重介旋流器
重介质旋流器综述

重介质旋流器综述重介质旋流器的发展重介质旋流器,它是从分级浓缩旋流器演变而来的,它是用重悬浮液或重液作为介质,在外加压力产生的离心场和密度场中,把轻产物和重产物进行分离的一种特定结构的设备。
是目前重力选煤方法效率最高的一种。
1891年美国公布了分级浓缩旋流器专利;1945年荷兰国家矿山局(Duth State mines)在分级旋流器的基础上,研制成功第一台圆柱圆锥形重介质旋流器,用黄土作加重质配制悬浮液进行了选煤中间试验。
因为黄土作加重质不能配成高密度悬浮液,而且回收净化困难,所以在工业生产上未能得到实际应用。
只有在采用了磁铁矿粉作为加重质之后,才使这一技术在工业上得到推广。
这是因为磁铁矿粉能够配制成适合于选煤使用的不同密度的悬浮液,而且易于用磁力净化回收的缘故。
随后,美、德、英、法等国相继购买了这一专利,并在工业使用中,对圆柱圆锥形重介质旋流器做了不同的改进,派生出一批新的、不同型号的重介质旋流器。
如1956年美国维尔莫特(Wilmont)公司研制成功的无压给煤圆筒形重介质旋流器,简称DWP;60年代英国研制成有压给料圆筒形重介质旋流器,即沃赛尔(Vorsyl)旋流器;1966年原苏联研制成功,用一台圆柱形旋流器与另一台圆柱圆锥旋流器并相串联组成“有压”和“无压”三产品旋流器。
1967年日本田川机械厂研制成倒立式圆柱圆锥形重介质旋流器,即涡流(Swirl)旋流器,80年代初意大利学者研制成用两台圆筒形旋流器轴线串联组成(Tri-Flo)三产品重介质旋流器;80年代中期英国煤炭局在吸收DWP和沃赛尔两种旋流器的特点,推出直径为1200mm 的中心给料圆筒形重介质旋流器(Large Coal Dense medium),用于分选粒度为100~0.5mm的原煤。
中国重介质选煤,从1958年在吉林省通化矿务局铁厂选煤厂建成第一个重介选煤车间。
1966年又在辽宁省采屯煤矿选煤厂建成重介质旋流器选煤车间。
重介旋流器操作和维护说明书

目录页码1.介绍与使用说明 (2)2.安装 (3)3.操作变量与说明 (4)4.故障排除 (5)5.起吊与存放说明 (6)6.图纸翻译 (7)1.介绍与使用说明重介质旋流器是一种按比重或密度来分离原矿中轻、重物料的设备。
它的设计较适用于煤的加工,因为它有很高的处理轻质成分(清洁煤)的能力,一般情况,进料的主要组成为轻质的物料。
重介质旋流器包括一个切向进口,它使材料进入旋流器机体内的平行边的圆柱形部分。
旋流器的直径以这一平行体部分的内径为基础。
旋流器的机体连接着一个圆锥形或者说逐渐缩小的部分,该锥顶处装有一个可拆卸的(活)喷嘴。
安装在平行体部分和旋流器机体进口处的是一根加长管,它被居中放置在称为涡流定向器的旋流器体的轴线上,这根管子沿两个方向延伸至机罩内,该卸载机罩可以根据大多数工厂布局的要求放置。
进给材料以矿浆(含有固体煤和由水、磁铁矿构成的传输介质)的形式进入旋流器,由于磁铁矿精细的尺寸,传输介质形成了一种“伪液体”,通常均匀地散布于水中,“伪液体”的相对密度显然大于水。
根据给定的煤颗粒自身的密度及液体介质的密度,在重于水的环境中浸没的颗粒或上升至液体表面,呈现为旋流器中朝着涡流定向器流动的空心体;或下沉至旋流器机壁的介质中并经阀门排出。
“浮”和“沉”这两个术语充分描述了相关的材料的情况。
其密度等于或非常接近液体介质密度的煤的颗粒称作“近似比重材料”。
这些颗粒受诸多因素,比如粘滞作用,分离效率等的影响,可以归类为”浮“或”沉“产品。
在重介质型旋流器中,分离的过程进行得非常快,隔离/分离进料的时间少于五秒,进料进入旋流器之后因旋转运动被施以巨大离心力,从而获得很高的分离效率。
分离不依赖需要较长工作时间的引力,因此旋流器的工作不受安装方位范围的限制,这是因为在旋流器里面的分离环境中,径向力和切向力大大超过了重力。
所产生的径向力约为75G。
高密度的煤和页岩颗粒(含有较大比例的灰粉成分)在通过切向进口进入旋流器机体之后在力的作用之下围绕旋流器机体的内壁形成旋转的材料层。
选煤常识-重介质旋流器

形式和以前的一样,时间为5月22日三产品重介质旋流器三产品重介质旋流器,用一种密度的悬浮液系统可选出三种最终产品,省掉了一套高密度悬浮液系统及设备,大大简化了工艺流程。
设备,投资和厂房体积均可降低15%以上。
一、大型无压三产品旋流器系统及特点1、大型无压三产品旋流器的结构、原理及工作过程(见图6—12)。
图6—12大型无压给料三产品旋流器是由一台圆筒形旋流器和一台圆筒圆锥旋流器串联而成的设备,原煤由刮板给入,一段旋流器悬浮液由泵给入。
其分选过程是重产物在旋流器内沿筒壁形成外螺旋由底流口排出,轻产物在旋流器中心形成内螺旋由溢流口排出,从低密度到高密度。
在第一段旋流器中不但可以把原煤分成两种产品,而且还把进入第二段旋流器的悬浮液浓缩到需要的密度。
重产品与浓缩后的悬浮液一起经连接管给入第二段旋流器进行再选,最终获得中煤和矸石。
2、大型无压给料三产品旋流器系统的特点①入洗粒度范围较宽,有效分选下限低。
跳汰机入料粒度50mm以下,分选下限0.5mm,而三产品旋流器入料粒度80mm以下,可有效分选到0.3mm。
②次生煤泥少。
由于物料靠自重进入旋流器,介质液由泵沿切线给入,减少了物料之间的碰撞机率,且重产物运行路线短,从而可减少3—5%次生煤泥量,旋流器分选时间短,水量小,可减少泥化,更有利于易泥化煤的分选;可使浮选系统入料量大幅度减少,预计可减少1/4入浮煤泥量,从而降低了浮选的成本。
③分选精度高。
用三产品重介旋流器洗选,由于采用轴向中心给料,减少了界面上循环物料的干扰,提高了分选效果,一般Ep1≤0.04,Ep2≤0.06。
也使原煤分选易于控制,矸石损失降低,精煤产率提高。
与跳汰工艺相比,用三产品重介旋流器洗选,可提高产率5%左右,使矸石损失降至3%以下,而且可保证精煤质量。
④有利于实现自动化控制,减小工作量,降低劳动强度。
⑤整个系统简单有效。
下面是三产品重介旋流器流程示意图,图6—13。
图6—13⑥容易实现煤泥重介分选。
无压三产品重介质旋流器工作原理

无压三产品重介质旋流器工作原理引言旋流器是一种重要的固液分离设备,在许多工业领域有着广泛的应用。
