加氢精制装置说明与危险因素以及防范措施
加氢精制装置说明与危险因素以及防范措施

加氢精制装置说明与危险因素以及防范措施一、装置简介(一)装置发展及类型1.装置发展现代炼油工业的加氢技术(包括加氢工艺、催化剂和专用设备)是在第二次世界大战以前经典的煤和煤焦油高压催化加氢技术的基础上发展起来的。
1949年铂重整技术的发明和工业应用,除生产大量高辛烷值汽油组分外还副产大量廉价的氢气,对现代加氢技术的发明和发展起到了关键作用。
1950年炼油厂出现了加氢精制装置,1959年出现了加氢裂化装置,1963年出现了沸腾床渣油低转化率加氢裂化装置,1969年出现了固定床重油加氢脱硫装置,1977年出现了固定床渣油加氢脱硫装置,1984年出现了沸腾床渣油高转化率加氢裂化装置。
这些加氢技术的发明和工业应用,使加氢技术由发生、发展走向成熟。
加氢(包括加氢裂化、加氢精制和加氢处理)成为世界上加工能力最大的二次加32212艺,是炼油工业的三大支柱技术(加氢、催化裂化和催化重整)之一。
生产低硫、低芳烃和高十六烷值的优质柴油是当前世界范围内车用柴油燃料的生产趋势,也已成为国内各石化企业正在面临的挑战。
中石化股份公司已在2003年提出在国内实施《城市车用柴油》标准(Q/SHll008—2002),其主要质量指标:硫质量分数不大于0.030%,总芳烃质量分数不大于25%,多环芳烃质量分数不大于5%。
欧洲提出2005年将要求硫含量小于50X10—6,世界燃料规范Ⅲ类柴油的硫含量指标是30X10—6。
近几年,国内外文献报道有许多关于未来柴油规格的研究和推测,更低的柴油硫规格的推广正在加速。
所以研究开发能够生产低硫、低芳烃和高十六烷值的优质柴油的催化剂成为柴油加氢的主要发展方向。
本节主要以柴油加氢精制装置展开讨论说明。
2.装置的主要类型加氢精制是各种油品在氢压下进行改质的一个总称。
加氢精制处理原料油范围宽,产品灵活性大,液体产品收率高质量好。
加氢精制的目的主要是对油品进行脱硫、脱氮、脱氧、烯烃饱和、芳烃饱和和脱除金属、沥青杂质等,以达到改善油晶的气味、颜色和安定性,防止腐蚀,进一步提高产品质量,满足油品的使用要求。
加氢装置的组成与设备说明危险因素防范措施
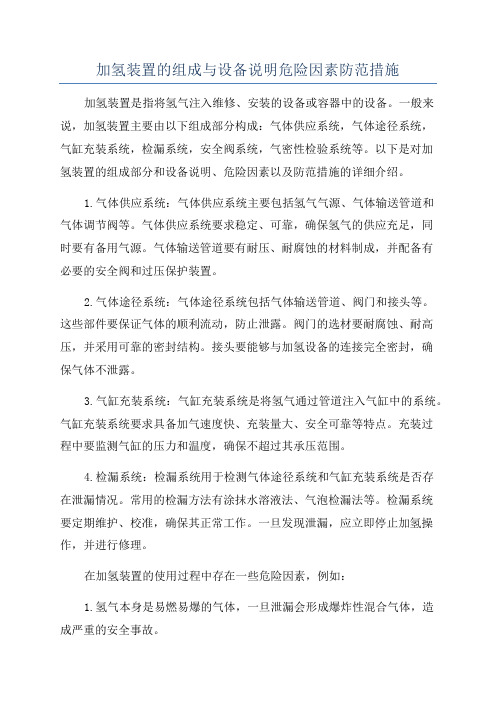
加氢装置的组成与设备说明危险因素防范措施加氢装置是指将氢气注入维修、安装的设备或容器中的设备。
一般来说,加氢装置主要由以下组成部分构成:气体供应系统,气体途径系统,气缸充装系统,检漏系统,安全阀系统,气密性检验系统等。
以下是对加氢装置的组成部分和设备说明、危险因素以及防范措施的详细介绍。
1.气体供应系统:气体供应系统主要包括氢气气源、气体输送管道和气体调节阀等。
气体供应系统要求稳定、可靠,确保氢气的供应充足,同时要有备用气源。
气体输送管道要有耐压、耐腐蚀的材料制成,并配备有必要的安全阀和过压保护装置。
2.气体途径系统:气体途径系统包括气体输送管道、阀门和接头等。
这些部件要保证气体的顺利流动,防止泄露。
阀门的选材要耐腐蚀、耐高压,并采用可靠的密封结构。
接头要能够与加氢设备的连接完全密封,确保气体不泄露。
3.气缸充装系统:气缸充装系统是将氢气通过管道注入气缸中的系统。
气缸充装系统要求具备加气速度快、充装量大、安全可靠等特点。
充装过程中要监测气缸的压力和温度,确保不超过其承压范围。
4.检漏系统:检漏系统用于检测气体途径系统和气缸充装系统是否存在泄漏情况。
常用的检漏方法有涂抹水溶液法、气泡检漏法等。
检漏系统要定期维护、校准,确保其正常工作。
一旦发现泄漏,应立即停止加氢操作,并进行修理。
在加氢装置的使用过程中存在一些危险因素,例如:1.氢气本身是易燃易爆的气体,一旦泄漏会形成爆炸性混合气体,造成严重的安全事故。
2.加氢装置的压力系统要求工作压力高,一旦发生管道破裂或阀门失灵,会造成压力突然释放,引发危险。
3.加氢装置存在气体泄漏的可能,泄漏的氢气有毒性,对人员健康造成威胁。
针对这些危险因素,需要采取一系列的防范措施,包括:1.加氢装置的设计、制造和安装必须符合国家标准和规范要求,确保设备质量稳定可靠。
2.加氢装置在使用前要进行严格检查,确保各个部件没有损坏、泄漏等问题。
3.加氢装置的操作人员必须经过专业培训,熟悉设备的使用方法和安全操作规程。
石蜡加氢精制装置说明与危险因素、防范措施

石蜡加氢精制装置说明与危险因素、防范措施一、装置简介(一)装置发展及类型1.装置发展石蜡精制工艺有白土精制、渗透精制、硫酸精制和加氢精制四种类型,其中白土精制和渗透精制都不容易脱净蜡中的稠环芳烃,难以生产对于纯度要求很高的食品工业用蜡:而硫酸精制方法的主要缺点是产品产率低,劳动条件恶劣,有大量的废渣产生,污染环境。
无论在生产成本上,产品产率和质量及环境保护上,石蜡加氢精制均比其他精制工艺有明显的优越性。
因此,在国外主要炼油厂中,石蜡加氢精制己逐步代替其他精制工艺。
1957年加拿大萨尼亚炼油厂首先宣布用钼钻铝催化剂加氢精制生产白石蜡,由于该工艺对蜡中稠环芳烃组分有很好的加氢转化能力,容易制取食品级纯度商品蜡而进一步为人们重视;其后催化重整工艺的兴起,为炼油厂提供了廉价的氢气来源,尤为石蜡加氢精制装置的建设创造了有利条件。
1962年一套处理量为1.5X104t/a、10.0MPa的石蜡和凡士林加氢精制装置在西德汉堡建成。
1963年美国大西洋公司费城炼油厂建成日处理量300t/a的石蜡加氢精制装置,代替原来的石蜡硫酸和渗透精制工艺。
我国从20世纪70年代初正式开始研究石蜡加氢精制催化剂和工艺,1979年11月大庆石化总厂首次采用5053催化剂进行处理量6X104t/a的低压石蜡加氢装置开工投产。
