FPC常见不良及预防
FPC柔性电路板铜电镀制程中常见不良因素

FPC柔性电路板铜电镀制程中常见不良因素一、FPC铜电镀(化铜或叫黑孔、PTH)PTH即在不外加电流的情况下,通过镀液的自催化(钯和铜原子作为催化剂)氧化还原反应,使铜离子析镀在经过活化处理的孔壁及铜箔表面上的过程,也称为化学镀铜或自催化镀铜。
A、PTH流程及各步作用整孔→水洗→微蚀→水洗→酸洗→水洗→水洗→预浸→活化→水洗→速化→水洗→水洗→化学铜→水洗.1.整孔;清洁板面,将孔壁的负电荷极化为政电荷,已利与带负电荷的钯胶体粘附.2.微蚀;清洁板面;粗化铜箔表面,以增加镀层的附着性.3.酸洗;清洁板面;除去氧化层,杂质.4.预浸;防止对活化槽的污染.5.活化;使钯胶体附着在孔壁.6.速化;将Pd离子还原成Pd原子,使化学铜能锡镀上去。
7.化学铜:通过化学反应使铜沉积于孔壁和铜箔表面。
B、PTH生产中不良状况处理办法1.孔无铜a:活化钯吸附沉积不好。
b:速化槽:速化剂溶度不对。
c:化学铜:温度过低,使反应不能进行反应速度过慢;槽液成分不对。
2.孔壁有颗粒,粗糙a:化学槽有颗粒,铜粉沉积不均,须安装过滤机装置。
b:板材本身孔壁有毛刺。
3.板面发黑a:化学槽成分不对(NaOH浓度过高)b:建浴时建浴剂不足.C、产品品质检验常见不良:破孔,表面粗糙,表面残胶,尺寸涨缩.(黑孔就是碳黑沉积)1、破孔:钻孔时扯胶引起.2、表面粗糙:铜电镀时电流密度过大引起.3、表面残胶:原材料涂布时引起,裁切断时引起(残碎硝胶遗留在材料上)4、尺寸涨缩:正常的铜电镀的产生尺寸涨缩为0.04-0.07%,影响尺寸涨缩主要与产品生产和使用的环境温度,刷板,蚀刻,设计有关.残留的铜箔越多尺寸涨缩越小。
二、FPC镀铜镀铜即提高孔内镀层均匀性,保证整个版面(孔内及孔口附近的整个镀层)镀层厚度达到一定的要求。
A、制程管控:1、产品确认2、流程确认3、药液确认4、机台参数的确认。
B、品质管控:化学铜应每周都倒槽,作用:有铜沉积于槽底,槽底的铜越来越多,消耗药水就越多,从而使成本变高。
FPC各工序控制要点

自动裁剪裁剪是整个FPC原材料制作的首站,其质量问题对后其影响较大,而且是成本的一个控制点,由于裁剪机械程度较高,对机械性能和保养大为重要.而且裁剪机设备精度基本可以达到所裁剪物的精度要求,所以在对操作员操作技术及熟练程度和责任心提高为重点.1. 原材料编码的认识如; B 08 N N 0 0 R 1 B 250B铜箔类08:厂商代码1N层别,N,铜片S,单面板D,双面板2N绝缘层类别N.无绝缘层类别K.kapthon P.polyster 10 绝缘层厚度0,无1:1mil 2:2mil 20绝缘层与铜片间有无粘着剂0;无1;有R,铜皮类别A:铝箔H:高延展性电解铜R:压延铜E:电解铜1,铜皮厚度B,铜皮处理R:棕化G:normal 250,宽度码Coverlay编码原则2. 制程质量控制根据首件A.操作者应带手套和指套,防止铜箔表面因接触手上之汗渍等氧化.B.正确的架料方式,防止皱折.C.不可裁偏,手对裁时不可破坏冲制定位孔和测试孔.如无特殊说明裁剪公差为张裁时在±1mm 条D.裁时在0.3mm 内E.裁剪尺寸时不能有较大误差,而且要注意其垂直性,即裁剪为张时四边应为垂直(<2°)G.材料质量,材料表面不可有皱折,污点,重氧化现象,所裁切材料不可有毛边,溢胶等.3. 机械保养严格按照<自动裁剪机保养检查纪录表>之执行.CNC:CNC是整个FPC流程的第一站,其质量对后续程序有很大影响.CNC基本流程:组板→打PIN→钻孔→退PIN. 1. 组板选择盖板→组板→胶带粘合→打箭头(记号)基本组板要求:单面板15张单一铜10张或15张双面板10张单一铜10张或15张黄色Coverlay 10张或15张白色Coverlay 25张辅强板根据情况3-6张盖板主要作用:A:减少进孔性毛头B:防止钻机和压力脚在材料面上造成的压伤.C:使钻尖中心容易定位避免钻孔位置的偏斜D:带走钻头与孔壁摩擦产生的热量.减少钻头的扭断.2. 钻针管制办法a. 使用次数管制b. 新钻头之辨识方法c. 新钻头之检验方法3. 品质管控点a. 正确性;b. 根据对钻片及钻孔数据确认产品孔位与c. 孔数的正确性,并check断针监视孔是否完全导通.d. 外观质量;e. 不可有翘铜,毛边之不良现象.4. 制程管控a. 产品确认b.流程确认c. 组合确认d.尺寸确认e. 位置确认f. 程序确认g.刀具确认h.坐标确认i. 方向确认.5. 常见不良表现即原因断针 a.钻机操作不当b.钻头存有问题c.进刀太快等毛边 a.盖板,垫板不正确b. 钻孔条件不对c. 静电吸附等等7. 良好的钻孔质量a. 操作人员;技术能力,责任心,熟练程度b. 钻针;材质,形状,钻数,钻尖c. 压板;垫板;材质,厚度,导热性d. 钻孔机;震动,位置精度,夹力,辅助性能e. 钻孔参数;分次/单次加工方法,转数,进刀退刀速.f. 加工环境;外力震h. 动,噪音,温度,湿度P.T.H站1.PTH原理及作用PTH即在不外加电流的情况下,通过镀液的自催化(钯和铜原子作为催化剂)氧化还原反应,使铜离子析镀在经过活化处理的孔壁及铜箔表面上的过程,也称为化学镀铜或自催化镀铜,化学反应方程式:2.PHT流程及各步作用整孔→水洗→微蚀→水洗→酸洗→水洗→水洗→预浸→活化→水洗→速化→水洗→水洗→化学铜→水洗.a. 整孔;清洁板面,将孔壁的负电荷极化为政电荷,已利与带负电荷的钯胶体粘附.b. 微蚀;清洁板面;粗化铜箔表面,以增加镀层的附着性.c. 酸洗;清洁板面;除去氧化层,杂质.d. 预浸;防止对活化槽的污染.e. 活化;使钯胶体附着在孔壁.f. 速化;将Pd离子还原成Pd原子,使化学铜能锡镀上去。
