生物制品车间西林瓶无菌灌装验证方案知识讲解
培养基无菌灌装工艺验证方案
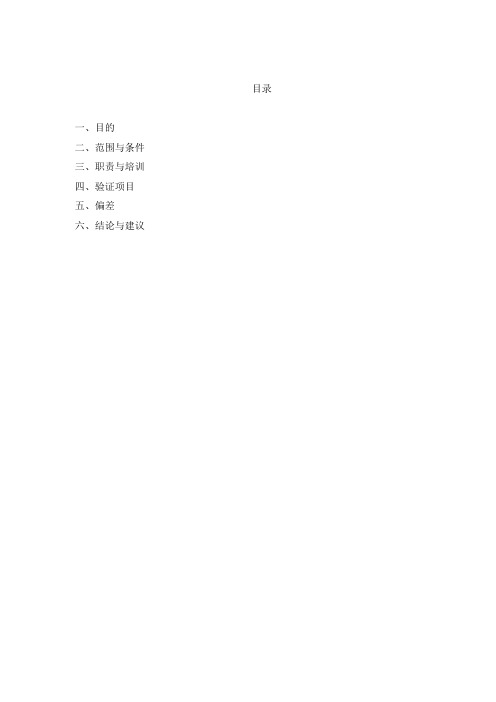
目录一、目的二、范围与条件三、职责与培训四、验证项目五、偏差六、结论与建议一、目的:1.1验证目的:通过培养基无菌生产工艺验证,证实无菌生产工艺过程的可靠性。
二、验证范围和条件:2.1验证范围:本验证方案适用于冻干粉针生产线(激素)培养基无菌灌装。
2.2验证条件:培养基无菌灌装工艺验证是用与正常的实际生产工艺相同的条件和操作方法,在其他各个系统(诸如公用系统、无菌环境保持系统、设备验证等)验证工作完成的基础上进行的。
本方案必须在动力部门相关验证和冻干车间相关验证完成的条件下进行。
2.3 按照《培养基灌装SOP》,在各个系统验证完成后,开始进行培养基灌装工艺验证。
工艺流程图:2.4执行的标准操作规程:严格按照冻干车间工艺SOP、设备SOP、卫生SOP、物料SOP、基础SOP执行操作。
三、职责和培训:3.1 验证小组成员和职责:3.2 培训内容:3.2.1 培训目的:为建立并保持良好的质量保证系统,应配备足够数量并具有适当资质的人员完成各项操作,所有人员应明确理解自己的职责,熟悉与之相关的GMP原则,并接受良好的培训。
3.2.2人员培训:所有负责该验证操作的操作人员。
四、验证项目:4.1批的选择:冻干生产线的产品规格为,用7ml的西林瓶灌装2ml的培养基。
灌装大豆胰蛋白胨液体培养基(TSB)3批,批号为201406211、201406231、201406251,灌装装量为2ml。
为确保冻干机A、B每台不少于40000支,灌装数量为8万支需16.8万ml大豆胰蛋白胨液体培养基,灌装完毕后,先置23-28℃培养7天,再置30-35℃培养7天,每天观察培养基的微生物生长情况。
培养基灌装与培养基促生长试验同步进行。
4.2 抑菌作用的避免:培养基灌装使用促进微生物生长的培养基来挑战评估污染风险,因此抑菌因素应当在培养基灌装中予以考虑。
将培养基灌装的注射用水冷却至室温20-25℃配制,并在室温下保存培养基液体。
无菌灌装(培养基灌装)验证方案word资料9页
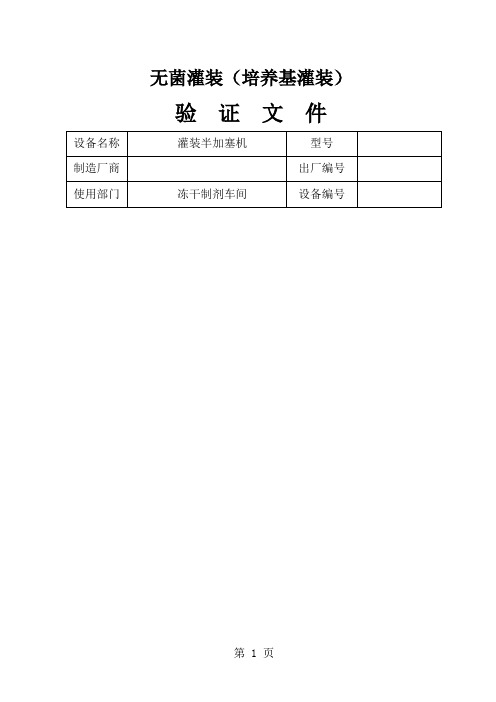
无菌灌装(培养基灌装)验证文件目录验证方案一、验证目的二、设备概述三、验证小组组成四、验证程序五、验证进度六、验证内容与方法验证报告一、验证实施二、验证结果三、结果分析四、评价五、验证后期工作六、建议验证记录一、培养基灌装验证记录附:1.灭菌后西林瓶、胶塞无菌检测记录2.百级区表面微生物及操作人员手和衣物微生物动态监测记录无菌灌装(培养基灌装)验证方案无菌灌装(培养基灌装)验证方案一、验证目的:通过培养基无菌灌装试验时已灌装培养基的西林瓶染菌率能否达到规定的合格标准,来确认冻干车间的洁净环境以及进行无菌灌装过程中所采用的各种防止微生物污染的方法和规程的可行性,从而为保证所生产产品的无菌性提供依据。
二、概述:无菌灌装是指由掌握了无菌操作的人员在一个有控制的环境中将经灭菌的无菌药液灌封于灭菌后的容器中,制成无菌药物的过程。
无菌灌装验证,是在与无菌灌装生产过程有关的其他验证,如:洁净厂房、公用系统、灭菌设备(包括蒸汽灭菌柜、隧道式灭菌干燥器、热循环烘箱等)验证合格后,且操作人员熟练掌握了岗位SOP后进行的。
培养基灌装作为无菌灌装的模拟实验,可以直观、方便、准确地反映出无菌灌装过程的污染情况及问题。
三、验证小组的成员:本设备的验证按文件SMP—YZ—0001—01规定组成验证小组,其成员及职责为:组长:全面负责本验证工作。
生产部:负责培养基的灌装操作。
质管部:负责样品的检测工作。
负责验证全过程的监控。
四、验证程序:本验证按文件SMP—XX—XXXX—XX规定的程序进行验证。
五、验证进度:年月日至年月日完成。
六、验证内容与方法:1.验证前须确认项目: 确认人员培训合格,公用系统、工艺用水系统和空调系统、车间设备处于正常运行状态,并提供相关的合格报告。
2.验证方法及过程监测项目:2.1 培养基的准备:培养基名称:胰蛋酶胨大豆肉汤培养基。
在临试验前,按规定配置好所需的液体培养基,并于121℃、20分钟进行灭菌。
无菌培养基灌装验证方案

验证方案1、目的:对生产部制剂车间的灌装机进行培养基无菌灌装试验,通过灌装后的产品污染程度检测灌装工艺能否保证产品的无菌。
2、范围:生产部制剂车间的灌装生产线。
3、责任:3.1验证小组3.1.1设计、组织和协调验证试验。
3.1.2准备、检查和批准验证方案。
3.1.3准备验证报告并且流转批准。
3.1.4评估所有的测试结果。
3.1.5完成此文件规定的验证报告。
3.1.6验证小组成员名单3.2生产部3.2.1对灌装车间进行清扫、消毒,保证环境清洁。
3.2.2操作灌装机。
3.2.3按照规定的程序进行培养基灌装。
3.2.4进行日常清洗、维护。
3.3QA3.3.1取样。
3.3.2进行目检。
3.3.3进行环境监测。
3.3.4检查和批准验证方案和报告。
4、描述制剂车间使用x公司的灌装流水线,包括:洗瓶机、隧道烘箱、灌装机、轧盖机,y公司的冻干机进行冻干。
5、程序5.1使用的设备及材料5.1.1洗瓶机5.1.2隧道烘箱5.1.3灌装机5.1.4冻干机5.1.5灌装材料5.1.5.1瓶子5.1.5.2胶塞5.1.5.3铝盖5.1.6培养基5.1.7菌种5.1.7.1枯草杆菌(Bacillus Subtilis) ATCC 6633 5.1.7.2白色念珠菌(Candida alblcans) ATCC 10231 5.1.7.3厂房环境分离菌5.2培养基准备5.2.1在10L血清瓶中加入2L的热注射用水,再加入240g胰蛋白胨大豆肉汤充分搅拌,等溶解后再加入6L的热注射用水,整个培养基量为8L。