1981年10月石油工业部对481—2B催化剂及中压石蜡加氢精制工艺组织技术鉴定,本工艺先后在东方红炼油厂(现中石化燕山分公司炼油厂)、抚顺石油一厂、荆们炼油厂、大连石油七厂茂名炼油厂实现工业化。
1983年11月第一套采用石蜡加氢专用催化剂处理量为6×104t/a的石蜡加氢装置在东方红炼油厂投产,1984年另两套石蜡加氢装置在抚顺石油一厂和荆门炼油厂投产,1986年又两套石蜡加氢装置在大连石油七厂和茂名炼油厂相继投产。
2.装置的主要类型20世纪60年代以来国外陆续发展的蜡加氢精制工艺有十多种,可归纳为五种类型见表2—85。
加氢精制装置的危险因素与防范措施

加氢精制装置的危险因素与防范措施摘要:加氢精制装置是一种用于石油、化工等行业的工艺装置,其核心过程是利用氢气与原料油中的不饱和烃进行加成反应,从而降低原料油的硫、氮、氧等杂质的含量,提高其纯度和收率。
然而,由于加氢精制过程中涉及到高温、高压、高纯度氢气等危险因素,因此存在着许多危险因素和安全隐患。
本文将介绍加氢精制装置的危险因素与防范措施。
关键词:加氢精制装置;危险因素;防范措施1 加氢精制装置运行过程中的设备危险因素及预防措施1.1 加氢精制装置运行过程中的设备危险因素加氢精制装置中的设备通常会受到腐蚀的影响,例如设备表面受到氧化、硫化物等物质的腐蚀,设备内部的金属受到氢脆、氢裂等损伤。
这些腐蚀和损伤会导致设备的损坏和失效,从而影响装置的正常运行。
设备磨损加氢精制装置中的设备也会受到磨损的影响,例如设备内部的金属受到摩擦、冲刷等作用的磨损,设备表面的涂层和密封材料受到磨损和剥落的影响。
这些磨损会导致设备的性能下降,从而影响装置的正常运行。
设备超载加氢精制装置中的设备可能会因为负荷过大而超载运行,例如原料油中含有的有害物质过多,导致装置的处理能力不足。
超载运行会导致设备的损坏和失效,从而影响装置的正常运行。
设备操作失误加氢精制装置中的设备需要严格的操作控制,例如温度、压力、流速等参数的控制。
如果操作失误,例如温度过高、压力过低等,会导致设备的损坏和失效,从而影响装置的正常运行。
1.2 如何预防加氢精制装置设备危险因素设备防腐措施对于加氢精制装置中的设备,可以采用多种防腐措施来减少腐蚀和损伤的影响。
例如,可以采用耐腐蚀材料制作设备,例如不锈钢、钛合金等;可以采用防腐涂层来保护设备表面,例如喷涂、电镀等;可以采用防腐处理来提高设备的耐腐蚀性能,例如钝化处理、磷化处理等。
设备耐磨措施对于加氢精制装置中的设备,可以采用多种耐磨措施来减少磨损的影响。
例如,可以采用高强度材料制作设备,例如高强度钢、陶瓷等;可以采用耐磨涂层来保护设备表面,例如喷涂、熔敷等;可以采用耐磨处理来提高设备的耐磨性能,例如喷丸处理、滚压处理等。
润滑油加氢补充精制装置腐蚀分析及防护措施
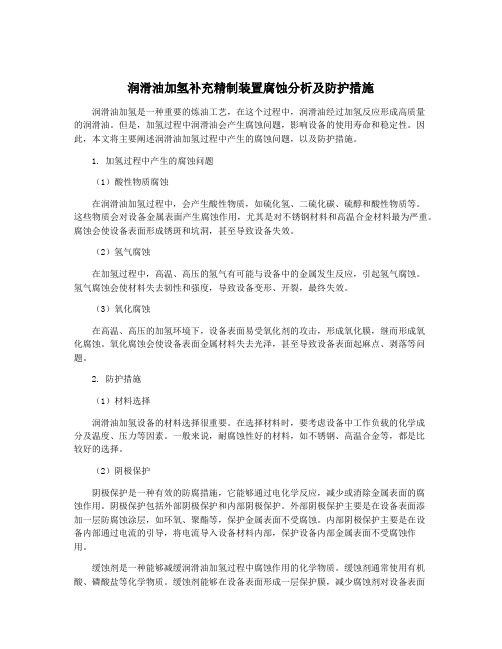
润滑油加氢补充精制装置腐蚀分析及防护措施润滑油加氢是一种重要的炼油工艺,在这个过程中,润滑油经过加氢反应形成高质量的润滑油。
但是,加氢过程中润滑油会产生腐蚀问题,影响设备的使用寿命和稳定性。
因此,本文将主要阐述润滑油加氢过程中产生的腐蚀问题,以及防护措施。
1. 加氢过程中产生的腐蚀问题(1)酸性物质腐蚀在润滑油加氢过程中,会产生酸性物质,如硫化氢、二硫化碳、硫醇和酸性物质等。
这些物质会对设备金属表面产生腐蚀作用,尤其是对不锈钢材料和高温合金材料最为严重。
腐蚀会使设备表面形成锈斑和坑洞,甚至导致设备失效。
(2)氢气腐蚀在加氢过程中,高温、高压的氢气有可能与设备中的金属发生反应,引起氢气腐蚀。
氢气腐蚀会使材料失去韧性和强度,导致设备变形、开裂,最终失效。
(3)氧化腐蚀在高温、高压的加氢环境下,设备表面易受氧化剂的攻击,形成氧化膜,继而形成氧化腐蚀。
氧化腐蚀会使设备表面金属材料失去光泽,甚至导致设备表面起麻点、剥落等问题。
2. 防护措施(1)材料选择润滑油加氢设备的材料选择很重要。
在选择材料时,要考虑设备中工作负载的化学成分及温度、压力等因素。
一般来说,耐腐蚀性好的材料,如不锈钢、高温合金等,都是比较好的选择。
(2)阴极保护阴极保护是一种有效的防腐措施,它能够通过电化学反应,减少或消除金属表面的腐蚀作用。
阴极保护包括外部阴极保护和内部阴极保护。
外部阴极保护主要是在设备表面添加一层防腐蚀涂层,如环氧、聚酯等,保护金属表面不受腐蚀。
内部阴极保护主要是在设备内部通过电流的引导,将电流导入设备材料内部,保护设备内部金属表面不受腐蚀作用。
缓蚀剂是一种能够减缓润滑油加氢过程中腐蚀作用的化学物质。
缓蚀剂通常使用有机酸、磷酸盐等化学物质。
缓蚀剂能够在设备表面形成一层保护膜,减少腐蚀剂对设备表面的腐蚀作用。
但需要注意的是,缓蚀剂的使用要控制在一定的浓度范围内,否则会对设备的运行产生负面影响。
总之,润滑油加氢的防腐措施是非常重要的。
加氢裂化装置危险因素分析及防范措施

加氢裂化装置危险因素分析及防范措施加氢裂化装置是一种常见的石油炼制设备,用于将重质石油馏分转化为轻质产品。
由于其涉及高温、高压和易燃气体的处理,加氢裂化装置存在一定的危险因素。
以下是对加氢裂化装置危险因素进行分析及防范措施的详细讨论:1.高温、高压环境:加氢裂化装置的操作温度和压力很高,这可能导致爆炸、烫伤和压力容器失效等危险。
防范措施包括进行严格的设备检测和维护,确保设备的可靠性和安全性。
同时,操作人员应接受专业培训,了解设备操作程序,并采取必要的个体防护措施。
