电子装联技术
电子行业电子装联工艺技术课件
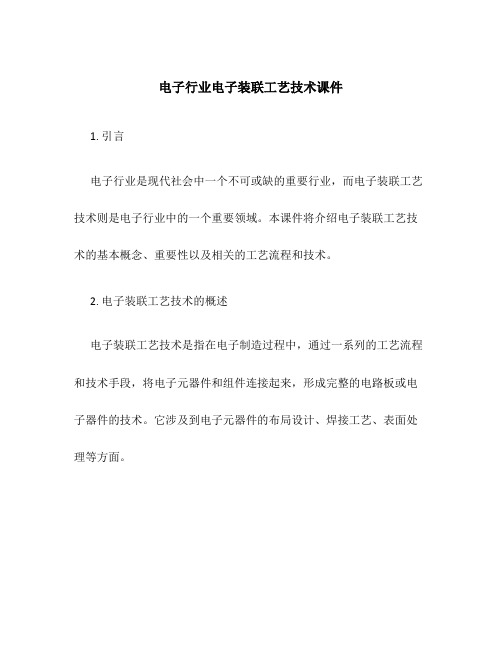
电子行业电子装联工艺技术课件1. 引言电子行业是现代社会中一个不可或缺的重要行业,而电子装联工艺技术则是电子行业中的一个重要领域。
本课件将介绍电子装联工艺技术的基本概念、重要性以及相关的工艺流程和技术。
2. 电子装联工艺技术的概述电子装联工艺技术是指在电子制造过程中,通过一系列的工艺流程和技术手段,将电子元器件和组件连接起来,形成完整的电路板或电子器件的技术。
它涉及到电子元器件的布局设计、焊接工艺、表面处理等方面。
3. 电子装联工艺技术的重要性电子装联工艺技术在电子制造中起着至关重要的作用。
它不仅直接影响到电子产品的质量,还关系到产品的可靠性和寿命。
合理的工艺技术能够提高产品的性能和稳定性,减少生产成本,提高生产效率。
4. 电子装联工艺技术的工艺流程4.1 元器件布局设计 - 元器件布局设计是电子装联工艺技术的第一步,它涉及到元器件的选型和布局设计,要考虑到电路的功能要求、接线的合理性以及生产工艺的可行性。
- 元器件布局设计的目标是最大程度地减少电路板上的线路长度和线路复杂度,提高电路板的性能和稳定性。
4.2 焊接工艺 - 焊接工艺是电子装联工艺技术中最关键的一个环节。
- 常见的焊接工艺包括手工焊接、波峰焊接、表面贴装焊接等。
- 焊接工艺的选择要根据电路板的设计和元器件的要求来确定,同时要考虑到生产效率和成本。
4.3 表面处理 - 表面处理是为了改善电子元器件的导电性和耐环境腐蚀性。
- 常见的表面处理方法包括镀金、镀锡和喷锡等。
- 表面处理工艺的选择要根据产品的要求和使用环境来确定。
5. 电子装联工艺技术的常见问题与解决方法5.1 接触不良问题 - 这是电子装联工艺技术中常见的问题之一,可能导致电路板无法正常工作。
- 解决方法包括重新焊接、更换元器件等。
5.2 过热问题 - 在焊接过程中,由于温度过高可导致元器件损坏。
- 解决方法包括控制焊接温度、加强散热设计等。
5.3 氧化问题 - 元器件的接触表面可能会因为氧化而导致导电性能下降。
现代电子装联先进制造技术的发展展望(二)

五.电子装联1.电子装联的基本概念1)电子组装(Electronic packaging)的定义根据成熟的电路原理图,将各种电子元器件、机电元器件以及基板合理地设计、互连、安装、调试,使其成为适用的、可生产的电子产品(包括集成电路、模块、整机、系统)的技术过程。
2)电子装联技术电子装联技术缩写为EICT,俗称电装技术;是按照电子装备总体设计的技术要求,通过一定的连接技术和连接用辅料等手段,将构成电子装备的各种光、电元器件、部件和组件等,在电气上互连成一个具有特定功能的和预期的技术性能的完整的功能体系的全过程。
它包含了从板级组装互连、机柜组装互连、以及它们之间通过线缆互连而构成一个满足预期设计技术要求的设备体系的所有工序的集合。
电子装联技术,包括从产品设计的可制造性(DFM)、可组装性(DFA)、可检测性(DFT)、可维修性(DFS)、可靠性(DFR)和环境适应性(DFE),到原材料进厂的工艺性要求、加工制造诸元素(人、料、机、测、环)的优化和控制以及对应用环境的防护措施等全部加工制造和管理技术的总和。
电子装联技术是一门电路、工艺、结构、组件、器件、材料紧密结合的多学科交叉的工程学科;涉及集成电路固态技术、厚薄膜混合微电子技术、印制电路技术、THT、SMT、MPT、电子电路技术、CAD/CAPP/CAM/CAT技术、互连与连接技术、热控制技术、封装技术、测量技术、微电子学、物理学、化学、金属学、电子学、机械学、计算机学、材料科学、陶瓷及硅酸盐学等领域。
3)电子装联工程包括电子装联工艺、电子组装技术和电子封装工程三个领域,都是应用各种组装技术将电子元器件及部件转为产品的技术。
(1)电子装联工艺一般是将电子元器件通过基板、背板、线缆进行互连的技术;(2)电子组装技术是指将半导体、电子元器件安装在基板上的技术,它主要包括通孔插装技术(THT)、表面组装技术(SMT)和微组装技术(MPT),例如MCM、DCA。
电子装联工艺技术

保持一定的弯曲半径,以消除应力影响; 保持元器件本体或熔接点到弯曲点的最小距离至少为2倍
的引线直径或厚度,但不得小于0.75mm。 引线成形后的尺寸与PCB安装孔孔距相匹配; 引线直径大于1.3mm时,一般不可弯曲成形,小于1.3mm的硬引线(回火处
3.1 元器件通孔插装(THT)
3.1.2 安装次序 先低后高、先轻后重、先非敏感元器件后敏感元件、先
表面安装后通孔插装、先分立元器件后集成电路。
3.1 元器件通孔插装(THT)
