气辅注塑工艺的应用和工艺过程
气辅注塑原理
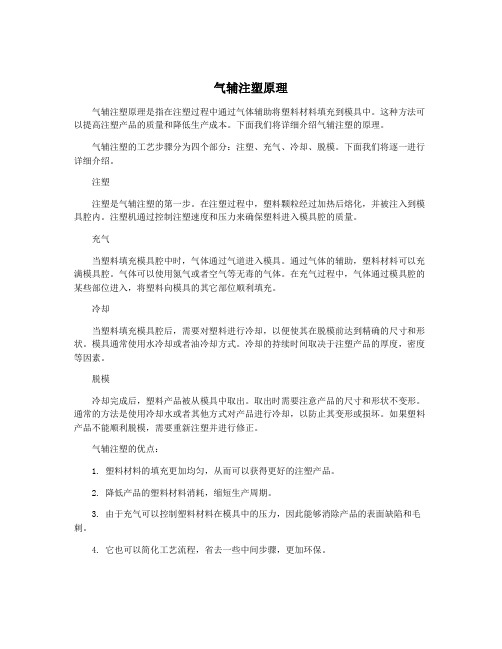
气辅注塑原理气辅注塑原理是指在注塑过程中通过气体辅助将塑料材料填充到模具中。
这种方法可以提高注塑产品的质量和降低生产成本。
下面我们将详细介绍气辅注塑的原理。
气辅注塑的工艺步骤分为四个部分:注塑、充气、冷却、脱模。
下面我们将逐一进行详细介绍。
注塑注塑是气辅注塑的第一步。
在注塑过程中,塑料颗粒经过加热后熔化,并被注入到模具腔内。
注塑机通过控制注塑速度和压力来确保塑料进入模具腔的质量。
充气当塑料填充模具腔中时,气体通过气道进入模具。
通过气体的辅助,塑料材料可以充满模具腔。
气体可以使用氮气或者空气等无毒的气体。
在充气过程中,气体通过模具腔的某些部位进入,将塑料向模具的其它部位顺利填充。
冷却当塑料填充模具腔后,需要对塑料进行冷却,以便使其在脱模前达到精确的尺寸和形状。
模具通常使用水冷却或者油冷却方式。
冷却的持续时间取决于注塑产品的厚度,密度等因素。
脱模冷却完成后,塑料产品被从模具中取出。
取出时需要注意产品的尺寸和形状不变形。
通常的方法是使用冷却水或者其他方式对产品进行冷却,以防止其变形或损坏。
如果塑料产品不能顺利脱模,需要重新注塑并进行修正。
气辅注塑的优点:1. 塑料材料的填充更加均匀,从而可以获得更好的注塑产品。
2. 降低产品的塑料材料消耗,缩短生产周期。
3. 由于充气可以控制塑料材料在模具中的压力,因此能够消除产品的表面缺陷和毛刺。
4. 它也可以简化工艺流程,省去一些中间步骤,更加环保。
气辅注塑是一种高效、环保、节能的注塑工艺。
它可以提高生产效率,降低生产成本,同时还能有效改善产品的质量和外观。
近年来,气辅注塑工艺广泛应用于各个领域。
它可以用于制造电子产品、医疗器械、汽车零配件、家用电器等。
它的灵活性和可塑性极高,满足了市场对产品多样化、品质一致化、成本低价化等需求。
在汽车零配件的制造中,气辅注塑的运用已成为一种趋势。
由于汽车零配件的尺寸和数量大,所以制造成本非常高。
而这里正是气辅注塑的优势所在。
利用气辅注塑工艺,能够更好的控制塑料材料在模具中的填充,从而提高产品的密度、强度和耐用性。
气体辅助注塑工艺原理及优点.
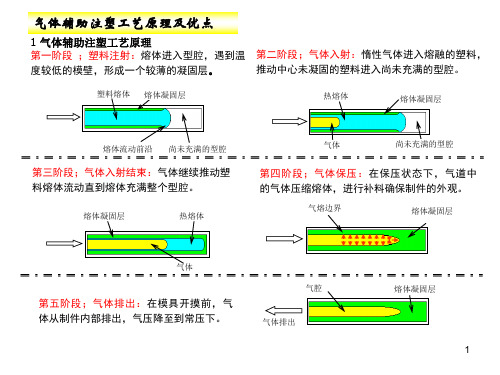
1 气体辅助注塑工艺原理 第一阶段 ;塑料注射:熔体进入型腔,遇到温 第二阶段;气体入射:惰性气体进入熔融的塑料,
度较低的模壁,形成一个较薄的凝固层。
推动中心未凝固的塑料进入尚未充满的型腔。
塑料熔体 熔体凝固层
热熔体
熔体凝固层
熔体流动前沿 尚未充满的型腔
第三阶段;气体入射结束:气体继续推动塑 料熔体流动直到熔体充满整个型腔。
射嘴进气方式,即使用专用的自封闭式或主动式气辅射嘴,在塑料注射结束后,将 高压气体依靠射嘴直接进入塑料内部,按气道形成一个延展的封闭空间-气腔并保持一 定压力,直至冷却,在模具打开之前,通过座台后退使射嘴与制品料道强行分离,使气 体排出制品。
图4自封闭气辅射嘴
图5主动式气辅射嘴 7
(2) 气针进气方式 气针进气方式即在模具的某个特定位置,安装排气装置-气针。当塑料注入型腔后,
2
气辅技术应用
气体辅助注射可以应用在除特别柔软的塑料以外的任何热塑性塑料和部分热 固性塑料。
根据气辅成型制品的结构形状不同,大致分为3类: (1).棒类制品,类似把手之类大壁厚制件; (2).板类制品,容易产生翘曲变形和局部表面收缩的大平面制件; (3).特殊制品,由传统注塑技术难以一次成型的特殊结构的制件。
(5).气道截面尺寸变化应平缓过渡,以免引起收缩不均。 (6).气道入口不应设置在外观面或制件承受机械外力处。
(7).进气口位置应接近浇口,以保证气体与熔体流动方向一致,但两者距离应>30mm, 以避免类制品
气辅注塑成型技术的主要应用之一就是板类制件的成型。因为气体总是沿 着阻力最小的方向前进,容易在较厚的部位进行穿透,因此,在板类制品设计时常 将加强筋作为气道,气道一般设在制品的边缘或壁的转角处。对制品的设计也就是 对加强筋和肋板的设计,即气道的设计。基本原则如下: (1).在设计制作加强筋时,应避免设计又细又密的加强筋。 (2).“手指”效应是大平面制件容易产生的主要问题。 (3).当制件仅由一个气针进气而形成多个加强筋或肋板(气道)时,气道不能形 成回 路。 (4).为避免熔体聚集产生凹陷,气道末端的外形应采用圆角过渡。 (5).采用多点进气时,气道之间的距离不能太近。 (6).气道布置尽量均匀,尽量延伸至制品末端。
