内轮廓零件加工2
2数控铣床加工工艺
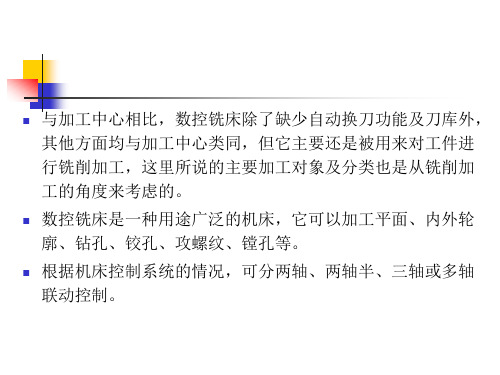
(1)准备功能及辅助功能 (2)机床坐标系及工件坐标系
1.机床坐标系 机床上固有的坐标系。机床坐标系的原点由设计厂家在设
计机床时确定。 一般情况下,铣床原点的位置可在启动机床后,使机床三
个坐标轴的坐标依次运动到其正方向的极限位置确定,机 床三个坐标轴所达到的这个位置就是机床坐标系原点 2.工件坐标系 工件坐标系原点在工件上或在夹具的某一点上,由编程人 员设定,其位置随工件和夹具在机床工作台上的安装位置 而定,所以又叫浮动原点或编程原点,一般在程序开头设 置。
序内往往需要采用不同的刀具和切削用量,对不同的表面 进行加工。 为了便于分析和描述较复杂的工序;在工序内又细分为工 步。下面以加工中心为例来说明工步划分的原则: 1) 同一表面按粗加工、半精加工、精加工依次完成全部加工 表面,按先粗后精加工分开进行。 2) 对于既有铣面又有镗孔的零件,可先铣面后镗孔。 3) 某些机床工作台回转时间比换刀时间短,可采用按刀具划 分工步,以减少换刀次数,提高加工效率。 总之,工序与工步的划分要根据具体零件的结构特点、技 术要求等情况综合考虑。
参考平面
R
工件上表面
主轴顺时针转动 Z
主轴逆时针转动
G85:镗孔循环
• 指令格式:G85 X_ Y_ Z_ R_ F_ K_ LF • G85与G84相同,只是在孔底主轴不反转
G98 初始平面
工件平面
G99 参考平面 Z点
G86:镗削循环
指令格式:G86 X_ Y_ Z_ R_ F_ K_ LF 和G81相同,只是在孔底主轴停,然后用快速返回
二、数控加工零件的工艺性分析
1. 零件图的几何尺寸标注及轮廓的几何要素 (1)要彻底读董图样 (2)要分析透零件的加工工艺性 (3)研究分析零件的精度 (4)研究分析零件的刚性 (5)研究分析零件的定位基准 (6)研究零件的毛坯和材料
《数控编程技术》作业2参考答案

《数控编程技术》作业2参考答案第4章基本功能指令的编程方法一、填空题1、用于控制开关量的功能指令是_______M_______。
2、T0400的含义是____取消4号刀补_________。
3、采用恒线速度控制车削带锥度的外圆时,若线速度为200米/分钟,最高转速限定在1300转/分钟,正确的编程格式为_____f200 f1300____________。
4、直线进给率的单位为______mm/min___________;旋转进给率的单位为__________r/min_______。
5、只有当机床操作面板上的“选择停止键”被按下,才能生效的暂停指令是__M01_______。
二、选择题1、G96 S150 表示切削点线速度控制在(c)。
(A)150 m/min (B)150 r/min(C)150 mm/min(D)150 mm/r2、程序结束,并返回到起始位置的指令是(d)。
(A)M00(B)M01(C)M02(D)M303、()。
(A)M00(B)M01(C)M02(D)M304、当执行M02指令时,机床(b)。
(A)进给停止、冷却液关闭、主轴不停(B)主轴停止、进给停止、冷却液关闭,但程序可以继续执行(C)主轴停止、进给停止、冷却液未关闭、程序返回至开始状态(D)主轴停止、进给停止、冷却液关闭、程序结束三、判断题1、恒线速控制的原理是当工件的直径越大,进给速度越慢。
