波峰焊操作步骤
波峰焊操作规程

波峰焊操作规程波峰焊是一种常用于电子元器件的焊接方式,主要应用于印刷电路板(PCB)的组装过程中。
波峰焊操作规程是指在进行波峰焊工艺时所需要遵守的规范和操作流程。
下面是一份关于波峰焊操作规程的大致内容,以供参考:一、工艺流程1. 前期准备:- 检查设备的工作状态和焊接工具的完好程度。
- 检查焊接材料的存放情况,确保其质量和数量。
- 清洁焊接区域,确保无灰尘和杂物。
2. PCB准备:- 检查PCB的尺寸和表面的平整程度。
- 清洁PCB的表面,确保无油污或划痕。
- 检查PCB上的元器件位置是否正确,无误差。
3. 准备焊接材料:- 检查焊盘的质量,确保无翘曲、斑点或孔隙。
- 配置焊接剂,确保其粘稠度和涂覆面积适当。
4. 设定焊接工艺参数:- 根据焊接材料和PCB的要求,设定合适的焊接温度和时间。
- 确保焊接参数的准确性和稳定性。
5. 进行焊接:- 将PCB放置在焊接机上,并根据设备的要求夹紧。
- 使用自动或手动程序,将PCB送入预热区。
- 当PCB达到预设的焊接温度时,将其送入波峰区。
- PCB在波峰区停留适当时间,以确保焊接质量。
- 将焊接完成的PCB从波峰区取出,静置冷却。
6. 检查和维护:- 对焊接后的PCB进行视觉和功能检查,确保焊接质量良好。
- 定期检查和维护设备,确保其正常工作。
二、安全注意事项1. 防止触电:- 确保设备与电源接地,避免触电危险。
- 禁止将湿手或带有金属物品接近设备。
2. 防止火灾:- 防止焊接工作区域附近存在易燃物品。
- 注意焊接过程中的渣滓和烟尘,防止引发火灾。
3. 防护措施:- 确保焊接工作区域通风良好,避免吸入有害气体。
- 在进行焊接时,佩戴防护眼镜、手套和工作服等防护设备。
4. 废弃物处理:- 将焊接过程中产生的废弃物,如焊渣和焊剂,分类储存并妥善处理。
三、质量控制1. 密封性:- 确保焊接后的焊点完整且牢固,防止出现短路和断路。
- 使用无腐蚀性的焊剂,避免产生腐蚀性物质。
波峰焊的工艺流程
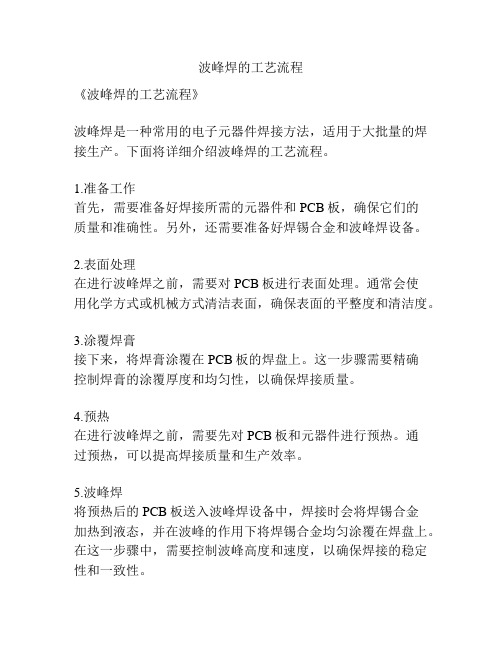
波峰焊的工艺流程
《波峰焊的工艺流程》
波峰焊是一种常用的电子元器件焊接方法,适用于大批量的焊接生产。
下面将详细介绍波峰焊的工艺流程。
1.准备工作
首先,需要准备好焊接所需的元器件和PCB板,确保它们的
质量和准确性。
另外,还需要准备好焊锡合金和波峰焊设备。
2.表面处理
在进行波峰焊之前,需要对PCB板进行表面处理。
通常会使
用化学方式或机械方式清洁表面,确保表面的平整度和清洁度。
3.涂覆焊膏
接下来,将焊膏涂覆在PCB板的焊盘上。
这一步骤需要精确
控制焊膏的涂覆厚度和均匀性,以确保焊接质量。
4.预热
在进行波峰焊之前,需要先对PCB板和元器件进行预热。
通
过预热,可以提高焊接质量和生产效率。
5.波峰焊
将预热后的PCB板送入波峰焊设备中,焊接时会将焊锡合金
加热到液态,并在波峰的作用下将焊锡合金均匀涂覆在焊盘上。
在这一步骤中,需要控制波峰高度和速度,以确保焊接的稳定性和一致性。
6.冷却
焊接完成后,PCB板需要进行冷却。
冷却过程中,焊锡合金会固化,形成可靠的焊接连接。
7.清洗
最后,对焊接完成的PCB板进行清洗。
清洗可以去除焊接过程中产生的残留物,确保焊接质量和电路可靠性。
通过以上步骤,波峰焊的工艺流程就完成了。
这种焊接方式具有生产效率高、焊接质量稳定的特点,因此在电子制造行业得到了广泛应用。
波峰焊操作步骤

预热与熔融
预热
将焊接托盘放置在预热区域,使 焊料达到熔融状态。预热温度和 时间根据焊料和元件的特性而定 。
熔融
将熔融状态的焊料均匀涂敷在需 要焊接的元件引脚上,确保焊料 覆盖整个引脚。
波峰焊接
波峰形成
通过加热使焊料熔化形成波峰,波峰 的高度和宽度根据需要进行调整。
焊接
将涂敷了焊料的元件引脚浸入波峰中 ,通过波峰的流动将元件引脚与基板 进行焊接。
波峰焊的特点
波峰焊具有焊接效率高、焊接质量稳定、成本低等 优点,广泛应用于电子制造行业的PCB板焊接。
波峰焊的焊接质量与焊料、助焊剂、温度和时间等 参数密切相关,需要严格控制。
波峰焊适用于大规模、高效率的生产环境,能够快 速、准确地完成大量焊接任务。
波峰焊的应用
波峰焊广泛应用于电子制造行业中的PCB板焊接,尤其适用于大 规模、高效率的生产环境。
总结词
提高了生产效率和产品质量,降低了生产成本
详细描述
波峰焊在LED灯具生产中也有广泛应用,通过精确控制温度和时间,实现了高效率、高质量的生产。 在LED灯具生产中,波峰焊能够有效地将LED芯片焊接在支架上,避免了传统手工焊接的缺陷,提高 了生产效率和产品质量,同时也降低了生产成本。
THANK YOU
冷却与后处理
冷却
将焊接完成的电子元件从波峰中取出,自然冷却至室温。
后处理
对焊接完成的电子元件进行检查、清洁和修整,确保焊接质 量符合要求。
04
波峰焊操作注意事项
安全防护
020103 Nhomakorabea操作人员应佩戴防护眼镜、手套、工作服等个人防护 用品,以防止高温、飞溅和有害气体对人体的伤害。
操作区域应设置安全警示标识,并保持安全通道畅通 ,以便在紧急情况下快速撤离。
波峰焊作业指导书
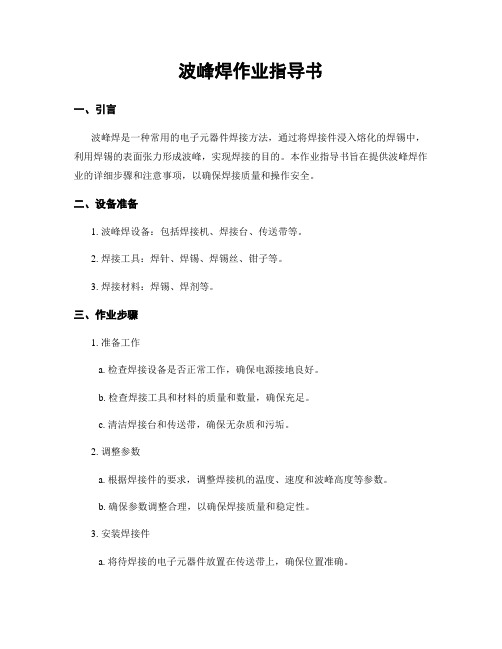
波峰焊作业指导书一、引言波峰焊是一种常用的电子元器件焊接方法,通过将焊接件浸入熔化的焊锡中,利用焊锡的表面张力形成波峰,实现焊接的目的。
本作业指导书旨在提供波峰焊作业的详细步骤和注意事项,以确保焊接质量和操作安全。
二、设备准备1. 波峰焊设备:包括焊接机、焊接台、传送带等。
2. 焊接工具:焊针、焊锡、焊锡丝、钳子等。
3. 焊接材料:焊锡、焊剂等。
三、作业步骤1. 准备工作a. 检查焊接设备是否正常工作,确保电源接地良好。
b. 检查焊接工具和材料的质量和数量,确保充足。
c. 清洁焊接台和传送带,确保无杂质和污垢。
2. 调整参数a. 根据焊接件的要求,调整焊接机的温度、速度和波峰高度等参数。
b. 确保参数调整合理,以确保焊接质量和稳定性。
3. 安装焊接件a. 将待焊接的电子元器件放置在传送带上,确保位置准确。
b. 使用钳子或其他工具将焊接件固定在焊接台上,防止移动。
4. 进行焊接a. 打开焊接机的电源,启动传送带。