气辅注塑工艺成本降低

气辅注塑工艺成本降低一、气辅注塑工艺概述气辅注塑工艺是一种先进的注塑技术,它通过在塑料制品成型过程中注入惰性气体,来实现产品的内部结构优化和成本降低。
这种技术不仅能够提高产品的质量和性能,还能有效减少材料的使用量,从而达到降低成本的目的。
1.1 气辅注塑工艺的核心特性气辅注塑工艺的核心特性主要体现在以下几个方面:- 材料节省:通过注入气体,可以在保证产品强度和刚性的前提下,减少塑料材料的使用量。
- 产品性能提升:气辅注塑可以改善产品的内部结构,提高产品的强度和刚性。
- 成本降低:由于材料使用量的减少,可以显著降低产品的生产成本。
- 环境友好:减少材料使用量有助于减少塑料废弃物,对环境更为友好。
1.2 气辅注塑工艺的应用场景气辅注塑工艺的应用场景非常广泛,包括但不限于以下几个方面:- 汽车零部件:如保险杠、仪表盘等,可以减轻重量,提高强度。
- 家电产品:如电视机外壳、洗衣机外壳等,可以提高产品的耐用性和美观性。
- 包装材料:如食品包装盒、饮料瓶等,可以提高包装的强度和保护性能。
二、气辅注塑工艺的实施气辅注塑工艺的实施是一个系统化的过程,需要精确的控制和优化。
2.1 气辅注塑工艺的关键技术气辅注塑工艺的关键技术包括以下几个方面:- 注气系统:需要精确控制气体的注入量和注入时间,以保证产品的内部结构均匀。
- 模具设计:模具的设计需要考虑到气体的流动路径和分布,以确保气体能够均匀地填充产品的内部空间。
- 材料选择:选择合适的塑料材料,以确保其与气体的兼容性,以及在注塑过程中的流动性和成型性。
- 工艺参数控制:需要精确控制注塑过程中的温度、压力、速度等参数,以保证产品质量。
2.2 气辅注塑工艺的实施步骤气辅注塑工艺的实施步骤主要包括以下几个阶段:- 产品设计:在产品设计阶段就需要考虑到气辅注塑工艺的特点,设计出适合气辅注塑的产品结构。
- 模具制造:根据产品设计,制造出适合气辅注塑的模具。
- 工艺参数设定:根据产品和模具的特点,设定合适的注塑工艺参数。
气辅注塑加工工艺与一般注塑工艺
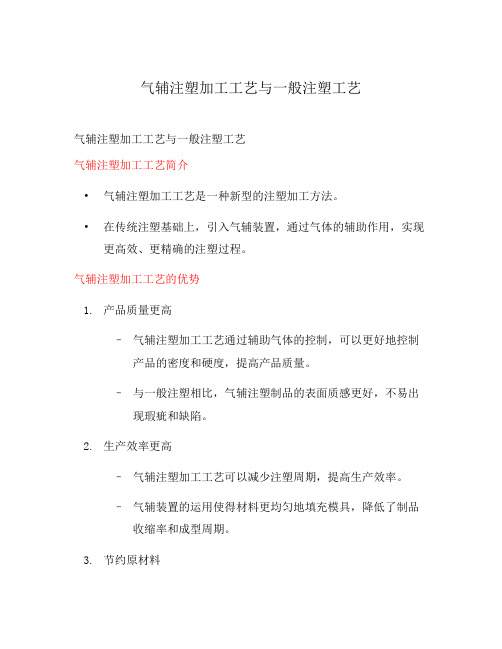
气辅注塑加工工艺与一般注塑工艺气辅注塑加工工艺与一般注塑工艺气辅注塑加工工艺简介•气辅注塑加工工艺是一种新型的注塑加工方法。
•在传统注塑基础上,引入气辅装置,通过气体的辅助作用,实现更高效、更精确的注塑过程。
气辅注塑加工工艺的优势1.产品质量更高–气辅注塑加工工艺通过辅助气体的控制,可以更好地控制产品的密度和硬度,提高产品质量。
–与一般注塑相比,气辅注塑制品的表面质感更好,不易出现瑕疵和缺陷。
2.生产效率更高–气辅注塑加工工艺可以减少注塑周期,提高生产效率。
–气辅装置的运用使得材料更均匀地填充模具,降低了制品收缩率和成型周期。
3.节约原材料–气辅注塑加工工艺由于材料分布更均匀,减少了材料的浪费。
–相比较于一般注塑,气辅注塑制品在制造时所需的原材料用量更少。
4.环保节能–气辅注塑加工工艺不需要额外的加热或冷却设备,节约了能源。
–通过优化制程,减少了废品率,降低了对环境的负面影响。
气辅注塑加工工艺的应用领域•电子产品:手机壳、电池壳、硬盘壳等。
•汽车配件:车灯壳、仪表板、车门把手等。
•家居用品:儿童玩具、家具配件、文具等。
一般注塑工艺的特点与局限性•一般注塑工艺在制品的表面平整度和精度方面有一定的局限性。
•一般注塑制造过程中,因为材料无法完全填充到模具中的每个角落,易产生瑕疵和缺陷。
结语气辅注塑加工工艺相对于一般注塑工艺具有众多优势,无论是产品质量、生产效率还是原材料的节约都占有明显的优势。
在如今注塑加工行业日益竞争激烈的背景下,气辅注塑加工工艺的应用前景非常广阔。
希望本文能对读者对气辅注塑加工工艺与一般注塑工艺有更深入的了解。
气辅注塑加工工艺的工作原理1.注塑过程中,将塑料颗粒加热融化。
2.融化的塑料通过注塑机的螺杆被注入模具腔中。
3.气辅装置通过喷嘴向注入的塑料中喷入压缩空气。
4.压缩空气通过气门控制,辅助塑料充填模具,使得塑料更加均匀地填充到模具的每个角落。