5.2.2将配制好的培养基放到高压蒸汽灭菌柜中121℃灭菌30分钟,灭菌后取出血清瓶,从瓶中取4瓶(50ml/瓶)作为阴性对照,其中2瓶于32±2℃培养14天,另外2瓶于23±2℃培养14天。
观察有无微生物污染。
5.3培养基无菌灌装5.3.1准备无菌的灌装器具(针、硅管、等等),联接到灌装机上。
硅管一头放入灭菌培养基中。
无菌灌装验证方案

无菌灌装模拟试验方案验证分类:工艺验证验证部门:冻干粉针剂车间甘肃大得利制药有限公司1.概述:为证明在确定的环境、工艺和操作下,生产过程能有效地防止微生物污染,使产品达到无菌要求,需进行培养基模拟灌装试验,来验证所提供产品的无菌可靠性达到可接受的标准。
这是GMP对非最终灭菌无菌冻干粉注射剂生产的基本要求,是无菌制剂工艺验证的重要组成部分。
但是此试验不能对常规生产造成不良影响。
无菌灌装模拟试验是指由掌握了无菌操作的人员在一个有控制的环境中,利用适宜的设备系统,将经灭菌(或经除菌过滤)的无菌培养基灌装于事先灭菌的容器中,制成无菌药物的过程。
该验证是在与无菌灌装生产过程有关的其他验证如:洁净厂房、公用系统(工业用水系统等)、设备(包括蒸汽灭菌柜、隧道式干燥灭菌器等)等验证合格后,且操作人员熟练掌握了岗位SOP后进行的。
采用培养基代替药品进行无菌灌装对无菌工艺进行验证,即用经过湿热灭菌(除菌过滤)的液体胰酪胨大豆肉汤培养基代替产品药液,进行无菌灌装、半加塞操作,灌装后的样品送入冻干箱内放置产品冻干程序所需时间,再进行压塞、轧盖,然后进行培养观察,以确认无菌灌装工艺的可靠性,以上整个操作过程应模拟正常的产品生产时的最差状态。
培养基灌装作为无菌灌装的模拟实验,可以直观、方便、准确地反映出无菌灌装过程的污染情况及问题。
2.目的:通过培养基无菌灌装模拟试验,来确认在冻干粉针剂灌装过程中所采用的各种方法和各种规程,防止微生物污染的水平达到可接受的合格标准的能力,或提供保证所生产产品的无菌性的可信限度达到可接受的合格标准的证据,为今后对粉针车间进行冻干粉针剂灌装作业管理确定依据,即通过对经过培养的灌装样品进行检查并对结果进行分析解读可以综合评估无菌工艺的可靠性,借以确定实际生产中产品被污染的概率,确保无菌产品的无菌性。
3.范围:此验证方案适用于粉针车间,非最终灭菌的无菌生产工艺模拟试验。
4.依据:药品生产质量管理规范》2010修订版附录1:无菌药品生产;《中国药典》2010年版二部附录无菌检查;GMP指南5.责任:质量部、生产部、质检科、粉针车间、设备部等部门负责本试验的执行、分析及报告。
灌装量IPC检测方法验证

文件编号VP.10.00.501.02PV设备编号S-A-J-2007-156灌装量IPC检测方法验证(KGS10A直线式灌装加塞机)前验证□再验证□回顾性验证□同步验证适用系统:公用系统文件编号:VP.10.00.501.02PV起草人:部门:Rabies Project 日期审核人:部门:灌封冻干车间日期部门:工程设备部日期部门:QC 日期部门:QA 日期批准:部门:QA经理日期文件编号VP.10.00.501.02PV设备编号S-A-J-2007-1561 目录1. 目录 (2)2. 简介 (3)3. 背景 (3)4. 验证范围 (3)5. 适用文件 (3)6. 验证人员及职责 (4)7. 验证项目及合格标准 (4)7.1 校验检查 (4)7.2 验证设备及物料准备 (4)7.3 环境监测 (4)7.4 模拟灌装试验 (4)8. 偏差列表 (7)9. 变更控制 (7)10. 附件列表 (8)11. 附件 (9)12. 验证报告及综合评价 (15)13. 无菌实施灌装计划 (16)文件编号VP.10.00.501.02PV设备编号S-A-J-2007-1562 简介本方案中提及了所需实施验证项目的要求及合格标准,所有验证数据都将被记录。
验证实施过程中,若所有验证结果在合格标准内或出现微小的缺陷、偏差或变更,均可被接受,相应的缺陷、偏差或变更应给予解释并可追溯。
验证实施过程中出现的所有偏差及变更都应由验证领导小组负责人确认。
3 背景KGS10A直线式灌装加塞机,设备编号为--------,安装于B级灌封冻干车间?的A级层流下,用于生物制品的灌装。
该灌装机具备装量IPC检测功能,其检测方法及流程为:称量灌装后瓶重W1倒空西林瓶WFI清洗3遍压缩空气吹干称量空瓶重W2计算装量W = W1 - W24 验证范围对KGS10A直线式灌装加塞机的灌装量IPC检测方法进行验证,本方案适用于公司西林瓶制品灌装工序的无菌灌装验证。
无菌灌装风险分析及对应的设备设计和验证
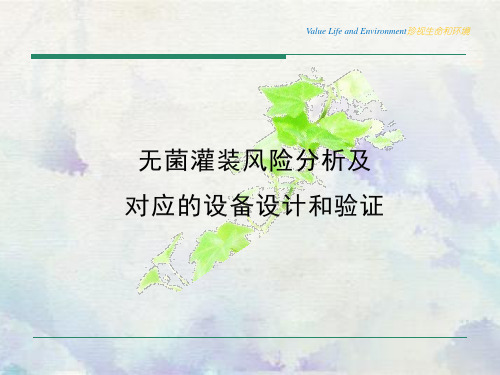
Value Life and Environment珍视生命和环境
有必要先设定在无菌区域进行操作的操作者是污染源,且是最大的污 染源。若从此方面来看各操作步骤,这是长期产品暴露接触污染调查 实践得出的普遍共识。
人员污染风险的规模一个已经更衣后的操作人员将释放: 10,000 CFU / 小时或更多, 数据来自于“受控的第一次使用的衣物以及规定的动作”
设备设计 (隧道烘箱)
Value Life and Environment珍视生命和环境
隧道烘箱:交付无菌、无热原的玻璃瓶
与操作相关的风险
风险消减设计特点
验证
• 没有达到除热原目标
• 均匀的温度穿透和分布
• 加热区域的除热原,热穿
• 传送带变频控制
透测试,降低3个对数单
• 各区域以及与周围环境的压
• 层板温度分布
盘管上的均匀结冰
• 层板的平整
• 板层温度均匀性测定.