2.氢气泄漏:加氢裂化过程需要大量的氢气供应,氢气泄漏可能导致爆炸和火灾。
防范措施包括建立有效的检测系统,例如氢气泄漏传感器和气体监测装置。
同时,设立紧急切断阀以及紧急撤离和逃生计划,以应对可能的危险情况。
3.操作错误:不正确的操作可能导致设备失控、爆炸和火灾。
防范措施包括操作人员的严格培训和技能认证,强调正确操作程序和注意事项,以及建立安全监控和控制系统,控制操作参数,并及时警报和采取应对措施。
4.化学品泄漏:在加氢裂化过程中使用的化学品可能泄漏,对人员和环境造成危害。
防范措施包括使用正确的储存和搬运设备,建立紧急泄漏应急预案,设立泄漏控制设备如泄漏检测器和紧急疏散装置,以及进行必要的防护措施如化学品接触个体防护装备。
5.火灾和爆炸风险:加氢裂化装置中操作的高温、高压环境以及易燃气体的存在,使得火灾和爆炸风险变得更高。
防范措施包括使用防火和防爆设备、建立火灾报警和满足灭火系统,完善紧急疏散和撤离计划。
6.设备失效:设备故障可能导致操作失控和危险情况的发生。
防范措施包括进行定期设备检测和维护,实施预防性维护计划,及时更换老化设备,以及建立备用设备和应急备件库存。
7.环境污染:加氢裂化装置的操作会产生废气和废水,其中可能含有有毒物质。
防范措施包括建立废气和废水处理系统,确保其符合环境法规标准。
此外,通过合理的能源利用和废弃物管理措施,减少对环境的不良影响。
制氢—装置重点部位设备说明与危险因素及防范措施
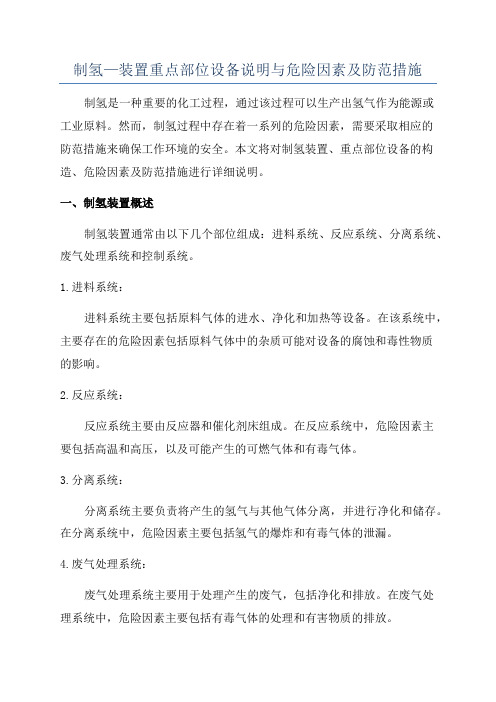
制氢—装置重点部位设备说明与危险因素及防范措施制氢是一种重要的化工过程,通过该过程可以生产出氢气作为能源或工业原料。
然而,制氢过程中存在着一系列的危险因素,需要采取相应的防范措施来确保工作环境的安全。
本文将对制氢装置、重点部位设备的构造、危险因素及防范措施进行详细说明。
一、制氢装置概述制氢装置通常由以下几个部位组成:进料系统、反应系统、分离系统、废气处理系统和控制系统。
1.进料系统:进料系统主要包括原料气体的进水、净化和加热等设备。
在该系统中,主要存在的危险因素包括原料气体中的杂质可能对设备的腐蚀和毒性物质的影响。
2.反应系统:反应系统主要由反应器和催化剂床组成。
在反应系统中,危险因素主要包括高温和高压,以及可能产生的可燃气体和有毒气体。
3.分离系统:分离系统主要负责将产生的氢气与其他气体分离,并进行净化和储存。
在分离系统中,危险因素主要包括氢气的爆炸和有毒气体的泄漏。
4.废气处理系统:废气处理系统主要用于处理产生的废气,包括净化和排放。
在废气处理系统中,危险因素主要包括有毒气体的处理和有害物质的排放。
5.控制系统:控制系统主要对整个制氢过程进行自动化控制和监测。
危险因素主要包括设备的故障和操作失误导致的事故。
1.高温和高压:在反应系统中,由于制氢过程需要高温和高压条件,因此存在爆炸和火灾的危险。
为了防范此类危险,应采取以下措施:-选择高温和高压下耐热、耐压的材料,并定期检查其状况。
-安装压力传感器和温度传感器,实时监测反应器的压力和温度,并设置相应的报警装置。
-定期对反应器进行检修和维护,确保其安全运行。
2.毒性与腐蚀性物质:制氢过程中会引入原料气体,可能存在毒性物质和腐蚀性物质。
为了防范这些危险,应采取以下措施:-在进料系统中加入净化设备,去除原料气体中的杂质。
-选择耐腐蚀的材料,并定期对设备进行检查和维护。
-在可能泄漏的部位安装气体泄漏报警装置,并制定相应的应急处理措施。
-对操作人员进行必要的防护措施培训,提供必要的个人防护设备。
加氢装置开停工时的危险因素及防范措施

加氢装置开停工时的危险因素及防范措施开工时的危险因素及其防范措施1加氢反应系统干燥、烘炉加氢装置反应系统干燥、烘炉的目的是除去反应系统内的水分,脱除加热炉耐火材料中的自然水和结晶水,烧结耐火材料,增加耐火材料的强度和使用寿命。
加热炉煤炉时,装置需引进燃料气,在引燃料气前应认真做好瓦斯的气密及隔离工作,一般要求燃料气中氧含量要小于1%。
防止瓦斯泄漏及窜至其他系统。
加热炉点火要彻底用蒸汽吹扫炉膛,其中不能残余易燃气体。
加热炉烘炉时应严格按烘炉曲线升温、降温,避免升温过快,耐火材料中的水分迅速蒸发而导致炉墙倒塌2加氢反应器催化剂装填催化剂装填应严格按催化剂装填方案进行,催化剂装填的好坏对加氢装置的运行情况及运行周期有重要影响。
催化剂装填前应认真检查反应器及其内构件,检查催化剂的粉尘情况,决定催化剂是否需要过筛。
催化剂装填最好选择在干燥晴朗的天气进行,保证催化剂装填均匀,否则在开工时反应器内会出现偏流或“热点”,影响装置正常运行。
催化剂装填时工作人员须要进入反应器工作,因此,要特别注意工作人员劳动保护及安全问题,需要穿劳动保护服装,带能供氧气或空气的呼吸面罩,进反应器工作人员不能带其他杂物,以防止异物落入反应器内(一般催化剂装填由专业公司专业人员进行)3加氢反应系统置换加氢反应系统置换分为两个阶段,即空气环境置换为氮气环境、氮气环境置换为氢气环境。
在空气环境置换为氮气环境时需要注意,置换完成后系统氧含量应<1%,否则系统引入氢气时易发生危险;在氮气环境置换为氢气环境时应注意,使系统内气体有一个适宜的平均分子量,以保证循环氢压缩机在较适宜的工况下运行,一般氢气纯度为85%较为适宜。
4加氢反应系统气密加氢反应系统气密是加氢装置开工阶段一项非常重要的工作,气密工作的主要目的是查找漏点,消除装置隐患,保证装置安全运行。
加氢反应系统的气密工作分为不同压力等级进行,低压气密阶段所用的介质为氮气,氮气气密合格后用氢气作低压气密。
加氢装置危险因素及其防范措施