无压三产品重介质旋流器是近年来引入的一种新型旋流器,具有较高的分离效率和处理能力。
本文将详细介绍无压三产品重介质旋流器的工作原理及其应用。
旋流器的基本原理旋流器是通过高速旋转产生的离心力实现固液分离的设备。
其基本原理是将待处理的流体分为内旋流和外旋流两部分,随着流体在旋转过程中的离心力增大,固体颗粒被迫向内旋流移动,最终被集中排出。
传统旋流器的不足传统的旋流器存在一些问题,如分离效率低、易堵塞、处理能力有限等。
为了解决这些问题,无压三产品重介质旋流器应运而生。
无压三产品重介质旋流器的工作原理无压三产品重介质旋流器是在传统旋流器的基础上改进而来的。
它具有三个输出口,分别用于排出固相、液相和重介质。
其工作原理如下:1. 初始状态无压三产品重介质旋流器的初始状态为向旋流器内输入待处理的流体。
流体在旋流器内部形成一个旋转的涡流。
2. 内部分离随着旋转速度的增加,流体中的固相开始受到离心力的作用,向内旋流移动。
同时,重介质也会沉积在旋流器的底部。
3. 外部分离固相进一步向内旋流移动,最终通过固相排出口被集中排出。
液相则向外旋流移动,经过液相排出口排出。
4. 重介质回收重介质在旋流器底部积聚,经由重介质排出口排出,并进行回收和再利用。
无压三产品重介质旋流器的应用无压三产品重介质旋流器在多个领域有着广泛的应用,包括但不限于:1. 石油工业在石油开采过程中,常常需要进行固液分离。
无压三产品重介质旋流器可以高效地分离油水混合物,将固相和重介质分别排出,使油水分离更加彻底。
2. 矿山工业在矿山中,常常需要对含有矿石颗粒的水进行处理。
无压三产品重介质旋流器可以将固相颗粒和重介质分离,实现固液分离,从而提高矿石提取效率。
3. 食品加工在食品加工过程中,常常需要进行污水处理和固液分离。
无压三产品重介质旋流器可以高效地将固相和重介质分离,使污水净化更加彻底。
无压三产品重介质旋流器工作原理
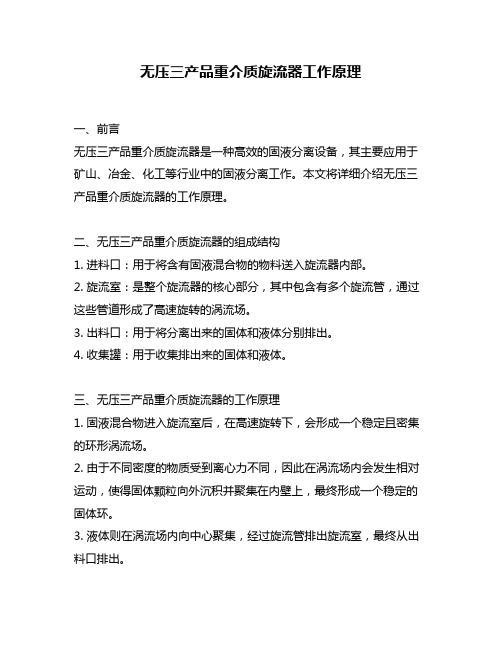
无压三产品重介质旋流器工作原理一、前言无压三产品重介质旋流器是一种高效的固液分离设备,其主要应用于矿山、冶金、化工等行业中的固液分离工作。
本文将详细介绍无压三产品重介质旋流器的工作原理。
二、无压三产品重介质旋流器的组成结构1. 进料口:用于将含有固液混合物的物料送入旋流器内部。
2. 旋流室:是整个旋流器的核心部分,其中包含有多个旋流管,通过这些管道形成了高速旋转的涡流场。
3. 出料口:用于将分离出来的固体和液体分别排出。
4. 收集罐:用于收集排出来的固体和液体。
三、无压三产品重介质旋流器的工作原理1. 固液混合物进入旋流室后,在高速旋转下,会形成一个稳定且密集的环形涡流场。
2. 由于不同密度的物质受到离心力不同,因此在涡流场内会发生相对运动,使得固体颗粒向外沉积并聚集在内壁上,最终形成一个稳定的固体环。
3. 液体则在涡流场内向中心聚集,经过旋流管排出旋流室,最终从出料口排出。
4. 由于固体和液体的密度不同,因此在旋流室内形成了两个不同密度的环,其中固体环与液体环之间的分界面称为分离面。
5. 分离面位置可以通过调整进料流量、旋流管数量和大小等参数来实现。
四、无压三产品重介质旋流器的优势1. 高效:由于采用了高速旋转的涡流场进行分离,因此可以达到很高的分离效率。
2. 稳定:无压三产品重介质旋流器采用了多个旋流管进行分离,因此具有更好的稳定性和可靠性。
3. 适应性强:无压三产品重介质旋流器适用于各种不同颗粒大小和密度范围内的物料分离。
4. 维护简单:无压三产品重介质旋流器结构简单、易于维护,并且使用寿命长。
五、总结无压三产品重介质旋流器是一种高效、稳定且适应性强的固液分离设备,其工作原理是通过高速旋转的涡流场将不同密度的物质分离出来。
在实际应用中,需要根据不同物料的特性和要求进行参数调整,以达到最佳的分离效果。
重介质旋流器
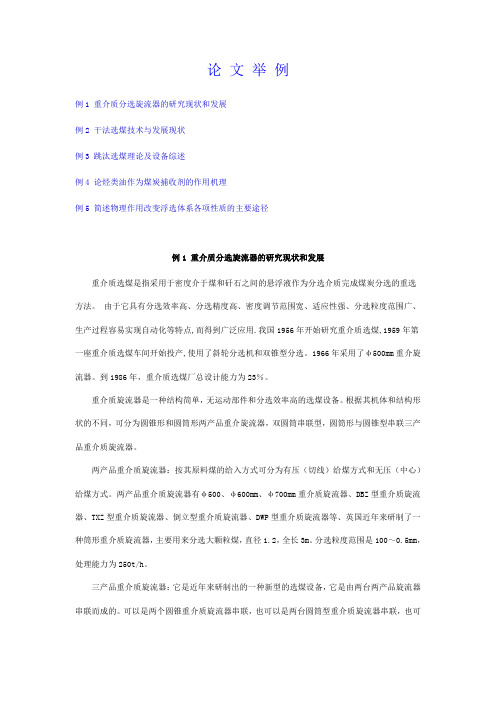
论文举例例1 重介质分选旋流器的研究现状和发展例2 干法选煤技术与发展现状例3 跳汰选煤理论及设备综述例4 论烃类油作为煤炭捕收剂的作用机理例5 简述物理作用改变浮选体系各项性质的主要途径例1 重介质分选旋流器的研究现状和发展重介质选煤是指采用于密度介于煤和矸石之间的悬浮液作为分选介质完成煤炭分选的重选方法。
由于它具有分选效率高、分选精度高、密度调节范围宽、适应性强、分选粒度范围广、生产过程容易实现自动化等特点,而得到广泛应用.我国1956年开始研究重介质选煤,1959年第一座重介质选煤车间开始投产,使用了斜轮分选机和双锥型分选。
1966年采用了φ500mm重介旋流器。
到1986年,重介质选煤厂总设计能力为23%。
重介质旋流器是一种结构简单,无运动部件和分选效率高的选煤设备。
根据其机体和结构形状的不同,可分为圆锥形和圆筒形两产品重介旋流器,双圆筒串联型,圆筒形与圆锥型串联三产品重介质旋流器。
两产品重介质旋流器:按其原料煤的给入方式可分为有压(切线)给煤方式和无压(中心)给煤方式。
两产品重介质旋流器有φ500、φ600mm、φ700mm重介质旋流器、DBZ型重介质旋流器、TXZ型重介质旋流器、倒立型重介质旋流器、DWP型重介质旋流器等、英国近年来研制了一种筒形重介质旋流器,主要用来分选大颗粒煤,直径1.2,全长3m。
分选粒度范围是100~0.5mm,处理能力为250t/h。
三产品重介质旋流器:它是近年来研制出的一种新型的选煤设备,它是由两台两产品旋流器串联而成的。
可以是两个圆锥重介质旋流器串联,也可以是两台圆筒型重介质旋流器串联,也可是一台圆筒和一台圆锥重介质旋流器串联,其中圆筒型重介质旋流器又分无压和有压两种。
因此,三产品重介质旋流器有多种不同的组合形式。
三产品重介质旋流器的优点是用一种悬浮液形成两个分选密度,省掉一个悬浮液循环系统和再选物料运输系统,但是由于第二段悬浮液入料由第一段旋流器浓缩而来,因此二段分选密度因测量较为困难,密度调节主要靠调节一段入料悬浮液密度和二段旋流器底流口大小。
大型无压给料三产品重介质旋流器介绍
