公称容量小于或等于120t的转炉余热锅炉炉口段宜设置为一段,公称容量大于120t的转炉余热锅炉炉口段宜设置为两段。
4、转炉采用上修炉方式时,炉口段烟道宜设置为可横移烟道,与活动烟罩、炉口段连接的管道应满足升降、横移、拆卸和密封要求。
5、转炉余热锅炉应按未燃法设计,余热锅炉出口设计烟气温度宜为800℃~10 00℃。
6、炉口段烟道与转炉炉口之间应设置可升降的活动烟罩。
7、活动烟罩与炉口段烟道之间、氧枪口、副枪口、下料口应采用密封。
8、转炉余热锅炉系统的循环泵入口、给水泵入口,强制循环烟道入口应设置便于拆卸清洗的过滤装置。
某钢厂电炉余热发电系统的余热锅炉设计

设计总说明 (I)INTRODUCTION (II)1绪论 (1)1.1背景 (1)1.2我国余热利用现状 (1)1.3我国钢铁工业余热资源的回收利用现状与分析 (2)1.4余热锅炉的型式 (3)1.5余热锅炉的发展动向 (3)1.6本设计的主要内容 (4)2余热锅炉的选型及结构布置 (6)2.1余热锅炉设计主要参数 (6)2.2余热锅炉的选型 (6)2.3余热锅炉整体布置结构 (7)2.4余热锅炉结构及系统组成 (8)3受热面计算方法的概述 (11)3.1热平衡方程式 (11)3.2传热方程式 (12)3.3考查壁面污垢热阻传热过程计算方法 (14)3.4肋片管的传热系数计算 (15)3.5管内流体换热系数 (17)3.6辐射换热系数计算方法 (18)4余热锅炉设计计算 (19)4.1设计计算总体框图 (19)4.2整体设计计算步骤 (19)4.3热力平衡计算 (20)4.4省煤器结构参数选取及热力计算 (22)4.4.1省煤器结构参数选取 (22)4.4.2省煤器热力计算流程图 (24)4.4.3省煤器热力计算 (24)4.5蒸发器热力计算及结构参数 (29)4.5.1蒸发器结构参数选取 (29)4.5.2蒸发器热力计算流程图 (31)4.5.3蒸发器热力计算 (31)4.6水冷壁热力计算及结构参数 (36)4.6.1水冷壁结构参数选取 (36)4.6.2水冷壁热力计算流程图 (37)4.6.3水冷壁热力计算 (37)4.7过热器结构参数选取及热力计算 (40)4.7.1过热器结构参数选取 (40)4.7.2过热器计算方法流程图 (42)4.7.3过热器热力计算 (43)4.8热力校核 (48)4.9烟气阻力计算 (50)5余热锅炉主要零部件 (52)5.1管组支吊架 (52)5.2锅筒 (52)5.3集箱 (53)5.4联箱 (53)6积灰处理 (54)6.1积灰对传热面传热的影响 (54)6.2影响飞灰沉积和结渣的因素 (54)6.3减少积灰的措施 (55)7锅炉经济效益计算 (58)7.1年产蒸汽效益 (58)7.2锅炉的耗钢量 (58)8总结 (60)鸣谢 (61)参考文献 (62)设计总说明某钢厂生产过程中产生烟气的排烟温度较高,如果直接排出到大气不加以利用,会浪费比较多的燃料,加大该钢厂的生产成本,而且对自然环境污染也较大,不利于可持续发展。
炼钢电炉烟气余热锅炉

炼钢电炉烟气余热锅炉NT型热管余热锅炉将炼钢电炉四孔烟气温度由800℃(最高1000℃)降至180℃以下。
产饱和蒸汽用地VD炉真空脱气精炼炉或进入企业蒸汽管网。
设备运行稳定,解决了烟气对设备的冲刷问题、换热面和设备内积灰问题,同时解决了布袋除尘布袋的烟气超温问题热管余热锅炉在冶金电炉烟气余热回收中应用摘要:本文介绍在炼钢电炉烟气布袋除尘系统中,降低烟气温度来满足布袋除尘器的许用温度的一项技术。
该技术采用热管做传热元件,并用水做降温介质,利用热管内工质相变吸收烟气的热量,并产生饱和蒸汽供用户使用。
关键词:热管蒸发器电炉烟气相变降温1.前言随着改革开放的深入进行我国国民经济迅猛发展,发展与环保问题的是我国经济发展的重中之重,冶金领域的环保治理与余热回收是其重要内容。
冶金电炉烟气含尘粒度较小,其直径为40~300目,这一粒度的灰尘一般采用布袋除尘器收集灰尘。
但是电炉尾气温度为500℃至800℃,这一温度超出了布袋除尘器的许用工作温度。