3.1.3安装要求 安装高度要符合产品防震、绝缘、散热等要求及设计文件要求; 元器件加固要求:7g、3.5g及设计工艺文件的规定; 接线端子、铆钉不应作界面或层间连接用,导通孔(金属化孔)不能安装元器件; 一孔一线,孔径与引线直径的合理间隙(0.2~0.4mm) 空心铆钉不能用于电气连接; 元器件之间有至少为1.6mm的安全间距; 元器件安装后,引线伸出板面的长度应为1.5±0.8mm; 元器件安装后,引线端头采用弯曲连接时,引线弯曲长度为3.5 ~5.5d; 如底面无裸露的电路(印制导线);元件可贴板安装(玻璃二极管除外),如底面有裸露电路,
2.2 元器件引线搪锡工艺
锡和锡铅合金为最佳的可焊性镀层,其厚度
为5~7μm。 镀金引线的搪锡(除金):
Cu μm/s
金镀层是抗氧化性很强的镀层,与SnPb焊料
Ag Au
7
有很好的润湿性,但直接焊接金镀层时,
6
Pb
5
SnPb合金对金镀层产生强烈的溶解作用,金
4
Pt 3
与焊料中的Sn金属结合生成AuSn4合金,枝晶 2
对于表面贴装元器件,不管金层厚度为多少,在焊接前,应去除至少95% 被焊表面的金层;
电子装联基础知识
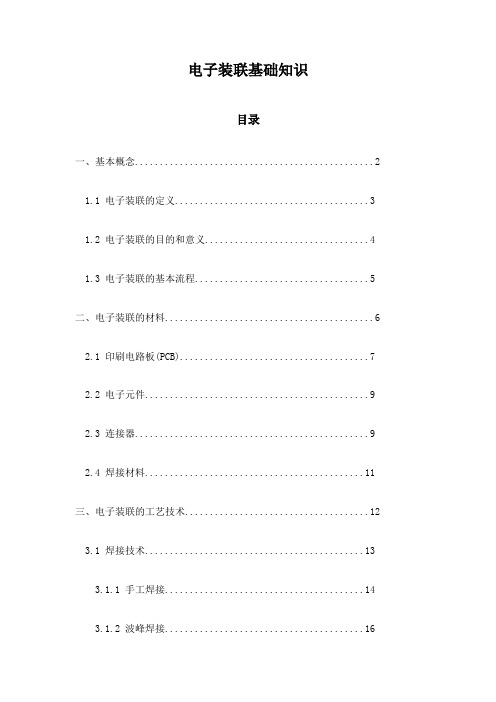
电子装联基础知识目录一、基本概念 (2)1.1 电子装联的定义 (3)1.2 电子装联的目的和意义 (4)1.3 电子装联的基本流程 (5)二、电子装联的材料 (6)2.1 印刷电路板(PCB) (7)2.2 电子元件 (9)2.3 连接器 (9)2.4 焊接材料 (11)三、电子装联的工艺技术 (12)3.1 焊接技术 (13)3.1.1 手工焊接 (14)3.1.2 波峰焊接 (16)3.1.3 回流焊接 (17)3.2 装配技术 (18)3.2.1 零件装配 (19)3.2.2 组件装配 (20)3.3 导线加工技术 (21)3.3.1 导线剥皮 (23)3.3.2 导线接头制作 (24)3.3.3 导线固定 (25)四、电子装联的质量控制 (26)4.1 质量管理体系 (27)4.2 质量控制流程 (28)4.3 质量检测方法 (30)五、电子装联的标准化与规范化 (30)5.1 标准化工作 (32)5.2 规范化操作 (33)六、电子装联的发展趋势与创新 (34)6.1 智能化生产 (36)6.2 自动化与机器人技术 (37)6.3 绿色制造与环保要求 (38)一、基本概念电子装联基础知识是电子制造领域中的基础环节,涉及到电子元器件的组装、焊接、测试等一系列过程。
这一环节的质量直接影响到电子产品的性能和可靠性。
电子元器件:这是构成电子产品的基本单元,包括电阻、电容、电感、二极管、晶体管等。
这些元件通过特定的封装形式(如SMD,即表面贴装设备)被集成到电路板上。
电路板:作为电子元器件的支撑和连接载体,电路板通常由多层印刷电路板(PCB)组成,上面布满了导电层和绝缘层,用于传输电流和信号。
焊接技术:焊接是将电子元器件与电路板牢固连接的关键步骤。
常见的焊接方法有手动焊接和波峰焊接等,手动焊接适用于短期建立稳定的电气连接,而波峰焊接则适合大批量生产。
装配:装配是将电子元器件按照设计要求组装到电路板上的过程。
现代电子装联工艺技术浅析
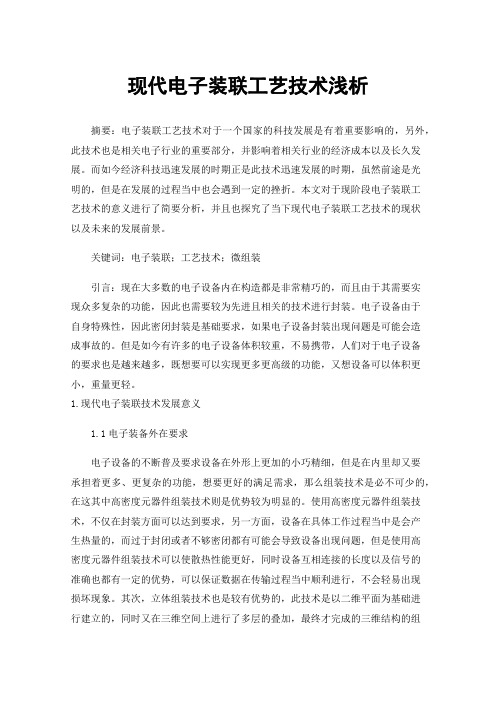
现代电子装联工艺技术浅析摘要:电子装联工艺技术对于一个国家的科技发展是有着重要影响的,另外,此技术也是相关电子行业的重要部分,并影响着相关行业的经济成本以及长久发展。
而如今经济科技迅速发展的时期正是此技术迅速发展的时期,虽然前途是光明的,但是在发展的过程当中也会遇到一定的挫折。
本文对于现阶段电子装联工艺技术的意义进行了简要分析,并且也探究了当下现代电子装联工艺技术的现状以及未来的发展前景。
关键词:电子装联;工艺技术;微组装引言:现在大多数的电子设备内在构造都是非常精巧的,而且由于其需要实现众多复杂的功能,因此也需要较为先进且相关的技术进行封装。
电子设备由于自身特殊性,因此密闭封装是基础要求,如果电子设备封装出现问题是可能会造成事故的。
但是如今有许多的电子设备体积较重,不易携带,人们对于电子设备的要求也是越来越多,既想要可以实现更多更高级的功能,又想设备可以体积更小,重量更轻。
1.现代电子装联技术发展意义1.1电子装备外在要求电子设备的不断普及要求设备在外形上更加的小巧精细,但是在内里却又要承担着更多、更复杂的功能,想要更好的满足需求,那么组装技术是必不可少的,在这其中高密度元器件组装技术则是优势较为明显的。
使用高密度元器件组装技术,不仅在封装方面可以达到要求,另一方面,设备在具体工作过程当中是会产生热量的,而过于封闭或者不够密闭都有可能会导致设备出现问题,但是使用高密度元器件组装技术可以使散热性能更好,同时设备互相连接的长度以及信号的准确也都有一定的优势,可以保证数据在传输过程当中顺利进行,不会轻易出现损坏现象。