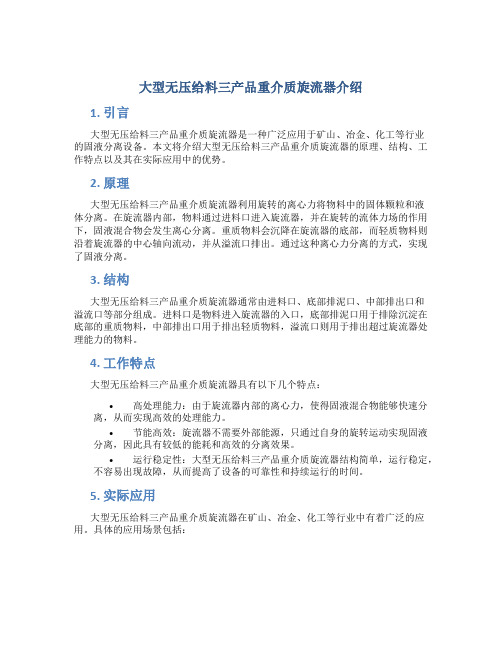
大型无压给料三产品重介质旋流器介绍1. 引言大型无压给料三产品重介质旋流器是一种广泛应用于矿山、冶金、化工等行业的固液分离设备。
本文将介绍大型无压给料三产品重介质旋流器的原理、结构、工作特点以及其在实际应用中的优势。
2. 原理大型无压给料三产品重介质旋流器利用旋转的离心力将物料中的固体颗粒和液体分离。
在旋流器内部,物料通过进料口进入旋流器,并在旋转的流体力场的作用下,固液混合物会发生离心分离。
重质物料会沉降在旋流器的底部,而轻质物料则沿着旋流器的中心轴向流动,并从溢流口排出。
通过这种离心力分离的方式,实现了固液分离。
3. 结构大型无压给料三产品重介质旋流器通常由进料口、底部排泥口、中部排出口和溢流口等部分组成。
进料口是物料进入旋流器的入口,底部排泥口用于排除沉淀在底部的重质物料,中部排出口用于排出轻质物料,溢流口则用于排出超过旋流器处理能力的物料。
4. 工作特点大型无压给料三产品重介质旋流器具有以下几个特点:•高处理能力:由于旋流器内部的离心力,使得固液混合物能够快速分离,从而实现高效的处理能力。
•节能高效:旋流器不需要外部能源,只通过自身的旋转运动实现固液分离,因此具有较低的能耗和高效的分离效果。
•运行稳定性:大型无压给料三产品重介质旋流器结构简单,运行稳定,不容易出现故障,从而提高了设备的可靠性和持续运行的时间。
5. 实际应用大型无压给料三产品重介质旋流器在矿山、冶金、化工等行业中有着广泛的应用。
具体的应用场景包括:5.1 矿山行业在矿山行业中,大型无压给料三产品重介质旋流器主要用于煤矸石的分离,可以将煤矸石中的煤炭和岩石分离出来,从而提高矿石的品位,减少对环境的影响。
5.2 冶金行业在冶金行业中,大型无压给料三产品重介质旋流器可以用于铝土矿、锌矿、铅矿等矿石的分离,提高矿石的品位和冶炼效率。
5.3 化工行业在化工行业中,大型无压给料三产品重介质旋流器可以用于液体和固体的分离,如酸碱废水的处理、有机物质的分离等。
无压三产品重介旋流器精煤产品带矸原因分析及对策

无压三产品重介旋流器精煤产品带矸原因分析及对策(总3页)-CAL-FENGHAI.-(YICAI)-Company One1-CAL-本页仅作为文档封面,使用请直接删除无压三产品重介旋流器精煤产品带矸原因分析及对策1 重介质旋流器选煤原理重介质旋流器是一种结构简单,分选效率高的选煤设备。
由于旋流器本身无运动部件,因而其分选过程完全是靠自身的结构参数与外部操作参数的灵活配合来实现最佳分选精度,这是旋流器选煤与其他选煤方法截然不同的突出特征。
在重介质旋流器分选过程中,物料和悬浮液以一定压力沿切线方向给入旋流器,形成强有力的旋涡流;液流从入料口开始沿旋流器内壁形成一个下降的外螺旋流;在旋流器轴心附近形成一股上升的内螺旋流;由于内螺旋流具有负压而吸入空气,在旋流器轴心形成空气柱;入料中的精煤随内螺旋流向上,从溢流口排出,矸石随外螺旋流向下,从底流口排出.2 无压三产品重介旋流器及其存在问题无压三产品重介旋流器 ( 图 1) 工作过程中,循环介质以一定的压力在一段旋流器的下部沿切线方向给入, 入选物料则在一段旋流器的筒体上端靠旋流器中心空气柱的真空吸气及自重作用进入旋流器, 有少部分循环悬浮液给到入料漏斗中对原煤起润湿作用;物料在旋流器内回转运动的悬浮液中得到快速分选, 高密度物料随浓缩的重悬浮液进入第二段旋流器分选, 而低密度物在第一段旋流器的内螺旋流带动下经中心管排出, 成为精煤; 重产物与部分密度较高的重悬浮液通过外旋流沿旋流器内壁向上, 进入二段旋流器, 分别选出中煤和矸石。
图1无压三产品重介旋流器简图3 精煤产品带矸原因浅析经反复调查, 认真分析研究, 发现以下因素是造成精煤产品带矸的主要原因:( 1) 煤质变化。
原煤性质是影响重介旋流器分选效果的主要因素。
随着采煤机械化程度的不断提高, 选煤厂入选原煤含矸量增大, 同时还混有高密度的片状页岩成分; 原煤粒度组成呈减小趋势, 末煤量增多, 且含粘性矿物成分, 水分增大。
煤泥重介质旋流器的工作原理
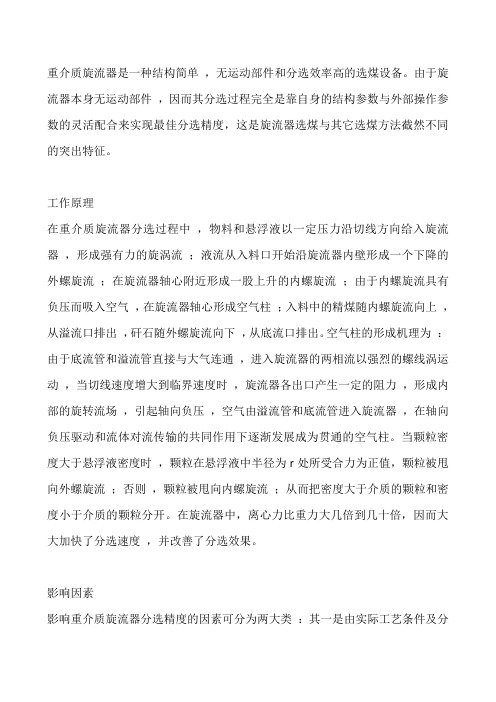
重介质旋流器是一种结构简单,无运动部件和分选效率高的选煤设备。
由于旋流器本身无运动部件,因而其分选过程完全是靠自身的结构参数与外部操作参数的灵活配合来实现最佳分选精度,这是旋流器选煤与其它选煤方法截然不同的突出特征。
工作原理在重介质旋流器分选过程中,物料和悬浮液以一定压力沿切线方向给入旋流器,形成强有力的旋涡流;液流从入料口开始沿旋流器内壁形成一个下降的外螺旋流;在旋流器轴心附近形成一股上升的内螺旋流;由于内螺旋流具有负压而吸入空气,在旋流器轴心形成空气柱;入料中的精煤随内螺旋流向上,从溢流口排出,矸石随外螺旋流向下,从底流口排出。
空气柱的形成机理为:由于底流管和溢流管直接与大气连通,进入旋流器的两相流以强烈的螺线涡运动,当切线速度增大到临界速度时,旋流器各出口产生一定的阻力,形成内部的旋转流场,引起轴向负压,空气由溢流管和底流管进入旋流器,在轴向负压驱动和流体对流传输的共同作用下逐渐发展成为贯通的空气柱。
当颗粒密度大于悬浮液密度时,颗粒在悬浮液中半径为r处所受合力为正值,颗粒被甩向外螺旋流;否则,颗粒被甩向内螺旋流;从而把密度大于介质的颗粒和密度小于介质的颗粒分开。
在旋流器中,离心力比重力大几倍到几十倍,因而大大加快了分选速度,并改善了分选效果。
影响因素影响重介质旋流器分选精度的因素可分为两大类:其一是由实际工艺条件及分选设备本身所决定的生产中不易变动的因素,如入料煤质特征、旋流器入料口的形状、直径等结构参数等;其二是一定程度上可以调整的因素,比如入口压力、矿浆入料量、入料方式等。
1、入料煤质特性重介质旋流器是一个封闭的、相对容积很小的分选容器。
对于两产品旋流器,有一个入口两个出口,其进入和排出的瞬间体积流量相等。
底流口和溢流口排量的分配,在一定的条件下是基本固定的,但当入选原煤的密度组成发生变化时,例如高密度物含量增加,那么要求底流固体排出量增加,溢流固体排出量相对减少,但底流口的排放能力有限,因而会将一部分中等密度的煤颗粒和重介质挤向溢流口排出,使实际分选密度升高。