(对)2、有些车削数控系统,选择刀具和刀具补偿号只用T指令;而铣削数控系统,通常用T指令指定刀具,用D、H代码指定刀具补偿号。
(对)3、用M02和M30作为程序结束语句的效果是相同的。
(错)四、简答题1、指令M00和M01有什么相同点?区别是什么?1. M00:程式停止.程式自動執行時.當執行到M00時,機台將停止執行下一動作。
2. M01:選擇性程式停止.與M00功能相同:當面板功能鍵打開.程式執行到M01時會停止,如功能鍵不打開則不執行。
端面切削循环指令G94讲解

限定最高转速2000r/min
G96 S200
启用恒线速度功能,切削速度为200m/min
G01 X40.0 F0.08;
Z-5.0; X0 Z0;
精车端面轮廓
G00 X61.0 Z2.0;
(转下页)
项目四 内、外轮廓加工
刀具 N220 N230 N240 N250
1号:93°端面车刀
G97 S500;
(粗车时主轴转速n为 500r/min,进给量f为 0.15mm/r)
图例
粗车斜端面,Z向留 0.3mm精加工余量
(粗车时主轴转速n 为500r/min,进给量f为 0.15mm/r)
(转下页)
项目四 内、外轮廓加工
步骤
图例
完成轮廓的精加工 (精车选择恒线速功 能,转速n为200m/min, 最高转速限2000r/min, 进给量f为0.08mm/r)
取消恒线速度功能
G00 X100.0 Z100.0;
M9;
程序结束部分
M30;
为保证零件端面加工的表面粗糙度要求,在精加工中 使用恒线速度功能编程。
项目四 内、外轮廓加工
三、加工准备
选用的机床为配备FANUC 0i系统的CKA6140型数控车床。
毛坯为φ60mm×22mm的圆钢。刀具使用机夹端面车刀。量具
3
进给量 背吃刀量 加工内容 主轴转速
(mm/r) (mm)
粗车端面 500r/min
0.15
2
精车端面 1000m/min 0.08
0.3
项目四 内、外轮廓加工
二、程序编制 任务2参考程序
刀具
1号:93°端面车刀
程序 段号
加工程序 O4020;
任务6 具有非圆曲线轮廓的零件加工编程与操作第2版(FANUC)

能 报
4.手动安装φ20mm粗加工两刃立铣刀至主轴。
国
5.用铣刀直接对刀,将X、Y对刀值输入G54地址,设置工件坐标系零点偏置 值,G54地址中的Z地址须为0。在每把刀的刀补界面输入Z对刀值及刀具半径补偿
值。工件坐标系的原点设在工件上表面的对称中心。
1166
四、任务实施
勤 学
(二)零件加工
苦
6.输入程序,并反复检查。检查无误后,自动状态下进行外轮廓粗加工。
勤 学 苦 练
技 能
任务六 具有非圆曲线轮廓的零件
报
加工编程与操作
国
11
一、任务导入
勤 (一)任务描述
学
使用FAUNC系统数控铣床,对如图2-40所示的非圆曲线
苦
练
类零件进行编程及加工。
技 能 报 国
图2-40 二维椭圆零件
22
一、任务导入
勤
学 (二)知识目标
苦 1.掌握FANUC数控系统宏指令的使用与编程。 练 2.掌握FANUC数控系统条件转移或循环语句在非圆曲线轮廓编
抬刀,取消刀具长度补偿,回到机床原点
1133
四、任务实施
勤 (一)编写零件加工程序
学
表2-37 加工主程序
苦
N80 M00;
(机床动作暂停,手工装φ20mm 三刃立铣刀)
练
