机械毕业设计英文外文翻译108低滚动阻力轮胎 - 副本
(机械制造行业)机械外文翻译中英文

Engine lathes, of course, are general-purpose machine used in production and maintenance shop all over the the world. Sized ranger from small bench models to huge heavy duty pieces of equipment. Many of the larger lathes come equipped with attachments not commonly found in the ordinary shop, such as automatic shop for the carriage.
Because the high quality and low price of ball and roller bearing depends on quantity production,the task of the machine designer becomes one of selection rather than design. Rolling-contact bearings are generally made with steel which is through-hardened to about 900HV,although in many mechanisms special races are not provided and the interacting surfaces are hardened to about 600HV. It is not surprising that,owing to the high stresses involved,a predominant form of failure should be metal fatigue, and a good deal of work is based on accept values of life and it is general practice in b load capacity of the bearing as that value below which 90 percent of a batch will exceed life of one million revolutions.
机械设计中英文词汇表(按英文排序)
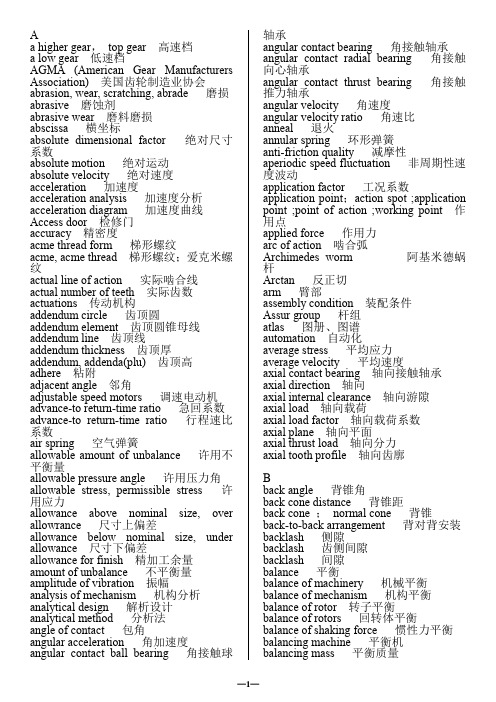
Aa higher gear,top gear 高速档a low gear 低速档AGMA (American Gear Manufacturers Association) 美国齿轮制造业协会abrasion, wear, scratching, abrade 磨损abrasive 磨蚀剂abrasive wear 磨料磨损abscissa 横坐标absolute dimensional factor 绝对尺寸系数absolute motion 绝对运动absolute velocity 绝对速度acceleration 加速度acceleration analysis 加速度分析acceleration diagram 加速度曲线Access door 检修门accuracy 精密度acme thread form 梯形螺纹acme, acme thread 梯形螺纹;爱克米螺纹actual line of action 实际啮合线actual number of teeth 实际齿数actuations 传动机构addendum circle 齿顶圆addendum element 齿顶圆锥母线addendum line 齿顶线addendum thickness 齿顶厚addendum, addenda(plu) 齿顶高adhere 粘附adjacent angle 邻角adjustable speed motors 调速电动机advance-to return-time ratio 急回系数advance-to return-time ratio 行程速比系数air spring 空气弹簧allowable amount of unbalance 许用不平衡量allowable pressure angle 许用压力角allowable stress, permissible stress 许用应力allowance above nominal size, over allowrance 尺寸上偏差allowance below nominal size, under allowance 尺寸下偏差allowance for finish 精加工余量amount of unbalance 不平衡量amplitude of vibration 振幅analysis of mechanism 机构分析analytical design 解析设计analytical method 分析法angle of contact 包角angular acceleration 角加速度angular contact ball bearing 角接触球轴承angular contact bearing 角接触轴承angular contact radial bearing 角接触向心轴承angular contact thrust bearing 角接触推力轴承angular velocity 角速度angular velocity ratio 角速比anneal 退火annular spring 环形弹簧anti-friction quality 减摩性aperiodic speed fluctuation 非周期性速度波动application factor 工况系数application point;action spot ;applicationpoint ;point of action ;working point 作用点applied force 作用力arc of action 啮合弧Archimedes worm 阿基米德蜗杆Arctan 反正切arm 臂部assembly condition 装配条件Assur group 杆组atlas 图册、图谱automation 自动化average stress 平均应力average velocity 平均速度axial contact bearing 轴向接触轴承axial direction 轴向axial internal clearance 轴向游隙axial load 轴向载荷axial load factor 轴向载荷系数axial plane 轴向平面axial thrust load 轴向分力axial tooth profile 轴向齿廓Bback angle 背锥角back cone distance 背锥距back cone ;normal cone 背锥back-to-back arrangement 背对背安装backlash 侧隙backlash 齿侧间隙backlash 间隙balance 平衡balance of machinery 机械平衡balance of mechanism 机构平衡balance of rotor 转子平衡balance of rotors 回转体平衡balance of shaking force 惯性力平衡balancing machine 平衡机balancing mass 平衡质量—1—balancing quality 平衡品质balancing speed 平衡转速balata spring 橡胶弹簧ball 球ball bearing 球轴承ball screw 滚珠丝杆band brake 带式制动器barrel (cylindric) cam 圆柱式凸轮步进运动机构base circle 基圆base cone 基圆锥base cylinder 基圆柱base pitch 基圆齿距basic dynamic axial load rating 轴向基本额定动载荷basic dynamic radial load rating 径向基本额定动载荷basic rating life 基本额定寿命basic static axial load rating 轴向基本额定静载荷basic static radial load tating 径向基本额定静载荷beading stress 弯曲应力bearing alloy 轴承合金bearing block 轴承座bearing bore diameter 轴承内径bearing bush 轴瓦、轴承衬bearing capacity 承载能力bearing capacity factor 承载量系数bearing cup 轴承盖bearing height 轴承高度bearing life 轴承寿命bearing outside diameter 轴承外径bearing ring 轴承套圈bearing width 轴承宽度belleville spring 碟形弹簧belt driving 带传动belt pulley 带轮bending moment 弯矩bevel gear 锥齿轮bevel gears 圆锥齿轮机构bevel pulley, bevel wheel 锥轮bisector 平分线black box 黑箱blank 齿轮轮坯blank 轮坯block diagram 框图blower 鼓风机body guidance mechanism 刚体导引机构bold line 粗线bolts 螺栓bottom clearance 顶隙boundary dimension 外形尺寸brake 制动器buttress thread form 锯齿形螺纹Ccage 保持架calculated bending moment 计算弯矩cam 凸轮cam , cam mechanism 凸轮机构cam profile 实际廓线cam profile 凸轮廓线cam with oscillating follower 摆动从动件凸轮机构cantilever beam 悬臂梁cantilever structure 悬臂结构Cartesian coordinate manipulator 直角坐标操作器cascade speed control 串级调速case-based design,CBD 基于实例设计center distance 中心距center distance change 中心距变动center of mass 质心center of pressure 压力中心central gear 中心轮centrifugal force 离心力centrifugal force 向心力centrifugal seal 离心密封centrifugal stress 离心应力chain 链chain dotted line 点划线chain gearing 链传动装置chamfer 倒角change gear, change wheel 变速齿轮characteristics 特性chassis 底座circular gear 圆形齿轮circular pitch 齿距circular pitch, pitch of teeth 节距circular thickness 圆弧齿厚circulating power load 循环功率流clearance 径向间隙clockwise 顺时针closed chain mechanism 闭链机构closed kinematic chain 闭式链clutch 离合器coarse thread 粗牙螺纹coefficient of addendum 齿顶高系数coefficient of friction 摩擦系数coefficient of normal addendum 法面齿顶高系数coefficient of speed fluctuation 机械运转不均匀系数coefficient of speed fluctuation 速度不均匀coefficient of transverse addendum 端面—2—齿顶高系数coefficient of travel speed variation 行程速度变化系数coefficient of velocity fluctuation 运转不均匀系数coincident points 重合点combination in parallel 并联式组合combination in series 串联式组合combined efficiency, overall efficiency 总效率combined mechanism 组合机构combined mechanism 组合机构combined stress 复合应力common apex of cone 锥顶common normal line 公法线compensation 补偿complex mechanism 复杂机构composite tooth form 组合齿形compound (or combined) gear train 复合轮系compound combining 复合式组合compound flat belt 复合平带compound gear train 混合轮系compound hinge 复合铰链Compound screw mechanism 复式螺旋机构compression strength 抗压强度compressive stress 压应力compressor 压缩机computer aided design, CAD 计算机辅助设计computer aided manufacturing, CAM 计算机辅助制造computer integrated manufacturing system, CIMS 计算机集成制造系统concavity 凹面、凹度concept design, CD 方案设计、概念设计concurred design, CD 并行设计concurrent engineering 并行工程condition of self-locking 自锁条件conduction of heat 导热性cone angle 圆锥角cone distance 锥距conjugate cam 共轭凸轮conjugate profiles 共轭齿廓conjugate yoke radial cam 等径凸轮connecting rod, coupler 连杆conoid helical-coil compression spring 圆锥螺旋扭转弹簧constant-breadth cam 等宽凸轮constant-velocity (or double) universal joint 双万向联轴节constitution of mechanism 机构组成constraining force 约束反力constraint 约束constraint condition 约束条件consumption 消耗contact points 啮合点contact ratio 重合度contact seal 接触式密封contact stress 接触应力conventional mechanism, mechanism incommon use 常用机构convex 凸的,凸面体convex roller 球面滚子coordinate frame 坐标系correcting plane 平衡平面correcting plane 校正平面corrosion resistance 耐腐蚀性cosine acceleration (or simple harmonic)motion 余弦加速度运动counterclockwise (or anticlockwise) 逆时针counterweight 平衡重couple 力偶coupler-curve 连杆曲线coupling, shaft coupling 联轴器crank 曲柄crank angle between extreme (or limiting)positions 极位夹角crank arm, planet carrier 系杆crank shaft 曲轴crank shaper (guide-bar) mechanism 曲柄导杆机构crank-rocker mechanism 曲柄摇杆机构creation design 创新设计critical speed 临界转速cross-belt drive 交叉带传动crossed helical gears 交错轴斜齿轮crown gear 冠轮curvature 曲率curve matching 曲线拼接curved-shoe follower 曲面从动件curvilinear motion 曲线运动cutter 刀具cutting accuracy 切削精度cycle of motion 运动周期cycloidal gear 摆线齿轮cycloidal motion 摆线运动规律cycloidal tooth profile 摆线齿形cycloidal-pin wheel 摆线针轮cylindric pair 圆柱副cylindrical cam 圆柱凸轮cylindrical coordinate manipulator 圆柱坐标操作器cylindrical roller 圆柱滚子—3—cylindrical roller bearing 圆柱滚子轴承cylindrical worm 圆柱蜗杆cylindroid helical-coil compression spring 圆柱螺旋压缩弹簧cylindroid helical-coil extension spring 圆柱螺旋拉伸弹簧cylindroid helical-coil torsion spring 圆柱螺旋扭转弹簧Ddead point 死点dedendum 齿根高dedendum circle 齿根圆deep groove ball bearing 深沟球轴承deformation 变形degree of freedom, mobility 自由度degree of reliability 可靠度denominator 分母depth of cut 切齿深度derivative 导数design constraints 设计约束design for product`s life cycle, DPLC 面向产品生命周期设计design methodology 设计方法学design variable 设计变量detrimental resistance 有害阻力diameter of addendum 齿顶圆直径diameter series 直径系列diametral pitch 径节diametral quotient 蜗杆直径系数diametral quotient 直径系数differential 差速器differential gear train 差动轮系differential screw mechanism 差动螺旋机构differential screw mechanism 微动螺旋机构dimension series 尺寸系列direct (forward) kinematics 正向运动学disc brake 圆盘制动器disc friction clutch 圆盘摩擦离合器disk cam 盘形凸轮disk-like rotor 盘形转子displacement 位移displacement diagram 位移曲线double Haas planer 龙门刨床double crank mechanism 双曲柄机构double rocker mechanism 双摇杆机构double roller chain coupling 滚子链联轴器double row bearing 双列轴承double slider coupling, Oldham‘s coupling 十字滑块联轴器double-direction thrust bearing 双向推力轴承double-slider mechanism, ellipsograph双滑块机构driven gear 从动轮driven link, follower 从动件driven pulley 从动带轮driven system 传动系统driving force 驱动力driving gear 主动齿轮driving link 原动件driving link 主动件driving moment (torque) 驱动力矩driving pulley 主动带轮dwell 停歇dyad IIdynamic analysis design 动态分析设计dynamic analysis of machinery 机械动力分析dynamic balance 动平衡dynamic balancing machine 动平衡机dynamic characteristics 动态特性dynamic design of machinery 机械动力设计dynamic energy 动能dynamic equivalent axial load 轴向当量动载荷dynamic equivalent radial load 径向当量动载荷dynamic load 动载荷dynamic lubrication 动力润滑dynamic reaction 动压力dynamic viscosity 动力粘度dynamically equivalent model 等效动力学模型dynamics 动力学dynamics of machinery 机械动力学Eeccentric 偏心盘eccentric mass 偏心质量eccentricity ratio 偏心率effective circle force 有效圆周力effective length of line of action 实际啮合线段长度effective resistance 工作阻力effective resistance moment 工作阻力矩effective tension 有效拉力elastic coupling, flexible coupling 弹性联轴器elasticity sliding motion 弹性滑动end-effector 末端执行器energy 能量engagement, mesh, gearing, action 啮合—4—engaging-in 啮入engaging-out 啮出epicyclic gear train 周转轮系equilibrium 力平衡equivalent 等效量equivalent coefficient of friction 当量摩擦系数equivalent force 等效力equivalent link 等效构件equivalent load 当量载荷equivalent mass 等效质量equivalent mechanism 替代机构equivalent moment of force 等效力矩equivalent moment of inertia 等效转动惯量equivalent spur gear of the bevel gear 锥齿轮的当量直齿轮equivalent spur gear of the helical gear 斜齿轮的当量直齿轮equivalent spur gear, virtual gear 当量齿轮equivalent teeth number, virtual number of teeth 当量齿数evaluation and decision 评价与决策executive link, working link 执行构件external force 外力external gear 外齿轮external loads 工作载荷extreme (or limiting) position 极限位置Fface width 齿宽face width 平底宽度face-to-face arrangement 面对面安装factor of stress concentration 应力集中系数factored moment, calculation moment 计算力矩fastener 紧固件fatigue limit 疲劳极限fatigue strength 疲劳强度feather key 滑键、导键feedback combining 反馈式组合felt ring seal 毡圈密封ferrofluid seal 铁磁流体密封field balancing 现场平衡fillet radius 圆角半径final contact, end of contact 终止啮合点fine threads 细牙螺纹fixed link, frame 固定构件flange coupling 凸缘联轴器flat belt 平带flat belt driving 平带传动flat leaf spring 板簧flat-face follower 平底从动件flexible automation 柔性自动化flexible impulse, soft shock 柔性冲击flexible manufacturing system, FMS 柔性制造系统flexible rotor 挠性转子flexspline 柔轮fluctuating circulating stress 脉动循环应力fluctuating load 脉动载荷Fluctuating loads 变载荷flywheel 飞轮follower dwell 从动件停歇follower motion 从动件运动规律force 力force polygon 力多边形force-drive (or force-closed) cammechanism 力封闭型凸轮机构forced vibration 强迫振动forge 锻造form cutting 仿形法form factor 齿形系数four-bar linkage 四杆机构frame, fixed link 机架freezing point, solidifying point 凝固点frequency 频率frequency control of motor speed 变频调速frequency converters 变频器frequency of vibration 振动频率friction 摩擦friction angle 摩擦角friction circle 摩擦圆friction force 摩擦力friction moment 摩擦力矩frictional resistance 摩擦阻力full balance of shaking force 惯性力完全平衡function analyses design 功能分析设计function generation 函数生成function generator 函数发生器fundamental law of gearing, fundamentallaw of gear-tooth action 齿廓啮合基本定律fundamental mechanism 基础机构fuzzy evaluation 模糊评价fuzzy set 模糊集Ggas bearing 气体轴承gasket 垫圈gasket seal 垫片密封gear 齿轮gear 齿轮机构—5—gear coupling 齿轮联轴器gear ratio 齿数比gear shaper 插齿机gear train 轮系gear wheel 大齿轮gearing, transmission gear, Actuations 传动装置general constraint 公共约束generalized coordinate 广义坐标generalized kinematic chain 一般化运动链generating 展成法generating cutting 范成法generating line 发生线generating line of involute 渐开线发生线generating plane 发生面generation mechanism 广义机构Geneva mechanism ;Maltese cross 槽轮机构Geneva numerate 槽数Geneva wheel 槽轮Geneva wheel, Geneva gear 马耳他机构graphical method 图解法Grashoff`s law 格拉晓夫定理Grashoff`s law 曲柄存在条件green design, design for environment 绿色设计grey cast iron 灰铸铁grinding wheel groove 砂轮越程槽groove cam 槽凸轮gyroscope 陀螺仪HH. Hertz equation 赫兹公式hands of worm 蜗杆旋向harmonic driving 谐波传动harmonic gear 谐波齿轮harmonic generator 谐波发生器heat balance, thermal equilibrium 热平衡height series 高度系列height series 高度系列helical bevel gear 螺旋锥齿轮helical gear 斜齿圆柱齿轮helical pair 螺旋副helical torsion spring 扭簧helix ,helical line 螺旋线helix angle 螺旋角helix angle at reference cylinder 分度圆柱螺旋角herringbone gear 人字齿轮high speed belt 高速带higher pair 高副hindley worm 直廓环面蜗杆hinge 铰链、枢纽hob 滚刀hob ,hobbing cutter 齿轮滚刀hollow flank worm 圆弧圆柱蜗杆Hooks coupling, universal coupling 万向联轴器hour-glass 砂漏hydraulic couplers 液力耦合器hydraulic mechanism 液压机构hydraulic stepless speed changes 液压无级变速hydrodynamic drive 液力传动hyperboloid gear 双曲面齿轮hypoid gear 准双曲面齿轮Iidle 空转idle gear 惰轮imbalance (or unbalance) 不平衡in-line slider-crank (or crank-slider)mechanism 对心曲柄滑块机构increment or decrement work 盈亏功inertia force 惯性力infinite 无穷大initial contact , beginning of contact 起始啮合点inner ring 内圈innovation, creation 创新input link 输入构件instantaneous center 瞬心instantaneous center of velocity 速度瞬心integrate 积分intelligent design, ID 智能化设计interchangeable gears 互换性齿轮interference 干涉intermittent gearing 不完全齿轮机构intermittent motion mechanism 间歇运动机构internal force 内力internal gear 内齿轮inverse ( or backward) kinematics 反向运动学inverse cam mechanism 凸轮倒置机构involute 渐开线involute equation 渐开线方程involute function 渐开线函数involute gear 渐开线齿轮involute helicoid 渐开螺旋面involute profile 渐开线齿廓involute spline 渐开线花键involute worm 渐开线蜗杆—6—Jjack 千斤顶Jacobi matrix 雅可比矩阵jaw (teeth) positive-contact coupling 牙嵌式联轴器jerk 跃度jerk diagram 跃度曲线jointed manipulator 关节型操作器journal 轴颈Kkenematic viscosity 运动粘度Kennedy`s theorem 三心定理key 键keyway 键槽kinematic analysis 运动分析kinematic chain 运动链kinematic design 运动设计kinematic design of mechanism 机构运动设计kinematic inversion 反转法kinematic inversion 机架变换kinematic inversion 运动倒置kinematic pair 运动副kinematic precept design 运动方案设计kinematic sketch 运动简图kinematic sketch of mechanism 机构运动简图kinematic synthesis 运动综合kinematical seal 动密封knife-edge follower 尖底从动件Llabyrinth seal 迷宫密封lathe 车床layout of cam profile 凸轮廓线绘制lead 导程lead 螺纹导程lead angle 导程角lead angle at reference cylinder 分度圆柱导程角leakage 泄漏length of line of action 啮合线长度lift 升距limit of action 极限啮合点line of action 啮合线line of centers 连心线linear motion 直线运动link 构件linkage 连杆机构lip rubber seal 唇形橡胶密封liquid spring 液体弹簧load 载荷load balancing mechanism 均衡装置load rating 额定载荷load—deformation curve 载荷load—deformation diagram 载荷loom 织布机lower pair 低副lubricant 润滑剂lubricant film 润滑油膜lubrication 润滑lubrication device 润滑装置Mmachine 机器machine design, mechanical design 机械设计machinery 机械magnetic fluid bearing 磁流体轴承Maltese cross 马耳他十字manipulator 机器人操作器manipulator 机械手mass 质量mass-radius product 质径积matching 拼接mathematic model 数学模型matrix 矩阵maximum difference work between plusand minus work 最大盈亏功mean diameter 中径mean screw diameter 平均中径mechanical advantage 机械利益mechanical behavior 机械特性mechanical creation design, MCD 机械创新设计mechanical efficiency 机械效率mechanical speed governors 机械调速mechanical stepless speed changes 机械无级变速mechanical system 机械系统mechanical system design, MSD 机械系统设计mechanical-electrical integration systemdesign 机电一体化系统设计mechanism 机构mechanism 机构学mechanism with flexible elements 挠性机构membership 隶属度metric gears 公制齿轮mid-plane 中间平面milled helicoids worm 锥面包络圆柱蜗杆minimum radius 最小向径minimum teeth number 最少齿数minor diameter 小径—7—modern machine design 机械的现代设计modification coefficient 变位系数modified gear 变位齿轮modified sine acceleration motion 修正正弦加速度运动规律modified trapezoidal acceleration motion 修正梯形加速度运动规律modular design, MD 模块化设计modular system 模块式传动系统modulation, regulation 调节module 模数moment 力矩moment of couple 力偶矩moment of flywheel 飞轮矩moment of inertia ,shaking moment 惯性力矩moment of torque 扭矩morphology box 模幅箱moving link 运动构件multi-diameter shaft 阶梯轴multi-row bearing 多列轴承Nneedle roller 滚针needle roller bearing 滚针轴承negetive allowarance 负公差nominal diameter 公称直径nominal stress 名义应力、公称应力Nomogram 诺模图non-circular gear 非圆齿轮non-contact seal 非接触式密封nonstandard gear 非标准齿轮normal circular pitch 法面齿距normal force 法向力normal load 垂直载荷、法向载荷normal module 法面模数normal parameters 法面参数normal pitch 法向齿距normal plane 法面normal pressure angle 法面压力角normal stress 正应力、法向应力normal tooth profile 法向齿廓number of threads 蜗杆头数number of waves 波数numerator 分子OO ring seal O 形密封圈密封objective function 目标函数offset 偏置式offset circle 偏距圆offset distance 偏offset knife-edge follower 偏置尖底从动件offset roller follower 偏置滚子从动件offset slider-crank mechanism 偏置曲柄滑块机构oil bearing 含油轴承oil bottle 油杯oil can 油壶oil consumption 耗油量oil consumption factor 耗油量系数oily ditch seal 油沟密封Oldham coupling 双转块机构on-net design, OND 网上设计open chain mechanism 开链机构open kinematic chain 开式链open-belt drive 开口传动operation control device 操纵及控制装置operation mechanism 工作机构optimal design 优化设计ordinary gear train, gear train with fixedaxes 定轴轮系ordinate 纵坐标original mechanism 原始机构oscillating bar 摆杆oscillating follower 摆动从动件oscillating guide-bar mechanism 摆动导杆机构other mechanism in common use 其他常用机构outer ring 外圈output link 输出构件output mechanism 输出机构output shaft 输出轴output torque 输出力矩output work 输出功overlap contact ratio 纵向重合度Ppacker 打包机paired mounting 成对安装parabolic motion 抛物线运动parabolic motion, constant accelerationand deceleration motion 等加等减速运动规律parallel combined mechanism 并联组合机构parallel helical gears 平面轴斜齿轮parallel key 普通平键parallel mechanism 并联机构parameterization design, PD 参数化设计partial balance of shaking force 惯性力部分平衡passive degree of freedom 局部自由度—8—path generation 轨迹生成path generator 轨迹发生器path of action 啮合轨迹pawl 棘爪pedal 踏板periodic speed fluctuation 周期性速度波动phase angle of unbalance 不平衡相位pin 销pinion 小齿轮pinion and rack 齿轮齿条机构pinion cutter, pinion-shaped shaper cutter 齿轮插刀pinion unit 齿轮传动系pitch 周节pitch circle 节圆pitch cone 节圆锥pitch cone angle 节圆锥角pitch curve 理论廓线pitch curve 凸轮理论廓线pitch diameter 节圆直径pitch line 节线pitch point 节点pitting (疲劳)点蚀planar cam 平面凸轮planar cam mechanism 平面凸轮机构planar kinematic pair 平面运动副planar linkage 平面连杆机构planar mechanism 平面机构planar pair, flat pair 平面副planet gear 行星轮planetary differential 封闭差动轮系planetary drive with small teeth difference 少齿差行星传动planetary gear train 行星轮系planetary speed changing devices 行星轮变速装置planetary transmission 行星齿轮装置plasticine 橡皮泥pneumatic mechanism 气动机构pointing, cusp 尖点polar coordinate manipulator 球坐标操作器poly V-belt 多楔带polynomial motion 多项式运动规律pose , position and orientation 位姿positive allowrance 正公差positive-drive (or form-closed) cam mechanism 形封闭凸轮机构potted component 密封元件powder metallurgy 粉末合金power 功率power screw 螺旋传动power spring 涡圈形盘簧preload 预紧力pressure 压力pressure angle 压力角pressure angle of base circle 基圆压力角pressure angle of involute 渐开线压力角prime mover 原动机primer mover 原动机prismatic joint 移动关节prismatic pair, sliding pair 移动副productive resistance 生产阻力pulsating stepless speed changes 脉动无级变速punch 冲床Qquadrant 象限quick-return characteristics 急回特性quick-return mechanism 急回机构quick-return motion 急回运动Rraceway 滚道rack 齿条rack cutter, rack-shaped shaper cutter齿条插刀rack gear 齿条传动radial (or in-line ) roller follower 对心滚子从动件radial (or in-line ) translating follower对心直动从动件radial bearing 向心轴承radial contact bearing 径向接触轴承radial direction 径向radial internal clearance 径向游隙radial load 径向载荷radial load factor 径向载荷系数radial plane 径向平面radial reciprocating follower 对心移动从动件radius of addendum 齿顶圆半径radius of base circle 基圆半径radius of curvature 曲率半径radius of roller 滚子半径rating life 额定寿命reciprocating follower 移动从动件reciprocating motion 往复移动reciprocating seal 往复式密封reduction gear 减速齿轮、减速装置reduction ratio 减速比redundant (or passive) constraint 虚约束redundant degree of freedom 冗余自由—9—度reference circle, standard (cutting) pitch circle 分度圆reference cone, standard pitch cone 分度圆锥reference line, standard pitch line 分度线regulator, governor 调速器relative gap 相对间隙relative motion 相对运动relative velocity 相对速度reliability 可靠性reliability design, RD 可靠性设计repeated fluctuating load 交变载荷repeated stress 交变应力residual stress 残余应力resistance 阻抗力resultant bending moment 合成弯矩resultant force 合力resultant force 总反力resultant moment of force 合力矩resultant moment of inertia 惯性主矩resultant vector of inertia 惯性主失return 回程revolute (turning) pair 转动副revolute joint 转动关节revolving shaft 转轴Reynolds‘s equation 雷诺方程right triangle 直角三角形rigid bearing 刚性轴承rigid circular spline 刚轮rigid coupling 刚性联轴器rigid impulse (shock) 刚性冲击rigid rotor 刚性转子ring gear 内齿圈rise 升程rise 推程rivet 铆钉robot 机器人robotics 机器人学robust design 稳健设计rocker 摇杆roller 滚子roller bearing 滚子轴承roller chain 滚子链roller clutch 滚柱式单向超越离合器roller follower 滚子从动件rolling bearing 滚动轴承rolling bearing identification code 滚动轴承代号rolling element 滚动体rotary motion 旋转运动rotating seal 旋转式密封rotor 转子rotor with several masses 多质量转子round belt 圆带round belt drive 圆带传动rubber-cushioned sleeve bearing coupling 弹性套柱销联轴器running torque 旋转力矩Ssafe load 安全载荷safety factor, factor of safety 安全系数scale 比例尺scoring 胶合screw 螺杆screw efficiency 螺纹效率screw mechanism 螺旋机构screw nut 螺母screws 螺钉seal 密封seal belt 密封带seal gum 密封胶sealing arrangement 密封装置section 截面self-aligning ball bearing 调心球轴承self-aligning bearing 调心轴承self-aligning roller bearing 调心滚子轴承self-locking 自锁series combined mechanism 串联式组合机构serration spline 三角形花键shaft 轴shaft angle 轴角shaft collar 轴环shaft end ring 轴端挡圈shaft shoulder 轴肩shaking couple 振动力矩shaper 牛头刨床shockproof device 防振装置shocks, shock-absorber 缓冲装置shortening coefficient of addendum 齿顶高缩短系数silent chain 齿形链、无声链simple harmonic motion 简谐运动sine generator, scotch yoke 正弦机构single row bearing 单列轴承single universal joint 单万向联轴节single-direction thrust bearing 单向推力轴承singular position 奇异位置six-bar linkage 六杆机构slack-side 松边sleeve 套筒slider 滑块slider-crank (or crank-slider) mechanism—10—曲柄滑块机构sliding bearing 滑动轴承sliding ratio 滑动率slipping 打滑solid lubricant 固体润滑剂spacewidth 齿槽宽spatial cam 空间凸轮机构spatial kinematic chain 空间运动链spatial kinematic pair 空间运动副spatial linkage 空间连杆机构spatial mechanism 空间机构special kinematic chain 特殊运动链specific heat capacity 比热容speed change 变速speed control system 调速系统speed fluctuation 速度波动speed governing 调速speed reducer 减速器speed-changing gear boxes 齿轮变速箱sphere-pin pair 球销副spheric pair 球面副spherical involute 球面渐开线spherical motion 球面运动spindle 心轴spiral bevel gear 曲齿锥齿轮spiral seal 螺旋密封spline 花键spontaneous ignition 燃点spring constant 弹簧[刚度]系数sprocket, sprocket-wheel, sprocket gear, chain wheel 链轮spur gear 直齿圆柱齿轮square threaded form 矩形螺纹square-jaw positive-contact clutch 矩形牙嵌式离合器stack mounting 组合安装standard addendum 标准齿顶高standard gear 标准齿轮standard spur gear 标准直齿轮starting period 起动阶段starting torque 启动力矩static balance 静平衡static equivalent axial load 轴向当量静载荷static equivalent radial load 径向当量静载荷static force 静力static load 静载荷static seal 静密封steady motion period 稳定运转阶段step pulley 塔轮stepless speed changes devices 无级变速装置stiffiness; rigidity; severity; toughness 刚度stiffness coefficient 刚度系数stopping phase 停车阶段straight bevel gear 直齿锥齿轮straight shaft 直轴straight sided normal worm 法向直廓蜗杆stress amplitude 应力幅stress concentration 应力集中stress diagram 应力图stress-strain diagram 应力structural design 结构设计structure 结构studs 双头螺柱sub-mechanism 子机构subroutine 子程序sun gear 太阳轮sunk key 嵌入键superficial mass factor 表面质量系数surface coefficient of heat transfer 表面传热系数surface of action 啮合曲面surface roughness 表面粗糙度swiveling speed, rotating speed 转速symmetry circulating stress 对称循环应力synchronous belt 同步带synchronous belt drive 同步带传动synthesis of mechanism 机构综合system of normal addendum 正常齿高制Ttangent mechanism 正切机构taper key 斜键、钩头楔键tapered roller 圆锥滚子tapered roller bearing 圆锥滚子轴承technical and economic evaluation 技术经济评价technique process 技术过程technique system 技术系统technological design 工艺设计tension 张紧力tension pulley 张紧轮theoretical line of action 理论啮合线theory of constitution 组成原理theory of machines and mechanisms 机械原理thickness on pitch circle 节圆齿厚third gear 三档thread (of a screw) 螺纹thread pitch 螺距three-dimensional cam 三维凸轮thrust ball bearing 推力球轴承thrust bearing 推力轴承tight-side 紧边toggle mechanism 肘形机构tool withdrawal groove 退刀槽tooth curve 齿廓曲线tooth number 齿数tooth profile 齿廓tooth ratchet mechanism 齿式棘轮机构tooth space 齿槽tooth thickness 齿厚toroid helicoids worm 环面蜗杆torsion stress 扭转应力total contact ratio 总重合度transmission angle 传动角transmission ratio, speed ratio 传动比transmission shaft 传动轴transverse circular pitch 端面齿距transverse contact ratio 端面重合度transverse module 端面模数transverse parameters 端面参数transverse plane 端面transverse pressure angle 端面压力角transverse tooth profile 端面齿廓tribology design, TD 摩擦学设计two-dimensional cam 两维凸轮type selection 选型Uundercutting 根切undercutting 过度切割undercutting 运动失真uniform motion, constant velocity motion 等速运动规律unit vector 单位矢量useful resistance 有益阻力useless resistance 有害阻力VV belt V带V thread screw 三角形螺纹tight-up V belt 联组V 带narrow V belt 窄V 带variable voltage control 调压调速vector 矢量velocity 速度velocity diagram 速度曲线vibration 振动vice 台钳、虎钳virtual reality 虚拟现实virtual reality design, VRD 虚拟现实设计virtual reality technology, VRT 虚拟现实技术viscosity 能量指示图Wwave generator 波发生器wear resistance 耐磨性wedge cam 移动凸轮weight sets 权重集weighting efficient 加权系数whitworth mechanism 转动导杆机构whole depth 全齿高width of flat-face 从动件平底宽度width series 宽度系列wire soft shaft 钢丝软轴woodruff key 半圆键work 功working cycle diagram 工作循环图working pressure angle, angle of action 啮合角working space 工作空间working stress 工作应力worm 蜗杆worm and worm gear 蜗杆蜗轮机构worm cam interval mechanism 蜗杆形凸轮步进机构worm gear 蜗轮worm gearing 蜗杆传动机构wrench 扳手wrist 腕部Zzone of action 啮合区域。
机械类外文文献及翻译
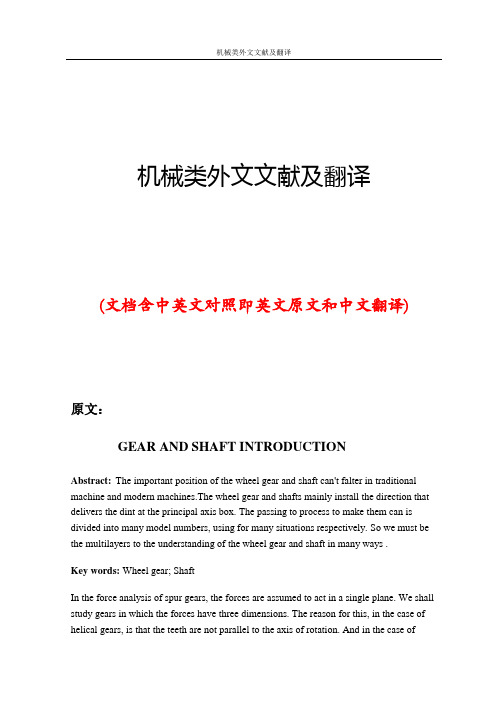