5.注塑机冷却塑料,然后开模取出制品。
气体辅助注射成型技术原理及应用

气体辅助注射成型技术原理及应用
气体辅助注射成型技术的应用
● 管状和棒状零件,如门把手、转椅支座、吊 钩、扶手、导轨、衣架等。这是因为,管状结 构设计使现存的厚截面适于产生气体管道,利 用气体的穿透作用形成中空,从而可消除表面 成型缺陷,节省材料并缩短成型周期。
气体辅助注射成型技术原理及应用
在进行模具设计之前,利用MoldFlow MPI 5.0对设计方案进行了模拟。 分析模型如图8所示,在该分析模型中确定了浇口及进气口位置。在模拟中, 设定预注射量为70%,熔体温度为230℃,注射时间为3s,延迟时间为1.5s, 气体压力为20MPa。
气体辅助注射成型技术原理及应用
● 可通过气体的穿透减轻制品重量,节省原材料 用量,并缩短成型周期,提高生产率。
● 该技术可适用于热塑性塑料、一般工程塑料及 其合金以及其他用于注射成型的材料。
气体辅助注射成型技术原理及应用
气体辅助注射成型技术的缺点是:
●需要增加供气和回收装置及气体压力控制单元, 从而增加了设备投资;对注射机的注射量和注射 压力的精度要求有所提高;制品中接触气体的表 面与贴紧模壁的表面会产生不同的光泽;制品质 量对工艺参数更加敏感,增加了对工艺控制的精 度要求。
气体辅助注射成型CAE分析的主要作用是:
1.分析产品的成型工艺性 2.评价模具的设计是否合理 3.优化成型工艺参数 4.预测制品可能出现的缺陷
气体辅助注射成型技术原理及应用
下面以成型把手为例,介绍气体辅助注射成型 CAE分析的过程。
如图7所示的把手材料为ABS,手柄位置壁厚为14mm。由于是外观件,对 其成型要求很高。
9气体辅助注塑成型

气体辅助注射成型
可能的问题-内部起泡
原因是气体进入了熔体里.
气体辅助注射成型
可能的问题-内部起泡
解决方案:
增加气体保压时间 缓慢地释放气体 增加延迟时间 降低气体压力 保持材料干燥 降低熔体温度 改变塑料材料
气体辅助注射成型
可能的问题-手指效应
气体辅助注射成型
可能的问题-手指效应
解决方案:
增加熔体注入量 增加气体注入时间 增加气体延迟时间 降低气体压力 增加气道高度尺寸
进气位臵
通过模具型腔进气
气体辅助注射成型
制品形状-加强筋
普通塑件加强筋的厚度应比塑件主体壁厚薄 ( 约为其一半 ) ,即使这样也免不了在加强筋所 在壁的对面产生凹陷,因此应尽量少采用。在 气辅注塑中加强筋可设计得比塑件主体壁厚大 得多,作为气体通路,不但可避免产生凹陷, 而且可大大地增加塑件的刚度,粗大的加强筋 通常不会增加制品总重,因为平板部分可减薄, 在筋中的大量气体也可减轻重量。
气体辅助注射成型
翘曲和变形
气辅成型能消除制品 的翘曲和变形吗?
气体辅助注射成型
翘曲和变形
气体辅助注射成型
剩余壁厚-注入树脂量
太少
太多
气体辅助注射成型
剩余壁厚-注入树脂量
气体辅助注射成型
剩余壁厚-模温
以PC(Makrolon® 2458)为例子,模温变化大于 30°C而 制品的壁厚基本上不变,平均壁厚的改变量仅 0.02mm.
气体辅助注射成型
适宜成型的制品
例子:电视机前框改为气辅注塑成型,制件经重新设 计后,重量减轻了26%,零件数减少了54%。
气体辅助注射成型
适宜成型的制品
例子:马自达汽车保险杠。用气辅成型克服了表面凹陷,
气辅注塑成型工艺

气辅注塑成型工艺这种成型工艺,对于很多工程师来说很陌生,因为平时大家接触的产品很少会用到这种成型工艺,包括我本人也是一样,直到我接触到一款产品,才慢慢了解,就是以下这个锅体。
锅体的把手部分,除了2个螺丝塞,整个把手是一个完整的塑胶件,且外观并没有缩水等缺陷,看下侧面和背面图。
咋一看,以为内部是实心的,实际上并不是,而是空心的,是利用了气体辅助注塑成型技术。
01气辅成型的原理气体辅助注塑系统,是把惰性气体(通常用氮气)经由分段压力控制系统直接注射入模腔内的塑化塑料里,使塑件内部膨胀而造成中空,但仍然保持产品表面的外形完整无缺。
气辅注塑成型可被认为是中空吹塑成型的变型,其过程是先向模具腔中注入经过准确计量的占模腔一定比例的塑胶熔体,这一过程称为“欠料注塑”,再直接往熔融塑胶中注入一定体积和压力的高压氮气,气体在塑胶熔体的包围下沿着阻力最小的方向扩散前进。