加氢装置危险因素及其防范措施一、开停工时的危险因素及其防范措施1、开工时的危险因素及其防范措施(1)加氢反应系统干燥、烘炉加氢装置反应系统干燥、烘炉的目的是除去反应系统内的水分,脱除加热炉耐火材料中的自然水和结晶水,烧结耐火材料,增加耐火材料的强度和使用寿命。
加热炉煤炉时,装置需引进燃料气,在引燃料气前应认真做好瓦斯的气密及隔离工作,一般要求燃料气中氧含量要小于1.0%。
防止瓦斯泄漏及窜至其他系统。
加热炉点火要彻底用蒸汽吹扫炉膛,其中不能残余易燃气体。
加热炉烘炉时应严格按烘炉曲线升温、降温,避免升温过快,耐火材料中的水分迅速蒸发而导致炉墙倒塌。
(2)加氢反应器催化剂装填催化剂装填应严格按催化剂装填方案进行,催化剂装填的好坏对加氢装置的运行情况及运行周期有重要影响。
催化剂装填前应认真检查反应器及其内构件,检查催化剂的粉尘情况,决定催化剂是否需要过筛。
催化剂装填最好选择在干燥晴朗的天气进行,保证催化剂装填均匀,否则在开工时反应器内会出现偏流或热点,影响装置正常运行。
催化剂装填时工作人员须要进入反应器工作,因此,要特别注意工作人员劳动保护及安全问题,需要穿劳动保护服装,带能供氧气或空气的呼吸面罩,进反应器工作人员不能带其他杂物,以防止异物落入反应器内(一般催化剂装填由专业公司专业人员进行)O(3)加氢反应系统置换加氢反应系统置换分为两个阶段,即空气环境置换为氮气环境、氮气环境置换为氢气环境。
在空气环境置换为氮气环境时需要注意,置换完成后系统氧含量应V1%,否则系统引入氢气时易发生危险;在氮气环境置换为氢气环境时应注意,使系统内气体有一个适宜的平均分子量,以保证循环氢压缩机在较适宜的工况下运行,一般氢气纯度为85%较为适宜。
(4)加氢反应系统气密加氢反应系统气密是加氢装置开工阶段一项非常重要的工作,气密工作的主要目的是查找漏点,消除装置隐患,保证装置安全运行。
加氢反应系统的气密工作分为不同压力等级进行,低压气密阶段所用的介质为氮气,氮气气密合格后用氢气作低压气密。
石蜡加氢精制装置说明与危险因素防范措施

石蜡加氢精制装置说明与危险因素防范措施石蜡加氢精制装置是一种用于将黄蜡或石蜡通过加氢处理转化为白蜡的一种工业设备。
这种设备将石蜡加热至一定温度后与氢气反应,通过饱和烃的裂解与合成反应,将石蜡中的不饱和化合物去除,从而得到更纯净的白蜡产品。
然而,在进行石蜡加氢精制过程中,也存在一些危险因素需要引起注意,并采取相应的防范措施来保证设备操作的安全。
下面将对石蜡加氢精制装置的危险因素和防范措施进行详细说明。
1.高温和高压:石蜡加氢精制过程需要高温和高压环境,而高温和高压环境下容易引发爆炸和火灾等危险。
因此,需要严格控制加热温度和操作压力,确保设备的安全运行。
同时,需要定期检查和维护设备的阀门、管道和容器,确保其能够承受高温和高压环境的要求。
2.氢气泄漏:石蜡加氢精制过程需要使用氢气,而氢气是一种易燃易爆的气体,一旦泄漏可能引发火灾和爆炸。
因此,需要在装置中设置可靠的气体泄漏报警装置,并定期检查其是否正常工作。
同时,需要定期对氢气系统进行检查和维护,确保气体管道的完整性,避免泄漏的发生。
3.工作环境污染:石蜡加氢精制过程中会产生一些有害气体和污染物,如硫化氢、二甲苯等。
这些物质对人体健康有一定的危害。
因此,需要在装置周围设置通风系统和排气装置,确保工作环境的良好通风。
同时,操作人员需要佩戴防护装备,如防毒面具、防护手套和防护眼镜等,避免有害物质的直接接触。
4.废水和废气处理:石蜡加氢精制过程会产生大量的废水和废气。
这些废水和废气中含有一些有害物质,需要进行处理,以避免对环境造成污染。
因此,需要在装置中设置废水处理和废气处理系统,并定期进行检查和维护,确保其正常工作。
综上所述,石蜡加氢精制装置的操作过程中需要注意防范各种危险因素,以保证设备操作的安全。
通过控制加热温度和操作压力、设置气体泄漏报警装置、保持良好的通风环境、佩戴防护装备和进行废水和废气的处理等措施,可以有效减少事故的发生,保障人员的身体健康和环境的安全。
加氢装置火灾爆炸危险性及安全措施(2021年)
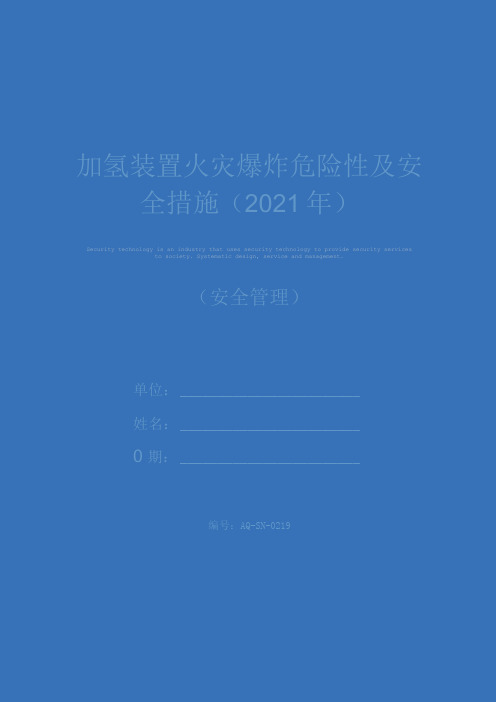
加氢装置火灾爆炸危险性及安全措施(2021年)Security technology is an industry that uses security technology to provide security services to society. Systematic design, service and management.(安全管理)单位:________________________姓名:________________________0 期:________________________编号:AQ-SN-0219化工安全加氢装置火灾爆炸危险性及安全措施(2021 年)作业五区8套装置,基本都有加氢工艺,以加氢工艺装置为例, 汽柴油加氢装置含有多种可燃气体,且有高温、中压的特点,因而具有易燃易爆的特点。
工艺物料中的氢气、燃料气、汽柴油等这些物质具有强爆炸危险性和穿透性;而主要危险性为火灾爆炸危险性, 以下主要分析物料的火灾爆炸危险性;工艺装置火灾危险性;工艺设备的火灾危险性。
通过对主要危险性分析,结合作业05年以来,发生的火灾情况,从装置的工艺、设备及安全管理方面提出综合控制措施,降低装置发生火灾的概率,提高装置安全运行。
一、汽柴油加氢装置火灾爆炸危险性1物料的火灾爆炸危险性汽柴油加氢装置以焦化汽柴油、催化柴油和直镭柴油为原料,化工安全技术I Chemical Safety Technology 化工安全在催化剂作用下,经高温、中压、临氢反应,并在分储塔内进行脱硫化氢以及汽、柴油的分离,以生产高质量的汽柴油产品。