机械类外文文献及翻译(文档含中英文对照即英文原文和中文翻译)原文:GEAR AND SHAFT INTRODUCTIONAbstract:The important position of the wheel gear and shaft can't falter in traditional machine and modern machines.The wheel gear and shafts mainly install the direction that delivers the dint at the principal axis box. The passing to process to make them can is divided into many model numbers, using for many situations respectively. So we must be the multilayers to the understanding of the wheel gear and shaft in many ways .Key words: Wheel gear; ShaftIn the force analysis of spur gears, the forces are assumed to act in a single plane. We shall study gears in which the forces have three dimensions. The reason for this, in the case of helical gears, is that the teeth are not parallel to the axis of rotation. And in the case ofbevel gears, the rotational axes are not parallel to each other. There are also other reasons, as we shall learn.Helical gears are used to transmit motion between parallel shafts. The helix angle is the same on each gear, but one gear must have a right-hand helix and the other a left-hand helix. The shape of the tooth is an involute helicoid. If a piece of paper cut in the shape of a parallelogram is wrapped around a cylinder, the angular edge of the paper becomes a helix. If we unwind this paper, each point on the angular edge generates an involute curve. The surface obtained when every point on the edge generates an involute is called an involute helicoid.The initial contact of spur-gear teeth is a line extending all the way across the face of the tooth. The initial contact of helical gear teeth is a point, which changes into a line as the teeth come into more engagement. In spur gears the line of contact is parallel to the axis of the rotation; in helical gears, the line is diagonal across the face of the tooth. It is this gradual of the teeth and the smooth transfer of load from one tooth to another, which give helical gears the ability to transmit heavy loads at high speeds. Helical gears subject the shaft bearings to both radial and thrust loads. When the thrust loads become high or are objectionable for other reasons, it may be desirable to use double helical gears. A double helical gear (herringbone) is equivalent to two helical gears of opposite hand, mounted side by side on the same shaft. They develop opposite thrust reactions and thus cancel out the thrust load. When two or more single helical gears are mounted on the same shaft, the hand of the gears should be selected so as to produce the minimum thrust load.Crossed-helical, or spiral, gears are those in which the shaft centerlines are neither parallel nor intersecting. The teeth of crossed-helical fears have point contact with each other, which changes to line contact as the gears wear in. For this reason they will carry out very small loads and are mainly for instrumental applications, and are definitely not recommended for use in the transmission of power. There is on difference between a crossed heli : cal gear and a helical gear until they are mounted in mesh with each other. They are manufactured in the same way. A pair of meshed crossed helical gears usually have the same hand; that is ,a right-hand driver goes with a right-hand driven. In the design of crossed-helical gears, the minimum sliding velocity is obtained when the helix angle areequal. However, when the helix angle are not equal, the gear with the larger helix angle should be used as the driver if both gears have the same hand.Worm gears are similar to crossed helical gears. The pinion or worm has a small number of teeth, usually one to four, and since they completely wrap around the pitch cylinder they are called threads. Its mating gear is called a worm gear, which is not a true helical gear. A worm and worm gear are used to provide a high angular-velocity reduction between nonintersecting shafts which are usually at right angle. The worm gear is not a helical gear because its face is made concave to fit the curvature of the worm in order to provide line contact instead of point contact. However, a disadvantage of worm gearing is the high sliding velocities across the teeth, the same as with crossed helical gears.Worm gearing are either single or double enveloping. A single-enveloping gearing is onein which the gear wraps around or partially encloses the worm.. A gearing in which each element partially encloses the other is, of course, a double-enveloping worm gearing. The important difference between the two is that area contact exists between the teeth of double-enveloping gears while only line contact between those of single-enveloping gears. The worm and worm gear of a set have the same hand of helix as for crossed helical gears, but the helix angles are usually quite different. The helix angle on the worm is generally quite large, and that on the gear very small. Because of this, it is usual to specify the lead angle on the worm, which is the complement of the worm helix angle, and the helix angle on the gear; the two angles are equal for a 0-deg. Shaft angle.When gears are to be used to transmit motion between intersecting shaft, some of bevel gear is required. Although bevel gear are usually made for a shaft angle of 0 deg. They may be produced for almost any shaft angle. The teeth may be cast, milled, or generated. Only the generated teeth may be classed as accurate. In a typical bevel gear mounting, one of the gear is often mounted outboard of the bearing. This means that shaft deflection can be more pronounced and have a greater effect on the contact of teeth. Another difficulty, which occurs in predicting the stress in bevel-gear teeth, is the fact the teeth are tapered.Straight bevel gears are easy to design and simple to manufacture and give very good results in service if they are mounted accurately and positively. As in the case of squr gears, however, they become noisy at higher values of the pitch-line velocity. In these cases it is often go : od design practice to go to the spiral bevel gear, which is the bevel counterpart of thehelical gear. As in the case of helical gears, spiral bevel gears give a much smoother tooth action than straight bevel gears, and hence are useful where high speed are encountered.It is frequently desirable, as in the case of automotive differential applications, to have gearing similar to bevel gears but with the shaft offset. Such gears are called hypoid gears because their pitch surfaces are hyperboloids of revolution. The tooth action between such gears is a combination of rolling and sliding along a straight line and has much in common with that of worm gears.A shaft is a rotating or stationary member, usually of circular cross section, having mounted upon it such elementsas gears, pulleys, flywheels, cranks, sprockets, and other power-transmission elements. Shaft may be subjected to bending, tension, compression, or torsional loads, acting singly or in combination with one another. When they are combined, one may expect to find both static and fatigue strength to be important design considerations, since a single shaft may be subjected to static stresses, completely reversed, and repeated stresses, all acting at the same time.The word “shaft” covers numerous v ariations, such as axles and spindles. Anaxle is a shaft, wither stationary or rotating, nor subjected to torsion load. A shirt rotating shaft is often called a spindle.When either the lateral or the torsional deflection of a shaft must be held to close limits, the shaft must be sized on the basis of deflection before analyzing the stresses. The reason for this is that, if the shaft is made stiff enough so that the deflection is not too large, it is probable that the resulting stresses will be safe. But by no means should the designer assume that they are safe; it is almost always necessary to calculate them so that he knows they are within acceptable limits. Whenever possible, the power-transmission elements, such as gears or pullets, should be located close to the supporting bearings, This reduces the bending moment, and hence the deflection and bending stress.Although the von Mises-Hencky-Goodman method is difficult to use in design of shaft, it probably comes closest to predicting actual failure. Thus it is a good way of checking a shaft that has already been designed or of discovering why a particular shaft has failed in service. Furthermore, there are a considerable number of shaft-design problems in which the dimension are pretty well limited by other considerations, such as rigidity, and it is only necessary for the designer to discover something about the fillet sizes, heat-treatment,and surface finish and whether or not shot peening is necessary in order to achieve the required life and reliability.Because of the similarity of their functions, clutches and brakes are treated together. In a simplified dynamic representation of a friction clutch, or brake, two in : ertias I and I traveling at the respective angular velocities W and W, one of which may be zero in the case of brake, are to be brought to the same speed by engaging the clutch or brake. Slippage occurs because the two elements are running at different speeds and energy is dissipated during actuation, resulting in a temperature rise. In analyzing the performance of these devices we shall be interested in the actuating force, the torque transmitted, the energy loss and the temperature rise. The torque transmitted is related to the actuating force, the coefficient of friction, and the geometry of the clutch or brake. This is problem in static, which will have to be studied separately for eath geometric configuration. However, temperature rise is related to energy loss and can be studied without regard to the type of brake or clutch because the geometry of interest is the heat-dissipating surfaces. The various types of clutches and brakes may be classified as fllows:. Rim type with internally expanding shoes. Rim type with externally contracting shoes. Band type. Disk or axial type. Cone type. Miscellaneous typeThe analysis of all type of friction clutches and brakes use the same general procedure. The following step are necessary:. Assume or determine the distribution of pressure on the frictional surfaces.. Find a relation between the maximum pressure and the pressure at any point. Apply the condition of statical equilibrium to find (a) the actuating force, (b) the torque, and (c) the support reactions.Miscellaneous clutches include several types, such as the positive-contact clutches, overload-release clutches, overrunning clutches, magnetic fluid clutches, and others.A positive-contact clutch consists of a shift lever and two jaws. The greatest differences between the various types of positive clutches are concerned with the design of the jaws. To provide a longer period of time for shift action during engagement, the jaws may be ratchet-shaped, or gear-tooth-shaped. Sometimes a great many teeth or jaws are used, and they may be cut either circumferentially, so that they engage by cylindrical mating, or on the faces of the mating elements.Although positive clutches are not used to the extent of the frictional-contact type, they do have important applications where synchronous operation is required.Devices such as linear drives or motor-operated screw drivers must run to definite limit and then come to a stop. An overload-release type of clutch is required for these applications. These clutches are usually spring-loaded so as to release at a predetermined toque. The clicking sound which is heard when the overload point is reached is considered to be a desirable signal.An overrunning clutch or coupling permits the driven member of a machine to “freewheel” or “overrun” bec ause the driver is stopped or because another source of power increase the speed of the driven. This : type of clutch usually uses rollers or balls mounted between an outer sleeve and an inner member having flats machined around the periphery. Driving action is obtained by wedging the rollers between the sleeve and the flats. The clutch is therefore equivalent to a pawl and ratchet with an infinite number of teeth.Magnetic fluid clutch or brake is a relatively new development which has two parallel magnetic plates. Between these plates is a lubricated magnetic powder mixture. An electromagnetic coil is inserted somewhere in the magnetic circuit. By varying the excitation to this coil, the shearing strength of the magnetic fluid mixture may be accurately controlled. Thus any condition from a full slip to a frozen lockup may be obtained.齿轮和轴的介绍摘要:在传统机械和现代机械中齿轮和轴的重要地位是不可动摇的。
外文翻译:探讨汽车轮胎滚动阻力以及测试技术
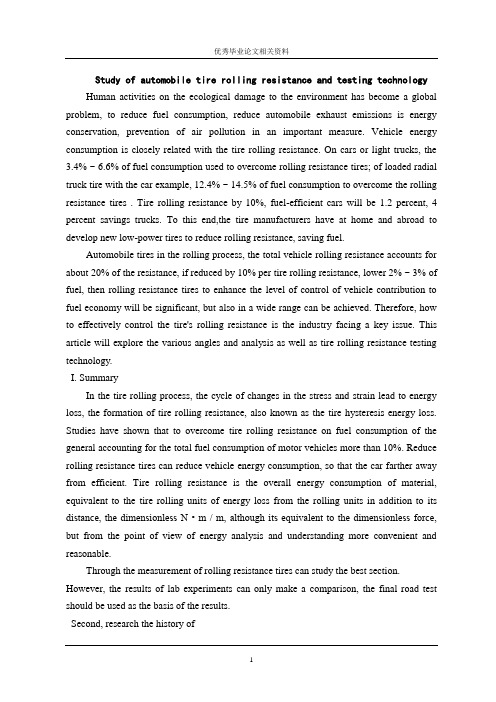
Study of automobile tire rolling resistance and testing technology Human activities on the ecological damage to the environment has become a global problem, to reduce fuel consumption, reduce automobile exhaust emissions is energy conservation, prevention of air pollution in an important measure. Vehicle energy consumption is closely related with the tire rolling resistance. On cars or light trucks, the 3.4% ~ 6.6% of fuel consumption used to overcome rolling resistance tires; of loaded radial truck tire with the car example, 12.4% ~ 14.5% of fuel consumption to overcome the rolling resistance tires . Tire rolling resistance by 10%, fuel-efficient cars will be 1.2 percent, 4 percent savings trucks. To this end,the tire manufacturers have at home and abroad to develop new low-power tires to reduce rolling resistance, saving fuel.Automobile tires in the rolling process, the total vehicle rolling resistance accounts for about 20% of the resistance, if reduced by 10% per tire rolling resistance, lower 2% ~ 3% of fuel, then rolling resistance tires to enhance the level of control of vehicle contribution to fuel economy will be significant, but also in a wide range can be achieved. Therefore, how to effectively control the tire's rolling resistance is the industry facing a key issue. This article will explore the various angles and analysis as well as tire rolling resistance testing technology.I. SummaryIn the tire rolling process, the cycle of changes in the stress and strain lead to energy loss, the formation of tire rolling resistance, also known as the tire hysteresis energy loss. Studies have shown that to overcome tire rolling resistance on fuel consumption of the general accounting for the total fuel consumption of motor vehicles more than 10%. Reduce rolling resistance tires can reduce vehicle energy consumption, so that the car farther away from efficient. Tire rolling resistance is the overall energy consumption of material, equivalent to the tire rolling units of energy loss from the rolling units in addition to its distance, the dimensionless N • m / m, although its equivalent to the dimensionless force, but from the point of view of energy analysis and understanding more convenient and reasonable.Through the measurement of rolling resistance tires can study the best section. However, the results of lab experiments can only make a comparison, the final road test should be used as the basis of the results.Second, research the history ofAs early as age 60 in the 20th century, Beijing Research and Design Institute of Rubber Industry in turn on the drum machine and measured the wire cotton tire cord tire power loss, also measured on the road when the vehicle speed steady traction resistance. At that time, due to restrictions on the use of equipment, the pilot is in its early exploratory phase of long-term. Since the mid-80s, with the accelerated development of China's tire needs, a small number of tire manufacturers from the United States, Japan and Germany with the introduction of the rolling resistance of the switch position test tire drum testing machine, combined with the development of a new type of radial tire and the analysis of foreign samples a number of tire rolling resistance tires test.Inspection. 70s from the 20th century in the United States, Japan and Europe, such as the economically developed countries, in order to solve energy shortages and the deterioration of environmental quality issues and the rolling resistance tires for a large number of experiments and research work. At the same time, tire rolling resistance testing technologies have also made remarkable progress. Beginning in 2004, the U.S. National Research Center on the control of rolling resistance tires to start a new round of extensive research. In 2007, the European Rubber Manufacturers Association also made to the EU to control the level of rolling resistance of the recommendations. Therefore, China will also face the control of rolling resistance.Third, testing technologyAt present, China has established a laboratory test-based, supplemented by the direction of the outdoor experiment. Steady-state conditions in the interior that is a constant load and speed, the tires when driving to reach thermal equilibrium Tire rolling resistance measurement method of standardization has been achieved.Preliminary results show that the simulation of the city of tire rolling resistance condition than under the conditions of steady-state rolling resistance by 26% ~ 47% of the difference between the two aroused people's interest in the emergence of a simulation of various operating conditions of automobile tires non-steady-state test. But so far did not see a unified standard test methods or test protocols. Carried out in the outdoor tire rolling resistance test methods are mainly trailer Act, taxiways and three kinds of torque method, in which a wider application of the trailer Act.Fourth, laboratory equipmentLaboratory test equipment, through decades of effort, has appeared in various types of tire rolling resistance testing machine. Their roads in accordance with the form of simulation points, and to have a steel drum two broad categories. Strip-type test machine to simulate the continuous flat surface, is very expensive test equipment tires. At present, it is the most widely to drum testing machine, in particular, a diameter of 1.7 meters to the drum. These test equipment measuring tire rolling resistance by way of points, and measuring method, torque law, power law and reduce the rate of four kinds of law. The use of existing equipment to load and torque of law are most welcome. In the past two decades, the accuracy of test equipment greatly enhanced to reduce the double measurement error, and has formed a set of test data to ensure the repeatability of the equipment necessary for accuracy. Has the full realization of China's current industrial production equipment is Jiurong Tianjin rolling resistance testing machine, is divided into car and truck tire with two types of tires, and its accuracy in line with the requirements of ISO. As the outdoor test line tire rolling resistance of non-standard test, the test equipment they use is not changed. Association for the Study of the British automobile industry with the use of the pilot housing trailers, all kinds of tires for air resistance in the same test under the conditions created.V. Test Methods1. Indoor and outdoor test testIndoor and outdoor test test test is based on the distinction between the two types of tire place test method. Indoor test of tire rolling resistance testing machine were conducted, and its experimental conditions, although the Department of simulated conditions of use but can be under control, so that good reproducibility of experimental data. Outdoor test rolling resistance tires are used on test vehicles on the road completed, it is true although the experimental conditions, but susceptible to external factors, pilot error, and therefore tire rolling resistance test to test the main indoor and outdoor test Des.2. Steady-state conditions and non-steady-state conditionsSteady-state conditions in the constant refers to the tire load and speed, and traveling in the tire to reach thermal equilibrium when measuring rolling resistance; non-steady-state conditions, it means the tire change with time in the load and speed, and tire temperature in the process of moving measuring rolling resistance. Of course, the tires in the car on the non-steady-state condition is varied. To the total points, tire condition of the car has the city,the suburbs of the car and coach on. However, a breakdown, and another empty, heavy vehicles, drive, driven, acceleration, deceleration, taxiways, brake, turn, etc. and combinations there of. Typical working condition of the tires as the standard test of non-steady-state conditions, needs to be done to investigate and test a large number of research work. So whether it is the latest ISO 18164 or the existing SAEJ 1269, they were under steady-state conditions. In addition, SAEJ 2452 slowdown is a complex experiment, the experimental conditions than under the uniform steady-state movement is much more complicated, but it is not completely under non-steady-state experiment. As can accurately predict tire rolling resistance is uniform or slowdown, more tests need to be verified, such comparison tests being investigated. However, the tire manufacturer's tire rolling resistance testing machine mostly for the use of steady-state conditions, if used for non-steady-state conditions by the test needs Plus many new features, testing may be a substantial increase in cost.First of all, to deal with the choice of tires to test full consideration, such as the representativeness of the sample, the tire size, type, rated speed, the original production equipment and the type of wheel rim, as well as the technological level of producers and industry status.Secondly, the performance evaluation of the establishment of test methods. Is not any test method can be used to evaluate the performance level, especially the study of test methods, and therefore take into account the actual tire, the combination of existing technology and the means test, set up in line with the experimental detection conditions.Third, laboratory equipment to ensure precision and accuracy of the equipment of the establishment of standards to ensure that test reproducibility and repeatability, such as samples of the same specifications of the rolling resistance tires are consistent and repeatable, with the control tire for the different experiments comparison.Fourth, the establishment of quality control procedures to ensure that the different rolling resistance testing machine test results are consistent and repeatable, the data in these experiments should also include information such as equipment.Fifth, repeat the same tire test, test results are consistent and repeatable.Sixth, tire prices and the relationship between the dynamic resistance.Seventh, most importantly, in the protection of national industries and safeguard the environment and conserve fuel, to resist the flow of low-quality tires to enter the market, the need for serious thinking.A lot of tests in measuring very small load rolling resistance tire rolling resistance is measured the basic characteristics of the tire positioning accuracy, therefore, control precision and accuracy requirements and other equipment is key. According to many years of experience confirm the accuracy of test equipment requirements is necessary, otherwise the test data can not be guaranteed to reach the standards of repeatability and comparability.Lower rolling resistance tires can significantly save energy and protect the environment, with considerable economic and social benefits. Under the conditions of typical use of the tire rolling resistance and fuel consumption the relationship between the steady-state conditions with non-steady-state conditions compared with the torque method, power law and measured by the speed difference in rolling resistance tires will be The next step of our research objectives.Should be established and planned research projects, and used to determine the appropriate control of the rolling resistance or grade; from different points of view to promote and strengthen the grasp of the concept of rolling resistance and applications.探讨汽车轮胎滚动阻力以及测试技术人类活动对生态环境的破坏已成为全球性问题,减少燃料消耗、降低汽车尾气排放量是节约能源、防止大气污染的重要措施。
机械设计专业的毕业设计(英文版)

Mechanical EngineeringIntroduction to Mechanical EngineeringMechanical engineering is the branch of engineering that deals with machines and the production of power. It is particularly concerned with forces and motion.History of Mechanical EngineeringThe invention of the steam engine in the latter part of the 18th century, providing a key source of power for the Industrial Revolution, gave an enormous impetus to the development of machinery of all types. As a result a new major classification of engineering, separate from civil engineering and dealing with tools and machines, developed, receiving formal recognition in 1847 in the founding of the Institution of Mechanical Engineers in Birmingham, England.Mechanical engineering has evolved from the practice by the mechanic of an art based largely on trial and error to the application by the professional engineer of the scientific method in research, design, and production.The demand for increased efficiency, in the widest sense, is continually raising the quality of work expected from a mechanical engineer and requiring of him a higher degree of education and training. Not only must machines run more economically but capital Costs also must be minimized.Fields of Mechanical EngineeringDevelopment of machines for the production of goods the high material standard of living in the developed countries owes much to the machinery made possible by mechanical engineering. The mechanical engineer continually invents machines to produce goods and develops machine tools of increasing accuracy and complexity to build the machines.The principal lines of development of machinery have been an increase in the speed of operation to obtain high rates of production, improvement in accuracy to obtain quality and economy in the product, and minimization of operating costs. These three requirements have led to the evolution of complex control systems.The most successful production machinery is that in which the mechanical design of the machine is closely integrated with the control system, whether the latter is mechanical orelectrical in nature. A modern transfer line (conveyor) for the manufacture of automobile engines is a good example of the mechanization of a complex series of manufacturing processes. Developments are in hand to automate production machinery further, using computers to store and process the vast amount of data required for manufacturing a variety of components with a small number of versatile machine tools. One aim is a completely automated machine shop for batch production, operating on a three shift basis but attended by a staff for only one shift per day.Development of machines for the production of power Production machinery presuppose an ample supply of power. The steam engine provided the first practical means of generating power from heat to augment the old sources of power from muscle, wind, and water One of the first challenges to the new profession of mechanical engineering was to increase thermal efficiencies and power; this was done principally by the development of the steam turbine and associated large steam boilers. The 20th century has witnessed a continued rapid growth in the power output of turbines for driving electric generators, together with a steady increase in thermal efficiency and reduction in capital cost per kilowatt of large power stations. Finally, mechanical engineers acquired the resource of nuclear energy, whose application has demanded an exceptional standard of reliability and safety involving the solution of entirely new problems- The control systems of large power plank and complete nuclear power stations have become highly sophisticated networks of electronic, fluidic. Electric, hydraulic, and mechanical components, ail of these involving me province of the mechanical engineer.The mechanical engineer is also responsible for the much smaller internal combustion engines, both reciprocating (gasoline and diesel) and rotary (gas-turbine and Wankel) engines, with their widespread transport applications- In the transportation field generally, in air and space as well as on land and sea. the mechanical engineer has created the equipment and the power plant, collaborating increasingly with the electrical engineer, especially in the development of suitable control systems.Development of military weapons The skills applied to war by the mechanical engineer are similar to those required in civilian applications, though the purpose is to enhance destructive power rather than to raise creative efficiency. The demands of war have channeled huge resources into technical fields, however, and led to developments that have profound benefits in peace. Jet aircraft and nuclear reactors are notable examples.Biaengineering Bioengineering is a relatively new and distinct field of mechanical engineering that includes the provision of machines to replace or augment the functions of the human body and of equipment for use in medical treatment. Artificial limbs have been developed incorporating such lifelike functions as powered motion and touch feedback. Development is rapid in the direction of artificial spare-part surgery. Sophisticated heart-lung machines and similar equipment permit operations of increasing complexity and permit the vital functions in seriously injured or diseased patients to be maintained.Environmental control Some of the earliest efforts of mechanical engineers were aimed at controlling man's environment by pumping water to drain or irrigate land and by ventilating mines. The ubiquitous refrigerating and air-conditioning plants of the modem age are based on a reversed heat engine, where the supply of power "pumps" heat from the cold region to the warmer exterior.Many of the products of mechanical engineering, together with technological developments in other fields, have side effects on the environment and give rise to noise, the pollution of water and air, and the dereliction of land and scenery. The rate of production, both of goods and power, is rising so rapidly that regeneration by natural forces can no longer keep pace. A rapidly growing field for mechanical engineers and others is environmental control, comprising the development of machines and processes that will produce fewer pollutants and of new equipment and techniques that can reduce or remove the pollution already generated.Functions of Mechanical EngineeringFour functions of the mechanical engineering, common to all the fields mentioned, are cited. The first is the understanding of and dealing with the bases of mechanical science. These include dynamics, concerning the relation between forces and motion, such as in vibration; automatic control; thermodynamics, dealing with the relations among the various forms of heat, energy, and power; fluid flow; heat transfer; lubrication; and properties of materials.Second is the sequence of research, design, and development. This function attempts to bring about the changes necessary to meet present and future needs. Such work requires not only a dear understanding of mechanical science and an ability to analyze a complex system into its basic factors, but also the originality to synthesize and invent.Third is production of products and power, which embraces planning, operation, and maintenance. The goal is to produce the maximum value with the minimum investment and cost while maintaining or enhancing longer term viability and reputation of the enterprise or the institution.Fourth is the coordinating functioning of the mechanical engineering, including management, consulting, and, in some cases, marketing.In all of these functions there is a long continuing trend toward the use of scientific instead of traditional or intuitive methods, an aspect of the ever-growing professionalism of mechanical engineering. Operations research, value engineering, and PABLA (problem analysis by logical approach) are typical titles of such new rationalized approaches. Creativity, however, cannot be rationalized. The ability to take the important and unexpected step that opens up new solutions remains in mechanical engineering, as elsewhere, largely a personal and spontaneous characteristic.The Future of Mechanical EngineeringThe number of mechanical engineers continues to grow as rapidly as ever, while the duration and quality of their training increases. There is a growing: awareness, however, among engineers and in the community at large that the exponential increase in populationand living standards is raising formidable problems in pollution of the environment andthe exhaustion of natural resources; this clearly heightens the need for all of the technical professions to consider the long-term social effects of discoveries and developments. -There will be an increasing demand for mechanical engineering skills to provide for man's needs while reducing to a minimum the consumption of scarce raw materials and maintaining a satisfactory environment.Introduction to DesignThe Meaning of DesignTo design is to formulate a plan for the satisfaction of a human need. The particular need to be satisfied may be quite well defined from the beginning. Here are two examples in which needs are well defined:1. How can we obtain large quantities of power cleanly, safely, and economical/ without using fossil fuels and without damaging the surface of the earth?2. This gear shaft is giving trouble; there have been eight failures in the last six weeks. Do something about it.On the other hand, the statement of a particular need to be satisfied may be so nebulous and ill defined that a considerable amount of thought and effort is necessary in ( order to state it dearly as a problem requiring a solution. Here are two examples.