b. 等待焊接机预热至设定温度后,将焊接件送入焊接区域。
c. 等待焊接完成后,将焊接件从焊接台上取下,放置在冷却区域。
5. 检查焊接质量a. 观察焊接点是否均匀、完整,无明显缺陷。
b. 使用测试工具进行电气性能测试,确保焊接质量符合要求。
四、安全注意事项1. 在进行波峰焊作业前,必须戴上防静电手套和防静电鞋,以防止静电对焊接件造成损害。
2. 确保焊接区域通风良好,避免焊接烟雾对人体健康的影响。
3. 在进行焊接操作时,应注意避免焊接机和焊接台的高温表面,以免烫伤。
4. 确保焊接机的电源接地良好,避免电击事故的发生。
5. 在进行焊接操作时,应注意保持集中注意力,避免操作失误导致事故发生。
五、维护保养1. 定期清洁焊接设备,包括焊接机、焊接台和传送带等,以确保设备正常运行。
2. 定期检查焊接工具和材料的质量和数量,及时补充和更换。
3. 定期检查焊接机的参数调整,确保焊接质量和稳定性。
4. 定期检查焊接件的焊接质量,及时修复和更换不合格的焊接件。
波峰焊操作步骤

波峰高度一般控制在印制板厚度的2/3 处。插元器件引脚成形要求元件引脚露出印制板焊接0.8~3mm。
助焊剂活性差
更换助焊剂。
插装元件引线直经与插装孔比例不 正,插装孔过大,大焊盘吸热量大。
爬坡角度小,焊接时间长
爬坡角度大,焊接时间短
图8-7 传送带倾斜角度与焊接时间的关系
工艺参数的综合调整对提高波峰焊质量是非常重要的。
焊接温度和时间是形成良好焊点的首要条件。焊接温度和时间与预热温度、焊料波的温度、倾斜角度、传输速度都有关系。
综合调整工艺参数时首先要保证焊接温度和时间。双波峰焊的第一个波峰一般在235~240℃/1s 左右, 第二个波峰一般在240~260℃/3s左右。两个波峰的总时间控制在10s以内。
5.3 设置焊接参数
5.4 首件焊接并检验(待所有焊接参数达到设定值后进行) a 把PCB轻轻地放在传送带(夹具)上,机器自动进行喷涂助焊、干燥、预热、波峰焊、冷却。 b 在波峰焊出口处接住PCB。 c 进行首件焊接质量检验。 5.5 根据首件焊接结果调整焊接参数 5.6 连续焊接生产 a 方法同首件焊接。 b 在波峰焊出口处接住PCB,检查后将PCB装入防静电周转箱送修后附工序(或直接送连线式清洗机进行清洗)。 c 连续焊接过程中每块印制板都应检查质量,有严重焊接缺陷的制板,应立即重复焊接一遍。如重复焊接后还存在问题,应检查原对工艺参数作相应调整后才能继续焊接。
打开波峰焊机和排风机电源。 根据PCB宽度调整波峰焊机传送带(或夹具)的宽度
5.2 开炉
发泡风量或助焊剂喷射压力:根据助焊剂接触PCB底面的情况定。 预热温度:根据波峰焊机预热区的实际情况设定 传送带速度:根据不同的波峰焊机和待焊接PCB的情况设(0.8—1.92m/min) 焊锡温度:(必须是打上来的实际波峰温度为250±5℃时的表显示温度)
波峰焊作业指导书
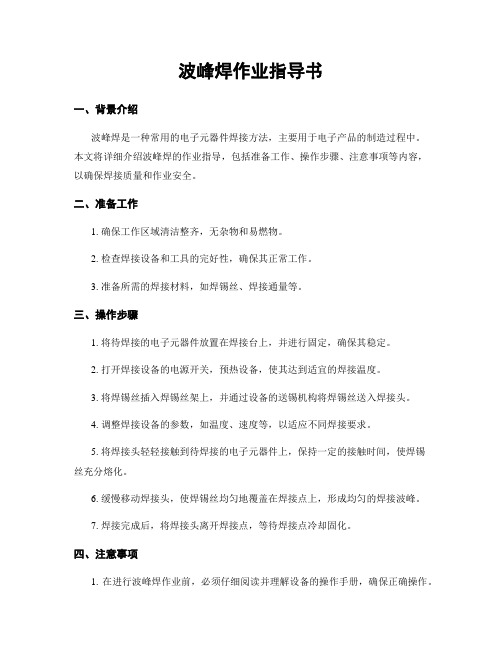
波峰焊作业指导书一、背景介绍波峰焊是一种常用的电子元器件焊接方法,主要用于电子产品的制造过程中。
本文将详细介绍波峰焊的作业指导,包括准备工作、操作步骤、注意事项等内容,以确保焊接质量和作业安全。
二、准备工作1. 确保工作区域清洁整齐,无杂物和易燃物。
2. 检查焊接设备和工具的完好性,确保其正常工作。
3. 准备所需的焊接材料,如焊锡丝、焊接通量等。
三、操作步骤1. 将待焊接的电子元器件放置在焊接台上,并进行固定,确保其稳定。
2. 打开焊接设备的电源开关,预热设备,使其达到适宜的焊接温度。
3. 将焊锡丝插入焊锡丝架上,并通过设备的送锡机构将焊锡丝送入焊接头。
4. 调整焊接设备的参数,如温度、速度等,以适应不同焊接要求。
5. 将焊接头轻轻接触到待焊接的电子元器件上,保持一定的接触时间,使焊锡丝充分熔化。
6. 缓慢移动焊接头,使焊锡丝均匀地覆盖在焊接点上,形成均匀的焊接波峰。
7. 焊接完成后,将焊接头离开焊接点,等待焊接点冷却固化。
四、注意事项1. 在进行波峰焊作业前,必须仔细阅读并理解设备的操作手册,确保正确操作。
2. 在操作过程中,应佩戴防护眼镜和手套,以防止热溅和其他伤害。
3. 注意焊接设备的安全使用,避免触摸热部件和电源线,以免发生电击和烫伤。
4. 确保焊接设备的通风良好,避免产生有害气体的积聚。
5. 根据具体焊接要求,合理调整焊接参数,以获得最佳的焊接效果。
6. 在操作过程中,要保持专注和集中注意力,避免分心和疏忽造成事故。
7. 焊接完成后,及时清理焊接设备和工作区域,以保持整洁。
五、总结波峰焊作业是一项关键的电子元器件焊接工艺,正确的操作步骤和注意事项对于焊接质量和作业安全至关重要。
通过本指导书的详细介绍,相信您已经掌握了波峰焊作业的基本要点,希望能够在实际操作中取得良好的效果。
如有任何疑问或需要进一步的指导,请随时与我们联系。
祝您工作顺利!。
波峰焊操作步骤课件
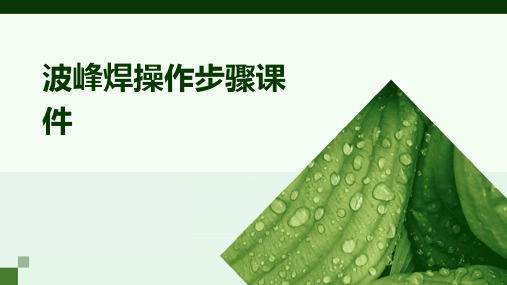
将适量的锡条放置在波峰焊机的 熔化槽中,以确保焊接过程中锡 的供应充足。
启动波峰焊机并监控焊接过程
启动波峰焊机,开始加热和熔化锡条。 监控焊接过程,观察焊接效果,及时调整焊接参数,以确保焊接质量和可靠性。
当焊接完成后,关闭波峰焊机,取出焊接好的PCB板,并进行质量检查。
04
波峰焊操作注意事项
准备好所需的焊接材料,如焊锡 丝、助焊剂等。
环境准备
确保波峰焊操作区域整洁、无 杂物,保证设备正常运行。
检查空气压缩机、冷却设备等 辅助设备是否正常运转,确保 操作过程中无异常情况。
准备好操作工具,如烙铁、镊 子等,确保操作过程中使用方 便。
03
波峰焊操作步骤
ቤተ መጻሕፍቲ ባይዱ
PCB板预处理
1 2 3
清洁PCB板
保持设备清洁与维护保养
01
02
03
定期清理炉腔
波峰焊的炉腔经常会有残 留物和氧化物,这些物质 会影响焊接效果,因此需 要定期清理。
定期保养设备
设备保养是保持设备良好 状态的关键,应定期对设 备进行润滑、检查等保养 工作。
避免设备过度使用
设备长时间使用可能会导 致过热、磨损等问题,应 合理安排设备使用时间, 避免设备过度使用。
05
波峰焊常见问题及解决方 案
焊接不良问题及解决方案
焊接不良总结