FPCB生产不良看板分析

误冲孔
冲孔偏移
M/K
不良种类
印 刷 不 良
不良图例
M/K印刷缺失
M/K印刷溅落
M/K印刷蔓延
不良说明
1、目前我社最主要的 印刷为“M/K印刷”、 “S/M印刷”、“PSR 印刷”,三种印刷有 各自的作用,不良种 类也有各自的特点。 2、“M/K印刷”的不 良类似我们刷房常见 的不良,有的地方没 刷到、有的地方刷多 了、油墨太稀等。 3、检验员在检验产品 印刷状况时,需要仔 细确认检验标准书上 产品的印刷状态,与 实物对比检验。 4、产品上的生产周期、 产品号、客户标示, 就是“M/K印刷”。
过腐蚀
不良种类
NG
未腐蚀
未 腐 蚀
OK
合格
不良图例
不良说明
1、未腐蚀不良,恰好 与过腐蚀不良相反、 是由于制品在经过 “现象腐蚀”工序过 程中,由于药液浓度 过低或者传动轴太快 或者喷淋器喷淋不顺 畅导致。 2、请查看左边图 “1”,即为未腐蚀现 象,每根线路的两边 均有突出,类似一个 “底座”,两根线路 之间的距离也较短。 而图“2”的产品是合 格产品,每根线路间 的距离均有适当的缝 隙。 3、大家多看看实物, 就会更深刻的了解了。
不良种类
不良图例
漏冲孔
GUIDE
重眼
不良
不良说明
1、“GUIDE”不良, 特指“GUIDE”工序 造成的不良, “GUIDE”工序是为 了后续工序的定位, 而进行的冲孔工程, 这个工序的常见不良 有漏冲孔、重眼、误 冲孔、冲孔偏移等。 2、“漏冲”、“偏移” 等冲孔不良容易造成 裁切歪斜、印刷歪斜、 粘贴歪斜等连带不良。
不良种类
不良图例
粘
贴
剂
保强板缺失
FPC板面常见的缺陷及解决办法

1.FP C柔性线路板线条间或单根线条侧面显影后产生气泡主要原由:两根或多根线条间起气泡主假如因为线条间距过窄且线条过高,网印时使阻焊料没法印到基材上,以致阻焊料与基材间有空气或潮气存在,在固化和曝光时气体受热产生膨胀惹起单根线条主假如因为线条过高惹起,在刮刀与线条接触时,线条过高,刮刀与线条间的角度增大,使阻焊料没法印到线条根部,使线条根部侧面与阻焊层间有气体存在,受热后产生气泡。
解决方法:网印时应目检网印料能否完整印到基材及线条侧壁,电镀时严格控制电流。
2.FP C柔性线路板孔里有阻焊和图形有针孔主要原由: FPC柔性线路板在网印时没有实时印纸,造成网版聚积剩余油墨过多,在刮刀压力下把剩余油墨印入孔内,还有丝网目数太低,也会造成孔里阻焊。
照相底版上有污物造成 FPC柔性线路板在曝光过程中应见光的部分没有见光,造成图形有针孔。
解决方法:实时印纸和采用高网目的丝网制版;曝光过程中常常检查照相底版的洁净度。
3.FP C柔性线路板阻焊层下铜箔线条上有发黑的迹象主要原由: FPC柔性线路板在擦板后水未烘干,印阻焊前印制板表面被液体溅过或是用手模过。
解决方法:网印时目检印制板两面铜箔能否有氧化现象。
4.FP C柔性线路板表面有污物和不平均主要原由:表面有污物是空气中的飞毛等杂物造成的,表面不平均是因为在网印时没有注意实时印纸,消除网版的剩余油墨,造成表面不平均现象。
解决方法:干净间要充足保证操作者的洁净度,防止没关人员穿行干净间,按期打扫干净间,在网印时实时印纸消除网版的剩余油墨。
5. FP C柔性线路板有重影和龟裂的现象主要原由:重影是因为在网印时 FPC柔性线路板定位不牢和网版上的残墨没有实时去掉聚积到印制板上造成整个FP C焊盘旁边有规律的墨点存在,龟裂是因为在 FPC曝光过程中,曝光量不足,造成板面有渺小裂纹。
解决方法:用定位销固定坚固和实时印纸去掉网版上的残墨;测曝光量使曝光灯能量,曝光时间等参数综合值达到9~11 级曝光级数之间,在这个范围内就不会出现龟裂。
FPC常见不良

开料:裁剪是FPC原材料制作的首站,其品质问题对其后影响较大,而且也是成本的一个控制点,由于裁剪机械程度较高,对机械性能和保养尤为重要,且要求裁剪设备精度基本可以达到所裁剪的精度,所以在对操作员操作技术熟练程度及责任心特别要求。
1、开料前要注意检查:1>、取出来的材料型号是否与MI是否一致2>、确保材料在生产日期之内3>、检查材料对否因为存储环境导致变质2、产品常见不良及预防:未数不足、压痕、折痕、板翘、氧化、幅宽。
1>、未数不足:裁切公差引起,手工操作引起。
2>、压痕:材料本身,操作引起(裁切机转动引起)。
3>、折痕:卷曲包装材料与管轴连接处,材料的接点,操作引起(裁切机转动引起)。
4>、板翘:卷曲包装材料的管轴偏小(77mm可换成152mm),冷藏的材料(Coverlay)。
冰箱里取出后回温四小时后亦会自然平整,过分干燥亦会引起材料翘板。
5>、氧化:材料的氧化主要与保存环境的湿度和保存时间有关。
6>、幅宽:产生材料的幅宽误差是与材料的分切设备有关。
3、控制不良方法:上述大部分不良都与员工操作有关,即认为因素。
针对此,采取以下解决方法。
1>、操作者应带手套和指套,防止铜箔表面因接触手上的汗渍等氧化。
2>、正确的架料方式,防止邹折。
3>、不可裁偏,手对裁时不可破坏冲制定位孔和测试孔。
如无特殊说明时裁剪公差为单面板为±1mm ,双面板为±0.3mm。
4>、裁剪尺寸时不能有较大误差,而且要注意其垂直性,即裁剪为张时四边应为垂直(<2°)。