-1. Lots of people are killed in airplane accidents.2. In big cities there are too many automobiles on the streets and highways.This second type of design situation is characterized by the fact that neither the need nor the problem to be solved has been identified. Note, too, that the situation may contain not one problem but many.We can classify design, too. For instance, we speak of:1. Clothing design 7. Bridge design2. Interior design 8. Computer-aided design3. Highway design 9. Heating system design.4. Landscape design 10. Machine design5. Building design 11. Engineering design6. Ship design 12. Process designIn fact, there are an endless number, since we can classify design according to the particular article or product or according to the professional field,In contrast to scientific or mathematical problems, design problems have no unique answers; it is absurd, for example, to request the "correct answer" to a design problem, because there is none. In fact, a "good" answer today may well turn out to be a "poor" answer tomorrow, if there is a growth of knowledge during the period or if there are other structural or societal changes.Almost everyone is Involved with design in one way or another, even in dally living, because problems are posed and situations arise which must be solved. A design problem is not a hypothetical problem at all. Design has an authentic purpose—the creation of an end result by taking definite action, or the creation of something having physical reality. In engineering, the word design conveys different meanings to different persons. Some think of a designer as one who employs the drawing board to draft the details of a gear, clutch, or other machine member. Others think of design as the creation of a complex system, such as a communications network. In some areas of engineering the word design has been replaced by other terms such as systems engineering or applied decision theory. But no matter what words are used to describe the design function, in engineering it is still the process in which scientific principles and the tools of engineering—mathematics, computers, graphics, and English—are used to produce a plan which, when carried out, will satisfy a human need.Mechanical Engineering DesignMechanical design means die design of things and systems of a mechanical nature machines, products, structures, devices, and instruments. For the most part, mechanical design utilizes mathematics, the materials sciences, and the engineering-mechanics sciences.Mechanical engineering design includes all mechanical design, but it is a broader study, because it includes all the disciplines of mechanical engineering, such as the thermal and fluids sciences, too. Aside from the fundamental sciences that are required, the first studies in mechanical engineering design are in mechanical design.The Phases of DesignThe complete process, from start to finish. The process W begins with a recognition of a need and a decision to do something about it. After much iteration, the process ends with the presentation of the plans for satisfying the need.Design ConsiderationsSometimes the strength required of an element in a system is an important factor in the determination of the geometry and the dimensions of the element. In such a situation we say that strength is an important design consideration. When we use the expression design consideration, we are referring to some characteristic which influences the design of the element or, perhaps, the entire system. Usually quite a number of such characteristics must be considered in a given design situation. Many of the important ones are as follows:1. Strength2. Reliability3. Thermal properties4. Corrosion5. Wear6. Friction7. Processing8. Utility9. Cost10. Safety11. Weight12. Life13. Noise14. Styling15. Shape16. Size17. Flexibility18. Control19. Stiffness20. Surface finish21. Lubrication22. Maintenance23. Volume24. LiabilitySome of these have to do directly with the dimensions, the material, the processing, and the joining of the elements of the system. Other considerations affect the configuration of the total system.To keep the correct perspective, however, it should be observed that in many design situations the important design considerations are such that no calculations or experiments are necessary in order to define an element or system. Students, especially, are often confounded when they run into situations in which it is virtually impossible to make a single calculation and yet an important design decision must be made. These are not extraordinary occurrences at all; they happen every day. Suppose that it is desirable from a sales standpoint—for example, in medical laboratory machinery—to create an impression of great strength and durability. Thicker parts assembled with larger-than-usual oversize bolts can be used to create a rugged-looking machine. Sometimes machines and their parts are designed purely from the standpoint of styling and nothing else. These points are made here so that you will not be misled into believing that there is a rational mathematical approach to every design decision.ManufacturingManufacturing is that enterprise concerned with converting raw material into finished products. There are three distinct phases in manufacturing. These phases are as follows: input, processing, and output.The first phase includes all of the elements necessary to create a marketable product. First, there must be a demand or need for the product. The necessary materials must be (available. Also needed are such resources as energy, time, human knowledge, and human skills. Finally, it takes capital to obtain all of the other resources.Input resources are channeled through the various processes in Phase Two. These are the processes used to convert raw materials into finished products. A design is developed. Based on the design, various types of planning are accomplished. Plans are put into action through various production processes. The various resources and processes are managed to ensure efficiency and productivity. For example, capital resources must be carefully managed to ensure they are used prudently. Finally, the product in question is marketed.The final phase is the output or finished product. Once the finished product has been purchased it must be transported to users. Depending on the nature of the product, installation and ongoing field support may be required. In addition, with some products, particularly those of a highly complex nature, training is necessary.Materials and Processes in ManufacturingEngineering materials covered herein are divided into two broad categories: metals and nonmetals. Metals are subdivided into ferrous metals, nonferrous metals, high-performance alloys, and powdered metals. Nonmetals are subdivided into plastics, elastomers, composites, and ceramics. Production processes covered herein are divided into several broad categories including forming, forging,casting/molding, .heat treatment^ .fastening joining metrology/quality control, and material removal. Each of these is subdivided into several other processes.Stages in the Development of ManufacturingOver the years, manufacturing processes have- gone through four distinct,-although overlapping, stages of development. These stages are as follows: Stage 1 ManualStage 2 MechanizedStage 3 AutomatedStage 4 IntegratedWhen people first began converting raw materials into finished products, they used manual processes. Everything was accomplished using human hands and manually operated tools. This was a very rudimentary form of fully integrated manufacturing. A person identified the need, collected materials, designed a product to meet the need, produced the product, and used it. Everything from start to finish was integrated within the mind of the person who did all the work.Then during the industrial revolution mechanized processes were introduced and humans began using machines to accomplish work previously accomplished manually. This led to work specialization which, in turn, eliminated the integrated aspect of manufacturing. In this stage of development, manufacturing workers might see only that part of an overall manufacturing operation represented by that specific piece on which they worked. There was no way to tell how their efforts fit into the larger picture or their workpiece into the finished product.The next stage in the development of manufacturing processes involved the automation of selected processes. This amounted to computer control of machines and processes. During this phase, islands of automation began to spring up on the shop floor. Each island represented a distinct process or group of processes used in the production of a product. Although these islands of automation did tend to enhance the productivity of the individual processes within the islands, overall productivity often was unchanged. This was because the islands were sandwiched in among other processes that were not automated and were not synchronized with them.The net result was that workpieces would move quickly and efficiently through the automated processes only to back up at manual stations and create bottlenecks. To understand this problem, think of yourself driving from stoplight to stoplight in rush hour traffic Occasionally you find an opening and an: able to rush ahead of the other cars that are creeping along, only to find yourself backed up at the next light. The net effect of your brief moment of speeding ahead is canceled out by the bottleneck at the next stoplight. Better progress would be made if you and the other drivers could synchronize your speed to the changing of the stoplights. Then all cars would move steadily and consistently along and everyone would make better progress in the long run.This need for steady, consistent flow on the shop floor led to the development of integrated manufacturing, a process that is still emerging. In fully integrated settings, machines and processes are computer controlled and integration is accomplished through computers. In the analogy used in the previous paragraph, computers would synchronize the rate of movement of all cars with the changing of the stoplights so that everyone moved steadily and consistently along.The Science of MechanicsThat branch of scientific analysis which deals with motions, time, and forces is called mechanics and is made up of two parts, static’s and dynamics. Static’s deals with the analysis of stationary systems, i. e., those in which time is not a factor, and dynamics deals with systems which change with time.Dynamics is also made up. of tyro major disciplines, first recognized as separate entities by Euler in 1775.The investigation of the motion of a rigid body may be conveniently separated into two parts, the one geometrical, the other mechanical. In the first part, the transference of the body from a given position to any other position must be investigated without respect to the cause of the motion, and must be represented by analytical formulae, which will define the position of each point of the body. This investigation will therefore be referable solely to geometry, or rather to stereotomy.It is clear that by the separation of this part of the question from the other, which belongs properly to Mechanics, the determination of the motion from dynamical principles will be made much easier than if the two parts were undertaken conjointly.These two aspects of dynamics were later recognized as the distinct sciences of kinematics and kinetics, and deal with motion and the forces producing it respectively.The initial problem in the design of a mechanical system therefore understands its kinematics. Kinematics is the study of motion, quite apart from the forces whichproduce that motion. More particularly, kinematics is the study of position, displacement rotation, speed, velocity, and acceleration. The study, say of planetary or orbital motion is also a problem in kinematics.It should be carefully noted in the above quotation that Euler based his separation of dynamics into kinematics and kinetics on the assumption that they should deal with rigid bodies. It is this very important assumption that allows the two to be treated separately. For flexible bodies, the shapes of the bodies themselves, and therefore their motions, depend on the forces exerted on them. In this situation, the study of force and motion must take place simultaneously, thus significantly increasing the complexity of the analysis.Fortunately, although all real machine parts are flexible to some degree, machines are usually designed from relatively rigid materials, keeping part deflections to a minimum. Therefore, it is common practice to assume that deflections are negligible and parts are rigid when analyzing a machine's kinematics performance, and then, after the dynamic analysis when loads are known, to design the parts so that this assumption is justified.。
机械工程毕业设计外文翻译

毕业设计论文外文资料原文及译文学院:机电工程学院专业:机械设计制造及其自动化班级:学号:姓名:Mechanical engineering1.The porfile of mechanical engineeringEngingeering is a branch of mechanical engineerig,it studies mechanical and power generation especially power and movement.2.The history of mechanical engineering18th century later periods,the steam engine invention has provided a main power fountainhead for the industrial revolution,enormously impelled each kind of mechznical biting.Thus,an important branch of a new Engineering – separated from the civil engineering tools and machines on the branch-developed together with Birmingham and the establishment of the Associantion of Mechanical Engineers in 1847 had been officially recognized.The mechanical engineering already mainly used in by trial and error method mechanic application technological development into professional engineer the scientific method of which in the research,the design and the realm of production used .From the most broad perspective,the demend continuously to enhance the efficiencey of mechanical engineers improve the quality ofwork,and asked him to accept the history of the high degree of education and training.Machine operation to stress not only economic but also infrastructure costs to an absolute minimun.3.The field of mechanical engineeringThe commodity machinery development in the develop country,in the high level material life very great degree is decided each kind of which can realize in the mechanical engineering.Mechanical engineers unceasingly will invent the machine next life to produce the commodity,unceasingly will develop the accuracy and the complexity more and more high machine tools produces the machine.The main clues of the mechanical development is:In order to enhance the excellent in quality and reasonable in price produce to increase the precision as well as to reduce the production cost.This three requirements promoted the complex control system development.The most successful machine manufacture is its machine and the control system close fusion,whether such control system is essentially mechanical or electronic.The modernized car engin production transmission line(conveyer belt)is a series of complex productions craft mechanizationvery good example.The people are in the process of development in order to enable further automation of the production machinery ,the use of a computer to store and handle large volumes of data,the data is a multifunctional machine tools necessary for the production of spare parts.One of the objectives is to fully automated production workshop,three rotation,but only one officer per day to operate.The development of production for mechanical machinery must have adequate power supply.Steam engine first provided the heat to generate power using practical methods in the old human,wind and hydropower,an increase of engin .New mechanical engineering industry is one of the challenges faced by the initial increase thermal effciency and power,which is as big steam turbine and the development of joint steam boilers basically achieved.20th century,turbine generators to provide impetus has been sustained and rapid growth,while thermal efficiency is steady growth,and large power plants per kW capital consumption is also declining.Finally,mechanical engineers have nuclear energy.This requires the application of nuclear energy particularly high reliability and security,which requires solving many new rge power plants and the nuclear power plant control systems have become highly complex electroonics,fluid,electricity,water and mechanical parts networks All in all areas related to the mechanical engineers.Small internal combustion engine,both to the type (petrol and diesel machines)or rotary-type(gas turbines and Mong Kerr machine),as well as their broad application in the field of transport should also due to mechanical enginerrs.Throughout the transport,both in the air and space,or in the terrestrial and marine,mechanial engineers created a variety of equipment and power devices to their increasing cooperation with electrical engineers,especially in the development of appropration control systems.Mechanical engineers in the development of military weapons technology and civil war ,needs a similar,though its purpose is to enhance rather than destroy their productivity.However.War needs a lot of resources to make the area of techonlogy,many have a far-reaching development in peacetime efficiency.Jet aircraft and nuclear reactors are well known examples.The Biological engineering,mechanical engineering biotechnology is a relatively new and different areas,it provides for the replacement of the machine or increase thebody functions as well as for medical equipment.Artficial limbs have been developed and have such a strong movement and touch response function of the human body.In the development of artificial organ transplant is rapid,complex cardiac machines and similar equipment to enable increasingly complex surgery,and injuries and ill patients life functions can be sustained.Some enviromental control mechanical engineers through the initial efforts to drainage or irrigation pumping to the land and to mine and ventilation to control the human environment.Modern refrigeration and air-conditioning plant commonaly used reverse heat engine,where the heat from the engine from cold places to more external heat.Many mechanical engineering products,as well as other leading technology development city have side effects on the environment,producing noise,water and air pollution caused,destroyed land and landscape.Improve productivity and diver too fast in the commodity,that the renewable naturalforces keep pace.For mechanical engineers and others,environmental control is rapidly developing area,which includes a possible development and production of small quantities of pollutants machine sequnce,and the development of new equipment and teachnology has been to reduce and eliminate pollution.4.The role of mechanical engineeringThere are four generic mechanical engineers in common to the above all domains function.The 1st function is the understanding and the research mechanical science foundation.It includes the power and movement of the relationship dynamics For example,in the vibration and movement of the relationship;Automatic control;Study of the various forms of heart,energy,power relations between the thermodynamic;Fluidflows; Heat transfer; Lubricant;And material properties.The 2nd function will be conducts the research,the desing and the development,this function in turn attempts to carry on the essential change to satisfy current and the future needs.This not only calls for a clear understanding of mechanical science,and have to breakdown into basic elements of a complex system capacity.But also the need for synthetic and innovative inventions.The 3rd function is produces the product and the power,include plan,operation and maintenance.Its goal lies in the maintenance eitherenhances the enterprise or the organization longer-tern and survivabilaty prestige at the same time,produces the greatest value by the least investments and the consumption.The 4th function is mechanical engineer’s coordinated function,including the management,the consultation,as well as carries on the market marking in certain situation.In all these function,one kind unceasingly to use the science for a long time the method,but is not traditional or the intuition method tendency,this is a mechanical engineering skill aspect which unceasingly grows.These new rationalization means typical names include:The operations research,the engineering economics,the logical law problem analysis(is called PABLA) However,creativity is not rationalization.As in other areas,in mechanical engineering,to take unexpected and important way to bring about a new capacity,still has a personal,marked characteristice.5.The design of mechanical engineeringThe design of mechanical is the design has the mechanical property the thing or the system,such as:the instrument and the measuring appliance in very many situations,the machine design must use the knowledge of discipline the and so on mathematics,materials science and mechanics.Mechanical engineering desgin includeing all mechanical desgin,but it was a study,because it also includes all the branches of mechsnical engineering,such as thermodynamics all hydrodynamics in the basic disciplines needed,in the mechanical engineering design of the initial stude or mechanical design.Design stages.The entire desgin process from start to finish,in the process,a demand that is designed for it and decided to do the start.After a lot of repetition,the final meet this demand by the end of the design procees and the plan.Design considerations.Sometimes in a system is to decide which parts needs intensity parts of geometric shapesand size an important factor in this context that we must consider that the intensity is an important factor in the design.When we use expression design considerations,we design parts that may affect the entire system design features.In the circumstances specified in the design,usually for a series of such functions must be taken into account.Howeever,to correct purposes,we should recognize that,in many cases thedesign of important design considerations are not calculated or test can determine the components or systems.Especially students,wheen in need to make important decisions in the design and conduct of any operation that can not be the case,they are often confused.These are not special,they occur every day,imagine,for example,a medical laboratory in the mechanical design,from marketing perspective,people have high expectations from the strength and relevance of impression.Thick,and heavy parts installed together:to produce a solid impression machines.And sometimes machinery and spare parts from the design style is the point and not the other point of view.Our purpose is to make those you do not be misled to believe that every design decision will needreasonable mathematical methods.Manufacturing refers to the raw meterials into finished products in the enterprise.Create three distinct phases.They are:input,processing exprot.The first phase includes the production of all products in line with market needs essential.First there must be the demand for the product,the necessary materials,while also needs such as energy,time,human knowledge and technology resourcess .Finall,the need for funds to obtain all the other resources. Lose one stage after the second phase of the resources of the processes to be distributed.Processing of raw materials into finished products of these processes.To complete the design,based on the design,and then develop plans.Plan implemented through various production processes.Management of resources and processes to ensure efficiency and productivity.For example,we must carefully manage resources to ensure proper use of funds.Finally,people are talking about the product market was cast.Stage is the final stage of exporting finished or stage.Once finished just purchased,it must be delivered to the users.According to product performance,installation and may have to conduct further debugging in addition,some products,especially those very complex products User training is necessary.6.The processes of materials and maunfacturingHere said engineering materials into two main categories:metals and non-ferrous,high-performance alloys and power metals.Non-metallic futher divided into plastice,synthetic rubber,composite materials and ceramics.It said the productionproccess is divided into several major process,includingshape,forging,casting/ founding,heat treatment,fixed/connections ,measurement/ quality control and materal cutting.These processes can be further divide into each other’s craft.Various stages of the development of the manufacturing industry Over the years,the manufacturing process has four distinct stages of development, despite the overlap.These stages are:The first phase is artisanal,the second Phase is mechanization.The third phase is automation the forth Phase is integrated.When mankind initial processing of raw materials into finished products will be,they use manual processes.Each with their hands and what are the tools manuslly produced.This is totally integrated production take shape.A person needs indentification,collection materials,the design of a product to meet that demand,the production of such products and use it.From beginning to end,everything is focused on doing the work of the human ter in the industrial revolution introduced mechanized production process,people began to use machines to complete the work accomplished previously manual. This led to the specialization.Specialization in turn reduce the manufacture of integrated factors.In this stage of development,manufacturing workers can see their production as a whole represent a specific piece of the part of the production process.One can not say that their work is how to cope with the entire production process,or how they were loaded onto a production of parts finished.Development of manufacting processes is the next phase of the selection process automation.This is a computer-controlled machinery and processes.At this stage,automation island began to emerge in the workshop lane.Each island represents a clear production process or a group of processes.Although these automated isolated island within the island did raise the productivity of indivdual processes,but the overall productivity are often not change.This is because the island is not caught in other automated production process middle,but not synchronous with them .The ultimate result is the efficient working fast parked through automated processes,but is part of the stagnation in wages down,causing bottlenecks.To better understand this problem,you can imagine the traffic in the peak driving a red light from the red Service Department to the next scene. Occasionally you will find a lot less cars,more than being slow-moving vehicles,but the results can be found by thenext red light Brance.In short you real effect was to accelerate the speed of a red Department obstruction offset.If you and other drivers can change your speed and red light simultaneously.Will advance faster.Then,all cars will be consistent,sommth operation,the final everyone forward faster.In the workshop where the demand for stable synchronization of streamlined production,and promoted integration of manufacturing development.This is a still evolving technology.Fully integrated in the circumstances,is a computer-controllrd machinery and processing.integrated is completed through computer.For example in the preceding paragraph simulation problems,the computer will allow all road vehicles compatible with the change in red.So that everyone can steady traffic.Scientific analysis of movement,timing and mechanics of the disciplines is that it is composed of two pater:statics and dynamics.Statics analyzed static system that is in the system,the time is not taken into account,research and analysis over time and dynamics of the system change.Dynameics from the two componets.Euler in 1775 will be the first time two different branches: Rigid body movement studies can conveniently divided into two parts:geometric and mechanics.The first part is without taking into account the reasons for the downward movement study rigid body from a designated location to another point of the movement,and must use the formula to reflect the actual,the formula would determine the rigid body every point position. Therefore,this study only on the geometry and,more specifically,on the entities from excision.Obviously,the first part of the school and was part of a mechanical separation from the principles of dynamics to study movement,which is more than the two parts together into a lot easier.Dynamics of the two parts are subsequently divided into two separate disciplines,kinematic and dynamics,a study of movement and the movement strength.Therefore,the primary issue is the design of mechanical systems understand its kinematic.Kinematic studies movement,rather than a study of its impact.In a more precise kinematic studies position,displacement,rotation, speed,velocity and acceleration of disciplines,for esample,or planets orbiting research campaing is a paradigm.In the above quotation content should be pay attention that the content of the Euler dynamics into kinematic and rigid body dynamics is based on the assumptionthat they are based on research.In this very important basis to allow for the treatment of two separate disciplines.For soft body,soft body shape and even their own soft objects in the campaign depends on the role of power in their possession.In such cases,should also study the power and movement,and therefore to a large extent the analysis of the increased complexity.Fortunately, despite the real machine parts may be involved are more or less the design of machines,usually with heavy material designed to bend down to the lowest parts.Therefore,when the kinematic analysis of the performance of machines,it is often assumed that bend is negligible,spare parts are hard,but when the load is known,in the end analysis engine,re-engineering parts to confirm this assnmption.机械工程1.机械工程简介机械工程是工程学的一个分支,它研究机械和动力的产,尤其是力和动力。
