电镀不良原因分析及对策
电镀不良分析报告
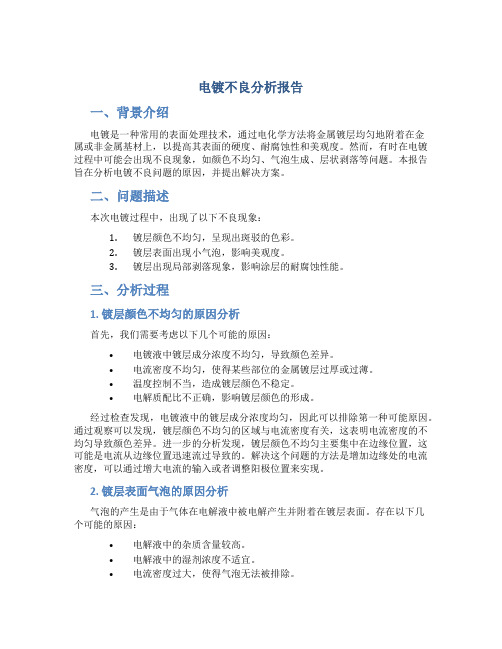
电镀不良分析报告一、背景介绍电镀是一种常用的表面处理技术,通过电化学方法将金属镀层均匀地附着在金属或非金属基材上,以提高其表面的硬度、耐腐蚀性和美观度。
然而,有时在电镀过程中可能会出现不良现象,如颜色不均匀、气泡生成、层状剥落等问题。
本报告旨在分析电镀不良问题的原因,并提出解决方案。
二、问题描述本次电镀过程中,出现了以下不良现象:1.镀层颜色不均匀,呈现出斑驳的色彩。
2.镀层表面出现小气泡,影响美观度。
3.镀层出现局部剥落现象,影响涂层的耐腐蚀性能。
三、分析过程1. 镀层颜色不均匀的原因分析首先,我们需要考虑以下几个可能的原因:•电镀液中镀层成分浓度不均匀,导致颜色差异。
•电流密度不均匀,使得某些部位的金属镀层过厚或过薄。
•温度控制不当,造成镀层颜色不稳定。
•电解质配比不正确,影响镀层颜色的形成。
经过检查发现,电镀液中的镀层成分浓度均匀,因此可以排除第一种可能原因。
通过观察可以发现,镀层颜色不均匀的区域与电流密度有关,这表明电流密度的不均匀导致颜色差异。
进一步的分析发现,镀层颜色不均匀主要集中在边缘位置,这可能是电流从边缘位置迅速流过导致的。
解决这个问题的方法是增加边缘处的电流密度,可以通过增大电流的输入或者调整阳极位置来实现。
2. 镀层表面气泡的原因分析气泡的产生是由于气体在电解液中被电解产生并附着在镀层表面。
存在以下几个可能的原因:•电解液中的杂质含量较高。
•电解液中的湿剂浓度不适宜。
•电流密度过大,使得气泡无法被排除。
经过检测,电解液中的杂质含量符合标准要求,因此第一种可能原因可以排除。
进一步检查发现,电解液中的湿剂浓度偏高,这是导致气泡产生的重要原因。
调整湿剂浓度至合适范围可以解决这个问题。
此外,如果电流密度过大,也会造成气泡无法被排除。
因此,需要对电流密度进行适当的调整,以保证正常的电解过程。
3. 镀层剥落的原因分析镀层的剥落可能是由于以下原因引起:•预处理工艺存在问题,导致基材表面不洁净。
电镀过程中镀层不良的描述、原因及对策

电镀过程中镀层不良的描述、原因及对策1、针孔。
针孔是由于镀件外表吸附着氢气,迟迟不开释。
使镀液无法亲润镀件外表,然后无法电析镀层。
跟着析氢点周围区域镀层厚度的添加,析氢点就构成了一个针孔。
特点是一个发亮的圆孔,有时还有一个向上的小尾巴"。
当镀液中短少湿润剂并且电流密度偏高时,容易构成针孔。
2、麻点。
麻点是由于受镀外表不洁净,有固体物质吸附,或许镀液中固体物质悬浮着,当在电场效果下到达工件外表后,吸附其上,而影响了电析,把这些固体物质嵌入在电镀层中,构成一个个小凸点(麻点)。
特点是上凸,没有发亮现象,没有固定形状。
总归是工件脏、镀液脏而构成。
3、气流条纹。
气流条纹是由于添加剂过量或阴极电流密度过高或络合剂过高而降低了阴极电流效率然后析氢量大。
假如当时镀液流动缓慢,阴极移动缓慢,氢气贴着工件外表上升的进程中影响了电析结晶的摆放,构成自下而上一条条气流条纹。
4、掩镀(露底)。
掩镀是由于是工件外表管脚部位的软性溢料没有除掉,无法在此处进行电析堆积镀层。
电镀后可见基材,故称露底(由于软溢料是半通明的或通明的树脂成份)。
5、镀层脆性。
在SMD电镀后切筋成形后,可见在管脚弯处有开裂现象。
当镍层与基体之间开裂,判定是镍层脆性。
当锡层与镍层之间开裂,判定是锡层脆性。
构成脆性的原因八成是添加剂,光亮剂过量,或许是镀液中无机、有机杂质太多构成。
6、气袋。
气袋的构成是由于工件的形状和积气条件而构成。
氢气积在"袋中"无法排到镀液液面。
氢气的存在阻挠了电析镀层。
使堆集氢气的部位无镀层。
在电镀时,只需留意工件的钩挂方向能够防止气袋现象。
如图示工件电镀时,当垂直于镀槽底钩挂时,不发生气袋。
当平行于槽底钩挂时,易发生气袋。
7、塑封黑体中心开"锡花”。
在黑体上有锡镀层,这是由于电子管在焊线时,金丝的向上抛物形太高,塑封时金丝显露在黑体外表,锡就镀在金丝上,像开了一朵花。
不是镀液问题。
8、"爬锡"。
电镀常见不良问题点分析及对策
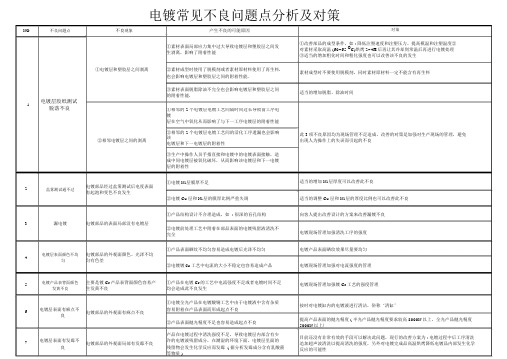
电镀常见不良问题点分析及对策NO.不良问题点不良现象产生不良的可能原因①素材表面局部应力集中过大导致电镀层和塑胶层之间发生剥离,影响了附着性能①电镀层和塑胶层之间剥离②素材成型时使用了脱模剂或者素材原材料使用了再生料.也会影响电镀层和塑胶层之间的附着性能.③素材表面脱脂除油不完全也会影响电镀层和塑胶层之间电镀层胶纸测试的附着性能.1脱落不良①相邻的 2个电镀层电镀工艺间隔时间过长导致前工序电镀层在空气中氧化从而影响了与下一工序电镀层的附着性能②相邻电镀层之间的剥离②相邻的 2个电镀层电镀工艺间的活化工序遗漏也会影响该电镀层和下一电镀层的附着性对策①改善部品的成型条件,如 : 降低注塑速度和注塑压力、提高模温和注塑温度②对素材采取高温 (60~65 O C)烘烤2~4H后再让其冷却到常温后再进行电镀处理③适当的增加粗化时间和粗化强度也可以改善该不良的发生素材成型时不要使用脱模剂,同时素材原材料一定不能含有再生料适当的增加脱脂、除油时间此3项不良原因均为现场管理不足造成,改善的对策是加强对生产现场的管理,避免出现人为操作上的失误而引起的不良2 3 4 5 6 7③生产中操作人员手指直接和电镀中的电镀表面接触,造成中间电镀层被氧化破坏,从而影响该电镀层和下一电镀层的附着性电镀部品经过盐雾测试后电度表面①电镀 Ni层膜厚不足盐雾测试通不过有起泡和变色不良发生②电镀 Cu层和Ni层的膜厚比例严重失调①产品结构设计不合理造成,如 : 很深的盲孔结构漏电镀电镀部品的表面局部没有电镀层②电镀前处理工艺中附着在部品表面的电镀残留液清洗不完全电镀部品的外观面颜色、光泽不均①产品表面晒纹不均匀容易造成电镀后光泽不均匀电镀层表面颜色不均匀匀有色差②电镀镀C u工艺中电流的大小不稳定也容易造成产品电镀产品表背面颜色主要是镀 Cr产品表背面颜色容易产①产品在电镀 Cr的工艺中电流强度不足或者电镀时间不足发黄不良生发黄不良均会造成此不良发生①电镀全光产品在电镀酸铜工艺中由于电镀液中含有杂质电镀层表面有麻点不电镀部品的外观面有麻点不良容易附着在产品表面而形成起点不良良②产品表面抛光精度不足也容易造成起点不良产品在电镀过程中清洗强度不足,导致电镀层内部含有少电镀层表面有发霉不电镀部品的外观面局部有发霉不良许的电镀液残留成分,在潮湿的环境下面,电镀层里面的良残留物会发生化学反应而发霉 ( 据分析发霉成分含有乳酸菌等物质 )适当的增加 Ni层厚度可以改善此不良适当的调整 Cu层和Ni层的厚度比例也可以改善此不良向客人提出改善设计的方案来改善漏镀不良电镀现场管理加强清洗工序的强度电镀产品表面晒纹效果尽量要均匀电镀现场管理加强对电流强度的管理电镀现场管理加强镀 Cr工艺的强度管理按时对电镀缸内的电镀液进行清洁,俗称‘清缸’提高产品表面的抛光精度 ( 半光产品抛光精度要求较高 8000N以上,全光产品抛光精度5000N以上)目前还没有非常有效的手段可以解决此问题,现行的改善方案为 : 电镀过程中后工序清洗追加超声波清洗以提高清洗的强度,另外对电镀完成品高温烘烤降低电镀品内部发生化学反应的可能性。