由于靠模壁部分的塑胶温度低,表面粘度高,而製作较厚部分中心塑胶熔体的温度高,粘度低,所以气体容易对中心塑胶熔体进行穿透和排空,在制件的厚部形成中空气道,而被气体所排空的熔融塑胶又被气体压力推向模具末端直至充满模具型腔,在冷却阶段压缩气体对塑胶熔体进行保压补缩。
待制品冷却凝固后再卸气,然后开模顶出。
以上气辅成型过程实际上分为四个阶段:熔体短射、气体注射、气体保压、气体排出和制件顶出。
02气辅成型的方法除了常规的欠料注塑成型法,还有:1.副腔成型法(也叫满料注塑法)2.型芯成型法3.熔体回流成型法上面的锅体的把手猜测是采用了副腔成型法(也叫满料注塑法):具体细节可参考下图:03气辅注塑成型与普通注塑成型的区别主要区别在于多了一套气辅设备:(1)普通注塑机(计料精度稍高些为好)。
(2)氮气控制系统,包括自封闭式气辅喷嘴。
(3)高压氮气发生器。
(4)工业氮气钢瓶以及提供增压动力的空气压缩机。
(5)为气体辅助注射设计制造的模具。
(6)气辅注塑气辅喷嘴喷嘴进气方式,即使用专用的自封闭式气辅喷嘴,在塑料注射结束后,将高压气体依靠喷嘴直接进入塑料内部,按气道形成一个延展的封闭空间—气腔并保持一定压力,直至冷却,在模具打开之前,通过座台后退使喷嘴与制品料道强行分离,使气体排出制品。
气体辅助注射成型特点、方法与工艺过程
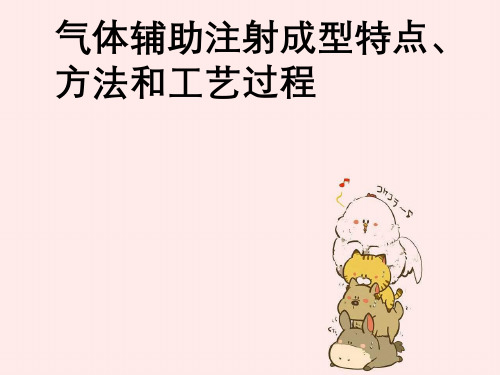
气体辅助注射成型与普通注射成型相比,多一 个气体注射阶段,
在原来注射成型的保压阶段,由压力相对低的 气体进行保压,成型后的制品中就有由气体形 成的中空部分。/
(1)塑料充模阶段:气辅注射时熔体只充满局部型 腔,其余部分靠气体补充。
⑵切换延迟阶段:塑料熔体注射结 束到气体注射开始时的时间。
3)对注射机的注射量和注射压力的精度有更 高的要求。
4)制品质量对模具温度和保压时间等工艺参 数更加敏感。 /
一类是厚壁、偏壁、管状制件, 如手柄、方向盘、衣架、马桶、座垫等制件; 另一类是大型平板制件, 如仪表盘、踏板、保险杠及桌面等。/
a.注射温度
熔体温度太高时,粘度太小,增加了气体进入 制品薄壁的可能性,会导致发生吹穿和薄壁穿 透现象;
有很大意义. /
6.9.6 气体辅助注射成型制品 和模具的设计特点
(a)壁厚 (b)厚薄壁之间的过渡 (c)加强筋 (d)凸台和角撑板 /
①沿气体通道部位的制件壁厚应较厚, ②一般只使用一个浇口,该浇口的设置应使
“欠料注射”的熔料可以均匀地充满模腔; ③由气体所推动的塑料必须将模腔充满;/
而RIM设备的关键则在于对原料的精确计量和高 效混合。/
(1)流量及混合比率要准确, (2)快速加热或冷却原料, (3)两组分应同时进入混合头,在混合头内能获
的穿透作用使多余出来的熔体流入副型腔 /
气辅之2.exe
⑶.熔体回流法 与副腔成型法类似, 气体注入时多余的熔体流回注射机的料筒。/
气辅之3.exe
⑷.活动型芯法
在模腔中设置活动型芯 气体推动熔体使活动型芯从型腔中退出,让
出所需的空间,/
气辅之4.exe
外门把手气辅工艺介绍

成型 成型
主 流 道
Hale Waihona Puke 次流道成型成型1
每腔旳气辅工艺分解--注塑
阀1开启 注塑开始
阀2关闭
原理:同注塑工艺(注意一 定要将阀1开启,阀2关闭)。
注塑把手主体
注塑结束
2
每腔旳气辅工艺分解--吹气
阀1关闭
原理:当模具周围物料已经冷 却,但是内部依然为熔蠕状态 时,将熔蠕物料用氮气吹入余 料井(注意一定要将阀1关闭, 阀2开启)。
阀2开启 吹出内部物料
吹出内部物料
吹气
吹出内部物料
3
此模具旳优点
此模具旳优点 1、模具精度非常高,分型线非常细微,且非常均匀。 2、吹出旳物料假如太多,将影响把手旳强度,无法经过5万次旳开启试
验;假如太少,会使把手内部壁厚不均匀产生缩印(如SGM811把 手)。而HUF旳此副模具设计旳非常精确,只要余料井物料积满,设 备将停止吹气,有效旳控制了壁厚,当然吹气旳走向也直接影响壁厚 是否均匀。
Lessons Learned: 目前国内供给商还不具有对吹气过程在零件设计及开模之迈进行模拟 分析旳能力,SGM 也没有这方面旳Mold-flow 旳经验。加强吹气工艺 旳前期分析应该作为我们在门把手开发中旳一种突破要点,以处理困 扰我们旳缩印问题!