• 层板的准确温度控制
• 加热速率
• 精确的真空/压力系统和控制 • 冷却速率
• 带边的层板
• 真空速率
• 密封系统的压力开关
• CIP / SIP
• 自动装载和出料系统
• 处方开发和确认
• 无线温度监测
• 工艺循环的自动控制
• 装料期间倒瓶和污染 • 出料期间倒瓶和污染
二是虽然在“OPEN”状态下,尽量减少人员的干预;
其三,是不得已需要干预,至少要规范和优化干预方式。
无菌灌装的风险
Value Life and Environment珍视生命和环境
干预至少是通过手套箱,屏蔽了操作员和A级环境的直 接接触实现的
隔离器不能排除干预;但优化了干预方式,将操作者对A级区域 的直接干预变成了间接干预,风险降低很多;
无菌药品包装容器的密封性验证方案

无菌药品包装容器的密封性验证方案1.概述:无菌药品的容器应能在整个有效期内有完好的密封性,防止微生物的浸入。
药品包材的设计及选择要考察相互的配合情况。
无菌容器/密封件系统的完整性测试可以在培养基灌装时进行。
2.目的:评估产品包装的密封性,以充分保护产品在储存期的无菌状态。
3.依据:《药品生产质量管理规范》2010修订版:附录1:第九十五条无菌药品包装容器的密封性应经过验证,以避免产品遭受污染。
4.责任:质量部、生产部对本验证负责。
5.微生物浸入试验法验证密封完整性:往产品容器内灌入培养基并按照常规方式压塞封盖,灭菌后冷却备用。
将冷却后的容器倒置并将瓶口完全浸没于高浓度(108CFU/ml)的运动性菌液中,4小时后,将容器外表面消毒并培养,看是否有挑战性细菌在容器内生长。
多准备一些灌装培养基的样品,在与产品相同地的贮存条件下贮存。
在贮存的一定时间间隔(12,24,36和48个月等),取出部分样品,进行微生物浸入试验,以确定密封系统在贮存期内的有效性。
6.范围:西林瓶、胶塞及铝盖的密封性验证,共有10ml及2ml两种规格。
7.用品:胆盐乳糖培养基铜绿假单胞菌(ATCC 9027)乙酸异丙醇8.实施:8.1制备样品:取已经按相应清洗灭菌操作规程制备好的西林瓶、胶塞及铝塑组合盖150套,西林瓶内灌装入已灭菌的胆盐乳糖培养基,在正常生产线上抽真空、压塞、轧盖。
将每一试样品倒转,使培养基与西林瓶内表面及胶塞充分接触,在30~35℃竖立倒置培养14天,培养基应澄清,无菌落生长。
8.2制备微生物菌悬液:从铜绿假单胞菌(ATCC 9027)的新鲜斜面上取培养物,分别接入含6ml无菌胆盐乳糖培养基的试管中,在30~35℃下培养18~24h;将每管的培养物分别转入含600ml相同培养基的容器内,于30~35℃下培养(约24小时),在培养结束时,能明显见容器内培养基出现浑浊,计数,当菌落数大于108CFU/ml时,停止培养,待用(在微生物侵入试验开始,所用菌悬液浓度(活菌数)必须达到1×108CFU/ml。
无菌模拟灌装工艺验证[指南]
![无菌模拟灌装工艺验证[指南]](https://img.taocdn.com/s3/m/f74cc6ae6c85ec3a86c2c524.png)
无菌工艺模拟验证-培养基灌装试验王新峰QA/QC 厂房设施人员灭菌工艺无菌保证培养基灌装HVAC,水操作规程日常监控EM&PM内容1.培养基灌装的目的2.法规要求3.不同制剂工艺的培养基灌装(液体、冻干产品,干粉分装产品)4.风险分析5.实验设计6.审计要点培养基灌装试验的定义定义:培养基灌装-采用培养基代替产品,按照正常生产的程序来进行无菌灌装工艺验证。
培养基灌装试验目的目的:–评估在既定无菌生产环境和过程控制条件下生产无菌产品的能力–证明指定的无菌工艺设计和变更是否可行–证明无菌工艺过程中的相关操作是否可行–评估无菌工艺人员的操作水平(资格确认组成部分)– QAR调查的手段–证明符合cCMP的要求–发现无菌工艺过程中潜在的微生物污染因素培养基灌装试验应用范围•无菌药品和生物制剂的生产•用无菌工艺进行医疗器械,人和动物保健品的生产法规要求2010GMP•第四十七条无菌生产工艺的验证应当包括培养基模拟灌装试验。
•应当根据产品的剂型、培养基的选择性、澄清度、浓度和灭菌的适用性选择培养基。
应当尽可能模拟常规的无菌生产工艺,包括所有对无菌结果有影响的关键操作,及生产中可能出现的各种干预和最差条件。
•培养基模拟灌装试验的首次验证,每班次应当连续进行3次合格试验。
空气净化系统、设备、生产工艺及人员重大变更后,应当重复进行培养基模拟灌装试验。
培养基模拟灌装试验通常应当按照生产工艺每班次半年进行1次,每次至少一批。
•培养基灌装容器的数量应当足以保证评价的有效性。
批量较小的产品,培养基灌装的数量应当至少等于产品的批量。
培养基模拟灌装试验的目标是零污染,应当遵循以下要求:•(一)灌装数量少于5000支时,不得检出污染品。
•(二)灌装数量在5000至10000支时:•1.有1支污染,需调查,可考虑重复试验;•2.有2支污染,需调查后,进行再验证。
•(三)灌装数量超过10000支时:•1.有1支污染,需调查;•2.有2支污染,需调查后,进行再验证。
粉针车间无菌分装工艺验证
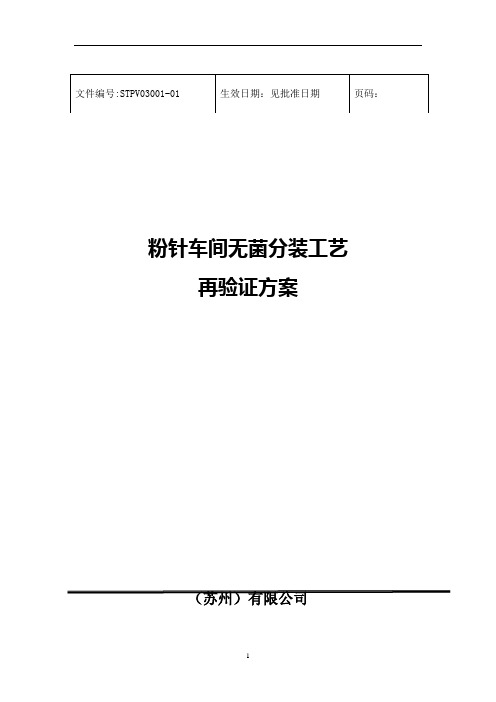
4.4.3乳糖抑菌性试验
4.4.3.1方法:
将经过Co60辐射灭菌的乳糖粉末按无菌操作进行取样。
用经湿热灭菌的肉汤培养基将上述乳糖样品分别稀释成5%和10%的样品溶液。
分别吸取不同浓度样品溶液各10ml,分别分装于4支无菌试管中,其中两支接种金黄色葡萄球菌菌液(10~100CFU/ml)1ml,两支接种白色念珠菌菌液(10~100CFU/ml)1ml。
附表二:培养基灵敏度检查记录………………………………………………11
附表三:无菌检查验证记录……………………………………………………12
附表四:培养室温度记录……………………………………………………13
1目的
通过培养基模拟灌装试验确认粉针车间在现有设备和环境下,按现有标准操作规程操作,执行现行分装工艺规程能生产出合格的无菌分装产品来。
用空白肉汤培养基接种相同的金黄色葡萄球菌和白念珠菌作为阳性对照。
于30℃~35℃(或23℃~28℃)下培养7天,应每天观察微生物生长情况。
4.4.3.2结果判断:全部样品、对照品均应有明显的微生物生长。