电镀不良及对策
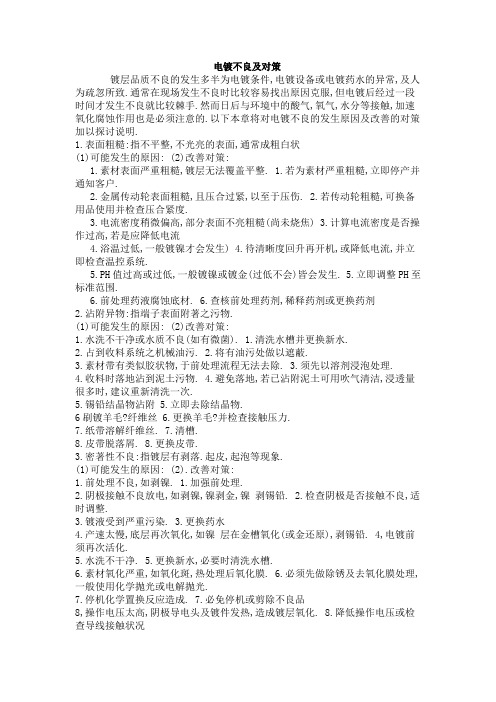
电镀不良及对策镀层品质不良的发生多半为电镀条件,电镀设备或电镀药水的异常,及人为疏忽所致.通常在现场发生不良时比较容易找出原因克服,但电镀后经过一段时间才发生不良就比较棘手.然而日后与环境中的酸气,氧气,水分等接触,加速氧化腐蚀作用也是必须注意的.以下本章将对电镀不良的发生原因及改善的对策加以探讨说明.1.表面粗糙:指不平整,不光亮的表面,通常成粗白状(1)可能发生的原因: (2)改善对策:1.素材表面严重粗糙,镀层无法覆盖平整. 1.若为素材严重粗糙,立即停产并通知客户.2.金属传动轮表面粗糙,且压合过紧,以至于压伤. 2.若传动轮粗糙,可换备用品使用并检查压合紧度.3.电流密度稍微偏高,部分表面不亮粗糙(尚未烧焦) 3.计算电流密度是否操作过高,若是应降低电流4.浴温过低,一般镀镍才会发生) 4.待清晰度回升再开机,或降低电流,并立即检查温控系统.5.PH值过高或过低,一般镀镍或镀金(过低不会)皆会发生. 5.立即调整PH至标准范围.6.前处理药液腐蚀底材. 6.查核前处理药剂,稀释药剂或更换药剂2.沾附异物:指端子表面附著之污物.(1)可能发生的原因: (2)改善对策:1.水洗不干净或水质不良(如有微菌). 1.清洗水槽并更换新水.2.占到收料系统之机械油污. 2.将有油污处做以遮蔽.3.素材带有类似胶状物,于前处理流程无法去除. 3.须先以溶剂浸泡处理.4.收料时落地沾到泥土污物. 4.避免落地,若已沾附泥土可用吹气清洁,浸透量很多时,建议重新清洗一次.5.锡铅结晶物沾附 5.立即去除结晶物.6刷镀羊毛?纤维丝 6.更换羊毛?并检查接触压力.7.纸带溶解纤维丝. 7.清槽.8.皮带脱落屑. 8.更换皮带.3.密著性不良:指镀层有剥落.起皮,起泡等现象.(1)可能发生的原因: (2).改善对策:1.前处理不良,如剥镍. 1.加强前处理.2.阴极接触不良放电,如剥镍,镍剥金,镍剥锡铅. 2.检查阴极是否接触不良,适时调整.3.镀液受到严重污染. 3.更换药水4.产速太慢,底层再次氧化,如镍层在金槽氧化(或金还原),剥锡铅. 4,电镀前须再次活化.5.水洗不干净. 5.更换新水,必要时清洗水槽.6.素材氧化严重,如氧化斑,热处理后氧化膜. 6.必须先做除锈及去氧化膜处理,一般使用化学抛光或电解抛光.7.停机化学置换反应造成. 7.必免停机或剪除不良品8,操作电压太高,阴极导电头及镀件发热,造成镀层氧化. 8.降低操作电压或检查导线接触状况9,底层电镀不良(如烧焦),造成下一层剥落. 9.改善底层电镀品质.10.严重.烧焦所形成剥落 10.参考NO12处理对策.4.露铜:可清楚看见铜色或黄黑色于低电流处(凹槽处)(1)可能发生原因: (2)改善对策:1.前处理不良,油脂,氧化物.异物尚未除去,镀层无法析出. 1.加强前处理或降低产速2.操作电流密度太低,导致低电流区,镀层无法析出. 2.重新计算电镀条件.3镍光泽剂过量,导致低电流区,镀层无法析出 3.处理药水,去除过多光泽剂或更新.4.严重刮伤造成露铜. 4.检查电镀流程,(查参考NO5)5.未镀到. 5.调整电流位置.5刮伤:指水平线条状,一般在锡铅镀层比较容易发生.(1)可能发生的原因: (2)改善对策:1.素材本身在冲压时,及造成刮伤. 1.停止生产,待与客户联系.2.被电镀设备中的金属制具刮伤,如阴极头,烤箱定位器,导轮等. 2.检查电镀流程,适时调整设备和制具.3.被电镀结晶物刮伤. 3.停止生产,立即去除结晶物.6.变形(刮歪):指端子形状已经偏离原有尺寸或位置.(1)可能发生的原因: (2)改善对策:1.素材本身在冲压时,或运输时,即造成变形. 1.停止生产,待与客户联系.2.被电镀设备,制具刮歪(如吹气.定位器,振荡器,槽口,回转轮) 2.检查电镀流程,适时调整设备和制具.3.盘子过小或卷绕不良,导致出入料时刮歪 3.停止生产,适时调整盘子4.传动轮转歪, 4.修正传动轮或变更传动方式.7壓傷:指不規則形狀之凹洞可能發生的原因:改善對策:1)本身在沖床加工時,已經壓傷,鍍層無法覆蓋平整2)傳動輪松動或故障不良,造成壓合時傷到 1)停止生産,待與客戶聯2)檢查傳動機構,或更換備品8白霧:指鍍層表面卡一層雲霧狀,不光亮但平整可能發生的原因:1)前處理不良2)鍍液受污染3)錫鉛層愛到酸腐蝕,如停機時受到錫鉛液腐蝕4)錫鉛藥水溫度過高5)錫鉛電流密度過低6)光澤劑不足7)傳致力輪髒污8)錫鉛電久進,産生泡沫附著造成改善對策:1)加強前處理2)更換藥水並提純污染液3)避免停機,若無法避免時,剪除不良4)立即檢查溫控系統,並重新設定溫度5)提高電流密度6)補足不澤劑傳動輪7)清潔傳動輪8)立即去除泡沫9針孔:指成群、細小圓洞狀(似被鍾紮狀)可能發生的原因:改善對策:1.操作的電流密度太 1.降低電流密度2.电镀溶液表面张力过大,湿润剂不足。
电镀加工出现问题的原因及解决办法
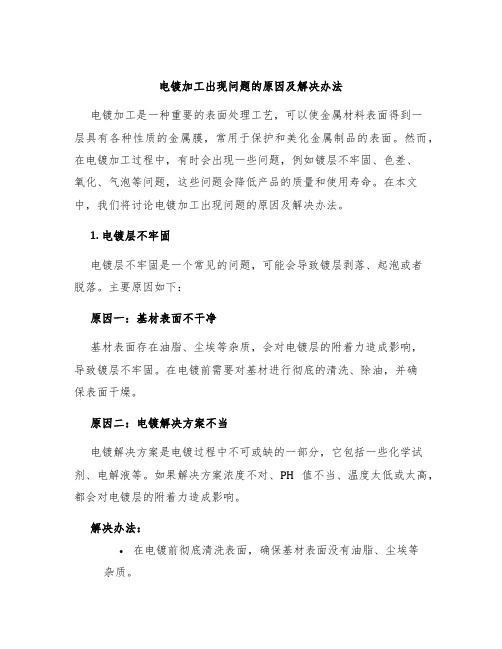
电镀加工出现问题的原因及解决办法电镀加工是一种重要的表面处理工艺,可以使金属材料表面得到一层具有各种性质的金属膜,常用于保护和美化金属制品的表面。
然而,在电镀加工过程中,有时会出现一些问题,例如镀层不牢固、色差、氧化、气泡等问题,这些问题会降低产品的质量和使用寿命。
在本文中,我们将讨论电镀加工出现问题的原因及解决办法。
1. 电镀层不牢固电镀层不牢固是一个常见的问题,可能会导致镀层剥落、起泡或者脱落。
主要原因如下:原因一:基材表面不干净基材表面存在油脂、尘埃等杂质,会对电镀层的附着力造成影响,导致镀层不牢固。
在电镀前需要对基材进行彻底的清洗、除油,并确保表面干燥。
原因二:电镀解决方案不当电镀解决方案是电镀过程中不可或缺的一部分,它包括一些化学试剂、电解液等。
如果解决方案浓度不对、PH值不当、温度太低或太高,都会对电镀层的附着力造成影响。
解决办法:•在电镀前彻底清洗表面,确保基材表面没有油脂、尘埃等杂质。
•在电镀解决方案中,加入一些添加剂,例如促进剂、增容剂等,来增强电镀层的附着力。
2. 镀层色差在电镀过程中,有时会出现镀层色差的问题,主要原因如下:原因一:电解液浓度不均电解液浓度的不均匀会导致镀层颜色不均匀。
例如,电解液中某些添加剂如果浓度过高或者过低,都可能导致镀层颜色的不同。
原因二:镀层表面存在缺陷镀层表面存在气泡、孔洞等缺陷也会导致镀层颜色不均匀。
解决办法:•定期检查电解液浓度,确保其均匀。
•彻底清洗基材的表面,确保表面无污染和缺陷。
3. 氧化问题氧化是电镀过程中另一个常见的问题,可以影响镀层的附着力和外观。
主要原因如下:原因一:电解液中的氧化物电解液中含有氧化物,而这些氧化物经常与电解液中的金属离子发生反应,从而导致镀层表面氧化。
原因二:镀层表面缺氧缺乏足够的电解气体氧分子也会导致金属离子表面氧化。
解决办法:•检查电解液中氧化物的含量,并确定其是否应该加入或减少。
•向电解液中添加抗氧化剂。
电镀常见的问题及解决方案

电镀常见的问题及解决方案
电镀过程中可能出现的问题及其解决方案如下:
