苎麻脱胶。
国内苎麻脱胶技术
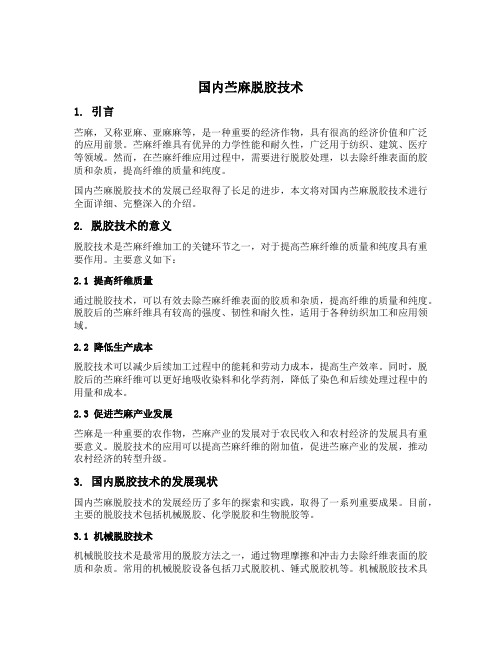
国内苎麻脱胶技术1. 引言苎麻,又称亚麻、亚麻麻等,是一种重要的经济作物,具有很高的经济价值和广泛的应用前景。
苎麻纤维具有优异的力学性能和耐久性,广泛用于纺织、建筑、医疗等领域。
然而,在苎麻纤维应用过程中,需要进行脱胶处理,以去除纤维表面的胶质和杂质,提高纤维的质量和纯度。
国内苎麻脱胶技术的发展已经取得了长足的进步,本文将对国内苎麻脱胶技术进行全面详细、完整深入的介绍。
2. 脱胶技术的意义脱胶技术是苎麻纤维加工的关键环节之一,对于提高苎麻纤维的质量和纯度具有重要作用。
主要意义如下:2.1 提高纤维质量通过脱胶技术,可以有效去除苎麻纤维表面的胶质和杂质,提高纤维的质量和纯度。
脱胶后的苎麻纤维具有较高的强度、韧性和耐久性,适用于各种纺织加工和应用领域。
2.2 降低生产成本脱胶技术可以减少后续加工过程中的能耗和劳动力成本,提高生产效率。
同时,脱胶后的苎麻纤维可以更好地吸收染料和化学药剂,降低了染色和后续处理过程中的用量和成本。
2.3 促进苎麻产业发展苎麻是一种重要的农作物,苎麻产业的发展对于农民收入和农村经济的发展具有重要意义。
脱胶技术的应用可以提高苎麻纤维的附加值,促进苎麻产业的发展,推动农村经济的转型升级。
3. 国内脱胶技术的发展现状国内苎麻脱胶技术的发展经历了多年的探索和实践,取得了一系列重要成果。
目前,主要的脱胶技术包括机械脱胶、化学脱胶和生物脱胶等。
3.1 机械脱胶技术机械脱胶技术是最常用的脱胶方法之一,通过物理摩擦和冲击力去除纤维表面的胶质和杂质。
常用的机械脱胶设备包括刀式脱胶机、锤式脱胶机等。
机械脱胶技术具有操作简便、能耗低、对环境无污染等优点,但脱胶效果受纤维质量和设备性能的影响较大。
3.2 化学脱胶技术化学脱胶技术是利用化学药剂对苎麻纤维进行处理,去除胶质和杂质。
常用的化学脱胶方法包括碱法脱胶、酶法脱胶等。
化学脱胶技术具有脱胶效果好、操作灵活、适用范围广等优点,但需要注意对环境的影响和化学药剂的安全性。
生化物化组合工艺处理苎麻脱胶废水
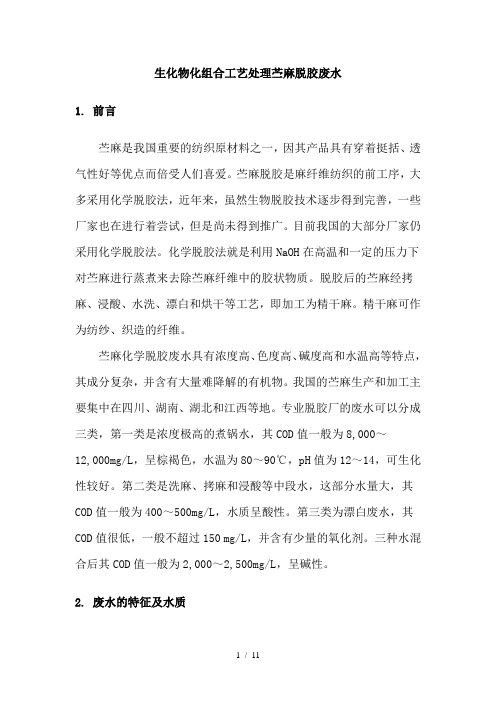
生化物化组合工艺处理苎麻脱胶废水1. 前言苎麻是我国重要的纺织原材料之一,因其产品具有穿着挺括、透气性好等优点而倍受人们喜爱。
苎麻脱胶是麻纤维纺织的前工序,大多采用化学脱胶法,近年来,虽然生物脱胶技术逐步得到完善,一些厂家也在进行着尝试,但是尚未得到推广。
目前我国的大部分厂家仍采用化学脱胶法。
化学脱胶法就是利用NaOH在高温和一定的压力下对苎麻进行蒸煮来去除苎麻纤维中的胶状物质。
脱胶后的苎麻经拷麻、浸酸、水洗、漂白和烘干等工艺,即加工为精干麻。
精干麻可作为纺纱、织造的纤维。
苎麻化学脱胶废水具有浓度高、色度高、碱度高和水温高等特点,其成分复杂,并含有大量难降解的有机物。
我国的苎麻生产和加工主要集中在四川、湖南、湖北和江西等地。
专业脱胶厂的废水可以分成三类,第一类是浓度极高的煮锅水,其COD值一般为8,000~12,000mg/L,呈棕褐色,水温为80~90℃,pH值为12~14,可生化性较好。