如果不进行降温处理,布袋很快烧穿,无法运行。
这样电炉烟气在进入除尘器的前的降温显得十分必要。
因此开发了热管余热回收系统回收烟气余热,既可将高温烟气能量转化为高温高压蒸汽,满足日常生活和生产的需求,又可将烟气温度降至200℃左右(布袋许用温度),保证了布袋除尘器的可靠运行。
本文通过新疆八一钢厂70t电炉余热回收系统的实例,介绍一种余热回收装置,它成功解决了电炉烟气温度高、灰尘多且细的技术难题。
2. 新疆八一钢厂70t电炉余热回收技术该余热利用系统主要由热管蒸汽发生器、热管软水预热器和蒸汽聚集器、冲击波吹灰系统组成。
热管蒸汽发生器、热管软水预热器主要采用高效传热元件—热管,较一般余热回收装置有许多明显优点。
2.1工艺流程根据70t电炉余热的工艺参数和使用要求,电炉余热回收装置流程见图1(软水流程)、图2(烟气流程)。
工业自来水经水处理软化后进除氧器,再经加压水泵加压进入热管水预热器,经过预热后进入蒸汽聚集器,通过下降管和上升管与热管蒸汽发生器进行自然循环,除氧水吸收热量后,气化形成1.6 MPa的饱和蒸汽,进入蒸汽总管供用户使用。
- 1、下载文档前请自行甄别文档内容的完整性,平台不提供额外的编辑、内容补充、找答案等附加服务。
- 2、"仅部分预览"的文档,不可在线预览部分如存在完整性等问题,可反馈申请退款(可完整预览的文档不适用该条件!)。
- 3、如文档侵犯您的权益,请联系客服反馈,我们会尽快为您处理(人工客服工作时间:9:00-18:30)。
炼钢电炉烟气余热锅炉
NT型热管余热锅炉将炼钢电炉四孔烟气温度由800℃(最高1000℃)降至180℃以下。
产饱和蒸汽用地VD炉真空脱气精炼炉或进入企业蒸汽管网。
设备运行稳定,解决了烟气对设备的冲刷问题、换热面和设备内积灰问题,同时解决了布袋除尘布袋的烟气超温问题
热管余热锅炉在冶金电炉烟气余热回收中应用
摘要:本文介绍在炼钢电炉烟气布袋除尘系统中,降低烟气温度来满足布袋除尘器的许用温度的一项技术。
该技术采用热管做传热元件,并用水做降温介质,利用热管内工质相变吸收烟气的热量,并产生饱和蒸汽供用户使用。
关键词:热管蒸发器电炉烟气相变降温
1.前言
随着改革开放的深入进行我国国民经济迅猛发展,发展与环保问题的是我国经济发展的重中之重,冶金领域的环保治理与余热回收是其重要内容。
冶金电炉烟气含尘粒度较小,其直径为40~300目,这一粒度的灰尘一般采用布袋除尘器收集灰尘。
但是电炉尾气温度为500℃至800℃,这一温度超出了布袋除尘器的许用工作温度。
如果不进行降温处理,布袋很快烧穿,无法运行。
这样电炉烟气在进入除尘器的前的降温显得十分必要。
因此开发了热管余热回收系统回收烟气余热,既可将高温烟气能量转化为高温高压蒸汽,满足日常生活和生产的需求,又可将烟气温度降至200℃左右(布袋许用温度),保证了布袋除尘器的可靠运行。
本文通过新疆八一钢厂70t电炉余热回收系统的实例,介绍一种余热回收装置,它成功解决了电炉烟气温度高、灰尘多且细的技术难题。
2. 新疆八一钢厂70t电炉余热回收技术
该余热利用系统主要由热管蒸汽发生器、热管软水预热器和蒸汽聚集器、冲击波吹灰系统组成。
热管蒸汽发生器、热管软水预热器主要采用高效传热元件—热管,较一般余热回收装置有许多明显优点。
2.1工艺流程
根据70t电炉余热的工艺参数和使用要求,电炉余热回收装置流程见图1(软水流程)、图2(烟气流程)。
工业自来水经水处理软化后进除氧器,再经加压水泵加压进入热管水预热器,经过预热后进入蒸汽聚集器,通过下降管和上升管与热管蒸汽发生器进行自然循环,除氧水吸收热量后,气化形成
1.6 MPa的饱和蒸汽,进入蒸汽总管供用户使用。
2.2工艺条件
(1)平均出钢量:70t/炉
(2)最大烟气量:160000Nm3/h
(3)烟气最高入口温度:800℃
(4)烟气出口温度180 ℃
(5)饱和蒸汽压力:1.25MPa
(6) 回收热量:38500KW
(7)最大蒸汽流量:16t/h
2.3热管余热回收系统结构