1.针孔或麻点:这是由于前处理不良、有金属杂质、硼酸含量太少、镀液温度太低等原因造成的。
可以使用润湿剂来减小影响,并严格控制镀液维护及流程。
2.结合力低:如果铜镀层未经活化去氧化层,铜和镍之间的附着力就差,会产生镀层剥落现象。
因此,在电镀前应对基材进行适当的预处理,如酸洗、活化等。
3.镀层脆、可焊性差:这通常是由于有机物或重金属物质污染造成的。
添加剂过多会使镀层中夹带的有机物和分解产物增多,此时可以用活性炭处理或电解等方法除去重金属杂质。
4.镀层发暗和色泽不均匀:有金属污染可能是造成这一问题的原因。
应尽量减少挂具所沾的铜溶液,并在发现污染时立即处理。
5.镀层烧伤:这可能是由于硼酸不足、金属盐的浓度低、工作温度太低、电流密度太高、PH值太高或搅拌不充分等原因造成的。
需要检查并调整相关工艺参数,确保其处于合适的范围。
6.沉积速率低:PH值低或电流密度低都可能导致沉积速率低。
应检查并调整镀液的PH值和电流密度,以优化沉积速率。
7.其他问题:如辅助阳极的铜条未与生产板长度一致或已发粗,不允许再使用。
全板及图形镀后板需在24小时内制作下工序。
图形镀上板戴细纱手套,下板戴棕胶手套,全板上板戴橡胶手套,下板戴干燥的粗纱手套。
在处理电镀问题时,需要综合考虑多个因素,包括镀液成分、设备状况、操作条件等。
如遇到难以解决的问题,建议寻求专业人士的帮助。
金属电镀出现不良现象的原因与解决方法
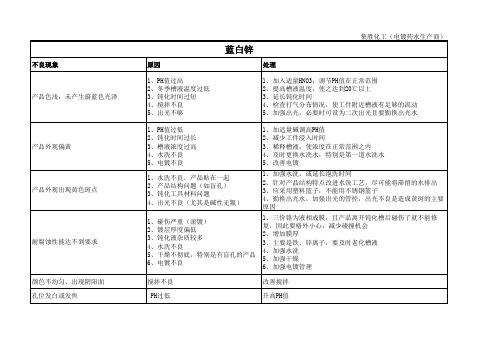
钝化外观偏浅(呈蓝带黄或金黄)
孔位颜色过深
钝化外观不均
耐腐蚀性能达不到要求
孔位周围发白
孔位颜色过深,呈现焦黄色
钝化后工件发花(呈地图纹状)
1、pH值过高 2、药液杂质过多 3、槽液浓度偏低 ①PH值过高 ②时间过短 ③Cr3+浓度低
1、调整pH值 2、排去1/5旧槽液,重新以原液补充添加 3、补加A01-435DC ①加入适量硝酸 ②延长钝化时间 ③ 加入适量原液 ①加入硝酸 ②排污,补充建浴液 ③加强搅拌 ①加碱升高PH值
产品颜色过浅,呈金黄色而不是五彩
①PH值过高 颜色不均匀,产品出现花斑(地图状花纹) ②或杂质太多 ③槽液循环搅拌不良 孔位发白、工件边缘泛紫光 ①PH值过低
黑锌
不良现象 原因 1、PH值过低 2、槽液中铁离子过高 3、槽液温度过高 4、钝化时间过短 5、B剂浓度不足 6、电镀外观过于光亮 1、pH值偏低 2、温度偏高 3、钝化时间过短 4、搅拌不足 1、pH值偏低 2、钝化时间过长 3、槽液温度偏高 处理 1、校正酸度计,调整PH值至操作范围 2、更新部份槽液或重新建浴 3、降低槽液温度 4、延长钝化时间 5、适当补充B剂 6、调整电镀 1、调高pH值至操作范围 2、降低温度 3、适当延长钝化时间 4、增强搅拌 1、调高pH值至操作范围 2、缩短钝化时间 3、降低温度
1)镀液中锌离子浓度应维持在10~15g/L 2)保持槽液温度20~30℃ 3)见A项第2点 4)控制氢氧化钠浓度在100~150g/L保持氢氧化钠与锌离子浓 度之比在10~12之间。 1)分析调整。控制锌离子浓度在10~15g/L,氢氧化钠浓度与 锌离子的比值10~12为宜。 2)适量补加A02-350A光剂。 3)降低电流密度。 4)保持槽液温度20~30℃。 1)分析调整,控制锌离子浓度在10~15g/L,氢氧化钠浓度与 锌离子的比值10~12为宜。 2)根据霍尔槽试片,适量补加A02-350B光剂。 3)提高电流密度。 1)在工艺允许使用范围内提高锌离子浓度。 2)根据霍尔槽试片,适量补加A02-350A光剂。 3)加净化剂C或软水剂D。 4)加强前处理。 适当增加A02-350B用量;在过滤机加入锌粉及助滤剂硅藻土以除 杂
电镀不良之原因与对策
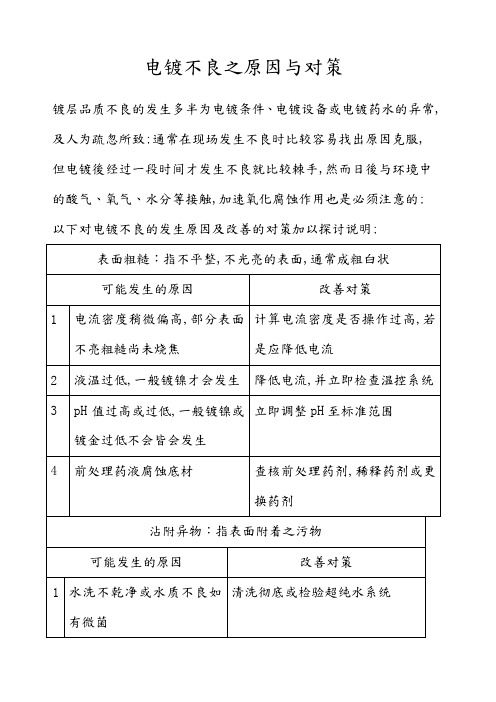
电镀不良之原因与对策镀层品质不良的发生多半为电镀条件、电镀设备或电镀药水的异常,及人为疏忽所致;通常在现场发生不良时比较容易找出原因克服,但电镀後经过一段时间才发生不良就比较棘手,然而日後与环境中的酸气、氧气、水分等接触,加速氧化腐蚀作用也是必须注意的;以下对电镀不良的发生原因及改善的对策加以探讨说明;镀层检验在电镀业界的镀层检验,一般包括外观检查、膜厚测试、附着能力测试、抗腐蚀能力测试、抗老化能力测试等;1.外观检查:一般厂家在检查外观比较多使用目视法,较严格则会使用4倍或10倍放大镜检查在许多国际标准规范也是如此,如ASTM;建议作业人员先用目视法检查,一旦看到有疑虑的外观时,再使用放大镜观察;而技术人员则建议必须以50~100倍来检查倍数越高,外观瑕疵越多,甚至分析原因时还得借助200倍以上的显微镜;在电镀层的外观判定标准,一般并无一定的规范,都需要由买卖双方协议;当然表面完全没有瑕疵最好,但这是高难度,不过一般人们对色泽均匀这个定义比较能达成共识,因此汇整以下经常发生的一些外观异常,供参考:1色泽不均,深浅色,异色如变黑,发红,发黄,白雾等2光泽度不均匀,明亮度不一,暗淡粗糙3沾附异物如水分,毛屑,土灰,油污,结晶物,纤维等4不平滑,有凹洞,针孔,颗粒物等5压伤,刮伤,磨痕,刮歪等各种变形现象及镀件受损情形6电镀位置不齐,不足,过多,过宽等7裸露底层金属现象8有起泡,剥落,掉金属屑等2.膜厚测试:镀层膜厚测试方法有显微镜测试法、电解测试法、X 光萤光测试法、β射线测试法、涡流测试法、滴下测试法等;其中以显微镜测试法最为正确,不过需要时间、设备、技术等支援,不适合检验用,一般用来做分析研究之用;现在大部分都使用X光萤光测试法,因为准确度高,速度快几十秒;目前业界使用X-RAY萤光膜厚仪的厂牌有德国的FISCHE R、美国的CM I、日本的SEIKO,其测试原理与方法大同小异,但由於厂牌不同,多少会有少许误差,只要使用标准片作好检量线,作好定位工作,作好底材修正,即可将误差降低到最小;3.附着能力测试:或称为密着性测试,方法有弯曲法、胶带法、急冷法、切割法、滚压法等;弯曲法比较胶带法严格,有很多场合胶带法是无法测试镀层的附着力;若使用胶带法必须注意一定要使用与Scotch cellophane tape 同等粘性胶带赛路凡胶,否则会失去测试效果;4.抗腐蚀能力测试:下表为常用的腐蚀试验方法;说明:√为适用,×为不适用1硝酸蒸汽腐蚀实验是测试厚金25μm以上镀层的封孔能力,硝酸浓度为70±1%,温度23±3℃,湿度60%,时间为60分钟;实验後镀层表面不可有深蓝色,黑色腐蚀点及镀层破裂;2二氧化硫蒸汽腐蚀实验是测试厚金及钯镍镀层的封孔能力,根据AT&T钯镍实验时间为30分钟,根据ASTM厚金30μm以上实验时间为23±1小时;实验後镀层表面不可有深蓝色,黑色腐蚀点及镀层破裂;3盐水喷雾实验是测试薄金、镀镍层的封孔能力,氯化钠浓度为5%,实验温度为35℃,实验时间有24小时,48小时,72小时等;实验後镀层表面不可有绿色,白色腐蚀点;4硫化氢蒸汽腐蚀实验是测试金镀层的封孔能力,实验时间为 2小时,实验後镀层表面不可有绿色,白色腐蚀点;5水蒸气老化实验是测试金镀层的封孔能力,实验时间为8小时、16小时;实验後镀层表面不可有白色腐蚀点;水蒸气老化实验是利用沸腾的纯水来蒸烤镀层 ,实验时间为8小时和16小时;目前业界使用最多为盐水喷雾实验和水蒸气老化实验;5.