所用燃料气来自管网,产品主要是汽油、柴油,还有部分轻烧和污油产生。
上述物料在生产过程中大多处于高温、中压条件,一旦出现泄漏,易引发火灾爆炸事故。
装置主要原料及产品火灾爆炸危险性见表一:表1:主要原料及产品火灾爆炸危险性名称爆炸极限%(v∕v)引燃温度℃闪点℃火灾危险类别汽油1. 1-9.5%263—300-50甲化工安全柴油1.4~4. 5%25760℃丙(乙B)氢气4.1—74. 1560甲燃料气3.0~13. 0538甲硫化氢化工安全5.3—45. 3260甲丙烷6.1-9. 5450-104. 1甲燃料油自燃点384℃,2工艺装置火灾危险性汽柴油加氢生产过程中有甲类火灾危险性物质存在,且操作温度高、压力大,一旦系统中出现泄漏现象,泄漏介质在高温下,一旦遇到空气就会着火,有可能引发火灾爆炸事故。
加氢装置——重点部位设备说明及危险因素、防范措施

加氢装置——重点部位设备说明及危险因素、防范措施一、重点部位1.加热炉及反应器区:加氢装置的加热炉及反应器区布置有加氢反应加热炉、分馏部分加热炉、加氢反应加热器、高压换热器等设备,其中大部分设备为高压设备,介质温度比较高,而且加热炉又有明火,因此,该区域潜在的危险性比较大,主要危险为火灾、爆炸是安全上重点防范的区域。
2.高压分离器及高压空冷区:高压分离器及高压空冷区内有高压分离器及高压空冷器,若高压分离器的液位控制不好,就会出现严重问题。
主要危险为火灾、爆炸和H2S中毒,因此该区域是安全上重点防范的区域。
3.加氢压缩机厂房:加氢压缩机厂房内布置有循环氢压缩机、氢气增压机,该区域为临氢环境,氢气的压力较高,而且压缩机为动设备,出现故障的机率较大,因此,该区域潜在的危险性比较大,主要危险为火灾、爆炸中毒,是安全上重点防范的区域。
4.分馏塔区:分馏塔区的设备数量较多,介质多为易燃、易爆物料,高温热油泵是应重点防范的设备,高温热油一旦发生泄漏,就可能引起火灾事故,分馏塔区内有大量的燃料气、液态烃及油品,如发生事故,后果将十分严重,此外,脱丁烷塔及其干气、液化气中H2S浓度高,有中毒危险,因此该区域也是安全上重点防范的区域。
二、主要设备1.加氢反应器:加氢反应器多为固定床反应器,加氢反应属于气-液-固三相涓流床反应,加氢反应器分冷壁反应器和热壁反应器两种:冷壁反应器内有隔热衬里,反应器材质等级较低;热壁反应器没有隔热衬里,而是采用双层堆焊衬里,材质多为2×1/4Cr-1Mo。
加氢反应器内的催化剂需分层装填,中间使用急冷氢,因此加氢反应器的结构复杂,反应器入口设有扩散器,内有进料分配盘、集垢篮筐、催化剂支承盘、冷氢管、冷氢箱、再分配盘、出口集油器等内构件。
加氢反应器的操作条件为高温、高压、临氢,操作条件苛刻,是加氢装置最重要的设备之一。
2.高压换热器:反应器出料温度较高,具有很高热焓,应尽可能回收这部分热量,因此加氢装置都设有高压换热器,用于反应器出料与原料油及循环氢换热。
加氢装置火灾爆炸危险性及安全措施
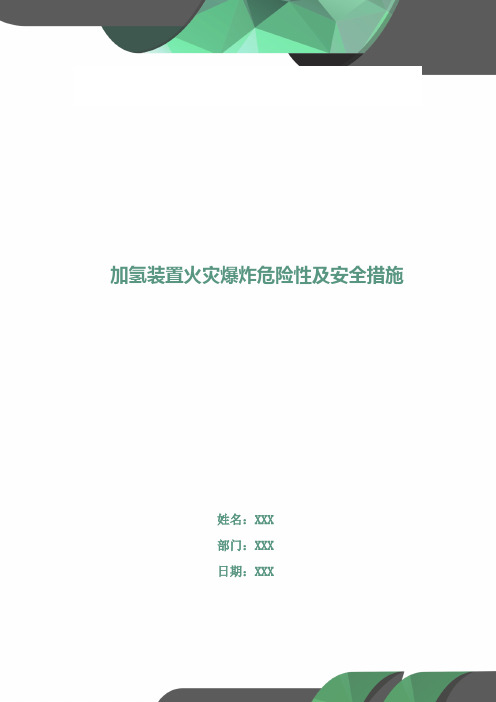
加氢装置火灾爆炸危险性及安全措施姓名:XXX部门:XXX日期:XXX加氢装置火灾爆炸危险性及安全措施作业五区8套装置,基本都有加氢工艺,以加氢工艺装置为例,汽柴油加氢装置含有多种可燃气体,且有高温、中压的特点,因而具有易燃易爆的特点。
工艺物料中的氢气、燃料气、汽柴油等这些物质具有强爆炸危险性和穿透性;而主要危险性为火灾爆炸危险性,以下主要分析物料的火灾爆炸危险性;工艺装置火灾危险性;工艺设备的火灾危险性。
通过对主要危险性分析,结合作业05年以来,发生的火灾情况,从装置的工艺、设备及安全管理方面提出综合控制措施,降低装置发生火灾的概率,提高装置安全运行。
一、汽柴油加氢装置火灾爆炸危险性1物料的火灾爆炸危险性汽柴油加氢装置以焦化汽柴油、催化柴油和直馏柴油为原料,在催化剂作用下,经高温、中压、临氢反应,并在分馏塔内进行脱硫化氢以及汽、柴油的分离,以生产高质量的汽柴油产品。
所用燃料气来自管网,产品主要是汽油、柴油,还有部分轻烃和污油产生。
上述物料在生产过程中大多处于高温、中压条件,一旦出现泄漏,易引发火灾爆炸事故。
装置主要原料及产品火灾爆炸危险性见表一:表1:主要原料及产品火灾爆炸危险性名称爆炸极限%(V/V)引燃温度℃闪点℃火灾危险类别汽油1.1~9.5%263~300-50甲柴油1.4~4.5%25760℃丙(乙B)氢气4.1~74.1560-甲燃料气3.0~13.O538-甲硫化氢4.3~45.3260-甲丙烷2.1-9.5450-104.1甲燃料油自燃点384℃,2工艺装置火灾危险性汽柴油加氢生产过程中有甲类火灾危险性物质存在,且操作温度高、压力大,一旦系统中出现泄漏现象,泄漏介质在高温下,一旦遇到空气就第 2 页共 7 页会着火,有可能引发火灾爆炸事故。
按照《石油化工企业设计防火规范》对生产装置或装置内单元的火灾危险性确定的原则,汽柴油加氢装置应为甲类火灾危险性装置。
●爆炸性气体环境分区在汽柴油加氢生产过程中,一旦出现泄漏,就会在装置区作业环境的空气中形成爆炸性气体混合物。
加氢装置—重点部位设备说明及危险因素及防范措施

加氢装置—重点部位设备说明及危险因素及防范措施一、重点部位及设备(一)重点部位1.加热炉及反应器区加氢装置的加热炉及反应器区布置有加氢反应加热炉、分馏部分加热炉、加氢反应加热器、高压换热器等设备,其中大部分设备为高压设备,介质温度比较高,而且加热炉又有明火,因此,该区域潜在的危险性比较大,主要危险为火灾、爆炸是安全上重点防范的区域。
