加氢催化剂的硫化_翟京宋
加氢裂化反应器飞温的因素及控制措施
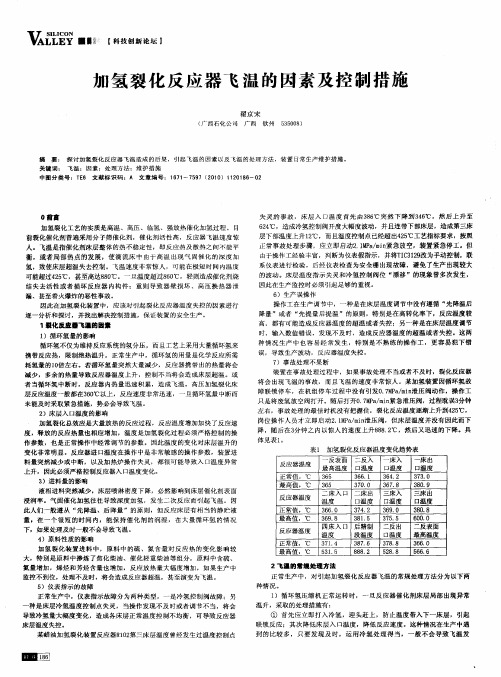
6 )生产 误操作
结 失去 活 性或 者 损 坏 反应 器 内构 件 ;重 则导 致 器 壁损 坏 、高压 换 热 器 泄
漏、甚 至着 火爆炸 的恶性 事故 。
因此在加 氢裂 化装 置 中,应 该对 引起裂 化反应 器温 度 失控 的因素 进行 逐一分 析和探 讨 ,并找 出解决控 制措 施 ,保 证装 置 的安 全生 产。
操作 工在 生产 调节 中, 一种是 在床 层温度 调 节 中没有 遵循 “ 降温 后 先
降量 ”或 者 “ 先提 量 后提 温 ”的原 则 ,特别 是在 高转 化 率下 ,反应 温度 较 高 ,都有 可 能造成 反 应器温 度 的超温 或 者失 控 ;另一 种 是在床 层温 度调 节
1曩 化反应 嚣飞 疆的 因素
可能超 过4 5 2 ℃,甚至 高达 80 。一旦温 度超过 80 8℃ 6 ℃,轻则造 成催化 剂烧
正常 事故 处理 步骤 ,应 立 即启 动2 1P/ J紧 急放 空 ,装置 紧 急停 工。但 . ̄a mn I 由于操 作工 经验丰 富 ,判断 为仪表假 指示 ,并将 TC 19 I32 改为手 动控 制 ,联 系 仪表 进行 检验 ,后经 仪表 检查 为安 全栅 出现 故 障,避 免 了生产 出现 较大 的波动 。床 层温 度 指示失 灵和 冷氢 控 制 阀位 “ 漂移 ”的现象 曾多次发 生 ,
一
反表面 二反入 一床入
一床 出 口温度 330 7.
上升 ,因此 必须严 格控 制反应 器入 口温度 变化 。
失 灵 的事 故 , 床层 入 口温 度 首先 由3 6C突 然 下 降到 3 6C, 然后 上 升 至 8" 4"
加氢催化剂预硫化方案

1. 引言加氢催化剂是广泛应用于石化工业领域的关键催化剂之一。
为了提高加氢催化剂的活性和稳定性,预硫化技术被广泛应用。
本文将从预硫化的原理、影响因素以及常见的预硫化方案等方面进行探讨。
2. 预硫化的原理预硫化是指在加氢催化剂使用之前,使用硫化物溶液进行处理,使其表面形成一层硫化物膜。
这一膜可以防止催化剂表面被氧化物或其他不活性物质占据,从而提高催化剂的活性和稳定性。
预硫化的原理可以归结为两个方面:•活性金属硫化物的形成:活性金属如镍、钼等能够与硫化物反应形成硫化物,这种硫化物能够促进加氢反应的进行,提高催化剂的反应活性。
•表面硫化膜的形成:硫化物膜可以阻隔外界氧气和不活性物质的侵蚀,减少催化剂的表面被氧化的机会,提高催化剂的稳定性。
3. 预硫化的影响因素预硫化的效果受到多种因素的影响,下面列举了一些主要的影响因素:3.1 硫化剂的选择预硫化过程中使用的硫化剂对催化剂的性能起着至关重要的作用。
常用的硫化剂包括硫化氢(H2S)、二硫化碳(CS2)等。
不同的硫化剂在反应中会产生不同的硫化物,并对催化剂表面的化学状态产生影响。
3.2 预硫化温度和时间预硫化温度和时间是影响预硫化效果的关键因素。
一般来说,高温和长时间的预硫化会使硫化剂更充分地与催化剂发生反应,生成更完善的硫化物膜。
然而,过高的温度可能会导致催化剂的部分活性成分被分解或损失,因此需要根据具体情况选择合适的预硫化温度和时间。
3.3 氛围条件预硫化过程中的气氛条件也会对催化剂的预硫化效果产生影响。
一般情况下,加氢环境中的氢气浓度越高,硫化剂与催化剂的反应速度越快,硫化物膜形成的效果也越好。
4. 常见的预硫化方案4.1 H2S气体预硫化H2S气体预硫化是一种常用的预硫化方式。
预硫化过程中,将催化剂放入加热炉中,通入含有H2S气体的加硫气体。
通过控制炉内温度和气氛浓度,使硫化剂与催化剂表面反应生成硫化物。
4.2 溶液浸泡预硫化溶液浸泡预硫化是另一种常见的预硫化方式。
苯加氢催化剂预硫化技术探讨

Ke r s: Hy r r fn n Caa y t P e uf r t n y wo d d oe ig i t ls r —s lu ai o