4.4.4乳糖无菌性试验
4.4.4.1方法:
将经过Co60辐射灭菌的乳糖粉末按无菌操作进行取样。
按中国药典2005年版附录“无菌检查法”对乳糖样品进行无菌检查。
记录人
胶塞的清洗、灭菌;
无菌工作服的清洗灭菌;
液体灌装机配套的针头、硅胶管等的清洗灭菌;
4.3.2.4最多数量的操作者在无菌室内参与操作。
4.3.2.5分装时间按正常班次进行,从8:30~11:30,12:30~17:00期间分装,分装过程中可停顿,保证分装持续时间应有6小时。
4.3.2.5模拟产品批号的编制:由于生产线数量多,样品批量大,所以对每条线每次验证的产品编制批号,便于区分与管理。
冻干粉针剂培养基无菌灌装模拟试验再验证方案

冻干粉针剂培养基无菌灌装模拟试验再验证方案xxxxxx制药股份有限公司1.概述培养基灌装试验是用正常的实际生产工艺相同的条件和操作方法,向冻干制品容器(西林瓶)内灌装经除菌过滤器过滤的培养基,然后将此模拟产品在适当的条件下培养,以确认无菌工艺过程的可靠性。
2008年11月冻干粉针剂百级区域进行了厂房改造,更换了高效风口。
根据xxxx《验证总则》和GMP的要求,当厂房、环境发生改变时,需要进行再验证。
在厂房和净化空调系统验证合格后,连续灌装三批培养基已证实无菌工艺的可靠性。
2.验证目的通过培养基模拟灌装试验,证实无菌工艺过程的可靠性。
3.验证计划及合格标准验证计划:按照xxxxx《培养基灌装模拟试验标准操作程序》,在厂房验证、净化空调系统验证完成后,使用正常生产的工艺条件,每批培养基配液量80L,采用10ml的西林瓶,每瓶灌装4ml,每批灌装4750~5000瓶,连续生产3批。
灌装过程半压塞,灌装结束将半压塞的西林瓶至冻干箱内,模拟冻干过程结束后全压塞,轧盖。
将培养基上下颠倒几次使培养基与胶塞基整个容器内壁充分接触,然后倒置,先置30~35℃培养7天,再置23~28℃培养7天。
于每一培养阶段的0、3、7、14天观察培养基的微生物生长情况,并分析污染的平中微生物的特点。
合格标准:每批培养基中污染品均不得多于1个,且三批的检验结果具有重现性。
4.人员、职责5.验证过程5.1验证条件确认5.1.1 厂房和空调系统确认由于原灌装间内厂房和空调系统都进行了变更,培养基灌装前应首先确认已完成厂房和净化空调系统的变更验证;5.1.2设备和系统确认模拟试验开始前还应对与本次试验密切相关的设备和系统进行确认,查阅半年的下列各系统验证档案、运行记录或监测记录确认以下内容;执行人:QA:日期:5.1.3人员和物料确认5.1.3.1查阅无菌操作室人员的健康档案和培训资料确认一下人员的2008年体检和培训情况;执行人:教育办公室:日期:5.1.3.2查阅培养基生产用物料的进货记录和检验报告,确保物料已经检验合格并在储存期内;执行人:QA: 日期:5.1.4文件确认培养基灌装试验前确认与培养基灌装有关的关键文件、记录已齐全。
无菌灌装过程验证剖析
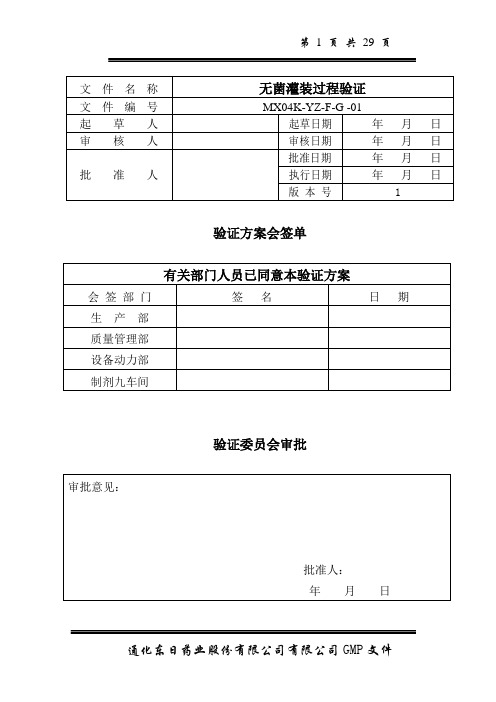
验证方案会签单验证委员会审批目录1 引言1.1 验证项目小组成员及责任1.2 验证工作中部门责任2 概述3 验证的目的4 依据4.1 生产相关文件4.2 主要设备5 验证项目6 污染率计算7 验证周期8 附件1 引言1.1 验证项目小组成员及责任1.1.2 责任验证项目小组组长:组织进行验证方案的设计、起草;验证过程的组织、协调、保证验证按预期的计划完成,提出验证报告。
验证项目小组成员:分别负责落实方案实施中各部分验证的具体工作。
1.2 验证工作中部门责任:验证小组:组织编写验证方案,领导协调验证项目的实施,协调验证委员会及专家组的工作,对验证过程的技术、质量负责,参加验证方案的会签、终审和批准,参加验证报告的批准。
生产部:负责组织协调并保证每批产品的生产全过程,严格按照本方案实施。
质量管理部:负责验证计划的组织落实、验证过程监控、结果评价及设备、设施的微生物限度、培养基取样及药液准备、成品取样;负责验证过程的检验、测试及结果报告。
设备动力部:负责在公用系统、生产设备、设备维修及校正等各项工作中提供及时可靠的支持和服务。
物料管理部:负责为验证过程提供物资支持。
制剂九车间:负责全面协调各项验证试验,并负责报告试验结果。
2 概述厂房、设施、设备均已经过全面验证。
在生产线投入生产前,用胰酶酪胨大豆肉汤培养基无菌溶液代替无菌药液模拟生产并于冻干箱内模拟冻干,然后进行微生物培养,污染率<0.1%为合格。
3 验证目的无菌灌装过程验证目的是通过无菌培养基溶液模拟灌装、冻干的试验的方法,证明无菌灌装过程的可靠性。
4依据5 验证项目5.1 胰酶胳胨大豆肉汤培养基无菌干粉的性能试验5.1.1 胰酶胳胨大豆肉汤培养基无菌干粉的溶解性试验:取胰酶胳胨大豆肉汤无菌干粉0.3g加入15ml试管中,注入10ml无菌注射用水(室温),盖好胶塞,振摇,应能完全溶解。
5.1.2 胰酶胳胨大豆肉汤无菌干粉微生物生长性能试验:胰酶胳胨大豆肉汤无菌干粉按处方溶解后,灌装于大试管中,经115℃热压灭菌30分钟(严格按无菌操作也可不灭菌)。
生物制品车间西林瓶无菌灌装验证方案知识讲解
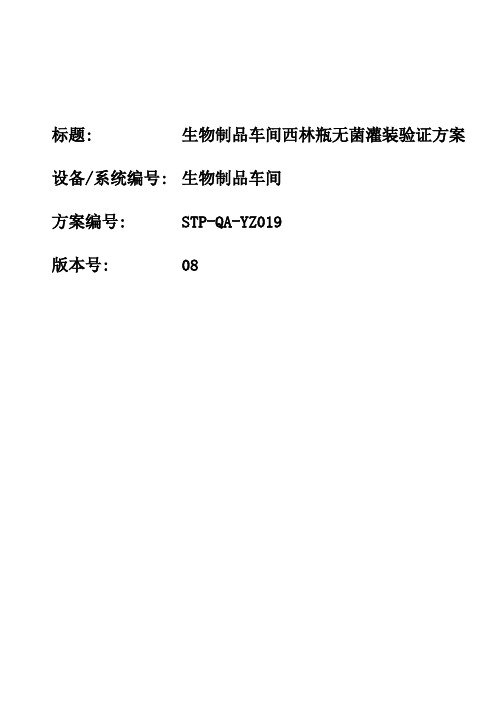
标题: 生物制品车间西林瓶无菌灌装验证方案设备/系统编号: 生物制品车间方案编号: STP-QA-YZ019版本号: 08方案执行前批准注:签名表示已对方案的准确性、完整性和GMP的符合性进行了审核并符合相关要求,同时承诺及时安排相应的人力物力资源执行该方案。
同意批准方案用于执行。
目录方法执行前批准 (2)1 目的 (4)2 范围 (4)3 编订依据 (4)4. 部门职责 (4)5. 验证内容 (5)5.1 概述 (5)5.1.1生产所用主要设备 (5)5.1.2生产工艺和品种情况 (5)5.1.3参加无菌灌装验证人员情况 (6)5.2验证方法 (6)5.3 再验证周期 (8)6. 附录 (9)1 目的此验证方案的设计有助于证明采用此无菌灌装工艺生产出的产品符合成品质量标准,尤其是无菌性的控制标准。
无菌分装过程的验证是在人员进行相关培训及水系统、空调系统、消毒系统及清洗等验证合格基础上进行的。