5>、材料品质,材料表面不可有皱折、污点、重氧化现象,所裁切材料不可有毛边、溢胶等。
6>、机械保养:严格按照<自动裁剪机保养检查纪录表>之执行。
钻孔:有时为了让一般的线路板符合客户的要求,常常要钻出不同用途的孔,例如,测试孔、定位孔、导通孔(双面板、多面板)、零件孔、识别孔等。
FPC常见不良及预防PPT文档31页

31、只有永远躺在泥坑里的人,才不会再掉进坑里。——黑格尔 32、希望的灯一旦熄灭,生活刹那间变成了一片黑暗。——普列姆昌德 33、希望是人生的乳母。——科策布 34、形成天才的决定因素应该是勤奋。——郭沫若 35、学到很多东西的诀窍,就是一下子不要学很多。——洛克
FPC常见不良及预防
16、自己选择的路、跪着也要把它走 完。 17、一般情况下)不想三年以后的事, 只想现 在的事 。现在 有成就 ,以后 才能更 辉煌。
18、敢于向黑暗宣战的人,心里必须 充满光 明。 19、学习的关键--重复。
20、懦弱的人只会裹足不前,莽撞的 人只能 引为烧 身,只 有真正
fpc各种问题及改善方法

fpc各种问题及改善方法一、FPC软性电路板简介以俱挠性之基材制成之印刷电路板具有体积小重量轻可做3D 立体组装及动态挠曲等优。
1.1. 基本材料1.1.1. 铜箔基材COPPER CLAD LAMINATE由铜箔+胶+基材组合而成亦有无胶基材亦即仅铜箔+基材其价格较高在目前应用上较少除非特殊需求。
1.1.2. 铜箔Copper Foil在材料上区分为压延铜(ROLLED ANNEAL Copper Foil)及电解铜(ELECTRO DEPOSITED Copper Foil)两种在特性上来说压延铜之机械特性较佳有挠折性要求时大部分均选用压延铜厚度上则区分为1/2oz (0.7mil) 1oz 2oz 等三种一般均使用1oz。
.1.1.3: 基材Substrate在材料上区分为PI (Polymide ) Film 及PET (Polyester) Pilm 两种PI 之价格较高但其耐燃性较佳PET 价格较低但不耐热因此若有焊接需求时大部分均选用PI 材质厚度上则区分为1mil 2mil 两种。
1.1.3: FPC原物料種類FPC即軟性印刷電路板(Flexible Printed Circuit)的簡稱,由具可撓性質的絕緣層及銅箔為基礎原料組合而成。
FPC應用普遍存在於電子產品中,尤其在手機和LCD顯示器的應用成長性最高。
FPC原物料特性影響FPC的性質表現,FPC原物料的供應則影響FPC的產能,FPC所使用的原材料可以區分為樹脂、銅箔、接著劑、表面護膜(Coverlay)、軟性銅箔基板(FCCL)等,由於PI 在延展性、CTE值、耐熱能力等物理性質較優異,是較常應用的樹脂材料。
FPC和原材料的關係為:由銅箔和PI可以先製成軟性銅箔基板(FCCL),再由FCCL、覆蓋膜(Coverlay,一種PI製成)、補強板、防靜電層等材料製作FPC(如圖一所示)。
1.1.4 FPC原物料簡介1.1.4.1. PIPI對於FPC的功用,除用作FCCL製作過程中的中間層(接著層)和基材外,亦是FPC製作最後加上覆蓋膜(Coverlay)的材料。
FPC常见的问题分析及解决办法

1.FPC的材料:FPC主要由4部分组成:铜箔基板(Copper Film)、保护胶片(Cover Film)、补强胶片(PI Stiffener Film)、接着剂胶片(Adhesive Sheet)。
涉及到的具体材料如下:铜箔(copper):基本分成电解铜与压延铜两种(手机FPC一般常用压延铜箔)。
厚度上常见的为1oz与1/2oz(1/2oz铜厚度=0.7 mil=0.018mm。
)。
基板胶片(base film):常用材料为PI(聚酰亚胺)。
常见的厚度有1mil与1/2mil两种。
接着剂:厚度依客户要求而決定,一般为0.5mil环氧树脂热固胶。
保护胶片:表面绝缘用。
常用材料为PI(聚酰亚胺)。
常见的厚度有1mil与1/2mil。
补强胶片:补强FPC的机械强度,方便表面实装作业。
常见的厚度有5mil与9mil。
离形纸:避免接着剂在压着前沾附异物,便于穴作业。
补强材料:常用是PI(屏蔽层内补强),FR4(屏蔽层内补强),钢片。
层与层之间的胶:1mil环氧树脂热固胶。
注:1mil=1/1000in=0.025mm。
mil也称为毫英寸,密耳(千分之一英寸)。
1mm=40mil。
所有,每层单面板的厚度大概为:0.5mil保护胶片+0.5mil热固胶+1/2oz铜箔+0.5mil热固胶+0.5mil基板=2.7mil=0.0675mm。
2.FPC的结构:FPC有单面、双面和多层板之分。
双面、多层印制线路板的表层和内层导体通过金属化实现内外层电路的电气连接。
一般我们所指的单面板是只有一层铜箔,但其实它一共有5层(包括胶带,不算补强板),双面板9层(常规)。
而一般的双面板是中间一层base film,两边有两层copper。
以下两图分别为FPC单面板断面图和双面板断面图:———————————————————————————————————————从图中我们也可以看出,单面板有5层,双面板有9层。
3.FPC的连接方式及测试:FPC的连接方式主要有插接与焊接两种。
FPC制程中常见不良因素

FPC制程中常见不良因素在FPC(柔性印刷电路)制程中,常见的不良因素包括以下几个方面:1. 材料问题:材料是FPC制程的基础,而使用劣质或不合格的材料会直接影响到产品质量。