机械类毕业设计外文翻译

本科毕业论文(设计)外文翻译学院:机电工程学院专业:机械工程及自动化姓名:高峰指导教师:李延胜2011年 05 月 10日教育部办公厅Failure Analysis,Dimensional Determination And Analysis,Applications Of Cams INTRODUCTIONIt is absolutely essential that a design engineer know how and why parts fail so that reliable machines that require minimum maintenance can be designed.Sometimes a failure can be serious,such as when a tire blows out on an automobile traveling at high speed.On the other hand,a failure may be no more than a nuisance.An example is the loosening of the radiator hose in an automobile cooling system.The consequence of this latter failure is usually the loss of some radiator coolant,a condition that is readily detected and corrected.The type of load a part absorbs is just as significant as the magnitude.Generally speaking,dynamic loads with direction reversals cause greater difficulty than static loads,and therefore,fatigue strength must be considered.Another concern is whether the material is ductile or brittle.For example,brittle materials are considered to be unacceptable where fatigue is involved.Many people mistakingly interpret the word failure to mean the actualbreakage of a part.However,a design engineer must consider a broader understanding of what appreciable deformation occurs.A ductile material,however will deform a large amount prior to rupture.Excessive deformation,without fracture,may cause a machine to fail because the deformed part interferes with a moving second part.Therefore,a part fails(even if it has not physically broken)whenever it no longer fulfills its required function.Sometimes failure may be due to abnormal friction or vibration between two mating parts.Failure also may be due to a phenomenon called creep,which is the plastic flow of a material under load at elevated temperatures.In addition,the actual shape of a part may be responsible for failure.For example,stress concentrations due to sudden changes in contour must be taken into account.Evaluation of stress considerations is especially important when there are dynamic loads with direction reversals and the material is not very ductile. In general,the design engineer must consider all possible modes of failure,which include the following.——Stress——Deformation——Wear——Corrosion——Vibration——Environmental damage——Loosening of fastening devicesThe part sizes and shapes selected also must take into account many dimensional factors that produce external load effects,such as geometric discontinuities,residual stresses due to forming of desired contours,and the application of interference fit joints.Cams are among the most versatile mechanisms available.A cam is a simple two-member device.The input member is the cam itself,while the output member is called the follower.Through the use of cams,a simple input motion can be modified into almost any conceivable output motion that is desired.Some of the common applications of cams are ——Camshaft and distributor shaft of automotive engine ——Production machine tools——Automatic record players——Printing machines——Automatic washing machines——Automatic dishwashersThe contour of high-speed cams (cam speed in excess of 1000 rpm) must be determined mathematically.However,the vast majority of cams operate at low speeds(less than 500 rpm) or medium-speed cams can be determined graphically using a large-scale layout.In general,the greater the cam speed and output load,the greater must be the precision with which the cam contour is machined.DESIGN PROPERTIES OF MATERIALSThe following design properties of materials are defined as they relate to the tensile test.FigureStatic Strength.The strength of a part is the maximum stress that the part can sustain without losing its ability to perform its required function.Thus the static strength may be considered to be approximately equal to the proportional limit,since no plastic deformation takes place and no damage theoretically is done to the material.Stiffness.Stiffness is the deformation-resisting property of a material.The slope of the modulus line and,hence,the modulus of elasticity are measures of the stiffness of a material.Resilience.Resilience is the property of a material that permits it to absorb energy without permanent deformation.The amount of energy absorbed is represented by the area underneath the stress-strain diagram within the elastic region.Toughness.Resilience and toughness are similar properties.However,toughness is the ability to absorb energy without rupture.Thus toughness is represented by the total area underneath the stress-strain diagram,as depicted in Figure 2.8b.Obviously,the toughness and resilience of brittle materials are very low and are approximately equal.Brittleness. A brittle material is one that ruptures before any appreciable plastic deformation takes place.Brittle materials are generally considered undesirable for machine components because they are unable to yield locally at locations of high stress because of geometric stress raisers such as shoulders,holes,notches,or keyways.Ductility. A ductility material exhibits a large amount of plastic deformation prior to rupture.Ductility is measured by the percent of areaand percent elongation of a part loaded to rupture.A 5%elongation at rupture is considered to be the dividing line between ductile and brittle materials.Malleability.M alleability is essentially a measure of the compressive ductility of a material and,as such,is an important characteristic of metals that are to be rolled into sheets.Hardness.The hardness of a material is its ability to resist indentation or scratching.Generally speaking,the harder a material,the more brittle it is and,hence,the less resilient.Also,the ultimate strength of a material is roughly proportional to its hardness.Machinability.Machinability is a measure of the relative ease with which a material can be machined.In general,the harder the material,the more difficult it is to machine.FigureCOMPRESSION AND SHEAR STATIC STRENGTHIn addition to the tensile tests,there are other types of static load testing that provide valuable information.Compression Testing.M ost ductile materials have approximately the same properties in compression as in tension.The ultimate strength,however,can not be evaluated for compression.As a ductile specimen flows plastically in compression,the material bulges out,but there is no physical rupture as is the case in tension.Therefore,a ductile material fails in compression as a result of deformation,not stress.Shear Testing.Shafts,bolts,rivets,and welds are located in such a way that shear stresses are produced.A plot of the tensile test.The ultimate shearing strength is defined as the stress at which failure occurs.The ultimate strength in shear,however,does not equal the ultimate strength in tension.For example,in the case of steel,the ultimate shear strength is approximately 75% of the ultimate strength in tension.This difference must be taken into account when shear stresses are encountered in machine components.DYNAMIC LOADSAn applied force that does not vary in any manner is called a static or steady load.It is also common practice to consider applied forces that seldom vary to be static loads.The force that is gradually applied during a tensile test is therefore a static load.On the other hand,forces that vary frequently in magnitude and direction are called dynamic loads.Dynamic loads can be subdivided to the following three categories.Varying Load.W ith varying loads,the magnitude changes,but the direction does not.For example,the load may produce high and low tensile stresses but no compressive stresses.Reversing Load.In this case,both the magnitude and direction change.These load reversals produce alternately varying tensile and compressive stresses that are commonly referred to as stress reversals.Shock Load.This type of load is due to impact.One example is an elevator dropping on a nest of springs at the bottom of a chute.The resulting maximum spring force can be many times greater than the weight of the elevator,The same type of shock load occurs in automobile springs when a tire hits a bump or hole in the road.FATIGUE FAILURE-THE ENDURANCE LIMIT DIAGRAMThe test specimen in Figure .,after a given number of stress reversals will experience a crack at the outer surface where the stress is greatest.The initial crack starts where the stress exceeds the strength of the grain on which it acts.This is usually where there is a small surface defect,such as a material flaw or a tiny scratch.As the number of cycles increases,the initial crack begins to propagate into a continuous series of cracks all around the periphery of the shaft.The conception of the initial crack is itself a stress concentration that accelerates the crack propagation phenomenon.Once the entire periphery becomes cracked,the cracks start to move toward the center of the shaft.Finally,when the remaining solid inner area becomes small enough,the stress exceeds the ultimate strength and the shaft suddenly breaks.Inspection of the break reveals a very interesting pattern,as shown in Figure .The outer annular area is relatively smooth because mating cracked surfaces had rubbed against each other.However,the center portion is rough,indicating a sudden rupture similar to that experienced with the fracture of brittle materials.This brings out an interesting fact.When actual machine parts fail as a result of static loads,they normally deform appreciably because of the ductility of the material.FigureThus many static failures can be avoided by making frequent visual observations and replacing all deformed parts.However,fatigue failures give to warning.Fatigue fail mated that over 90% of broken automobile parts have failed through fatigue.The fatigue strength of a material is its ability to resist the propagation of cracks under stress reversals.Endurance limit is a parameter used to measure the fatigue strength of a material.By definition,the endurance limit is the stress value below which an infinite number of cycles will not cause failure.Let us return our attention to the fatigue testing machine in Figure .The test is run as follows:A small weight is inserted and the motor is turned on.At failure of the test specimen,the counter registers the number of cycles N,and the corresponding maximum bending stress is calculated from Equation .The broken specimen is then replaced by an identical one,and an additional weight is inserted to increase the load.A new value of stress is calculated,and the procedure is repeated until failure requires only one complete cycle.A plot is then made of stress versus number of cycles to failure.Figure shows the plot,which is called the endurance limit or S-N curve.Since it would take forever to achieve an infinite number of cycles,1 million cycles is used as a reference.Hence the endurance limit can be found from Figure by noting that it is the stress level below which the material can sustain 1 million cycles without failure.The relationship depicted in Figure is typical for steel,because the curve becomes horizontal as N approaches a very large number.Thus the endurance limit equals the stress level where the curve approaches a horizontal tangent.Owing to the large number of cycles involved,N is usually plotted on a logarithmic scale,as shown in Figure .When this is done,the endurance limit value can be readily detected by the horizontal straight line.For steel,the endurance limit equals approximately 50% of the ultimate strength.However,if the surface finish is not of polished equality,the value of the endurance limit will be lower.For example,for steel parts with a machined surface finish of 63 microinches ( μin.),the percentage drops to about 40%.For rough surfaces (300μin.or greater),the percentage may be as low as 25%.The most common type of fatigue is that due to bending.The next mostfrequent is torsion failure,whereas fatigue due to axial loads occurs very seldom.Spring materials are usually tested by applying variable shear stresses that alternate from zero to a maximum value,simulating the actual stress patterns.In the case of some nonferrous metals,the fatigue curve does not level off as the number of cycles becomes very large.This continuing toward zero stress means that a large number of stress reversals will cause failure regardless of how small the value of stress is.Such a material is said to have no endurance limit.For most nonferrous metals having an endurance limit,the value is about 25% of the ultimate strength.EFFECTS OF TEMPERATURE ON YIELD STRENGTH AND MODULUS OF ELASTICITY Generally speaking,when stating that a material possesses specified values of properties such as modulus of elasticity and yield strength,it is implied that these values exist at room temperature.At low or elevated temperatures,the properties of materials may be drastically different.For example,many metals are more brittle at low temperatures.In addition,the modulus of elasticity and yield strength deteriorate as the temperature increases.Figure shows that the yield strength for mild steel is reduced by about 70% in going from room temperature to 1000o F.Figure shows the reduction in the modulus of elasticity E for mild steel as the temperature increases.As can be seen from the graph,a 30% reduction in modulus of elasticity occurs in going from room temperature to 1000o F.In this figure,we also can see that a part loaded below the proportional limit at room temperature can be permanently deformed under the same load at elevated temperatures.FigureCREEP: A PLASTIC PHENOMENONTemperature effects bring us to a phenomenon called creep,which is the increasing plastic deformation of a part under constant load as a function of time.Creep also occurs at room temperature,but the process is so slow that it rarely becomes significant during the expected life of the temperature is raised to 300o C or more,the increasing plastic deformation can become significant within a relatively short period of time.The creep strength of a material is its ability to resist creep,and creep strength data can be obtained by conducting long-time creep tests simulating actual part operating conditions.During the test,theplastic strain is monitored for given material at specified temperatures.Since creep is a plastic deformation phenomenon,the dimensions of a part experiencing creep are permanently altered.Thus,if a part operates with tight clearances,the design engineer must accurately predict the amount of creep that will occur during the life of the machine.Otherwise,problems such binding or interference can occur.Creep also can be a problem in the case where bolts are used to clamp tow parts together at elevated temperatures.The bolts,under tension,will creep as a function of time.Since the deformation is plastic,loss of clamping force will result in an undesirable loosening of the bolted joint.The extent of this particular phenomenon,called relaxation,can be determined by running appropriate creep strength tests.Figure shows typical creep curves for three samples of a mild steel part under a constant tensile load.Notice that for the high-temperature case the creep tends to accelerate until the part fails.The time line in the graph (the x-axis) may represent a period of 10 years,the anticipated life of the product.FigureSUMMARYThe machine designer must understand the purpose of the static tensile strength test.This test determines a number of mechanical properties of metals that are used in design equations.Such terms as modulus of elasticity,proportional limit,yield strength,ultimate strength,resilience,and ductility define properties that can be determined from the tensile test.Dynamic loads are those which vary in magnitude and direction and may require an investigation of the machine part’s resistance to failure.Stress reversals may require that the allowable design stress be based on the endurance limit of the material rather than on the yield strength or ultimate strength.Stress concentration occurs at locations where a machine part changes size,such as a hole in a flat plate or a sudden change in width of a flat plate or a groove or fillet on a circular shaft.Note that for the case of a hole in a flat or bar,the value of the maximum stress becomes much larger in relation to the average stress as the size of the hole decreases.Methods of reducing the effect of stress concentration usuallyinvolve making the shape change more gradual.Machine parts are designed to operate at some allowable stress below the yield strength or ultimate strength.This approach is used to take care of such unknown factors as material property variations and residual stresses produced during manufacture and the fact that the equations used may be approximate rather that exact.The factor of safety is applied to the yield strength or the ultimate strength to determine the allowable stress.Temperature can affect the mechanical properties of metals.Increases in temperature may cause a metal to expand and creep and may reduce its yield strength and its modulus of elasticity.If most metals are not allowed to expand or contract with a change in temperature,then stresses are set up that may be added to the stresses from the load.This phenomenon is useful in assembling parts by means of interference fits.A hub or ring has an inside diameter slightly smaller than the mating shaft or post.The hub is then heated so that it expands enough to slip over the shaft.When it cools,it exerts a pressure on the shaft resulting in a strong frictional force that prevents loosening.TYPES OF CAM CONFIGURATIONSPlate Cams.This type of cam is the most popular type because it is easy to design and manufacture.Figure 6.1 shows a plate cam.Notice that the follower moves perpendicular to the axis of rotation of the camshaft.All cams operate on the principle that no two objects can occupy the same space at the same time.Thus,as the cam rotates ( in this case,counterclockwise ),the follower must either move upward or bind inside the guide.We will focus our attention on the prevention of binding and attainment of the desired output follower motion.The spring is required to maintain contact between the roller of the follower and the cam contour when the follower is moving downward.The roller is used to reduce friction and hence wear at the contact surface.For each revolution of the cam,the follower moves through two strokes-bottom dead center to top dead center (BDC to TDC) and TDC to BDC.Figure illustrates a plate cam with a pointed follower.Complex motions can be produced with this type of follower because the point can follow precisely any sudden changes in cam contour.However,this design is limited to applications in which the loads are very light;otherwisethe contact point of both members will wear prematurely,with subsequent failure.Two additional variations of the plate cam are the pivoted follower and the offset sliding follower,which are illustrated in Figure .A pivoted follower is used when rotary output motion is desired.Referring to the offset follower,note that the amount of offset used depends on such parameters as pressure angle and cam profile flatness,which will be covered later.A follower that has no offset is called an in-line follower.Figure 6..3Translation Cams.Figure depicts a translation cam.The follower slides up and down as the cam translates motion in the horizontal direction.Note that a pivoted follower can be used as well as a sliding-type follower.This type of action is used in certain production machines in which the pattern of the product is used as the cam.A variation on this design would be a three-dimensional cam that rotates as well as translates.For example,a hand-constructed rifle stock is placed in a special lathe.This stock is the pattern,and it performs the function of a cam.As it rotates and translates,the follower controls a tool bit that machines the production stock from a block of wood.FigurePositive-Motion Cams.In the foregoing cam designs,the contact between the cam and the follower is ensured by the action of the spring forces during the return stroke.However,in high-speed cams,the spring force required to maintain contact may become excessive when added to the dynamic forces generated as a result of accelerations.This situation can result in unacceptably large stress at the contact surface,which in turn can result in premature wear.Positive-motion cams require no spring because the follower is forced to contact the cam in two directions.Thereare four basic types of positive-motion cams: the cylindrical cam,the grooved-plate cam ( also called a face cam ) ,the matched-plate cam,and the scotch yoke cam.Cylindrical Cam.The cylindrical cam shown in Figure produces reciprocating follower motion,whereas the one shown in Figure illustrates the application of a pivoted follower.The cam groove can be designed such that several camshaft revolutions are required to produce one complete follower cycle.Grooved-plate Cam.In Figure we see a matched-plate cam with a pivoted follower,although the design also can be used with a translation follower.Cams E and F rotate together about the camshaft B.Cam E is always in contact with roller C,while cam F maintains contact with roller D.Rollers C and D are mounted on a bell-crank lever,which is the follower oscillating about point A.Cam E is designed to provide the desired motion of roller C,while cam F provides the desired motion of roller D.Scotch Yoke Cam.This type of cam,which is depicted in Figure ,consists of a circular cam mounted eccentrically on its camshaft.The stroke of the follower equals two times the eccentricity e of the cam.This cam produces simple harmonic motion with no dwell times.Refer to Section for further discussion.CAM TERMINOLOGYBefore we become involved with the design of cams,it is desirable to know the various terms used to identify important cam design parameters.The following terms refer to Figure .The descriptions will be more understandable if you visualize the cam as stationary and the follower as moving around the cam.Trace Point.The end point of a knife-edge follower or the center of the roller of a roller-type follower.Cam Contour.The actual shape of the cam.Base Circle.The smallest circle that can be drawn tangent to the cam contour.Its center is also the center of the camshaft.The smallest radial size of the cam stars at the base circle.Pitch Curve.The path of the trace point,assuming the cam is stationary and the follower rotates about the cam.Prime Circle.The smallest circle that can be drawn tangent to the pitch curve.Its center is also the center of the camshaft.Pressure Angle.The angle between the direction of motion of the follower and the normal to the pitch curve at the point where the center of the roller lies.Cam Profile.Same as cam contour.BDC.Bottom Dead Center,the position of the follower at its closest point to the cam hub.Stroke.The displacement of the follower in its travel between BDC and TDC.Rise.The displacement of the follower as it travels from BDC to TDC.Return.The displacement of the follower as it travels from TDC or BDC.Ewell.The action of the follower when it remains at a constant distance from the cam hub while the cam turns.A clearer understanding of the significance of the pressure angle can be gained by referring to Figure .Here FTis the total force acting on the roller.It must be normal to the surfaces at the contact point.Its direction is obviously not parallel to the direction of motion of the follower.Instead,it is indicated by the angle α,the pressure angle,measured from the line representing the direction of motion of thefollower.Therefore,the force FT has a horizontal component FHand avertical component FV.The vertical component is the one that drives thefollower upward and,therefore,neglecting guide friction,equals thefollower Fload.The horizontal component has no useful purpose but it is unavoidable.In fact,it attempts to bend the follower about its guide.This can damage the follower or cause it to bind inside its guide.Obviously,we want the pressure angle to be as possible to minimize the side thrustFH.A practical rule of thumb is to design the cam contour so that the pressure angle does not exceed 30o.The pressure angle,in general,depends on the following four parameters:——Size of base circle——Amount of offset of follower——Size of roller——Flatness of cam contour ( which depends on follower stroke and type of follower motion used )Some of the preceding parameters cannot be changed without altering the cam requirements,such as space limitations.After we have learned how to design a cam,we will discuss the various methods available to reducethe pressure angle.故障的分析、尺寸的决定以及凸轮的分析和应用前言介绍:作为一名设计工程师有必要知道零件如何发生和为什么会发生故障,以便通过进行最低限度的维修以保证机器的可靠性。
机械专业毕业论文外文翻译

附录一英文科技文献翻译英文原文:Experimental investigation of laser surface textured parallel thrust bearingsPerformance enhancements by laser surface texturing (LST) of parallel-thrust bearings is experimentally investigated. Testresults are compared with a theoretical model and good correlation is found over the relevant operating conditions. A compari-son of the performance of unidirectional and bi-directional partial-LST bearings with that of a baseline, untextured bearing ispresented showing the benefits of LST in terms of increased clearance and reduced friction.KEY WORDS: fluid film bearings, slider bearings, surface texturing1. IntroductionThe classical theory of hydrodynamic lubrication yields linear (Couette) velocity distribution with zero pressure gradients between smooth parallel surfaces under steady-state sliding. This results in an unstable hydrodynamic film that would collapse under any external force acting normal to the surfaces. However, experience shows that stable lubricating films can develop between parallel sliding surfaces, generally because of some mechanism that relaxes one or more of the assumptions of the classical theory.A stable fluid film with sufficient load-carrying capacity in parallel sliding surfaces can be obtained, for example, with macro or micro surface structure of different types. These include waviness [1] and protruding microasperities [2–4]. A good literature review on the subject can be found in Ref. [5]. More recently, laser surface texturing (LST) [6–8], as well as inlet roughening by longitudinal or transverse grooves [9] were suggested to provide load capacity in parallel sliding. The inlet roughness concept of Tonder [9] is based on ‘‘effective clearanc e’’ reduction in the sliding direction and in this respect it is identical to the par- tial-LST concept described in ref.