波峰焊过程中的焊接不良主要 表现为焊点不饱满、有气泡、
不光亮等。
焊接温度不够
适当提高焊接温度,通常比正 常温度高5-10℃。
助焊剂不足
适当增加助焊剂的使用量,保 证焊接过程中有足够的助焊剂 覆盖在PCB板上。
PCB板预热不足
适当增加预热时间,保证PCB 板在进入波峰前已经充分预热
波峰焊焊接工艺指导书

波峰焊焊接工艺指导书一、概述波峰焊是一种常用的焊接方法,主要适用于焊接插件、接插件等电子元器件。
它通过将焊接头置于熔化的焊料表面,使焊料以波峰的形式包裹住焊接部分,实现焊接连接。
本指导书将介绍波峰焊焊接工艺的操作步骤和注意事项。
二、操作步骤1.准备工作(1)确认焊接板的质量和尺寸是否符合要求;(2)确认焊料种类和规格,保证焊料质量良好;(3)检查和调整焊机的参数,如预热温度、焊接时间等。
2.安装板料将待焊接的板料放入焊接机的工作台上,确认板料位置正确、稳定。
3.清洗板料使用无尘布或擦拭纸对板料进行清洁,去除灰尘和油污。
4.预热打开焊接机,根据焊料的要求设定预热温度。
等待焊机达到设定温度后,开始预热,保持稳定的预热温度。
5.上锡将焊料条放在焊接头下方,并调整焊料高度,使其紧贴焊料表面。
然后启动焊机,将焊料熔化并上升形成波峰。
6.板料焊接(1)将焊接板垂直放入焊接波峰中,焊接部分被焊料波峰完全覆盖。
(2)等待一段时间,让焊接部分充分受热,保证焊料与焊接部分的接触良好。
(3)取出焊接板,等待焊料凝固。
7.检查焊接质量(1)检查焊接部分是否完全被焊料覆盖,无漏焊现象;(2)检查焊料与焊接部分的接触是否良好,无孔洞或松动现象;(3)测量焊接部分的电阻值,确保电阻值符合要求。
8.清理工作台清除工作台上焊料的残留物,保持工作台整洁。
三、注意事项1.操作人员必须戴好防静电手套和防静电服,以防止静电对元器件的损坏。
2.焊接前要确保焊接板没有脏污和油渍,以免影响焊接质量。
3.焊接过程中应保持焊接板的稳定,避免晃动或移位导致焊接不良。
4.控制预热温度和焊接时间,避免过高温度或时间过长导致焊接部分或焊料损坏。
5.焊接时要注意焊接区域与人体的安全距离,避免烫伤或其他安全事故发生。
6.焊接完成后应对焊接部分进行检查,确保焊接质量符合要求。
7.使用过的焊料和废弃物应按规定的方法进行处理,以保护环境。
四、总结波峰焊是一种常用的焊接方法,它可以实现快速、高质量的焊接连接。
波峰焊作业指导书
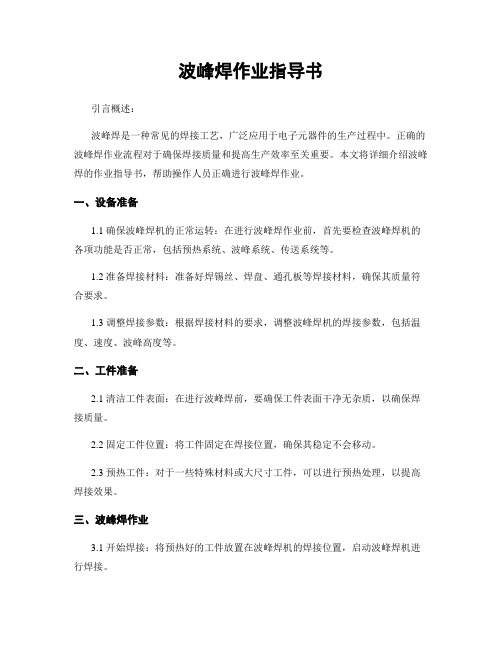
波峰焊作业指导书引言概述:波峰焊是一种常见的焊接工艺,广泛应用于电子元器件的生产过程中。
正确的波峰焊作业流程对于确保焊接质量和提高生产效率至关重要。
本文将详细介绍波峰焊的作业指导书,帮助操作人员正确进行波峰焊作业。
一、设备准备1.1 确保波峰焊机的正常运转:在进行波峰焊作业前,首先要检查波峰焊机的各项功能是否正常,包括预热系统、波峰系统、传送系统等。
1.2 准备焊接材料:准备好焊锡丝、焊盘、通孔板等焊接材料,确保其质量符合要求。
1.3 调整焊接参数:根据焊接材料的要求,调整波峰焊机的焊接参数,包括温度、速度、波峰高度等。
二、工件准备2.1 清洁工件表面:在进行波峰焊前,要确保工件表面干净无杂质,以确保焊接质量。
2.2 固定工件位置:将工件固定在焊接位置,确保其稳定不会移动。
2.3 预热工件:对于一些特殊材料或大尺寸工件,可以进行预热处理,以提高焊接效果。
三、波峰焊作业3.1 开始焊接:将预热好的工件放置在波峰焊机的焊接位置,启动波峰焊机进行焊接。
3.2 控制焊接时间:根据工件的要求,控制焊接时间,确保焊接质量。
3.3 检查焊接质量:焊接完成后,及时检查焊接质量,包括焊点是否完整、焊接是否均匀等。
四、焊后处理4.1 清洁焊接残渣:焊接完成后,及时清洁焊接残渣,以免影响下一次焊接的质量。
4.2 进行质量检测:对焊接完成的工件进行质量检测,确保焊接质量符合要求。
4.3 记录数据:对每次焊接的参数、时间、质量等数据进行记录,以便后续分析和改进。
五、安全注意事项5.1 穿戴防护装备:在进行波峰焊作业时,要穿戴好防护眼镜、手套等防护装备,确保安全。
5.2 避免操作失误:操作人员应经过专业培训,避免因操作失误导致事故发生。
5.3 定期维护设备:定期对波峰焊机进行维护保养,确保其正常运转。
结论:波峰焊作业指导书是确保波峰焊作业质量和效率的重要工具,操作人员应严格按照指导书的要求进行操作,确保焊接质量和安全。
同时,定期对设备进行维护保养,及时处理问题,以提高生产效率和产品质量。
波峰焊的使用操作流程

波峰焊的使用操作流程1. 准备工作在进行波峰焊前,需要准备以下工作:•检查设备和工具是否完好无损•准备焊接材料,如焊丝、焊盘等•清洁焊接区域,确保无杂质•确保焊接区域没有易燃物质2. 设定焊接参数在进行波峰焊前,需要设定合适的焊接参数,以确保焊接质量的稳定。
2.1 温度设定根据焊接材料和要求,设定合适的焊接温度。
一般来说,高温可以提高焊接速度,但可能会导致焊接缺陷。
低温则需要较长的焊接时间,但可以减少焊接缺陷。
2.2 波峰高度设定根据焊接材料和要求,设定合适的波峰高度。
波峰高度的设定直接影响到焊盘的引动效果。
波峰高度过高可能引发短路,而过低可能导致焊接不牢固。
2.3 速度设定根据焊接材料和要求,设定合适的焊接速度。
焊接速度的设定需要根据焊接材料的熔点和粘度来确定。
速度过快会导致焊接质量下降,速度过慢则会导致焊接时间延长。
3. 焊接操作流程3.1 元件安装将待焊接的元件按照布局图的要求安装在焊盘上。
确保元件与焊盘之间的接触良好,避免阻碍焊接过程。
3.2 流通液设置根据焊接要求,设置流通液的速度和压力。
流通液的作用是冷却焊接区域,防止元件热损伤和焊接缺陷。
3.3 波峰调整通过调整波峰的温度、高度和速度等参数,确保波峰的形状和引动效果符合要求。
3.4 基板加热使用专用的加热设备对焊盘进行加热,使焊盘的温度达到焊接要求的温度。
3.5 元件焊接将焊盘移动至焊接位置,并启动波峰焊设备。
确保焊接过程中元件保持稳定,避免移动和变形。
3.6 剪切清理焊接完成后,使用剪切工具将多余的焊丝剪除,保持焊接的整洁。
清理焊接区域,确保焊接留下的氧化物和焊剂等杂质被清除。
4. 检查与测试完成焊接后,需要进行检查和测试,以确保焊接质量。