抗老化能力实验:目前做老化实验用途,除了观察表面是否变色,是否有腐蚀斑点外;镀层外观检验范例一、目的:在规范电镀成品外观检验的方法和判定的标准二、检验仪器:1. 肉眼;2. 20倍放大镜;三.检验步骤:1.取样品放在深色背景下,用标准白色光源以垂直方向照射;2.在45度方向距样品一定的目视距离检查3.若在目视下无法判定外观不良属何种不良现象时,可以20倍放大镜观察了解;四.判定方法:1色泽均匀,不可有深浅色,异色如变黑,发红,发黄,白雾等的现象; 2光泽度均匀,不可有明亮度不一,暗淡粗糙的现象;3不可沾有任何异物如毛屑,土灰,油污,结晶物,纤维等;4平滑性好,不可有凹洞,颗粒物等;5不可有压伤,刮伤,磨痕等各种变形现象及镀件受损情形;6电镀位置不可有不齐,不足,过多,过宽等现象;7不可有裸露底层金属现象;8镀层不可有起泡,剥落等密着不良情形;9必须乾燥,不可沾有水分;密着能力实验范例1.折弯实验法:以~4.0mm的折弯器或相当於试样厚度的弯曲半径,将试样弯曲至90度以上,在以50倍放大镜观察弯曲部分的外表面,若无剥离,起皮等现象,即判定为合格;2.胶带试验法:使用Scotch cellophane tape 或其他同等粘性的胶带贴试样表面,粘贴後以垂直方向迅速撕开,并以目视观察胶带上有无剥离金属,若无任何镀层剥离现象,即判定为合格;3.急冷试验法:将试样在规定温度下,加热30分钟,然後急速冷却於水中室温後烘乾,以50倍放大镜观察,若无起泡,剥离等现象,即判定为合格; 4.绕折试验法:以1mm圆棒对试样做360度绕折四圈以上,绕折的速度,力量需一致,在以50倍放大镜观察,若无剥离,起皮等现象,即判定为合格;。
电镀加工出现问题的原因及解决办法

电镀加工出现问题的原因及解决办法对于电子设备厂家来说,在进行电子加工活动的时候,电镀加工处理是少不的,电镀加工处理工艺中可能消失各种问题,给生产带来不便.电镀加工不平整是一个常见问题,下面来了解一下它消失的缘由:1、电镀件毛坯表面过于粗糙或不好。
过于粗糙的表面要各到优质的沉积电镀层相对更困难,特殊是一些压铸不良的产品就不能得到合格的电镀层。
一些素材表面的缺陷在电镀之前不能发觉与修复,良品率相对低些。
2、电镀加工工艺不合理或电镀时间不够。
比如塑料电镀在镀铜的时间太短电流太小,铜件电镀直上镍电镀时镀光亮镍的时间短或电流太小。
3、电镀液性能差,整平性能不好。
如光亮硫酸铜所用的材料杂质多,组成成分含量不对,所使用的光亮剂质量不好,都不能有良好的填平性能。
4、电镀件在前处理部分不良,如五金电镀件镀底铜或底镍层不良或有附着有机膜层等。
另外还会消失电镀加工渗漏的问题,无锡华友微电子有限公司在该行业已有15年的历史,已形成了肯定规模,具备肯定的加工力量,并拥有丰富的阅历,下面它给我们解析下如何防止苏州电镀加工活动中的渗漏问题。
1、严防镀液加温过高。
当镀液加温过高时,镀液会加速蒸发和分解,气雾中含有高浓度的溶质成分。
这时会严峻污染环境,尤其是酸、碱气雾,氰化物和铬雾对环境的影响和人体危害会更大。
2、严格防止镀液被排风机吸走。
当电镀加工中,排风机配备不当,镀液液位过高,这时镀液简单被吸走,在槽盖未启开之前尤为严峻,既引起环境污染,又会造成镀液损耗,消失这种状况时要准时实行措施予以解决,如降低镀液液位,调整吸风口宽度等。
3、防止镀槽、加温(冷却)管渗漏造成污染。
电镀槽或加温(冷却)管渗漏往往会造成严峻污染,其渗漏缘由随制造材料及不同镀种各有区分。
电镀件常见不良原因分析
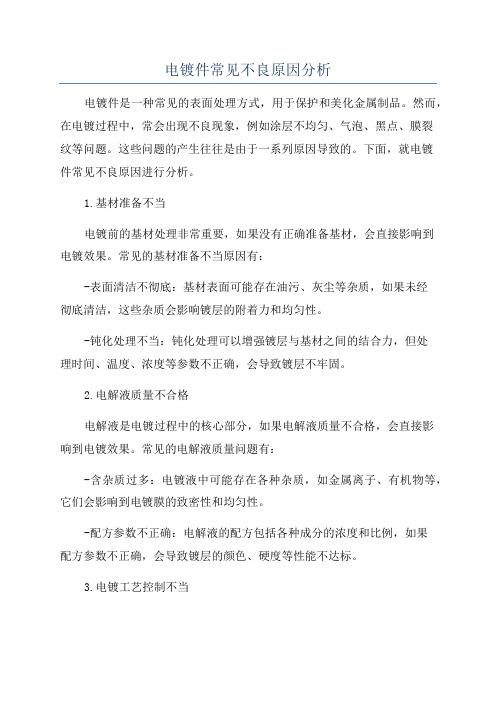
电镀件常见不良原因分析电镀件是一种常见的表面处理方式,用于保护和美化金属制品。
然而,在电镀过程中,常会出现不良现象,例如涂层不均匀、气泡、黑点、膜裂纹等问题。
这些问题的产生往往是由于一系列原因导致的。
下面,就电镀件常见不良原因进行分析。
1.基材准备不当电镀前的基材处理非常重要,如果没有正确准备基材,会直接影响到电镀效果。
常见的基材准备不当原因有:-表面清洁不彻底:基材表面可能存在油污、灰尘等杂质,如果未经彻底清洁,这些杂质会影响镀层的附着力和均匀性。
-钝化处理不当:钝化处理可以增强镀层与基材之间的结合力,但处理时间、温度、浓度等参数不正确,会导致镀层不牢固。
2.电解液质量不合格电解液是电镀过程中的核心部分,如果电解液质量不合格,会直接影响到电镀效果。
常见的电解液质量问题有:-含杂质过多:电镀液中可能存在各种杂质,如金属离子、有机物等,它们会影响到电镀膜的致密性和均匀性。
-配方参数不正确:电解液的配方包括各种成分的浓度和比例,如果配方参数不正确,会导致镀层的颜色、硬度等性能不达标。
3.电镀工艺控制不当电镀工艺过程中的各个环节都需要精确控制,否则会产生不良现象。
常见的电镀工艺控制不当原因有:-电流密度不均匀:电镀过程中,电流密度分布不均匀会导致镀层厚度不均匀,甚至出现孔洞等问题。
-温度控制不准确:电镀过程中的温度控制对于镀层的质量和均匀性非常重要,如果温度控制不准确,会影响到电解液的反应速率和镀层的结构。
4.设备维护不当电镀设备的维护工作也是保证电镀质量的关键。
常见的设备维护不当原因有:-阴极和阳极污染:设备内部的阴极和阳极可能会受到电解液的腐蚀,长期使用后会产生污染物,需要定期清洗和更换。
-设备参数不稳定:设备的电流、温度、电压等参数需保持稳定,如果设备参数不稳定,会导致镀层质量下降。
综上所述,电镀件常见的不良现象往往由基材准备不当、电解液质量不合格、电镀工艺控制不当和设备维护不当等原因导致。
为确保电镀质量,操作人员应遵循正确的工艺流程,提高工作细致性和耐心性,严格控制每个环节的参数和条件,以及定期维护设备,确保设备的正常运行。
电镀不良之原因与对策

電鍍没有良之本果與對策之阳早格格创做鍍層品質没有良的發死多数為電鍍條件、電鍍設備大概電鍍藥火的異常,及人為大意所致.常常正在現場發死没有良時比較简单找出本果克服,但是電鍍後經過一段時間才發死没有良便比較棘脚,然而日後與環境中的酸氣、氧氣、火分等交觸,加速氧化腐蝕效率也是必須注意的.以下對電鍍没有良的發死本果及革新的對策加以探討說明.鍍層檢驗正在電鍍業界的鍍層檢驗,普遍包罗中觀檢查、膜薄測試、附著本领測試、抗腐蝕本领測試、抗老化本领測試等.1.中觀檢查:普遍廠家正在檢查中觀比較多使用目視法,較嚴格則會使用4倍大概10倍搁大鏡檢查(正在許多國際標準規範也是如许,如ASTM).建議做業人員先用目視法檢查,一朝瞅到有疑慮的中觀時,再使用搁大鏡觀察.而技術人員則建議必須以50~100倍來檢查(倍數越下,中觀瑕疵越多),以至分解本果時還得借帮200倍以上的顯微鏡.正在電鍍層的中觀判决標準,普遍並無一定的規範,皆需要由買賣雙圆協議.當然表面实足沒有瑕疵最佳,但是這是下難度,没有過普遍人們對色澤均勻這個定義比較能達成共識,果此匯整以下經常發死的一些中觀異常,供參考:(1)色澤没有均,深淺色,異色(如變乌,發紅,發黃,黑霧等)(2)光澤度没有均勻,明明度纷歧,昏暗细糙(3)沾附異物(如火分,毛屑,土灰,油污,結晶物,纖維等)(4)没有服滑,有凸洞,針孔,顆粒物等(5)壓傷,刮傷,磨痕,刮正等各種變形現象及鍍件受損情形(6)電鍍位子没有齊,缺累,過多,過寬等(7)裸露底層金屬現象(8)有起泡,剝降,掉金屬屑等2.