[10] for generating hydrostatic effect in high-pressure mechanical seals.Very recently Wang et al. [11] demonstrated experimentally a doubling of the load-carrying capacity for the surface- texture design by reactive ion etching of SiCparallel-thrust bearings sliding in water. These simple parallel thrust bearings are usually found in seal-less pumps where the pumped fluid is used as the lubricant for the bearings. Due to the parallel sliding their performance is poorer than more sophisticated tapered or stepped bearings. Brizmer et al. [12] demon-strated the potential of laser surface texturing in the form of regular micro-dimples for providing load-carrying capacity with parallel-thrust bearings. A model of a textured parallelslider was developed and the effect of surface texturing on load-carrying capacitywas analyzed. The optimum parameters of the dimples were found in order to obtainmaximum load-carrying capacity. A micro-dimple ‘‘collective effect’’ was identi-fied that is capable of generating substantial load-carrying capacity, approaching that of optimumconventional thrust bearings. The purpose of the present paper is to investigate experimentally the validity of the model described in Ref. [12] by testing practical thrust bearings and comparing the performance of LST bearings with that of the theoretical predictions and with the performance of standard non-textured bearings2. BackgroundA cross section of the basic model that was analyzed in Ref. [12] is shown in figure1. A slider having a width B is partially textured over a portion Bp =αB of its width.The textured surface consists of multiple dimples with a diameter,depth and area density Sp. As a result of the hydrodynamic pressure generated by the dimples the sliding surfaces will be separated by a clearance depending on the sliding velocity U, the fluid viscosity l and the external load It was found in Ref. [12] that an optimum ratio exists for the parameter that provides maximum dimensionless load-carrying capacity where L isthe bearing length, and this optimum value is hp=1.25. It was further found in Ref. [12] that an optimum value exists for the textured portion a depending onthe bearing aspect ratio L/B. This behavior is shown in figure 2 for a bearing with L/B = 0.75 at various values of the area density Sp. As can be seen in the range of Sp values from 0.18 to 0.72 the optimum a value varies from 0.7 to 0.55, respectively. It can also be seen from figure 2 that for a < 0.85 no optimum value exists for Sp and the maximum load W increases with increasing Sp. Hence, the largest area density that can be practically obtained with the laser texturing is desired. It is also interesting to note from figure 2 the advantage of partial-LST (a < 1) over the full LST (a = 1) for bearing applications. At Sp= 0.5, for example, the load W at a = 0.6 is about three times higher than its value at a = 1. A full account of this behavior is given in Ref. [12].3. ExperimentalThe tested bearings consist of sintered SiC disks 10 mm thick, having 85 mm outer diameter and 40 mm inner diameter. Each bearing (see figure 3) comprises a flat rotor (a) and a six-pad stator (b). The bearings were pr ovided with an original surface finish by lapping to a roughness average Ra= 0.03 lm. Each pad has an aspect ratio of 0.75 when its width is measured along the mean diameter of the stator. The photographs of two partial-LST stators are shown in figure 4 wher e the textured areas appear as brighter matt surfaces. The first stator indicated (a) is a unidirectional bearing with the partial-LST adjacent to the leading edge of each pad, similar to the model shown in figure 1. The second stator (b) is a bi-directional version of a partial-LST bearing having two equal textured portions, a/2, on each of the pad ends. The laser texturing parameters were the following; dimple depth, dimplediameter and dimple area density Sp= 0.60.03. These dimple dimensions were obtained with 4 pulses of 30 ns duration and 4 mJ each using a 5 kHz pulsating Nd:YAG laser. The textured portion of the unidirectional bearing was a= 0.73 and that of the bi-directional bearing was a= 0.63. As can be seen from figure 2 both these a values should produce load-carrying capacity vary close to the maximum theoretical value.The test rig is shown schematically in figure 5. An electrical motor turns a spindle to which an upper holder of the rotor is attached. A second lower holder of the stator is fixed to a housing, which rests on a journal bearing and an axial loading mechanism that can freely move in the axial direction. An arm that presses against a load cell and thereby permits friction torque measurements prevents the free rotation of this housing. Axial loading is provided by means of dead weights on a lever and is measured with a second load cell. A proximity probe that is attached to the lower holder of the stator allows on-line measurements of the clearance change between rotor and stator as the hydrodynamiceffects cause axial movement of the housing to which the stator holder is fixed. Tapwater is supplied by gravity from a large tank to the center of the bearing and the leakage from the bearing is collected and re-circulated. A thermocouple adjacent to the outer diameter of the bearing allows monitoring of the water temperature as the water exit the bearing. A PC is used to collect and process data on-line. Hence,theinstantaneous clearance, friction coefficient, bearing speed and exit water temperaturecan be monitored constantly.The test protocol includes identifying a reference “zero” point for the clearance measurements by first loading and then unloading a stationary bearing over the full load range. Then the lowest axial load is applied, the water supply valve is opened and the motor turned on. Axial loading is increased by steps of 40 N and each load step is maintained for 5 min following the stabilization of the friction coefficient ata steady-state value. The bearing speed and water temperature are monitored throughout the test for any irregularities. The test ends when a maximum axial load of 460 N is reached or if the friction coefficient exceeds a value of 0.35. At the end ofthe last load step the motor and water supply are turned off and the reference for the clearance measurements is rechecked. Tests are performed at two speeds of 1500and 3000 rpm corresponding to average sliding velocities of 4.9 and 9.8 m/s, respectively and each test is repeated at least three times.4. Results and discussionAs a first step the validity of the theoretical model in Ref. [12] was examined by comparing the theoretical and experimental results of bearing clearance versus bearing load for a unidirectional partial-LST bearing. The results are shown in fig ure 6 for the two speeds of 1500 and 3000 rpm where the solid and dashed lines correspond to the model and experiment, respectively. As can be seen, the agreement between the model and the experiment is good, with differences of less than 10%, aslong as the load is above 150 N. At lower loads the measured experimental clearances are much larger than the model predictions, particularly at the higher speed of 3000 rpm where at 120 N the measured clearance is 20 lm, which is about 60% higher than the predicted value. It turns out that the combination of such large clearances and relatively low viscosity of the water may result in turbulent fluid film. Hence, the assumption of laminar flow on which the solution of the Reynolds equation in Ref.[12] is based may be violated making the model invalid especially at the higher speed and lowest load. In order to be consistent with the model of Ref. [12] it was decided to limit further comparisons to loads above 150 N.It should be noted here that the first attempts t o test the baseline untextured bearing with the original surface finish of Ra= 0.03 lm on both the stator and rotor failed due to extremely high friction even at the lower loads. On the other hand the partial-LST bearing ran smoothly throughout the load range. It was found that the post-LST lapping to completely remove about 2 lm height bulges, which are formed during texturing around the rims of the dimples, resulted in a slightly rougher surface with Ra= 0.04 lm. Hence, the baseline untextured stator was also lapped to the same rough- ness of the partial-LST stator and all subsequent tests were performed with the same Ra value of 0.04 lm for all the tested stators. The rotor surface roughness remained, the original one namely, 0.03 lm. Figure 7 presents the experimental resultsfor the clearance as a function of the load for a partial-LST unidirectional bearing (see stator in figure 4(a)) and a baseline untextured bearing. The comparison is made at the two speeds of 1500 and 3000 rpm. The area density of the dimples in the partial-LST bearing is Sp= 0.6 and the textured portion is a ¼ 0:734. The load range extends from 160 to 460 N. The upper load was determined by the test-rig limitation that did not permit higher loading. It is clear from figure 7 that the pa rtial-LST bearing operates at substantially larger clearances than the untextured bearing. At the maximum load of 460 N and speed of 1500 rpm the partial-LST bearing has a clearance of 6 lm while the untextured bearing clearance is only 1.7 lm. At 3000 rpm the clearances are 6.6 and 2.2 lm for the LST and untextured bearings, respectively. As can be seen from figure 7 this ratio of about 3 in favor of the partial-LST bearing is maintained over the entire load range.Figure 8 presents the results for the bi-directionalbearing (see stator in figure 4(b)). In this case the LST parameters are Sp ¼ 0:614 and a ¼ 0:633. The clearances of the bi-directional partial-LST bearing are lower compared to these of the unidirectional bearing at the same load. At 460 N load the clearance for the 1500 rpm is 4.1 lm and for the 3000 rpm it is 6 lm. These values represent a reduction of clearance between 33 and 10% compared to the unidirectional case. However, as can be seen from figure 8 the performance of the partial-LST bi-directional bearing is still substantially better than that of the untextured bearing.The friction coefficient of partial-LST unidirectional and bi-directional bearings was compared with that of the untextured bearing in figures 9 and 10 for the two speeds of 1500 and 3000 rpm, respectively. As can be seen the friction coefficient of the two partial-LST bearings is very similar with slightly lower values in the case of the more efficient unidirectional bearing. The friction coefficient of the untextured bearing is much larger compared to that of the LST bearings. At 1500 rpm (figure 9) and the highest load of 460 N the friction coefficient of the untextured bearing is about 0.025 compared to about 0.01 for the LST bearings.At the lowest load of 160 N the values are about 0.06 for the untextured bearing and around 0.02 for the LST bearings. Hence, the friction values of the untextured bearing are between 2.5 and 3 times higher than the corresponding values for the partial-LST bearings over the entire load range. Similar results were obtained at the velocity of3000 rpm (figure 10) but the level of the friction coefficients is somewhat higherdue to the higher speed. The much higher friction of the untextured bearing is due to the much smaller clearances of this bearing (see figures 7 and 8) that result in higher viscous shear.Bearings fail for a number of reasons,but the most common are misapplication,contamination,improper lubricant,shipping or handling damage,and misalignment. The problem is often not difficult to diagnose because a failed bearing usually leaves telltale signs about what went wrong.However,while a postmortem yields good information,it is better to avoid the process altogether by specifying the bearing correctly in The first place.To do this,it is useful to review the manufacturers sizing guidelines and operating characteristics for the selected bearing.Equally critical is a study of requirements for noise, torque, and runout, as well as possible exposure to contaminants, hostile liquids, and temperature extremes. This can provide further clues as to whether a bearing is right for a job.1 Why bearings failAbout 40% of ball bearing failures are caused by contamination from dust, dirt, shavings, and corrosion. Contamination also causes torque and noise problems, and isoften the result of improper handling or the application environment.Fortunately, a bearing failure caused by environment or handling contamination is preventable,and a simple visual examination can easily identify the cause.Conducting a postmortem il1ustrates what to look for on a failed or failing bearing.Then,understanding the mechanism behind the failure, such as brinelling or fatigue, helps eliminate the source of the problem.Brinelling is one type of bearing failure easily avoided by proper handing and assembly. It is characterized by indentations in the bearing raceway caused by shock loading-such as when a bearing is dropped-or incorrect assembly. Brinelling usually occurs when loads exceed the material yield point(350,000 psi in SAE 52100 chrome steel).It may also be caused by improper assembly, Which places a load across the races.Raceway dents also produce noise,vibration,and increased torque.A similar defect is a pattern of elliptical dents caused by balls vibrating between raceways while the bearing is not turning.This problem is called false brinelling. It occurs on equipment in transit or that vibrates when not in operation. In addition, debris created by false brinelling acts like an abrasive, further contaminating the bearing. Unlike brinelling, false binelling is often indicated by a reddish color from fretting corrosion in the lubricant.False brinelling is prevented by eliminating vibration sources and keeping the bearing well lubricated. Isolation pads on the equipment or a separate foundation may be required to reduce environmental vibration. Also a light preload on the bearing helps keep the balls and raceway in tight contact. Preloading also helps prevent false brinelling during transit.Seizures can be caused by a lack of internal clearance, improper lubrication, or excessive loading. Before seizing, excessive, friction and heat softens the bearing steel. Overheated bearings often change color,usually to blue-black or straw colored.Friction also causes stress in the retainer,which can break and hasten bearing failure.Premature material fatigue is caused by a high load or excessive preload.When these conditions are unavoidable,bearing life should be carefully calculated so that a maintenance scheme can be worked out.Another solution for fighting premature fatigue is changing material.When standard bearing materials,such as 440C or SAE 52100,do not guarantee sufficient life,specialty materials can be recommended. In addition,when the problem is tracedback to excessive loading,a higher capacity bearing or different configuration may be used.Creep is less common than premature fatigue.In bearings.it is caused by excessive clearance between bore and shaft that allows the bore to rotate on the shaft.Creep can be expensive because it causes damage to other components in addition to the bearing.0ther more likely creep indicators are scratches,scuff marks,or discoloration to shaft and bore.To prevent creep damage,the bearing housing and shaft fittings should be visually checked.Misalignment is related to creep in that it is mounting related.If races are misaligned or cocked.The balls track in a noncircumferencial path.The problem is incorrect mounting or tolerancing,or insufficient squareness of the bearing mounting site.Misalignment of more than 1/4·can cause an early failure.Contaminated lubricant is often more difficult to detect than misalignment or creep.Contamination shows as premature wear.Solid contaminants become an abrasive in the lubricant.In addition。
机械专业中英文对照翻译大全

机械专业中英文对照翻译大全机械专业英语词汇中英文对照翻译一览表陶瓷ceramics合成纤维synthetic fibre电化学腐蚀electrochemical corrosion车架automotive chassis悬架suspension转向器redirector变速器speed changer板料冲压sheet metal parts孔加工spot facing machining车间workshop工程技术人员engineer气动夹紧pneuma lock数学模型mathematical model画法几何descriptive geometry机械制图Mechanical drawing投影projection视图view剖视图profile chart标准件standard component零件图part drawing装配图assembly drawing尺寸标注size marking技术要求technical requirements刚度rigidity内力internal force位移displacement截面section疲劳极限fatigue limit断裂fracture塑性变形plastic distortion脆性材料brittleness material刚度准则rigidity criterion垫圈washer垫片spacer直齿圆柱齿轮straight toothed spur gear 斜齿圆柱齿轮helical-spur gear直齿锥齿轮straight bevel gear运动简图kinematic sketch齿轮齿条pinion and rack蜗杆蜗轮worm and worm gear虚约束passive constraint曲柄crank摇杆racker凸轮cams共轭曲线conjugate curve范成法generation method定义域definitional domain值域range导数\\微分differential coefficient求导derivation定积分definite integral不定积分indefinite integral曲率curvature偏微分partial differential毛坯rough游标卡尺slide caliper千分尺micrometer calipers攻丝tap二阶行列式second order determinant 逆矩阵inverse matrix线性方程组linear equations概率probability随机变量random variable排列组合permutation and combination 气体状态方程equation of state of gas动能kinetic energy势能potential energy机械能守恒conservation of mechanical energy动量momentum桁架truss轴线axes余子式cofactor逻辑电路logic circuit触发器flip-flop脉冲波形pulse shape数模digital analogy液压传动机构fluid drive mechanism机械零件mechanical parts淬火冷却quench淬火hardening回火tempering调质hardening and tempering磨粒abrasive grain结合剂bonding agent砂轮grinding wheel后角clearance angle龙门刨削planing主轴spindle主轴箱headstock卡盘chuck加工中心machining center 车刀lathe tool车床lathe钻削镗削bore车削turning磨床grinder基准benchmark钳工locksmith锻forge压模stamping焊weld拉床broaching machine拉孔broaching装配assembling铸造found流体动力学fluid dynamics流体力学fluid mechanics加工machining液压hydraulic pressure切线tangent机电一体化mechanotronics mechanical-electrical integration气压air pressure pneumatic pressure稳定性stability介质medium液压驱动泵fluid clutch液压泵hydraulic pump阀门valve失效invalidation强度intensity载荷load应力stress安全系数safty factor可靠性reliability螺纹thread螺旋helix键spline销pin滚动轴承rolling bearing滑动轴承sliding bearing弹簧spring制动器arrester brake十字结联轴节crosshead联轴器coupling链chain皮带strap精加工finish machining粗加工rough machining变速箱体gearbox casing腐蚀rust氧化oxidation磨损wear耐用度durability随机信号random signal离散信号discrete signal超声传感器ultrasonic sensor 集成电路integrate circuit挡板orifice plate残余应力residual stress套筒sleeve扭力torsion冷加工cold machining电动机electromotor汽缸cylinder过盈配合interference fit热加工hotwork摄像头CCD camera倒角rounding chamfer优化设计optimal design工业造型设计industrial moulding design有限元finite element滚齿hobbing插齿gear shaping伺服电机actuating motor铣床milling machine钻床drill machine镗床boring machine步进电机stepper motor丝杠screw rod导轨lead rail组件subassembly可编程序逻辑控制器Programmable Logic Controller PLC电火花加工electric spark machining电火花线切割加工electrical discharge wire - cutting 相图phase diagram热处理heat treatment固态相变solid state phase changes有色金属nonferrous metal陶瓷ceramics合成纤维synthetic fibre电化学腐蚀electrochemical corrosion车架automotive chassis悬架suspension转向器redirector变速器speed changer板料冲压sheet metal parts孔加工spot facing machining车间workshop工程技术人员engineer气动夹紧pneuma lock数学模型mathematical model画法几何descriptive geometry机械制图Mechanical drawing投影projection视图view剖视图profile chart标准件standard component零件图part drawing装配图assembly drawing尺寸标注size marking技术要求technical requirements刚度rigidity内力internal force位移displacement截面section疲劳极限fatigue limit断裂fracture塑性变形plastic distortion脆性材料brittleness material刚度准则rigidity criterion垫圈washer垫片spacer直齿圆柱齿轮straight toothed spur gear 斜齿圆柱齿轮helical-spur gear直齿锥齿轮straight bevel gear运动简图kinematic sketch齿轮齿条pinion and rack蜗杆蜗轮worm and worm gear虚约束passive constraint曲柄crank摇杆racker凸轮cams共轭曲线conjugate curve范成法generation method定义域definitional domain值域range导数\\微分differential coefficient求导derivation定积分definite integral不定积分indefinite integral曲率curvature偏微分partial differential毛坯rough游标卡尺slide caliper千分尺micrometer calipers攻丝tap二阶行列式second order determinant 逆矩阵inverse matrix线性方程组linear equations概率probability随机变量random variable排列组合permutation and combination气体状态方程equation of state of gas动能kinetic energy势能potential energy机械能守恒conservation of mechanical energy 动量momentum桁架truss轴线axes余子式cofactor逻辑电路logic circuit触发器flip-flop脉冲波形pulse shape数模digital analogy液压传动机构fluid drive mechanism机械零件mechanical parts淬火冷却quench淬火hardening回火tempering调质hardening and tempering磨粒abrasive grain结合剂bonding agent砂轮grinding wheel Assembly line 组装线Layout 布置图Conveyer 流水线物料板Rivet table 拉钉机Rivet gun 拉钉枪Screw driver 起子Pneumatic screw driver 气动起子worktable 工作桌OOBA 开箱检查fit together 组装在一起fasten 锁紧(螺丝)fixture 夹具(治具)pallet 栈板barcode 条码barcode scanner 条码扫描器fuse together 熔合fuse machine热熔机repair修理operator作业员QC品管supervisor 课长ME 制造工程师MT 制造生技cosmetic inspect 外观检查inner parts inspect 内部检查thumb screw 大头螺丝lbs. inch 镑、英寸EMI gasket 导电条front plate 前板rear plate 后板chassis 基座bezel panel 面板power button 电源按键reset button 重置键Hi-pot test of SPS 高源高压测试Voltage switch of SPS 电源电压接拉键sheet metal parts 冲件plastic parts 塑胶件SOP 制造作业程序material check list 物料检查表work cell 工作间trolley 台车carton 纸箱sub-line 支线left fork 叉车personnel resource department 人力资源部production department生产部门planning department企划部QC Section品管科stamping factory冲压厂painting factory烤漆厂molding factory成型厂common equipment常用设备uncoiler and straightener整平机punching machine 冲床robot机械手hydraulic machine油压机lathe车床planer |plein|刨床miller铣床grinder磨床linear cutting线切割electrical sparkle电火花welder电焊机staker=reviting machine铆合机position职务president董事长general manager总经理special assistant manager特助factory director厂长department director部长deputy manager | =vice manager副理section supervisor课长deputy section supervisor =vice section superisor副课长group leader/supervisor组长line supervisor线长assistant manager助理to move, to carry, to handle搬运be put in storage入库pack packing包装to apply oil擦油to file burr 锉毛刺final inspection终检to connect material接料to reverse material 翻料wet station沾湿台Tiana天那水cleaning cloth抹布to load material上料to unload material卸料to return material/stock to退料scraped |\\'skr?pid|报废scrape ..v.刮;削deficient purchase来料不良manufacture procedure制程deficient manufacturing procedure制程不良oxidation |\\' ksi\\'dei?n|氧化scratch刮伤dents压痕defective upsiding down抽芽不良defective to staking铆合不良embedded lump镶块feeding is not in place送料不到位stamping-missing漏冲production capacity生产力education and training教育与训练proposal improvement提案改善spare parts=buffer备件forklift叉车trailer=long vehicle拖板车compound die合模die locker锁模器pressure plate=plate pinch压板bolt螺栓administration/general affairs dept总务部automatic screwdriver电动启子thickness gauge厚薄规gauge(or jig)治具power wire电源线buzzle蜂鸣器defective product label不良标签identifying sheet list标示单location地点present members出席人员subject主题conclusion结论decision items决议事项responsible department负责单位pre-fixed finishing date预定完成日approved by / checked by / prepared by核准/审核/承办PCE assembly production schedule sheet PCE组装厂生产排配表model机锺work order工令revision版次remark备注production control confirmation生产确认checked by初审approved by核准department部门stock age analysis sheet 库存货龄分析表on-hand inventory现有库存available material良品可使用obsolete material良品已呆滞to be inspected or reworked 待验或重工total合计cause description原因说明part number/ P/N 料号type形态item/group/class类别quality品质prepared by制表notes说明year-end physical inventory difference analysis sheet 年终盘点差异分析表physical inventory盘点数量physical count quantity帐面数量difference quantity差异量cause analysis原因分析raw materials原料materials物料finished product成品semi-finished product半成品packing materials包材good product/accepted goods/ accepted parts/good parts良品defective product/non-good parts不良品disposed goods处理品warehouse/hub仓库on way location在途仓oversea location海外仓spare parts physical inventory list备品盘点清单spare molds location模具备品仓skid/pallet栈板tox machine自铆机wire EDM线割EDM放电机coil stock卷料sheet stock片料tolerance工差score=groove压线cam block滑块pilot导正筒trim剪外边pierce剪内边drag form压锻差pocket for the punch head挂钩槽slug hole废料孔feature die公母模expansion dwg展开图radius半径shim(wedge)楔子torch-flame cut火焰切割set screw止付螺丝form block折刀stop pin定位销round pierce punch=die button圆冲子shape punch=die insert异形子stock locater block定位块under cut=scrap chopper清角active plate活动板baffle plate挡块cover plate盖板male die公模female die母模groove punch压线冲子air-cushion eject-rod气垫顶杆spring-box eject-plate弹簧箱顶板bushing block衬套insert 入块club car高尔夫球车capability能力parameter参数factor系数phosphate皮膜化成viscosity涂料粘度alkalidipping脱脂main manifold主集流脉bezel斜视规blanking穿落模dejecting顶固模demagnetization去磁;消磁high-speed transmission高速传递heat dissipation热传rack上料degrease脱脂rinse水洗alkaline etch龄咬desmut剥黑膜D.I. rinse纯水次Chromate铬酸处理Anodize阳性处理seal封孔revision版次part number/P/N料号good products良品scraped products报放心品defective products不良品finished products成品disposed products处理品barcode条码flow chart流程表单assembly组装stamping冲压molding成型spare parts=buffer备品coordinate座标dismantle the die折模auxiliary fuction辅助功能poly-line多义线heater band 加热片thermocouple热电偶sand blasting喷沙grit 砂砾derusting machine除锈机degate打浇口dryer烘干机induction感应induction light感应光response=reaction=interaction感应ram连杆edge finder巡边器concave凸convex凹short射料不足nick缺口speck瑕??shine亮班splay 银纹gas mark焦痕delamination起鳞cold slug冷块blush 导色gouge沟槽;凿槽satin texture段面咬花witness line证示线patent专利grit沙砾granule=peuet=grain细粒grit maker抽粒机cushion缓冲magnalium镁铝合金magnesium镁金metal plate钣金lathe车mill锉plane刨grind磨drill铝boring镗blinster气泡fillet镶;嵌边through-hole form通孔形式voller pin formality滚针形式cam driver铡楔shank摸柄crank shaft曲柄轴augular offset角度偏差velocity速度production tempo生产进度现状torque扭矩spline=the multiple keys花键quenching淬火tempering回火annealing退火carbonization碳化tungsten high speed steel钨高速的moly high speed steel钼高速的organic solvent有机溶剂bracket小磁导liaison联络单volatile挥发性resistance电阻ion离子titrator滴定仪beacon警示灯coolant冷却液crusher破碎机阿基米德蜗杆Archimedes worm安全系数safety factor; factor of safety 安全载荷safe load凹面、凹度concavity扳手wrench板簧flat leaf spring半圆键woodruff key变形deformation摆杆oscillating bar摆动从动件oscillating follower摆动从动件凸轮机构cam with oscillating follower 摆动导杆机构oscillating guide-bar mechanism 摆线齿轮cycloidal gear摆线齿形cycloidal tooth profile摆线运动规律cycloidal motion摆线针轮cycloidal-pin wheel包角angle of contact保持架cage背对背安装back-to-back arrangement背锥back cone ;normal cone背锥角back angle背锥距back cone distance比例尺scale比热容specific heat capacity闭式链closed kinematic chain闭链机构closed chain mechanism臂部arm变频器frequency converters变频调速frequency control of motor speed变速speed change变速齿轮change gear change wheel变位齿轮modified gear变位系数modification coefficient标准齿轮standard gear标准直齿轮standard spur gear表面质量系数superficial mass factor表面传热系数surface coefficient of heat transfer 表面粗糙度surface roughness并联式组合combination in parallel并联机构parallel mechanism并联组合机构parallel combined mechanism并行工程concurrent engineering并行设计concurred design, CD不平衡相位phase angle of unbalance不平衡imbalance (or unbalance)不平衡量amount of unbalance不完全齿轮机构intermittent gearing波发生器wave generator波数number of waves补偿compensation参数化设计parameterization design, PD残余应力residual stress操纵及控制装置operation control device槽轮Geneva wheel槽轮机构Geneva mechanism ;Maltese cross槽数Geneva numerate槽凸轮groove cam侧隙backlash差动轮系differential gear train差动螺旋机构differential screw mechanism差速器differential常用机构conventional mechanism; mechanism in common use车床lathe承载量系数bearing capacity factor承载能力bearing capacity成对安装paired mounting尺寸系列dimension series齿槽tooth space齿槽宽spacewidth齿侧间隙backlash齿顶高addendum齿顶圆addendum circle齿根高dedendum齿根圆dedendum circle齿厚tooth thickness齿距circular pitch齿宽face width齿廓tooth profile齿廓曲线tooth curve齿轮gear齿轮变速箱speed-changing gear boxes齿轮齿条机构pinion and rack齿轮插刀pinion cutter; pinion-shaped shaper cutter 齿轮滚刀hob ,hobbing cutter齿轮机构gear齿轮轮坯blank齿轮传动系pinion unit齿轮联轴器gear coupling齿条传动rack gear齿数tooth number齿数比gear ratio齿条rack齿条插刀rack cutter; rack-shaped shaper cutter齿形链、无声链silent chain齿形系数form factor齿式棘轮机构tooth ratchet mechanism插齿机gear shaper重合点coincident points重合度contact ratio冲床punch传动比transmission ratio, speed ratio传动装置gearing; transmission gear传动系统driven system传动角transmission angle传动轴transmission shaft串联式组合combination in series串联式组合机构series combined mechanism 串级调速cascade speed control创新innovation creation创新设计creation design垂直载荷、法向载荷normal load唇形橡胶密封lip rubber seal磁流体轴承magnetic fluid bearing从动带轮driven pulley从动件driven link, follower从动件平底宽度width of flat-face从动件停歇follower dwell从动件运动规律follower motion从动轮driven gear粗线bold line粗牙螺纹coarse thread大齿轮gear wheel打包机packer打滑slipping带传动belt driving带轮belt pulley带式制动器band brake单列轴承single row bearing单向推力轴承single-direction thrust bearing单万向联轴节single universal joint单位矢量unit vector当量齿轮equivalent spur gear; virtual gear当量齿数equivalent teeth number; virtual number of teeth当量摩擦系数equivalent coefficient of friction当量载荷equivalent load刀具cutter导数derivative倒角chamfer导热性conduction of heat导程lead导程角lead angle等加等减速运动规律parabolic motion; constant acceleration and deceleration motion等速运动规律uniform motion; constant velocity motion 等径凸轮conjugate yoke radial cam等宽凸轮constant-breadth cam等效构件equivalent link等效力equivalent force等效力矩equivalent moment of force等效量equivalent等效质量equivalent mass等效转动惯量equivalent moment of inertia等效动力学模型dynamically equivalent model底座chassis低副lower pair点划线chain dotted line(疲劳)点蚀pitting垫圈gasket垫片密封gasket seal碟形弹簧belleville spring顶隙bottom clearance定轴轮系ordinary gear train; gear train with fixedaxes动力学dynamics动密封kinematical seal动能dynamic energy动力粘度dynamic viscosity动力润滑dynamic lubrication动平衡dynamic balance动平衡机dynamic balancing machine动态特性dynamic characteristics动态分析设计dynamic analysis design动压力dynamic reaction动载荷dynamic load端面transverse plane端面参数transverse parameters端面齿距transverse circular pitch端面齿廓transverse tooth profile端面重合度transverse contact ratio端面模数transverse module端面压力角transverse pressure angle锻造forge对称循环应力symmetry circulating stress对心滚子从动件radial (or in-line ) roller follower对心直动从动件radial (or in-line ) translating follower 对心移动从动件radial reciprocating follower对心曲柄滑块机构in-line slider-crank (or crank-slider) mechanism多列轴承multi-row bearing多楔带poly V-belt多项式运动规律polynomial motion多质量转子rotor with several masses惰轮idle gear额定寿命rating life额定载荷load ratingII 级杆组dyad发生线generating line发生面generating plane法面normal plane法面参数normal parameters法面齿距normal circular pitch法面模数normal module法面压力角normal pressure angle法向齿距normal pitch法向齿廓normal tooth profile法向直廓蜗杆straight sided normal worm法向力normal force反馈式组合feedback combining反向运动学inverse ( or backward) kinematics反转法kinematic inversion反正切Arctan范成法generating cutting仿形法form cutting方案设计、概念设计concept design, CD防振装置shockproof device飞轮flywheel飞轮矩moment of flywheel非标准齿轮nonstandard gear非接触式密封non-contact seal非周期性速度波动aperiodic speed fluctuation非圆齿轮non-circular gear粉末合金powder metallurgy分度线reference line; standard pitch line分度圆reference circle; standard (cutting) pitch circle 分度圆柱导程角lead angle at reference cylinder分度圆柱螺旋角helix angle at reference cylinder分母denominator分子numerator分度圆锥reference cone; standard pitch cone 分析法analytical method封闭差动轮系planetary differential复合铰链compound hinge复合式组合compound combining复合轮系compound (or combined) gear train 复合平带compound flat belt复合应力combined stress复式螺旋机构Compound screw mechanism复杂机构complex mechanism杆组Assur group干涉interference刚度系数stiffness coefficient刚轮rigid circular spline钢丝软轴wire soft shaft刚体导引机构body guidance mechanism刚性冲击rigid impulse (shock)刚性转子rigid rotor刚性轴承rigid bearing刚性联轴器rigid coupling高度系列height series高速带high speed belt高副higher pair格拉晓夫定理Grashoff`s law根切undercutting公称直径nominal diameter高度系列height series功work工况系数application factor工艺设计technological design工作循环图working cycle diagram工作机构operation mechanism工作载荷external loads工作空间working space工作应力working stress工作阻力effective resistance工作阻力矩effective resistance moment 公法线common normal line公共约束general constraint公制齿轮metric gears功率power功能分析设计function analyses design 共轭齿廓conjugate profiles共轭凸轮conjugate cam构件link鼓风机blower固定构件fixed link; frame固体润滑剂solid lubricant关节型操作器jointed manipulator惯性力inertia force惯性力矩moment of inertia ,shaking moment 惯性力平衡balance of shaking force惯性力完全平衡full balance of shaking force惯性力部分平衡partial balance of shaking force 惯性主矩resultant moment of inertia惯性主失resultant vector of inertia冠轮crown gear广义机构generation mechanism广义坐标generalized coordinate轨迹生成path generation轨迹发生器path generator滚刀hob滚道raceway滚动体rolling element滚动轴承rolling bearing滚动轴承代号rolling bearing identification code滚针needle roller滚针轴承needle roller bearing滚子roller滚子轴承roller bearing滚子半径radius of roller滚子从动件roller follower滚子链roller chain滚子链联轴器double roller chain coupling 滚珠丝杆ball screw滚柱式单向超越离合器roller clutch过度切割undercutting函数发生器function generator函数生成function generation含油轴承oil bearing耗油量oil consumption耗油量系数oil consumption factor赫兹公式H. Hertz equation合成弯矩resultant bending moment合力resultant force合力矩resultant moment of force黑箱black box横坐标abscissa互换性齿轮interchangeable gears花键spline滑键、导键feather key滑动轴承sliding bearing滑动率sliding ratio滑块slider环面蜗杆toroid helicoids worm环形弹簧annular spring缓冲装置shocks; shock-absorber灰铸铁grey cast iron回程return回转体平衡balance of rotors混合轮系compound gear train积分integrate机电一体化系统设计mechanical-electrical integration system design机构mechanism机构分析analysis of mechanism机构平衡balance of mechanism机构学mechanism机构运动设计kinematic design of mechanism机构运动简图kinematic sketch of mechanism机构综合synthesis of mechanism机构组成constitution of mechanism机架frame, fixed link机架变换kinematic inversion机器machine机器人robot机器人操作器manipulator机器人学robotics技术过程technique process技术经济评价technical and economic evaluation 技术系统technique system机械machinery机械创新设计mechanical creation design, MCD 机械系统设计mechanical system design, MSD机械动力分析dynamic analysis of machinery机械动力设计dynamic design of machinery机械动力学dynamics of machinery机械的现代设计modern machine design机械系统mechanical system机械利益mechanical advantage机械平衡balance of machinery机械手manipulator机械设计machine design; mechanical design机械特性mechanical behavior机械调速mechanical speed governors机械效率mechanical efficiency机械原理theory of machines and mechanisms机械运转不均匀系数coefficient of speed fluctuation 机械无级变速mechanical stepless speed changes 基础机构fundamental mechanism基本额定寿命basic rating life基于实例设计case-based design,CBD基圆base circle基圆半径radius of base circle基圆齿距base pitch基圆压力角pressure angle of base circle基圆柱base cylinder基圆锥base cone急回机构quick-return mechanism急回特性quick-return characteristics急回系数advance-to return-time ratio急回运动quick-return motion棘轮ratchet棘轮机构ratchet mechanism棘爪pawl极限位置extreme (or limiting) position极位夹角crank angle between extreme (or limiting) positions计算机辅助设计computer aided design, CAD计算机辅助制造computer aided manufacturing, CAM计算机集成制造系统computer integrated manufacturing system, CIMS计算力矩factored moment; calculation moment计算弯矩calculated bending moment加权系数weighting efficient加速度acceleration加速度分析acceleration analysis加速度曲线acceleration diagram尖点pointing; cusp尖底从动件knife-edge follower间隙backlash间歇运动机构intermittent motion mechanism减速比reduction ratio减速齿轮、减速装置reduction gear减速器speed reducer减摩性anti-friction quality渐开螺旋面involute helicoid渐开线involute渐开线齿廓involute profile渐开线齿轮involute gear渐开线发生线generating line of involute 渐开线方程involute equation渐开线函数involute function渐开线蜗杆involute worm渐开线压力角pressure angle of involute 渐开线花键involute spline简谐运动simple harmonic motion键key键槽keyway交变应力repeated stress交变载荷repeated fluctuating load交叉带传动cross-belt drive交错轴斜齿轮crossed helical gears胶合scoring角加速度angular acceleration角速度angular velocity角速比angular velocity ratio角接触球轴承angular contact ball bearing角接触推力轴承angular contact thrust bearing 角接触向心轴承angular contact radial bearing 角接触轴承angular contact bearing铰链、枢纽hinge校正平面correcting plane接触应力contact stress接触式密封contact seal阶梯轴multi-diameter shaft结构structure结构设计structural design截面section节点pitch point节距circular pitch; pitch of teeth节线pitch line节圆pitch circle节圆齿厚thickness on pitch circle节圆直径pitch diameter节圆锥pitch cone节圆锥角pitch cone angle解析设计analytical design紧边tight-side紧固件fastener径节diametral pitch径向radial direction径向当量动载荷dynamic equivalent radial load径向当量静载荷static equivalent radial load径向基本额定动载荷basic dynamic radial load rating 径向基本额定静载荷basic static radial load tating径向接触轴承radial contact bearing径向平面radial plane径向游隙radial internal clearance径向载荷radial load径向载荷系数radial load factor径向间隙clearance静力static force静平衡static balance静载荷static load静密封static seal局部自由度passive degree of freedom矩阵matrix矩形螺纹square threaded form锯齿形螺纹buttress thread form矩形牙嵌式离合器square-jaw positive-contact clutch 绝对尺寸系数absolute dimensional factor绝对运动absolute motion绝对速度absolute velocity均衡装置load balancing mechanism 抗压强度compression strength开口传动open-belt drive开式链open kinematic chain开链机构open chain mechanism可靠度degree of reliability可靠性reliability可靠性设计reliability design, RD空气弹簧air spring空间机构spatial mechanism空间连杆机构spatial linkage空间凸轮机构spatial cam空间运动副spatial kinematic pair空间运动链spatial kinematic chain 空转idle宽度系列width series框图block diagram雷诺方程Reynolds‘s equation离心力centrifugal force离心应力centrifugal stress。