N90 M03 S500 G00 X62. Y5.; (设置T2主轴转速,快移至加工定位点,)
N100 G01 G43 Z5. F1000 H02; 带入刀具长度补偿,下移至工件上5mm处
练
7.粗加工完毕后,机床暂停,手动测量工件,如数据与理想状态相符,则不
需修改精铣刀刀补值。
浅谈线切割加工的穿丝孔

统 而 又详细的介绍,基 于 此 ,笔者系统全面介绍了线切 割 穿 丝 孔 的 作 用 、位 置 的 具 体 确 定 、加 工 方 法 及 大 小 的
夹 持 部 分 少 ,工件刚度大大降低,后面部分加工容易产
c 生 变 形 ,加 工 误 差 较 大 。图 1( )这 种 走 丝 路 径 最 好 。因
Discussion on Wear of Cutting Hole
CAO Qing-xiang
(Hunan Biological and Electromechanical Polytechnic,Changsha,Hunan 410126,China)
Abstract:Outline of parts within a wire through hole,you must advance through hole,wire to fit in to be processed.High cutting precision of contour parts,or to advance through the hole from the wire hole wire processing,this can reduce the deformation of the workpiece can also prevent jammed or broken electrode wire.Wire hole position determinates the machining quality and smooth processing of parts. Keywords:Wire cutting;EDM;wire holes;Electrode wire;punch;die
切割通孔凹模或者带孔工件时,必须先有一个孔用 减少外形工件在线切割加工中的变形。如图1所 示 ,加工
2机械零件的钳加工课程标准

10.錾子的使用方法及使用注意事项
11.锉刀的类型及使用范围
12.锉刀的使用方法及使用注意事项
13.去毛刺的方法
14.用砂纸抛光的方法
15.开瓶器的质量分析及评价方法
16.现场5s管理规程7.对工作完成情况的评价
一、评价形式
1.自我评价:学习准备及计划实施的学习效果,工作页填写情况
建议课时
教学建议
与说明
学习任务1:开瓶器的制作
1.能通过各种渠道获取信息,并向老师咨询信息的可靠性并表述出所获取开瓶器的材料、价格、形状信息
2.能绘制零件草图
3.能在毛坯上利用划线工具根据样板描绘出起瓶器轮廓
4.能安全使用手工工具或设备去除工件余料
5.能够安全使用榔头击打錾子进行錾削
6.能正确使用台虎钳夹紧零件
5.能规范使用钻床,合理选择钻头对孔进行加工,并能正确保养钻床。
6.能正确使用游标卡尺、刀口直尺、刀口角尺对錾口榔头进行检测,并准确记录测试结果。
7.能按加工工艺步骤对錾口榔头进行加工。并用专业术语进行交流。
8.能对錾口榔头进行淬火处理。
9.能根据现场管理规范要求,清理场地,归置物品并按环保要求处理废弃物。
机电一体化技术专业基本技能培养课程标准