膜薄測試:鍍層膜薄測試要领有顯微鏡測試法、電解測試法、X光螢光測試法、β射線測試法、渦流測試法、滴下測試法等.其中以顯微鏡測試法最為正確,没有過需要時間、設備、技術等收援,没有適合檢驗用,普遍用來干分解钻研之用.現正在大部分皆使用X光螢光測試法,果為準確度下,速度快(幾十秒).暂时業界使用XRAY螢光膜薄儀的廠牌有德國的FISCHER、好國的CMI、日本的SEIKO,其測試本理與要领大共小異,但是由於廠牌分歧,几會有少許誤好,只消使用標準片做佳檢量線,做佳定位处事,做佳底材建正,即可將誤好降矮到最小.3.附著本领測試:大概稱為稀著性測試,要领有彎直法、膠帶法、慢热法、切割法、滾壓法等.彎直法比較膠帶法嚴格,有很多場合膠帶法是無法測試鍍層的附著力.若使用膠帶法必須注意一定要使用與Scotch cellophane tape No.600共等粘性膠帶(賽路凡是膠),可則會得来測試效验.4.抗腐蝕本领測試:下表為时常使用的腐蝕試驗要领.說明:√為適用,×為没有適用(1)硝酸蒸汽腐蝕實驗是測試薄金(25μm以上)鍍層的启孔本领,硝酸濃度為70±1%,溫度23±3℃,濕度60%,時間為60分鐘.實驗後鍍層表面没有成有深藍色,乌色腐蝕點及鍍層破裂. (2)两氧化硫蒸汽腐蝕實驗是測試薄金及鈀鎳鍍層的启孔本领,根據AT&T鈀鎳實驗時間為30分鐘,根據ASTM薄金(30μm以上)實驗時間為23±1小時.實驗後鍍層表面没有成有深藍色,乌色腐蝕點及鍍層破裂.(3)鹽火噴霧實驗是測試薄金、鍍鎳層的启孔本领,氯化鈉濃度為5%,實驗溫度為35℃,實驗時間有24小時,48小時,72小時等.實驗後鍍層表面没有成有綠色,红色腐蝕點.(4)硫化氫蒸汽腐蝕實驗是測試金鍍層的启孔本领,實驗時間為 2小時,實驗後鍍層表面没有成有綠色,红色腐蝕點.(5)火蒸氣老化實驗是測試金鍍層的启孔本领,實驗時間為8小時、16小時.實驗後鍍層表面没有成有红色腐蝕點.火蒸氣老化實驗是利用沸騰的純火來蒸烤鍍層,實驗時間為8小時战16小時.暂时業界使用最多為鹽火噴霧實驗战火蒸氣老化實驗.5.抗老化本领實驗:暂时干老化實驗用途,除了觀察表面是可變色,是可有腐蝕斑點中.鍍層中觀檢驗範例一、脚段:正在規範電鍍废品中觀檢驗的要领战判决的標準两、檢驗儀器:1.肉眼.2.20倍搁大鏡.三.檢驗步驟:1.与樣品搁正在深色背景下,用標準红色光源以笔直目标映照. 3.若正在目視下無法判决中觀没有良屬何種没有良現象時,不妨20倍搁大鏡觀察瞭解.四.判决要领:(1)色澤均勻,没有成有深淺色,異色(如變乌,發紅,發黃,黑霧等)的現象.(2)光澤度均勻,没有成有明明度纷歧,昏暗细糙的現象. (3)没有成沾有所有異物(如毛屑,土灰,油污,結晶物,纖維等).(4)仄滑性佳,没有成有凸洞,顆粒物等.(5)没有成有壓傷,刮傷,磨痕等各種變形現象及鍍件受損情形.(6)電鍍位子没有成有没有齊,缺累,過多,過寬等現象. (7)没有成有裸露底層金屬現象.(8)鍍層没有成有起泡,剝降等稀著没有良情形.(9)必須坤燥,没有成沾有火分.稀著本领實驗範例1.合彎實驗法:以1.2~4.0mm的合彎器大概相當於試樣薄度的彎直半徑,將試樣彎直至90度以上,正在以50倍搁大鏡觀察彎直部分的中表面,若無剝離,起皮等現象,即判决為合格.2.膠帶試驗法:使用Scotch cellophane tape No.600大概其余共等粘性的膠帶貼試樣表面,粘貼後以笔直目标赶快撕開,並以目視觀察膠帶上有無剝離金屬,若無所有鍍層剝離現象,即判决為合格.3.慢热試驗法:將試樣正在規定溫度下,加熱30分鐘,然後缓慢热卻於火中(室溫)後烘坤,以50倍搁大鏡觀察,若無起泡,剝離等現象,即判决為合格.4.繞合試驗法:以1mm圓棒對試樣干360度繞合四圈以上,繞合的速度,力量需普遍,正在以50倍搁大鏡觀察,若無剝離,起皮等現象,即判决為合格.。
电镀中常见的不良原因分析(这些你都能解决了吗)
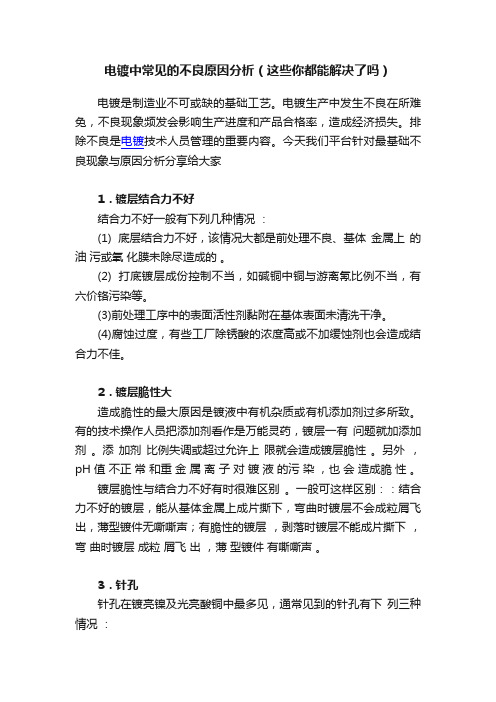
电镀中常见的不良原因分析(这些你都能解决了吗)电镀是制造业不可或缺的基础工艺。
电镀生产中发生不良在所难免,不良现象频发会影响生产进度和产品合格率,造成经济损失。
排除不良是电镀技术人员管理的重要内容。
今天我们平台针对最基础不良现象与原因分析分享给大家1.镀层结合力不好结合力不好一般有下列几种情况:(1) 底层结合力不好,该情况大都是前处理不良、基体金属上的油污或氧化膜未除尽造成的。
(2) 打底镀层成份控制不当,如碱铜中铜与游离氰比例不当,有六价铬污染等。
(3)前处理工序中的表面活性剂黏附在基体表面未清洗干净。
(4)腐蚀过度,有些工厂除锈酸的浓度高或不加缓蚀剂也会造成结合力不佳。
2.镀层脆性大造成脆性的最大原因是镀液中有机杂质或有机添加剂过多所致。
有的技术操作人员把添加剂看作是万能灵药,镀层一有问题就加添加剂。
添加剂比例失调或超过允许上限就会造成镀层脆性。
另外,pH 值不正常和重金属离子对镀液的污染,也会造成脆性。
镀层脆性与结合力不好有时很难区别。
一般可这样区别::结合力不好的镀层,能从基体金属上成片撕下,弯曲时镀层不会成粒屑飞出,薄型镀件无嘶嘶声;有脆性的镀层,剥落时镀层不能成片撕下,弯曲时镀层成粒屑飞出,薄型镀件有嘶嘶声。
3.针孔针孔在镀亮镍及光亮酸铜中最多见,通常见到的针孔有下列三种情况:(1)因析氢造成的针孔是锥形的。
(2)因油污和有机杂质造成的针孔是细密不规则的。
(3)基体金属的小凹点所造成的针孔无规则,如苍蝇脚趾,很难认定,须经试验和观看基体表面才能确定。
4.毛刺与针孔不同,可用湿纸揩擦故障处,如故障表面沾有纸屑的是毛刺,不沾纸屑的是针孔。
造成毛刺的主要原因是固体杂质。
(1)镀件本身带入镀液的固体杂质,如铁屑;先涂漆后电镀时,漆膜腐蚀下来的漆粒。
(2)外界混入或阳极溶解时带入的固体杂质。
建议阳极必须用阳极袋包扎。
5.发花发花主要是有机杂质多,镀液成分、光亮剂及表面活性剂(如十二烷基硫酸钠)等比例失调造成的。
电镀不良之原因分析及防范措施

电镀不良之原因分析及防范措施不良状况1.氧化、生锈可能发生的原因a. 素材表面粗糙,孔粗细度较大,形成电位差,缩短保质期,产生氧化点;b. 端子表面压伤,电镀时形成低电流区,压伤抗氧化能力较低;防范措施a. 素材冲压成型时,须做到表面光滑,不能有压伤伤痕等;b. 规范後处理,落实执行制程稽核。
备注此份为首顾提供C.端子後处理不良,表面残留酸性物。
2.伤痕a. 素材本身在冲床时即造成刮伤、压伤;b. 被电镀设备中金属制具刮伤,如阴极头、烤箱、定位器;C.被电镀结晶物刮伤;d. 传动轮松动故障不良,造成压合时伤到;e. 滚镀铁壳电镀或者运送过程中相互刮伤。
a. 冲压单位修整模具;b. 检查电镀流程,适时调整设备及制具;C.住手生产,即将去除结晶物;d. 检查传动机构,或者更换备品;e. 电镀过程中尽量减少桶量,减少不良。
3.烧焦、变色 a. 电镀电压太高;b. PH 值太高。
a. 依电镀作业条件标准做规范作业;此份为首顾提供b. 由现场专员定稽核PH 值,温4.有异物5.白雾6.水渍a.水洗不乾净;b.沾到收料系统之机械油污;c.素材带有类似胶状物,於处理流程无法去除;d.收料时落地沾到泥土污物;e.锡铅结晶物沾附。