4
气体辅助注塑工艺简介

气体辅助注塑工艺简介1.气体辅助注塑目前所指的气体辅助注塑:是指将氮气注射入产品内,使产品内部形成中空。
模具打开前,控制器会将塑胶工件内的氮气释放回大气中。
2.气辅注塑成形工艺的优势1)低射胶、低锁模力;2)压力分布均匀、收缩均匀、残余应力低、不易翘曲,尺寸稳定;3)消除凹陷,型面再现性高;4)省塑料,可用强度及价格更低的塑料;5)可用强度和价格更低的模具金属;6)厚薄件一体成型,减少模具及装配线数目;7)可用较厚的筋,角板等补强件,提高制品刚性,使得制件公称厚度得以变薄。
8)增强设计自由度。
3.气辅射胶控制工艺1)短射工艺,即胶料未完全充满型腔时,继之以氮气注射;2)满射工艺,塑胶熔体充满型腔之后,停止注射,继之以氮气注射。
短射工艺的特点:在气辅注塑中,塑胶注射取决于胶件形状及胶料性能,在以下条件才可进行短射。
1)胶件必须有独立完整的气体通道,即气流在穿透胶件时,无分支气道可走。
2)气体通道中多余胶料有足够的溢流空间。
3)胶料流动性优良,粘度不可太低,尽量避免使用含破坏高分子键的填充物的胶料。
4)胶料导热度较低,有可较长时间保持熔融状态的能力。
满射工艺特点:胶件射胶完成,通过气体代替啤机,防止胶件收缩。
其优点在于,啤机保压是以射胶量及压力来防止胶件收缩,气辅保压,则以气体穿透塑胶收缩后的空间,防止胶件表层埸陷。
4.气辅压力分析:现我们看以下气辅压力与啤机压力的对比:1)气辅压力a)低气压800psi=56.34kg/cm2b)中气压1500psi=105.63 kg/cm2c)高气压2500psi=176.06kg/cm22)啤机压力a)100 TON注塑最大压力188Mpa=1917 kg/cm2b)280 TON注塑最大压力150Mpa=1530 kg/cm2c)650TON注塑最大压力153Mpa=1560 kg/cm2从以上压力对比可知,氮气压力只相当于普通啤机注塑压力的十分之一,甚至更少。
气体辅助注射成型在汽车塑料件中的应用

气体辅助注射成型在汽车塑料件中的应用随着汽车工业的迅速发展,注塑已发展为汽车用塑料件生产的最重要的技术。
如风扇、挡泥板、保险杠、仪表盘、车门等大多数塑料件都是用注塑方法生产的。
气体辅助注射成型( Gas Assisted Injection Molding ,简称GA IM) 又称为Air Mould 法,是在传统的注塑基础上发展起来的一种新的成型工艺。
近年来, GA IM因其充模压力低、制品内应力小、表面光洁等优点已成为塑料工业中重要的加工方法。
气体辅助注射成型基本原理和基本过程其原理是:在一定量的熔体注入型腔后,再将压缩空气注入熔体中心, 然后在压缩空气的作用下充满型腔。
GA IM 基本过程主要包括以下几个阶段:(1) 熔体注塑,即将聚合物熔体注入模具型腔,该过程与传统注塑成型相同,熔体一般充满型腔60 %~97 %(随产品而异) ;(2) 气体注塑,即把高压氮气注入熔体芯部,熔体流动前沿在高压气体驱动下继续向前流动,直到充满整个型腔;(3) 气体保压,即制件在保持气体压力情况下冷却,在冷却过程中,气体由内向外施压,保证制品外表面紧贴模壁,并通过气体二次穿透从内部补充因熔体冷却凝固带来的体积收缩;(4) 气体泄压并回收循环使用;(5) 模腔打开,取出制件气体辅助注射成型在汽车塑料件中的应用采用该工艺,可成型尺寸大、壁厚差较大的制品,且大大降低了表面粗糙度、内应力和生产成本, 用于生产汽车仪表板、车窗滑槽、甚至保险杠等.可以认为应用GA IM 的目的,主要是对粗厚件减重并改善表面质量;对大型平板制件降低锁模力,减小翘曲变形等.GA IM 用于汽车塑料件生产. 凯奥采用GA IM 制得了中空的PB T/ PC复合材料制件,其厚度均匀性、表面光洁性优良,且脱模容易,可用作汽车的前后挡板、门把手等. 而凯奥用GA IM 制备的玻纤增强的聚酰胺复合材料制件,具有高光泽、高强度等优点,断裂拉伸强度达210M Pa ,弯曲模量12 GPa ,表面粗糙度低,可用作汽车部件。
注塑成型中的气体辅助技术应用
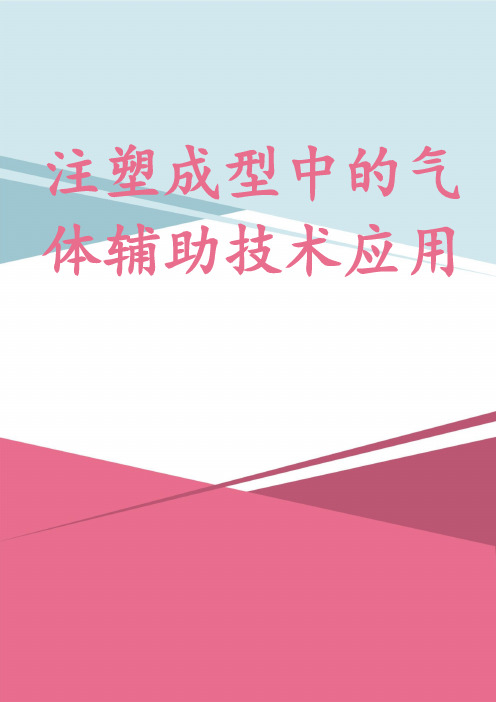
注塑成型中的气体辅助技术应用注塑成型中的气体辅助技术应用注塑成型是一种常用的塑料加工方法,通过将熔化的塑料注入模具中,经过冷却固化后得到所需的塑料制品。
然而,在注塑成型过程中,常常会出现一些问题,如缺陷、翘曲等。
为了解决这些问题,气体辅助技术在注塑成型中得到了广泛的应用。
气体辅助技术是指在注塑成型过程中,通过向模具中注入气体,利用气体的性质对塑料进行辅助成型的一种方法。
在注塑成型过程中,通过在模具中注入气体,可以改善产品表面质量,减少翘曲和缩水等缺陷,提高产品的整体性能。
首先,气体辅助技术可以改善产品的表面质量。
在注塑成型中,由于塑料的热胀冷缩和浇注冷却的不均匀性,常常会出现产品表面的缺陷,如气泡、痕迹等。
通过在模具中注入气体,可以使塑料在充填过程中更加均匀,减少气泡的产生,从而改善产品的表面质量,使其更加光滑。
其次,气体辅助技术可以减少产品的翘曲和缩水。
在注塑成型中,由于塑料的收缩性质,产品往往会出现翘曲和缩水等问题。
通过在模具中注入气体,可以产生一定的气压,使塑料在冷却固化过程中更加均匀,减少翘曲和缩水的可能性,从而提高产品的几何稳定性和尺寸精度。
最后,气体辅助技术可以改善产品的整体性能。
在注塑成型中,由于塑料的结晶性质,产品往往会出现内部应力集中的问题,从而影响产品的强度和韧性。
通过在模具中注入气体,可以使塑料在充填过程中形成空腔结构,减少内部应力的集中,提高产品的整体性能,使其更加坚固耐用。
综上所述,气体辅助技术在注塑成型中的应用可以改善产品的表面质量,减少翘曲和缩水,提高产品的整体性能。
随着技术的不断发展,气体辅助技术在注塑成型中的应用前景更加广阔,将为塑料制品的生产提供更多的可能性。
气体辅助注射成型技术原理及应用.