其次,立体组装技术也是较有优势的,此技术是以二维平面为基础进行建立的,同时又在三维空间上进行了多层的叠加,最终才完成的三维结构的组装。
例如,三维电路在装配的过程当中,体积较小,重量较轻的组件占比较多,甚至已经达到80%,而由于此技术的优势所在,不仅可以使设备在重量和体积上达到更加小型化,另外在此基础上,装配空间的使用效率反而可以得到增加,在三维空间内可以得到更加全面且更好的信号以及更快的传输速度,在传输的过程当中也可以减少电路干扰程度,更好地进行工作。
电子装联技术概述
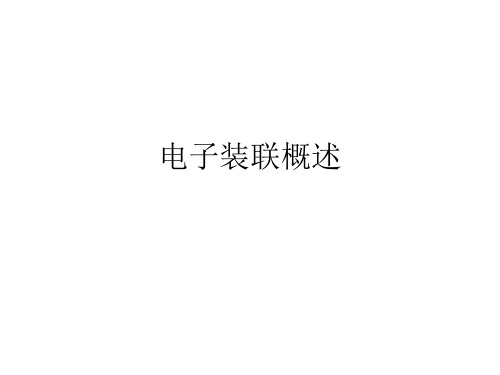
• 机构件的形式更加标准化和模块化,结构 设计的可制造性较好,结构设计基本上能 符合先进加工设备的要求;
• 机的问题—电路设计
• 电子装联的情况很不乐观:如果说结构设 计专业与机加工工艺在技术上有某些共性 之处,那么电路设计专业和电子装联技术 根本没有共性之处;与结构设计人员对机 加工工艺和机加工设备的了解相比较,电 路设计人员对电子装联技术和电子装联设 备的了解就显得十分不足;
电子装联焊接管理五个方面
• 设计可制造性DFM(Design for manufacture)
• 物流质量(采购、外包、流转、储存等生 产过程的各个环节,都应符合电子装联质 量要求。) • 工艺优化(现场工艺=?DFM、产品导入和 工艺试制) • 管理模式 • 人员素质
管理模式
• 必须建立一个完整的工艺体系,包括有一 个独立的工艺研究部门;建立比较完善的 电装工艺规范,包括针对电路设计的规范 和针对制造的规范;建立可制造性设计的 企业文化;具有创新能力,能够开展先进 制造技术研究和建立完整的电装工艺师系 统。
• 绝大部分的电子装联还基本上处于手工作 业,因此在机加工工人大幅度减少的同时, 电装工人的数量不但没有减少,反而不断 增加。
• 一方面是电路设计跟不上元器件、电子装 联技术和电子装联设备的高速发展,电路 设计文件可制造性差; • 另一方面,绝大部分电子产品的电子装联 基本上还处于手工作业,新工人大量增加, 组装焊接质量得不到有效保证;而我们的 工艺管理模式又制约了这些矛盾的解决; 这几个因素加起来对于电装工艺无疑是雪 上加霜,电装工艺真可谓是举步维艰
工艺不等于手艺
• • • • • 知识面 融会贯通, 对技术精益求精 多去想办法,多动脑筋 处理复杂技术问题的能力和应变能力。
电子产品装联技术介绍课件
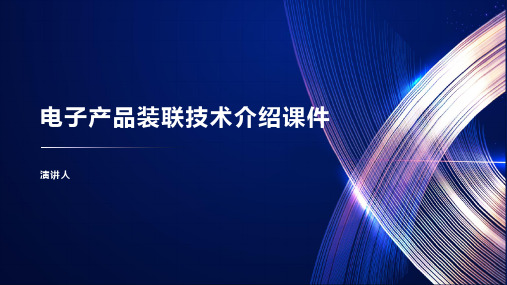
装联技术的发展趋势
01
自动化:提高生产效率, 降低人工成本
02
智能化:实现自动检测、 自动调整、自动优化
03
绿色化:减少废弃物,降 低能耗,提高环保性能
04
微型化:提高集成度, 减小体积,降低成本
05
网络化:实现远程监控、 远程诊断、远程维护
06
定制化:满足不同客户需 求,提高产品竞争力
电子产品装联技术 的分类
电子产品维修过程中的应用
检测故障:利用装联技术检测电子 01 产品的故障部位和原因
更换部件:利用装联技术更换损坏 02 的电子部件
修复电路:利用装联技术修复电子 03 产品的电路问题
升级改造:利用装联技术对电子产 0 4 品进行升级改造,提高性能和功能
电子产品升级改造过程中的应用
01
更换电子元件:通过更换更高性能的电
焊接技术
手工焊接:使用 电烙铁、焊锡丝 等工具进行焊接
回流焊接:利用 熔融焊料在电路 板表面流动,实 现元器件的焊接
波峰焊接:利用 熔融焊料在电路 板表面流动,实 现元器件的焊接
激光焊接:利用 激光束进行焊接, 精度高,速度快
连接器技术
1 连接器类型:插头、插座、端子等 2 连接器功能:传输信号、电源、数据等 3 连接器材料:金属、塑料、陶瓷等 4 连接器结构:线对线、线对板、板对板等 5 连接器应用:消费电子、汽车电子、医疗电子等 6 连接器发展趋势:小型化、高速化、智能化等
02
智能检测技术:提高产 品质量,减少不良品率
01
自动化生产线:提高生 产效率,降低人工成本
谢谢
子元件,提高电子产品的性能和功能。
02
优化电路设计:通过优化电路设计,提
电子装联技术讲义---杨松林

2、电缆装配技术介绍
2、电缆装配技术介绍
2.1.2、常用的射频电缆以外导体来划分可分为半刚、 半柔、柔性三大类。 2.1.2.1、半刚性电缆:外导体多为无缝紫铜管,内导
体为铜包钢镀银线,在内导体与外导体之间是实芯或
包绕聚四氟乙烯介质,常用的半刚性电缆有:SFT50-3、SFT-50-2;
2、电缆装配技术介绍
2、电缆装配技术介绍
⑥按图4装外壳(1),将衬管(6)旋入外壳用专用扳手扳紧。 ⑦标牌按图要求作标记,安装在距插头尾端30mm处。
图4.