课程名称
机械零件的钳加工
基准学时
390
工作任务描述
机电一体化技术人员根据零件加工图,手工操作钳工常用工量具及钻床等,通过划线、锯削、锉配、刮削、研磨、钻孔、扩孔、锪孔、铰孔、攻螺丝和套螺纹等进行零件的内、外轮廓及孔等加工。在工作过程中,技术人员以小组合作或独立工作的形式,使用专用软件和工具,遵守“6S”管理的工作要求,自觉安全文明工作,并填写工作记录,保存相关资料。
内轮廓零件的对刀方法

内轮廓零件的对刀方法
对于内轮廓零件的对刀方法,通常可以采用寻边器对刀,具体步骤如下:
1. 将工件通过夹具装在机床工作台上,装夹时,工件的四个侧面都应留出寻边器的测量位置。
2. 快速移动工作台和主轴,让寻边器测头靠近工件的左侧。
3. 改用微调操作,让测头慢慢接触到工件左侧,直到寻边器发光,记下此时机床坐标系中的X坐标值。
4. 抬起寻边器至工件上表面之上,快速移动工作台和主轴,让测头靠近工件右侧。
5. 改用微调操作,让测头慢慢接触到工件左侧,直到寻边器发光,记下此时机械坐标系中的X坐标值。
6. 根据测得的X坐标值,可以计算出工件长度,从而确定工件坐标系原点
W在机床坐标系中的X坐标值。
7. 同理,可以测得工件坐标系原点W在机械坐标系中的Y坐标值。
对刀完成后,就可以开始进行零件的加工了。
对刀是数控加工中的重要步骤,对刀的精度和准确性会直接影响零件的加工精度和表面质量,因此要认真对待。
指尖陀螺工艺设计与数控编程加工毕业设计说明书

图一和图二是装配件为了表面粗糙度保持相同所以同一表面粗糙度为 Ra3.2
(六)毛坯的选择
1.毛坯材料 材料:不锈钢 302 2.材料特点 1 表面美观以及使用可能性多样化; 2 耐腐蚀性能好,比普通钢长久耐用; 3 耐高温氧化及强度高,因此能够抗火灾; 4 强度高,因而薄板使用的可能性大; 5 常温加工,即容易塑性加工; 因为不必表面处理,所以简便、维护简单; 图一毛坯选择(图 2-1)不锈钢方材 40X80X20mm 图二毛坯选择(图 2-2)不锈钢圆材 30X20mm
内r角加工方法

内r角加工方法
内R角加工方法有以下两种:
1. 使用修饰柱或者玻璃钢纤维绳把需要的R角包裹起来,再用激光扫描该转角,通过CAE软件进行仿真模拟该转角成型的塑性流动,进而得到适合的工艺参数。
之后进行热处理并检查加工零件的表面质量。
这种方法需要专业的设备和技术,不适合普通操作人员。
2. 使用数控机床或雕刻机进行加工。
先将板材放入数控机床或雕刻机的工作台上,通过调整刀具和路径规划,按照合适的路径进行切割,即可得到内R角。
这种方法相对简单,适合大量生产,但可能需要一定的数控机床专业知识。
请注意,以上方法可能存在差异,建议咨询专业人士以获得准确的方法。
机械零件加工技术要求汇总

机械零件加工技术要求汇总一、零件表面处理:1、零件加工表面上,不应有划痕、擦伤等损伤零件表面的缺陷。
2、加工的螺纹表面不允许有黑皮、磕碰、乱扣和毛刺等缺陷。
所有需要进行涂装的钢铁制件表面在涂漆前,必须将铁锈、氧化皮、油脂、灰尘、泥土、盐和污物等除去。
3、除锈前,先用有机溶剂、碱液、乳化剂、蒸汽等除去钢铁制件表面的油脂、污垢。
4、经喷丸或手工除锈的待涂表面与涂底漆的时间间隔不得多于6h。
5、铆接件相互接触的表面,在连接前必须涂厚度为30~40μm防锈漆。
搭接边缘应用油漆、腻子或粘接剂封闭。
由于加工或焊接损坏的底漆,要重新涂装。