2.高压分离器及高压空冷区高压分离器及高压空冷区内有高压分离器及高压空冷器,若高压分离器的液位控制不好,就会出现严重问题。
主要危险为火灾、爆炸和H2S中毒,因此该区域是安全上重点防范的区域。
3.加氢压缩机厂房加氢压缩机厂房内布置有循环氢压缩机、氢气增压机,该区域为临氢环境,氢气的压力较高,而且压缩机为动设备,出现故障的机率较大,因此,该区域潜在的危险性比较大,主要危险为火灾、爆炸中毒,是安全上重点防范的区域。
4.分馏塔区分馏塔区的设备数量较多,介质多为易燃、易爆物料,高温热油泵是应重点防范的设备,高温热油一旦发生泄漏,就可能引起火灾事故,分馏塔区内有大量的燃料气、液态烃及油品,如发生事故,后果将十分严重,此外,脱丁烷塔及其干气、液化气中H2S浓度高,有中毒危险,因此该区域也是安全上重点防范的区域。
(二)主要设备1.加氢反应器加氢反应器多为固定床反应器,加氢反应属于气—液—固三相涓流床反应,加氢反应器分冷壁反应器和热壁反应器两种:冷壁反应器内有隔热衬里,反应器材质等级较低;热壁反应器没有隔热衬里,而是采用双层堆焊衬里,材质多为2×1/4Cr—1Mo。
加氢反应器内的催化剂需分层装填,中间使用急冷氢,因此加氢反应器的结构复杂,反应器入口设有扩散器,内有进料分配盘、集垢篮筐、催化剂支承盘、冷氢管、冷氢箱、再分配盘、出口集油器等内构件。
加氢反应器的操作条件为高温、高压、临氢,操作条件苛刻,是加氢装置最重要的设备之一。
2.高压换热器反应器出料温度较高,具有很高热焓,应尽可能回收这部分热量,因此加氢装置都设有高压换热器,用于反应器出料与原料油及循环氢换热。
加氢装置——重点部位设备说明及危险因素防范措施
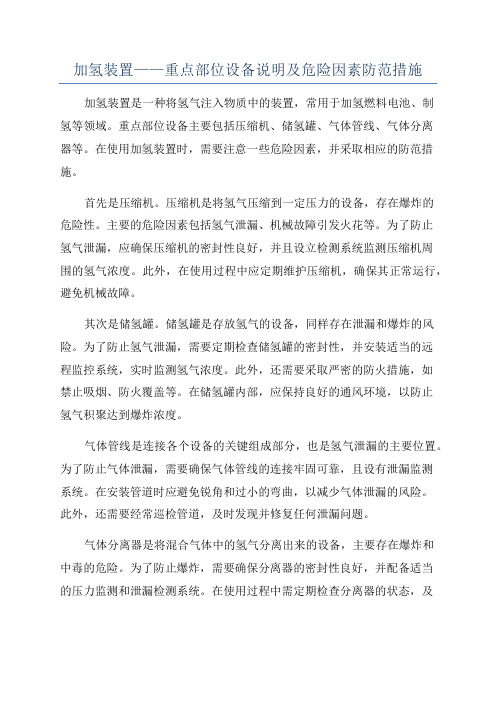
加氢装置——重点部位设备说明及危险因素防范措施加氢装置是一种将氢气注入物质中的装置,常用于加氢燃料电池、制氢等领域。
重点部位设备主要包括压缩机、储氢罐、气体管线、气体分离器等。
在使用加氢装置时,需要注意一些危险因素,并采取相应的防范措施。
首先是压缩机。
压缩机是将氢气压缩到一定压力的设备,存在爆炸的危险性。
主要的危险因素包括氢气泄漏、机械故障引发火花等。
为了防止氢气泄漏,应确保压缩机的密封性良好,并且设立检测系统监测压缩机周围的氢气浓度。
此外,在使用过程中应定期维护压缩机,确保其正常运行,避免机械故障。
其次是储氢罐。
储氢罐是存放氢气的设备,同样存在泄漏和爆炸的风险。
为了防止氢气泄漏,需要定期检查储氢罐的密封性,并安装适当的远程监控系统,实时监测氢气浓度。
此外,还需要采取严密的防火措施,如禁止吸烟、防火覆盖等。
在储氢罐内部,应保持良好的通风环境,以防止氢气积聚达到爆炸浓度。
气体管线是连接各个设备的关键组成部分,也是氢气泄漏的主要位置。
为了防止气体泄漏,需要确保气体管线的连接牢固可靠,且设有泄漏监测系统。
在安装管道时应避免锐角和过小的弯曲,以减少气体泄漏的风险。
此外,还需要经常巡检管道,及时发现并修复任何泄漏问题。
气体分离器是将混合气体中的氢气分离出来的设备,主要存在爆炸和中毒的危险。
为了防止爆炸,需要确保分离器的密封性良好,并配备适当的压力监测和泄漏检测系统。
在使用过程中需定期检查分离器的状态,及时清理污物,保持其正常运行。
同时,应加强通风和排放系统,减少氢气在设备内积聚的风险。
除了以上重点部位设备的危险因素和防范措施外1.周围环境的安全:加氢装置应远离易燃物、易爆物和高温物质等危险场所,确保周围环境安全。
2.人员安全培训:加氢装置的操作人员应经过充分的培训,了解设备的危险性,并熟悉紧急情况下的应急措施。
3.灭火设备:加氢装置周围应配备足够的灭火器材,以应对突发火灾。
4.泄漏处置:如发生氢气泄漏,应及时启动紧急排气系统,将泄漏氢气排出,并采取相应的措施清除泄漏源。
制氢—装置、重点部位设备说明与危险因素及防范措施

制氢—装置、重点部位设备说明与危险因素及防范措施一、装置简介(一)装置的发展及类型1.制氢装置的发展氢气是石油化工的基本原料,随着加氢技术的发展,对氢气的需求量日益增加,一般对于加氢装置较多的炼油厂,除利用重整副产氢外,尚须有专门制氢装置。
我国第一套轻烃蒸汽转化制氢装置是20世纪60年代建成的,随后又陆续建立起多套制氢装置,这时期的氢气净化技术为化学净化法。
进入20m世纪80年代以后,随着变压吸附技术的发展,新建的制氢装置多采用变压吸附净化法。
2.装置的主要类型以制氢装置的原料分:有天然气制氢:油田伴生气制氢;液化气制氢;炼厂气制氢;轻石脑油制氢等。
以产品精制方法分:有化学净化法制氢:变压吸附(PSA)净化法制氢。
天然气制氢造气单元和PSA单元工艺流程见图2—19a、图2—19b、图2—19c。
二、重点部位及设备(一)重点部位制氢装置的原料及产品多为易燃、易爆物质,整个装置区内都具有较大危险性,其中危险性最大的区域属转化炉区和压缩机区。
(二)主要设备1.制氢转化炉转化炉是制氢装置的核心设备,它处于高温、高压、临氢状态下操作,对炉管材质及结构有严格要求。
目前,流行的转化炉有三种炉型:一是以托普索公司为代表的侧烧炉:二是以凯洛格公司为代表的顶烧炉;三是以福斯特惠勒公司为代表的阶梯式转化炉。
•国内流行的为顶烧炉和刚烧炉。
转化炉炉管一般为DNl00mm×l2000mm,材质为HK—40或HP—40的离心浇铸管,由于炉管的温度高,设计时应充分考虑热膨胀问题。
2.PSA吸附床变压吸附分离为间歇操作,对于每个吸附床来讲,在高压下吸附,在低压下脱附,因此吸附床受交变压力的作用,为疲劳容量,在设计、制造时要引起足够重视。