催 化剂 预硫 化是 指原 料 进人 催化 剂 床层 之前 。 在氢气存 在下 ,用硫化氢 与催化 剂 中活性 金属氧 化 物反应 .使其 成 为活性金属硫 化物 。催化剂 预硫化
燃 料 与 化 工
Fe u l& Ch mia r c s e e c IP o e s s
J12 l u. 00
Vo . . 1 No4 41
・
煤气 净化 与 化 学产 品 加 工 ・
苯 加 氢 催化 剂预 硫化 技术 探讨
薛 占强 臧 旭 ( 鞍钢股份 有 限公 司化 工总厂 ,鞍 山 14 2 ) 10 1
素 .提 出 了操 作 时 的注 意 事项 。 关键 词 :苯 加 氢 催 化 剂 预 硫 化
中图 分 类号 :T 5 2 2 Q 2. 6
文献 标 识码 :A
文 章 编 号 :10 - 7 9 (0 0 4 04 - 3 0 1 30 2 1 )0 — 0 4 0
Te hn c l s u so npr -s lu a i n f rhy o e n n a a y t c ia c s in o e u f r to o dr r fi gc t l s di i
通 常催化 剂硫化在 氢气和 硫化氢存 在条件下 发
生硫化反应 :
Mo + H2+ . Mo 23 0 O32 s H2+ S+ H2 9 o + H2+ — C 989 0 C 0 8 s H2+ os+ H2 3 O+ H2+ — N 323 0 Ni 2 s H2+ i + H2 ¥
加氢催化剂器外预硫化技术研究

学
工
程
师
C h e m i c a l E n g i n e e r
文章 编 号 : 1 0 0 2 — 1 1 2 4 ( 2 0 1 3 ) 0 7 — 0 0 7 0 — 0 4
2 0 1 3 年第 7 期
芏= Biblioteka 程 : 圉 弛 加 氢催化剂器外预硫化技 术研 究
丁庆 玉 , 于春 梅 , 王 燕
通 常情 况 下 , 加氢 催 化剂 的预硫 化 过程 是 在 反
国 内外 的器 外 预 硫化 技 术 主 要有 C R I T E R I O N 公 司的 a c t i C A T技术 、 E U R E C A T公 司与 A K Z O公 司 的S u l f i c a t 技术及 E a s y A c t i v e技 术 、 T R I C A T公 司 的 x p r e s s 技术 、 中 国石油 化 工股 份 有 限公 司石 油科 学 研究 院 的 R P S技 术 , 中国石 油 化工 股份 有 限公 司抚 顺石 油化 工研究 院的 E P R E S 技 术 等【 2 . 引 。 国外 公 司 的研究 工 作 开展 的较 早 , 技 术 发展 经 历 了硫 单 质 粘 结 预 硫 化 、 气相预硫化 、 有 机 多 硫 化 物 浸渍 的发展 过程 , 石 油科 学 研究 院和 抚顺 石油 化 工 研 究 院 对 于器 外 预 硫 化 技 术 的研 究 工作 开展 的 相 对 晚一 些 , 主要 以含硫 有 机硫 化物 一 步或 分 步 浸
Ke y wo r d s :o f f - s i t e p r e s u l f u r i z a t i o n ; h y d r o g e n a t i o n c a t a l y s t ; o n e — s t e p i mp r e g n a t i o n
加氢催化剂的硫化_翟京宋
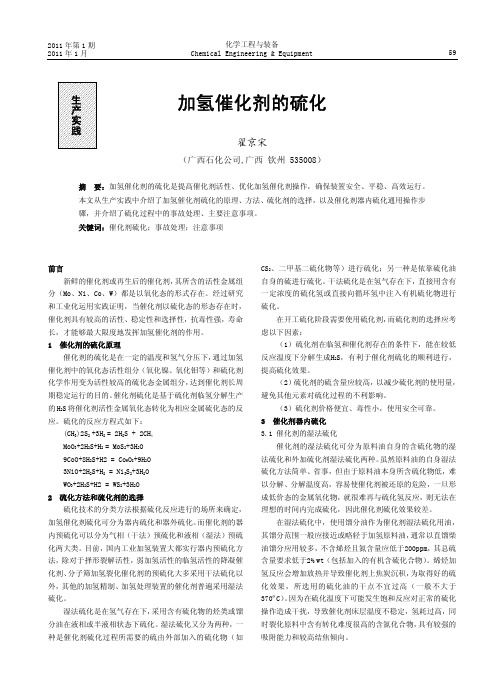
2011 年第 1 期 2011 年 1 月化学工程与装备 Chemical Engineering & Equipment59生产实践摘 前言 1 催化剂的硫化原理 应。
硫化的反应方程式如下: (CH3)2S2 +3H2 = 2H2S + 2CH4 MoO3+2H2S+H2 = MoS2+3H2O 9CoO+8H2S+H2 = Co9O8+9H2O 3NiO+2H2S+H2 = Ni3S2+3H2O WO3+2H2S+H2 = WS2+3H2O 2 硫化方法和硫化剂的选择 硫化。