例如,基材的厚度不均匀、柔韧度不够或表面有缺陷等都会导致制程中的不良。
2. 印刷问题:印刷是FPC制程中的一个重要步骤,而不良的印刷会直接影响到导线的连接和绝缘层的性能。
常见的印刷问题包括图形失真、线宽不一致、线间距不符合要求等。
3. 焊接问题:焊接是FPC制程中连接电子元件的关键步骤,而不良的焊接会导致电子元件与FPC之间的连接不牢固,甚至出现接触不良或短路等问题。
常见的焊接问题有焊点不完整、焊接温度不稳定或焊盘设计不良等。
4. 切割问题:在FPC制程中,切割是将制成好的FPC板切割成需要的尺寸的步骤。
然而,不良的切割会导致切割边缘不平整、切割过深或切割过浅等问题,影响到产品的外观和实用性。
5. 测试问题:最后一个环节是对FPC产品进行测试,以确保其质量符合要求。
不良的测试会导致缺陷产品进入市场,给消费者带来损失。
常见的测试问题包括测试设备故障、测试程序不完善或测试指标不准确等。
综上所述,FPC制程中的不良因素主要包括材料问题、印刷问题、焊接问题、切割问题和测试问题。
在FPC制程中,为了确保产品质量和性能,必须对这些不良因素进行有效的预防和控制。
延续上述所说的FPC制程中常见不良因素,以下是关于每个因素的详细解释和有效控制措施:1. 材料问题:在FPC制程中,选择高质量的基材和覆盖层材料至关重要。
首先,基材的厚度应均匀,以确保整个FPC板的弯曲性和柔韧性一致。
其次,基材表面应无异物、凹凸或损伤,以防止材料在制程中的破裂或损坏。
另外,覆盖层材料的粘附性和耐磨性也必须符合要求,以确保FPC板的绝缘和保护功能。
要解决材料问题,厂商应严格选择和采购合格的材料,并确保供应商提供的材料符合相关标准和要求。
2. 印刷问题:在FPC制程中,印刷是将导线层印在基材表面的关键步骤。
FPC不良因素

FPC不良因素钻孔(CNC)CNC是整个FPC流程的第一站,其品质对后续程序有很大影响.CNC基本流程:组板→打PIN→钻孔→退PIN.A.产品常见不良:扯胶,尺寸涨缩.1.扯胶:A.胶粘剂性能(胶粘剂的软化点是60-90℃),B.叠层数量(正常9张),受到的阻力,转速,孔径(⊙为3),钻孔条件(设备,垫板,进刀数,退刀数)(进刀数0.6M/分钟,转速7.5万/分钟,退刀数25M/分钟,切片后150℃烘烤1小时).2.尺寸涨缩:材料切片后150℃烘烤1小时钻孔,正常标准为0.1%的尺寸涨缩,一般情况下MD方向会收缩,TD方向会膨胀.B. 生产工艺要求选择盖板→组板→胶带粘合→打箭头(记号)1.基本组板要求:单面板 15张单一铜 10张或15张双面板 10张单一铜 10张或15张黄色Coverlay 10张或15张白色Coverlay 25张辅强板根据情况3-6张2.盖板主要作用:a.减少进孔性毛头.b.防止钻机和压力脚在材料面上造成的压伤.c.使钻尖中心容易定位避免钻孔位置的偏斜.d.带走钻头与孔壁摩擦产生的热量,减少钻头的扭断.3.钻针管制办法a.使用次数管制.b.新钻头之辨识方法.c.新钻头之检验方法.4.品质管控要点a.依据钻片及钻孔资料确认产品孔位与孔数的正确性,并检查断针,验视钻孔是否完全导通.b.外观品质不可有翘铜,毛边之不良现象.5.生产制程管控要点a.产品确认b.流程确认c.组合确认d.尺寸确认e.位置确认f.程序确认g.刀具确认h.坐标确认i.方向确认.6. 生产中操作常见不良表现和原因a.断针:①钻机操作不当,②钻头存有问题,③进刀太快等b.毛边:①盖板,垫板不正确,②钻孔条件不对,③静电吸附等等7. 影响到钻孔品质的主要原因:a. 操作人员;技术能力,责任心,熟练程度b. 钻针;材质,形状,钻数,钻尖c. 压板;垫板;材质,厚度,导热性d. 钻孔机;震动,位置精度,夹力,辅助性能e. 钻孔参数;分次/单次加工方法,转数,进刀退刀速.f. 加工环境;外力震动,噪音,温度,湿度裁切裁剪是FPC原材料制作的首站,其品质问题对其后影响较大,而且也是成本的一个控制点,由于裁剪机械程度较高,对机械性能和保养尤为重要.且要求裁剪设备精度基本可以达到所裁剪物的精度,所以在对操作员操作技术熟练程度及责任心特别要求.A.产品常见不良:未数不足,压痕,摺痕,板翘,氧化,幅宽.1.未数不足:裁切公差引起,手工操作引起.2.压痕:材料本身,操作引起(裁切机转动引起).3.摺痕:卷曲包装材料与管轴连接处,材料的接点, 操作引起(裁切机转动引起).4.板翘: 卷曲包装材料的管轴偏小(77mm可换成152mm),冷藏的材料(Coverlay)冰箱里取出后回温四小时后亦会自然平整,过分干燥亦会引起材料翘板.5.氧化:材料的氧化主要与保存环境的湿度和保存时间有关.6.幅宽:产生材料的幅宽误差是与材料的分切设备.B. 认识原材料的编码:如铜箔类别;厂商代码;层别;单双面板;绝缘层类别;无绝缘层类别绝缘层厚度;绝缘层与铜片间有无粘着剂;铜皮厚度;铜皮处理;宽度码.C.生产工艺要求:1.操作者应带手套和指套,防止铜箔表面因接触手上之汗渍等氧化.2.正确的架料方式,防止邹折.3.不可裁偏,手对裁时不可破坏冲制定位孔和测试孔.如无特殊说明时裁剪公差为单面板为±1mm 双面板为±0.3mm4.裁剪尺寸时不能有较大误差,而且要注意其垂直性,即裁剪为张时四边应为垂直(<2°)5.材料品质,材料表面不可有皱折,污点,重氧化现象,所裁切材料不可有毛边,溢胶等.6.机械保养:严格按照<自动裁剪机保养检查纪录表>之执行.二.磨刷研磨是FPC制程中可能被多次利用的一个辅助制程,作为其它制程的预处理或后处理工序,一般先对板子进行酸洗,微蚀或抗氧化处理,然后利用尼龙轮刷对板子的表面进行刷磨以除去板子表面的杂质,黑化层,残胶等。