4.1 目视检查通过目视检查,检查焊接区域是否有焊接缺陷,如焊接不牢固、焊盘短路等。
4.2 X射线检测对焊接区域进行X射线检测,以检测焊接接头的质量和焊点的连续性。
4.3 电阻测试使用电阻测试器对焊接区域进行电阻测试,以检测焊接点的电阻值是否符合要求。
波峰焊作业指导书
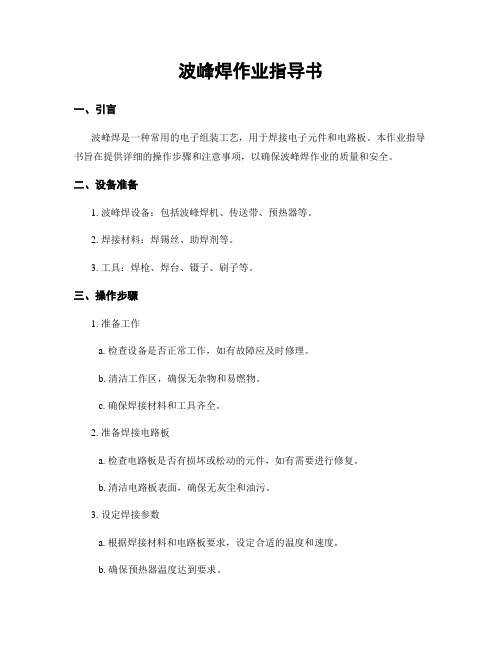
波峰焊作业指导书一、引言波峰焊是一种常用的电子组装工艺,用于焊接电子元件和电路板。
本作业指导书旨在提供详细的操作步骤和注意事项,以确保波峰焊作业的质量和安全。
二、设备准备1. 波峰焊设备:包括波峰焊机、传送带、预热器等。
2. 焊接材料:焊锡丝、助焊剂等。
3. 工具:焊枪、焊台、镊子、刷子等。
三、操作步骤1. 准备工作a. 检查设备是否正常工作,如有故障应及时修理。
b. 清洁工作区,确保无杂物和易燃物。
c. 确保焊接材料和工具齐全。
2. 准备焊接电路板a. 检查电路板是否有损坏或松动的元件,如有需要进行修复。
b. 清洁电路板表面,确保无灰尘和油污。
3. 设定焊接参数a. 根据焊接材料和电路板要求,设定合适的温度和速度。
b. 确保预热器温度达到要求。
4. 进行焊接a. 将电路板放置在传送带上,确保位置准确。
b. 使用焊枪将焊锡丝放置在焊台上,等待熔化。
c. 将焊枪放置在焊锡丝上方,使焊锡丝在焊枪的作用下均匀涂布在电路板焊盘上。
d. 确保焊接质量良好,焊点光滑均匀,无明显缺陷。
5. 检查和清理a. 检查焊接质量,确保焊点牢固可靠。
b. 清理焊接过程中产生的焊锡渣和杂物。
c. 对焊接过程中发现的问题进行记录和处理。
四、注意事项1. 操作人员应穿戴防护设备,如手套、护目镜等,以确保安全。
2. 在焊接过程中,应保持工作区域整洁,防止杂物干扰操作。
3. 操作人员应熟悉设备的使用方法和维护要求,如有问题应及时向相关人员咨询。
4. 焊接过程中应注意温度和速度的控制,以避免焊接质量不良。
5. 焊接后应及时清理焊接设备和工作区域,以保持设备的正常运行和工作环境的整洁。
五、常见问题及解决方法1. 焊接不牢固:可能是焊接温度不够高或焊接时间不够长,应适当调整参数。
2. 焊点出现缺陷:可能是焊接材料或助焊剂质量不好,应更换优质材料。
3. 焊接过程中出现短路:可能是电路板上的元件位置不准确,应仔细检查并修正。
六、总结波峰焊作业是一项重要的电子组装工艺,正确的操作步骤和注意事项能够保证焊接质量和安全。
波峰焊工作流程

波峰焊工作流程一、准备工作1.1 设备检查波峰焊设备就像我们干活的好伙伴,在开始工作之前,得好好检查它。
看看锡炉,就像查看炉灶是不是能正常生火做饭一样,锡量得合适,不能太多也不能太少,少了就像做饭没米,多了又容易溢出造成浪费和危险。
还有波峰发生器,这可是关键部件,就如同汽车的发动机,得确保它能正常产生波峰,不然焊接就没法顺利进行。
1.2 材料准备焊接用到的材料也不能马虎。
焊锡条就像建筑用的砖头,质量得过关。
要选择合适熔点和成分的焊锡条,不然就像穿错鞋子走路,怎么都不得劲。
助焊剂也很重要,它就像炒菜时的油,能让焊接过程更顺畅。
而且助焊剂的量要控制好,少了焊接效果不好,多了又可能留下残渣,就像糖放多了齁得慌。
二、电路板预处理2.1 清洁电路板就像要上战场的士兵,得干干净净的。
如果电路板上有油污、灰尘或者氧化物,那就像士兵带着伤病上战场,肯定影响战斗力。
所以要把电路板清理干净,这就好比给士兵疗伤,让它以最好的状态去接受焊接。
2.2 插件插件这一步就像给电路板组建队伍。
把各种电子元件准确无误地插到电路板上对应的位置,这得小心又小心,就像走钢丝一样,一个插错了,整个电路板可能就没法正常工作,那就成了“一着不慎,满盘皆输”。
三、焊接过程3.1 预热预热是焊接的前奏,就像跑步前的热身运动。
适当的预热可以让电路板和元件先适应一下高温环境,防止突然进入高温的锡炉时受到热冲击,就像人突然从寒冷的地方进入炎热的地方容易生病一样。
预热的温度和时间都要掌握好,不然就会前功尽弃。
3.2 焊接终于到了焊接这一重头戏。
电路板通过波峰焊设备,就像士兵穿过枪林弹雨。
锡液形成的波峰就像汹涌的海浪,把电路板上的焊点包裹起来,让元件和电路板牢牢地结合在一起。
这时候要时刻关注焊接的情况,确保每个焊点都焊接得饱满、光滑,没有虚焊或者短路的情况。
如果出现虚焊,就像盖房子时砖头没砌稳,随时可能出问题;短路就更严重了,就像电路里的交通堵塞,整个电路板就瘫痪了。
波峰焊操作规程

波峰焊操作规程一、引言波峰焊是一种常见的电子产品焊接方式,它通过将插件的引脚浸入熔化的焊锡中,实现焊接与固定。
为了保证焊接质量的稳定性和一致性,有必要制定一套详尽的波峰焊操作规程。
本文将介绍波峰焊操作规程的主要内容及步骤。
二、设备准备1. 检查设备在开始波峰焊操作之前,需要检查设备的工作状态。
确保焊接机、热风机和冷却装置等设备运行正常。
2. 准备焊锡及助焊剂选择合适的焊锡丝以及助焊剂,并保证其质量符合相关标准。
焊锡丝的直径、成分和熔点应根据焊接任务而确定。
三、钢网准备1. 检查钢网确保钢网的孔径、厚度和平整度符合要求。
检查钢网是否有损坏或变形,并及时更换。
2. 调整钢网高度根据焊接任务需求,调整钢网的高度。
确保钢网与插件引脚之间的距离符合要求,通常为2-3mm。
四、波峰焊操作步骤1. 设定焊接程序根据焊接任务的要求,在焊接机上设定相应的焊接程序。
确定焊接温度、波峰高度、预热时间等参数。
2. 开始预热启动焊接机,让其进行预热。
预热时间通常为5-10分钟,待设定温度达到后方可进行下一步操作。
3. 调整波峰高度根据焊接任务的要求,调整波峰高度。
通常情况下,波峰高度应略高于插件引脚的高度。
4. 准备插件将焊锡丝和助焊剂涂抹在插件的焊盘上,确保焊点涂覆均匀。
5. 插件定位将准备好的插件放置在钢网上,并调整位置,使其与焊点对齐。
6. 开始焊接将钢网缓慢地下移,插件的引脚将被浸入焊锡中。
要保持匀速下移,以确保焊接质量的稳定性。
7. 波峰焊完成当焊点完全浸入焊锡中后,继续下移一段距离,以确保焊点形成一定的柱状形态。
待上升时,焊点会被波峰除锡剂清除。
8. 冷却焊接完成后,打开冷却装置,将焊点快速冷却。
冷却时间通常为2-3分钟。