加氢催化剂的硫化翟京宋(广西石化公司,广西 钦州 535008)要:加氢催化剂的硫化是提高催化剂活性、优化加氢催化剂操作,确保装置安全、平稳、高效运行。
本文从生产实践中介绍了加氢催化剂硫化的原理、方法、硫化剂的选择,以及催化剂器内硫化通用操作步 骤,并介绍了硫化过程中的事故处理、主要注意事项。
关键词:催化剂硫化;事故处理;注意事项CS2、二甲基二硫化物等)进行硫化;另一种是依靠硫化油 自身的硫进行硫化。
干法硫化是在氢气存在下, 直接用含有 一定浓度的硫化氢或直接向循环氢中注入有机硫化物进行 硫化。
在开工硫化阶段需要使用硫化剂, 而硫化剂的选择应考 虑以下因素: (1)硫化剂在临氢和催化剂存在的条件下,能在较低 反应温度下分解生成H2S,有利于催化剂硫化的顺利进行, 提高硫化效果。
(2) 硫化剂的硫含量应较高, 以减少硫化剂的使用量, 避免其他元素对硫化过程的不利影响。
(3)硫化剂价格便宜、毒性小,使用安全可靠。
3 催化剂器内硫化 催化剂的湿法硫化可分为原料油自身的含硫化物的湿 法硫化和外加硫化剂湿法硫化两种。
虽然原料油的自身湿法 硫化方法简单、省事,但由于原料油本身所含硫化物低,难 以分解、分解温度高,容易使催化剂被还原的危险,一旦形 成低价态的金属氧化物, 就很难再与硫化氢反应, 则无法在 理想的时间内完成硫化,因此催化剂硫化效果较差。
加氢催化剂预硫化技术探讨

加氢催化剂预硫化技术探讨发表时间:2020-08-13T15:14:11.920Z 来源:《科学与技术》2020年3月第8期作者:铁鲁越[导读] 加氢催化剂大多是由Ni,W,Mo,Co等活性金属组分和载体组成,摘要:加氢催化剂大多是由Ni,W,Mo,Co等活性金属组分和载体组成,其中金属组分是以氧化态形式分散在载体上,可进行加氢脱硫、氮,加氢脱芳烃及加氢裂化等反应。
研究表明,未经预硫化的催化剂的活性、选择性和稳定性均低于硫化态的催化剂,而且使用寿命较短。
将氧化态的催化剂进行预硫化,使活性金属组分转变为硫化态,可最大限度的发挥加氢催化剂的活性,因而加氢催化剂预硫化技术的开发和应用,成为国内外研究的热点,受到广泛关注。
关键词:加氢;催化剂;预硫化技术 1 预硫化机理在加氢催化剂预硫化的过程中会放出大量的热量。
其反应原理是在H2存在的条件下,硫化剂加氢生成H2S,在H2和H2S同时存在的氛围下,加氢催化剂活性金属由氧化态转变为硫化态,预硫化过程分为如下两个反应步骤:加氢催化剂预硫化可使催化剂中的金属组分由氧化态变成硫化态,处于最佳活性价态。
在H2和H2S同时存在的条件下,金属氧化物上可发生还原反应和硫化反应的竞争,硫化效果的好坏会直接影响催化剂的性能和寿命,由于预硫化过程中放出大量的热,并伴随有水生成,因此预硫化过程中需密切监控反应器床层的温度和循环气中的水含量,防止床层飞温。
2 预硫化方式加氢催化剂的预硫化方式可根据硫化反应进行的场所不同,分为器内预硫化和器外硫化。
器内预硫化是在催化剂装入反应器之后,加入H2和硫化剂将金属活性组分转变为硫化态。
器内预硫化有干法预硫化和湿法预硫化两种方式。
干法预硫化是在H2存在的条件下,使用一定浓度的H2S、在循环气中注入CS2或使用其它有机硫化物;湿法预硫化是在H2存在下,用含硫化合物(如CS2或DMDS等)的烃类或馏分油在半液相或液相状态下进行硫化。
器外预硫化方式有两种:一种是将新鲜的或者再生后的催化剂进行硫化,再经冷却、钝化和过筛后装填到反应器;另一种是将硫化剂直接添加到氧化态的催化剂上,经处理后装入反应器。
加氢催化剂常用硫化剂的理化性质
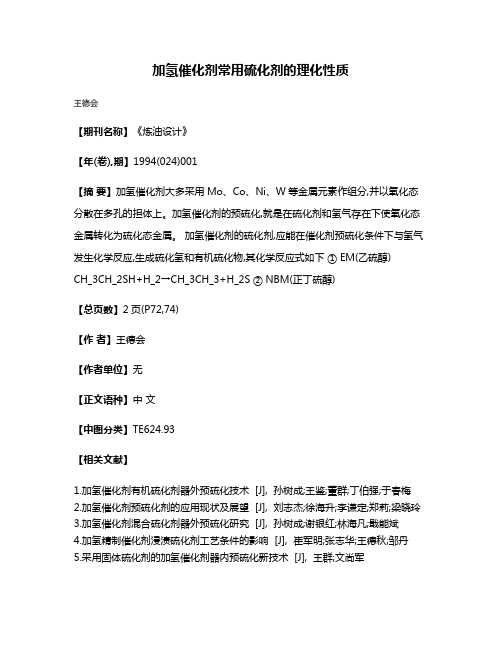
加氢催化剂常用硫化剂的理化性质
王德会
【期刊名称】《炼油设计》
【年(卷),期】1994(024)001
【摘要】加氢催化剂大多采用Mo、Co、Ni、W等金属元素作组分,并以氧化态分散在多孔的担体上。
加氢催化剂的预硫化,就是在硫化剂和氢气存在下使氧化态金属转化为硫化态金属。
加氢催化剂的硫化剂,应能在催化剂预硫化条件下与氢气发生化学反应,生成硫化氢和有机硫化物,其化学反应式如下① EM(乙硫醇)