二、零件的轮廓处理:1、未注形状公差应符合GB1184-80的要求。
2、未注长度尺寸允许偏差±0.5mm。
3、未注圆角半径R5。
4、未注倒角均为C2。
5、锐角倒钝。
6、锐边倒钝,去除毛刺飞边。
三、零件的热处理:1、经调质处理,HRC50~55。
2、中碳钢:45 或40Cr 零件进行高频淬火,350~370℃回火,HRC40~45。
3、渗碳深度0.3mm。
4、进行高温时效处理。
精加工后技术要求1、精加工后的零件摆放时不得直接放在地面上,应采取必要的支撑、保护措施。
2、加工面不允许有锈蛀和影响性能、寿命或外观的磕碰、划伤等缺陷。
3、滚压精加工的表面,滚压后不得有脱皮现象。
4、最终工序热处理后的零件,表面不应有氧化皮。
经过精加工的配合面、齿面不应有退火四、零件的密封处理:1、各密封件装配前必须浸透油。
2、组装前严格检查并清除零件加工时残留的锐角、毛刺和异物。
保证密封件装入时不被擦伤。
3、粘接后应清除流出的多余粘接剂。
五、齿轮技术要求:1、齿轮装配后,齿面的接触斑点和侧隙应符合GB10095和GB11365的规定。
2、齿轮(蜗轮)基准端面与轴肩(或定位套端面)应贴合,用0.05mm塞尺检查不入。
并应保证齿轮基准端面与轴线的垂直度要求。
3、齿轮箱与盖的结合面应接触良好。
六、轴承技术要求:1、装配滚动轴承允许采用机油加热进行热装,油的温度不得超过100℃。
习题册参考答案-《数控铣床加工中心编程与操作(华中系统)(第二版)习题册》-A02-3934

全国技工院校数控加工类专业通用(中级技能层级)数控铣床加工中心编程与操作(华中系统)(第二版)习题册答案中国劳动社会保障出版社第一章数控铣床/加工中心编程基础知识第一节数控铣床/加工中心概述一、填空题(将正确答案填写在横线上)1. 铣削加工镗削加工2. 立式卧式立卧两用3. 水平水平4. 刀库多工序5.卧式立式6.变斜角7.曲面8. 刀库刀具自动交换9. 数控装置伺服系统10. 中枢11. 控制运算器12. 驱动执行13. 进给主轴14. 斗笠圆盘链条15. 气动润滑二、判断题(正确的,在括号内打√;错误的,在括号内打×)1. ×2. ×3. √4. ×5. √6. √7. ×8. √9. √10. √三、选择题(将正确答案的序号填写在括号内)1. B2. C3. D四、简答题答案略第二节数控铣床/加工中心的坐标系一、填空题(将正确答案填写在横线上)1. 刀具工件2. 右手笛卡儿直角3. X Y Z4. A B C5. 刀具工件6. 正7. Z8. Z9. 右手笛卡儿10.A11.正12. 机床13. 限位开关14. 工件15.刀位点16. 底面中心钻尖球心刀尖17. 对刀程序起点18. 工件机床19. X、Y Z20. Z 高度二、判断题(正确的,在括号内打√;错误的,在括号内打×)1. ×2. √3. ×4. ×5. ×6. √7. √8. ×9. √10. ×11. √12. √13. √14. √15. √16. √17. ×18. ×三、选择题(将正确答案的序号填写在括号内)1. B2. D3. C4. C5. D6. A7. B8. C9. C10. D四、名词解释答案略。
五、简答题答案略。