重介质旋流器安全技术操作规程(3篇)
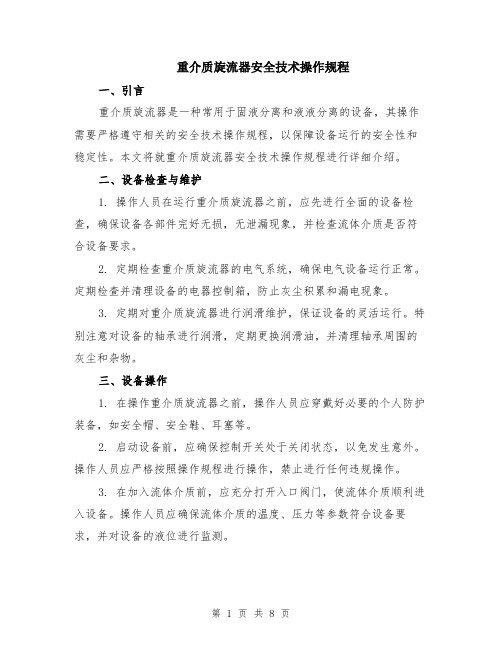
重介质旋流器安全技术操作规程一、引言重介质旋流器是一种常用于固液分离和液液分离的设备,其操作需要严格遵守相关的安全技术操作规程,以保障设备运行的安全性和稳定性。
本文将就重介质旋流器安全技术操作规程进行详细介绍。
二、设备检查与维护1. 操作人员在运行重介质旋流器之前,应先进行全面的设备检查,确保设备各部件完好无损,无泄漏现象,并检查流体介质是否符合设备要求。
2. 定期检查重介质旋流器的电气系统,确保电气设备运行正常。
定期检查并清理设备的电器控制箱,防止灰尘积累和漏电现象。
3. 定期对重介质旋流器进行润滑维护,保证设备的灵活运行。
特别注意对设备的轴承进行润滑,定期更换润滑油,并清理轴承周围的灰尘和杂物。
三、设备操作1. 在操作重介质旋流器之前,操作人员应穿戴好必要的个人防护装备,如安全帽、安全鞋、耳塞等。
2. 启动设备前,应确保控制开关处于关闭状态,以免发生意外。
操作人员应严格按照操作规程进行操作,禁止进行任何违规操作。
3. 在加入流体介质前,应充分打开入口阀门,使流体介质顺利进入设备。
操作人员应确保流体介质的温度、压力等参数符合设备要求,并对设备的液位进行监测。
4. 在设备运行过程中,操作人员应经常观察设备运行状态,如发现异常现象应立即停机并进行检修。
在操作设备时,切勿随便离开设备,以免发生危险。
四、异常处理和紧急情况应对1. 在设备运行过程中,如果发生异常情况,操作人员应立即停机,并进行相关检修。
对于无法解决的故障,应及时报告上级,并等待相关人员的处理意见。
2. 在设备运行过程中,如果发生漏液、泄漏等情况,操作人员应立即采取应急措施,如封闭阀门、隔离泄漏源等,并报告上级灭火处理。
3. 在设备运行过程中,如果发生火灾等紧急情况,操作人员应立即拨打急救电话,并迅速撤离现场,待消防人员到达后协助处理。
五、设备停机与保养1. 每次停机前,应将相关阀门关闭,并切断电源。
在设备停机后,应清理设备内部的残留物,并进行相应的保养工作。
煤泥重介质旋流器技术要求(

煤泥重介质旋流器技术要求(
一、总则
2、煤泥重介质旋流器的设计、制造及安装应满足防火、防爆和防止煤泥出口污染的要求。
二、外形及尺寸
1、煤泥重介质旋流器的外形可根据客户的要求选择,要求旋流器的结构安装尺寸应符合《煤泥炉旋流器》中的规定。
2、煤泥重介质旋流器尺寸及连接尺寸须按客户提供的电厂煤泥系统的尺寸及连接尺寸、吊重及工况的要求确定。
三、设计
1、煤泥重介质旋流器的设计须按客户提供的煤泥系统的工况参数与生产要求确定,按煤泥泵中途连接系统的满足参数来完成设计。
2、煤泥重介质旋流器的设计要求:旋流器的出口流量可以达到设计要求,旋面顺序合理,选用的驱动轴材质和动力传动部件要满足设计工况的要求,旋流器的联轴器可靠性高,外壳强度及防震性能要满足设计工况的要求。
3、煤泥重介质旋流器应装配润滑装置,用于旋转部件的润滑及温度检测。
四、制造
1、煤泥重介质旋流器的制造要求:符合国家质量标准及电厂工艺要求。
三产品重介质旋流器
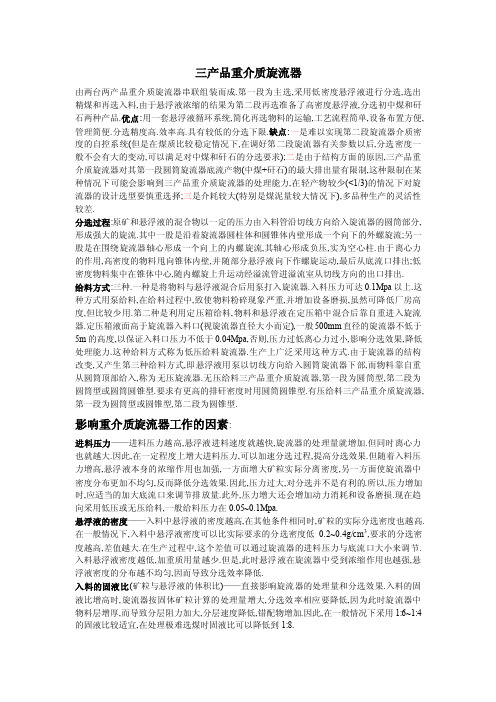
三产品重介质旋流器由两台两产品重介质旋流器串联组装而成.第一段为主选,采用低密度悬浮液进行分选,选出精煤和再选入料,由于悬浮液浓缩的结果为第二段再选准备了高密度悬浮液,分选初中煤和矸石两种产品.优点:用一套悬浮液循环系统,简化再选物料的运输,工艺流程简单,设备布置方便,管理简便.分选精度高.效率高.具有较低的分选下限.缺点:一是难以实现第二段旋流器介质密度的自控系统(但是在煤质比较稳定情况下,在调好第二段旋流器有关参数以后,分选密度一般不会有大的变动,可以满足对中煤和矸石的分选要求);二是由于结构方面的原因,三产品重介质旋流器对其第一段圆筒旋流器底流产物(中煤+矸石)的最大排出量有限制,这种限制在某种情况下可能会影响到三产品重介质旋流器的处理能力,在轻产物较少(<1/3)的情况下对旋流器的设计选型要慎重选择;三是介耗较大(特别是煤泥量较大情况下),多品种生产的灵活性较差.分选过程:原矿和悬浮液的混合物以一定的压力由入料管沿切线方向给入旋流器的圆筒部分,形成强大的旋流.其中一股是沿着旋流器圆柱体和圆锥体内壁形成一个向下的外螺旋流;另一股是在围绕旋流器轴心形成一个向上的内螺旋流,其轴心形成负压,实为空心柱.由于离心力的作用,高密度的物料甩向锥体内壁,并随部分悬浮液向下作螺旋运动,最后从底流口排出;低密度物料集中在锥体中心,随内螺旋上升运动经溢流管进溢流室从切线方向的出口排出.给料方式:三种.一种是将物料与悬浮液混合后用泵打入旋流器.入料压力可达0.1Mpa以上.这种方式用泵给料,在给料过程中,致使物料粉碎现象严重,并增加设备磨损,虽然可降低厂房高度,但比较少用.第二种是利用定压箱给料,物料和悬浮液在定压箱中混合后靠自重进入旋流器.定压箱液面高于旋流器入料口(视旋流器直径大小而定),一般500mm直径的旋流器不低于5m的高度,以保证入料口压力不低于0.04Mpa,否则,压力过低离心力过小,影响分选效果,降低处理能力.这种给料方式称为低压给料旋流器.生产上广泛采用这种方式.由于旋流器的结构改变,又产生第三种给料方式,即悬浮液用泵以切线方向给入圆筒旋流器下部,而物料靠自重从圆筒顶部给入,称为无压旋流器.无压给料三产品重介质旋流器,第一段为圆筒型,第二段为圆筒型或圆筒圆锥型.要求有更高的排矸密度时用圆筒圆锥型.有压给料三产品重介质旋流器,第一段为圆筒型或圆锥型,第二段为圆锥型.影响重介质旋流器工作的因素:进料压力——进料压力越高,悬浮液进料速度就越快,旋流器的处理量就增加.但同时离心力也就越大.因此,在一定程度上增大进料压力,可以加速分选过程,提高分选效果.但随着入料压力增高,悬浮液本身的浓缩作用也加强,一方面增大矿粒实际分离密度,另一方面使旋流器中密度分布更加不均匀,反而降低分选效果.因此,压力过大,对分选并不是有利的.所以,压力增加时,应适当的加大底流口来调节排放量.