第二类是洗麻、拷麻和浸酸等中段水,这部分水量大,其COD值一般为400~500mg/L,水质呈酸性。
第三类为漂白废水,其COD值很低,一般不超过150 mg/L,并含有少量的氧化剂。
三种水混合后其COD值一般为2,000~2,500mg/L,呈碱性。
2. 废水的特征及水质该苎麻纺织厂排放的水质情况见表1和表2。
处理后水质要求达到GB8978-1996《污水综合排放标准》的二级标准,具体参数见表3。
3. 工艺工艺的选择处理苎麻脱胶废水的典型工艺有厌氧-好氧(活性污泥)工艺、生物转盘工艺和氧化沟工艺等,上述处理工艺虽然有一定的效果,但是随着人们对周围水体的环境质量要求越来越高,排放污染物质的控制指标(如COD、BOD)也越来越严,这种处理远远达不到目前的环境要求。
我们经过研究和多次试验得出结论:单纯的生化或物化工艺处理脱胶废水均有一定的效果,但是不能达标排放,而且处理效果不稳定,运行费用也居高不下,因此我们在一家苎麻纺织厂的废水设施改造中采用了“生化-物化”组合工艺,该工艺具有耐冲击负荷、运行稳定、易于管理和运行费用低等优点。
苎麻脱胶工艺
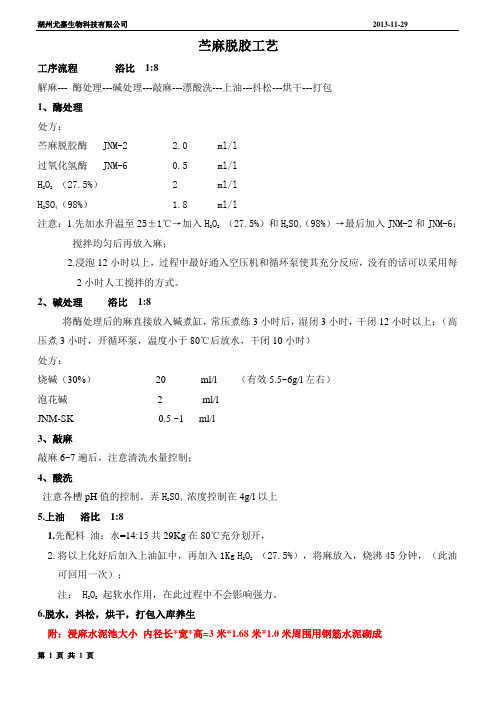
湖州尤嘉生物科技有限公司2013-11-29第 1 页共 1 页苎麻脱胶工艺工序流程浴比1:8解麻--- 酶处理---碱处理---敲麻---漂酸洗---上油---抖松---烘干---打包1、酶处理处方:苎麻脱胶酶 JNM-2 2.0 ml/l过氧化氢酶 JNM-6 0.5 ml/lH 2O2(27.5%) 2 ml/lH 2SO4(98%) 1.8 ml/l注意:1.先加水升温至25±1℃→加入H2O2(27.5%)和H2SO4(98%)→最后加入JNM-2和JNM-6;搅拌均匀后再放入麻;2.浸泡12小时以上,过程中最好通入空压机和循环泵使其充分反应,没有的话可以采用每2小时人工搅拌的方式。
2、碱处理浴比1:8将酶处理后的麻直接放入碱煮缸,常压煮练3小时后,湿闭3小时,干闭12小时以上;(高压煮3小时,开循环泵,温度小于80℃后放水,干闭10小时)处方:烧碱(30%)20 ml/l (有效5.5~6g/l左右)泡花碱 2 ml/lJNM-SK 0.5 ~1 ml/l3、敲麻敲麻6~7遍后,注意清洗水量控制;4、酸洗注意各槽pH值的控制。
弄H2SO4浓度控制在4g/l以上5.上油浴比1:81.先配料油:水=14:15共29Kg在80℃充分划开,2.将以上化好后加入上油缸中,再加入1Kg H2O2(27.5%),将麻放入,烧沸45分钟,(此油可回用一次);注: H2O2起软水作用,在此过程中不会影响强力。
6.脱水,抖松,烘干,打包入库养生附:浸麻水泥池大小内径长*宽*高=3米*1.68米*1.0米周围用钢筋水泥砌成。
第三章 苎麻脱胶
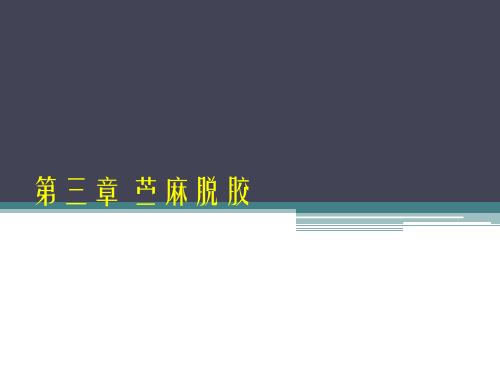
• 脱胶是苎麻纺织品生产加工过程中的关键环节。脱胶效果 的好坏,直接影响纺纱质量。
一、苎麻脱胶的要求