FPC各制程的不良原因分析及管制重点

FPC各制程的不良原因分析及管制重点各制程的制作要点自动裁剪裁剪是整个FPC源材料制作的首站,其质量问题对后其影响较大,而且是成本的一个控制点,由于裁剪机械程度较高,对机械性能和保养大为重要.而且裁剪机设备精度基本可以达到所裁剪物的精度要求,所以在对操作员操作技术及熟练程度和责任心提高为重点.1. 原材料编码的认识如; B 08 N N 0 0 R 1 B 250B铜箔类 08:厂商代码 1N层别,N,铜片S,单面板D,双面板 2N绝缘层类别 N.无绝缘层类别K.kapthon P.polyster 10 绝缘层厚度 0,无 1:1mil 2:2mil 20绝缘层与铜片间有无粘着剂 0;无 1;有R,铜皮类别 A:铝箔H:高延展性电解铜R:压延铜E:电解铜 1,铜皮厚度 B,铜皮处理 R:棕化G:normal 250,宽度码Coverlay编码原则2. 制程质量控制根据首件A.操作者应带手套和指套,防止铜箔表面因接触手上之汗渍等氧化.B.正确的架料方式,防止邹折.C.不可裁偏,手对裁时不可破坏冲制定位孔和测试孔.如无特殊说明裁剪公差为张裁时在±1mm 条D.裁时在0.3mm内E.裁剪尺寸时不能有较大误差,而且要注意其垂直性,即裁剪为张时四边应为垂直(<2°)G.材料质量,材料表面不可有皱折,污点,重氧化现象,所裁切材料不可有毛边,溢胶等.3. 机械保养严格按照<自动裁剪机保养检查纪录表>之执行.CNC:CNC是整个FPC流程的第一站,其质量对后续程序有很大影响.CNC基本流程:组板→打PIN→钻孔→退PIN.1. 组板选择盖板→组板→胶带粘合→打箭头(记号)基本组板要求:单面板 15张单一铜 10张或15张双面板 10张单一铜 10张或15张黄色Coverlay 10张或15张白色Coverlay 25张辅强板根据情况3-6张盖板主要作用:A:减少进孔性毛头B:防止钻机和压力脚在材料面上造成的压伤.C:使钻尖中心容易定位避免钻孔位置的偏斜D:带走钻头与孔壁摩擦产生的热量.减少钻头的扭断.2. 钻针管制办法a. 使用次数管制b. 新钻头之辨识方法c. 新钻头之检验方法3. 品质管控点a. 正确性;依据对b. 钻片及钻孔数据确认产品孔位与c. 孔数的正确性,并check断针监视孔是否完全导通.d. 外观质量;不e. 可有翘铜,毛边之不f. 良现象.4. 制程管控a. 产品确认b.流程确认c. 组合确认d.尺寸确认e. 位置确认f. 程序确认g.刀具确认h.坐标确认i. 方向确认.5. 常见不良表现即原因断针 a.钻机操作不当 b.钻头存有问题c.进刀太快等毛边 a.盖板,垫板不正确 b. 钻孔条件不对 c. 静电吸附等等7. 良好的钻孔质量a. 操作人员;技术能力,责任心,熟练程度b. 钻针;材质,形状,钻数,钻尖c. 压板;垫板;材质,厚度,导热性d. 钻孔机;震动,位置精度,夹力,辅助性能e. 钻孔参数;分次/单次加工方法,转数,进刀退刀速.f. 加工环境;外力震h. 动,噪音,温度,湿度相关连接;我司28日,机种F5149-001-CO1 由于程序的使用误用,造成钻孔’’不良’’2700张,虽然两公司都有工作上的疏忽,但对于我司的质量要求,故也要对程序要有个相对完善的管理方案.P.T.H站1.PTH原理及作用PTH即在不外加电流的情况下,通过镀液的自催化(钯和铜原子作为催化剂)氧化还原反应,使铜离子析镀在经过活化处理的孔壁及铜箔表面上的过程,也称为化学镀铜或自催化镀铜,化学反应方程式:2.PHT流程及各步作用整孔→水洗→微蚀→水洗→酸洗→水洗→水洗→预浸→活化→水洗→速化→水洗→水洗→化学铜→水洗.a. 整孔;清洁板面,将孔壁的负电荷极化为政电荷,已利与带负电荷的钯胶体粘附.b. 微蚀;清洁板面;粗化铜箔表面,以增加镀层的附着性.c. 酸洗;清洁板面;除去氧化层,杂质.d. 预浸;防止对活化槽的污染.e. 活化;使钯胶体附着在孔壁.f. 速化;将Pd离子还原成Pd原子,使化学铜能锡镀上去。
FPC板面常见的缺陷及解决办法

1. FP C柔性线路板线条间或单根线条侧面显影后产生气泡主要原因:两根或多根线条间起气泡主要是由于线条间距过窄且线条过高,网印时使阻焊料无法印到基材上,致使阻焊料与基材间有空气或潮气存在,在固化和曝光时气体受热产生膨胀引起单根线条主要是由于线条过高引起,在刮刀与线条接触时,线条过高,刮刀与线条间的角度增大,使阻焊料无法印到线条根部,使线条根部侧面与阻焊层间有气体存在,受热后产生气泡。
解决方法:网印时应目检网印料是否完全印到基材及线条侧壁,电镀时严格控制电流。
2. FP C柔性线路板孔里有阻焊和图形有针孔主要原因:FP C柔性线路板在网印时没有及时印纸,造成网版堆积残余油墨过多,在刮刀压力下把残余油墨印入孔内,还有丝网目数太低,也会造成孔里阻焊。
照相底版上有污物造成FP C柔性线路板在曝光过程中应见光的部分没有见光,造成图形有针孔。
解决方法:及时印纸和选用高网目的丝网制版;曝光过程中经常检查照相底版的清洁度。
3. FP C柔性线路板阻焊层下铜箔线条上有发黑的迹象主要原因:FP C柔性线路板在擦板后水未烘干,印阻焊前印制板表面被液体溅过或是用手模过。
解决方法:网印时目检印制板两面铜箔是否有氧化现象。