五、注意事项1. 运行时的注意事项在进行波峰焊操作时,操作人员应站立在稳定的位置上,并戴上相应的防护设备,如防静电手套、护目镜等。
2. 设备维护定期对波峰焊设备进行维护和保养,保持其正常工作状态,清理焊接头、钢网和焊炉等部件。
波峰焊使用方法掌握

波峰焊使用方法掌握过程:1.将波峰通道从锡炉中卸下。
2.将锡炉温度设置成280~300℃,升温,同时去除锡面浮渣。
3.当温度达到设置温度时,关闭加热器电源,自然降温。
4.自然降温至195℃左右时,开始打捞铜锡合金结晶体。
5.低于190℃时,停止打捞(需要时,重复2、3、4项)。
注意事项:1.280~300℃降至195℃的时间约1.5小时(因锡炉容量而异)。
2.约220℃时,可观察到锡面点、絮状的晶核产生。
随温度的进一步降低,晶核不断聚集增大,逐步形成松针状的CUSN结晶体。
3.195~190℃的时间约20分钟(因锡炉容量而异),打捞期间要快速有序。
4.打捞时漏勺要逐片捞取,切勿搅拌(结晶体受震动极易解体)。
5.打捞时漏勺提出锡面时要轻缓,要让熔融焊料尽量返回炉内。
6.CUSN结晶体性硬、易脆断,小心扎手!化学分析结果:两份取样(脆性体),铜含量分别为17WT%和22WT%。
补充说明:1.铜含量较CU6SN5低,是由于样品中的焊料无法分离的结果。
2.锡炉铜含量达0.25WT%时,凝固后的洁净锡面就可以观察到CU6SN5的结晶体(位置一般靠近结构件)。
铜含量达0.3WT%以上,每星期除一次(这时通道可不撤除,但需要把峰口撤掉,让锡面扩大,便于打捞),每次约5~10GK。
有铅焊料的铜含量已达0.25%是SMD焊接的一个界线,超过就容易发生桥接等焊接缺陷...。
捞前要将锡渣先清除干净了再降温...,然后在190C时打捞...,其他的仔细看一楼的步骤啊...。
波峰炉的工艺参数及常见问题的探讨一、工艺方面:工艺方面主要从助焊剂在波峰炉中的使用方式,以及波峰炉的锡波形态这两个方面作探讨;1、在波峰炉中助焊剂的使用工艺一般来讲有以下几种:发泡、喷雾、喷射等;A、当使用“发泡”工艺时,应该注意的是助焊剂中稀释剂添加的问题,因为助焊剂在使用过程中容易挥发,易造成助焊剂浓度的升高,如果不能及时添加适量的稀释剂,将会影响焊接效果及PCB 板面光洁程度;B、如果使用“喷雾”工艺,则不需添加或添加很少量的稀释剂,因为密封的喷雾罐能够有效地防止助焊剂的挥发,只需根据需要调整喷雾量即可;并要选择固含较低的最好不含松香树脂成份的,适合喷雾用的助焊剂;C、因为“喷射”时易造成助焊剂的涂布不均匀,且易造成原材料的浪费等原因,目前使用喷射工艺的已不多。
波峰焊工艺流程说明
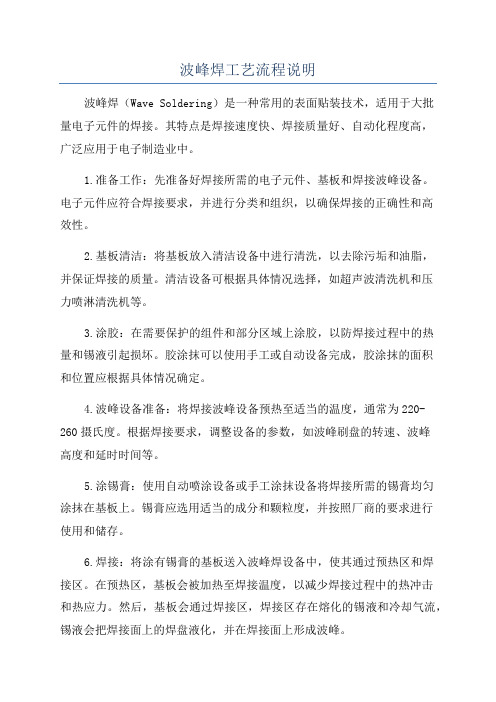
波峰焊工艺流程说明波峰焊(Wave Soldering)是一种常用的表面贴装技术,适用于大批量电子元件的焊接。
其特点是焊接速度快、焊接质量好、自动化程度高,广泛应用于电子制造业中。
1.准备工作:先准备好焊接所需的电子元件、基板和焊接波峰设备。
电子元件应符合焊接要求,并进行分类和组织,以确保焊接的正确性和高效性。
2.基板清洁:将基板放入清洁设备中进行清洗,以去除污垢和油脂,并保证焊接的质量。
清洁设备可根据具体情况选择,如超声波清洗机和压力喷淋清洗机等。
3.涂胶:在需要保护的组件和部分区域上涂胶,以防焊接过程中的热量和锡液引起损坏。
胶涂抹可以使用手工或自动设备完成,胶涂抹的面积和位置应根据具体情况确定。
4.波峰设备准备:将焊接波峰设备预热至适当的温度,通常为220-260摄氏度。
根据焊接要求,调整设备的参数,如波峰刷盘的转速、波峰高度和延时时间等。
5.涂锡膏:使用自动喷涂设备或手工涂抹设备将焊接所需的锡膏均匀涂抹在基板上。
锡膏应选用适当的成分和颗粒度,并按照厂商的要求进行使用和储存。
6.焊接:将涂有锡膏的基板送入波峰焊设备中,使其通过预热区和焊接区。
在预热区,基板会被加热至焊接温度,以减少焊接过程中的热冲击和热应力。
然后,基板会通过焊接区,焊接区存在熔化的锡液和冷却气流,锡液会把焊接面上的焊盘液化,并在焊接面上形成波峰。
7.冷却:基板离开焊接区后,通过冷却区进行冷却。
冷却区通常通过冷却风扇或冷却装置来实现,以使焊接后的电子元件迅速冷却,并保持其焊接质量。
8.检测:对焊接后的基板进行外观检测和功能测试,以确保焊接的质量和可靠性。
外观检测可以通过目视检查或辅助工具进行,功能测试需要使用相应的测试设备。
9.清理:清除焊接过程中产生的残留物,如焊渣和焊接剩余物。
清理可以通过手工或自动设备进行,以保持焊接面和基板的干净。
以上是波峰焊工艺的一般流程,具体的工艺参数和设备配置可以根据不同的焊接要求和生产情况进行调整和优化。
简述波峰焊的工艺流程 -回复

简述波峰焊的工艺流程-回复【波峰焊的工艺流程】波峰焊是一种广泛应用于电子组装行业的焊接技术,主要用于印刷电路板(PCB)上各种电子元器件的批量焊接。
其工艺流程精密且高效,主要包括以下步骤:一、预处理阶段1. 元件装载:首先,对已经过SMT贴片或其他方式固定好元器件的PCB进行检查,确保所有元器件正确无误且定位精确。
然后,将PCB放入专门设计的夹具或传送带上,准备进入波峰焊机。
2. 助焊剂涂敷:在波峰焊之前,需在PCB待焊接部位均匀涂敷助焊剂。
助焊剂的主要作用是清除氧化物、降低焊料与被焊金属之间的表面张力,从而提高焊接质量。
这一过程可以采用喷雾、浸泡或发泡等方式实现。
3. 预热处理:预热是为了减少PCB和元器件因温度突变而产生的热应力,并使助焊剂充分活化,去除PCB上的潮气及其它杂质。
预热温度通常设定在80-120之间,时间视PCB大小和厚度调整。
二、焊接阶段1. 接触波峰:经过预处理的PCB随着传送带进入焊接区,接触到由焊锡炉熔化的高温液态焊料形成的连续波峰。
此波峰高度一般略高于PCB上最大元器件引脚的高度,以保证所有引脚都能完全浸入焊料中。
2. 焊接过程:当PCB通过液态焊料波峰时,由于热传导效应,元器件引脚迅速加热至焊料熔点以上,形成冶金结合,完成焊接。
同时,助焊剂在此过程中发挥关键作用,消除氧化层并降低焊接界面的表面张力,确保焊接质量。
三、冷却与后处理阶段1. 冷却固化:焊接完成后,PCB会立即经过冷却区域,让焊点快速凝固以形成稳定的结构。
冷却速度应适中,过快可能会导致焊点内部产生内应力,过慢则可能导致焊点形状不佳或者焊料过多流失。