• 苎麻单纤维长度很长,平均长度在60mm以上。苎麻纤维强 度是天然纤维中最高者,长度和强度足以满足纺纱加工的 要求,所以,为纺制细度细、均匀度好的苎麻纱,苎麻脱 胶时应全部脱去胶质而获得单纤维,即采用全脱胶的方法。 苎麻纤维单细胞在韧皮中互相疏松地排列结构,也使全脱 胶成为可能。在脱胶过程中,要注意尽量减少损伤纤维, 获得尽可能高的制成率。
存在的问题
• 迄今为止,国内苎麻生物脱胶法还未能普及,国外也仅仅停留在试验生产阶 段。脱胶菌种产酶能力低,菌种脱胶关键酶活力不高或分泌的酶系不全、脱 胶效果不稳定等使脱胶处理达不到麻对纤维残胶率的要求,主要原因有:
• (1)苎麻胶质成分十分复杂,根据酶的专一性原理,需要相应的复杂酶系。 而自然界的菌株往往只有一种或几种相关的酶类,或者缺少脱胶关键酶。故 需要复合菌群的作用降低苎麻胶质,达到脱胶的目的。
• (2)节能、环保优势
苎麻生物脱胶较化学脱胶
可节约脱胶用水30%以上,节约能耗15%以上,污 水排放能够达到国家和地方政府规定的约束性指 标。脱胶剂投入减少80%。化学脱胶中原麻的木质 素,依靠酸、碱、氯等化学药品对其氯化,产生 大量的色素,而生物脱胶中的污水色素大量降低, 在污水整理中生物脱胶废水的色度处理较为简单。
二、脱胶方法
主要有两种: 1、化学脱胶 2、生物脱胶
(一)化学脱胶
• 化学脱胶是根据原麻中纤维素和胶质成分化学性质的 差异,以化学处理为主去除胶质的脱胶方法。由前面 分析可知,纤维素和胶质对烧碱作用的稳定性差异最 大。因此,苎麻化学脱胶只能以碱液煮练为主的方法 进行。其它化学药剂的处理,如酸和氧化剂的处理, 以及机械物理方法的处理等,是获得优良质量的精干 麻的辅助手段,化学脱胶可以去除原麻中绝大部分胶 质,达到全脱胶的要求。所以,目前国内外工业脱胶 基本上采用化学脱胶的方法。
苎麻微生物脱胶菌株的筛选
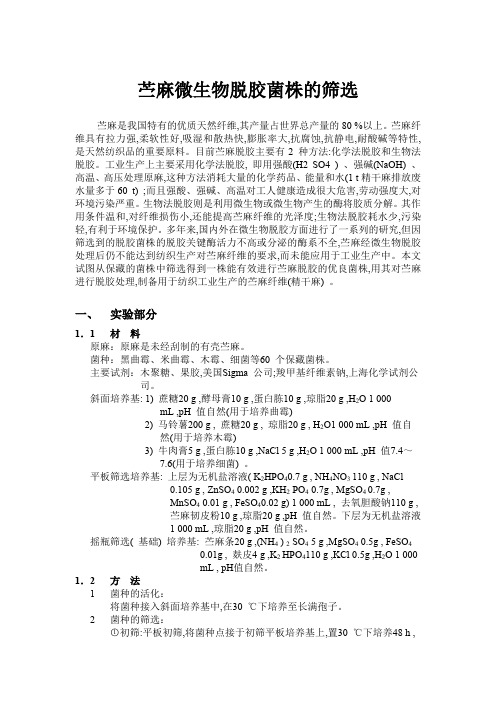
苎麻微生物脱胶菌株的筛选苎麻是我国特有的优质天然纤维,其产量占世界总产量的80 %以上。
苎麻纤维具有拉力强,柔软性好,吸湿和散热快,膨胀率大,抗腐蚀,抗静电,耐酸碱等特性,是天然纺织品的重要原料。
目前苎麻脱胶主要有2 种方法:化学法脱胶和生物法脱胶。
工业生产上主要采用化学法脱胶, 即用强酸(H2 SO4 ) 、强碱(NaOH) 、高温、高压处理原麻,这种方法消耗大量的化学药品、能量和水(1 t精干麻排放废水量多于60 t) ;而且强酸、强碱、高温对工人健康造成很大危害,劳动强度大,对环境污染严重。
生物法脱胶则是利用微生物或微生物产生的酶将胶质分解。
其作用条件温和,对纤维损伤小,还能提高苎麻纤维的光泽度;生物法脱胶耗水少,污染轻,有利于环境保护。
多年来,国内外在微生物脱胶方面进行了一系列的研究,但因筛选到的脱胶菌株的脱胶关键酶活力不高或分泌的酶系不全,苎麻经微生物脱胶处理后仍不能达到纺织生产对苎麻纤维的要求,而未能应用于工业生产中。
本文试图从保藏的菌株中筛选得到一株能有效进行苎麻脱胶的优良菌株,用其对苎麻进行脱胶处理,制备用于纺织工业生产的苎麻纤维(精干麻) 。
一、实验部分1.1 材料原麻:原麻是未经刮制的有壳苎麻。
菌种:黑曲霉、米曲霉、木霉、细菌等60 个保藏菌株。
主要试剂:木聚糖、果胶,美国Sigma 公司;羧甲基纤维素钠,上海化学试剂公司。