第三节数控编程的基本知识一、填空题(将正确答案填写在横线上)1.几何形状2.手工编程自动编程3.手工4.自动5.程序校验6.字母数字和小数点符号7.字符字符组8.次序89.N10.G G11.续效失效12.地址数字13.毫米英寸度14.F 进给速度15.G94 G9516.S m/min r/min17.G96 G9718.刀具号T19.辅助M20.正反停止21.T M0622.喷雾开关23.M98 M9924.程序号二、判断题(正确的,在括号内打√;错误的,在括号内打×)1.√2.×3.√4.×5.√6.√7.√8.√9.√10.×11.×12.×13.√14.×15.√16.√17.√18.√19.√20.√三、选择题(将正确答案的序号填写在括号内)1.A2.D3.B4.B5.C6.A7.B9.C10.C11.B12.B13.C14.C15.D16.A17.A18.D19.A20.A21.D22.C23.D24.C25.C26.B四、名词解释答案略。
《数控铣床编程与操作项目教程》习题集附答案模块4
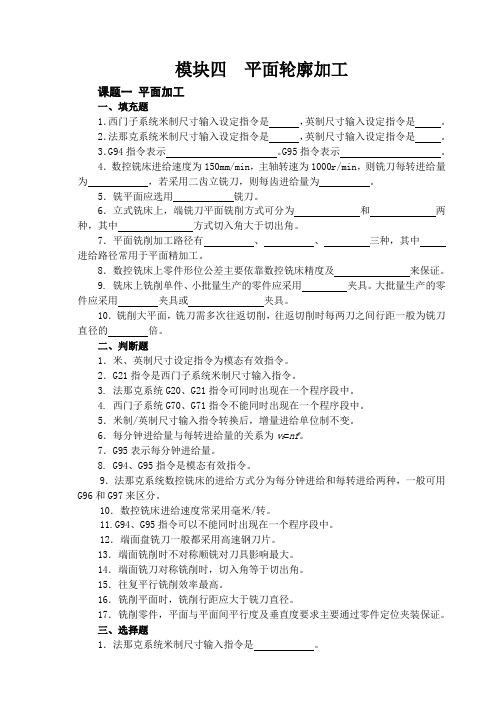
模块四平面轮廓加工课题一平面加工一、填充题1.西门子系统米制尺寸输入设定指令是,英制尺寸输入设定指令是。
2.法那克系统米制尺寸输入设定指令是,英制尺寸输入设定指令是。
3.G94指令表示。
G95指令表示。
4.数控铣床进给速度为150mm/min,主轴转速为1000r/min,则铣刀每转进给量为,若采用二齿立铣刀,则每齿进给量为。
5.铣平面应选用铣刀。
6.立式铣床上,端铣刀平面铣削方式可分为和两种,其中方式切入角大于切出角。
7.平面铣削加工路径有、、三种,其中进给路径常用于平面精加工。
8.数控铣床上零件形位公差主要依靠数控铣床精度及来保证。
9. 铣床上铣削单件、小批量生产的零件应采用夹具。
大批量生产的零件应采用夹具或夹具。
10.铣削大平面,铣刀需多次往返切削,往返切削时每两刀之间行距一般为铣刀直径的倍。
二、判断题1.米、英制尺寸设定指令为模态有效指令。
2.G21指令是西门子系统米制尺寸输入指令。
3. 法那克系统G20、G21指令可同时出现在一个程序段中。
4. 西门子系统G70、G71指令不能同时出现在一个程序段中。
5.米制/英制尺寸输入指令转换后,增量进给单位制不变。
6.每分钟进给量与每转进给量的关系为v f=nf。
7.G95表示每分钟进给量。
8. G94、G95指令是模态有效指令。
9.法那克系统数控铣床的进给方式分为每分钟进给和每转进给两种,一般可用G96和G97来区分。
10.数控铣床进给速度常采用毫米/转。
11.G94、G95指令可以不能同时出现在一个程序段中。
12.端面盘铣刀一般都采用高速钢刀片。
13.端面铣削时不对称顺铣对刀具影响最大。
14.端面铣刀对称铣削时,切入角等于切出角。
15.往复平行铣削效率最高。
16.铣削平面时,铣削行距应大于铣刀直径。
17.铣削零件,平面与平面间平行度及垂直度要求主要通过零件定位夹装保证。
三、选择题1.法那克系统米制尺寸输入指令是。
A. G71B. G70C. G21D. G202.西门子系统米制尺寸输入指令是。
(二)内外轮廓的铣削方法_数控加工工艺设计与程序编制(第3版)_[共2页]
![(二)内外轮廓的铣削方法_数控加工工艺设计与程序编制(第3版)_[共2页]](https://img.taocdn.com/s3/m/347a60cb59eef8c75fbfb3f4.png)
数控加工工艺设计与程序编制(第3版)