此外,压力增大还会增加动力消耗和设备磨损.现在趋向采用低压或无压给料,一般给料压力在0.05~0.1Mpa.悬浮液的密度——入料中悬浮液的密度越高,在其他条件相同时,矿粒的实际分选密度也越高.在一般情况下,入料中悬浮液密度可以比实际要求的分选密度低0.2~0.4g/cm3,要求的分选密度越高,差值越大.在生产过程中,这个差值可以通过旋流器的进料压力与底流口大小来调节.入料悬浮液密度越低,加重质用量越少.但是,此时悬浮液在旋流器中受到浓缩作用也越强,悬浮液密度的分布越不均匀,因而导致分选效率降低.入料的固液比(矿粒与悬浮液的体积比)——直接影响旋流器的处理量和分选效果.入料的固液比增高时,旋流器按固体矿粒计算的处理量增大,分选效率相应要降低,因为此时旋流器中物料层增厚,而导致分层阻力加大,分层速度降低,错配物增加.因此,在一般情况下采用1:6~1:4的固液比较适宜,在处理极难选煤时固液比可以降低到1:8.旋流器的结构参数:圆柱体的长度——在旋流器的直径和锥角确定后,旋流器的容积和总长度主要取决于圆柱部分的长度.旋流器圆柱部分的长短对分选效果影响很大.当圆柱部分增长时其容积和总长度都增加.因此,入选物料在旋流器中的停留时间增长,实际分选密度提高.但圆柱长度太长,会使低密度产品质量变坏.反之,圆柱部分过短,会引起圆柱部分的介质流不稳定,实际分选密度降低,使部分浮物损失到底流中去.圆锥角的大小——在同样直径同样容积的旋流器的情况下,随着锥角的增大,实际分选密度也增大.溢流口的直径——溢流口的直径增大后,可增大实际分选密度.但溢流口过大时,会造成圆柱部分溢流速度过大,影响溢流的稳定.虽然溢流出量增加,但浮物(精煤)质量降低.一般情况下溢流口直径为(0.30~0.40)D(旋流器直径).底流口直径——实践证明,缩小底流口可使实际分选密度增大.但底流口过小时会造成矿粒在底流口挤压.对于选煤来说,底流口过小会使矸石易混入到精煤中,严重时引起底流口堵塞,但底流口过大时,又会引起精煤损失.一般情况下底流口直径为(0.24~0.30)D.锥比——底流口直径与溢流口直径之比.锥比的大小与旋流器直径,入选物料性质,介质性质等因素有关.当旋流器直径较小,可选性较差时,锥比要小一点.反之,锥比可大一点.加重质的粒度较粗时,锥比可大一些.实践证明,锥比一般在0.7~0.8为宜.入料口尺寸——当入料口尺寸过小时,入料粒度上限受限制,易发生堵塞现象.入料口尺寸过大时,旋流器切线速度减小(或相应增加入料压头,以保证入料速度).一般情况下入料口在(0.20~0.25)D范围内.旋流器的入料口,溢流口,底流口的直径比大致为0.2:0.4:0.3.溢流管插入深度——插入深度在320~400mm范围效果较好.重介质旋流器的安装——一般倾斜安装,旋流器轴线与水平夹角为10°,便于旋流器入料,溢流和底流管路系统的安装.当设备停止运转时,物料能顺利的从旋流器中排出来.对低压给料旋流器更应该倾斜安装.如采用正立垂直安装,溢流口于底流口高差引起压力变化,底流口所受压力比溢流口大,从而使矿浆大量从底流口排出,影响旋流器正常工作.日本涡流旋流器,采用粗粒磁铁矿粉作加重质,在结构上有所改变,采用倒立安装方式.。
三产品重介质旋流器工作原理
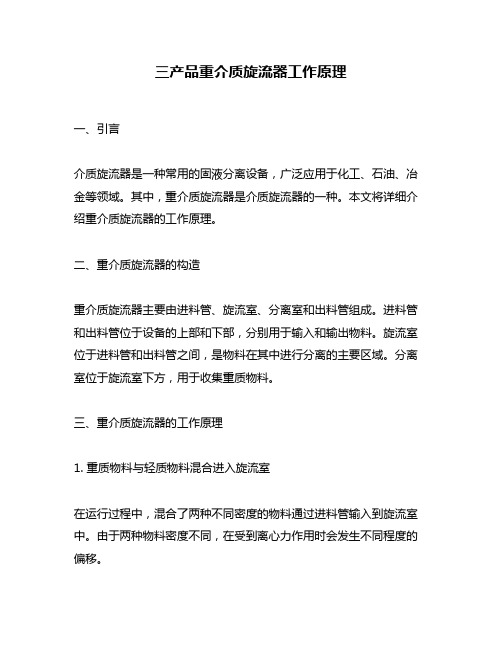
三产品重介质旋流器工作原理一、引言介质旋流器是一种常用的固液分离设备,广泛应用于化工、石油、冶金等领域。
其中,重介质旋流器是介质旋流器的一种。
本文将详细介绍重介质旋流器的工作原理。
二、重介质旋流器的构造重介质旋流器主要由进料管、旋流室、分离室和出料管组成。
进料管和出料管位于设备的上部和下部,分别用于输入和输出物料。
旋流室位于进料管和出料管之间,是物料在其中进行分离的主要区域。
分离室位于旋流室下方,用于收集重质物料。
三、重介质旋流器的工作原理1. 重质物料与轻质物料混合进入旋流室在运行过程中,混合了两种不同密度的物料通过进料管输入到旋流室中。
由于两种物料密度不同,在受到离心力作用时会发生不同程度的偏移。
2. 产生环形涡流当物料通过进口时,在转子内部会产生一个环形涡流,并且在涡轮叶片上形成一个高速旋转的涡流。
在这个过程中,由于离心力的作用,物料中密度较大的部分会向涡轮叶片外侧移动,而密度较小的部分则会向内侧移动。
3. 重质物料沉降随着涡流继续旋转,密度较大的重质物料会沉降到旋流室底部,并且通过分离室进入出料管。
而密度较小的轻质物料则会在离心力作用下被挤出旋流室,并且通过出料管排出设备。
4. 调节介质浓度为了使重介质旋流器达到最佳分离效果,需要根据物料性质和工艺要求调节介质浓度。
当介质浓度增加时,重质物料沉降速度加快,轻质物料被挤压出去的速度减慢。
反之亦然。
四、重介质旋流器的优点1. 分离效率高重介质旋流器可以有效地将混合了两种不同密度的物料进行分离。
在实际应用中,其分离效率可达到90%以上。
2. 适用范围广重介质旋流器适用于处理各种不同的物料,具有较好的通用性。
尤其在处理密度差异较大的物料时,其优势更加明显。
3. 操作简便重介质旋流器操作简单,维护方便。
在实际应用中,只需要调节介质浓度即可满足不同物料的分离要求。
五、总结重介质旋流器是一种高效、通用、易操作的固液分离设备。
其工作原理基于离心力和密度差异原理,可以将混合了两种不同密度的物料进行有效分离。
重介质旋流器工作原理
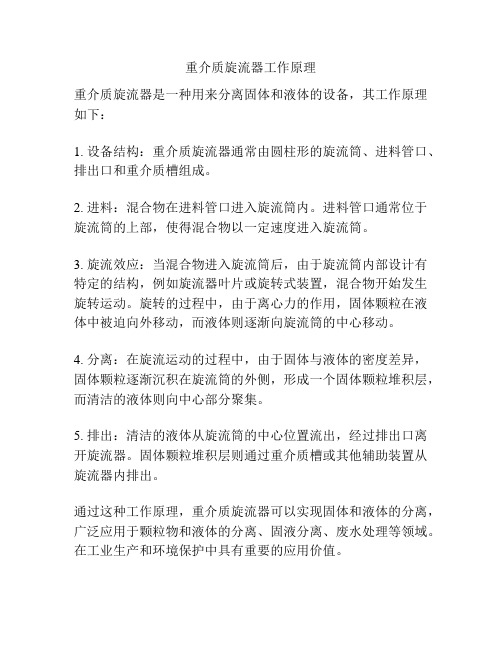
重介质旋流器工作原理
重介质旋流器是一种用来分离固体和液体的设备,其工作原理如下:
1. 设备结构:重介质旋流器通常由圆柱形的旋流筒、进料管口、排出口和重介质槽组成。
2. 进料:混合物在进料管口进入旋流筒内。
进料管口通常位于旋流筒的上部,使得混合物以一定速度进入旋流筒。
3. 旋流效应:当混合物进入旋流筒后,由于旋流筒内部设计有特定的结构,例如旋流器叶片或旋转式装置,混合物开始发生旋转运动。
旋转的过程中,由于离心力的作用,固体颗粒在液体中被迫向外移动,而液体则逐渐向旋流筒的中心移动。
4. 分离:在旋流运动的过程中,由于固体与液体的密度差异,固体颗粒逐渐沉积在旋流筒的外侧,形成一个固体颗粒堆积层,而清洁的液体则向中心部分聚集。