气体辅助注射成型技术原理及应用气体辅助注射成型(Gas-Assisted Injection Molding, GAIM)技术最早可追溯到20世纪70年代,该技术在20世纪80年代末得到了完善并实现了商品化。
从20世纪90年代开始,作为一项成功的技术,气体辅助注射成型技术在美、日、欧等发达国家和地区得到了广泛应用。
目前该技术主要被应用在家电、汽车、家具、日常用品、办公用品等加工领域中。
气体辅助注射成型技术的工艺过程气体辅助注射成型技术的工艺过程是:先向模具型腔中注入塑料熔体,再向塑料熔体中注入压缩气体。
借助气体的作用,推动塑料熔体充填到模具型腔的各个部分,使塑件最后形成中空断面而保持完整外形。
在成型后的制品中,由气体形成的中空部分被称为气道。
由于具有廉价、易得且不与塑料熔体发生反应的优点,因此一般所使用的压缩气体为氮气。
气体辅助注塑成型周期可分为以下六个阶段。
(1)塑料充模阶段这一阶段与普通注塑成型基本相同,只是普通注塑成型时塑料熔体是充满整个型腔,而气体辅助注塑成型时塑料熔体只充满局部型腔,其余部分要靠气体补充。
(2)切换延迟阶段这一阶段是塑料熔体注射结束到气体注射开始时的时间,这一阶段非常短暂。
(3)气体注射阶段此阶段是从气体开始注射至整个型腔被充满的时间,这一阶段也比较短,但对制品质量的影响极为重要,如控制不好,会产生空穴、吹穿、注射不足和气体向较薄的部分渗透等缺陷。
(4)保压阶段熔体内气体压力保持不变或略有上升使气体在塑料内部继续穿透,以补偿塑料冷却引起的收缩(5)气体释放阶段使气体入口压力降到零。
(6)冷却开模阶段将制品冷却到具有一定刚度和强度后开模取出制品。
根据具体工艺过程的不同,气体辅助注射成型可分为标准成型法、副腔成型法、熔体回流法和活动型芯法四种。
1、标准成型法标准成型法是先向模具型腔中注入经准确计量的塑料熔体(如图1a所示),再通过浇口和流道注入压缩气体。
气体在型腔中塑料熔体的包围下沿阻力最小的方向扩散前进,对塑料熔体进行穿透和排空(如图1b所示),最后推动塑料熔体充满整个模具型腔并进行保压冷却(如图1c所示),待塑料制品冷却到具有一定刚度和强度后,开模将其顶出(如图1d所示)。
气辅注塑 气道设计
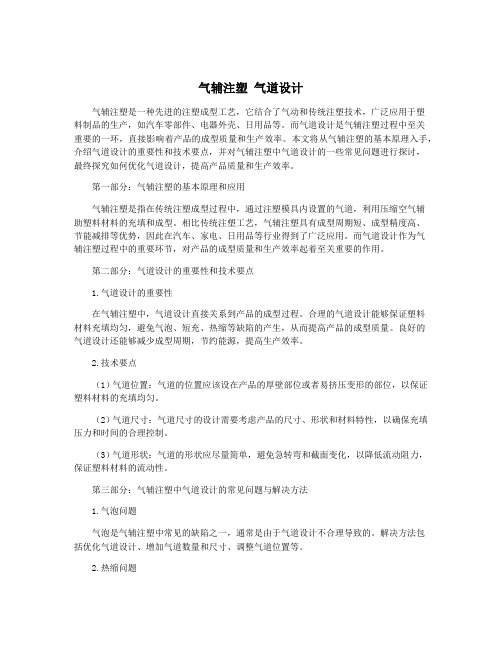
气辅注塑气道设计气辅注塑是一种先进的注塑成型工艺,它结合了气动和传统注塑技术,广泛应用于塑料制品的生产,如汽车零部件、电器外壳、日用品等。
而气道设计是气辅注塑过程中至关重要的一环,直接影响着产品的成型质量和生产效率。
本文将从气辅注塑的基本原理入手,介绍气道设计的重要性和技术要点,并对气辅注塑中气道设计的一些常见问题进行探讨,最终探究如何优化气道设计,提高产品质量和生产效率。
第一部分:气辅注塑的基本原理和应用气辅注塑是指在传统注塑成型过程中,通过注塑模具内设置的气道,利用压缩空气辅助塑料材料的充填和成型。
相比传统注塑工艺,气辅注塑具有成型周期短、成型精度高、节能减排等优势,因此在汽车、家电、日用品等行业得到了广泛应用。
而气道设计作为气辅注塑过程中的重要环节,对产品的成型质量和生产效率起着至关重要的作用。
第二部分:气道设计的重要性和技术要点1.气道设计的重要性在气辅注塑中,气道设计直接关系到产品的成型过程。
合理的气道设计能够保证塑料材料充填均匀,避免气泡、短充、热缩等缺陷的产生,从而提高产品的成型质量。
良好的气道设计还能够减少成型周期,节约能源,提高生产效率。
2.技术要点(1)气道位置:气道的位置应该设在产品的厚壁部位或者易挤压变形的部位,以保证塑料材料的充填均匀。
(2)气道尺寸:气道尺寸的设计需要考虑产品的尺寸、形状和材料特性,以确保充填压力和时间的合理控制。
(3)气道形状:气道的形状应尽量简单,避免急转弯和截面变化,以降低流动阻力,保证塑料材料的流动性。
第三部分:气辅注塑中气道设计的常见问题与解决方法1.气泡问题气泡是气辅注塑中常见的缺陷之一,通常是由于气道设计不合理导致的。
解决方法包括优化气道设计、增加气道数量和尺寸、调整气道位置等。
2.热缩问题热缩是指产品在冷却后出现收缩不均匀的现象,通常是由于气道位置不当或尺寸设计不合理引起的。
解决方法包括优化气道位置、增加气道数量、调整气道尺寸等。
3.短充问题短充是指产品某一部位塑料材料未充填完全的现象,常常与气道设计不当有关。
5.6气体辅助注塑

尚未充满的型腔 气体 (4) 保压冷却阶段:成品内部被气体充填后,气体作用 于成品中空部分的压力就成为保压压力,可大大减低成品 的收缩和变形率。 气熔边界 熔体凝固层
3、气辅注塑成型工艺过程
(5)气体释放阶段:在模具开摸前,气体从制件内部排 出,气压降至到常压下。 气腔 气体排出 (6)开模阶段:开模取出产品 熔体凝固层
为控制气道的形成和避免气体“吹破”, 塑料应有一定的熔体强度, 像 聚氨脂等非常柔软的塑料就不适用。PA 和PBT 类型的易结晶塑料尤 其适用于气辅注塑。气辅注塑最常用的塑料是PA6、PA66 及PP(通常 是玻璃纤维增强的)。
9、气辅注塑成型应用