本次结合灌装生产技术指标和技术要求,确定无菌灌装工艺的再验证内容。
通过培养基无菌灌装试验考察无菌灌装过程中环境是否达到要求,人员操作是否规范,灌装工艺是否合理,为灌装产品的无菌保证提供依据。
2006年10月西林瓶生产线完成改造后进行了首次验证,2007年生物制品车间空调系统改造后进行了西林瓶生产线无菌灌装的再验证,2008、2009年在设备连续正常运行一年后分别进行了再验证,此次验证为2011年冻干粉针投产前的再验证。
2 范围适用于生物制品车间西林瓶无菌灌装工艺的再验证。
3 依据3.1 《药品生产质量管理规范》(2010年修订)。
3.2 《药品生产验证指南》(2003年)。
4 责任人4.1 验证委员会4.1.1 负责验证方案的审批。
4.1.2 负责验证的协调工作,以保证本验证方案规定项目的顺利实施。
4.1.3负责验证数据及结果的审核。
4.1.4 验证报告的审批。
4.1.5 再验证周期的确认。
4.2 生产部4.2.1 负责验证方案的起草。
无菌培养基灌装验证方案Media fill
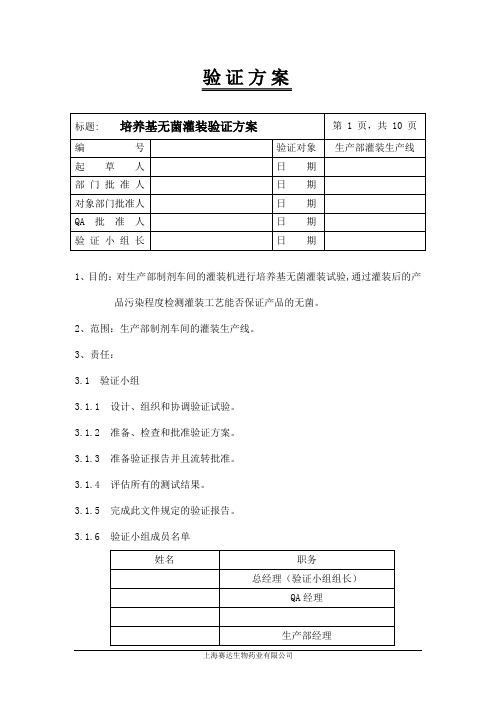
验证方案1、目的:对生产部制剂车间的灌装机进行培养基无菌灌装试验,通过灌装后的产品污染程度检测灌装工艺能否保证产品的无菌。
2、范围:生产部制剂车间的灌装生产线。
3、责任:3.1验证小组3.1.1设计、组织和协调验证试验。
3.1.2准备、检查和批准验证方案。
3.1.3准备验证报告并且流转批准。
3.1.4评估所有的测试结果。
3.1.5完成此文件规定的验证报告。
3.1.6验证小组成员名单3.2生产部3.2.1对灌装车间进行清扫、消毒,保证环境清洁。
3.2.2操作灌装机。
3.2.3按照规定的程序进行培养基灌装。
3.2.4进行日常清洗、维护。
3.3QA3.3.1取样。
3.3.2进行目检。
3.3.3进行环境监测。
3.3.4检查和批准验证方案和报告。
4、描述制剂车间使用x公司的灌装流水线,包括:洗瓶机、隧道烘箱、灌装机、轧盖机,y公司的冻干机进行冻干。
5、程序5.1使用的设备及材料5.1.1洗瓶机5.1.2隧道烘箱5.1.3灌装机5.1.4冻干机5.1.5灌装材料5.1.5.1瓶子5.1.5.2胶塞5.1.5.3铝盖5.1.6培养基5.1.7菌种5.1.7.1枯草杆菌(Bacillus Subtilis) ATCC 66335.1.7.2白色念珠菌(Candida alblcans) ATCC 102315.1.7.3厂房环境分离菌5.2培养基准备5.2.1在10L血清瓶中加入2L的热注射用水,再加入240g胰蛋白胨大豆肉汤充分搅拌,等溶解后再加入6L的热注射用水,整个培养基量为8L。
5.2.2将配制好的培养基放到高压蒸汽灭菌柜中121℃灭菌30分钟,灭菌后取出血清瓶,从瓶中取4瓶(50ml/瓶)作为阴性对照,其中2瓶于32±2℃培养14天,另外2瓶于23±2℃培养14天。
观察有无微生物污染。
5.3培养基无菌灌装5.3.1准备无菌的灌装器具(针、硅管、等等),联接到灌装机上。
硅管一头放入灭菌培养基中。
西林瓶灌装机清洗验证方案

清洗验证编号:SOP-VM/EC-001-00万级滴眼(耳、鼻)剂灌装联动机清洗验证ABC有限公司目录1.验证方案审批1.1 验证方案起草1.2 验证方案批准1.3 验证方案实施2. 验证报告的审批2.1 验证报告的起草2.2 验证报告的批准3.验证小组成员4. 验证目的5. 设备概况6.安装确认6.1 相关文件及SOP6.2 验证资料6.3 设备安装检查及记录7. 运行测试7.1 功能测试7.2 万级滴眼(耳、鼻)剂灌装联动机速度测试8、性能确认8.1灌装装量测试8.2加塞、拧盖状态测试8.3拧盖后瓶密封性检查9.验证结论1.验证方案审批1.2 验证方案批准1.3 验证方案实施2. 验证报告的审批2.2 验证报告的批准3.验证小组成员组长:组员:验证小组成员主要职责○○○:负责验证的组织协调及验证方案、验证报告的审核。
○○○:负责验证的组织协调工作。
○○○、○○○:负责验证过程中取样及检验工作。
○○○、○○○:负责按设备操作规程进行操作。
○○○:负责设备的检查、设备的运行和性能的。
一、验证目的:本验证从目检、化学和微生物角度试验并再次证明,西林瓶灌装机按清洗规程(QG/HY WS-QJ-36-2000)进行清洗后,使用该设备进行无菌灌装生产时没有来自上批产品及清洗过程所带来污染的风险,以考证该SOP的可行性和可靠性。
三、清洗规程:执行SOP QG/HY WS-QJ-36-2000清洗流程图计量泵0.1NNaOH 注射用水冲净输液管道及针头反复冲洗干净浸泡1h贮药液罐121℃、蒸汽灭菌15minPH值与冲洗用注射用水相同无菌状态最终荡洗水装入灭菌盒胶塞振荡器盘面注射用水75%乙醇输瓶转盘面冲洗适量灭菌无尘绢布无菌棉球擦拭三遍擦拭台面取样检验四、验证方法:1、取样方法:1.1关键部位及取样点:a、计量泵、输液管及针头b、贮药液罐c、胶塞振荡器盘面d、输瓶转盘面e、灌装机台面1.2取样液及取样方法:a、b点取最终荡洗水(洗出液)——按《中国药典》2000版二部相关项下检验合格并经无菌过滤的新鲜注射用水冲洗的最终荡洗水;c、d、e三个设备工作面用无菌棉签擦抹法作无菌及内毒素检查。
无菌灌装验证
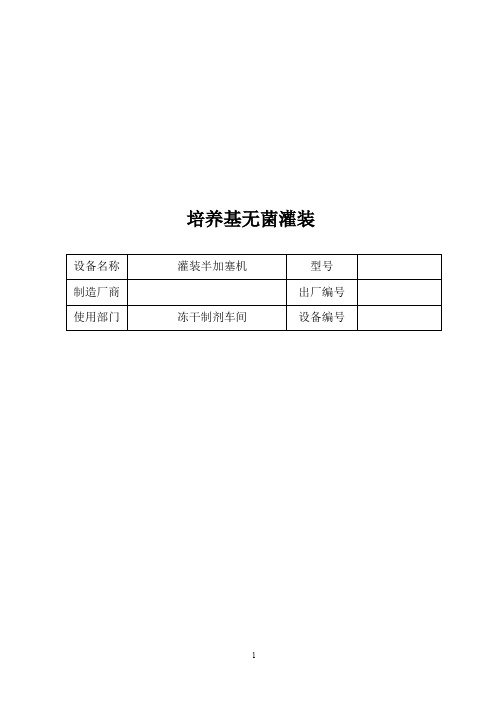
培养基无菌灌装目录验证方案一、验证目的二、设备概述三、验证小组组成四、验证程序五、验证进度六、验证内容与方法验证报告一、验证实施二、验证结果三、结果分析四、评价五、验证后期工作六、建议验证记录一、培养基灌装验证记录附:1.灭菌后西林瓶、胶塞无菌检测记录2.百级区表面微生物及操作人员手和衣物微生物动态监测记录培养基无菌灌装验证方案无菌灌装(培养基灌装)验证方案一、验证目的:通过培养基无菌灌装试验时已灌装培养基的西林瓶染菌率能否达到规定的合格标准,来确认冻干车间的洁净环境以及进行无菌灌装过程中所采用的各种防止微生物污染的方法和规程的可行性,从而为保证所生产产品的无菌性提供依据。
二、概述:无菌灌装是指由掌握了无菌操作的人员在一个有控制的环境中将经灭菌的无菌药液灌封于灭菌后的容器中,制成无菌药物的过程。