5. 排出:清洁的液体从旋流筒的中心位置流出,经过排出口离开旋流器。
固体颗粒堆积层则通过重介质槽或其他辅助装置从旋流器内排出。
通过这种工作原理,重介质旋流器可以实现固体和液体的分离,广泛应用于颗粒物和液体的分离、固液分离、废水处理等领域。
在工业生产和环境保护中具有重要的应用价值。
重介旋流器
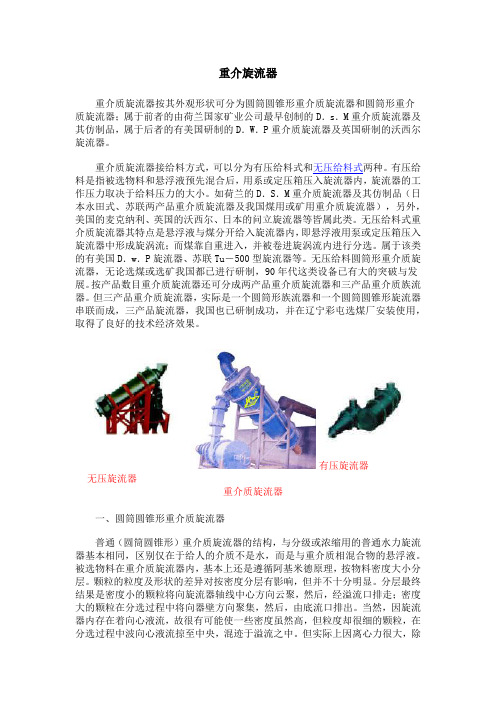
重介旋流器重介质旋流器按其外观形状可分为圆筒圆锥形重介质旋流器和圆筒形重介质旋流器;属于前者的由荷兰国家矿业公司最早创制的D .s .M 重介质旋流器及其仿制品,属于后者的有美国研制的D .W .P 重介质旋流器及英国研制的沃西尔旋流器。
重介质旋流器接给料方式,可以分为有压给料式和无压给料式两种。
有压给料是指被选物料和悬浮液预先混合后,用系或定压箱压入旋流器内,旋流器的工作压力取决于给料压力的大小。
如荷兰的D .S .M 重介质旋流器及其仿制品(日本永田式、苏联两产品重介质旋流器及我国煤用或矿用重介质旋流器),另外,美国的麦克纳利、英国的沃西尔、日本的问立旋流器等皆属此类。
无压给料式重介质旋流器其特点是悬浮液与煤分开给入旋流器内,即悬浮液用泵或定压箱压入旋流器中形成旋涡流;而煤靠自重进入,并被卷进旋涡流内进行分选。
属于该类的有美国D .w .P 旋流器、苏联Tu -500型旋流器等。
无压给料圆筒形重介质旋流器,无论选煤或选矿我国都已进行研制,90年代这类设备已有大的突破与发展。
按产品数目重介质旋流器还可分成两产品重介质旋流器和三产品重介质族流器。
但三产品重介质旋流器,实际是一个圆筒形族流器和一个圆筒圆锥形旋流器串联而成,三产品旋流器,我国也已研制成功,并在辽宁彩屯选煤厂安装使用,取得了良好的技术经济效果。
无压旋流器重介质旋流器有压旋流器一、圆筒圆锥形重介质旋流器普通(圆筒圆锥形)重介质旋流器的结构,与分级或浓缩用的普通水力旋流器基本相同,区别仅在于给人的介质不是水,而是与重介质相混合物的悬浮液。
被选物料在重介质旋流器内,基本上还是遵循阿基米德原理,按物料密度大小分层。
颗粒的粒度及形状的差异对按密度分层有影响,但并不十分明显。
分层最终结果是密度小的颗粒将向旋流器轴线中心方向云聚,然后,经溢流口排走;密度大的颗粒在分选过程中将向器壁方向聚集,然后,由底流口排出。
当然,因旋流器内存在着向心液流,故很有可能使一些密度虽然高,但粒度却很细的颗粒,在分选过程中波向心液流掠至中央,混迹于溢流之中。
重介选煤厂用重介质旋流器的结构参数
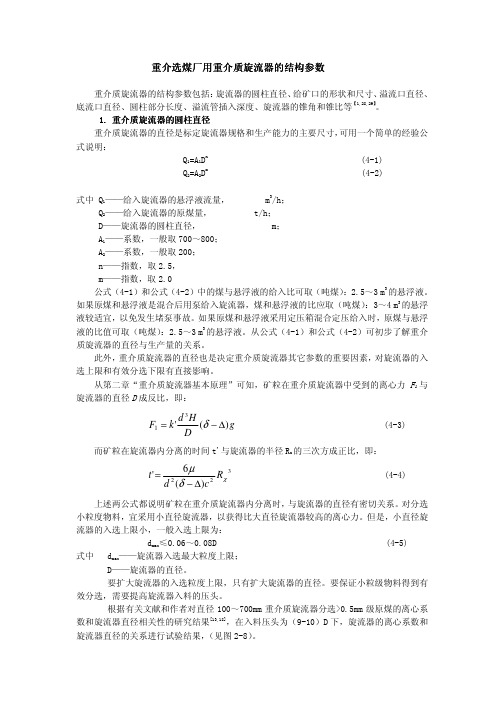
重介选煤厂用重介选煤厂用重介质旋流器重介质旋流器重介质旋流器的结构参数的结构参数的结构参数重介质旋流器的结构参数包括:旋流器的圆柱直径、给矿口的形状和尺寸、溢流口直径、底流口直径、圆柱部分长度、溢流管插入深度、旋流器的锥角和锥比等【1,28,29】。
1. 重介质旋流器重介质旋流器的圆柱直径的圆柱直径的圆柱直径重介质旋流器的直径是标定旋流器规格和生产能力的主要尺寸,可用一个简单的经验公式说明:Q 1=A 1D n (4-1)Q 2=A 2D m (4-2)式中 Q 1——给入旋流器的悬浮液流量, m 3/h;Q 2——给入旋流器的原煤量,t/h; D——旋流器的圆柱直径, m;A 1——系数,一般取700~800;A 2——系数,一般取200;n——指数,取2.5,m——指数,取2.0公式(4-1)和公式(4-2)中的煤与悬浮液的给入比可取(吨煤):2.5~3 m 3的悬浮液。
如果原煤和悬浮液是混合后用泵给入旋流器,煤和悬浮液的比应取(吨煤):3~4 m 3的悬浮液较适宜,以免发生堵泵事故。
如果原煤和悬浮液采用定压箱混合定压给入时,原煤与悬浮液的比值可取(吨煤):2.5~3 m 3的悬浮液。
从公式(4-1)和公式(4-2)可初步了解重介质旋流器的直径与生产量的关系。
此外,重介质旋流器的直径也是决定重介质旋流器其它参数的重要因素,对旋流器的入选上限和有效分选下限有直接影响。
从第二章“重介质旋流器基本原理”可知,矿粒在重介质旋流器中受到的离心力F 1与旋流器的直径D 成反比,即:g DH d k F )('31∆−=δ (4-3)而矿粒在旋流器内分离的时间t'与旋流器的半径R x 的三次方成正比,即: 322)(6'χδµR cd t ∆−= (4-4) 上述两公式都说明矿粒在重介质旋流器内分离时,与旋流器的直径有密切关系。
对分选小粒度物料,宜采用小直径旋流器,以获得比大直径旋流器较高的离心力。
三产品重介质旋流器工作原理
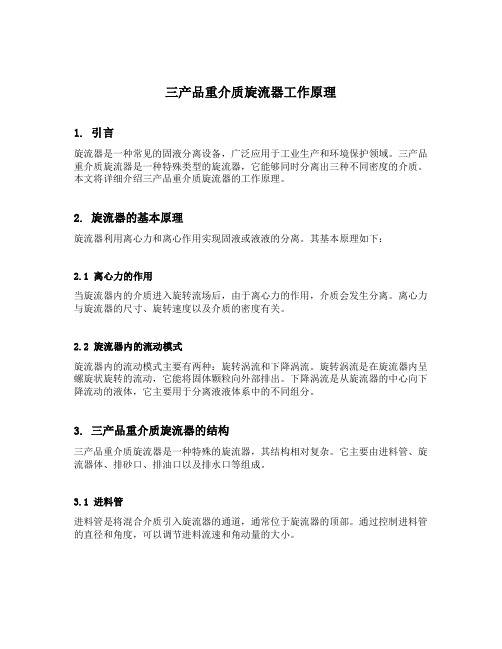
三产品重介质旋流器工作原理1. 引言旋流器是一种常见的固液分离设备,广泛应用于工业生产和环境保护领域。
三产品重介质旋流器是一种特殊类型的旋流器,它能够同时分离出三种不同密度的介质。
本文将详细介绍三产品重介质旋流器的工作原理。
2. 旋流器的基本原理旋流器利用离心力和离心作用实现固液或液液的分离。
其基本原理如下:2.1 离心力的作用当旋流器内的介质进入旋转流场后,由于离心力的作用,介质会发生分离。
离心力与旋流器的尺寸、旋转速度以及介质的密度有关。
2.2 旋流器内的流动模式旋流器内的流动模式主要有两种:旋转涡流和下降涡流。
旋转涡流是在旋流器内呈螺旋状旋转的流动,它能将固体颗粒向外部排出。
下降涡流是从旋流器的中心向下降流动的液体,它主要用于分离液液体系中的不同组分。
3. 三产品重介质旋流器的结构三产品重介质旋流器是一种特殊的旋流器,其结构相对复杂。
它主要由进料管、旋流器体、排砂口、排油口以及排水口等组成。
3.1 进料管进料管是将混合介质引入旋流器的通道,通常位于旋流器的顶部。
通过控制进料管的直径和角度,可以调节进料流速和角动量的大小。
3.2 旋流器体旋流器体是三产品重介质旋流器的核心部件,它通常由圆筒形容器和旋转装置构成。
圆筒形容器内部有多层锥体,用于形成旋转流场。
旋转装置则通过驱动旋流器体旋转,产生离心力。