1)管状或杆状制件:如衣架、钳柄、椅子扶手、喷射头 和水龙头开关等;——节省物料、缩短周期、实现制品 的功能。
活动型芯法成型示意图
7、气辅注塑成型特点
优点
(1) 可成型传统注射成型工艺难以加工的壁厚差异较大制件。 (2) 可消除厚壁处的缩痕,提高表面质量。 (3) 降低产品出模后残余内应力,减轻翘曲变形,提高产品 强度。(克服30%凹陷翘曲) (4) 缩短成型周期,提高生产效率(缩短20%成型周期) (5) 可减轻制品重量,节省材料,在保证产品质量的前提下 大幅度降低成本。(降低30%成本) (6) 所需注射压力和锁模力小,可大幅度降低对注塑机和模 具的要求。 (7) 改善材料在制品断面上的分布,改善制品的刚性。
5.6 气体辅助注塑成型工程
主讲:魏雅丽
1、气体注塑辅助工艺产生背景
最初:改善模具设计;提高注射机质量;调整工艺参数; 结果:成本提高,制品质量仍较差; 解决方法:气体辅助注射成型 。 气体辅助注塑成型GAIM(Gas Assist Injection Molding) 自20世纪80年代出现,20世纪90年代进入实用阶段。 气辅成型应用:欧、美、日等发达国家应用广泛;我国 家电、汽车等行业也积极采用。
气体辅助注塑成型简介
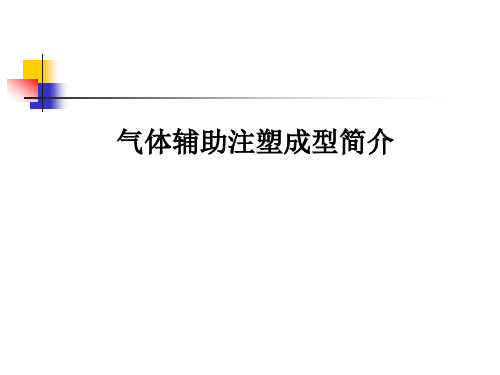
1.什么是气体辅助注射成型?
气体辅助注塑成型其原理是利用高压气体在塑件内部产生中空截面,利用 气体保压代替塑料注射保压,消除制品缩痕,完成注射成型过程。 气体辅助注塑成型的工艺过程主要包括塑料熔体注射、气体注射、气体保 压三个阶段。气体辅助注射成型过程首先是向模腔内进行树脂的欠料注射,然后 把经过高压压缩的氮气导入熔融物料当中,气体沿着阻力最小方向流向制品的低 压和高温区域。当气体在制品中流动时,它通过置换熔融物料而掏空厚壁截面。 这些置换出来的物料充填制品的其余部分。当填充过程完成以后,由气体继续提 供保压压相比,气体辅助注塑成型有更多的工艺参数需要确 定和控制,因而对于制品设计、模具设计和成型过程的控制都有特殊的要求。
5. 气辅成型常见问题及对策
⑹气道与薄壁连接处缩凹 气道由于气体穿透,导致气道与薄壁接触部分壁厚较大,解决方法: 1.在气道与薄壁接触位置增设防缩槽 2.气道与薄壁连接处尽量不采用圆角过渡 3.尽量增大气道表面积,以利于迅速冷却 ⑺气体穿透不均 原因: 1.熔体流动不平衡 2.气道布局不合理 3.模具精度差,导致塑件壁厚不均 解决方法: 1.修改浇口布局 2.修改气道布局 3.提高模具制造精度
2.气体辅助注射成型有什么优点?
(1)解决制件表面缩痕问题,能够大大提高制件的表面质量。 (2)局部加气道增厚可增加制件的强度和尺寸稳定性,并降低制品内应力,减 少翘曲变形。 (3)节约原材料,最大可达40%~50%。
(4)简化制品和模具设计,降低模具加工难度。
(5)降低模腔压力,减小锁模力,延长模具寿命。 (6)冷却加快,生产周期缩短。
5. 气辅成型常见问题及对策
⑴制件表面银纹(streak) 浇口处料流速度过快,剪切速率过大 修改浇口类型,或者增大浇口尺寸,减小料流速度
塑料注塑气辅成型原理

塑料注塑气辅成型原理塑料注塑气辅成型是一种常见的塑料成型方法,它结合了注塑成型和气辅成型两种工艺,使得产品的成型效果更加精确和高效。
本文将从原理、工艺流程、优点和应用等方面介绍塑料注塑气辅成型。
一、原理塑料注塑气辅成型是指在注塑成型的过程中,通过加入气体辅助来实现产品的成型。
其原理是在注塑成型时,通过注射机将熔化的塑料注入模具中,然后在注塑过程中加入一定的气体,使得塑料在模具中充分膨胀,从而得到所需的产品形状。
注塑气辅成型可以有效地解决一些注塑过程中容易产生缺陷的问题,如翘曲、收缩等。
二、工艺流程塑料注塑气辅成型的工艺流程主要包括以下几个步骤:1. 原料准备:选用适合注塑成型的塑料原料,并进行预处理,如干燥、混合等。
2. 模具设计:根据产品的需求设计模具,并制作成型模具。
3. 注塑成型:将预处理好的塑料原料放入注塑机的料斗中,经过加热、熔化后,通过注射机将熔化的塑料注入模具中。
4. 气辅成型:在注塑过程中,通过气体辅助装置向模具中注入一定的气体,使得塑料在模具中膨胀成型。
5. 冷却固化:待塑料在模具中冷却固化后,将成型产品从模具中取出。
6. 后处理:对成型产品进行修整、去除余料、清洁等处理。
三、优点塑料注塑气辅成型相比传统的注塑成型有以下几个优点:1. 产品质量好:通过气辅成型可以减少或避免一些常见的缺陷,如翘曲、收缩等,提高产品的质量。
2. 成型效率高:气辅成型可以在注塑过程中快速膨胀,提高成型效率,缩短生产周期。
3. 成本低:相比其他成型工艺,注塑气辅成型的设备和工艺要求相对简单,成本较低。
4. 适用范围广:注塑气辅成型适用于各种塑料材料,适用于各种形状的产品,具有很大的灵活性。
四、应用塑料注塑气辅成型在各个领域都有广泛的应用,特别是对于一些形状复杂、尺寸精确的产品,更加适用。
以下是一些常见的应用领域:1. 汽车零部件:如汽车灯罩、仪表盘等。