CH_3CH_2SH+H_2→CH_3CH_3+H_2S ② NBM(正丁硫醇)
【总页数】2页(P72,74)
【作者】王德会
【作者单位】无
【正文语种】中文
【中图分类】TE624.93
【相关文献】
1.加氢催化剂有机硫化剂器外预硫化技术 [J], 孙树成;王鉴;董群;丁伯强;于春梅
2.加氢催化剂预硫化剂的应用现状及展望 [J], 刘志杰;徐海升;李谦定;郑莉;梁晓玲
3.加氢催化剂混合硫化剂器外预硫化研究 [J], 孙树成;谢银红;林海凡;戢能斌
4.加氢精制催化剂浸渍硫化剂工艺条件的影响 [J], 崔军明;张志华;王德秋;邹丹
5.采用固体硫化剂的加氢催化剂器内预硫化新技术 [J], 王群;文尚军
因版权原因,仅展示原文概要,查看原文内容请购买。
加氢催化剂预硫化技术进展
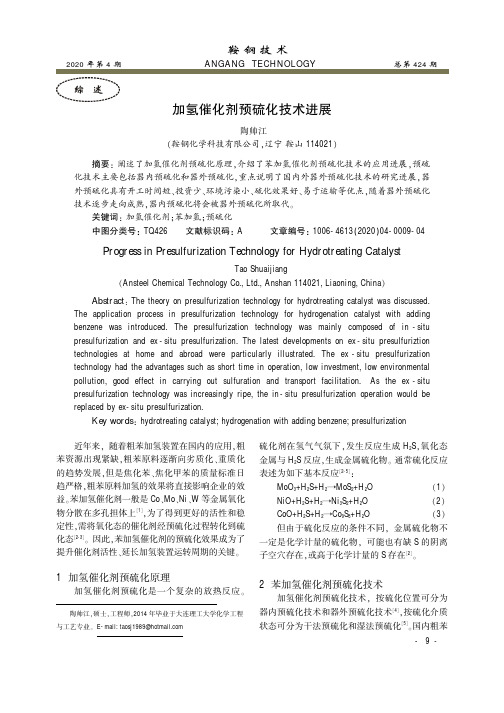
陶帅江,硕士,工程师,2014年毕业于大连理工大学化学工程与工艺专业。
E-mail:*********************加氢催化剂预硫化技术进展陶帅江(鞍钢化学科技有限公司,辽宁鞍山114021)摘要:阐述了加氢催化剂预硫化原理,介绍了苯加氢催化剂预硫化技术的应用进展,预硫化技术主要包括器内预硫化和器外预硫化,重点说明了国内外器外预硫化技术的研究进展,器外预硫化具有开工时间短、投资少、环境污染小、硫化效果好、易于运输等优点,随着器外预硫化技术逐步走向成熟,器内预硫化将会被器外预硫化所取代。
关键词:加氢催化剂;苯加氢;预硫化中图分类号:TQ426文献标识码:A文章编号:1006-4613(2020)04-0009-04Progress in Presulfurization Technology for Hydrotreating CatalystTao Shuaijiang(Ansteel Chemical Technology Co.,Ltd.,Anshan 114021,Liaoning,China )Abstract :The theory on presulfurization technology for hydrotreating catalyst was discussed.The application process in presulfurization technology for hydrogenation catalyst with addingbenzene was introduced.The presulfurization technology was mainly composed of in -situ presulfurization and ex -situ presulfurization.The latest developments on ex -situ presulfuriztion technologies at home and abroad were particularly illustrated.The ex -situ presulfurization technology had the advantages such as short time in operation,low investment,low environmental pollution,good effect in carrying out sulfuration and transport facilitation.As the ex -situpresulfurization technology was increasingly ripe,the in -situ presulfurization operation would be replaced by ex-situ presulfurization.Key words :hydrotreating catalyst;hydrogenation with adding benzene;presulfurization近年来,随着粗苯加氢装置在国内的应用,粗苯资源出现紧缺,粗苯原料逐渐向劣质化、重质化的趋势发展,但是焦化苯、焦化甲苯的质量标准日趋严格,粗苯原料加氢的效果将直接影响企业的效益。