2、电缆装配技术介绍
(3) TNC插头装配工艺(插头TNC-J3,电缆SYV-50-2-1) 同BNC装配工艺相同,唯一区别就是插头外壳的连接形式不一样! (4)N型插头装配工艺(插头N-J5,电缆SYV-50-3) 同BNC装配工艺剥头尺寸存在一定差异,如下:
2、电缆装配技术介绍
2.1.3、射频电缆主要有以下几个参数: (4)相位稳定性:相位稳定性一般是指电缆在弯曲 时相位的变化情况,一般来说电缆弯曲半径越小或 弯曲次数越多,相位变化越大。同时传输信号频率、 电缆介质形式都会对电缆的相位稳定性产生影响。 (5)插损:是衡量电缆信号传输效率的一个重要指 标。同轴电缆的插损是同轴电缆在信号传输时的介 质损耗、外导体损耗、内导体损耗之和。 (6)驻波:驻波通常用电压驻波比(VSWR)来表 征。同时驻波也是表征回波损耗的一个物理量。
④以接地套(2)端面为基准,保留芯线绝缘层0.4mm,剥去其余 的绝缘层(不得损伤芯线),保证芯线长度为4mm,芯线浸锡并用 无水乙醇纱布清洗(参见图4)。 ⑤将插芯(8)焊接孔内用烙铁浸入少量焊锡,插芯(8)插入绝缘 子(7)内再插入芯线进行焊接,焊后用无水乙醇、纱布进行清洗, 要求插芯外表面平滑光洁、无锡锡瘤,插芯焊接良好,无虚焊,多 余的焊锡可用刀片刮去。
电子装联技术PPT课件
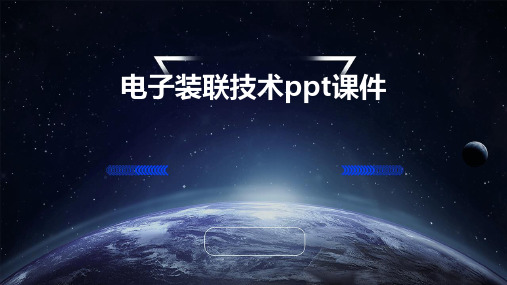
排列规则
遵循一定的排列规则,使元器件易 于识别、装配和维护,同时保持产 品美观。
考虑散热
合理规划元器件的布局,有利于散 热设计和降低温升,提高产品稳定 性和寿命。
焊接质量的控制
焊接材料选择
根据元器件和基材的特性,选择合适 的焊接材料,确保焊接质量可靠。
焊接温度和时间控制
焊点检测
采用适当的检测手段,对焊点进行质 量检查和控制,及时发现并处理不良 焊点。
评估电子装联产品在电磁干扰环境下能否正常工作,不会出 现性能下降或故障。
05
电子装联技术的实际应用案例
手机电路板的装联技术
手机电路板装联技术
随着手机功能的多样化,手机电路板 上的元器件数量不断增加,对装联技 术的要求也越来越高。目前,常用的 手机电路板装联技术包括表面贴装技 术(SMT)和通孔插装技术(THT)。 表面贴装技术主要用于将小型化的元 器件安装在手机电路板的表面,而通 孔插装技术则用于将元器件插入电路 板的通孔中。
可靠性检测
在模拟实际工作环境下,对电子装联 产品进行长时间运行或加速老化试验, 以评估其可靠性。
可靠性评估的指标与测试方法
平均故障间隔时间(MTBF)
衡量电子装联产品在正常工作条件下平均无故障运行的时间长度。
故障率
评估电子装联产品在规定时间内出现故障的概率。
可靠性增长
通过在各种环境条件下进行加速老化试验,监测电子装联产品的性能 退化情况,以评估其可靠性增长。
02
电子装联技术的基本原理
电路板的基本组成
电路板主要由导电材 料制成,如铜箔,具 有传导电流的作用。
电路板上的导电路径 或迹线用于连接元器 件的引脚,形成完整 的电路。
绝缘材料作为基板, 提供支撑和保护电路, 防止短路和断路。
电子装联技术
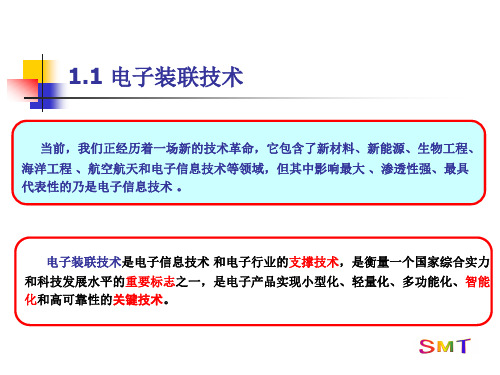
1.3 表面组装技术——SMT
SMT工艺技术的发展趋势: A. 与新型表面组装元器件的组装相适应; B. 与新型组装材料的发展相适应; C. 与现代电子产品的品种多、更新快特性相适应; D. 与新型组装形式的组装要求相适应;
1.4 SMT与THT的比较
从组装工艺技术的角度分析,是“贴”和“插”
SMT和THT的根本区别
波峰焊是将熔融的液态焊料﹐借助泵的作用﹐在焊料 槽液面形成特定形状的焊料波﹐插装(贴装)了元器 件的PCB置于传送链上﹐经过某一特定的角度以及一 定的浸入深度直线穿过焊料波峰而实现焊点焊接的过 程。
1.2 THT技术—波峰焊
链条倾角3至7度
压锡深度为PCB厚度的 1/3~1/2
助 焊 剂 涂 覆
焊接
1.5 MPT技术简介
微组装技术始于二十世纪八十年代中期,被人们称之为第五代电子装联技术。 该技术的核心是打破了元器件封装与印制板焊装的界限,将半导体集成电技 术、薄/厚膜混合集成电路技术、表面贴装技术以及封工艺加以综合运用, 在多层板上高密度地实施机械与电子互连,在板级完成系统的组装。实现电 子产品(如组件、部件、系统)的外形微小化、功能模块化。20世纪律性 80年代后期就出现的多芯片组件/模块(MCM)就是微组装技术实用化中最 具有代表性的产品之一。
1.2 THT技术—成型
电容的成型
电阻的成型
1.2 THT技术—成型
1.2 THT技术—成型
元器件引线的弯曲成型要求
⑴ 引线弯曲的最小半径不得小于引线直径的2倍,不能“打死弯”; ⑵ 引线弯曲处距离元器件本体至少在2mm以上,绝对不能从引线 的根部开始弯折。
1.2 THT技术—成型
滚轮式电阻整形机