图6-1 凸模板零件图
如图6-3所示,面铣刀的圆周表面和端面上都有切削刃,端部切削刃为副切削刃。
面铣刀多制成套式镶齿结构,刀齿为高速钢或硬质合金,刀体材料为40Cr 。
图6-2 平面铣削 图6-3 面铣刀 高速钢面铣刀按国家标准规定,直径为80~250mm ,螺旋角为10°,刀齿数为10~26。
硬质合金面铣刀与高速钢面铣刀相比,铣削速度较高,加工效率高,加工表面质量也比较好,并可加工带有硬皮和淬硬层的工件,故得到广泛应用。
硬质合金面铣刀按刀片和刀齿的安装方式不同,可分为整体焊接式、机夹焊接式和可转位式3种。
其中可转位式面铣刀在数控加工中使用广泛。
标准可转位面铣刀的直径为16~630mm 。
选择面铣刀直径时,主要是根据工件宽度选择,同时要考虑机床的功率、刀具的位置和刀齿与工件的接触形式等,也可将机床主轴直径作为选取的依据,面铣刀直径可按D = 1.5d (D 为面铣刀直径,d 为主轴直径)选取。
一般来说,面铣刀的直径应比切宽大20%~50%。
(二)内外轮廓的铣削方法
1.铣削方式
铣削内、外轮廓时,有顺铣和逆铣两种方式。
(1)顺铣。
顺铣时,刀具旋转方向和进给方向相同,如图6-4所示。
顺铣开始时切屑的厚度为最大值,切削力是指向机床台面的。
《数控车床》理实一体化PPT 项目七 套类零件的编制与加工 任务二

知识三 内沟槽零件的编写与加工
实例15 内沟槽零件的编写与加工
任务二
2、 确定工件的装夹方式
工件是一个套类零件,并且轴的长度不是很长,采用工件的右端面和Φ35mm外圆作 为定位基准。使用普通三爪卡盘加紧工件,因外轮廓不需要加工,所以适当伸出一定的 长度下,保证零件装夹安全就行。取工件右端面的轴线上作为工件坐标系的原点,如图7 -11所示。
零件的加工程序,观看其加工路线轨迹,并进行加工。 用游标卡尺进行检测,根据实际尺寸调刀具磨损量,直至尺寸符合要求为止。 零件加工结束后进行检测,并把检测结果填写在表7-10中。(见下一页)。
知识三 内沟槽零件的编写与加工
实例15 内沟槽零件的编写与加工
7、 数控加工
表7-10 内沟槽零件评分表
任务二
1
内沟槽车刀刀位点的选择
2 内沟槽车刀的对刀方式
3
内沟槽零件的编写与加工
Contents
知识二 内沟槽车刀的对刀方式
n 取内沟槽车刀的刀尖为刀位点,对刀说明如下:
1)X轴对刀 主轴正转,移动内沟槽车刀,
使刀尖轻轻碰至工件内孔面(可以 取内孔车刀试车削的内孔表面)或 车一段内孔,Z方向退出刀具;停 车,测量内孔直径,如下图7-8, 然后进行面板操作,面板操作步骤 同外圆车刀车刀对刀步骤一致。
图7-11 工件装夹示意图
知识三 内沟槽零件的编写与加工
实例15 内沟槽零件的编写与加工
任务二
3、 确定数控加工工序
根据零件的加工要求,选用中心钻一把钻中心孔定位;Φ16麻花钻一把,用于钻通 孔;选用内孔车刀两把,用于粗、精车削加工;内沟槽槽车刀一把,用于切内槽。该零 件的数控加工工序卡如表7-6所示。
数控铣床加工中心加工工艺与编程第二版习题册参考答案

《数控铣床/加工中心加工工艺与编程(第二版)习题册》参考答案模块一数控机床编程与操作基础任务一认识数控机床及其操作面板一、填空题1.刀库刀具自动交换装置2.钼丝钨钼合金丝3.铣削镗削4.选择机床操作AUTO5.程序编辑手轮进给方式DNC二、选择题三、判断题四、简答题1.数控系统的输入/输出装置接受加工程序等各种外来信息,由数控装置进行处理和分配,向驱动机构发出执行命令。