一种加氢催化剂的硫化方法[发明专利]
![一种加氢催化剂的硫化方法[发明专利]](https://img.taocdn.com/s3/m/0b08c9cd4b35eefdc9d333c4.png)
专利名称:一种加氢催化剂的硫化方法
专利类型:发明专利
发明人:冯秋庆,黄岳寅,洪涛,孙祥,杜林,肖秋香,秦鸣霞,杨婧,李华金
申请号:CN200810024073.9
申请日:20080425
公开号:CN101260319A
公开日:
20080910
专利内容由知识产权出版社提供
摘要:一种加氢催化剂的硫化方法,它是将挂载了活性组分的催化剂只经过干燥除去催化剂中的游离水后直接在加氢反应器进行硫化,即将直馏石脑油或直馏煤油,加入其质量的2%的二硫化碳配制成硫化油,硫化油与氢混合后经热交换器升温进入加氢反应器,将加氢反应器的温度维持在催化剂的分解硫化温度,催化剂的分解硫化温度区间在150-450℃,严格控制升温速率,防止催化剂床层超温,升温速率为10℃/h-30℃/h,催化剂分解硫化结束后,系统程序降温,降温速率为25~45℃/h,温度降至催化剂正常反应温度时,将硫化油切换为需加氢精制处理的原料油,开始加氢处理,处理汽油在180-220℃,处理柴油在240-290℃。
本方法硫化的催化剂对油品进行加氢精制,脱硫效果好,而对辛烷值影响小。
申请人:江苏佳誉信实业有限公司
地址:212400 江苏省镇江市句容边城镇
国籍:CN
代理机构:南京知识律师事务所
代理人:黄嘉栋
更多信息请下载全文后查看。
加氢精制催化剂的硫化方法[发明专利]
![加氢精制催化剂的硫化方法[发明专利]](https://img.taocdn.com/s3/m/21a8bd39ba68a98271fe910ef12d2af90242a8d9.png)
(10)申请公布号 (43)申请公布日 2013.04.24C N 103059910 A (21)申请号 201110321357.6(22)申请日 2011.10.21C10G 45/08(2006.01)B01J 37/20(2006.01)(71)申请人中国石油化工股份有限公司地址100728 北京市朝阳区朝阳门北大街22号申请人中国石油化工股份有限公司抚顺石油化工研究院(72)发明人柳伟 刘继华 李扬 宋永一牛世坤 李士才 徐大海 丁贺赵桂芳(54)发明名称加氢精制催化剂的硫化方法(57)摘要本发明公开了一种加氢精制催化剂硫化方法。
首先在氮气氛围下,将催化剂床层温度升至120~180℃,开始注入硫化开工油;充分润湿后将催化剂床层温度升至230~260℃,用含硫化氢的氢气置换反应系统中的氮气,开始往反应系统注入硫化剂;待循环气中氢纯度大于75%后,按照正常的硫化过程进行硫化。
本发明在较高温度下才向系统内引入硫化氢和注入硫化剂,可以避免Co和/或Ni 的低温单独硫化,从而在较高温度和硫化氢存在的情况下,Mo 和/或W 与Co 和/或Ni同时硫化形成高活性Mo(W)-Co(N)-S 活性相,本发明方法有利于提高催化剂深度加氢脱硫活性。
(51)Int.Cl.权利要求书1页 说明书5页(19)中华人民共和国国家知识产权局(12)发明专利申请权利要求书1页 说明书5页(10)申请公布号CN 103059910 A*CN103059910A*1/1页1.一种加氢催化剂的硫化方法,包括以下步骤:(1)催化剂干燥结束且装置气密合格后,启动循环压缩机,用氮气升压,逐渐将催化剂床层入口温度升温至120~180 ℃,启动原料油泵注入硫化油;(2)待催化剂床层充分润湿后,升高催化剂床层温度至220~260℃,用含有硫化氢的氢气置换反应系统中的氮气,同时,开始往反应系统注入硫化剂;(3)待循环气中氢纯度大于75%后,在220~260℃恒温硫化2~10h ;恒温过程中控制循环气中硫化氢浓度为0.5v%~1.5v%;(4)步骤(3)中220~260 ℃恒温硫化结束后,继续升高催化剂床层温度至260~340 ℃,并在此温度下恒温硫化2~10 h ,硫化结束;恒温过程中控制循环气中硫化氢浓度为1.0v%~2.5v%。