4. FP C柔性线路板表面有污物和不均匀主要原因:表面有污物是空气中的飞毛等杂物造成的,表面不均匀是因为在网印时没有注意及时印纸,清除网版的残余油墨,造成表面不均匀现象。
解决方法:洁净间要充分保证操作者的清洁度,避免无关人员穿行洁净间,定期打扫洁净间,在网印时及时印纸清除网版的残余油墨。
5. FP C柔性线路板有重影和龟裂的现象主要原因:重影是因为在网印时FP C柔性线路板定位不牢和网版上的残墨没有及时去掉堆积到印制板上造成整个 FP C焊盘旁边有规律的墨点存在,龟裂是由于在FP C曝光过程中,曝光量不足,造成板面有细小裂纹。
解决方法:用定位销固定牢固和及时印纸去掉网版上的残墨;测曝光量使曝光灯能量,曝光时间等参数综合值达到9 ~11级曝光级数之间,在这个范围内就不会出现龟裂。
FPC制程中常见不良因素
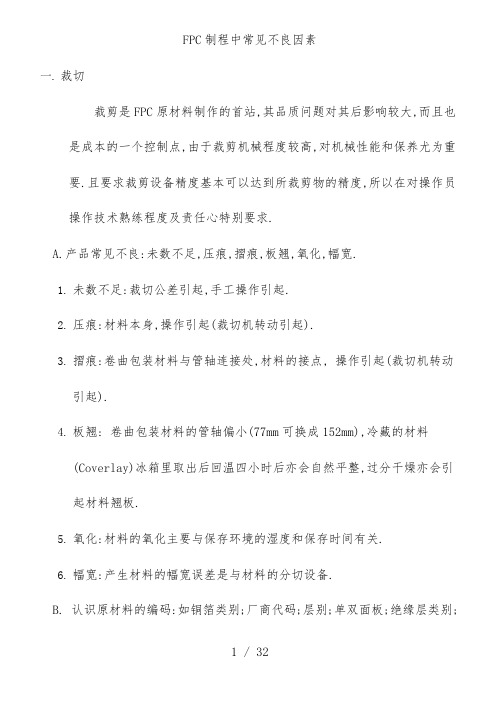
FPC制程中常见不良因素一. 裁切裁剪是FPC原材料制作的首站,其品质问题对其后影响较大,而且也是成本的一个控制点,由于裁剪机械程度较高,对机械性能和保养尤为重要.且要求裁剪设备精度基本可以达到所裁剪物的精度,所以在对操作员操作技术熟练程度及责任心特别要求.A.产品常见不良:未数不足,压痕,摺痕,板翘,氧化,幅宽.1.未数不足:裁切公差引起,手工操作引起.2.压痕:材料本身,操作引起(裁切机转动引起).3.摺痕:卷曲包装材料与管轴连接处,材料的接点, 操作引起(裁切机转动引起).4.板翘: 卷曲包装材料的管轴偏小(77mm可换成152mm),冷藏的材料(Coverlay)冰箱里取出后回温四小时后亦会自然平整,过分干燥亦会引起材料翘板.5.氧化:材料的氧化主要与保存环境的湿度和保存时间有关.6.幅宽:产生材料的幅宽误差是与材料的分切设备.B. 认识原材料的编码:如铜箔类别;厂商代码;层别;单双面板;绝缘层类别;无绝缘层类别绝缘层厚度;绝缘层与铜片间有无粘着剂;铜皮厚度;铜皮处理;宽度码.C.生产工艺要求:1.操作者应带手套和指套,防止铜箔表面因接触手上之汗渍等氧化.2.正确的架料方式,防止邹折.3.不可裁偏,手对裁时不可破坏冲制定位孔和测试孔.如无特殊说明时裁剪公差为单面板为±1mm 双面板为±0.3mm4.裁剪尺寸时不能有较大误差,而且要注意其垂直性,即裁剪为张时四边应为垂直(<2°)5.材料品质,材料表面不可有皱折,污点,重氧化现象,所裁切材料不可有毛边,溢胶等.6.机械保养:严格按照<自动裁剪机保养检查纪录表>之执行.二. 钻孔(CNC)CNC是整个FPC流程的第一站,其品质对后续程序有很大影响.CNC基本流程:组板→打PIN→钻孔→退PIN.A.产品常见不良:扯胶,尺寸涨缩.1.扯胶:A.胶粘剂性能(胶粘剂的软化点是60-90℃),B.叠层数量(正常9张),受到的阻力,转速,孔径(⊙为3),钻孔条件(设备,垫板,进刀数,退刀数)(进刀数0.6M/分钟,转速7.5万/分钟,退刀数25M/分钟,切片后150℃烘烤1小时).2.尺寸涨缩:材料切片后150℃烘烤1小时钻孔,正常标准为0.1%的尺寸涨缩,一般情况下MD方向会收缩,TD方向会膨胀.B. 生产工艺要求选择盖板→组板→胶带粘合→打箭头(记号)1.基本组板要求:单面板 15张单一铜 10张或15张双面板 10张单一铜 10张或15张黄色Coverlay 10张或15张白色Coverlay 25张辅强板根据情况3-6张2.盖板主要作用:a.减少进孔性毛头.b.防止钻机和压力脚在材料面上造成的压伤.c.使钻尖中心容易定位避免钻孔位置的偏斜.d.带走钻头与孔壁摩擦产生的热量,减少钻头的扭断.3.钻针管制办法a.使用次数管制.b.新钻头之辨识方法.c.新钻头之检验方法.4.品质管控要点a.依据钻片及钻孔资料确认产品孔位与孔数的正确性,并检查断针,验视钻孔是否完全导通.b.外观品质不可有翘铜,毛边之不良现象.5.生产制程管控要点a.产品确认b.流程确认c.组合确认d.尺寸确认e.位置确认f.程序确认g.刀具确认h.坐标确认i.方向确认.6. 生产中操作常见不良表现和原因a.断针 :①钻机操作不当,②钻头存有问题,③进刀太快等b.毛边 :①盖板,垫板不正确,②钻孔条件不对,③静电吸附等等7. 影响到钻孔品质的主要原因:a. 操作人员;技术能力,责任心,熟练程度b. 钻针;材质,形状,钻数,钻尖c. 压板;垫板;材质,厚度,导热性d. 钻孔机;震动,位置精度,夹力,辅助性能e. 钻孔参数;分次/单次加工方法,转数,进刀退刀速.f. 加工环境;外力震动,噪音,温度,湿度三. 磨刷研磨是FPC制程中可能被多次利用的一个辅助制程,作为其它制程的预处理或后处理工序,一般先对板子进行酸洗,微蚀或抗氧化处理,然后利用尼龙轮刷对板子的表面进行刷磨以除去板子表面的杂质,黑化层,残胶等。
fpc常见不良

1.作业 时要保持 底片和板 子的清 洁;
2.底片 与板子应 对准,正 确;
3.不可 有气泡, 杂质;放 片时要注 意将孔露 出。
4.双面 板作业时 应垫黑纸 以防止曝 光。
B.品质 确认:
底片的 规格,露 光机的曝 光能量, 底片与干 膜的紧贴 度都会影 响线路的 精密度。
1.准确 性
B.PTH 流程及各 步作用
整孔→ 水洗→微 蚀→水洗 →酸洗→ 水洗→水 洗→预浸 →活化→ 水洗→速 化→水洗 →水洗→ 化学铜→ 水洗. 1.整孔; 清洁板 面,将孔 壁的负电 荷极化为 政电荷, 已利与带 负电荷的 钯胶体粘 附.