1.3 表面组装技术——SMT
电子装联技术在整机装配中的应用
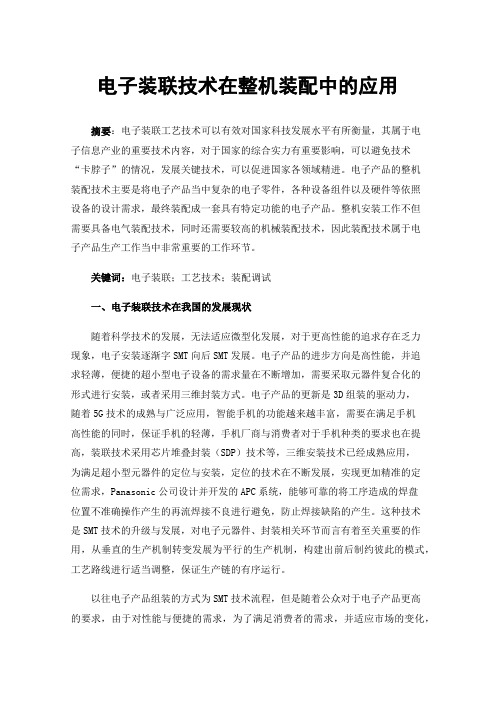
电子装联技术在整机装配中的应用摘要:电子装联工艺技术可以有效对国家科技发展水平有所衡量,其属于电子信息产业的重要技术内容,对于国家的综合实力有重要影响,可以避免技术“卡脖子”的情况,发展关键技术,可以促进国家各领域精进。
电子产品的整机装配技术主要是将电子产品当中复杂的电子零件,各种设备组件以及硬件等依照设备的设计需求,最终装配成一套具有特定功能的电子产品。
整机安装工作不但需要具备电气装配技术,同时还需要较高的机械装配技术,因此装配技术属于电子产品生产工作当中非常重要的工作环节。
关键词:电子装联;工艺技术;装配调试一、电子装联技术在我国的发展现状随着科学技术的发展,无法适应微型化发展,对于更高性能的追求存在乏力现象,电子安装逐渐字SMT向后SMT发展。
电子产品的进步方向是高性能,并追求轻薄,便捷的超小型电子设备的需求量在不断增加,需要采取元器件复合化的形式进行安装,或者采用三维封装方式。
电子产品的更新是3D组装的驱动力,随着5G技术的成熟与广泛应用,智能手机的功能越来越丰富,需要在满足手机高性能的同时,保证手机的轻薄,手机厂商与消费者对于手机种类的要求也在提高,装联技术采用芯片堆叠封装(SDP)技术等,三维安装技术已经成熟应用,为满足超小型元器件的定位与安装,定位的技术在不断发展,实现更加精准的定位需求,Panasonic公司设计并开发的APC系统,能够可靠的将工序造成的焊盘位置不准确操作产生的再流焊接不良进行避免,防止焊接缺陷的产生。
这种技术是SMT技术的升级与发展,对电子元器件、封装相关环节而言有着至关重要的作用,从垂直的生产机制转变发展为平行的生产机制,构建出前后制约彼此的模式,工艺路线进行适当调整,保证生产链的有序运行。
以往电子产品组装的方式为SMT技术流程,但是随着公众对于电子产品更高的要求,由于对性能与便捷的需求,为了满足消费者的需求,并适应市场的变化,我国电子装联工艺技术已经提供技水准,增强自身技术提高。
整机电子装联技术

19 印制板组件装配技 术
19.4 通孔插装工艺
19.4.1 元器件搪锡 19.4.2 元器件成型 19.4.3 元器件焊接
20 电缆组件装配技术
20.1 低频 电缆组件制
造技术
20.2 射频 电缆组件装
配技术
20.3 线扎 的制作
20 电缆组件装配技术
20.1 低频电缆组件制造技术
20.1.1 绝缘导线加工 20.1.2 屏蔽导线端头的加 工 20.1.3 电缆与插头、插座 的连接
A
4.2 空气净化技 术
B
5.1 温度
5.2 湿度
5.3 元 器件的存 储环境
5.4 光照度
第二部分 整机电子装联环境
5 其他工作环境
5.5 噪声
第三部分 整机电子装联材
03 料
6 印制板
6.1 印制电路 板的定义
6.2 印制电路 板的组成和结构
6.3 特种印制 板
6.3.1 金属基印制 板
6.3.2 微波高频基 板
21 整机装配技术
21.1 整机装配的顺序和基本要求
21.1.1 整机装配的基本顺序 21.1.2 整机装配的基本要求
21.2 整机装配的流水线
21.3 整机装配的工艺流程
21.3.1 整机装配的流程 21.3.2 整机装配中的准备工艺及接线工 艺 21.3.3 整机装配中的机械安装工艺要求 21.3.4 整机装配中的面板、机壳装配 21.3.5 常见的其他装配工艺
6.3.3 数字/微波 混合电路基板
6.3.4 光电印制板
6.4 印制板的 制造技术
6.5 印制板的 发展趋势
7.1 片式电阻、电 容、电感
7.2 小外形封装晶 体管
现代电子装联技术

压接。需要设备。 3、装配:单板—机壳—机箱—系统 4、基板:PCB、铝基板、陶瓷基板、纸
基板。
2020/4/30
5
一、电子装联技术
电子装联技术范围: 电子装联工艺技术 电子装联设备设计制造术 电子元器件设计制造技术; PCB设计制造技术(非PCB板材); 电子装联生产辅料设计制造技术; 静电防护技术; 电子产品企业质量管理。
(CTE)一致性差。 4、初始投资大,生产设备结构复杂,
涉及技术面宽,费用昂贵。
2020/4/30
11
一、电子装联技术
MPT微组装技术
综合 运用微电子焊接技术、表面贴装技术以及封装工艺,将元器 件等高密度地互连于多层板上并将其构成三维立体结构的高密度、 高速度、高可靠性,外形微小化,功能模块式的电子产品的一种 电子装联技术。
该技术的核心是打破了元器件封装与印制板焊装的界限,将半导 体集成电路技术、薄/厚膜混合集成电路技术、表面贴装技术以 及封工艺加以综合运用,在多层板上高密度地实施机械与电子互 连,在板级完成系统的组装。实现电子产品(如组件、部件、系 统)的外形微小化、功能模块化。20世纪律性80年代后期就出现 的多芯片组件/模块(MCM)就是微组装技术实用化中最具有代表 性的产品之一。