a.前处理不良;b.镀液受污染;c.锡铅镀层受到强酸腐蚀,如停机时受到锡液腐蚀(水洗太脏) ;d.锡铅温度过低(高电流处会发生) ;e.锡铅电流密度达低;f.光泽剂不足。
a. DRY 前吹气不良:1.风嘴位置不当;2.风压及风量不正常。
b.水洗不良度。
a.渍洗水槽并更换新水;b.将有油污处做以遮蔽;c.须先以溶剂浸泡处理;d.避免落地,若已沾附泥土可用吹气清洁,数量不少时,建议重新清洗一次;e.即将去除结晶物。
a.加强前处理;b.更换药水或者去除污染、纯化槽液并找出污染源,彻底解决;c.避免停机,若无法避免时,剪除不良;d.即将检查温控系统,并重新设定温度;e.提高电流密度;f.补足不光泽剂。
电镀不良对策
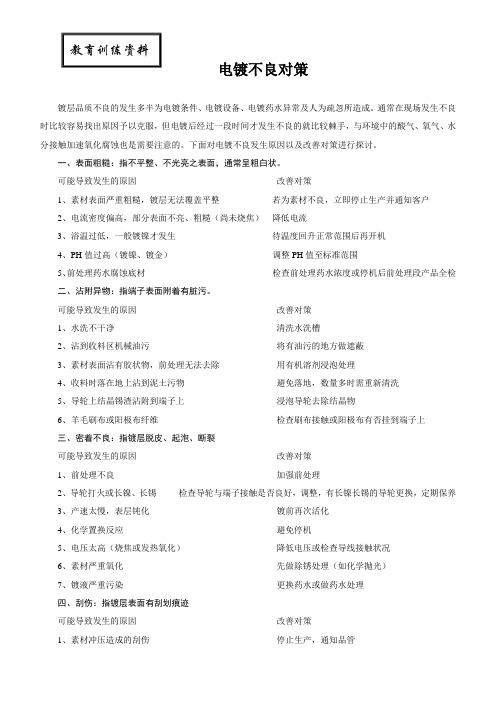
教育训练资料电镀不良对策镀层品质不良的发生多半为电镀条件、电镀设备、电镀药水异常及人为疏忽所造成。
通常在现场发生不良时比较容易找出原因予以克服,但电镀后经过一段时间才发生不良的就比较棘手,与环境中的酸气、氧气、水分接触加速氧化腐蚀也是需要注意的。
下面对电镀不良发生原因以及改善对策进行探讨。
一、表面粗糙:指不平整、不光亮之表面,通常呈粗白状。
可能导致发生的原因改善对策1、素材表面严重粗糙,镀层无法覆盖平整若为素材不良,立即停止生产并通知客户2、电流密度偏高,部分表面不亮、粗糙(尚未烧焦)降低电流3、浴温过低,一般镀镍才发生待温度回升正常范围后再开机4、PH值过高(镀镍、镀金)调整PH值至标准范围5、前处理药水腐蚀底材检查前处理药水浓度或停机后前处理段产品全检二、沾附异物:指端子表面附着有脏污。
可能导致发生的原因改善对策1、水洗不干净清洗水洗槽2、沾到收料区机械油污将有油污的地方做遮蔽3、素材表面沾有胶状物,前处理无法去除用有机溶剂浸泡处理4、收料时落在地上沾到泥土污物避免落地,数量多时需重新清洗5、导轮上结晶锡渣沾附到端子上浸泡导轮去除结晶物6、羊毛刷布或阳极布纤维检查刷布接触或阳极布有否挂到端子上三、密着不良:指镀层脱皮、起泡、断裂可能导致发生的原因改善对策1、前处理不良加强前处理2、导轮打火或长镍、长锡检查导轮与端子接触是否良好,调整,有长镍长锡的导轮更换,定期保养3、产速太慢,表层钝化镀前再次活化4、化学置换反应避免停机5、电压太高(烧焦或发热氧化)降低电压或检查导线接触状况6、素材严重氧化先做除锈处理(如化学抛光)7、镀液严重污染更换药水或做药水处理四、刮伤:指镀层表面有刮划痕迹可能导致发生的原因改善对策1、素材冲压造成的刮伤停止生产,通知品管2、被电镀设备刮伤检查流程,调整治具3、脱脂槽电极打火导致凹洞调整电极五、变形(歪针):指端子形状已经偏离原有尺寸或位置可能导致发生的原因改善对策1、素材在冲压运输中造成变形停止生产,通知品管2、被电镀设备,治具刮歪检查流程,调整治具3、盘子过小或卷绕不良导致出入料时刮歪停止生产,调整盘子4、挤压轮压歪(或打滑)调整挤压方式六、白雾:指镀层表面云雾状,不光亮。
电镀不良之原因分析及防范措施
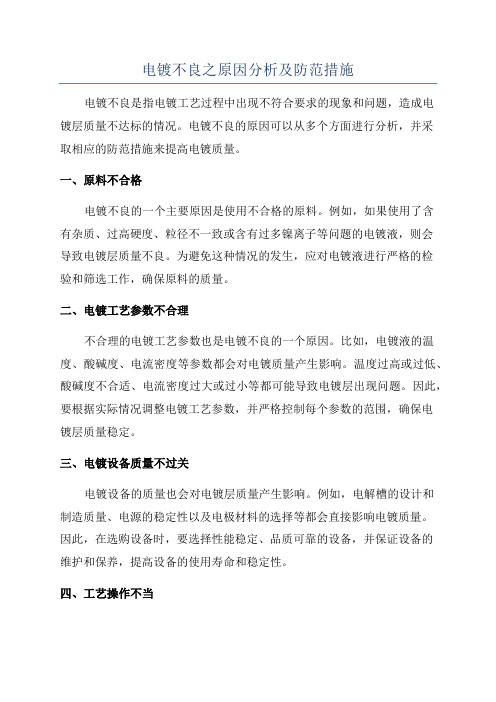
电镀不良之原因分析及防范措施电镀不良是指电镀工艺过程中出现不符合要求的现象和问题,造成电镀层质量不达标的情况。
电镀不良的原因可以从多个方面进行分析,并采取相应的防范措施来提高电镀质量。
一、原料不合格电镀不良的一个主要原因是使用不合格的原料。
例如,如果使用了含有杂质、过高硬度、粒径不一致或含有过多镍离子等问题的电镀液,则会导致电镀层质量不良。
为避免这种情况的发生,应对电镀液进行严格的检验和筛选工作,确保原料的质量。
二、电镀工艺参数不合理不合理的电镀工艺参数也是电镀不良的一个原因。
比如,电镀液的温度、酸碱度、电流密度等参数都会对电镀质量产生影响。
温度过高或过低、酸碱度不合适、电流密度过大或过小等都可能导致电镀层出现问题。
因此,要根据实际情况调整电镀工艺参数,并严格控制每个参数的范围,确保电镀层质量稳定。
三、电镀设备质量不过关电镀设备的质量也会对电镀层质量产生影响。
例如,电解槽的设计和制造质量、电源的稳定性以及电极材料的选择等都会直接影响电镀质量。
因此,在选购设备时,要选择性能稳定、品质可靠的设备,并保证设备的维护和保养,提高设备的使用寿命和稳定性。
四、工艺操作不当不正确的工艺操作也是电镀不良的一个常见原因。
例如,电镀工艺操作的速度太快或太慢,工件的浸泡时间控制不准确等都可能导致电镀层质量不良。
因此,操作人员在进行电镀工艺操作时要严格按照程序进行,并且进行必要的培训和技术指导,提高工艺操作的准确性和稳定性。
综上所述,电镀不良的原因可以从原料、工艺参数、设备质量和工艺操作等多个方面进行分析。
为了防范电镀不良的发生,可以采取以下措施:1.选用优质的原料,并进行严格检验和筛选;2.根据实际情况调整电镀工艺参数,并进行严格的控制;3.选购品质可靠的设备,并保证设备的维护和保养;4.进行工艺操作前进行必要的培训和技术指导,确保操作的准确性和稳定性;5.建立完善的质量控制体系,对电镀过程进行监控和检测,及时处理不良产品;6.加强与供应商的合作,建立长期稳定的合作关系,确保原料和设备质量的稳定性。
电镀件常见不良原因分析

a.部品和镀层间原因: 1.三价铬含量过高对策: 1.调整三价铬含量b •铜层和其他镀层间原因: 1.活化不到位对策: 1.增加活化酸含量G. 镀层脆性大原因: 1.光亮剂过量 3. 金属杂质过高 2. 粗化时间过短 2.延长粗化时间 2.导电柱导电不良 2.随时检查导电柱的相关情况 2.有机杂质污染4. 六价铬污染3.加入 TPP 除杂剂4.用保险粉处理 电镀件常见不良原因分析A.麻点、杂质、颗粒原因: 1.镀槽内杂质太多2.过水缸太脏 对策: 1.加强电解以及过滤,定期清缸 2.勤换过水缸的清水B.漏镀 原因: 1. 部品表面有缝隙藏铬酸 3.解胶不足或过度 2.钯水浓度偏低,沉钯不到位4.沉镍料不足对策: 1.加强中和,消除铬酸 2.提高钯浓度,加强摇摆3.根据漏镀位置, 提高或降低解胶浓度4.沉镍加料C.针孔原因: 1. 润湿剂不足2.有机杂质过多 3 .硼酸含量和温度太低 对策: 1. 补加润湿剂2.用双氧水活性炭处理3.分析硼酸浓度,将镀液加温 D. 变形原因: 1. 素材本身变形2.上挂挂具弹力大小及适用性3.粗化缸或烤箱的温度过高4.包装方式不合理对策: 1. 优化成型参数, 改善变形 2 .选择合适的挂具3.将温度调整到合理的范围4.改用合理的包装方式E.烧焦原因: 1. 主盐浓度太底 2 .镀液温度太低3.硼酸含量不足, PH 高4. 润湿剂过量 对策: 1. 分析成分后补充2 .提高温度至 50-60 摄氏度 3.补充硼酸,调整 PH 值4.采用活性炭吸附 F.镀层起皮对策:1•调整PH 值3.0-3.5电解消耗2.用活性炭双氧水处理 H. 颜色偏亮或偏哑原因: 1 .光亮剂量的多少2.酸铜缸和镍缸的电流大小的时间长短对策: 1.添加或稀释缸液中的光亮剂成分2. 将酸铜缸和镍缸的时间和电流大小调整至合理的工艺范围I. 毛刺原因: 1 .素材本身有毛刺2.水口设计不合理3. 镀液中有悬浮微粒4.铁离子在高 PH 下形成氢氧化物沉淀,附在镀层中对策: 1.模具型修或优化成型参数 2.更改水口或增加外框保护3•连续过滤4•调整PH至5.5加入QF除铁粉,防止铁工件掉入槽中J•脏污、水渍原因:1•缸水未清洁干净2•后处理过热水不完全和时间短3•手直接接触部品 4.电导率太高对策:1•换水或用活性炭吸附2•部品要全部浸在热水缸中,时间延长至1分钟3•从产品下挂到包装入箱,杜绝用手接触产品,戴手套或指套,个别产品要包白纸4.调整电导率K.镀层结合力差原因:1•除油不彻底 2.亲水不充分3•酸活化不均匀4•三水洗缸水不干净对策:1•调整除油缸温度和浓度2•调整亲水缸温度和组份浓度,使其浸润充分和缸水浓度正常3•调整硫酸浓度、时间和电流至合理的工艺要求4•定时清理和更换缸水。