《机械设计基础》常用单词中英文对照
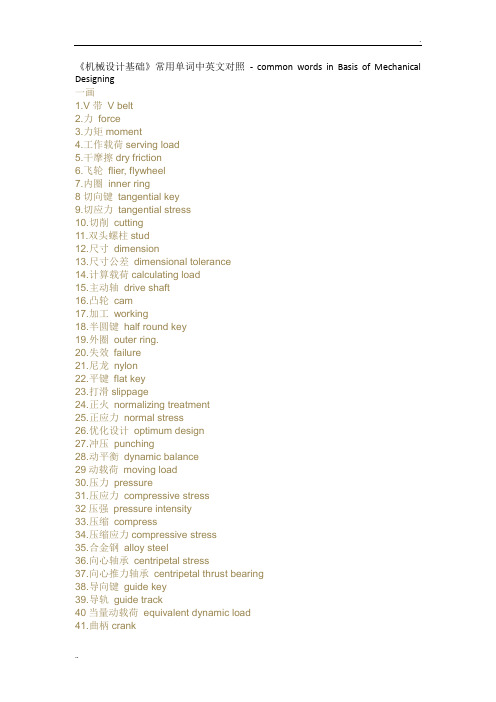
《机械设计基础》常用单词中英文对照- common words in Basis of Mechanical Designing一画1.V带V belt2.力force3.力矩moment4.工作载荷serving load5.干摩擦dry friction6.飞轮flier, flywheel7.内圈inner ring8切向键tangential key9.切应力tangential stress10.切削cutting11.双头螺柱stud12.尺寸dimension13.尺寸公差dimensional tolerance14.计算载荷calculating load15.主动轴drive shaft16.凸轮cam17.加工working18.半圆键half round key19.外圈outer ring.20.失效failure21.尼龙nylon22.平键flat key23.打滑slippage24.正火normalizing treatment25.正应力normal stress26.优化设计optimum design27.冲压punching28.动平衡dynamic balance29动载荷moving load30.压力pressure31.压应力compressive stress32压强pressure intensity33.压缩compress34.压缩应力compressive stress35.合金钢alloy steel36.向心轴承centripetal stress37.向心推力轴承centripetal thrust bearing38.导向键guide key39.导轨guide track40当量动载荷equivalent dynamic load41.曲柄 crank42.曲轴crank axle43.曲率半径curvature radius44.有色金属non ferrous metal45.机构mechanism46.机架framework47.机座machine base48.机械machine49.机械加工mechanical working50.机械零件machine element51.机器machine52.灰铸铁gray cast iron53.自锁self locking54.行星轮系planetary gear train55.许用应力allowable stress56.防松locking57.刨削planning58.寿命life59.应力stress60.应力集中stress concentration61.应变strain62.扭转torsion63扭转角angle of torsion64.抗压强度compression strength65抗拉强度tensile strength66.抗弯强度bending strength67.材料material68.极限应力limit stress69.极惯性矩polar moment of inertial70.花键spline71.连杆connecting rod72.周转轮系epicyclic gear train73.屈服强度yield strength74.底板base plate75.底座underframe76.径向力radial force77.径向当量动载荷radial equivalent dynamic load78.径向轴承journal bearing79.径向基本额定动载荷radial elementary rated life80.性能performance81.承载量load carrying capacity82.拉力pulling force83.拉伸tension84.拉伸应力tensile stress85.油膜oil film86.泊松比Poisson’s ratio87.直径diameter88.空心轴hollow axle89.空气轴承air bearing90表面处理surface treatment91.表面淬火surface quenching92转矩torque93.金属材料metallic material94.青铜合金bronze alloy95.非金属材料non metallic material96.齿轮gear97.齿轮模数module of gear teeth98.齿数tooth number99.保持架holding frame100.变应力dynamic stress101.变形deflection, deformation102.变载荷dynamic load103.轮系gear train104.垫片shim105.垫圈washer106.复合材料composite material107.带传动belt driving108.弯曲bend109.弯曲应力bending stress110.弯曲强度bending strength111.弯矩bending moment112.挡圈retaining ring113.残余应力residual stress114.残余变形residual deformation115.点蚀pitting116.相对运动relative motion117.相对滑动relative sliding118.相对滚动relative rolling motion119.矩形花键square key120.结构structure121.结构设计structural design121.结构钢structural steel122.耐磨性wearing quality123.脉动循环应力repeated stress124.轴shaft125.轴瓦bushing126.轴向力axial force127.轴向当量动载荷axial equivalent dynamic load 128.轴向基本额定动载荷axial elementary rated life129.轴承bearing130.轴承合金bearing metal131.轴承油沟grooves in bearing132.轴承衬bearing bush133.轴承座bearing block134.轴承盖bearing cap135.轴环axle ring136.轴肩shaft neck137.轴套shaft sleeve138.退刀槽tool escape139.钢材steel140.钩头楔键gib head key150.钩头螺栓gib head bolt151.挺杆tappet, tapper152.圆柱销cylindrical pin153.圆锥销cone pin154.圆螺母circular nut155.流体动力润滑hydrodynamic lubrication 156.流体静力润滑hydrostatic lubrication 157.润滑lubrication158.润滑油膜lubricant film159.热处理heat treatment160.热平衡heat balance161.疲劳fatigue162.疲劳失效fatigue failure163.疲劳寿命fatigue Life164.疲劳强度fatigue strength165.疲劳裂纹fatigue cracking166.离合器clutch167.紧定螺钉tightening screw168.胶合seizing of teeth169.能量energy170.脆性材料brittle material171.调质钢quenched and tempered steel 172.载荷load173.载荷谱load spectrum174.通用零件universal element175.速度velocity176.部件parts177.铆接riveting178.陶瓷ceramics179.预紧pretighten180.高速传动轴high speed drive shaft181.偏心载荷eccentric load182.偏转角deflection angle183.减速器reductor184.剪切应力shearing stress185.剪切应力shear stress186.基本额定动载荷elementary rated dynamic load 187.基本额定寿命elementary rated life188.密封seal189.密度density190.弹性变形elastic deformation191.弹性流体动力润滑elastohydrodynamic lubrication 192.弹性啮合elastic engagement193.弹性滑动elastic slippage194.弹性模量modulus of elasticity195.弹簧spring196.弹簧垫圈spring washer197.惯性力inertial force198.惯性矩moment of inertia199.接触应力contact stress200.接触角Contact Angle201.推力轴承thrust bearing202.断裂break203.液压hydraulic pressure204.混合润滑mixed lubrication205.渐开线花键involute spline206.焊接welding207.球形阀globe valve208.球墨铸铁nodular cast iron209.粗糙度roughness210.铜合金copper alloy211.铝合金aluminum alloy212.铰链hinge213.黄铜brass214.剩余预紧力residual initial tightening load215.喷丸sand blast216.强度strength217.强度极限ultimate strength218.最小油膜厚度minimum film thickness219.棘轮传动ratchet wheel220.滑动轴承sliding bearing221.滑块slide block222.滑键slide key223硬度hardness224.联轴器coupling225.装配assembly226.铸件casting227.铸钢cast steel228.铸造cast229.铸铁cast iron230.铸铝cast aluminum231.链chain232.链轮chain wheel233.销pin234.销钉联接pin connection235.塑性材料ductile material236.塑性变形plastic deformation 237.塑料plastics238.摇杆rocker239.楔键wedge key240.滚动体Rolling Body241.滚动轴承rolling bearing242.滚压rolling243.滚珠丝杆ball leading screw 244.锡青铜tin bronze245.锥形阀cone valve246.键key247.键槽keyways248.碳化carbonization249.碳素钢carbon steel250.稳定性stability251.腐蚀corrosion252.锻件forged piece253.锻钢forged steel254.锻造forging255.静压轴承hydrostatic bearing 256.静应力steady stress257.静载荷/应力static load/stress 258.摩擦friction259.摩擦力friction force260.摩擦功friction work261.摩擦系数friction coefficient 262.摩擦角friction angle263.摩擦学tribology264.槽轮sheave wheel265.橡胶rubber266.箱体box267.磨削grinding268.磨损wear269.磨损过程wear process270.螺母nut271.螺纹screw272.螺纹threads273.螺纹联接threaded and coupled 274.螺钉pitch275.螺栓bolt276.螺栓联接bolting277.螺旋传动screw-driven机械设计名词术语中英对照机械设计名词术语中英文对照表Chinese English阿基米德蜗杆Archimedes worm安全系数safety factor; factor of safety安全载荷safe load凹面、凹度concavity扳手wrench板簧flat leaf spring半圆键woodruff key变形deformation摆杆oscillating bar摆动从动件oscillating follower摆动从动件凸轮机构cam with oscillating follower 摆动导杆机构oscillating guide-bar mechanism摆线齿轮cycloidal gear摆线齿形cycloidal tooth profile摆线运动规律cycloidal motion摆线针轮cycloidal-pin wheel包角angle of contact保持架cage背对背安装back-to-back arrangement背锥back cone ;normal cone背锥角back angle背锥距back cone distance比例尺scale比热容specific heat capacity闭式链closed kinematic chain闭链机构closed chain mechanism臂部arm变频器frequency converters变频调速frequency control of motor speed变速speed change变速齿轮change gear ; change wheel变位齿轮modified gear变位系数modification coefficient标准齿轮standard gear标准直齿轮standard spur gear表面质量系数superficial mass factor表面传热系数surface coefficient of heat transfer 表面粗糙度surface roughness并联式组合combination in parallel并联机构parallel mechanism并联组合机构parallel combined mechanism并行工程concurrent engineering并行设计concurred design, CD不平衡相位phase angle of unbalance不平衡imbalance (or unbalance)不平衡量amount of unbalance不完全齿轮机构intermittent gearing波发生器wave generator波数number of waves补偿compensation参数化设计parameterization design, PD残余应力residual stress操纵及控制装置operation control device槽轮Geneva wheel槽轮机构Geneva mechanism ;Maltese cross 槽数Geneva numerate槽凸轮groove cam侧隙backlash差动轮系differential gear train差动螺旋机构differential screw mechanism差速器differential常用机构conventional mechanism; mechanism in common use车床lathe承载量系数bearing capacity factor承载能力bearing capacity成对安装paired mounting尺寸系列dimension series齿槽tooth space齿槽宽spacewidth齿侧间隙backlash齿顶高addendum齿顶圆addendum circle齿根高dedendum《机械设计基础》常用单词中英文对照寿命life应力stress应力集中stress concentration应变strain扭转torsion扭转角angle of torsion抗压强度compression strength抗拉强度tensile strength抗弯强度bending strength材料material极限应力limit stress极惯性矩polar moment of inertial花键spline连杆connecting rod周转轮系epicyclic gear train屈服强度yield strength底板base plate底座underframe径向力radial force径向当量动载荷radial equivalent dynamic load 径向轴承journal bearing径向基本额定动载荷radial elementary rated life 性能performance承载量load carrying capacity拉力pulling force拉伸tension拉伸应力tensile stress油膜oil film泊松比Poisson’s ratio直径diameter空心轴hollow axle空气轴承air bearing表面处理surface treatment表面淬火surface quenching转矩torque金属材料metallic material青铜合金bronze alloy非金属材料non metallic material齿轮gear齿轮模数module of gear teeth齿数tooth number保持架holding frame变应力dynamic stress变形deflection, deformation变载荷dynamic load。
机械毕设外文翻译
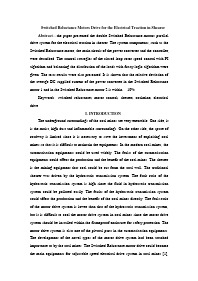
Switched Reluctance Motors Drive for the Electrical Traction in Shearer Abstract—the paper presented the double Switched Reluctance motors parallel drive system for the electrical traction in shearer. The system components, such as the Switched Reluctance motor, the main circuit of the power converter and the controller, were described. The control strategies of the closed-loop rotor speed control with PI algorithm and balancing the distribution of the loads with fuzzy logic algorithm were given. The tests results were also presented. It is shown that the relative deviation of the average DC supplied current of the power converter in the Switched Reluctance motor 1 and in the Switched Reluctance motor 2 is within 10%.Keywords- switched reluctance; motor control; shearer; coalmine; electrical drive.I. INTRODUCTIONThe underground surroundings of the coal mines are very execrable. One side, it is the moist, high dust and inflammable surroundings. On the other side, the space of roadway is limited since it is necessary to save the investment of exploiting coal mines so that it is difficult to maintain the equipments. In the modern coal mines, the automatization equipments could be used widely. The faults of the automatization equipments could affect the production and the benefit of the coal mines. The shearer is the mining equipment that coal could be cut from the coal wall. The traditional shearer was driven by the hydrostatic transmission system. The fault ratio of the hydrostatic transmission system is high since the fluid in hydrostatic transmission system could be polluted easily. The faults of the hydrostatic transmission system could affect the production and the benefit of the coal mines directly. The fault ratio of the motor drive system is lower than that of the hydrostatic transmission system, but it is difficult to cool the motor drive system in coal mines since the motor drive system should be installed within the flameproof enclosure for safety protection. The motor drive system is also one of the pivotal parts in the automatization equipments. The development of the novel types of the motor drive system had been attached importance to by the coal mines. The Switched Reluctance motor drive could become the main equipments for adjustable speed electrical drive system in coal mines [1],because it has the high operational reliability and the fault tolerant ability [2]. The Switched Reluctance motor drive made up of the double-salient pole Switched Reluctance motor, the unipolar power converter and the controller is firm in the motor and in the power converter. There is no brush structure in the motor and no fault of am bipolar power converter in the power converter [3][4]. The Switched Reluctance motor drive could be operated at the condition of lacked phases fault depended on the independence of each phase in the motor and the power converter [5]. There is no winding in the rotor so that there is no copper loss in the loss and there is only little iron loss in the rotor. It is easy to cool the motor since it is not necessary to cool the rotor. The shearer driven by theSwitched Reluctance motor drive had been developed. The paper presented the developed prototype.II. SYSTEM COMPONENTSThe developed SwitchedReluctance motors drive for the electrical traction in shearer is a type of the double Switched Reluctance motors parallel drive system. The system is made up of two Switched Reluctance motors; a control box installed the power converter and the controller. The adopted two Switched Reluctance motors are all three-phase 12/8 structure Switched Reluctance motor, which were shown in Figure 1. Figure1. Photograph of the two three-phase .12/8 structure Switched Reluctance motorThe two Switched Reluctance motors were packing by the explosion-proof enclosure, respectively. The rated output power of one motor is 40 KW at the rotor speed 1155 r/min, and the adjustable speed range is from 100 r/min to 1500r/min.The power converter consists of two three-phase asymmetric bridge power converter in parallel. The IGBTs were used as the main switches. Three-phase 380V AC power source was certificated and supplied to the power converter. The maincircuit of the power converter was shown in Figure 2.In the controller, there were the rotor position detection circuit, the commutation circuit, the current and voltage protection circuit, the main switches’ gate driver circuit and the digital controller for rotor speed closed-loop and balancing the distribution of the loads.III. CONTROL STRATEGYThe two Switched Reluctance motor could all drive the shearer by the transmission outfit in the same traction guide way so that the rotor speed of the two Switched Reluctance motors could be synchronized.The closed-loop rotor speed control of the double Switched Reluctance motors parallel drive system could be implemented by PI algorithm. In the Switched Reluctance motor 1, the triggered signals of the main switches in the power converter are modulated by PWM signal, the comparison of the given rotor speed and the practical rotor speed are made and the duty ratio of PWM signal are regulated as follows,1()11()1(1)1()e=()g fk i k p k k k k k n n D k e K e e D D D ---∆=+-=+∆where, ng is the given rotor speed, nf is the practical rotorspeed, e is the difference of the rotor speed, 1()k D ∆is the increment of the dutyratio of PWM signal of the Switched Reluctance motor 1 at k time, Ki is the integral coefficient, Kp is the proportion coefficient, ek is the difference of the rotor speed at k time, ek-1 is the difference of the rotor speed at k-1 time, D1(k) is the duty ratio of PWM signal of the Switched Reluctance motor 1 at k time, and D1(k-1) is the duty ratio of PWM signal of the Switched Reluctance motor 1 at k-1 time.The output power of the Switched Reluctance motordrive system is approximately in proportion to theaverage DC supplied current of the power converter asfollows, 2in p I ∝ where, P2 is the output power of the Switched Reluctance motor drive system, Iin is the average DC supplied current of the power converter.In the Switched Reluctance motor 2, the triggered signals of the main switches in the power converter are also modulated by PWM signal. The balancing the distribution of the loads between the two Switched Reluctance motors could be implemented by fuzzy logic algorithm. In the fuzzy logic regulator, there are two input control parameters, one is the deviation of the average DC supplied current of the power converter between the two Switched Reluctance motors, and the other is the variation of the deviation of the average DC supplied current of the power converter between the two Switched Reluctance motors. The output control parameter is the increment of the duty ratio of the PWM signal of the Switched Reluctance motor 2. The block diagram of the double Switched Reluctance motors parallel drive system for the electrical traction in shearer was shown in Figure 3.The deviation of the average DC supplied current ofthe power converter between the two Switched Reluctance motors at the moment of ti is12i in in e I I =-:.1i i i e e e -=- where, ei-1 is the deviation of the average DC suppliedcurrent of the power converter between the two SwitchedReluctance motors at the moment of ti-1. The duty ratio of the PWM signal of the Switched Reluctance motor 2 at the moment of ti is2()2(1)2()i i i D D D -=+∆where, 2()i D ∆ is the increment of the duty ratio of the PWM signal of theSwitched Reluctance motor 2 at the moment of ti and D2(i-1) is the duty ratio of the PWM signal of the Switched Reluctance motor 2 at the moment of ti-1.The fuzzy logic algorithm could be expressed asfollows,if ~~if E i E = and ~~EC j E C = then U~ ~~U U U =i = 1,2,…, m, j = 1,2, …,nwhere, E~ is the fuzzy set of the deviation of the average DC supplied current of the power converter between the two Switched Reluctance motors, E~C is the fuzzy set of the variation of the deviation of the average DC supplied current of the power converter between the two Switched Reluctance motors, and U~ is the fuzzy set of the increment of the duty ratio of the PWM signal of the Switched Reluctance motor 2.The continuous deviation of the average DC supplied current of the powerconverter between the two Switched Reluctance motors could be changed into the discrete amount at the interval [-5, +5], based on the equations as follows,[]10220e i e e INT K e K ==The discrete increment of the duty ratio of PWM signal of the Switched Reluctance motor 2 at the interval [-5, +5] could be changed into the continuous amount at the interval [-1.0%, +1.0%], based on the equations as follows,12()[]100.02i D D D INT K D K -==There is a decision forms of the fuzzy logic algorithm based on the above principles, which was stored in the programme storage cell of the controller.While the difference of the distribution of the loads between the two Switched Reluctance motors could be got, the duty ratio of PWM signal of the Switched Reluctance motor 2 will be regulated based on the decision forms of the fuzzy logic algorithm and the distribution of the loads between the two Switched Reluctance motors could be balanced.IV. TESTED RESULTSThe developed double Switched Reluctance motors parallel drive system prototype had been tested experimentally. Table I gives the tests results, where 1σis the relative deviation of the average DC supplied current of the power converter in the Switched Reluctance motor 1, 2σis the relative deviation of the average DC supplied current of the power converter in the Switched Reluctance motor 2, and,1211122100%2in in in in in I I I I I σ+-=⨯+ 1222122100%2in in in in in I I I σ+-=⨯It is shown that the relative deviation of the average DC supplied current of the power converter in the SwitchedReluctance motor 1 and in the Switched Reluctance motor2 is within 10%V. CONCLUSIONThe paper presented the double Switched Reluctance motors parallel drive system for the electrical traction in shearer. The novel type of the shearer in coal mines driven by the Switched Reluctance motors drive system contributes to reduce the fault ratio of the shearer, enhance the operational reliability of the shearer and increase the benefit of the coal mines directly. The drive type of the double Switched Reluctance motors parallel drive system could also contribute to enhance the operational reliability compared with the drive type of the single Switched Reluctance motor drive system.中文翻译:关磁阻电动机驱动电牵引采煤机摘要-本文介绍了双开关磁阻电动机并联传动系统控制驱动电牵引采煤机。
机械专业毕业设计外文翻译相关外文文献

A new driver based on dual-mode frequency and phase control for traveling-wave type ultrasonic motorTien-Chi Chen a,*,Chih-Hsien Yu a ,Mi-Ching Tsai ba Department of Engineering Science,National Cheng Kung University,Tainan,Taiwan bDepartment of Mechanical Engineering,National Cheng Kung University,Tainan,Taiwana r t i c l e i n f o Article history:Received 6August 2007Accepted 24March 2008Available online 12May 2008Keywords:Ultrasonic motorFrequency and phase modulation controla b s t r a c tA mode conversion rotary traveling-wave ultrasonic motor (TWUSM)has potential applications in min-iature robotics.However,its electrical drive circuit presents unique challenges,particularly in producing a high frequency (about 40kHz),high voltage (400V peak-to-peak)signal input to a low impedance capacitive motor,while achieving high efficiency.A novel driving circuit is proposed to provide two-phase balance voltage for a TWUSM.This paper describes the design of TWUSM drive circuit,intended for simultaneously employs both the driving frequency and phase modulation control scheme.The oper-ating principles and a detailed analysis of the proposed driving circuit,consisting of voltage-controlled oscillator (VCO),voltage-controlled phase-shifter circuit and power amplifier circuit,are introduced.To drive the USM effectively a two-phase power amplifier converter using non-resonant technique was designed to provide a balanced two-phase voltage source,and the two-phase output driving voltages could be maintained at the same peak voltage value at the driving frequency under varying phase-mod-ulation processes.Detailed experimental results are provided to demonstrate the effectiveness of the pro-posed driving circuit.Crown Copyright Ó2008Published by Elsevier Ltd.All rights reserved.1.IntroductionThe ultrasonic motor (USM)has many excellent performance features,including high-retention torque,high torque at low speed,silence,compactness in size,and no electromagnetic inter-ference.The USM has been used in a number of industrial,medical,space,robotic,and automotive applications.The driving principles of the USM are high-frequency mechani-cal vibrations and frictional force and its mathematical model is thus difficult to derive.As a result,a lumped motor model of the USM is presently unavailable [1].Moreover,the control character-istics of the USM are complicated and highly nonlinear,as motor parameters are time-varying,owing to increases in temperature and changes in motor-drive operating conditions,such as driving frequency,source voltage and load.Basically,the speed of the TWUSM can be manipulated by con-trolling the frequency,phase difference and the voltage amplitude of the two sinusoidal voltage waveforms which input to the TWUSM.Many researchers have opted for the frequency of the sinusoidal voltage waveforms as the control variable [2–5].It can easily be controlled digitally and spans the entire allowable speed range of the TWUSM.Most TWUSMs contain a two-phase half-bridge series-resonant inverter with an approximated unityswitching frequency (f s )to resonant frequency (f o )ratio.According to the description in the previous paragraph,the quality factors of the two phases are different and time varying.Moreover,when the frequency ratio (f s /f o )of a series-resonant inverter approaches unity,the voltage gain varies severely with the variation of the quality factor [6].Thus,the two-phase sinusoid output voltages are unbalanced under the same switching frequency.Conse-quently,good dynamic performance of the USM is difficult to ob-tain due to the variation in the unbalanced peak values of the two-phase voltages.By contrast,a voltage amplitude control strat-egy using additional boost choppers was employed in [7].Each chopper–inverter driving circuit is composed of one boost chopper cascading with one half-bridge series-resonant parasitic load impedance inverter.Since the two phase constructions of the USM are coupled mechanically and the reaction from the electrical to the mechanical part is unbalanced for both phases,the equiva-lent two-phase loads of the rotor are unbalanced and varied for dif-ferent rotating directions,rotor speeds,load torque,applied voltages and static pressure force between stator and rotor.In addition,the internal two-phase blocking capacitors of the USM are unbalanced and will vary in value under different rotational directions.As a result,it is difficult maintain the two-phase sinu-soid output voltages at the same constant peak value at the same switching frequency.However,a driving circuit proposed by Lin and Kuo [8]operates within working limits where the inverter voltage gain is greatly affected by the variation of the quality0196-8904/$-see front matter Crown Copyright Ó2008Published by Elsevier Ltd.All rights reserved.doi:10.1016/j.enconman.2008.03.023*Corresponding author.E-mail address:tchichen@.tw (T.-C.Chen).Energy Conversion and Management 49(2008)2767–2775Contents lists available at ScienceDirectEnergy Conversion and Managementj ou r na l h om e pa ge :w w w.e lse vi e r.c om /lo c at e /en c on manfactor.Moreover,to resolve the difficulty of the amplitude varia-tion in the output voltages of the parallel-resonant inverter,an ex-tra energy feedback circuit is added to reduce the quality factors in the parallel-resonant circuit.However,the energy feedback circuit increases the complexity of the driving circuit.In addition to the use of a boost converter,a voltage amplitude control strategy may also be implemented using pulse-width mod-ulation(PWM).In[9],the voltage amplitude was adjusted by the forward and backward PWM method for position control of the TWUM.In[10],the voltage amplitude was adjusted by the ON–OFF PWM method for speed control.Both methods essentially adopted the same principle in which the modulation was used to control the ratio of the number of ultrasonic cycles within the for-ward-direction or on-time duration to the total number of ultra-sonic cycles,including the backward-direction or off-time duration.Such control methods cause intermittent operation of the TWUM,leading to the creation of severe audible noise.In order to suppress this audible noise,the PWM should be applied to each ultrasonic cycle[11].Given these limitations,a specific drive circuit control tech-nique is required.Hence,it is desirable to develop a novel drive system that solves these issues while supplying the necessary power with high efficiency.Compared to work on drive circuit design for TWUSM based on the phase difference between the two-phase voltages,less research has been done in other areas of drive circuit design for TWUSM. Only the phase difference control strategy offers the advantage of bidirectional rotation,while the other two parameters of the con-trol scheme,frequency and voltage amplitude,need the assistance of phase-shift change between p/2toÀp/2.In the design of modern drive circuits with adjustable phase dif-ferences,a low-cost and simple phase shifter circuit providing two-phase signals of two-phase voltage source is a critical design issue. The motivation of this study is to design a novel driving scheme that simultaneously employs both the driving frequency and phase difference as dual-mode control variables to handle system nonlin-earities and parameter variations.In order to reduce the system hardware size and cost,the proposed phase shifter circuit is imple-mented by using a voltage-controlled resistance(VCR)and all-pass filter circuit that can provide piecewise-linear phase control over the entire speed range.In the conventional series and parallel resonant converter archi-tecture,two inductances must be inserted in parallel or series with the load for each phase,respectively,in order to become resonant with the inherent two-phase parasitic capacitances of the USM. Moreover,the motor parameters of the USM are dependent on the operating temperature,the running time,and the load.In addi-tion,the equivalent two-phase loads of the rotor are also unbal-anced and the equivalent resistor values vary for different operating conditions.Therefore the quality factors of the resonant inverters in two-phase are unequal and time-varying,resulting in the consumption of time to determine suitable RLC tank compo-nents.In contrast with conventional series and parallel resonant converters with two reactive components,the power amplifier circuit in this study is implemented to build high-frequency two-phase high drive voltages for USM(e.g.400V peak to peak) and is not in need of additional reactive components or a compli-cated energy feedback circuit.Although the quality factors of the two RLC tanks vary at different rotating speeds and are not equal, the output driving voltage of the proposed power amplifier circuit in two-phase can be maintained at the same peak voltage value when the driving frequency is operated close to the resonant frequency.In this paper,the design of a novel phase shifter circuit for applying TWUSM driving is presented.For a USM prototype,the operating principles and characteristics at the operating conditions will be also briefly described.Next,the novel driving circuit for the TWUSM,which contains VCO,VCR,voltage-controlled phase shif-ter,and power amplifier driving circuit,is introduced.The results of experiments investigating the effectiveness of the proposed dri-ver are given in Section4.Finally,a discussion and conclusions are provided in Section5.2.Operating principle and characteristicIn the operation of the TWUSM,a two-stage energy conversion is formed.Thefirst stage consists of the electro-mechanical energy conversion where the electrical energy is converted into mechani-cal energy.This is achieved by excitation of the piezoelectric cera-mic by ultrasonic range frequency.The second stage comprises mechanical energy conversion where the mechanical vibrations are converted to linear or rotary motion by the friction force gen-erated in the stator–rotor interface.Fig.1illustrates the operating principles of the TWUSM.The stator,designed with comb-tooth surface,is attached above the sectors of piezoelectric elements. The piezoelectric elements are divided into sectors instead of form-ing a complete ring so that they can be applied with different voltages.The rotor is pressed against the stator by means of a pressure spring disc.It should be noted that the spring as shown is for illus-tration only,since in reality it is not a normal spring,but a pressure disc.The operating principle of the TWUSM is based on the mechanical vibrations of the piezoelectric elements.As a result of voltages applied to them,they produce a traveling wave in the sta-tor.The surface interaction between the stator and the rotor cre-ates a driving torque in the rotor.As shown in Fig.1, piezoelectric elements are positioned at an appropriate distance from one another.One is produces a mechanical vibration by being fed by the phase-A voltage source V m sin x t,while the other is fed by the phase-B voltage source V m sin(x t+U),generating another vibration,where V m is the amplitude,x=2p f is the angular version of frequency f,and U is the phase difference of the two driving volt-age sources.Each voltage source generates a mode of vibration throughout the stator,and the superposition of them forms a trav-eling wave that propagates along the stator.Depending on which phase of the voltage leads the other,the traveling wave will travel in either a right or left direction.Elliptical motion can be observed at the wave peak of the surface of the stator.Such motion produces a tangential force at the contact surface between the stator and the rotor.With a spring disc to keep the rotor in pressure contact with the stator,the rotor can be driven to travel in the opposite direc-tion from the traveling wave by this tangential force at the contactsurface.Fig.1.TWUSM operating principle[1].2768T.