2020/4/30
13
一、电子装联技术
第二代与第三代安装技术,代表元器件特征明 显 ,都是以长元器穿过印制板上通孔的安装方 式。 第四代技术 ,使电子产品体积缩小,重量变轻, 功能增强、可靠性提高、推动了信息产业高速 发展。 第五代安装技术,使用一般工具,设备和工艺 是无法完成的,目前还处于技术发展和局部领 域应用的阶段,但它代表了当前电子系统安装 技术发展的方向。
电子装联发展前景分析
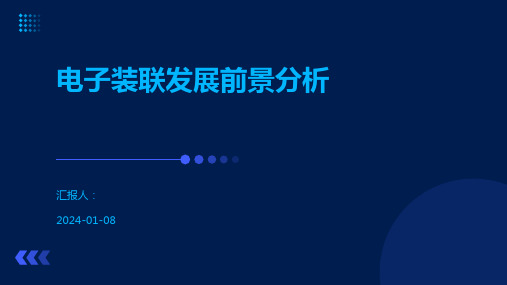
创新激励机制
建立创新奖励机制,鼓励企业、研究机构和个人积极开展电子装联技术创新活 动。
提高产业集中度与规模效应
优化产业结构
通过政策引导和市场机制,推动电子装联产 业集中度和规模效应的提升。
培育龙头企业
重点培育具有核心竞争力的电子装联企业, 发挥其示范引领作用。
提升产业链协同
加强产业链上下游企业间的合作与协同,提 高整体竞争力。
特点
电子装联具有精细化、高密度化、微 型化的特点,对工艺技术和设备要求 较高。
电子装联的重要性
01
02
03
保证产品质量
电子装联的质量直接影响 产品的性能和稳定性,是 保证产品质量的关键环节 。
降低生产成本
高效的电子装联工艺和自 动化设备可以降低生产成 本,提高生产效率。
促进技术创新
电子装联技术的发展推动 了电子产品的小型化、轻 量化、高性能化,促进了 技术创新。
ห้องสมุดไป่ตู้
、高稳定性的组装。
可靠性测试标准不统一
02
不同厂商和地区对于可靠性测试的标准不统一,导致测试结果
可比性差。
环保与安全问题
03
电子装联过程中涉及的化学品和废弃物对环境和人体健康存在
潜在威胁,需要加强环保和安全管理。
03
电子装联市场需求
市场需求现状
消费电子需求持续增长
随着智能手机的普及和更新换代,消费电子市场对电子装联的需 求不断攀升。
全球电子制造转移
随着全球电子制造向中国等发展中国 家转移,电子装联行业将迎来更大的 发展空间。同时,随着一带一路倡议 的深入推进,电子装联行业也将迎来 更多的国际市场机会。
产业政策支持发展
国家政策支持
电子装联简介演示
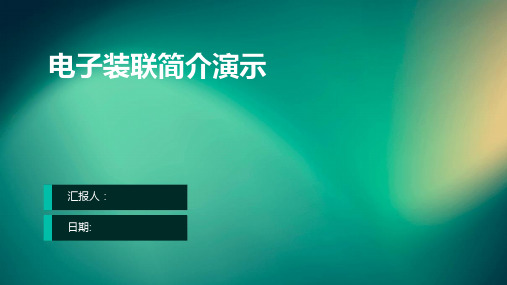
高生产效率挑战与解决方案
高生产效率挑战
为了满足市场需求和提高经济效益,电 子装联需要实现高效、快速的生产。然 而,随着组件的微型化和复杂化,生产 效率受到很大影响。
VS
高生产效率解决方案
采用自动化、机器人技术和智能制造技术 ,实现快速、准确的组装和检测。同时, 优化生产线设计和流程管理,提高生产效 率和质量控制。此外,采用模块化、可重 构的组装平台设计,能够快速适应不同产 品的生产需求。
智能制造与定制化结合
将智能制造与定制化结合,实现生产过程的自动化、柔性化和个性 化,提高生产效率和客户满意度。
THANKS FOR WATCHING
感谢您的观看
聚氨酯胶粘剂
一种多用途的胶粘剂,适用于 各种材料的粘接。
硅胶粘合剂
一种高强度、高耐温的粘接材 料,适用于电子、航空等领域
的粘接。
压接材料
压接端子
用于将电线或电缆压接在连接器 上,具有高导电性和耐久性。
压接工具
用于压接端子的专用工具,可提 供适当的压力和温度。
绕接材料
绕接线
一种用于绕接的特殊导线,具有高导电性和耐高温性。
06 电子装联未来趋势
自动化与机器人技术应用
自动化生产线
采用自动化生产线,提高生产效率,降低人工成本。
机器人技术
应用机器人技术实现自动化装配、焊接、搬运等功能,提高生产 精度和产品质量。
智能化物流
采用智能化物流系统,实现物料高效、准确配送,减少库存和运 成本。
新材料与新工艺的发展
新材料应用
采用高强度、轻质、耐腐蚀等新材料,提高产品性能和可靠性。
医疗监护设备
03
医疗手术设备
04
医疗康复设备
电子产品结构工艺第5章电子产品装联技术课件
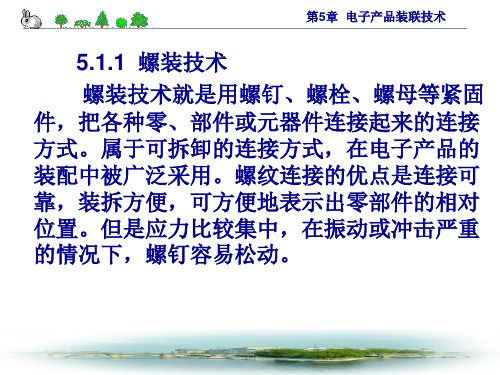
第5章 电子产品装联技术
5.螺栓连接
第5章 电子产品装联技术
6.螺钉连接
第5章 电子产品装联技术
8.紧定螺钉连接
第5章 电子产品装联技术
第5章 电子产品装联技术
5.1.2 铆装技术 铆装就是用铆钉等紧固件,把各种零部 件或元器件连接起来的连接方式。目前,在 小部分零部件及产品中仍然在使用。
第5章 电子产品装联技术
第5章 电子产品装联技术
第5章 电子产品装联技术
图5.3.8 压接的操作过程
第5章 电子产品装联技术
3.绕接
绕接是直接将导线缠绕在接线柱 上,形成电气和机械连接的一种技术。 是利用金属的塑性,将一金属缠绕在另 一金属表面上或互相缠绕形成的连接。
(1)绕接机理 对两个金属表面施加足够的压力, 使之产生塑性变形,让两金属表面原子 层产生强力结合,达到牢固连接的目的。