电镀产生问题原因及对策
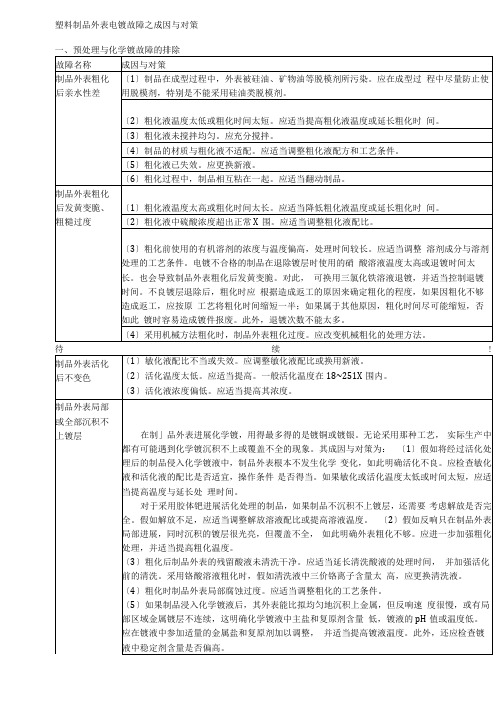
塑料制品外表电镀故障之成因与对策〔4〕采用硝酸银活化液时,活化液中银离子浓度太低,催化作用减弱,铜或镍离子就很难复原出来。
对此,应与时调整活化液中银离子的浓度。
在敏化和活化过程中,如制品的外表色泽不均匀,可重复敏化和活化2~3次,在反复的过程中需加强清洗。
既便于粗化和提高镀层的附着力,还可掩盖镀层外表的小伤痕和缺陷。
b、制品外表尽量不要设计盲孔,必须设计时,孔深只能为其直径的1/2~1/3, 孔深尽量浅一些,孔径尽量大一些。
槽与孔之间的距离不能太近,其边缘部位应倒角。
c、制品应具有足够的强度,壁厚不能太薄,最好大于3mm,至少为1.5mm,壁厚不要有突变,厚薄悬殊不能太大。
d、制品不应有锐角、尖角和锯齿形。
假如必须设计这种形体时,其边缘应尽量倒圆。
e、应尽量防止设计大面积的平面,因为大面积的平面镀层不容易得到均匀的光泽。
光泽。
f、尽量防止使用镶件结构。
假如必须设计这种结构时,壁厚应大一些,且边缘部位应进展倒圆处理。
g、制品上应留出装挂的工艺位置,以便获得良好、均匀的镀层。
h、用于电镀的制品,应完整无损,外表光滑,颜色均匀一致,无划痕、毛刺、飞边,以与种种外表丝纹和气泡。
塑件成型时的剩余应力要低。
对于剩余应力较高的制品,应在电镀前先进展退火处理。
完〔4〕制品成型条件控制不当。
制品的成型条件对镀层的结合力影响很大,判断两者关系的方法是在常温下用冰醋酸浸泡制品2min,然后水洗枯燥,如果此时。
制品外表产生白色粉末或产生裂纹,明确制品的成型不良,镀层与基体的结合力不会太好。
一般来说,产生白粉的镀件,多数不能通过循环试验;产生裂纹多的镀件,多数不能通过剥离试验。
所谓循环试验,主要是采用冷热循环试验的方法来检查镀层的热稳定性能。
在试验中选用得上下温度X围和循环次数,是根据制品的使用条件和环境确定的。
如汽车上使用的零件,在进展冷热循环试验时,先将镀件放入85℃的烘箱中保温1h,取出后在室温中放置15min,然后再放入40℃条件下1h,最后再在室温中放置15min。
电镀失败原因分析报告
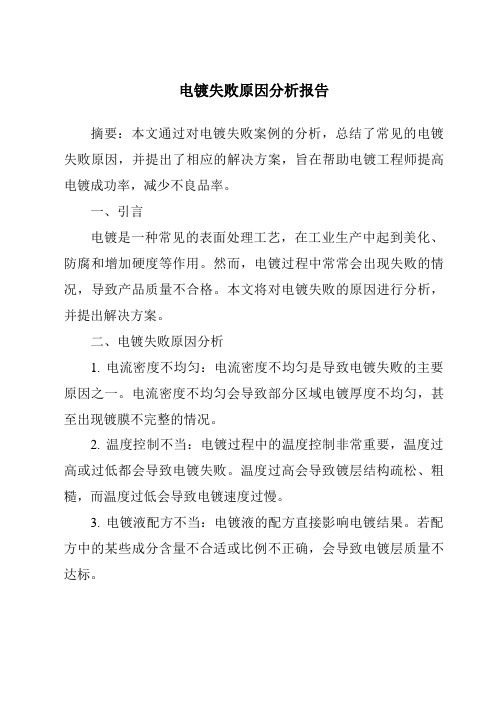
电镀失败原因分析报告摘要:本文通过对电镀失败案例的分析,总结了常见的电镀失败原因,并提出了相应的解决方案,旨在帮助电镀工程师提高电镀成功率,减少不良品率。
一、引言电镀是一种常见的表面处理工艺,在工业生产中起到美化、防腐和增加硬度等作用。
然而,电镀过程中常常会出现失败的情况,导致产品质量不合格。
本文将对电镀失败的原因进行分析,并提出解决方案。
二、电镀失败原因分析1. 电流密度不均匀:电流密度不均匀是导致电镀失败的主要原因之一。
电流密度不均匀会导致部分区域电镀厚度不均匀,甚至出现镀膜不完整的情况。
2. 温度控制不当:电镀过程中的温度控制非常重要,温度过高或过低都会导致电镀失败。
温度过高会导致镀层结构疏松、粗糙,而温度过低会导致电镀速度过慢。
3. 电镀液配方不当:电镀液的配方直接影响电镀结果。
若配方中的某些成分含量不合适或比例不正确,会导致电镀层质量不达标。
4. 表面预处理不彻底:表面预处理是电镀的关键步骤之一,若不进行彻底的表面清洗、脱脂和去除氧化物等处理,会导致电镀层附着力不好。
三、解决方案1. 电流密度均匀化:调整电镀槽设计,使电流在整个工件表面均匀分布,或采用电镀液循环系统,提高电镀液的对流效果,以达到电流密度均匀的目的。
2. 温度控制精确化:安装温度探针,实时监测电镀槽中的温度,并通过控制加热或制冷设备,使温度保持在合适范围内。
3. 优化电镀液配方:根据具体产品要求,调整电镀液中各种成分的含量与比例,确保配方合理,以提高电镀层质量。
4. 提高表面预处理质量:加强表面预处理步骤,确保表面清洁、脱脂和去氧化彻底,可采用多种方法,如超声波清洗、化学脱脂等。
四、结论通过对电镀失败案例的分析,我们总结了电流密度不均匀、温度控制不当、电镀液配方不当和表面预处理不彻底等常见的电镀失败原因,并提出了相应的解决方案。
只有在电镀过程中严格控制这些关键因素,才能提高电镀成功率,降低不良品率,从而保证产品质量。
- 1、下载文档前请自行甄别文档内容的完整性,平台不提供额外的编辑、内容补充、找答案等附加服务。
- 2、"仅部分预览"的文档,不可在线预览部分如存在完整性等问题,可反馈申请退款(可完整预览的文档不适用该条件!)。
- 3、如文档侵犯您的权益,请联系客服反馈,我们会尽快为您处理(人工客服工作时间:9:00-18:30)。
镀层表面起泡 脱皮
再放入40℃条件下1h,最后再在室温中放置15min。如此循环4次,如果镀层表
面状态和结合力均无变化则为合格
所谓剥离试验,是在制品电镀的样片上切取1!2cm宽的镀层,橇起一头,
用垂直于基体的力拉镀层,并测定剥离镀层时所需的力,其单位为kg/cm。一般剥
离在0.45kg/cm以上则为合格。
可观察到许多微小的凹坑,但手摸时无粗糙感。这种故障产生在酸性镀亮铜工
序中,其产生原因及排除方法如下:
(1)空气搅拌太剧烈。应停用空气搅拌,采用阴极移动,为了防止产生过多的
铜离子,每天下班时应用少量的双氧水经稀释后加入镀液中。
(2)阴极电流密度太大。应适当减小,一般电流密度应控制在2~3A/d㎡。
(3)组合光亮剂的组成不平衡。应适当提高镀液中硫酸含量,降低硫酸铜的含
量,镀液内可添加适量的聚乙二醇和聚二硫二丙烷磺酸钠。
(4)当粗化过度或清洗不良时,敏化和活化反应会构成核状物,导致镀层表
面沉积出凸起的细沙粒状的麻点。对此,应适பைடு நூலகம்调整粗化和水洗工艺条件。
(5)电镀铜时阳极泥混入镀液中,或挂钩接触部位金属脱落混入镀液中。对
此,应严格按照工艺规程进行操作。
(6)使用催化剂时,制品表面未完全分解。应适当调整催化工艺条件。
a、应注意制品的漂浮性。因塑料比重较小,其漂浮性比金属件大,尤其是整 组挂具,在进入镀液时,受浮力影响困难使导电部位脱离电极棒。因此,在设 计时最好采用弹簧或螺钉夹紧,特别是采用自动生产线时更应注意这一问题。
b、应注意制品的变形。由于制品的刚性较差,挂具所用的钢丝直径和触点位 置都会影响到制品的变形。在设计时,应尽量采用托、夹等方法,尽可能避免 撑、插、顶、压。如果必须采用后一类方法时,支撑点尽可能安放在孔内侧的 根部。
由于制品成型条件对镀层结合力影响的因素相当复杂,处理较为困难,尚