无菌灌装验证,是在与无菌灌装生产过程有关的其他验证,如:洁净厂房、公用系统、灭菌设备(包括蒸汽灭菌柜、隧道式灭菌干燥器、热循环烘箱等)验证合格后,且操作人员熟练掌握了岗位SOP后进行的。
培养基灌装作为无菌灌装的模拟实验,可以直观、方便、准确地反映出无菌灌装过程的污染情况及问题。
三、验证小组的成员:本设备的验证按文件SMP—YZ—0001—01规定组成验证小组,其成员及职责为:组长:全面负责本验证工作。
生产部:负责培养基的灌装操作。
质管部:负责样品的检测工作。
负责验证全过程的监控。
四、验证程序:本验证按文件SMP—XX—XXXX—XX规定的程序进行验证。
五、验证进度:年月日至年月日完成。
六、验证内容与方法:1.验证前须确认项目: 确认人员培训合格,公用系统、工艺用水系统和空调系统、车间设备处于正常运行状态,并提供相关的合格报告。
2.验证方法及过程监测项目:2.1 培养基的准备:培养基名称:胰蛋酶胨大豆肉汤培养基。
在临试验前,按规定配置好所需的液体培养基,并于121℃、20分钟进行灭菌。
2.2 灌装过程:按规程做好无菌灌装前的一切准备工作,开始无菌灌装,每支装量2毫升,每机灌装数量不得少于3000瓶,加塞为半加塞,灌装加塞同步完成后,每盘依次编号入冻干箱,模拟生产状态时压塞,压塞完毕传入轧盖间加铝盖轧盖后交QC培养。
无菌模拟灌装工艺验证[指南]
![无菌模拟灌装工艺验证[指南]](https://img.taocdn.com/s3/m/f74cc6ae6c85ec3a86c2c524.png)
无菌工艺模拟验证-培养基灌装试验王新峰QA/QC 厂房设施人员灭菌工艺无菌保证培养基灌装HVAC,水操作规程日常监控EM&PM内容1.培养基灌装的目的2.法规要求3.不同制剂工艺的培养基灌装(液体、冻干产品,干粉分装产品)4.风险分析5.实验设计6.审计要点培养基灌装试验的定义定义:培养基灌装-采用培养基代替产品,按照正常生产的程序来进行无菌灌装工艺验证。
培养基灌装试验目的目的:–评估在既定无菌生产环境和过程控制条件下生产无菌产品的能力–证明指定的无菌工艺设计和变更是否可行–证明无菌工艺过程中的相关操作是否可行–评估无菌工艺人员的操作水平(资格确认组成部分)– QAR调查的手段–证明符合cCMP的要求–发现无菌工艺过程中潜在的微生物污染因素培养基灌装试验应用范围•无菌药品和生物制剂的生产•用无菌工艺进行医疗器械,人和动物保健品的生产法规要求2010GMP•第四十七条无菌生产工艺的验证应当包括培养基模拟灌装试验。
•应当根据产品的剂型、培养基的选择性、澄清度、浓度和灭菌的适用性选择培养基。
应当尽可能模拟常规的无菌生产工艺,包括所有对无菌结果有影响的关键操作,及生产中可能出现的各种干预和最差条件。
•培养基模拟灌装试验的首次验证,每班次应当连续进行3次合格试验。
空气净化系统、设备、生产工艺及人员重大变更后,应当重复进行培养基模拟灌装试验。
培养基模拟灌装试验通常应当按照生产工艺每班次半年进行1次,每次至少一批。
•培养基灌装容器的数量应当足以保证评价的有效性。
批量较小的产品,培养基灌装的数量应当至少等于产品的批量。
培养基模拟灌装试验的目标是零污染,应当遵循以下要求:•(一)灌装数量少于5000支时,不得检出污染品。
•(二)灌装数量在5000至10000支时:•1.有1支污染,需调查,可考虑重复试验;•2.有2支污染,需调查后,进行再验证。
•(三)灌装数量超过10000支时:•1.有1支污染,需调查;•2.有2支污染,需调查后,进行再验证。
培养基模拟灌装无菌生产工艺验证方案

培养基模拟灌装无菌生产工艺验证方案一、研究目的及背景无菌生产是制药和食品工业中至关重要的一项工艺。
培养基是无菌生产过程中不可或缺的一部分,它提供了细菌、真菌等微生物的生长所需的营养物质。
因此,为了确保产品质量和安全性,对培养基的无菌灌装工艺进行验证是非常重要的。
本研究的目的是验证培养基的无菌灌装工艺的有效性,以确保生产过程中的无菌状态。
通过验证,可以确定灌装工艺的可行性和合理性,并提供指导和保障无菌生产的稳定性和安全性。
二、研究方法1.确定灌装工艺的关键参数和控制点:包括温度、压力和速度等因素。
通过前期的实验研究和参考相关文献资料,确定灌装工艺的最佳参数设置。
2.建立合适的实验方案:选择合适的微生物作为试验菌株,并使用合适的培养基进行培养。
根据已有的灌装工艺参数,进行一定数量的灌装试验,并尽可能模拟实际生产过程。
3.进行灌装工艺验证试验:根据实验方案,按照一定的时间和数量进行培养基的灌装试验。
同时,进行相应的对照试验,采集样品进行微生物学检验。
4.微生物学检验:采集灌装好的培养基样品,通过无菌条件下培养,观察是否有微生物生长。
并进行定性定量分析,以判断培养基是否被污染。
5.数据分析和结果评估:根据实验结果,对培养基的无菌灌装工艺进行评估。
比较实验组和对照组的差异,并统计相关数据,计算灌装工艺的合格率和不合格率。
6.结果报告和验证方案调整:将实验结果进行总结和分析,撰写验证方案报告。
根据结果对灌装工艺进行调整和改进,并制定相应的控制措施。
三、实施计划和进度安排1.研究期限:本研究计划为期三个月。
2.实施计划:-第一周:搜集相关文献资料,确定研究目的和方法。
-第二周:设计实验方案,确定试验菌株和培养基。
-第三周至第五周:进行实验,进行灌装试验并采集样品。
-第六周至第七周:进行微生物学检验,观察和分析实验结果。
-第八周:数据分析和结果评估,撰写验证方案报告。
-第九周至第十二周:根据结果调整灌装工艺,并制定相应的控制措施。
生物制品车间西林瓶无菌灌装验证方案

标题:生物制品车间西林瓶无菌灌装验证方案设备/系统编号:生物制品车间方案编号:STP-QA-YZ019版本号:08方案执行前批准注:签名表示已对方案的准确性、完整性和GMP的符合性进行了审核并符合相关要求,同时承诺及时安排相应的人力物力资源执行该方案。
同意批准方案用于执行。
目录方法执行前批准 (2)1目的 (4)2范围 (4)3编订依据 (4)4.部门职责 (4)5.验证内容 (5)5.1概述 (5)5.1.1生产所用主要设备 (5)5.1.2生产工艺和品种情况 (5)5.1.3参加无菌灌装验证人员情况 (6)5.2验证方法 (6)5.3再验证周期 (8)6.附录 (9)1目的此验证方案的设计有助于证明采用此无菌灌装工艺生产出的产品符合成品质量标准,尤其是无菌性的控制标准。