1.螺钉 (1)螺钉的结构
第5章 电子产品装联技术
第5章 电子产品装联技术
(2)螺钉的选择 用在一般仪器上的连接螺钉,可以选用 镀锌螺钉,用在仪器面板上的连接螺钉,为 增加美观和防止生锈,可以选择镀铬或镀镍 的螺钉。紧固螺钉由于埋在元件内,所以只 需选择经过防锈处理的螺钉即可。对要求导 电性能比较高的连接和紧固,可以选用黄铜 螺钉或镀银螺钉。
第5章 电子产品装联技术
形成良好粘接的三要素是:选择适宜的 粘合剂、处理好粘接表面和选择正确的固化 方法。
第5章 电子产品装联技术
5.2.1 粘合机理
由于物体之间存在分子、原子间作用力,种类不同的 两种材料紧密靠在一起时,可以产生粘合(或称粘附)作 用,这种粘合作用可分为本征粘合和机械粘合两种。本征 粘合表现为粘合剂与被粘工件表面之间分子的吸引力;机 械粘合则表现为粘合剂渗入被粘工件表面孔隙内,粘合剂 固化后被机械地镶嵌在孔隙中,从而实现被粘工件的连接。 作为对粘合作用的理解,也可以认为机械粘合是扩大了本 征粘合接触面的粘合作用,这种作用类似于锡焊的作用, 具有浸润、扩散、结合三个过程。
- 1、下载文档前请自行甄别文档内容的完整性,平台不提供额外的编辑、内容补充、找答案等附加服务。
- 2、"仅部分预览"的文档,不可在线预览部分如存在完整性等问题,可反馈申请退款(可完整预览的文档不适用该条件!)。
- 3、如文档侵犯您的权益,请联系客服反馈,我们会尽快为您处理(人工客服工作时间:9:00-18:30)。
当前,我们正经历着一场新的技术革命,它包含了新材料、新能源、生物工程、 海洋工程 、航空航天和电子信息技术等领域,但其中影响最大 、渗透性强、最具 代表性的乃是电子信息技术 。
电子装联技术是电子信息技术 和电子行业的支撑技术,是衡量一个国家综合实力 和科技发展水平的重要标志之一,是电子产品实现小型化、轻量化、多功能化、智能 化和高可靠性的关键技术。
1.2 THT技术—成型
电容的成型
电阻的成型
1.2 THT技术—成型
1.2 THT技术—成型
元器件引线的弯曲成型要求
⑴ 引线弯曲的最小半径不得小于引线直径的2倍,不能“打死弯”; ⑵ 引线弯曲处距离元器件本体至少在2mm以上,绝对不能从引线 的根部开始弯折。
1.2 THT技术—成型
滚轮式电阻整形差别还体现在:基板、元器件、组件形态、焊点形态和组装工艺方法各个 方面
1.5 MPT技术简介
MPT微组装技术 :Microelectronic Packaging Technology MPT
综合运用微电子焊接接技术、表面贴装技术以及封装工艺,将大规模/或 超大规模集成电路裸芯片、薄/厚膜混合集成电路、表面贴装元器件等高密 度地互连于多层板上并将其构成三维立体结构的高密度、高速度、高可靠性, 外形微小化,功能模块式的电子产品的一种电子装联技术。
●电子产品企业质量管理。
1.1 电子装联技术
电子装联方式:
●插装(THT) 通孔插装技术 Through Hole Technology
●表面贴装(SMT) 表面贴装技术 Surface Mount Technology
●微组装(MPT) 微组装技术 Microelectronic Packaging Technology
1.3 表面组装技术——SMT
SMT工艺技术的发展趋势: A. 与新型表面组装元器件的组装相适应; B. 与新型组装材料的发展相适应; C. 与现代电子产品的品种多、更新快特性相适应; D. 与新型组装形式的组装要求相适应;
1.4 SMT与THT的比较
从组装工艺技术的角度分析,是“贴”和“插”
SMT和THT的根本区别
各焊点符合标准规定的物理特性和电特性的要求。
电连接:常见的有焊接、插接、绕接、铆接、压接 基板:PCB、铝基板、陶瓷基板、纸基板。 PCB 即 Printed Circuit Board 的缩写,中文名称为印制电路板,又称印刷电 路板、印刷线路板
1.1 电子装联技术
1.1 电子装联技术
研究范围
●电子装联设备设计制造术 ●电子元器件设计制造技术; ●PCB设计制造技术(非PCB板材); ●电子装联生产辅料设计制造技术; ●静电防护技术;
1.5 MPT技术简介
微组装技术始于二十世纪八十年代中期,被人们称之为第五代电子装联技术。 该技术的核心是打破了元器件封装与印制板焊装的界限,将半导体集成电技 术、薄/厚膜混合集成电路技术、表面贴装技术以及封工艺加以综合运用, 在多层板上高密度地实施机械与电子互连,在板级完成系统的组装。实现电 子产品(如组件、部件、系统)的外形微小化、功能模块化。20世纪律性 80年代后期就出现的多芯片组件/模块(MCM)就是微组装技术实用化中最 具有代表性的产品之一。
自动带式电容裁断机
1.2 THT技术—插件
插件:
利用手工和机械将电子元器件插入基板的孔内。
分为手动、半自动、全自动三种方式