一种加氢催化剂的预硫化方法、得到的预硫化加氢催化剂与应用[发明专利]
![一种加氢催化剂的预硫化方法、得到的预硫化加氢催化剂与应用[发明专利]](https://img.taocdn.com/s3/m/fc7560469a6648d7c1c708a1284ac850ad020496.png)
专利名称:一种加氢催化剂的预硫化方法、得到的预硫化加氢催化剂与应用
专利类型:发明专利
发明人:施晓秋,刘仲能,余强,刘东东
申请号:CN202011122723.0
申请日:20201020
公开号:CN114433092A
公开日:
20220506
专利内容由知识产权出版社提供
摘要:本发明公开了一种加氢催化剂的预硫化方法、得到的预硫化加氢催化剂与应用,所述预硫化方法包括以下步骤:步骤1、将含硫化合物分散于溶剂中,形成浸渍液;步骤2、将加氢催化剂浸渍于所述浸渍液中,静置、干燥得到预硫化前体;步骤3、对所述硫化前体于还原剂存在下进行处理,得到预硫化加氢催化剂。
在步骤1中,所述含硫化合物选自多硫化盐、硫代硫酸盐、亚硫酸盐、二硫化碳、二甲基二硫醚中的至少一种。
在步骤3中,所述还原剂选自有机酸,优选自醋酸、草酸、甲酸中的至少一种。
现有技术中,催化剂预硫化处理的常规还原性气体为氢气,而本发明采用有机酸,原因在于有机酸比氢气温和,加氢活性提高,寿命提高。
申请人:中国石油化工股份有限公司,中国石油化工股份有限公司上海石油化工研究院
地址:100728 北京市朝阳区朝阳门北大街22号
国籍:CN
更多信息请下载全文后查看。
- 1、下载文档前请自行甄别文档内容的完整性,平台不提供额外的编辑、内容补充、找答案等附加服务。
- 2、"仅部分预览"的文档,不可在线预览部分如存在完整性等问题,可反馈申请退款(可完整预览的文档不适用该条件!)。
- 3、如文档侵犯您的权益,请联系客服反馈,我们会尽快为您处理(人工客服工作时间:9:00-18:30)。
2011 年第 1 期 2011 年 1 月化学工程与装备 Chemical Engineering & Equipment59生产实践摘 前言 1 催化剂的硫化原理 应。
硫化的反应方程式如下: (CH3)2S2 +3H2 = 2H2S + 2CH4 MoO3+2H2S+H2 = MoS2+3H2O 9CoO+8H2S+H2 = Co9O8+9H2O 3NiO+2H2S+H2 = Ni3S2+3H2O WO3+2H2S+H2 = WS2+3H2O 2 硫化方法和硫化剂的选择 硫化。
加氢催化剂的硫化翟京宋(广西石化公司,广西 钦州 535008)要:加氢催化剂的硫化是提高催化剂活性、优化加氢催化剂操作,确保装置安全、平稳、高效运行。
本文从生产实践中介绍了加氢催化剂硫化的原理、方法、硫化剂的选择,以及催化剂器内硫化通用操作步 骤,并介绍了硫化过程中的事故处理、主要注意事项。
关键词:催化剂硫化;事故处理;注意事项CS2、二甲基二硫化物等)进行硫化;另一种是依靠硫化油 自身的硫进行硫化。
干法硫化是在氢气存在下, 直接用含有 一定浓度的硫化氢或直接向循环氢中注入有机硫化物进行 硫化。
在开工硫化阶段需要使用硫化剂, 而硫化剂的选择应考 虑以下因素: (1)硫化剂在临氢和催化剂存在的条件下,能在较低 反应温度下分解生成H2S,有利于催化剂硫化的顺利进行, 提高硫化效果。
(2) 硫化剂的硫含量应较高, 以减少硫化剂的使用量, 避免其他元素对硫化过程的不利影响。
(3)硫化剂价格便宜、毒性小,使用安全可靠。
3 催化剂器内硫化 催化剂的湿法硫化可分为原料油自身的含硫化物的湿 法硫化和外加硫化剂湿法硫化两种。
虽然原料油的自身湿法 硫化方法简单、省事,但由于原料油本身所含硫化物低,难 以分解、分解温度高,容易使催化剂被还原的危险,一旦形 成低价态的金属氧化物, 就很难再与硫化氢反应, 则无法在 理想的时间内完成硫化,因此催化剂硫化效果较差。
在湿法硫化中,使用馏分油作为催化剂湿法硫化用油, 其馏分范围一般应接近或略轻于加氢原料油, 通常以直馏柴 油馏分应用较多, 不含烯烃且氮含量应低于200ppm, 其总硫 含量要求低于2% wt(包括加入的有机含硫化合物) 。