2.微蚀; 清洁板 面;粗化 铜箔表 面,以增 加镀层的 附3.着酸性洗.; 清洁板 面;除去 氧化层, 杂4.质预.浸; 防止对活 化槽的污 染5..活化; 使钯胶体 附着在孔 壁6..速化; 将Pd离 子还原成 Pd原 子,使化 学铜能锡 镀上去。 7.化学 铜:通过 化学反应 使铜沉积 于孔壁和 铜箔表面 。
0.3mm
4.裁剪尺 寸时不能 有较大误 差,而且 要注意其 垂直性, 即裁剪为 张时四边 应为垂直
(5<.材2°料) 品 质,材料 表面不可 有皱折, 污点,重 氧化现 象,所裁 切材料不 可有毛 边,溢胶 6.机械保 养:严格 按照<自 动裁剪机 保养检查 纪录表> 之执行.
钻孔
(CNC) CNC是 整个FPC 流程的第 一站,其 品质对后 续程序有 很大影 响.CNC 基本流 程:组板 →打PIN →钻孔→ 退A.P产IN品. 常见不 良:扯胶, 尺寸涨 缩.
B. 认识 原材料的 编码:如 铜箔类 别;厂商 代码;层 别;单双 面板;绝 缘层类 别;无绝 缘层类别 绝缘层厚 度;绝缘 层与铜片 间有无粘 着剂;铜 皮厚度; 铜皮处
FPC常见不良

开料:裁剪是FPC原材料制作的首站,其品质问题对其后影响较大,而且也是成本的一个控制点,由于裁剪机械程度较高,对机械性能和保养尤为重要,且要求裁剪设备精度基本可以达到所裁剪的精度,所以在对操作员操作技术熟练程度及责任心特别要求。
1、开料前要注意检查:1>、取出来的材料型号是否与MI是否一致2>、确保材料在生产日期之内3>、检查材料对否因为存储环境导致变质2、产品常见不良及预防:未数不足、压痕、折痕、板翘、氧化、幅宽。
1>、未数不足:裁切公差引起,手工操作引起。
2>、压痕:材料本身,操作引起(裁切机转动引起)。
3>、折痕:卷曲包装材料与管轴连接处,材料的接点,操作引起(裁切机转动引起)。
4>、板翘:卷曲包装材料的管轴偏小(77mm可换成152mm),冷藏的材料(Coverlay)。
冰箱里取出后回温四小时后亦会自然平整,过分干燥亦会引起材料翘板。
5>、氧化:材料的氧化主要与保存环境的湿度和保存时间有关。
6>、幅宽:产生材料的幅宽误差是与材料的分切设备有关。
3、控制不良方法:上述大部分不良都与员工操作有关,即认为因素。
针对此,采取以下解决方法。
1>、操作者应带手套和指套,防止铜箔表面因接触手上的汗渍等氧化。
2>、正确的架料方式,防止邹折。
3>、不可裁偏,手对裁时不可破坏冲制定位孔和测试孔。
如无特殊说明时裁剪公差为单面板为±1mm ,双面板为±0.3mm。
4>、裁剪尺寸时不能有较大误差,而且要注意其垂直性,即裁剪为张时四边应为垂直(<2°)。
5>、材料品质,材料表面不可有皱折、污点、重氧化现象,所裁切材料不可有毛边、溢胶等。
6>、机械保养:严格按照<自动裁剪机保养检查纪录表>之执行。
钻孔:有时为了让一般的线路板符合客户的要求,常常要钻出不同用途的孔,例如,测试孔、定位孔、导通孔(双面板、多面板)、零件孔、识别孔等。
FPC制程中常见不良因素
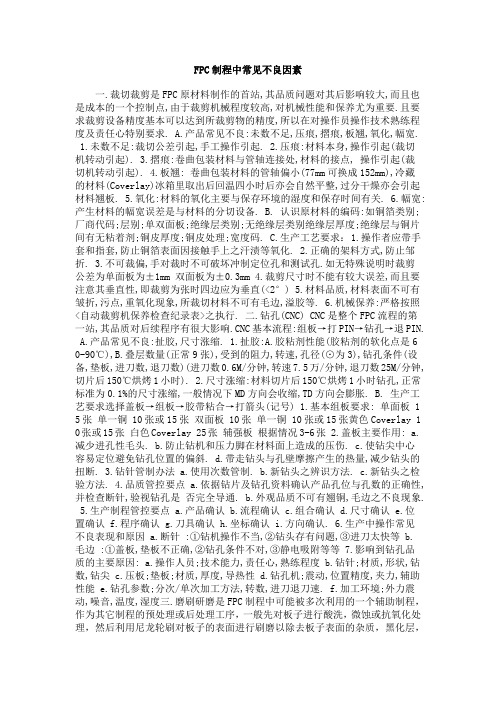
FPC制程中常见不良因素一.裁切裁剪是FPC原材料制作的首站,其品质问题对其后影响较大,而且也是成本的一个控制点,由于裁剪机械程度较高,对机械性能和保养尤为重要.且要求裁剪设备精度基本可以达到所裁剪物的精度,所以在对操作员操作技术熟练程度及责任心特别要求. A.产品常见不良:未数不足,压痕,摺痕,板翘,氧化,幅宽.1.未数不足:裁切公差引起,手工操作引起.2.压痕:材料本身,操作引起(裁切机转动引起).3.摺痕:卷曲包装材料与管轴连接处,材料的接点, 操作引起(裁切机转动引起).4.板翘: 卷曲包装材料的管轴偏小(77mm可换成152mm),冷藏的材料(Coverlay)冰箱里取出后回温四小时后亦会自然平整,过分干燥亦会引起材料翘板.5.氧化:材料的氧化主要与保存环境的湿度和保存时间有关.6.幅宽:产生材料的幅宽误差是与材料的分切设备. B. 认识原材料的编码:如铜箔类别;厂商代码;层别;单双面板;绝缘层类别;无绝缘层类别绝缘层厚度;绝缘层与铜片间有无粘着剂;铜皮厚度;铜皮处理;宽度码. C.生产工艺要求: 1.操作者应带手套和指套,防止铜箔表面因接触手上之汗渍等氧化. 2.正确的架料方式,防止邹折. 3.不可裁偏,手对裁时不可破坏冲制定位孔和测试孔.如无特殊说明时裁剪公差为单面板为±1mm 双面板为±0.3mm 4.裁剪尺寸时不能有较大误差,而且要注意其垂直性,即裁剪为张时四边应为垂直(<2°) 5.材料品质,材料表面不可有皱折,污点,重氧化现象,所裁切材料不可有毛边,溢胶等. 6.机械保养:严格按照<自动裁剪机保养检查纪录表>之执行. 二.钻孔(CNC) CNC是整个FPC流程的第一站,其品质对后续程序有很大影响.CNC基本流程:组板→打PIN→钻孔→退PIN.A.产品常见不良:扯胶,尺寸涨缩. 1.扯胶:A.胶粘剂性能(胶粘剂的软化点是6 0-90℃),B.