2. 清洗与检验:冷却后的PCB需要进行清洗,以去除残留的助焊剂和其他污染物,防止对后续工序或产品性能造成影响。
清洗完毕后,对PCB进行全面的目检和AOI(自动光学检测)等方法,确认焊点是否饱满、是否存在冷焊、虚焊、桥连等不良现象。
3. 修复与终检:对于发现的问题焊点,需要及时进行人工修复或返工。
波峰焊操作说明书
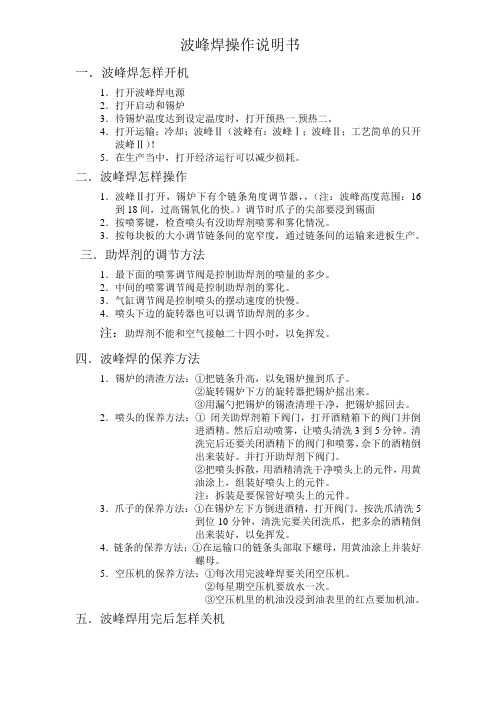
一.波峰焊怎样开机1.打开波峰焊电源2.打开启动和锡炉3.待锡炉温度达到设定温度时,打开预热一.预热二。
4.打开运输;冷却;波峰Ⅱ(波峰有:波峰Ⅰ;波峰Ⅱ;工艺简单的只开波峰Ⅱ)!5.在生产当中,打开经济运行可以减少损耗。
二.波峰焊怎样操作1.波峰Ⅱ打开,锡炉下有个链条角度调节器,,(注:波峰高度范围:16到18间,过高锡氧化的快。
)调节时爪子的尖部要浸到锡面2.按喷雾键,检查喷头有没助焊剂喷雾和雾化情况。
3.按每块板的大小调节链条间的宽窄度,通过链条间的运输来进板生产。
三.助焊剂的调节方法1.最下面的喷雾调节阀是控制助焊剂的喷量的多少。
2.中间的喷雾调节阀是控制助焊剂的雾化。
3.气缸调节阀是控制喷头的摆动速度的快慢。
4.喷头下边的旋转器也可以调节助焊剂的多少。
注:助焊剂不能和空气接触二十四小时,以免挥发。
四.波峰焊的保养方法1.锡炉的清渣方法:①把链条升高,以免锡炉撞到爪子。
②旋转锡炉下方的旋转器把锡炉摇出来。
③用漏勺把锡炉的锡渣清理干净,把锡炉摇回去。
2.喷头的保养方法:①闭关助焊剂箱下阀门,打开酒精箱下的阀门并倒进酒精。
然后启动喷雾,让喷头清洗3到5分钟。
清洗完后还要关闭酒精下的阀门和喷雾,佘下的酒精倒出来装好。
并打开助焊剂下阀门。
②把喷头拆散,用酒精清洗干净喷头上的元件,用黄油涂上,组装好喷头上的元件。
注:拆装是要保管好喷头上的元件。
3.爪子的保养方法:①在锡炉左下方倒进酒精,打开阀门。
按洗爪清洗5到位10分钟,清洗完要关闭洗爪,把多佘的酒精倒出来装好,以免挥发。
4.链条的保养方法:①在运输口的链条头部取下螺母,用黄油涂上并装好螺母。
5.空压机的保养方法:①每次用完波峰焊要关闭空压机。
②每星期空压机要放水一次。
③空压机里的机油没浸到油表里的红点要加机油。
五.波峰焊用完后怎样关机1.停止波峰焊的运输;波峰;冷却。
2.关闭锡炉;启动。
3.检查操作盘各键是否关闭。
4.关闭波峰焊的电源。
六.单面和双面板的工艺范围表1单面板的温度范围是:280℃到300 ℃预热一是:110℃到120℃预热二是:120℃到140℃速度范围是:快慢随意调动,速度和助焊剂是相辅的。
波峰焊作业指导书
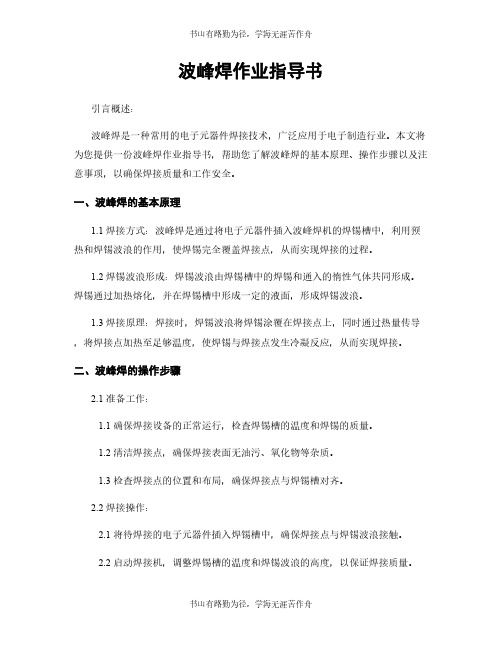
波峰焊作业指导书引言概述:波峰焊是一种常用的电子元器件焊接技术,广泛应用于电子制造行业。
本文将为您提供一份波峰焊作业指导书,帮助您了解波峰焊的基本原理、操作步骤以及注意事项,以确保焊接质量和工作安全。
一、波峰焊的基本原理1.1 焊接方式:波峰焊是通过将电子元器件插入波峰焊机的焊锡槽中,利用预热和焊锡波浪的作用,使焊锡完全覆盖焊接点,从而实现焊接的过程。
1.2 焊锡波浪形成:焊锡波浪由焊锡槽中的焊锡和通入的惰性气体共同形成。
焊锡通过加热熔化,并在焊锡槽中形成一定的液面,形成焊锡波浪。
1.3 焊接原理:焊接时,焊锡波浪将焊锡涂覆在焊接点上,同时通过热量传导,将焊接点加热至足够温度,使焊锡与焊接点发生冷凝反应,从而实现焊接。
二、波峰焊的操作步骤2.1 准备工作:1.1 确保焊接设备的正常运行,检查焊锡槽的温度和焊锡的质量。
1.2 清洁焊接点,确保焊接表面无油污、氧化物等杂质。
1.3 检查焊接点的位置和布局,确保焊接点与焊锡槽对齐。
2.2 焊接操作:2.1 将待焊接的电子元器件插入焊锡槽中,确保焊接点与焊锡波浪接触。
2.2 启动焊接机,调整焊锡槽的温度和焊锡波浪的高度,以保证焊接质量。
2.3 控制焊接时间,使焊锡与焊接点充分接触并冷凝。
2.3 检验焊接质量:3.1 检查焊接点的焊锡覆盖情况,确保焊锡完全涂覆焊接点。
3.2 使用显微镜检查焊接点的焊锡形状,确保焊锡呈现光滑、亮丽的外观。
3.3 进行焊接点的电性能测试,确保焊接点的电阻和导通性符合要求。
三、波峰焊的注意事项3.1 安全操作:在进行波峰焊作业时,必须佩戴防护手套、护目镜等个人防护装备,避免烫伤和眼部损伤。
3.2 焊接环境:确保焊接环境通风良好,避免焊锡烟雾对人体的危害。
3.3 设备维护:定期清洁焊锡槽,更换焊锡,确保设备的正常运行。
四、总结波峰焊作业指导书提供了波峰焊的基本原理、操作步骤以及注意事项。
正确理解和遵循这些指导,可以保证焊接质量和工作安全。
波峰焊操作规程

波峰焊操作规程波峰焊是一种常见的电子元器件焊接技术,它广泛应用于电子制造业中。
波峰焊的操作规程是指在进行波峰焊焊接时需要遵守的步骤和操作要求。
本文将为大家详细介绍波峰焊操作规程。
一、焊接前的准备工作在进行波峰焊之前,必须进行充分的准备工作。
1.检查焊接设备和工具:确保焊接设备和工具的完好,包括焊接机、焊盘、焊针、焊料等。
2.清洗焊料槽:波峰焊需要通过焊料槽进行焊料的加热和润湿元器件引脚的操作,所以焊料槽必须保持清洁,没有杂质。
3.调整焊接机参数:根据焊接工艺要求,调整焊接机的参数,包括焊接温度、波峰高度、波峰宽度、波峰速度等。
4.准备元器件和PCB板:确定需要焊接的元器件和对应的PCB板,进行检查和整理,确保无损坏、无偏差、无误装现象。
二、焊接操作步骤1.预热焊料槽:开启焊接机,将焊料槽加热至设定的温度,待焊料溶化后,确保焊料处于液态状态。
2.装载PCB板:将要焊接的PCB板放置在焊盘上,确保PCB板平稳且与焊盘接触良好。
3.调整焊接机参数:根据实际焊接需求,调整焊接机参数,确保波峰焊的质量和稳定性。
4.元器件安装:将需要焊接的元器件正确插入到PCB板上,注意对应焊接点位置,避免错位或倒装。
5.焊接操作:将已插入的元器件和PCB板一同送入焊料槽中,使其完全浸入焊料中。
保持一定的停留时间,让焊料充分润湿焊接点。
6.焊接完成:将焊接完成的PCB板从焊料槽中取出,放置在过水池中冷却并清洗焊料残留。
检查焊接点的焊接质量,确保焊点形成良好的焊接状态。