斜面培养基: 1) 蔗糖20 g ,酵母膏10 g ,蛋白胨10 g ,琼脂20 g ,H2O 1 000mL ,pH 值自然(用于培养曲霉)2) 马铃薯200 g , 蔗糖20 g , 琼脂20 g , H2O1 000 mL ,pH 值自然(用于培养木霉)3) 牛肉膏5 g ,蛋白胨10 g ,NaCl 5 g ,H2O 1 000 mL ,pH 值7.4~7.6(用于培养细菌) 。
平板筛选培养基: 上层为无机盐溶液( K2HPO40.7 g , NH4NO3 110 g , NaCl0.105 g , ZnSO4 0.002 g ,KH2 PO4 0.7g , MgSO4 0.7g ,MnSO4 0.01 g , FeSO40.02 g) 1 000 mL , 去氧胆酸钠110 g ,苎麻韧皮粉10 g ,琼脂20 g ,pH 值自然。
苎麻的化学脱胶

苎麻的化学脱胶1.方案二煮一漂化学方法脱胶2.工艺流程原麻拆包、拣麻。
扎把—浸酸—水洗—一次碱液煮练—热水洗—二次碱液煮练—水洗—打纤—漂白—酸洗—水洗—脱水—给油—脱水—抖松—干燥,得到精干麻。
3.工艺参数碱液煮练工艺参数氢氧化钠的浓度一般选择10g/l,占溶液的11%左右,化学助剂占溶液的3%到4%,压力采用147kpa,温度控制在123摄氏度左右,煮练时间大约为3小时左右,采用的浴比是1:20浸酸工艺参数(预处理工艺)硫酸溶液的浓度在1.5/1—2.0/1之间,温度控制在55度,浸酸时间是1小时,浴比是1:20酸洗(后处理工艺)硫酸浓度在1.5g/1—2.0g/1之间,只要浸泡2至3分钟,浴比采用1:20 漂白常用的有效氯浓度在1.5g/1—2.0g/1之间,实验室没有氯,所以用双氧水,浓度为30%,只要浸泡2到3分钟,浴比采用1:20.给油工序将已脱水并经抖松的嘛束浸入给油槽中,给油槽内的温度在85摄氏度以上,焖煮时间为4小时以上,要求给油精干麻的含油率在0.7%到1.5%之间。
机械处理工序给油处理后麻束再经脱水、给松、干燥。
三、实验1. 实验材料:(1)主要仪器:TG32BA型电光分析天平(最大载荷200g,分度0.1mg);PHB 一29酸度仪(pH测量范围0~14);各种大小的烧杯;Y802型八篮烘箱;HHS11—6电热恒温水浴锅;XQ一1纤维拉伸仪;普通天平;三角量杯;酒精灯;支撑架;石棉网;火柴;电磁炉;玻璃棒;打纤槌。
(2)主要原料和化学药品苎麻原麻;自来水;氢氧化钠固体;双氧水(密度1.11gcm);硅酸钠固体;三聚磷酸钠;渗透剂;98%浓硫酸;98%茶油。
2.实验步骤:1. 取样从老师提供的苎麻中选出一部分,并手工将剩余的一点点未清除的青皮去掉,扎把后用电子天平称,称取10g苎麻。
2. 浸酸工艺参数:①硫酸浓度:2.0g/L ②浴比:1:20 ③温度:恒温槽中,约50℃ ④时间1小时步骤:a. 计算和准备通过浴比计算出溶液质量为200g;利用溶液质量和硫酸浓度计算出硫酸用量为0. 4g(0.010*20*2=0.4g 因所配硫酸浓度很低,所以密度按1g/ml计算)b. 制取溶液⑴将干燥的空烧杯放在称重仪上,得到烧杯重量为2.9g;⑵用滴管往烧杯中滴入一滴浓硫酸,观查屏幕变化(不可超过3.0g),未到达3.0g则再滴入少量浓硫酸,直至到达3.0g左右,误差小于百分之一。