此热管余热回收系统主要由热管蒸发器、热管软水预热器、和蒸汽聚集器、冲击波吹灰系统组成。
烟气先经过蒸发器,后经过水预热器。
换热设备(蒸发器和水预热器)之间有过渡段连接,过渡段上设有不锈钢膨胀节(以满足设备的热膨胀)和人孔(供设备安装和停炉检修时使用)以及冲击波吹灰器(吹灰用)。
另外,每台蒸发器和每台水预热器上都设有吹扫管,可根据积灰的情况辅助吹灰。
在蒸发器和水预热器底部设有灰斗,用于储灰和排灰。
2.4系统工作原理
(1)热管蒸发器是由若干根热管元件组合而成。
其基本结构及工作原理如图2所示。
热管的受热段置于热流体风道内,热风横掠热管受热段,热管元件的放热段插在汽一水系统内。
由于热管的存在使得该汽一水系统的受热及循环完全和热源分离而独立存在于热流体的风道之外,汽一水系统不受热流体的直接冲刷。
热流体的热量由热管传给水套管内的饱和水(饱和水由下降管输入),并使其汽化,所产蒸汽(汽、水混合物)经蒸汽上升管到达汽包,经汽水分离以后再经主汽阀输出。
这样热管不断将热量输入水套管,通过外部汽一水管道的上升及下降完成基本的汽一水循环,达到将热烟气降温,并转化为蒸汽的目的。
(2)热管水预热器(省煤器)也是由若干根特殊的热管元件组合而成,热管的受热段置于烟气风道内,热管受热,将热量传至夹套管中从除氧器进来的除氧水,加热到180℃以上,送至蒸汽聚集器。
2.5系统特点
2.5.1采用热管作为传热元件,具有极高的传热性能;气——液换热,一侧是具有一定流速的烟气另一侧是软水相变为蒸汽,换热时对流换热系数为40—60W/m2.℃。
700—800℃的烟气经过热管蒸发器,温度降至180 ℃左右。
同时产生1.6MPa的饱和蒸汽,供用户使用。
2.5.2整个汽水系统的受热及循环完全和热流体隔离而独立存在于热流体烟
道以外,这就使本系统有别于一般余热锅炉。
2.5.3设备中热管元件间相互独立,热流体与蒸汽发生区双重隔离互不影响,即使单根或数根热管损坏,也不影响系统正常运行,同时水、汽也不会由于热管破损而进入热流体。
2.5.4设计时调节热管两端的传热面积可有效地调节和控制壁温,防止低温
酸露点腐蚀。
2.5.5操作简单、维修方便、工作可靠,整个系统的热量输送过程不需要任何外界动力,故障率低,效率高。
2.8换热器的积灰问题
电炉烟气含尘量是8—15g/m3,也就是说每小时500Kg左右的灰尘通过换热器。
电炉烟尘粒度较小0—10μm的灰占灰尘总量的70%以上,该种灰有较强的吸附力,换热器的除灰是该换热器的设计的核心内容
2.6.1在换热器结构的设计上采用以下措施
(1)换热管间距较其他工况设备增大。
(2)烟气在设备中流速设计一般为8米左右。
(3)换热器的布置形式必须考虑便于除尘,换热器布置上采用立式。
2.6.2采用冲击波吹灰系统
冲击波吹灰系统是我国引进前苏联军工技术,我国消化研制开发的在线吹灰产品。
其工作原理是将空气和可燃气按一定比例混合,经高能点火后在冲击波发生器内形成可控强度的冲击波,冲击动能吹扫受热面的同时伴有高声强声波震荡和热清洗作用,以达到吹除积灰保证受热面清洁,提高传热效率,恢复锅炉出力的目的。
2.7 设备运行及使用寿命分析
应用于该工段的换热设备在设计上需考虑三个方面的问题。
一是高温烟气的换热问题;二是设备冲刷问题;三是热应力造成设备损坏问题;四是积灰问题。
热管换热器工作时烟气通过热管换热器的流速为8m/s,流速较低;烟气侧热管镍基钎焊有纵翅片,镍基合金厚度≥0.05mm,硬度HRC≥56。
因此合理的解决烟气对设备的冲刷问题。
热管换热器的热管单支点焊接在联箱壁上,其热涨冷缩变形不受约束,避免了应力破坏。
因此热管换热器不存在热应力造成设备损坏问题。
热管具有单管作业性能,有一根热管(即使部分热管)损坏不会造成换热的烟气和水混淆,对换热的影响也不大。
因此可保证设备长周期稳定运行。
3.结论
余热利用系统投入运行后,不仅确保了粉尘浓度符合环保要求,达到了利用高温烟气的热量产生蒸汽供VD真空炉生产和其他生活用汽使用的目标,而且采用烟气余热利用新技术后原VD真空炉使用进口柴油锅炉作为备用,每年节标煤1.8万吨。