7.清洁设备和工具:将焊料槽中的焊料清除,清洁焊接机和焊接工具,备用下次使用。
三、注意事项在进行波峰焊时,还需要注意以下几个事项。
1.保持焊接环境干燥清洁:焊接环境应保持干燥,避免水汽或其他杂质进入焊料槽。
同时,焊接操作者应保持双手清洁,避免油脂或灰尘污染焊点。
2.注意焊接温度:焊接温度是影响焊接质量的重要因素,需要根据不同的元器件和焊接要求设定合理的温度值。
波峰焊的工艺流程
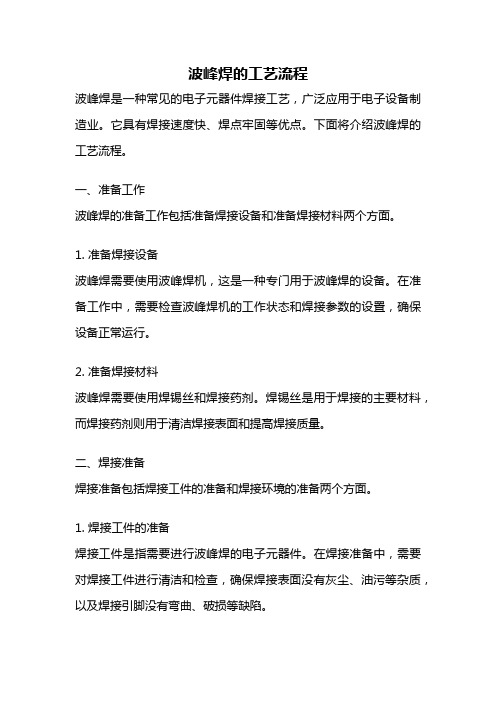
波峰焊的工艺流程波峰焊是一种常见的电子元器件焊接工艺,广泛应用于电子设备制造业。
它具有焊接速度快、焊点牢固等优点。
下面将介绍波峰焊的工艺流程。
一、准备工作波峰焊的准备工作包括准备焊接设备和准备焊接材料两个方面。
1. 准备焊接设备波峰焊需要使用波峰焊机,这是一种专门用于波峰焊的设备。
在准备工作中,需要检查波峰焊机的工作状态和焊接参数的设置,确保设备正常运行。
2. 准备焊接材料波峰焊需要使用焊锡丝和焊接药剂。
焊锡丝是用于焊接的主要材料,而焊接药剂则用于清洁焊接表面和提高焊接质量。
二、焊接准备焊接准备包括焊接工件的准备和焊接环境的准备两个方面。
1. 焊接工件的准备焊接工件是指需要进行波峰焊的电子元器件。
在焊接准备中,需要对焊接工件进行清洁和检查,确保焊接表面没有灰尘、油污等杂质,以及焊接引脚没有弯曲、破损等缺陷。
2. 焊接环境的准备焊接环境需要保持整洁、安静,以减少焊接过程中的干扰和误操作。
此外,还需要确保焊接环境的温度和湿度适宜,以保证焊接质量。
三、焊接过程波峰焊的焊接过程主要包括上锡、预热、焊接和冷却四个阶段。
1. 上锡上锡是波峰焊的第一步,也是最关键的一步。
在上锡阶段,需要将焊锡丝通过波峰焊机的焊锡槽加热熔化,并将焊锡液槽中的焊锡液上升至波峰区域。
然后,将焊接工件的焊接表面浸入焊锡液中,使焊锡液覆盖住焊接表面,形成一层均匀的焊锡涂层。
2. 预热上锡后,需要对焊接工件进行预热。
预热的目的是提高焊接质量,减少焊接过程中的热应力。
在预热阶段,需要将焊接工件放置在预热区域,使其温度逐渐升高,直到达到预定的焊接温度。
3. 焊接预热后,进入焊接阶段。
在焊接阶段,需要将预热后的焊接工件通过传送带送入焊接区域。
焊接区域有一个波峰,由焊锡液形成。
当焊接工件经过波峰时,焊锡液会涂覆在焊接表面上,形成焊点。
焊接工件经过波峰后,焊点会冷却固化。
4. 冷却焊接完成后,需要对焊接工件进行冷却。
冷却的目的是使焊点固化,确保焊接质量。
- 1、下载文档前请自行甄别文档内容的完整性,平台不提供额外的编辑、内容补充、找答案等附加服务。
- 2、"仅部分预览"的文档,不可在线预览部分如存在完整性等问题,可反馈申请退款(可完整预览的文档不适用该条件!)。
- 3、如文档侵犯您的权益,请联系客服反馈,我们会尽快为您处理(人工客服工作时间:9:00-18:30)。
(3) 每天清理波峰喷嘴和焊料锅表面的氧化物等残渣。 (4) 坚持定期设备维护,使设备始终保持在正常运行状态。 (5) 把日常发生的质量问题记录下来,定期做总结、分析, 累经验。
印制焊盘、元器件端头和引脚表面的氧化膜以及其它污染 物,时起到保护金属表面防止发生再氧化的作用;
c 使印制板和元器件充分预热,避免焊接时急剧升温 产生应力损坏印制板和元器件。
印制板预热温度和时间要根据印制板的大小、厚度、元 器件大小和多少、以及贴装元器件的多少来确定。预热温度 在90~130℃(PCB表面温度),多层板以及有较多贴装元 器件时预热温度取限,不同PCB类型和组装形式的预热温度 参考表8-1。参考时一定结合组装板的具体情况,做工艺试 验或试焊后进行设置。有条件可测实时温度曲线。预热时间 由传送带速度来控制。如预热温度低或和预热时间过短,焊 剂中的溶剂挥发不充分,焊接时产生气引起气孔、锡球等焊 接缺陷;如预热温度偏高或预热时间过长,剂被提前分解, 使焊剂失去活性,同样会引起毛刺、桥接等焊接陷。因此要 恰当控制预热温度和时间,最佳的预热温度是在波峰前涂覆 在PCB底面的焊剂带有粘性。
(a)爬坡角度小,焊接时间长
(b) 爬坡角度大,焊接时间短
图8-7 传送带倾斜角度与焊接时间的关系
5.8.5 工艺参数的综合调整 工艺参数的综合调整对提高波峰焊质量是非常重要的。 焊接温度和时间是形成良好焊点的首要条件。焊接温度
和时间与预热温度、焊料波的温度、倾斜角度、传输速度都 有关系。
综合调整工艺参数时首先要保证焊接温度和时间。双波 峰焊的第一个波峰一般在235~240℃/1s 左右, 第二个波峰 一般在240~260℃/3s左右。两个波峰的总时间控制在10s以 内。
d 金属化孔质量差或阻焊剂流入孔中。 反映给印制板加工厂,提高加工质量。
e 波峰高度不够。不能使印制板对焊料 波峰高度一般控制在印制板厚度的2/3 处。
波产生压力,不利于上锡。
f 印制板爬坡角度偏小,不利于焊剂排气。 印制板爬坡角度为3-7°。
(2) 焊料过多——元件焊端和引脚 周围被过多的焊料包围,或焊点中 间裹有气泡,不能形成标准的弯月 面焊点。润湿角θ>90°
5.8 波峰焊工艺参数控制要点
5.8.1 焊剂涂覆量 要求在印制板底面有薄薄的一层焊剂,要均匀,不能
太厚,对于免清洗工艺特别要注意不能过量。焊剂涂覆 量要根据波峰焊机的 焊剂涂覆系统,以及采用的焊剂类型进行设置。焊剂涂 覆方法主要有涂刷、发泡及定量喷射两种方式。
① 采用涂刷与发泡方式时,必须控制焊剂的比重。焊剂的 比重一般控制在0.8-0.84之间(液态松香焊剂原液的比 重),焊接过程中随着时间的延长,焊剂中的溶剂会逐渐 挥发,使焊剂的比重增大,其黏度随之增大,流动性也随 之变差,影响焊剂润湿金属表面,妨碍熔融的焊料在金属 表面上的润湿,引起焊接缺陷,因此采用传统涂刷及发泡 方式时应定时测量焊剂的比重,如发现比重增大,应及时 用稀释剂调整到正常范围内,但稀释剂不能加入过多,比 重偏低会使焊剂的作用下降,对焊接质量也会造成不良影 响。另外还要注意不断补充焊剂槽中的焊剂量,不能低于 最低极限位置。
预防对策
预热温度在90—130℃,有较多贴装元 器件时预热温度取上限;锡波温度为 250±5℃,焊接时间3~5s。 插装孔的孔径比引脚直经0.15~0.4mm (细引线取下限,粗引线取上限)。