苎麻脱胶工艺的研究
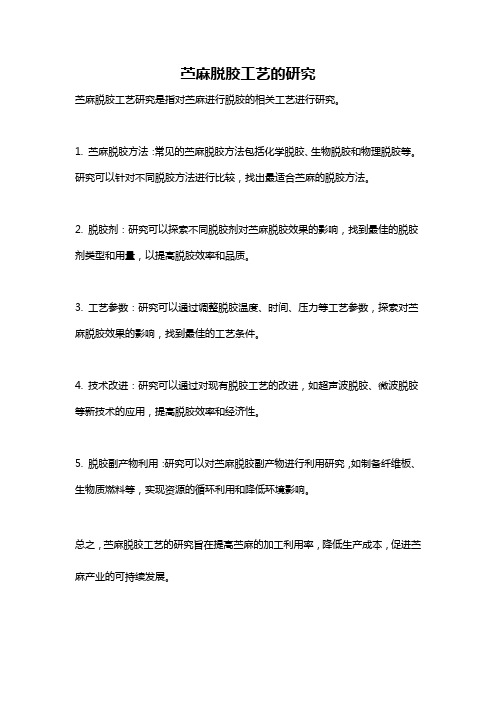
苎麻脱胶工艺的研究
苎麻脱胶工艺研究是指对苎麻进行脱胶的相关工艺进行研究。
1. 苎麻脱胶方法:常见的苎麻脱胶方法包括化学脱胶、生物脱胶和物理脱胶等。
研究可以针对不同脱胶方法进行比较,找出最适合苎麻的脱胶方法。
2. 脱胶剂:研究可以探索不同脱胶剂对苎麻脱胶效果的影响,找到最佳的脱胶剂类型和用量,以提高脱胶效率和品质。
3. 工艺参数:研究可以通过调整脱胶温度、时间、压力等工艺参数,探索对苎麻脱胶效果的影响,找到最佳的工艺条件。
4. 技术改进:研究可以通过对现有脱胶工艺的改进,如超声波脱胶、微波脱胶等新技术的应用,提高脱胶效率和经济性。
5. 脱胶副产物利用:研究可以对苎麻脱胶副产物进行利用研究,如制备纤维板、生物质燃料等,实现资源的循环利用和降低环境影响。
总之,苎麻脱胶工艺的研究旨在提高苎麻的加工利用率,降低生产成本,促进苎麻产业的可持续发展。
一种苎麻的脱胶方法

一种苎麻的脱胶方法
苎麻的脱胶方法可以分为化学脱胶和机械脱胶两种。
化学脱胶方法:
1. 将苎麻浸泡在碱液中,常用的碱液有氧化钠溶液或氢氧化钠溶液。
苎麻在碱液中浸泡一段时间,胶质会被分解,然后用清水冲洗。
2. 使用酶类脱胶剂,将苎麻浸泡在酶液中。
酶可以分解胶质,使其变得松散,然后用清水冲洗。
机械脱胶方法:
1. 使用刮刀将苎麻的表面胶层刮掉。
2. 使用切割机或切割工具将苎麻纤维切碎,然后通过筛网分离胶质。
无论是化学脱胶还是机械脱胶,处理后的苎麻纤维需要经过洗涤和干燥等工艺步骤,以便进一步加工和应用。
- 1、下载文档前请自行甄别文档内容的完整性,平台不提供额外的编辑、内容补充、找答案等附加服务。
- 2、"仅部分预览"的文档,不可在线预览部分如存在完整性等问题,可反馈申请退款(可完整预览的文档不适用该条件!)。
- 3、如文档侵犯您的权益,请联系客服反馈,我们会尽快为您处理(人工客服工作时间:9:00-18:30)。
《纺织加工化学》课程设计课程设计题目: 苎麻的初加工工艺设计姓 名:班 级:学 号:指 导 老 师:日 期: 2 0 0 9 年 1 2 月目录一、任务书 (1)二、前言 (3)三、设计原理 (6)四、实验 (9)五、结论 (14)六、参考文献 (17)七、致谢(心得) (18)八、附件 (18)一、任务书(一)目的通过该课程设计周培养学生查阅资料,综合要运用所学的纺织加工化学等专业课程知识进行设计、实验、撰写设计说明书等的能力。
(二)课程设计简介及基本要求课程设计是纺织加工化学教学中极为重要的一个环节,本课程设计为一周时间。
为培养学生查阅资料能力、独立设计、计算和安排实验以及动手操作的能力,要求在老师的指导下由学生独立完成。
课程设计要求:1.做好设计前预习,巩固和加深纺织加工化学基本理论知识,能综合运用所学知识解决纺织加工化学问题。
2.能通过查阅资料,对比分析,根据设计要求进行实验方案设计,并具有创新性。