烯烃加 氢反应会增加放热并导致催化剂上焦炭沉积, 为取得好的硫 化效果,所选用的硫化油的干点不宜过高(一般不大于 370ºC) 。
因为在硫化温度下可能发生饱和反应对正常的硫化 操作造成干扰,导致催化剂床层温度不稳定,氢耗过高,同 时裂化原料中含有转化难度很高的含氮化合物, 具有较强的 吸附能力和较高结焦倾向。
3.1 催化剂的湿法硫化新鲜的催化剂或再生后的催化剂, 其所含的活性金属组 分(Mo、Ni、Co、W)都是以氧化态的形式存在。
经过研究 和工业化运用实践证明,当催化剂以硫化态的形态存在时, 催化剂具有较高的活性、稳定性和选择性,抗毒性强,寿命 长,才能够最大限度地发挥加氢催化剂的作用。
催化剂的硫化是在一定的温度和氢气分压下, 通过加氢 催化剂中的氧化态活性组分(氧化镍、氧化钼等)和硫化剂 化学作用变为活性较高的硫化态金属组分, 达到催化剂长周 期稳定运行的目的。
催化剂硫化是基于硫化剂临氢分解生产 的 H2S 将催化剂活性金属氧化态转化为相应金属硫化态的反硫化技术的分类方法根据硫化反应进行的场所来确定, 加氢催化剂硫化可分为器内硫化和器外硫化。
而催化剂的器 内预硫化可以分为气相(干法)预硫化和液相(湿法)预硫 化两大类。
目前, 国内工业加氢装置大都实行器内预硫化方 法, 除对于择形裂解活性, 弱加氢活性的临氢活性的降凝催 化剂、 分子筛加氢裂化催化剂的预硫化大多采用干法硫化以 外, 其他的加氢精制、 加氢处理装置的催化剂普遍采用湿法 湿法硫化是在氢气存在下, 采用含有硫化物的烃类或馏 分油在液相或半液相状态下硫化。
湿法硫化又分为两种, 一 种是催化剂硫化过程所需要的硫由外部加入的硫化物(如60 通用的催化剂湿法硫化过程如下:翟京宋:加氢催化剂的硫化量(催化剂硫化理论需硫量) ,反应器床层温升不再增加, 则催化剂的干法硫化结束。
4(1)氢气全量循环,将催化剂床层温度控制在 150~160 ºC,或者根据不同的催化剂要求,催化剂的床层温度控硫化过程的事故处理 硫化剂中断后会导致催化剂缺少硫化氢, 从而导致催化制更低。
(2)以小于或等于设计体积空速向反应系统引入硫化 油,并根据循环氢流率、催化剂装填量、催化剂硫化的理论 需硫量及硫化时间等相关条件,确定起始的注硫量。
(3)待反应器催化剂床层温度稳定后,以较慢的速度 提升反应器入口温度,在循环氢中检测出 H2S 之前,催化 剂床层任一点温度不得超过 230ºC。
(4)当循环氢中的 H2S 浓度大于 0.1%时,调整反应器 入口温度,使催化剂床层温度维持在 230 ºC 左右,恒温硫 化一定时间(一般不得少于 8h) ,此期间循环氢中 H2S 浓度 应维持在 0.1%~0.5%; (5)230 ºC 恒温硫化结束后,调整硫化剂的注入量, 使循环氢中的硫化氢浓度达到 0.5%~2.0%,同时以适宜的 升温速度,将反应器入口温度提升至 290 ºC,并恒温硫化8h。
4.1 硫化剂中断剂金属还原和活性损失。
发生硫化剂中断时应立即降低催化 剂的床层温度,直到恢复硫化剂的注入。
如果催化剂硫化过程中硫化剂中断,可按以下步骤处 理。
(1)反应器立即停止升温。
(2)如果硫化氢穿透之前发生硫化剂中断,把反应器 温度降到注硫温度以下。
如果穿透之后发生硫化剂中断, 催 化剂床层温度降到比硫化剂中断时的温度低 30℃,并定期 检查循环氢中硫化氢的含量, 如果循环氢中的硫化氢含量已 经明显减少时,则继续把温度降低到 175℃以下。
(3)当硫化剂恢复注入时,把床层温度升到 DMDS 中 断时的温度,然后继续正常的硫化步骤。
(4)如果注入硫化剂后,观察不到反应器床层入口温 度的上升, 必须检查硫化剂是否已经注入, 若已经注入硫化 剂则停止注硫。
待反应器入口温度提高至硫化剂的分解温度 后,再恢复注入硫化剂。
4.2 循环氢中断(6)290 ºC 恒温硫化结束后,调整循环氢中 H2S 浓度 至 1.0%~2.0%(任何时候循环氢中的 H2S 浓度都不能超过2.0%) , 提高反应器入口温度, 当催化剂床层温度升至 320 ºC左右时,再恒温硫化一段时间。