3.3 排砂口排砂口位于旋流器体的底部,用于排出重介质中的固体颗粒。
排砂口的尺寸和位置可以根据实际需求进行调整,以控制排砂效果。
3.4 排油口和排水口排油口和排水口通常位于旋流器体的上部,用于分别排出轻介质和水。
通过控制排油口和排水口的开度,可以调节产品的质量和产量。
4. 三产品重介质旋流器的工作过程三产品重介质旋流器的工作过程可以分为进料、分离和排出三个阶段。
4.1 进料阶段混合介质通过进料管进入旋流器体,并在旋流器体内形成旋转流场。
进料流速、进料角度和进料浓度等因素会影响进料阶段的效果。
4.2 分离阶段在旋流器体内,由于离心力的作用,混合介质被分离为重介质、轻介质和水三种组分。
重介质旋流器选煤工艺

重介质旋流器选煤工艺今年来,由于旋流器分选技术不断成熟,旋流器规格不断完善,分选工艺不断简化,介质密度自动控制水平不断提高,以及操作管理难度不断降低,重介质旋流器选煤工艺在国内外得到广泛的推广和应用,并成为近以阶段我国选美技术更新与发展的热点和方向之一,特别是简化的大型重介质旋流器分选工艺的研究与应用方心未艾。
由于旋流器的适应性强,采用旋流器分选的煤种越来越广泛。
随着设备的大型化,旋流器分选的入料上限不断提高,给料粒度范围越来越宽。
上限不断扩大的同时,小直径旋流器煤泥重介质分选技术的研究与应用也正在逐步展开。
一、重介质旋流器的主要类型。
目前广泛使用的重介质旋流器有以下几种类型:1、圆锥两产品重介质旋流器2、圆筒形两产品重介质旋流器3、三产品重介质旋流器4、煤泥重介质旋流器二、重介质旋流器选煤工艺重介质旋流器选煤工艺有两产品、三产品分选工艺。
重介质旋器分选工艺既可以单独使用,也可以与其他选煤方法组合使用,形成各种形式多样、灵活多表的工艺组合,以适应不同的工艺要求。
采用重介质旋流器分选的典型流程有:(1)块煤重介质分选机分选+末煤重介质旋流器分选:该程可用于无烟煤、炼焦煤与动力煤的分选。
(2)跳汰粗选+重介质旋流器再选:多用于高硫、难选煤的脱硫、降灰。
(3)三产品重介质旋流器分选(4)大直径重介质旋流器分选+小直径煤泥重介质旋流器分选1、两产品重介质旋流器分选工艺根据入料煤给如旋流器的方式,两产品重介质旋流器可以分为有压给料和无压给料两种工艺类型。
有压与无压是针对旋流器的入料煤而言的。
(1)有压给料两产品重介质旋流器分选根据工艺实现方式有压给料可分为泵给料和定压箱给料两种方式。
泵给料方式:预先将待分选的煤与合格介质悬浮液在煤介混合桶中混合均匀,然后用泵打入旋流器。
该泵筒式完成给料并提供旋流器分选的动力。
泵给料方式目前多采用离心式渣浆泵作为旋流器的入料泵。
由于管路布置灵活性及无须定压高度,可以大幅度降低厂房的高度,简化工艺、布置灵活、基建投资省。
- 1、下载文档前请自行甄别文档内容的完整性,平台不提供额外的编辑、内容补充、找答案等附加服务。
- 2、"仅部分预览"的文档,不可在线预览部分如存在完整性等问题,可反馈申请退款(可完整预览的文档不适用该条件!)。
- 3、如文档侵犯您的权益,请联系客服反馈,我们会尽快为您处理(人工客服工作时间:9:00-18:30)。
定压箱给料:
煤t:悬浮液m3=1:(2.5~4) H=(9~11)D 混合泵给料: 煤t:悬浮液m3=1:(3~5)
P=(9~10)D× ρ × 105 (帕)
4 、影响重介质旋流器工作的主要操作因素
2、悬浮液密度
悬浮液密度波动在± 10kg/m3。
高密度分选可放宽一些,低密度分选要求更严一些( ± 5kg/m3 )
Q 0.03d i d 0 gH 式中:
1.82
0.2
Q 生产能力,m 3 / h d i、d 0 溢流口、入料口直径, cm H 入料压头,kPa
旋流器锥顶角
g 重力加速度
溢流口直径与分离密度、可能偏差的关系
3.4 溢流管长度和器壁的影响
1、溢流管长度对切向速度无明显影响,但对精煤质量和分选精度又较大 的影响。溢流管增长时,溢流管下端至锥体下部距离缩短,促使实际分离 密度增大,使分选结果变坏。 溢流管长度=(0.8~1.0)圆柱长 2、溢流管壁厚对切向速度影响较大,壁厚加大,使溢流管与器壁之间 空间变小、流层变薄,从而使相同半径上的切线速度梯度增大。 厚管壁的轴向零速区较宽,速度由向下变向上有缓慢过渡区,使分选 精度提高。 过厚的溢流管壁使重量增加,容积变小,对结果也不利。
EP 0.03 P 0.015 EP 0.014 P 0.01F1F2
F1 直径系数。( 0.98 / 350 、、 1 / 500 、、 1.04 / 600 、、 1.08 / 700 ) F2 入料粒度系数。( 0.8 / 0.5 ~ 50、、 1.0 / 0.5 ~ 30、、 1.2 / 0.5 ~ 6)
分离锥面构想图
2.5 、重介旋流器分选过程(有压给料旋流器)
1、入料管 2、锥体 3、底流口 4、溢流管 5、溢流室 6、支架
2.5 、重介旋流器分选过程(有压给料旋流器)
优点:分选精度高、介质循环量少。 缺点:系统磨损严重、原料破碎泥化严重、入料上限小。
2.6 、重介旋流器分选过程(无压给料旋流器)
底流密度与溢流密度差异、重介质粒度
差异决定了煤和矸石的分析密度。
2.2、重介质旋流器等密度面
影响因素 1、加重质粒度 2、重介质密度 3、给料压力 4、锥角 5、底流口尺寸
Ф 150圆筒圆锥型旋流器
Ф 200圆筒型旋流器
入料密度为1.43t/m3
圆锥型密度场变化大
圆柱型密度场均匀
2.3、矿物分选过程
L kD
200圆柱圆锥旋流器: > 200圆柱圆锥旋流器: k=(0.7~2)D 圆柱旋流器: k=(2~6)D
圆柱长度与分离密度及效率的关系
k=(0.6~0.7)D
直径大的选小值,直径小的选大值。
4.3 溢流口的直径
溢流口直径在(0.32~0.4)D
一般选取0.4D。 易选煤溢流口可选取大一些。 旋流器直径确定后,溢流口直 径与生产能力成正比。
a=0.5,b=0.6
圆柱形:
a=0.7,b=0.8
2.4、分离锥面
分离锥面的形成决定于垂直零速面,并与径向零位面有关,而分离锥面周 截面的确定则与旋流器的结构有关。流场运动特性的实验结果证实了分离锥面
的存在。
DO D 2d D 旋流器直径 d 入料口直径