无菌分装过程的验证是在人员进行相关培训及水系统、空调系统、消毒系统及清洗等验证合格基础上进行的。
本次结合灌装生产技术指标和技术要求,确定无菌灌装工艺的再验证内容。
通过培养基无菌灌装试验考察无菌灌装过程中环境是否达到要求,人员操作是否规范,灌装工艺是否合理,为灌装产品的无菌保证提供依据。
2006年10月西林瓶生产线完成改造后进行了首次验证,2007年生物制品车间空调系统改造后进行了西林瓶生产线无菌灌装的再验证,2008、2009年在设备连续正常运行一年后分别进行了再验证,此次验证为2011年冻干粉针投产前的再验证。
2范围适用于生物制品车间西林瓶无菌灌装工艺的再验证。
3依据3.1《药品生产质量管理规范》(2010年修订)。
3.2《药品生产验证指南》(2003年)。
4责任人4.1验证委员会4.1.1负责验证方案的审批。
4.1.2负责验证的协调工作,以保证本验证方案规定项目的顺利实施。
4.1.3负责验证数据及结果的审核。
4.1.4验证报告的审批。
4.1.5再验证周期的确认。
4.2生产部4.2.1负责验证方案的起草。
4.2.2负责验证方案的实施和设备的操作。
7、无菌药品关键设备--西林瓶灌装加塞机检查要点

西林瓶灌装加塞机检查要点
西林瓶灌装加塞机由控制系统、进瓶系统、灌装系统、加塞系统等组成,主要用于非最终灭菌产品的灌装和加塞操作,该操作使产品暴露在开放空气环境下,属高风险操作。
为有效降低微生物污染风险,并能最大限度减少对操作人员的暴露,可将西林瓶灌装加塞机安装在无菌隔离系统内。
西林瓶灌装加塞机的灌装精度及稳定性关系到产品的装量差异,灌装和加塞过程中环境状况、人员干预、内包材本身均可带如微粒异物等,直接威胁产品的安全。
因此,检查过程中应重点对灌装和加塞操作的环境状况、人员干预情况等进行检查,此外,也有必要对设备验证报告在内的文件系统进行检查,查看其记录的内容真实性和完整性。
检查时应关注以下几个方面:
(1)西林瓶灌装加塞机所处环境:灌装加塞机所处功能间的洁净级别应符合要求,运行期间应规定最多容纳人数。
灌装和加塞区应当用单向流维持该区环境状况,检查时应关注其层流系统的风速设置,及环境监测情况。
(2)西林瓶灌装加塞机的确认与验证:灌装和加塞属于高风险操作,应验证其单向流的气流方式不会导致污染风险,检查时关注气流流线型测试的录像,特别是人员干预情况是否具有代表性;灌装和加塞过程中可能存在倒瓶、理瓶、停电、空调系统故障等情况,检查时应关注其对失效模式验证及实施情况;此外,为降低微生物污染的
风险,应对灌装过程的时间限度进行验证。
(3)人员操作风险:人员是最大的污染源,检查时应关注人员的相关岗位培训情况,人员更衣情况及人员操作规范性,特别是倒瓶、理瓶处理的规范性。
- 1、下载文档前请自行甄别文档内容的完整性,平台不提供额外的编辑、内容补充、找答案等附加服务。
- 2、"仅部分预览"的文档,不可在线预览部分如存在完整性等问题,可反馈申请退款(可完整预览的文档不适用该条件!)。
- 3、如文档侵犯您的权益,请联系客服反馈,我们会尽快为您处理(人工客服工作时间:9:00-18:30)。
标题: 生物制品车间西林瓶无菌灌装验证方案设备/系统编号: 生物制品车间方案编号: STP-QA-YZ019版本号: 08方案执行前批准注:签名表示已对方案的准确性、完整性和GMP的符合性进行了审核并符合相关要求,同时承诺及时安排相应的人力物力资源执行该方案。
同意批准方案用于执行。
目录方法执行前批准 (2)1 目的 (4)2 范围 (4)3 编订依据 (4)4. 部门职责 (4)5. 验证内容 (5)5.1 概述 (5)5.1.1生产所用主要设备 (5)5.1.2生产工艺和品种情况 (5)5.1.3参加无菌灌装验证人员情况 (6)5.2验证方法 (6)5.3 再验证周期 (8)6. 附录 (9)1 目的此验证方案的设计有助于证明采用此无菌灌装工艺生产出的产品符合成品质量标准,尤其是无菌性的控制标准。
无菌分装过程的验证是在人员进行相关培训及水系统、空调系统、消毒系统及清洗等验证合格基础上进行的。
本次结合灌装生产技术指标和技术要求,确定无菌灌装工艺的再验证内容。
通过培养基无菌灌装试验考察无菌灌装过程中环境是否达到要求,人员操作是否规范,灌装工艺是否合理,为灌装产品的无菌保证提供依据。
2006年10月西林瓶生产线完成改造后进行了首次验证,2007年生物制品车间空调系统改造后进行了西林瓶生产线无菌灌装的再验证,2008、2009年在设备连续正常运行一年后分别进行了再验证,此次验证为2011年冻干粉针投产前的再验证。
2 范围适用于生物制品车间西林瓶无菌灌装工艺的再验证。
3 依据3.1 《药品生产质量管理规范》(2010年修订)。
3.2 《药品生产验证指南》(2003年)。
4 责任人4.1 验证委员会4.1.1 负责验证方案的审批。
4.1.2 负责验证的协调工作,以保证本验证方案规定项目的顺利实施。
4.1.3负责验证数据及结果的审核。
4.1.4 验证报告的审批。
4.1.5 再验证周期的确认。
4.2 生产部4.2.1 负责验证方案的起草。
4.2.2 负责验证方案的实施和设备的操作。
4.2.3 负责公用系统的操作及保养。
4.3设备部4.3.1 负责验证所需仪器、仪表、量具的校验。
4.3.2 负责设备的维修保养。
4.3.3负责提供技术服务。
4.4 质管部4.4.1 负责取样及对样品的检验,负责环境监测。
4.4.2 负责验证过程中的监控。
4.4.3 收集验证试验结果并对结果进行分析评价。
4.4.4 起草验证报告并报验证小组。
5 内容生物制品车间目前生产品种有2个,重组人干扰素α2b注射液和注射用重组人干扰素α2b,共用一条生产线,生产灌装工艺参数如下:从上表可以看出,灌装工艺有2种,一种为小容量注射剂(全压塞),转轧盖;一种为冻干粉针剂(半加塞),转冻干机冻干后压塞,转轧盖。
此次验证工艺为冻干粉针剂,因其所有产品均为1ml,所以选择灌装体积为1ml。