( 7 )若硫化剂注入量已达硫化理论需硫量的 100 ~120%,且催化剂床层基本无温升、高分生成水量无明显增循环氢作为携带出硫化反应放出的反应热量的介质, 如 果出现循环氢压缩机故障, 导致循环氢中断时, 新鲜催化剂 上有可能发生飞温现象。
如果硫化期间发生循环氢压缩机故 障, 按正常停循环氢压缩机步骤处理, 并且切断硫化剂的注 入。
当循环氢压缩机重新启动时, 操作员必须密切观察催化 剂床层温度的变化, 必要时用冷氢控制催化剂床层温度。
催 化剂床层温度稳定后, 重新注入硫化剂恢复硫化。
在催化剂 床层温度稳定之前不要注入 DMDS,否则会使催化剂床层 温度更加不稳定。
4.3 氢气中断加后,催化剂硫化结束。
3.2 催化剂的干法硫化新鲜或再生后的催化剂, 在与油接触之前, 均需要在严 格控制的工艺条件下进行硫化。
催化剂干法硫化通常是在装 置的操作压力、 循环氢压缩机全量循环的条件下进行, 起始 硫化温度为175℃,终止硫化温度为370℃。
在催化剂干法硫化的过程中, 首先要根据操作压力、 循 环氢流率来确定催化剂硫化的最大起始注硫速率。
在最大起 始注硫速率下,按反应器入口循环氢中 H2S 浓度为 0.30 ~0.33%(体积)来估算。
当发生氢气中断时,按以下步骤进行处理。
(1)停止注入硫化剂,如果反应系统正在排放废氢, 则立即停止排放。
保持最大量氢气循环, 并迅速将催化剂床 层入口温度降到 175℃,必要时使用冷氢控制床层温度。
(2)当氢气恢复时,反应系统压力恢复至正常操作压 力,温度升至 175℃,重新注入硫化剂。
如果循环氢中硫化 氢含量超过 1.0%时减少硫化剂注入量,如果循环氢中硫化 氢含量超过 2.0%时停止注入 DMDS,循环氢中硫化氢含量 开始减少后再逐渐恢复注硫。
(下接第77页)催化剂硫化是从低温到高温分阶段进行的, 各个硫化阶 段,除了对循环氢中的 H2S 含量有一定的要求外,还有一 些相应的控制指标要求和限制条件。
催化剂干法硫化的主要控制指标和限制条件主要有: 各 个硫化阶段的升温速率、 循环氢中的硫化氢浓度、 床层温升、 硫化恒温时间等。
当催化剂 370℃恒温硫化已经超过 8h, 若反应器出入口 循环氢中的水含量、H2S 浓度相近,高分生成水量不再增加 (或变化甚微) ,硫化剂的注入量已达到或者接近预定的用张国星:入炉煤水分对焦炭强度的影响77由图1可以看到随着水分的减小,焦炭M40指标逐渐变 好,但从10%到6%的区间变化趋势趋缓。
由表2可以看到焦炭的热性能随着入炉煤水分的升高逐 渐变差, 这跟上面分析的焦炭成焦过程有关。
成焦过程中产 生的大量气孔, 致使焦炭在高温下反应性变大, 反应后强度 变差。
3 结论 (1)虽然入炉煤的水分对煤料本身所固有的性质没有 产生影响但, 但在炼焦过程中对焦炉生产有影响。
由于入炉 煤水分大, 能使立火道的温度降低。
如果温度过低焦炭收缩 性不好,不成熟,这时推焦的话容易造成推焦困难,甚至损坏炉体。
如果要使焦炭按时成熟, 就得增加燃烧的回炉煤气 量,增加了耗热量,增加回炉煤气的使用量。
(2)在固定入炉煤重量的生产条件下,入炉煤水分高 将影响焦炭的产量, 降低生产效率, 因此应该尽可能的降低 入炉煤水分。
(3)考虑到过低的入炉煤水分会引起粉尘等过多等问 题,水分不易控制太低。
(4)通过以上分析,焦炭在入炉煤水分较低的情况下 有较高的冷热性能, 但考虑到生产中不具备配合煤干燥的条 件的情况下控制 10%的入炉煤水分比较经济合理。
(上接第 60 页)4.4 反应器温度偏离和飞温 一般注入硫化剂后, 催化剂床层会产生一定的温波。
该 温波通过反应器, 需要半小时或更长时间, 在温波未通过反 应器催化剂床层之前, 应保持反应器入口温度恒定, 硫化操 作不能继续进行,如果温波超过 30℃时要降低硫化剂的注 入量。
催化剂硫化期间, 不允许反应器床层任何点温度超过设 计值, 且任一床层温升不能超过允许的最大温升。
硫化期间 发生反应器床层温度偏离或飞温情况, 一般是因为在该催化 剂床层温度下注入的 DMDS 太多。