垂直零速面与最大切线 恒速面的相交线。 当锥角为20o时 m0=0.4~0.6
重悬浮液在离心力场作用下,内部形成
空气柱 溢流管
1.20 1.30 1.40 1.50
不同的“等密度面”。密度自上而下,由
内项外增加。 越靠近锥壁和底流口的密度越大
1.60
越靠近溢流管附近的密度越小
产生原因:重介质是由高密度固体粒子
与水混合成的不均匀两相体系。在较大的离 心力场作用下,悬浮液在旋流器中受到强烈 的浓缩作用。从而造成悬浮液的密度在旋流 器中分布不均匀。
三、重介质旋流器分类
重介质旋流器分类方法较多;下面是几种常规的分类方法:
(1)按其外形结构可分为:
圆柱形重介质旋流器; 圆柱圆锥形重介质旋流器。; 三产品重介质旋流器。
(3)按给入旋流器的物料方式可分为: 周边(有压》给原煤、给介质的重介质旋流器; 中心(无压)给原煤、周边(有压)给介质的重介质旋流器。 (4)按旋流器的安装方式可分为: 正(直)立式、倒立式和卧式三种。
重介质旋流器工作机理
与水介质旋流器类似 分选流场与水介质旋流器有很大差别
2.1、重介旋流器分选机理
当料浆以一定的速度进入旋流器,遇到 旋流器器壁后被迫作回转运动。由于所 受的离心力不同,密度大的颗粒所受的 离心力大,能够克服水力阻力向器壁运 动,并在自身重力的共同作用下,沿器 壁螺旋向下运动,细而小的颗粒及大部 分水则因所受的离心力小,未及靠近器 壁即随料浆做回转运动。在后续给料的 推动下,料浆继续向下和回转运动,于 是粗颗粒继续向周边浓集,而密度小颗 粒则停留在中心区域, 随着料浆从旋流 器的柱体部分流向锥体部分,流动断面 越来越小,在外层料浆收缩压迫之下, 含有大量细小颗粒的内层料浆不得不改 变方向,转而向上运动,形成内旋流, 自溢流管排出,成为溢流,而粗大颗粒 则继续沿器壁螺旋向下运动,形成外旋 流,最终由底流口排出。
k 2 0.7 9
2
底流口直径在(0.24~0.32)D范围内 底流口直径>3dmax`
3.6入料口形状和尺寸
入料口有圆形、矩形、扇形等多种,入料流线有切线、摆线、渐开线等方式。 入料流线对入料压头损失和液流稳定有一定的作用。 入料口形状无较大影响, 入料尺寸过大,使流线难以保证,尺寸过少,影响入料上限。
2.1、重介旋流器分选机理
2、“矿粒在重介旋流器内受上升、下降液流作用的过程 中,是按密度进行分离的,使分离点在重介旋流器的下部, 即底流口附近。因此重介旋流器的底流介质密度是决定矿 粒在旋流器内分离密度的主要因素。”
实际分离密度
u p 1.42
---底流介质密度
u p 1.42
2.1、重介旋流器分选机理
分离
锥面
排出。
2.3、矿物分选过程
悬浮液形成密度场对精确分离过程起决定性作用的。实际生产中对重介质旋流 器内密度场检测困难。只能通过实验室实验,结合旋流器入料点和各排料点悬浮液 的流变特性测定,找出它们之间的关系,达到对旋流器内流场的调控。
圆柱圆锥型:
分选密度: p a i b 0
3.5 底流口的直径
Q 0.03k1k 2 d 0 d u gH 式中: Q 生产能力 d 0、d u 溢流口、底流口直径 H 入料压头 k1、k 2 系数
k1 0.0 8D 2 0.1D 1 0.0 4 4 0.3 7 9 tg
重介质选矿工作影响因素
3、影响重介质旋流器工作的主要结构因素
3.1、结构参数
1、重介质旋流器的圆柱直径
2、旋流器圆柱长度 3、旋流器的溢流口直径 4、溢流管长度和器壁 5、旋流器的底流口直径 6、旋流器入料口形状和尺寸 7、旋流器的锥比
8、旋流器圆锥角
9、旋流器的安装角
3.1旋流器的圆柱直径
直径D影响处理能力和入料上限。
厂房高、基建投资多。
原煤破碎轻;
管路磨损轻;
入料上限不受泵限制; 循环量小; 生产操作直观。
三产品重介旋流器流程(定压给料)
2.7 、重介旋流器分选工艺流程(无压给料旋流器)
工艺复杂; 对细粒煤分选效果差。
无压给料(中心给料)三产品重介旋流器流程
2.7 、重介旋流器分选工艺流程(无压给料旋流器)
入料速度: 4~5米/秒 当量直径:(0.2~0.3)D
3.7 锥比
重介质旋流器锥比:溢流口直径与底流口直径的比值。
锥比越小,分选密度越高。反之,越低。
入选原煤属于难选煤时,锥比宜选小一点。 一般锥比在0.5~0.8。 溢流口与底流口直径由于磨损而增大的部分不能超过原来直径的3%。 一般在2%以下。
分选悬浮液形成的密度场对保证物料在
空气柱 溢流管
1.20 1.30 1.40 1.50 1.60
重介质旋流器内按密度进行精确分离起决
定性作用
矿粒进入旋流器中,矿粒逐渐扩散, 按矿粒密度不同而处于相应的等密度线上。 在离心力作用下,密度大的矸石很快奔 向器壁,在外旋流作用下由底流口排出。 密度轻的精煤在内旋流作用下从溢流口
介质量: Q1 A1 D
n
中心给料: 周边泵给料:
煤:2.5~5m3悬浮液; 煤:3~ 5m3悬浮液
原煤量: Q2 A2 D m
周边定压箱给料: 煤:2.5~ 4m3悬浮液
Q1 给入旋流器的悬浮液流 量,m 3 / h Q2 给入旋流器的原煤量, t/h
式中:D 旋流器的圆柱直径, m
5 、影响重介质旋流器工作的主要操作因素
3、煤泥含量
重介选煤原理及重介旋流器
授课人:王振龙
一、重介质选煤原理
重介质选矿是重力选矿的一种方式,只是所采用的介质不同而已。 通常将密度大于水的介质称为重介质。在这样的介质中进行的选矿叫 做重介质选矿,它是按照阿基米德原理进行的。 通常所选用的重介质密度是介于被选物料中轻产物和重产物两者的密 度之间,或者说使介质 ρ 介等于所需求浮物(或沉物)质量指标的分 选密度δp,即 ρ浮<ρ介<ρ沉 或ρ介=δp 在重介质中,选分过程完全属于静力作用的过程。此时,介质的 运动状态和颗粒在介质中的沉降规律,已不是形成分层的主导因素, 而重介质本身的性质(如密度、粘度等)却是影响分选的重要因素
。
二、重介质选煤特点及适用范围
重介质选煤特点: 1、分选效率高。如图所示,各种选煤设备的可能偏差E值 的比较。从图中不难看出,重介质分选机和重介质旋流器的分 选效率在各种重力选煤方法中是最高的。