三、危险因素及其防范措施本装置在火灾危险性分类中为甲类危险性装置。
(一)开停工时的危险因素及其防范措施1.开工时的危险因素及其防范措施(1)装置全面大检查装置全面大检查是开工前非常重要的步骤,装置在设计、施工当中必然存在一些问题,通过检查,发现问题,并进行整改,以保证装置安全顺利开工。
加氢裂化—装置、重点部位设备说明及危险因素及防范措施
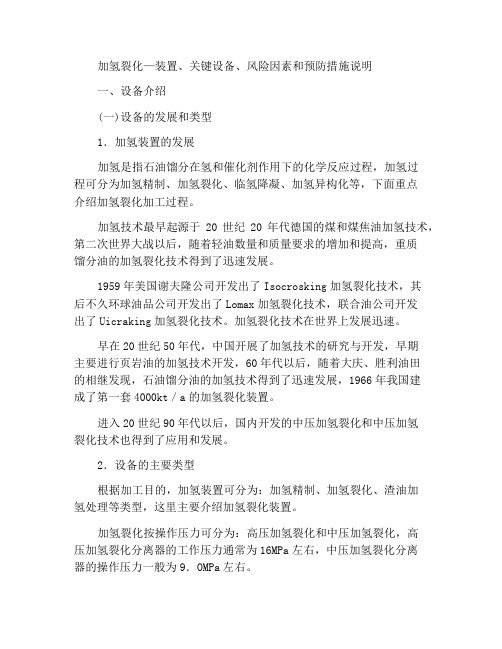
加氢裂化—装置、关键设备、风险因素和预防措施说明一、设备介绍(一)设备的发展和类型1.加氢装置的发展加氢是指石油馏分在氢和催化剂作用下的化学反应过程,加氢过程可分为加氢精制、加氢裂化、临氢降凝、加氢异构化等,下面重点介绍加氢裂化加工过程。
加氢技术最早起源于20世纪20年代德国的煤和煤焦油加氢技术,第二次世界大战以后,随着轻油数量和质量要求的增加和提高,重质馏分油的加氢裂化技术得到了迅速发展。
1959年美国谢夫隆公司开发出了Isocrosking加氢裂化技术,其后不久环球油品公司开发出了Lomax加氢裂化技术,联合油公司开发出了Uicraking加氢裂化技术。
加氢裂化技术在世界上发展迅速。
早在20世纪50年代,中国开展了加氢技术的研究与开发,早期主要进行页岩油的加氢技术开发,60年代以后,随着大庆、胜利油田的相继发现,石油馏分油的加氢技术得到了迅速发展,1966年我国建成了第一套4000kt/a的加氢裂化装置。
进入20世纪90年代以后,国内开发的中压加氢裂化和中压加氢裂化技术也得到了应用和发展。
2.设备的主要类型根据加工目的,加氢装置可分为:加氢精制、加氢裂化、渣油加氢处理等类型,这里主要介绍加氢裂化装置。
加氢裂化按操作压力可分为:高压加氢裂化和中压加氢裂化,高压加氢裂化分离器的工作压力通常为16MPa左右,中压加氢裂化分离器的操作压力一般为9.OMPa左右。
加氢裂化可分为:一段加氢裂化流程、二段加氢裂化流程、串联加氢裂化流程。
一段加氢裂化流程是指只有一个加氢反应器,原料的加氢精制和加氢裂化在一个反应器中进行。
该流程的特点是:工艺流程简单,但对原料的适应性及产品的分布有一定限制。
第二阶段加氢裂化工艺涉及两个加氢反应器,第一个加氢反应器装加氢精制催化剂,第二个加氢反应器装加氢裂化催化剂,两段加氢形成两个独立的加氢体系,该流程的特点是:对原料的适应性强,操作灵活性较大,产品分布可调节性较大,但是,该工艺的流程复杂,投资及操作费用较高。
润滑油加氢补充精制装置腐蚀分析及防护措施

润滑油加氢补充精制装置腐蚀分析及防护措施润滑油加氢补充精制装置是炼油厂中重要的设备之一,它主要用于加氢处理过程中对润滑油的再加工和加氢补充。
在润滑油加氢补充精制装置的运行过程中,由于工艺条件、原料性质及操作不当等原因,设备容易受到腐蚀的影响,进而影响设备的安全和稳定运行。
本文将对润滑油加氢补充精制装置在运行过程中可能遇到的腐蚀问题进行分析,并提出相应的防护措施。
1. 腐蚀原因(1)工艺条件导致的腐蚀:在润滑油加氢补充精制装置的工艺过程中,可能存在高温、高压、有机酸、硫化物等腐蚀性物质的存在,导致设备金属表面因化学反应而受到侵蚀。
(2)原料性质导致的腐蚀:润滑油中可能含有酸、碱、水分、硫化物等腐蚀性成分,当这些成分在设备内部长期停留,就会导致设备金属材料的腐蚀。
(3)操作不当导致的腐蚀:设备的运行和维护过程中可能存在操作不当,如温度控制不当、化学品投加量不准确、设备清洗不及时等,都会导致设备金属表面的腐蚀。
2. 腐蚀部位润滑油加氢补充精制装置中容易发生腐蚀的部位主要包括反应器、换热器、管道、泵等设备,这些设备在工艺过程中承受着高温、高压和腐蚀性物质的影响,容易受到腐蚀破坏。
3. 腐蚀类型润滑油加氢补充精制装置中的腐蚀类型主要包括普通腐蚀、应力腐蚀、磨蚀腐蚀、腐蚀疲劳等,其中应力腐蚀对设备的破坏作用最大,容易引发设备的泄漏或断裂。
二、防护措施1. 选用耐腐蚀材料:在设计和制造润滑油加氢补充精制装置时,应选择耐腐蚀材料,如不锈钢、镍基合金、钛合金等作为设备的主要构造材料,以提高设备的耐腐蚀性能。
2. 设备内涂层保护:在设备内部的腐蚀易发部位,如反应器内壁、管道内壁等,可以采用耐腐蚀性能优良的涂层进行保护,以降低腐蚀对设备的影响。
3. 控制工艺条件:加强对润滑油加氢补充精制装置工艺条件的控制,包括控制温度、压力、流速、化学品浓度等,避免过高或过低的工艺条件对设备的腐蚀影响。
4. 定期检查和维护:对润滑油加氢补充精制装置进行定期的检查和维护,包括设备的清洗、除锈、涂层的修复和更换等,及时发现并处理设备的腐蚀问题。
润滑油加氢补充精制装置腐蚀分析及防护措施
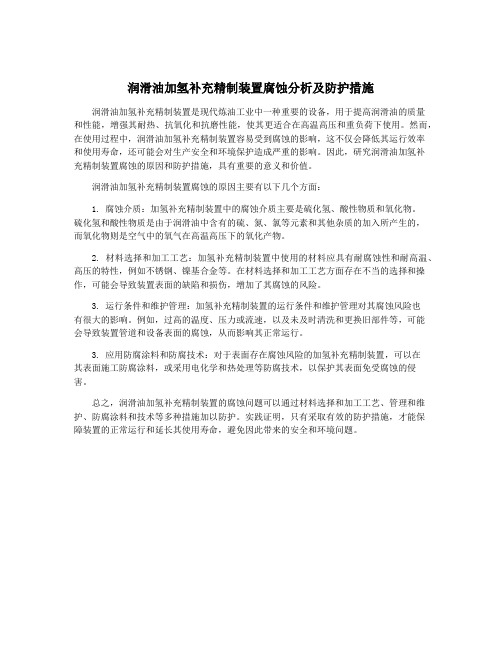
润滑油加氢补充精制装置腐蚀分析及防护措施润滑油加氢补充精制装置是现代炼油工业中一种重要的设备,用于提高润滑油的质量和性能,增强其耐热、抗氧化和抗磨性能,使其更适合在高温高压和重负荷下使用。
然而,在使用过程中,润滑油加氢补充精制装置容易受到腐蚀的影响,这不仅会降低其运行效率和使用寿命,还可能会对生产安全和环境保护造成严重的影响。
因此,研究润滑油加氢补充精制装置腐蚀的原因和防护措施,具有重要的意义和价值。
润滑油加氢补充精制装置腐蚀的原因主要有以下几个方面:1. 腐蚀介质:加氢补充精制装置中的腐蚀介质主要是硫化氢、酸性物质和氧化物。
硫化氢和酸性物质是由于润滑油中含有的硫、氮、氯等元素和其他杂质的加入所产生的,而氧化物则是空气中的氧气在高温高压下的氧化产物。