当孔径比引线(脚)宽(大)0.05 - 0.2mm,焊盘直径为孔 径的2 - 2.5倍时,是焊接比较理想的条件。
1.2 THT技术—插件
元件的插装
1.2 THT技术—波峰焊
有源元件 (陶瓷封装)
SMD泛指有源表 面安装元件
1.3 表面组装技术——SMT
SMT技术的主要特点: A. B. C. D. 组装密度高,电子产品体积小、重量轻; 自动化生产程度高,生产效率高,组装成本低; 高频特性好; 可靠性高;
1.3 表面组装技术——SMT
● SMT是从70年代发展起来,到90年代广泛应用的电 子装联技术。由于其涉及多学科领域,使其在发展初其较为 缓慢,随着各学科领域的协调发展,SMT在90年代得到讯 速发展和普及,21世纪SMT已成为电子装联技术的主流。 ● 1963年第一只贴装元件诞生。 ● 2010年是中国引进SMT设备25年。 ● 现在中国已能生产所有SMT设备
1.1 电子装联技术
电子装联技术( Electronic Assembly ):电子或电气产品在形成 过程中产生的电连接和装配的工艺过程。
● 将电子元器件焊接、装配在基板(PCB、铝基板、陶瓷基板等上
的过程。
1.1 电子装联技术
电子装联的过程就是把电子元器件:无源器件,有源器件,接插件等按着设计的要 求——装焊图或电原理图,准确无误的装焊到基板上的指定焊盘上,并且保证
1.2 THT技术
一种需要对焊盘进行钻插装孔,再将电子元器件 的引线(或引脚)(即通孔插装元器件)插入印
制板的焊盘孔内并加以焊接,与导电图形进行电
连接的电子装联技术 。 特点:元器件脚穿过PCB;元器件与焊接点不共面。
1.2 THT技术
●
插装(THT)的发展:
手工 焊—— 浸焊 —— 波峰焊
1904年第一只电子管诞生;1947年第一只晶体管诞生。电子元 器件的发展推进着电子装联的发展。
SMC泛指无源表面 安装元件总称
单片陶瓷电容
钽电容 厚膜电阻器
薄膜电阻器
轴式电阻器 CLCC (ceramic leaded chip carrier) 陶瓷密封带引线芯片载体 SOP(small outline package)小尺寸封装 QFP(quad flat package) 四面引线扁平封装 BGA( ball grid array) 球栅阵列
●插装(THT)工艺流程:
元件成型
插
件
波峰焊
检 修
1.2 THT技术—成型
元件引脚成型是指根据元器件在印制板上的安装形式,对元 器件的引线进行整形,使之符合在印制板上的安装孔位。
●成型内容:电阻的剪脚,打弯,IC的成型,元件的倒装成型(例:为散热 将元件倒装)等。
●元件引脚成形有利于提高装配质量和生产效率,使安装到印制板上的元器 件美观
1956年英国Fry‘s Metal公司发明了印制电路板波峰焊法,意味 着PCB焊接领域的一个新时代的开始,它使PCB由人工烙铁逐点 焊接进入到机器自动化大面积高效率焊接的新时代。 全自动焊接机最早出现在日本,七十年代作为黑白/彩色电视机 的主要生产设备。八十年代起引进国内。
1.2 THT技术
90℃~130℃ 1min~3min 250℃±5℃ 3至5秒(有铅 焊料)
波峰焊示意图
1.2 THT技术—波峰焊
插装好的PCB板装架
助焊区
焊接区
传输区
1.3 表面组装技术——SMT
表面组装技术: 一种无需对焊盘进行钻插装孔,直接将表面组装元件 /器件(SMC /SMD)贴、焊到印制板表面规定位置上的装联技术, 简称SMT(Surface Mount Technology)
波峰焊是将熔融的液态焊料﹐借助泵的作用﹐在焊料 槽液面形成特定形状的焊料波﹐插装(贴装)了元器 件的PCB置于传送链上﹐经过某一特定的角度以及一 定的浸入深度直线穿过焊料波峰而实现焊点焊接的过 程。
1.2 THT技术—波峰焊
链条倾角3至7度
压锡深度为PCB厚度的 1/3~1/2
助 焊 剂 涂 覆
焊接
特点:元件脚不穿过PCB,元件与焊点共面。
1.3 表面组装技术——SMT
SMT的主要工艺流程:
SMT工艺流程图
1.3 表面组装技术——SMT
SMT主要流程示意图:
焊膏印刷 贴片与焊接
Squeege e
Solder paste
焊膏 贴片元件
Stenci l
PCB 板
1.3 表面组装技术—SMT
表面贴装元件的种类 无源元件
1.3 表面组装技术——SMT
SMT是电子装联技术的发展趋势
其表现在: 1.电子产品追求小型化,使得以前使用的穿孔插件元件已无法适应其要 求。 2.电子产品功能更完整,所采用的集成电路(IC)因功能强大使引脚众多, 已无法做成传统的穿孔元件,特别是大规模、高集成IC,不得不采用表面 贴片元件的封装。 3.产品批量化,生产自动化,厂方要以低成本高产量,出产优质产品以 迎合顾客需求及加强市场竞争力。 4.电子元件的发展,集成电路(IC)的开发,半导体材料的多元应用。 5.电子产品的高性能及更高装联精度要求。 6.电子科技革命势在必行,追逐国际潮流。