3.能通过查阅仪器使用说明书和有关资料,正确的使用仪器设备并了解设备的使用、测试原理。
4.复习和巩固化学实验的知识,能独立正确的完成试剂的配置、用具的洗涤、具体操作等等。
5.实验过程中认真观察每一个现象并记录,实验结果记录具有科学性、准确性,及时修改自己的设计方案。
6.撰写设计说明书要真实的记载设计、实验结果,并加以分析讨论,得出有说服力的结论。
(三)课程设计目的要求纺织加工化学是纺织工程专业的主干课程之一,需要通过一定的课程设计在纺织化学加工中综合应用基本的化学实验技能。
通过课程设计及实验使学生巩固和加深纺织加工化学的理论知识,加强学生独立分析问题和解决问题的能力、综合设计能力及创新能力。
培养学生实事求是、严肃粉针的科学作风和良好的设计、实验习惯。
(四)课程设计的基本内容1.麻纤维的化学脱胶设计化学处理工艺、物理化学处理工艺及其碱处理工艺设计。
2.羊毛的洗涤及炭化设计洗毛工艺设计、炭化方法设计、散毛炭化工艺设计。
3.绢纺原料精炼设计绢纺原料微生物精炼的工艺设计、酶制剂精炼、微生物精炼设计绢纺原料化学精炼的工艺设计、工艺流程设计、工艺参数设计、绢纺原料除油等设计。
(五)时间安排一周分为四个阶段:第一阶段:(时间为半天)由指导老师布置任务、讲解课程设计要求和任务第二阶段:(时间为1天半)学生查阅相关资料,初步确定课程设计的题目、课程设计多种方案及设计方案。
交给指导老师检查、审核。
第三阶段:(时间为2天)在实验室做实验并修正自己的方案(2人一组)。
第四阶段:(时间为1天)撰写设计说明书并修改和完善。
(六)设计说明书的打印要求:1、中文题目(黑体、加粗、3号字);中文摘要、关键词、正文;2、一级标题(黑体、小3号字);二级标题(黑体、4号字);三级标题(黑体、小4号字);目录(小4号字);图题表题(黑体、5号字);图表文字(5号宋体);注释、参考文献(宋体、5号字)。
3、页眉:5号宋体内容为课程设计说明书题目,居中;页码:右下角;4、行距:1.5倍;5、打印用纸规格为A4。
(七)、课程设计说明书的要求:学生一人撰写一篇设计说明书,设计说明书应包括封面、目录、设计任务书、中文题目、摘要、关键词、正文、参考文献、附件、封底。
字数要求在8000字以上,参考文献应不少于10篇(不包括辞典、手册)。
要求手写。
(八)、成绩评定:根据学生提交的设计设计质量、实验情况、设计说明书书写质量、参考学生出勤情况、工作态度、文明作风等,按优秀、良好、中等、及格和不及格五级计分。
二、前言(一)、羊毛的洗涤炭化洗涤可以分为干洗和湿洗两大类型,原毛洗涤系湿加工。
在湿洗过程中除使用大量热水外,还需一定数量的洗涤剂和助洗剂。
最早的洗毛方法是在肥皂和纯碱溶液中进行的,这就是通常所说的皂碱洗毛法,但自从合成洗涤剂问世后,就逐渐用于洗毛工业,目前在国内外洗毛工业中均普遍使用了各种合成洗涤剂,有利于保护羊毛纤维的优良品质和提高洗净毛的质量。
洗毛工程用剂主要指洗涤剂和助洗剂。
我国的洗毛工业中目前仍以采用阴离子型洗涤剂为主,如烷基磺酸钠、烷基苯磺酸钠等。
国外目前采用非离子型洗涤剂较多。
此外,在洗毛过程中还用些助洗剂。
这些助洗剂大多为电解质。
在羊毛中常常黏附着各种草杂,其品种和数量随产地与饲养管理方法的不同而不同。