c 插装元件细引线大焊盘,焊料被拉到
焊盘尺寸与引脚直径应匹配,要有利于
焊盘上,使焊点干瘪。
形成弯月面的焊点。
5.10 波峰焊常见焊接缺陷分析及预防对策 随着目前元器件变得越来越小,PCB组装密度越来越
密,另外由于免清洗助焊剂不含卤化物,固体含量不能超 过2%,因此去氧化和助焊作用大大减小,使波峰焊工艺的 难度越来越大。
5.10.1 影响波峰焊质量的因素 a 设备——助焊剂喷涂系统的可控制性;预热和焊接温
5.8.4 印制板爬坡(传送带倾斜)角度和波峰高度 印制板爬坡角度为3-7°,有利于排除残留在焊点和元
件周由焊剂产生的气体,有SMD时,通孔比较少,爬坡角 度应大一些。
适当的爬坡角度还可以少量调节焊接时间。 适当的波峰高度使焊料波对焊点增加压力和流速有利于 焊料湿金属表面、流入小孔,波峰高度一般控制在印制板 厚度的2/处
每天结束工作后应清理残渣
(3) 焊点拉尖——或称冰柱。 焊点顶部拉尖呈冰柱状,小旗状。
焊点拉尖产生原因
预防对策
PCB 预热温度过低,使PCB 与元器件 根据PCB 尺寸、是否多层板、元器件 温偏低,焊接时元件与PCB 吸热。 多少、有贴装元器件等设置预热温度。
预热温度在90~130℃,有较多贴装元器 件时预热温度取上限。
5.5 根据首件焊接结果调整焊接参数 5.6 连续焊接生产
a 方法同首件焊接。 b 在波峰焊出口处接住PCB,检查后将PCB装入防静电 周转箱送修后附工序(或直接送连线式清洗机进行清洗)。 c 连续焊接过程中每块印制板都应检查质量,有严重焊 接缺陷的制板,应立即重复焊接一遍。如重复焊接后还存
在问题,应检查原对工艺参数作相应调整后才能继续焊接。
焊接时间= 焊点与波峰的接触长度/传输速度 焊点与波峰的接触长度可以用一块带有刻度的耐高温玻 璃测试板走一次波峰进行测量。 传输速度是影响产量的因素。在保证焊接质量的前提下, 通过合理的综合调整各工艺参数,可以实现尽可能的提高产 量的
5.9 波峰焊质量控制方法
(1) 严格工艺制度 每小时记录一次温度等焊接参数。定时或对每块印制板进行 后质量检查,发现质量问题,及时调整参数,采取措施。
b 用比重计测量助焊剂比重,若比重大,用稀释剂稀释。 c 将助焊剂倒入助焊剂槽
5.2 开炉 a 打开波峰焊机和排风机电源。 b 根据PCB宽度调整波峰焊机传送带(或夹具)的宽度
5.3 设置焊接参数 a 发泡风量或助焊剂喷射压力:根据助焊剂接触PCB底面的
情况定。 b 预热温度:根据波峰焊机预热区的实际情况设定 c 传送带速度:根据不同的波峰焊机和待焊接PCB的情况设
5 波峰焊操作步骤
5.1 焊接前准备 a 在待焊PCB(该PCB已经过涂敷贴片胶、SMC/SMD贴
片、胶固并完成THC插装工序)后附元器件插孔的焊接面涂 阻焊剂或粘贴耐温粘带,以防波峰焊后插孔被焊料堵塞。如 有较大尺寸的槽和孔应用耐高温粘带贴住,以防波峰焊时焊 锡流到PCB的上表面。(如溶性助焊剂只能采用阻焊剂,涂 敷后放置30min或在烘灯下烘15min 再插装元器件,焊接后可直接水清洗)
(a) 插装元器件焊点
(b)贴装元件焊点
图8 插装元器件和贴装元件焊点润湿示意图
c 虚焊和桥接等缺陷应降至最少; d 焊接后贴装元件无损坏、无丢失、端头电极无脱落; e 要求插装元器件的元件面上锡好(包括元件引脚和金 属化)。 f 焊接后印制板表面允许有微小变色,但不允许严重变 色,不允阻焊膜起泡和脱落。
作用复杂过程,必须控制好焊接温度和时间,如焊接温度 偏低。液体料的黏度大,不能很好地在金属表面润湿和扩 散,容易产生拉尖桥连、焊点表面粗糙等缺陷;如焊接温 度过高,容易损坏元器件还会产生焊点氧化速度加快、焊 点发乌、焊点不饱满等问题。
根据印制板的大小、厚度、印制板上搭载元器件的大小 和多来确定波峰焊温度,波峰温度一般为250±5℃(必须 测打上来的际波峰温度)。由于热量是温度和时间的函数, 在一定温度下焊和元件受热的热量随时间的增加而增加, 波峰焊的焊接时间通过整传送带的速度来控制,传送带的 速度要根据不同型号波峰焊机长度、波峰的宽度来调整, 以每个焊点接触波峰的时间来表示焊或 引脚长,使引脚底部不能与波峰接 触。因为磁泵波峰焊机是空心波, 空心波的厚度4~5mm 左右, 助焊剂活性差
波峰高度一般控制在印制板厚度的2/3 处。插元器件引脚成形要求元件引脚 露出印制板焊接0.8~3mm。
更换助焊剂。
插装元件引线直经与插装孔比例不 正,插装孔过大,大焊盘吸热量大。
5.7 检验 检验方法:目视或用2-5倍放大镜观察。 检验标准:
a 焊接点表面应完整、连续平滑、焊料量适中,无大 气孔、砂眼;
b焊点的润湿性好,呈弯月形状,插装元件的润湿角θ 应小于90°,以15—45°为最好,见图8(a);片式元件 的润湿角θ小于90°,焊料应在片式元件金属化端头处 全面铺开,形成连续均匀的覆盖层,见图8(b);
(0.8—1.92m/min) d 焊锡温度:(必须是打上来的实际波峰温度为250±5℃
时的表显示温度)
5.4 首件焊接并检验(待所有焊接参数达到设定值后进行) a 把PCB轻轻地放在传送带(夹具)上,机器自动进行
喷涂助焊、干燥、预热、波峰焊、冷却。 b 在波峰焊出口处接住PCB。 c 进行首件焊接质量检验。
度。PCB 底面温度在90—130℃,有 较多贴装元器件时预热温度取上限。
c 焊剂活性差或比重过小
更换焊剂或调整适当的比重。
e 焊料中锡的比例减少,或焊料中杂 质Cu成分过高(Cu<0.08%),使熔 融焊料黏度增加、流动性变差。
锡的比例<61.4%时,可适量添加一 些纯锡,杂质过高时应更换焊料。
f 焊料残渣太多
插装孔的孔径比引线直经大 0.15~0.4mm(细引取下限,粗引线取 上限)。
4) 焊点桥接或短路——桥接又称连 桥。元件端头之、元器件相邻的焊点之间以及焊点与邻近 的导线、孔等电气上不该连接的部位被焊锡连接在一起
焊点桥接或短路产生原因
预防对策
PCB 设计不合理,焊盘间距过窄。 按照PCB设计规范进行设计。两个端头 Chip 的长轴焊接方向垂直,SOT、SOP 的长轴应与焊接方向平行将SOP 最后一个 引脚的焊盘加宽(设计一个窃锡焊
度控制系统的稳定性;波峰高度的稳定性及可调整性;传输 系统的平稳性;以及是否配置了扰流(震动)波、热风刀、 氮气保护等功能。