2. 材料选择和加工工艺:加氢补充精制装置中使用的材料应具有耐腐蚀性和耐高温、高压的特性,例如不锈钢、镍基合金等。
在材料选择和加工工艺方面存在不当的选择和操作,可能会导致装置表面的缺陷和损伤,增加了其腐蚀的风险。
3. 运行条件和维护管理:加氢补充精制装置的运行条件和维护管理对其腐蚀风险也有很大的影响。
例如,过高的温度、压力或流速,以及未及时清洗和更换旧部件等,可能会导致装置管道和设备表面的腐蚀,从而影响其正常运行。
3. 应用防腐涂料和防腐技术:对于表面存在腐蚀风险的加氢补充精制装置,可以在其表面施工防腐涂料,或采用电化学和热处理等防腐技术,以保护其表面免受腐蚀的侵害。
总之,润滑油加氢补充精制装置的腐蚀问题可以通过材料选择和加工工艺、管理和维护、防腐涂料和技术等多种措施加以防护。
实践证明,只有采取有效的防护措施,才能保障装置的正常运行和延长其使用寿命,避免因此带来的安全和环境问题。
- 1、下载文档前请自行甄别文档内容的完整性,平台不提供额外的编辑、内容补充、找答案等附加服务。
- 2、"仅部分预览"的文档,不可在线预览部分如存在完整性等问题,可反馈申请退款(可完整预览的文档不适用该条件!)。
- 3、如文档侵犯您的权益,请联系客服反馈,我们会尽快为您处理(人工客服工作时间:9:00-18:30)。
编号:AQ-JS-05627
( 安全技术)
单位:_____________________
审批:_____________________
日期:_____________________
WORD文档/ A4打印/ 可编辑
加氢精制装置说明与危险因素
以及防范措施
Description, risk factors and preventive measures of hydrofining unit
加氢精制装置说明与危险因素以及
防范措施
使用备注:技术安全主要是通过对技术和安全本质性的再认识以提高对技术和安全的理解,进而形成更加科学的技术安全观,并在新技术安全观指引下改进安全技术和安全措施,最终达到提高安全性的目的。
一、装置简介
(一)装置发展及类型
1.装置发展
现代炼油工业的加氢技术(包括加氢工艺、催化剂和专用设备)是在第二次世界大战以前经典的煤和煤焦油高压催化加氢技术的基础上发展起来的。
1949年铂重整技术的发明和工业应用,除生产大量高辛烷值汽油组分外还副产大量廉价的氢气,对现代加氢技术的发明和发展起到了关键作用。
1950年炼油厂出现了加氢精制装置,1959年出现了加氢裂化装置,1963年出现了沸腾床渣油低转化率加氢裂化装置,1969年出现了固定床重油加氢脱硫装置,1977年出现了固定床渣油加氢脱
硫装置,1984年出现了沸腾床渣油高转化率加氢裂化装置。
这些加氢技术的发明和工业应用,使加氢技术由发生、发展走向成熟。
加氢(包括加氢裂化、加氢精制和加氢处理)成为世界上加工能力最大的二次加32212艺,是炼油工业的三大支柱技术(加氢、催化裂化和催化重整)之一。
生产低硫、低芳烃和高十六烷值的优质柴油是当前世界范围内车用柴油燃料的生产趋势,也已成为国内各石化企业正在面临的挑战。
中石化股份公司已在2003年提出在国内实施《城市车用柴油》标准(Q/SHll008—2002),其主要质量指标:硫质量分数不大于0.030%,总芳烃质量分数不大于25%,多环芳烃质量分数不大于5%。
欧洲提出2005年将要求硫含量小于50X10—6,世界燃料规范Ⅲ类柴油的硫含量指标是30X10—6。
近几年,国内外文献报道有许多关于未来柴油规格的研究和推测,更低的柴油硫规格的推广正在加速。
所以研究开发能够生产低硫、低芳烃和高十六烷值的优质柴油的催化剂成为柴油加氢的主要发展方向。
本节主要以柴油加氢精制装置展开讨论说明。
2.装置的主要类型
加氢精制是各种油品在氢压下进行改质的一个总称。
加氢精制处理原料油范围宽,产品灵活性大,液体产品收率高质量好。
加氢精制的目的主要是对油品进行脱硫、脱氮、脱氧、烯烃饱和、芳烃饱和和脱除金属、沥青杂质等,以达到改善油晶的气味、颜色和安定性,防止腐蚀,进一步提高产品质量,满足油品的使用要求。
加氢精制工艺装置主要类型有:石脑油加氢、煤油加氢、柴油加氢、润滑油加氢和石蜡加氢等。
还可以对劣质渣油进行加氢处理,得到安全性好的低硫、低黏度的馏分,除生产部分石脑油和优质柴油外,其重组分可做重油催化裂化的原料。
加氢精制工艺操作条件视原料性质而定,一般反应总压力为3.0~8.0MPa之间。
反应温度300—360°C,液时空速1.0~2.0之间。
渣油加氢工艺条件要求苛刻,如孤岛减压渣油加氢要求压力高达16.9MPa,温度385%。
随着加氢工业技术的发展,我国加氢催化剂水平也有很大的发展,基本上能满足炼油厂加氢精制的要求。
二、重点部位及设备
(一)重点部位
1.反应系统
反应系统主要有加热炉、加氢反应器和高压分离器三部分组成。
(1)加热炉采用纯烧瓦斯的方箱式加热炉,双排管双面辐射,一旦有问题,直接影响反应温度和产品的质量。
(2)反应器分三个床层,其中第一床层上部加有一层保护剂,其余三层为加氢催化剂。
在第二床和第三床层入口设有急冷氢,防止催化剂的结焦和床层超温或“飞温”。
反应器是装置的心脏,一旦出现问题直接导致装置的停工。
(3)高压分离器主要是将反应产物分离为循环氢、低分油和含硫含氨污水(酸性水)部分。
高分器液位超高可以导致循环氢带液危害压缩机的正常运行;如低液位,或液位抽空,会使高压气窜人低分器,导致恶性爆炸事故发生。
反应部分属于高压高温部位,在选材时要考虑耐高压高温和耐腐蚀,一旦出现问题将影响正常生产。