5.1 概述无菌分装过程的验证即培养基灌装实验,是在其它各系统如灭菌系统、公用系统、无菌环境保持系统及清洗等验证合格基础上进行的。
本方案实施时,其它配套系统均应正常运转。
此次验证的无菌灌装人员列表如下:5.2 验证方法5.2.1 概述:模拟生产无菌灌装过程,无菌灌装除菌过滤后的胰蛋白胨大豆肉汤培养基(TSB),半加塞,转冻干,轧盖。
生产过程中应完全模拟真实生产过程,进行装量检查。
连续灌装3次,每次正常灌装6000支,装量1ml/支,半加塞,灌装加塞后转移至冻干机中放置至少30小时压塞后轧盖。
灌装完毕的培养基首先在20-25℃培养7天,然后在30-35℃培养7天,观察西林瓶内培养基长菌情况,并记录。
5.2.2 公用介质的准备5.2.2.1 纯化水A.评价方法:按《工艺用水管理制度》规定的频次和《水质检验标准操作规程》规定的检验方法对纯化水进行检测。
B.标准:5.2.2.2 注射用水A.评价方法:按《工艺用水管理制度》规定的频次和《水质检验标准操作规程》规定的检验方法对纯化水进行检测。
B.标准:5.2.3 无菌环境控制与监测5.2.3.1 洁净区沉降菌、浮游菌和悬浮粒子测试A.评价方法:生产前按《洁净区沉降菌测试标准操作规程》、《洁净区浮游菌测试标准操作规程》和《洁净区悬浮粒子测试标准操作规程》对洁净区的沉降菌、浮游菌和悬浮粒子进行测定,在生产过程中,在关键操作的全过程,包括设备组装应对百级灌装区进行沉降菌的动态监测。
在灌装前段、中段、后段对关键操作区分装设备上方、理瓶机上方、冻干机门前上方进行动态悬浮粒子的监测。
动态取样应避免对洁净区造成不良影响。
B.标准:5.2.3.2 操作间压差测定A.评价方法:生产前测定,将所有门关闭,观察安装在各个相应房间的压差计,记录,灌装间与相临房间有传输口的地方做气流流向测定以确保无菌状况。
B.标准:相邻不同级别空间的静压差绝对值>5Pa;洁净区与室外的压差>10Pa;灌装间应相对正压。
5.2.4 操作间、设备、操作人员表面微生物测定5.2.4.1 操作人员A.评价方法:对表面和操作人员的监测,应在关键操作完成后进行。
对百级灌装区的操作人员的手套、胸前、手臂等部位的微生物进行监测,手套为接触平皿,其它部位采用棉签擦拭法进行,取出事先准备好的浸泡在5ml灭菌注射用水中的无菌棉签,从左到右擦拭面积25 cm2,然后将擦拭后的棉签放回原盛装容器中,振摇1min,吸取1ml浸出液于灭菌平皿中,将融化的营养琼脂培养基倒入培养皿中,混匀,水平放置,凝固后将培养皿倒置于30~35℃培养48小时,计算菌落数,每个棉签做两块平皿。
灌装间的每个人员包括现场QA均取样,详细标记和记录被取样人、取样时间、取样部位。
B.标准:手套全部检出菌数<1个,操作者身上每个部位的两个平皿检出菌数之和<1个。
5.2.4.2 操作间、设备表面A.评价方法:取出事先准备好的浸泡在5ml灭菌注射用水中的无菌棉签,从左到右擦拭操作间及设备表面,擦拭面积为25 cm2,然后将擦拭后的棉签放回原盛装容器中,振摇1min,吸取1ml浸出液于灭菌平皿中,将融化的营养琼脂培养基倒入培养皿中,混匀,水平放置,凝固后将培养皿倒置于30~35℃培养48小时,计算菌落数,每个棉签做两块平皿。
操作间四面墙壁各取1个点,两台旋转理瓶机和灌装机轨道表面、冻干机板层上各取2个点。
B. 标准:百级区域表面微生物<1个/25cm2,即2个平皿检出菌数之和<1个。
5.2.5 原料和包装材料确认5.2.5.1 西林瓶的灭菌效果检查A.评价方法:任取灭菌后的西林瓶40支,分为两份,20支/份,分别接种至硫乙醇酸盐流体培养基和改良马丁培养基中,分别置30—35℃和20—25℃培养14天。
B.标准:应无菌生长。
5.2.5.2 胶塞的灭菌效果检查A.评价方法:任取灭菌后的胶塞40个,分为两份,20个/份,分别接种至硫乙醇酸盐流体培养基和改良马丁培养基中,置30—35℃和20—25℃培养14天。
B. 标准:应无菌生长。
5.2.6 培养基灌装实验5.2.6.1 液体培养基说明A.成份:胰蛋白胨大豆肉汤培养基。
培养基的配制:取脱水胰蛋白胨大豆肉汤培养基,按说明书上的配方配制,按正常生产过程无菌过滤。
5.2.6.2 模拟灌装试验按灌装标准操作规程进行灌装,模拟生产过程进行装量等检测。
半加塞,装载入冻干机板层上,关闭冻干机前箱大门,放置至少30小时后在冻干机内压赛,取出轧盖。
5.2.6.3 合格标准将上述灌装后的培养基50%正放,50%倒放,先置20-25℃培养7天,接着在30-35℃培养7天,分别于第7天、第14天观察结果,灌装少于5000支时,不应检出污染品;灌装在5000至10000时:污染概率应为0%。
有1支污染需进行调查,并考虑重复培养基灌装试验;2支污染需进行调查,并需要再验证。
发生任何微生物污染时,均应进行调查。
5.2.7 阳性对照和阴性对照的制备A.方法:灌装结束后,用灭菌后的试管从配制的除菌滤器后接取培养基,15ml/管,共装4支,分两组,每组两支,一组作为阳性,接种金黄葡萄球菌稀释菌液(100CFU/ml),接种量1.0ml,于30-35℃培养48小时,一组作为阴性,于30-35℃培养14天。
B.标准:24hr内阳性应有菌明显生长,阴性在14天内无菌生长。
5.3 再验证周期:1)培养基模拟试验的初始验证每班次需要连续进行3次合格试验。
2)培养基模拟试验通常按生产工艺每班次半年进行1次,每次至少一批。
停产半年后,再生产前,应进行再验证。
3)设备、空调净化系统有重大变更后,应进行再验证。
4)当产品的分装工艺及人员或影响产品质量的主要因素有重大变更后,应进行再验证。
6.验证结果记录及结果评价,见附件。
附件1 液体灌装工艺验证结果及记录(1)附件2 液体灌装工艺验证结果及记录(2)附件3 液体灌装工艺验证结果及记录(3)附件4 液体灌装工艺验证结果及记录(4)附件5 液体灌装工艺验证结果及记录(5)附件6无菌灌装验证培养基配制生产记录附件7 西林瓶无菌灌装验证生产记录附件1液体灌装工艺验证结果及记录(1)液体灌装工艺验证结果及记录(2)第次液体灌装工艺验证结果及记录(3)第次液体灌装工艺验证结果及记录(4)液体灌装工艺验证结果及记录(5)附件6 液体灌装工艺验证结果及记录(6)培养基污染情况统计附件7。