-C.Chen et al./Energy Conversion and Management49(2008)2767–2775The speed of the USM is controlled by:Frequency of two-phase voltages.Amplitude of two-phase voltages.Phase difference between two-phase voltages.3.Drive circuit designFig.2shows actual configuration view of a typical USR-60circu-lar traveling wave type motor(from Shinsei of Japan),in which the specification is a40kHz,0.32Nm,3W,120rev/min type motor. The operation of a mode conversion USM is based on the torque generated by piezoelectric ultrasonic vibrations.An optimal supply voltage for the USM is a sinusoidal voltage with frequency near the mechanical resonance frequency of the stator–rotor assembly. Since this USM presents a large capacitive load and requires a high operating frequency(40kHz),its equivalent impedance could be extremely low.This USM also requires a high drive voltage (400V peak-to-peak),which leads to a large drive current.The goals for drive circuit design are to satisfy these require-ments,as well as achieve high power efficiency and reduce the sys-tem hardware size and cost.In the design of modern drive circuit with adjustable phase difference,the key technology is a low-cost and simple phase shifter circuit,provided two-phase signals from a two-phase voltage source.The purpose of this study is to design a novel driving scheme that simultaneously employs both the driv-ing frequency and phase difference as the dual-mode control vari-ables to handle system nonlinearities and parameter variations. The block diagram of the driving circuit is shown in Fig.3.This cir-cuit is composed of voltage-controlled oscillator(VCO),voltage-controlled phase shifter,power amplifier,and transformer.The design procedures of the proposed drive system are described in detail below.3.1.Voltage-controlled oscillatorThe ICL8038waveform generator is a monolithic integrated cir-cuit capable of producing high accuracy sine,square,triangular, sawtooth,and pulse waveforms with a minimum of external com-ponents[12].The frequency(or repetition rate)can be selected externally from0.001Hz to more than300kHz using either resis-tors or capacitors,and frequency modulation and sweeping can be accomplished with an external frequency-modulated voltage(V f). The frequency of the waveform generator is a direct function of the DC voltage at Terminal8,shown in Fig.4.By altering this volt-age,frequency modulation is performed by means of a voltage-controlled oscillator(VCO).To clarify the relation between the frequency-modulated voltage and the magnitude of the single fre-quency,experimental measurements were made at different volt-age values in Fig.5.Fig.5shows that this characteristic is quite linear.In this study,motor speed is controlled at40–44kHz,which may be considered the linear frequency range.3.2.Voltage-controlled phase shifterFig.6shows afirst-order all-passfilter with a junctionfield-effect transistor(JFET)used as a variable resistor to control the pole and zero time constants in thefilter transfer function.Let VCR R eq be the resistance of the JFET.If we assume that this is a linear resis-tor,the transfer function isTðsÞ¼V oi¼s sÀ1ð1Þwhere the time constant s is given by s=R eq C.By varying the gate-source voltage of JFET(V GS),i.e.the phase-modulated voltage(V p)in Fig.3,the resistance of the JFET can be varied,which in turn changes the time constant s.For s=j x,the phase difference of the transfer function is therefore\Tðj xÞ¼À2tanÀ1x R eq Cð2ÞFig.2.The photograph of experimentalsetup.The magnitude of the transfer function (j T (j x )j )is 1for all fre-quency x .The phase displacement not only depends on the oper-ating frequency of the TWUSM but is also affected by the timeconstant (s ).At different frequencies,between 41and 44kHz,the voltage signal (V i )applied to the USM,the VCR (R eq )drifting through the control voltage (V GS ),and the relationship between them were measured (Table 1).At a specific resonant frequency (f o =41kHz),the goals for phase shifter circuit designed to adjust the phase differential from Àp /2to Àp rad.Fig.6shows a general all-pass filter circuit.The circuit is composed of a resistor,a capac-itor,and an operational amplifier.The frequency of the input signalfor the circuit has to be near the resonant frequency of the TWUSM.We inset the VCR instead of the resistor,and adjusted the proper-ties of the circuit components (R =10k X ,C =0.01l F).As a result,when the operating frequency equal the resonant frequency (f o )and the control voltage minimizes as zero (V GS =0),the phase dis-placement reaches Àp /2rad,i.e.x R eq C =1.Conversely,if the R eq is increased in small increments,the phase difference gradually diminishes.3.3.Voltage-controlled resistanceVoltage-controlled filter,voltage-controlled oscillators,and voltage-to-time period/frequency converters have been applied in many instrumentation and measurement situations.A simple way to realize such circuits is to start from known circuits and then replace resistors by voltage-controlled resistances (VCR).Schemes to construct such VCR using FET’s are known in literature [13].Fig.4.A voltage-controlled oscillatorcircuit.Fig. 5.The measured relation between controlled voltage and output single frequency.Table 1Measurement results of V GS versus R eq V GS (V)0À0.2À0.4À0.6À0.8À1.0R eq (X )357.1416.7471.7531.9617.3746.3V GS (V)À1.2À1.4À1.6À1.8À2.0À2.2R eq (X )943.4128219233846291661Fig.8.FET output characteristics (K30A).2770T.-C.Chen et al./Energy Conversion and Management 49(2008)2767–2775The VCR configuration is shown in Fig.7.A routine analysis of the circuit shows that when the FET is confined to operate in a non-saturated region under the same constraints as in [13,14],the output characteristic of the FET may be represented by a qua-dratic function given by I DS ¼I DSS V p½2ðV GS ÀV p ÞV DS ÀV 2DSð3Þwhere I DSS and V p are saturation current and pinch-off voltage,respectively.The implementation of the voltage-tunable resistance can be simplified by neglecting the V 2DS term of Eq.(3),in which case R eq would be R eq¼V DS DS %V 2pDSS GS p ;providedV DS <j 0:5jð4ÞA typical set of characteristics obtained experimentally for an n-channel JFET (K30A)is shown in Fig.8.The range of values includes those prescribed in [14]as well as larger values,to show the nonlinear nature of these curves.Clearly if thisfield-effectFig.9.Phase displacement against controlvoltage.Fig.10.Measured results of the divergent index coefficient under difference ope-rating control voltage.Fig.12.Generated signals of phase-shifted circuit.(a)Phase difference set at p /2rad (b)p /3(c)p /6(d)0(e)Àp /6(f)Àp /3(g)Àp /2.Fig.13.Measured results of the phase shifter circuit under difference operating driving frequency.T.-C.Chen et al./Energy Conversion and Management 49(2008)2767–27752771transistor(FET)is to be used as a bidirectional linear resistor,j V DS j should be kept low,at least less than500mV,particularly for prac-tical circuit applications.For the relationship between the phase displacement angle(U) and the control voltage(V GS),the analysis of the phase shifter cir-cuit should yield the following results by observing the phase dis-placement versus control voltage curve in Fig.9x R eq C%tanðaV GSþbÞð5ÞUsing Eq.(5)to simplify Eq.(2),the following relationship results:\T¼À2ðaVGSþbÞð6Þwhere the constants a and b are calculated to define as a=À0.3865, b=p/4,and were used in the verifications below.Note that,as ex-pected,even nonlinearities do not appear in Eq.(6),as they are can-celed out.In the following,we test the divergence between the theoretical formula and experimental data and also define the divergent index coefficient D(the ratio of the phase value according to Eq.(6)di-vided by the actual phase displacement relating to Eq.(2)of exper-imental data)asD¼À2ðaV GSþbÞÀ2tanÀ1ðx R eq CÞð7ÞTo illustrate the difference between(2)and(6),actual and esti-mated UÀV GS curves using both schemes are presented in Fig.9. The measured index coefficient(D)of the divergence as the input control voltage swing during different operating values is shown in Fig.10.As thisfigure shows,a reasonably good correspondence is observed between the two sets of data,confirming the validity of the above supposition property regarding Eq.(6).A phase shifter circuit was designed to provide two-phase sig-nals of two-phase driving voltage sources with a phase difference ranging from p/2toÀp/2.To design a low-cost,simple phase shifter circuit for a TWUSM,we constructed a phase-regulating driving circuit for the USM by utilizing the VCR and all-passfilter circuit.The proposed phase shifter circuit,shown in Fig.11, has dual complementary channels,in which the sinusoid output signals have angles complementary to each other (\A+\B=90°).The driving voltage signals with the phase difference from the phase shifter circuit for the resonance frequency of TWUSMsetFig.14.A Push–pull class-B amplifier with Darlingtonpairs.Fig.15.Rotational speed versus driving frequency under freeloading.Fig.16.Two-phase output voltages of phase-modulation driving circuit for drivingfrequency set at41kHz:the phase regulated as equal value.2772T.-C.Chen et al./Energy Conversion and Management49(2008)2767–2775at 40kHz are shown in Fig.12.Even if the phase in the phase shifter circuit was slightly affected by the operating driving frequency,the output signals in phase A and B can still maintain symmetrical amplitude and the range of phase difference reaches ±p /2rad.By observing the characteristics of the measured phase difference angle versus the phase-modulated voltage (V p ),shown in Fig.13,we found that the relationship between the phase difference angle (U )and phase-modulated voltage (V p )is highly linear over a wide operating range under different driving frequencies.3.4.Power amplifiers and transformerA practical circuit using ClassB elements is a complementary pair or push–pull arrangement.Here,complementary devices are used to each amplify the opposite halves of the input signal,which is then recombined at the output.This arrangement gives excellent efficiency,but can suffer from the drawback of a small glitch at the joins between the two halves of the signal,a problem known as crossover distortion.A solution to this is to bias the devices just on,rather than off altogether,when they are not in use.One way to greatly boost the current gain (A I )of a Class B push–pull ampli-fier is to use Darlington pairs instead of single transistors,shown in Fig.14.Since this USM presents a large capacitive load and requires a high operating frequency,its equivalent impedance could be extre-mely low.This USM also requires a high drive voltage,which leads to a large drive current.Hence,a ferrite-core transformer which features high efficiency,small size,and light weight,was chosen to isolate and boost the high frequency AC voltage.The non-reso-nant power amplifier circuits are designed in order to provide two-phase,phase A and B,sinusoid output voltages V A and V B with the same amplitude under the variable frequency and phase con-trol.According to experiment test in Section 4,the amplitude of the output voltage will not be affected by the variation of the qual-ity when the driving frequency is operated closely to the resonant frequency of the TWUSM.The phase B power amplifier circuit is designed using the same method as for phase A.4.Experimental resultsA prototype of power driver for a TWUSM was built and tested.Based on the circuit design of TWUSM driver discussed above,mo-tor performance was measured by experimental results.There are three basic input signals for the TWUSM:frequency,independence amplitude,and phase.It is important to confirm the driving char-acteristics for eachparameter.Fig.17.Experimental results of phase-modulation driving circuit for driving frequency set at 41kHz,10l s/div.(a)Two-phase output voltages with phase difference p /6for CW rotation.(b)Two-phase output voltages with phase difference p /6for CCWrotation.Fig.18.Experimental results of phase-modulation driving circuit for driving frequency set at 41kHz,10l s/div.(a)Two-phase output voltages with phase difference p /3for CW rotation.(b)Two-phase output voltages with phase difference p /3for CCW rotation.T.-C.Chen et al./Energy Conversion and Management 49(2008)2767–27752773First,we measured the rotational speed in relation to the driv-ing frequency in Fig.15.The mechanical resonant frequency of the USM (USR-60)ranges from 39to 40kHz in the ultrasonic fre-quency range.The switching frequency of the voltage-controlled oscillator,which is designed to vary between 40.5and 44kHz,should be higher than the resonant frequency of the mechanical vibration.The highest rotational speeds around the phase differ-ence p /2were roughly 229and 221rpm in the direction of CW and CCW,respectively.The frequency,at around 40.5kHz,is nearly the same as the natural resonance frequency of TWUSM as de-scribed above.This characteristic is the same as that of a conven-tional single-frequency-mode control ultrasonic motor.The vibration velocity becomes high near the resonant frequency of the stator,which means the rotational velocity of the rotor reaches its maximum value.Subsequently,we tested the rotational speed in relation to the phase difference.The phase shifter circuit worked as mentioned above.The control input to the drive circuit (V p )is calculated by the control algorithm.According to the control input,the phase dif-ference (U )is regulated by means of the designed phase shifter cir-cuit.The phase shifter circuit is designed for the two-phase power amplifier to provide two-phase output voltages V A and V B with var-iable phase difference,where the rotational direction (CW or CCW)can be controlled by allowing either V A or V B to lead.In order to as-sess the performance and stability of the proposed phase-mode driver for TWUSM,the phase differences of two-phase AC outputvoltage has been regulated from 0to ±p /2rad,shown in Figs.16–19,respectively.The two-phase sinusoid output V A and V B can thus be maintained at the same constant peak value at the switching frequency under varying phase-modulation processes.The driving phase difference of the designed phase-shifter circuit is the major control variable,and balanced two-phase sinusoid output voltages with the same amplitudes and variable-phase control results in satisfactory control performance of the TWUSM servo drive.Fig.20shows the experimental results of the Speed versus phase difference curves under variable operating driving frequencies.Experimental results confirm that the rotor could be rotated using the design driving circuit.By comparison,the phase-mode driving can offer a much wider controllable range,which verifies that the proposed driver circuit can successfully adapt the change of com-mand signals.In addition to these advantages,only the phase shift parameter can control the rotational direction of a rotor,which the phase-shift varies between p /2and Àp /2.5.ConclusionsUSMs are potentially interesting for a number of industry appli-cations,such as miniature robotics.Their electrical drive circuits present unique challenges,particularly in producing signals of several hundred volts and tens of kilohertz with variable phase dif-ferences,inputted to a low impedance capacitive motor,whileFig.20.Rotational speed versus phase difference under difference operating drivingfrequency.Fig.19.Experimental results of phase-modulation driving circuit for driving frequency set at 41kHz,10l s/div.(a)Two-phase output voltages with phase difference p /2for CW rotation.(b)Two-phase output voltages with phase difference p /2for CCW rotation.2774T.-C.Chen et al./Energy Conversion and Management 49(2008)2767–2775。
机械专业外文翻译(中英文翻译)

机械专业外文翻译(中英文翻译)第1页Among the methods of material conveying employed,belt conveyorsplaya very important part in the reliable carrying of material over longdistances at competitive cost.Conveyor systems have become larger and morecomplex and drive systems have also been going through a process of evolutionand will continue to do so.Nowadays,bigger belts require more power and havebrought the need for larger individual drives as well as multiple drives suchas 3 drives of 750 kW for one belt(this is the case for the conveyor drivesin Chengzhuang Mine).The ability to control drive acceleration torque iscritical to belt conveyors’ performance.An efficient drive system should beable to provide smooth,soft starts while maintaining belt tensions withinthe specified safe limits.For load sharing on multiple drives.torque andspeed control are also important considerations in the drive system’s design.Due to the advances in conveyor drive control technology,at present many morereliable.Cost-effective and performance-driven conveyor drive systems[1]covering a wide range of power are available for customers’ choices. Full-voltage starters.With a full-voltage starter design,the conveyor head shaft is direct-coupled to the motor through the gear drive.Direct full-voltage startersare adequate for relatively low-power, simple-profile conveyors.With direct fu11-voltage starters.no control is provided for various conveyor loadsand.depending on the ratio between fu11- and no-1oad power requirements,empty starting times can be three or four times faster than full load.The maintenance-free starting system is simple,low-cost and very reliable.However, they cannot control starting torque and maximum stall torque;therefore.they are第2页 limited to the low-power, simple-profile conveyor belt drives.Reduced-voltage starters.As conveyor power requirements increase,controlling the applied motor torque during the acceleration period becomes increasinglyimportant.Because motor torque 1s a function of voltage,motor voltage must be controlled.This can be achieved through reduced-voltage starters by employinga silicon controlled rectifier(SCR).A common starting method with SCRreduced-voltage starters is to apply low voltage initially to takeup conveyorbelt slack.and then to apply a timed linear ramp up to full voltage and beltspeed.However, this starting method will not produce constant conveyor beltacceleration.When acceleration is complete.the SCRs, which control the applied voltage to the electric motor. are locked in full conduction, providing fu11-linevoltage to the motor.Motors with higher torque and pull—uptorque,can provide better starting torque when combined with the SCR starters, which are availablein sizes up to 750 KW.Wound rotor induction motors.Wound rotor induction motors are connecteddirectly to the drive system reducer and are a modifiedconfiguration of a standardAC induction motor.By inserting resistance in series with the motor’s rotor windings.the modified motor control system controlsmotor torque.For conveyor starting,resistance is placed in series with the rotor for low initial torque.As the conveyor accelerates,the resistance is reduced slowly to maintain a constantacceleration torque.On multiple-drive systems.an external slip resistor may beleft in series with the rotor windings to aid in load sharing.The motor systems have a relatively simple design.However, the control systems for these can behighly complex,because they are based on computer control of the resistanceswitching.Today,the majority of control systems are custom designed to meet aconveyor system’s particular specifications.Wound rotor motors are appropriatefor systems requiring more than 400 kW .DC motor.DC motors.available from a fraction of thousands of kW ,are designed to deliver constant torque below base speed and constant kW above base speed tothe maximum allowable revolutions per minute(r/min).with the majority of conveyordrives, a DC shunt wound motor is used.Wherein the motor’srotating armature is第3页 connected externally.The most common technology for controlling DC drives is aSCR device. which allows for continual variable-speed operation.The DC drive system is mechanically simple, but can include complex custom-designed electronicsto monitor and control the complete system.This system option is expensive incomparison to other soft-start systems.but it is a reliable, cost-effective drivein applications in which torque,1oad sharing and variable speed are primaryconsiderations.DC motors generally are used with higher-power conveyors,including complex profile conveyors with multiple-drive systems,booster tripper systems needing belt tension control and conveyors requiring a wide variable-speed range.Hydrokinetic couplings,commonly referred to as fluid couplings.are composed of three basic elements; the driven impeller, which acts as a centrifugal pump;the driving hydraulic turbine known as the runner and a casing that encloses thetwo power components.Hydraulic fluid is pumped from the driven impeller to thedriving runner, producing torque at the driven shaft.Because circulating hydraulicfluid produces the torque and speed,no mechanical connection is required betweenthe driving and driven shafts.The power produced by this coupling is based onthe circulated fluid’s amount and density and the torque in proportion to inputspeed.Because the pumping action within the fluid coupling depends on centrifugalforces.the output speed is less than the input speed.Referred to as slip.this normally is between l% and 3%.Basic hydrokinetic couplings are available inconfigurations from fractional to several thousand kW .Fixed-fill fluid couplings.Fixed-fill fluid couplings are the most commonlyused soft-start devices for conveyors with simpler belt profiles and limitedconvex/concave sections.They are relativelysimple,1ow-cost,reliable,maintenance free devices that provide excellent softstarting results to the majority of belt conveyors in use today.Variable-fill drain couplings.Drainable-fluid couplings work on the sameprinciple as fixed-fill couplings.The coupling’s impellers are mounted on the ACmotor and the runners on the driven reducer high-speed shaft.Housing mounted to the drive base encloses the working circuit.The coupling’s rotating casing contains第4页 bleed-off orifices that continually allow fluid to exit the working circuit intoa separate hydraulic reservoir.Oil from the reservoir is pumped through a heatexchanger to a solenoid-operated hydraulic valve that controls the filling of thefluid coupling.To control the starting torque of a single-drive conveyor system,the AC motor current must be monitored to provide feedback to the solenoid controlvalve.Variable fill drain couplings are used in medium to high-kW conveyor systemsand are available in sizes up to thousands of kW .The drives can be mechanicallycomplex and depending on the control parameters.the system can be electronicallyintricate.The drive system cost is medium to high, depending upon size specified.Hydrokinetic scoop control drive.The scoop control fluid coupling consistsof the three standard fluid coupling components:a driven impeller, a driving runnerand a casing that encloses the working circuit.The casing is fitted with fixedorifices that bleed a predetermined amount of fluid into a reservoir.When the scoop tube is fully extended into the reservoir, the coupling is l00 percentfilled.The scoop tube, extending outside the fluid coupling,is positioned using an electric actuator to engage the tube from the fully retracted to the fullyengaged position.This control provides reasonably smooth acceleration rates.to but the computer-based control system is very complex.Scoop control couplings are applied on conveyors requiring single or multiple drives from l50 kW to 750kW.Variable frequency control is also one of the direct drive methods.The emphasizing discussion about it here is because that it has so uniquecharacteristic and so good performance compared with other driving methods forbelt conveyor. VFC devices Provide variable frequency and voltageto the inductionmotor, resulting in an excellent starting torque and acceleration rate for beltconveyor drives.VFC drives.available from fractional to several thousand(kW ),are electronic controllers that rectify AC line power to DC and,through an inverter, convert DC back to AC with frequency and voltage contro1.VFC drives adopt vector control or direct torquecontrol(DTC)technology,and can adopt different operating speeds according to different loads.VFC drives can make starting or stalling第5页 according to any given S-curves.realizing the automatic track for starting orstalling curves.VFC drives provide excellent speed and torque control for startingconveyor belts.and can also be designed to provide load sharing for multipledrives.easily VFC controllers are frequently installed on lower-powered conveyordrives,but when used at the range of medium-high voltage in the past.the structure of VFC controllers becomes very complicated due to the limitation of voltage ratingof power semiconductor devices,the combination of medium-high voltage drives andvariable speed is often solved with low-voltage inverters usingstep-uptransformer at the output,or with multiple low-voltage inverters connected inseries.Three-level voltage-fed PWM converter systems are recently showingincreasing popularity for multi-megawatt industrial driveapplications becauseof easy voltage sharing between the series devices and improved harmonic qualityat the output compared to two-level converter systems With simple series connectionof devices.This kind of VFC system with three 750 kW /2.3kV inverters has been successfully installed in ChengZhuang Mine for one 2.7-km long belt conveyordriving system in following the principle of three-level inverterwill be discussedin detail.Three-level voltage-fed inverters have recently become more and more popularfor higher power drive applications because of their easy voltage sharingfeatures.1ower dv/dt per switching for each of the devices,and superior harmonic quality at the output.The availability of HV-IGBTs has led to the design of anew range of medium-high voltage inverter using three-level NPC topology.This kind of inverter can realize a whole range with a voltagerating from 2.3 kV to 4.1 6 kV Series connection of HV-IGBT modules is used in the 3.3 kV and 4.1[2,3]6 kV devices.The 2.3 kV inverters need only one HV-IGBT per switch.To meet the demands for medium voltage applications.a three-level neutral point clamped inverter realizes the power section.In comparison to a two-levelinverter.the NPC inverter offers the benefit that three voltage levels can besupplied to the output terminals,so for the same output current quality,only第6页1/4 of the switching frequency is necessary.Moreover the voltage ratings of theswitches in NPC inverter