伺服系统根据数控装置输出信号,经放大转换后驱动执行电机,带动机床运动部件按约定的速度和位置进行运动。
2.日本的FANUC数控系统:FANUC 0-MD、FANUC 0i-MA;德国的SIEMENS数控系统:SIEMENS 802D/C/S 、SIEMENS 840D/C;中国的华中数控系统:HNC-21M;北京航天数控系统:CASNUC 2100;美国的A-B数控系统;日本的三菱数控系统。
3.按数控机床的主轴位置分为:卧式机床、立式机床;按数控机床的用途分:数控铣床、加工中心、数控车床、数控钻床;数控电火花成形机床、数控线切割机床、数控激光加工机床;数控磨床、数控镗床、数控钻床。
任务二数控机床的手动操作1.对刀2.X轴的正Y轴的正Z轴的正3.机械偏心式寻边器电子式寻边器机械式Z向对刀器机外对刀仪4.机床坐标系传递切削力的主轴轴线5.Y6.机床参考点和机床原点不重合二、选择题三、判断题四、简答题1.FANUC 0i-Mate-TC(1)选择模式按钮“HANDLE”;(2)按下“超程解除”按钮不松开,同时按下“RESET”键,消除报警画面;(3)不松开“超程解除”按钮,让机床朝超程的反向进给,退出超行程位置。
2.(1)手动返回参考点,注意机床返回参考点前工作台、主轴位置是否恰当。
(2)利用“HANDLE”“JOG”驱动机床时,注意进给倍率的位置。
(3)避免机床接近极限位置,以免超程。
五、计算题略。
任务三数控程序输入与编辑一、填空题1.手工编程自动编程2.零件造型生成刀具轨迹后置处理生成加工程序3.1号4号4.模态指令非模态指令5./6.尺寸功能字进给功能字刀具功能字辅助功能字三、判断题四、简答题1.(1)分析零件图样;(2)确定加工工艺;(3)数值计算;(4)编写加工程序单;(5)制作控制介质;(6)程序校验。
- 1、下载文档前请自行甄别文档内容的完整性,平台不提供额外的编辑、内容补充、找答案等附加服务。
- 2、"仅部分预览"的文档,不可在线预览部分如存在完整性等问题,可反馈申请退款(可完整预览的文档不适用该条件!)。
- 3、如文档侵犯您的权益,请联系客服反馈,我们会尽快为您处理(人工客服工作时间:9:00-18:30)。
教案
车孔和磨孔时作退刀用或为了拉油
防止轴上的润滑剂溢
教学过程2、内沟槽车刀
内沟槽车刀与切断刀的几何形状相似,只是装夹方向相反,且在内孔中车槽。
加工小孔中的内沟槽车刀做成整体式内沟槽车刀,如图7-2和图7-3所示。
图7-2 图7-3
3、车内沟槽方法
宽度较小和要求不高的内沟槽,可以用主切削刃宽度等于槽宽的内沟槽刀,采用直进法一次车出。
较高或较宽的内沟槽,可采用直进法分几次车出。
粗车时,槽侧和槽底应留精车余量,然后根据槽宽、槽深要求进行精车。
深度浅、宽度大的内沟槽,可采用特殊角度的镗孔刀先车出内凹槽,再用内沟槽刀车出两侧面。
外圆粗、精镗孔。
40mm加工至接刀处。
三、程序编制
二、内三角螺纹加工
、相关工艺知识:
刀具选择:在数控车床上车削普通三角螺纹一般选用精密级机夹可转位不重
普通三角螺纹内孔径D=公称直径-P*1.0826+0.1~0.2 注:式中P为螺纹螺距, +0.1~0.2,是由于内孔加工螺纹后的变形补偿和螺纹间隙补偿量。
例如:毛坯为φ45mm×45mm的45钢,用FANUC 0i系统进行编程加工该零
件。