由于草杂种类的不同,它与羊毛联系状态亦有区别,有的易于分离,经开毛‘洗毛等加工之后,基本上可以去除,有的与羊毛紧密纠结在一起,不但开毛不能将它去除,就是梳毛时也不能除尽[4]。
若羊毛中的草杂去除不干净,会对后道加工带来困难。
为此,必须在羊毛初步加工过程中设法将草杂除去。
去草有机械和化学两种方法,在粗疏毛纺的原料初加工中一般采用化学的去草方法,又称炭化,这种方法去除草杂比较彻底,但易造成羊毛纤维的化学损伤,进而影响后续加工的进行和产品质量。
炭化加工是化学加工,最理想的炭化用剂应当是只对草杂发生作用,而又无损于羊毛纤维,但是至今还未发现有这样的化学药品。
现行炭化加工是利用硫酸处理含有植物性草杂的羊毛,使酸于草杂发生作用而最后将其除去,但这也将给羊毛纤维带来一定程度的损伤,只是在加工过程中严格控制炭化工艺条件,以尽量减少羊毛纤维的损伤程度。
(二).绢纺原料精炼绢纺原料通过精炼要把多余的丝胶从茧丝上脱下,使纤维上保持均匀一致的残胶,是一项很重要的工作。
因为脱胶的多少,其残胶是否均匀,直接影响到绢丝的质量和制成率。
由于各厂对脱胶的认识不一致,因此,各厂的产质量制成率及成本有时相差很大。
绢纺原料的脱胶主要靠水,其次才是化学助剂。
因为单靠水已可以脱去胶质,化学助剂在脱胶中仅起辅助作用,即起到促进或缩短脱胶时间的作用。
精炼方法:根据精炼时加入的药剂的不同,绢纺原料的精炼可分为碱精炼法和酸精炼法两种。
碱精炼法又可分为纯碱精炼法和皂碱精炼法两种。
由于丝胶蛋白质偏酸性,其等电点在ph=3.8-4.5,在碱性溶液中溶解较好,故目前普遍采用的是纯碱筒式精炼法[10]绢丝原料的除油问题,一直是精炼中的难题。
在现有的除油方法中,为降低成本,主要使用廉价的纯碱和肥皂。
但这两种助剂的除油效果均不理想。
为发挥纯碱的作用,就必须使油脂完善的水解成脂肪酸。
可采用在纯碱溶液中低温长期浸泡和微生物处理的方法,是油脂水解。
再经纯碱液复练,使水解出的脂肪酸与纯碱反应而去除[5]。
在除油过程中能否充分发挥纯碱的作用,其中控制精炼的温度,是精炼中保胶除油的关键。
肥皂在除油中其到乳化除油和洗涤除油的作用。
[3](三).苎麻的脱胶中国是世界上麻类资源最丰富的国家之一,主要的麻纤维包括苎麻、亚麻、黄麻、大麻等。
苎麻是我国独有的特色资源,号称“中国萆”,主要分布在湖北、湖南、江西、四川等省,总产量约占世界的90%,我国常年种植面积约在10万-20万公顷之间,纤维总产能达到12万-25万吨。
[1]麻类作物韧皮中除含有纤维素外,还含有一些胶杂质,包括果胶物质、半纤维素和木质素等成分。
韧皮组织中的纤维处于胶质的包围之中,胶质将各单纤维粘结成片状。
不能直接用来纺纱。
[2]此外,在植物生长过程中,由于风灾和病虫害的侵袭而形成的风斑、虫斑等疵点,以及由于收获、剥制等操作不良而使一些麻壳、皮屑留在原麻中,同样不利于纺织加工。
所以梳纺工程前必须进行脱胶工程处理,脱去原麻中的胶质,制取出其中的苎麻纤维。
[3]麻纤维的脱胶过程严格说就是精致纤维素的过程。
脱胶过程的组织和工艺参数的选择必须注意掌握两点原则,脱去原麻中的胶质,使制取出的纤维满足纺纱工程和产品质量的要求,为其一,其二是对纤维的损伤要尽量少[6]。