2. 家电产品:如电视外壳、空调面板等。
3. 医疗器械:如注射器、输液器等。
- 1、下载文档前请自行甄别文档内容的完整性,平台不提供额外的编辑、内容补充、找答案等附加服务。
- 2、"仅部分预览"的文档,不可在线预览部分如存在完整性等问题,可反馈申请退款(可完整预览的文档不适用该条件!)。
- 3、如文档侵犯您的权益,请联系客服反馈,我们会尽快为您处理(人工客服工作时间:9:00-18:30)。
气辅注塑工艺的应用和工艺过程
一、气辅注塑的原理
利用高压惰性气体(氮气)注射到熔融的塑胶中形成真空截面并推动融料前进,实现注射、保压、冷却等过程。
由于气体具有高效的压力传递性,可使气道内部各处的压力保持一致,因而可消除内部应力,防止产品变形,同时大幅度降低模腔内压力,因此在成型过程中不需要很高的锁模力,还可以减轻产品重量、消除缩痕等。
二、气辅设备
气辅设备包括气辅控制单元和氮气发生装置。
它是独立于注塑机外的另一套系统,其与注塑机的唯一接口是注射信号连接线。
注塑机将一个注射信号注射开始或螺杆位置传递给气辅控制控制单元之后,便开始一个注气过程,等下一个注射过程开始时给出另一个注射信号,开始另一个循环,如此反复进行。
气辅注塑所使用的气体必须是惰性气体(通常为氮气),气体最高压为35MPa,特殊者可达70MPa,氮气纯度≥98%。
气辅控制单元是控制注气时间和注气压力的装置,它具有多组气路设计,可同时控制多台注塑机的气辅生产,气辅控制单元设有气体回收功能,尽可能降低气体耗用量。
三、气辅工艺控制
•注气参数
气辅控制单元是控制各阶段气体压力大小的装置,气辅参数只有两个值:注气时间(秒)和注气压力(MPa)
气辅注塑过程是在模具内注入塑胶熔体的同时注入高压气体,熔体与气体之间存在着复杂的两相作用,因此工艺参数控制显得相当重要,各参数的控制方法如下:
•注射量
气辅注塑是采用所谓的“短射”方法,即先在模腔内注入一定量的料(通常为满射时的70-95%),然后再注入气体,实现全充满过程。
熔胶注射量与模具气道大小及模腔结构关系最大。
气道截面越大,气体越易穿透,掏空率越高,适宜于采用较大的“短射率”。
这时如果使用过多料量,则很容易发生熔料堆积,料多的地方会出现缩痕。
如果料太少,则会导致吹穿。
如果气道与流料方向完全一致,那么最有利于气体的穿透,气道的掏空率最大。
因此在模具设计时尽可能将气道与流料方向保持一致。
•注射速度及保压
在保证制品表现不出现缺陷的情况下,尽可能使用较高的注射速度,使熔料尽快充填模腔,这时熔料温度仍保持较高,有利于气体的穿透及充模。
气体在推动熔料充满模腔后仍保持一定的压力,相当于传统注塑中的保压阶段,因此一般讲气辅注塑工艺可省却用注塑机来保压的过程。
但有些制品由于结构原因仍需使用一定的注塑保压来保证产品表现的质量。
但不可使用高的保压,因为保压过高会使气针封死,腔内气体不能回收,开模时极易产生吹爆。
保压高亦会使气体穿透受阻,加大注塑保压有可能使制品表现出现更大缩痕。
•气体压力及注气速度
气体压力与材料的流动性关系最大。
流动性好的材料(如PP)采用较低的注气压力。
气体压力大,易于穿透,但容易吹穿;气体压力小,可能出现充模不足,填不满或制品表面有缩痕;注气速度高,可在熔料温度较高的情况下充满模腔。
对流程长或气道小的模具,提高注气速度有利于熔胶的充模,可改善产品表面的质量,但注气速度太快则有可能出现吹穿,对气道粗大的制品则可能会产生表面流痕、气纹。
•延迟时间
延迟时间是注塑机射胶开始到气辅控制单元开始注气时的时间段,可以理解为反映射胶和注气“同步性”的参数。
延迟时间短,即在熔胶还处于较高温度的情况下开始注气,显然有利于气体穿透及充模,但延迟时间太短,气体容易发散,掏空形状不佳,掏空率亦不够。
四、气辅模具
气辅模具与传统注塑模具无多大差别,只增加了进气元件(称为气针),并增加气道的设计。
所谓“气道”可简单理解为气体的通道,即气体进入后所流经的部分,气道有些是制品的一部分,有些是为引导气流而专门设计的胶位。
气针是气辅模具很关键的部件,它直接影响工艺的稳定和产品质量。
气针的核心部分是由众多细小缝隙太大会被熔胶堵塞,出气量反而下降。
五、气体辅助注射成型工艺过程
气体辅助注射成型的工艺有四个步骤第一步树脂充模:模具部分地被熔体填充。
第二步气体充模:氮气根据要求注入到热的熔体中。
气体在高温低压区域流动讯速。
气体流动的方向通常是阻力最小的方向。
根据设计,气道要放在便于引导气体到低压区域的地方。
用压力气体代替的塑件中厚截面处的热熔融物料,用该压力气体来完成塑料的填充;
第三步气体保压:由于熔体和气体共同作用,在模具填充之后,氮气留在塑件的气体流道内,它有足够的压力使塑件压实。
随后树脂冷却和收缩,气体压迫道还没有凝固的树脂到收缩造成的空隙中。
用保压压力来消除塑件表面上的缩痕,并且保证在下一个成型周期,模具有较好的表面质量,以成型表面质量好的塑件;
第四步气体排出:整个工艺过程中需要的所有气体,有开模之前必须排出。
如果没有及时排出压力气体,会使塑件胀大甚至胀破。