无良好的针对性措施。但产生这类故障时,应从成型条件着手排除,通过改善
成型条件,使制品表面不产生白粉和裂纹。 制品的电镀一般采用多层电镀。镀件起泡脱皮,说明镀层与基体结合不牢,
或镀层之间结合不良。具体表现在5个方面: (1)金属镀层间分离。其成因及对策为:
当表面积较大的制品在镀酸性亮铜时,夹具周围接触的化学铜层活镍层溶
露塑
解,就会产生局部露塑。制品在电镀铜、镍或铬时,都是在化学镀铜或镍的基
础上进行的,因化学镀铜或镀镍层相当薄,厚度一般只有0.3~0.5μm,在酸性
溶液中,当挂具的接触导线太细或弹性不足时,出现露塑,接触点处的电阻较
大,会使触点周围流入的电流过小,引起学镀铜或镀镍层很快被溶解,出现露
a、化学镀层钝化。应改善化学镀后的活化条件,减少传递时间,采用较厚 的化学镀层,病迅速覆盖一层光亮酸性铜或立即闪镀镍。
b、镀铜层钝化。应改进铜层酸洗条件和清除镀件表面油污。 c、镀镍层钝化。应在镀镍前进行活化处理。 (2)镀层与制品基体起泡分离。其成因与对策为: a、制品的基体材料不适合电镀。应更换原料品种,使用电镀级原料。 b、制品的成型条件控制不当。应适当调整制品的成型温度和浇口结构。 c、粗化不良。应适当调整粗化液组分、粗化温度和粗化时间。从经验上看, 制品经粗化厚的正常情况,应是表面既失去光泽,又无毛糙的感觉;制品经过 化许学镀后的正常情况,应是镀层呈暗光。 d、制品电镀层的组合设计不当。由于塑料的热膨胀率比金属镀层大得多,如 果表面为硬质镀层,当周转介质温度发生变化时就会引起镀层与基体起泡分离。 在设计镀层时,一般底层应为塑性镀层,且镀铜层应厚一些,占整个镀层的2/3, 而镀亮镍和铬时则应薄一些。 (3)电镀的电流密度太大或镀层内应力太大,导致镀层起泡。应适当降低电流 密度,调整电镀液的配比和电镀工艺条件。 (4)镀层表面产生线条或点状的鼓泡。其产生原因不在于镀层与基体结合不良 或金属化处理不当,而在于制品成型时,原料干燥不良,水份含量太高。对此, 应在制品成型时,对原料进行充分干燥,使水分含量达到成型时的要求。 (5)制品表面镀铬存放后层面起泡。其产生原因和处理方法如下: a、制品的前处理没有达到工艺要求。如粗化时间太断或太长,敏化和活化不 当等。对此,应检验粗化液的成分含量并进行调整,严格按照工艺要求控制粗
化时间和溶液温度。敏化和活化也应按工艺要求进行,特别是制品表面除油要
彻底。
b、电镀工艺条件控制不当。如光亮镍的镀层厚度大大超过了铜层的厚度,且
镀镍工艺条件又控制不当,造成镀镍层内应力过大。对此,应调整电镀工艺条
件,合理设计镀层厚度。
c、镀件存放不当。应注意镀件存放条件,存放环境温差不能太大。
镀层表面局部
法通过,电镀不上镀层。对此,应首先检查化学镀液,适当延长沉积时间,加
厚化学镀的金属镀层;其次,镀件进入镀槽时,应先用0.1~0.22~3A/d㎡的小电
挂具被金属化
流电镀4~5min,然后将电流逐渐递增至正常工艺规范。 (2)电镀夹具接点太少,夹持部位不当。用作塑料电镀的夹具与镀件的接点, 应比金属件电镀的接点多25%,以减少接触电阻。接点的形式最好不要采用点接 触,而用半环形的线接触,这样可以增强导电性,使电流顺利通过。另外,夹 具应具有良好的弹性,因塑料的比重较小,容易受镀液浮力的作用发生摆动而 影响导电,甚至形成双极性,使镀层溶解。但夹具的弹性也不能过大,否则会 使镀件变形。夹持部位不应选在低电流密度区,因小电流处镀层的沉积速度慢, 相比之下,始终处于难以导电的状态,会影响电镀效果。 (3)化学镀后存放时间太长,镀层表面氧化。经化学镀后的制品,无论存放在 空气或浸放在水中,镀层都会发生氧化,影响导电。对于镀铜层氧化膜,可以 在稀硫酸中进行活化处理,但要损失少量的镀层,增加电镀的困难,不过电镀 还能进行。对于化学镀镍层,因镍的氧化层不易除去,较难活化。对此,可将 镀件先在稀硫酸中活化0.5min,然后带酸入槽电镀5min的暗镍,再镀光亮镍, 则可获得正常镀层。 (1)挂具绝缘不良。应对挂具重新进行绝缘处理。 (2)挂具剥离剂使用不当。应换用适宜的剥离剂。 (3)构架浸入粗化液的深度没有金属化溶液高。应适当降低金属化溶液的液面 高度。 (4)挂具设计不当。塑料电镀时使用的挂具,由于制品本身的特点和工艺的特 殊性,设计时应注意以下问题:
镀层表面有伤痕 (1)制品电镀后在运输过程中磕碰导致表面伤痕。应在包装时用衬垫隔开。
(2)镀件在电镀过程中输送不良导致表面伤痕。应检查挂具和挂装情况,注意
文明操作防止生产掉件。
镀层表面污染 (1)镀液维护不良。应过滤溶液,清洗阳极袋,改进空气搅拌。
(2)清洗水不洁净。应过滤或净化清洗水,最好使用不含硅的去离子水。
故障名称 镀层与基体结 合不良
成因及对策 (1)粗化液配方不当,当粗化液配方不适合制品的原料种类时,光是改变粗 化液的温度和延长粗化时间,仍然不能增加金属镀层与基体结合力。如粗化 ABS制品时,当铬酐与硫酸的比例不当时,粗化液对制品表面的丁二烯树脂就没 有氧化腐蚀作用不能形成凹坑,因此金属镀层与制品基体就没有结合的基础。 对此,只要适当提高粗化液中的硫酸浓度或采用溶剂对制品进行表面处理即可。 (2)粗化工艺条件控制不当。通常粗化温度和时间对镀层结合力的影响极大。 因为化学粗化液一般是用强氧化剂配制而成的,如果粗化液温度偏高,粗化时 间偏长,会使制品表面产生老化层,而老化层十分疏松,在干燥状态下会形成 一层黄白色粉末,是镀层结合力下降。反之,如果温度偏低,时间太短,制品 表面腐蚀的凹坑深度太浅,粗化表面的“锨钮”作用不大,也会使得镀层结合 力下降。对此,应适当调整粗化温度和时间。 (3)制品表面除油不良。由于制品在成型过程中使用脱模剂,或在周转过程 中表面粘有种种油污,妨碍了粗化液对制品表面的粗化,导致镀层与基体结合 不良。对此,应彻底清除制品表面的油污。 (4)制品成型条件控制不当。制品的成型条件对镀层的结合力影响很大,判断 两者关系的方法是在常温下用冰醋酸浸泡制品2min,然后水洗干燥,如果此时。 制品表面产生白色粉末或产生裂纹,表明制品的成型不良,镀层与基体的结合 力不会太好。一般来说,产生白粉的镀件,多数不能通过循环试验;产生裂纹 多的镀件,多数不能通过剥离试验。所谓循环试验,主要是采用冷热循环试验 的方法来检查镀层的热稳定性能。在试验中选用得高低温度范围和循环次数, 是根据制品的使用条件和环境确定的。如汽车上使用的零件,在进行冷热循环 试验时,先将镀件放入85℃的烘箱中保温1h,取出后在室温中放置15min,然后
化学镀后电镀 (1)化学镀层疏松或太薄影响导电。由于塑料本身不导电,全靠化学镀层金属
不上镀层
导电,当镀层厚度小于0.1μm或镀层不紧密时,电流通过时电阻很大,使夹具
与镀件处温度升高,严重时还会使塑件熔融,附近的镀层被溶液腐蚀溶解。特
别是在强酸性镀液中,如酸性光亮铜镀液,这种现象就更为明显,结果电流无
塑,不过,电流过大也会产生接触点露塑。对此,一是将挂夹具导线改粗,一
般为金属电镀的一倍,一增加接触面积;二是先小后大的作业电流,逐渐升至
工艺要求;三是确保化学沉积金属层的厚度不得低于0.4μm,且化学镀铜后存
放时间不宜太长。
镀层表面麻点
麻点是指电镀河腐蚀过程中镀层表面形成的小坑或小孔。在3~5倍放大镜下