因此,麻纤维的化学脱胶工艺过程不能采用以无机酸为主的工艺,也不能采用以氧化剂为主的工艺,只能采用以碱液煮炼为中心的工艺过程。
麻纤维的化学脱胶过程基于此理组织的。
概括地说,就是利用原麻中的纤维素和胶杂质成分对碱、无机酸和氧化剂作用的稳定性的不同,在不损伤纤维原有机械性质的原则下,去除其中的胶质成分,而保留或制取纤维素的化学加工过程为了弥补化学药剂作用的不足,在脱胶工艺中还必须辅以一定的机械物理的、化学的和物理化学的作用[7]。
为提高碱液的煮炼效果,提高脱胶麻的质量,在碱液煮炼前后分别加以预处理和后处理两大工艺过程。
因此,麻纤维的化学脱胶工艺从大的方面来说包括三个主要工艺过程,即预处理工艺、碱液煮炼工艺和后处理工艺。
从原麻的化学成分及纺织工业对麻纤维的品质要求中知道,原麻中的果胶物质、半纤维素、木质素等胶质成分都是妨碍合理利用麻纤维的杂质。
利用微生物的生命活动脱去原麻中的胶质的方法成为微生物脱胶法,是麻纤维脱胶的方法之一。
微生物脱胶的基本原理就是利用某些微生物以这些胶质为其碳素营养来源的特性,将果胶物质、半纤维素以及木质素等物质分解转换为简单的低分子物质,从中得到本身生命活动所需的营养物质和热能,从而完成麻纤维的脱胶过程[8]。
因此,对脱胶用的微生物来说,要求它的碳素营养来源的专性要特别强,即要求脱胶用微生物只能从分解果胶物质、半纤维素和木质素物质中作为自己唯一的碳素营养来源。
否则,可能破坏纤维素的结构而恶化麻纤维的品质。
苎麻的氧化脱胶法:苎麻氧化脱胶法,是利用氧化的方法把竺麻纤维中半纤维素,果胶,木质素的大分子切断,降解成小分子。
双氧水在酸性介质中很稳定,分解速率非常低,而在碱性介质中可以被活化,因此需要加人适量的氢氧化钠,为双氧水提供一个碱性环境[9]。
苎麻氧化脱胶的优点是精干麻制成率提高,脱胶的同时完成漂白工艺,流程简单,时间缩短,能耗大大减少,而且药品的量比脱胶、漂白二步法要少,相应的排污量也减少,有利于环境保护。
在氧化脱胶过程中,所涉及的主要工艺参数有H2O2用量,Na0H用量,煮练温度和煮练时间[10]。
为了找出最佳工艺参数,进行本实验并通过对工艺参数的方差分析,得出最优工艺参数。
该方法突破苎麻用老工艺所制成的支数,提高了原麻的经济效益和纤维的等级,为开发高档或细薄苎麻织物提供了原料基础,推动我国苎麻高档产品开发研究。
对开发国内外潜在市场和提高单位产品的换汇率有积极影响。
扶持苎麻纺织行业走出低谷,促进发挥我国兰麻栽培、加工及出口优势,推动农、工、贸经济发展。
工艺流程:苎麻-氧化煮练-水洗-亚硫酸钠洗-水洗-给油-脱油、脱水-烘干。
三、设计原理所选实验内容:苎麻的化学脱胶方案一:二煮一漂法工艺过程:原麻拆包、拣麻、扎把——浸酸▲——水洗——装笼▲(或装笼——浸酸——水洗)——一次碱液煮练▲——热水洗——二次碱液煮练▲——打纤▲(水冲洗)——漂白▲——酸洗▲——水洗——脱水——给油▲——脱水——抖松——干燥,得到精干麻。
▲:为重点工序。
预处理工艺过程:一次碱液煮练之前的工艺。
碱液煮练工艺过程:一次碱液煮练到二次碱液煮练的工序。
后处理工艺过程:二次碱液煮练之后的工序。