topology will be reduced to 1/2.and the additional transient voltage stress on the motor can also be reduced to 1/2 compared to thatof a two-level inverter.The switching states of a three-level inverter are summarized in Table 1.U.V and W denote each of the three phases respectively;P N and O are the dc bus points.The phase U,for example,is in stateP(positive bus voltage)when theswitches S and S are closed,whereas it is in state N (negative bus voltage) 1u2uwhen the switches S and S are closed.At neutral point clamping,the phase is 3u4uin O state when either Sor S conducts depending on positive or negative phase 2u 3ucurrent polarity,respectively.For neutral point voltage balancing,the average current injected at O should be zero.For standard applications.a l2-pulse diode rectifier feeds the divided DC-linkcapacitor.This topology introduces low harmonics on the line side.For even higher requirements a 24-pulse diode rectifier can be used as an input converter.For more advanced applications where regeneration capability is necessary, an activefront.end converter can replace the diode rectifier, using the same structureas the inverter.Motor Contro1.Motor control of induction machines is realized by using a rotorflux.oriented vector controller.Fig.2 shows the block diagram of indirect vector controlled drive thatincorporates both constant torque and high speed field-weakening regions wherethe PW M modulator was used.In this figure,the command flux is generated as function of speed.The feedback speed is added with the feed forward slip commandsignal . the resulting frequency signal is integrated and then the unit vectorsignals(cos and sin )are generated.The vector rotator generates the voltageand angle commands for the PW M as shown.PWM Modulator.The demanded voltage vector is generated using an elaborate第7页 PWM modulator.The modulator extends the concepts of space-vector modulation tothe three-level inverter.The operation can be explained by starting from aregularly sampled sine-triangle comparison from two-level inverter.Instead of using one set of reference waveforms and one triangle defining the switchingfrequency, the three-level modulator uses two sets of reference waveforms U and r1U and just one triangle.Thus, each switching transition is used in an optimal r2way so that several objectives are reached at the same time.Very low harmonics are generated.The switching frequency is low and thusswitching losses are minimized.As in a two-level inverter, a zero-sequencecomponent can be added to each set of reference waveform s in order to maximizethe fundamental voltage component.As an additional degree of freedom,the position of the reference waveform s within the triangle can be changed.This can be used for current balance in the two halves of the DC-1ink.After Successful installation of three 750 kW /2.3 kV three-level invertersfor one 2.7 km long belt conveyor driving system in Chengzhuang Mine.The performance of the whole VFC system was tested.Fig.3 is taken from the test,which shows the excellent characteristic of the belt conveyor driving system withVFC controller.Fig.3 includes four curves.The curve 1 shows the belt tension.From the curve it can be find that the fluctuation range of the belt tension is very smal1.Curve 2 and curve 3 indicate current and torque separately.Curve 4 shows the velocityof the controlled belt.The belt velocity have the“s”shape characteristic.A1l the results of the test show a very satisfied characteristic for belt drivingsystem.Advances in conveyor drive control technology in recent years have resultedin many more reliable.Cost-effective and performance-driven conveyor drive systemchoices for users.Among these choices,the Variable frequency control (VFC) methodshows promising use in the future for long distance belt conveyor drives due toits excellent performances.The NPC three-level inverter using high voltage IGBTs第8页 make the Variable frequency control in medium voltage applications become muchmore simple because the inverter itself can provide the medium voltage needed atthe motor terminals,thus eliminating the step-up transformer in most applicationsin the past.The testing results taken from the VFC control system with NPC three.1evel inverters used in a 2.7 km long belt conveyor drives in Chengzhuang Mine indicatesthat the performance of NPC three-level inverter using HV-IGBTs together with thecontrol strategy of rotor field-oriented vector control for induction motor driveis excellent for belt conveyor driving system.第9页在运送大量的物料时,带式输送机在长距离的运输中起到了非常重要的竞争作用。
轧机机械专业毕业设计外文翻译
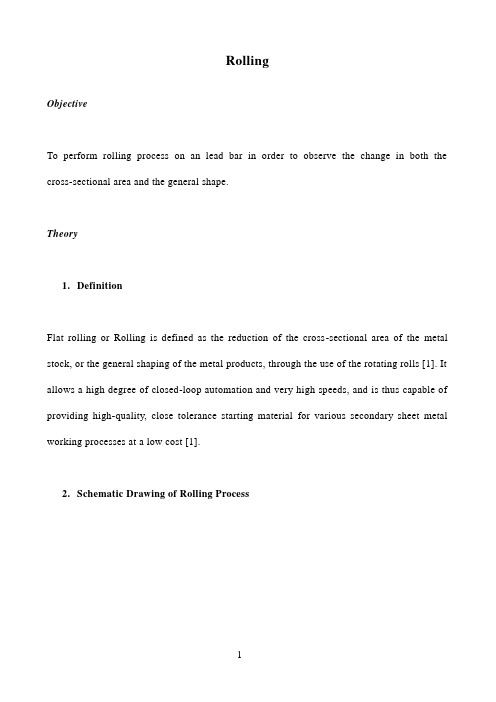
RollingObjectiveTo perform rolling process on an lead bar in order to observe the change in both the cross-sectional area and the general shape.Theory1.DefinitionFlat rolling or Rolling is defined as the reduction of the cross-sectional area of the metal stock, or the general shaping of the metal products, through the use of the rotating rolls [1]. It allows a high degree of closed-loop automation and very high speeds, and is thus capable of providing high-quality, close tolerance starting material for various secondary sheet metal working processes at a low cost [1].2.Schematic Drawing of Rolling ProcessFigure 1. Rolling Process [2]The rolls rotate as illustrated in Figure 1. to pull and simultaneously squeeze the work between them. The basic process shown in Figure 1 is flat rolling, used to reduce the thickness of a rectangular cross section.Figure 2. Various configurations of rolling mills: (a) two high, (b) three high, (c) four high,(d) cluster mill, and (e) tandem rolling mill [2].Various rolling mill configurations are available to deal with the variety of applications and technical problems in the rolling process. The basic rolling mill consists of two opposite rotating rolls and is referred to as a two-high rolling mill (Figure 2a). In the three-high configuration Figure 2(b), there are three rolls in a vertical column, and the direction of rotation of each roll remains unchanged. To achieve a series of reductions, the work can be a passed through from either side by raising or lowering the strip after each pass. Theequipment in a three-high rolling mill becomes more complicated, because an elevator mechanism is needed to raise and lower the work [2].Roll-work contact length is reduced with a lower roll radius, and this lads to lower forces, torque, and power. The four-high rolling mill uses two smaller diameter rolls to contact the work and two backing rolls behind them. Another roll configuration that allows smaller working rolls against the work is the cluster rolling mill.To achieve higher throughput rates in standard products, a tandem rolling mill is often used. This configuration consists of a series of rolling stands. With each rolling step, work velocity increases, and the problem of synchronizing the roll speeds at each stand is significant [2].3.General Overview of ProcessThe primary objectives of the flat rolling process are to reduce the cross-section of the incoming material while improving its properties and to obtain the desired section at the exit from the rolls. The process can be carried out hot, warm, or cold, depending on the application and the material involved. The rolled products are flat plates and sheets. Rolling of blooms, slabs, billets, and plates is usually done at temperatures above the recr ystallization temperature (hot rolling). Sheet and strip often are rolled cold in order to maintain close thickness tolerances.Basically flat rolling consists of passing metal between two rolls that revolve in oppositedirections, the space between the rolls being somewhat less than the thickness of the entering metal. Because the rolls rotate with a surface velocity exceeding the speed of the incoming metal, friction along the contact interface acts to propel the metal forward. The metal is squeezed and elongated and usually changed in cross section. The amount of deformation that can be achieved in a single pass between a given pair of rolls depend on the friction conditions along the interface. If too much is demanded, the rolls will simply skid over stationery metal. Too little deformation per pass results in excessive cost.Rolling involves high complexity of metal flow during the process. From this point of view, rolling can be divided into the following categories [3]:•Uniform reduction in thickness with no change in width: Here, the deformation is in plane strain, that is, in the directions of rolling and sheet thickness. This type occurs in rolling of strip, sheet, or foil.•Uniform reduction in thickness with an increase in width: Here, the material is elongated in the rolling direction, is spread in the width direction, and is compressed uniformly in the thickness direction. This type occurs in the rolling of blooms, slabs, and thick plates.•Moderately non-uniform reduction in cross section: Here, the metal is elongated in the rolling direction, is spread in the width direction, and is reduced non-uniformly in the thickness direction.•Highly non-uniform reduction in cross section: Here, the reduction in the thicknessdirection is highly non-uniform. A portion of the rolled section is reduced in thickness while other portions may be extruded or increased in thickness. As a result, in the width direction metal flow may be toward the center [3].Hot RollingThe distinctive mark of hot rolling is not a crystallized structure, but the simultaneous occurrence of dislocation propagation and softening processes, with or without recrystallization during rolling. The dominant mechanism depends on temperature and grain size. In general, the recrystallized structure becomes finer with lower deformation temperature and faster cooling rates and material of superior properties are obtained by controlling the finishing temperature [1].Hot rolling offers several advantages [1]:1)Flow stresses are low, hence forces and power requirements are relatively low, andeven very large workpieces can be deformed with equipment of reasonable size.2)Ductility is high; hence large deformations can be taken.3)Complex part shapes can be generated.The upper limit for hot rolling is determined by the temperature at which either melting or excessive oxidation occurs. Generally, the maximum working temperature is limited to 50°C below the melting temperature. This is to allow the possibility of segregated regions of lowermelting material [4].Cold RollingCold rolling, in the everyday sense, means rolling at room temperature, although the work of deformation can raise temperatures to 100-200°C. Cold rolling usually follows hot rolling. A material subjected to cold rolling strain hardness considerably. Dislocation density increases, and when a tension test is performed on this strain-hardened material, a higher stress will be needed to initiate and maintain plastic deformation; thus, the yield stress increases. However, the ductility of the material – as expressed by total elongation and reduction of area – drops because of the higher initial dislocation density. Similarly, strength coefficient rises and strain-hardening exponent drops. Crystals (grains) become elongated in the direction of major deformation [1].Cold rolling has several advantages [1]:1)In the absence of cooling and oxidation, tighter tolerances and better surface finish canbe obtained.2)Thinner walls are possible.3)The final properties of the workpiece can be closely controlled and, if desired, thehigh strength obtained during cold rolling can be retained or, if high ductility is needed, grain size can be controlled before annealing.4)Lubrication is, in general, easier.Rolling Problems and DefectsThe main problem during rolling process is the calibration of rollers. This calibration faults may occur in case of used bearings and may affect the thickness of parts. A simple classification is as here below:a.Lengthwise Occurring DefectsChange of rollers speedMaterial temperatureRoller temperatureInlet thicknessMaterial propertiesEccentric and conical rollersUsed bearingsb.Transversally Occurring DefectsParallel position of rollersSurface geometry of rollers轧制目的:为了观察在执行轧制过程中铅条的横截面积和一般形状的变化。
机械毕业设计外文翻译

A Comparison of Drive Starting Mechanisms forAggregate Belt ConveyorsAbstractThe purpose of this paper is to describe the torque/speed characteristics,during starting conditions,of the most common drives used on belt conveyors today. Requirements of a Belt Conveyor DriveA belt conveyor is considered to be a constant torque device. In other words,the required driving torque is approximately constant at varying speeds (see figure l).other applications,such as a pump drive,have variable torque requirements(see figure2).However,to increase the speed of a conveyor additional torque must be added untilthe desired speed is obtained. Newton’s Second Law of Motion governs this relationship.∑F m a=The most straightforward example would be a constant acceleration torque(see figure3).In reality the acceleration torque is rarely constant. However,static calculation models as outlined in the Conveyor Equipment Manufacturers Association handbook (CEMA) make this assumption. When using static models the average acceleration torque is estimated over the entire acceleration time and assumed to be linear. Dynamic models,which are beyond the scope of this paper,allow acceleration torque values to vary in magnitude during the acceleration(or deceleration)Period.It should be noted that,given a constant load,a larger acceleration torque results in a faster acceleration time and also higher Peak belt tensions. Conversely,a smaller acceleration torque results in a longer start time and smaller Peak belt tensions. Across-The-Line AC Motor StartTechnically this is the simplest type of drive used on a belt conveyor. In this drive type an AC squirrel cage induction motor is started by simply throwing the contactor and energizing the motor. The resulting output torque,assuming that rated voltage is maintained,is strictly a function of the motor design. NEMA has Provided design standards that define the output torque characteristics of the most commonly used 3 Phase motors up to approximately 250 hp(figure4).In sizes larger than 250 hp manufacturers generally use the NEMA design codes in a relative manner(i.e.,NEMA C has a greater locked rotor torque than a NEMA B motor).The most critical locations on the AC motor speed/torque curve have been named for definition purposes. These common names are provided in figure 5.The most rigorous method of determining average acceleration torque,for static calculations,is to break the curve into several vertical sections,then sum the individual areas under the curve and finally divide by the number of sections.The more common way is to apply the following simplified equation:These static approximation methods work for most belt conveyors but can get the designer into trouble from time to time,especially on long and/or steep and/or fastconveyors. One item that needs to be examined is breakaway torque. Just because the drive provides enough average torque to accelerate the load doesn’t mean that it provides enough torque to break it away from zero speed and get it moving.CEMA defines breakaway torque as twice the torque required to overcome the total friction plus the torque required to lift the load vertically. Locked rotor torque (LRT) needs to be greater than breakaway torque! A good static Program makes this check.In addition to examining the effect that average torque has on the conveyor components the belt designer needs to determine the effect of peak torque. It is not uncommon for the breakdown torque (BDT) of a NEMA C motor to be greater than2.5 times full load torque (FLT).Generally the belting and Pulley manufacturers allowa transient overload of 1.5 times full load operating load. An across-the-line start can easily cause tensions to exceed these maximums. These higher than normal loads can be designed into the conveyor if they are known up front.Considering only average starting torque can cause the conveyor designer to undersize the take-up weight. It is not uncommon for conveyors with across-the-line starters to experience intermittent drive slip. This generally happens when Peak torque (BDT) is input by the drive and the take-up has been sized for average torque but not peak torque. The result can be devastating. When the drive pulley slips during this condition,the tension on the Tl and T2 sides (high and low)of the drive Pulley tries to equalize. This can subject a low tension bend or take-up pulley,just behind the drive pulley,to tensions that approach Tl tension. These Pulleys are rarely,if ever,designed for this load condition and the result is low tension Pulley failure. This condition is easily demonstrated with dynamic analysis.Another common Problem with across-the-line starts is caused by voltage dips during starting. If the power distribution system is not stiff enough to handle the huge inrush currents of an across-the-1ine start,the starting torque of the motors can be reduced to a Point that the conveyor will not start. This is due to the fact that the output torque ofan AC squirrel cage induction motor is reduced by the square of the applied voltage. In other words,a voltage drop of 10%would equate to a torque reduction of 19%. Reduced Voltage StartingThe reduced voltage starting of an AC squirrel cage induction motor is done for two basic reasons:1 .To reduce the inrush current that naturally occurs when a motor is Startedacross-the-1ine. A typical current/speed graph is shown in figure 6.It is not uncommon for the inrush current to be 6 times or more than it is at full load torque. As stated above high inrush currents cause the voltage in a power distribution system to sag. The cost of electrical power distribution equipment can become very high if it needs to be designed to handle the high inrush currents.2 . To reduce Peak motor torque during starting conditions,which subsequentlyincreases acceleration time. By reducing the Peak torques the conveyor components can be designed for lower tension loads. This primarily includes belting,Pulleys and external support structure. This can result in significant cost savings.Two common types of reduced voltage starters are the Current Limiting and the Constant Torque devices.Graphs are included above(figures 7 through 8) that depict the same motor/conveyor application with an Across-The-Line,a limitd Curren, and a constant Torque start. After studying the graphs it becomes apparent that the best use of the limited torque start is to protect the power distribution system from high inrush currents. The constant torque start reduces the high torque Peaks and Protects the conveyor’s mechanical components. In both cases the Start time is increased because the over all magnitude of accelerating torque is reduced. However,neither method will make it easier to start a“hard-to-start conveyor.”Correcting a hard starting conveyor is not areason to use a reduced voltage starter!翻译带式输送机驱动方式比较摘要本文的目的是描述最常见的机用输送皮带起动时的扭矩/转速特性。
- 1、下载文档前请自行甄别文档内容的完整性,平台不提供额外的编辑、内容补充、找答案等附加服务。
- 2、"仅部分预览"的文档,不可在线预览部分如存在完整性等问题,可反馈申请退款(可完整预览的文档不适用该条件!)。
- 3、如文档侵犯您的权益,请联系客服反馈,我们会尽快为您处理(人工客服工作时间:9:00-18:30)。
附录附录A:LOW ROLLING RESISTANCE TIRESAccording to the report,80% or more of a car’s fuel energy is wasted by friction and other such losses. 1.5 to 4.5% of total gasoline use could be saved if allreplacement tires in use had low rolling resistance. About 237 million replacement tires are sold in the U.S. each year – none has rolling resistance labeling.1. America’s Fuel Use, Its Impacts,and Opportunities for SavingsThe environmental impacts of America’s gasoline use are profound. With over 160 million passenger cars and light trucks on the road, we burn about 126 billion gallons of gasoline per year. Our fuel use continues to rise about 3% annually, propelled by continued increases in total number of vehicles, rising average distance driven per car, and falling average fuel economy.Today, light-duty vehicles (cars & light trucks) are responsible for about 20% of the nitrogen oxides, 27% of the volatile organic compounds, 51% of the carbon monoxide, and roughly 30% of all the carbon dioxide (the main greenhouse gas) emitted from human activities nationwide. Rising fuel use also has enormous implications for protection of wilderness and public lands (vulnerable to increasedexploration), water resources (vulnerable to tanker and pipeline accidents), and national security. So the opportunity to save money and improve environmental quality through fuel use reductions is clear.One of the most promising opportunities for fuel savings across the entire fleet of existing vehicles is to utilize low rolling resistance tires instead of standard replacement models. This change improves the inherent efficiency of the vehicle, automatically saving fuel over the typical 30,000 to 50,000 mile lifetime of a set of tires.This report examines the opportunity for saving gasoline through use of improved tire technology and recommends particular tire models for which our initial test data suggest environmental advantages. Its findings are applicable to government and corporate fleet managers as well as individual tire buyers.2. How Tires Can Reduce Fuel ConsumptionAccording to the National Academy of Sciences, about 80 to 88% of the energy in a vehicle’s gasoline tank is wasted in various thermal, frictional, and standby losses in the engine and exhaust system. This leaves only about 12 to 20% of the potential energy actually converted to vehicle motion. One of the key ways to improve that efficiency is to reduce the rolling resistance of vehicle tires. This is not a measure of a tire’s traction or “grip” on the road surface, but rather simply indicates how easily a tire rolls down the road, minimizing the energy wasted asheat between the tire and the road, within the tire sidewall itself, and between the tire and the rim.Detailed modeling conducted by the National Renewable Energy Laboratory concluded that a 10% reduction in tire rolling resistance should yield fuel savings of about 1 to 2%, depending on driving conditions and vehicle type. According to research for the California Energy Commission, about 1.5 to 4.5% of total gasoline use could be saved if all replacement tires in use had low rollingresistance. This translates roughly into average savings of up to 30 gallons of gasoline savings per vehicle per year, or from $2.5 to $7.5 billion worth of national average gasoline savings.As part of their efforts to meet Federal fuel economy standards, automakers routinely specify low rolling resistance tires on their new vehicles. Between 1980 and 1994, the lowest rolling resistance tire models available achieved a 48% reduction in rolling resistance, and have likely continued to improve thereafter. These original equipment (OE) tire models are occasionally available in the replacement tire market, but often only by special order. In general, the tires marketed to the replacement tire market tend to place greater emphasis on longevity and low price, and therefore often have higher rolling resistance than OE tires.Unfortunately both OE and replacement tires lack any sort of rollingresistance labeling currently, so fleet managers and consumers that wish to buy highly energy-efficient tires when their first set of OE tires wear out have been stymied. Even when tire makers claim that particular replacement models are more fuelefficient than others, they do not always use consistent test methods or independent laboratory data to back up those claims. About 237 million replacement tires are sold in the U.S. each year for cars and light trucks, and none of them provides rolling resistance labeling.In 2002, the Energy Foundation funded Ecos Consulting to analyze the tire market, select representative models for rolling resistance testing, and work with Green Seal to recommend particular models that perform well while achieving low rolling resistance. Those findings are being published for the first time in this Choose Green Report. Additional background on Ecos Consulting’s key findings can be found in a separate report prepared for the California Energy Commission, available at3. Balancing Tire Resistance and Other ConsiderationsThe manufacture of tires, like other industrial processes, involves material extraction and production, as well as energy consumption and the emission of various pollutants. Each of these manufacturing stages impacts the environment in different ways. However, tires, like a number of other consumer products, are actually responsible for more environmental impacts in their use and ultimate disposition than in theirmanufacturing. They significantly impact the amount of fuel consumed by the vehicle to which they are attached, leading to global warming emissions as well as local and regional air pollution. They create particulate air pollution in the process of wearing, and they can be a significant solid waste problem if not properly recycled.An analysis conducted by Italian tire manufacturer Pirelli (Figure 1) revealed the dominance of tire use in overall life-cycle energy consumption. Fully 82% of the lifecycle energy use occurs from t he tire’s contribution to vehicle fuel use, compared to roughly 18% associated with obtaining the raw materials and manufacturing the tire itself. Thus, a tire’s rolling resistance is likely to be a larger factor in its life-cycle environmental impact than its composition, longevity, or ultimate fate, though those factors merit consideration as well.This report places greatest significance on the measured rolling resistance of tires, followed closely by consideration of the tire’s expected longevity and performance characteristics. A tire with high rolling resistance can cause profound environmental impact, even if it capably grips the road and lasts for 80,000 miles. By contrast, a very low rolling resistance tire may not be worth recommending if its lifetime is unusually short or test data indicate that it provides poor traction.Every tire currently on the market represents a balance between a wide assortment of desired performance characteristics and price (wesurveyed tires ranging from $25 to over $200 per tire). Careful balancing of these characteristics can yield not only a high-performing tire, but also one that is better for the environment than others currently available on the market.4.Rating Tire Rolling Resistance and Related FactorsRolling resistance has traditionally been measured through an official Society of Automotive Engineers (SAE) test procedure known as J1269. It measures the force required to roll a tire against a dynamometer at a fixed speed of 50 miles per hour. A newer procedure, SAE J2452, promises improved accuracy by assessing rolling resistance at a variety of speeds, but no independent laboratory currently has the capability to conduct such testing in-house. As a result, all of our testing was conducted at a single independent laboratory according to SAE J1269.The highest and lowest rolling resistance tires we tested differed in efficiency by 60%, indicating that tire choice can have a bigger impact on fuel economy than most people realize. Rolling resistance differences of 20 to 30% are not uncommon among tires of an otherwise similar size, type, and level of performance. This means an individual vehicle could save up to 6% of its gasoline use if it were fitted with very efficient tires, paying for the modest additional cost of low rolling resistance tires in approximately a year of fuel savings. In other words, a typical compactcar such as a Ford Focus can improve its mileage from 30 mpg to 32 mpg simply by using lower rolling resistance tires. For a car averaging 15,000 miles per year the fuel savings is about $50 (at $1.50 per gallon).All tires have imprinted information on their sidewalls indicating size, type, load, and speed ratings, as described in Figure 2. The majority of tire models employ a “P” designation for passe nger vehicle use, but some bear the “LT” designation for use with light trucks. In general, “P” tires appear to be gaining in popularity relative to “LT” tires of a given size.In addition, the U.S. Department of Transportation requires each manufacturer to grade its tires under the Uniform Tire Quality Grading System (UTQGS) and establish ratings for the following characteristics: tread wear, traction, and temperature resistance. Unfortunately, the ultimate results published for each tire model are less “uniform” than they should be. The government specifies how each test should be conducted and prevents a manufacturer from claiming better performance than measured. However, it does not prevent manufacturers from claiming worse performance than measured. And, curiously enough, many do, primarily to amplify marketing distinctions among their tires at different price points and encourage buyers to move up from a “good” to a “better” or “best” model in a particular category.Given the variability of ratings and the number of relevant factors, we have compiled our own composite metrics of performance for assessing tires, including the Federal ratings noted below and a variety of other published data.5.Rolling On to the FutureEfforts to differentiate replacement tires on the basis of rolling resistance are still in their very early stages. Without data on the rolling resistance of all tire models across a range of sizes, it is impossible to say for sure if the models identified in this report represent the most efficient models or simply a subset of them. For now, consumers and fleet managers can start with the data shown here and request additional information directly from retailers and manufacturers.附录B:低滚动阻力轮胎根据报告80%的或更多的汽车的燃料是由摩擦和其他类似的损失所消耗的。