叠层数量(正常9张),受到的阻力,转速,孔径(⊙为3),钻孔条件(设备,垫板,进刀数,退刀数)(进刀数0.6M/分钟,转速7.5万/分钟,退刀数25M/分钟,切片后150℃烘烤1小时). 2.尺寸涨缩:材料切片后150℃烘烤1小时钻孔,正常标准为0.1%的尺寸涨缩,一般情况下MD方向会收缩,TD方向会膨胀. B. 生产工艺要求选择盖板→组板→胶带粘合→打箭头(记号) 1.基本组板要求: 单面板 1 5张单一铜 10张或15张双面板 10张单一铜 10张或15张黄色Coverlay 1 0张或15张白色Coverlay 25张辅强板根据情况3-6张 2.盖板主要作用: a.减少进孔性毛头. b.防止钻机和压力脚在材料面上造成的压伤. c.使钻尖中心容易定位避免钻孔位置的偏斜. d.带走钻头与孔壁摩擦产生的热量,减少钻头的扭断. 3.钻针管制办法 a.使用次数管制. b.新钻头之辨识方法. c.新钻头之检验方法. 4.品质管控要点 a.依据钻片及钻孔资料确认产品孔位与孔数的正确性,并检查断针,验视钻孔是否完全导通. b.外观品质不可有翘铜,毛边之不良现象.5.生产制程管控要点 a.产品确认 b.流程确认 c.组合确认 d.尺寸确认 e.位置确认 f.程序确认 g.刀具确认 h.坐标确认 i.方向确认.6.生产中操作常见不良表现和原因 a.断针:①钻机操作不当,②钻头存有问题,③进刀太快等 b.毛边:①盖板,垫板不正确,②钻孔条件不对,③静电吸附等等7.影响到钻孔品质的主要原因: a.操作人员;技术能力,责任心,熟练程度 b.钻针;材质,形状,钻数,钻尖 c.压板;垫板;材质,厚度,导热性 d.钻孔机;震动,位置精度,夹力,辅助性能 e.钻孔参数;分次/单次加工方法,转数,进刀退刀速. f.加工环境;外力震动,噪音,温度,湿度三.磨刷研磨是FPC制程中可能被多次利用的一个辅助制程,作为其它制程的预处理或后处理工序,一般先对板子进行酸洗,微蚀或抗氧化处理,然后利用尼龙轮刷对板子的表面进行刷磨以除去板子表面的杂质,黑化层,残胶等。
- 1、下载文档前请自行甄别文档内容的完整性,平台不提供额外的编辑、内容补充、找答案等附加服务。
- 2、"仅部分预览"的文档,不可在线预览部分如存在完整性等问题,可反馈申请退款(可完整预览的文档不适用该条件!)。
- 3、如文档侵犯您的权益,请联系客服反馈,我们会尽快为您处理(人工客服工作时间:9:00-18:30)。
四 溢胶
覆膜或补强 在高温高压 作用下,有 部分胶溢出
FPC
AD胶
补强
五 补强不良
5.1
补强偏位 a:补强贴偏 b:压合机上下 模板压力不均 匀,造成偏位
补强板孔
FPC孔
五 补强不良
5.2
补强剥离
FPC与补 强明显剥 离
a:补强局部缺 胶 b:压合机上下 模板压力不均 匀,造成压不 实现象 c:胶已过期, 与产品的结合 力不足
五 补强不良
5.3
补强异物
a:产品未清洁 干净,有异物 粘在板面上 b:补强上粘有 异物
五 补强不良
5.4
补强内气泡 a:补强局部缺胶 b:压合参数不当 造成补强内气泡的 产生 c:压机上下模板压
力不均匀
6 油墨不良
6.1
油墨脱落
a:油墨过期 b:油墨调配比例不当 c:烘烤不足 导致丝印字符在3M胶 拉力测试中脱落
防止压折伤通则
2 清洁作业规范化
用粘尘滚轮 对产品进行 清洁作业
防止压折伤通则
3 作业台面的清洁
每天用粘尘滚 筒对贴合台面 进行清洁,防 止有异物造成 压伤
防止压折伤通则
4 压合副资材清洁 每天开机生产 前,检查副资 材上有无脏污 和异物 保持副资材的 洁净度
防止压折伤通则
5 物料框保持干净无异物
电检产品的压伤: a:电测治具探 针弹性太大 b:使用找点笔 时,笔头与金面 接触的压力太大 造成焊接面的压 伤
二 折伤
压合副资材老化、 皱折、破损等造 成产品折皱
二 折伤
单手拿板
二 折伤
点数不标准, 造成产品折 伤
防止压折伤通则
防止压折伤通则
1 取放板动作标准化
要双手对角拿 板,做到放板 不拉板,取板 不推板
六 油墨不良
Байду номын сангаас.2
油墨污染
:
印刷中有粘 网现象,造 成油墨污染 板面
七 开、短路不良
7.1 短路(SC)
曝光、蚀刻不 良造成线路与 线路之间相连
7 开、短路不良
7.2 开路(OC)
曝光、蚀刻 不良造成线 路中间断开
:
八 外周不良
良品
冲型模具异 常造成产品 外周偏差
不良品
定期对物料 框进行清洁
防止压折伤通则
6 产品定量叠放
转料时要一个 物料盒放一个 单,严禁一个 盒内放几个单, 防止压伤
防止压折伤通则
7 模具清洁
每冲1PNL 用酒精加无 尘布对上下 模清洁,防 止压伤
全 员 参 与 勿 以 善 小 而 不 为 勿 以 恶 小 而 为 之
三 覆盖膜错位
:
覆盖膜贴偏, 盖住孔环
良率 个人机会
公司获利
公司发展
所以降低不良势在必行
FPC常见不良
一 二 三 四 五 六 七 八
压伤 折伤 覆盖膜错位 溢胶 补强板剥离、错位、异物、气泡、漏贴等 油墨不良 开路 短路 外周不良
一 压伤
有异物粘在 板面,会造 成压伤
副资材上粘有 异物,会造成 压伤
一 压伤